齿轮精度设计实例
1圆柱齿轮精度(GB10095-88)
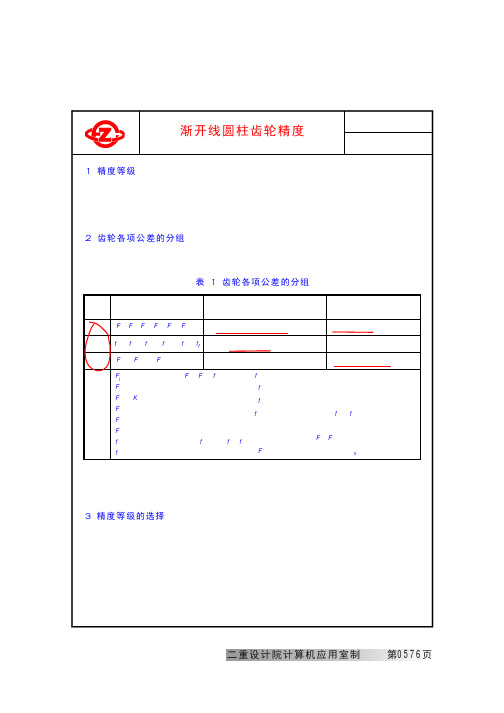
注:主传动齿轮或重要的传动,偏上限选择;辅助传动或一般传动,居中或偏下限选择。
表2各类机器所用齿轮传动的精度等级范围机器类别机器类别精度等级精度等级汽轮机金属切削机床航空发动机轻型汽车载重汽车3 ̄63 ̄84 ̄85 ̄87 ̄9拖拉机通用减速器锻压机床起重机农业机械6 ̄86 ̄86 ̄97 ̄108 ̄11表3常用精度等级齿轮的加工方法及应用范围精度等级5级(精密级)6级(高精度级)7级(比较高的精度级)8级(中等精度级)9级10级(低精度级)加工方法齿面最终精加工齿面粗糙度Ra/μm应用范围效率(%)③在周期性误差非常小的精密齿轮机床上展成加工精密磨齿。
大型齿轮用精密滚齿滚切后,再研磨或剃齿0.8在高精度的齿轮机床上展成加工精密磨齿或剃齿在高精度的齿轮机床上展成加工不淬火的齿轮推荐用高精度的刀具切制。
淬火的齿轮需要精加工(磨齿、剃齿、研磨、珩齿)精密的分度机构用齿轮;用于高速、并对运转平稳性和噪声有比较高的要求的齿轮;高速汽轮机用齿轮;8级或9级齿轮的标准齿轮①①用于在高速下平稳地回转,并要求有最高的效率和低噪声的齿轮;分度机构用齿轮;高速减速器的齿轮;飞机、汽车和机床中的重要齿轮②①用于高速、载荷小或反转的齿轮;机床的进给齿轮;需要运动有配合的齿轮;中速减速器的齿轮;飞机、汽车制造中的齿轮②①对精度没有特别要求的一般机械用齿轮;机床齿轮(分度机构除外);特别不重要的飞机、汽车拖拉机齿轮;起重机、农业机械、普通减速器用齿轮、用于对精度要求不高,并且在低速下工作的齿轮99(98.5)以上99(98.5)以上98(97.5)以上97(96.5)以上96(95)以上用展成法或仿型法加工用任意的方法加工不磨齿。
必要时剃齿或研磨不需要精加工12.5253.2 ̄6.31.600.8注:本表不属国家标准,仅供参考。
①Ⅱ组精度可以降低1级;②Ⅰ组精度可以降低1级;③括号内的效率是包括轴承损失的数值。
表4齿轮圆周速度与最低精度(Ⅱ组)的关系直齿斜齿(平行轴)最低精度Ⅱ组等级()ν≥1515>ν≥1010>ν≥66>ν≥22>ν≥3030>ν≥1515>ν≥1010>ν≥44>ν56789圆周速度ν/(m/s)注:本表不属国家标准,仅供参考。
齿轮结合精度设计
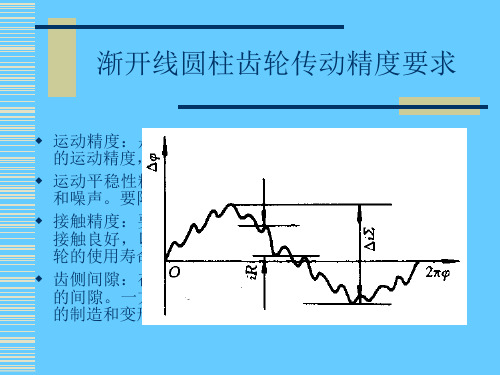
公法线平均长度偏差(△EWm)
公法线平均长度偏差△EW是指在齿轮一周内, 公法线长度平均值与公称值之差。即
△EWm =(W1+W2+…+Wn)/z — W公称 齿轮因齿厚减薄使公法线长度也相应减小,所
以可用公法线平均长度偏差作为反映侧隙的一 项指标。通常是通过跨一定齿数测量公法线长 度来检查齿厚偏差的。
●滚刀本身的基节、齿形等制造误差。此误差会复映到被 加工齿轮的每一齿上,使之产生基节偏差和齿形误差。
以上三项误差在齿坯一转中多次重复出现,为短周期误差。
HOME
圆柱齿轮传动精度的评定指标
根据齿轮精度要求,把齿轮的误差分成影响运 动准确性误差、影响运动平稳性误差、影响载
荷分布均匀性误差和影响侧隙的误差。并相应 提出精度评定指标。
齿形误差(△ff)
齿形误差是在端截面上,齿形工作部分内(齿顶 部分除外),包容实际齿形且距离为最小的两条 设计齿形间的法向距离。设计齿形可以根据工作 条件对理论渐开线进行修正为凸齿形或修缘齿形。
齿形误差会造成齿廓面在啮合过程中使接触点偏 离啮合线,引起瞬时传动比的变化,破坏了传动 的平稳性。
齿距偏差 (△fpt )
几何偏心误差
以滚切直齿圆柱齿轮为例,分析在切齿过程中所产 生的主要加工误差 。
齿坯孔与机床心轴的安装偏心(e),也称几何偏心, 是台齿回坯转在轴机线床OO上不安重装合时形,成齿的坯偏基心准e。轴加线工O1时O1,与滚工刀作 轴线与工作台回转轴线OO距离保持不变,但与齿坯 基滚准切轴成线如O图1所O1示的的距齿离轮不,断使变齿化面(位最置大相变对化于量齿为轮2 e基)。 准中心在径向发生了变化,故称为径向误差。工作 时产生以一转为周期的转角误差,使传动比不断改 变。
3高速级齿轮设计

2K H“1 u 1 Zd H Z E Z;'-H 1mm (3-2)3高速级齿轮设计3.1选定齿轮类型,精度等级,材料及齿数3.1.1压力角选定直齿圆柱齿轮,属于一般用途的齿轮传动,压力角取203.1.2精度选择带式输送机为一般工作机器(通用减速器),参考表10-6⑵,选用7级精度3.1.3材料选择由表10-1[2],选择小齿轮材料为40Cr (调质),齿面硬度280HBS,大齿轮材料为45号钢(调质),齿面硬度为240HBS。
硬度差为40HBS。
3.1.4齿数选择闭式齿轮传动,试选小齿轮齿数Z1=20,大齿轮齿数Z2为:z2= u Z| (3-1)式中:乙——小齿轮齿数;u——I轴与U轴之间的传动比。
故由式3-1,得大齿轮齿数Z2:z2=4.83 20=96.6取z2=97。
