转炉喷溅渣循环利用技术的开发与应用
溅渣护炉技术 冶金

毕业设计(论文)学校:专业:冶金技术班级:学生:学号:指导教师:摘要溅渣护炉技术作为一项工艺简单、综合经济效益高的新技术,正别外国许多厂家推广、使用,分析了该技术的优势及存在的问题和解决办法,以及该技术的应用现状和应用前景。
转炉溅渣护炉是在出钢后,将转炉内留渣的粘度和氧化镁含量调整到合适的范围,在车间原有的氧枪或另设专用喷枪,向氧化镁含量、高粘度的炉渣喷一定压力和流量的氮气,将粘渣吹溅到炉衬上全面涂挂、冷却、凝固成一层炉渣质的保护层,避免了在冶炼时炉衬和炉渣的直接接触,从而起到减缓耐火材料的蚀损,延长转炉炉龄的作用。
溅渣护炉作为一项实用技术,经过国内外许多钢厂实践后,对提高转炉炉龄和降低耐火材料消耗的效果非常显著。
关键词:溅渣护炉;转炉;应用目录1存在问题及解决办法 (1)2溅渣护炉工艺的冶金因素及其优势 (2)3国外溅渣炉技术的发展 (3)4国内转炉炉龄现状及溅渣护炉技术的发展 (5)5应用现状及应用前景 (6)致谢信 (7)参考文献 (8)1存在问题及解决办法任何一项技术的应用不可能没有缺陷,在一些早期设备上,氧枪结瘤就是一个问题。
溅渣技术使用后,往往使枪结瘤出现次数增加。
实践证明,在溅渣过程中,若炉内残留少量钢水,氧枪结瘤将更加严重。
解决这个问题,有几种方法证明是有效的。
第一,有充足冷却水的炉子不出现结瘤问题;第二,将用于吹炼的热氧枪移走,换上冷枪完成溅渣,氧枪结瘤几乎完全消除。
这表明氧枪结瘤与温度和热量的传递有关。
渣子和冷枪的表面结合并不紧密,如果在溅渣时冷凝钢不出现在氧枪上,那就不会再氧枪上形成粗糙的外壳以使炉渣粘附其上。
溅渣后将氧枪停放在支架上,形成的渣壳将冷却,并与氧枪分离,脱落。
使用底吹搅拌技术的BOF转炉对溅渣技术的应用提出了新的要求。
在溅渣时炼钢工必须小心,不能使炉底的渣太多;氮气的流速必须足够高,以便将炉渣吹离炉底;另外要调整经过透气砖喷吹气体的压力、流量。
最终,随着炉衬寿命的提高,额外的操作需要增加辅助设备的使用寿命,如BoF炉的烟罩、钢包车和轨道等设备。
转炉溅渣护炉技术

转炉溅渣护炉技术的应用方法1.溅渣护炉的基本原理,是在转炉出完钢后加入调渣剂,使其中的Mg与炉渣产生化学反应,生成一系列高熔点物质,被通过氧枪系统喷出的高压氮气喷溅到炉衬的大部分区域或指定区域,粘附于炉衬内壁逐渐冷凝成固态的坚固保护渣层,并成为可消耗的耐材层。
转炉冶炼时,保护层可减轻高温气流及炉渣对炉衬的化学侵蚀和机械冲刷,以维护炉衬、提高炉龄并降低耐材包括喷补料等消耗。
氧气顶吹转炉溅渣护炉是在转炉出钢后将炉体保持直立位置,利用顶吹氧枪向炉内喷射高压氮气(1. 0MPa) ,将炉渣喷溅在炉衬上。
渣粒是以很大冲击力粘附到炉衬上,与炉壁结合的相当牢固,可以有效地阻止炉渣对炉衬的侵蚀。
复吹转炉溅渣护炉是将顶吹和底吹均切换成氮气,从上、下不同方向吹向转炉内炉渣,将炉渣溅起粘结在炉衬上以实现保护炉衬的目的。
溅渣护炉充分利用了转炉终渣并采用氮气作为喷吹动力,在转炉技术上是一个大的进步,它比干法喷补、火焰喷补、人工砌砖等方法更合理,其既能抑制炉衬砖表面的氧化脱碳,又能减轻高温渣对炉砖的侵蚀冲刷,从而保护炉衬砖,降低耐火材料蚀损速度,减少喷补材料消耗,减轻工人劳动强度,提高炉衬使用寿命,提高转炉作业率,减少操作费用,而且不需大量投资,较好地解决了炼钢生产中生产率与生产成本的矛盾。
因此,转炉溅渣护炉技术与复吹炼钢技术被并列为转炉炼钢的2项重大新技术。
2 溅渣护炉主要工艺因素2. 1 合理选择炉渣并进行终渣控制炉渣选择着重是选择合理的渣相熔点。
影响炉渣熔点的物质主要有FeO、MgO和炉渣碱度。
渣相熔点高可提高溅渣层在炉衬的停留时间,提高溅渣效果,减少溅渣频率,实现多炉一溅目标。
由于FeO易与CaO和MnO等形成低熔点物质,并由MgO和FeO的二元系相图可以看出,提高MgO的含量可减少FeO相应产生的低熔点物质数量,有利于炉渣熔点的提高。
从溅渣护炉的角度分析,希望碱度高一点,这样转炉终渣C2 S 及C3 S之和可以达到70%~75%。
转炉溅渣护炉技术
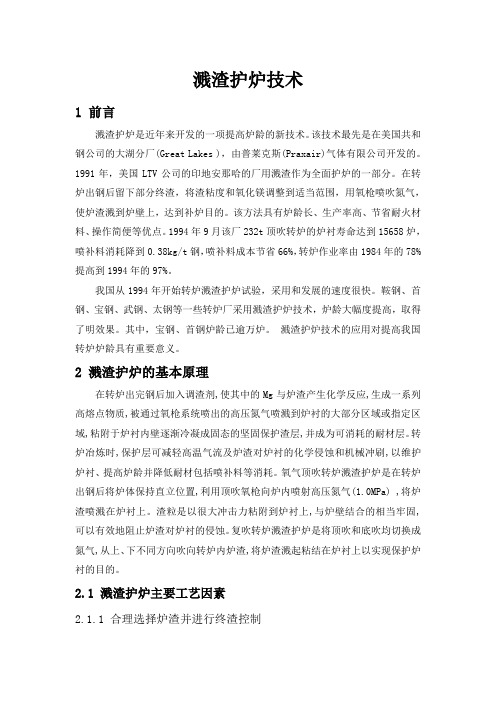
溅渣护炉技术1 前言溅渣护炉是近年来开发的一项提高炉龄的新技术。
该技术最先是在美国共和钢公司的大湖分厂(Great Lakes ),由普莱克斯(Praxair)气体有限公司开发的。
1991年,美国LTV公司的印地安那哈的厂用溅渣作为全面护炉的一部分。
在转炉出钢后留下部分终渣,将渣粘度和氧化镁调整到适当范围,用氧枪喷吹氮气,使炉渣溅到炉壁上,达到补炉目的。
该方法具有炉龄长、生产率高、节省耐火材料、操作简便等优点。
1994年9月该厂232t顶吹转炉的炉衬寿命达到15658炉,喷补料消耗降到0.38kg/t钢,喷补料成本节省66%,转炉作业率由1984年的78%提高到1994年的97%。
