浅谈整车工厂项目阶段扭力控制管理办法
整车新项目流程管理
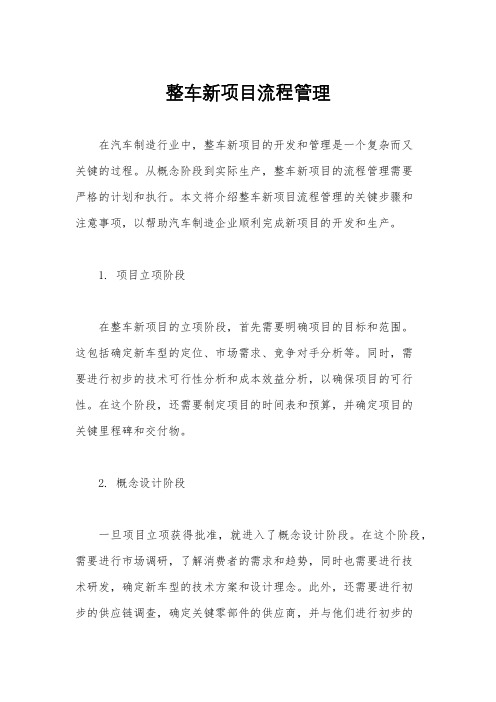
整车新项目流程管理在汽车制造行业中,整车新项目的开发和管理是一个复杂而又关键的过程。
从概念阶段到实际生产,整车新项目的流程管理需要严格的计划和执行。
本文将介绍整车新项目流程管理的关键步骤和注意事项,以帮助汽车制造企业顺利完成新项目的开发和生产。
1. 项目立项阶段在整车新项目的立项阶段,首先需要明确项目的目标和范围。
这包括确定新车型的定位、市场需求、竞争对手分析等。
同时,需要进行初步的技术可行性分析和成本效益分析,以确保项目的可行性。
在这个阶段,还需要制定项目的时间表和预算,并确定项目的关键里程碑和交付物。
2. 概念设计阶段一旦项目立项获得批准,就进入了概念设计阶段。
在这个阶段,需要进行市场调研,了解消费者的需求和趋势,同时也需要进行技术研发,确定新车型的技术方案和设计理念。
此外,还需要进行初步的供应链调查,确定关键零部件的供应商,并与他们进行初步的合作意向沟通。
3. 详细设计阶段在概念设计阶段确定了新车型的整体方向后,就需要进入详细设计阶段。
在这个阶段,需要进行更加深入的技术研发和设计工作,包括车身结构设计、动力总成设计、电子系统设计等。
同时,还需要进行供应链的深入调查和谈判,确定关键零部件的供应商,并签订正式的合作协议。
4. 工程验证阶段一旦详细设计完成,就需要进行工程验证阶段。
在这个阶段,需要进行样车制造和测试,验证车辆的性能和安全性能。
同时,还需要进行供应链的准备工作,确保关键零部件的供应和质量可控。
在这个阶段,需要进行大量的试验和测试工作,确保新车型的各项指标符合设计要求。
5. 试制阶段在工程验证通过后,就需要进行试制阶段。
在这个阶段,需要进行小批量试制和生产,确保生产工艺和质量控制的可行性。
同时,还需要进行市场测试,了解消费者的反馈和市场的接受程度。
在这个阶段,需要进行大量的调试和改进工作,确保新车型的生产工艺和质量控制符合要求。
6. 正式生产阶段一旦试制阶段通过,就需要进入正式生产阶段。
汽车零件生产中的项目管理与进度控制方法
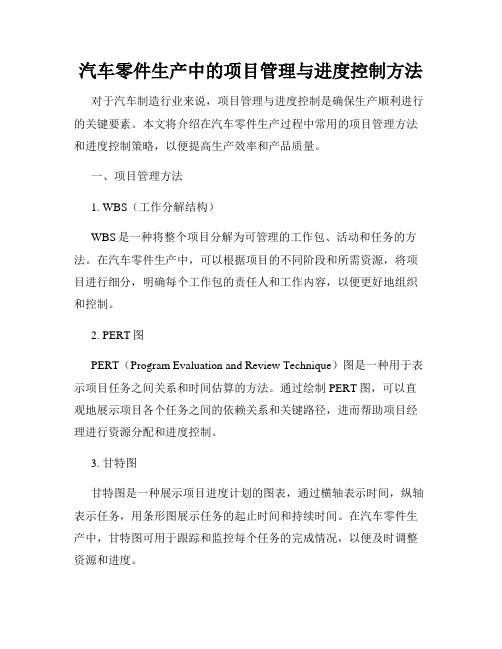
汽车零件生产中的项目管理与进度控制方法对于汽车制造行业来说,项目管理与进度控制是确保生产顺利进行的关键要素。
本文将介绍在汽车零件生产过程中常用的项目管理方法和进度控制策略,以便提高生产效率和产品质量。
一、项目管理方法1. WBS(工作分解结构)WBS是一种将整个项目分解为可管理的工作包、活动和任务的方法。
在汽车零件生产中,可以根据项目的不同阶段和所需资源,将项目进行细分,明确每个工作包的责任人和工作内容,以便更好地组织和控制。
2. PERT图PERT(Program Evaluation and Review Technique)图是一种用于表示项目任务之间关系和时间估算的方法。
通过绘制PERT图,可以直观地展示项目各个任务之间的依赖关系和关键路径,进而帮助项目经理进行资源分配和进度控制。
3. 甘特图甘特图是一种展示项目进度计划的图表,通过横轴表示时间,纵轴表示任务,用条形图展示任务的起止时间和持续时间。
在汽车零件生产中,甘特图可用于跟踪和监控每个任务的完成情况,以便及时调整资源和进度。
二、进度控制方法1.里程碑里程碑是项目中的重要节点或关键事件,通常与某个阶段的完成或重要决策相关。
在汽车零件生产中,可以设定里程碑来标记关键任务或阶段的完成,以便及时评估项目进展并进行调整。
2.风险管理对于生产过程中可能出现的风险和问题,及时进行风险管理是非常重要的。
通过制定风险应对计划和实施风险监控,可以减少风险对进度造成的影响,确保项目按时完成。
3.资源管理合理的资源管理对于项目的进度控制至关重要。
在汽车零件生产中,需要合理安排人员、原材料和设备的使用,确保资源的有效利用和高效运作,以提高项目的完成效率。
4.持续改进持续改进是一种通过周期性的评估和反馈来提高项目管理和进度控制的方法。
在汽车零件生产中,定期进行项目绩效评估和反思,及时调整和完善项目管理方法和控制策略,以便不断提高生产效率和产品质量。
结论对于汽车零件生产中的项目管理与进度控制,采用适当的方法和策略是至关重要的。
