第九章 热锻工艺概述
热模锻工艺流程

热模锻工艺流程我呀,今天就想和大家唠唠热模锻这个超酷的工艺流程。
这热模锻啊,就像是一场金属的华丽变身秀,那可老精彩了。
咱先得从原材料说起。
这就好比做饭,你得先有食材一样。
热模锻的原材料大多是各种金属坯料。
这些坯料可不能随随便便就拿来用,得先检查检查呢。
质检员老王那可是个仔细人儿,他拿着各种工具,这儿量量,那儿看看,眼睛瞪得像铜铃似的。
要是这坯料有啥缺陷,老王就会大喊:“嘿,这可不行,这坯料不合格,就像那病恹恹的小鸡,可经不住后面的折腾。
”合格的坯料呢,就要开始加热了。
这加热就像是给金属坯料洗个热水澡,让它浑身暖洋洋的,变得柔软好塑形。
加热炉就像一个大蒸笼,坯料放进去,温度蹭蹭往上升。
操作加热炉的小李可不敢马虎,眼睛时刻盯着温度表。
他常说:“这温度要是控制不好,就像炒菜盐放多放少一样,整个热模锻就全毁了。
”要是温度低了,金属硬邦邦的,就像个倔脾气的老头,根本不愿意变形;温度高了呢,金属可能就像融化的冰淇淋一样,变得太软,失去了应有的强度。
等坯料加热到合适的温度,就该进入模具进行锻造了。
这模具就像是金属的塑形师,决定了最后成品的模样。
锻造工人小赵那肌肉可是相当发达,他熟练地把热乎乎的坯料放到模具里。
小赵说:“这时候就像在捏泥巴,不过这泥巴可烫得很,而且得按照严格的形状来捏。
”压力机一压下来,那可是千钧之力,“轰”的一声,坯料就开始按照模具的形状发生改变了。
这过程就像把一个任性的孩子教育成守规矩的小大人一样,压力之下,坯料乖乖听话,从原来的形状变成了模具设定的形状。
在锻造的过程中,还得注意一些细节呢。
比如说润滑,这就好比给模具和坯料之间涂一层润滑油,让它们之间的摩擦小一点,就像滑冰的时候给冰鞋擦油一样。
负责润滑工作的小张可认真了,他说:“要是不润滑好,那模具和坯料就会互相‘掐架’,磨损得特别快,这可不行。
”锻造完成后,可还没结束呢。
这刚锻造出来的工件还带着一身的热乎劲儿,而且表面可能还不那么光滑平整。
锻压技术和热加工工艺
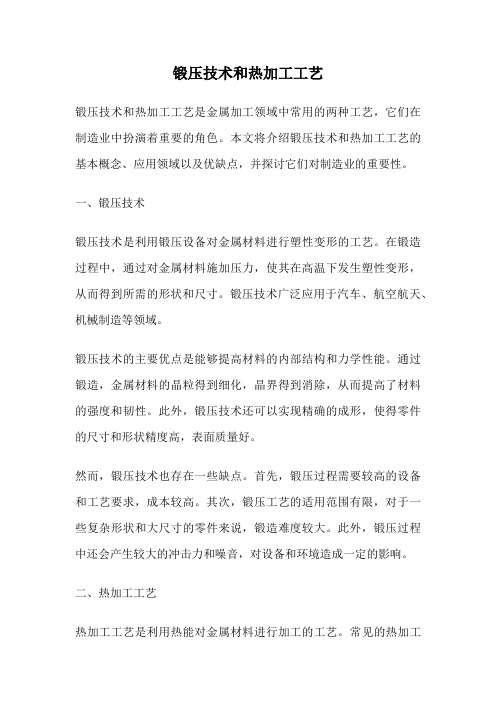
锻压技术和热加工工艺锻压技术和热加工工艺是金属加工领域中常用的两种工艺,它们在制造业中扮演着重要的角色。
本文将介绍锻压技术和热加工工艺的基本概念、应用领域以及优缺点,并探讨它们对制造业的重要性。
一、锻压技术锻压技术是利用锻压设备对金属材料进行塑性变形的工艺。
在锻造过程中,通过对金属材料施加压力,使其在高温下发生塑性变形,从而得到所需的形状和尺寸。
锻压技术广泛应用于汽车、航空航天、机械制造等领域。
锻压技术的主要优点是能够提高材料的内部结构和力学性能。
通过锻造,金属材料的晶粒得到细化,晶界得到消除,从而提高了材料的强度和韧性。
此外,锻压技术还可以实现精确的成形,使得零件的尺寸和形状精度高,表面质量好。
然而,锻压技术也存在一些缺点。
首先,锻压过程需要较高的设备和工艺要求,成本较高。
其次,锻压工艺的适用范围有限,对于一些复杂形状和大尺寸的零件来说,锻造难度较大。