我国从1994年开始转炉溅渣护炉试验,采用和发展的速度很快。
鞍钢、首钢、宝钢、武钢、太钢等一些转炉厂采用溅渣护炉技术,炉龄大幅度提高,取得了明效果。
其中,宝钢、首钢炉龄已逾万炉。
溅渣护炉技术的应用对提高我国转炉炉龄具有重要意义。
2 溅渣护炉的基本原理在转炉出完钢后加入调渣剂,使其中的Mg与炉渣产生化学反应,生成一系列高熔点物质,被通过氧枪系统喷出的高压氮气喷溅到炉衬的大部分区域或指定区域,粘附于炉衬内壁逐渐冷凝成固态的坚固保护渣层,并成为可消耗的耐材层。
转炉冶炼时,保护层可减轻高温气流及炉渣对炉衬的化学侵蚀和机械冲刷,以维护炉衬、提高炉龄并降低耐材包括喷补料等消耗。
氧气顶吹转炉溅渣护炉是在转炉出钢后将炉体保持直立位置,利用顶吹氧枪向炉内喷射高压氮气(1.0MPa) ,将炉渣喷溅在炉衬上。
渣粒是以很大冲击力粘附到炉衬上,与炉壁结合的相当牢固,可以有效地阻止炉渣对炉衬的侵蚀。
复吹转炉溅渣护炉是将顶吹和底吹均切换成氮气,从上、下不同方向吹向转炉内炉渣,将炉渣溅起粘结在炉衬上以实现保护炉衬的目的。
2.1 溅渣护炉主要工艺因素2.1.1 合理选择炉渣并进行终渣控制炉渣选择着重是选择合理的渣相熔点。
影响炉渣熔点的物质主要有FeO、MgO 和炉渣碱度。
转炉溅渣护炉的工艺原理与实际应用_胡勋

摘要:本文简要介绍了转炉溅渣护炉的工艺原理和总结了实际应用中几个例如氮气喷吹参数,设备维护等关键因素。
关键词:转炉溅渣护炉工艺原理应用为了提高转炉炉龄,降低生产成本,减轻工人劳动强度,炼钢工作者采取了许多方法例如改善耐火材料质量,采取有效的喷补技术等。
这些措施对提高炉龄均起到了积极的作用使转炉炉龄有了一定程度的提高,但是随着炼钢技术的发展,炼钢工作者对炉渣和炉衬侵蚀机理的进一步研究,上世纪九十年代初美国LTV 公司率先开发出了溅渣护炉技术,通过近几年国内外实践得出溅渣护炉技术对炉衬维护有着喷补,贴补不可比拟的效果。
可以说溅渣护炉技术是转炉炉衬维护的又一大进步。
一.溅渣护炉的工艺原理1总述溅渣护炉是指在转炉吹炼结束出钢后,将转炉内留渣的粘度和氧化镁含量调整到合适的范围,用转炉系统原有的氧枪或专用氧枪向高氧化镁含量高粘度的炉渣喷吹一定压力和流量的氮气,将粘渣吹溅到炉衬上,使炉渣全面地炉衬上涂挂,冷却,凝固成一层炉渣质的保护层,避免了下一炉冶炼时钢水及炉渣直接和炉衬接触,从而达到减缓炉衬耐火材料层的蚀损,延长转炉炉龄的效果。
经过过国内外许多钢厂结合自己本厂的资源,工艺特点,进行开发应用证明溅渣护炉工艺对提高转炉炉龄和降低耐火材料消耗的效果非常显著,转炉炉龄在采用溅渣护炉后都有成倍的提高。
2溅渣层保护炉衬机理溅渣护炉的微观过程就是:高速氮气由喷枪喷溅到炉渣液面上,炉渣在氮气的巨大剪切力作用下迅速微粒化,微粒获得动能离开液体渣系向各个方向飞溅,以不同角度(高度)打在炉衬上。
微粒在形成,飞溅,粘结过程中不断被氮气冷却,最后在炉衬上粘附,固化,反应而形成一层炉渣的固体层覆盖住炉衬,从而减小炉衬的侵蚀,延长了炉衬的寿命。
2.1液态炉渣对炉衬的侵蚀机理炉渣对Mg-C 砖的侵蚀过程是:渣中(FeO)扩散到炉衬—渣界面,并与炉衬中的C 发生氧化还原反应而析出单质铁,同时对砖脱C 形成孔隙,铁单质进入炉渣,炉渣渗入孔隙与MgO 生成FeO ·MgO 固熔体进入渣中。
转炉炼钢工艺(溅渣护炉)

溅渣护炉的负面影响
吹炼终点[%C] ·[%O]积随炉龄变化情 吹炼终点 积随炉龄变化情 况
关于经济炉龄的问题
生产率、 生产率、成本与炉龄关系
溅渣护炉的优点
大幅度降低耐材消耗; 大大提高转炉作业率,达到高效增产目的; 投资回报率高; 溅渣护炉综合效益每吨钢约为2~10元。
溅渣护炉的负面影响
底吹透气砖覆盖渣层厚度与吹炼终点[%C] ·[%O]积的关 底吹透气砖覆盖渣层厚度与吹炼终点 积的关 系
溅渣护炉的负面影响
底吹透气砖覆盖渣层厚度与吹炼终点[%C] ·[%O]积的关 底吹透气砖覆盖渣层厚度与吹炼终点 积的关 系
炉渣粘度的控制
过低的炉渣粘度有利溅渣的操作,即易溅起、挂 渣且均匀,但由于渣层过薄,会在摇炉时挂渣流 落; 而粘度过大,溅渣效果差,耳轴!渣线处不易溅到, 且炉底易上涨,炉膛变形,所以粘度需要根据实 际情况合理调整; 炉渣过热度增高,粘度下降。
溅渣操作参数控制
为了在尽可能短的时间内将炉渣均匀喷 敷在整个炉衬表面而形成有足够厚度的 致密溅渣层。必须控制好溅渣操作手段, 即根据炉形尺寸,来控制喷吹N2气压力 和流量、枪位和喷枪结构尺寸等喷溅参 数。
其它参数
喷溅时间:通常为2.5~4min; 喷枪夹角:许多厂家的经验表明采用12 度夹角比较理想。
需要采取的其它措施
炉衬材质不能因实行溅渣护炉技术而降 低,对使用镁碳砖而言,其碳含量应控 制为下限; 控制和降低终渣FeO含量; FeO 合理调整终渣MgO含量; 提高溅渣层熔化性温度,降低炉渣过热 度; 降低出钢温度。
炼钢转炉溅渣护炉技术的应用与实践