汽车制造过程中装配扭矩的控制和管理
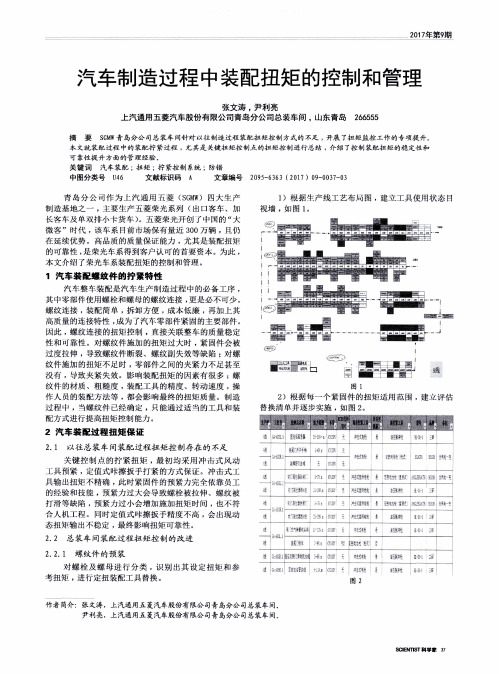
青 岛分公司作为上汽通用五菱 ( S G M W ) 四 大 生 产 制造 基 地之 一 ,主 要生 产 五菱 荣光 系 列 ( 出 口客 车 、加 长客 车 及单 双排 小卡 货车 ) 。五 菱 荣光开 创 丫中国 的 “ 大 微客 ”时代 ,该车 系 日前 市场 保有 量 近 3 0 0万辆 ,且 仍 在 延续 优 势 。高 品质 的质 量保 证 能力 , 尤 其 是装 配扭 矩 的 可靠 性 , 是荣 光车 系得 到 客户 认可 的首 要 资本 。为此 , 本 文介 绍 了荣光 车 系装 配扭矩 的控 制 和管 理 。
1 )根 据牛 产 线工 艺布 图 , 建 立工 具使 用 状 态 目
视墙 ,如 图 1 。
1 汽 车装配 螺纹 件 的拧 紧特 性
汽车 整 车装 配 是汽 车生 产 制 造过 程 中 的必 备工 序 , 其 中零 部件 使用 螺栓 和 螺母 的螺纹 连 接 , 更是必 不 可少 。 螺 纹连 接 , 装 配简 单 , 拆 卸方 便 , 成 本低 廉 , 再 加上 其 高 质量 的连 接特 性 , 成为 了汽 车 零部件 紧 崮 的主要 部件 。 因此 ,螺 纹连 接 的扭矩 控 制 ,直接 关 联整 车 的质 量稳 定 性 和可 靠 性 。对螺 纹件 施 加 的扭矩 过 大 时 , 紧 固件会 被 过 度拉 伸 , 导 致螺 纹件 断 裂 、螺纹 副 失 效等 缺陷 ; 对 螺 纹 件施 加 的扭 矩不 足 时 , 零部 件之 间 的火 紧 力不 足甚 至 没 有 ,. 导致 夹 紧失 效 。影 响装 配扭 矩 的 冈素有 很 多 :螺 纹 件 的材 质 、粗糙 度 , 装 配工 具 的精 度 、转 动速 度 ,操 作 人 员 的装 配 方法 等 , 都会 影 响最 终 的扭 矩质 量 。制 造 过 程 中 ,当螺 纹件 已经 确 定 ,只 能通 过适 当的工 具和 装 配 方式 进行 提高 扭矩控 制 能力 。
扭力管理办法

电批扭力管理办法
1、目的:确保电批在使用过程中具有最佳的扭力,保证产品质量,避免造成物料的损坏;
2、范围:公司生产作业工位打入螺钉的电批;
3、权责:
3.1 技术中心:负责生产作业工位打入螺钉电批扭力范围的制定;
3.2 制造部设备组:负责生产作业工位打入螺钉电批扭力的测试和记录的保存;
3.3 QA:负责生产作业工位打入螺钉电批扭力测试情况的稽核;
4、定义:无
5、作业内容:
5.1 技术中心确定相关机种和产品相关工位打入螺钉电批扭力以及误差范围;
5.2 技术中心制作首版作业指导书和制造部工艺人员修订作业指导书时明确规范和说明
电批扭力以及误差范围;
5.3 各制造部设备组自行确定电批扭力测试人员,每天在各拉线的打入螺钉工位的电批
使用或更换作业内容前用扭力测试仪测试电批扭力的大小,如扭力大小在作业指导书规定的范围内,则通知电批使用人员可以开始作业,并在《电批扭力测试记录表》相应位置填写测量扭力数据,且以上数值单位为Kgf.cm,如所测试的扭力不在作业指导书规定的范围内,则扭力测试人员可以对电批的扭力进行调整,直到所测试的扭力符合作业指导书的要求方可使用,否则在《电批扭力测试记录表》上的相应位置打“X”,并报送制造部设备组人员进行调整;
5.4 扭力测试合格后,测试人员应用不干胶标签贴在电批调节旋钮和电批主体的交界处,
并写明扭力的测试数值,防止电批调节旋钮转动造成扭力变动;
5.5 电批使用人员应保持标签的完好;
5.6 除测试记录人员外,其他任何人不得随便调整电批的扭力,但可以提出测试或调整
建议;
6、相关文件:
《WI-TE3-0062设备维护保养、维修管理规定A》
7、使用表单:
《电批扭力测试记录表》
8、附件:无。
汽车总装制造过程力矩管理

汽车总装制造过程力矩管理汽车总装制造的主要任务是将汽车各组成部分零部件组装成为整车,其中力矩问题一直被认为是汽车总装制造的核心问题,螺纹紧固力矩偏大或偏小直接关乎汽车驾驶者的行驶安全,因此建立一套有效的力矩管理体系对于保障总装装配质量尤其重要。
