转炉留渣操作原因与注意事项
莱钢60t转炉单渣留渣操作实践

莱钢60t转炉单渣留渣操作实践安全规律,因此一直没有得到大范围推广应用。
但氧气转炉留渣操作能够充分利用前炉钢终点炉渣的热量、碱度和氧化性,大幅降低渣料消耗,在转炉吹炼初期可以快速造就高碱度氧化渣,有利于提高生产效率,并具有显著的经济效益,特别在铁水资源不足的钢厂效益更加突出。
因此各钢厂一直在进行生产试验,以求实现留渣操作的稳定。
留渣操作主要有两方面的危害:一是兑铁时碳氧剧烈反应发生大喷;二是转炉开吹打不着火,转炉烟道内氧气和一氧化碳达到爆炸极限,产生烟道爆炸事故。
1.1兑铁大喷的原因及预防即温度低于1507℃时,铁水和上一炉的炉渣接触,首先是硅的氧化(但也不排除有碳的氧化,因为铁水中含碳量较高),也就限制了碳的激烈氧化。
另外,也可根据不同温度下各种纯氧化物的分解压力找出碳和硅优先氧化的温度。
由氧化物标准生成自由焓的变化与温度的关系可知:SiO2分解壓力曲线与CO分解压力曲线相交的对应温度为1530℃。
当t小于1530℃时,[Si]先于[C]被氧化;当t大于1530℃时则[C]先于[Si]被氧化。
既便是在热力学满足式(3)的情况下,反应也不一定进行或进行的很缓慢而不会造成喷溅,这是由复杂的动力学因素决定的。
上式表明,化学反应速度随温度升高而加快,也就是说温度越高发生喷溅的概率越大。
反之,化学反应速度降低,发生喷溅的概率越小。
从热力学和动力学的分析都可以看出,降低炉渣温度是避免出现兑铁大喷的关键因素,目前转炉大部分实现了溅渣护炉,溅渣后炉渣温度均低于1500℃。
可以说留渣操作的条件已经具备。
同时在溅渣操作时,通过溅干炉渣,防止有液态炉渣,溅渣终点由炉长亲自查看炉渣状态,溅渣时加入一部分石灰等渣料等措施,可以确保兑铁时不出现大喷危害。
1.2 开吹打不着火的原因及预防开吹打不着火主要是由于留渣操作炉渣、加入的废钢带入的渣钢以及铁水带入的铁水渣量大,漂浮在表面,导致氧气流股不能够直接穿透渣层,发生反应。
开吹打火时间超过40s,则前期氧气流股一部分冲击炉渣表面,造成(FeO)聚集,一部分进入烟道内,造成烟道内氧气含量大于2%。
转炉车间溅渣操作要点11.19概要

转炉车间溅渣操作管理制度针对目前各班溅渣操作不统一,不能正确的通过溅渣来维护炉子,造成炉子频频告急,给厂部和车间带来极大的工艺事故和安全事故隐患,通过这几个月来对炉前工艺操作和终点控制情况,特对溅渣作出下规定:一、溅渣条件1、钢水必须出尽炉长、必须炉炉关注后大面的情况,不能出现凹坑或不平,必须观察出钢口位置高低,确保出钢口不高于后大面,保证每炉钢钢水都出尽,(如有钢水出不完的现象,跟班技术员、作业长、炉长必须在3炉钢内处理好保证炉渣的可溅性。
2、在出钢过程中,炉长、操枪工必须从炉后观察炉内炉渣情况,炉长需及时指导操枪工的调渣密度和用量,确保渣子不调死,保证溅渣时间和效果,并指导自己下一炉的化渣枪位和方法。
3、操枪工必须确定有正常的工作氮压和流量,确保溅渣过程效果。
4、值班长必须保证炉后有充份的丢补料,每炉钢保证在出钢过程中向炉内加入10-15包的丢补料(30kg(遇渣很粘时,可以少丢或不丢。
5、遇拉后吹严重时,操枪工必须先加入轻烧白云石或改渣剂来稠渣,稠渣后倒掉1/3再进行溅渣。
6、在钢水没出尽或溅渣发现炉口钢花很严重时,但炉况又很差时,溅渣枪位必须比正常高200mm以上,并且通过调渣来把渣子溅干。
二、溅渣操作要点1 、调渣工艺及要求调渣工艺是指在炼钢结束后,通过炉口观察炉渣状况,判定炉渣是否适宜溅渣。
如果炉渣过于稀,应加入少量改渣剂调整炉渣,增强炉渣的黏稠度,如果炉渣过热度高,炉渣稀,流动性良好,应加入少量轻烧白云石降低熔渣温度,提高炉渣黏度,使之更适宜溅渣的操作工艺。
(1直接溅渣工艺:即以炼钢过程中调整炉渣为主,炼钢后的渣较好适合溅渣基本不进行调渣,而直接进行溅渣操作。
要求铁水及原燃料条件比较稳定,吹炼平稳,终点控制准确,出钢温度低,终渣较好,适合出钢[C]>0.10%,出钢<1660℃的炉次。
(2出钢后调渣工艺:即在炼钢结束后,根据炉渣状况适当加入少量改渣剂或轻烧白云石用以降低炉渣过热度,提高炉渣黏度,改善炉渣的渣系使溅渣层更耐高温和侵蚀。
转炉车间溅渣操作要点11.19

转炉车间溅渣操作管理制度针对目前各班溅渣操作不统一,不能正确的通过溅渣来维护炉子,造成炉子频频告急,给厂部和车间带来极大的工艺事故和安全事故隐患,通过这几个月来对炉前工艺操作和终点控制情况,特对溅渣作出下规定:一、溅渣条件1、钢水必须出尽炉长、必须炉炉关注后大面的情况,不能出现凹坑或不平,必须观察出钢口位置高低,确保出钢口不高于后大面,保证每炉钢钢水都出尽,(如有钢水出不完的现象,跟班技术员、作业长、炉长必须在3炉钢内处理好)保证炉渣的可溅性。