此外,锻压过程中还会产生较大的冲击力和噪音,对设备和环境造成一定的影响。
二、热加工工艺热加工工艺是利用热能对金属材料进行加工的工艺。
常见的热加工工艺包括热轧、热挤压、热拉伸等。
热加工工艺主要适用于金属材料的塑性变形和形状修整。
热加工工艺的主要优点是能够提高材料的塑性和变形能力。
在高温下,金属材料的塑性增加,容易发生塑性变形,从而实现较大的形状变化。
此外,热加工还可以改善材料的内部结构和力学性能,提高材料的强度和韧性。
然而,热加工工艺也存在一些缺点。
首先,热加工过程需要大量的能源消耗,对环境造成一定的影响。
其次,热加工对设备和工艺要求较高,需要控制好加热温度和加工速度,以避免产生缺陷和变形。
此外,热加工过程中还会产生较大的热应力和残余应力,对材料的性能和寿命产生影响。
三、锻压技术和热加工工艺的应用锻压技术和热加工工艺在制造业中有着广泛的应用。
锻压技术主要应用于汽车、航空航天、机械制造等领域,用于生产发动机零部件、车轮、轴承等关键零件。
热加工工艺主要应用于钢铁、有色金属等行业,用于生产钢材、铝材等金属材料。
锻造的工艺过程

锻造的工艺过程简介锻造是一种常见的金属加工方法,通过将金属材料加热至一定温度后施加压力,使其发生塑性变形,以改变其形状和内部组织结构。
锻造广泛应用于航空航天、汽车、能源、机械制造等行业,是制造业中不可或缺的一部分。
本文将详细介绍锻造工艺过程。
热锻工艺过程加热在锻造过程中,首先需要将金属材料加热至一定温度,以提高其塑性和可锻性。
加热温度取决于金属材料的种类和锻件的形状复杂程度,一般可分为低温、中温和高温锻造。
加热可以使用电阻加热炉、气体加热炉等设备进行。
锻造1.预制坯料在加热到适当温度后,需要对金属材料进行预制坯料的加工,即将原始材料切割成适合锻造的形状和尺寸。
预制坯料的形状和尺寸要符合最终锻件的要求,以便于后续的锻造操作。
2.模具设计和制造在锻造之前,需要根据最终产品的形状和尺寸设计和制造相应的模具。
模具是锻造操作的关键,可以确定最终产品的形状和精度。
模具制造一般采用机械加工和热处理等工艺,确保模具具有足够的强度和耐磨性。
3.锻造操作锻造操作是将加热好的金属材料放入模具中,施加适当的压力进行变形的过程。
锻造过程中,压力可以通过液压机、锤击或压力机等工艺设备施加,以使金属材料发生塑性变形。
同时,根据需要进行多次锻造,以逐步改变金属材料的形状和组织结构。
4.热处理锻造后的金属材料通常需要进行热处理,以改善其力学性能和组织结构。
热处理可以包括退火、正火、淬火等工艺,通过控制加热和冷却过程,使金属材料获得理想的硬度和强度。
5.后续加工经过锻造和热处理后,锻件可能需要进行进一步的加工,包括切割、车削、铣削、钻孔等。
这些加工操作将锻件加工成最终产品,并满足其形状和精度要求。
冷锻工艺过程材料准备冷锻过程中使用的材料通常是冷硬性较高的金属,例如铝合金、不锈钢等。
在冷锻前,需要对材料进行预处理,如去除氧化层、清洁表面等,以保证冷锻过程的质量。
设备和工艺参数选择冷锻可以使用液压机、螺旋式冷锻机等设备进行。
