降低钢铁料消耗实践.
降低120t转炉钢铁料消耗生产实践
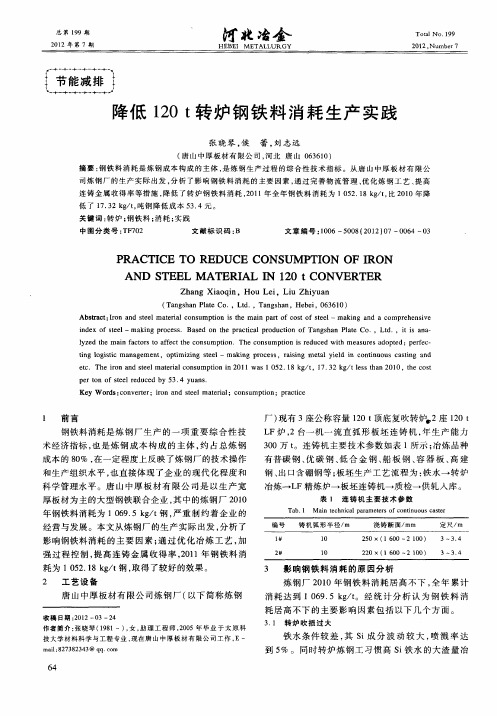
奖惩 考核 调动职 工 的积极 性 。
4 2 优 化 炼 钢 工 艺 .
4 2 1 调 整 炉 料 结 构 ..
转炉 的装 入量 为 10~10 t而铁 水量 仅 为 10 4 5 , 2
( ) 据 浇 铸 周 期 确 定 转 炉 装 入 量 , 装 入 量 1根 将 由原来 10~10t 整为 10~10t 4 5 调 3 4 。之 后炼 铁 厂
21 0 0年 连铸 机高 温钢 事故 占总事 故 率 的 6 % 以上 , 0
由于事故 多发 导致 回浇 余钢 水 、 连铸坯 甩废 量 增 多 。
同 时 由于切割 割 嘴 更换 不 及 时 , 压不 合 理 致 使 割 氧 口较 大 , 大大 降低 了钢 水收 得率 。
3 4 物 流 管理 不 完 善 .
机 的浇铸周 期 为 3 6~3 n 炉 机 生 产 不 匹配 。 为 8 mi , 缓 解 生产 节奏 的影 响 , 采取 了“ 高温 慢 铸 ” 的操 作 思
1 5t以满足 一次 装铁 的需 求 。与 公 司 技术 科 等 相 2 , 关部 门配 合 , 定铁 水成 分及 温度控 制 , 炼 钢铁 水 稳 供
ma l 8 7 8 3 3@ q c r i: 2 3 2 4 q. o n
铁 水 条件较 差 , s 成 分 波 动 较 大 , 其 i 喷溅 率 达
到 5 。 同时转炉炼 钢工 习惯 高 S 铁水 的大 渣量 冶 % i
河 北 冶金 Leabharlann 21 0 2年 第 7期
炼 , 到低 s 铁水 时易 因热 量 不 充 足 、 作不 当造 遇 i 操 成 严重 后 吹 , 渣 中氧化 铁含 量大 增 , 加 了铁损 。 使 增
影响钢铁料消耗主要原因学习和总结

影响钢铁料消耗主要原因学习和总结影响钢铁料消耗主要原因学习和总结在炼钢生产中,钢铁料消耗是炼钢生产总成本的关键,而转炉冶炼过程的钢铁料消耗在总的钢铁料消耗中也占有很大的比例。
因此抓好转炉冶炼的钢铁料成本对控制总成本起关键性的作用。
通过改进原料结构和炉前冶炼工艺,采用少渣炼钢工艺,控制喷溅,减少倒渣带钢减少后吹,降低吹损,提高一次拉碳率等有效措施来降低钢铁料消耗。
进7月份以来我对影响我车间钢铁料消耗的主要原因学习和总结如下;影响转炉钢铁料消耗的主要原因影响转炉钢铁料消耗的主要因素包括炉渣中的铁损失、降低吹损、喷溅及倒渣带钢的铁损失等。
为了减少转炉炼钢拉碳时出现的碳低磷高和碳高磷低成分不合后吹的造成吹损,降低钢铁料损耗,应采取合理的原料结构,稳定的装入量及合适的渣量和稳定的操作。
1.优化入炉原料结构在合适的用量范围内,通过增加矿石和铁皮球的用量,也就说的含铁冷料,可有效地减少铁水的消耗,从而降低钢铁料消耗,因此在实际操作中可加大含铁冷料的加入。
因为吹炼前期为满足前期脱磷条件,需要大量的氧化铁,吹炼中期为避免反干,要求渣中含有适当的氧化铁,增加矿石消耗的工艺措施,降低钢铁料消耗。
实际生产中,由于铁皮球中SIO2含量较高,因此使用铁皮球产生的渣量大,造成渣中铁消耗较高,但是价格相对便宜,也可以少量食用。
为了尽量增加矿石的用量,提高矿石还原效果和减少吹炼过程中矿石加入量过多对冶炼稳定性的影响,在实际生产中,根据矿石的反应程度,在吹炼前、中期全部加完,在保证化渣效果和避免喷溅的情况下尽量早加和均匀加入矿石,以保证矿石化渣还原时间和效果。
吹炼中期矿石应分批次少量加入,避免集中加入,导致积聚过多的氧化铁造成的喷溅;吹炼后期严禁加入矿石,避免矿石加入过晚造成还原效果差和钢水的氧化性强脱氧不到位和对脱氧合金化的影响。
2.减少喷溅,降低终渣氧化铁(1)控制好熔池温度,吹炼前期温度不要过低,并防止突然的温降,保持熔池均匀升温,碳氧反应均衡进行,避免碳氧反应失衡造成爆发性的喷溅。
影响钢铁料消耗因素探讨与实践

2017年第2期LYS Science-Technology& Management・8・影响钢铁料消耗因素探讨与实践一炼轧厂黄伟豪摘要本文对影响钢铁料消耗的因素进行了具体分析。
通过改进入炉料结构、优化造渣工艺、减少转炉喷溅率、加强内部含铁资源回收,有效提高了转炉钢水收得率,降低了钢铁料消耗。
1 引言目前钢铁行业竞争日益激烈,钢材利润空间急剧压缩,为应对市场带来的挑战,必须采取措施来降本增效。
而钢铁料消耗占转炉炼钢生产成本的70%以上,且钢铁料指标的好坏直观体现了该厂综合技术水平、管理水平的高低,它关系到炼钢厂以挖潜增效为主的竞争活动的成败,因此降低钢铁料消耗对炼钢企业来说显得尤为迫切。
本文综合分析了涟钢一炼轧厂转炉线的实际生产情况,提出针对性的改进措施,付诸实施后,钢铁料消耗取得了明显进步。
2 炼钢线生产现状涟钢一炼轧厂转炉线现有公称容量100t氧气顶底复吹转炉3座,铁水预处理一座,吹氩站3座,2台6机6流弧形连铸机。
年产钢390万吨。
主要品种有HRB系列、CSP低碳钢、CSP普碳钢、低碳合金钢、高碳高强钢及其它新钢种。
3 钢铁料消耗计算口径与现状3.1 钢铁料消耗计算方法钢铁料消耗(kg/t)=入炉钢铁料(kg)÷合格钢产量(t);钢铁料消耗量(t)=铁水量(t)+生铁量(t)+废钢量(t)+矿石(t);废钢从来源上分为外购废钢和自产废钢,加生铁是由于炼钢能力大于高炉生产能力,铁水量不足,靠采购生铁块来发挥转炉产能。
3.2 钢铁料消耗现状2016年一炼轧厂的钢铁料实物消耗1079.31kg/t,较往年明显好转。
4 影响钢铁料消耗的主要因素涟钢6#高炉处于炉役后期,铁水质量较差,入炉铁水渣量、温度、成分波动大,转炉炉容比小,受入炉原材料质量以及入炉料结构的影响较大。
转炉冶炼过程易喷溅、喷溅渣含铁量大,熔剂消耗高,终渣TFe高,终点温度、成分控制较差导致回炉与中断连铸次数较多,过吹、高温现象较严重;连铸操作稳定性差,铸余钢水流失多,严重影响着钢铁料消耗的降低。
降低炼钢钢铁料消耗的生产实践
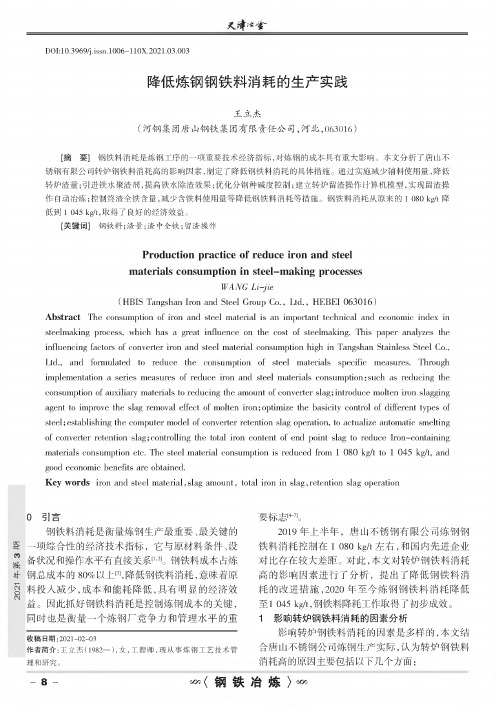