炼钢转炉溅渣护炉技术的应用与实践介紹了炼钢转炉溅渣护炉技术的主要工艺参数,本钢集团北营炼钢厂在实际应用中遇到的问题。
为稳定氮气吹溅的运行现状,提高使用精度,自主创新了溅渣氮气智能管理系统技术,实现了优化溅渣工艺,缩短溅渣时长,降低溅渣氮气消耗,达到国内先进水平。
在一定程度上减轻了高温渣对炉衬砖的侵蚀冲刷,降了低耐火材料损耗速度,同时减轻工人劳动强度,提高炉衬使用寿命,提高转炉作业率,降低生产成本。
标签:溅渣;炉衬;氮气;挂渣引言转炉溅渣护炉技术是多年以来用于保护转炉提高炉龄的一项技术。
我国自90年代开始着手研发适应国情的转炉溅渣护炉工艺。
溅渣护炉技术就是将高压氮气通过喷枪喷出,渣通过喷射撞击区的孔穴外侧喷溅,并吸附到转炉炉衬上面从而形成一层渣层,这样可以对下一炉冶炼起到保护炉衬的作用。
转炉终渣不仅可以满足冶炼过程的要求,还应该符合溅渣护炉的条件,也就是说炉渣应易于喷溅到炉衬上,且溅到炉衬上的炉渣能很好地与之结合,所溅的炉渣应具有一定的耐火与抗高温侵蚀能力[1]。
近年来,节能环保与提质增效的工作要求越来越严格。
因此,研究溅渣护炉工艺中影响溅渣层寿命的主要因素,并在溅渣护炉工艺中进行量化控制,实现溅渣护炉工艺的科学量化,这些正是现代炼钢科技工作者需要着手解决的问题。
1溅渣的重要工艺参数1.1渣成分转炉一般都使用镁碳砖作为它的炉衬,减少炉衬侵蚀的重点就在于提高渣中氧化镁含量。
当渣中氧化镁的含量接近饱和时,炉衬中氧化镁的溶解量就很少,也就提高了炉衬的寿命。
炉渣碱度也是影响渣中氧化镁含量的重要因素,如果终渣碱度为三左右时,氧化镁含量则在百分之八左右就能使氧化镁达到炮和。
所以国内各种外转炉溅渣的氧化镁含量一般控制在百分之八到十四。
渣中氧化铁含量的高低严重影响着炉衬侵蚀和溅渣效果。
渣中氧化铁的矿物多为低熔点铁酸盐,熔点远远低于出钢温度,且氧化铁含量越高,铁酸盐也随之就越多,渣的流动性也就越好,造成对炉衬侵蚀作用加大且不容易附着在炉衬上。
鞍钢转炉溅渣护炉技术的应用
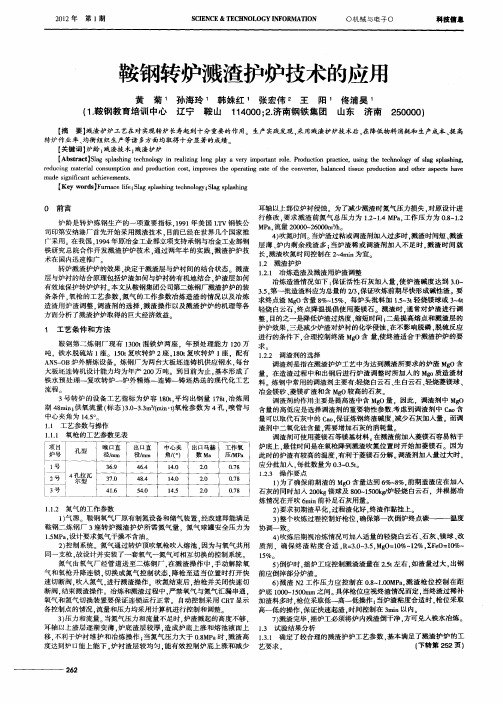
【 yw rsFrae i ;l lhn cnl yS gs a i Ke od]unc leS gs a i t ho g ;l l h g f a p s ge o a p s n
0 前 言
炉龄是转 炉炼钢 生产的一项 重要指标 .9 1 19 年美 国 I l 钢铁公 v 司印第安纳港厂首先开始采用溅渣技术 . 前 已经 在世界几个 国家推 目 广采用 。 在我国 .9 4 19 年原冶金 工业部 立项支持 承钢 与冶金 工业部钢 铁研究 总院合作 开发溅渣 护炉技 术 。 通过两年半 的实践 . 溅渣护炉技 术在国内迅速推广 转炉溅渣护炉 的效果 , 决定 于溅渣层与炉衬 间的结合状态 。溅 渣 层与炉衬的结合原理包括炉渣如何 与炉衬砖有机 地结合 . 炉渣层 如何 有效地保护转炉炉衬 。 本文从鞍钢集 团公 司第二炼钢厂溅渣 护炉 的装 备条件 . 氧枪 的工艺参数 . 氮气 的工作参数冶炼 造渣 的情 况 以及冶炼 造 渣用炉渣调整 . 调渣剂 的选择 . 溅渣操作 以及 溅渣护炉 的机理等各 方 面分析了溅渣护炉取得 的巨大经济效益 耳轴 以上部位炉衬侵蚀 。为 了减少溅渣时氮气压力损 失 . 对原设计进 行修 改 . 要求 溅渣前 氮气总 压力为 1 . M a 工作 压力为 O . . 1 P. 2 4 . 1 8 2
21 0 2年
第1 期
S I N E&T C NO O CE C E H L GYI F R T O N O MA I N
o机械 与电子0
科技信息
鞍钢转炉溅渣护炉技术的应用
黄 菊 孙海 玲 韩 姝 红 , 张 宏伟 2 王 阳 , 佟浦 昊 (. 1 鞍钢教育培训 中心 辽宁 鞍 山 1 4 0 ;. 0 0 2济南钢铁集团 山东 济南 1
转炉渣罐喷涂料的研制与使用总结材料

转炉渣罐喷涂料的研制与使用总结报告一、前言90t转炉投产后,转炉渣直接用8m3渣罐运往渣场处理,为便于翻渣,提高返罐率,稳定转炉炼钢的生产,有效地减少渣罐破损现象,降低生产成本;同时渣罐喷涂料是一种需长期消耗的新材料,长期从外地采购,价格较高,运输也不方便。
为此,特成立喷涂料研制与使用课题组。
课题组从五月底开始着手研制,六月份进行实验室试验,七月份在三炼钢15t转炉上进行工艺性试验,九月份在90t转炉上正式使用,现总结如下:二、试验目的及要求本次试验研制的喷涂料的使用温度是1200-1400℃,主要是防止转炉液态渣及残余钢水粘住渣罐内壁而使渣罐粘死报废,并且自动翻罐,顺利生产,因而要求喷涂料抗渣性能好,不粘渣;耐高温性强;抗热震稳定性好;抗剥落性好;施工性能好,48小时后不沉淀分层。
渣罐喷涂料的反应机理是:喷涂料中的白云石-在高温下分解产生CO2气体,反应方程式为:MgCO3.nCaCO3—→MgO+nCaO+(n-1)CO2↑;在940℃时CO2全部排出,白云石成为MgO和CaO的混合物。