在选择设备时,需要考虑材料的硬度、形状复杂度和生产效率等因素。
锻造工艺的概念和分类

锻造工艺的概念和分类
锻造工艺是一种通过施加力量和热量将金属材料变形成所需形状的制造方法。
锻造工艺可以分为以下几种分类:
1. 锻造温度分类:根据输入能量的形式,可以将锻造工艺分为冷锻、热锻和半热锻三类。
冷锻是在室温下进行的锻造工艺;热锻是在高温下进行的锻造工艺,其温度通常在再结晶温度以上;半热锻是介于冷锻和热锻之间的温度下进行的锻造工艺。
2. 锻造设备分类:根据施加力量的方式和设备的类型,可以将锻造工艺分为手工锻造、机械压力锻造、液压锻造和气动锻造等几类。
3. 锻造方法分类:根据金属材料在锻造过程中的变形方式,可以将锻造工艺分为自由锻造、模锻、粉末冶金锻造和特殊锻造等几类。
自由锻造是指将金属材料置于锻模之间施加锻击力来实现变形的锻造方法;模锻是在金属材料周围设置一定形状的模具,通过挤压和压缩变形金属来实现锻造的工艺;粉末冶金锻造是通过将金属粉末和粘结剂混合后进行成型和锻造的工艺;特殊锻造是指一些特殊的锻造方法,如旋压锻、横剪锻、搓锻等。
4. 锻造产品分类:根据产品的形状和用途,可以将锻造工艺分为轴类锻件、盘类锻件、复杂形状锻件和板类锻件等几类。
轴类锻件主要是指长度大于直径的圆柱体形锻件,如轴、销、凸轮等;盘类锻件主要是指直径大于长度的扁圆形锻件,如齿轮、法兰等;复杂形状锻件主要是指形状复杂、截面变化较大的锻
件;板类锻件主要是指长宽比大于3的薄板形锻件。
以上是常见的锻造工艺的分类,根据具体情况和需求,还可以进一步细分和分类。
锻造工艺概述
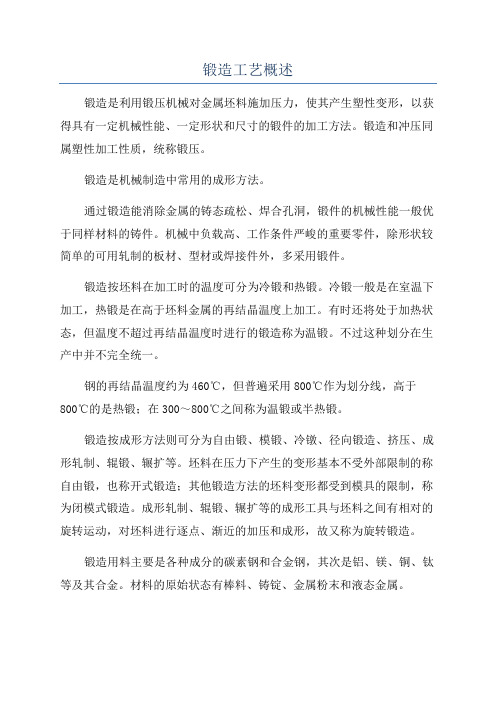
锻造工艺概述锻造是利用锻压机械对金属坯料施加压力,使其产生塑性变形,以获得具有一定机械性能、一定形状和尺寸的锻件的加工方法。
锻造和冲压同属塑性加工性质,统称锻压。
锻造是机械制造中常用的成形方法。
通过锻造能消除金属的铸态疏松、焊合孔洞,锻件的机械性能一般优于同样材料的铸件。
机械中负载高、工作条件严峻的重要零件,除形状较简单的可用轧制的板材、型材或焊接件外,多采用锻件。
锻造按坯料在加工时的温度可分为冷锻和热锻。
冷锻一般是在室温下加工,热锻是在高于坯料金属的再结晶温度上加工。
有时还将处于加热状态,但温度不超过再结晶温度时进行的锻造称为温锻。
不过这种划分在生产中并不完全统一。
钢的再结晶温度约为460℃,但普遍采用800℃作为划分线,高于800℃的是热锻;在300~800℃之间称为温锻或半热锻。
锻造按成形方法则可分为自由锻、模锻、冷镦、径向锻造、挤压、成形轧制、辊锻、辗扩等。
坯料在压力下产生的变形基本不受外部限制的称自由锻,也称开式锻造;其他锻造方法的坯料变形都受到模具的限制,称为闭模式锻造。
成形轧制、辊锻、辗扩等的成形工具与坯料之间有相对的旋转运动,对坯料进行逐点、渐近的加压和成形,故又称为旋转锻造。
锻造用料主要是各种成分的碳素钢和合金钢,其次是铝、镁、铜、钛等及其合金。
材料的原始状态有棒料、铸锭、金属粉末和液态金属。