2、在出钢过程中,炉长、操枪工必须从炉后观察炉内炉渣情况,炉长需及时指导操枪工的调渣密度和用量,确保渣子不调死,保证溅渣时间和效果,并指导自己下一炉的化渣枪位和方法。
3、操枪工必须确定有正常的工作氮压和流量,确保溅渣过程效果。
4、值班长必须保证炉后有充份的丢补料,每炉钢保证在出钢过程中向炉内加入10-15包的丢补料(30kg)(遇渣很粘时,可以少丢或不丢)。
5、遇拉后吹严重时,操枪工必须先加入轻烧白云石或改渣剂来稠渣,稠渣后倒掉1/3再进行溅渣。
6、在钢水没出尽或溅渣发现炉口钢花很严重时,但炉况又很差时,溅渣枪位必须比正常高200mm以上,并且通过调渣来把渣子溅干。
二、溅渣操作要点1 、调渣工艺及要求调渣工艺是指在炼钢结束后,通过炉口观察炉渣状况,判定炉渣是否适宜溅渣。
如果炉渣过于稀,应加入少量改渣剂调整炉渣,增强炉渣的黏稠度,如果炉渣过热度高,炉渣稀,流动性良好,应加入少量轻烧白云石降低熔渣温度,提高炉渣黏度,使之更适宜溅渣的操作工艺。
(1)直接溅渣工艺:即以炼钢过程中调整炉渣为主,炼钢后的渣较好适合溅渣基本不进行调渣,而直接进行溅渣操作。
要求铁水及原燃料条件比较稳定,吹炼平稳,终点控制准确,出钢温度低,终渣较好,适合出钢[C]>0.10%,出钢<1660℃的炉次。
(2)出钢后调渣工艺:即在炼钢结束后,根据炉渣状况适当加入少量改渣剂或轻烧白云石用以降低炉渣过热度,提高炉渣黏度,改善炉渣的渣系使溅渣层更耐高温和侵蚀。
转炉炼钢中留渣技术的原理及应用

2.3留渣安锂 近年来,随着我国转炉炼钢技术不断发展和完
善,由于顶底复合吹炼、溅渣护炉等一系列的工艺出 现之后,能有效地解决喷溅问题。对于渣循环来说, 它能够带来良好的经济效益,从单扎法中衍生出各 种各样的操作工艺,自从留渣技术应用之初,要考虑 到它自身的安全,采取留渣操作之后进入废钢以后,
间,这对前期脱离有着积极的推动作用,经过反复的 实践研究,其中影响脱离效率撮主要的因素就在于 物质的酸碱度和炉渣的含量,避免炉渣中氧化铁过 多,产生的喷溅,必须要确保它的游离氧含量大于 900x10电科学的调整留渣含量叫 32稳定留渣量
对于绝大部分的炼钢厂来说,冶炼效果和留渣 量的稳定性,两者密切相关。如果炉渣发泡过稀,此 时可以使用氮气进行溅渣 ,能有效的控制问题的发 生,进而实现渣量稳定控制。我国首先使用的是
钢工艺实践[J].新疆钢铁,2018(2):26-30.
(编辑:苗运平)
(下转第116页)
・116・
.山酉肖金 E—mail:sxyjbjb@
第44卷
问题根源,实施改进措施。
3结论 1) 棒材劈头堆钢主要由钢坯质量问题引起(偏
析、夹杂)。
2) 钢坯内裂属于铸造缺陷,但与冶炼时成分相关。 3) 冶炼时应避开包晶点,可以有效避免偏析、 内裂。
4) 提高钢中镒硫比例可防治方坯内裂。 5) 轧制过程中,粗轧岗位密切盯钢,尽量及时处 理钢质问题。
6 )年修时,对轧机的轧制线对正,跟换更耐磨的
3、5架导卫衬板。 7)适当调大2、4机架导卫扭转角。
参考文献
[1 ]王凯.降低高线粗轧机轧辐轴承消耗的措施[J] •轧钢,2006,23
转炉冶炼操作技巧

吹炼过程发现喷溅迹象,立即加少量白灰压喷,若喷溅大得不到缓和必须及时提枪喊开周围人员,缓慢倒渣。
然后加入≥3吨白灰稠渣,并先降枪后开氧。
留渣操作,因为所留渣中有大量的氧化铁,应该不会容易返干。
但是,因为吹炼前期有大量氧化铁,前期为防喷溅应该低枪位操作,如果中期枪位不做改变,提高会出现返干炉渣返干:是吹炼中期由于碳氧剧烈反应,炉渣中(FeO)降低,致使炉渣中2CaO.SiO2、CaO等高熔点的物质析出,炉渣变稠,这一现象称之为炉渣返干。
在吹炼过程中,因氧压高,枪位过低,尤其是在碳氧化激烈的中期,(TFe)含量低导致熔渣高熔点矿物的析出,造成熔渣黏度增加,不能覆盖金属液面的现象。
TFe即为全铁的意思。
上面说的是一部分,实际上Si,Mn反应期结束后..说说办法吧:提提枪,让FeO上来点...返干一般在冶炼中期(碳氧化期)的后半阶段发生,是化渣不良的一种特殊表现形式。
冶炼中期(碳氧化期)的后半阶段正常火焰特征是:白亮,刺眼,柔软性稍微变差。
但发生返干的火焰现象特征为:由于气体循环不正常而使正常的火焰(有规律,柔和的一伸一缩)变的直窜,硬直,火焰不出烟罩;同时由于返干炉渣结块成团未能化好,氧流冲击到未化的炉渣上面而发出刺耳的怪声;又是还有看到金属颗粒喷出。