CO2气体使涂层结构疏松,隔热性增强,热震稳定性增强,使用中不易剥落;同时由于涂料中石墨对渣的不浸润性,有效阻止了渣中Fe2O3、SiO2及Al2O3与涂料中MgO、CaO的进一步反应;由于反应产物溶点较低,结构中出现一定量的液相,有助于涂料中石灰与方镁石晶粒的生长与长大,加速涂料的烧结,在最表层形成一层含有大量高溶点物(CaO与MgO)的组织结构,阻止渣进一步侵蚀。
三、试验研制情况喷涂料研制是在合理利用本地产的廉价主体原料的基础上,保证颗粒的目数,按一定的配方,加入有机和无机复合结合剂和其它添加剂搅拌而成。
具体试验过程如下:1.信息搜集:五月底对武钢二炼钢、三炼钢渣罐喷涂料进调查。
喷涂料的技术指标已基本清楚,它是采用耐高温无机化合物配以适当的胶粘剂、添加剂充分乳化而成的水乳液。
使用效果较好,自动翻罐率在90%以上,价格为850元/t。
溅渣护炉技术的应用_刘玉敏
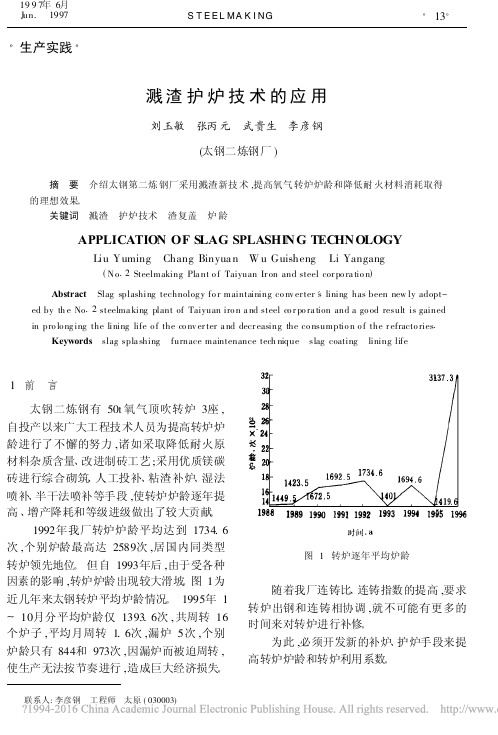
( MgO )含量保持在 6% ~ 12% ,加入菱镁球 团矿来提高 ( M gO)含量。 3. 5. 3 炉渣粘度
炉渣粘度大 , 渣稠不易溅起 ,附着力差。 粘度小 ,渣稀 ,溅渣覆盖较易 ,但覆盖层较薄 , 摇炉有挂渣流落现象 ,需加渣料调整。
加造渣剂调整炉渣 ,白云石≤ 300kg ,菱 镁矿球团≤ 200kg ,否则有不熔和扒炉底现象。
蚀速度明显降低 ,按目前实行的三段法溅渣 操作 (前期不溅 ,中期间隔溅 ,后期炉炉溅 ) , 2 号、 3号转炉第 295炉役的最大平均过程浸 蚀速度只有 0. 095mm /炉左右 , 与不采用溅 渣护炉工艺相比只有其三分之一。 从而使炉 龄大幅度提高 ,最高炉龄达到 5492次 ,平均 炉龄达到 3137次 ,见表 5。
重量 ,比较了溅渣与未溅渣之间的造渣量和 残余倒渣量 ,得出不同溅渣时间下的溅渣量 见表 4。用 2. 5~ 3. 5min的时间溅渣后 ,附着 在炉壁上的炉渣重量约 2t 左右。
实际上在后期炉衬砖达到一定厚度时坚
持炉炉溅渣其浸蚀速度更小 ,几乎未浸蚀炉 衬砖 ,使砖衬达到平衡厚度。 3. 4 溅渣护炉后炉形浸蚀均匀
单 ,劳动强度低。 ( 2)利用转炉剩余的渣和氮气 ,成本低。 ( 3) 每次只 需 2min30s~ 3min30s,不 影
响正常生产秩序。 ( 4)覆盖面积完全 ,整个炉壁都可覆盖 ,
挂渣效果明显。 ( 5)炉膛温度稳定 ,炉衬砖无急冷急热变
化。
( 6)对新旧炉衬都易于附着 ,加强了对新 炉衬的补炉效果。 2. 2. 3 溅渣方法
出完钢将炉子摇正 ,视渣稠稀 ,添加适当 的调渣料 ,调整渣子粘度 ,将氧枪降至下极 限 ,用装在操作盘上的切换装置开启氮气 ,溅 2min30s至 3mi n提枪 ,倒掉剩余的渣 子 ,装 炉冶炼下一炉。
溅渣护炉的应用上交

转炉的溅渣护炉操作【摘要】介绍氧气顶吹转炉溅渣护炉的理论与实践,对溅渣操作过程中出现的喷枪结瘤、炉底上涨及钢液脱磷等问题作了探讨。
【关键词】溅渣枪口结瘤炉底上涨脱磷前言钢铁工业一直面临着一种压力,即在不增加投资的条件下,提高产量,降低成本。
最早由新日铁奥进等人于1981年开发的转炉溅渣护炉工艺(亦称强制涂层工艺),就是一项不需要大的投资,而且增加生产率,降低操作费用,提高炉龄的新技术。
溅渣护炉工艺的基本思想是在转炉出钢后,将终渣留在炉内,然后适当调整终渣成分(主要是MgO含量),然后高压氮气通过吹氧枪吹渣,使终渣溅起附在炉衬上(见图1),形成炉衬的保护层,从而减轻炼钢过程对炉衬的机械冲刷和化学侵蚀,达到保护炉衬,大幅度提高炉龄的目的。
图1 溅渣示意图溅渣护炉工艺是转炉补炉方法上的根本性突破,使转炉炉龄大幅度提高,美国LTV公司1991年开发应用这项新技术并在1994年获得成功,炉龄已突破20000炉,转炉作业率由1984年的78%提高到1994年的97%,北美国家转炉炉龄平均都在5000炉以上,有6个厂已超过10000炉。
我国炼钢界从1996年开发这项工作并应用在大、中、小型转炉上。
宝钢于1996年末引进了美国LTV公司的溅渣(MgO)控制等工艺,使炉龄从原来的3500~5000炉跃升到10000炉左右。
鞍钢第三炼钢厂180t复吹转炉溅渣后不更换底吹原件,炉龄从2000炉左右提高到5700炉以上。
太钢二炼钢50t转炉炉龄由不溅渣平均1419次提高到1996年平均3774次,最高炉龄达8580炉,拆炉时残砖仍有200mm左右。
马钢三炼钢50t转炉首次试验时在已见保险砖的情况下用溅渣护炉工艺又冶炼了800多炉,炉龄达到1800炉。
小型转炉方面,南京钢厂已达2500炉水平,莱芜、济南钢厂也已超过3000炉,首钢一炼钢30t转炉最高炉龄达3361炉,平均炉龄2200炉左右。
福建三明钢厂15t小转炉已达到6000~7000炉的水平。
转炉返回渣再利用技术的开发

42 前期 溢渣 加剧 .