一般的中小型锻件都用圆形或方形棒料作为坯料。
棒料的晶粒组织和机械性能均匀、良好,形状和尺寸准确,表面质量好,便于组织批量生产。
只要合理控制加热温度和变形条件,不需要大的锻造变形就能锻出性能优良的锻件。
铸锭仅用于大型锻件。
铸锭是铸态组织,有较大的柱状晶和疏松的中心。
因此必须通过大的塑性变形,将柱状晶破碎为细晶粒,将疏松压实,才能获得优良的金属组织和机械性能。
经压制和烧结成的粉末冶金预制坯,在热态下经无飞边模锻可制成粉末锻件。
锻件粉末接近于一般模锻件的密度,具有良好的机械性能,并且精度高,可减少后续的切削加工。
热锻温锻成型工艺
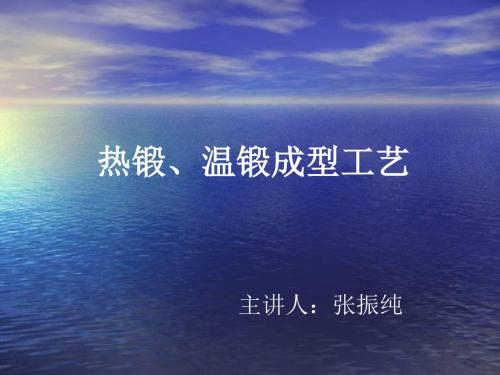
两个工序时,顶镦模结构
与图36-47所示结构基本
相同。
C.冲床上热顶镦螺栓模具结构实 例:图36-48所示为 M12×1.25×118-10.9汽车用六角
头法兰面高强螺栓热顶镦具工 作部分的结构简图。坯料为40Gr 钢冷拔料,坯料外径为ф12.7,下料 长度偏差≤0.5mm。在2500kN冲 床上进行闭式顶镦。采用中频感 应炉进行端部局部加热,
5.2 两种常用设备上热顶镦螺栓、螺钉的工艺流程与优缺点对比
在螺旋压力机或冲床上热顶镦螺栓、螺钉的工艺流程基本相同,一般为: 下料→加热→(聚料)→自由顶镦→锻后热处理→清理→(去毛刺)→检 验。
其中,聚料工序(步)只用于5.1条所列举的极少数特殊种类的螺栓或螺钉。 当聚料安排在另外一台设备上进行时,即聚料工序;当聚料安排在同一台设 备上进行时(在同一台双点单动压力机上设置两套顶镦模或在同一台设备 上设置两个可更换工位的冲头),即聚料工步。
2 适用于紧固件成型的热模锻工艺类型、特点及成型原理
热模锻可以根据塑性变形方式与所用成型设备的不同分为多种
工艺类型。其中,适用于紧固件成型的工艺类型、特点及其简要成型
原理见表36-6。
3.异形紧固件开式热模锻(简称开式模锻)
3.1开式热模锻的工艺流程、设备与工模具
以吊环螺钉开式模锻的工艺流程为例,一般为:下料→加热→
锻件的工艺

锻件的工艺锻件是一种常见的金属加工工艺。
它通过在高温和高压环境下对金属材料进行塑性变形,从而使材料变形成所需形状和尺寸的零件。
锻件工艺具有诸多优点,如提高材料的力学性能、改善材料微观结构、提高零件的密实度和尺寸精度等。
下面我将详细介绍锻件的工艺过程和原理。
锻件的工艺过程主要包括预制备、加热、锻造、冷却和后处理等环节。
首先是预制备阶段,需要选取适当的材料,并制备成合适的锻坯。
材料选择通常考虑材料的塑性、韧性和可焊性等因素。
锻坯的制备可以通过热轧、锯切、剪切、锯片和钳子等工具进行。
第二个阶段是加热,将锻坯加热到其材料的变形温度以上,使其达到可塑性的状态。
加热方法通常有火焰加热、电加热和感应加热等。
加热后的锻坯需要保持一定的温度和时间,以确保其达到均匀的温度,并排除内部和表层的应力。
接下来是锻造阶段,将加热后的锻坯置于锻模之间,通过压力使其变形成所需形状。
锻造分为冷锻和热锻两种方式。
