转炉留渣操作技术
莱钢60t转炉单渣留渣操作实践

莱钢60t转炉单渣留渣操作实践安全规律,因此一直没有得到大范围推广应用。
但氧气转炉留渣操作能够充分利用前炉钢终点炉渣的热量、碱度和氧化性,大幅降低渣料消耗,在转炉吹炼初期可以快速造就高碱度氧化渣,有利于提高生产效率,并具有显著的经济效益,特别在铁水资源不足的钢厂效益更加突出。
因此各钢厂一直在进行生产试验,以求实现留渣操作的稳定。
留渣操作主要有两方面的危害:一是兑铁时碳氧剧烈反应发生大喷;二是转炉开吹打不着火,转炉烟道内氧气和一氧化碳达到爆炸极限,产生烟道爆炸事故。
1.1兑铁大喷的原因及预防即温度低于1507℃时,铁水和上一炉的炉渣接触,首先是硅的氧化(但也不排除有碳的氧化,因为铁水中含碳量较高),也就限制了碳的激烈氧化。
另外,也可根据不同温度下各种纯氧化物的分解压力找出碳和硅优先氧化的温度。
由氧化物标准生成自由焓的变化与温度的关系可知:SiO2分解壓力曲线与CO分解压力曲线相交的对应温度为1530℃。
当t小于1530℃时,[Si]先于[C]被氧化;当t大于1530℃时则[C]先于[Si]被氧化。
既便是在热力学满足式(3)的情况下,反应也不一定进行或进行的很缓慢而不会造成喷溅,这是由复杂的动力学因素决定的。
上式表明,化学反应速度随温度升高而加快,也就是说温度越高发生喷溅的概率越大。
反之,化学反应速度降低,发生喷溅的概率越小。
从热力学和动力学的分析都可以看出,降低炉渣温度是避免出现兑铁大喷的关键因素,目前转炉大部分实现了溅渣护炉,溅渣后炉渣温度均低于1500℃。
可以说留渣操作的条件已经具备。
同时在溅渣操作时,通过溅干炉渣,防止有液态炉渣,溅渣终点由炉长亲自查看炉渣状态,溅渣时加入一部分石灰等渣料等措施,可以确保兑铁时不出现大喷危害。
1.2 开吹打不着火的原因及预防开吹打不着火主要是由于留渣操作炉渣、加入的废钢带入的渣钢以及铁水带入的铁水渣量大,漂浮在表面,导致氧气流股不能够直接穿透渣层,发生反应。
开吹打火时间超过40s,则前期氧气流股一部分冲击炉渣表面,造成(FeO)聚集,一部分进入烟道内,造成烟道内氧气含量大于2%。
转炉石灰石造渣留渣操作工艺实践分析
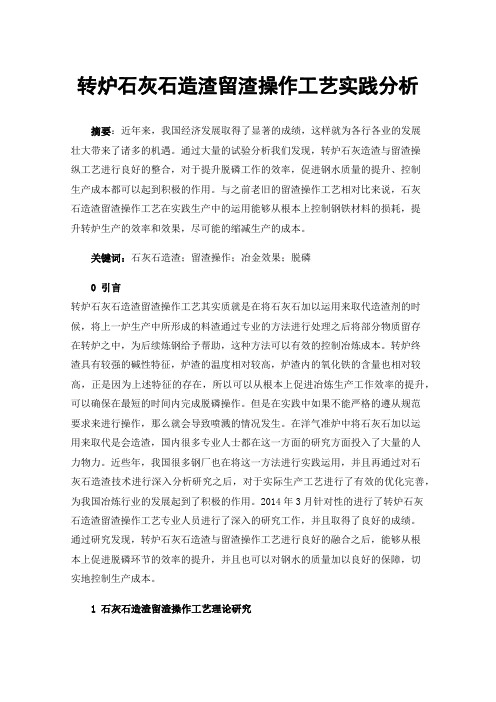
转炉石灰石造渣留渣操作工艺实践分析摘要:近年来,我国经济发展取得了显著的成绩,这样就为各行各业的发展壮大带来了诸多的机遇。
通过大量的试验分析我们发现,转炉石灰造渣与留渣操纵工艺进行良好的整合,对于提升脱磷工作的效率,促进钢水质量的提升、控制生产成本都可以起到积极的作用。
与之前老旧的留渣操作工艺相对比来说,石灰石造渣留渣操作工艺在实践生产中的运用能够从根本上控制钢铁材料的损耗,提升转炉生产的效率和效果,尽可能的缩减生产的成本。
关键词:石灰石造渣;留渣操作;冶金效果;脱磷0 引言转炉石灰石造渣留渣操作工艺其实质就是在将石灰石加以运用来取代造渣剂的时候,将上一炉生产中所形成的料渣通过专业的方法进行处理之后将部分物质留存在转炉之中,为后续炼钢给予帮助,这种方法可以有效的控制冶炼成本。
转炉终渣具有较强的碱性特征,炉渣的温度相对较高,炉渣内的氧化铁的含量也相对较高,正是因为上述特征的存在,所以可以从根本上促进冶炼生产工作效率的提升,可以确保在最短的时间内完成脱磷操作。
但是在实践中如果不能严格的遵从规范要求来进行操作,那么就会导致喷溅的情况发生。
在洋气准炉中将石灰石加以运用来取代是会造渣,国内很多专业人士都在这一方面的研究方面投入了大量的人力物力。
近些年,我国很多钢厂也在将这一方法进行实践运用,并且再通过对石灰石造渣技术进行深入分析研究之后,对于实际生产工艺进行了有效的优化完善,为我国冶炼行业的发展起到了积极的作用。
2014年3月针对性的进行了转炉石灰石造渣留渣操作工艺专业人员进行了深入的研究工作,并且取得了良好的成绩。
通过研究发现,转炉石灰石造渣与留渣操作工艺进行良好的融合之后,能够从根本上促进脱磷环节的效率的提升,并且也可以对钢水的质量加以良好的保障,切实地控制生产成本。
1石灰石造渣留渣操作工艺理论研究1.1转炉概况及工艺路线石钢的60t顶底复吹转炉炉容比为0.82,氧枪采用Φ159mm四孔拉瓦尔型,在整个行业快速发展的过程中,行业内的竞争形势也越发的严峻,以往老旧的生产工艺模式已经无法再满足生产的需要了,所以还需要我们进一步的结合行业发展趋势来进行优化和完善,在对脱磷的效果加以根本保障的基础上,尽可能的控制冶炼的成本。
转炉冶炼操作技巧

吹炼过程发现喷溅迹象,立即加少量白灰压喷,若喷溅大得不到缓和必须及时提枪喊开周围人员,缓慢倒渣。
然后加入≥3吨白灰稠渣,并先降枪后开氧。
留渣操作,因为所留渣中有大量的氧化铁,应该不会容易返干。