发, 降低了转炉钢铁料消耗 0 8 g , . / 降低造渣料石 7 kt 灰 消耗 36k/ 降低 了炼 钢成 本 , 有 明显 的 直 接 . g, t 具 经济效 益 。
表 1 不 同 时段 钢 渣 成 分
收集 点 样本量/ C O% M O % S d F O% T e M O% P s S% 碱度 爪 a/ g/ i % e/ O F/ % n/ 2/ 0 % /
前期溢 渣
喷溅 渣
l 5
1 3
4 .9 1 . 1 .1 1.1 2 . 19 96 07 5 38 99 68 5 . 4
过 程 中未完 全溶 化 的小 颗粒 石灰 , 同时 还存 在喷 溅
收 。对转 炉前期 渣 、 喷溅渣 、 倒炉渣 和溅渣 后 的翻渣 严格 区分 , 后期 倒 炉 渣 和溅渣 后 翻渣 不直 接 返 回转
炉利用 , 是 闷渣 后外运 处理 。 而
收稿 日期 :0 10 — 5 2 1- 3 1
炉 冶 炼 前期 溢 渣 以及 带 金 属 较 多 的 喷溅 渣 进 行 筛 选、 集, 收 并返 炉 利用 , 少 了 因此造 成 的金 属损 失 减 和造 渣料 的浪 费 , 降低 了炼 钢成本 。
转 炉钢渣 按其在 冶炼过 程 中生产 的 时间段不 同
分为前 期溢渣 、 过程 喷溅渣 、 炉倒 炉渣 和溅 渣护 炉 转 后 的翻 渣 。为确 定 主要 的返 回渣 回收来 源 , 不 同 对 时间段产生 的钢渣进行取样分析 , 结果见 表 1 。
针对 上 述 问题 采 取 了 以下 改 进措 施 :) 高氧 1提
浅析转炉溅渣护炉技术的应用
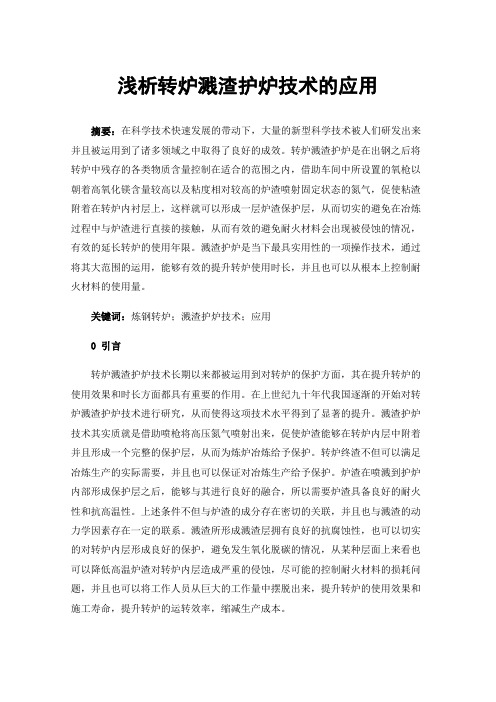
浅析转炉溅渣护炉技术的应用摘要:在科学技术快速发展的带动下,大量的新型科学技术被人们研发出来并且被运用到了诸多领域之中取得了良好的成效。
转炉溅渣护炉是在出钢之后将转炉中残存的各类物质含量控制在适合的范围之内,借助车间中所设置的氧枪以朝着高氧化镁含量较高以及粘度相对较高的炉渣喷射固定状态的氮气,促使粘渣附着在转炉内衬层上,这样就可以形成一层炉渣保护层,从而切实的避免在冶炼过程中与炉渣进行直接的接触,从而有效的避免耐火材料会出现被侵蚀的情况,有效的延长转炉的使用年限。
溅渣护炉是当下最具实用性的一项操作技术,通过将其大范围的运用,能够有效的提升转炉使用时长,并且也可以从根本上控制耐火材料的使用量。
关键词:炼钢转炉;溅渣护炉技术;应用0引言转炉溅渣护炉技术长期以来都被运用到对转炉的保护方面,其在提升转炉的使用效果和时长方面都具有重要的作用。
在上世纪九十年代我国逐渐的开始对转炉溅渣护炉技术进行研究,从而使得这项技术水平得到了显著的提升。
溅渣护炉技术其实质就是借助喷枪将高压氮气喷射出来,促使炉渣能够在转炉内层中附着并且形成一个完整的保护层,从而为炼炉冶炼给予保护。
转炉终渣不但可以满足冶炼生产的实际需要,并且也可以保证对冶炼生产给予保护。
炉渣在喷溅到护炉内部形成保护层之后,能够与其进行良好的融合,所以需要炉渣具备良好的耐火性和抗高温性。
上述条件不但与炉渣的成分存在密切的关联,并且也与溅渣的动力学因素存在一定的联系。
溅渣所形成溅渣层拥有良好的抗腐蚀性,也可以切实的对转炉内层形成良好的保护,避免发生氧化脱碳的情况,从某种层面上来看也可以降低高温炉渣对转炉内层造成严重的侵蚀,尽可能的控制耐火材料的损耗问题,并且也可以将工作人员从巨大的工作量中摆脱出来,提升转炉的使用效果和施工寿命,提升转炉的运转效率,缩减生产成本。
1溅渣护炉工艺的冶金因素及其优势就溅渣护炉工艺的实际操作流程来说,主要包括下面几个方面:第一,将钢水从转炉转移到大包中。
转炉溅渣护炉技术(朱绪龙)毕业论文
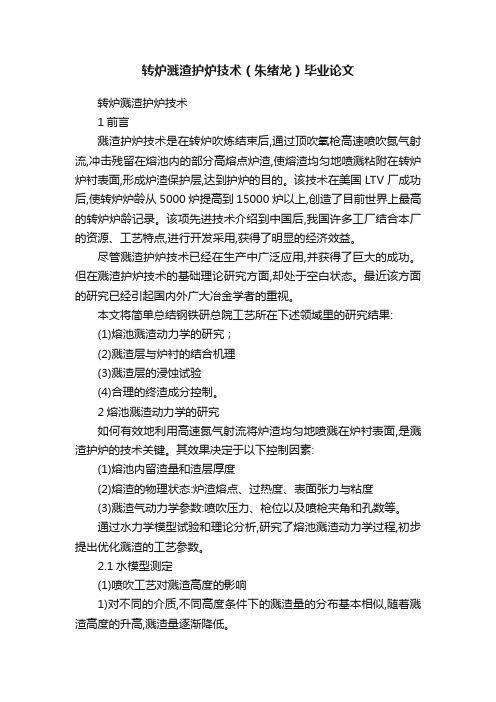
转炉溅渣护炉技术(朱绪龙)毕业论文转炉溅渣护炉技术1前言溅渣护炉技术是在转炉吹炼结束后,通过顶吹氧枪高速喷吹氮气射流,冲击残留在熔池内的部分高熔点炉渣,使熔渣均匀地喷溅粘附在转炉炉衬表面,形成炉渣保护层,达到护炉的目的。
该技术在美国LTV厂成功后,使转炉炉龄从5000炉提高到15000炉以上,创造了目前世界上最高的转炉炉龄记录。
该项先进技术介绍到中国后,我国许多工厂结合本厂的资源、工艺特点,进行开发采用,获得了明显的经济效益。
尽管溅渣护炉技术已经在生产中广泛应用,并获得了巨大的成功。
但在溅渣护炉技术的基础理论研究方面,却处于空白状态。
最近该方面的研究已经引起国内外广大冶金学者的重视。
本文将简单总结钢铁研总院工艺所在下述领域里的研究结果:(1)熔池溅渣动力学的研究;(2)溅渣层与炉衬的结合机理(3)溅渣层的浸蚀试验(4)合理的终渣成分控制。
2熔池溅渣动力学的研究如何有效地利用高速氮气射流将炉渣均匀地喷溅在炉衬表面,是溅渣护炉的技术关键。
其效果决定于以下控制因素:(1)熔池内留渣量和渣层厚度(2)熔渣的物理状态:炉渣熔点、过热度、表面张力与粘度(3)溅渣气动力学参数:喷吹压力、枪位以及喷枪夹角和孔数等。
通过水力学模型试验和理论分析,研究了熔池溅渣动力学过程,初步提出优化溅渣的工艺参数。
2.1水模型测定(1)喷吹工艺对溅渣高度的影响1)对不同的介质,不同高度条件下的溅渣量的分布基本相似,随着溅渣高度的升高,溅渣量逐渐降低。