冷锻是在室温下进行的,适用于有些特殊材料或形状复杂的锻件。
热锻是在材料的变形温度以上进行的,可以提高锻件的塑性和变形能力。
锻造时需要根据锻件的形状和材料的性质选择合适的工艺参数,如锻模的设计、压力大小和锻造次数等。
锻造后需要进行冷却处理,以使锻件在加工过程中的组织结构稳定下来。
冷却的方式可以有空冷、水冷、盐浴淬火和油浸等。
冷却速率对于锻件的组织结构和性能有很大影响,因此需要根据具体材料和要求确定适当的冷却方式。
最后是后处理,包括退火、淬火、表面处理和精加工等。
退火可以消除锻件变形过程中的应力,改善其组织结构和性能。
淬火是将锻件加热至临界温度以上,然后迅速冷却,以获得较高的硬度和强度。
表面处理可以改善锻件的耐腐蚀性、增加其表面光洁度。
精加工包括车、铣、刨、磨等工序,用于修整锻件的尺寸和形状。
总之,锻件是一种重要的金属加工工艺,可以生产出具有高强度、高耐磨性和良好表面质量的零件。
锻件工艺的过程需要经过预制备、加热、锻造、冷却和后处理等阶段,每个环节都对于锻件的质量和性能至关重要。
热模锻工艺介绍 180813
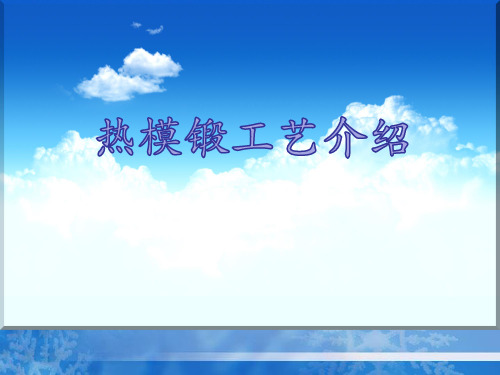
1)模锻锤: G=(3.5~6.3)KF(公斤) 2)热模锻压力机 P=(6.3~7.4)F(吨) 圆形锻件:P=8(1-0.001D)(1.1+20/D)2 FБbt 非圆形:P=8(1-0.001D)(1.1+20/D)2 (1+0.1 )FБbt 3)平锻机 P=5(1-0.001D)(D+10)2Бbt 4)螺旋压力机 P=KБbtF
热模锻压力机 (曲柄压力机)
和同样能力的模锻锤相比, 热模锻压力机的初次投资 大,但维护费用低,动力 消耗小。
和摩擦压力机模锻相比, 生产率较高,便于自动化。
热模锻压力机结构复杂, 制造条件要求高。
螺旋压力机种类:
摩擦螺旋压力机 电动螺旋压力机 离合器螺旋压力机 液压传动螺旋压力机
1、摩擦压力机靠飞轮积蓄 的能量工作,原则上可多次打击 干大活。实际有效打击次数不超 过3次。
键块分别紧固在锤头和下模座
的燕尾槽中。
•
燕尾使模块固定在锤头
(或砧座)上,使燕尾底面与
锤头(或砧座)底面紧密贴合。
•
楔铁使模块在左右方向定
位。键块使模块在前后方向定
位。
热模锻压力机与模锻锤相比,其 工作特性为: (1)静压成形,无震动和噪音; (2)机架和曲柄连杆机构的刚性 大,工作时弹性变形小; (3)滑块行程一定,每一模锻工 步只要一次行程完成; (4)导向精度和承受偏载的能力 强; (5)有上下顶件装置,便于锻件 脱模。
部分汽车件产品
转向系统 Steering System
制动系统 Braking System
传动系统 Drive System
➢ 转向系统 Components of Steering System
锻造的工艺类别 -回复

锻造的工艺类别-回复关于锻造的工艺类别锻造是一种利用金属材料进行塑性变形的加工工艺,广泛应用于航空航天、汽车制造、机械制造等众多领域。
