影响介耗的因素分析.
重介选煤厂介耗的分析及对策
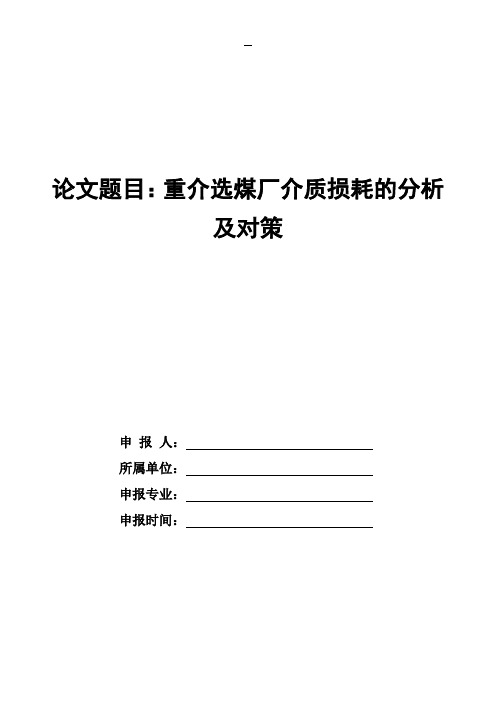
论文题目:重介选煤厂介质损耗的分析及对策申报人:所属单位:申报专业:申报时间:重介选煤厂介质损耗的分析及对策在重介选煤过程中,重介悬浮液加重质(磁铁矿粉)的损耗是避免不了的。
而介质损耗一直是重介选煤厂一项重要的技术评价指标。
通常分选块煤的介耗要比分选末煤时低,用低密度悬浮液时比用高密度悬浮液时低。
按选煤厂设计规范规定,吨原煤介质损耗指标是:块煤系统为0.2~0.3kg,末煤系统为0.5~1.0k g。
事实上,选煤厂极少有能达到上述指标的。
目前,吨原煤介质损耗较先进的指标在1.5kg左右,一般在2~3kg,高的在5~6kg。
因此,对重介选煤厂影响介质损耗因素进行系统分析十分必要。
选煤厂介质损耗高时,一方面可能是因煤质变化较大而使原设计的系统不相匹配或设计存在缺陷;另一方面可能是生产管理问题,这就需要在生产中进行有效管理,减少管理损失,控制技术损失。
一、影响介耗的因素及对策选煤厂介质损耗(简称:介耗)常规分为管理损失和技术损失两方面。
管理损失一般较直观,主要表现在跑、冒、滴、漏、事故放料、储运等流失的介质;而技术损失影响因素比较复杂,各厂因工艺不同而有所不同。
技术损失主要表现在最终产品带介和磁选尾矿流失两方面。
要减少实际介耗的损失量,必须对影响介耗的因素进行分析、排查并进行治理。
1、磁铁矿粉质量有的选煤厂存在介质技术损失并不大、但介耗却很高的情况,原因可能是由于磁铁矿粉质量没有达到要求。
因为加重质粒度越细,重悬浮液密度也越稳定,在重悬浮液中为起稳定作用而掺入的煤泥量也相应减少;加重质粒度变粗后,重悬浮液稳定性变差,为了满足稳定性的要求势必要加大泥质物含量,从而导致脱介筛和分选机效率下降,加重质损失明显增大。
故我国设计规范规定,用磁铁矿粉作加重质时,密度须在4.5g/cm 3左右。
对加重质磁性物含量的要求是:磁铁矿粉磁性物含量需达到90%以上。
对加重质粒度含量要求是分选块煤时,-0.074mm粒度含量必须达到规定的80%以上;分选末煤时,-0.044mm粒度含量必须达到90%以上。
影响重介选煤厂介质消耗的因素分析

3・ 0
露天采矿技术 21年 期 00 第3
影响重介选 煤厂介质消耗 的因素分析
李希鹏
( 中煤 西安设 计工程有 限责任公 司。陕西 西安 7 0 5 ) 10 4
摘
要 : 质 消耗 是重介 选 煤 厂非 常 重要 的 生产指 标 , 文从介 质 消耗 的途径 入 手进 行分 析 , 点对 影 介 本 重
匿目 重
露 采 技 20 第 期 天 矿 术 o 年 3 l
门进行 合理调 节 。
33 设备 因素 .
・・ 3 1
多 , 就意 味着进入 介质 回收 系统 的量增 大 , 也 由于 回
收磁选 机本身 回收率 的制 约 ,使 得 随磁 选尾 矿损 失 的磁铁矿 粉就会 增多 ,这也 是煤 泥量 大 的重介 选 煤 厂介 耗 高的原 因之一 。
( ) 冒滴 漏损 失 。 冒滴漏 在选 煤厂 的生产 中 3跑 跑 是一 种常 见 的现象 ,它 的严重与 否跟 设计 和 生产 管 理有 关系 。选煤 厂 的跑 冒滴漏水 通 常都是 被 汇于厂 房一层 的集 水坑 ,这 部分 煤泥水 中往 往会 含 有介质
收稿 日期 :0 0 0 一 7 2 1 — l 0
设计 和生 产是 很有 意义 的 。 2 介质 消耗 的途径
起进 入磁 选机得 到有 效 回收 。 的大型 、 有 特大 型选
煤 厂单 独设煤 泥筛 回收 ,筛 下水进 磁选 机 回收跑 冒 滴 漏 的介 这样 跑 冒滴漏 的介 质就 得不 到有效 回收 , 而随 煤 泥产 品带走 。
重介 选煤 厂在 正 常生产 中介 质消 耗 主要 有 以下
3种途径 :
( ) 品煤带 介 。 1产 经过 重介 分选设 备分 选 出的产
加强管理降低介耗提高经济效益B5

加强管理降低介耗提高经济效益介质费用是构成洗煤成本的重要部分,约占直接洗煤成本16%,而且由于介质市场价格大幅上升,虽然吨耗有了一定幅度降低,但介质费用在洗煤成本的构成比重仍提高1%,而且有上扬势头,所以介耗控制直接影响洗煤经济效益的进一步提高,而且对于洗煤厂这样的年处理能力200多万乃至300万吨的大型企业而言,介耗每降低零点几公斤,都会给企业带来几十万元及至上百万元的经济效益。
所以控制介耗对提高现代重介洗煤厂的经营管理有着举足轻重的意义。
加强对影响介耗的各种因素管理就起到了积极的作用,降低介质消耗,提高企业的经济效益。
洗煤存在的主要问题,主要表现在:⑴ 由于介耗大,补充介质次数频繁,影响生产的连续性。
⑵ 产品质量不稳定,特别是对精煤产品污染严重,在一定程度上降低了精煤回收率,导致副产品带煤增多。
⑶ 介质仓液位不稳定,介水不平衡,分选比重不易保持,无法进行正常的洗煤过程控制与操作。
⑷ 脱介筛筛面直接跑水,跑介,磁选机负荷急聚增大,经常跑、冒料,介质流失严重。
并进入煤泥水处理系统,恶化浮选处理效果。
第一、应考虑采取尽可能完善或充分的传统脱介方式有效脱介,如加大喷水压力,增加了筛面面积,减少堆积、粘附或物料过厚等状态。
从技术解决路线方面来考虑:(1)影响介质消耗的因素分析传统脱介方式:介质消耗的控制是一个项系统工程,对于重介质选煤而言,介质消耗无非包括三个方面: ⑴ 产品带介损失;⑵ 磁选效率损失;⑶无法有效回收的跑、冒、滴、漏损失或储、运流失。
前者常称之为工艺损失,后两者称之为管理损失。
其中磁选效率损失在磁选机定型安装后,这种损失的大小取决于磁选机工艺效率高的高低和维护、使用和管理水平;跑、冒、滴、漏流失只要加强管路、溜槽更换和维修,并确保有效回收进入介质净化回收系统,也可得到充分复用,所以我认为,在影响介耗的众多因素中,产品带介损失和磁选机的效率才是工艺管理和控制的关键和重点,它不但大大增加了洗煤消耗成本,而且由于不利于保持介水平衡,导致洗煤操作分选比重大幅波动,分选比重上限波动对产品质量造成不利影响,分选比重下限波动在一定程度上会增加副产品和带煤率,降低了精煤有效回收率,制约了经济效益的进一步提高。
