IF钢成品碳稳定控制的工业实践
IF钢300t RH的生产实践

00 % ,ed[ ]0 0 % ~ . 8 adt igt p rt e1 8 .6 n 0 .5 0 0 % n pn e ea r 60~1 0 a m u 0℃ ;a agni et ns t nt F O)ad 7 t ro n ci t i e( e j o ao h n
第 3 卷 第 6期 1
・
特 殊 钢
S PECI TEEL AL S
4 ・ 2 . De e e 2 0 c mb r 01
I F钢 3 0 t 0 的 生 产 实 践 RH
焦兴利 1 王 , 2 泉 张 虎
1 8 0 0~1 0℃ ; 6 7 吹氩 站 钢 包 顶 渣 的 ( e 和 ( a ) ( 1 , 分 别 由原 来 的 1. % 和 67降至 5 0 和 17 以增 加 F O) C O / A ) O 22 . .% .,
其 吸附夹杂 的能力 ; 根据生产数据 , 建立 了 R H脱碳操作 的 自动计算模 型 , 有效 提高 R H精炼过程 各项技术 指标的
J oXn l 一 i ig .Wa gQ a adZ a gH a i n u n n h n u
( e ta rna dSelRee rhIsi t 1C nrl o n te sae n tue,B in 0 8 ;2 Maa s a rna dSe l t I t ej g1 0 ’n h nIo n te Ld,Ma n h n2 3 0 ) i 0 1 Co ’ sa 4 0 0 a
A s a t B fr d cr o i n f igI te b 0 R nt i i rq i d t c n o c n et n 【 ≤ b t c e e eab nz gri n s l y a3 0 t H u i, t s e ur o o t l o v r r d C I r o i en F e e r ee
IF钢中成分及夹杂物的过程控制研究

IF钢中成分及夹杂物的过程控制研究一、本文概述随着现代工业的发展,钢铁材料作为国民经济的重要支柱,其质量和性能的提升对于满足社会生产的需求至关重要。
IF钢(Interstitial Free Steel,无间隙原子钢)作为一种优质的低碳钢,以其高强度、高韧性、良好的焊接性和成形性等特点,在汽车、石油、化工、建筑等领域得到了广泛应用。
然而,IF钢的生产过程中,钢中成分的控制以及夹杂物的控制对于其最终性能的影响至关重要。
因此,本文旨在深入研究IF钢中成分及夹杂物的过程控制,为提高IF钢的质量和性能提供理论支持和实践指导。
本文将首先介绍IF钢的基本特性和应用领域,阐述研究IF钢中成分及夹杂物过程控制的必要性。
接着,将重点分析IF钢生产过程中成分控制的关键因素,包括碳、氮、氧等主要元素的含量控制,以及合金元素的添加和调整。
还将探讨夹杂物对IF钢性能的影响及其形成机制,提出有效的夹杂物控制策略。
在此基础上,本文将总结国内外在IF钢成分及夹杂物过程控制方面的研究成果和进展,以期为我国IF钢生产技术的进步提供借鉴和参考。
通过本文的研究,期望能够为IF钢的生产过程优化提供理论依据,为提升我国钢铁工业的整体竞争力做出贡献。
二、IF钢的成分控制IF钢(Interstitial-Free Steel)作为一种高级别的深冲用钢,其成分控制对于最终产品的质量和性能具有至关重要的影响。
成分控制不仅关乎钢的强度、韧性、耐腐蚀性,还直接影响到其深冲加工性能和表面质量。
因此,对IF钢的成分进行精确控制是提升产品质量、满足市场需求的关键。
在IF钢的生产过程中,碳(C)、氮(N)和硫(S)等元素是需要特别关注的。
碳元素是影响IF钢性能的主要因素之一,通过降低钢中的碳含量,可以有效提高钢的深冲性能和焊接性能。
氮元素同样对钢的强度、韧性和焊接性有显著影响,因此需要通过精确控制冶炼和精炼过程来降低钢中的氮含量。
硫元素虽然在一定程度上可以提高钢的切削加工性能,但过高的硫含量会导致钢的韧性降低,因此也需要对其进行严格控制。
国内外超低碳IF钢炼钢工艺分析
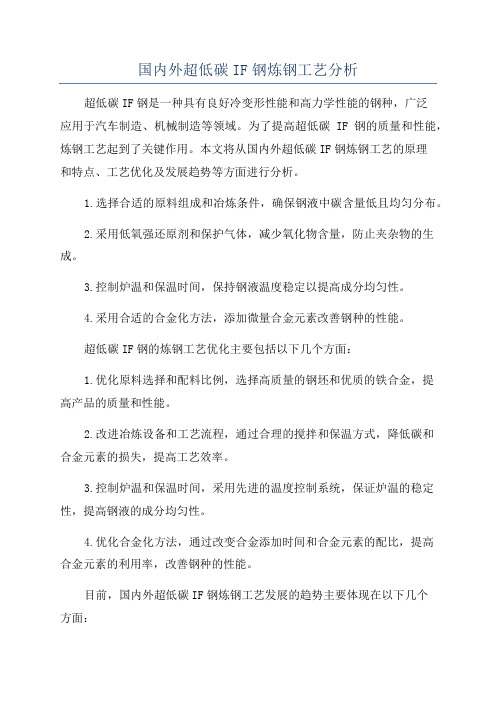
国内外超低碳IF钢炼钢工艺分析超低碳IF钢是一种具有良好冷变形性能和高力学性能的钢种,广泛应用于汽车制造、机械制造等领域。
为了提高超低碳IF钢的质量和性能,炼钢工艺起到了关键作用。
本文将从国内外超低碳IF钢炼钢工艺的原理和特点、工艺优化及发展趋势等方面进行分析。
1.选择合适的原料组成和冶炼条件,确保钢液中碳含量低且均匀分布。
2.采用低氧强还原剂和保护气体,减少氧化物含量,防止夹杂物的生成。
3.控制炉温和保温时间,保持钢液温度稳定以提高成分均匀性。
4.采用合适的合金化方法,添加微量合金元素改善钢种的性能。
超低碳IF钢的炼钢工艺优化主要包括以下几个方面:1.优化原料选择和配料比例,选择高质量的钢坯和优质的铁合金,提高产品的质量和性能。
2.改进冶炼设备和工艺流程,通过合理的搅拌和保温方式,降低碳和合金元素的损失,提高工艺效率。
3.控制炉温和保温时间,采用先进的温度控制系统,保证炉温的稳定性,提高钢液的成分均匀性。
4.优化合金化方法,通过改变合金添加时间和合金元素的配比,提高合金元素的利用率,改善钢种的性能。
目前,国内外超低碳IF钢炼钢工艺发展的趋势主要体现在以下几个方面:1.工艺自动化:通过引入先进的自动控制系统,实现对整个炼钢过程的自动化控制,提高生产的稳定性和质量。