但是,因为吹炼前期有大量氧化铁,前期为防喷溅应该低枪位操作,如果中期枪位不做改变,提高会出现返干炉渣返干:是吹炼中期由于碳氧剧烈反应,炉渣中(FeO)降低,致使炉渣中2CaO.SiO2、CaO等高熔点的物质析出,炉渣变稠,这一现象称之为炉渣返干。
在吹炼过程中,因氧压高,枪位过低,尤其是在碳氧化激烈的中期,(TFe)含量低导致熔渣高熔点矿物的析出,造成熔渣黏度增加,不能覆盖金属液面的现象。
TFe即为全铁的意思。
上面说的是一部分,实际上Si,Mn反应期结束后..说说办法吧:提提枪,让FeO上来点...返干一般在冶炼中期(碳氧化期)的后半阶段发生,是化渣不良的一种特殊表现形式。
冶炼中期(碳氧化期)的后半阶段正常火焰特征是:白亮,刺眼,柔软性稍微变差。
但发生返干的火焰现象特征为:由于气体循环不正常而使正常的火焰(有规律,柔和的一伸一缩)变的直窜,硬直,火焰不出烟罩;同时由于返干炉渣结块成团未能化好,氧流冲击到未化的炉渣上面而发出刺耳的怪声;又是还有看到金属颗粒喷出。
有以上现象发生,说明炉渣已经返干。
产生返干的处理方法:1)补加一定量的氧化铁皮,增加FeO的浓度含量;2)适当提高氧枪。
提高枪位使冲击面积相对扩大,也使FeO的浓度含量增加;3)适当提高氧枪的同时,适当调低吹炼氧亚,是吹炼时间延长,使FeO的浓度含量增加,达到改善炉渣流动性的目的,改善炉渣状况,达到消除返干的目的。
吹炼过程中怎样预防爆发性喷溅?根据爆发性喷溅产生的原因,可以从以下几方面预防:(1)控制好熔池温度。
前期温度不要过低,中后期温度不要过高,均匀升温,碳氧反应得以均衡的进行;严禁突然冷却熔池,消除爆发性碳氧反应的条件。
(2)控制(TFe)不出现聚积现象,以避免熔渣过分发泡或引起爆发性的碳氧反应。
8-转炉“留渣-双渣”少渣炼钢工艺实践
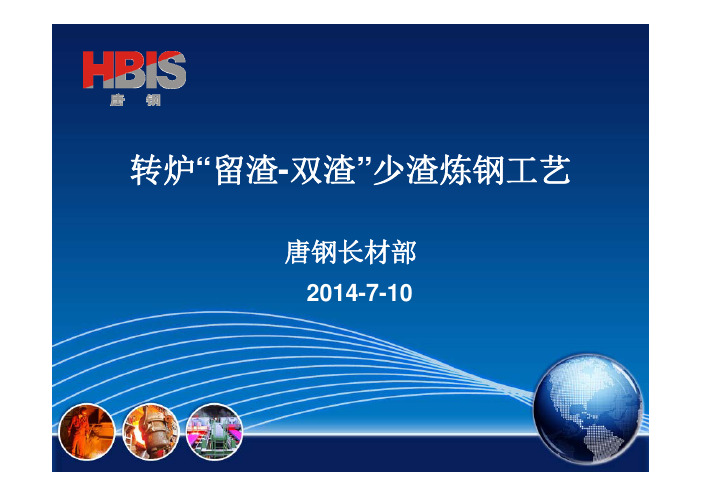
“留渣-双渣”工艺示意图
3.转炉脱磷影响因素
3.脱磷的基本原理
2[P]+5(FeO)+4(CaO)=4CaO·P2O5+5[Fe]
a 4CaO P2 O 5 a a
2 p 5 F eO
Kp
a
4 C aO
% 4CaO P2 O 5 4CaO P O 4 5 4 % P 2 f P2 % F e O 5 F e O % CaO C aO
演变:首钢公司从2011年开始,在首钢首秦和迁钢分别连续试验单
转炉“留渣-双渣”操作,取得较好的效果,目前首钢集团首钢长治, 首钢水钢均推广应用“留渣-双渣”少渣炼钢操作工艺,工艺相对成熟 。
1. 大幅度减少炼钢石灰、白云石等渣料消耗和炼钢渣量; 2. 可以利用出钢后炉渣的物理热,预热废钢; 3. 炼钢终渣含Tfe:15~25%,渣量减少可以降低钢铁料消耗; 4. 双渣倒渣的炉渣主要为脱磷阶段低碱度渣,自由CaO含量低, 可以简化炉渣处理; 5. 常规转炉出钢后留在炉内钢水随炉渣倒出,采用“留渣-少渣”工 艺终点少倒渣、出钢后不倒渣,可以提高钢水收得率。
FeO%
H11Mn2SiA
3A14306-1 3A14306-2 3B14615-1 3B14615-2 3C14935-1 3C14935-2 3A14301-1 3A14301-2 3B14603-1 3B14603-2 3B14612-1 3B14612-1
1 冶炼周期影响
类别 加料 脱磷期 双渣 脱碳期 终点 加废钢 兑铁时间 前期吹炼时间 氮气刹渣 倒渣时间 中后期吹炼 拉碳、补吹时间 等待终点成分 出钢时间 溅渣时间 总冶炼周期 留渣-双渣 1.7 2.4 4.5 2.1 3 8.8 2 1 2.5 2 30 单渣法 1.7 2.2 4.5 / / 8.7 2 1 2.5 2.5 25.1
转炉留渣操作技术
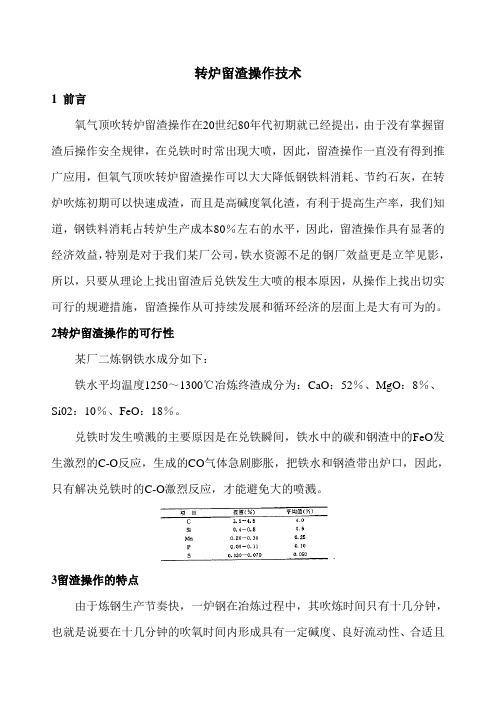
转炉留渣操作技术1 前言氧气顶吹转炉留渣操作在20世纪80年代初期就已经提出,由于没有掌握留渣后操作安全规律,在兑铁时时常出现大喷,因此,留渣操作一直没有得到推广应用,但氧气顶吹转炉留渣操作可以大大降低钢铁料消耗、节约石灰,在转炉吹炼初期可以快速成渣,而且是高碱度氧化渣,有利于提高生产率,我们知道,钢铁料消耗占转炉生产成本80%左右的水平,因此,留渣操作具有显著的经济效益,特别是对于我们某厂公司,铁水资源不足的钢厂效益更是立竿见影,所以,只要从理论上找出留渣后兑铁发生大喷的根本原因,从操作上找出切实可行的规避措施,留渣操作从可持续发展和循环经济的层面上是大有可为的。
2转炉留渣操作的可行性某厂二炼钢铁水成分如下:铁水平均温度1250~1300℃冶炼终渣成分为:CaO:52%、MgO:8%、Si02:10%、FeO:18%。
兑铁时发生喷溅的主要原因是在兑铁瞬间,铁水中的碳和钢渣中的FeO发生激烈的C-O反应,生成的CO气体急剧膨胀,把铁水和钢渣带出炉口,因此,只有解决兑铁时的C-O激烈反应,才能避免大的喷溅。