影响选煤厂介耗的几点因素分析

影响选煤厂介耗的几点因素分析前言在重介质选煤过程中,磁铁矿粉的吨煤损耗量是重介质洗煤厂的一项主要技术经济指标,也是目前选煤厂节能降耗的重点之一。
我国选煤厂设计规范中规定,重介质选煤过程中,吨原煤的介质损耗指标是:块煤系统为0.2~0.3kg,末煤系统为0.5~1.0k g。
事实上,我国选煤厂极少有能达到上述指标的。
目前,吨原煤介质损耗较先进的指标在1.5kg左右,一般在2~3kg,高的在5~6kg。
选煤厂介质损耗高时,一方面可能是因煤质变化较大而使原设计的系统不相匹配;另一方面可能是生产管理问题,这就需要在生产中进行有效管理,减少管理损失,控制技术损失。
下面我结合我矿洗煤厂现状就目前洗煤厂影响介质消耗的几点因素做出分析请领导审阅:1. 我矿洗煤厂介耗现状我矿洗煤厂为重介洗煤厂,目前吨原煤介质消耗平均在5 kg,有时甚至更高,但这在较增设TBS前(7~8kg/t)有了很大程度的提高。
介质消耗居高不下是摆在我矿洗煤厂面前的一大难题。
2. 影响我矿洗煤厂介耗的因素分析1)磁铁矿粉质量管理。
我矿洗煤厂用作加重质的磁铁矿粉,真密度为4.5g /cm3,磁性物含量为98.9%(刚做过检测)符合重介洗煤厂对磁铁矿粉的要求,但水分含量相对较高为16.5%(中国神华神东煤炭集团洗选中心对磁铁矿粉水分的考核指标为≤8%)。
磁铁矿粉水分对介耗也是有影响的。
案例:神东煤炭集团补连塔洗煤厂采用抓斗机直接将介质加于合介桶,如果水分高,会使介质结团成块,不仅造成加介困难,而且,介质进入悬浮液中难于分散,造成悬浮液不稳定,集控中心显示的合介桶磁性物含量会相对较低,即配置相同密度的重介质磁铁矿粉水分越大所需要的磁铁矿粉越多。
特别是在冬天,介质送来时经过较远的路程,如果水分太大,磁铁矿粉会冻结成块,影响更大。
2)生产技术管理。
①我矿洗煤厂在增设TBS后小时入洗量明显增加,但其它设备并没有相应的扩能,生产能力适应不了目前的上煤量造成介质的损失。
影响介耗的因素分析
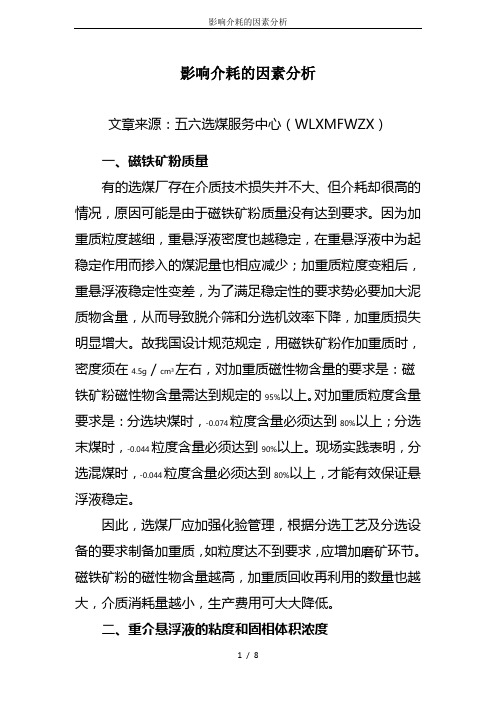
影响介耗的因素分析文章来源:五六选煤服务中心(WLXMFWZX)一、磁铁矿粉质量有的选煤厂存在介质技术损失并不大、但介耗却很高的情况,原因可能是由于磁铁矿粉质量没有达到要求。
因为加重质粒度越细,重悬浮液密度也越稳定,在重悬浮液中为起稳定作用而掺入的煤泥量也相应减少;加重质粒度变粗后,重悬浮液稳定性变差,为了满足稳定性的要求势必要加大泥质物含量,从而导致脱介筛和分选机效率下降,加重质损失明显增大。
故我国设计规范规定,用磁铁矿粉作加重质时,密度须在4.5g/cm3左右,对加重质磁性物含量的要求是:磁铁矿粉磁性物含量需达到规定的95%以上。
对加重质粒度含量要求是:分选块煤时,-0.074粒度含量必须达到80%以上;分选末煤时,-0.044粒度含量必须达到90%以上。
现场实践表明,分选混煤时,-0.044粒度含量必须达到80%以上,才能有效保证悬浮液稳定。
因此,选煤厂应加强化验管理,根据分选工艺及分选设备的要求制备加重质,如粒度达不到要求,应增加磨矿环节。
磁铁矿粉的磁性物含量越高,加重质回收再利用的数量也越大,介质消耗量越小,生产费用可大大降低。
二、重介悬浮液的粘度和固相体积浓度重介悬浮液的粘度随固相体积浓度增大而增大。
当固相体积浓度达到35%时,粘度急速上升,当达到50%后,粘度接近最高值,重悬浮液表现为几乎没有流动性,成浆流状态,悬浮液透筛就会很困难:固相体积浓度越高,产品带介越高,反之越低。
要想降低产品带介,就需加大重悬浮液分流量,排除多余的煤泥,以提高悬浮液流动性,从而降低介耗。
分流量过大时,势必又会加大磁铁矿粉在磁选尾矿中的损失(尽管这部分损失相对稳定)。
磁选尾矿中的介质损失比因固相体积浓度高而导致的产品带介损失要小得多。
因此,应重视重悬浮液体积浓度对介耗的影响。
众所周知,重悬浮液粘度对重介质旋流器的分选效果影响较大。
重悬浮液粘度过高会影响原煤的分选效果,而对末煤和煤泥的分选影响尤为显著。
在悬浮液密度满足分选密度要求的条件下,要求悬浮液粘度低,稳定性好,因此固相体积浓度要适宜,这主要取决于非磁性物含量。
刍议重介选煤厂介耗的主要影响因素

刍议重介选煤厂介耗的主要影响因素摘要:许多的选煤厂都存在介质高消耗、难以降介耗的问题,为使介质消耗能有所降低,减少洗选成本,就需认真研究选煤厂介耗的主要影响因素。
本文对洗煤厂介耗的主要影响进行简单的分析,以供参考。
关键词:重介选煤厂介耗影响因素介耗属于重介选煤厂的生产、设计管理的技术经济指标,介耗水平的高低直接影响了重介系统的稳定和正常,决定了选煤厂的经济效益。
根据选煤厂的相关规范设计规定,在进行重介选煤时,原煤介质的消耗应控制在以下指标内:针对块煤系统,0.25kg/t左右的原煤,针对末煤系统,0.6~0.9kg/t的原煤。
但在具体的运营中,仅有少数选煤厂符合上述标准。
重介质选煤厂目前的介耗较为优良的在1.5kg/t左右的原煤,大部分通常均为2.5kg/t左右的原煤,严重影响了选煤厂的经济效益与生产稳定。
重介选煤厂在这种高介耗的情况下,如何降低介耗减少洗选成本,已成为选煤厂的重要课题。
而研究选煤厂介耗的主要影响因素,是降低介耗的基础和重点,选煤厂的介耗主要因技术和管理失误造成损失,管理损失比较直观,一般主要有储运、放料、漏、冒、跑等管理不当,导致介质损失。
技术损失则是因最终的产品遴选、带走尾矿,导致介质的流失。
因此,要使介质的实际损失量减少,必须分析介质的主要影响因素,并进行排查和处理。
1 磁铁粉的质量磁铁粉主要包括纯度、密度、水分、磁性、粒度等,与重介系统介耗、分选有着直接的联系。
