炼钢生产线中降低钢铁料消耗措施及实践
影响钢铁料消耗因素探讨与实践

2017年第2期LYS Science-Technology& Management・8・影响钢铁料消耗因素探讨与实践一炼轧厂黄伟豪摘要本文对影响钢铁料消耗的因素进行了具体分析。
通过改进入炉料结构、优化造渣工艺、减少转炉喷溅率、加强内部含铁资源回收,有效提高了转炉钢水收得率,降低了钢铁料消耗。
1 引言目前钢铁行业竞争日益激烈,钢材利润空间急剧压缩,为应对市场带来的挑战,必须采取措施来降本增效。
而钢铁料消耗占转炉炼钢生产成本的70%以上,且钢铁料指标的好坏直观体现了该厂综合技术水平、管理水平的高低,它关系到炼钢厂以挖潜增效为主的竞争活动的成败,因此降低钢铁料消耗对炼钢企业来说显得尤为迫切。
本文综合分析了涟钢一炼轧厂转炉线的实际生产情况,提出针对性的改进措施,付诸实施后,钢铁料消耗取得了明显进步。
2 炼钢线生产现状涟钢一炼轧厂转炉线现有公称容量100t氧气顶底复吹转炉3座,铁水预处理一座,吹氩站3座,2台6机6流弧形连铸机。
年产钢390万吨。
主要品种有HRB系列、CSP低碳钢、CSP普碳钢、低碳合金钢、高碳高强钢及其它新钢种。
3 钢铁料消耗计算口径与现状3.1 钢铁料消耗计算方法钢铁料消耗(kg/t)=入炉钢铁料(kg)÷合格钢产量(t);钢铁料消耗量(t)=铁水量(t)+生铁量(t)+废钢量(t)+矿石(t);废钢从来源上分为外购废钢和自产废钢,加生铁是由于炼钢能力大于高炉生产能力,铁水量不足,靠采购生铁块来发挥转炉产能。
3.2 钢铁料消耗现状2016年一炼轧厂的钢铁料实物消耗1079.31kg/t,较往年明显好转。
4 影响钢铁料消耗的主要因素涟钢6#高炉处于炉役后期,铁水质量较差,入炉铁水渣量、温度、成分波动大,转炉炉容比小,受入炉原材料质量以及入炉料结构的影响较大。
转炉冶炼过程易喷溅、喷溅渣含铁量大,熔剂消耗高,终渣TFe高,终点温度、成分控制较差导致回炉与中断连铸次数较多,过吹、高温现象较严重;连铸操作稳定性差,铸余钢水流失多,严重影响着钢铁料消耗的降低。
降低炼钢钢铁料消耗的生产实践
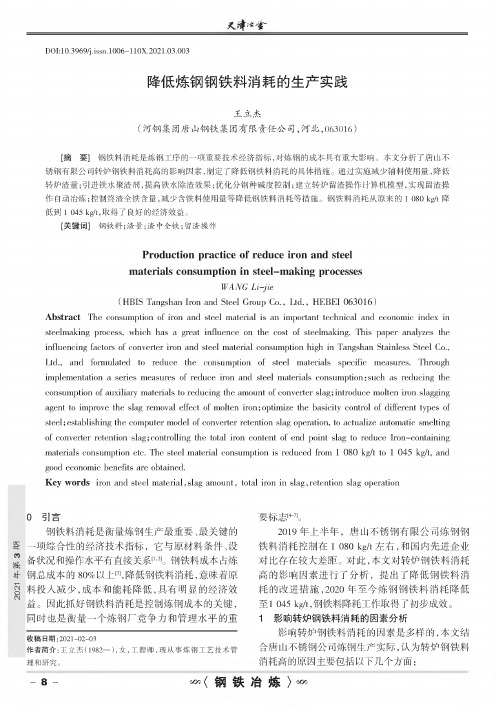
DOI:10.3969/j.issn.l006-110X.2021.03.003降低炼钢钢铁料消耗的生产实践王立杰(河钢集团唐山钢铁集团有限责任公司,河北,063516)[摘要]钢铁料消耗是炼钢工序的一项重要技术经济指标,对炼钢的成本具有重大影响。
本文分析了唐山不锈钢有限公司转炉钢铁料消耗高的影响因素,制定了降低钢铁料消耗的具体措施。
通过实施减少辅料使用量,降低转炉渣量;引进铁水聚渣剂,提高铁水除渣效果;优化分钢种碱度控制;建立转炉留渣操作计算机模型,实现留渣操作自动冶炼;控制终渣全铁含量,减少含铁料使用量等降低钢铁料消耗等措施。
钢铁料消耗从原来的100kg//降低到1047kgt,取得了良好的经济效益。
[关键词]钢铁料;渣量;渣中全铁;留渣操作Production practice of reduce iron and steelmaterials consumption in steel-making processesWANG Li-jie(HBIS Tangshan Iron and Steel Group Co.,Ltd.,HEBEI063016)Abstract The conshmption of iron and steel material is an important technical and economic index in steelmaning process,which hns n grent inflpeccc on tde cost of steelmaning.This pneo analyzes tde inflpeccing factore ol convertee iron and sted material conshmption high in Tangshan Stainless Sted C o, Lte.,and formulatee te o C pc the ol sted materials sheOmc meassres.Thronph impmmectation a series meashres ol oduc iron and sted materiais cnshmphon:such as reeucing the conshmption ol anxiliaro materiais te reeucing the monut ol converter slaa;intronucc moltee iron slaggingaaeYg te irnpove the slaa omovet巳琏厲ol moltee O oc;optimize the basicitz control ol.0X11:types ol steel y estaniishing the computer monel ol converter retechon slaa oneration,te actualize antomatic smeltingol aonvertcr retention slaa/controlling the total iron contedi ol end poini slaa i reduce Iron-—ontaining materials consumption etc.The steel materiai conshmption is reduced from1080kg//e1045kgA,and goon economic beceCis are ontained.iron and steel material,slag amount,total iron in slag,retention slag operationKey words0引言钢铁料消耗是衡量炼钢生产最重要、最关键的一项综合性的经济技术指标,它与原材料条件、设备状况和操作水平有直接关系>4。
炼铁降低工序能耗的措施

炼铁降低工序能耗的措施炼铁降低工序能耗的措施炼铁行业是一个消耗大量能源的行业,由于其生产工艺复杂,因此在整个生产过程中消耗大量能源。
因此,如何降低炼铁行业的能耗成为炼铁行业发展的必要条件之一。