有以上现象发生,说明炉渣已经返干。
产生返干的处理方法:1)补加一定量的氧化铁皮,增加FeO的浓度含量;2)适当提高氧枪。
提高枪位使冲击面积相对扩大,也使FeO的浓度含量增加;3)适当提高氧枪的同时,适当调低吹炼氧亚,是吹炼时间延长,使FeO的浓度含量增加,达到改善炉渣流动性的目的,改善炉渣状况,达到消除返干的目的。
吹炼过程中怎样预防爆发性喷溅?根据爆发性喷溅产生的原因,可以从以下几方面预防:(1)控制好熔池温度。
前期温度不要过低,中后期温度不要过高,均匀升温,碳氧反应得以均衡的进行;严禁突然冷却熔池,消除爆发性碳氧反应的条件。
(2)控制(TFe)不出现聚积现象,以避免熔渣过分发泡或引起爆发性的碳氧反应。
8-转炉“留渣-双渣”少渣炼钢工艺实践
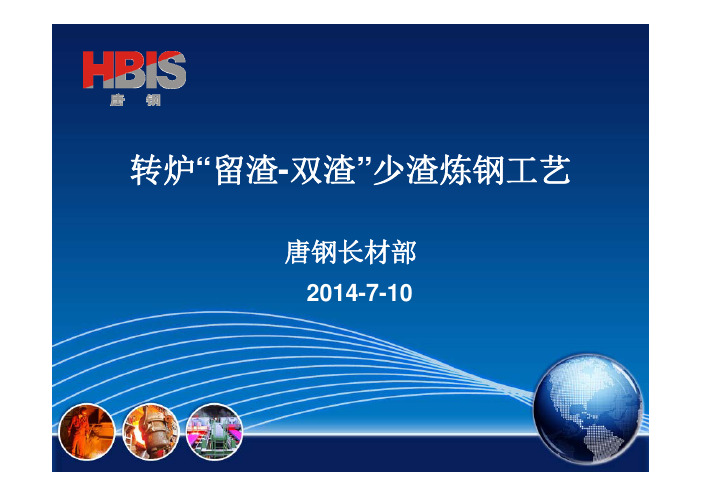
“留渣-双渣”工艺示意图
3.转炉脱磷影响因素
3.脱磷的基本原理
2[P]+5(FeO)+4(CaO)=4CaO·P2O5+5[Fe]
a 4CaO P2 O 5 a a
2 p 5 F eO
Kp
a
4 C aO
% 4CaO P2 O 5 4CaO P O 4 5 4 % P 2 f P2 % F e O 5 F e O % CaO C aO
演变:首钢公司从2011年开始,在首钢首秦和迁钢分别连续试验单
转炉“留渣-双渣”操作,取得较好的效果,目前首钢集团首钢长治, 首钢水钢均推广应用“留渣-双渣”少渣炼钢操作工艺,工艺相对成熟 。
1. 大幅度减少炼钢石灰、白云石等渣料消耗和炼钢渣量; 2. 可以利用出钢后炉渣的物理热,预热废钢; 3. 炼钢终渣含Tfe:15~25%,渣量减少可以降低钢铁料消耗; 4. 双渣倒渣的炉渣主要为脱磷阶段低碱度渣,自由CaO含量低, 可以简化炉渣处理; 5. 常规转炉出钢后留在炉内钢水随炉渣倒出,采用“留渣-少渣”工 艺终点少倒渣、出钢后不倒渣,可以提高钢水收得率。
FeO%
H11Mn2SiA
3A14306-1 3A14306-2 3B14615-1 3B14615-2 3C14935-1 3C14935-2 3A14301-1 3A14301-2 3B14603-1 3B14603-2 3B14612-1 3B14612-1
1 冶炼周期影响
类别 加料 脱磷期 双渣 脱碳期 终点 加废钢 兑铁时间 前期吹炼时间 氮气刹渣 倒渣时间 中后期吹炼 拉碳、补吹时间 等待终点成分 出钢时间 溅渣时间 总冶炼周期 留渣-双渣 1.7 2.4 4.5 2.1 3 8.8 2 1 2.5 2 30 单渣法 1.7 2.2 4.5 / / 8.7 2 1 2.5 2.5 25.1
转炉铸渣安全操作规程
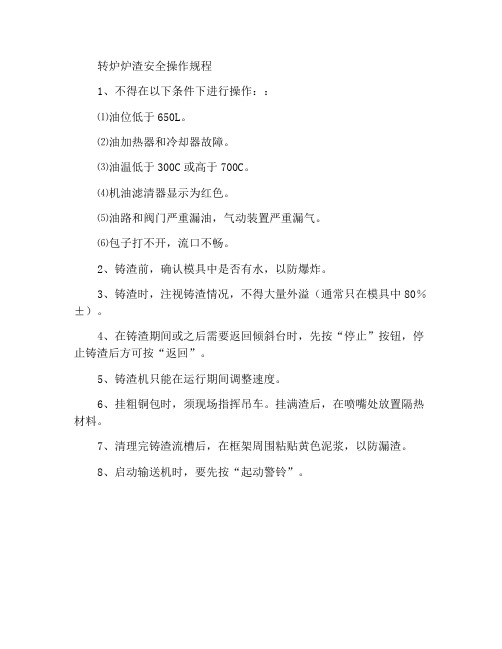
转炉炉渣安全操作规程
1、不得在以下条件下进行操作::
⑴油位低于650L。
⑵油加热器和冷却器故障。
⑶油温低于300C或高于700C。
⑷机油滤清器显示为红色。
⑸油路和阀门严重漏油,气动装置严重漏气。
⑹包子打不开,流口不畅。
2、铸渣前,确认模具中是否有水,以防爆炸。
3、铸渣时,注视铸渣情况,不得大量外溢(通常只在模具中80%±)。
4、在铸渣期间或之后需要返回倾斜台时,先按“停止”按钮,停止铸渣后方可按“返回”。
5、铸渣机只能在运行期间调整速度。
6、挂粗铜包时,须现场指挥吊车。
挂满渣后,在喷嘴处放置隔热材料。
7、清理完铸渣流槽后,在框架周围粘贴黄色泥浆,以防漏渣。
8、启动输送机时,要先按“起动警铃”。
底吹转炉钢中渣的形成机理与控制技术
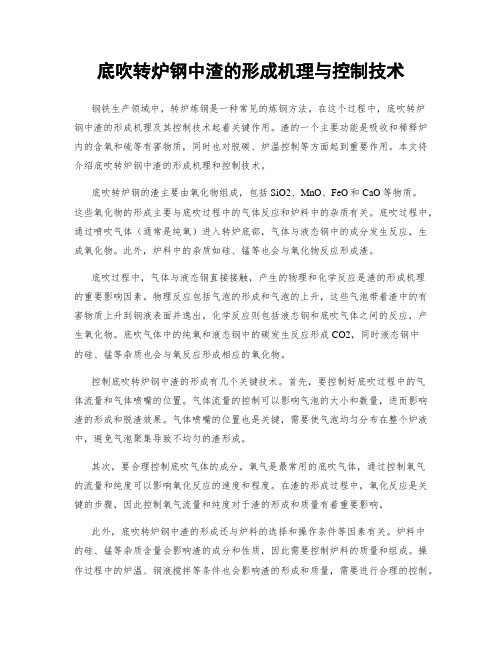
底吹转炉钢中渣的形成机理与控制技术钢铁生产领域中,转炉炼钢是一种常见的炼钢方法。
在这个过程中,底吹转炉钢中渣的形成机理及其控制技术起着关键作用。
渣的一个主要功能是吸收和稀释炉内的含氧和硫等有害物质,同时也对脱碳、炉温控制等方面起到重要作用。
本文将介绍底吹转炉钢中渣的形成机理和控制技术。
底吹转炉钢的渣主要由氧化物组成,包括SiO2、MnO、FeO和CaO等物质。
这些氧化物的形成主要与底吹过程中的气体反应和炉料中的杂质有关。
底吹过程中,通过喷吹气体(通常是纯氧)进入转炉底部,气体与液态钢中的成分发生反应,生成氧化物。
此外,炉料中的杂质如硅、锰等也会与氧化物反应形成渣。
底吹过程中,气体与液态钢直接接触,产生的物理和化学反应是渣的形成机理的重要影响因素。
物理反应包括气泡的形成和气泡的上升,这些气泡带着渣中的有害物质上升到钢液表面并逸出。