2.工艺精细化:通过优化炼钢工艺参数和工艺流程,控制各个环节的时间和温度,实现精确的合金化和冶炼过程,提高产品的性能。
3.绿色环保:采用清洁能源和环保材料,减少二氧化碳的排放和对环境的污染,实现绿色炼钢。
4.资源循环利用:通过废钢回收和炼钢渣的综合利用,降低资源浪费和能源消耗,实现资源的循环利用。
综上所述,国内外超低碳IF钢炼钢工艺的发展正朝着工艺自动化、精细化、绿色环保和资源循环利用的方向发展。
这将进一步提高超低碳IF钢的质量和性能,满足不同领域对高性能钢的需求。
IF钢中成分及夹杂物的过程控制研究共3篇
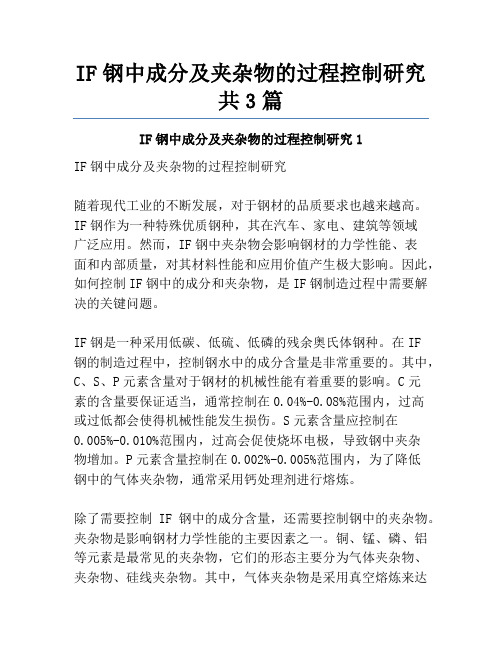
IF钢中成分及夹杂物的过程控制研究共3篇IF钢中成分及夹杂物的过程控制研究1IF钢中成分及夹杂物的过程控制研究随着现代工业的不断发展,对于钢材的品质要求也越来越高。
IF钢作为一种特殊优质钢种,其在汽车、家电、建筑等领域广泛应用。
然而,IF钢中夹杂物会影响钢材的力学性能、表面和内部质量,对其材料性能和应用价值产生极大影响。
因此,如何控制IF钢中的成分和夹杂物,是IF钢制造过程中需要解决的关键问题。
IF钢是一种采用低碳、低硫、低磷的残余奥氏体钢种。
在IF钢的制造过程中,控制钢水中的成分含量是非常重要的。
其中,C、S、P元素含量对于钢材的机械性能有着重要的影响。
C元素的含量要保证适当,通常控制在0.04%-0.08%范围内,过高或过低都会使得机械性能发生损伤。
S元素含量应控制在0.005%-0.010%范围内,过高会促使烧坏电极,导致钢中夹杂物增加。
P元素含量控制在0.002%-0.005%范围内,为了降低钢中的气体夹杂物,通常采用钙处理剂进行熔炼。
除了需要控制IF钢中的成分含量,还需要控制钢中的夹杂物。
夹杂物是影响钢材力学性能的主要因素之一。
铜、锰、磷、铝等元素是最常见的夹杂物,它们的形态主要分为气体夹杂物、夹杂物、硅线夹杂物。
其中,气体夹杂物是采用真空熔炼来达到控制的。
夹杂物控制主要采用铝剂、钝化剂来控制,将夹杂物和夹杂物粒子分散固溶。
夹杂物控制涉及到工艺流程中的温度、时间、气氛等多个因素。
其中,温度是控制夹杂物形成和发展的最主要因素。
在熔炼过程中,温度不稳定会导致夹杂物粗化、合并,影响到产品的质量。
时间是影响夹杂物生成的另一个因素。
时间越长,夹杂物的净化越好,但同时也会增加钢材的消耗和制造成本,因此需要在时间与效果之间做出平衡。
气氛对于夹杂物的控制也是至关重要的。
在IF钢制造过程中,要求钢水在加工过程中不氧化,因此需要高纯氧化铝和氮气配制的高保护因素。
总而言之,IF钢中成分及夹杂物的过程控制是IF钢提高品质的关键。
IF钢成品碳稳定控制的工业实践

( te Ma ig ln ,B T E ,B n i io ig1 7 2 ) Se l kn a t X S E L P e x L a nn 10 1
Ab t a t Th o g v s g t g t ef co swh c n u n et e s b ec nr l n fn s e r d c a b no s r c : r u h i e t a n a t r i h i f e c t l o to ih d p o u t r o f F n i i h l h a o i c I se l a d i t g a i g t e p o u t n p a t e o te n BX TEE t ep e o d t n o q i t e e o e te , n n e r t r d c o r c c fI se l n h i i F i S L, r c n i o f i u d se l f r h i l b RH,t e c n r lo e ab rz t n d r g RH n e c n r l n c b rz t n at rRH r a y e , h h o t n d c r u i ai u n o o i a d t o to a u i ai f h o r o e we e a l z d t e n me o a e n f u d t o to n s e r d c a b n sa l . h t d h s e o n c nr l ih d p o u t r o t b y b o i f c
R H前钢水的前题条件 、R H的脱碳控制及 R H后增 碳控制 3 个方面进行研究。
l 本钢 I F钢生产工 艺概 况
钢铁行业降碳行动方案

钢铁行业降碳行动方案全文共四篇示例,供读者参考第一篇示例:钢铁行业是全球工业生产中最重要的行业之一,但同时也是碳排放量最大的行业之一。
随着全球气候变暖问题日益严重,减少碳排放已成为全球各国共同面临的挑战。
钢铁行业作为高碳排放行业,应该积极参与降碳行动,减少对环境的污染,推动可持续发展。
一、降低能源消耗钢铁行业的生产过程消耗大量的能源,尤其是煤炭,其排放的二氧化碳是主要的温室气体之一。
降低能源消耗是降碳行动的首要任务。
钢铁企业可以通过技术改造,提高炉石煤气化效率,采用高效燃烧技术,减少燃料使用量,从而降低碳排放。
二、提高能源利用率钢铁行业在生产过程中会产生大量的余热和余气,利用这些资源可以有效提高能源利用率,减少碳排放。
钢铁企业可以建设余热发电厂,利用余热发电,提供给企业自身或者周边社区使用;还可以利用余气发电,将其转化为电能,提高生产效率。