(1)根据重介选煤系统的实际情况,在保证系统效益、稳定性的前提下,在进行混煤分选的过程中,0.045mm颗粒必须达91%以上的含量。
某些选煤厂技术损失较低,但介质仍然很高,主要是由于磁铁粉的粒度不符合标准。
如果加重介质的粒度越细,相对就有较为稳定的重悬浮液密度。
在受到重悬浮液的稳定作用下,煤泥的掺入量则随之减少。
当加重介质的粒度越粗,影响了重悬浮液的稳定性,为达到稳定性的标准,就必须增加煤泥的含量,致使分选机、脱介筛的效率下降,明显加重了介质的损失。
影响重介洗煤厂介耗的因素分析

影响重介洗煤厂介耗的因素分析随着煤炭装备的不断升级,重介洗煤厂成为了煤炭加工行业的重要环节。
然而,重介洗煤厂介耗作为一个重要的经济指标,影响着企业的生产效益和经济效益。
因此,深入分析影响重介洗煤厂介耗的因素,对于提高企业生产效益具有重要的指导意义。
1.煤种煤种是影响重介洗煤厂介耗的最重要的因素之一。
不同的煤种化学成分、物理性质不同,对于介的吸附能力和特征也有很大的影响。
一般来说,烟煤介耗较低,焦炭煤介耗较高。
因此,对于不同的煤种,需要采用不同的重介洗煤工艺,调整操作参数,以达到最佳介耗效果。
2.洗选工艺洗选工艺是影响重介洗煤厂介耗的另一个重要因素。
洗选工艺的不同,也会导致介耗的差异。
对于传统悬浮介选法,因为粉煤矸石的粒径较小,介吸附能力较大,介耗量较高。
而对于气浮洗选工艺,因为分选介为气体,对煤矸天然具有较小的粘附力,介耗相比传统介选方法落差很大。
3.工艺参数工艺参数是影响介耗的非常重要的因素之一。
重介洗煤厂采用的各项工艺参数都对介耗产生很大的影响,包括介质浓度、旋流器转速、介质温度、浮选时间等。
适当的调整工艺参数可以达到降低介耗的目的,例如增大悬浮液浓度,可以增加悬浮液的接触面积,降低介耗。
4.设备性能重介洗煤厂的设备性能也是影响介耗的因素之一。
包括设备的维护、清洗、检修、更换等方面的因素。
设备的准确度、对于介体加压的能力等都会对重介洗煤厂产生影响。
5.原材料品质原材料品质也是影响介耗的一个因素。
由于原材料有不同的透气性、不同的化学成分分布、不同热值,因此影响煤炭介耗也不尽相同。
同时,原材料含尘量也是影响煤炭介耗的重要因素之一。
总之,影响重介洗煤厂介耗的因素是多方面的。
针对不同的煤种、洗选工艺和原料品质,需要采取不同的优化措施,如调整工艺参数、清洗维护设备等,从而降低介耗,提高生产效益。
介耗高,解决办法

介耗高的原因与解决方法1、筛子。
根据观察,发现筛子上的喷水的给入量有一点问题,我们都知道,筛子上的喷水共3段。
想要控制好介耗,主要也是根据喷水来调节。
总所周知,筛子的第一段喷水不能流到第二段、第二段不能流到第三段。
而我们筛子上的喷水,第一段已经流到第二段了,而且还是以较大的流量,这样对于我们的介质回收很不利,从而引起跑介。
解决方法:要调整筛上的喷水,不能让第一段喷水流到第二段,可以采用(中、大、小(或中))的喷水方式。
而且根据观察,第一段喷水与第二段喷水之间的间隙有点小(而且由于处理量的增加,导致筛上喷水的增大,,这样就容易引起第一段喷水跑到第二段)所以,我觉得我们应该把第一段喷水(逆煤流方向)移一道筛板,这样对于跑介应该回有一点效果。
2、煤种。
相对煤种而言,引起跑介严重的就是4#原煤了。
根据浮选情况与尾矿的板数、精矿的板数,可以知道,4#原煤的氧化程度严重,次生煤泥含量大,由于次生煤泥含量大,导致弧形筛与直线振动筛的脱介效果差,导致产品带介严重。
解决方法:我们要保证弧形筛不串料,喷水要调整好,如果保证这两点,不只会减少介耗,也会增加精煤的产率。
(如果调整不好,那么不只产品带介高,同样会使一部分煤泥粘附在产品表面,使产品灰分增加。
)3、弧形筛。
如果弧形筛脱介效果不好,那么跑介非常严重,所以一定要保证弧形筛不串料。
4、磁选机。
如果筛子跑粗那么会进入磁选机中,使磁选机中含有大颗粒的物料,这对于介质的回收很不利,同时也对磁选机的滚筒有一些磨损。
如果大颗粒物料过多将会堵塞磁选机,这样会损失更多的介质。
磁选机的溢流,一定要保证。
解决方法:如有大颗粒物料进入磁选机应及时检查脱介筛,同时进行筛子与磁选机的相应处理。
由于4#原煤的次生煤泥含量大,可以根据进入磁选机的入料浓度的高低,适当的调整磁选机的磁偏角。
5、管路。
一些介管的损坏导致漏介。
解决方法:如发现管路的滴漏或损坏严重的,应及时处理,不应该往检修日上推。
选煤厂介耗因素分析
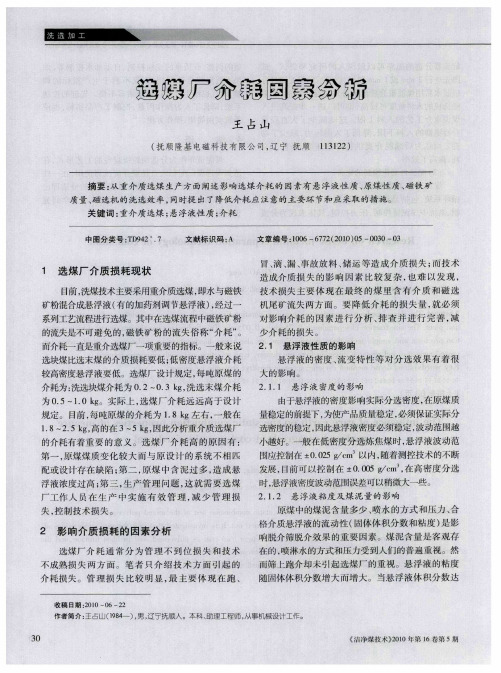
块 煤重 介 质 分选 粒 度 范 围一 般 在 8—10 m 5 m,
由于各 级粒 度 干扰 沉 降 速 度 不 同 , 颗 粒 从 入 料 口 小
到 排料 口这 段 时间 可 能 分 选 不好 , 浮煤 中可 能 存 在 在 密度 高 的小颗 粒 , 者 是 低 密 度 的 小 颗 粒 进 入沉 或
原煤 中的煤 泥含 量 多少 、 喷水 的方 式 和压 力 、 合
2 影 响 介质 损 耗 的 因素 分 析
选 煤 厂介 耗 通 常 分 为 管理 不 到 位 损 失 和 技 术 不成熟 损 失 两 方 面 。笔 者 只介 绍 技 术 方 面 引起 的
格介质悬 浮液的流 动性 ( 固体体 积分数 和粘 度 ) 影 是
随 固体体积 分数 增大 而增 大 。当悬 浮液 体积分 数 达
作者简介: 王占山(9 4 ) 男 , 18 一 , 辽宁抚顺人 。本科 、 助理工程师 , 从事机械设计工作。
3 0
《 洁净煤技术)0 0年第 1 ) 1 2 6卷第 5期
全国中 文核心期刊 矿业类核心期刊 《 A— D规范》 C JO 执行优秀期刊_ J
矿粉混合成悬 浮液 ( 的加 药剂调节悬 浮液 )经 过一 有 , 系列工艺流程进行选 煤。其 中在选煤流程 中磁铁 矿粉