对于汽车来讲,力矩是影响汽车驾驶安全性能的关键因素,对快节拍的总装制造车间流水线人工螺栓拧紧作业来讲,螺栓联接力矩要受到5M1E即人、机、料、法、环、测等诸方面影响,其中任何一个环节出现异常都会导致力矩产生异常波动,而力矩非正常波动后未及时发现并返工则会给车辆售出后顾客乘坐带来难以预料的突发灾难。
因此做好总装车间力矩管理对于一个企业的可持续发展至关重要。
力矩的重要性1.螺栓联接后力的分布情况首先了解一下螺栓紧固过程中相关件的受力分布情况(见图1),从图1中可以看出螺栓紧固后,联接件与被联接件之间将形成一定的“夹紧力”,这个力是螺栓联接想要达到的目的,但事实上达到这个“夹紧力”的同时,联接件与被联接件还要承受一对横向的“剪切力”,而联接后螺栓受到来自联接件与被联接件施加的“张力”,根据牛顿第三定律得知,螺栓本身也会产生一个“抗张力”以保持受力平衡。
2.联接件与被联接件受力特性由上述分析可知,螺栓联接后想要的是使联接件与被联接件之间达到设计的夹紧力要求,夹紧力的大小就决定了联接的松紧。
通过图1我们可以看出,联接件与被联接件之间的夹紧力大小与螺栓旋转圈数有关,事实上它们之间存在着特定的线性关系(见图2)。
从图2中看出,夹紧力与螺栓旋转角度呈现的是一种分段型的线性关系,以联接件与被联接件开始接触时螺栓角度为初始角度0°、旋转1周角度递增360°计算,夹紧力大小将呈现以下三种状况:(1)当螺栓旋转处于0~角度1时,夹紧力与螺栓角度呈现单调递增关系,螺栓在角度1时夹紧力达到最大值;(2)当螺栓旋转处于角度1~角度2时,夹紧力基本不随角度增大而改变;(3)当螺栓旋转处于角度2~角度3时,夹紧力随角度增大而呈现递减关系;(4)当螺栓旋转≥角度3时,此时螺栓承受的抗张力超过螺栓屈服极限即螺栓断裂。
汽车总装过程中螺栓扭矩偏差的控制方法

汽车厂总装配车间负责将汽车的各个零部件 进行组装形成整车,而其中大部分零部件都依靠 螺栓进行组合,螺栓扭矩的控制效果将直接影响 到整车的安全性和性能,螺栓扭矩是总装过程质 量控制的重点。随着总装流水线由单品种大批量 向多品种小批量柔性化方向发展,如何有效控制 螺栓扭矩偏差来适应这种趋势,就需要对扭矩偏 差的原因进行分析和实际验证,进而形成一套合 理的扭矩控制方法。本文以某轻型卡车为例,探 讨总装过程中螺栓扭矩偏差的控制方法。
这些问题有: 1)半浮式驾驶后悬部位的螺栓扭矩偏差反 复较明显。 分析:驾驶室半浮式后悬,由于增加了减震弹 簧,导致其宽度增加,根据其结构特点(U 型结构, 螺栓安装孔在 U 型结构的底部),宽度增加后其与
纵梁腹面配合的安装孔位置偏靠内,空间局限,气 动扳手无法按常规方式(驱动头+套筒)对该处螺 栓进行锁紧;需配合转接杆和万向套筒对该处的 螺栓进行紧固,而接杆的形变和万向套筒的甩动 会造成其扭矩不易控制。
7)零 部 件 的 法 兰 带 齿 螺 栓 扭 矩 防 松 能 力 下降。
分析:紧固部位的法兰锁止齿凹槽被零部件 表面过厚的漆膜填满(螺栓在锁紧的过程中锁止 齿将破坏漆膜),法兰锁止齿嵌入量有限;根据螺 栓扭矩原理,螺栓与支撑面的摩擦力变小,无法达 到预期紧固效果。
3 实际生产验证
针对上述出现的螺栓扭矩偏差问题,通过实 际试验收集数据分析和实际生产验证,进行整改 后,扭矩控制效果良好。分述如下:
第1期
机电技术
35
汽车整车厂的管理制度

汽车整车厂的管理制度一、概述汽车整车厂是指从设计、研发、生产到销售一系列汽车产品的企业,其管理制度对于保证生产质量、提高效率、发展创新非常重要。
下面将从组织管理、生产管理、质量管理和安全管理等方面对汽车整车厂的管理制度进行详细介绍。
二、组织管理1. 组织结构汽车整车厂的组织结构一般包括总经理办公室、生产部门、研发部门、采购部门、销售部门、质量部门、人力资源部门等。
各部门之间应该建立明确的职责分工和协作机制,确保整个企业的运作顺畅。
2. 职责分工各部门应该根据公司的发展战略和业务需求,合理确定各自的职责范围和工作内容。
同时,要建立健全的部门间协作机制,加强信息共享和沟通,提高工作效率。
3. 岗位设置根据企业规模和业务需求,确定合理的岗位设置和人员编制。
同时,要对各岗位的职责、权限、责任进行明确规定,确保人员能够清晰地知晓自己的工作任务和责任。
4. 人才培养汽车整车厂应该重视人才培养和引进,建立健全的人才培养体系和培训机制,逐步提升员工的技术水平和综合素质,为企业的长期发展和壮大奠定人才基础。