化学反应则包括液态钢和底吹气体之间的反应,产生氧化物。
底吹气体中的纯氧和液态钢中的碳发生反应形成CO2,同时液态钢中的硅、锰等杂质也会与氧反应形成相应的氧化物。
控制底吹转炉钢中渣的形成有几个关键技术。
首先,要控制好底吹过程中的气体流量和气体喷嘴的位置。
气体流量的控制可以影响气泡的大小和数量,进而影响渣的形成和脱渣效果。
气体喷嘴的位置也是关键,需要使气泡均匀分布在整个炉液中,避免气泡聚集导致不均匀的渣形成。
其次,要合理控制底吹气体的成分。
氧气是最常用的底吹气体,通过控制氧气的流量和纯度可以影响氧化反应的速度和程度。
在渣的形成过程中,氧化反应是关键的步骤,因此控制氧气流量和纯度对于渣的形成和质量有着重要影响。
此外,底吹转炉钢中渣的形成还与炉料的选择和操作条件等因素有关。
炉料中的硅、锰等杂质含量会影响渣的成分和性质,因此需要控制炉料的质量和组成。
操作过程中的炉温、钢液搅拌等条件也会影响渣的形成和质量,需要进行合理的控制。
对于底吹转炉钢中渣的形成机理和控制技术的研究,可以通过实验和数值模拟等方法来进行。
转炉留渣操作原因与注意事项

转炉留渣操作原因与注意事项
一、转炉留渣操作可以极大降低原料消耗,在吹炼初期可以快速成渣,有利于提高生产率,因而推广应用的潜力很大,但转炉留渣操作易发生大喷溅,限制了其应用。
二、分析认为需要注意以下几点,可以使留渣操作得到切实可行:
1、安全问题:兑铁时喷溅,因此所留的炉渣应确保:一是温度不能太高(W 1500C),二是溅渣时间必须保证,因为留渣操作一般与溅渣护炉并用,必要时要加入一定量的改质剂稠渣。
2、初期渣化的早,尤其是前期低温时易发生喷溅,随之而来发生返干现象,导致沾枪沾罩操作困难,应注意。
3、开吹时打火困难,可以采用前后摇炉或者先点吹30-40s 再加废钢的办法。
4、吹气渣化得早,前期渣来得迅速,低温炉渣容易从炉口涌出,特别是吹炼到
约 6 分钟时,压料后易“返干”,特别是Si 数低时更明显,而铁水Si 含量高时,过程渣不易控制易发生喷溅,当铁水Si 数超过0.5%时,喷溅率直线上升。
5、拉碳时火焰判断不准,易拉高碳,点吹时降碳量和升温速度相比单渣法要低,由于留渣造成热平衡不好计算且留渣火焰相比单渣法时火焰亮,温度控制难度加大,需要特别注意。
260t转炉留渣操作实践

a d i v l e t e — k n n e e y c n e e r n lz d a d t u h e h o o i a a a - n n ov d se l ma i g i d x s b o v r r a e a ay e n h s t e t c n l gc l p r me- — t
。 、
、
鞍 钢 技 术
AN GAN G TECH NOLOGY 总 第 3 4期 7
21 0 2年 第 2期 生
一产 ~ ~实 一
、践 ~ , 一
、. . ’
2 0t 炉 留渣 操 作 实践 6 转
牛 兴 明 , 文 飞 , 超 , 春新 , 国义 刘 李 魏 徐
Ni ng n Li e f i LiCha W e un i Xu Gu y u Xi mi g, u W n e , o, iCh x n, o i
(B y q a rn& S e l u sd ayC mp n f g n te o, t . a u u n Io te b i ir o a yo a gS e lC . Ld, S An
Y n k u 1 0 , i nn , hn ig o 0 7 La ig C ia) 1 5 o
Absr c :I fu n i g f c o s o h a ey o l g e i i p r to n t 60 tc n e t r t a t n e c n a tr n t e s f t fsa -r ma n ng o e a in i he 2 o v re l
中图分 类 号 : F 1 T 73
文 献标 识 码 : A
文章 编 号 :1 0 — 6 3 2 1 } 2 0 4 — 4 0 6 4 1 (0 2 0 — 0 2 0
留渣操作注意事项

转炉留查操作工艺注意事项
①每炉钢留渣量约为1.5~2.0吨左右,在溅渣时应把渣溅好,溅
渣时间应控制在150~240秒,保证炉渣挂到炉壁上,当炉口甩出的渣片由细小颗粒转变为较大块状物渣块时,提枪结束溅渣,即可进行下一炉加废钢、兑铁水操作;
②在加废钢前根据铁水质量准确计算出石灰、白云石、冷料等渣
料的加入量,控制好过程渣,保证转炉良好的运行状态;