的流失是不可避 免 的 , 铁 矿粉 的 流失俗 称 “ 磁 介耗 ” 。 而介耗一直是重介选煤厂一项重要 的指标 。一般来 说 选块煤 比选末 煤 的介 质损耗要 低 ; 低密度悬 浮液介 耗 较高密度悬 浮液要 低。选 煤厂设计 规定 , 吨原煤 的 每 介耗为 : 洗选块煤介耗 为 0 2— . g 洗选末 煤 介耗 。 03 k ,
浅析影响末煤重介系统介质消耗的因素
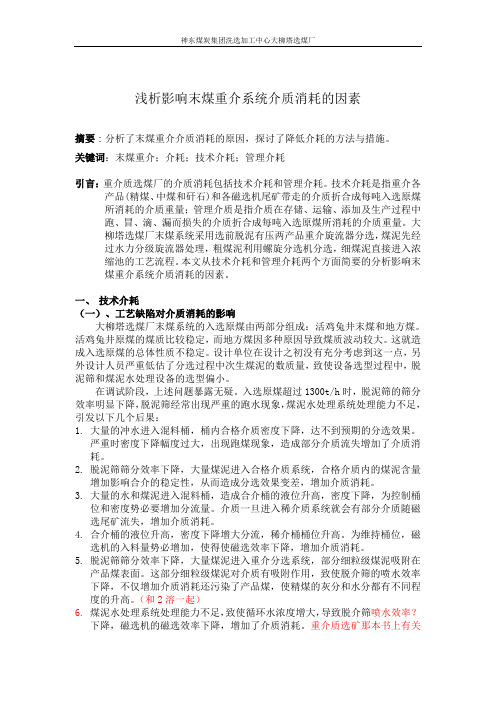
浅析影响末煤重介系统介质消耗的因素摘要:分析了末煤重介介质消耗的原因,探讨了降低介耗的方法与措施。
关键词:末煤重介;介耗;技术介耗;管理介耗引言:重介质选煤厂的介质消耗包括技术介耗和管理介耗。
技术介耗是指重介各产品(精煤、中煤和矸石)和各磁选机尾矿带走的介质折合成每吨入选原煤所消耗的介质重量;管理介质是指介质在存储、运输、添加及生产过程中跑、冒、滴、漏而损失的介质折合成每吨入选原煤所消耗的介质重量。
大柳塔选煤厂末煤系统采用选前脱泥有压两产品重介旋流器分选,煤泥先经过水力分级旋流器处理,粗煤泥利用螺旋分选机分选,细煤泥直接进入浓缩池的工艺流程。
本文从技术介耗和管理介耗两个方面简要的分析影响末煤重介系统介质消耗的因素。
一、技术介耗(一)、工艺缺陷对介质消耗的影响大柳塔选煤厂末煤系统的入选原煤由两部分组成:活鸡兔井末煤和地方煤。
活鸡兔井原煤的煤质比较稳定,而地方煤因多种原因导致煤质波动较大。
这就造成入选原煤的总体性质不稳定。
设计单位在设计之初没有充分考虑到这一点,另外设计人员严重低估了分选过程中次生煤泥的数质量,致使设备选型过程中,脱泥筛和煤泥水处理设备的选型偏小。
在调试阶段,上述问题暴露无疑。
入选原煤超过1300t/h时,脱泥筛的筛分效率明显下降,脱泥筛经常出现严重的跑水现象,煤泥水处理系统处理能力不足,引发以下几个后果:1.大量的冲水进入混料桶,桶内合格介质密度下降,达不到预期的分选效果。
严重时密度下降幅度过大,出现跑煤现象,造成部分介质流失增加了介质消耗。
2.脱泥筛筛分效率下降,大量煤泥进入合格介质系统,合格介质内的煤泥含量增加影响合介的稳定性,从而造成分选效果变差,增加介质消耗。
3.大量的水和煤泥进入混料桶,造成合介桶的液位升高,密度下降,为控制桶位和密度势必要增加分流量。
介质一旦进入稀介质系统就会有部分介质随磁选尾矿流失,增加介质消耗。
4.合介桶的液位升高,密度下降增大分流,稀介桶桶位升高。
洗煤工艺中介质损耗的原因

洗煤工艺中介质损耗的原因
洗煤工艺是指通过物理或化学方法,将煤炭中的杂质和灰分分离出来,从而提高煤的
纯度和热值的过程。
洗煤工艺中会产生不同程度的介质损耗,介质损耗的原因主要有以下
几方面。
1、介质流失
介质流失是洗煤过程中介质损耗的主要原因之一。
洗煤过程中需要用到介质如水、重
介质、轻介质等。
在介质流动过程中,由于管道、设备堵塞、介质处理不当等原因导致介
质流失,进而导致介质损耗。
2、介质污染
洗煤过程中,介质容易污染,如水中的泥沙、重介质中的锆石、钨矿等,轻介质中的
泡沫、细小颗粒等。
介质污染会影响到洗煤效果,进而导致介质的加工次数增加,介质损
耗增大。
3、介质中物料的磨损
介质中物料的磨损也是导致介质损耗的原因之一。
洗煤过程中,煤炭、粘土等杂质的
磨损会导致介质的松散程度增加,进而提高介质的流动性能,但也会导致介质磨损和粉碎,从而扩大介质的处理范围,导致介质的损耗。
4、介质管道磨损
洗煤设备中的水泵、阀门、管道等设备会因为介质的冲刷和磨擦而产生磨损。
当管道
磨损或设备损坏时,介质会泄漏,流失,导致介质的损耗。
5、介质化学性质变化
洗煤过程中,介质中的酸、碱度、离子、PH等因素都会发生改变,造成介质的化学性质变化,从而导致介质降解、老化、腐蚀等现象发生,引起介质的损耗。
总之,洗煤工艺中介质损耗的原因比较复杂,需要从介质本身、设备和操作等多个方
面去进行分析和控制。
针对不同的损耗原因,可以采取相应的措施来减少介质损耗,提高
洗煤工艺的效率和经济效益。
影响重介选煤厂介质消耗的因素分析

重介选煤厂在正常生产中介质消耗主要有以下 3 种途径:
(1)产品煤带介。经过重介分选设备分选出的产 品煤,虽然经过脱介脱水后绝大部分介质会脱除掉, 但仍会有小部分黏附在产品煤表面的介质随产品带 出,未返回介质循环系统。这部分介耗受脱介设备和 脱介喷水的影响较大。
(2)磁选尾矿带介。稀介质以及被分流部分的介 质,要进入介质回收系统进行介质的净化回收,目前 在重介选煤厂应用最多、最普遍的介质净化回收设备 是磁选机,由于受磁选效率的影响,介质不能 100% 回收,所以总会有部分介质随磁选尾矿被带走。
(3)煤泥量。煤泥量的多少对介耗的影响也是非 常大的,煤泥量过大,对介质系统的稳定性造成不利 影响,重介选煤厂是通过分流来保证循环介质系统 的稳定的,如果煤泥量过大,会导致分流的介质量增
选矿工程
露天采矿技术 2010 年第 3 期
·31·
多,也就意味着进入介质回收系统的量增大,由于回 收磁选机本身回收率的制约,使得随磁选尾矿损失 的磁铁矿粉就会增多,这也是煤泥量大的重介选煤 厂介耗高的原因之一。 3.2 工艺因素
(3)跑冒滴漏损失。跑冒滴漏在选煤厂的生产中 是一种常见的现象,它的严重与否跟设计和生产管 理有关系。选煤厂的跑冒滴漏水通常都是被汇于厂 房一层的集水坑,这部分煤泥水中往往会含有介质
收稿日期:2010 - 01 - 07 作 者 简 介 :李 希 鹏(1977 -),男 ,山 东 日 照 人 ,工 程 师 , 2002 年毕业于中国矿业大学化工学院矿物加工工程专业,长 期在中煤西安设计工程有限责任公司选煤工厂所从事选煤 厂咨询、设计工作。
3.1 煤质本身因素 (1)煤的粒度组成。煤的粒度组成对介质消耗的
影响主要表现在产品带介上。对于粒度组成细的煤 来说,块煤量小而末煤量大,相对而言煤的比表面积 大,增加了产品带介的可能,实践证明往往末煤量大 的重介选煤厂,介耗比较高。从国内外的块煤及末煤 重介选煤厂的实际生产情况看,结果也是如此。
单晶硅 介电损耗

单晶硅是一种常用的材料,具有良好的光电特性和介电特性。
