xxds_24
Hikvision DS-2SE7C425MW-AEB(14F1)(P3) 4 MP 25 × IR

DS-2SE7C425MW-AEB(14F1)(P3) 4 MP 25 × IR Network Speed DomeHikvision DS-2SE7C425MW-AEB(14F1)(P3) 4 MP 25 × IR Network Speed Dome adopts 1/2.8" progressive scan CMOS chip. With the 25 × optical zoom lens, the camera offers more details over expansive areas. This series of cameras can be widely used for wide ranges of high-definition, such as rivers, roads, railways, airports, squares, parks, scenic spots, and venues, etc.⏹Captures a large area and great details at the same time ⏹High quality imaging with 4 MP resolution⏹Excellent low-light performance withpowered-by-DarkFighter technology⏹Secures an expansive area with 25× optical zoom and 16× digital zoom⏹Supports WDR, HLC, BLC, 3D DNR, defog, regional exposure, regional focus⏹Expansive night view with up to 200 m IR distance⏹Supports 24 VAC & Hi-PoE⏹Active strobe light and audio alarm to warn intruders off⏹DORIThe DORI (detect, observe, recognize, identify) distance gives the general idea of the camera ability to distinguish persons or objects within its field of view. It is calculated based on the camera sensor specification and the criteria given by EN 62676-4: 2015.DORI Detect Observe Recognize IdentifyDefinition25 px/m63 px/m125 px/m250 px/m Distance (Tele)2200.0 m (7217.8 ft)873.0 m (2864.2 ft)440.0 m (1443.6 ft)220.0 m (721.8 ft)⏹SpecificationCameraImage Sensor [Bullet channel]: 1/1.8" Progressive Scan CMOS; [PTZ channel]: 1/1.8" progressive scan CMOSMin. Illumination [Bullet channel]: 0.0005 Lux @ (F1.0, AGC ON), 0 Lux with light;[PTZ channel]: Color: 0.005 Lux @ (F1.6, AGC ON), B/W: 0.001 Lux @ (F1.6, AGC ON), 0 Lux with IRShutter Speed 1 s to 1/30,000 sSlow Shutter YesFocus semi-auto, manual, autoDay & Night ICRDay/Night Switch day, night, auto, scheduled-switchBLC YesWDR 120 dB WDRHLC Yes3D DNR YesDefog YesEIS YesRegional Exposure YesRegional Focus YesImage Settings saturation, brightness, contrast, sharpnessImage Parameters Switch [Bullet channel]: yes; [PTZ channel]: yesWhite Balance auto, ATW, sodium lamp, fluorescent lamp, indoor, outdoor, MWB, Locked WB Zoom [PTZ channel] 25 × optical, 16 × digitalPrivacy Mask polygon region, mosaic mask, mask color configurable, [Bullet channel] 8 masks, [PTZ channel] 24 masksSNR >52dBGeneral Function mirror, password protection, watermark, IP address filterLensFocal Length [Bullet channel]: 4 mm; [PTZ channel]: 4.8 to 120 mm, 25 × optical Zoom Speed [PTZ channel]: approx. 3.6 sFOV [Bullet channel]: Horizontal field of view: 88.7°, Vertical field of view: 44.7°; [PTZ channel]:Horizontal field of view: 55° to 2.4° (wide-tele)Vertical field of view: 33° to 1.4° (wide-tele),Diagonal field of view: 61.5° to 2.8° (wide-tele)Aperture [Bullet channel]: F1.0; [PTZ channel]: F1.6IlluminatorSupplement Light Type [PTZ channel]: IR; [Bullet channel]: White LightSmart Supplement Light YesSupplement Light Range [PTZ channel]: up to 200 m; [Bullet channel]: up to 30 mPTZMovement Range (Pan) 360°Movement Range (Tilt) -15° to 90° (auto flip)Pan Speed pan speed: configurable from 0.1° to 160°/s; preset speed: 240°/s Tilt Speed tilt speed: configurable from 0.1° to 120°/s, preset speed 200°/s Proportional Zoom YesPresets 300Patrol Scan 8 patrols, up to 32 presets for each patrolPattern Scan 4 pattern scansPower-off Memory YesPark Action preset, pattern scan, patrol scan, auto scan, tilt scan, random scan, frame scan, panorama scan3D Positioning Yes PTZ Status Display Yes Preset Freezing YesScheduled Task preset, pattern scan, patrol scan, auto scan, tilt scan, random scan, frame scan, panorama scan, dome reboot, dome adjust, aux outputException Detection IP address conflict, HDD full, illegal login, HDD error, network disconnected VideoMax. Resolution [Bullet channel]: 2560 × 1440; [PTZ channel]: 2560 × 1440Stream Type main stream, sub-stream, third streamMain Stream [Bullet channel]:50 Hz: 25 fps (2560 × 1440, 1920 × 1080, 1280 × 960, 1280 × 720) 60 Hz: 30 fps (2560 × 1440, 1920 × 1080, 1280 × 960, 1280 × 720) [PTZ channel]:50 Hz: 25 fps (2560 × 1440, 1920 × 1080, 1280 × 960, 1280 × 720) 60 Hz: 30 fps (2560 × 1440, 1920 × 1080, 1280 × 960, 1280 × 720)Sub-Stream [Bullet channel]:50 Hz: 25 fps (704 × 576, 640 × 480, 352 × 288) 60 Hz: 30 fps (704 × 480, 640 × 480, 352 × 240) [PTZ channel]:50 Hz: 25 fps (704 × 576, 640 × 480, 352 × 288) 60 Hz: 30 fps (704 × 480, 640 × 480, 352 × 240)Third Stream [Bullet channel]:50 Hz: 25 fps (1920 × 1080, 1280 × 960, 1280 × 720, 704 × 576, 640 × 480, 352 × 288) 60 Hz: 30 fps (1920 × 1080, 1280 × 960, 1280 × 720, 704 × 480, 640 × 480, 352 × 240) [PTZ channel]:50 Hz: 25 fps (1920 × 1080, 1280 × 960, 1280 × 720, 704 × 576, 640 × 480, 352 × 288) 60 Hz: 30 fps (1920 × 1080, 1280 × 960, 1280 × 720, 704 × 480, 640 × 480, 352 × 240)Video Compression H.265, H.264, MJPEGVideo Bit Rate 32 kbps to 16384 kbpsH.264 Type baseline profile, main profile, high profileH.265 Type main profileH.264+ YesH.265+ YesSVC YesROI Main stream, sub-stream and third stream respectively support eight fixed areas AudioAudio Compression G.711, G.722.1, G.726, MP2L2, PCMAudio Bit rate 32 to 192 Kbps (MP2L2)Audio Sampling Rate 8 kHz, 16 kHz, 32 kHz, 48 kHzEnvironment Noise Filtering YesSmart FeaturesFace Capture [Bullet channel] no [PTZ channel] yesBasic Event [PTZ channel] motion detection, video tampering alarm[PTZ channel & bullet channel] alarm input, alarm output, exceptionSmart Event [Bullet channel] intrusion detection, line crossing detection, region entrance detection, region exiting detection, audio exception detection[PTZ channel] intrusion detection, line crossing detection, region entrance detection, region exiting detection, audio exception detectionAuto Tracking [PTZ channel] yesSmart Linkage Manual tracking, auto tracking, tracking takeover, track in turn Smart Record ANR, Dual-VCAAlarm Linkage [Bullet channel] Upload to FTP/NAS/memory card, notify surveillance center, send email, trigger alarm output, trigger recording, audible warning, white light flashing [PTZ channel] Upload to FTP/NAS/memory card, notify surveillance center, send email, trigger alarm output, trigger recording, audible warning, white light flashing, and PTZ actions (such as preset, patrol scan, pattern scan)Warning and Alert white light and audible warning NetworkNetwork Storage NAS (NFS, SMB/ CIFS), ANRProtocols IPv4/IPv6, HTTP, HTTPS, 802.1x, QoS, FTP, SMTP, UPnP, SNMP, DNS, DDNS, NTP, RTSP, RTCP, RTP, TCP/IP, UDP, IGMP, ICMP, DHCP, PPPoE, Bonjour, Websocket, WebsocketsAPI Open-ended API, Open Network Video Interface (Profile S, Profile G), ISAPI, Hikvision SDK, Third-party management platform, ISUPSimultaneous Live View 20 User/Host 32Security Measures Authenticated username and password, MAC address binding, HTTPS encryption, 802.1X authenticated access, IP address filterClient iVMS-4200, Hik-ConnectWeb Browser IE 10+, Chrome 57+, Firefox 52+, Safari 12+InterfaceCommunication Interface RJ45, self-adaptive 10M/100M Ethernet portOn-board Storage Built-in memory card slot, support Micro SD/Micro SDHC/Micro SDXC, up to 256 GB Alarm Input 2 alarm inputsAlarm Output 1 alarm outputAudio Input 1 audio input, 2.0 to 2.4Vp-p, 1k Ohm±10%Audio Output 1 audio output, line level, impedance: 600 ΩGeneralPower 24 VAC, Hi-PoEPower Consumption and Current Max. 42 W, including max. 2.6 W for heater and max. 11 W for supplement light Operating Conditions -30°C to 65°C (-22°F to 149°F), humidity lower than 90%RHReset YesDemist Demist by heating the glassMaterial ADC12Dimensions Ø 220 mm × 382.1 mm (Ø 8.66" × 15.04")Weight Approx. 6 kg (13.23 lb.)ApprovalProtection IP66 Standard, IK10 (excluding glass window), 6000 V Lightning Protection, Surge Protection and Voltage Transient ProtectionAvailable ModelDS-2SE7C425MW-AEB(14F1)(P3)⏹Dimension⏹Accessory ⏹OptionalDS-1661ZJ Pendant Mount DS-1602ZJ-CornerCorner mountDS-1602ZJ-PoleVertical pole mountDS-1602ZJWall mountDS-1681ZJ-2Installation AdaptorDS-2681ZJ Cardan Joint。
Maximizing Performance on dsPIC33EP and PIC24EP - Channel Version

Architectural improvements enable faster extended precision math operations (mixed sign DSP mode) Take advantage of the Architecture’s enhancements:
DO Loops and Repeat Instructions for accessing constants in PSV
Interrupt Latency
Don’t call functions from within interrupt service routine Avoid unnecessary interrupts, maximize peripheral FIFO buffers
HPMD 3
New / Improved Peripherals dsPIC33E / PIC24E
dsPIC33E/PIC24EP512XX (64- to 144-pin) (Released) 512KB Flash/52KB RAM 64KB Flash/16KB RAM Auxiliary Flash (24KB) USB v2.0 OTG (w/ aux PLL) X -X X ---X X X X X X (up to 25) X X dsPIC33E/PIC24EP64XX (28- to 64-pin) (CQ4 ’11) -X --X X X X X X X X X (up to 11) X -4
HPMD 6
Extended Precision Data Support Enhancements
IDC D-Sub 连接器插座, 26-24AWG实心线条大小, .13-0.32mm
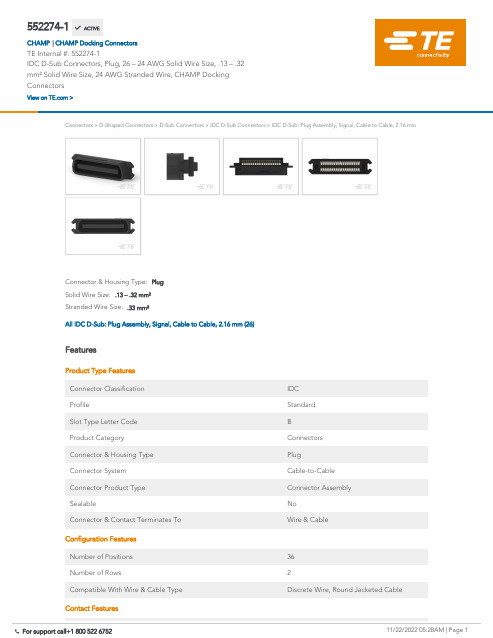
552274-1IDC D-Sub Connectors, Plug, 26 – 24 AWG Solid Wire Size, .13 – .32 mm² Solid Wire Size, 24 AWG Stranded Wire, CHAMP Docking ConnectorsConnectors > D-Shaped Connectors > D-Sub Connectors > IDC D-Sub Connectors >IDC D-Sub: Plug Assembly, Signal, Cable to Cable, 2.16 mmStranded Wire Size:.33 mm²Solid Wire Size:.13 – .32 mm²Connector & Housing Type:PlugAll IDC D-Sub: Plug Assembly, Signal, Cable to Cable, 2.16 mm (26)FeaturesProduct Type Features Connector Classification IDC ProfileStandard Slot Type Letter Code BProduct CategoryConnectors Connector & Housing Type PlugConnector System Cable-to-Cable Connector Product Type Connector Assembly SealableNoConnector & Contact Terminates To Wire & CableConfiguration Features Number of Positions 36Number of Rows2Compatible With Wire & Cable Type Discrete Wire, Round Jacketed CableContact Features552274-1 ACTIVECHAMP TE Internal #:552274-1IDC D-Sub Connectors, Plug, 26 – 24 AWG Solid Wire Size, .13 – .32 mm² Solid Wire Size, 24 AWG Stranded Wire, CHAMP Docking ConnectorsView on >CHAMP Docking Connectors|Contact Mating Area Plating Thickness.76 µm[30 µin]Contact Mating Area Plating Material Gold, Gold Flash, Gold Flash overPalladium NickelContact Underplating Material Palladium NickelContact Base Material Copper AlloyContact Current Rating (Max) 3.5 AMechanical AttachmentFlange Thickness ThickMating Connector Lock WithMating Connector Lock Type ScrewlocksPanel Mount Feature WithoutConnector Mounting Type Cable Mount (Free-Hanging) Housing FeaturesHousing Material ThermoplasticHousing Color Dot Designation BlueHousing Color BlackCenterline (Pitch) 2.16 mm[.085 in]DimensionsInsulation Diameter (Max) 1.14 mm[.045 in]Solid Wire Size.13 – .32 mm²Stranded Wire Size.33 mm²Wire Size24 AWGUsage ConditionsOperating Temperature Range-40 – 75 °C[-40 – 167 °F] Operation/ApplicationShielded NoCircuit Application SignalPackaging FeaturesPackaging Method Box & Tray, Package Packaging Quantity100Product ComplianceFor compliance documentation, visit the product page on >EU RoHS Directive 2011/65/EU Compliant EU ELV Directive 2000/53/ECCompliantChina RoHS 2 Directive MIIT Order No 32, 2016No Restricted Materials Above Threshold EU REACH Regulation (EC) No. 1907/2006Current ECHA Candidate List: JUNE 2022 (224)Candidate List Declared Against: JUNE 2022 (224)Does not contain REACH SVHCHalogen ContentLow Bromine/Chlorine - Br and Cl < 900 ppm per homogenous material. Also BFR /CFR/PVC FreeSolder Process CapabilityNot applicable for solder process capabilityProduct Compliance DisclaimerThis information is provided based on reasonable inquiry of our suppliers and represents our current actual knowledge based on the information they provided. This information is subject to change. The part numbers that TE has identified as EU RoHS compliant have a maximum concentration of 0.1% by weight in homogenous materials for lead, hexavalent