在锻造过程中,金属材料通过施加力量使其发生塑性变形,从而得到所需的形状和性能。
根据锻造的不同方式和应用需求,可以将其分为以下几个工艺类别。
1. 锻造分类的基本原则针对不同的应用需求,锻造工艺可以根据工作温度、加工方式、材料形态等因素进行分类。
根据工作温度,锻造可以分为冷锻、热锻和半热锻。
根据加工方式,分为自由锻造、模锻和挤压锻造。
根据材料形态,分为块锻和片锻。
2. 冷锻冷锻是指在室温下进行的锻造工艺。
冷锻适用于一些低碳钢、合金钢等材料,常用于大批量生产零件,具有高效、成本低的特点。
冷锻的主要优点是能够保持金属材料的机械性能,但对于一些高碳钢和有色金属来说,冷锻会导致良好的塑性变形困难。
热锻是指在高温下进行的锻造工艺,通常应用于高碳钢、合金钢和不锈钢等材料。
热锻能够降低金属的形变阻力,提高金属的塑性变形能力,使其更容易塑性变形,从而获得更好的工艺性能。
热锻的工艺温度通常在材料的非再结晶温度至再结晶温度之间。
热锻不仅能够得到复杂形状的零件,还能够提高材料的机械性能和耐热性。
4. 半热锻半热锻是指在金属材料的工作温度接近再结晶温度时进行的锻造工艺。
半热锻结合了冷锻和热锻的优点,能够在保持较高塑性的同时降低锻造过程中的形变阻力。
这种工艺适用于很多钢材、高温合金和有色金属的锻造,可以得到更好的成形精度和机械性能。
5. 自由锻造自由锻造也称为自由锤锻造,是锻造中最常见的一种工艺。
在自由锻造中,金属材料被放置在将要锻造的位置上,然后用锤头或锻压机施加冲击力或压力进行塑性变形。
自由锻造适用于锻造不规则形状的零件,可以得到良好的成形效果和机械性能。
模锻是利用模具将金属材料压制成所需形状的锻造工艺。
模锻适用于精密锻造,能够获得更高的形状精度和尺寸一致性。
模锻通常需要使用专门设计的模具和模锻设备,具有较高的成本。
热锻工艺概述

四、我国锻造生产的发展概况及今后发展的方向和任务
我国的锻造生产起源较早,但是发展缓慢。上世纪50年代后有 了迅速发展:
1、在工艺方面:由手工锻造发展到了胎模锻及模锻,还采用了 高效率、少无切削的特种锻造,如精密模锻、锟锻和挤压等, 基本上掌握了合金钢和大型锻件的各种锻造技术。 2、在设备方面:
第二节 热锻原材料及下料方法
热锻原材料:钢锭(大、中型自由锻体)、金属棒料(其余)
常用的下料方法:
1、锯切:园盘锯、弓型锯、高速带锯
2、剪切:在剪床上或在冲床的剪切模里下料,生产效率高, 切口没有材料损耗,端部质量较差。
3、折断下料:先在材料上锯切或气割一个口子,通过压力机在预切口折 断。生产率高、设备简单、没有材料损耗、端面质量高。
第三节 锻前加热的目的、方法及钢在加热中的常见缺陷
一、目的:提高金属塑性、降低变形抗力、使之易于流动成形并获 得良好的锻后组织。
二、加热方法:
1、火焰加热:利用燃料(煤、焦炭、重油、柴油和煤气)在火 焰加热炉内燃烧产生含有大量热能的高温气体(火焰),通过对流、 辐射把热能传给毛坯表面,再由表面向中心热传导而使金属毛坯加 热。
第二篇 热锻工艺与模锻设计 第九章 热锻工艺概述
第一节 热锻工艺特点
一、什么是锻造?