3留渣操作的特点由于炼钢生产节奏快,一炉钢在冶炼过程中,其吹炼时间只有十几分钟,也就是说要在十几分钟的吹氧时间内形成具有一定碱度、良好流动性、合适且TFe和MgO含量正常泡沫化的炉渣,以保证冶炼成分和温度同时双命中的钢水,并减少对炉衬的侵蚀,留渣操作贯穿于炼钢整个冶炼周期,主要是靠所留炉渣的物理热和炉渣化学性能,使其具有迅速参与反应、并促进前期炉渣的快速形成、提高去除P、S的效率、节省石灰用量。
3.1有利于去磷在氧气顶吹转炉中,磷的氧化是在炉渣-金属界面中进行的,其反应式为:生成的磷酸铁在高温下极其不稳定,它可以重新分解生成P2O5,而P2O5是不稳定的化合物,因此,仅靠生成P2O5。
不能去除磷,但P2O5是酸性化合物,若用碱性化合物与其结合生成稳定的化合物可以去除。
研究认为,在碱性渣中P2O5与CaO形成稳定的(CaO)x P2O5型的化合物,其中x为3或4,因此,操作中需加入石灰,使其生成稳定的化合物3CaO· P2O5。
转炉留渣操作原因与注意事项

转炉留渣操作原因与注意事项
一、转炉留渣操作可以极大降低原料消耗,在吹炼初期可以快速成渣,有利于提高生产率,因而推广应用的潜力很大,但转炉留渣操作易发生大喷溅,限制了其应用。
二、分析认为需要注意以下几点,可以使留渣操作得到切实可行:
1、安全问题:兑铁时喷溅,因此所留的炉渣应确保:一是温度不能太高(W 1500C),二是溅渣时间必须保证,因为留渣操作一般与溅渣护炉并用,必要时要加入一定量的改质剂稠渣。
2、初期渣化的早,尤其是前期低温时易发生喷溅,随之而来发生返干现象,导致沾枪沾罩操作困难,应注意。
3、开吹时打火困难,可以采用前后摇炉或者先点吹30-40s 再加废钢的办法。
4、吹气渣化得早,前期渣来得迅速,低温炉渣容易从炉口涌出,特别是吹炼到
约 6 分钟时,压料后易“返干”,特别是Si 数低时更明显,而铁水Si 含量高时,过程渣不易控制易发生喷溅,当铁水Si 数超过0.5%时,喷溅率直线上升。
5、拉碳时火焰判断不准,易拉高碳,点吹时降碳量和升温速度相比单渣法要低,由于留渣造成热平衡不好计算且留渣火焰相比单渣法时火焰亮,温度控制难度加大,需要特别注意。
260t转炉留渣操作实践

a d i v l e t e — k n n e e y c n e e r n lz d a d t u h e h o o i a a a - n n ov d se l ma i g i d x s b o v r r a e a ay e n h s t e t c n l gc l p r me- — t
。 、
、
鞍 钢 技 术
AN GAN G TECH NOLOGY 总 第 3 4期 7
21 0 2年 第 2期 生
一产 ~ ~实 一
、践 ~ , 一
、. . ’
2 0t 炉 留渣 操 作 实践 6 转
牛 兴 明 , 文 飞 , 超 , 春新 , 国义 刘 李 魏 徐
Ni ng n Li e f i LiCha W e un i Xu Gu y u Xi mi g, u W n e , o, iCh x n, o i
(B y q a rn& S e l u sd ayC mp n f g n te o, t . a u u n Io te b i ir o a yo a gS e lC . Ld, S An
Y n k u 1 0 , i nn , hn ig o 0 7 La ig C ia) 1 5 o
Absr c :I fu n i g f c o s o h a ey o l g e i i p r to n t 60 tc n e t r t a t n e c n a tr n t e s f t fsa -r ma n ng o e a in i he 2 o v re l
中图分 类 号 : F 1 T 73
文 献标 识 码 : A
文章 编 号 :1 0 — 6 3 2 1 } 2 0 4 — 4 0 6 4 1 (0 2 0 — 0 2 0
干法除尘工艺下转炉留渣操作的探索与实践

化学反 应 处于富 氧的气 氛下 ,熔 池 f } 1 的碳无 论是与
气体 氧接触 反应 ,还是与 金属 中溶解 的氧反应 ,生  ̄ g l f ' , j c o气体( 见化学 反应式 ( 3 ) ) 在排 m熔池 前 ,经过 化学反应( 4 ) 后 ,牛成物 以C O , 为主 :
放电, 与 C 0≥9 % ,O ≥6 %1 时, 或 { H , ≥3 %,
F } { 丁初 期 产 生 的CO全 部转 变h  ̄ , c o, .高浓 度
供稿} 张 书欣 ,马 旭 朝 ,张 朝 发 ’ ,宋悦 ,安 海 玉 ,王 生金
s h u x i n , M A Xu — Z h a o }z H Nc
,
,
一 ,t
}
?