3.2按齿面接触疲劳强度设计3.2.1试算小齿轮分度圆直径小齿轮分度圆直径d1t可由下式近似计算:(1)确定公式中的各参数值①试选K Ht=1.3(3-3)O d = 1。
(3-4)式中:?a ——端面重合度,按下式计算:a1=arccos[ Zcos-::] *]N 2h =arccos[ z 2cos:Z 2 2h ;](3-5)z/tan J a1-tan J ) - z 2(tan _::a2-tan r )2 二式中:Z 1 小齿轮齿数;z 2 -------- 大齿轮齿数; h a ---------- 齿顶高系数;② 小齿轮传递的转矩T i 为:h =9.55 106 旦 N mm式中:P i —— I 轴的输入功率,单位:kW ;n i --------- I 轴的转速,单位:r/min 。
故由式3-3,得小齿轮传递的转矩T i :T=9.55"06PN mm = 2.381 如04N mmn i③ 因为小齿轮相对支承非对称布置,所以由表10-7⑵,可查得齿宽系数 ④ 由图10-20⑵,可查得区域系数Z H =2.5。
斜齿圆柱齿轮传动参数选择和设计示例

斜齿圆柱齿轮传动参数选择和设计示例螺旋角的选择提示斜齿轮传动参数选择与直齿轮基本相同,所不同的是多了一个螺旋角β。
斜齿轮传动的轴向力Fa与tgβ成正比,为不使轴承承受过大的轴向力,斜齿圆柱齿轮传动的螺旋角β不宜选得过大。
但β若过小,斜齿轮的特点显示不明显,一般取β=8?,20?,常用β=8?,15?。
近年来设计中β有增大趋势,有的达到25?。
在设计斜齿轮传动时应先初选β角,待其它参数确定后再作精确计算。
β角可用来调整中心距:-1?a=m(z+z)/(2×cosβ)?β=cos[m(z+)/(2×a)] n12n1z2例题试设计一带式输送机减速器的斜齿圆柱齿轮传动。
已知输入功率P,40kW,小齿轮转速n,11960r/min,齿数比u,3.2,由电动机驱动,工作寿命15年(设每年工作300天),两班制,带式输送机工作平稳,转向不变,试设计此传动。
[解]1(选精度等级、材料及齿数1)材料及热处理仍按直齿轮传动例题:大、小齿轮都选用硬齿面。
由表1选得大、小齿轮的材料均为40Cr,并经调质及表面淬火,齿面硬度为48,55HRC;2)精度等级仍选7级精度;3)仍选小齿轮齿数z=24,大齿轮齿数z=77; 124)初选螺旋角β,14?2(按齿面接触强度设计齿面接触强度计算公式为:1) 确定公式内的各计算数值(1)试选K=1.6。
t(2)由图10查取区域系数Z=2.433。
H(3)由图8查得端面重合度ε=0.78,ε=0.87,则ε=ε+ε=1.65。
α1α2αα1α2(4)许用接触应力=1041.5 MPa。
2) 计算(1)试算小齿轮分度圆直径d1tmm =60.49 mm(2)计算圆周速度(3)计算齿宽b及模数m nth=2.25 m=5.51mm b/h=9.88 nt(4)计算纵向重合度ε β(5)计算载荷系数K已知使用系数=l。
根据v=3.04m/s,7级精度,由图5查得动载系数=l.11;由表4查得接触强度计算用的齿向载荷分布系数=1.41;由图6查得弯曲强度计算的齿向载荷分布系数=1.37。
直齿轮传动设计计算实例

直齿轮传动设计计算实例直齿轮传动设计计算实例已知条件:斜齿圆柱齿轮传动,输入功率为PI =4.17kw,齿轮转速为nI=626r/min,传动比为i2=3.7,由电动机驱动,工作寿命为10年,每年工作300天,每天工作16小时,轻微冲击,转向不变。
1、齿轮基本参数选定(齿轮设计参照《机械设计》教材进行设计)(1)运输机为一般工作机器,速度不高,故选用8级精度。
(2)材料:参照表10-1高速级小齿轮选用45#钢调质处理,齿面硬度为250HBS。
高速级大齿轮选用45#钢调质,齿面硬度为220HBS。
(3)小齿轮齿数初选为,大齿轮齿数。
2、按齿面接触强度计算由设计计算公式(10-9a)进行计算,即(1)确定公式内的各计算数据①试选载荷系数②计算小齿轮传递的转矩③由表10-7选取齿宽系数④由表10-6查得材料的弹性影响系数⑤由图10-21d按齿面硬度查得小齿轮的接触疲劳强度极限,大齿轮的接触疲劳强度极限⑥由式10-13计算应力循环次数。
⑦由图10-19取接触疲劳寿命系数。
⑧计算接触疲劳许用应力取失效概率为1%,安全系数S=1,由式(10-12)得﹙2﹚计算①试算小齿轮分度圆直径,代入中最小值。
②计算圆周速度v③计算齿宽b④计算齿宽与齿高之比模数齿高⑤计算载荷系数根据,8级精度,由图10-8查得动载荷系数;直齿轮,;由表10-2查得使用系数;由表10-4用插值法查得8级精度、小齿轮相对支承非对称布置时,。
由,查图得;故载荷系数⑥按实际的载荷系数校正所算得的分度圆直径,由式(10-10a)得⑦计算模数m3、按齿根弯曲强度设计由式(10-5)得弯曲强度的设计公式为(1)确定公式内的各计算数值①由图10-20c查得小齿轮的弯曲疲劳强度极限,大齿轮的弯曲疲劳强度极限;②由图10-18取弯曲疲劳寿命系数,;③计算弯曲疲劳许用应力取弯曲疲劳安全系数S=1.3,由式(10-12)得④计算载荷系数K⑤查取齿形系数由表10-5查得⑥查取应力校正系数由表10-5查得⑦计算大、小齿轮的并加以比较故小齿轮的数值较大。