DOI:10.3969/j.issn.l006-110X.2021.03.003降低炼钢钢铁料消耗的生产实践王立杰(河钢集团唐山钢铁集团有限责任公司,河北,063516)[摘要]钢铁料消耗是炼钢工序的一项重要技术经济指标,对炼钢的成本具有重大影响。
本文分析了唐山不锈钢有限公司转炉钢铁料消耗高的影响因素,制定了降低钢铁料消耗的具体措施。
通过实施减少辅料使用量,降低转炉渣量;引进铁水聚渣剂,提高铁水除渣效果;优化分钢种碱度控制;建立转炉留渣操作计算机模型,实现留渣操作自动冶炼;控制终渣全铁含量,减少含铁料使用量等降低钢铁料消耗等措施。
钢铁料消耗从原来的100kg//降低到1047kgt,取得了良好的经济效益。
[关键词]钢铁料;渣量;渣中全铁;留渣操作Production practice of reduce iron and steelmaterials consumption in steel-making processesWANG Li-jie(HBIS Tangshan Iron and Steel Group Co.,Ltd.,HEBEI063016)Abstract The conshmption of iron and steel material is an important technical and economic index in steelmaning process,which hns n grent inflpeccc on tde cost of steelmaning.This pneo analyzes tde inflpeccing factore ol convertee iron and sted material conshmption high in Tangshan Stainless Sted C o, Lte.,and formulatee te o C pc the ol sted materials sheOmc meassres.Thronph impmmectation a series meashres ol oduc iron and sted materiais cnshmphon:such as reeucing the conshmption ol anxiliaro materiais te reeucing the monut ol converter slaa;intronucc moltee iron slaggingaaeYg te irnpove the slaa omovet巳琏厲ol moltee O oc;optimize the basicitz control ol.0X11:types ol steel y estaniishing the computer monel ol converter retechon slaa oneration,te actualize antomatic smeltingol aonvertcr retention slaa/controlling the total iron contedi ol end poini slaa i reduce Iron-—ontaining materials consumption etc.The steel materiai conshmption is reduced from1080kg//e1045kgA,and goon economic beceCis are ontained.iron and steel material,slag amount,total iron in slag,retention slag operationKey words0引言钢铁料消耗是衡量炼钢生产最重要、最关键的一项综合性的经济技术指标,它与原材料条件、设备状况和操作水平有直接关系>4。
降低钢铁料耗的措施
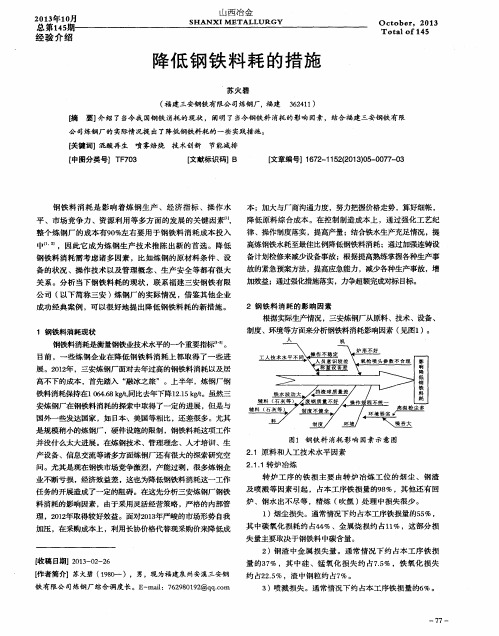
中“ ’ ,因此它成为炼钢生产技术推陈出新的首选 。降低
钢铁料 消 耗需 考虑 诸多 因素 ,比如 炼 钢的 原材料 条 件 、设
备的状 况 、操 作技术 以及 管理 概 念 、生产 安全 等都 有很 大
关 系 。分 析 当下钢铁 料 耗 的现状 ,联 系福 建三 安钢 铁有 限
2 0 1 3 年1 0 月
山西冶 金
SH A N X I M E T A LLU R G Y
总 第1 4 5 期・
经 验 介绍
Oc t obe r, 201 3 T ot a l of1 45
降 低 钢 铁 料 耗 的 措 施
苏 火 碧
( 福建三安钢铁有限公 司炼钢厂, 福 建 3 6 2 4 1 1 )
律、操作制度落实,提高产量;结合铁水生产充足睛况 , 提
高炼钢铁水耗 至最佳 比例 降低钢铁料消耗 ;通过加强连铸设 备计划检修来 减少设 备事故 ;根据提高熟练掌握各种生产事 故 的紧急预案方 法 ,提高应急能力 ,减少各种生产事故 ,增 加效益 ; 通过强化措施 落实 ,力争超 额完成对标 目 标。
【 摘 要】 介绍了当今我国钢铁消耗的现状 ,阐明了当今钢铁料消耗的影响因素,结合福建三安钢铁有限
公 司炼钢厂 的实际情 况提 出了降低 钢铁料耗 的一些 实践措 施。 【 关键词】混酸再 生 喷 雾焙烧 技术创新 节能减排
冲 图分类号】T F 7 0 3
【 文献标识码】 B
【 文章编号】 1 6 7 2 - 1 1 5 2 ( 2 0 1 3 ) 0 5 - 0 0 7 7 - 0 3
间。尤 其是现在钢铁市场竞 争激烈 ,产能过剩 , 很 多炼钢企 业不 断亏损 ,经济效益差 ,这也为降低钢铁料 消耗这一工作 任务 的开展造成了一定 的阻碍 。在这先分析三 安炼 钢厂钢铁 料消耗 的影响因素 ,由于采 用灵 活经营策略 , 严格 的内部管 理 ,2 0 1 2 年取得 较好效益 。面对 2 0 1 3 年严峻的市场 形势 自我 加压 ,在采购成本上 ,利用 长协价格代替现采购价 来降低成