S O NG Y u e , A N H a i . y u , WA NG S h e n g - j i n
2 [ C 1 + { O 1 / [ O 1 = 2 { C O} { C 0} + [ 0 ] = { c o ! }
{ CO! } 十 [ C] = 2{ CO}
转 炉炼 钢 过 程 r I l ,炉 内 的铁 水 瓴气 发 ' 1 - 剧 烈 的化学 反应而 成大 } 的高 温炯气 ,伴 随炉 L = I 有
,
謇 留 渣 操 作 就 是 将 炼 钢 转 炉 上 一 炉 所 形 成 的 高 温 、 高 碱 度 、 含 有 一 定 量 F e 。 的 终 渣 全 部 或 部 分 留
导 在 炉 内,可 以显 著降低转 炉 台炼成本。 河钢 唐钢长材部 转炉采 用干 法除尘技 术 ,在投 产的初期 无法
一
部分卒气混 入 ,州 气主 芟成 分为C O、C O, 、O 、
留渣操作注意事项

转炉留查操作工艺注意事项
①每炉钢留渣量约为1.5~2.0吨左右,在溅渣时应把渣溅好,溅
渣时间应控制在150~240秒,保证炉渣挂到炉壁上,当炉口甩出的渣片由细小颗粒转变为较大块状物渣块时,提枪结束溅渣,即可进行下一炉加废钢、兑铁水操作;
②在加废钢前根据铁水质量准确计算出石灰、白云石、冷料等渣
料的加入量,控制好过程渣,保证转炉良好的运行状态;
③留渣操作的前期采用低枪位操作,减少头批料的加入量,中后
期适当提枪,同时跟进一定量的冷料来控制温度,从而达到准确控制终点的目的;
④在放完钢后认真观察,待炉内炉渣的黏度和流动性适宜时,直
接溅渣并进行严格的时间控制,把炉渣温度降至1500℃以下;
⑤为避免留渣量积累过多,坚持每隔4~5炉进行一次倒渣操作;
⑥为避免炉底上涨,每天必须测炉底零位,及时清除引起炉底上
涨的炉渣。
52-2-1备-C-复吹转炉留渣操作成渣过程探讨(OK)

494复吹转炉留渣操作成渣过程探讨雷 强, 朱志鹏, 王光进, 钱高伟武汉钢铁集团公司条材总厂一炼钢分厂,湖北 武汉 430083摘 要:转炉冶炼的操作方法成渣路线均属于钙质成渣路线,但留渣操作的脱磷动力学和热力学条件明显优于传统单渣不留渣操作。
在目前钢厂的设备条件下,留渣操作是值得推广的。
关键词:成渣路线;留渣操作;脱磷1 前言复吹转炉是钢铁生产中脱磷的重要设备。
但对于冶炼磷含量较高的铁水来说,复吹转炉仍存在着渣量大、冶炼操作不稳定、喷溅严重、炉衬寿命短和终点命中率低的缺点,且给冶炼低磷及超低磷钢种带来很大困难。
转炉留渣操作就是解决此问题的一种冶炼工艺。
如图1所示,因受没有附枪限制,传统操作存在很多弊端。
图2所示即进行留渣操作,留下上炉高碱度高氧化性的炉渣供下炉前期造渣使用,倒炉出渣后在同一炉内进行少渣脱碳冶炼,前后期任务的本质不同导致成渣过程存在根本性的不同。
因此,转炉留渣操作成渣路线的分析,对合理加料造渣制度有普遍意义。
图1 转炉传统操作工艺流程Fig.1Technological process of traditional operation in BOF图2 留渣操作工艺流程Fig.2 Technological process of Slag remaining practices in BOF2 成渣路线目前,转炉冶炼大多采用恒压变枪位冶炼工艺。
在这种工艺下成渣路线可分为两大类:钙质成渣路线和铁质成渣路线。
在吹炼过程中,渣中FeO的增加是促使石灰块加速造渣的关键所在,FeO能显著降低C 2S初晶495区液相面的温度,有利于C 2S壳层的破坏。
转炉吹炼初期,炉渣成分大致位于图中的A区,而终渣成分要求达到C区。
A区为酸性初渣区,其形成的主要原因是:在开吹的头几分钟内熔池温度比较低(约为1400℃),石灰仅刚刚开始溶解,铁、硅、锰等元素优先氧化,生成FeOn、SiO2和MnO,形成了高氧化性的酸性初渣区。
转炉定量留渣-溅渣-全留渣的工艺实践
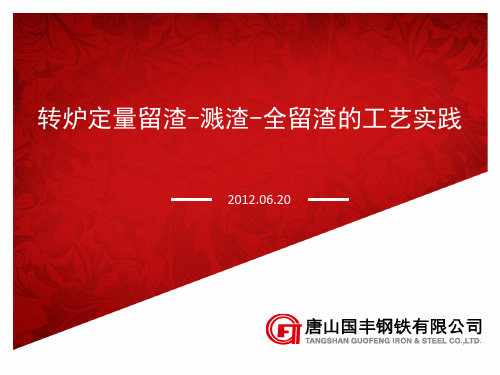
9.96——降低石灰消耗,kg/吨钢
0.4 ——石灰成本,元/kg 0.8 ——钢铁料消耗与留渣溅渣率相关系数
0.4 ——项目本身贡献系数
四、溅渣护炉效果与经济效益
4.3经济效益
通过应用转炉定量留渣溅渣技术研究成果后,溅渣效果较好,降低补 炉耐材消耗。 按降低耐材消耗0.49元/吨钢计算,年可降低耐材消耗效益: 200×1.53×0.24×0.4=29.38万元/年 其中: 200 ——年钢产量,万吨/年
8.4 ——降低钢铁料消耗,kg/吨钢
2.75 ——钢铁料成本,元/kg 0.7 ——钢铁料消耗与留渣溅渣率相关系数
0.4 ——项目本身贡献系数
四、溅渣护炉效果与经济效益
4.3经济效益
溅渣后可利用热态渣提高转炉化渣效果,同时,可充分提高转炉初期 渣碱度,从而提高转炉脱磷效果,达到降低石灰消耗的目的; 按按降低石灰消耗9.96kg/吨钢计算,年可降低石灰消耗效益: 200×9.96×0.4×0.8×0.4=254.97万元/年 其中: 200 ——年钢产量,万吨/年