数控机床技术的齿形加工实例解析
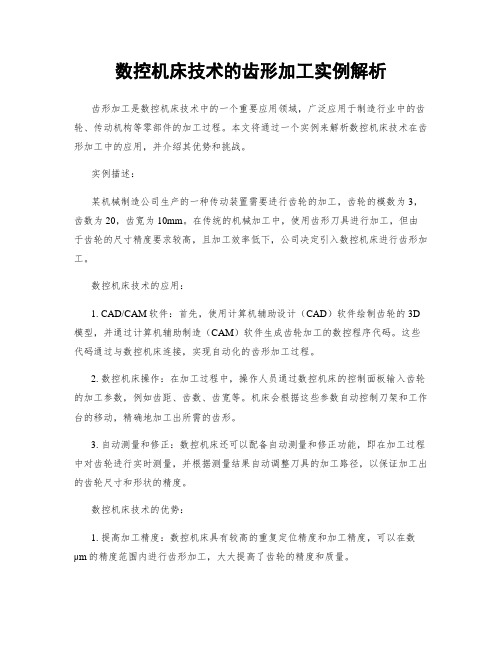
数控机床技术的齿形加工实例解析齿形加工是数控机床技术中的一个重要应用领域,广泛应用于制造行业中的齿轮、传动机构等零部件的加工过程。
本文将通过一个实例来解析数控机床技术在齿形加工中的应用,并介绍其优势和挑战。
实例描述:某机械制造公司生产的一种传动装置需要进行齿轮的加工,齿轮的模数为3,齿数为20,齿宽为10mm。
在传统的机械加工中,使用齿形刀具进行加工,但由于齿轮的尺寸精度要求较高,且加工效率低下,公司决定引入数控机床进行齿形加工。
数控机床技术的应用:1. CAD/CAM软件:首先,使用计算机辅助设计(CAD)软件绘制齿轮的3D 模型,并通过计算机辅助制造(CAM)软件生成齿轮加工的数控程序代码。
这些代码通过与数控机床连接,实现自动化的齿形加工过程。
2. 数控机床操作:在加工过程中,操作人员通过数控机床的控制面板输入齿轮的加工参数,例如齿距、齿数、齿宽等。
机床会根据这些参数自动控制刀架和工作台的移动,精确地加工出所需的齿形。
3. 自动测量和修正:数控机床还可以配备自动测量和修正功能,即在加工过程中对齿轮进行实时测量,并根据测量结果自动调整刀具的加工路径,以保证加工出的齿轮尺寸和形状的精度。
数控机床技术的优势:1. 提高加工精度:数控机床具有较高的重复定位精度和加工精度,可以在数μm的精度范围内进行齿形加工,大大提高了齿轮的精度和质量。
2. 提高生产效率:相比传统的机械加工方法,数控机床技术具有高度自动化的特点,可以实现多轴同时加工,提高生产效率,缩短加工周期。
3. 灵活性和可编程性:数控机床可以根据不同的加工要求进行编程和设置,具有较高的灵活性。
同时,数控程序可以保存和复制,方便批量生产。
数控机床技术的挑战:1. 高成本:数控机床的引入和维护成本相对较高,需要公司投入较大的资金。
2. 技术要求高:数控机床操作需要专业的技术人员进行操作和维护,对操作人员的技术要求较高,需要进行培训和学习。
3. 刀具选择和磨损:齿形加工过程对刀具的选择和磨损情况要求较高,需要合理选择刀具材料和使用寿命。
精度设计实例
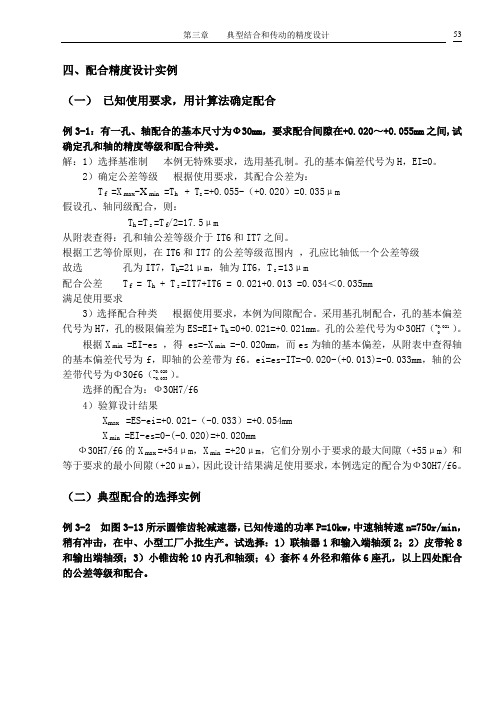
第三章典型结合和传动的精度设计- 53 四、配合精度设计实例(一)已知使用要求,用计算法确定配合例3-1:有一孔、轴配合的基本尺寸为Ф30mm,要求配合间隙在+0.020~+0.055mm之间,试确定孔和轴的精度等级和配合种类。
解:1)选择基准制本例无特殊要求,选用基孔制。
孔的基本偏差代号为H,EI=0。
2)确定公差等级根据使用要求,其配合公差为:T f =X max-X min =T h + T s =+0.055-(+0.020)=0.035μm假设孔、轴同级配合,则:T h =T s =T f/2=17.5μm从附表查得:孔和轴公差等级介于IT6和IT7之间。
根据工艺等价原则,在IT6和IT7的公差等级范围内,孔应比轴低一个公差等级故选孔为IT7,T h=21μm,轴为IT6,T s =13μm配合公差 T f = T h + T s =IT7+IT6 = 0.021+0.013 =0.034<0.035mm满足使用要求3)选择配合种类根据使用要求,本例为间隙配合。
采用基孔制配合,孔的基本偏差)。
代号为H7,孔的极限偏差为ES=EI+ T h =0+0.021=+0.021mm。
孔的公差代号为Ф30H7(+0.0210根据X min =EI-es ,得 es=-X min =-0.020mm,而es为轴的基本偏差,从附表中查得轴的基本偏差代号为f,即轴的公差带为f6。
ei=es-IT=-0.020-(+0.013)=-0.033mm,轴的公)。
差带代号为Ф30f6(-0.020-0.033选择的配合为:Ф30H7/f64)验算设计结果X max =ES-ei=+0.021-(-0.033)=+0.054mmX min =EI-es=0-(-0.020)=+0.020mmФ30H7/f6的X max =+54μm,X min =+20μm,它们分别小于要求的最大间隙(+55μm)和等于要求的最小间隙(+20μm),因此设计结果满足使用要求,本例选定的配合为Ф30H7/f6。
齿轮齿条设计计算举例

第四章 齿轮设计4.1 齿轮参数的选择[8]齿轮模数值取值为m=10,主动齿轮齿数为z=6,压力角取α=20°,齿轮螺旋角为β=12°,齿条齿数应根据转向轮达到的值来确定。
齿轮的转速为n=10r/min ,齿轮传动力矩2221Nm ⋅,转向器每天工作8小时,使用期限不低于5年. 主动小齿轮选用20MnCr5材料制造并经渗碳淬火,而齿条常采用45号钢或41Cr4制造并经高频淬火,表面硬度均应在56HRC 以上。