2)当溅渣高度hs/D=1.0时,不同高度下的溅渣量的分布规律发生变化。
当hs/D≤l.0时,溅渣量的比例高达总渣量的30%~60%,随着高度的增加,溅渣量将迅速降低。
在hs/D≥1.0以后溅渣量随高度增加,溅渣量减少的速率降低。
在这一高度的范围内,溅渣量约占溅渣总量的0~20%。
由此推论,炉内溅渣存在两个反应区:当hs/D≤1.0时,溅渣以渣液面波动为主,溅渣量大,并随溅渣高度增加迅速降低。
转炉溅渣护炉工艺的研究与应用

16Metallurgical smelting冶金冶炼转炉溅渣护炉工艺的研究与应用朱元涛(山东石横特钢集团有限公司,山东 肥城 271612)摘 要:介绍了石横特钢集团有限公司炼钢车间通过优化转炉溅渣工艺,转炉炉体安全稳定运行,熔池未出现侵蚀扩径现象,炉壳温度稳定,影响钢产量增加,溅渣护炉效果明显,炉型稳定,大面料补炉砖消耗降低,取得明显经济及社会效益,具有很好的推广应用价值。
关键词:转炉;溅渣层中图分类号:TF748.2 文献标识码:A 文章编号:11-5004(2021)06-0016-2 收稿日期:2021-03作者简介:朱元涛,男,生于1975年,汉族,山东泰安人,本科,经济师,研究方向:冶金工程。
目前转炉实行炉炉溅渣工艺,在生产过程中会出现炉底波动大、炉帽过厚、熔池侵蚀严重等不利于转炉冶炼的现象,导致停炉换包时修补熔池侵蚀部位,停炉时间长,影响产能降低、补炉料消耗升高,同时炉型发生变化后,影响冶炼稳定性喷溅、溢渣严重。
为稳定炉型,缩短转炉停炉辅助时间,降低补炉料消耗等,一炼钢成立技术攻关小组,在改进溅渣层质量,优化氮气压力、流量与枪位,控制合理的留渣量等三方面进行技术优化,综合生产成本降低。
1 溅渣护炉工艺原理1.1 溅渣护炉分析初期渣对炉衬的侵蚀在转炉冶炼初期,首先是铁水中Si、Mn 的大量氧化,生成大量的SiO 2等,石灰的熔化速度较缓慢(石灰活性度低时更差),炉渣碱度的提高需要一个较长的过程,在低碱度阶段炉渣对炉衬的侵蚀较严重。
因为在酸性渣中,MgO 可以有很高的溶解度,加速了炉衬中MgO 的熔解速度。
因此,在初期加入白云石造渣,使渣中有一定的MgO 可以减轻对炉衬的化学侵蚀。
实际生产中,溅渣层为高熔点的C 2S 和MgO 结晶体,熔化温度较高。
由于冶炼初期温度较低,溅渣层为不明显熔化。
初期渣对溅渣层的侵蚀较弱,当渣中FeO 含量相同时,高钙渣的侵蚀速度明显高于高镁渣。
因此提高溅渣层的碱度或MgO 含量,均有利于减轻炉渣的侵蚀。
溅渣护炉技术在转炉上的应用

溅渣护炉技术在转炉上的应用
溅渣护炉技术是一项新兴的技术,它可以提高转炉的燃烧效率,减少对环境的影响。
溅渣护炉技术是通过把大量的液体或气体加到炉内,使溅射出来的渣滓变得更轻而易于把它带走而得以应用于转炉上。
这样可以大大提高转炉的燃烧效率,减少对环境的影响。
溅渣护炉技术的主要原理是在炉子内部加入溅射液体或气体,使溅射出来的渣滓变得更轻,而且更易于把它带走。
此外,溅渣护炉技术还可以改善炉子内部燃烧状态,提高燃烧效率,从而降低炉子本身的耗能。
溅渣护炉技术在转炉上的应用主要体现在以下几个方面:
1、降低转炉内部的温度:在转炉内部加入溅射液体或气体,使渣滓变得更轻,从而降低转炉内部的温度,提高转炉的燃烧效率。
2、减少对环境的污染:由于转炉内部的温度较低,因此溅渣护炉技术也可以减少对环境的污染。
3、改善转炉内部燃烧状态:在转炉内部加入溅射液体或气体后,可以改善转炉内部的燃烧状态,从而提高燃烧效率,减少渣滓的生成。
4、降低燃料的消耗:由于溅渣护炉技术可以提高转炉的燃烧效率,从而降低燃料的消耗,节省能源,降低成本。
总之,溅渣护炉技术可以有效提高转炉的燃烧效率,减少对环境的污染,节省能源,降低成本。
在转炉上应用溅渣护炉技术,将会带来很好的经济效益和社会效益。
转炉溅渣护炉与长寿复吹技术

我国自主研发的先进技术——转炉溅渣护炉与长寿复吹技术2010-5-19 9:21:39 来源:中国钢铁产业网信息中心编辑:王宝玉炉龄是转炉炼钢一项综合性技术指标。
提高炉龄不仅可以降低耐火材料消耗,提高作业率、降低生产成本,而且有利于均衡组织生产,促进生产的良性循环。
所以,大幅度提高转炉炉龄是钢铁企业始终追求的目标。
转炉炉衬工作在高温、高氧化性条件下,通常以0.2~0.8mm/炉的速度被侵蚀。
溅渣护炉是近年来开发的一项提高炉龄的新技术。
该技术是利用MgO含量达到饱和或过饱和的炼钢终点渣,通过高压氮气的吹溅,冷却凝固在炉衬表面上,形成一层高熔点的熔渣层,并与炉衬很好地粘结附着。
溅渣形成的溅渣层耐蚀性较好,可抑制炉衬砖表面的氧化脱碳,又能减轻高温渣对炉衬砖的侵蚀冲刷,从而保护炉衬砖,降低耐火材料损耗速度,减少喷补材料消耗,同时提高炉衬使用寿命,提高转炉作业率,降低生产成本。
与溅渣护炉技术紧密相连的问题是如何提高复吹率。
因为炉渣在炉底停留的时间越长,粘结在炉底的就越多,导致炉底上涨,这就可能堵塞底气喷孔,使转炉复吹效果变差。
所以,转炉溅渣后,如何实现全程复吹,提高底吹喷嘴的寿命是全世界钢厂急待解决的重大技术难题。
如果复吹元件寿命不能同步提高,使复吹比大幅度降低,就会使大部分炉役期内复吹转炉丧失复吹功能。