三、推动碳交易碳交易是一种通过市场机制来减少碳排放的手段,通过设立碳排放权,让企业购买和出售碳排放权,来实现碳排放的减少。
钢铁企业可以主动参与碳交易,购买碳排放权来弥补自身的碳排放,同时也可以通过降低碳排放来赚取碳排放权的收益。
四、加强环保监管钢铁行业是一个高污染、高能耗的行业,环保监管工作尤为重要。
政府部门应该加强对钢铁企业的环保监管,严格执行环保法规和标准,要求企业减少碳排放,规范生产行为,推动企业向清洁、低碳发展方向转变。
五、加大科技创新力度科技创新是推动钢铁行业向低碳发展的主要力量。
钢铁企业应该加大科技研发投入,推动新技术、新材料的应用,提高生产效率,减少碳排放。
政府部门也应该加大对科技创新的支持,鼓励企业开展环保技术研究,推动行业向低碳方向发展。
钢铁行业降碳行动是全球气候变暖问题的一个重要方面。
钢铁企业应该积极采取措施,减少碳排放,降低对环境的影响,推动行业可持续发展。
政府部门应该加大环保监管力度,加强政策引导,促进钢铁行业转向清洁、低碳发展,共同保护地球环境,营造宜居的生态环境。
IF钢连铸增碳控制措施
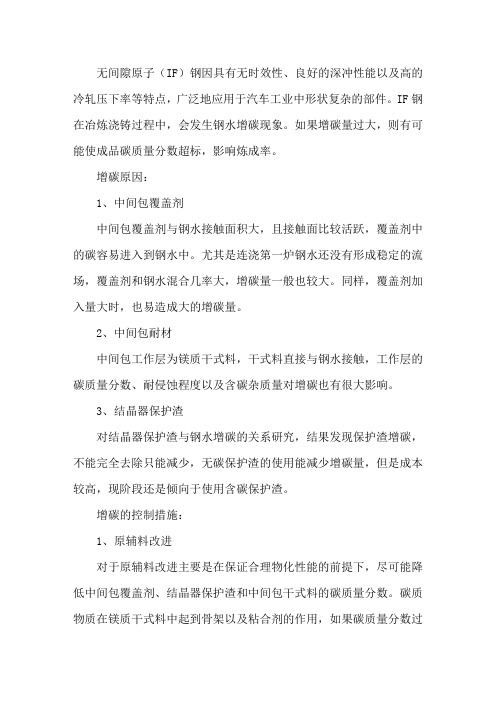
无间隙原子(IF)钢因具有无时效性、良好的深冲性能以及高的冷轧压下率等特点,广泛地应用于汽车工业中形状复杂的部件。
IF钢在冶炼浇铸过程中,会发生钢水增碳现象。
如果增碳量过大,则有可能使成品碳质量分数超标,影响炼成率。
增碳原因:1、中间包覆盖剂中间包覆盖剂与钢水接触面积大,且接触面比较活跃,覆盖剂中的碳容易进入到钢水中。
尤其是连浇第一炉钢水还没有形成稳定的流场,覆盖剂和钢水混合几率大,增碳量一般也较大。
同样,覆盖剂加入量大时,也易造成大的增碳量。
2、中间包耐材中间包工作层为镁质干式料,干式料直接与钢水接触,工作层的碳质量分数、耐侵蚀程度以及含碳杂质量对增碳也有很大影响。
3、结晶器保护渣对结晶器保护渣与钢水增碳的关系研究,结果发现保护渣增碳,不能完全去除只能减少,无碳保护渣的使用能减少增碳量,但是成本较高,现阶段还是倾向于使用含碳保护渣。
增碳的控制措施:1、原辅料改进对于原辅料改进主要是在保证合理物化性能的前提下,尽可能降低中间包覆盖剂、结晶器保护渣和中间包干式料的碳质量分数。
碳质物质在镁质干式料中起到骨架以及粘合剂的作用,如果碳质量分数过低,在烘烤时容易引起中间包塌陷。
为了解决这一问题,对干式料的配方进行了改进,消除了中间包塌陷。
2、操作方式改进对中间包覆盖剂操作的改进措施有:1)开浇炉次覆盖剂加入方法:当液面超过下挡墙时,加入100~150kg覆盖剂;当液面接近长水口下沿时加入400~450kg覆盖剂,开浇炉次覆盖剂加入量小于800kg。
2)连浇炉次覆盖剂加入量根据中间包钢水重量加入,确保中间包能够全覆盖,并且液渣层控制大于2mm即可。
3)加覆盖剂时,尽量减少中间包液面的波动。
对结晶器操作改进的措施有:1)加保护渣时,采用自动加料机进行加入,防止人工加入时对液面造成影响。
2)采用电磁制动,减少液面波动,控制液面波动值的标准差。
izaksjw 阳极氧化设备。
安钢超低碳IF钢生产工艺实践

‘
2 . 主要 工序控制
I F 钢以其优 良的加工 、 成型性能广泛应用于汽车 、
( 1 ) 铁水脱硫预处理控制
家电制造、 金属包装等领域。为了 改善品种结构, 随着2
为了减轻转炉脱硫负担, 在铁水预处理工序, 除了
0 . 0 0 2 %, 扒净渣外, 还对原料铁 座R H 真空精炼炉的建成投产, 安钢开始探索超低碳钢 要求脱硫铁水硫含量≤ 水温度提出了要求, 根据实践表明, 当铁水温度≥1 3 0 0 ℃ 种的生产冶炼工艺。 更容易扒净渣。 由于I F 钢不仅要求极低的 碳含量, 而 且对杂质元素 时, 如硫、 氮等的 含量也要求严格, 同时对钢水洁净度要求很 ( 2 ) 转炉冶炼工序控制 高, 生产难度很大。经过调整工艺路线, 改进生产工艺, 可的情况下, I F 钢的碳、 磷、 硫、 氮含量分别可以达到
0 . 0 0 3 %、 0 . 0 1 %、 0 . 0 1 %和0 . 0 0 3 %以下 , 不更换浸入式水1 5
在超低碳钢冶炼过程中, 由 于精炼工序不能进行脱 此必须减少转炉人炉的硫含量。为此, 在转炉工序采用 优质冶金石灰、 低硫白云石等造渣料、 低硫废钢、 烧结矿 等冷却剂, 要求炉渣二元碱度> 1 3 . 5 , 同时增大渣量以提 高转炉脱磷、 脱硫率。通过这些措施使得转炉出钢硫含
调整。同时, 通过添加适量改质剂和铝屑对钢渣进行改
三、 l F 钢生产工艺优化
1 . 精炼工艺路线调整
为了保证工序的稳定顺行以及钢水质量, 采用了 L F — R H 精炼工艺路线。 L F — R H 的 组合精炼方式, 可以 利 用L F 精炼在升温、 去除夹杂物方面的强大功能,
及钢水纯净度, 要求终点碳含量小于等于0 . 0 5 %, 氧含 的问 题: 一是为了 保证R H 到 站温度, 需要转炉 终点 温度太 以 高( 大于等于1 7 0 0 ℃) , 对转炉操作和维护影响很大; 二是 量 5 0 0 ~ 6 0 0 p p m 。为了控制氮含量 , 复吹转炉除了全程吹
国内外超低碳IF钢炼钢工艺分析

国内外超低碳IF钢炼钢工艺分析超低碳IF钢是一种具有优异冷成形性能和高强度的钢种,广泛应用于汽车制造、家用电器、建筑结构等领域。
研究国内外超低碳IF钢炼钢工艺对于提高钢材质量和性能具有重要意义。