为减轻质量,壳体用铝合金压铸。
4.2 齿轮几何尺寸确定[2] 齿顶高 ha =()()mmh m n an n 25.47.015.2=+⨯=+*χ,ha=17齿根高 hf()()mmc h m n n an n 375.17.025.015.2=-+⨯=-+=**χ,hf=5.5齿高 h = ha+ hf =17+5.5=22.5分度圆直径 d =mz/cos β=mm337.1512cos 65.2=⨯d=61.348齿顶圆直径 da =d+2ha =61.348+2×17=95.348齿根圆直径 df =d-2hf =61.348-2×11基圆直径mmd d b 412.1420cos 337.15cos =⨯== α db=57.648法向齿厚为 5.2364.07.022tan 22⨯⎪⎭⎫⎝⎛⨯⨯+=⎪⎭⎫ ⎝⎛+=παχπn n n n m smm 593.4=×4=18.372端面齿厚为 5253.2367.0cos 7.022tan 222⨯⎪⎪⎭⎫ ⎝⎛⨯⨯+=⎪⎭⎫⎝⎛+=βπαχπt t t t m smm 275.5=×4=21.1分度圆直径与齿条运动速度的关系 d=60000v/πn1=⇒v 0.001m/s齿距 p=πm=3.14×10=31.4齿轮中心到齿条基准线距离 H=d/2+xm=37.674(7.0)4.3 齿根弯曲疲劳强度计算[11]4.3.1齿轮精度等级、材料及参数的选择(1) 由于转向器齿轮转速低,是一般的机械,故选择8级精度。
齿轮精度设计
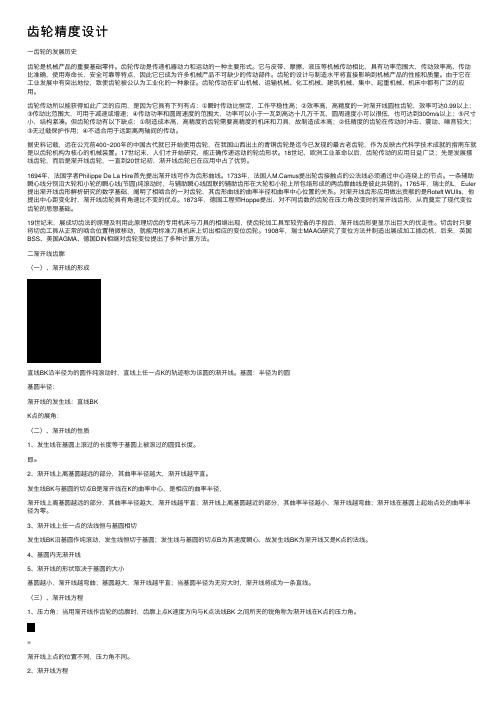
齿轮精度设计⼀齿轮的发展历史齿轮是机械产品的重要基础零件。
齿轮传动是传递机器动⼒和运动的⼀种主要形式。
它与⽪带、摩擦、液压等机械传动相⽐,具有功率范围⼤,传动效率⾼、传动⽐准确,使⽤寿命长,安全可靠等特点,因此它已成为许多机械产品不可缺少的传动部件。
齿轮的设计与制造⽔平将直接影响到机械产品的性能和质量。
由于它在⼯业发展中有突出地位,致使齿轮被公认为⼯业化的⼀种象征。
齿轮传动在矿⼭机械、运输机械、化⼯机械、建筑机械、集中、起重机械、机床中都有⼴泛的应⽤。
齿轮传动所以能获得如此⼴泛的应⽤,是因为它具有下列有点:①瞬时传动⽐恒定,⼯作平稳性⾼;②效率⾼,⾼精度的⼀对渐开线圆柱齿轮,效率可达0.99以上;③传动⽐范围⼤,可⽤于减速或增速;④传动功率和圆周速度的范围⼤,功率可以⼩于⼀⽡到⾼达⼗⼏万千⽡,圆周速度⼩可以很低,也可达到300m/s以上;⑤尺⼨⼩,结构紧凑。
但齿轮传动有以下缺点:①制造成本⾼,⾼精度的齿轮需要⾼精度的机床和⼑具,故制造成本⾼;②低精度的齿轮在传动时冲击、震动、噪⾳较⼤;③⽆过载保护作⽤;④不适合⽤于远距离两轴间的传动。
据史料记载,远在公元前400~200年的中国古代就已开始使⽤齿轮,在我国⼭西出⼟的青铜齿轮是迄今已发现的最古⽼齿轮,作为反映古代科学技术成就的指南车就是以齿轮机构为核⼼的机械装置。
17世纪末,⼈们才开始研究,能正确传递运动的轮齿形状。
18世纪,欧洲⼯业⾰命以后,齿轮传动的应⽤⽇益⼴泛;先是发展摆线齿轮,⽽后是渐开线齿轮,⼀直到20世纪初,渐开线齿轮已在应⽤中占了优势。
1694年,法国学者Philippe De La Hire⾸先提出渐开线可作为齿形曲线。
1733年,法国⼈M.Camus提出轮齿接触点的公法线必须通过中⼼连绕上的节点。
⼀条辅助瞬⼼线分别沿⼤轮和⼩轮的瞬⼼线(节圆)纯滚动时,与辅助瞬⼼线固联的辅助齿形在⼤轮和⼩轮上所包络形成的两齿廓曲线是彼此共轭的。
1765年,瑞⼠的L.Euler 提出渐开线齿形解析研究的数学基础,阐明了相啮合的⼀对齿轮,其齿形曲线的曲率半径和曲率中⼼位置的关系。
六级精度齿轮齿形加工方案
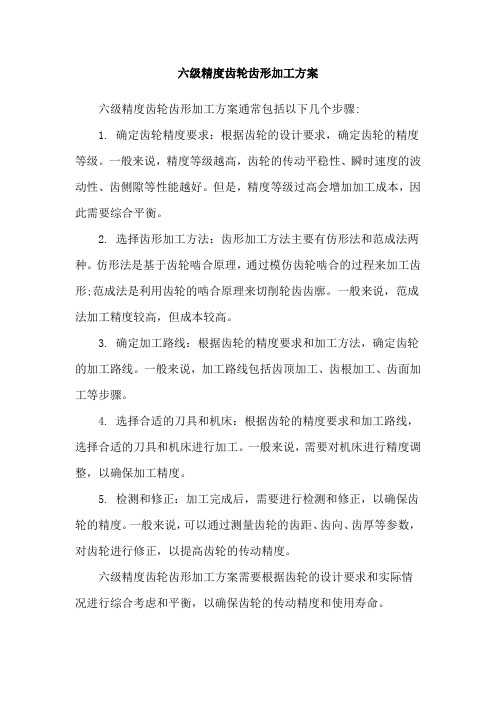
六级精度齿轮齿形加工方案
六级精度齿轮齿形加工方案通常包括以下几个步骤:
1. 确定齿轮精度要求:根据齿轮的设计要求,确定齿轮的精度等级。
一般来说,精度等级越高,齿轮的传动平稳性、瞬时速度的波动性、齿侧隙等性能越好。
但是,精度等级过高会增加加工成本,因此需要综合平衡。
2. 选择齿形加工方法:齿形加工方法主要有仿形法和范成法两种。
仿形法是基于齿轮啮合原理,通过模仿齿轮啮合的过程来加工齿形;范成法是利用齿轮的啮合原理来切削轮齿齿廓。
一般来说,范成法加工精度较高,但成本较高。
3. 确定加工路线:根据齿轮的精度要求和加工方法,确定齿轮的加工路线。
一般来说,加工路线包括齿顶加工、齿根加工、齿面加工等步骤。
4. 选择合适的刀具和机床:根据齿轮的精度要求和加工路线,选择合适的刀具和机床进行加工。
一般来说,需要对机床进行精度调整,以确保加工精度。
5. 检测和修正:加工完成后,需要进行检测和修正,以确保齿轮的精度。
一般来说,可以通过测量齿轮的齿距、齿向、齿厚等参数,对齿轮进行修正,以提高齿轮的传动精度。