chromium, mercury, PBB, PBDE, DBP, BBP, DEHP, DIBP, and 0.01% for cadmium, or qualify for an exemption to these limits as defined in the Annexes of Directive 2011/65/EU (RoHS2). Finished electrical and electronic equipment products will be CE marked as required by Directive 2011/65/EU. Components may not be CE marked. Additionally, the part numbers that TE has identified as EU ELV compliant have a maximum concentration of 0.1% by weight in homogenous materials for lead, hexavalent chromium, and mercury, and 0.01% for cadmium, or qualify for an exemption to these limits as defined in the Annexes of Directive 2000/53/EC (ELV). Regarding the REACH Regulation, the information TE provides on SVHC in articles for this part number is based on the latest European Chemicals Agency (ECHA) ‘Guidance on requirements for substances in articles’ posted at this URL: https://echa.europa.eu/guidance-documents/guidance-on-reachTE Part #230238-1EXTRACTORTE Part #229384-1TOOL, INSERTION, HAND, T-GRIPTE Part #229378-1ASSY, MI-1 TOOL,STD 14-50 POSNTE Part #CAT-357-D601IDC D-Sub: Receptacle Assembly, Signal, 2.16 mmCompatible PartsAlso in the Series CHAMP Docking ConnectorsTE Part #3-1437685-13TK2-48=SNAP TRACK,TERMINAL BLTE Part #3-6450820-5MBXL VERT HDR 3ACP + 4S + 2PTE Part #1-1939638-7DYNAMIC 1100D HDR ASSY H 34P XBLACK GOLDTE Part #171825-3POST HEADER ASSY EI SRS 3POSTE Part #3-640601-202P MTA156 CONN ASSY 22AWG LFTE Part #1-770166-002P MINI-UMNL ASSY VO SNNI*TE Part #3-640428-404P MTA156 CONN ASSY 22AWG REDTE Part #206306-123-37 RECEPT REV SEXTE Part #164163-2PIN ASSYTE Part #206430-2CPC 11-4 Free Hanging ReceptaclePCB D-Sub Connectors(1)IDC D-Sub Connectors(79)Docking Connectors(31)Docking Connector Guide Hardware(5)D-Sub Locking & Mounting(29)D-Sub Covers(28)Customers Also BoughtDocumentsProduct DrawingsASSY, PLUG, 36 POS, B SLOT EnglishCAD FilesCustomer View ModelENG_CVM_552274-1_M.3d_igs.zip EnglishCustomer View ModelENG_CVM_552274-1_M.3d_stp.zip EnglishCustomer View ModelENG_CVM_552274-1_M.2d_dxf.zip English3D PDFEnglishTerms and Conditions By downloading the CAD file I accept and agree to the of use. Product Specifications Application SpecificationEnglishProduct Environmental Compliance TE Material DeclarationEnglishAgency ApprovalsUL ReportEnglishUL ReportEnglish。
UR-24 chinese manual

安装、使用及维修手册数字折光仪UR-24型手册编号 n° 01246C0011适用于仪器编号 n°____________________Maselli测量仪器公司 墨西哥Maselli 测量仪器公司, S.A. de C.V. 地址:7746 Lorraine Avenue, Suite 201 地址:Plan de San Luis No. 101, Int. 301 Stockton, California 95210 USA(美国) Col. Coecillo, C.P. 37260 电话: (209) 474-9178 León, Gto., México(墨西哥)免费电话(仅适用美国): (800) 964-9600 电话、传真: (52) (47) 63-36-23 传真:(209) 474-9241 电话、传真: (52) (47) 63-36-38电子邮件:info@ 电子邮件:maselli@ciatec.mx本手册说明了仪器的主要特点。
同时包含有关安全使用、编程及维护工作的重要说明。
因此本手册必须妥善保管。
本手册还是设备的一个完整组成部分。
必须认真阅读本手册以后,方可以着手开展设备的安装、启动和使用。
对于因为不遵守设备的使用说明、违背有关使用地点的规定以及违背本手册中各项说明而造成的任何损坏,MASELLI Misure 公司宣布概不承担任何责任。
本使用手册由Maselli公司出版,但是不提供任何类型的保证。
手册中所包含的资料,仅仅是作为一种介绍。
由于存在着印刷错误,内容不准确,软件的改进,和/或设备、技术或商业条件的差异,Maselli Misure公司保留在任何时候对本手册做出变更的权利,事先不提供通知。
保留一切权利。
按照法律条款,未得到我方许可,严禁全部或部分地将本手册复制或传递给第三方。
Maselli Misure公司于2006年05月如果需要了解更多资料,请登陆Maselli公司网站。
24CXX中文资料

方框图
极限参数
工作温度 工业级 -55 +125
商业级 0 +75
贮存温度 -65 +150
各管脚承受电压 -2.0 Vcc+2.0V
Vcc 管脚承受电压 -2.0 +7.0V
封装功率损耗 Ta=25
1.0W
焊接温度(10 秒) 300
输出短路电流 100mA
可靠性参数
符号
概述
CAT24WC01/02/04/08/16 是 一 个 1K/2K/4K/8K/16K 位 串 行 CMOS E2PROM 内 部 含 有 128/256/512/1024/2048 个 8 位字节 CATALYST 公司的先进 CMOS 技术实质上减少了器件的功耗 CAT24WC01 有一个 8 字节页写缓冲器 CAT24WC02/04/08/16 有一个 16 字节页写缓冲器 该器件通过 I2C 总线接口进行操作 有一个专门的写保护功能
图 5 从器件地址位
1. A0 A1 和 A2 对应器件的管脚 1 2 和 3 2. a8 a9 和 a10 对应存储阵列地址字地址
7
微控实验网 单片机学习开发、电子制作驿站 http://www.mcusy.cn QQ:479780666 shenglinwan@126.com
管脚配置
管脚描述
管脚名称
A0 A1 A2 SDA SCL WP Vcc Vss
功能 器件地址选择 串行数据/地址 串行时钟 写保护 +1.8V 6.0V 工作电压 地
2
微控实验网 单片机学习开发、电子制作驿站 http://www.mcusy.cn QQ:479780666 shenglinwan@126.com
焊接工程一览表

(锅炉)焊接工程一览表
xxxxxxxxxx有限公司2013 年11 月10 日焊---01
专业知识分享
填表:审核:
(锅炉)焊接工程一览表
xxxxxxxxxx有限公司2013 年11 月10 日焊---01
专业知识分享
填表:审核:
(锅炉)焊接工程一览表
xxxxxxxxxx有限公司2013 年11月10 日焊---01
专业知识分享
填表:审核:
(锅炉)焊接工程一览表
xxxxxxxxxx有限公司2013 年11 月10 日焊---01
专业知识分享
填表:审核:
(锅炉)焊接工程一览表
焊---01
xxxxxxxxxx有限公司2013 年11 月10 日
专业知识分享
填表:审核:
(锅炉)焊接工程一览表
xxxxxxxxxx有限公司2013 年11 月10 日焊---01
专业知识分享
填表:审核:
(锅炉非承压部件)焊接工程一览表
xxxxxxxxxx有限公司2013 年11 月10 日焊---01
专业知识分享
填表:审核:
(锅炉非承压部件)焊接工程一览表
xxxxxxxxxx有限公司2013 年11 月10 日焊---01
专业知识分享
填表:审核:
焊接工艺评定项目及应用范围统计表
专业知识分享
注:依据①《锅炉安全技术监察规程》TSG G0001-2012 ②《承压设备焊接工艺评定》NB/T47014—2011(JB/T4708) ③关于执行《承压设备焊接工艺评定》NB/T47014—2011的意见)(质检特函<2011>102号④“焊接工艺评定报告”等编制本统计表
专业知识分享。
TMS320x28xx, 28xxx Enhanced Capture (ECAP) Module Reference Guide (Rev. A)

TMS320x28xx,28xxx Enhanced Capture(eCAP)ModuleReference GuideLiterature Number:SPRU807ANovember2004–Revised October20062SPRU807A–November2004–Revised October2006Submit Documentation FeedbackPreface (6)1Introduction (9)2Description (9)3Capture and APWM Operating Mode (10)4Capture Mode Description (12)4.1Event Prescaler (12)4.2Edge Polarity Select and Qualifier (13)4.3Continuous/One-Shot Control (13)4.432-Bit Counter and Phase Control (14)4.5CAP1-CAP4Registers (15)4.6Interrupt Control (15)4.7Shadow Load and Lockout Control (16)4.8APWM Mode Operation (17)5Capture Module-Control and Status Registers (18)6Register Mapping (26)7Application of the ECAP Module (27)7.1Example1-Absolute Time-Stamp Operation Rising Edge Trigger (28)7.2Example2-Absolute Time-Stamp Operation Rising and Falling Edge Trigger (30)7.3Example3-Time Difference(Delta)Operation Rising Edge Trigger (32)7.4Example4-Time Difference(Delta)Operation Rising and Falling Edge Trigger (34)8Application of the APWM Mode (36)8.1Example1-Simple PWM Generation(Independent Channel/s) (36)8.2Example2-Multi-channel PWM Generation With Synchronization (37)8.3Example3-Multi-channel PWM Generation With Phase Control (39)Appendix A Revision History (42)SPRU807A–November2004–Revised October2006Table of Contents3 Submit Documentation Feedback1Multiple eCAP Modules In A28x System (10)2Capture and APWM Modes of Operation (11)3Capture Function Diagram (12)4Event Prescale Control (13)5Prescale Function Waveforms (13)6Details of the Continuous/One-shot Block (14)7Details of the Counter and Synchronization Block (15)8Interrupts in eCAP Module (16)9PWM Waveform Details Of APWM Mode Operation (17)10Time-Stamp Counter Register(TSCTR) (18)11Counter Phase Control Register(CTRPHS) (18)12Capture-1Register(CAP1) (18)13Capture-2Register(CAP2) (18)14Capture-3Register(CAP3) (19)15Capture-4Register(CAP4) (19)16ECAP Control Register1(ECCTL1) (19)17ECAP Control Register2(ECCTL2) (21)18ECAP Interrupt Enable Register(ECEINT) (23)19ECAP Interrupt Flag Register(ECFLG) (24)20ECAP Interrupt Clear Register(ECCLR) (24)21ECAP Interrupt Forcing Register(ECFRC) (25)22Capture Sequence for Absolute Time-stamp and Rising Edge Detect (28)23Capture Sequence for Absolute Time-stamp With Rising and Falling Edge Detect (30)24Capture Sequence for Delta Mode Time-stamp and Rising Edge Detect (32)25Capture Sequence for Delta Mode Time-stamp With Rising and Falling Edge Detect (34)26PWM Waveform Details of APWM Mode Operation (36)27Multichannel PWM Example Using4eCAP Modules (38)28Multi-phase(channel)Interleaved PWM Example Using3eCAP Modules (40)4List of Figures SPRU807A–November2004–Revised October2006Submit Documentation Feedback1Time-Stamp Counter Register(TSCTR)Field Descriptions (18)2Counter Phase Control Register(CTRPHS)Field Descriptions (18)3Capture-1Register(CAP1)Field Descriptions (18)4Capture-2Register(CAP2)Field Descriptions (19)5Capture-3Register(CAP3)Field Descriptions (19)6Capture-4Register(CAP4)Field Descriptions (19)7ECAP Control Register1(ECCTL1)Field Descriptions (19)8ECAP Control Register2(ECCTL2)Field Descriptions (21)9ECAP Interrupt Enable Register(ECEINT)Field Descriptions (23)10ECAP Interrupt Flag Register(ECFLG)Field Descriptions (24)11ECAP Interrupt Clear Register(ECCLR)Field Descriptions (25)12ECAP Interrupt Forcing Register(ECFRC)Field Descriptions (25)13Control and Status Register Set (26)A-1Changes Made in This Revision (42)SPRU807A–November2004–Revised October2006List of Tables5 Submit Documentation FeedbackPrefaceSPRU807A–November2004–Revised October2006The enhanced capture(eCAP)module is used in systems where accurate timing ofexternal events is important.This guide describes the module and how to use it.Related Documentation From Texas InstrumentsThe following documents describe the TMS320C28x and related support tools and can be downloaded from the TI website():Data Manuals—SPRS357:contains the pinout,signalF28044device.User's Guides—SPRU051:describes theSCI,modulessupport digital communications between the CPU and other asynchronous peripherals that use thestandard non-return-to-zero(NRZ)format.SPRU059:describes the SPI-a ofprogrammed length(one to sixteen bits)to be shifted into and out of the device at a programmedbit-transfer rate.SPRU074:in electrically noisy environments.SPRU430:describes the centralfixed-point digital signal processors(DSPs).It also describes emulation features available on these DSPs.SPRU513:—describes the assembly languagetools code),assembler directives,macros,common object file format,and symbolic debugging directives for the TMS320C28x device.SPRU514:describes the TMS320C28x™C/C++code and produces TMS320DSP assembly language source code for the TMS320C28x device.SPRU566:describes the peripheral referenceguidesSPRU608:—describes the simulator,the instruction set of the C28x™core.6Preface SPRU807A–November2004–Revised October2006Submit Documentation FeedbackRelated Documentation From Texas Instruments SPRU625:SPRU712:describes the(DSPs).SPRU716:SPRU721:—describes the featuresand TMS320x280xdigital signal processor(DSP).SPRU722:describes the purpose andIt also describes other contents of the device on-chip boot ROM and identifies where all of the information is located withinthat memory.SPRU790:encoder to get position,direction,and speed information from a rotating machine in highperformance motion and position control systems.It includes the module description and registers SPRU791:switch mode power supply control,UPS(uninterruptible power supplies),and other forms of powerconversionSPRU807:describes theSPRU924:describes theApplication Reports—SPRAA58:—describes differences between theTexas assist in application migration fromthe281x to the280x.While the main focus of this document is migration from281x to280x,usersconsidering migrating in the reverse direction(280x to281x)will also find this document useful.SPRA550:describes a scenario of a3.3-V-only motor controllerissue of interfacing between3.3V and5V exists.On-chip3.3-V analog-to-digital converter(ADC)versus5-V ADC is also discussed.Guidelines for component layout and printed circuit board(PCB)design that can reduce systemnoise and EMI effects are summarized.SPRA820:presents the methodology foronline code is provided thatcontains functions for implementing the overflow detection on both DSP/BIOS™andnon-DSP/BIOS applications.SPRA861:provides an easy way to use thean arbitrary device.This application report presents a sample implementation of a user-defined device driver.SPRA873:signal processor(DSP)and DRV592power amplifier.The DSP implements a digitalproportional-integral-derivative feedback controller using an integrated12-bit analog-to-digitalconverter to read the thermistor,and direct output of pulse-width-modulated waveforms to theH-bridge DRV592power amplifier.A complete description of the experimental system,along withsoftware and software operating instructions,is provided.SPRU807A–November2004–Revised October2006Read This First7 Submit Documentation Feedback Related Documentation From Texas InstrumentsSPRA876:contains several programmingmodes of operation to help you come