转炉钢铁料消耗分析与对策

转炉钢铁料消耗分析与对策钢铁料消耗⼀般占转炉⽣产成本80%以上[1]。
降低钢铁料消耗不仅可以降低⽣产成本,⽽且有利于改善其它技术经济指标,是企业降低产品成本的有效⼿段之⼀[2]。
降低钢铁料消耗将有效降低各类废弃物的产⽣量,为开展清洁⽣产、发展循环经济创造良好条件。
钢铁料消耗涉及到原料、炼钢、连铸及管理等各⼯序或部门,影响因素较多,⽽各企业⽣产钢种、品种、原料质量、⼯艺装备、操作⽔平等均不同,因此分析时主要以定性为主。
⼆、影响钢铁料消耗的主要因素1.转炉钢铁料损耗概述转炉炼钢⽣产过程,由于氧化吹炼、切割、容器的倒运等,钢铁料(钢⽔、铸坯)均要受到不同程度的损耗,如表1所⽰。
摘要:对炼钢⽣产过程中影响钢铁料消耗的各种因素进⾏了分析研究,并提出了⼀些降低钢铁料消耗的措施。
关键词:转炉;钢铁料消耗;措施中图分类号:F403.7⽂献标识码:A序号123⽣产⼯序铁⽔预处理转炉(包括精炼)连铸合计影响因素前扒渣铁损、后扒渣铁损、渣中⾦属损失、喷溅等。
(碳、硅、锰等)化学烧损、钢渣中⾦属损失、喷溅、回炉钢、炉内剩钢等。
⼤包剩余、中包剩余、氧化损失、切头切尾、切缝损失、漏钢损失、废品、清理损失等。
损耗率/%0.5~1.55.8~12(⾦属料→钢⽔)1.5~4(钢⽔→合格坯)7.8~16.8(⾦属料→合格坯)表1转炉炼钢各⼯序钢铁料损耗汇总注:部分企业由于钢种、原料、⼯艺装备等条件所限,损耗率有较⼤出⼊。
2.转炉钢铁料损耗分析(1)铁⽔预处理。
铁⽔是转炉炼钢的主要原料,为了减轻转炉冶炼负担,⽬前已普遍采⽤铁⽔脱硫预处理⼯艺。
铁⽔脱硫处理的铁损主要发⽣在处理前后的扒渣带铁和处理过程中的喷溅及铁⽔倒运泼铁、沾铁等。
扒渣带铁与铁⽔⾃带的⾼炉渣和脱硫渣量成正⽐,其中脱硫渣量的⼤⼩与采⽤的脱硫粉剂有关。
例如,某⼚采⽤混合喷吹脱硫⼯艺和纯镁喷吹脱硫⼯艺,脱硫剂消耗分别为4kg/t 铁和0.3kg/t 铁,相应的渣量分别为4.64kg/t 铁和0.65kg/t 铁,扒渣铁损分别为2.09kg/t 铁和0.29kg/t 铁,并得出当粉⽓⽐≥100kg/m 3时,可使喷溅控制在1%以下,有效减少了铁⽔喷溅损耗。
炼钢生产线中降低钢铁料消耗措施及实践
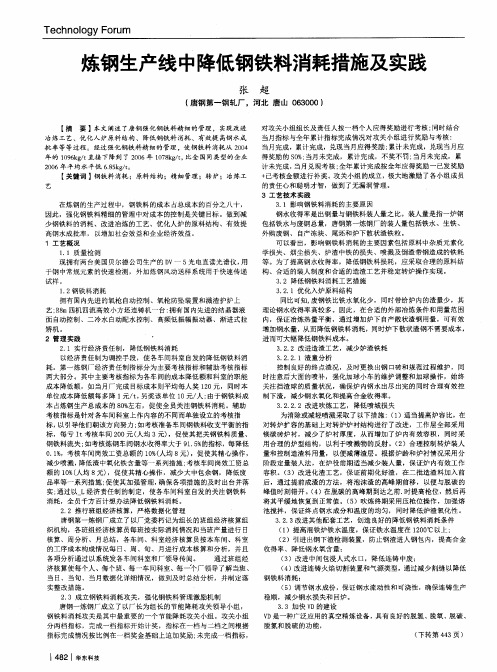
2.3 成 立 钢 铁 料 消耗 攻 关 ,强 化 钢 铁 料 管 理 激 励 机 制
唐钢一炼钢 厂成立 了以厂 长为组长 的节 能降耗攻关领导小组 ,
钢铁 料消耗攻关是其 中最重要 的一个节能 降耗攻关小组 。攻关小组
分 两 档 指 标 , 完 成 一 档 指标 开 始 计 奖 ,指 标 在 一 档 与 二 档 之 间 根 据
0.1%,考核车间岗效工资总额 的 10%(人均 8元),促使其精 心操作 ,
减少喷溅 ,降低渣中氧化铁含 量等一系列措施 :考 核车 间岗效工 资总
额 的 10%(人均 8元),促使其精 心操作 ,减少大 中包余钢 ,降低废
品率等一系列措施 :促使其加强管理,确保 各项措 施的及 时出台并落
本 占炼钢 生产 总成本 的 80%左右 ,促使全员关注钢铁料消耗。辅助
考核指标是针对各车 间科室上作 内容 的不 同而单独设立的考核指 标,以引导他们朝该方 向努力 :如考核准备车 间钢铁料收支平衡 的指
标,每亏 It考核车间 200元 (人均 3元),促使其把关钢铁料质量、
钢铁料流失 :如考核炼钢 车间钢水 收得率大于 91.5%的指标 ,每 降低
构、合适的装人制度和合适 的造渣工艺并稳定转炉操作实现 。
3.2 降低钢铁料消耗工 艺措施
3.2.1优化入炉原料 结构
同比可知,废钢铁比铁 水氧化 少,同时带给 炉内的渣量少 ,其
理论钢水收得率高较多。因此,在合适 的外部冶炼条件和用量范 围 内,保证冶炼热量平衡,通过增加 炉下 自产散状渣钢用量 ,可有效
包括铁水 与废钢总量 ,唐钢第一炼钢厂的装人量包括铁水、生铁、
外购废钢 、 自产冻块 、尾坯和炉下散状渣铁粒 。
“降低钢铁料消耗”获优秀成果奖

总 第 1 7期 9
员 50 0余 人参 加会议 。 0 为深人 学 习宣 传 贯 彻 国 务 院 《 量 发 展 纲 要 质 (0 1~ 0 0) , 力 推 进 全 省 群 众 性 质 量 管 理 活 2 1 22 》 大
动 的开 展 , 议 表 彰 了 10个 河 北 省质 量 管 理 活 动 会 0 优 秀班组 、0 1 0项 河 北 省 质 量 管 理 活 动 优 秀 成 果 和 质量 标兵 。 由文件 起草 人之一 国家 质检 总局 质量 管 理司 惠博 阳进 行解 读宣 贯 。
团将 引进 国 内外 先进 生产线 , 以高水准 、 高精 度 的 工 艺技术 开展 现代 化生 产与管 理 , 走绿色 环保 、 学 发 科
展 之 路 , 争 将 此 项 目建 设 成 元 氏 县 的 亮 点 工 程 。 力
元 氏县县 长陈联 记指 出 , 此项 目的开工 建设 , 将 进 必
步壮大 元 氏县 装备 制 造 业 整体 实 力 , 进 县 产 业 促
该项 目建 成 后 , 有 力 带 动 周 边 地 区 餐 饮 、 将 住
结构 调整 和优 化升级 。 宿、 物流等 行业 的发展 , 繁荣 经济 的 同时将 为 当地 在 提供 更 多就业 机会 。
顺 利 通 过 安 全 设 施 “ 同 时 ’ 收 三 ’ 验
1 9 6亿 元 , 缴税 金 4亿 元 。 0. 上
在开工 典礼 上 , 慧 明总经 理表示 , 北敬 业 集 李 河
举行 。李慧 明总 经 理 等集 团领 导 、 石家 庄 市 南 部 工
业 区管 委会 主任刘 春秋 、 氏县县 委书记 吴 时茂 、 元 县 长 陈联 记等领 导 及 我 集 团部 分 领 导 、 营 系统 员 工 经 参 加 了开工 仪式 。李 慧 明总 经 理在 典 礼 上致 辞 , 县
日钢120t复吹转炉降低钢铁料消耗实践