六级精度齿轮齿形加工方案需要根据齿轮的设计要求和实际情况进行综合考虑和平衡,以确保齿轮的传动精度和使用寿命。
齿轮的精度与公差

1、齿轮精度主要是控制齿轮在运转时齿轮之间传递的精度,比如:传动的平稳性、瞬时速度的波动性、若有交变的反向运行,其齿侧隙是否达到最小,如果有冲击载荷,应该稍微提高精度,从而减少冲击载荷带给齿轮的破坏。
2、如果以上这些设计要求比较高,则齿轮精度也就要定得稍高一点,反之可以定得底一点3、但是,齿轮精度定得过高,会上升加工成本,需要综合平衡4、你上面的参数基本上属于比较常用的齿轮,其精度可以定为:7FL,或者7-6-6GM精度标注的解释:7FL:齿轮的三个公差组精度同为7级,齿厚的上偏差为F级,齿厚的下偏差为L级7-6-6GM:齿轮的第一组公差带精度为7级,齿轮的第二组公差带精度为6级,齿轮的第三组公差带精度为6级,齿厚的上偏差为G级,齿厚的下偏差为M级5、对于齿轮精度是没有什么计算公式的,因为不需要计算,是查手册得来的。
6、精度等级的确定是工程师综合分析的结果,传动要求精密、或者是高负载、交变负载……就将精度等级定高一点7、精度等级有5、6、7、8、9、10级,数值越小精度越高8、(齿厚)偏差等级也是设计者综合具体工况给出的等级,精密传动给高一点,一般机械给低一点,闭式传动给高一点,开式传动给低一点。
9、(齿厚)偏差等级有C、D、E、F、G、H、J、K、L、M、N、P、R、S级,C级间隙最大,S级间隙最小。
10、不管是精度等级,还是偏差等级,定得越高,加工成本也越高,需要综合分析之后再具体的给出一个恰当的精度等级和偏差等级。
11、对于齿轮的常规检验项目,分为3组检验项目,分别如下:12、第一组检验项目主要是保证传递运动的准确性,其项目包括:切向综合公差Fi'、周节累积公差Fp、k个周节累积公差Fpk、径向综合公差Fi"、齿圈径向跳动公差Fr、公法线长度变动公差Fw13、第二组检验项目主要是保证传递运动的平稳性、噪声、振动,其项目包括:切向一齿综合公差fi'、基节极限偏差fpb、周节极限偏差fpt、径向一齿综合公差fi"14、第三组检验项目主要是保证载荷分布的均匀性,其项目包括:齿向公差Fβ、接触线公差Fb、轴向齿距极限偏差Fpx15、齿轮的齿坯公差的精度等级为:5、6、7、8、9、10级16、齿轮中间的孔公差、及其形位公差:IT5、IT6、IT7、IT8级17、齿轮轴的尺寸公差、及其形位公差:IT5、IT6、IT718、顶圆直径公差:IT7、IT8、IT919、基准面的径向跳动、基准面的端面跳动:根据直径的大小,按照5、6、7、8、9、10级查表20、需要说明一下:我给出的·第一组、第二组、第三组检验项目是比较全的,但是,在实际中,在实际的图纸上,我们列出的检验项目没有这么多,太多了不但给检验带来麻烦,还增加制造成本,所以,在图纸上只检验其中的几项即可,你可以参看一下专业的齿轮图纸,也可以在《机械设计手册》上看看例题,在此给你列出常规要检查的、在图纸上要列出来的项目:21、小齿轮的检验项目:21、根据你上面给出的参数,小齿轮的精度等级可以定为7FL,接下来级,就是按照精度等级差手册:22、周节积累公差Fp:0.06323、周节极限偏差fpt:0.01824、在图纸上标注的齿坯公差:内孔按照IT7级:在手册上按照孔径大小查《标准公差表》25、顶圆的径向跳动:按照外径尺寸大小查《标准公差表》26、大齿轮的检验项目:27、周节积累公差Fp:0.09028、周节极限偏差fpt:0.02029、在图纸上标注的齿坯公差:内孔按照IT7级:在手册上按照孔径大小查《标准公差表》30、顶圆的径向跳动:按照外径尺寸大小查《标准公差表》从你不断提问来看,你钻研得很深,非常不错,未来的工程师!但是,要系统的学习呀,机械工程师目前是非常吃香的,毕业后是可以拿高工资的,希望你努力!希望以上能够对你有所帮助。
齿轮精度标准及测量解决方案
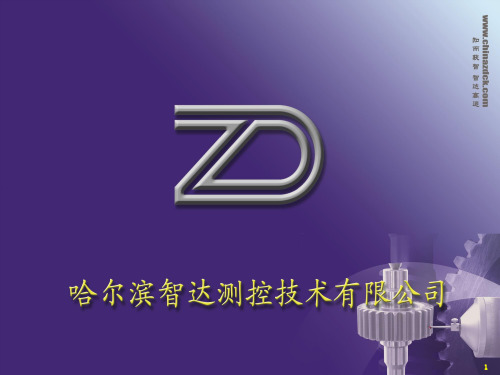
24
JD45与新一代JD50的区别
25
JE 系列经济型齿轮测量中心 保持电子展成式齿轮测量仪的核心技术特点,对产品进行优化设计,适合生 产现场使用。
26
JC25型齿形齿向测量仪 经典的机械展成式结构,适用 性强,测量精度高,方便快捷。
27
JS系列智能齿轮双面啮合综合测量仪
JS10型齿轮双面啮合仪
• 1、JL系列大规格齿轮测量中心 • 2、JLR系列极坐标(直角坐标)大规格齿轮测量中心 • 3、JA系列新一代电子展成齿轮测量中心 • 4、JD系列电子展成齿轮测量仪 • 5、JE系列经济型电子展成齿轮测量仪 • 6、JC型机械展成式齿形齿向测量仪 • 7、JS系列智能齿轮双面啮合测量仪 • 8、老仪器的改造
22
JA100 JA80 JA65 JA50 JA30
JA系列新一代齿轮测量中心
高端齿轮测量中心, 在成熟技术上,进行了软 硬件的全面升级,适用于 对高精度齿轮、齿轮刀具、 涡轮蜗杆、弧齿锥齿轮进 行快速、准确、全面检测
23