渣制度、温度制度和终点控制的优化,成功解决传统全留渣工艺存在的 问题。
三、定量留渣-溅渣-全留渣的工艺实践
3.5定量留渣-溅渣-全留渣工艺制度
表9 定量留渣-溅渣-全留渣工艺制度
溅渣前渣量控制 渣量适中(根据 炉体侵蚀情况调 整适当转炉倾角 ,保证留渣量2~ 2.5)且稳定
溅渣压力 Mpa
溅渣时间 min
溅渣枪位(标尺) m
全留渣控制
1.1~1.3
1.5-2.5
1.5→0,交变溅渣 枪位
溅渣完毕全 部留渣
四、溅渣护炉效果与经济效益
4.1 溅渣护炉效果
表10 溅渣护炉效果对比
转炉留渣操作控制要点分析

转炉留渣操作规程
转炉留渣操作规程
一、操作步骤
1. 炉前倒炉时要倒掉1/3左右炉渣,控制留渣量在3t左右;
2. 根据终渣情况和出钢温度加改质剂溅渣,炉口渣粒粒度大于30mm为宜,吹氮时间必保2分钟以上;
3. 留渣量为溅渣后全部渣量,不倒渣;
4. 必须先加废钢,向后摇到出钢面30°;
5. 兑铁时兑铁量1/2以前要小流缓慢兑入,一半以后可正常兑入;
6. 开吹采用低枪位操作,枪位比正常枪位低100~200mm,留渣炉次石灰加入量为正常加入量的2/3,轻烧白云石为正常加入量的1/2;头批料加入2/3的石灰,轻烧白云石加入1 /3,起渣后(留渣操作第3、4炉后起渣时间在2分半左右)氧压比正常氧压低0.1~0.15 MPa,视情况加入其余渣料,最晚9分钟以前加完;
7. 可以连续留渣4炉,但最多不超过5炉,将炉渣倒净,换新渣。
二、留渣操作中职责划分
1. 炉长:负全责,控制好留渣量;
2. 一助手:负责溅渣操作,将炉渣温度降到1500℃以下,具体方法保证吹氮时间>2分钟,溅渣时氮气压力不低于1.0MPa;并根据终点情况确定改质剂加入量,目的溅完渣后炉渣成块状,加废钢后要向后摇炉,使铁块完全盖住炉渣;
3. 二助手:观察炉口渣粒情况,渣粒粒度太小或炉口看不到时要向前倒炉进行观察;兑铁时要保证炉前两侧无人,尤其是两炉中间门前也要无人,同时注意脚下要无杂物,站的位置靠近挡墙,以刚好看见炉口为宜。
三、以下情况严禁留渣操作
1. 铁水Si>0.70%;
2. 未溅渣炉次;
3. 氮气压力低,溅渣不正常的炉次;
4. 炉内剩钢炉次;
5. 下一炉测枪位炉次;
6. 其它异常情况,没有把握的炉次;。
转炉炼钢中留渣技术的原理及应用分析

转炉炼钢中留渣技术的原理及应用分析发布时间:2021-11-17T02:43:17.083Z 来源:《中国科技人才》2021年第22期作者:郑信彬[导读] 伴随着转炉炼钢技术的不断升级,急需引进新技术强化钢渣回收利用,减少炼钢产生的能耗和污染。
基于此,对转炉炼钢中留渣技术原理展开了分析,并对技术应用要点进行了探究,发现需要通过开展工艺试验合理确定脱磷效率、留渣量等各项参数,确保技术应用取得理想效果。
郑信彬新疆天山钢铁巴州有限公司新疆 841300摘要:伴随着转炉炼钢技术的不断升级,急需引进新技术强化钢渣回收利用,减少炼钢产生的能耗和污染。
基于此,对转炉炼钢中留渣技术原理展开了分析,并对技术应用要点进行了探究,发现需要通过开展工艺试验合理确定脱磷效率、留渣量等各项参数,确保技术应用取得理想效果。
关键词:转炉炼钢;留渣技术;原理分析引言:作为国家重要的基础产业,钢铁工业在发展过程中一直存在资源消耗量多、废弃物排放量大等问题,不利于行业可持续发展。
在国内产钢量中,转炉炼钢占据较大比重,每年需消耗上千万吨石灰石和生白云石,产生的钢渣也数以千万计,造成资源消耗严重的同时,给环境发展带来了不利影响。
引入留渣技术开发新工艺,可以解决上述问题,加速产业转型升级。
1转炉炼钢中留渣技术的原理分析在转炉炼钢期间,钢渣密度比钢水小,将漂浮在钢水之上。
在转炉倾至20~35°时,液面漫过出钢口前钢渣将先流入钢包,出渣量占总体20~30%,属于前期渣[1]。
出钢后,由于钢水产生涡旋,将表面钢渣吸入,产生30%出渣量。
全部钢水倒入后,最后流出的钢水下渣量较大,出渣量达到40~50%,属于终渣,需及时摇起转炉结束出钢。
由于钢渣中含有的磷、硫等元素将给钢材性能带来较大影响,所以需加强下渣量控制,避免过多钢渣进入钢包,减少钢水精炼时间和铁合金加入量,达到提高效率和节约成本的双重目标。
运用留渣技术,需要将上一炉约2/3终渣留在炉内,对铁液加入废钢。
转炉炼钢中留渣技术的原理及应用杨正府

转炉炼钢中留渣技术的原理及应用杨正府发布时间:2021-09-26T07:45:34.951Z 来源:《防护工程》2021年15期作者:杨正府[导读] 转炉留渣法炼钢技术的普及和推广应用,为冶炼技术发展做出了极大的贡献。
在明确技术应用方法和工艺的基础上,做好对技术的创新与完善,将会进一步提升留渣冶炼技术应用价值。
柳钢转炉炼钢厂广西壮族自治区柳州市 545002摘要:转炉留渣法炼钢技术的普及和推广应用,为冶炼技术发展做出了极大的贡献。
在明确技术应用方法和工艺的基础上,做好对技术的创新与完善,将会进一步提升留渣冶炼技术应用价值。