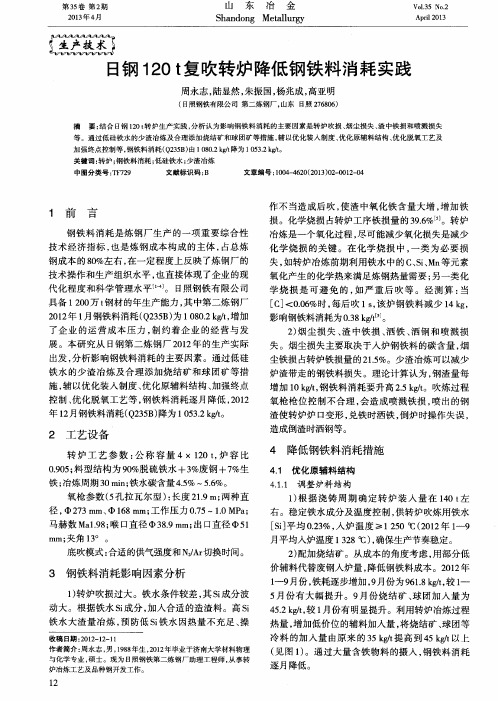
1 前
言
作 不 当造 成 后 吹 , 使渣 中氧化 铁 含量 大 增 , 增 加铁 损 。化 学烧 损 占转炉 工序 铁损 量 的 3 9 . 6 %日 】 。转 炉
2 ) 烟尘损失 、 渣 中铁 损 、 洒铁 、 洒 钢 和 喷 溅 损
代 化 程 度 和科 学管 理水 平 n 。 E l 照 钢铁 有 限公 司 具备 1 2 0 0 万t 钢材 的年 生产 能力 , 其 中第 二炼钢 厂
2 0 1 2 年1 月钢铁料 消耗 ( Q 2 3 5 B) 为1 0 8 0 . 2 k g / t , 增 加
等。通过低硅铁水 的少渣冶炼及合理添加烧结矿和球 团矿 等措施 , 辅 以优化装入制度 、 优 化原辅料结构 、 优化脱氧工艺及 加强终点控制等 , 钢铁料 消耗 ( Q 2 3 5 B ) 由1 0 8 0 . 2 k g / t 降为 1 0 5 3 . 2 k g / t 。 关键词 : 转炉 ; 钢铁料 消耗 ; 低硅铁水 ; 少渣冶炼
造成倒 渣时洒钢 等 。
2 工艺设 备
转炉 工 艺参 数 : 公 称 容 量 4×1 2 0 t , 炉 容 比 0 . 9 0 5 ; 料 型结 构为 9 0 %脱 硫 铁水 - 4 - 3 %废 钢 - 4 - 7 %生
铁; 冶炼周期 3 0 m i n ; 铁水碳 含量 4 . 5 % ~5 . 6 %。 氧枪 参 数 ( 5 孔拉 瓦 尔型 ) : 长度 2 1 . 9 1 T I ; 两 种直
4 降低 钢铁料消耗措施
转炉厂降低钢铁料消耗分析与对策

2 跟 踪调 查 结 果
为 准确 掌握 冶 炼 的铁水 和 钢铁 料消 耗情 况 ,
共 调 查 了 4个 横 班 计 1 6炉 。 图 l为 炼 钢至 连 0
成 投 产 以来 ,一直 致 力 于该 指 标 的 提 高 ,由 于 生 产规 模 、工 艺装 备受 设计 能力 的 限制 与 制 约 ,
G o H i a F n Qn z e H a g Hac u h o G agu n u a h n a igh n u n n h Z a u n y a s (ho u n I n& SelC . t. S ag a r o te o d) ,L
Ab t a t T e mea o s st a in f m l n i n o h o - l w o v  ̄e y tm o c si g s r c h tl l s i t r u o o mo t r f t e t p b o n c n e r s se t a t e o n sr n wa a ay e , a d h e o n e me s r s f r r d c n e b o n ls f c n e t r e h n i g t d a s n lzd n t c u tr a u e o e u i g t lwi g o s o o v r , n a cn h e
技
20 年泛 07 珠三角1省( 1 区)
炼 钢 连 铸 学 会 论 文 专 辑
转炉厂 降低钢铁料消耗分析 与对策
郭海 山 范 庆镇 黄汉初 赵光 远 ( 关 钢铁 集团有 限公 司 ) 韶
摘
要
分析 了顶 吹转 炉 系统铁 水 至 铸 坯 的金属 料损 耗情 况 ,并 提 出降低 转 炉 吹损率 、提高 钢
采用铁矿石替代废钢的炼钢工艺实践

轻烧白云石的热量消耗情况为 28 kg/t,在冶炼前期加完,并保持渣中 w(MgO)≥8%,以减少炉衬蚀损。 冶炼后期根据渣况和溅渣要求确定是否补加轻烧白云石,若渣稀则补加 300~500 kg。
原炼钢工艺中,每炉钢约需添加萤石等化渣材料 300 kg。采用铁矿石替代废钢工艺时,因(FeO)是氧化 剂,且能加速石灰的溶解,故冶炼过程中可不用添加萤石等化渣材料。
采用铁矿石替代废钢工艺的造渣操作要点可总结为:前期快速成渣,中期熔渣化透,后期终渣作黏。在 造渣过程中将温度调控结合起来,通过调整矿石加入的时间、批次进行化渣,通过调整枪位控制过程喷溅和 返干。
2.4 温度制度
根据具体情况,正确判断冶炼过程中的温度变化情况,及时调整铁矿石的用量。开吹时加入铁矿石 2 t 左右,占加入总质量的 50%~60%,以取代废钢的冷却作用。冶炼过程的中后期,分批次加入铁矿石,每 批次加入质量不大于 500 kg,否则会造成熔池温度下降过多、渣料结团、石灰块表面形成一层金属凝壳而推 迟成渣。冶炼过程的中后期,铁矿石具体加入方法为:在硅及锰的氧化基本结束、头批渣料已经化好、碳焰 初起的时候(开吹约 5 min)加入 2 批铁矿石,每批约加入 0.5 t。在吹炼中期(开吹约 8~10 min)返干或熔 池温度高时加入 1 批铁矿石,在终点前 3 min 左右,根据熔池温度情况加入铁矿石 1 批,以调整熔池温度。 吹炼末期不再加入铁矿石,主要进行升温和均匀温度工作。
降低钢铁料消耗的探索
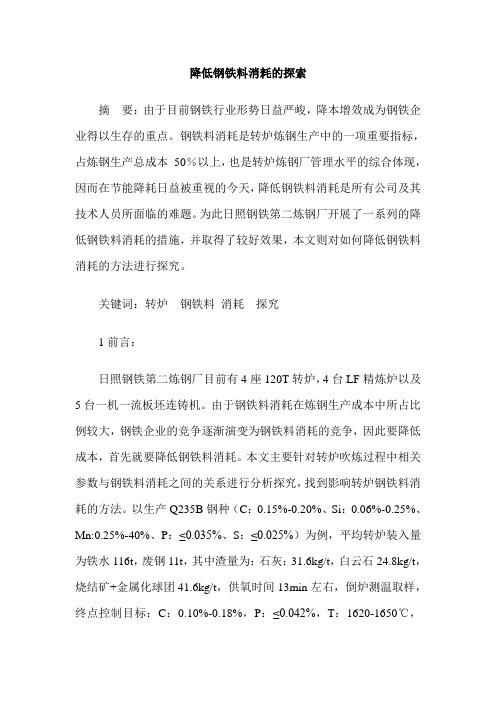
降低钢铁料消耗的探索摘要:由于目前钢铁行业形势日益严峻,降本增效成为钢铁企业得以生存的重点。
钢铁料消耗是转炉炼钢生产中的一项重要指标,占炼钢生产总成本50%以上,也是转炉炼钢厂管理水平的综合体现,因而在节能降耗日益被重视的今天,降低钢铁料消耗是所有公司及其技术人员所面临的难题。
为此日照钢铁第二炼钢厂开展了一系列的降低钢铁料消耗的措施,并取得了较好效果,本文则对如何降低钢铁料消耗的方法进行探究。
关键词:转炉钢铁料消耗探究1前言:日照钢铁第二炼钢厂目前有4座120T转炉,4台LF精炼炉以及5台一机一流板坯连铸机。
由于钢铁料消耗在炼钢生产成本中所占比例较大,钢铁企业的竞争逐渐演变为钢铁料消耗的竞争,因此要降低成本,首先就要降低钢铁料消耗。
本文主要针对转炉吹炼过程中相关参数与钢铁料消耗之间的关系进行分析探究,找到影响转炉钢铁料消耗的方法。