JD系列电子展成式测量中心
JD18 JD30 JD50 JD65
高精度,高可靠性的电 子展成式测量中心,适合于 工厂计量室用于对圆柱齿轮, 齿轮刀具,蜗轮蜗杆,弧 (直)锥齿轮的测量。
9
上端修形
下端 修形
三压力角评定
齿顶修形
齿根 修形
10
K形图评定
11
热前热后比较
12
热前热后统计表格
13
热前热后统计图表
14
热前热后统计图表
15
扭曲测量(多截面测量)
16
形貌测量
17
空齿并齿设定
18
全齿测量
齿轮精度及检测
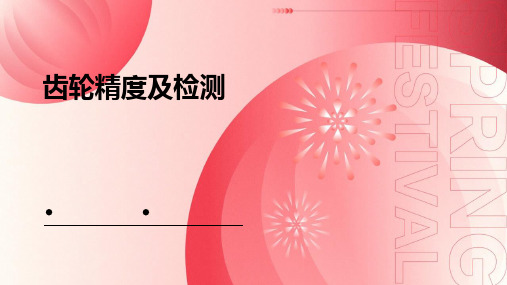
通过使用高精度的测量设备和测量方法,对减速机齿轮的齿形、 齿向、齿距等进行测量,确保齿轮精度符合设计要求。
齿轮精度优化
根据测量结果,对齿轮进行优化设计,调整齿轮参数,提高齿轮的 承载能力和使用寿命。
优化效果评估
通过实验验证,对比优化前后的齿轮性能,评估优化效果,为后续 齿轮设计提供参考。
径向跳动检测是齿轮精度检测中的一 种重要方法,用于测量齿轮在旋转一 周过程中,齿轮轴线产生的最大径向 位移量。
径向跳动的大小反映了齿轮的加工精 度和装配质量,对于保证齿轮传动的 平稳性和减小振动具有重要意义。
径向跳动检测通常采用测量仪器,如 千分表或激光测微仪,对齿轮的齿面 进行逐个测量,以获取每个齿面的径 向跳动值。
齿厚检测是齿轮精度检测中的 一项基本指标,用于测量齿轮 上任意一个齿的实际厚度。
齿厚检测通常采用测量仪器, 如卡尺或千分尺,对齿轮的齿 面进行逐个测量,以获取每个 齿面的齿厚值。
齿厚的大小直接影响到齿轮的 强度和装配质量,因此对于保 证齿轮传动的性能和安全性具 有重要意义。
接触斑点检测
接触斑点检测是齿轮精度检测中的一种常用方法,用于评估齿轮副在正 常工作状态下接触面的分布情况。
接触斑点检测通常采用涂色法或光学投影法,将齿轮副装配在一起,然 后通过观察接触面上的颜色变化或投影图像来分析接触斑点的分布情况。
接触斑点的大小和分布反映了齿轮副的接触性能和传动质量,对于保证 齿轮传动的平稳性和减小振动具有重要意义。
03
齿轮精度对设备性能的影 响
对传动效率的影响
总结词
齿轮精度对传动效率具有显著影响。
对设备噪声的影响
总结词
齿轮精度对设备噪声有显著影响。
详细描述
齿轮精度等级的选择
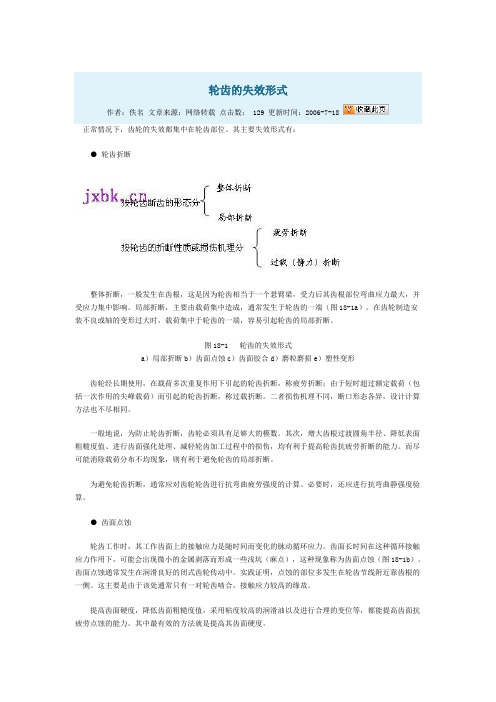
轮齿的失效形式作者:佚名文章来源:网络转载点击数: 129 更新时间:2006-7-18正常情况下,齿轮的失效都集中在轮齿部位。
其主要失效形式有:● 轮齿折断整体折断,一般发生在齿根,这是因为轮齿相当于一个悬臂梁,受力后其齿根部位弯曲应力最大,并受应力集中影响。
局部折断,主要由载荷集中造成,通常发生于轮齿的一端(图18-1a)。
在齿轮制造安装不良或轴的变形过大时,载荷集中于轮齿的一端,容易引起轮齿的局部折断。
图18-1 轮齿的失效形式a)局部折断b)齿面点蚀c)齿面胶合d)磨粒磨损e)塑性变形齿轮经长期使用,在载荷多次重复作用下引起的轮齿折断,称疲劳折断;由于短时超过额定载荷(包括一次作用的尖峰载荷)而引起的轮齿折断,称过载折断。
二者损伤机理不同,断口形态各异,设计计算方法也不尽相同。
一般地说,为防止轮齿折断,齿轮必须具有足够大的模数。
其次,增大齿根过渡圆角半径、降低表面粗糙度值、进行齿面强化处理、减轻轮齿加工过程中的损伤,均有利于提高轮齿抗疲劳折断的能力。
而尽可能消除载荷分布不均现象,则有利于避免轮齿的局部折断。
为避免轮齿折断,通常应对齿轮轮齿进行抗弯曲疲劳强度的计算。
必要时,还应进行抗弯曲静强度验算。
● 齿面点蚀轮齿工作时,其工作齿面上的接触应力是随时间而变化的脉动循环应力。
齿面长时间在这种循环接触应力作用下,可能会出现微小的金属剥落而形成一些浅坑(麻点),这种现象称为齿面点蚀(图18-1b)。
齿面点蚀通常发生在润滑良好的闭式齿轮传动中。
实践证明,点蚀的部位多发生在轮齿节线附近靠齿根的一侧。
这主要是由于该处通常只有一对轮齿啮合,接触应力较高的缘故。
提高齿面硬度,降低齿面粗糙度值,采用粘度较高的润滑油以及进行合理的变位等,都能提高齿面抗疲劳点蚀的能力。
其中最有效的方法就是提高其齿面硬度。
为了避免出现齿面点蚀,对于闭式齿轮传动,通常需要进行齿面接触疲劳强度计算。
●齿面胶合齿面胶合是相啮合轮齿的表面,在一定压力下直接接触发生粘着,并随着齿轮的相对运动,发生齿面金属撕脱或转移的一种粘着磨损现象(图18-1c)。
圆柱齿轮精度标准

公差组 检验组
附注
△fi’
综合项目,成批生产时优先选用
△ff与△fpb △ff能反映单个齿的齿形误差,
△ff与△fpt
而△fpb或△fpt反映出换齿时是
否平稳
II
*
f fβ
用于6级及以上精度的斜齿轮或 人字齿轮
△fi’’ 需保证齿形精度
△fpt与△fpb 用于9~12级精度
第II公差组:Δfi’’ 第III公差组:ΔFβ 各项目的公差值查表12-13、12-14、12-15 3.计算齿轮副侧隙和确定齿厚极限偏差代号 (1)计算jnmin:按喷油润滑和v=4.78m/s查表