up to speed quickly in programming the eCAN.All projects and CANalyzer configuration filesare included in the attached SPRA876.zip file.SPRA953:describes the traditional and new thermal metrics and will puttheir to system level junction temperature estimation.SPRA958:coverson-chip flash memory.Requirements for both DSP/BIOS™and non-DSP/BIOS projects arepresented.Example code projects are included.SPRA963:describes reliability data forSPRA989:describes a method for improving the absolutefound on the F2810/F2811/F2812devices.This application note is accompanied by an example program(ADCcalibration.zip)that executesfrom RAM on the F2812eZdsp.SPRA991:them to evaluate system alternatives more effectively.TrademarksTMS320C28x,C28x are trademarks of Texas Instruments.8Read This First SPRU807A–November2004–Revised October2006Submit Documentation Feedback1Introduction2DescriptionReference GuideSPRU807A–November 2004–Revised October 2006The enhanced Capture (eCAP)module is essential in systems where accurate timingof external events is important.This reference guide is applicable for the eCAP found on the TMS320x28xx andTMS320x28xxx family of processors.This includes all Flash-based,ROM-based,andRAM-based devices within the 280xx and 28xxx family.Uses for eCAP include:•Speed measurements of rotating machinery (e.g.,toothed sprockets sensed via Hall sensors)•Elapsed time measurements between position sensor pulses•Period and duty cycle measurements of pulse train signals•Decoding current or voltage amplitude derived from duty cycle encoded current/voltage sensors The eCAP module described in this guide includes the following features:•32-bit time base with 10-nS time resolution with a 100-MHz system clock•4-event time-stamp registers (each 32bits)•Edge polarity selection for up to four sequenced time-stamp capture events•Interrupt on either of the four events•Single shot capture of up to four event time-stamps•Continuous mode capture of time-stamps in a four-deep circular buffer•Absolute time-stamp capture•Difference (Delta)mode time-stamp capture•All above resources dedicated to a single input pin•When not used in capture mode,the ECAP module can be configured as a single channel PWM output The eCAP module represents one complete capture channel that can be instantiated multiple times depending on the target device.In the context of this guide,one eCAP channel has the followingindependent key resources:•Dedicated input capture pin•32-bit time base (counter)•4x 32-bit time-stamp capture registers (CAP1-CAP4)•4-stage sequencer (Modulo4counter)that is synchronized to external events,ECAP pin rising/falling edges.•Independent edge polarity (rising/falling edge)selection for all 4events•Input capture signal prescaling (from 2-62)•One-shot compare register (2bits)to freeze captures after 1to 4time-stamp events•Control for continuous time-stamp captures using a 4-deep circular buffer (CAP1-CAP4)scheme •Interrupt capabilities on any of the 4capture eventsSPRU807A–November 2004–Revised October 2006Enhanced Capture (eCAP)Module 9Submit Documentation Feedback Capture and APWM Operating ModeMultiple identical eCAP modules can be contained in a280x system as shown in Figure1.The number of modules is device-dependent and is based on target application needs.Figure1.Multiple eCAP Modules In A28x System3Capture and APWM Operating ModeYou can use the eCAP module resources to implement a single-channel PWM generator(with32bitcapabilities)when it is not being used for input captures.The counter operates in count-up mode,providing a time-base for asymmetrical pulse width modulation(PWM)waveforms.The CAP1and CAP2 registers become the active period and compare registers,respectively,while CAP3and CAP4registers become the period and capture shadow registers,respectively.Figure2is a high-level view of both the capture and auxiliary pulse-width modulator(APWM)modes of10Enhanced Capture(eCAP)Module SPRU807A–November2004–Revised October2006Submit Documentation FeedbackCapture and APWM Operating Mode Figure2.Capture and APWM Modes of OperationA A single pin is shared between CAP and APWM functions.In capture mode,it is an input;in APWM mode,it is anoutput.B In APWM mode,writing any value to CAP1/CAP2active registers also writes the same value to the correspondingshadow registers CAP3/CAP4.This emulates immediate mode.Writing to the shadow registers CAP3/CAP4invokesthe shadow mode.4Capture Mode Description4.1Event PrescalerCapture Mode DescriptionFigure 3shows the various components that implement the capture function.Figure 3.Capture Function Diagram•An input capture signal (pulse train)can be prescaled by N =2-62(in multiples of 2)or can bypass the prescaler.This is useful when very high frequency signals are used as inputs.Figure 4shows a functional diagram and Figure 5shows the operation of the prescale function.12Enhanced Capture (eCAP)ModuleSPRU807A–November 2004–Revised October 2006ECAPx pin (from GPIO)PSoutECAPxPSout div 2PSout div 4PSout div 6PSout div 8PSout div 104.2Edge Polarity Select and Qualifier4.3Continuous/One-Shot ControlCapture Mode DescriptionFigure 4.Event Prescale ControlAWhen a prescale value of 1is chosen (i.e.ECCTL1[13:9]=0,0,0,0,0)the input capture signal by-passes the prescale logic completely.Figure 5.Prescale Function Waveforms•Four independent edge polarity (rising edge/falling edge)selection MUXes are used,one for each capture event.•Each edge (up to 4)is event qualified by the Modulo4sequencer.•The edge event is gated to its respective CAPx register by the Mod4counter.The CAPx register is loaded on the falling edge.•The Mod4(2bit)counter is incremented via edge qualified events (CEVT1-CEVT4).•The Mod4counter continues counting (0->1->2->3->0)and wraps around unless stopped.•A 2-bit stop register is used to compare the Mod4counter output,and when equal stops the Mod4counter and inhibits further loads of the CAP1-CAP4registers.This occurs during one-shot operation.CEVT1CEVT2CEVT3CEVT4ECCTL2[CONT/ONESHT]4.432-Bit Counter and Phase ControlCapture Mode DescriptionThe continuous/one-shot block controls the start/stop and reset (zero)functions of the Mod4counter via a mono-shot type of action that can be triggered by the stop-value comparator and re-armed via software control.Once armed,the eCAP module waits for 1-4(defined by stop-value)capture events before freezing both the Mod4counter and contents of CAP1-4registers (i.e.,time-stamps).Re-arming prepares the eCAP module for another capture sequence.Also re-arming clears (to zero)the Mod4counter and permits loading of CAP1-4registers again,providing the CAPLDEN bit is set.In continuous mode,the Mod4counter continues to run (0->1->2->3->0,the one-shot action is ignored,and capture values continue to be written to CAP1-4in a circular buffer sequence.Figure 6.Details of the Continuous/One-shot BlockThis counter provides the time-base for event captures,and is clocked via the system clock.A phase register is provided to achieve synchronization with other counters,via a hardware and software forced sync.This is useful in APWM mode when a phase offset between modules is needed.On any of the four event loads,an option to reset the 32-bit counter is given.This is useful for time difference capture.The 32-bit counter value is captured first,then it is reset to 0by any of the LD1-LD4signals.14Enhanced Capture (eCAP)ModuleSPRU807A–November 2004–Revised October 2006SYNCOSYNCECCTL2[SYNCI_EN]Delta−modeCTR−OVFCTR[31−0]4.5CAP1-CAP4Registers4.6Interrupt ControlCapture Mode DescriptionFigure 7.Details of the Counter and Synchronization BlockThese 32-bit registers are fed by the 32-bit counter timer bus,CTR[0-31]and are loaded (i.e.,capture a time-stamp)when their respective LD inputs are strobed.Loading of the capture registers can be inhibited via control bit CAPLDEN.During one-shot operation,this bit is cleared (loading is inhibited)automatically when a stop condition occurs,i.e.StopValue =Mod4.CAP1and CAP2registers become the active period and compare registers,respectively,in APWM mode.CAP3and CAP4registers become the respective shadow registers (APRD and ACMP)for CAP1and CAP2during APWM operation.An Interrupt can be generated on capture events (CEVT1-CEVT4,CTROVF)or APWM events (CTR =PRD,CTR =CMP).A counter overflow event (FFFFFFFF->00000000)is also provided as an interrupt source (CTROVF).The capture events are edge and sequencer qualified (i.e.,ordered in time)by the polarity select and Mod4gating,respectively.One of these events can be selected as the interrupt source (from the eCAPx module)going to the PIE.Seven interrupt events (CEVT1,CEVT2,CEVT3,CEVT4,CNTOVF,CTR=PRD,CTR=CMP)can be generated.The interrupt enable register (ECEINT)is used to enable/disable individual interrupt eventsources.The interrupt flag register (ECFLG)indicates if any interrupt event has been latched and contains the global interrupt flag bit (INT).An interrupt pulse is generated to the PIE only if any of the interrupt events are enabled,the flag bit is 1,and the INT flag bit is 0.The interrupt service routine must clear the global interrupt flag bit and the serviced event via the interrupt clear register (ECCLR)before any other interrupt pulses are generated.You can force an interrupt event via the interrupt force register (ECFRC).This is useful for test purposes.4.7Shadow Load and Lockout ControlCapture Mode DescriptionNote:The CEVT1,CEVT2,CEVT3,CEVT4flags are only active in capture mode (ECCTL2[CAP/APWM ==0]).The CTR=PRD,CTR=CMP flags are only valid in APWM mode (ECCTL2[CAP/APWM ==1]).CNTOVF flag is valid in both modes.Figure 8.Interrupts in eCAP ModuleIn capture mode,this logic inhibits (locks out)any shadow loading of CAP1or CAP2from APRD and ACMP registers,respectively.In APWM mode,shadow loading is active and two choices are permitted:•Immediate -APRD or ACMP are transferred to CAP1or CAP2immediately upon writing a new value.•On period equal,i.e.,CTR[31:0]=PRD[31:0]Enhanced Capture (eCAP)Module16SPRU807A–November 2004–Revised October 20064.8APWM Mode OperationAPRDACMPtimeCapture Mode DescriptionMain operating highlights of the APWM section:•The time-stamp counter bus is made available for comparison via 2digital (32-bit)comparators.•When CAP1/2registers are not used in capture mode,their contents can be used as Period and Compare values in APWM mode.•Double buffering is achieved via shadow registers APRD and ACMP (CAP3/4).The shadow register contents are transferred over to CAP1/2registers either immediately upon a write,or on a CTR =PRD trigger.•In APWM mode,writing to CAP1/CAP2active registers will also write the same value to thecorresponding shadow registers CAP3/CAP4.This emulates immediate mode.Writing to the shadow registers CAP3/CAP4will invoke the shadow mode.