以生产Q235B钢种(C:0.15%-0.20%、Si:0.06%-0.25%、Mn:0.25%-40%、P:≤0.035%、S:≤0.025%)为例,平均转炉装入量为铁水116t,废钢11t,其中渣量为:石灰:31.6kg/t,白云石24.8kg/t,烧结矿+金属化球团41.6kg/t,供氧时间13min左右,倒炉测温取样,终点控制目标:C:0.10%-0.18%,P:≤0.042%,T:1620-1650℃,保证出钢过程为红包出钢,脱氧合金化顺序为:硅钙钡镁球、硅锰、硅铁、铝铁;挡渣采用挡渣塞+挡渣锥双重挡渣措施,严禁出钢下渣。
2 影响钢铁料消耗的原因分析第二炼钢厂2011年Q235B钢铁料消耗居高不下,全年累计消耗达到1076.5 kg /t。
通过不断的摸索和实践,2012年Q235B钢铁料消耗达到1048.4 kg /t。
,经统计分析认为影响钢铁料消耗的主要因素包括以下几个方面。
2.1 转炉入炉铁水Si、温度对钢铁料消耗的影响由于第二炼钢厂转炉车间没有混铁炉,铁水成分波动较大,Si 高时可以达到0.89%,低时只有0.05%,温度高时可以达到1429℃,低时只有1200℃,由于铁水条件较差,其Si 成分波动大,给转炉的操作带来很大的影响,高Si 铁水的大渣量冶炼,溢渣、喷溅频繁,遇到低Si 铁水时易因热量不充足、操作不当造成终点温度过低,后吹时间较长,使渣中氧化铁含量大增,增加了铁损。
钢铁料消耗影响因素探讨与生产实践

控制炉渣的碱度, 用枪位控制炉渣的 ( FeO) 的 浓度, 使成渣路线趋向合理。 3.1.3 石灰管理
严把石灰质量关, 对外购石灰加强验收, 并对外购石灰分仓堆放, 让炉前在冶炼时知道 是使用哪种石灰, 以便根据石灰质量区分使用, 避免将气烧窑石灰当作外购石灰使用, 大幅降 低了石灰的消耗量。
图 3 是终点 [ C] 与炉渣全铁的关系, 从图 3 可以看出, [ C] 越低, 炉渣中的全铁含量就高, 炉渣带走的铁损就增加。而对于 [ P] 低的钢种 来说, 要达到终点磷低的效果, 冶炼过程就要 大渣量、高碱度和高氧化铁的炉渣, 而这些导
20
湖南冶金
Vol.34 No.1
图 3 ( TFe) 与 [ C] 的关系
2006 年第 1 期
冯建新: 钢铁料消耗影响因素探讨与生产实践
19
损增加, 甚至引起严重喷溅。 2.3.2 钢铁料结构
转炉厂消耗的生铁块主要是外购小高炉生 产的土铁, 往往含硅、锰、硫较高; 而外购废 钢中又含有一定比例 ( 且波动较大) 的废铸铁 件; 此外就是自产废钢 ( 连铸冻块、切头切尾、 炉下回收废钢和回收的废旧设备等) 及渣山上 回收的渣钢和球磨铁粒子。
渣中一定量的氧化铁是化好渣、提高脱磷 能力的必要条件。渣中氧化铁的含量太低, 炉 渣返干, 易导致金属喷溅和粘枪; 而氧化铁太 高, 又易形成泡沫渣, 引发泡沫性喷溅。图 1 反映的是终点 [ P] 与终点炉渣 ( FeO) 的关系。
图 1 钢水终点 [ P] 与 ( FeO) 的关系
2.4.3 渣量 渣量与铁水成分、铁水单耗、炉渣碱度、
致了炉渣带走的铁损增加。 2.5.3 合金加入量的不同影响钢铁料消耗
钢种不同, 加入的合金量不一样。以 Q235 和 HRB335 两钢种为例: Q235 钢合金进入钢水 的 量 为 7.8 kg /t, HRB335 钢 合 金 进 入 钢 水 的 量 为 22.9 kg /t, 二者相差超过 15 kg /t。 因此 Q235 的终点成分与 HRB335 的终点成分控制正常情况 下, 两钢种的钢铁料消耗相差超过 15 kg /t。
低铁钢比工艺条件下降低转炉钢铁料消耗应用实践
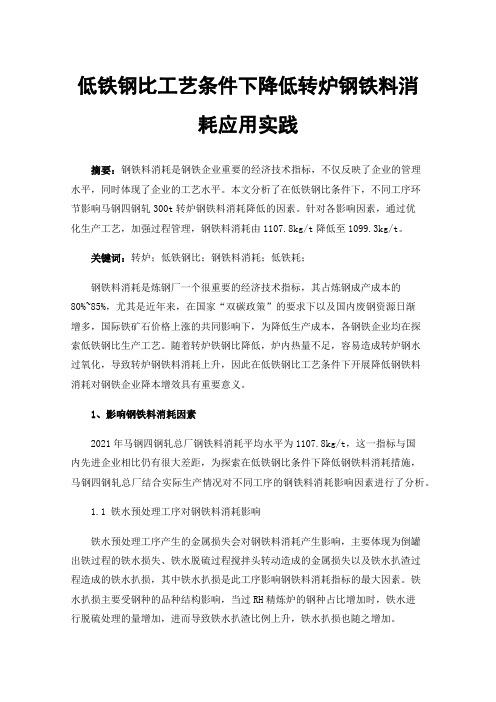
低铁钢比工艺条件下降低转炉钢铁料消耗应用实践摘要:钢铁料消耗是钢铁企业重要的经济技术指标,不仅反映了企业的管理水平,同时体现了企业的工艺水平。
本文分析了在低铁钢比条件下,不同工序环节影响马钢四钢轧300t转炉钢铁料消耗降低的因素。
针对各影响因素,通过优化生产工艺,加强过程管理,钢铁料消耗由1107.8kg/t降低至1099.3kg/t。
关键词:转炉;低铁钢比;钢铁料消耗;低铁耗;钢铁料消耗是炼钢厂一个很重要的经济技术指标,其占炼钢成产成本的80%~85%,尤其是近年来,在国家“双碳政策”的要求下以及国内废钢资源日渐增多,国际铁矿石价格上涨的共同影响下,为降低生产成本,各钢铁企业均在探索低铁钢比生产工艺。
随着转炉铁钢比降低,炉内热量不足,容易造成转炉钢水过氧化,导致转炉钢铁料消耗上升,因此在低铁钢比工艺条件下开展降低钢铁料消耗对钢铁企业降本增效具有重要意义。
1、影响钢铁料消耗因素2021年马钢四钢轧总厂钢铁料消耗平均水平为1107.8kg/t,这一指标与国内先进企业相比仍有很大差距,为探索在低铁钢比条件下降低钢铁料消耗措施,马钢四钢轧总厂结合实际生产情况对不同工序的钢铁料消耗影响因素进行了分析。
1.1 铁水预处理工序对钢铁料消耗影响铁水预处理工序产生的金属损失会对钢铁料消耗产生影响,主要体现为倒罐出铁过程的铁水损失、铁水脱硫过程搅拌头转动造成的金属损失以及铁水扒渣过程造成的铁水扒损,其中铁水扒损是此工序影响钢铁料消耗指标的最大因素。
铁水扒损主要受钢种的品种结构影响,当过RH精炼炉的钢种占比增加时,铁水进行脱硫处理的量增加,进而导致铁水扒渣比例上升,铁水扒损也随之增加。
1.2转炉工序对钢铁料消耗影响转炉工序影响钢铁料消耗因素较多,主要有以下几个因素:1)转炉渣量。
转炉冶炼过程中会有部分铁进入到转炉渣中,目前四钢轧转炉终渣全铁在16%左右,渣量增大会导致进入到转炉渣中的铁增加,因此会造成钢铁料消耗上升。
转炉生产降低钢铁料消耗的探讨与实践

2 11 铁水温度过高( 1 0 .. > 0o 3 C)
t
铁水温度高时, 铁水带来的物理热也相应增加 ,、 导致操作前期温度上升过快 , 从而容易 出现前期溢 。
渣中氧化铁含量大增 ,降低 了金属收得率。经 : 左炳伟 ( 99一) 男 , 16 , 莱钢 技校炼钢专业 , 为炼钢厂 4 现
转炉车间总炉长。
损。
2 17 渣 料加 入时 机及批 量不 当 ..