③留渣操作的前期采用低枪位操作,减少头批料的加入量,中后
期适当提枪,同时跟进一定量的冷料来控制温度,从而达到准确控制终点的目的;
④在放完钢后认真观察,待炉内炉渣的黏度和流动性适宜时,直
接溅渣并进行严格的时间控制,把炉渣温度降至1500℃以下;
⑤为避免留渣量积累过多,坚持每隔4~5炉进行一次倒渣操作;
⑥为避免炉底上涨,每天必须测炉底零位,及时清除引起炉底上
涨的炉渣。
转炉清扫操作规程
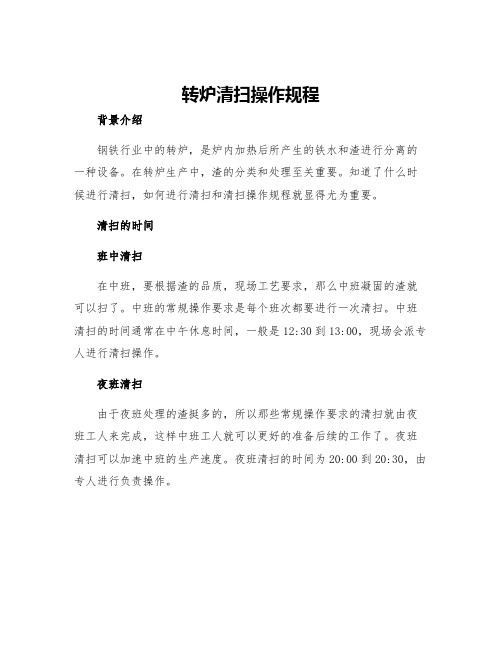
转炉清扫操作规程背景介绍钢铁行业中的转炉,是炉内加热后所产生的铁水和渣进行分离的一种设备。
在转炉生产中,渣的分类和处理至关重要。
知道了什么时候进行清扫,如何进行清扫和清扫操作规程就显得尤为重要。
清扫的时间班中清扫在中班,要根据渣的品质,现场工艺要求,那么中班凝固的渣就可以扫了。
中班的常规操作要求是每个班次都要进行一次清扫。
中班清扫的时间通常在中午休息时间,一般是12:30到13:00,现场会派专人进行清扫操作。
夜班清扫由于夜班处理的渣挺多的,所以那些常规操作要求的清扫就由夜班工人来完成,这样中班工人就可以更好的准备后续的工作了。
夜班清扫可以加速中班的生产速度。
夜班清扫的时间为20:00到20:30,由专人进行负责操作。
清扫的操作清扫前的准备1.确认转炉状况。
看炉子质量、炉口点火情况、转炉顶部状况等等。
2.关闭出渣阀门,注意将炉子里的“火嘴”盖好。
清扫操作1.打开转炉边缘盖板,提供通道。
2.打开炉口盖子,进入炉膛。
3.用铁铲去除渣锅中的大块渣块,小渣块可以留在锅中。
4.将渣坑中的渣桶、小铲子和长铲按要求摆放在炉口处,待清扫完成后进行收纳。
5.在现场派专人负责清理渣坑之外的渗渣地面。
清扫后的操作1.关闭炉口盖子。
2.将渣坑中的渣桶、小铲子和长铲回收并清洁。
3.通知现场工人就位。
开启出渣阀门,启动转炉,进行下一组浇铸。
清扫的注意事项1.几个班次之间必须进行清扫,不然对后续的生产、设备的使用会带来负面影响。
2.清扫前务必要对炉子状态进行检查,防止产生危险。
3.清理渣坑之外的渗渣地面需要专人进行负责。
总结转炉清扫操作规程的意义,在于为了确保生产能够顺畅地进行。
在操作过程中要注意对炉子状态进行检查,准备工作要充分做好,清扫操作要严格遵守要求。
只有这样,才能够提高生产的效率,避免不必要的损失,保障生产设备的正常运作。
转炉留渣操作工艺的优化
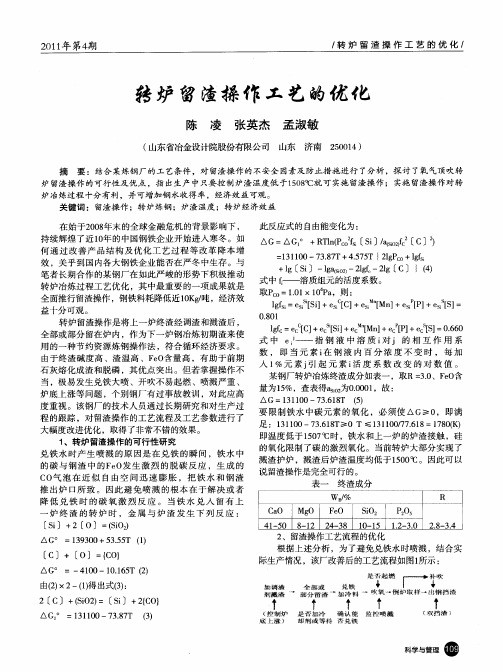
2 、留渣操作工艺流程 的优化 根据上述 分析 ,为了避免兑铁 水时喷溅 ,结合 实
际生产情况 ,该 厂改善 后的工艺流程如 图l 所示 :
魑 巍越 燃 广 — — 补峨 . -
g I
由() 一( 得 出式 ( : 2 ×2 1 ) 3 )
2【 +(i 2 = 【 i + {o CJ SO ) s J 2c l
2 1# 第4 0 1 - 期
/ 炉 留 渣 操作 工 艺 的 优 化 / 转
转 炉 留 渣操 作 工 艺 的优 化
陈 凌 张英杰 孟 淑敏
济南 20 1 504) ( 山东省 冶金设 计院股 份有限公司 山东
摘 要 :结合 某炼钢厂 的工艺条件 ,对 留渣操作 的不安全 因素及 防止措施 进行 了分析 ,探 讨 了氧 气顶吹转 炉 留渣操 作的 可行 性及优 点 ,指 出生产 中只要控 制炉渣 温度低 于 10 ℃ 就可 实施 留渣操作 ;实施 留渣操作 对转 58 炉 冶炼过程十分有利 ,并可增加 钢水收得率 ,经济效益 可观 。 关键词 :留渣操作 ;转炉炼钢 ;炉渣温度 ;转 炉经济效益
在始 于2 0 年 末 的全球 金融危机 的背景影 响下 , 08 持续辉煌 了近 1 年 的中国钢铁企 业开始进 人寒冬 。如 0 何 通 过 改 善 产 品结 构及 优 化 工 艺过 程 等 改 革 降本 增 效 ,关乎 到 国内各大钢铁 企业能 否在严冬 中生存 。与 笔者长期 合作 的某钢厂在 如此严 峻 的形势 下积极 推动 转 炉冶炼 过程工 艺优化 ,其 中最 重要 的一 项成果 就是 全 面推行 留渣操作 ,钢 铁料耗降低近 lK / ,经济效 O g吨 益 十分 可观。 转炉 留渣 操作是将 上一炉终 渣经调渣 和溅渣 后 , 全 部或部 分 留在 炉 内,作 为下一 炉钢冶炼 初期渣来 使 用 的一种 节约资 源炼钢操作 法 ,符 合循环 经济要求 。 由于终渣 碱度 高 、渣温 高 、F O 量高 ,有 助于前 期 e含 石灰 熔化成 渣和脱磷 ,其优 点突 出。