国外一些国家采用转炉溅渣护炉技术后,或牺牲复吹工艺(如美国);或牺牲溅渣技术,只保留复吹工艺(如日本、欧洲等国家),经济损失较大。
为了解决这一问题,我国国内转炉厂发明了炉渣蘑菇头保护底吹透气砖的先进技术,使底吹喷嘴的一次寿命与炉龄同步,并保证复吹比100%,已成功地解决了保持复吹转炉底吹供气元件寿命与转炉炉龄同步这一国际炼钢生产中的重大难题。
我国自主研发的转炉溅渣护炉与长寿复吹技术,完全适合于中国国情的各种转炉溅渣护炉作业,并且很好地解决了复吹问题,经广泛推广采用,已获得巨大的经济效益。
我国采用转炉溅渣护炉技术的8年里,炉龄发生了质的飞跃,与采用溅渣技术前相比,我国转炉龄提高了5-10倍,转炉炉龄已不是制约转炉生产能力发展的瓶颈。
转炉在冶炼低碳钢时的溅渣护炉技术

。
目前, 三炼钢用于炼钢的铁水成分见表 1 。
表 1 铁水成分 T ab 1 M olten iron composition
成分 含量 /% C 3 5~ 4 6 Si 0 30 ~ 0 80 Mn 0 25~ 0 50 P 0 06~ 0 10 S 0 002 ~ 0 030
效果。 3 1 2 适当调整装入制度 在冶炼低碳钢时, 终点碳含量较低 , 相应的转 炉热量比较富裕。为了平衡多余的热量 , 就要加入 大量 的 铁 矿石 用 于降 温。铁 矿石 中 含 有较 高 的 FeO, 大量的铁矿 石加 入炉 内, 加剧 了炉 衬的 侵 蚀。为了降低铁矿石的加入量, 可以适当地调整装 入制度, 增加废钢配比。在吹炼后期接近终点时, 尽量避免加入矿石调温。 3 1 3 适当降低拉碳枪位 在吹炼接近终点时 , 适当降低拉碳枪位 , 有利 于熔池的搅拌 , 促进钢渣间碳氧反应平衡, 使渣中 TF e 含量降低。 3 2 降低出钢温度 出钢温度是影响炉衬寿命的一个重要因素。转 炉后期溅渣层的蚀损一个重要原因是高温熔化。根 据统计, 出钢温度平均降低 1 , 转炉炉龄可以提 高 120 炉 。如低碳的 SPHC 等钢种 , 合金加入量 较少 , 出钢温降少, 出钢温度可以控 制在 1 630 左右。 3 3 淘汰萤石助熔剂 开发使用复合化渣剂 用萤石作助熔剂, 能够实现成渣快的目的, 但 是其资源少, 价格昂贵 , 其炼钢生成的氟化物排放 不仅会 造成 环境 污染 , 对炉 衬的侵 蚀也 非常 大。 2009 年开始, 济钢三炼钢开发应 用了一种复合化 渣剂。生产实践证明, 使用复合化渣剂 , 炉渣的成 渣速度快 , 对炉衬的侵蚀减小, 有利于提高转炉的 溅渣护炉质量和降低转炉吹损。 3 4 加强管理 , 减少泡炉 高温、高氧化性的钢水泡炉对转炉危害极大。 为了减少泡炉 , 炉前工要和调度室、装包工、渣车 工等及时联系和沟通, 以确定开吹时间 , 尽量减少 泡炉。
龙钢60t转炉喷溅返干预报考核系统的开发与应用

龙钢60t转炉喷溅返干预报考核系统的开发与应用发布时间:2023-03-21T08:03:36.793Z 来源:《科技新时代》2023年第1月1期作者:宋冰冯燕阮龙[导读] 本文介绍了喷溅返干预报系统在龙钢60t转炉的应用情况,该系统以音频化渣技术为核心宋冰冯燕阮龙陕西龙门钢铁有限公司炼钢厂陕西韩城 715400摘要:本文介绍了喷溅返干预报系统在龙钢60t转炉的应用情况,该系统以音频化渣技术为核心,结合炉前操作要求开发的一套集摇炉工参考和管理者监控于一体的炉前操作优化系统,系统的应用有效的改善了转炉冶炼过程的化渣效果,降低了喷溅率和返干率,提高了转炉一次拉碳率,经济效益显著。
关键词:音频化渣技术喷溅率返干率一次拉碳率1 前言在转炉炼钢中,炉渣的泡沫化程度直接影响着冶炼的进行,泡沫太多会引起喷溅,给操作带来困难,并导致铁损增加;泡沫渣太少会造成返干不利于脱P。
龙钢炼钢厂老区现有60t转炉4座,实际装入量铁水为42-47t,废钢5-12t。
由于铁水条件不稳定且炉容比较小,导致吹炼过程中炉渣化渣情况不稳定,经常出现喷溅或返干的现象。
这不仅让成本增加,还导致钢水质量和产量的降低,甚至给人员和设备带来很大的安全隐患。
为了提高冶炼操作水平,减少吹炼过程中喷溅和返干,降低钢铁料消耗,龙钢公司新上了喷溅返干预报系统。
该系统采用音频微机监控装置能真实地反映泡沫化程度,即渣面的位置,及时地为操作人员发出喷溅与返干预警,并能提前发出喷溅与返干报警,操作人员可根据计算机屏幕上的音强曲线及时采取措施控制返干和喷溅的发生。
该系统运行一年多以来,操作人员冶炼操作水平有了较大的提高,喷溅率和返干率明显降低,一次拉碳率大幅提升,降低了钢铁料消耗,给企业带来了巨大的经济效益。
2 系统设备组成喷溅返干预报考核系统以音频化渣技术为核心,由前端采音保护单元、信号处理单元、喷溅采集单元、画面处理显示单元、喷溅返干考核系统软件组成。
系统布置如图1所示:图1:系统布置图前端采音单元包括冷却水套、采音组件,此部分安装在转炉挡火墙外侧。
- 1、下载文档前请自行甄别文档内容的完整性,平台不提供额外的编辑、内容补充、找答案等附加服务。
- 2、"仅部分预览"的文档,不可在线预览部分如存在完整性等问题,可反馈申请退款(可完整预览的文档不适用该条件!)。
- 3、如文档侵犯您的权益,请联系客服反馈,我们会尽快为您处理(人工客服工作时间:9:00-18:30)。
・问题研究 Fra bibliotek问题 研 究 ・
.