jn1=0.01mn=0.03mm jn2=2a(α1Δt1-α2Δt2)sinα=0.031mm jnmin= jn1 +jn2=0.061mm
877fjgbt100951988应用范围精度等级应用范围精度等级测量齿轮拖拉机610汽轮机减速器轧钢设备小齿轮610内燃机与电气机车矿用绞车810轻型汽车起重机机构710重型汽车农业机械811航空发动机表表12126各种机械采用的齿轮的精度等级各种机械采用的齿轮的精度等级圆周速度3151553030表表12127第第iiii公差组等级的选择公差组等级的选择负荷性质要求噪声强度db重负荷中负荷轻负荷表表12128第第iiiiii公差组等级的选择公差组等级的选择表121210n1n1推荐值推荐值表表121210n1n1推荐值推荐值润滑方法圆周速度ms101025256060喷油润滑001m油池润滑0005001
轮齿厚减薄总量δS
s 2 fa sin n
f2 pb1
f2 pb 2
2.104F2
总的减薄量 SN jn1 jn2 S
- 1、下载文档前请自行甄别文档内容的完整性,平台不提供额外的编辑、内容补充、找答案等附加服务。
- 2、"仅部分预览"的文档,不可在线预览部分如存在完整性等问题,可反馈申请退款(可完整预览的文档不适用该条件!)。
- 3、如文档侵犯您的权益,请联系客服反馈,我们会尽快为您处理(人工客服工作时间:9:00-18:30)。
Wang chenggang
6 螺旋波度误差( △ffβ )
指宽斜齿轮齿高中部实际齿线(螺旋线)波纹最大波幅
螺旋线波纹
△ffβ
`
Wang chenggang
第Ⅱ公差组项目
1
2
一齿切向综合误差Δfi′及公差fi
′
一齿径向综合误差Δfi″及公差fi ″
第九章
圆柱齿轮的互换性 及其检测
`
Wang chenggang
第一节 概述 第二节 影响齿轮运动准确性的误差项目及公差 第三节 影响齿轮运动平稳性的误差项目及公差
第四节 影响载荷分布均匀性的误差项目及公差
第五节 齿轮副误差和检验项目及公差 第六节 渐开线圆柱齿轮精度标准
`
Wang chenggang
测量方法:
测量方法较简便,凡具有两个平行测量面,其量爪能插 入跨测齿槽的量仪,均可用以测量ΔFw 。常用的量仪有 游标卡尺,公法线千分尺,公法线指示规及万能测齿仪等。
公法线指示规
`
Wang chenggang
第Ⅰ公差组误差及公差项目
1 2 切向综合误差ΔFi′及公差Fi ′ 齿距累积误差ΔFp及公差Fp
-0.093
齿轮零件图
`
Wang chenggang
第一节
一 齿轮的传动要求
概述
对不同用途的齿轮,传动要求有: 分度机构和读数机构的齿轮 高速动力齿轮,如减速器、 汽轮机等 低速动力齿轮,如轧钢、矿 山及起重机械等 保证正常润滑、避免因发 热而卡死
`
传递运动的准确性 传递运动的平稳性 载荷分布的均匀性 传动侧隙
5 齿距偏差(△fpt)及极限偏差± fpt 指在分度圆上(允许在齿高中部测量)实际齿距 与公称齿距之差。 实际齿距
△fpt
公称齿 距
`
Wang chenggang
按基准不同分以下几种:
以齿顶圆为定位基准 以齿根圆为定位基准
以 孔 为 定 位 基 准
齿距偏差是由机床传动链误差(主要是分度蜗杆跳动)引起的 `
单圆盘渐开线检查仪 被测齿轮与 一直径等于该齿 基圆盘 轮基圆直径的基 圆盘同轴安装, 直尺与基圆盘作 纯滚动,测量头 直尺 与被测齿廓接触 点相对于基圆盘 的运动轨迹是理 想渐开线,若被 测齿廓不是理想 渐开线可从表中 读出。
`
被测齿轮
测量杆
Wang chenggang
4 基节偏差(△fpb)及极限偏差±fpb 指实际基节与公称基节之差
`
Wang chenggang
3
齿形误差(△ff)及公差 ff
指在齿轮端截面上,齿形工作部分内(齿顶倒棱部 分除外),包容实际齿形的两条设计齿形间的法向距离 齿顶倒棱 高度
齿形误差
设计齿形
工作部分
`
Wang chenggang
设计齿形可以是修正的理论渐开线,包括修缘 齿形和凸齿形等
齿顶
实际齿形
齿形工 作部分
(1)主动轮基节大于从动轮基节
从动轮基节
N
A2 A1
ω2
B2 B1
△fpb
N
主动轮基节
ω1
`
Wang chenggang
(2) 主动轮基节小于从动轮基节
ω2 N
A2′ A1′ B2′ B1′
ω1
N
两种情况造成瞬时传动比产生突变,引起振动,撞击
和噪音(后一种比前一种严重)
`
Wang chenggang
转角误差△φ
0 360°
△Fi′
转角φ
`
Wang chenggang
光栅式齿轮单面啮合仪
测 量 齿 轮
Z1
放大整形 被测齿轮Z2 圆光栅
倍频器 f1*Z1 ` 分频器 f1*Z1/Z2
Wang chenggang
比 相 计
滤 波 器
记 录 器
放大整形
2 齿距累积误差ΔFp及公差Fp (ΔFpk及 Fpk)K=2~Z/2
3