三、生产管理1. 生产计划汽车整车厂应该根据市场需求和销售计划,合理确定生产计划和生产进度。
同时,要加强供应链管理,确保原材料、零部件的及时供应,避免产生滞销和积压库存。
2. 装配生产对于整车的装配生产过程,汽车整车厂应该建立健全的生产线和工艺流程,提高生产效率和质量水平。
同时,要加强生产现场管理,规范作业流程,确保产品质量和生产安全。
3. 设备维护汽车整车厂应该重视设备的维护和保养工作,建立设备管理台账,定期进行设备检修和保养,确保生产设备的正常运转和生产效率。
4. 质量控制汽车整车厂的生产过程中,要加强对产品质量的控制,建立健全的质量检测体系和质量管理制度,确保产品符合标准和客户需求。
四、质量管理1. 质量管理体系汽车整车厂应该建立ISO9001质量管理体系,制定相关质量管理制度和程序,加强对产品质量的全面控制。
主机厂对紧固件扭矩质量的控制方法
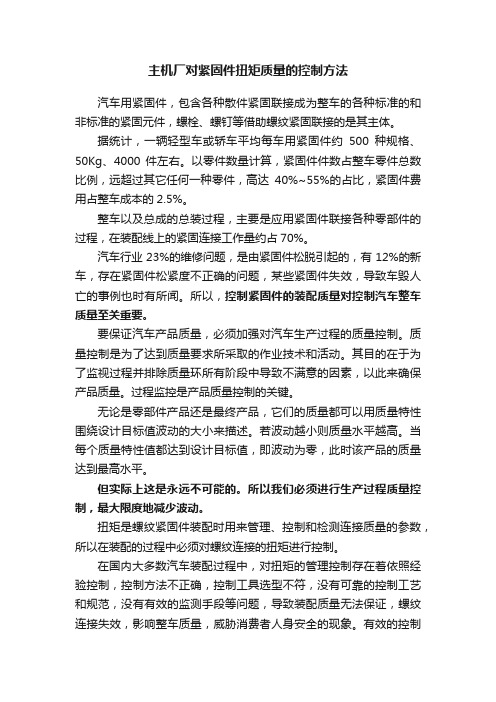
主机厂对紧固件扭矩质量的控制方法汽车用紧固件,包含各种散件紧固联接成为整车的各种标准的和非标准的紧固元件,螺栓、螺钉等借助螺纹紧固联接的是其主体。
据统计,一辆轻型车或轿车平均每车用紧固件约500种规格、50Kg、4000 件左右。
以零件数量计算,紧固件件数占整车零件总数比例,远超过其它任何一种零件,高达40%~55%的占比,紧固件费用占整车成本的2.5%。
整车以及总成的总装过程,主要是应用紧固件联接各种零部件的过程,在装配线上的紧固连接工作量约占70%。
汽车行业23%的维修问题,是由紧固件松脱引起的,有12%的新车,存在紧固件松紧度不正确的问题,某些紧固件失效,导致车毁人亡的事例也时有所闻。
所以,控制紧固件的装配质量对控制汽车整车质量至关重要。
要保证汽车产品质量,必须加强对汽车生产过程的质量控制。
质量控制是为了达到质量要求所采取的作业技术和活动。
其目的在于为了监视过程并排除质量环所有阶段中导致不满意的因素,以此来确保产品质量。
过程监控是产品质量控制的关键。
无论是零部件产品还是最终产品,它们的质量都可以用质量特性围绕设计目标值波动的大小来描述。
若波动越小则质量水平越高。
当每个质量特性值都达到设计目标值,即波动为零,此时该产品的质量达到最高水平。
但实际上这是永远不可能的。
所以我们必须进行生产过程质量控制,最大限度地减少波动。
扭矩是螺纹紧固件装配时用来管理、控制和检测连接质量的参数,所以在装配的过程中必须对螺纹连接的扭矩进行控制。
在国内大多数汽车装配过程中,对扭矩的管理控制存在着依照经验控制,控制方法不正确,控制工具选型不符,没有可靠的控制工艺和规范,没有有效的监测手段等问题,导致装配质量无法保证,螺纹连接失效,影响整车质量,威胁消费者人身安全的现象。
有效的控制方法,可靠地进行扭矩过程控制,确保螺纹紧固件的装配质量,成为各主机厂的重要工作内容。
国内外主机厂对扭矩质量控制的现状日本紧固件研究协会在1990年制定了有关螺纹紧固问题的两个标推,即:“ISB-1083螺纹紧固通则”和“ISB -1084螺纹零件紧固试验方法”。
整车生产工厂管理制度
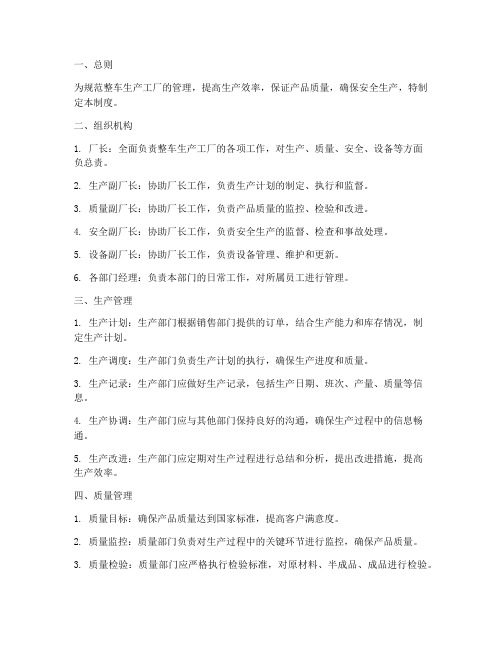
一、总则为规范整车生产工厂的管理,提高生产效率,保证产品质量,确保安全生产,特制定本制度。
二、组织机构1. 厂长:全面负责整车生产工厂的各项工作,对生产、质量、安全、设备等方面负总责。
2. 生产副厂长:协助厂长工作,负责生产计划的制定、执行和监督。
3. 质量副厂长:协助厂长工作,负责产品质量的监控、检验和改进。
4. 安全副厂长:协助厂长工作,负责安全生产的监督、检查和事故处理。
5. 设备副厂长:协助厂长工作,负责设备管理、维护和更新。
6. 各部门经理:负责本部门的日常工作,对所属员工进行管理。
三、生产管理1. 生产计划:生产部门根据销售部门提供的订单,结合生产能力和库存情况,制定生产计划。
2. 生产调度:生产部门负责生产计划的执行,确保生产进度和质量。
3. 生产记录:生产部门应做好生产记录,包括生产日期、班次、产量、质量等信息。
4. 生产协调:生产部门应与其他部门保持良好的沟通,确保生产过程中的信息畅通。