但若 掌握操作 不 当 ,极 易发 生兑铁 大喷 、开吹不 易起 燃 、喷溅严重 、 炉底 上涨等 问题 ,个 别钢 厂有过事故 教训 ,对此应 高 度重视 。该钢 厂 的技术 人员通 过长期研 究 和对生产 过 程 的跟 踪 ,对 留渣操作 的工 艺流程及 工艺参 数进行 了 大幅度改进优化 ,取得 了非 常不错 的效果 。 1 、转炉 留渣操作 的可行性研 究 兑铁 水 时 产 生 喷溅 的原 因是 在 兑 铁 的 瞬 间 ,铁 水 中 的碳 与钢 渣 中 的F O 生 激 烈 的脱 碳 反 应 ,生成 的 e发 C 气 泡 在 近 似 自由 空 间 迅 速 膨 胀 ,把 铁 水 和 钢 渣 O 推 出炉 口所 致 。 因此 避 免 喷溅 的根本 在 于 解 决 或者 降 低 兑 铁 时 的碳 氧 激 烈 反 应 。 当铁 水 兑 人 留 有 上 炉 终 渣 的 转 炉 时 ,金 属 与 炉 渣 发 生 下 列 反 应 : [ i 2[ s ]+ O] = SO) (i 2
转炉定量留渣-溅渣-全留渣的工艺实践
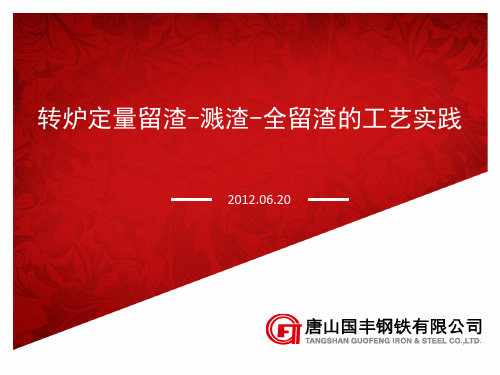
9.96——降低石灰消耗,kg/吨钢
0.4 ——石灰成本,元/kg 0.8 ——钢铁料消耗与留渣溅渣率相关系数
0.4 ——项目本身贡献系数
四、溅渣护炉效果与经济效益
4.3经济效益
通过应用转炉定量留渣溅渣技术研究成果后,溅渣效果较好,降低补 炉耐材消耗。 按降低耐材消耗0.49元/吨钢计算,年可降低耐材消耗效益: 200×1.53×0.24×0.4=29.38万元/年 其中: 200 ——年钢产量,万吨/年
8.4 ——降低钢铁料消耗,kg/吨钢
2.75 ——钢铁料成本,元/kg 0.7 ——钢铁料消耗与留渣溅渣率相关系数
0.4 ——项目本身贡献系数
四、溅渣护炉效果与经济效益
4.3经济效益
溅渣后可利用热态渣提高转炉化渣效果,同时,可充分提高转炉初期 渣碱度,从而提高转炉脱磷效果,达到降低石灰消耗的目的; 按按降低石灰消耗9.96kg/吨钢计算,年可降低石灰消耗效益: 200×9.96×0.4×0.8×0.4=254.97万元/年 其中: 200 ——年钢产量,万吨/年
渣制度、温度制度和终点控制的优化,成功解决传统全留渣工艺存在的 问题。
三、定量留渣-溅渣-全留渣的工艺实践
3.5定量留渣-溅渣-全留渣工艺制度
表9 定量留渣-溅渣-全留渣工艺制度
溅渣前渣量控制 渣量适中(根据 炉体侵蚀情况调 整适当转炉倾角 ,保证留渣量2~ 2.5)且稳定
溅渣压力 Mpa
溅渣时间 min
溅渣枪位(标尺) m
全留渣控制
1.1~1.3
1.5-2.5
1.5→0,交变溅渣 枪位
溅渣完毕全 部留渣
四、溅渣护炉效果与经济效益
4.1 溅渣护炉效果
表10 溅渣护炉效果对比
转炉留渣操作控制要点分析

转炉留渣操作规程
转炉留渣操作规程
一、操作步骤
1. 炉前倒炉时要倒掉1/3左右炉渣,控制留渣量在3t左右;
2. 根据终渣情况和出钢温度加改质剂溅渣,炉口渣粒粒度大于30mm为宜,吹氮时间必保2分钟以上;
3. 留渣量为溅渣后全部渣量,不倒渣;
4. 必须先加废钢,向后摇到出钢面30°;
5. 兑铁时兑铁量1/2以前要小流缓慢兑入,一半以后可正常兑入;
6. 开吹采用低枪位操作,枪位比正常枪位低100~200mm,留渣炉次石灰加入量为正常加入量的2/3,轻烧白云石为正常加入量的1/2;头批料加入2/3的石灰,轻烧白云石加入1 /3,起渣后(留渣操作第3、4炉后起渣时间在2分半左右)氧压比正常氧压低0.1~0.15 MPa,视情况加入其余渣料,最晚9分钟以前加完;
7. 可以连续留渣4炉,但最多不超过5炉,将炉渣倒净,换新渣。
二、留渣操作中职责划分
1. 炉长:负全责,控制好留渣量;
2. 一助手:负责溅渣操作,将炉渣温度降到1500℃以下,具体方法保证吹氮时间>2分钟,溅渣时氮气压力不低于1.0MPa;并根据终点情况确定改质剂加入量,目的溅完渣后炉渣成块状,加废钢后要向后摇炉,使铁块完全盖住炉渣;
3. 二助手:观察炉口渣粒情况,渣粒粒度太小或炉口看不到时要向前倒炉进行观察;兑铁时要保证炉前两侧无人,尤其是两炉中间门前也要无人,同时注意脚下要无杂物,站的位置靠近挡墙,以刚好看见炉口为宜。
三、以下情况严禁留渣操作
1. 铁水Si>0.70%;
2. 未溅渣炉次;
3. 氮气压力低,溅渣不正常的炉次;
4. 炉内剩钢炉次;
5. 下一炉测枪位炉次;
6. 其它异常情况,没有把握的炉次;。