•During initialization,you must write to the active registers for both period and compare.Thisautomatically copies the initial values into the shadow values.For subsequent compare updates,i.e.,during run-time,you only need to use the shadow registers.Figure 9.PWM Waveform Details Of APWM Mode OperationThe behavior of APWM active high mode (APWMPOL ==0)is as follows:CMP =0x00000000,output low for duration of period (0%duty)CMP =0x00000001,output high 1cycle CMP =0x00000002,output high 2cycles CMP =PERIOD,output high except for 1cycle (<100%duty)CMP =PERIOD+1,output high for complete period (100%duty)CMP >PERIOD+1,output high for complete periodThe behavior of APWM active low mode (APWMPOL ==1)is as follows:CMP =0x00000000,output high for duration of period (0%duty)CMP =0x00000001,output low 1cycle CMP =0x00000002,output low 2cycles CMP =PERIOD,output low except for 1cycle (<100%duty)CMP =PERIOD+1,output low for complete period (100%duty)CMP >PERIOD+1,output low for complete period Capture Module-Control and Status Registers5Capture Module-Control and Status RegistersFigure10.Time-Stamp Counter Register(TSCTR)R/W-0LEGEND:R/W=Read/Write;R=Read only;-n=value after resetTable1.Time-Stamp Counter Register(TSCTR)Field Descriptions Bit(s)Field Description31:0TSCTR Active32-bit counter register that is used as the capture time-baseFigure11.Counter Phase Control Register(CTRPHS)R/W-0LEGEND:R/W=Read/Write;R=Read only;-n=value after resetTable2.Counter Phase Control Register(CTRPHS)Field Descriptions Bit(s)Field Description31:0CTRPHS Counter phase value register that can be programmed for phase lag/lead.This register shadowsTSCTR and is loaded into TSCTR upon either a SYNCI event or S/W force via a control edto achieve phase control synchronization with respect to other eCAP and EPWM time-bases.Figure12.Capture-1Register(CAP1)R/W-0LEGEND:R/W=Read/Write;R=Read only;-n=value after resetTable3.Capture-1Register(CAP1)Field DescriptionsBit(s)Field Description31:0CAP1This register can be loaded(written)by:)Time-Stamp(i.e.,counter value TSCTR)during a captureevent)Software-may be useful for test purposes/initialization)APRD shadow register(i.e.,CAP3)when used in APWM modeFigure13.Capture-2Register(CAP2)R/W-0LEGEND:R/W=Read/Write;R=Read only;-n=value after reset18Enhanced Capture(eCAP)Module SPRU807A–November2004–Revised October2006Capture Module-Control and Status RegistersTable4.Capture-2Register(CAP2)Field DescriptionsBit(s)Field Description31:0CAP2This register can be loaded(written)by:•Time-Stamp(i.e.,counter value)during a capture event•Software-may be useful for test purposes•APRD shadow register(i.e.,CAP4)when used in APWM modeNote:In APWM mode,writing to CAP1/CAP2active registers also writes the same value to thecorresponding shadow registers CAP3/CAP4.This emulates immediate mode.Writing tothe shadow registers CAP3/CAP4invokes the shadow mode.Figure14.Capture-3Register(CAP3)R/W-0LEGEND:R/W=Read/Write;R=Read only;-n=value after resetTable5.Capture-3Register(CAP3)Field DescriptionsBit(s)Field Description31:0CAP3In CMP mode,this is a time-stamp capture register.In APWM mode,this is the period shadow(APER)register.You update the PWM period value through this register.In this mode,CAP3(APRD)shadows CAP1.Figure15.Capture-4Register(CAP4)R/W-0LEGEND:R/W=Read/Write;R=Read only;-n=value after resetTable6.Capture-4Register(CAP4)Field DescriptionsBit(s)Field Description31:0CAP4In CMP mode,this is a time-stamp capture register.In APWM mode,this is the compare shadow(ACMP)register.You update the PWM compare value via this register.In this mode,CAP4(ACMP)shadows CAP2.Figure16.ECAP Control Register1(ECCTL1)R/W-0R/W-0R/W-0R/W-0R/W-0R/W-0R/W-0R/W-0R/W-0R/W-0R/W-0 LEGEND:R/W=Read/Write;R=Read only;-n=value after resetTable7.ECAP Control Register1(ECCTL1)Field Descriptions Bit(s)Field Value Description15:14FREE/SOFT Emulation Control00TSCTR counter stops immediately on emulation suspend Capture Module-Control and Status RegistersTable7.ECAP Control Register1(ECCTL1)Field Descriptions(continued) Bit(s)Field Value Description01TSCTR counter runs until=01x TSCTR counter is unaffected by emulation suspend(Run Free)13:9PRESCALE Event Filter prescale select00000Divide by1(i.e,.no prescale,by-pass the prescaler)00001Divide by200010Divide by400011Divide by600100Divide by800101Divide by10...11110Divide by6011111Divide by628CAPLDEN Enable Loading of CAP1-4registers on a capture event0Disable CAP1-4register loads at capture event time.1Enable CAP1-4register loads at capture event time.7CTRRST4Counter Reset on Capture Event40Do not reset counter on Capture Event4(absolute time stamp operation)1Reset counter after Capture Event4time-stamp has been captured(used in difference mode operation)6CAP4POL Capture Event4Polarity select0Capture Event4triggered on a rising edge(RE)1Capture Event4triggered on a falling edge(FE)5CTRRST3Counter Reset on Capture Event30Do not reset counter on Capture Event3(absolute time stamp)1Reset counter after Event3time-stamp has been captured(used in difference mode operation)4CAP3POL Capture Event3Polarity select0Capture Event3triggered on a rising edge(RE)1Capture Event3triggered on a falling edge(FE)3CTRRST2Counter Reset on Capture Event20Do not reset counter on Capture Event2(absolute time stamp)1Reset counter after Event2time-stamp has been captured(used in difference mode operation)2CAP2POL Capture Event2Polarity select0Capture Event2triggered on a rising edge(RE)1Capture Event2triggered on a falling edge(FE)1CTRRST1Counter Reset on Capture Event10Do not reset counter on Capture Event1(absolute time stamp)1Reset counter after Event1time-stamp has been captured(used in difference modeoperation)0CAP1POL Capture Event1Polarity select0Capture Event1triggered on a rising edge(RE)1Capture Event1triggered on a falling edge(FE)20SPRU807A–November2004–Revised October2006 Enhanced Capture(eCAP)ModuleCapture Module-Control and Status RegistersFigure17.ECAP Control Register2(ECCTL2)R-0R/W-0R/W-0R/W-0R/W-0R/W-0R/W-0R/W-0R/W-1R/W-1R/W-0 LEGEND:R/W=Read/Write;R=Read only;-n=value after resetTable8.ECAP Control Register2(ECCTL2)Field DescriptionsBit(s)Field Description15:11Reserved Reserved10APWMPOL APWM output polarity select.This is applicable only in APWM operating mode0Output is active high(i.e.,Compare value defines high time)1Output is active low(i.e.,Compare value defines low time)9CAP/APWM CAP/APWM operating mode select0ECAP module operates in capture mode.This mode forces the followingconfiguration:•Inhibits TSCTR resets via CTR=PRD event•Inhibits shadow loads on CAP1and2registers•Permits user to enable CAP1-4register load•CAPx/APWMx pin operates as a capture input1ECAP module operates in APWM mode.This mode forces the followingconfiguration:•Resets TSCTR on CTR=PRD event(period boundary•Permits shadow loading on CAP1and2registers•Disables loading of time-stamps into CAP1-4registers•CAPx/APWMx pin operates as a APWM output8SWSYNC Software-forced Counter(TSCTR)Synchronizing.This provides a convenientsoftware method to synchronize some or all ECAP time bases.In APWM mode,the synchronizing can also be done via the CTR=PRD event.0Writing a zero has no effect.Reading always returns a zero1Writing a one forces a TSCTR shadow load of current ECAP module and anyECAP modules down-stream providing the SYNCO_SEL bits are0,0.After writinga1,this bit returns to a zero.Note:Selection CTR=PRD is meaningful only in APWM mode;however,you canchoose it in CAP mode if you find doing so useful.7:6SYNCO_SEL Sync-Out Select00Select sync-in event to be the sync-out signal(pass through)01Select CTR=PRD event to be the sync-out signal10Disable sync out signal11Disable sync out signal5SYNCI_EN Counter(TSCTR)Sync-In select mode0Disable sync-in option1Enable counter(TSCTR)to be loaded from TSCTR register upon either a SYNCIsignal or a S/W force event.4TSCTRSTOP Time Stamp(TSCTR)Counter Stop(freeze)Control0TSCTR stopped1TSCTR free-running3RE-ARM One-Shot Re-Arming Control,i.e.wait for stop trigger.Note:The re-arm function isvalid in one shot or continuous mode.0Has no effect(reading always returns a0)SPRU807A–November2004–Revised October2006Enhanced Capture(eCAP)Module21 Submit Documentation Feedback。
Wheelock HS-24系列产品说明手册说明书

273 Branchport AvenueLong Branch, NJ 07740 Thank you for using our products.(800) 631-2148 INSTALLATION INSTRUCTIONSHS-24 APPLIANCEUse this product according to this instruction manual. Please keep this instruction manual for future reference.GENERAL:The HS-24 Appliance can be field set to provide either Continuous Horn or Code 3 Horn. It can provide a continuous horn tone when connected directly to the Fire Alarm Control Panel (FACP), or synchronized Code 3 Horn when used in conjunction with the Sync Module (SM), Dual Sync Module (DSM) or Wheelock’s Power Supplies. Audible Horn Appliance can be field set to provide either High (HI) dBA, Medium (MED) dBA or Low (LO) dBA sound output and can be used on coded systems in which the applied voltage is cycled on and off. The HS-24 Appliance is UL Listed under Standard 464 for Audible Signal Appliances and also ULC Listed under Standard CAN/ULC-S525-99 for Audible Signaling Appliances for Fire Alarm Systems. It is listed for indoor use only and can be mounted to double-gang, 4” backbox, 100mm European backbox or SHBB surface backbox (See Mounting Options).The HS-24 is designed for use with either filtered DC or unfiltered Full-Wave-Rectified (FWR) input voltage. All inputs are polarized for compatibility with standard reverse polarity supervision of circuit wiring by a Fire Alarm Control Panel (FACP).NOTE: All CAUTIONS and WARNINGSFAILURE TO COMPLY WITH ANY OF THE FOLLOWING INSTRUCTIONS, CAUTIONS AND WARNINGS COULD RESULT IN IMPROPER APPLICATION, CANDELA SETTING, INSTALLATION AND/OR OPERATION OF THESE PRODUCTS IN AN EMERGENCY SITUATION, WHICH COULD RESULT IN PROPERTY DAMAGE AND SERIOUS INJURY OR DEATH TO YOU AND/OR OTHERS.SPECIFICATIONS:Table 1: UL Listed Models and RatingsMaximum RMS Current (AMPS) Model Regulated Voltage (VDC/VRMS)Voltage Range Limit Per UL 464 Lo Med Hi DC 16-33VDC 0.027 0.068 0.110 HS-24 24 FWR 16-33VRMS 0.041 0.050 0.094Table 1A: ULC Current Ratings (AMPS) Lo Med Hi ModelULC Voltage MEAN RMS MEAN RMS MEAN RMS 20.0VDC 0.014 0.018 0.020 0.033 0.035 0.067 24.0VDC 0.017 0.024 0.026 0.052 0.055 0.098 31.0VDC 0.021 0.027 0.035 0.068 0.069 0.11020.0VRMS ------ 0.016 ------ 0.028 ------ 0.05224.0VRMS ------ 0.031 ------ 0.043 ------ 0.075HS-24 31.0VRMS ------ 0.041 ------ 0.050 ------ 0.094Copyright 2005 Wheelock, Inc. All rights reserved.Table 2: dBA Sound Output for 24VDC ModelsDescription Volume Reverberant Per UL 464Anechoic dBA @ 10 Feet16.0VD C 24VDC 33.0VD C 20.0VD C 24VDC 31.0VDCLow 80 83 86 86 90 92 Medium 85 88 91 91 9598 Continuous Horn High 88 91 93 95 99101Low 75 79 82 86 9092Code 3 Horn Medium 80 84 86 91 95 98High 84 87 89 95 99 101BATTERY AND SUBTRACT THE VOLTAGE DROP FROM THE CIRCUIT WIRING RESISTANCE TO DETERMINE THE APPPLIED VOLTAGE TO THE APPLIANCES.Figure 1: ULC Directional Characteristics81dB 95dB85dB-3dB -3dB-6dB 95dB-6dBNOTES:1. The HS-24 is UL Listed for indoor use with a temperature range of +32°F to +120°F (0°C to +49°C) and maximumhumidity of 93% ± 2% RH.LIMITS OF 16-33 VOLTS USING FILTERED (DC) OR UNFILTERED FULL-WAVE-RECTIFIED (FWR). DO NOT APPLY 80% AND 110% OF THESE VOLTAGE VALUES FOR SYSTEM OPERATION.LIMITS OF 20-31 VOLTS USING FILTERED (DC) OR UNFILTERED FULL-WAVE-RECTIFIED (FWR). APPLY 80% AND 110% OF THESE VOLTAGE VALUES FOR SYSTEM OPERATION.REQUIRED BY ALL APPLIANCES THAT ARE CONNECTED TO THE SYSTEM’S PRIMARY AND SECONDARY POWER SOURCES, SIGNALING CIRCUITS, SM, DSM SYNC MODULES AND WHEELOCK’S POWER SUPPLIES DO NOT EXCEED THE POWER SOURCES’ RATED CAPACITY OR THE CURRENT RATINGS OF ANY FUSES ON THE CIRCUITS TO WHICH THIS APPLIANCE IS WIRED. OVERLOADING POWER SOURCES OR EXCEEDING FUSE RATINGS COULD RESULT IN LOSS OF POWER AND FAILURE TO ALERT OCCUPANTS DURING AN EMERGENCY, WHICH COULD RESULT IN PROPERTY DAMAGE AND SERIOUS INJURY OR DEATH TO YOU AND/OR OTHERS.When calculating the total currents: Use Table 1/1A to determine the highest value of “RMS Current” or “Average Current” for an individual horn (across the expected operating voltage range of the horn), then multiply these values by the total number of horns; be sure to add the currents for any other appliances, including audible signaling appliances, powered by the same source and include any required safety factors.If the peak current exceeds the power supplies’ peak capacity, the output voltage provided by the power supplies may drop below the listed voltage range of the appliances connected to the supply and the voltage