介电损耗是描述材料在电场中吸收和转换电能为热能的性质。
对于单晶硅而言,它的介电损耗主要取决于以下几个因素:
1. 晶体结构:单晶硅具有紧密的晶体结构,晶格中的原子排列有序,使得其具备较低的介电损耗。
2. 杂质浓度:杂质是指掺入晶格中的其他元素,如磷、硼等。
杂质浓度的增加会导致单晶硅的介电损耗增加,因为杂质引入了额外的能级,增加了电子与杂质能级之间的相互作用,从而产生额外的能量损耗。
3. 结晶质量:单晶硅的结晶质量越高,晶界和缺陷越少,其介电损耗也越低。
4. 温度:温度对单晶硅的介电损耗也有影响。
一般情况下,随着温度的升高,单晶硅的介电损耗会增加。
需要注意的是,单晶硅的介电损耗一般较低,适用于许多电子器件和光学器件的制造。
然而,在一些特殊应用中,对介电损耗的要求可能更高,需要选择其他具有更低介电损耗的材料。
总之,单晶硅的介电损耗受到晶体结构、杂质浓度、结晶质量和温度等因素的影响。
通过优化材料的制备工艺和控制相关参数,可以降低单晶硅的介电损耗,提高其在电子和光学领域的应用性能。
浅析影响重介质选煤厂介耗的因素
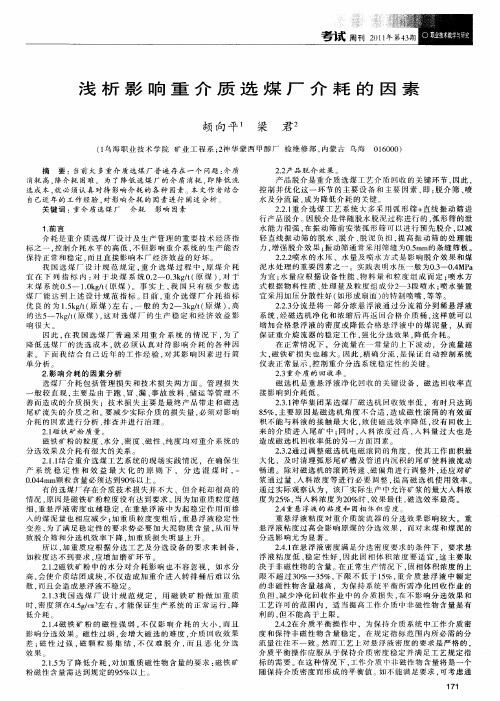
宜 采 用 加 压 分散 性 好 ( 如形 成 扇 商 ) 的特 制 喷 嘴 , 等 。 等 223 流是 将 一 部 分 浓 悬 浮液 通 过 分 流 箱 分 到 稀 悬 浮 液 .- 分
系 统 , 磁 选 机 净 化 和 浓 缩 后 再 返 回合 格 介 质 桶 . 样 就 可 以 经 这 增 加 合 格悬 浮液 的密 度 或 降低 合 格 悬 浮 液 中 的煤 泥 量 .从 而 保 证 重 介旋 流器 的稳 定 工 作 , 化 分 选 效果 , 低 介 耗 。 强 降 在 正 常情 况 下 ,分 流 量 在 一 常 量 的上 下 波 动 .分 流 量 越 大 , 铁 矿 损 失 也 越 大 。因 此 , 确 分 流 , 保 证 自动控 制 系 统 磁 精 是 仪 表 正 常显 示 , 制 重介 分 选 系统 稳 定 性 的关 键 。 控 23 介 质 的 回 收 率 。 _重 磁 选机 是 重 悬 浮 液 净 化 回 收 的关 键 设 备 ,磁 选 回收 率 直 接 影 响 到介 耗 低 23 1 华 集 团某 选 煤 厂磁 选 机 回收 效 率 低 。有 时 只 达 到 -. 神 8 %, 要 原 因 是 磁 选 机 角 度 不 合 适 , 成 磁 性 滚 筒 的 有 效 面 5 主 造 积 不 能 与料 液 的接 触 最 大 化 , 使 磁 选 效 率 降低 . 有 回收 上 致 没 来的介质进入尾矿 中 ; 同时 。 料 浓 度 过 高 , 料 量 过 大 也 是 人 人 造 成磁 选 机 回收 率 低 的 另 一 方 面 因素 。 232 过 调 整 磁 选 机 电磁 滚 筒 的角 度 ,使 其 工 作 面 积 最 -I 通 大 化 ,及 时 清 理 弧 形 尾 矿 槽 及 管 道 内沉 积 的 尾 矿 使 料 液 流 动 畅 通 。 除对 磁 选 机 的滚 筒 转 速 、 偏 角进 行 调 整 外 , 应 对 矿 磁 还
洗煤工艺中介质损耗的原因

洗煤工艺中介质损耗的原因1. 引言1.1 介质损耗在洗煤工艺中的重要性介质损耗在洗煤工艺中的重要性不可忽视。
洗煤工艺中介质扮演着重要的角色,其作用是分离煤与矸石,提高煤炭品位。
介质损耗的增加会导致生产成本的提高,对生产效率和经济效益造成负面影响。
介质损耗会直接影响洗煤工艺的稳定性和可靠性,影响煤炭品位的提升,降低洗选效果。
了解介质损耗的原因,并采取有效的措施减少介质损耗,对提高洗煤工艺的效率和经济效益具有重要意义。
介质损耗主要发生在介质粉碎、介质吸附和介质泄露等方面。
介质粉碎是介质损耗的主要原因,介质因受力过大或受介质直接破坏而损坏;介质吸附和介质泄露则是介质损耗的次要原因。
为了降低介质损耗,需要采取有效的措施,比如优化设备结构、选择耐磨耐腐介质等。
2. 正文2.1 介质损耗的主要原因:介质粉碎介质损耗的主要原因之一是介质粉碎。
在洗煤工艺中,介质需要不断地循环使用来完成煤炭的洗选过程。
由于煤炭中含有各种杂质和硬物,这些杂质和硬物会在介质中引起磨损,导致介质粉碎。
介质粉碎会导致介质的颗粒大小逐渐变小,表面积增大,从而使介质的吸附和分离性能下降。
特别是在高速搅拌和磨煤的过程中,介质的粉碎更为严重。
为了减少介质粉碎造成的损耗,可以采取一些措施。
可以选择硬度高、耐磨性好的介质材料,以增加介质的耐磨性。
可以在洗选过程中适当降低搅拌速度,减少介质受到的冲击力,从而减少介质的粉碎。
定期检查介质的磨损情况,及时更换磨损严重的介质,也是有效降低介质粉碎造成的损耗的方法。
介质粉碎不仅会增加洗选过程中的介质消耗,同时也会降低洗选效率,影响产品品质,增加生产成本,因此必须引起工艺工作者的高度重视。
通过有效控制介质粉碎问题,可以提高洗煤工艺的效率和经济性。
2.2 介质损耗的次要原因:介质吸附介质吸附是指在洗煤工艺过程中,介质表面会吸附一定量的杂质物质,导致介质的性能和效果下降,从而增加介质损耗。
介质吸附主要包括两种情况:一是介质表面对水分、灰分等杂质物质的吸附;二是介质表面对有机物等污染物质的吸附。
1 影响介质损耗的因素分析

1 影响介质损耗的因素分析1.1 磁铁矿粉质量有的选煤厂介耗很高,主要是因为原磁铁矿粉质量没有达到要求,同时,重悬浮液中掺入的煤泥量也少,使加重悬浮液稳定性变差,从而导致加重质损失明显增大。
为了满足稳定性要求,现场实践和多年经验表明,分选混煤时,磁铁矿粉水分对介耗影响也不容忽视。
不仅介质进入料桶后难于分散,而且会造成悬浮液不稳定。
1.2 重介悬浮液的粘度和固相体积浓度影响弧形筛和脱介筛脱介效果的主要因素,是重介悬浮液的粘度和固相体积浓度、原煤中的煤泥含量与合格介质悬浮液的流动性。
对煤泥含量而言,喷淋水的方式和压力受到人们的普遍重视。