齿圈径向跳动ΔFr及公差Fr
指在齿轮一转范围内,测头在齿槽内于齿高中部 双面接触,测头相对于齿轮轴线的最大变动量。
`
Wang chenggang
齿圈径向跳动ΔFr: 齿轮一转内,测头在齿 槽内于齿高中部双面接触, 测头相对于齿轮轴线的最 大变动量。
L
径向误差
ΔFr
齿序
1 2 3 4 5 6 7 8 9 10 11
△ff
△ff
△ff
理论齿形
凸齿形
`
修缘齿形
Wang chenggang
齿形误差是由刀具的齿形误差,刀具的跳动,机床 传动链中周期变动的误差而造成的。
齿形误差影响传动平 稳性,如图由于齿形误差 的影响,啮合点从a移到点 a′,从而引起瞬时传动 比的突变,破坏了传动的 平稳性。
啮合线
a
A1
A2
a′
`
Wang chenggang
指在分度圆上,任意两个同侧齿面间的实际弧长 与公称弧长的最大差值 Fp 1 8 2 7
Fpmin Fpmax 齿序
5 6 7
8 1
3 6 4
1
2 3
4
公称齿廓
5
实际齿廓
`
△Fp= △Fpmax- △Fpmin
Wang chenggang
齿距累积误差ΔFp的测量方法有相对法和绝对法两种: 1)相对法 利用圆周封闭原理,首先以被测齿轮的任一实际齿距作 为起始基准,调整仪器的零位,然后按顺序测量其它齿 距,得相对齿距差,通过数据处理便可求得ΔFp值。
a〃
测量齿轮
`
Wang chenggang
ΔFi″主要反映径向误差,可代替ΔFr检测。 ΔFi″比ΔFr检查效率高,且能得到一条连续的误 差曲线,故成批生产时,常检验ΔFi″项目。
双啮中心距△a
0
△Fi″
转角φ
360°
`
Wang chenggang
5
公法线长度变动ΔFw及公差Fw
齿轮一转范围内,实际公法线长度最大值与最小值之差
“ˊ”:单面仪测量
脚注i: 综合指标
“″”: 双面仪测量 Δ:误差或偏差
`
Wang chenggang
第二节 影响齿轮运动准性的误差项目及公差
一 第一公差组
1
2
切向综合误差ΔFi′及公差Fi′
齿距累积误差ΔFp及公差Fp (ΔFpk及Fpk)K=2~Z/2
3 齿圈径向跳动ΔFr及公差Fr 4 径向综合误差ΔFi〞及公差Fi〞
与0′同轴的圆
滚刀
齿坯 与0同轴的圆
e
几
e `
几
Wang chenggang
`
Wang chenggang
测量方法: ΔFr可在齿圈径向跳动仪,万能测齿仪或普通偏摆仪 上测量。
把测量头(球形或圆锥形)或小圆柱放在齿间,逐 齿进行测量。在轮齿一转中指示表最大读数与最小读数 之差即ΔFr
`
Wang chenggang
3
4 5
齿圈径向跳动ΔFr及公差Fr
径向综合误差ΔFi〞 〞及公差Fi 〞 公法线长度变动ΔFw及公差ΔFw
`
Wang chenggang
二 第Ⅰ公差规定检验组 评定运动准确性,需检验齿轮径向和切向两个方面的 误差。根据齿轮传动的用途,生产条件,检验量仪情况,在 第Ⅰ公差组中,选下列方案之一来评定齿轮运动准确性。 1) 切向综合误差ΔFi′ 综合指标 2)齿距累积误差ΔFp 3)径向综合误差ΔFi〞与公法线长度变动ΔFw 4)齿圈径向跳动ΔFr与公法线长度变动ΔFw 5)齿圈径向跳动ΔFr (仅用于10-12级) 对于10-12级齿轮,由于齿轮加工机床已有足够的精 度,因此只检验Fr一项,而不必检验Fw。 第Ⅰ公差组检验的结果,只能评定该齿轮的运动精度 是否合格,而不能断定整个齿轮是否合格,因此还需检验 第Ⅱ,Ⅲ公差组的指标。
基圆
ΔFw=Wmax-Wmin 当α=20 时,公法线长度的公称值W W=m[ 1.476(2k-1)+0.014z],k=z/9 +0.5 `
Wang chenggang
。
r+e运
r-e运
运动偏心e运
P1
r
0´ 0
e运
P2
e运
机床分度蜗轮加工误差 及安装偏心引起的。
`
Wang chenggang
1 一齿切向综合误差(△fi′)及公差fi′ 在切向综合误
指被测齿轮与理想 精确的测量齿轮单 面啮合时,在被测 齿轮一齿距角内实 际转角与公称转角 之差的最大幅度值
引起的原因:
转角误差△φ
0
△Fi′
转角φ
360°
刀具的制造误差和安装误差以及机床传动链短周期误差。
`
Wang chenggang
2 一齿径向综合误差(△fi″)及公差fi″ 指被测齿轮与理想精确的测量齿轮双面啮合时, 在被测齿轮一齿距角内,双啮中心距的最大变动量 在径向综合误差纪 录曲线上小波纹的 最大幅度值。
`
Wang chenggang
第三节 影响齿轮运动平稳性的误差项目及公差
一 第Ⅱ公差组
1
2
一齿切向综合误差(△fi′)
一齿径向综合误差(△fi〃)
3 4 5
齿形误差(△ff) 基节偏差(△fpb) 齿距偏差(△fpt)
二 第Ⅱ公差规定检验组
`
Wang chenggang
一
第Ⅱ公差组
差纪录曲线 上小波纹的 最大幅度值
Wang chenggang
二 齿轮的加工
范成法: 利用刀具 与被切齿轮的互 相啮合运动切出 齿形的方法。 插齿加工
Ⅲ
`