may not recover in some types of power supplies. For example, an auxiliary power supply that lacks filtering at its output stage (either via lack of capacitance and/or lack of battery backup across the output) may exhibit this characteristic.OUTPUT LEVEL BEFORE IT IS INSTALLED. THIS IS DONE BY PROPERLY INSERTING JUMPER PLUGS IN ACCORDANCE WITH THESE INSTRUCTIONS. INCORRECT SETTINGS WILL RESULT IN IMPROPER PERFORMANCE, WHICH COULD RESULT IN PROPERTY DAMAGE AND SERIOUS INJURY OR DEATH TO YOU AND/OR OTHERS.SOUND OUTPUT (SPL) SETTINGS:NOTE: The Code 3 Horn incorporates the temporal pattern (1/2 second on, 1/2 second off, 1/2 second on, 1/2 second off, 1/2 second on, 1-1/2 off and repeat) specified by ANSI/NFPA for standard emergency evacuation signaling. The Code 3 Horn should be used only for fire evacuation signaling and not for any other purpose.Figure 2: Showing Location of Jumper PlugsFactory setting is on Medium dB and Code 3.Figure 3: Jumper Plug Settings for High, Medium, Low dB, Code 3 Horn and Continuous Horn Setting. HIGH LOW H 33SETTING HORN SETTING HORN J2J2J2M L MEDIUM SETTING HORN CODE 3SETTING HORN CONTINUOUS SETTING* HORN(Use needle nose pliers to pull and properly insert the jumper plug.)No jumper plug is needed for continuous horn setting. However, it is recommended that the jumper plug be retained in the unit for future use (if needed) as shown in Figure 3.NOTE: The HS-24 must be set for Code 3 horn when used with the sync module. Refer to Sync Module Installation Instruction sheets SM (P83123), DSM (P83177) and Wheelock’s Power Supplies for additional information. If the HS-24 is connected to a coded system the continuous horn setting must be usedFigure 3:1.HS-24 Appliance has in-out wiring terminals that accept two #12 to #18 American Wire Gauge(AWG) wires at each screw terminal. Strip leads 3/8” inches for connection to screw terminals.2.Break all in-out wire runs on supervised circuits or circuits in which supervision is used as shownin Figure 3. The polarity shown in the wiring diagrams is for the operation of the appliances. Thepolarity is reversed by the FACP during supervision.MOUNTING OPTIONS:The following figures show the maximum number of field wires (conductors) that can enter the backbox used with each mounting option. If these limits are exceeded, there may be insufficient space in the backbox to accommodate the field wires and stresses from the wires could damage the product.Although the limits shown for each mounting option comply with the National Electrical Code (NEC), Wheelock recommends use of the largest backbox option shown and the use of approved stranded field wires, whenever possible, to provide additional wiring room for easy installation and minimum stress on the product from wiring.MOUNTING PROCEDURES:Use this mounting procedure to position the field wires in the backbox so that they use minimum space and produce minimum stress on the product. This is especially important for stiff, heavy gauge wires and wires with thick insulation or sheathing.1.Connect field wires to the HS-24 terminal block (polarity must be observed).2.Bend the field wires up 90° at the connection to the terminal block.3.Carefully push the field wires into the backbox by hand.4.Carefully press the HS-24 to the backbox, verifying that the HS-24 is seated and aligned correctly.5.Screw the HS-24 to the backbox using the screws supplied. Refer to Mounting Options for screw size.MOUNTING NOTES:Check that the installed product will have sufficient clearance and wiring room prior to installing backboxes and conduit, especially if sheathed multiconductor cable or 3/4" conduit fittings are used.1. Conduit entrances to the backbox should be selected to provide sufficient wiring clearance for the installed product.2.When terminating field wires, do not use more lead length than required. Excess lead length could result in insufficientwiring space for the signaling appliance.3.Do not pass additional wires (used for other than the signaling appliance) through the backbox. Such additional wires couldresult in insufficient wiring space for the signaling appliance.If these appliances are operated within 15 inches of a person's ear, they can produce a sound pressure level that exceeds the maximum 120dBA permitted by ADA and OSHA rules. Exposure to such sound levels can result in damage to a person's hearing.This appliance can produce a distinctive three pulse Temporal Pattern Fire Alarm Evacuation Signal (for total evacuation) inCheck the installation instructions of the manufacturers of other equipment used in the system for any guidelines or restrictions on wiring and/or locating Notification Appliance Circuits (NAC) and notification appliances. Some system communication circuits and/or audio circuits, for example, may require special precautions to assure electrical noise immunity (e.g. audio crosstalk).NOTE: This equipment has been tested and found to comply with the limits for a Class B digital appliance, pursuant to Part 15 of the FCC Rules. These limits are designed to provide reasonable protection against harmful interference in residential installation. This equipment generates, uses and can radiate radio frequency energy and, if not installed and used in accordance with the instructions, may cause harmful interference to radio communications. However, there is no guarantee that interference will not occur in a particular installation. If this equipment does cause harmful interference to radio or television reception, which can be determined by turning the equipment off and on, the user is encouraged to try to correct the interference by one or more of the following measures: 1) Reorient or relocate the receiving antenna, 2) Increase the separation between the equipment and receiver, 3) Connect the equipment into an outlet on a circuit different from that to which the receiver is connected, and 4) Consult the dealer or an experienced radio/TV technician for help.The HS-24 and these instructions are copyrighted by Wheelock and the HS-24 contain proprietary, confidential and trade secrets of Wheelock. No part of the HS-24 product and these instructions may be photocopied, printed or reproduced in any form or modified, adapted, changed or enhanced, or converted to another programming language, or used to create updated, related or derivative works, without the prior written consent of Wheelock. No part of the HS Series products shall be decomposed, disassembled or reverse engineered.ANY MATERIAL EXTRAPOLATED FROM THIS DOCUMENT OR FROM WHEELOCK MANUALS OR OTHER DOCUMENTS DESCRIBING THE PRODUCT FOR USE IN PROMOTIONAL OR ADVERTISING CLAIMS, OR FOR ANY OTHER USE, INCLUDING DESCRIPTION OF THE PRODUCT'S APPLICATION, OPERATION, INSTALLATION AND TESTING IS USED AT THE SOLE RISK OF THE USER AND WHEELOCK WILL NOT HAVE ANY LIABILITY FOR SUCH USE.IMPORTANT: READ SEPARATE "GENERAL INFORMATION" SHEET FOR INFORMATION ON THE PLACEMENT, LIMITATIONS, INSTALLATION, FINAL CHECKOUT, AND PERIODIC TESTING OF NOTIFICATION APPLIANCES.Limited WarrantyWheelock products must be used within their published specifications and must be PROPERLY specified, applied, installed, operated, maintained and operationally tested in accordance with these instructions at the time of installation and at least twice a year or more often and in accordance with local, state and federal codes, regulations and laws. Specification, application, installation, operation, maintenance and testing must be performed by qualified personnel for proper operation in accordance with all of the latest National Fire Protection Association (NFPA), Underwriters' Laboratories (UL), Underwriters’ Laboratories of Canada (ULC), National Electrical Code (NEC), Occupational Safety and Health Administration (OSHA), local, state, county, province, district, federal and other applicable building and fire standards, guidelines, regulations, laws and codes including, but not limited to, all appendices and amendments and the requirements of the local authority having jurisdiction (AHJ). Wheelock products when properly specified, applied, installed, operated, maintained and operationally tested as provided above are warranted against mechanical and electrical defects for a period of three years from date of manufacture (as determined by date code). Correction of defects by repair or replacement shall be at Wheelock's sole discretion and shall constitute fulfillment of all obligations under this warranty. THE FOREGOING LIMITED WARRANTY SHALL IMMEDIATELY TERMINATE IN THE EVENT ANY PART NOT FURNISHED BY WHEELOCK IS INSTALLED IN THE PRODUCT. THE FOREGOING LIMITED WARRANTY SPECIFICALLY EXCLUDES ANY SOFTWARE REQUIRED FOR THE OPERATION OF OR INCLUDED IN A PRODUCT. WHEELOCK MAKES NO REPRESENTATION OR WARRANTY OF ANY OTHER KIND, EXPRESS, IMPLIED OR STATUTORY WHETHER AS TO MERCHANTABILITY, FITNESS FOR A PARTICULAR PURPOSE OR ANY OTHER MATTER.USERS ARE SOLELY RESPONSIBLE FOR DETERMINING WHETHER A PRODUCT IS SUITABLE FOR THE USER'S PURPOSES, OR WHETHER IT WILL ACHIEVE THE USER'S INTENDED RESULTS. THERE IS NO WARRANTY AGAINST DAMAGE RESULTING FROM MISAPPLICATION, IMPROPER SPECIFICATION, ABUSE, ACCIDENT OR OTHER OPERATING CONDITIONS BEYOND WHEELOCK'S CONTROL.SOME WHEELOCK PRODUCTS CONTAIN SOFTWARE. WITH RESPECT TO THOSE PRODUCTS, WHEELOCK DOES NOT WARRANTY THAT THE OPERATION OF THE SOFTWARE WILL BE UNINTERRUPTED OR ERROR-FREE OR THAT THE SOFTWARE WILL MEET ANY OTHER STANDARD OF PERFORMANCE, OR THAT THE FUNCTIONS OR PERFORMANCE OF THE SOFTWARE WILL MEET THE USER'S REQUIREMENTS. WHEELOCK SHALL NOT BE LIABLE FOR ANY DELAYS, BREAKDOWNS, INTERRUPTIONS, LOSS, DESTRUCTION, ALTERATION, OR OTHER PROBLEMS IN THE USE OF A PRODUCT ARISING OUT OF OR CAUSED BY THE SOFTWARE.THE LIABILITY OF WHEELOCK ARISING OUT OF THE SUPPLYING OF A PRODUCT, OR ITS USE, WHETHER ON WARRANTIES, NEGLIGENCE, OR OTHERWISE, SHALL NOT IN ANY CASE EXCEED THE COST OF CORRECTING DEFECTS AS STATED IN THE LIMITED WARRANTY AND UPON EXPIRATION OF THE WARRANTY PERIOD ALL SUCH LIABILITY SHALL TERMINATE. WHEELOCK IS NOT LIABLE FOR LABOR COSTS INCURRED IN REMOVAL, REINSTALLATION OR REPAIR OF THE PRODUCT BY ANYONE OTHER THAN WHEELOCK OR FOR DAMAGE OF ANY TYPE WHATSOEVER, INCLUDING BUT NOT LIMITED TO, LOSS OF PROFIT OR INCIDENTAL OR CONSEQUENTIAL DAMAGES. THE FOREGOING SHALL CONSTITUTE THE SOLE REMEDY OF THE PURCHASER AND THE EXCLUSIVE LIABILITY OF WHEELOCK.IN NO CASE WILL WHEELOCK'S LIABILITY EXCEED THE PURCHASE PRICE PAID FOR A PRODUCT.Limitation of LiabilityWHEELOCK'S LIABILITY ON ANY CLAIM OF ANY KIND, INCLUDING NEGLIGENCE AND BREACH OF WARRANTY, FOR ANY LOSS OR DAMAGE RESULTING FROM, ARISING OUT OF, OR CONNECTED WITH THIS CONTRACT, OR FROM THE MANUFACTURE, SALE, DELIVERY, RESALE, REPAIR OR USE OF ANY PRODUCT COVERED BY THIS ORDER SHALL BE LIMITED TO THE PRICE APPLICABLE TO THE PRODUCT OR PART THEREOF WHICH GIVES RISE TO THE CLAIM. WHEELOCK'S LIABILITY ON ANY CLAIM OF ANY KIND SHALL CEASE IMMEDIATELY UPON THE INSTALLATION IN THE PRODUCT OF ANY PART NOT FURNISHED BY WHEELOCK. IN NO EVENT SHALL WHEELOCK BE LIABLE FOR ANY CLAIM OF ANY KIND UNLESS IT IS PROVEN THAT OUR PRODUCT WAS A DIRECT CAUSE OF SUCH CLAIM. FURTHER, IN NO EVENT, INCLUDING IN THE CASE OF A CLAIM OF NEGLIGENCE, SHALL WHEELOCK BE LIABLE FOR INCIDENTAL OR CONSEQUENTIAL DAMAGES. SOME STATES DO NOT ALLOW THE EXCLUSION OR LIMITATION OF INCIDENTAL OR CONSEQUENTIAL DAMAGES, SO THE PRECEDING LIMITATION MAY NOT APPLY TO ALL PURCHASERS.5/05。
DS2431_cn

PIN-PACKAGE TO-92 TO-92, tape-andreel TSOC TSOC, tape-andreel
引脚配置
1
, Top View
TSOC, TO-92 pinout: Pin 1 ------------- GND Pin 2 ------------- IO All other pins -- NC
VPUP RPUP CIO
IL
VTL
(Notes 2) (Notes 2, 3) (Notes 4, 5) I/O pin at VPUP