转炉炼钢中留渣技术的原理及应用分析

转炉炼钢中留渣技术的原理及应用分析发布时间:2021-11-17T02:43:17.083Z 来源:《中国科技人才》2021年第22期作者:郑信彬[导读] 伴随着转炉炼钢技术的不断升级,急需引进新技术强化钢渣回收利用,减少炼钢产生的能耗和污染。
基于此,对转炉炼钢中留渣技术原理展开了分析,并对技术应用要点进行了探究,发现需要通过开展工艺试验合理确定脱磷效率、留渣量等各项参数,确保技术应用取得理想效果。
郑信彬新疆天山钢铁巴州有限公司新疆 841300摘要:伴随着转炉炼钢技术的不断升级,急需引进新技术强化钢渣回收利用,减少炼钢产生的能耗和污染。
基于此,对转炉炼钢中留渣技术原理展开了分析,并对技术应用要点进行了探究,发现需要通过开展工艺试验合理确定脱磷效率、留渣量等各项参数,确保技术应用取得理想效果。
关键词:转炉炼钢;留渣技术;原理分析引言:作为国家重要的基础产业,钢铁工业在发展过程中一直存在资源消耗量多、废弃物排放量大等问题,不利于行业可持续发展。
在国内产钢量中,转炉炼钢占据较大比重,每年需消耗上千万吨石灰石和生白云石,产生的钢渣也数以千万计,造成资源消耗严重的同时,给环境发展带来了不利影响。
引入留渣技术开发新工艺,可以解决上述问题,加速产业转型升级。
1转炉炼钢中留渣技术的原理分析在转炉炼钢期间,钢渣密度比钢水小,将漂浮在钢水之上。
在转炉倾至20~35°时,液面漫过出钢口前钢渣将先流入钢包,出渣量占总体20~30%,属于前期渣[1]。
出钢后,由于钢水产生涡旋,将表面钢渣吸入,产生30%出渣量。
全部钢水倒入后,最后流出的钢水下渣量较大,出渣量达到40~50%,属于终渣,需及时摇起转炉结束出钢。
由于钢渣中含有的磷、硫等元素将给钢材性能带来较大影响,所以需加强下渣量控制,避免过多钢渣进入钢包,减少钢水精炼时间和铁合金加入量,达到提高效率和节约成本的双重目标。
运用留渣技术,需要将上一炉约2/3终渣留在炉内,对铁液加入废钢。
转炉炼钢中留渣技术的原理及应用杨正府

转炉炼钢中留渣技术的原理及应用杨正府发布时间:2021-09-26T07:45:34.951Z 来源:《防护工程》2021年15期作者:杨正府[导读] 转炉留渣法炼钢技术的普及和推广应用,为冶炼技术发展做出了极大的贡献。
在明确技术应用方法和工艺的基础上,做好对技术的创新与完善,将会进一步提升留渣冶炼技术应用价值。
柳钢转炉炼钢厂广西壮族自治区柳州市 545002摘要:转炉留渣法炼钢技术的普及和推广应用,为冶炼技术发展做出了极大的贡献。
在明确技术应用方法和工艺的基础上,做好对技术的创新与完善,将会进一步提升留渣冶炼技术应用价值。
关键词:转炉炼钢;留渣技术;脱磷引言在钢铁行业降本增效大背景下,转炉炼钢留渣法作为一种能够显著降低辅料消耗、降低钢铁料消耗的技术,使得炼钢生产成本得到了切实的控制和降低,并且提升了生产效率。
随着钢铁工业技术日益向精细化发展,转炉留渣法炼钢技术应用效果也越来越明显,更多的炼钢企业和技术人员愿意挖掘这一技术的潜在应用价值,对转炉留渣法炼钢技术进行不断创新和完善,进一步拓展该技术的使用范围。
1 转炉炼钢留渣技术原理转炉留渣法技术原理:将上一炉部分终渣留在炉内,溅渣护炉后,作为下一炉初渣,利用其高温,高碱度,高T.Fe以及含有MgO的碱性渣特点,促进石灰轻烧快速熔化成渣和前期脱磷,从而降低熔剂消耗,降低生产成本。
通过大规模工业试验和对转炉脱磷过程热力学、动力学分析,得到转炉铁水“三脱”预处理各工艺参数和如下主要结论:(1)转炉铁水脱磷效果决定于采用的脱磷工艺,经过工业实践:低碱度高FeO渣脱磷率为55.4%,中高碱度高FeO渣脱磷率为83.4%,中高碱度低FeO渣脱磷率为86.4%。
三种方案相比,中高碱度低FeO渣脱磷效果好、铁损低,应是脱磷工艺的首选方案。
(2)炉渣碱度是提高脱磷率的关键,炉渣碱度增大,脱磷率增加。
(3)在相同炉渣碱度条件下,随脱碳量增加,脱磷率增大;说明炉渣的脱磷能力决定了熔池中C.P平衡关系,在相同熔池C条件下,炉渣碱度越高,与C平衡的P越低。
钢铁冶炼中的转炉钢渣处理技术

钢铁冶炼中的转炉钢渣处理技术钢铁冶炼是重工业生产中的重要环节之一,其产生的钢渣处理技术对整个工业链的环保安全和经济效益都有着重要影响。
在钢铁冶炼过程中,转炉钢渣处理技术是一种常见的处理方式,本文将对转炉钢渣处理技术进行详细介绍。
一、转炉钢渣生成原因钢铁冶炼过程中,将生铁和废钢放入转炉中进行冶炼,转炉中加入的生料在高温下熔融,氧化生成气体和钢渣。
钢渣是指在钢铁冶炼过程中,从熔炼金属中分离出来的杂质物质,它是熔体和熔渣中的一部分物质。