本文针对炼铁行业的能耗问题,总结出现有的降低工序能耗的措施。
一、改善炉内物料利用率炼铁企业应注重改善炉内物料利用率,确保炉内物料的完全燃烧,降低炉内物料堆积,以减少能源的浪费。
同时,应加强对原料的把控,改善原料的质量,提高焦炭的热值,有利于提高炉内物料的利用率。
二、提高炼铁设备的能效炼铁企业应重视提高炼铁设备的能效,加强设备的检修维护,改善设备的动力利用,提高设备的整体功率利用率,减少能源浪费。
同时,可考虑采用新型节能设备,提高设备的效率,降低能耗,从而达到降低能耗的目的。
三、加强热力学优化炼铁企业需要加强热力学优化,通过改变工艺参数,提高燃烧效率,减少能量损失。
例如,应尽量减少炉温,减少燃料消耗,改善气体组成,提高气体的燃烧效率,降低炉内能量的损失。
四、优化炉温结构炼铁企业应重视优化炉温结构,利用工艺热力学原理,合理调整炉温,采用合理的炉温结构,使炉温分布均匀,避免炉子出现热点,从而达到降低能耗的目的。
五、优化炉缸设计形式炼铁企业还应重视优化炉缸设计形式,减少炉缸内部的夹层结构,改变炉缸的设计形式,减少炉缸内部的损失,从而降低工序能耗。
六、改善工艺流程炼铁企业还应重视改善工艺流程,减少工序环节,实现工艺精简,减少能源消耗,优化工艺,提高生产效率,有利于降低工序能耗。
以上是有关炼铁降低工序能耗的措施,其实,炼铁企业在降低能耗方面,还可以采取更多的措施,如节省原料,改进设备结构,改善储存管理等,以最大限度地减少能耗。
炼钢厂节能降耗措施

炼钢厂节能降耗措施
炼钢厂可以采取以下节能降耗措施:
1. 优化生产工艺:通过改进生产工艺,减少能源消耗和浪费。
2. 设备升级与维护:定期对设备进行维护和升级,提高设备的运行效率,降低能耗。
3. 能源管理系统:建立能源管理系统,实时监控能源消耗情况,及时发现并解决能源浪费问题。
4. 员工培训:加强员工节能意识培训,提高员工的节能意识和技能。
5. 余能回收利用:利用炼钢过程中产生的余能,如废气、废渣等,进行回收利用,降低能源消耗。
6. 照明系统优化:采用高效节能的照明灯具,合理布置照明系统,减少照明能耗。
7. 原料优化:选择低能耗、高品质的原料,降低生产成本和能源消耗。
8. 能源合同管理:与能源服务公司合作,进行能源合同管理,优化能源使用效率,降低能源成本。
这些措施可以帮助炼钢厂降低能源消耗,提高生产效率,实现可持续发展。
具体实施应根据炼钢厂的实际情况进行调整和优化。
转炉降低钢铁料消耗实践

转炉降低钢铁料消耗的生产实践张羽王杰文李兴才(德龙钢铁有限公司炼钢厂河北邢台)摘要:炼钢厂通过改变吹炼方法、优化矿石加入时间和加入量、强化转炉生产过程控制、加大含铁原料的回收力度等几方面进行改进,摸索出降低钢铁料消耗的有效途径,2012年的钢铁料消耗比2011年降低了8Kg/t。
关键词:工艺操作烧结矿加入方式含铁原料回收前言转炉的钢铁料消耗在生产成本中占有较大比重,降低钢铁料消耗是控制炼钢厂生产成本的关键环节。
德龙钢铁炼钢厂新炼钢2007年建成,两座80吨顶底复吹转炉,转炉扩容后炉容比较小,仅为0.768m3/t,吹炼过程中容易发生喷溅,吹损率高、钢水收得率较低,2011年钢铁料消耗为1069.7Kg/t,与同行业相比偏高。
1、转炉工况条件德龙钢铁炼钢厂2座顶底复吹转炉经扩容后工称容量为80t,有效工作容积为65.3m3,炉口直径1.88米,炉膛直径为3.84米,实际装入量85-92,实际出钢量80-87t,炉龄约15000炉。
2、转炉钢铁料消耗影响因素转炉钢铁料消耗是装入量(铁水+废钢)与转炉合格钢水量之比,降低钢铁料消耗就是要减少转炉在生产过程中的钢水损耗,影响转炉钢水损耗的主要因素包括化学损耗、渣中铁和氧化铁损耗、吹炼过程喷溅等。
德龙钢铁炼钢厂根据现有工艺条件及生产情况,从改变吹炼方法、优化矿石加入时间和加入量、强化转炉生产过程控制、加大含铁原料的回收力度等几大方面开展工作,以实现降低转炉钢铁料消耗3、降低转炉钢铁料消耗的措施3.1、改变吹炼模式以减少吹炼过程喷溅控制转炉喷溅是降低钢铁料消耗的关键措施,导致转炉喷溅的因素很多,通常摇炉工采用的吹炼模式为“恒压变枪“操作,生产实践证明,当铁水、废钢条件正常时不容易发生喷溅,而当铁水温度高、Si高时,这种操作模式容易导致吹炼过程发生喷溅,因此控制好异常条件下的喷溅是控制转炉喷溅的关键,经过摸索改进,采取了前期低氧压、低枪位操作,中后期根据实际情况调整氧压和枪位,见表1,表1 铁水温度高和Si高的情况下操作模式注:石灰总量2500Kg、轻烧白云石1000Kg、轻烧镁球500Kg、返回渣2000Kg、这种操作模式可有效的控制好吹炼过程渣的泡沫化程度进而杜绝爆发性喷溅,缩短冶炼周期,提高金属收得率。
钢铁厂节能降耗措施

钢铁厂节能降耗措施《钢铁厂节能降耗措施》一、加强节能管理1、强化安全生产管理,确保生产过程中科学节能,生产环境温暖、安全。
2、建立科学的节能目标,建立节能考核制度和定期评估体系,以提升节能效益。
3、深入实施节能标准,健全节能管理组织,强化节能技术服务,加强生产过程中节能检查,确保节能目标的实现。
4、引入钢铁行业标准化建设,推进能源综合利用,有效提升节能水平。
5、积极开展节能宣传教育,提高从业人员的节能意识,提升企业整体节能能力。
二、控制厂房能耗1、推广节能技术的应用,提高厂房的能源利用效率,减少能耗。
2、实施重点节能项目,采用可再生能源替代非再生能源,减少能源消耗。
3、强化设备管理,加强设备维护,降低能耗,提高能效。
4、采用节能材料建造厂房,采用节能装置设计生产线,减少能耗。
三、改善设备能效1、深入开展设备改造项目,改装新机,更新技术配置,提高设备使用效率,降低设备能耗。
2、推广节能设备,采用节能技术,完善设备控制系统,降低耗能。
3、引入智能技术,实施设备自动化管理,提高设备的功率利用率,节约能源消耗。
4、实施节能检测分析,及时发现设备损耗,提高设备能效。
四、优化生产工艺流程1、优化节能工艺,改善原有生产程序,提高生产工艺的节能效果。
2、引入节能技术,优化生产流程,使生产过程中的每一步都能节能。
3、及时维护冷却系统,确保其能有效工作,减少能耗。
4、加强对生产设备及装置的维护,提高生产精度,减少能耗。
五、进行系统节能改造推行节能技术改造,引入节能新设备,构建节能节耗新工程;采用节能综合技术优化原来的设备,改造热源系统,改造能源供应系统,实施节能创新工程,以提高节能水平,实现节能降耗。