(Notes 5, 6, 7)
Input Low Voltage Low-to-High Switching Threshold
VIL
(Notes 2, 8)
VTH
概述
DS2431 是一款 1024 位 1-Wire® EEPROM芯片,由 四个存储器页组成,每页 256 位。数据先被写入一个 8 字节暂存器中,经校验无误后复制到EEPROM存储 器。其特点在于,四个存储器页相互独立,可以单独
设置写保护或EPROM仿真模式,在EPROM仿真模式 下,所有位的状态只能从 1 变成 0。DS2431 通过一根 1-Wire总线进行通信。通信采用Dallas Semiconductor 标准的 1-Wire协议。每个器件都有唯一 的、不能更改 的 64 位ROM地址码,该地址码由工厂光刻写入芯 片。在一个多点的 1-Wire网络环境中,该地址码用于 对器件进行寻址。
Data Retention (Notes 24, 25, 26)
tDR
At +85°C (worst case)
(TA = -40°C to +85°C; see Note 1.)
CommScope 4-port 方向扬音器(LDXX-6515DS-VTM)产品说明书

Page of 134-port sector antenna, 4x 790–960 MHz, 65° HPBW, RET compatibleTwo DualPol® antennas under one radomeEach DualPol® array can be independently adjusted for greater flexibilityEngineered to provide wideband capability to support “Digital Dividend” band applications, future readyOBSOLETEThis product was discontinued on: March 31, 2023Replaced By:4P-4L-B24-port sector antenna, 4x 694–960 MHz, 65° HPBWGeneral SpecificationsAntenna Type Sector Band Single bandColorLight Gray (RAL 7035)Grounding Type RF connector inner conductor and body grounded to reflector and mounting bracket Performance Note Outdoor usage Radome Material Fiberglass, UV resistant Radiator Material Aluminum Reflector Material Aluminum RF Connector Interface 7-16 DIN Female RF Connector LocationBottom RF Connector Quantity, low band 4RF Connector Quantity, total4Remote Electrical Tilt (RET) InformationModel with Factory Installed AISG 2.0 ActuatorLDXX-6515DS-A2MDimensionsWidth 549 mm | 21.614 in Depth165 mm | 6.496 in 2070 mm | 81.496 inLength2070 mm | 81.496 inNet Weight, without mounting kit35.6 kg | 78.484 lbElectrical SpecificationsImpedance50 ohmOperating Frequency Band790 – 960 MHzPolarization±45°Electrical SpecificationsFrequency Band, MHz790–862824–894870–960 Gain, dBi16.316.417 Beamwidth, Horizontal, degrees68.165.963 Beamwidth, Vertical, degrees10.4109.6 Beam Tilt, degrees0–100–100–10 USLS (First Lobe), dB181817 Front-to-Back Ratio at 180°, dB322827 Front-to-Back Total Power at 180° ± 30°, dB262523CPR at Boresight, dB242323CPR at Sector, dB141310 Isolation, Cross Polarization, dB303030 VSWR | Return loss, dB 1.4 | 15.6 1.4 | 15.6 1.4 | 15.6 PIM, 3rd Order, 2 x 20 W, dBc-150-150-150 Input Power per Port, maximum, watts350350350 Electrical Specifications, BASTAFrequency Band, MHz790–862824–894870–960 Gain by all Beam Tilts, average, dBi15.71616.5 Gain by all Beam Tilts Tolerance, dB±0.3±0.5±0.4Gain by Beam Tilt, average, dBi0 ° | 15.75 ° | 15.810 ° | 15.50 ° | 16.05 ° | 16.110 ° | 15.90 ° | 16.45 ° | 16.610 ° | 16.4Beamwidth, Horizontal Tolerance, degrees±3.3±3.4±3.7Beamwidth, Vertical Tolerance, degrees±0.5±0.5USLS, beampeak to 20° above beampeak,dB191918CPR at Boresight, dB262525CPR at Sector, dB161512Page of23Mechanical SpecificationsWind Loading @ Velocity, frontal1,407.0 N @ 150 km/h (316.3 lbf @ 150 km/h) Wind Loading @ Velocity, lateral337.0 N @ 150 km/h (75.8 lbf @ 150 km/h) Wind Loading @ Velocity, rear1,558.0 N @ 150 km/h (350.3 lbf @ 150 km/h) Wind Speed, maximum241 km/h (150 mph)Packaging and WeightsWidth, packed693 mm | 27.283 inDepth, packed291 mm | 11.457 inLength, packed2294 mm | 90.315 inWeight, gross54.8 kg | 120.813 lbRegulatory Compliance/CertificationsAgency ClassificationCE Compliant with the relevant CE product directivesCHINA-ROHS Below maximum concentration valueISO 9001:2015Designed, manufactured and/or distributed under this quality management system REACH-SVHC Compliant as per SVHC revision on /ProductCompliance ROHS CompliantUK-ROHSCompliantIncluded ProductsBSAMNT-3–Wide Profile Antenna Downtilt Mounting Kit for 2.4 - 4.5 in (60 - 115 mm) OD round members.Kit contains one scissor top bracket set and one bottom bracket set.BSAMNT-M–Middle Downtilt Mounting Kit for Long Antennas for 2.4 - 4.5 in (60 - 115 mm) OD roundmembers. Kit contains one scissor bracket set.* FootnotesPerformance Note Severe environmental conditions may degrade optimum performancePage of33。
防雷检测作业指导书(可打印)

作业指导书受控号:ZYZDS-2021版本号:第二版受控状态:■受控□非受控编写: XXX审核: XXX批准: XXXXXX颁布日期:XXXX年XX月XX日实施日期:XXXX年XX月XX日1为了规范本XX防雷装置检测技术服务,提高服务质量和服务水平,保证本XX检测工作顺利开展,特制定本作业指导书。
2根据《中华人民共和国气象法》、《防雷减灾管理办法》、《XX省气象灾害防御条例》等法律法规规章和《建筑物防雷设计规范》GB50057-2010、《建筑物电子信息系统防雷技术规范》GB50343-2012、《建筑物防雷装置检测技术规范》GB/T21431-2015等一系列国家防雷、防静电标准、规范的规定,制定本作业指导书。
3本作业指导书规定了防雷、防静电设施安全性能检测的采用标准、检测内容、检测方法和判定规则等。
适用于防雷设施安全性能的检测验收和法定定期检测,也可适用于委托检测。
4本作业指导书同时作为防雷设施安全性能检测的技术规程,全XX的检测人员必须严格按本作业指导书实施检测。
5国家有新的法律法规、技术规范颁布时,本作业指导书将及时修订。
6本作业指导书已经批准颁布,自XXXX年XX 月XX 日实施。
《建筑物防雷设计规范》GB50057-2010、《建筑物电子信息系统防雷技术规范》GB50343-2012、《建筑物防雷装置检测技术规范》GB/T 21431-2015、《电子信息系统机房设计规范》GB50174-2008、《石油与石油设施雷电安全规范》GB15599-2009、《民用爆破器材工程设计安全规范》GB50089-2007、《汽车加油加气站设计与施工规范》GB50156-2012(2016年修订版)、《石油化工企业设计防火规范》GB50160-2015、《电信专用房屋设计规范》YD 5003-2014、《有线电视系统工程技术规范》GB50200-94 等国家、行业现行标准、规范(详见附录二)中的防雷标准作为检测判别标准,并据此编制本《作业指导书》Z Y Z D S--X X X X,作为本XX开展防雷装置检测的方法规范,本文件为受控文件。
ThermoFisher DS-33 Matrix Standard Kit (Dye Set G5
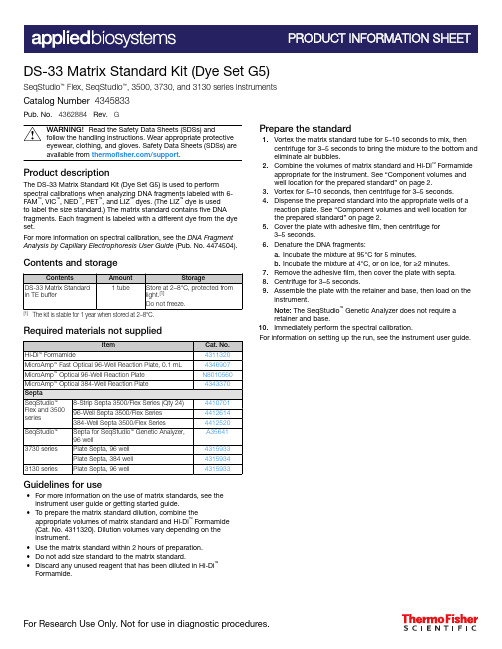
DS-33 Matrix Standard Kit (Dye Set G5) SeqStudio™ Flex, SeqStudio™, 3500, 3730, and 3130 series instruments Catalog Number 4345833Pub. No. 4362884 Rev.GWARNING! Read the Safety Data Sheets (SDSs) andfollow the handling instructions. Wear appropriate protectiveeyewear, clothing, and gloves. Safety Data Sheets (SDSs) areavailable from /support.Product descriptionThe DS-33 Matrix Standard Kit (Dye Set G5) is used to perform spectral calibrations when analyzing DNA fragments labeled with 6‐FAM™, VIC™, NED™, PET™, and LIZ™ dyes. (The LIZ™ dye is usedto label the size standard.) The matrix standard contains five DNA fragments. Each fragment is labeled with a different dye from the dye set.For more information on spectral calibration, see the DNA Fragment Analysis by Capillary Electrophoresis User Guide (Pub. No. 4474504). Contents and storage[1] The kit is stable for 1 year when stored at 2–8°C.Required materials not suppliedGuidelines for use•For more information on the use of matrix standards, see the instrument user guide or getting started guide.•To prepare the matrix standard dilution, combine the appropriate volumes of matrix standard and Hi‑Di™ Formamide (Cat. No. 4311320). Dilution volumes vary depending on theinstrument.•Use the matrix standard within 2 hours of preparation.•Do not add size standard to the matrix standard.•Discard any unused reagent that has been diluted in Hi‑Di™Formamide.Prepare the standard1.Vortex the matrix standard tube for 5–10 seconds to mix, thencentrifuge for 3–5 seconds to bring the mixture to the bottom and eliminate air bubbles.bine the volumes of matrix standard and Hi‑Di™ Formamideappropriate for the instrument. See “Component volumes andwell location for the prepared standard” on page 2.3.Vortex for 5–10 seconds, then centrifuge for 3–5 seconds.4.Dispense the prepared standard into the appropriate wells of areaction plate. See “Component volumes and well location forthe prepared standard” on page 2.5.Cover the plate with adhesive film, then centrifuge for3–5 seconds.6.Denature the DNA fragments:a.Incubate the mixture at 95°C for 5 minutes.b.Incubate the mixture at 4°C, or on ice, for ≥2 minutes.7.Remove the adhesive film, then cover the plate with septa.8.Centrifuge for 3–5 seconds.9.Assemble the plate with the retainer and base, then load on theinstrument.Note: The SeqStudio™ Genetic Analyzer does not require aretainer and base.10.Immediately perform the spectral calibration.For information on setting up the run, see the instrument user guide.For Research Use Only. Not for use in diagnostic procedures.Component volumes and well location for the prepared standardTable 1 SeqStudio ™ Flex Series Genetic AnalyzerTable 2 SeqStudio ™ Genetic AnalyzerTable 3 3500/3500xL Genetic AnalyzerTable 4 3730/3730xl DNA Analyzer[1]For 3730/3730xl Data Collection Software only when running the RCT configuration: Select dye set G5-RCT to perform fragment analysis in applications with a high dynamic range (large peaks with a signal intensity that is much higher than the signal intensity of small peaks).Table 5 3130/3130xl Genetic AnalyzerLimited product warrantyLife Technologies Corporation and/or its affiliate(s) warrant their products as set forth in the Life Technologies' General Terms and Conditions of Sale at /us/en/home/global/terms-and-conditions.html . If you have any questions, please contact Life Technologies at /support .2DS-33 Matrix Standard Kit (Dye Set G5) Product Information SheetThermo Fisher Scientific Baltics UAB | V.A. Graiciuno 8, LT-02241 | Vilnius, LithuaniaFor descriptions of symbols on product labels or product documents, go to /symbols-definition.The information in this guide is subject to change without notice.DISCLAIMER: TO THE EXTENT ALLOWED BY LAW, THERMO FISHER SCIENTIFIC INC. AND/OR ITS AFFILIATE(S) WILL NOT BE LIABLE FOR SPECIAL, INCIDENTAL, INDIRECT, PUNITIVE, MULTIPLE, OR CONSEQUENTIAL DAMAGES IN CONNECTION WITH OR ARISING FROM THIS DOCUMENT, INCLUDING YOUR USE OF IT.Revision history: Pub. No. 4362884Important Licensing Information: This product may be covered by one or more Limited Use Label Licenses. By use of this product, you accept the terms and conditions of all applicable Limited Use Label Licenses.©2022 Thermo Fisher Scientific Inc. All rights reserved. All trademarks are the property of Thermo Fisher Scientific and its subsidiaries unless otherwise specified./support | /askaquestion31 January 2022。
Schneider Electric XPSAF5130 产品数据手册说明书
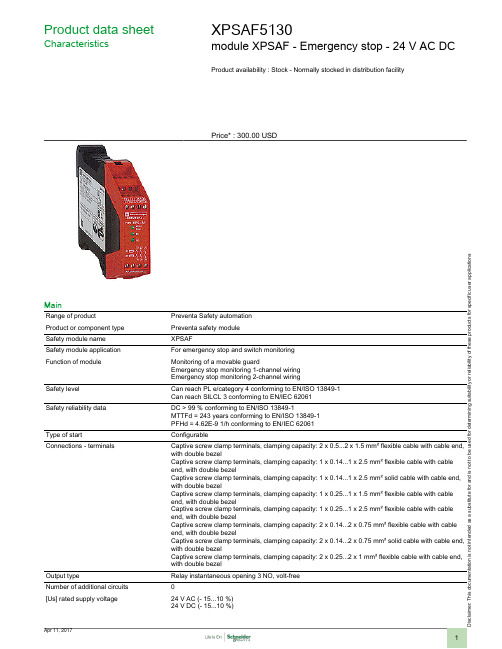
i s c l a i me r : T h i s d o c u m e n t a t i o n i s n o t i n t e n d e d a s a s u b s t i t u t ef o r a n d i s n o t t o b e u s e d f o r d e t e r m i n i ng s u i t a b i l i t y o r r e l i a b i l i t y o f th e s e p r o d u c t s f o r s p e ci f i c u s e r a p p l i c a t i o n sProduct data sheetCharacteristicsXPSAF5130module XPSAF - Emergency stop - 24 V AC DCProduct availability : Stock - Normally stocked in distribution facilityPrice* : 300.00 USDMainRange of productPreventa Safety automation Product or component type Preventa safety module Safety module name XPSAFSafety module application For emergency stop and switch monitoring Function of moduleMonitoring of a movable guardEmergency stop monitoring 1-channel wiring Emergency stop monitoring 2-channel wiringSafety levelCan reach PL e/category 4 conforming to EN/ISO 13849-1Can reach SILCL 3 conforming to EN/IEC 62061Safety reliability dataDC > 99 % conforming to EN/ISO 13849-1MTTFd = 243 years conforming to EN/ISO 13849-1PFHd = 4.62E-9 1/h conforming to EN/IEC 62061Type of startConfigurableConnections - terminalsCaptive screw clamp terminals, clamping capacity: 2 x 0.5...2 x 1.5 mm² flexible cable with cable end,with double bezelCaptive screw clamp terminals, clamping capacity: 1 x 0.14...1 x 2.5 mm² flexible cable with cable end, with double bezelCaptive screw clamp terminals, clamping capacity: 1 x 0.14...1 x 2.5 mm² solid cable with cable end,with double bezelCaptive screw clamp terminals, clamping capacity: 1 x 0.25...1 x 1.5 mm² flexible cable with cable end, with double bezelCaptive screw clamp terminals, clamping capacity: 1 x 0.25...1 x 2.5 mm² flexible cable with cable end, with double bezelCaptive screw clamp terminals, clamping capacity: 2 x 0.14...2 x 0.75 mm² flexible cable with cable end, with double bezelCaptive screw clamp terminals, clamping capacity: 2 x 0.14...2 x 0.75 mm² solid cable with cable end,with double bezelCaptive screw clamp terminals, clamping capacity: 2 x 0.25...2 x 1 mm² flexible cable with cable end,with double bezelOutput typeRelay instantaneous opening 3 NO, volt-free Number of additional circuits 0[Us] rated supply voltage24 V AC (- 15...10 %)24 V DC (- 15...10 %)ComplementarySynchronisation time between inputs