5. 生产改进:生产部门应定期对生产过程进行总结和分析,提出改进措施,提高生产效率。
四、质量管理1. 质量目标:确保产品质量达到国家标准,提高客户满意度。
2. 质量监控:质量部门负责对生产过程中的关键环节进行监控,确保产品质量。
3. 质量检验:质量部门应严格执行检验标准,对原材料、半成品、成品进行检验。
4. 质量改进:质量部门应定期对质量问题进行分析,提出改进措施,降低不良品率。
5. 客户投诉处理:质量部门应积极处理客户投诉,查明原因,采取措施,防止类似问题再次发生。
五、安全管理1. 安全目标:确保员工生命安全和财产安全,实现安全生产。
2. 安全培训:安全部门应定期对员工进行安全培训,提高员工安全意识。
3. 安全检查:安全部门应定期对生产现场、设备进行检查,确保安全设施完好。
4. 事故处理:发生安全事故时,安全部门应立即组织调查,查明原因,采取措施,防止事故再次发生。
5. 安全记录:安全部门应做好安全记录,包括事故发生时间、地点、原因、处理结果等信息。
扭力校准管理制度

扭力校准管理制度一、总则为了规范和管理扭力仪器的使用和校准工作,确保扭力仪器的准确性和稳定性,保障生产安全和产品质量,特制定本制度。
二、适用范围本制度适用于公司所有使用扭力仪器的部门和岗位,以及与扭力校准相关的所有工作。
三、校准管理机构1. 公司设立扭力校准管理机构,负责扭力仪器的校准、管理和监督工作。
2. 扭力校准管理机构的主要职责包括制定扭力校准管理制度、编制扭力校准计划、组织扭力校准工作、监督扭力仪器的使用和管理、定期评估扭力校准效果等。
四、扭力仪器管理1. 公司所有使用扭力仪器的部门和岗位必须进行扭力仪器的登记和备案。
2. 扭力仪器必须定期进行校准,并及时标识校准日期和有效期。
3. 严禁私自调整扭力仪器参数或者私自更换扭力仪器配件。
五、扭力校准计划1. 按照扭力校准管理机构的统一部署和要求,各部门和岗位制定扭力校准计划,并报扭力校准管理机构审核。
2. 根据扭力仪器的使用频率和使用环境,合理安排扭力校准的时间节点和周期。
六、扭力校准操作流程1. 扭力校准操作必须由经过专业培训并取得相应证书的人员进行,严禁无资质人员进行校准操作。
2. 扭力校准操作流程必须按照标准化的程序进行,保证校准的准确性和可靠性。
3. 扭力校准操作必须留下完整、真实的记录,包括校准日期、操作人员、校准数据、校准结果等。
七、扭力校准标准1. 扭力校准必须按照国家标准或行业标准进行,确保校准的合法性和科学性。
2. 扭力校准标准必须及时更新,跟踪最新的标准和技术要求。
八、扭力校准结果评估1. 所有扭力校准结果必须进行评估,确保校准结果符合要求。
2. 对于不符合要求的扭力仪器,必须及时处理和重新进行校准。
九、扭力校准档案管理1. 扭力校准档案必须建立和管理,包括扭力仪器基本信息、校准记录、校准结果、校准有效期等。
2. 扭力校准档案必须保存完整、真实和可查性,校准档案的查阅和调取必须有明确的管理规定和程序。
十、扭力校准监督检查1. 扭力校准管理机构有权对扭力校准工作进行监督检查,发现问题必须及时纠正。
整车装配力矩控制管理办法

x x x x x x汽车有限公司(xxxxxxx部)规程性文件文件名称:整车装配力矩控制管理办法文件编号:生效日期:版本号: A/0发文单位:(文件发行章)编制:审核:标准化:批准:规程性文件名称文件编号:整车装配力矩控制管理办法生效日期:版次:A/0 页码:1 ,共11页(文件会签记录)制定/修改内容说明新编文件发放/适用范围集团制造管理部、质量管理部、研究院、各制造公司文件会签栏会签部门会签人会签部门会签人(文件制定/修改情况记录)版次制定/修改内容摘要制定/修改人审核人批准人生效日期A/0规程性文件名称文件编号:整车装配力矩控制管理办法生效日期:版次:A/0 页码:2 ,共11页1.目的1.1 对整车装配力矩进行控制,确保联接件的质量稳定。
2. 范围2.1 适用于整车装配力矩的操作控制和质量/工艺部门对装配力矩控制的监控。
2.2 适用于集团制造管理部、质量管理部,研究院,各制造公司。
3. 术语和定义3.1 关键力矩:指零部件拧紧装配失效模式影响整车行驶安全的力矩。
在FMEA分析时,其失效严重度等级为 9-10 级。