而转炉钢渣则是指在转炉冶炼过程中产生的钢渣。
二、转炉钢渣组成以及处理方式转炉钢渣主要由氧化物和还原物质组成,包括氧化铁、氧化硅、氧化钙、氧化镁、氧化铝等,还有少量的碳酸盐、硅酸盐、氧化钾、氧化钠等。
不同氧化物的含量和比例不同,对应着钢渣的不同性质。
转炉钢渣处理技术主要包括常规方法和新型方法。
常规方法包括混合熔炼、渣铸、风冷、半干法处理、干法处理等,这些处理方法主要是通过钢渣的物化性质差异,采用相应的方法将其分离,保留其中有用的物质。
渣铸方法是把热钢渣倒入浇铸模型中,冷却后从模具中取出,得到经过初步分离的钢渣块。
这种处理方法不仅可以将有用的物质得到回收利用,还可以减少运输和处理的成本。
风冷方法则是将熔融的钢渣放入钢渣散落区内,通过冷却吹风使其迅速冷却硬化并散落。
这种方法具有成本低、空间占用少、对环境污染小等特点,但处理效率较低。
半干法处理和干法处理是化学方法,将熔融的钢渣加入反应器中,加入石灰石等化学剂,使钢渣成为固态。
这种方式不仅可以减少钢渣的体积,还可以回收其中的有价值的物质。
三、传统转炉钢渣处理存在的问题虽然传统转炉钢渣处理技术在一定程度上解决了钢渣处理的问题,但其存在着许多问题,主要表现在以下几个方面:1、难以满足环保要求。
传统的钢渣处理方法,往往会对环境造成一定的危害,例如渣铸处理方式会在周围环境中产生大量灰尘和噪音,而风冷处理方式则会对空气产生一定的污染。
这种处理方式对环境造成的危害大大降低了其应用范围和市场竞争力。
转炉留渣操作原因与注意事项
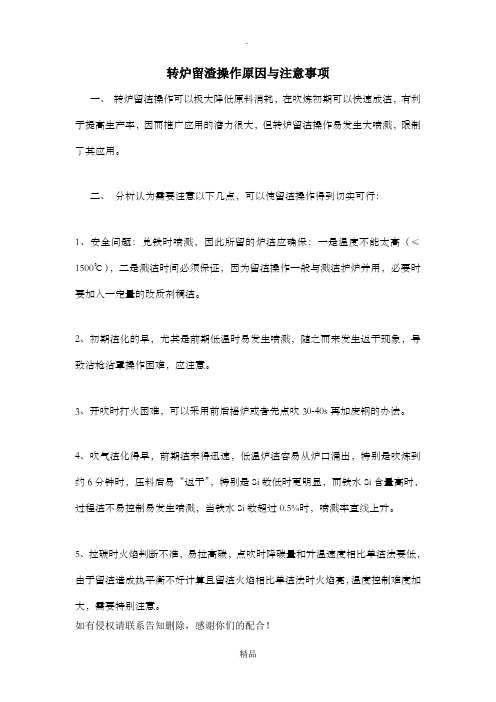
转炉留渣操作原因与注意事项
一、转炉留渣操作可以极大降低原料消耗,在吹炼初期可以快速成渣,有利于提高生产率,因而推广应用的潜力很大,但转炉留渣操作易发生大喷溅,限制了其应用。
二、分析认为需要注意以下几点,可以使留渣操作得到切实可行:
1、安全问题:兑铁时喷溅,因此所留的炉渣应确保:一是温度不能太高(≤1500℃),二是溅渣时间必须保证,因为留渣操作一般与溅渣护炉并用,必要时要加入一定量的改质剂稠渣。
2、初期渣化的早,尤其是前期低温时易发生喷溅,随之而来发生返干现象,导致沾枪沾罩操作困难,应注意。
3、开吹时打火困难,可以采用前后摇炉或者先点吹30-40s再加废钢的办法。
4、吹气渣化得早,前期渣来得迅速,低温炉渣容易从炉口涌出,特别是吹炼到约6分钟时,压料后易“返干”,特别是Si数低时更明显,而铁水Si含量高时,过程渣不易控制易发生喷溅,当铁水Si数超过0.5%时,喷溅率直线上升。
5、拉碳时火焰判断不准,易拉高碳,点吹时降碳量和升温速度相比单渣法要低,由于留渣造成热平衡不好计算且留渣火焰相比单渣法时火焰亮,温度控制难度加大,需要特别注意。
如有侵权请联系告知删除,感谢你们的配合!。
转炉造渣制度概要
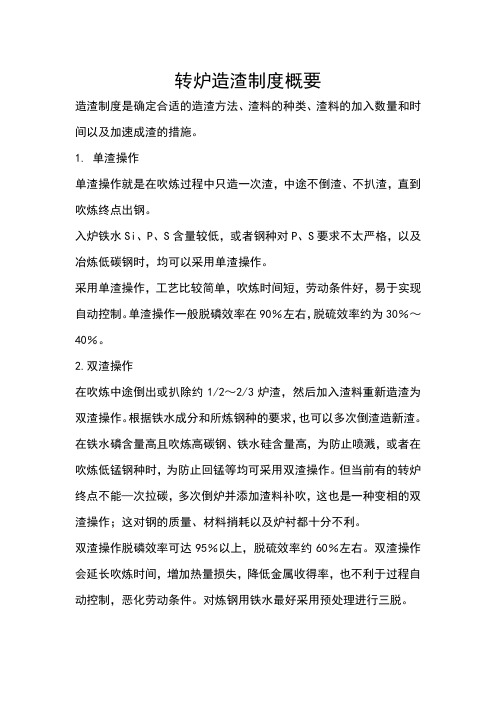
转炉造渣制度概要
造渣制度是确定合适的造渣方法、渣料的种类、渣料的加入数量和时间以及加速成渣的措施。
1. 单渣操作
单渣操作就是在吹炼过程中只造一次渣,中途不倒渣、不扒渣,直到吹炼终点出钢。
入炉铁水Si、P、S含量较低,或者钢种对P、S要求不太严格,以及冶炼低碳钢时,均可以采用单渣操作。
采用单渣操作,工艺比较简单,吹炼时间短,劳动条件好,易于实现自动控制。
单渣操作一般脱磷效率在90%左右,脱硫效率约为30%~40%。
2.双渣操作
在吹炼中途倒出或扒除约1/2~2/3炉渣,然后加入渣料重新造渣为双渣操作。
根据铁水成分和所炼钢种的要求,也可以多次倒渣造新渣。
在铁水磷含量高且吹炼高碳钢、铁水硅含量高,为防止喷溅,或者在吹炼低锰钢种时,为防止回锰等均可采用双渣操作。
但当前有的转炉终点不能—次拉碳,多次倒炉并添加渣料补吹,这也是一种变相的双渣操作;这对钢的质量、材料捎耗以及炉衬都十分不利。
双渣操作脱磷效率可达95%以上,脱硫效率约60%左右。
双渣操作会延长吹炼时间,增加热量损失,降低金属收得率,也不利于过程自动控制,恶化劳动条件。
对炼钢用铁水最好采用预处理进行三脱。
3. 留渣操作
留渣操作就是将上炉终渣的一部分留给下炉使用。
终点熔渣的碱度高,温度高,并且有一定(TFe)含量,留到下一炉,有利于初期渣尽早形成,并且能提高前期去除P、S的效率,有利于保护炉衬,节省石灰用量。
采用留渣操作时,在兑铁水前首先要加石灰或者先加废钢稠化冷凝熔渣,当炉内无液体渣时方可兑入铁水,以避免引发喷溅。
溅渣护炉技术在某种程度上可以看作是留渣操作的特例。