UnlimitedSupply frequency50/60 HzPower consumption in VA<= 5 VA ACInput protection type Internal, electronicControl circuit voltage24 VLine resistance90 OhmBreaking capacity C300: 180 VA, AC-15 (holding) relay outputC300: 1800 VA, AC-15 (inrush) relay outputBreaking capacity 1.5 A at 24 V (DC-13) time constant: 50 ms for relay outputOutput thermal current 6 A per relay relay output18 A[Ith] conventional free air thermalcurrentAssociated fuse rating 4 A fuse type gG or gL for relay output conforming to EN/IEC 60947-5-1, DIN VDE 0660 part 2006 A fuse type fast blow for relay output conforming to EN/IEC 60947-5-1, DIN VDE 0660 part 200 Minimum output current10 mA relay outputMinimum output voltage17 V relay outputResponse time on input open<= 40 ms[Ui] rated insulation voltage300 V (degree of pollution: 2) conforming to DIN VDE 0110 part 1300 V (degree of pollution: 2) conforming to IEC 60947-5-1[Uimp] rated impulse withstand voltage 4 kV overvoltage category III conforming to IEC 60947-5-14 kV overvoltage category III conforming to DIN VDE 0110 part 1Local signalling 3 LEDsCurrent consumption30 mA at 24 V AC (on power supply)Mounting support35 mm symmetrical DIN railProduct weight0.55 lb(US) (0.25 kg)EnvironmentStandards EN 1088/ISO 14119EN 60204-1EN/IEC 60947-5-1EN/ISO 13850Product certifications CSATÜVULIP degree of protection IP20 (terminals) conforming to EN/IEC 60529IP40 (enclosure) conforming to EN/IEC 60529Ambient air temperature for operation-13...140 °F (-25...60 °C)Ambient air temperature for storage-40...185 °F (-40...85 °C)Ordering and shipping detailsCategory22477 - SAFETY MODULES (PREVENTA)Discount Schedule SAF2GTIN00785901445463Nbr. of units in pkg.1Package weight(Lbs)0.55000000000000004Returnability YCountry of origin IDContractual warrantyWarranty period18 months。
Hikvision DS-2CDx1xxG0-xxx 网络摄像头快速使用指南说明书

DS-2CDx1xxG0-xxx Network Dome CameraQuick Start Guide© 2020 Hangzhou Hikvision Digital Technology Co., Ltd. All rights reserved.This Manual is the property of Hangzhou Hikvision Digital Technology Co., Ltd. or its affiliates (hereinafter referred to as “Hikvision”), and it cannot be reproduced, changed, translated, or distributed, partially or wholly, by any means, without the prior written permission of Hikvision. Unless otherwise expressly stated herein, Hikvision does not make any warranties, guarantees or representations, express or implied, regarding to the Manual, any information contained herein.About this ManualThe Manual includes instructions for using and managing the Product. Pictures, charts, images, and all other information hereinafter are for description and explanation only. The information contained in the Manual is subject to change, without notice, due to firmware updates or other reasons. Please find the latest version of this Manual at the Hikvision Website (/en/).Please use this Manual with guidance and assistance of professionals trained in supporting the Product. Trademarks Acknowledgementand other Hikvision trademarks and logos are the properties of Hikvision in various jurisdictions. Other trademarks and logos mentioned below are the properties of their respective owners. LEGAL DISCLAIMERTO THE MAXIMUM EXTENT PERMITTED BY APPLICABLE LAW, THIS MANUAL AND THE PRODUCT DESCRIBED, WITH ITS HARDWARE, SOFTWARE AND FIRMWARE, ARE PROVIDED “AS IS” AND “WITH ALL FAULTS AND ERRORS.” HIKVISION MAKES NO WARRANTIES, EXPRESS OR IMPLIED, INCLUDING WITHOUT LIMITATION, MERCHANTABILITY, SATISFACTORY QUALITY, OR FITNESS FOR A PARTICULAR PURPOSE. THE USE OF THE PRODUCT BY YOU IS AT YOUR OWN RISK. IN NO EVENT WILL HIKVISION BE LIABLE TO YOU FOR ANY SPECIAL, CONSEQUENTIAL, INCIDENTAL, OR INDIRECT DAMAGES, INCLUDING, AMONG OTHERS, DAMAGES FOR LOSS OF BUSINESS PROFITS, BUSINESS INTERRUPTION, OR LOSS OF DATA, CORRUPTION OF SYSTEMS, OR LOSS OF DOCUMENTATION, WHETHER BASED ON BREACH OF CONTRACT, TORT (INCLUDING NEGLIGENCE), PRODUCT LIABILITY, OR OTHERWISE, IN CONNECTION WITH THE USE OF THE PRODUCT, EVEN IF HIKVISION HAS BEEN ADVISED OF THE POSSIBILITY OF SUCH DAMAGES OR LOSS.YOU ACKNOWLEDGE THAT THE NATURE OF INTERNET PROVIDES FOR INHERENT SECURITY RISKS, AND HIKVISION SHALL NOT TAKE ANY RESPONSIBILITIES FOR ABNORMAL OPERATION, PRIVACY LEAKAGE OR OTHER DAMAGES RESULTING FROM CYBER-ATTACK, HACKER ATTACK, VIRUS INSPECTION, OR OTHER INTERNET SECURITY RISKS; HOWEVER, HIKVISION WILL PROVIDE TIMELY TECHNICAL SUPPORT IF REQUIRED.YOU AGREE TO USE THIS PRODUCT IN COMPLIANCE WITH ALL APPLICABLE LAWS, AND YOU ARE SOLELY RESPONSIBLE FOR ENSURING THAT YOUR USE CONFORMS TO THE APPLICABLE LAW. ESPECIALLY, YOU ARE RESPONSIBLE, FOR USING THIS PRODUCT IN A MANNER THAT DOES NOT INFRINGE ON THE RIGHTS OF THIRD PARTIES, INCLUDING WITHOUT LIMITATION, RIGHTS OF PUBLICITY, INTELLECTUAL PROPERTY RIGHTS, OR DATA PROTECTION AND OTHER PRIVACY RIGHTS. YOU SHALL NOT USE THIS PRODUCT FOR ANY PROHIBITED END USES, INCLUDING THE DEVELOPMENT OR PRODUCTION OF WEAPONS OF MASS DESTRUCTION, THE DEVELOPMENT OR PRODUCTION OF CHEMICAL OR BIOLOGICAL WEAPONS, ANY ACTIVITIES IN THE CONTEXT RELATED TO ANY NUCLEAR EXPLOSIVE OR UNSAFE NUCLEAR FUEL-CYCLE, OR IN SUPPORT OF HUMAN RIGHTS ABUSES.IN THE EVENT OF ANY CONFLICTS BETWEEN THIS MANUAL AND THE APPLICABLE LAW, THE LATTER PREVAILS.Regulatory Information FCC InformationPlease take attention that changes or modification not expressly approved by the party responsible for compliance could void the user’s authority to operate the equipment.FCC Compliance: This equipment has been tested and found to comply with the limits for a Class B digital device, pursuant to part 15 of the FCC Rules. These limits are designed to provide reasonable protection against harmful interference in a residential installation. This equipment generates, uses, and can radiate radio frequency energy and, if not installed and used in accordance with the instructions, may cause harmful interference to radio communications. However, there is no guarantee that interference will not occur in a particular installation. If this equipment does cause harmful interference to radio or television reception, which can be determined by turning the equipment off and on, the user is encouraged to try to correct the interference by one or more of the following measures:•Reorient or relocate the receiving antenna.•Increase the separation between the equipment and receiver.•Connect the equipment into an outlet on a circuit different from that to which the receiver is connected.•Consult the dealer or an experienced radio/TV technician for helpFCC ConditionsThis device complies with part 15 of the FCC Rules. Operation is subject to the following two conditions:•This device may not cause harmful i nterference.•This device must accept any interference received, including interference that may cause undesired operation.EU Conformity StatementThis product and, if applicable, the supplied accessories too are marked with “CE” and complytherefore with the applicable harmonized European standards listed under the EMC Directive2014/30/EU, the RoHS Directive 2011/65/EU.2012/19/EU (WEEE Directive): Products marked with this symbol cannot be disposed of asunsorted municipal waste in the European Union. For proper recycling, return this product to yourlocal supplier upon the purchase of equivalent new equipment, or dispose of it at designatedcollection points. For more information see: 2006/66/EC and its amendment 2013/56/EU (battery directive): This product contains a battery thatcannot be disposed of as unsorted municipal waste in the European Union. See the productdocumentation for specific battery information. The battery is marked with this symbol, which mayinclude lettering to indicate cadmium (Cd), lead (Pb), or mercury (Hg). For proper recycling,return the battery to your supplier or to a designated collection point. For more information see:www. .Industry Canada ICES-003 Compliance. This device meets the CAN ICES-3 (B)/NMB-3(B)standards r equirements.These instructions are intended to ensure that the user can use the product correctly to avoiddanger or property loss.Laws and RegulationsThe device should be used in compliance with local laws, electrical safety regulations, and fire prevention regulations.TransportationKeep the device in original or similar packaging while transporting it.Power SupplyThe input voltage should conform to IEC60950-1 standard: SELV (Safety Extra Low Voltage) and the LPS (Limited Power Source). Refer to the appropriate documentation for detailed information.DO NOT connect multiple devices to one power adapter, to avoid over-heating or fire hazards caused by overload.Make sure the plug is properly connected to the power socket.System SecurityThe installer and user are responsible for password and security configuration and its settings. BatteryImproper use or replacement of the battery may result in explosion hazard. Replace with the same or equivalent type only. Dispose of used batteries in conformance with the local codes. MaintenanceIf the product does not work properly, please contact your dealer or the nearest service center. We shall not assume any responsibility for problems caused by unauthorized repair or maintenance.A few device components (e.g., electrolytic capacitor) require regular replacement. The average lifespan varies, so periodic checking is recommended. Contact your dealer for details.CleaningPlease use a soft and dry cloth when clean inside andoutside surfaces of the product cover. Do not use alkaline detergents.Usage EnvironmentWhen any laser equipment is in use, make sure that the device lens is not exposed to the laser beam, or itmay burn out.Do not expose the device to high electromagnetic radiation or dusty environments.For an indoor-only device, place it in a dry and well-ventilated environment.Do not aim the lens at the sun or any other bright light.Make sure the running environment meets the requirement of the device. The operating temperature shall be -30° to 60° C (-22° to 140° F) or -40° to 60° C (-40° to 140° F), and the operating humidity shall be 95% or less (non-condensing).Do not place the camera in extremely hot, cold, dusty, or damp locations, and do not expose it to high electromagnetic radiation.EmergencyIf smoke, odor, or noise arises from the device, immediately turn off the power, unplug the power cable, and contact the service center.Time SynchronizationSet up camera time manually for the first time access if the local time is not synchronized with that of the network. Visit the camera via Web browser/client software and go to the time settings interface. InstallationMake sure the device is firmly secured to any wall or ceiling mountings.Be sure that there is enough space to install the camera and accessories.Make sure that the device in the package is in good condition and all the assembly parts are included. Make sure that the wall is strong enough to withstand at least foour times the weight of the camera and the mount.The standard power supply is 12 VDC, please make sure your power supply matches with your camera. Make sure that the power has been disconnected before you wire, install, or disassemble the device. Make sure that no reflective surface is too close to the camera lens. The IR light from the camera may reflect back into the lens causing reflection.For a device with this sticker, this device is intended for installation in a restrictedaccess location, access can only be gained by service persons or by users who havebeen instructed about the reasons for the restrictions applied to the location andabout any precautions that shall be taken.Symbols and MarksPackage ContentsInstallation 1.11.2*2.1A.2A.4B.22.23.13.23.4Camera Terminal Block WiringRS-485CVBSAlarm Output with Power from CameraAlarm Output with External PowerAlarm Input12 VDC OutputActivate and Access Network CameraScan the QR code to get Activate and Access Camera.NOTE: Mobile data charges may apply if Wi-Fi is unavailable.OperationReset and Restore CameraPress the Reset button for approximately 10s when the camera is powering on or rebooting to restore the default settings, including the user name, password, IP address, port no., etc.For the position of the reset button, refer to the figure in the interface introduction page.。