3.2 重要力矩:指零部件拧紧装配失效模式影响整车零件或系统的功能丧失,但不影响整车行驶安全的力矩。
在 FMEA 分析时,其失效严重度等级为 5-8 级。
3.3 预紧:指采用设定力矩值小于产品设计力矩值的工具,进行拧紧装配的方法。
一般情况下,工具设定力矩值为设计力矩值的80%及以下。
3.4 紧固:指采用拧紧工具以设计力矩值为目标值的拧紧方法。
3.5 复紧:指采用产品设计力矩值设定的工具,再次对已完成紧固的螺纹副进行紧固的装配方法。
3.6 力矩检验方法(紧固法):用检测扳手对已紧固的螺纹副进一步紧固,缓慢的在扳手手柄上施力,当螺栓/螺母产生微小的转角时,读出检测扳手显示的力矩值。
3.7 动态力矩:在紧固件被紧固时测的峰值,通过力矩设定的方法赋予在装配工具上,也可用力矩测量仪器在装配过程直接测量得到。
整车装配关键力矩控制管理办法
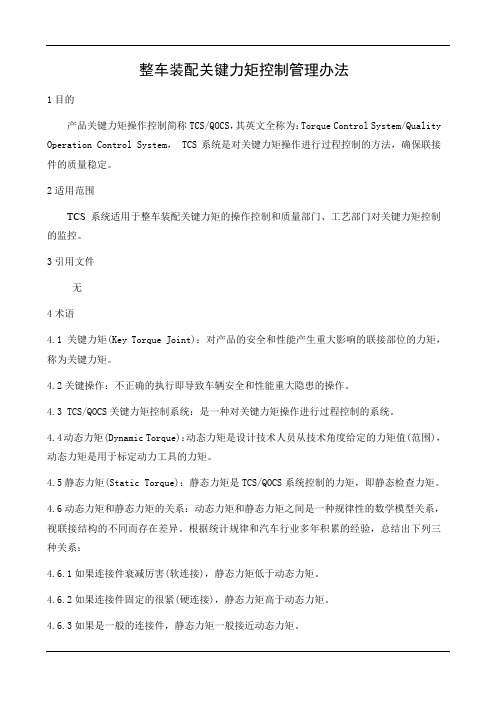
整车装配关键力矩控制管理办法1目的产品关键力矩操作控制简称TCS/QOCS,其英文全称为:Torque Control System/Quality Operation Control System, TCS系统是对关键力矩操作进行过程控制的方法,确保联接件的质量稳定。
2适用范围TCS系统适用于整车装配关键力矩的操作控制和质量部门、工艺部门对关键力矩控制的监控。
3引用文件无4术语4.1 关键力矩(Key Torque Joint):对产品的安全和性能产生重大影响的联接部位的力矩,称为关键力矩。
4.2关键操作:不正确的执行即导致车辆安全和性能重大隐患的操作。
4.3 TCS/QOCS关键力矩控制系统:是一种对关键力矩操作进行过程控制的系统。
4.4动态力矩(Dynamic Torque):动态力矩是设计技术人员从技术角度给定的力矩值(范围),动态力矩是用于标定动力工具的力矩。
4.5静态力矩(Static Torque):静态力矩是TCS/QOCS系统控制的力矩,即静态检查力矩。
4.6动态力矩和静态力矩的关系:动态力矩和静态力矩之间是一种规律性的数学模型关系,视联接结构的不同而存在差异。
根据统计规律和汽车行业多年积累的经验,总结出下列三种关系:4.6.1如果连接件衰减厉害(软连接),静态力矩低于动态力矩。
4.6.2如果连接件固定的很紧(硬连接),静态力矩高于动态力矩。
4.6.3如果是一般的连接件,静态力矩一般接近动态力矩。
5职责5.1技术中心负责在A图释放时一并释放产品关键动态力矩清单,以便工艺部门配备相应工具。
对成熟产品也可一次性提出产品关键动态力矩清单,每年年底维护一次,并下发工厂有关部门。
产品关键动态力矩清单是技术文件的一部分,其随后的变更和更改按技术文件更改的有关规定执行。
5.2制造技术部是关键力矩的归口管理部门5.2.1负责按照产品关键力矩清单,对动力工具进行系统的策划,提出动力工具配置要求。
汽车总装制造过程力矩管理

汽车总装制造过程力矩管理介绍了汽车生产过程中螺栓拧紧力矩控制的重要性及方法汽车总装制造的主要任务是将汽车各组成部分零部件组装成为整车,其中力矩问题一直被认为是汽车总装制造的核心问题,螺纹紧固力矩偏大或偏小直接关乎汽车驾驶者的行驶安全,因此建立一套有效的力矩管理体系对于保障总装装配质量尤其重要。
对于汽车来讲,力矩是影响汽车驾驶安全性能的关键因素,对快节拍的总装制造车间流水线人工螺栓拧紧作业来讲,螺栓联接力矩要受到5M1E即人、机、料、法、环、测等诸方面影响,其中任何一个环节出现异常都会导致力矩产生异常波动,而力矩非正常波动后未及时发现并返工则会给车辆售出后顾客乘坐带来难以预料的突发灾难。
因此做好总装车间力矩管理对于一个企业的可持续发展至关重要。
力矩的重要性1.螺栓联接后力的分布情况介绍了汽车生产过程中螺栓拧紧力矩控制的重要性及方法首先了解一下螺栓紧固过程中相关件的受力分布情况(见图1),从图1中可以看出螺栓紧固后,联接件与被联接件之间将形成一定的“夹紧力”,这个力是螺栓联接想要达到的目的,但事实上达到这个“夹紧力”的同时,联接件与被联接件还要承受一对横向的“剪切力”,而联接后螺栓受到来自联接件与被联接件施加的“张力”,根据牛顿第三定律得知,螺栓本身也会产生一个“抗张力”以保持受力平衡。