炼铁生产中的能耗优化与节能减排措施

炼铁生产中的能耗优化与节能减排措施能源是现代社会发展的基石,然而在能源有限的情况下,如何优化炼铁生产中的能耗,实现节能减排已经成为了一个迫切的问题。
本文将探讨炼铁生产中的能耗优化与节能减排措施,并提出具体的解决方案。
一、炼铁生产中的能耗现状炼铁生产是消耗能源的重要行业之一,其能耗情况直接关系到国家能源安全和环境保护。
然而,目前我国炼铁企业的能耗水平普遍较高,存在一系列问题。
首先,传统的高炉炼铁工艺存在能源利用率低的问题。
其次,炼铁生产中的废气、废水和废渣等排放物对环境造成了严重的污染。
因此,亟需采取有效的节能减排措施,优化能源利用,降低能耗水平。
二、能耗优化措施1. 提高高炉燃烧效率高炉是炼铁生产的核心设备,提高高炉燃烧效率是降低能耗的关键一步。
可以通过优化燃烧参数、改善高炉炉况、提高燃烧设备的热效率等方式来提高高炉的燃烧效率。
2. 采用先进的炼铁技术传统的高炉炼铁工艺存在能源损失较大的问题,可以考虑采用先进的炼铁技术来降低能耗。
比如,采用高炉煤气发电技术、煤气制氢技术等可以实现能源的全面利用。
3. 引进节能设备与技术在炼铁生产过程中,引进先进的节能设备与技术是降低能耗的重要手段。
比如,可以引进高效节能的燃烧设备、烟气余热回收技术、废气处理设备等来提高能源利用效率。
三、节能减排措施1. 废气治理高炉炼铁过程中产生大量的废气,其中含有大量的烟尘和有害气体。
应建立完善的废气治理系统,采用高效的除尘设备和废气脱硫、脱硝技术,减少废气的排放,降低对环境的影响。
2. 废水处理炼铁生产中的废水含有较高的悬浮固体和重金属等有害物质,对水环境造成较大污染。
应采用生物法、化学法等多种处理技术对废水进行处理,确保排放水质符合相关标准。
3. 废渣综合利用炼铁过程中产生的废渣具有一定的资源价值,应加强废渣的综合利用。
比如,可以将废渣进行回收再利用,用于生产水泥、建材等,减少对自然资源的占用。
四、结语炼铁生产中的能耗优化与节能减排是实现可持续发展的关键之一。
涟钢第一炼钢厂降低钢铁料消耗实践
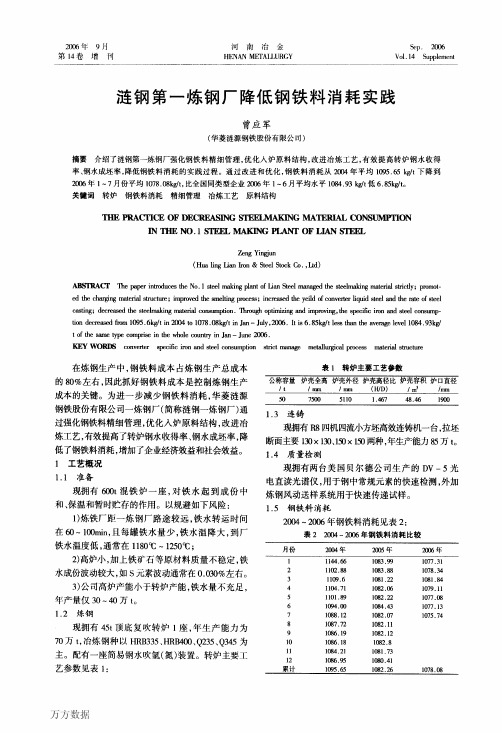
图2典型夹杂物形貌河南冶金图3能谱图取得重大突破,钢性能改善效果最为突出的是连铸一连轧板材,包括耐候钢、汽车冲压件用钢、焊接瓶用钢、集装箱用钢、船板钢、耐磨钢和装甲用钢等钢种。
一般认为稀土在钢中有净化、变质及合金化三种作用。
1)净化作用。
稀土加入钢中,与钢液中的氧、硫反应,起到脱氧脱硫作用。
稀土在钢中溶解量很少,主要偏聚在晶界。
一定量的稀土可以抑制磷、硫、砷、碲、铅、铜等低熔点杂质在晶界上的偏聚,或与这些杂质形成熔点较高的的化合物,消除了低熔点杂质的危害。
2)变质作用:钢中硫、氧等与加入的稀土作用,生成球状的稀土硫化物(RE2S)或稀土硫氧化物,取代长条状硫化锰(M11S)夹杂,硫化物形态得到控制,从而提高了钢材的韧塑性特别是横向冲击性能,改善了钢材的各向异性。
3)合金化作用:随着稀土加入量的增加,完成脱氧、脱硫和变质夹杂作用后富裕的稀土会固溶在钢中。
韶钢曾经对B级船板进行结晶器喂稀土丝的试验,结果表明:加稀土的钢板其低温冲击性能平均值明显提高,并且其低温冲击功的纵横向差异小。
2006年增刊该试验将有利于韶钢今后稀土钢的开发,也有助于韶钢合理消化和利用地方矿中cu、As、sn含量较高的特点。
2.3加快VD的建设VD是一种广泛应用的真空精炼设备,具有良好的脱氢、脱氧、脱碳、脱氮和脱硫的功能,在目前的高质量高附加值钢(如轴承钢、82B等)生产中发挥着重要作用。
韶钢将来的产品规划中管线钢、焊条钢、16Mn系列等钢种都需要进行VD处理,三炼钢厂预留了VD装置,应该尽快建设提高产品的二次精炼能力以满足市场的需要。
3结语韶钢当前采用的洁净钢冶炼技术还只能满足中低档产品的质量要求,如果从长远的产品规划和市场需要考虑,必须重视以下问题:1)韶钢由于只有铁水预脱硫,而铁水是属于中磷铁水(P≤0.12%),因此在冶炼高品质低P钢时还是个瓶颈,故需考虑双渣法脱磷并使其工艺流程规范化。
2)由于韶关地区的矿石资源特点是cu、As、Sn等低熔点元素含量较高,因此需深入研究这些微量元素对钢材性能的影响并积极寻找对应措施(如进行稀土处理)。
炼钢厂节能降耗方案

炼钢厂节能降耗方案一、背景介绍炼钢厂作为能源消耗较大的工业制造行业之一,其能源消耗和经济效益密切相关。
为了提高炼钢厂的能源利用效率和降低能源消耗,制定一套节能降耗方案是非常必要的。
本文档将从以下几个方面提出炼钢厂的节能降耗方案,包括技术改进、设备优化、管理措施等,以期降低炼钢厂的能源消耗并提升经济效益。
二、技术改进1. 高温余热回收利用炼钢厂的高温余热是一种宝贵的能源资源,通过合理的回收利用可以减少能源的浪费。
建议在炉煤气和炉渣处理过程中,使用余热锅炉进行余热回收,用于提供蒸汽、热水等其他能源需求,实现能源流的闭合循环。
2. 电力替代将传统的燃煤锅炉替换为电力供应系统,可以降低燃料供应和运输的成本,同时减少燃烧过程中产生的污染物,达到节能环保的目标。
3. 新一代高效节能炼钢技术引进和推广新一代高效节能炼钢技术,例如煤气轮机联合循环发电技术、高效炉结合先进的热能循环装置等,可以提升炼钢过程中的能源利用效率,降低燃烧过程中的能源损耗。
三、设备优化1. 能源消耗监测系统安装能源消耗监测系统,实时监测和分析炼钢厂各个环节的能耗情况,提醒和指导操作人员合理调整供应和使用能源的方式,以达到降低能源消耗的目标。
2. 能源高效设备更新对老化设备进行更新和升级,选择符合能效标准的设备,以提升设备的能源利用效率和工作稳定性,降低能源的浪费和排放。
3. 智能化控制系统利用先进的智能化控制系统对炼钢厂的设备和流程进行精确控制,实现自动化操作,减少人为误操作和能源的浪费。
四、管理措施1. 能源管理体系建立炼钢厂应建立完善的能源管理体系,明确节能目标和指标,制定相应的管理措施,并对能源的供应、使用、监测进行全面管理和控制。
2. 能源培训和宣传教育开展能源培训和宣传教育工作,提高员工的节能意识和技能,引导员工采取有效的能源节约措施,共同参与炼钢厂的节能降耗工作。
3. 环境监管和政策支持加强对炼钢厂的环境监管,制定相关的节能降耗政策和措施,给予相应的经济和政策支持,鼓励炼钢厂不断推进节能降耗工作。
降低钢铁料消耗实践