渣料加入时机及批量不当很容易引起溶池温度
增加 吹损 。
钢水再从转炉出钢到钢包内, 在钢包 内经过吹 A 站 r 处理后 , 直接到达 4连铸机 , 4连铸机浇铸成不 由 同规格的钢坯 , 而后送到 中型厂轧制成不 同规格 的
H型钢 。
2 15 操作枪位不当 ..
前期枪位过高 , 内 FO多 , 渣 e 当温度 上来 时反
据市场状况 , 不断调整其配 比。铁水经由铁水罐从
炼铁厂运送至脱硫站, 进行脱硫处理后兑进混铁炉 中, 然后再加入转炉和冷料一起冶炼为合格的钢水 。
2 14 矿 石摄 入量 大 ..
4转炉车间矿石的摄人量一般都在 2 g t 5k/ 以 上, 最高时 曾达到 5 gt大量矿石 的加入也使得 0k/, 炉内的溶池温度不好控制 , 容易出现前期大量溢渣,
关键 词 : 钢铁 料 消耗 吹损 率 标 准化操 作
O 前 言
炼钢厂 4转炉车间拥有一座 6 转炉 , 0 年 0t 2 2 0 1 月建成投产后 , 0 降低钢铁料消耗一直是不断探索 实践 的一项工作 , 尤其从 20 06年开始 , 为进一步节 能增效 , 提高企业的市场盈利能力 , 对影响钢铁料消
炼钢全流程钢铁料消耗的实践与分析
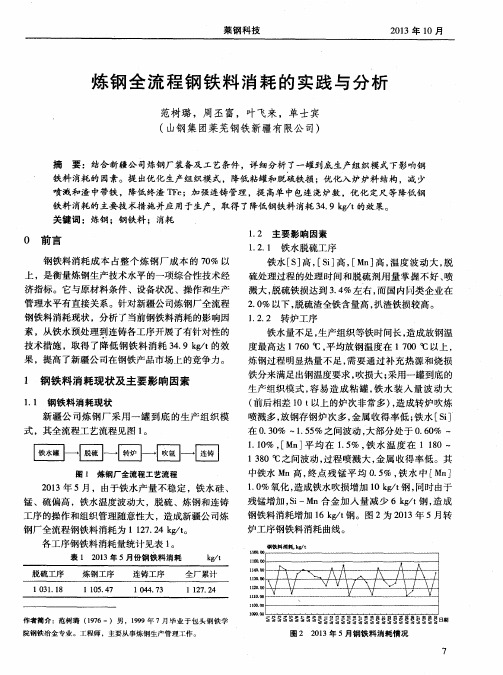
喷溅多 , 放钢存钢炉次多, 金属收得率低 ; 铁水 [ s i ]
在0 . 3 0 % 一1 . 5 5 % 之 间波动 , 大部 分 处 于 0 . 6 0 % ~ 1 . 1 0 %, [ Mn ] 平均 在 1 . 5 %, 铁水 温度 在 1 1 8 0~
1 . 2 . 2 转炉工 序
济指标。它与原材料条件、设备状况 、操作 和生产
管理 水平 有直 接关 系 。针对 新疆 公 司炼钢 厂全 流程
钢铁料消耗现状,分析 了当前钢铁料消耗的影响因 素, 从铁水预处理到连铸各工序开展了有针对性 的 技术措施 ,取得 了降低钢铁料消耗 3 4 . 9 k g / t 的效 果 ,提 高 了新疆 公 司在钢 铁产 品市 场上 的竞 争力 。
钢铁料消耗。 k Wt
i 瑚 . ∞
2 0 1 3年 5月 ,由于铁 水 产 量 不稳 定 ,铁 水 硅 、 锰 、硫偏 高 ,铁水 温度 波 动大 ,脱硫 、炼 钢和 连铸 工序 的操作 和 组织 管理 随意性 大 ,造 成新 疆公 司炼 钢厂 全流 程钢 铁料 消耗 为 1 1 2 7 . 2 4 k g / t 。
1 . 1 钢 铁料 消 耗现状
铁 分来 满足 出钢 温度要 求 , 吹损 大 ; 采 用一 罐到底 的 生 产组 织模 式 , 容易造成粘罐 , 铁 水 装 入 量 波 动 大 ( 前 后相 差 1 0 t 以上 的炉次 非 常 多 ) , 造 成 转 炉 吹炼
新疆公 司炼钢 厂采用一罐到底 的生产组织模
目的。经过对顶底复吹转炉氧枪枪位控制的调查研
究 ,提出 了吹炼过 程 的枪位 控制制 度 ,见 图 4 。
210转炉厂降低钢铁料消耗实践

内 , 渣 F O 的含 量控 制在 1 % ~l% 的范 终 e 4 6
围内 ; 终点 P不能 超过 0 0 8 的钢 种 , 对 .1% 如
耗 太高 , 容易 喷 溅 , 过 工 艺调 整 , 大 能 消 通 扩
钢 种 石 耗
.
2 ・ 6
S H 终渣 碱度 控制 在 3 2— . P C, . 3 6的 范 围 内 ,
终 渣 F O 的含 量 控 制 在 1 % ~1 % 的 范 围 e 6 8
起 大量 氧化 铁 , 随后在元 素 氧化 、 池被 加热 熔
时 , 往突然 引起 碳 的激 烈 氧化 , 往 容易造成 爆
内; 同时相应 降低 轻 烧镁球 加人 量 , 控制 好终
发性 的喷溅 。吹炼 到 2 % 以后 , 2 防止 F O蓄 e 积过 多 , 压枪脱 碳 , 吹炼 到 7 % 以后 , 防 止 0 为 熔 渣 返干 , 又提 高枪 位 , 近终点 压枪 均匀 成 接
渣 Mg O的含量 , 求调 度室 及 时根 据 转 炉热 要
2 0转 炉厂 降 低钢 铁 料 消 耗 实践 1
2 0转 泞 r 1
摘
刘
要
彭
钢铁料消耗 占转炉生产成本 7 % 以上 。降低 钢铁料 消耗不仅 可 以降低生 产成本 , 0 而且 有 利 于改善其他技术经济指标 , 是公 司降低产 品成本 的有效手段之 一。根据集团公司的要求和我 厂降本增效 的 目标 ,1 2 0转炉厂成立了降低钢铁料攻关小组 , 对 目前形势 , 针 在保证安全顺 产的
降低钢铁料消耗实现降本增效
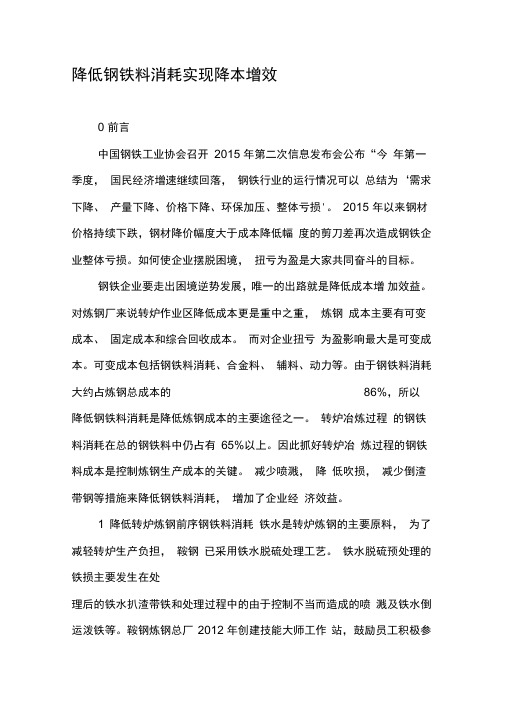