2.联接件与被联接件受力特性由上述分析可知,螺栓联接后想要的是使联接件与被联接件之间达到设计的夹紧力要求,夹紧力的大小就决定了联接的松紧。
通过图1我们可以看出,联接件与被联接件之间的夹紧力大小与螺栓旋转圈数有关,事实上它们之间存在着特定的线性关系(见图2)。
从图2中看出,夹紧力与螺栓旋转角度呈现的是一种分段型的线性关系,以联接件与被联接件开始接触时螺栓角度为初始角度0°、旋转1周角度递增360°计算,夹紧力大小将呈现以下三种状况:(1)当螺栓旋转处于0~角度1时,夹紧力与螺栓角度呈现单调递增关系,螺栓在角度1时夹紧力达到最大值;(2)当螺栓旋转处于角度1~角度2时,夹紧力基本不随角度增大而改变;介绍了汽车生产过程中螺栓拧紧力矩控制的重要性及方法(3)当螺栓旋转处于角度2~角度3时,夹紧力随角度增大而呈现递减关系;(4)当螺栓旋转≥角度3时,此时螺栓承受的抗张力超过螺栓屈服极限即螺栓断裂。
扭矩控制方法
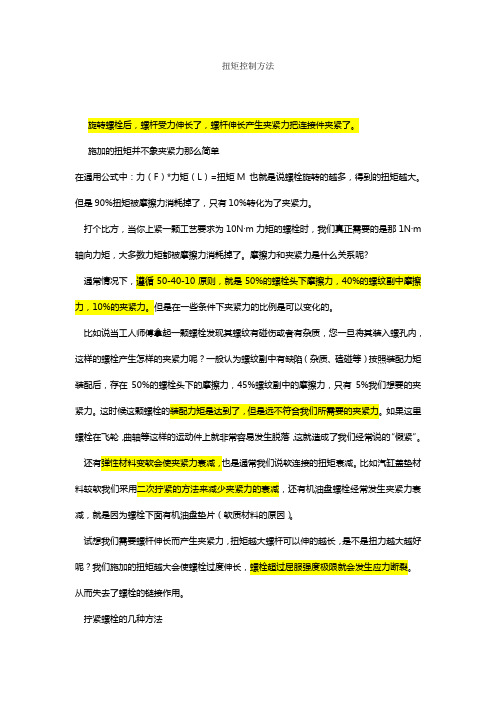
扭矩控制方法旋转螺栓后,螺杆受力伸长了,螺杆伸长产生夹紧力把连接件夹紧了。
施加的扭矩并不象夹紧力那么简单在通用公式中:力(F)*力矩(L)=扭矩M 也就是说螺栓旋转的越多,得到的扭矩越大。
但是90%扭矩被摩擦力消耗掉了,只有10%转化为了夹紧力。
打个比方,当你上紧一颗工艺要求为10N·m力矩的螺栓时,我们真正需要的是那1N·m 轴向力矩,大多数力矩都被摩擦力消耗掉了。
摩擦力和夹紧力是什么关系呢?通常情况下,遵循50-40-10原则,就是50%的螺栓头下摩擦力,40%的螺纹副中摩擦力,10%的夹紧力。
但是在一些条件下夹紧力的比例是可以变化的。
比如说当工人师傅拿起一颗螺栓发现其螺纹有碰伤或者有杂质,您一旦将其装入螺孔内,这样的螺栓产生怎样的夹紧力呢?一般认为螺纹副中有缺陷(杂质、磕碰等)按照装配力矩装配后,存在50%的螺栓头下的摩擦力,45%螺纹副中的摩擦力,只有5%我们想要的夹紧力。
这时候这颗螺栓的装配力矩是达到了,但是远不符合我们所需要的夹紧力。
如果这里螺栓在飞轮,曲轴等这样的运动件上就非常容易发生脱落,这就造成了我们经常说的“假紧”。
还有弹性材料变软会使夹紧力衰减,也是通常我们说软连接的扭矩衰减。
比如汽缸盖垫材料较软我们采用二次拧紧的方法来减少夹紧力的衰减,还有机油盘螺栓经常发生夹紧力衰减,就是因为螺栓下面有机油盘垫片(软质材料的原因)。
试想我们需要螺杆伸长而产生夹紧力,扭矩越大螺杆可以伸的越长,是不是扭力越大越好呢?我们施加的扭矩越大会使螺栓过度伸长,螺栓超过屈服强度极限就会发生应力断裂。
从而失去了螺栓的链接作用。
拧紧螺栓的几种方法1、扭矩控制法(T)扭矩控制法是最初始也是最简单的控制法,它是基于螺纹连接时,轴向夹紧力F拧紧时与拧紧扭矩T成正比关系,可用一个公式T=K·F来表示,这个K则是扭矩系数。
当一个螺钉设计出来时候他的轴向夹紧力F就是可知的,拧紧扭矩T通过工艺设定我们的拧紧扭矩也被工艺部门规范下来。
扭力控制原理

扭力控制原理扭力控制原理是一种用于控制和调节机械系统中扭矩的方法。
它广泛应用于许多工业和机械领域,例如汽车工业、飞机制造、机床加工等。
扭力控制原理的基本思想是通过调节输入到系统中的扭矩大小来实现对系统输出的控制。
在一个典型的扭力控制系统中,通常包括一个传感器用于测量输出的扭矩,一个控制器用于计算所需的输入扭矩,并且一个执行器用于调节输入扭矩。
控制器通常根据所需的系统性能要求来计算输入扭矩。
例如,在汽车上,扭力控制可以用来保持车辆在曲线行驶时的稳定性,通过调整引擎输出的扭矩来控制车辆在弯道中的动态特性。
在飞机上,扭力控制用于控制飞机发动机的推力,以保持飞机在不同飞行阶段的稳定性和操作性。
执行器的作用是根据控制器的指令调节输入扭矩。
在某些应用中,执行器可能是一个简单的机械装置,例如手动刹车踏板。
在其他应用中,执行器可能是一个复杂的系统,例如液压或电动驱动的装置,通过改变传动系统的状态来调节输入扭矩。
整个扭力控制系统的核心是传感器,用于测量系统的输出扭矩。
传感器可以采用不同的工作原理,例如应变计、压力传感器或磁性传感器。
传感器将输出扭矩的测量值传输给控制器,从而实现扭力控制系统的闭环控制。
在实际应用中,扭力控制原理可以通过不同的控制算法和方法来实现。