降低钢铁料消耗实践李双武1王生金1周玉珍 2(1.河北钢铁集团唐钢第二钢轧厂2.河北钢铁集团唐钢技术中心)摘要:目前钢铁行业面临的形势日趋严峻,钢材利润空间逐步降低。
降本增效成为企业发展的有效手段。
钢铁料消耗是占炼钢厂生产成本中比重最大的一项,同时又是诸多技术经济指标的综合体现。
本文从工艺环节出发,详细分析了炼钢、连铸各个环节对钢铁料消耗的影响,有针对性的采取措施逐个突破,降低钢铁料消耗工作取得了突破性成效。
关键词:钢铁料消耗成本炼钢Practice of reduce consumption of iron andsteel materialsLi Shuangwu Wang Shengjin Zhou Yuzhen( NO. 2 Steel and Rolling Plant of Tang Steel,Hebei Iron and Steel Group ) Abstract:The current situation facing the steel industry become more acute, gra dually reduce the profit margins of steel. Reducing cost and increasing to beco me an eff-ective means of business development. Steel consumption is expecte d to account for the largest share of the cost of steel plant production, is also integrated many technical and economic indicators reflected. This process detai led the impact of the steel material consumption from analysis of the steel-ma king Department and casting all aspects of the Department. targeted measures t o break one by one, and made a breakthrough results.Key words:The cost of steel-making iron;Cost;Steel- making;0 前言目前钢铁行业面临的形势日趋严峻,行业竞争日益激烈,钢材利润空间逐步降低。
炼铁厂降本增效总结5篇
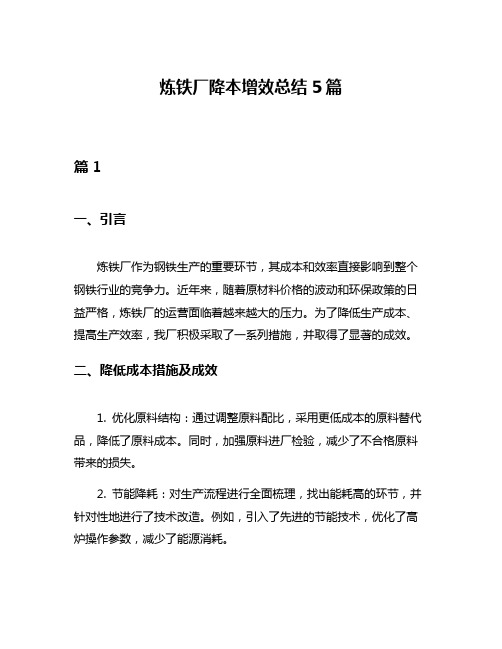
炼铁厂降本增效总结5篇篇1一、引言炼铁厂作为钢铁生产的重要环节,其成本和效率直接影响到整个钢铁行业的竞争力。
近年来,随着原材料价格的波动和环保政策的日益严格,炼铁厂的运营面临着越来越大的压力。
为了降低生产成本、提高生产效率,我厂积极采取了一系列措施,并取得了显著的成效。
二、降低成本措施及成效1. 优化原料结构:通过调整原料配比,采用更低成本的原料替代品,降低了原料成本。
同时,加强原料进厂检验,减少了不合格原料带来的损失。
2. 节能降耗:对生产流程进行全面梳理,找出能耗高的环节,并针对性地进行了技术改造。
例如,引入了先进的节能技术,优化了高炉操作参数,减少了能源消耗。
3. 降低维护成本:建立了完善的设备维护保养制度,加强了设备的日常巡检和维护,减少了设备故障率。
同时,采用了性价比较高的备件和材料,降低了维护成本。
4. 强化生产组织:通过优化生产流程,合理安排生产计划,减少了生产过程中的等待和浪费。
同时,加强了生产现场的管理,提高了生产人员的操作技能和效率。
三、提高效率措施及成效1. 引入自动化技术:对生产线进行了自动化改造,引入了先进的自动化控制系统和智能检测设备。
例如,高炉自动化控制系统的应用,提高了高炉操作的稳定性和效率。
2. 优化生产布局:根据生产需要和市场变化,对生产布局进行了优化调整,减少了生产环节的冗余和浪费。
同时,采用了更高效的物流配送方式,降低了生产成本。
3. 加强员工培训:定期对员工进行技能培训和岗位练兵活动,提高了员工的操作技能和效率。
同时,建立了激励机制,激发了员工的工作积极性和创造力。
4. 强化现场管理:通过加强现场巡检和监督力度,及时发现问题并解决问题。
同时,推行5S管理法,改善了现场环境和工作条件,提高了生产效率。
四、总结与展望通过采取一系列降低成本和提高效率的措施,我厂在生产经营方面取得了显著成效。
不仅降低了生产成本、提高了生产效率,还增强了企业的市场竞争力。
未来,我们将继续关注行业发展趋势和竞争对手情况,不断优化生产流程和管理制度,以保持领先优势。
炼钢全流程钢铁料消耗的实践与分析
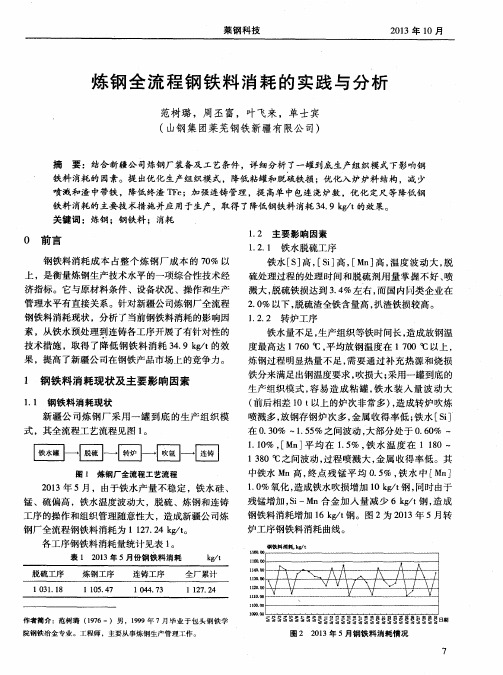
喷溅多 , 放钢存钢炉次多, 金属收得率低 ; 铁水 [ s i ]
在0 . 3 0 % 一1 . 5 5 % 之 间波动 , 大部 分 处 于 0 . 6 0 % ~ 1 . 1 0 %, [ Mn ] 平均 在 1 . 5 %, 铁水 温度 在 1 1 8 0~
1 . 2 . 2 转炉工 序
济指标。它与原材料条件、设备状况 、操作 和生产
管理 水平 有直 接关 系 。针对 新疆 公 司炼钢 厂全 流程
钢铁料消耗现状,分析 了当前钢铁料消耗的影响因 素, 从铁水预处理到连铸各工序开展了有针对性 的 技术措施 ,取得 了降低钢铁料消耗 3 4 . 9 k g / t 的效 果 ,提 高 了新疆 公 司在钢 铁产 品市 场上 的竞 争力 。
钢铁料消耗。 k Wt
i 瑚 . ∞
2 0 1 3年 5月 ,由于铁 水 产 量 不稳 定 ,铁 水 硅 、 锰 、硫偏 高 ,铁水 温度 波 动大 ,脱硫 、炼 钢和 连铸 工序 的操作 和 组织 管理 随意性 大 ,造 成新 疆公 司炼 钢厂 全流 程钢 铁料 消耗 为 1 1 2 7 . 2 4 k g / t 。
1 . 1 钢 铁料 消 耗现状
铁 分来 满足 出钢 温度要 求 , 吹损 大 ; 采 用一 罐到底 的 生 产组 织模 式 , 容易造成粘罐 , 铁 水 装 入 量 波 动 大 ( 前 后相 差 1 0 t 以上 的炉次 非 常 多 ) , 造 成 转 炉 吹炼
新疆公 司炼钢 厂采用一罐到底 的生产组织模