降低钢铁料消耗实现降本增效0 前言中国钢铁工业协会召开2015 年第二次信息发布会公布“今年第一季度,国民经济增速继续回落,钢铁行业的运行情况可以总结为‘需求下降、产量下降、价格下降、环保加压、整体亏损'。
2015 年以来钢材价格持续下跌,钢材降价幅度大于成本降低幅度的剪刀差再次造成钢铁企业整体亏损。
如何使企业摆脱困境,扭亏为盈是大家共同奋斗的目标。
钢铁企业要走出困境逆势发展,唯一的出路就是降低成本增加效益。
对炼钢厂来说转炉作业区降低成本更是重中之重,炼钢成本主要有可变成本、固定成本和综合回收成本。
而对企业扭亏为盈影响最大是可变成本。
可变成本包括钢铁料消耗、合金料、辅料、动力等。
由于钢铁料消耗大约占炼钢总成本的86%,所以降低钢铁料消耗是降低炼钢成本的主要途径之一。
转炉冶炼过程的钢铁料消耗在总的钢铁料中仍占有65%以上。
因此抓好转炉冶炼过程的钢铁料成本是控制炼钢生产成本的关键。
减少喷溅,降低吹损,减少倒渣带钢等措施来降低钢铁料消耗,增加了企业经济效益。
1 降低转炉炼钢前序钢铁料消耗铁水是转炉炼钢的主要原料,为了减轻转炉生产负担,鞍钢已采用铁水脱硫处理工艺。
铁水脱硫预处理的铁损主要发生在处理后的铁水扒渣带铁和处理过程中的由于控制不当而造成的喷溅及铁水倒运泼铁等。
鞍钢炼钢总厂2012 年创建技能大师工作站,鼓励员工积极参与创新活动,各作业区各班组相互交流学习,同时注重先进操作法的推广。
为减少脱硫扒渣带铁的问题,炼钢总厂各车间推行四控扒渣操作法,可显著降低扒渣操作中的铁水损失,扒渣铁损至少降低15Kg/t 钢。
按2014 年鞍山钢铁产钢2145 万吨,则可减少铁损32.175 万吨。
员工们发挥鞍钢宪法精神积极参与,形成一个又一个可控操作经验,有效地减少了铁水喷溅的损耗。
同时鞍钢采用高炉――转炉“一罐到底”的方式,减少了倒罐次数,降低了铁水热量的损失,减少了铁水的倒运损失,同时也减少了环境的污染,从而有效地降低了转炉钢铁料的损耗。
棒材厂降低转炉钢铁料消耗实践
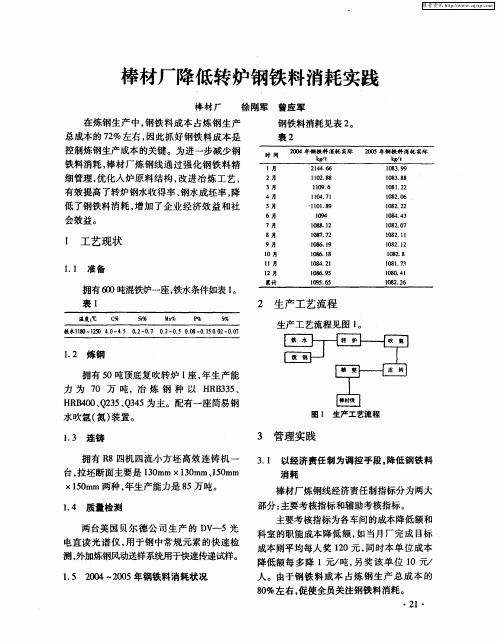
电直读光谱 仪, 用于钢中常规元素 的快速检 测, 外加炼钢风动送样 系统用于快速传递试样 。
15 2O 20 . O4— 0 5年钢铁 料 消耗状 况
科室 的职能成本降低额 , 如当月厂完 成 目标
成本 则平均 每人 奖 10元 . 时本 单 位成 本 2 同
降低额每 多降 1
吨, 另奖该单 位 1 O
一
9 . %的指标 , 15 每降低 0 1 , . % 考核车间岗效 工资总额的 1%( 0 人平 8 元) 促使他们实施 ,
一
精心操作 , 减少喷溅 , 降低渣中氧化铁含量等 系列措施 ; 又如考核连铸车间钢水成坯率 大于 9.3 的指标 , 76 % 每降低 0 1 , . % 考核车
铁料消耗 , 棒材厂炼钢线通过强化钢铁料精 细 管理 , 化人 炉 原 料 结构 , 优 改进 冶 炼工 艺 ,
有效提高了转炉钢水收得率 、 钢水成坯率 , 降 低了钢铁料消耗 , 增加 了企业经济效益 和社
. ■ _ =
雨
——— —一 2 月 128 1. 08
。 5 月 ‘ 19 1 . 18 0
人 。 由于 钢 铁 料 成 本 占炼 钢 生 产 总 成 本 的
8%左右, 0 促使全员关注钢铁料消耗。
・
21 ・
维普资讯
辅助考核指标是针对各车间科室工作 内 容的不同而单独设立的考核指标 , 以引导他 们朝该方 向努力 ; 如考核准备车 间钢铁料收
流 失 ; 考 核 炼 钢 车 间 钢 水 收 得 率 大 于 如
关小组组长及责任人按一档个人应得奖励进 行考核 ; 同时结合 当月指标 与全年 累计指标 完成情 况 对 攻关 小组 进 行 奖励 与 考 核 : a ()
湘钢二炼钢厂降低铁水消耗生产实践

炉一 连 铸 工 艺 的 技 术 进 步 。 大 限 度 提 最
高 冷 料 比 3. . 用 生 铁 块 代 替 部 分 废 钢 , 整 入 炉 钢 2I 调
铁 料 结 构 , 能 降耗 节
பைடு நூலகம்
由于生铁块 的冷 却效应 低 于 废 钢 , 以 可
硫 含 量 、 水 带 渣 量 及 铁水 计 量 、 铁块 磷 含 铁 生
量、 白灰 的 生 过 烧 率 、 性 度 进 行 跟 踪 和 复 活 检, 对不符合 条 件 的原料 及 时反 映给 公 司主 管部 门, 通过 公 司 内部及 外 部合 同进 行 动态 调 整 控 制 。一 定 程 度 上 促 进 了原 料结 构 的 优
l 0凹 . 3 9 9 . 9 7 l 7. 5 08 7
2 0 01
9 6. 9 2l 6 7 7. 2
l 3 66 0 2.