然而,对于重悬浮液的体积浓度过高未引起足够注意。
当粘度急速上升,达到50%后,重介悬浮液的粘度接近最高值,重悬浮液表现为成浆流状态。
这就有可能直接导致悬浮液透筛困难的异常现象,而且还会很明显感觉到脱介效果很差。
固相体积浓度越高,产品带介越多,就必须排除多余的煤泥,这样才能达到提高悬浮液流动性,从而降低介耗的目的。
另外一种情况是,分流量过大时,极有可能出现加大磁铁矿粉在磁选尾矿中的损失(尽管这部分损失相对稳定)。
所以,必须重视重悬浮液体积浓度对介耗的影响。
重悬浮液粘度过高对末煤和煤泥的分选影响尤为显著。
在重介悬浮液的粘度和固相体积浓度满足分选密度要求的情况下,其主要要求是悬浮液的粘度必须低,稳定性能必须好。
这样才能使固相体积浓度相对适宜。
一般情况下,重介质悬浮液中额定的非磁性物含量越高,选煤厂为了要保持系统的平衡所需净化回收的悬浮液数量越少。
因此,为减轻净化回收作业中的介质损失,可以在不影响分选效果和工艺许可范围内进行,这样,可以采取适当提高工作介质中额定非磁性物含量。
但是,切记不能超出上限。
在介质平衡操作中,为保持介质系统中工作介质密度在规定指标上所必需的分流量往往不一致。
然而,工艺上对保持非磁性物含量稳定在规定指介质的平衡操作应服从于保持介质密度稳定需要。
这种情况下,它是随保持介质密度稳定,不能够得到满足,则可以考虑通过研磨来解决。
介电损耗的影响因数

材料结构 本身
外界环境 或试验条
件
• 由于不同材料的漏导电流不同,由此引起 的损耗也各不相同,不同材料的极化机制 不同,也使极化损耗各不相同,在这里不 详加讨论。
• 我们主要讨论第二类情况,也就是外界环 境或试验条件对材料介电损耗的影响。
3.1对漏导损耗的影响
• 漏导电流的存在,相当于材料内部有一个电阻, 在电压的作用下因发热而产生损耗,其大小为
• 因此介质不论是在直流电压还是在交变电 压作用下都会产生能量损耗。由于一切适 用工程介质材料都有漏导电存在,因此一 切工程介质在电场作用下都有电导损耗发 生。
二、介电损耗的定量表征
• 通常以电介质中存在一个损耗电阻Rn来表示电能 的消耗。
• 这样,就等于把通过介质的电流分成消耗能量的
部分R和不消耗能量部分 (c 即通过介质纯电容
部分)。
• 定义介质损耗角正切为
•
tan R 1
c CRn
• 式中 代表交变电场的角频率,C就是带有
电极的介质样品的静电容值。
• 因为tan与介质中能量损耗成正比,往往也 就把tan 叫做损耗因子或直接叫做介电损耗。
• 事实上,Rn与电场强度、温度以及电场频 率都有关系,所以介电损耗也是也是与场 强、温度和电场频率有关的。
• 介质的漏电是介电损耗的另一个原因,特 别是在高温或强电场作用下,这方面的影 响是很重要的。
• 介质漏电也是通过发热而把部分电能消耗 掉。
• 对于理想的电介质来说,应该不存在电导, 亦即不存在电导损耗。但实际工作中的电 介质总是或多或少存在一些弱联系带电粒 子(或空位),这些带电粒子在外电场作 用下能沿着与电场平行的方向作贯穿于电 极之间的运动,结果产生了漏导电流,使 能量直接损耗。
选煤厂影响介耗因素分析及对策
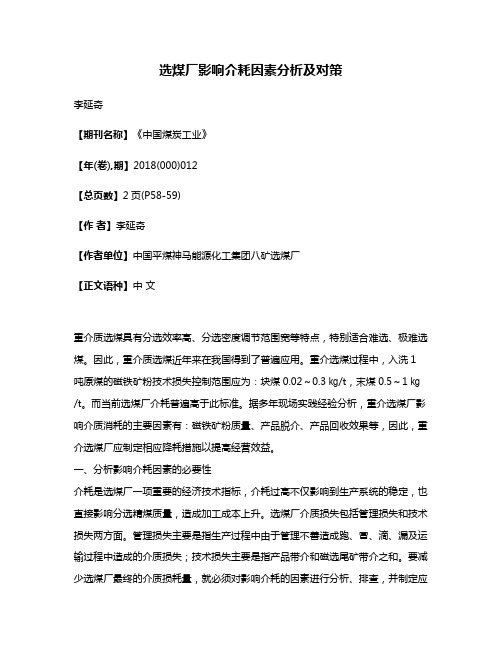
选煤厂影响介耗因素分析及对策李延奇【期刊名称】《中国煤炭工业》【年(卷),期】2018(000)012【总页数】2页(P58-59)【作者】李延奇【作者单位】中国平煤神马能源化工集团八矿选煤厂【正文语种】中文重介质选煤具有分选效率高、分选密度调节范围宽等特点,特别适合难选、极难选煤。
因此,重介质选煤近年来在我国得到了普遍应用。
重介选煤过程中,入洗1吨原煤的磁铁矿粉技术损失控制范围应为:块煤0.02~0.3㎏/t,末煤0.5~1㎏/t。
而当前选煤厂介耗普遍高于此标准。
据多年现场实践经验分析,重介选煤厂影响介质消耗的主要因素有:磁铁矿粉质量、产品脱介、产品回收效果等,因此,重介选煤厂应制定相应降耗措施以提高经营效益。
一、分析影响介耗因素的必要性介耗是选煤厂一项重要的经济技术指标,介耗过高不仅影响到生产系统的稳定,也直接影响分选精煤质量,造成加工成本上升。
选煤厂介质损失包括管理损失和技术损失两方面。
管理损失主要是指生产过程中由于管理不善造成跑、冒、滴、漏及运输过程中造成的介质损失;技术损失主要是指产品带介和磁选尾矿带介之和。
要减少选煤厂最终的介质损耗量,就必须对影响介耗的因素进行分析、排查,并制定应对措施,持续改进,这对选煤厂提质增效具有重要意义。
二、影响介耗因素分析及对策1.磁铁矿粉质量磁铁矿粉的粒度组成、真密度、磁性物含量是检验介质质量的重要技术指标。
(1)选煤厂在重介选煤中对介质质量有着一定的标准要求,煤炭行业标准《选煤用磁铁矿粉》(MT/T1017-2007)按重介质选煤工艺要求,介质应符合表1中的要求。
表1 我国选煤用磁铁矿粉的技术要求技术指标级别特粗粗细特细真密度/(g/cm3) >4.5 >4.5 >4.5 >4.5磁性物含量% ≥95 ≥95 ≥95 ≥95>125μm <10 <5 ——<75μm >70 >80 ——<45μm >55 >65 >80 >90外在水分% <6硫分% <3粒度组成%选煤厂某一阶段在生产工艺设备没有变化的情况下介耗突然升高,很可能的因素是介质质量变差,达不到生产要求。
新田煤矿选煤厂介质消耗原因分析

新田煤矿选煤厂介质消耗原因分析目前重介选煤厂介耗指标一般为2~3kg/t(原煤),我厂开始介耗为2.2kg/t。
进入7月以来,选煤厂生产过程中介质消耗量明显增加,7月26号采购200t磁铁矿粉,到8月9号使用完,期间生产原煤29477t,介耗达到6.8kg/t。
其中洗煤车间补加介质25t,原煤车间补加介质175t。
一、原因分析
技术人员对介耗数据进行分析,断定介质消耗在原煤车间,原因有两方面:
1、原煤车间的210(块煤脱介筛)、211(块矸脱介筛)两个脱介筛的筛板受到长时间块煤块矸的撞击破损严重。