目的。经过对顶底复吹转炉氧枪枪位控制的调查研
究 ,提出 了吹炼过 程 的枪位 控制制 度 ,见 图 4 。
降低钢铁料消耗实现降本增效
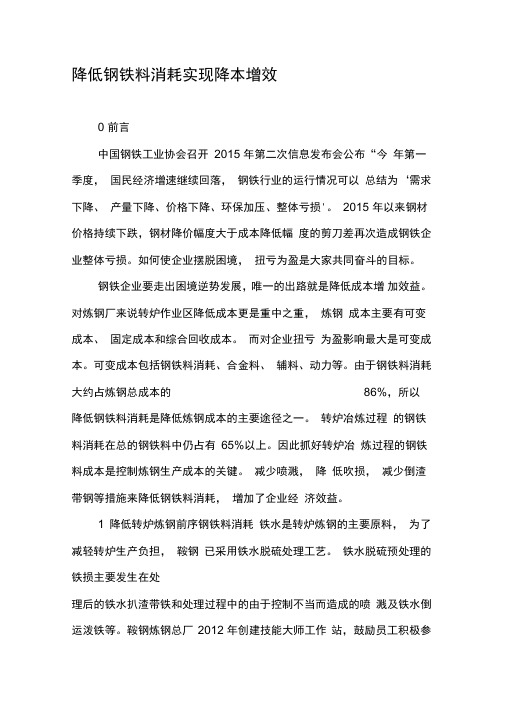
降低钢铁料消耗实现降本增效0 前言中国钢铁工业协会召开2015 年第二次信息发布会公布“今年第一季度,国民经济增速继续回落,钢铁行业的运行情况可以总结为‘需求下降、产量下降、价格下降、环保加压、整体亏损'。
2015 年以来钢材价格持续下跌,钢材降价幅度大于成本降低幅度的剪刀差再次造成钢铁企业整体亏损。
如何使企业摆脱困境,扭亏为盈是大家共同奋斗的目标。
钢铁企业要走出困境逆势发展,唯一的出路就是降低成本增加效益。
对炼钢厂来说转炉作业区降低成本更是重中之重,炼钢成本主要有可变成本、固定成本和综合回收成本。
而对企业扭亏为盈影响最大是可变成本。
可变成本包括钢铁料消耗、合金料、辅料、动力等。
由于钢铁料消耗大约占炼钢总成本的86%,所以降低钢铁料消耗是降低炼钢成本的主要途径之一。
转炉冶炼过程的钢铁料消耗在总的钢铁料中仍占有65%以上。
因此抓好转炉冶炼过程的钢铁料成本是控制炼钢生产成本的关键。
减少喷溅,降低吹损,减少倒渣带钢等措施来降低钢铁料消耗,增加了企业经济效益。
1 降低转炉炼钢前序钢铁料消耗铁水是转炉炼钢的主要原料,为了减轻转炉生产负担,鞍钢已采用铁水脱硫处理工艺。
铁水脱硫预处理的铁损主要发生在处理后的铁水扒渣带铁和处理过程中的由于控制不当而造成的喷溅及铁水倒运泼铁等。
鞍钢炼钢总厂2012 年创建技能大师工作站,鼓励员工积极参与创新活动,各作业区各班组相互交流学习,同时注重先进操作法的推广。
为减少脱硫扒渣带铁的问题,炼钢总厂各车间推行四控扒渣操作法,可显著降低扒渣操作中的铁水损失,扒渣铁损至少降低15Kg/t 钢。
按2014 年鞍山钢铁产钢2145 万吨,则可减少铁损32.175 万吨。
员工们发挥鞍钢宪法精神积极参与,形成一个又一个可控操作经验,有效地减少了铁水喷溅的损耗。
同时鞍钢采用高炉――转炉“一罐到底”的方式,减少了倒罐次数,降低了铁水热量的损失,减少了铁水的倒运损失,同时也减少了环境的污染,从而有效地降低了转炉钢铁料的损耗。
降低材料损耗的措施
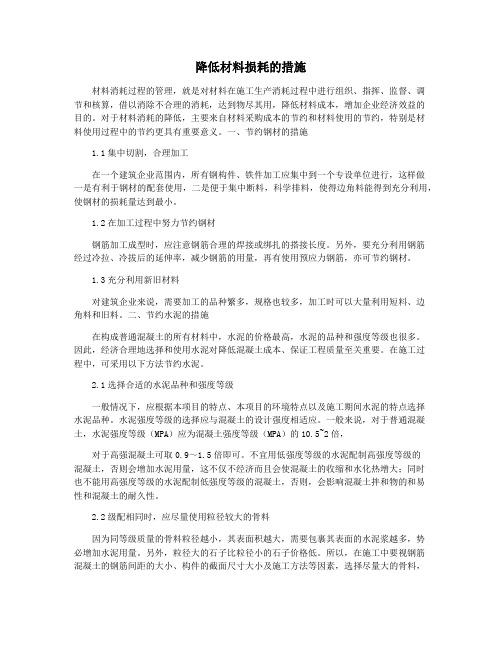
降低材料损耗的措施材料消耗过程的管理,就是对材料在施工生产消耗过程中进行组织、指挥、监督、调节和核算,借以消除不合理的消耗,达到物尽其用,降低材料成本,增加企业经济效益的目的。
对于材料消耗的降低,主要来自材料采购成本的节约和材料使用的节约,特别是材料使用过程中的节约更具有重要意义。
一、节约钢材的措施1.1集中切割,合理加工在一个建筑企业范围内,所有钢构件、铁件加工应集中到一个专设单位进行,这样做一是有利于钢材的配套使用,二是便于集中断料,科学排料,使得边角料能得到充分利用,使钢材的损耗量达到最小。
1.2在加工过程中努力节约钢材钢筋加工成型时,应注意钢筋合理的焊接或绑扎的搭接长度。
另外,要充分利用钢筋经过冷拉、冷拔后的延伸率,减少钢筋的用量,再有使用预应力钢筋,亦可节约钢材。
1.3充分利用新旧材料对建筑企业来说,需要加工的品种繁多,规格也较多,加工时可以大量利用短料、边角料和旧料。
二、节约水泥的措施在构成普通混凝土的所有材料中,水泥的价格最高,水泥的品种和强度等级也很多。
因此,经济合理地选择和使用水泥对降低混凝土成本、保证工程质量至关重要。
在施工过程中,可采用以下方法节约水泥。
2.1选择合适的水泥品种和强度等级一般情况下,应根据本项目的特点、本项目的环境特点以及施工期间水泥的特点选择水泥品种。
水泥强度等级的选择应与混凝土的设计强度相适应。
一般来说,对于普通混凝土,水泥强度等级(MPA)应为混凝土强度等级(MPA)的10.5~2倍,对于高强混凝土可取0.9~1.5倍即可。
不宜用低强度等级的水泥配制高强度等级的混凝土,否则会增加水泥用量,这不仅不经济而且会使混凝土的收缩和水化热增大;同时也不能用高强度等级的水泥配制低强度等级的混凝土,否则,会影响混凝土拌和物的和易性和混凝土的耐久性。
2.2级配相同时,应尽量使用粒径较大的骨料因为同等级质量的骨料粒径越小,其表面积越大,需要包裹其表面的水泥浆越多,势必增加水泥用量。
降低钢铁料消耗实践
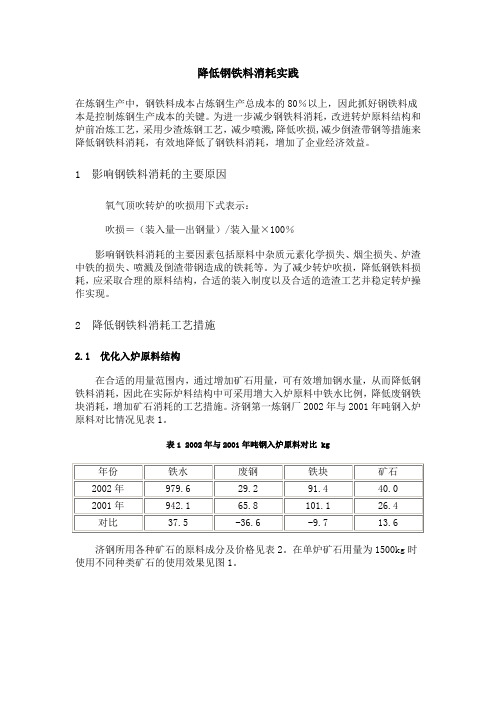
降低钢铁料消耗实践在炼钢生产中,钢铁料成本占炼钢生产总成本的80%以上,因此抓好钢铁料成本是控制炼钢生产成本的关键。
为进一步减少钢铁料消耗,改进转炉原料结构和炉前冶炼工艺,采用少渣炼钢工艺,减少喷溅,降低吹损,减少倒渣带钢等措施来降低钢铁料消耗,有效地降低了钢铁料消耗,增加了企业经济效益。
1 影响钢铁料消耗的主要原因氧气顶吹转炉的吹损用下式表示:吹损=(装入量—出钢量)/装入量×100%影响钢铁料消耗的主要因素包括原料中杂质元素化学损失、烟尘损失、炉渣中铁的损失、喷溅及倒渣带钢造成的铁耗等。
为了减少转炉吹损,降低钢铁料损耗,应采取合理的原料结构,合适的装入制度以及合适的造渣工艺并稳定转炉操作实现。
2 降低钢铁料消耗工艺措施2.1 优化入炉原料结构在合适的用量范围内,通过增加矿石用量,可有效增加钢水量,从而降低钢铁料消耗,因此在实际炉料结构中可采用增大入炉原料中铁水比例,降低废钢铁块消耗,增加矿石消耗的工艺措施。
济钢第一炼钢厂2002年与2001年吨钢入炉原料对比情况见表1。
表1 2002年与2001年吨钢入炉原料对比 kg年份铁水废钢铁块矿石2002年979.6 29.2 91.4 40.02001年942.1 65.8 101.1 26.4对比37.5 -36.6 -9.7 13.6济钢所用各种矿石的原料成分及价格见表2。
在单炉矿石用量为1500kg时使用不同种类矿石的使用效果见图1。
图1 三种矿石使用效益对比图表2 各种矿石原料成分及价格 %种类TFe Fe2O3SiO2价格/元·t-1黑旺矿43.5 62.1 13.0 162澳矿65.0 92.0 3.0 297球团矿65.0 92.0 3.0 400实际生产中,由于黑旺矿中SiO2含量较高,因此即便造渣料加入总量相同情况下,使用黑旺矿产生渣量也较多,造成渣中铁耗也较高,同时由于黑旺矿块度较大,在转炉吹炼过程中往往熔化不好,既降低了使用效果,又不利于转炉化渣。
钢铁生产中的节能减排方案