本文将分析国内外超低碳IF钢炼钢工艺的主要内容。
首先,国内外超低碳IF钢炼钢工艺的主要特点是采用先进的冶炼设备和工艺流程,以确保钢材的低碳含量和高纯度。
一般来说,超低碳IF 钢的碳含量在0.003%-0.007%范围内,硫、氮和氧等杂质含量也要控制在较低水平。
其次,国内外超低碳IF钢炼钢工艺主要包括原料准备、炼钢和连铸三个环节。
首先,原料准备是确保钢材质量的基础,包括选用高质量的铁矿石和冶炼副料,以及进行预处理和混合。
其次,炼钢过程是将原料进行高温冶炼和精炼的过程,以获得符合要求的钢液。
炼钢过程主要包括高炉冶炼、转炉冶炼和电炉冶炼等。
其中,电炉冶炼是一种较为常用的炼钢方式,具有能量控制和操作灵活等优点。
最后,连铸是将炼得的钢液浇铸成坯料的过程,主要包括普通铸造和连铸两种方式。
超低碳IF钢一般采用连铸工艺,以获得均匀的组织和良好的机械性能。
此外,国内外超低碳IF钢炼钢工艺中还广泛应用了一系列的技术手段和措施,以提高钢材的质量和性能。
例如,采用脱氧剂和渣融剂进行钢液精炼,控制冶炼温度和保持时间,以及进行深度净化处理等。
同时,还可以通过添加微量合金元素、采用定向凝固和控制速度冷却等方式,进一步改善钢材的组织和性能。
综上所述,国内外超低碳IF钢炼钢工艺的主要内容包括原料准备、炼钢和连铸三个环节。
炼钢工艺主要采用先进的冶炼设备和工艺流程,以确保钢材的低碳含量和高纯度。
此外,还应用了一系列的技术手段和措施,以提高钢材的质量和性能。
这些工艺和技术的应用为国内外超低碳IF钢的生产提供了有力支持,也为相关行业的发展提供了优质材料。
但是,炼钢工艺的优化和改进仍然是当前研究的重要方向,以满足不断提高的钢材需求和环境保护要求。
IF钢性能影响因素及控制措施

on
IF steel performance were more,the article carried
on
the analysis mainly from the composition controlling of IF steel,hot—rolling production
technique
schedule
and
SO
On.The results
showed that,the
steel
reason
Hale Waihona Puke of IF steel performance
unsteady was the higher Ti
content,“ng
making composition controlling process
1
影响Ⅲ钢性能的因素分析
根据2009年生产实绩数据.笔者对球钢炉
次代表成分,性能和轧制实绩数据进行了回归, 其回归方程为: 屈服强度=230+11 695C碳实绩一2 350S 实绩一53511钛实绩+3 862N
Ti一礤钢.供给下游用户用于各种深冲零件,但
在进行冲压性能检测中发现部分钢卷的性能偏 硬。不能达到理想要求,用户在使用过程中也 反映部分钢卷出现开裂的情况。
carbureting was large,the hot rolling temperature
schedule
had tO be
op"tunu脚,moreover
the corresponding prevention and the controlling measures were proposed,striking effect
IF钢碳含量的过程控制_卿家胜
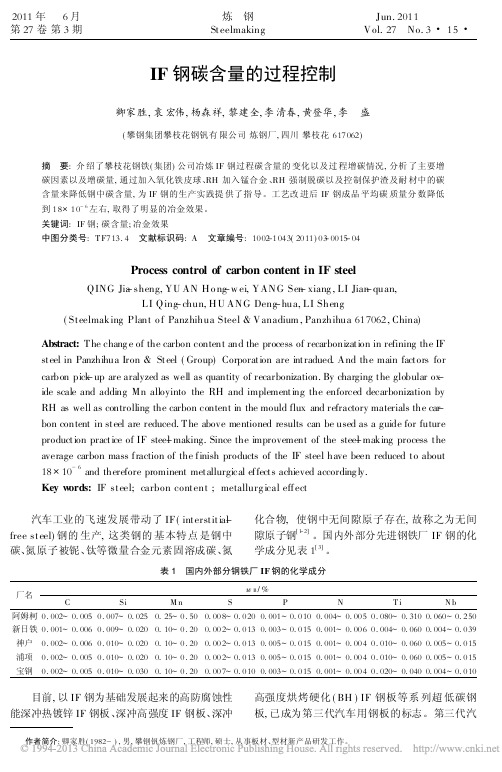
内, 钢中碳含量急剧降低。5~ 8 m in 钢水中碳质 量分数降低了0. 001 4 % ~ 0. 006 6 % , 此阶段钢 中碳含量较高, 碳与氧反应属一级反应, 脱碳速率 与钢中氧含 量成正 比。在 自然脱 碳处 理 8 min 后, 钢液中碳处于低碳区, 钢中的氧含量较高, 此 时碳的扩散成为脱碳反应的限制性环节, 脱碳速 率由钢中碳的传质速度决定[ 7-8] 。
1. 2 RH 过程碳含量变化情况
在 RH 处理过程中, 每间隔 5 m in 取样做碳 含量的分析, 整个 RH 处理过程碳含量变化如表 3 所示。
表 3 RH 处理各时段碳质量分数的变 化情况
炉号
10 464 4 10 464 5 10 464 6
RH 进站 0. 032 0. 025 0. 026
1. 3 过铸过程钢中增碳分析
对中间包和结晶器浇铸过程的前、中、后分别 取样, 碳含量的变化情况见表 4 所示。
由表 4 可见, 中间包浇铸过程钢水中碳含量 有所增加, w ( C) = 0. 000 3 % ~ 0. 000 4 % , 主 要是因为中包覆盖剂使用的主料、辅料和耐火砖 中的部分碳进入钢水; 结晶器浇铸过程 w ( C) = 0. 000 3 % ~ 0. 000 5 % , 这主要来源于保护渣和 耐火砖中的碳。
1. 1 出钢至 RH 进站过程碳含量变化情况
IF 钢出钢至 RH 进站过程碳含量变化包括:
出钢后 到 L F 工序 增碳, LF 至 RH 工 序增 碳。 LF 增碳因素主要是由于电极加热过程中增加碳 含量, 平均碳 质量分数 增量为 0. 003 % 。出钢至 RH 进站过程碳含量变化情况见表 2 所示。
IF钢的技术控制

T 和 N , I 中的 间隙原 子 ( N 得 以消 除 , i b 使 F钢 C、 )
得到纯净 的铁素体基体 , 从而消除 间隙原 子 的不利