关键词:转炉炼钢;留渣技术;脱磷引言在钢铁行业降本增效大背景下,转炉炼钢留渣法作为一种能够显著降低辅料消耗、降低钢铁料消耗的技术,使得炼钢生产成本得到了切实的控制和降低,并且提升了生产效率。
随着钢铁工业技术日益向精细化发展,转炉留渣法炼钢技术应用效果也越来越明显,更多的炼钢企业和技术人员愿意挖掘这一技术的潜在应用价值,对转炉留渣法炼钢技术进行不断创新和完善,进一步拓展该技术的使用范围。
1 转炉炼钢留渣技术原理转炉留渣法技术原理:将上一炉部分终渣留在炉内,溅渣护炉后,作为下一炉初渣,利用其高温,高碱度,高T.Fe以及含有MgO的碱性渣特点,促进石灰轻烧快速熔化成渣和前期脱磷,从而降低熔剂消耗,降低生产成本。
通过大规模工业试验和对转炉脱磷过程热力学、动力学分析,得到转炉铁水“三脱”预处理各工艺参数和如下主要结论:(1)转炉铁水脱磷效果决定于采用的脱磷工艺,经过工业实践:低碱度高FeO渣脱磷率为55.4%,中高碱度高FeO渣脱磷率为83.4%,中高碱度低FeO渣脱磷率为86.4%。
三种方案相比,中高碱度低FeO渣脱磷效果好、铁损低,应是脱磷工艺的首选方案。
(2)炉渣碱度是提高脱磷率的关键,炉渣碱度增大,脱磷率增加。
(3)在相同炉渣碱度条件下,随脱碳量增加,脱磷率增大;说明炉渣的脱磷能力决定了熔池中C.P平衡关系,在相同熔池C条件下,炉渣碱度越高,与C平衡的P越低。
济钢120t转炉留渣操作工艺的实践

中图 分 类号 : F 0 . T 7 36 文 献标 识 码 : B 文章 编 号 : 0 6 5 0 (01 1 0 — 0 8 2 0)0 4—0 2 0 5—0 2
LuX a sn WagN a xn J h n x eHe iLuJ j n i ioe , n in i,i C o g u , , i ni g a We ia
2F O) C =2 e + O (e +[ 】 [ ] C 2 F
() 2
要 防 止喷 溅 。最 直接 的办 法是 控 制炉 中气 体 , 杜 绝或 减缓式 ( )式 ( ) 1 、 2 的反应 。分 析认 为要 实现
少渣料 消耗 , 能提 高废 钢 比, 并 降低 钢铁 料 消耗 , 对
于提 高炉龄有 一定 的好处 。转炉 的 留渣 操作并 不是
一
项 全新 的工 艺 , 以前 由于 留渣后 下 炉兑 铁 水 时易
出现 喷溅 等 安 全 问题 , 这 项 工 艺 很 难 进 行 , 使 随着
溅 渣 护炉 技术 的产 生 和顶 底 复 吹转 炉 设 备 的 引进 ,
go . t
Ke o d : o v a r sa -e ; p r t n p o e s p a t e y W r s c n e o ; lg l f o e a i r c s ; r c i t o c
1 前 言
2 留 渣 喷 溅 的 根 本 时 , 会 同时发 生 以下式 () 必 1、 式() 2 的反应 。根 据经 验 当终渣 中 ( e 高 于 2 %, F O) 0 式 ( ) ( ) 应 激烈 , 间 产 生 大 量 的 气 体 附 带 炉 1 、2 反 瞬 渣、 铁水 冲出 。 造成 爆发性 喷溅 事故 。 (e + [] F】 O F O) C =【e +C () 1
转炉造渣制度概要
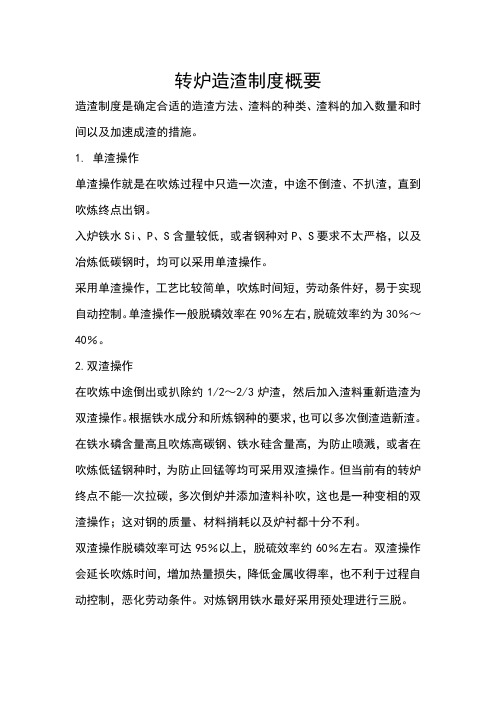
转炉造渣制度概要
造渣制度是确定合适的造渣方法、渣料的种类、渣料的加入数量和时间以及加速成渣的措施。
1. 单渣操作
单渣操作就是在吹炼过程中只造一次渣,中途不倒渣、不扒渣,直到吹炼终点出钢。
入炉铁水Si、P、S含量较低,或者钢种对P、S要求不太严格,以及冶炼低碳钢时,均可以采用单渣操作。
采用单渣操作,工艺比较简单,吹炼时间短,劳动条件好,易于实现自动控制。
单渣操作一般脱磷效率在90%左右,脱硫效率约为30%~40%。
2.双渣操作
在吹炼中途倒出或扒除约1/2~2/3炉渣,然后加入渣料重新造渣为双渣操作。
根据铁水成分和所炼钢种的要求,也可以多次倒渣造新渣。
在铁水磷含量高且吹炼高碳钢、铁水硅含量高,为防止喷溅,或者在吹炼低锰钢种时,为防止回锰等均可采用双渣操作。
但当前有的转炉终点不能—次拉碳,多次倒炉并添加渣料补吹,这也是一种变相的双渣操作;这对钢的质量、材料捎耗以及炉衬都十分不利。
双渣操作脱磷效率可达95%以上,脱硫效率约60%左右。
双渣操作会延长吹炼时间,增加热量损失,降低金属收得率,也不利于过程自动控制,恶化劳动条件。
对炼钢用铁水最好采用预处理进行三脱。
3. 留渣操作
留渣操作就是将上炉终渣的一部分留给下炉使用。
终点熔渣的碱度高,温度高,并且有一定(TFe)含量,留到下一炉,有利于初期渣尽早形成,并且能提高前期去除P、S的效率,有利于保护炉衬,节省石灰用量。
采用留渣操作时,在兑铁水前首先要加石灰或者先加废钢稠化冷凝熔渣,当炉内无液体渣时方可兑入铁水,以避免引发喷溅。
溅渣护炉技术在某种程度上可以看作是留渣操作的特例。
80t转炉冶炼SCM435钢留渣操作技术研究

· 工艺技术 ·
特 殊钢