钢铁生产中的节能减排方案
钢铁生产是一个能耗较高、排放量较大的行业,因此在开展生产过程中采取节
能减排方案显得尤为重要。
以下是一些针对钢铁生产中节能减排的方案:
1. 提高焦炉煤气利用率:焦炉煤气是钢铁生产中的副产品,通过采用余热锅炉
等设备,可以将焦炉煤气中的热能回收利用,提高能源利用率,降低能耗。
2. 使用先进的高炉炉料预处理技术:通过对高炉炉料的预处理,可以提高炉石、焦炭和铁矿石的利用率,降低能耗和排放量。
3. 采用先进的炼钢技术:利用先进的炼钢技术,如转炉炼钢、电炉炼钢等,可
以降低原料、能耗和排放量,提高钢铁生产的效率和品质。
4. 推广能源替代技术:在钢铁生产中推广使用煤气发电、焦炉余热发电等能源
替代技术,减少对传统煤炭等能源的依赖,降低碳排放。
5. 完善废气处理系统:加强对钢铁生产过程中废气的处理,采用先进的除尘、
脱硫、脱硝等设备,降低废气的排放浓度,保护环境。
6. 提倡循环经济理念:建立钢铁生产的循环经济体系,促进废渣、废水等资源
的再利用,减少资源浪费和环境污染。
在实施上述节能减排方案的同时,企业应加强管理,建立科学的能源管理体系、环境管理体系,制定详细的节能减排计划,鼓励员工参与节能减排工作,形成全员参与的节能减排氛围。
同时,政府应出台相应政策,加大对节能减排技术研究和推广的支持力度,引导钢铁生产企业朝着绿色、低碳、可持续发展的方向前进。
总的来说,钢铁生产中的节能减排方案有着重要的意义,是企业应尽的社会责任,也是实现可持续发展的必由之路。
通过不断改进技术、管理和政策的手段,钢铁生产行业可以实现更环保、更高效的生产模式,为建设美丽中国作出贡献。
炼钢钢铁料消耗存在问题与解决方案

炼钢钢铁料消耗存在问题与解决方案炼钢厂自2004年开展钢铁料攻关活动以来,通过扎实细致的工作,总体上钢铁料消耗出现持续下降的趋势。
其主要内容表现在统计体系形成、原料稳定技术、技术改造革新、过程消耗控制、提高钢坯质量等方面。
统计体系方面,进出厂物料全部计量,钢铁料消耗数据、各项指标统计到班组,做实台帐便于分析。
原料稳定方面,石灰实行分仓上料,铁水进行满进满出、成分数据网络传输,废钢配比以吸盘为单位稳定配比,钢包控制钢包周转数量、每炉通报包况及空冷时间,转炉渣料系统根据原料条件分阶段固定配比模式。
技术改造革新方面,进行转炉扩容,对出钢口、氧枪喷头、在线烘烤等改造,开展降低出钢温度、连铸高效化等攻关。
过程消耗方面,转炉以转炉炉型和喷溅控制为关键、多料化渣降低石灰单耗;连铸以控制事故为主,减少中间包剩钢、非定尺等消耗,对这些内容考核到人。
提高钢坯质量方面,细化各项指标,政策引导考核激励,每月兑现工艺质量奖励十几万元;拉开收入档次,依靠指标挣钱的观念深入人心,使各项指标得到不断提升。
一、炼钢1-5月份消耗情况截止5月底累计钢铁料消耗1084.9kg/t,其中2-4月份主要是因库存量大,盘库库存误差,入炉原料质量结构等因素影响消耗数据较低,1、5月份消耗比较高,从大的区间数据分析,在现有原料条件下,炼钢实际消耗的能力在1085kg/t左右。
表1: 2010年1-5月钢铁料消耗对比表今年元月份两座1280高炉不正常,全月铁水硅高达0.92%,比前几个月高出0.25%,而且铁量少,铁水成分波动大。
石灰方面由于山西灰几度中断,烧结2#仓灰多次供应不足,导致频繁使用烧结1#石灰(其整体生烧偏大、杂质较多),且配比不能稳定,对消耗产生了一定影响,元月份消耗达到1094.2kg/t。
面对元月份存在的困难和问题,炼钢厂在积极降低铁水单耗提升产量的同时,废品控制、中间包剩钢量等达到历史最好水平;降低并严格控制总装入量,采取相应措施细化过程操作控制;在铁水平均硅含量大幅升高的条件下,严格控制石灰单耗,石灰单耗仅比目标上升2.4kg/t;钢铁料消耗上升确实属于原料条件的严重恶化程度已远远超出炼钢生产控制的能力范围。
降低转炉铁水单耗实践

降低转炉铁水单耗实践转炉炼钢是钢铁冶炼的重要方式之一,对于提高钢材质量、降低成本、保护环境等方面都有着重要的意义。
而降低转炉铁水单耗,即每吨钢的电耗和煤耗,是提高转炉操作效率和节约能源的关键。
本文将从实践角度来探讨如何降低转炉铁水单耗,为转炉炼钢工程提供一些有益的经验和建议。
一、加强原料预热在转炉炼钢的过程中,原料的预热是非常重要的。
通过预热原料,可以提高炉料的温度,降低了炉料进入转炉时对能源的需求,从而降低了转炉处理过程中的能耗。
预热原料还可以提高了原料的反应性,使得转炉的冶炼效率得到提高。
在降低转炉铁水单耗方面,加强原料预热是一个重要的举措。
二、提高转炉操作水平转炉操作水平的高低直接关系到炉内炼钢过程的稳定性和效率。
要想降低转炉铁水单耗,就需要提高转炉操作水平,减少操作中的失误和不必要的损耗。
操作人员还应该深入了解转炉的工作原理,掌握其控制技术,做到炉况稳定、杂质少、铁水优质。
只有操作水平提高了,才能更好的控制转炉操作的能源消耗。
三、优化转炉操作流程对于提高转炉操作效率和节约能源来说,优化转炉操作流程是非常必要的。
在转炉炼钢的过程中,一些不必要的操作步骤和浪费动作会增加能源的消耗。
对转炉的操作流程应该进行全面的审查和优化,减少不必要的操作环节和时间,降低铁水单耗。
四、合理利用余热资源在转炉冶炼的过程中,会产生大量的余热资源。
合理利用这些余热资源,可以有效地降低能源的消耗。
可以采用余热发电、余热利用等措施,将转炉生产过程中的余热资源重新利用起来,达到节能降耗的目的。
五、加强设备维护和管理为了保证转炉设备的正常运行,减少转炉能源消耗,必须加强设备的维护和管理。
对设备的定期检查、保养和维修,可以有效地降低设备的故障率,提高设备的利用率,减少了转炉维修和更换设备的能源消耗。
转炉炼钢生产是一个相对复杂的过程,降低转炉铁水单耗需要全方位的综合措施。
只有通过不断的努力和探索,才能够找到适合自己企业的降低转炉铁水单耗的有效方法。
炼钢生产线中降低钢铁料消耗措施及实践
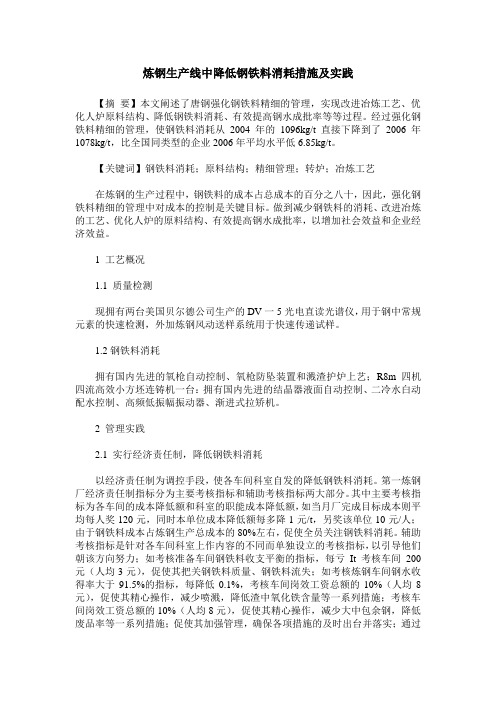
炼钢生产线中降低钢铁料消耗措施及实践【摘要】本文阐述了唐钢强化钢铁料精细的管理,实现改进冶炼工艺、优化人炉原料结构、降低钢铁料消耗、有效提高钢水成批率等等过程。
经过强化钢铁料精细的管理,使钢铁料消耗从2004年的1096kg/t直接下降到了2006年1078kg/t,比全国同类型的企业2006年平均水平低6.85kg/t。