影响 , 使钢具 有高的 r 。按 照添加 的合金元 素分 值 类, 目前生产 的 I 有两 种 , F钢 即单一 添加 T 的 r i r i
・
4 4・
梅 山科技
21 0 0年第 3期
I Fห้องสมุดไป่ตู้的 技术 控制
冉从锦 吴德 润
( 山钢铁 公 司制造部 南京 梅
20 3 ) 10 9
摘 要 : 简述 了 I F钢的产 品特性 , 分析 了钢 中主要 元 素 对 I 力 学性 能 的影 响 , 绍 了 F钢 介
梅钢 生产 I 的工 艺及 现状 , 比分析 了试验 前后 I F钢 对 F钢的性 能 变化 。 关键 词 : I F钢 ; 素 ; 能 ; 艺 ; 元 性 工 试验
是 低 的屈 服强度 和高 的延伸率 。并且 随着钢 中固
态或 者钢 液凝 固过 程 中形 成 的 TN 比较 粗 大 , i 而
且分布稀疏 , 并不 能有效 阻止 晶粒 长大 , 不能起 到 强化作用 。钢液凝 固 以后 析 出细小 的 TN颗 粒很 i
溶 C含量 的增 加 ,1 1织 构 密度 下降 , 品时效 {1 } 产
Te h c lCo r lo F t e c nia nt o fl S e l
R nC ni W eu a ogi n uD rn
( a uat igD pr et f rn& Sel o , aj g2 0 3 M n f u n eat n o cr m oI t . N ni 10 9) eC n
IF钢连铸过程增碳控制

a n d e x t r e me l y— l o w c a r b o n c o n t e n t ,mo l d c a s t i n g p o wd e r wi t h t h i c k h i g h —v i s c o s i t y mo l t e n l a y e r (C≤
围为 ( 1 1 . 8~ 6 3 . 9 )× 1 0 ~。分析 认为 , 造成 I F钢 成 品碳 含量超 标 的 主要 原 因是 连铸 过 程 增 碳 , 平 均 增
碳 9 . 1×1 0~。 3 连铸过 程增 碳原 因
连铸过 程增 碳 主 要包 括 中间 包 增 碳 、 结 晶 器 增 碳, 而 中间 包增 碳 主 要 由 于长 水 口、 中包 干 式料 、 中 包 覆 盖剂 、 塞棒 、 上水 口等 含碳 耐材 与钢水 接触 造 成
攀钢IF钢生产中碳的控制

1 引言
目前 , I 钢为基础发展起来的高防腐蚀性能 以 F 深冲热镀锌 I 钢板 、 F 深冲高强度 I 钢板、 F 深冲高强 度烘 烤硬化 ( H)F钢 板 等 系列 超 低 碳 钢 , B I 已成 为 第三代 汽 车用钢 板 的标 志 。第三代 汽 车用钢 板不但 对钢质量的要求 日益提高 , 对钢 中碳含量也提出了 更高的要求 , 特别是超深冲用钢 , 要求钢中碳含量控 制在 3 0×1 以内。 0
I 冶炼 技术 发 展 到今 天 , F钢 已形 成 了“ 水 预 铁
处理( 脱硫、 脱硅、 脱磷) 一转炉冶炼 ( 脱碳、 脱磷 ) 一 炉外精炼( 脱碳、 脱气 、 去除夹杂 ) 一连铸 ” 的基本工
艺 流程 。R H脱 碳 是 I F钢 生 产 中最 重 要 的脱 碳 环
在真空室内的碳氧化学反应的反映界面积增大。但 过大 的吹氩 量会导 致钢水 喷溅 , 常危 险 , 以一 般 非 所
[ bt c] C r ncn o adi a rn une at s fFS e a a se azi ain A s at r a o t l n g j f ec f o t l r a l i d nPnh u o b o r t m o i u migU iesyo cec n eh ooy K n ig 6 09 , u nn 1 K n n nvri fSi eadT cn l , u mn 50 3 Y n a ; t n g 2 Pnhh aI nadSel eerhIstt,a ziu 6 70 Scu n . aziu o n te R sac tue Pnhh a 10 0,iha ) r ni
,
环流量 的效果在某 个值 以上是呈饱 和状态 的。
首钢京唐IF钢RH精炼工艺开发实践

摘 要 :本文介绍了首钢京唐公司 IF 钢精炼工艺开发过程。IF 钢冶炼工艺控制关键是碳、氮含量成分控制。IF 钢碳含量控制的关
键是 RH 脱碳过程控制、防止合金增碳和精炼结束到中间包增碳,对应的措施有控制进站碳≤ 0.04%、控制过程废钢加入量、RH 脱
备注 2(TC 干空气,67Pa 时
2 IF钢冶炼工艺控制技术介绍 2.1 IF 钢的成分和生产工艺路线
成 分 :W[C] ≤ 0.003%wt( 少 数 钢 种 要 求 ≤ 0.0015%wt), w[Si] ≤ 0.03%wt,w[Mn]0.10~0.20%wt,w[P] ≤ 0.02%wt, w[S] ≤ 0.015%wt,w[Al]0.01~0.06%wt,W[N] ≤ 0.004%wt( 少数钢 种要求≤ 0.003%wt),W[Ti] ≤ 0.12%wt。
RH 脱碳结束后对钢水进行脱氧合金化,由于加入的合金 和脱氧剂自身含有微量碳或混入含碳量较高的合金,可能会造 成增碳。实际生产过程由于不恰当使用合金造成的增碳可能在 5~10×10-4%,而 由 于 混 料 原 因 造 成 的 增 碳 可 达 30×10-4%。采 用微碳锰铁或金属锰调整锰含量、以高钛含量的 70% 钛合金 取代 30% 钛合金,可以大幅度减少合金增碳,再严格管理实现 RH 清洁上料,RH 脱碳结束至 RH 离站一般增碳可稳定控制在 1~2×10-4%。 3.3 防止精炼结束到中间包增碳