2O 0 2年 I 4月
97 7 3. 8
平 均铁水 消耗 最 低铁 水 消耗
平均铁 耗 平 均钢铁 料 消耗
9 o. 6 6 1 l 2. 9 0l 9 l B 8 0 2. l
32. 应 用 钢 包 在线 烘 烤 技 术 , 幅 度 降 低 . 2 大
出钢 温 度 20 0 1年 , 由鞍 山热 能 院设 备 研 制 厂设 计
采 用 合 金 烘 烤 、 包 加 盖 保 温 和 钢 包 加 钢 隔 热 层 等 技 术 措 施 , 水 热 损 失 将 进 一 步 减 钢 少 , 计 降 低 出 钢 温 度 l ℃ 左 右 , 水 消 耗 预 5 铁 指 标 降 低 ll 0【 g以上 。
- 1、下载文档前请自行甄别文档内容的完整性,平台不提供额外的编辑、内容补充、找答案等附加服务。
- 2、"仅部分预览"的文档,不可在线预览部分如存在完整性等问题,可反馈申请退款(可完整预览的文档不适用该条件!)。
- 3、如文档侵犯您的权益,请联系客服反馈,我们会尽快为您处理(人工客服工作时间:9:00-18:30)。
降低钢铁料消耗实践
在炼钢生产中,钢铁料成本占炼钢生产总成本的80%以上,因此抓好钢铁料成本是控制炼钢生产成本的关键。
为进一步减少钢铁料消耗,改进转炉原料结构和炉前冶炼工艺,采用少渣炼钢工艺,减少喷溅,降低吹损,减少倒渣带钢等措施来降低钢铁料消耗,有效地降低了钢铁料消耗,增加了企业经济效益。
1 影响钢铁料消耗的主要原因
氧气顶吹转炉的吹损用下式表示:
吹损=(装入量—出钢量)/装入量×100%
影响钢铁料消耗的主要因素包括原料中杂质元素化学损失、烟尘损失、炉渣中铁的损失、喷溅及倒渣带钢造成的铁耗等。
为了减少转炉吹损,降低钢铁料损耗,应采取合理的原料结构,合适的装入制度以及合适的造渣工艺并稳定转炉操作实现。
2 降低钢铁料消耗工艺措施
2.1 优化入炉原料结构
在合适的用量范围内,通过增加矿石用量,可有效增加钢水量,从而降低钢铁料消耗,因此在实际炉料结构中可采用增大入炉原料中铁水比例,降低废钢铁块消耗,增加矿石消耗的工艺措施。
济钢第一炼钢厂2002年与2001年吨钢入炉原料对比情况见表1。
表1 2002年与2001年吨钢入炉原料对比 kg
年份铁水废钢铁块矿石
2002年979.6 29.2 91.4 40.0
2001年942.1 65.8 101.1 26.4
对比37.5 -36.6 -9.7 13.6
济钢所用各种矿石的原料成分及价格见表2。
在单炉矿石用量为1500kg时使用不同种类矿石的使用效果见图1。
图1 三种矿石使用效益对比图表2 各种矿石原料成分及价格 %
种类TFe Fe
2O
3
SiO
2
价格/元·t-1
黑旺矿43.5 62.1 13.0 162
澳矿65.0 92.0 3.0 297
球团矿65.0 92.0 3.0 400
实际生产中,由于黑旺矿中SiO
2
含量较高,因此即便造渣料加入总量相同情况下,使用黑旺矿产生渣量也较多,造成渣中铁耗也较高,同时由于黑旺矿块度较大,在转炉吹炼过程中往往熔化不好,既降低了使用效果,又不利于转炉化渣。
球团品位高,含氧量相应较高,有利于减少供氧消耗,同时又为熟料,有利于转炉化渣,但由于价格较高,使用成本较高。
对于澳矿,其品位较高,块度也合适,其主要成分为赤铁矿,有利于矿石还原,增加矿石还原和提高吹炼节奏,同时使用效益也最高。
通过统计计算,进行成本分析比较,品位高的矿石不仅Fe的回收率高,有利于冶炼操作,而且经济效益可观。
因此,在2002年生产中大量采用了进口澳矿,从使用情况和使用经济效益情况看均取得良好的效果。
为了尽量增加矿石用量,提高矿石还原效果和减少吹炼过程中矿石加入量过多对冶炼稳定的影响,在实际生产中,对矿石加入工艺进行了调整。
配合留渣操作,转炉溅完渣后直接将2/3左右的矿石加入炉内后再装铁,在装铁和废钢过程中搅拌以促进部分矿石的还原。
在保证化渣效果和避免喷溅原则下尽量保证剩余矿石早加和均匀加入,以保证矿石化渣还原时间和效果。
吹炼中期采用分批少量加入控制,避免吹炼中期加入量集中造成的喷溅;吹炼后期严禁加矿石,避免矿石加入过晚造成熔化还原效果差和炉渣氧化性强对脱氧合金化的影响。
2.2 改进造渣工艺,减少炉渣铁耗
2.2.1 炉渣量分析根据实际造渣料加入情况与炉渣成分,进行渣量推算如下:
化验炉渣成分:CaO 50%,MgO 9%,SiO
2
17%,TFe 14%
钢铁料装入量:铁水41.5t,废钢4.5t
造渣料加入量:石灰1300kg/炉,矿石1700kg/炉,萤石100kg/炉,白云石600kg/炉
白云石成分:MgO 30%,CaO 50%
石灰成分:MgO 3%,CaO 90%
萤石成分:CaF
80%(含Ca 41%)
2
烧减量:白云石15%,石灰6%
进入炉渣中CaO总量为1527.4kg,按终点炉渣中CaO含量50%计算,炉渣量为3055kg,由以上计算得出目前每炉渣量约为3.1t,加上留渣及溅渣层熔损,实际每炉渣量应在3.5t左右。
2.2.2降低终点炉渣FeO含量为了减少终点炉渣中FeO含量,在实际生产中采用终点降枪提氧压措施,终点枪位由正常吹炼枪位距液面1000mm降低到
800mm,同时将工作氧压由0.85MPa提高到0.95~1.0MPa;严格控制一次倒炉命中率,通过强化对一次拉碳率、增碳剂、SiC的控制考核,推广使用SiMnFe,终点碳有了大幅度提高,同时配合严禁吹炼后期加矿石降温等措施,渣中全铁含量由2001年的平均18%左右降为2002年的14%,按3t渣量计算,可降低单炉铁耗120kg。
2.2.3 减少渣量,实施少渣炼钢为了减少单炉产渣量,在生产中采取精料方针,在进一步完善转炉留渣操作工艺推广应用基础上努力提高入炉原料质量,使用高品位石灰和矿石,采用镁块代替白云石造渣。
根据原料情况和品种情况合理调整造渣料消耗,在铁水Si、S含量较高生产低S钢时适当减少石灰量消耗。
2002年单炉钢石灰消耗由2001年的49 kg降为30kg,由此减少单炉产渣量约1400kg,按渣中全铁含量14%计算减少铁耗201kg。
2.2.4改进吹炼工艺,降低喷溅损失为消除或减轻喷溅采取了以下措施:
(1)适当提高炉容比,在对转炉扩容的基础上对转炉炉衬结构进行了改进,工作层全部采用镁碳砖炉衬,减少了炉衬厚度,从而增加了炉内有效容积,同时采用合理的炉型结构,以利于喷溅物的反射。
(2)合理控制转炉装入量和控制造渣料用量,以便减薄渣层。
根据炉龄和炉衬情况采用分阶段定量装入法,在炉役前期适当减少装入量,保证炉内有效工作容积。
(3)改进化渣工艺,保证前期化好渣,在二批造渣料加入前后,通过提前成渣的方法,将泡沫渣的高峰期前移,以便与脱碳的峰值时刻错开。
(4)在脱碳的高峰期到达之前,暂时降低供氧强度,然后再将其平缓地恢复到正常值。
(5)吹炼终期采用大氧压底枪位操作,加强熔池搅拌,保证终点钢水成分和温度的均匀,同时降低炉渣氧化性。
3 经济效益分析
(1)2001年、2002年入炉金属料成本统计:钢铁料成本指济钢第一炼钢厂当年实际消耗钢铁料数量及成本,其中实际废钢消耗成本为入炉废钢总量减去生产过程中自产废钢和冶炼废钢成本后的实际外用废钢成本。
根据财务数据统计分析,2002年吨钢钢铁料成本比2001年降低9.26元,2002年钢产量257万t,则降低钢铁料成本2379.82万元。
(2)矿石结构调整使用成本对比:2001年和2002年主要使用矿石种类为球团矿和黑旺矿,2002年主要使用矿石种类为澳矿。
矿石使用量及成本见表3。
由表3中数据得出,矿石结构调整增加成本515.57万元。
表3 矿石成本统计
项目产钢量/万t 矿石消耗总
量/t
吨钢消耗量
/kg
矿石总成本/
万元
吨钢矿石成
本/元
2001年237.69 62987.97 26.50 2490.30 10.47 2002年257.39 101364.44 40.16 3005.87 11.67
(3)造渣料结构调整,减少石灰用量效益分析:吨钢石灰用量由2001年的49kg降低到30kg,石灰价格为260元/t,年产量按257万t计算,年直接经济效益为1269.58万元。
综合经济效益为3133.83万元。
4 结语
4.1 通过合理改进装入制度,稳定了转炉操作,提高了吹炼化渣质量,同时合理控制终点钢水氧化性,可有效减少喷溅和炉渣造成的铁耗。
4.2通过合理采用矿石种类及结构,可有效降低转炉钢铁料消耗,提高金属收得率,降低成本。
4.3通过合理控制转炉渣量,实施少渣炼钢工艺,可有效减少炉渣铁耗,提高金属收得率。
4.4合理改进转炉炼钢工艺,减少炼钢吹损,使钢铁料成本和金属料成本大幅降低,具有良好的经济效益和社会效益。