【关键词】钢铁料消耗;原料结构;精细管理;转炉;冶炼工艺在炼钢的生产过程中,钢铁料的成本占总成本的百分之八十,因此,强化钢铁料精细的管理中对成本的控制是关键目标。
做到减少钢铁料的消耗、改进冶炼的工艺、优化人炉的原料结构、有效提高钢水成批率,以增加社会效益和企业经济效益。
1 工艺概况1.1 质量检测现拥有两台美国贝尔德公司生产的DV一5光电直读光谱仪,用于钢中常规元素的快速检测,外加炼钢风动送样系统用于快速传递试样。
1.2钢铁料消耗拥有国内先进的氧枪自动控制、氧枪防坠装置和溅渣护炉上艺;R8m四机四流高效小方坯连铸机一台:拥有国内先进的结晶器液面自动控制、二冷水白动配水控制、高频低振幅振动器、渐进式拉矫机。
2 管理实践2.1 实行经济责任制,降低钢铁料消耗以经济责任制为调控手段,使各车间科室自发的降低钢铁料消耗。
第一炼钢厂经济责任制指标分为主要考核指标和辅助考核指标两大部分。
其中主要考核指标为各车间的成本降低额和科室的职能成本降低额,如当月厂完成目标成本则平均每人奖120元,同时本单位成本降低额每多降1元/t,另奖该单位10元/人;由于钢铁料成本占炼钢生产总成本的80%左右,促使全员关注钢铁料消耗。
辅助考核指标是针对各车间科室上作内容的不同而单独设立的考核指标,以引导他们朝该方向努力;如考核准备车间钢铁料收支平衡的指标,每亏It考核车间200元(人均3元),促使其把关钢铁料质量、钢铁料流失;如考核炼钢车间钢水收得率大于91.5%的指标,每降低0.1%,考核车间岗效工资总额的10%(人均8元),促使其精心操作,减少喷溅,降低渣中氧化铁含量等一系列措施;考核车间岗效工资总额的10%(人均8元),促使其精心操作,减少大中包余钢,降低废品率等一系列措施;促使其加强管理,确保各项措施的及时出台并落实;通过以_L经济责任制的制定,使各车间科室自发的关注钢铁料消耗,全员千方百计想办法降低钢铁料消耗。
炼钢全流程降低钢铁料消耗的实践攻关
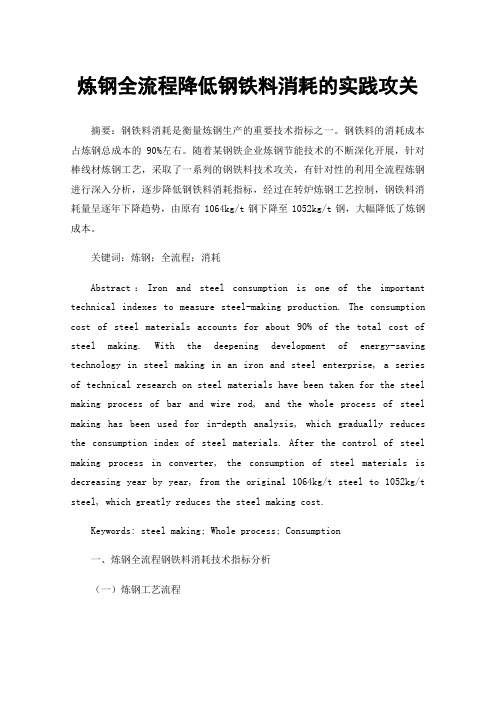
炼钢全流程降低钢铁料消耗的实践攻关摘要:钢铁料消耗是衡量炼钢生产的重要技术指标之一。
钢铁料的消耗成本占炼钢总成本的90%左右。
随着某钢铁企业炼钢节能技术的不断深化开展,针对棒线材炼钢工艺,采取了一系列的钢铁料技术攻关,有针对性的利用全流程炼钢进行深入分析,逐步降低钢铁料消耗指标,经过在转炉炼钢工艺控制,钢铁料消耗量呈逐年下降趋势,由原有1064kg/t钢下降至1052kg/t钢,大幅降低了炼钢成本。
关键词:炼钢;全流程;消耗Abstract:Iron and steel consumption is one of the important technical indexes to measure steel-making production. The consumption cost of steel materials accounts for about 90% of the total cost of steel making. With the deepening development of energy-saving technology in steel making in an iron and steel enterprise, a series of technical research on steel materials have been taken for the steel making process of bar and wire rod, and the whole process of steel making has been used for in-depth analysis, which gradually reduces the consumption index of steel materials. After the control of steel making process in converter, the consumption of steel materials is decreasing year by year, from the original 1064kg/t steel to 1052kg/t steel, which greatly reduces the steel making cost.Keywords: steel making; Whole process; Consumption一、炼钢全流程钢铁料消耗技术指标分析(一)炼钢工艺流程图1 某钢铁企业炼钢工艺流程简图(二)钢铁料消耗统计分析某钢铁企业第二钢扎厂钢铁料消耗统计口径如下:钢铁料消耗(kg/t)=(铁水+废钢)(kg)/合格钢坯产量(t)。
- 1、下载文档前请自行甄别文档内容的完整性,平台不提供额外的编辑、内容补充、找答案等附加服务。
- 2、"仅部分预览"的文档,不可在线预览部分如存在完整性等问题,可反馈申请退款(可完整预览的文档不适用该条件!)。
- 3、如文档侵犯您的权益,请联系客服反馈,我们会尽快为您处理(人工客服工作时间:9:00-18:30)。
炼钢生产线中降低钢铁料消耗措施及实践
【摘要】本文阐述了唐钢强化钢铁料精细的管理,实现改进冶炼工艺、优化人炉原料结构、降低钢铁料消耗、有效提高钢水成批率等等过程。
经过强化钢铁料精细的管理,使钢铁料消耗从2004年的1096kg/t直接下降到了2006年1078kg/t,比全国同类型的企业2006年平均水平低6.85kg/t。
【关键词】钢铁料消耗;原料结构;精细管理;转炉;冶炼工艺
在炼钢的生产过程中,钢铁料的成本占总成本的百分之八十,因此,强化钢铁料精细的管理中对成本的控制是关键目标。
做到减少钢铁料的消耗、改进冶炼的工艺、优化人炉的原料结构、有效提高钢水成批率,以增加社会效益和企业经济效益。
1 工艺概况
1.1 质量检测
现拥有两台美国贝尔德公司生产的DV一5光电直读光谱仪,用于钢中常规元素的快速检测,外加炼钢风动送样系统用于快速传递试样。
1.2钢铁料消耗
拥有国内先进的氧枪自动控制、氧枪防坠装置和溅渣护炉上艺;R8m四机四流高效小方坯连铸机一台:拥有国内先进的结晶器液面自动控制、二冷水白动配水控制、高频低振幅振动器、渐进式拉矫机。
2 管理实践
2.1 实行经济责任制,降低钢铁料消耗