转炉 喷溅 渣循 环利用技术 的开发与应用
颜景 春 邢 东方 赵 景泉 孙 惠玲
( 山 东钢 铁股 份有 限 公 司菜 芜分公 司炼 钢厂 菜 芜
【 摘
2 7 1 1 0 4 )
要】 通过枪位 、 渣料 、 氧压控制 有效解决 了转炉 台 炼前期 喷溅渣循环利 用造 成的喷溅 , 为转炉清洁生 喷溅 渣 循环利用
产 探 索 出新 途 径 。
【 关键词】 转炉
De v e l o p me n t a n d Ap p l i c a t i o n o f Ci r c u l a t i n g Ut i l i z a t i o n Te c h n o l o g y o f
3 . 2 转 炉冶 炼前期 喷 溅渣循 环利 用的喷 溅 与控制
Co nv e r t e r s l ag s pl a s hi n g
Y AN J i n - c h u n , XI NG D o n g — f a n g , Z HA0 J i n g - q u a n , S UN Hu i — l i n g
( S t e e l m a k i n g P l a n t o f S b a n g a n gL a i w u C o m p a n y , L a i w u 2 7 1 1 0 4 )
2 工艺 流程及 装 备水 平
工艺流程为 : 铁 水一 脱 硫 站一 混 铁 炉 一 转 炉 一L F ( 吹氩 ) 连铸。 山钢 股份 有 限公 司莱 芜 分公 司炼 钢 厂 共 有年 处理 4 0 0 万t 纯镁 粒 脱 硫 设 备 一 套 , 6 0 0 t 混铁炉 2 座, 5 0 t 顶 吹转 炉 3 座, 6 0 t 顶 吹转 炉 1 座, 配套 L F 精
【 A b s t r a c t 】 T h e s p l a s h i n g r e s u l t e d f r o m s l a g s p l a s h i n g c i r c u l a t i n g u t i l i z a t i o n i n t h e p r e v i o u s p e r i -
一
∑F e O S i O C a O M g O A 1 O S Mn O P z O s T i O R
1 号 2 4 . 1 8 1 9 . 9 7 3 7 . 9 1 7 . 3 7 1 . 4 3 0 . 1 5 6 3 . 3 1 0 . 9 3 0 . 7 9 1 . 9
开吹时打火滞后 , 严重时打火 困难 , 处理不当会造 成“ 吃枪” 引发炉 内进水事故 , 成为安全生产隐患 。 打 火 滞 后 主 要 原 因是 加 入 喷溅 渣 后 , 铁 水 表 面被厚渣层覆盖所致 , 主 要 采 取 的 应 对 措 施 是 适 当提高 开 吹 氧压 , 在开 氧 点开 氧 后 , 迅 速 降枪 至 正 常 吹炼 枪 位 , 或者 在 开 氧前 先 开 氮气 冲渣 , 然 后 开 氧 吹 炼 。若 出现 打 不 着 火 的情 况 , 可 以适 当前 后 摇炉 1 5 。 ~3 0 。 , 然 后按 照 上述 方法 开 吹 。
0 d o f c o n v e r t e r s me l t i ng i s e f f e c t i v e l y s o l v e d t h r o ug h c o n t r o l l i ng l a n c e p o s i t i o n , s l a g ma t e r i a l a n d o x y g e n p r e s s u r e . Th i s p r o v i d e s a n e w wa y f o r c o n v e r t e r c l e a n a n d p r o d u c t i o n.
2 号 1 7 . 1 1 7 . 0 7 4 3 . 3 8 . 0 4 1 . 4 8 0 . 1 4 2 2 . 3 4 0 . 9 5 0 . 5 1 2 . 5 4
平均 2 0 . 6 4 1 8 . 5 2 4 0 . 6 0 5 7 . 7 0 5 1 . 4 5 5 0 . 1 4 9 2 . 8 2 5 0 . 9 4 0 . 6 5 2 . 2 2
【 Ke y w o r d s 】 C o n v e r t e r , s l a g s p l a s h i n g , c i r c u l a t i n g u t i l i z a t i o n
1 前 言
表1 转炉冶炼前期喷溅渣主要化学成表 %
转炉冶炼喷溅渣循环利用就是将转炉冶炼过 程 中前 期 喷溅 出 的富 含 ∑F e O( 氧化亚铁 ) 并 具 有 定 碱 度 的炉 渣 返 回炉 内。取 代 部分 冷 料 和石 灰 的 综合 利 用技 术 , 该 技 术 在 莱 钢 自主 开 发 “ 铁水+ 矿石 ” 冶炼 工 艺 的基 础 上进 一 步 降低 了钢铁 料 、 石 灰及 耐材的消耗 , 进一 步减轻 因大批量使用矿石 带来 的环境 压 力 , 并 取得 可 观 的经 济 效 益 , 为转 炉 清洁生产走循环经济之路探索出新途径。