碳过程辅助钢包底吹、清洁上料和使用无碳耐材等。IF 钢氮含量控制的关键是控制好转炉吹炼过程脱氮效果、防止 RH 吸氮。
关键词 :成分控制 ;脱碳 ;中间包增碳 ;无碳钢包 ;脱氮
中图分类号 :X52
鞍钢二炼钢if钢碳成分控制实践
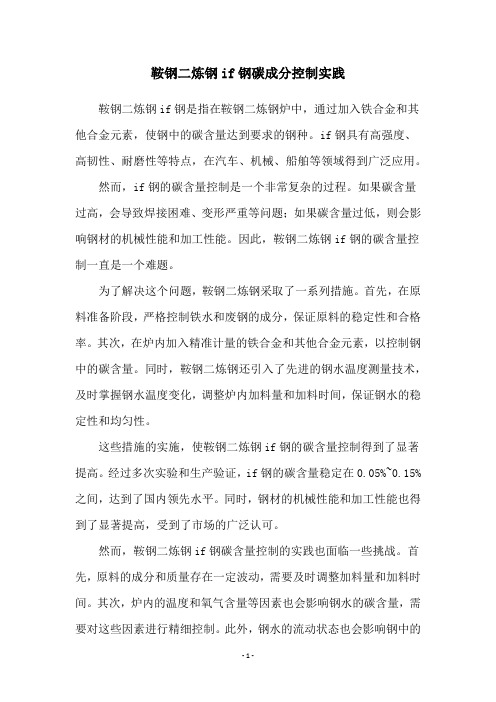
鞍钢二炼钢if钢碳成分控制实践鞍钢二炼钢if钢是指在鞍钢二炼钢炉中,通过加入铁合金和其他合金元素,使钢中的碳含量达到要求的钢种。
if钢具有高强度、高韧性、耐磨性等特点,在汽车、机械、船舶等领域得到广泛应用。
然而,if钢的碳含量控制是一个非常复杂的过程。
如果碳含量过高,会导致焊接困难、变形严重等问题;如果碳含量过低,则会影响钢材的机械性能和加工性能。
因此,鞍钢二炼钢if钢的碳含量控制一直是一个难题。
为了解决这个问题,鞍钢二炼钢采取了一系列措施。
首先,在原料准备阶段,严格控制铁水和废钢的成分,保证原料的稳定性和合格率。
其次,在炉内加入精准计量的铁合金和其他合金元素,以控制钢中的碳含量。
同时,鞍钢二炼钢还引入了先进的钢水温度测量技术,及时掌握钢水温度变化,调整炉内加料量和加料时间,保证钢水的稳定性和均匀性。
这些措施的实施,使鞍钢二炼钢if钢的碳含量控制得到了显著提高。
经过多次实验和生产验证,if钢的碳含量稳定在0.05%~0.15%之间,达到了国内领先水平。
同时,钢材的机械性能和加工性能也得到了显著提高,受到了市场的广泛认可。
然而,鞍钢二炼钢if钢碳含量控制的实践也面临一些挑战。
首先,原料的成分和质量存在一定波动,需要及时调整加料量和加料时间。
其次,炉内的温度和氧气含量等因素也会影响钢水的碳含量,需要对这些因素进行精细控制。
此外,钢水的流动状态也会影响钢中的碳含量分布,需要通过优化炉型和操作参数等手段进行改善。
综上所述,鞍钢二炼钢if钢碳含量控制实践是一个复杂而又关键的过程。
通过引入先进技术和工艺,结合实践经验和不断创新,鞍钢二炼钢成功实现了if钢碳含量的精准控制,为国内if钢的发展做出了重要贡献。
未来,鞍钢二炼钢将继续加强技术创新和工艺优化,为if钢的发展提供更加优质的钢材产品。
IF钢试生产实践

IF钢试生产实践袁方明1,王新华1,刘秀梅1,李 宏1,王万军1,张富强2,孙 群2,李 超2(1.北京科技大学冶金学院,北京100083;2.鞍山钢铁(集团)公司,辽宁鞍山114021)摘 要:为提高鞍钢三炼钢生产的IF钢质量,对三炼钢转炉-RH精炼-连铸生产IF钢的工艺过程开展了较为系统的分析研究。
研究发现试生产中RH真空精炼过程[C]含量过高,浇铸过程中增碳、二次氧化比较严重,经改进调整之后,铸坯中w(C)在30×10-6左右,w(N)在25×10-6以下,w(T.O)在20×10-6左右,达到了较高的洁净度水平。
关键词:IF钢;RH精炼;连铸中图分类号:TF762 文献标识码:B 文章编号:100221043(2004)0620013205R esearch of IF Steel Process at Anshan SteelYUAN Fang2ming1,WAN G Xin2hua1,L IU Xiu2mei1,L I Hong1,WAN G Wan2jun1,ZHAN G Fu2qiang2,SUN Qun2,L I Chao2(1.Metallurgy School of University of Science&Technology Beijing,Beijing100083,China;2.Anshan Iron&Steel Corp.,Anshan114021,China)Abstract:In order to improve the quality of IF steel.a systematic investigation in BOF2RH2 CC process route for production of the steel has been made in No.3Steel2making Plant of Anshan Steel Corp.Results show that[C]content in the slab exceeds the limit of IF steel in vacuum refining and carbon pick2up and reoxidization tremendously occurs during continuous casting.By appropriate readjustment of technologies the[C]content in slab has been cut down to about30ppm,[N]to25ppm and T[O]to20ppm and thereby higher level of cleanliness attained for the slab.K ey w ords:IF steel;RH refining;continuous casting 鞍山钢铁(集团)公司第三炼钢厂(以下简称鞍钢三炼钢)经过近年来的技术改造,已经具备了生产优质深冲、超深冲钢的设备条件,IF钢的生产已取得很大的进展,超深冲冷轧薄板各项性能指标初步满足了客户的要求,但在成分控制、铸坯洁净度方面还存在一定的问题,需要进一步改善。