SPECIAL STEEL
V01.39.No.5 October 2018
80 t转炉 冶 炼 SCM435钢 留渣 操 作技 术研 究
霍 志斌 赵 彦岭 王 建林 王秋 坤
(邢台钢铁有限责任公司炼钢厂 ,邢 台 054027)
steel SCM435 on lim e adding am ount.remaining slag heats of equilibr ium basicity and end slag basicity iS tested and stud— ied,and the points for attention in slag remaining operation are summ ar ized. As the 80t BOF rem aining slag operation is put into practice,the remaining slag rate is up to 68.9% ,the ratio of P content≤0.015% in product increases from origi- nal 49.3% to 62.2% ,and the lime consumption decreases by 4.5 kg/t,and the iron loss in slag decreases by 230 kg.
M aterial Index 80 t BOF,Steel SCM435,Remaining Slag,Deph08phorization,Splashing,End Phosphorus Content
炼铁造渣操作方法有哪些

炼铁造渣操作方法有哪些炼铁造渣是指在炼铁过程中,通过控制温度、炉料成分和加入造渣剂等操作手段,将炉料中的杂质和不需要的元素排除出去,从而得到纯净的铁水。
以下是几种常见的炼铁造渣操作方法。
1. 高炉造渣法高炉造渣法是指通过炉身内壁和炉内鼓风装置进行造渣的方法。
在高炉炼铁的过程中,鼓风装置会不断向炉内引入空气,形成高温高压的气流,加速炉料的燃烧和还原反应,从而排除炉料中的杂质和不需要的元素。
2. 转炉造渣法转炉造渣法是指通过转炉底部的氧气鼓风设备来进行造渣的方法。
在转炉炼钢的过程中,底吹氧枪会向炉底喷入高温高压的氧气,使炉料中的杂质和不需要的元素氧化,形成气态或液态的渣并排出炉外。
3. 电炉造渣法电炉造渣法是指通过电炉中的电弧和电流进行造渣的方法。
在电炉炼钢的过程中,通过电流和电弧的热效应,使炉料中的杂质和不需要的元素熔化,并通过电炉底部的出渣口排出。
4. 氧气顶吹造渣法氧气顶吹造渣法是指通过在炉顶部向炉料中加入高温高压的氧气来进行造渣的方法。
在炼钢过程中,通过顶吹氧枪向炉内喷入氧气,使炉料中的不需要的元素氧化,形成气态的渣并排出炉外。
5. 造渣剂的使用造渣剂是一种能够吸附和固定炉料中杂质和不需要的元素的物质。
在炼铁过程中,可以加入适量的造渣剂来吸附和固定炉料中的杂质,从而达到净化铁水的目的。
常见的造渣剂有石灰石、白云石、石英粉等。
除了以上几种操作方法,还有一些其他辅助的操作手段也可以用于炼铁造渣,如加热炉料、控制还原剂的添加量、调整炉底温度等。
这些操作手段的目的都是为了控制和优化炼铁过程,尽量将不需要的元素排除,从而得到高纯度的铁水。
总之,炼铁造渣操作方法有很多种,每一种方法都有其特点和适用范围。
在实际操作中,需要根据炉型、物料成分、生产要求等因素进行选择和调整,以达到最佳的炼铁效果。
留渣操作工艺介绍

转炉少渣冶炼工艺(SGRP )介绍Slag Generation Reduced Refining Process一、 工艺流程装料(加废钢、兑铁)—脱磷阶段(脱硅期0-3min ;脱磷期3-5.5min :)—倒渣操作(3-5min :排渣率50-70%)—脱碳阶段(脱碳期5.5-8min ;返干期8-12min ;吹炼末期12min-拉碳)—出钢和留渣—溅渣护炉—确认无液态渣—装料(加废钢、兑铁)二、 工艺控制内容1、辅料加料操作:合理控制石灰及白云石的加料分配系数(首秦:石灰30/70;白云石60/40)2、炉渣成分控制:脱磷阶段结束炉渣成分控制:碱度1.5-2.0、MgO 含量≥7.5%、FeO8%-12% 脱碳阶段终点炉渣成分控制:碱度3.0-3.5、MgO 含量≥10%、FeO12%-20%3、枪位控制:3.1供氧强度:脱磷期供氧强度为2.9-3.0m 3/mint ;脱碳期供氧强度为3.3-3.5 m 3/mint 。
3.2枪位控制:脱硅期(0-3min )1.8-2.0m ;脱磷期(3-5min )1.6-1.8m (采用低枪位减少FeO 含量,防止炉渣泡沫化);脱碳期(5-8min )1.7-1.8m 返干期(8min~12min )1.8-2.0m ;吹炼末期(12-拉碳)1.8-1.7-1.6-1.5-1.4m 终点3min 连续压枪操作(控制终渣泡沫化程度,防止出钢溢渣)4、脱磷渣排渣操作:转炉倒渣操作上要求快速倒掉脱磷阶段炉渣(3min 以内);排渣率大于50%。