锻造是利用锻压设备,通过工具或模具使金属毛坯产生 塑性变形,从而获得具有一定形状,尺寸和内部组织的工件 的一种压力加工方法。
锻造生产是机械制造工业中提供毛坯的主要途径之一。 它不但能获得一定的金属零件的形状,而且能改善金属的内 部组织,提高金属的力学性能和物理性能。
① 煤炉得到了改造:高效薄壁旋转加热炉、敞焰无氧化加 热炉、煤气、燃油加热炉、电加热炉已广泛采用感应,电加热(中 频、工频)在自动化锻压生产线上得到应用。
锻000冷锻第9章__冷锻工艺概述及其基本工序
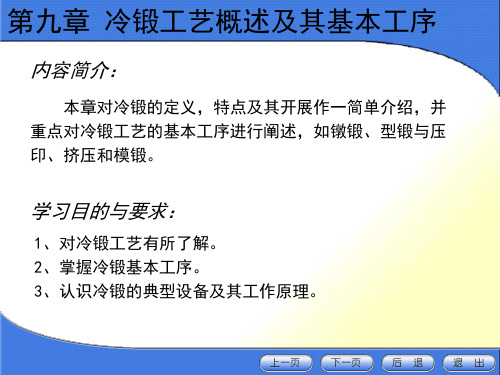
第九章 冷锻工艺概述及其基本工序
第二节 冷锻的特点
冷锻成形的特殊要求:
由于变形抗力大,故要求设备吨位较大; 对模具材料要求高,模具制造复杂; 对所加工的原材料要求高; 所有毛坯往往要进行软化退火和外表磷皂化等润滑处理。
第九章 冷锻工艺概述及其基本工序
冷挤压的毛坯进行外表处理可获得以下效果:降低毛坯
与模具间的外摩擦阻力;防止毛坯外表与模具直接摩擦而引 起的粘结现象;提高挤压件的外表质量,提高模具的寿命; 减低挤压时的变形力及变形功的消耗。
第九章 冷锻工艺概述及其基本工序
第七节 冷锻力确实定
一、压力行程曲线
第一阶段〔镦粗与充满阶段〕 是材料充满凹模型腔的过程。
第九章 冷锻工艺概述及其基本工序
第六节 冷锻毛坯的软化与外表处理
1.毛坯的软化
在冷锻之前及工序之间,大都需对毛坯或半成品进行软 化热处理,其目的是减小材料的硬度和强度,提高塑性,得 到良好的金相组织,以利于冷锻变形的进行。
2.坯料的外表处理与润滑
润滑对冷锻是非常重要的。冷锻时摩擦不仅影响到金属
的变形及挤压件的质量,而且也直接影响到单位挤压力的大 小、模具的寿命。所以要采用良好且可靠的润滑方法。
第三节 冷锻的开展
pp361自学
第九章 冷锻工艺概述及其基本工序
第四节 冷锻工艺的基本工序
一、镦锻
定义:冷镦锻是利用冷锻设备通过冷锻模具对金属坯料施加 轴向压力,使其产生轴向压缩横向增粗的冷锻成形方法。
镦锻的特点是坯料的横截面积增大。
根据坯料变形部位的不同以及模具工作局部形状的不同, 镦锻可以分为镦粗〔整体镦锻〕、顶镦〔镦头〕、中间镦粗 〔见图16-1〕 螺母、螺钉、铆钉及双头螺栓类零件,就是分别经过镦粗、 镦头及中间镦粗而成形出来〔录像〕
移烫锻扦醴 -回复

移烫锻扦醴-回复移动烫锻至于专业知识,无法为您提供支持。
本文将为您介绍烫锻的基本定义、过程、应用和注意事项。
烫锻,又称烫钢,是通过温度控制和压力施加,将金属材料加热至一定温度后进行成形和改性的一种热加工工艺。