- 1、下载文档前请自行甄别文档内容的完整性,平台不提供额外的编辑、内容补充、找答案等附加服务。
- 2、"仅部分预览"的文档,不可在线预览部分如存在完整性等问题,可反馈申请退款(可完整预览的文档不适用该条件!)。
- 3、如文档侵犯您的权益,请联系客服反馈,我们会尽快为您处理(人工客服工作时间:9:00-18:30)。
IF钢成品碳稳定控制的工业实践薛文辉(本溪钢铁公司炼钢厂,本溪 117021)摘 要通过对影响IF钢成品碳稳定控制的因素的研究,结合本钢IF钢的生产实践,对RH前钢水的前提条件、RH过程的脱碳控制及RH后的增碳控制方面进行分析,找出稳定控制成品碳的方法。
关键词 IF钢成品碳稳定控制Industrial Practice of Stable Control on Finished ProductCarbon of IF SteelXue Wenhui(Steel-making Plant , Benxi Iron And Steel Group Company,Benxi, 117021)Abstract Through investigating the factors which influence the stable control on finished product carbon of IF steel, and integrating the production practice of IF steel in Bengang, the precondition of liquid steel before RH, the control on decarburization during RH and the control on carburetion after RH were analyzed, the method has been found to control finished product carbon stably.Key words IF steel, finished product carbon, stable control碳作为主要的间隙原子会使IF钢的塑性降低,极大地影响IF钢的深冲性能。
因此IF钢对钢种成品碳都有较严格的要求,一般钢种要求低于30×10-6,有些特殊钢种对碳还有更低的要求。
目前IF钢的RH脱碳工艺已相当成熟,采用RH真空脱碳的热力学及动力学研究也已非常全面。
但对于IF钢生产企业,要获得较稳定且低碳成品碳含量,除了RH脱碳能力外,较好的钢水条件,稳定的过程增碳量也是必不可少的条件,也是生产过程中影响成品碳稳定性的关键因素。
本文主要根据本钢IF钢的生产实际,结合超低碳钢生产过程中影响碳控制稳定性的因素进行研究,介绍本钢成品碳稳定控制方面的研究和实践。
1 本钢IF钢生产工艺概况本钢从2003年起进行IF钢生产,目前年产量接近70万吨。
采用的生产工艺包括通过铁水脱硫预处理设备对铁水进行脱硫;顶底复吹转炉进行钢水冶炼;RH-TB处理进行深脱碳及脱气处理;板坯连铸机进行浇铸。
其主要设备的技术参数见表1。
表1 IF钢生产工艺的主要设备技术参数项目设备技术参数预处理设备达涅利引进的铁水预处理设备转炉设备公称150t,采用五孔喷枪的顶底复吹转炉RH精炼设备四级蒸气喷射泵的RH-TB设备板坯连铸设备全程保护浇铸的大板坯连铸机薛文辉(1971—),男,炼钢高级工程师,主要研究方向为连铸工艺及铸坯质量,AWH1971@第八届(2011)中国钢铁年会论文集2 碳在各工序的变化规律铁水原料经转炉及RH 进行脱碳最终得到超低碳钢,由于转炉的脱碳能力较大,因此铁水碳含量不会对最终的成品碳产生影响,而转炉终点至成品碳的统计结果如图1所示。
从图1中可知,RH 脱碳终点碳为各工序的最低值,而连铸过程则呈现一定的增碳趋势,RH 前的ω(C)基本控制在300~600×10-6,通过RH 深脱碳后将w(C)控制在20×10-6以内,而连铸过程的增碳质量应控制在3×10-6以内。
因此要想将成品w(C)控制稳定,必须从RH 前钢水的前提条件、RH 的脱碳控制及RH 后工序的增碳控制3个方面进行研究。
图1 冶炼过程中碳变化图3 RH 前钢水的前提条件对脱碳的影响真空脱碳前碳氧的不同直接影响脱碳的具体操作和处理时间[1]。
而RH 前钢水的温度可直接导致RH 脱碳是否需要升温操作。
因此真空脱碳前钢水的碳、氧含量及钢水温度是否合理非常重要。
从脱碳最初的热力学条件限制来讲,最为理想的碳、氧初始量为:钢中C 质量分数约为350×10-6,钢中O 质量分数约为600×10-6 [2]。
RH 前钢水温度与过程温降有关,应以避免大幅度升温为准。
3.1 RH 前钢水碳对终点碳的影响本钢RH 前碳含量有一定波动,2010年9月炼钢厂超低碳钢的RH 前碳含量如图2所示。
图2 2010年9月炼钢厂RH 前碳含量从图2可见,本钢RH 前碳含量基本在0.03%~0.06%之间。
RH 前不同碳含量对应RH 终点碳的平均值如图3所示。
图3 RH 前碳含量与RH 终点碳的关系IF钢成品碳稳定控制的工业实践从图3可见,RH前碳含量低时对应RH终点碳略低,这种关系在具体炉次上体现不明显,而在多炉次的统计结果规律性较强。