筛板正常使用寿命为6个月,因筛板无配件,为不影响生产在处理时用钢板把整块筛板封住,起不了脱介的作用。
目前210块煤脱介筛有封筛板4块占整个筛面的17%,211块矸脱介筛有封筛板14块占整个筛面的58%。
导致这两台设备脱介效果差,筛上跑介严重。
2、原煤准备车间215桶中间由隔板隔开,一半是合格介质,一半是煤泥水。
脱介筛筛板破损后会向合介断漏大块煤或矸石,因为篦子孔比较小,导致篦子被堵。
介质回收时会入煤泥水桶,导致介质流失。
二、整改措施
1、8月11日进行了筛板招标,预计8月底筛板到货进行安装。
2、215桶中间隔板已加高,相邻篦子孔打通,提高透介能力。
选煤厂重介质消耗影响因素分析与优化策略研究
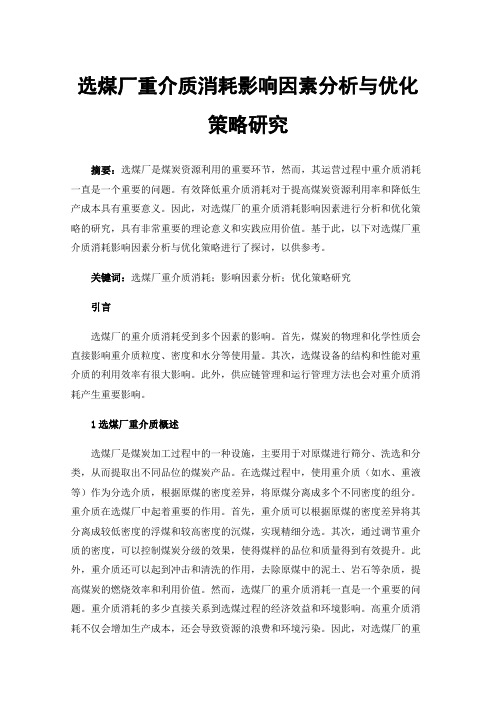
选煤厂重介质消耗影响因素分析与优化策略研究摘要:选煤厂是煤炭资源利用的重要环节,然而,其运营过程中重介质消耗一直是一个重要的问题。
有效降低重介质消耗对于提高煤炭资源利用率和降低生产成本具有重要意义。
因此,对选煤厂的重介质消耗影响因素进行分析和优化策略的研究,具有非常重要的理论意义和实践应用价值。
基于此,以下对选煤厂重介质消耗影响因素分析与优化策略进行了探讨,以供参考。
关键词:选煤厂重介质消耗;影响因素分析;优化策略研究引言选煤厂的重介质消耗受到多个因素的影响。
首先,煤炭的物理和化学性质会直接影响重介质粒度、密度和水分等使用量。
其次,选煤设备的结构和性能对重介质的利用效率有很大影响。
此外,供应链管理和运行管理方法也会对重介质消耗产生重要影响。
1选煤厂重介质概述选煤厂是煤炭加工过程中的一种设施,主要用于对原煤进行筛分、洗选和分类,从而提取出不同品位的煤炭产品。
在选煤过程中,使用重介质(如水、重液等)作为分选介质,根据原煤的密度差异,将原煤分离成多个不同密度的组分。
重介质在选煤厂中起着重要的作用。
首先,重介质可以根据原煤的密度差异将其分离成较低密度的浮煤和较高密度的沉煤,实现精细分选。
其次,通过调节重介质的密度,可以控制煤炭分级的效果,使得煤样的品位和质量得到有效提升。
此外,重介质还可以起到冲击和清洗的作用,去除原煤中的泥土、岩石等杂质,提高煤炭的燃烧效率和利用价值。
然而,选煤厂的重介质消耗一直是一个重要的问题。
重介质消耗的多少直接关系到选煤过程的经济效益和环境影响。
高重介质消耗不仅会增加生产成本,还会导致资源的浪费和环境污染。
因此,对选煤厂的重介质消耗进行合理管理和优化是十分必要的。
在选煤厂重介质的使用方面,通常需要考虑重介质的选择、循环与回收利用、消耗量的控制等问题。
通过合理调整设备参数、改进工艺流程、优化供应链管理等措施,可以降低重介质的消耗量,提高煤炭资源的利用效率和选煤厂的经济效益。
因此,选煤厂重介质的概述主要包括其在选煤过程中的作用,以及重介质消耗所带来的挑战和优化的重要性。
- 1、下载文档前请自行甄别文档内容的完整性,平台不提供额外的编辑、内容补充、找答案等附加服务。
- 2、"仅部分预览"的文档,不可在线预览部分如存在完整性等问题,可反馈申请退款(可完整预览的文档不适用该条件!)。
- 3、如文档侵犯您的权益,请联系客服反馈,我们会尽快为您处理(人工客服工作时间:9:00-18:30)。
影响介耗的因素分析
文章来源:五六选煤服务中心(WLXMFWZX)
一、磁铁矿粉质量
有的选煤厂存在介质技术损失并不大、但介耗却很高的情况,原因可能是由于磁铁矿粉质量没有达到要求。
因为加重质粒度越细,重悬浮液密度也越稳定,在重悬浮液中为起稳定作用而掺入的煤泥量也相应减少;加重质粒度变粗后,重悬浮液稳定性变差,为了满足稳定性的要求势必要加大泥质物含量,从而导致脱介筛和分选机效率下降,加重质损失明显增大。
故我国设计规范规定,用磁铁矿粉作加重质时,密度须在4.5g/cm3左右,对加重质磁性物含量的要求是:磁铁矿粉磁性物含量需达到规定的95%以上。
对加重质粒度含量要求是:分选块煤时,-0.074粒度含量必须达到80%以上;分选末煤时,-0.044粒度含量必须达到90%以上。
现场实践表明,分选混煤时,-0.044粒度含量必须达到80%以上,才能有效保证悬浮液稳定。
因此,选煤厂应加强化验管理,根据分选工艺及分选设备的要求制备加重质,如粒度达不到要求,应增加磨矿环节。
磁铁矿粉的磁性物含量越高,加重质回收再利用的数量也越大,介质消耗量越小,生产费用可大大降低。
二、重介悬浮液的粘度和固相体积浓度
重介悬浮液的粘度随固相体积浓度增大而增大。
当固相体积浓度达到35%时,粘度急速上升,当达到50%后,粘度接近最高值,重悬浮液表现为几乎没有流动性,成浆流状态,悬浮液透筛就会很困难:固相体积浓度越高,产品带介越高,反之越低。
要想降低产品带介,就需加大重悬浮液分流量,排除多余的煤泥,以提高悬浮液流动性,从而降低介耗。
分流量过大时,势必又会加大磁铁矿粉在磁选尾矿中的损失(尽管这部分损失相对稳定)。
磁选尾矿中的介质损失比因固相体积浓度高而导致的产品带介损失要小得多。
因此,应重视重悬浮液体积浓度对介耗的影响。
众所周知,重悬浮液粘度对重介质旋流器的分选效果影响较大。
重悬浮液粘度过高会影响原煤的分选效果,而对末煤和煤泥的分选影响尤为显著。
在悬浮液密度满足分选密度要求的条件下,要求悬浮液粘度低,稳定性好,因此固相体积浓度要适宜,这主要取决于非磁性物含量。
一般认为,固相体积浓度的上限不超过30-35%,下限不超过15%。
重介质悬浮液中额定的非磁性物含量越高,为保持系统的平衡所需净化回收的悬浮液数量越少。
所以,为减轻净化回收作业的负担,减少净化回收作业中的介质损失,在不影响分选效果和工艺许可的范围内,适当提高工作介质中额定非磁性物含量是有利的,但不能高于上限。
在介质平衡操作中,为保持介质系统中工作介质密度和为保持非磁性物含量稳定在规定指标上所必需的分流量往
往不一致。
然而工艺上对悬浮液密度的要求是严格的,介质平衡操作应服从于保持介质密度稳定在工艺规定指标的需要。