XX项目四足机器人关键性能目标

只考虑空旷 平地摔倒后
M空R载S情1 况下,分别用10、20、30N的力对正常行
走机的器机马器开马机各静部止分站进立行,干在扰rec,o测ve试ry整(机A)抗,干分扰别能以以
1机0器、马20开、机30静、止4站0k立g,,1m在单站摆立4(5°X,)自,分由别冲以击以机1器0
★
、20、30、40kg,1m单摆45°,自由冲击机器马
跨越
跳跃
低趴
04-能量管理(续航、能耗、充电) √ 04.01 续航能力(时间、里程)
原地踏步续航时间-(空载) 原地踏步续航时间-(满载、10、20、30kg) walk行走续航时间-空载 walk行走续航里程-空载 walk行走续航时间-(满载、10、20、30kg) walk行走续航里程-(满载、10、20、30kg) trot行走续航时间-空载 trot行走续航里程-空载 trot行走续航时间-(满载、10、20、30kg) trot行走续航里程-(满载、10、20、30kg) 骑乘续航时间-30kg 骑乘续航里程-30kg 综合场景路况续航时间-(空载、满载)
ET2
竞品机型
最大坡度(向上前进)-walk(空载+满载)
最大坡度(向上前进)-trot(空载+满载) 最大坡度(向下前进)-walk(空载+满载) 最大坡度(向下前进)-trot(空载+满载) 最大坡度(向上后退)-walk(空载+满载) 最大坡度(向上后退)-trot(空载+满载) 最大坡度(向下后退)-walk(空载+满载)
1)机器人额定负载,位于3°,6°或者10°坡的初 始位置; 2)机器人沿坡道直线行走,达到最大速度; 3)参考额定速度的测方法测试坡上最大速度; 4)测试条件同额定速度的测试。
DS2401_cn

DS2401硅序列号特性与DS2400引脚兼容的升级产品— 外部供电电源范围:2.8V至6.0V— 多个DS2401可以连接在一条公共的1-Wire®总线工厂刻入、经过检测的64位注册码(8位家族码 + 48位序列码 + 8位CRC校验码);保证没有任何两个器件的注册码是相同的内部多点控制器确保与其他1-Wire网络产品兼容8位家族码表明DS2401通信需要读取装置读取装置首次上电时将产生在线脉冲应答低成本TO-92、SOT-223和 TSOC表面贴封装将控制、地址、数据和供电集于一个引脚零待机电源直接与微处理器的一个口线连接,通信速率达16.3kbpsTO-92卷带包装具有倾斜引脚,间隔100mil (默认) 或直引脚 (DS2401T-SL)应用— PCB识别— 网络节点ID— 设备注册工作在扩展工业级温度范围: -40°C至+85°C引脚配置TO-92TSOC PACKAGETOP VIEW3.7mm x4.0mm x 1.5mm1 2 3TOP VIEWSee Mech. DrawingsSectionBOTTOM VIEW1 2Flip Chip, Top Viewwith Laser Mark,Contacts Not Visible.“rrd” = Revision/DateSee 56-G7009-001 for package outline.引脚说明TO-92,SOT-223 TSOC 倒装芯片引脚 1 地地数据(DQ)引脚2 数据 (DQ)数据(DQ) 地引脚3 无连接无连接—引脚4 地无连接—引脚5-6— 无连接—1-Wire是Dallas Semiconductor的注册商标。
定购信息型号无铅封装说明DS2401 DS2401+ TO-92封装DS2401/T&R DS2401+T&R TO-92 封装, 卷带包装DS2401/T&R/SL DS2401-SL+T&R TO-92 封装,直引脚,卷带包装DS2401Z DS2401Z+ SOT-223表面贴封装DS2401Z/T&R DS2401Z+T&R SOT-223表面贴封装, 卷带包装DS2401P DS2401P+ TSOC 表面贴封装DS2401P/T&R DS2401P+T&R TSOC表面贴封装, 卷带包装DS2401X1[JP1]— 晶片级封装, 卷带包装概述DS2401增强型硅序列号是一款低成本的电子注册码,以最少的电接口(通常只需一个微处理器端口)提供绝对、唯一的识别功能。
海康威视设备网络SDK编程指南报警主机

海康威视设备⽹络SDK编程指南报警主机设备(报警主机) ⽹络SDK编程指南V5.2声明⾮常感谢您购买我公司的产品,如果您有什么疑问或需要请随时联系我们。
●我们已尽量保证⼿册内容的完整性与准确性,但也不免出现技术上不准确、与产品功能及操作不相符或印刷错误等情况,如有任何疑问或争议,请以我司最终解释为准。
●产品和⼿册将实时进⾏更新,恕不另⾏通知。
●本⼿册中内容仅为⽤户提供参考指导作⽤,请以SDK实际内容为准。
⽬录声明 ........................................................................................................................................................................... I ⽬录.. (II)1 SDK简介 (1)2 版本更新 (4)3 功能接⼝介绍 (13)3.1报警主机通⽤接⼝ (13)3.2DS-19Axx⽹络报警主机 (15)3.3DS-19Axx总线式⽹络报警主机 (18)3.4DS-19Dxx动环监控主机 (20)3.5DS-19Cxx⾃助⾏报警主机 (23)3.6DS-19Sxx视频报警主机 (26)3.7DS-1H02防护舱控制器 (34)3.8DS-19xx系列报警主机 (38)4 函数调⽤顺序 (40)4.1参数配置模块流程 (40)4.2报告上传⽅式配置流程 (41)4.3报警模块流程 (42)4.3.1 报警(布防)流程 (42)4.3.2 报警(监听)流程 (43)5 函数说明 (44)5.1SDK初始化 (44)5.1.1 初始化SDK NET_DVR_Init (44)5.1.2 释放SDK资源NET_DVR_Cleanup (44)5.2SDK本地功能 (44)SDK本地参数配置 (44)5.2.1 获取SDK本地参数NET_DVR_GetSDKLocalCfg (44)5.2.2 设置SDK本地参数NET_DVR_SetSDKLocalCfg (45)连接和接收超时时间及重连设置 (45)5.2.3 设置⽹络连接超时时间和连接尝试次数NET_DVR_SetConnectTime (45)5.2.4 设置重连功能NET_DVR_SetReconnect (46)5.2.5 设置接收超时时间NET_DVR_SetRecvTimeOut (46)多⽹卡绑定 (46)5.2.6 获取所有IP,⽤于⽀持多⽹卡接⼝NET_DVR_GetLocalIP (46)5.2.7 设置IP绑定NET_DVR_SetValidIP (47)SDK版本、状态和能⼒ (47)5.2.8 获取SDK的版本号和build信息NET_DVR_GetSDKBuildVersion (47)5.2.9 获取当前SDK的状态信息NET_DVR_GetSDKState (47)5.2.10 获取当前SDK的功能信息NET_DVR_GetSDKAbility (47)SDK启⽤写⽇志 (48)5.2.11 启⽤写⽇志⽂件NET_DVR_SetLogToFile (48)异常消息回调 (48)5.2.12 注册接收异常、重连等消息的窗⼝句柄或回调函数NET_DVR_SetExceptionCallBack_V30 48获取错误信息 (50)5.2.13 返回最后操作的错误码NET_DVR_GetLastError (50)5.2.14 返回最后操作的错误码信息NET_DVR_GetErrorMsg (51)5.3⽤户注册 (51)5.3.1 激活设备NET_DVR_ActivateDevice (51)5.3.2 通过解析服务器,获取设备的动态IP地址和端⼝号NET_DVR_GetDVRIPByResolveSvr_EX51 5.3.3 ⽤户注册设备NET_DVR_Login_V40 (52)5.3.4 ⽤户注销NET_DVR_Logout (52)5.4获取设备能⼒集 (52)5.4.1 获取设备能⼒集NET_DVR_GetDeviceAbility (52)5.5布防、撤防 (53)设置报警等信息上传的回调函数 (53)5.5.1 注册回调函数,接收设备报警消息NET_DVR_SetDVRMessageCallBack_V30 (53)布防撤防 (55)5.5.2 建⽴报警上传通道NET_DVR_SetupAlarmChan_V41 (55)5.5.3 撤销报警上传通道NET_DVR_CloseAlarmChan_V30 (55)5.6监听报警 (55)5.6.1 启动监听,接收设备主动上传的报警等信息NET_DVR_StartListen_V30 (55)5.6.2 停⽌监听(⽀持多线程)NET_DVR_StopListen_V30 (56)5.7远程参数配置 (57)5.7.1 获取设备通⽤参数NET_DVR_GetDVRConfig (57)5.7.2 设置设备通⽤参数NET_DVR_SetDVRConfig (58)5.7.3 获取报警主机参数NET_DVR_GetDVRConfig (59)5.7.4 设置报警主机参数NET_DVR_SetDVRConfig (62)5.8批量配置参数 (65)5.8.1 批量获取配置信息NET_DVR_GetDeviceConfig (65)5.8.2 批量设置配置信息NET_DVR_SetDeviceConfig (66)5.9长连接配置 (67)5.9.1 启动长连接远程配置NET_DVR_StartRemoteConfig (67)5.9.2 逐个获取查找到的结果信息NET_DVR_GetNextRemoteConfig (69)5.9.3 关闭长连接配置接⼝所创建的句柄,释放资源NET_DVR_StopRemoteConfig (70) 5.10远程控制 (70)5.10.1 远程控制NET_DVR_RemoteControl (70)5.11设备⽤户和操作⽤户配置 (71)5.11.1 获取设备⽤户配置信息NET_DVR_GetAlarmDeviceUser (71)5.11.2 设置设备⽤户配置信息NET_DVR_SetAlarmDeviceUser (71)5.11.3 获取键盘操作⽤户配置信息NET_DVR_GetOperateUser (71)5.11.4 设置键盘操作⽤户配置参数NET_DVR_SetOperateUser (72)5.12RS485前端设备 (72)5.12.1 获取485前端设备能⼒列表NET_DVR_GetDeviceTypeList (72)5.12.2 获取RS485前端设备⽀持的协议列表NET_DVR_GetDeviceProtoList (72)5.13透明通道 (73)5.13.1 建⽴透明通道NET_DVR_AlarmHostSerialStart (73)5.13.2 发送透明通道数据NET_DVR_AlarmHostSerialSend (73)5.13.3 断开透明通道NET_DVR_AlarmHostSerialStop (74)5.14防区布防、撤防、旁路及撤销旁路 (74)5.14.1 对防区布防NET_DVR_AlarmHostSetupAlarmChan (74)5.14.2 对防区撤防NET_DVR_AlarmHostCloseAlarmChan (74)5.14.3 对防区旁路NET_DVR_BypassAlarmChan (74)5.14.4 对防区撤销旁路NET_DVR_UnBypassAlarmChan (75)5.15防区组旁路 (75)5.15.1 对防区进⾏组旁路NET_DVR_AlarmHostArrayBypass (75)5.15.2 对防区进⾏组旁路恢复NET_DVR_AlarmHostArrayBypassResume (75)5.16触发器和辅助输出控制 (75)5.16.1 设置触发器NET_DVR_SetAlarmHostOut (75)5.16.2 辅助功能控制NET_DVR_AlarmHostAssistantControl (76)5.16.3 门禁控制NET_DVR_ControlGateway (76)5.17⼦系统布防、撤防及消警 (76)5.17.1 对防区⼦系统布防NET_DVR_AlarmHostSubSystemSetupAlarmChan (76) 5.17.2 对防区⼦系统撤防NET_DVR_AlarmHostSubSystemCloseAlarmChan (77) 5.17.3 对防区⼦系统进⾏消警NET_DVR_AlarmHostClearAlarm (77)5.18获取报警上传⽅式配置 (77)5.18.1 获取报警上传⽅式参数NET_DVR_AlarmHostGetReportMode (77)5.18.2 设置报警上传⽅式NET_DVR_AlarmHostSetReportMode (77)5.19蓄电池电压查询 (78)5.19.1 蓄电池电压查询NET_DVR_GetBatteryVoltage (78)5.20语⾳控制 (78)5.20.1 语⾳控制NET_DVR_AudioCtrl (78)5.21语⾳上传下载 (78)5.21.1 开始语⾳上传NET_DVR_StartUploadFile (78)5.21.2 获取语⾳上传的进度NET_DVR_GetUploadFileProgress (79)5.21.3 获取语⾳上传的状态NET_DVR_GetUploadFileState (79)5.21.4 停⽌语⾳上传NET_DVR_StopUploadFile (79)5.21.5 开始语⾳下载NET_DVR_StartDownloadFile (79)5.21.6 获取语⾳下载的进度NET_DVR_GetDownloadFileProgress (80)5.21.7 获取语⾳下载的状态NET_DVR_GetDownloadFileState (80)5.21.8 停⽌语⾳下载NET_DVR_StopDownloadFile (80)5.22语⾳对讲 (80)5.22.1 启动语⾳对讲NET_DVR_StartVoiceCom_V30 (80)5.22.2 停⽌语⾳对讲NET_DVR_StopVoiceCom (82)5.23硬盘管理 (82)5.23.1 远程格式化设备硬盘NET_DVR_FormatDisk (82)5.23.2 获取格式化硬盘的进度NET_DVR_GetFormatProgress (82)5.23.3 关闭格式化硬盘句柄,释放资源NET_DVR_CloseFormatHandle (83)5.24设备维护管理 (83)状态获取 (83)5.24.1 获取外接设备状态信息NET_DVR_GetDeviceStatus (83)5.24.2 获取报警主机状态信息NET_DVR_GetDVRConfig (84)5.24.3 设备在线状态检测NET_DVR_RemoteControl (84)⽇志查询 (85)5.24.4 查找⽇志信息NET_DVR_FindAlarmHostLog (85)5.24.5 逐条获取⽇志信息NET_DVR_FindNextAlarmHostLog (85)5.24.6 关闭⽇志查找NET_DVR_FindAlarmHostLogClose (86)远程升级 (86)5.24.7 远程升级设备固件NET_DVR_Upgrade_V40 (86)5.24.8 获取远程升级的进度NET_DVR_GetUpgradeProgress (87)5.24.9 获取远程升级的状态NET_DVR_GetUpgradeState (87)5.24.10 关闭远程升级NET_DVR_CloseUpgradeHandle (87)恢复设备默认参数 (87)5.24.11 恢复设备默认参数NET_DVR_RestoreConfig (87)5.24.12 完全恢复出⼚默认参数NET_DVR_RemoteControl (87)6 错误代码及说明 (89)6.1⽹络通讯库错误码 (89)6.2语⾳对讲库错误码 (92)7 附录.名词解释 (94)1SDK简介设备⽹络SDK是基于设备私有⽹络通信协议开发的,为嵌⼊式⽹络硬盘录像机、NVR、视频服务器、⽹络摄像机、⽹络球机、解码器、报警主机等⽹络产品服务的配套模块,⽤于远程访问和控制设备软件的⼆次开发。
- 1、下载文档前请自行甄别文档内容的完整性,平台不提供额外的编辑、内容补充、找答案等附加服务。
- 2、"仅部分预览"的文档,不可在线预览部分如存在完整性等问题,可反馈申请退款(可完整预览的文档不适用该条件!)。
- 3、如文档侵犯您的权益,请联系客服反馈,我们会尽快为您处理(人工客服工作时间:9:00-18:30)。
(A
* 1
)
= A1
5 2 1 A = 2 2 0 1 0 1
例5 已知矩阵 X 满足矩阵方程
1 1 1 2 2 1 X 0 2 2 = 4 0 2 1 1 0 0 6 6
求矩阵 X .
1
1 1 2 = 6 ≠ 0, 0
解:方法 方法1(用逆矩阵) 由于 A = 0 2 方法 1 1 所以 A 可逆,故
1
1 1 1 1 2 2 1 1 1 X = BA1 = 4 0 2 0 2 2 = 2 0 2 0 6 6 1 1 0 0 3 0
方法 2(列初等变换)
1 1 1 1 0 0 0 2 2 0 1 0 0 0 1 I 1 1 1 A 1 1 0 = →→ = ,故 X = 2 0 2 1 1 1 X B 2 2 1 0 3 0 4 0 2 2 0 2 0 6 6 0 3 0
推论 1 可逆矩阵 A 可以表示为若干个初等矩阵的乘积. 证明:由定理1,存在初等矩阵 Q1 , Q2 , , Qs,使得
Qs Q2Q1 A = I ,从而有:
A = ( Qs Q2Q1 ) = ( Q1 )
1 1
( Q2 )
1
( Qs )
1
其中 ( Q1 ) , ( Q2 ) , , ( Qs )
5 2
1 0 0 1 1 0 1 0 1
1 0 1 → 0 1 0 0 0 1
2 1 0 1 0 0 → 0 1 0 1 1 0 1 0 1 0 0 1 2 2
1 1 2 1 1 0 1 1 0 2 2
1 1 1 5 1 1 2 2 有 A = 1 1 0 .又 A1 = 1 2 1 = 2 ,所以 1 1 0 1 1 3 2 2
←第 i 行 ←第 j 行 1
2. 用数 k ( k ≠ 0) 乘单位矩阵 I 的第 i 行(或列)得到 的初等矩阵记为 Ei (k ) ,即
1 1 ←第 i 行 Ei ( k ) = k 1 1
3. 把单位矩阵 I 的第
*
1
*
解:由 AA* = A I,用矩阵 A 左乘方程的两端,有:
AA X = A ( A + 2 X ),即 A X = I + 2 AX ,从而
* 1
( A I 2 A) X = I ,故 X = ( A I 2 A) .又
下面介绍用初等变换求逆矩阵的方法: 定理 1 可逆矩阵可以经过若干次行(列)初等变换 化为单位矩阵. 证明: n 阶可逆矩阵
a11 a 21 A= an1
a12 a1n a22 a2 n an 2 ann
的行列式 A ≠ 0 ,所以它的第一列元素不全为零.不 (如果 a11 = 0,必存在 ai1 ≠ 0 此时先 失一般性,设 a11 ≠ 0 把第1行与第 i 行对换),现将第1行乘
2 2 1 1 2 0 1 1 1
0 0 1 1 2 0 1 1 1
1 2 2 A1 = 1 1 2 所以: 0 1 1
例3 设 A 是一个 n 阶可逆矩阵,如果 A 中每行元素 之和都是 3,求 A1 中每行元素之和. 解:由于矩阵 A 的第 i 行元素之和
1 1 ai1 + ai 2 + + ain = [ ai1 , ai 2 , , ain ] = 3 ,故 1
二,初等矩阵
定义 3 对单位矩阵作一次初等变换所得的矩阵称 为初等矩阵. 三种初等变换对应着三种初等矩阵: 1. 交换单位矩阵 I 的第 i, j 行(或列)得到的初等 矩阵记为 E i j ,即
1 E ij =
1 0 1 1 1 1 0 1
故 PA是对 A 作一次行变换(一,三行互换),
P 2001 A = PA , AQ 是对 A 作一次列变换(二,三列互换),
从而 AQ
2002
7 8 9 = A ,故原式 = PA = 4 5 6 . 1 2 3
1 0 2 例2 求矩阵 A = 1 1 0 的逆矩阵. 1 1 1
第四节 矩阵的初等变换和初等矩阵
一,矩阵的初等变换
定义 1 矩阵的行(列)初等变换指的是一个矩阵施 行的下列三种变换: 1.交换矩阵的两行(列); 2.用一个不等于零的数乘矩阵的某一行(列),即 用一个不等于零的数乘矩阵的某一行(列)的每 一个元素;
3.用某一数乘矩阵的某一行(列)后加到另一行 (列),即用某一数乘矩阵的某一行(列)的每一 元素后加到另一行(列)的对应元素上. 矩阵的行初等变换和列初等变换统称为初等变换. 性质 1 矩阵的每一种初等变换都是可逆的,即若矩 阵 A 经过一次行(列)初等变换变为矩阵 B,则矩阵
1 = Eij , ( Ei ( k )) = Ei ( ), ( Eij ( k )) 1 = Eij ( k ) k
1
从而初等矩阵的逆阵还是同型的初等矩阵. 性质 4 设 A 是一个 m × n 矩阵,对矩阵 A 施行一次初 等行变换相当于在矩阵 A 的左边乘以一个相应的 m 阶初等矩阵;对矩阵 A 施行一次初等列变换相当于在 矩阵 A的右边乘以一个相应的 n 阶初等矩阵. 即有:
1 0 2 A I = 1 1 0 解: 1 1 1
1 0 0 1 0 2 0 1 0 → 1 1 0 0 0 1 0 0 1
0 0 0 1 0 0 1 1 1
1 0 2 → 0 1 2 0 0 1
1 0 0 → 0 1 0 0 0 1
0 0 1 0 2 1 1 0 → 0 1 0 0 1 1 0 0 1 1
方法 3(用方程组)
x1 设 X = x4 x7 x2 x5 x8 x3 x6 ,则有 x9
x1 + x3 x + x 4 6 x7 + x9
x1 + 2 x2 x3 x4 + 2 x5 x6 x7 + 2 x8 x9
x1 + 2 x2 2 2 1 = 4 0 2 x4 + 2 x5 x7 + 2 x8 0 6 6
2 0 1 1 1 2 X = ( A I ) ( A I ) = ( A I ) ( A I )( A + I ) = A + I = 0 3 6 1 6 2 1 1 1 例7 已知矩阵 A = 1 1 1,矩阵 X 满足: 1 1 1
A X = A + 2 X,其中 A 是 A 的伴随矩阵,求矩阵X.
1 3 1 3 A = ,从而用 A1 左乘上式的两端,有 1 3
1 1 1 3 1 1 1 3 1 1 1 1 ,故 A ,从而 A1 = A A =A 3 1 3 1 1
1 中每行元素之和为 . 3
伴随矩阵 A 的逆矩阵.
1 1
1
仍是初等矩阵,推论得证.
推论 2 如果对可逆矩阵 A 和同阶的单位矩阵 I 作同样 的行初等变换,那么当 A 变为单位矩阵时, I 就变为
行初等变换 矩阵 A1,即: A | I ] → → I | A 1 . 同理地,对 [
可逆矩阵 A 和同阶的单位矩阵 I 作同样的列初等变换, 那么当 A 变为单位矩阵时,I 就变为矩阵 A ,即:
1 c12 0 1 Q2l Q22Q21 B = 0 0
c1n c2 n C 1
其中 Q21 , Q22 , , Q2l 是对 B 作行初等变换所对应的初等 矩阵.再将 C 中的第 n, n 1, , 2 行依次分别乘某些 常数加到前面的第 n 1, n 2, ,1 行,就可使 C 化为单 位矩阵,即:Q3k Q32Q31C = I ,其中 Q31 , Q32 , , Q3k 是对
B 也可以经过一次同种行(列)初等变换变为矩阵 A.
定义 2 若矩阵 A 经过有限次初等变换变成矩阵 B , 则称矩阵 A与 B 相抵,记为 A B . 性质 2 矩阵的相抵关系是一个等价关系,即矩阵的 相抵关系满足:(设 A, B, C 是任意三个同型矩阵) 1,自反性 A A ; 2,对称性 若 A B, 则 B A ; 3,传递性 若 A B, B C, 则 A C .
C 作行初等变换所对应的初等矩阵.
综上就有
( Q3k Q32Q31 )( Q2l Q22Q21 )( Q1m Q12Q11 ) A = I
其中 A 左边的矩阵都是初等矩阵.从而可逆矩阵可以 经过若干次行初等变换化为单位矩阵. 类似的可证,可逆矩阵可以经过若干次列初等变 换化为单位矩阵.于是定理得证.
1 1 1 A 的逆矩阵为 A1 = 1 2 1 ,求 A 的 例4 已知矩阵 1 1 3 *
A 1 解:由 A = ,故 A* = A A1,于是 A
(A )
* 1
=( A A
1 1
)
1 = A = A1 A ,再由 A
1 1 1 A1 I = 1 2 1 1 1 3
1 0 0 1 1 1 0 1 0 → 0 1 0 0 0 1 0 0 2
Eij A 表示将 A 的第 i 行与第 j 行交换位置; AEij 表示将 A 的第 i 列与第 j 列交换位置;
Ei (k ) A 表示将 A 的第 i 行乘以 k (k ≠ 0); AEi (k ) 表示将 A 的第 i 列乘以 k (k ≠ 0); Eij (k ) A 表示将 A 的第 i 行乘以 k 加到第 j 行; AEij (k ) 表示将 A 的第 j 列乘以 k 加到第 i 列 .
列 初等变换 A I I → → A 1
1
三,例子 例1
0 0 1 计算:0 1 0 1 0 0
2001
1 2 3 1 0 0 4 5 6 0 0 1 7 8 9 0 1 0
2002
.
0 0 1 1 0 0 解:由于 P = 0 1 0 , Q = 0 0 1 都是初等矩阵,且 1 0 0 0 1 0
1 1 1 解方程得矩阵 X = 2 0 2 . 0 3 0