5、脱磷期结束半钢成分:脱磷期结束碳含量在3.0-3.2%;脱磷率50%~70%。
溅渣护炉渣固化确认添加废钢兑铁脱磷阶段脱碳阶段出钢和留渣三、SGRP工艺的优点1、转炉终点渣被用于脱磷期脱磷,排出约50%脱磷渣后,脱碳期仅加入少量石灰和白云石,从而减少了渣量,降低钢铁料消耗。
2、可大幅度降低石灰及白云石消耗,可节省石灰30-40%,节省白云石约50%。
- 1、下载文档前请自行甄别文档内容的完整性,平台不提供额外的编辑、内容补充、找答案等附加服务。
- 2、"仅部分预览"的文档,不可在线预览部分如存在完整性等问题,可反馈申请退款(可完整预览的文档不适用该条件!)。
- 3、如文档侵犯您的权益,请联系客服反馈,我们会尽快为您处理(人工客服工作时间:9:00-18:30)。
转炉留渣操作技术
1 前言
氧气顶吹转炉留渣操作在20世纪80年代初期就已经提出,由于没有掌握留渣后操作安全规律,在兑铁时时常出现大喷,因此,留渣操作一直没有得到推广应用,但氧气顶吹转炉留渣操作可以大大降低钢铁料消耗、节约石灰,在转炉吹炼初期可以快速成渣,而且是高碱度氧化渣,有利于提高生产率,我们知道,钢铁料消耗占转炉生产成本80%左右的水平,因此,留渣操作具有显著的经济效益,特别是对于我们某厂公司,铁水资源不足的钢厂效益更是立竿见影,所以,只要从理论上找出留渣后兑铁发生大喷的根本原因,从操作上找出切实可行的规避措施,留渣操作从可持续发展和循环经济的层面上是大有可为的。
2转炉留渣操作的可行性
某厂二炼钢铁水成分如下:
铁水平均温度1250~1300℃冶炼终渣成分为:CaO:52%、MgO:8%、Si02:10%、FeO:18%。
兑铁时发生喷溅的主要原因是在兑铁瞬间,铁水中的碳和钢渣中的FeO发生激烈的C-O反应,生成的CO气体急剧膨胀,把铁水和钢渣带出炉口,因此,只有解决兑铁时的C-O激烈反应,才能避免大的喷溅。
3留渣操作的特点
由于炼钢生产节奏快,一炉钢在冶炼过程中,其吹炼时间只有十几分钟,也就是说要在十几分钟的吹氧时间内形成具有一定碱度、良好流动性、合适且
TFe和MgO含量正常泡沫化的炉渣,以保证冶炼成分和温度同时双命中的钢水,并减少对炉衬的侵蚀,留渣操作贯穿于炼钢整个冶炼周期,主要是靠所留炉渣的物理热和炉渣化学性能,使其具有迅速参与反应、并促进前期炉渣的快速形成、提高去除P、S的效率、节省石灰用量。
3.1有利于去磷
在氧气顶吹转炉中,磷的氧化是在炉渣-金属界面中进行的,其反应式为:
生成的磷酸铁在高温下极其不稳定,它可以重新分解生成P2O5,而P2O5是不稳定的化合物,因此,仅靠生成P2O5。
不能去除磷,但P2O5是酸性化合物,若用碱性化合物与其结合生成稳定的化合物可以去除。
研究认为,在碱性渣中P2O5与CaO形成稳定的(CaO)x P2O5型的化合物,其中x为3或4,因此,操作中需加入石灰,使其生成稳定的化合物3CaO· P2O5。
或4CaO·P2O5存在于渣中,才能有效去磷,其反应为:
从式中可以看出脱磷的条件,(1)提高CaO含量即提高炉渣碱度,(2)提高炉渣氧化性,即FeO含量,(3)降低熔池温度。
以上分析可以说明,留渣操作对脱磷是有利的,因为(1)冶炼初期熔池温度比较低,碱度一般在1.8~2.2之间,且渣中含有一定的FeO,满足脱磷的热力学条件,(2)留渣操作可以使初期成渣速度更快、流动性好,满足脱磷的动力学条件。
3.2提高钢水收得率
一般转炉终渣FeO含量在15%左右,渣中游离的铁渣按8%计算,每炉留渣
1000公斤,则每炉可以回收120公斤铁左右,按二炼钢目前的产能,每年可节约一千五百万元。
3.3冶炼前期反应
由于所留炉渣本身的特点,从兑铁开始到吹炼之前,炉渣就和铁水之间发生物理化学反应,其主要反应有:
这些反应的存在可以从留渣操作的纯供氧时间比不留渣的纯供氧时间短的实践得到印证,因此留渣操作炉次的吹炼时间比正常单渣法操作供氧时间有所缩短,一般缩短大约在2%左右。
4 留渣操作需要注意的几个问题
1)安全问题:兑铁时喷溅,因此所留的炉渣应予以确认,一是温度不能太高,一般在1500℃可以保证其安全性,二是溅渣时间必须保证,因为目前留渣操作一般与溅渣护炉并用,必要时可以加入一定量的改质剂稠渣。
2)初期渣化的早、来的快,尤其是前期低温时易发生喷溅,随之而来产生返干现象,导致沾枪沾罩操作困难。
3)开吹时打火困难,可以采用前后摇炉或者先点吹30~40s再加人废钢的办法。
4)初期渣化得早,前期渣来得快,低温炉渣容易从炉口涌出,特别是吹炼到6分钟左右,压料后易“返干”,Si数低时尤甚,铁水硅含量高时,过程渣不易控制易发生喷溅,当铁水硅数超过0.5%时喷溅率呈直线上升。
5)拉碳时火焰判断不准,易拉高碳,点吹时降碳量和升温速度都比单渣法低,由于留渣造成热平衡不好计算且留渣操作火焰比单渣法火焰亮,温度不好
控制。
5 结语
1)留渣操作方向性是可行的,关键是合适的留渣量及溅渣效果的保证。
2)留渣操作对P、S的去除有利,同时可以大大降低钢铁料的消耗,是值得我们重点研究的课题。