在这种情况下,工作介质中非磁性物含量将是一个随保持介质密度稳定而形成的平衡值。
如不能满足要求,可考虑通过磨细介质来解决。
三、悬浮液循环量的调整
合格悬浮液循环量偏大也会造成脱介效果不好、产品带介量大。
在不影响分选效果的前提下,降低合格悬浮液循环量可减轻弧形筛、脱介筛的工作负荷,从而减少产品带介与磁选尾矿中的介质损失。
四、弧形筛、脱介筛的脱介效果影响
由于弧形筛和脱介筛在脱介系统中起到至关重要的作用,二者工作效果直接影响到介耗大小。
在生产或调试过程中,一旦出现产品带介高的局面,首先应检测设备运转是否正常,脱介效果如何。
某一环节出现问题,就应对其进行相应的调整。
影响脱介效果的主要因素有:设备的处理能力、入料沿筛宽分布情况、筛面包角、安装角度、筛面材质。
1)弧形筛
正常情况下,弧形筛的选型应满足循环悬浮液.70-80%的脱介能力,甚至更大些。
在生产或调试过程中,有时会出现脱介筛筛面跑介现象(此现象是由于弧形筛脱介能力不够,大量的介质进入脱介筛,使一段合格介质跑到二段稀介段)。
此种情况表明弧形筛脱介能力不够,一般会采取更换更大型号的设备,以满足脱介要求。
否则会影响稀介质段的正常喷水,造成产品带介明显增加。
介质随煤流失,又会造成合格介质桶液位和密度不稳定,影响重介系统的正常运行。
根据现场经验,在筛子合格段增设阻尼条,以增加矿浆流动阻力,降低矿浆流速,增强合格悬浮液透筛能力,这也是强化脱介的措施之一。
(2)弧形筛筛面包角以53度、60度时的脱介效果较理想。
(3)弧形筛安装角度以53度为宜,筛前无堆积物料的现象。
(4)弧形筛入料需沿筛宽均匀分布,并使入料沿其切线方向给入,易于脱介。
否则,弧形筛筛面上存在局部堆积物料,影响脱介效果。
(5)弧形筛筛面应选用防磁材质。
否则,因筛面材质无防磁性或防磁性较差,而影响弧形筛脱介效果,致脱介筛不能满足脱介需要,产品带介增加。
2)脱介筛
影响脱介筛脱介效果的因素有设备脱介能力、筛板材质。
(1)脱介筛设备型号一旦选定,其脱介能力也基本一定。
但筛板材质对脱介效果有一定影响。
众所周知,提高筛机振幅和筛板的自清能力是提高其工作性能的根本所在。
要降低
介耗,需提高脱介效果。
可供选择的较理想筛板材质有两种:一是聚氨酯筛板。
实践证明,聚氨酯筛板好于不锈钢筛板。
主要表现在:具有自清理能力:由于聚氨酯有较好的挠性,用聚氨材料制作的筛板在筛分过程中会产生二次振动,使细粒物料不易堵塞筛孔,实现筛机自清理功能,从而大大改善筛机的脱介效果,对细粒物料的筛分效果尤为明显。
耐磨性能好,使用寿命长:耐磨性是钢制筛板的#3-5倍。
质量轻:由于聚氨酯密度远远低于钢材,使筛机整体重量下降,参振重量的降低可使振幅增加,从而使筛机的处理能力得到提高,大大改善工作状态,利于脱介。
具有防磁功能:由于聚氨酯筛板属于非金属物,不会被磁化。
二是不锈钢筛板。
选用铱铬18镍19钛合金材料,具有磁性小、易于脱介等特点,而且开孔率比聚氨酯筛板通常高20-25%。
(2)喷水。
产品带介的高低除与上述因素有关外,还与喷水的水压、水量、喷水方式有关。
实践表明,喷水的水压一般以0.3-0.4MPa为宜;喷水量应根据设备性能、物料量和粒度组成而定;喷水方式可根据物料性质、处理量及粒度组成来选择,可分段喷水;喷水装臵应采用加压分散性好(如形成扇面)的喷嘴。
此外,在实际操作中,为了进一步降低介耗,需加强对弧形筛和脱介筛喷水制度的管理:
(a)弧形筛的筛面一般需要定期倒换,以保证物料通过弧形筛均匀流入而不是串入脱介筛,确保大部分介质在弧形筛脱除回收,以减轻脱介筛负担,提高脱介效果,降低介耗。
(b)调整脱介筛喷水压力、水量、喷水方式(与上述相同)。
喷水量应根据物料量等进行一系列的调整,否则,水量大时,可能影响磁选效率或造成筛面跑水,后续作业无法正常进行;水量小时,脱介效果不好,产品带介多。
五、分流量的调整
分选后悬浮液中的加重质有一部分被产品带走,又有一部分在悬浮液净化回收过程中流失到磁选尾矿中损失掉。
要减少这部分技术损失,应尽可能减少进入磁选机的分流量,并使合格介质在脱介筛一段完全回收。
六、提高磁选机的分选效率
磁选机作为介质净化回收系统的一种把关设备,磁选效率的高低直接影响介质的损耗。
目前,选煤用的磁选机效率一般在99%左右,仍有约1%,的重介质进入磁选尾矿而流失。
因此,需对磁选机的滚筒转速、磁偏角、矿浆通过量、入料浓度等进行必要的调整,提高磁选效率,减少介质损失。
就美国艺利磁选机使用情况看,允许矿浆的最大入料浓度为25%,当最佳入料浓度20%时,磁选效率最高。
七、改变磁铁矿粉添加方式
生产所需的磁铁矿粉要能及时添加到系统中,这就要求路径要短、反应要快。
若磁铁粉添加是采用介质添加池和高压水冲方式,当冲加的水量过大时,进入添加系统(一般为中煤及矸石磁选系统)的悬浮液密度就会过低,生产所需的介质就不能得到及时补加,会使生产陷于低密度运行而打乱系统应有的平衡状态,势必造成中煤及矸石产品带介增加的恶性循环。
甚至出现有的选煤厂在调试中一个班加介几十吨而密度仍未正常的现象。
解决的办法是:a调整冲加的水量,提高补加的悬浮液密度。
b改变磁铁粉添加方式:人工将磁铁粉直接添加到重介分选系统附近的浓介质转排桶内,使高密度悬浮液能及时补加到合格介质桶;或人工将磁铁粉直接添加到中煤及矸石稀介质桶,经磁选后添加到系统中。
八、严格控制从重介系统中向外排放介质
对于跑、冒、滴、漏、事故放料等流失的介质,应汇集并自成独立的介质回收系统,严格控制从重介系统中向外排放介质。
总之,当选煤厂介耗指标较高时,应进行损失分类分析并采取相应措施。
当管理损失占介耗比例过大时,就应从磁铁矿粉质量、存放、转运和添加等环节找原因,加强管理。
当技术损失占介耗比例过大时,应检查各工艺环节:如果是产品带介造成的损失,就应提高脱介环节的工艺效果;如果是磁选尾矿中流失介质多,则应提高磁选机的回收率;若因分流量处理不当,就应对分流量进行严格控制等等。