常见的控制方法包括比例控制、积分控制和微分控制等。
通过合理设计和优化,扭力控制原理可以实现准确的扭矩调节和精确的系统控制。
总的来说,扭力控制原理是一种重要的控制方法,通过调节输入扭矩来实现对机械系统的控制。
它在工业和机械领域中具有广泛的应用,并且通过不同的控制算法和方法可以实现准确和精确的控制效果。
- 1、下载文档前请自行甄别文档内容的完整性,平台不提供额外的编辑、内容补充、找答案等附加服务。
- 2、"仅部分预览"的文档,不可在线预览部分如存在完整性等问题,可反馈申请退款(可完整预览的文档不适用该条件!)。
- 3、如文档侵犯您的权益,请联系客服反馈,我们会尽快为您处理(人工客服工作时间:9:00-18:30)。
制管理清单要经过 5个环 节 ,多道传递过程会产生较大的误传
递 问题 。
后模拟正常生产验证 ,以便及 时发 现扭力值设定 和扭力范 围等
问题。
要解决上述 问题 ,需要对流转过程进行控制。
( 1 )缩减质量控 制管理清单 的形成环节 。
( 2 )任何 清单变化时 ,需备注更改 内容和更 改时间。
定爨 嚷橼撩钢
/
P F M E A
计 划
/
.
麓豢 率溺和 E j 睃 顶强时瓣受零疆鬻
嚣囊 孳
爨
2 . 质熏 科鞭 踪激爱 敬据
l
S O S
l
l
鏊率 f
.
.
一一 爰 诱 I i 一一l
一 一 一 … … 一
鬻
煮幼
数 据 开 始 验 证 和 扭 力 进 行 常 规 工 具 控 制
致性 或稳定性 方面基本无实践经验 。在样车制造环节 ,提前
验证扭力设定值 和扭力范 围,进行数据分析 ,并对 出现的 问题 制定相应措施 ,将措施添加到相应工艺文件 中。
定 ,形成新 的扭力管理流程图 ,详 情见 表 2 。
3 . 3 常规 量产 开始 阶段 ,扭 力 合格 率达 不到 9 9 %
3 . 2 P F ME A和控 制计 划对 扭 力提 升作 用 弱
P F M E A和控 制计划对扭 力管理方 式 的分 析基本是 基于 已 经量产 的整车项 目或理论可行性 ,造成在新增专用件扭力保持
一
( 3 )任何环节到下游 的传递需要发布正式文件 ,并 由下游
部门签字接 收。 ( 4 )负责工程师需及时查看工作上游清单 。 经过对 整车产 品项 目扭力管 理流程 的分析 和措施 的制
的工艺验证 ,此时 的重点工作是工具达到既定要求和员工熟练 度达到 4 / 4 。此外 ,还需要关注 借用零件 的扭 力值和扭力范 围
表 2 变 更 后 的 扭 力 管 理 流 程 图
缀 克发布藏稷
顼 猫输段
关键 内 容
l
l
P S  ̄T 2 M t
S W O( 禽 嚼 壤)
[ 责任编辑 :蒙k e j i y u f a z h a n
3 . 4 扭 力在 传递 过程 中一致性 的保 证
扭 力值 的传 递 自产 品数 据发布 到落实 到车间工 作作业 书
中,需要经过 7个环节 ,同时数据发布到落实到质量部质量控
制定 出新增专用件扭力清单 。依据新增专用件扭 力清单 ,试制
车间集 中资源购买或需求车间提供常规生产 所使 用的工具 ,然
l
l 数据
发耀
/
£ P k 和K P e 清肇
/
—
l ☆ c 。 ¥ 港 照 l
榉 车制造
. 数攘髓予黪 瀵遂 程中, 来蒋 赣效 验涟
2 . 翻匆嫒 瓣攒针 缀竽 糖濑
/
最一 》
:
嘲 C c
/
3 . 对 于 期 增 专 翔 僻 扭 力 点 俄 粥 援 力 缀 手 或
企业科技与发展 般会在试制车 间进行 。试制车 间的操作人员和工具设备与生产
在工作条件和工作环境发生变化后是否发生变化 。
线差异较大 ,并且制造 的重点在于零部件的试装和匹配 ,势必
对扭力 的控制不够严格和标准 。 为解决 上述 问题 ,需要制造工艺 工程师根 据 MP P和 K C C
扭力合格率 的提升需要合适的工具和熟练的员工操作 ,在
样车制造 阶段完成对新增专用件的扭力设定值和扭力范围的验 证后 ,需要在非卖车项 目造车 阶段进行批量 、连续和全部扭力
3 结语
通过对整车产品项 目扭力管理流程进行充分 的分析 ,针对 具体 问题制定相应措施 ,在工 厂内实现扭力保持一致性和稳定 性 ,并最终保证车辆的安全性 和功 能性 ,以及零部件使用寿命 达到要求 。