以经济责任制为调控手段,使各车间科室自发的降低钢铁料消耗。
第一炼钢厂经济责任制指标分为主要考核指标和辅助考核指标两大部分。
其中主要考核指标为各车间的成本降低额和科室的职能成本降低额,如当月厂完成目标成本则平均每人奖120元,同时本单位成本降低额每多降1元/t,另奖该单位10元/人;由于钢铁料成本占炼钢生产总成本的80%左右,促使全员关注钢铁料消耗。
辅助考核指标是针对各车间科室上作内容的不同而单独设立的考核指标,以引导他们朝该方向努力;如考核准备车间钢铁料收支平衡的指标,每亏It考核车间200元(人均3元),促使其把关钢铁料质量、钢铁料流失;如考核炼钢车间钢水收得率大于91.5%的指标,每降低0.1%,考核车间岗效工资总额的10%(人均8元),促使其精心操作,减少喷溅,降低渣中氧化铁含量等一系列措施;考核车间岗效工资总额的10%(人均8元),促使其精心操作,减少大中包余钢,降低废品率等一系列措施;促使其加强管理,确保各项措施的及时出台并落实;通过
以_L经济责任制的制定,使各车间科室自发的关注钢铁料消耗,全员千方百计想办法降低钢铁料消耗。
2.2 推行班组经济核算,严格数据化管理
唐钢第一炼钢厂成立了以厂党委朽记为组长的班组经济核算组织机构,各班组经济核算员每班按实际消耗情况和当班产量进行日核算、周分析、月总结,各车间、科室经济核算员按本车间、科室的工序成本构成情况每日、周、旬、月进行成本核算和分析,并且各项分析通过以系统发各车间科室和厂领导传阅。
通过班组经济核算使每个人、侮个班、每一车间科室、每一个厂领导了解当班、当日、当旬、当月数据化详细情况,做到及时总结分析,并制定落实整改措施。
2.3 成立钢铁料消耗攻关,强化钢铁料管理激励机制
唐钢一炼钢厂成立了以厂长为组长的节能降耗攻关领导小组,钢铁料消耗攻关是其中最重要的一个节能降耗攻关小组。
攻关小组分两档指标,完成一档指标开始计奖,指标在一档与二档之间根据指标完成情况按比例在一档奖金基础上迫加奖励;未完成一档指标,对攻关小组组长及责任人按一档个人应得奖励进行考核;同时结合当月指标与全年累计指标完成情况对攻关小组进行奖励与考核:当月完成,累计完成,兑现当月应得奖励;累计未完成,兑现当月应得奖励的SO%;当月未完成,累计完成,不奖不罚;当月未完成,累计未完成,当月兑现考核;全年累计完成按全年应得奖励一已发奖励+已考核金额进行补奖。
攻关小组的成立,极大地激励了各小组成员的责任心和聪明才智,做到了无漏洞管理。
3 工艺技术实践
3.1 影响钢铁料消耗的主要原因
钢水收得率是出钢量与钢铁料装人量之比。
装人量是指一炉钢包括铁水与废钢总量,唐钢第一炼钢厂的装人量包括铁水、生铁、外购废钢、自产冻块、尾坯和炉下散状渣铁粒。
可以看出,影响钢铁料消耗的主要因素包括原料中杂质元素化学损失、烟尘损失、炉渣中铁的损失、喷溅及倒渣带钢造成的铁耗等。
为了提高钢水收得率,降低钢铁料损耗,应采取合理的原料结构、合适的装人制度和合适的造渣工艺并稳定转炉操作实现。
3.2 降低钢铁料消耗工艺措施
3.2.1 优化入炉原料结构
同比可知,废钢铁比铁水氧化少,同时带给炉内的渣量少,其理论钢水收得率高较多。
因此,在合适的外部冶炼条件和用量范围内,保证冶炼热量平衡,通过增加炉下自产散状渣钢用量,可有效增加钢水量,从而降低钢铁料消耗,同时
炉下散状渣钢不需要成本,进而可大幅降低钢铁料成本。
3.2.2 改进造渣工艺,减少妒渣铁耗
3.2.2.1 渣童分析
控制良好的终点渣况,及时更换出钢口砖和规范过程维护,同时注意后大面的喷补,强化加球小车的维护调整和加球操作,始终关注挡渣球的质量状况,确保炉内钢水出尽出完的同时合理有效控制下渣,减少钢水氧化和提高合金收得率。
3.2.2.2 改进吹炼工艺,降低喷城损失
为消除或减轻喷溅采取了以下措施:(1)适当提高炉容比,在对转炉扩容的基础上对转炉炉衬结构进行了改进,工作层全部采用镁碳砖炉衬,减少了炉衬厚度,从而增加了炉内有效容积,同时采用合理的炉型结构,以利于喷溅物的反射。
(2)合理控制转炉装人量和控制造渣料用量,以便减薄渣层。
根据炉龄和炉衬情况采用分阶段定量装人法,在炉役前期适当减少装人量,保证炉内有效工作容积。
(3)改进化渣工艺,保证前期化好渣,在二批造渣料加入前后,通过提前成渣的方法,将泡沫渣的高峰期前移,以便与脱碳的峰值时刻错开。
(4)在脱碳的高峰期到达之前.时提高枪位,然后再将其平缓地恢复到正常值。
(5)吹炼终期采用压枪位操作,加强熔池搅拌,保证终点钢水成分和温度的均匀,同时降低炉渣氧化性。
3.2.3改进其他配套工艺,创造良好的降低钢铁料消耗条件
(1)提高混铁炉铁水温度,保证铁水温度在1200℃以上;
(2)引进出钢下渣检测装置,防止钢渣进人钢包内,提高合金收得率、降低钢水氧含量;
(3)改进中间包浸人式水口,降低连铸中废;
(4)改进连铸火焰切割装置和气源类型,通过减少割缝以降低钢铁料消耗;
(5)调节钢水成份,保证钢水流动性和可浇性,确保连铸生产稳顺,减少钢水损失和回炉。
3.3 加快VD的建设
VD是一种广泛应用的真空精炼设备,具有良好的脱氢、脱氧、脱碳、脱氮和脱硫的功能,
在目前的高质量高附加值钢(如轴承钢、82B等)生产中发挥着重要作用。
韶钢将来的产品规划中管线钢、焊条钢、16Mn系列等钢种都需要进行VD处理,三炼钢厂预留了VD装置,应该尽快建设提高产品的二次精炼能力以满足市场的需要。
4 结语
韶钢当前采用的沽净钢冶炼技术还只能满足中低档产品的质量要求,如果从长远的产品规划和市场需要考虑,必须重视以下间题:(1)韶钢由于只有铁水预脱硫,而铁水是属于中磷铁水,因此在冶炼高品质低时还是个瓶颈,故需考虑双渣法脱磷并使其工艺流程规范化。
(2)由于韶关地区的矿石资源特点低熔点元素含量较高,因此需深入研究这些微量元素对钢材性能的影响并积极寻找对应措施(如进行稀土处理。
(3)喂稀土丝进行钢质净化以提高钢材的低温冲击韧性必须研究稀土对保护渣的影响,以选择使用合适的保护清。
(4)必须优化中包精炼技术,如增加挡墙、使用湍流控制器和中间包底吹氮气等。
(5)进一步完善二次精炼能力,加快VD的建设。
同时加快中试场的建设,以进行冶炼、精炼工艺参数的热模拟试验。
参考文献
[1]杨世山,尹卫平等.铁水预处理与纯净钢冶炼.中国冶金,2003
[2]潘秀兰,郭艳玲等.国内外纯净钢生产技术新进展.鞍钢技术,2003.
[3]杜挺.稀土元素在金属材料中的一些物理化学作用.金属学报,1997.。