这是因为RH前碳并不是直接导致终点碳低,虽然RH前碳较高,只要钢中的氧充分RH前5min在大泵时都可将碳脱到100×10-6以下,但由于转炉的碳氧积相对固定,较多的碳含量对应钢种氧含量相对较低,而脱碳耗氧量是相对一定的,因此RH前较高的碳含量会导致前钢中的氧相对低,且前期耗氧量相对高,因此会导致前期补氧操作增加,而补氧过程会造成RH脱碳钢的真空度相对较高,因此造成RH终点碳相对略高。
3.2 RH前钢氧对终点碳的影响转炉的碳氧积相对稳定,除非钢水过氧化情况外,只要保证钢水的碳,钢中氧便可以满足要求,但由于超低碳钢存在顶渣改质的情况,因此存在改质剂质量及加入操作对钢中氧产生影响的问题。
正常情况下,对于具体的RH,每脱100×10-6碳所耗氧值是相对固定。
RH前氧的理想值为合适的RH脱碳终点氧与脱碳耗氧的和。
本钢目前RH前氧基本控制在500~700×10-6,较高的RH前氧对脱碳是有利的,但由于脱碳结束时钢中残氧较多,铝脱氧产物将对钢水的洁净度造成影响,因此RH前中应控制过高。
从脱碳原理上讲,较低的RH前是可以通过过程补氧得到解决的,但由于补氧会对脱碳过程中的真空度造成影响,而正常处理时间是一定的,因此会间接造成脱碳时间减少,同时RH的补氧与会造成顶渣氧含量增加,对钢水洁净度产生影响。
3.3 RH前温度对终点碳的影响不同钢厂对RH前温度的要求是不同的,因为不同钢厂钢包温降及RH过程温降是不同的,过低的RH 前温度会造成RH脱碳过程产生多次升温。
对本钢8~10月1117炉次,RH脱碳过程升温和不升温的平均RH终点碳统计结果如图4所示。
图4 RH过程升温对终点碳的影响从图4可知,RH过程升温操作与不升温相比,平均终点碳增加了2.35×10-6。
其主要原因为升温过程是先向钢水进行补氧,而本钢目前补氧时真空度降低较多,有时必须改泵,这样造成低真空度下的纯脱碳时间减少,升温过程的加铝使钢水的局部氧较低,面造成钢水的某此局部碳含量较高,在脱氧后净循环时随差钢水的均匀造成RH终点碳较高。
因此RH前温度的控制应以RH不升温或少升温为准。
4 RH过程的脱碳控制RH脱碳主要利用钢中的C、O进行反应生产以CO气体,通过对真空室抽真空降低CO分压使反应向生产CO气体的方向进行,具体反应式见式(1)。
[C]+[O]={CO}(1)由于该反应是在真空室中进行,因此该反应的热力学方面不需考虑,而动力学方面主要考虑的是脱碳速度,其表达式可见式(2)dw([C])/dt=-[(D×A)/(σ×V)]×w([C-Ce] (2)式(2)中,dw([C])/dt为脱碳速度;[(D×A)/(σ×V)]为反应速度常数Kc,其中D为扩散系数,σ为相界面厚第八届(2011)中国钢铁年会论文集度;A为反应界面积;V为钢液体积;C为原始碳浓度;Ce为平衡碳浓度。
由式(2)可知,增加反应速度常数和增加碳的浓度差均增加RH的脱碳反应速度。
对于已经正常使用的RH,真空度的稳定、过程补氧及终点氧的控制在生产过程中都是非常重要的。
4.1 RH真空度对脱碳的影响RH脱碳原理是通过抽真空降低CO的分压使反应进行,因为在常温下当钢水中C降低到一定水平时,过多的氧只能与铁反应而无法进行脱碳,因此一定的真空度是生产超低碳钢的前提条件,且越低的真空度对脱碳越有利。
本钢1号RH由于投产较早,目前真空度只能达到250Pa,而4号RH正常处理过程真空度可达到100Pa以内,其全部为老系统铸机供钢,钢水条件一致,对8~10月平均中包w(C)进行统计,结果见表2。
表2真空度对RH脱碳的影响最低真空度处理工位统计炉数平均中包w(C)/Pa1号RH25016419.614号RH10017917.06从表2中可看出,采用1号RH,虽然真空度达不到100Pa以内,中包平均成品碳含量也可达到20×10-6以内,但与最低真空度较低的4号RH相比,中包平均w(C)高2.55×10-6。
在RH最低真空较高的情况下,前期脱碳基本没有影响,因为钢中的碳含量较高,脱碳较剧烈,但当钢水中的碳含量较低的脱碳后期时,由于最低真空度高,平衡碳浓度相对高造成钢中碳的浓度差低,脱碳速度降低,因此脱碳终点的碳含量较高。
目前本钢在生产18×10-6以内的特殊钢种时不在1号RH处理。
4.2过程补氧对过程脱碳的影响在大生产过程中由于RH前氧有较大波动,当RH前氧不满足要求时,需进行补氧,本钢目前有近40%的炉次进行补氧,从本钢生产数据的统计结果看,补氧炉次的平均RH终点碳与不补氧炉次RH脱碳终点碳含量的影响见图5。
补氧炉次的终点平均碳与不补氧炉次相比高近1×10-6。
实际生产过程中,随着补氧量的增加对脱碳终点的影响也增加,因此减少过程补氧对降低RH终点碳是有利的。
图5 RH过程补氧对终点碳的影响此外,补氧时机也对脱碳有影响,生产实践证明早补氧比晚补对脱碳有利,但补氧过早会影响真空室压力的降低,目前本钢补氧在开泵2min左右,当真空度达到使钢水形成循环时进行。
一般根据RH前碳氧值,尽可能一次将氧补到合适。
4.3 RH终点氧对碳的影响从原理上讲,高氧势有利于脱碳,因此钢水氧高有利于反应进行,目前本钢脱碳终点氧控制在250×10-6~400×10-6之间,图6显示本钢实际生产中RH脱碳终点氧与终点碳的对应关系,从图中见看,较高的脱碳终点氧有降低终点碳的趋势,但总体上看,在250×10−6~400×10-6之间终点碳的变化不很明显。
IF钢成品碳稳定控制的工业实践图6 RH脱碳终点O与终点C的关系由于较高的脱碳终点氧会使脱氧铝增加,脱氧产物形成的夹杂物增加,从而影响钢水的洁净度,造成中包水口堵塞及后部工序的夹杂降级几率增加,因此应根据实际情况选择合适的终点氧含量控制。