这种工艺能够增加金属的强度、硬度和耐磨性,改善材料的性能,同时能够改善金属的焊接性和切削性能。
烫锻的基本过程包括加热、塑性变形和冷却三个阶段。
首先,需要将工件加热至一定温度,使其达到适合进行塑性变形的温度范围。
该温度取决于金属的种类和要达到的要求。
然后,在达到适宜的温度后,对工件施加压力,使其发生塑性变形。
在这个过程中,金属的晶粒会发生重排,同时内部的缺陷也会得到修复。
最后,将工件冷却至室温,使其保持新的形态。
烫锻的应用非常广泛,主要用于制造高强度、高硬度、高耐磨性的零件和设备。
钢材是最常见的烫锻材料,因为其具有良好的可锻性和成形性。
烫锻可用于制造各种零件,如汽车和航空发动机的曲轴、连杆和减震器。
此外,烫锻还可用于制造工具、螺栓、链条和摩擦副等工业零件。
在进行烫锻时,需要注意以下几个方面。
首先,需要选择适当的温度和压力。
温度过高会导致过度软化和晶粒长大,而过低则无法实现所需的塑性变形。
压力过大容易引起裂纹和断裂,而压力过小则无法达到预期的塑性变形。
其次,需要控制热处理的时间和速度。
时间过久会使金属过软,而时间过短则无法实现预期的效果。
最后,需要对热处理后的工件进行适当的冷却。
过快的冷却速度可能会导致应力和变形,而过慢的冷却速度则可能导致金属过软和晶粒长大。
总结而言,烫锻是一种通过温度控制和压力施加的热加工工艺,可用于改善金属材料的性能和机械性能。
它在汽车、航空航天和工业制造等领域中有着广泛的应用。
然而,成功进行烫锻需要选择适当的温度、压力和时间,并进行适当的冷却。
希望本文对您有所帮助。
锻造工艺介绍
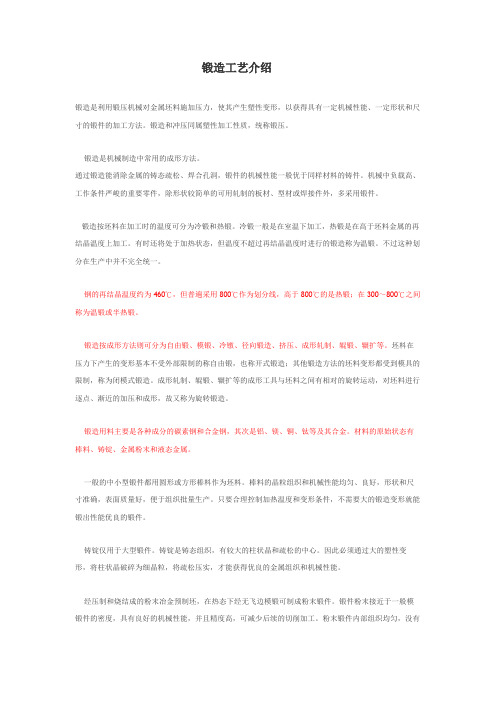
锻造工艺介绍锻造是利用锻压机械对金属坯料施加压力,使其产生塑性变形,以获得具有一定机械性能、一定形状和尺寸的锻件的加工方法。
锻造和冲压同属塑性加工性质,统称锻压。
锻造是机械制造中常用的成形方法。
通过锻造能消除金属的铸态疏松、焊合孔洞,锻件的机械性能一般优于同样材料的铸件。
机械中负载高、工作条件严峻的重要零件,除形状较简单的可用轧制的板材、型材或焊接件外,多采用锻件。
锻造按坯料在加工时的温度可分为冷锻和热锻。
冷锻一般是在室温下加工,热锻是在高于坯料金属的再结晶温度上加工。
有时还将处于加热状态,但温度不超过再结晶温度时进行的锻造称为温锻。
不过这种划分在生产中并不完全统一。
钢的再结晶温度约为460℃,但普遍采用800℃作为划分线,高于800℃的是热锻;在300~800℃之间称为温锻或半热锻。
锻造按成形方法则可分为自由锻、模锻、冷镦、径向锻造、挤压、成形轧制、辊锻、辗扩等。
坯料在压力下产生的变形基本不受外部限制的称自由锻,也称开式锻造;其他锻造方法的坯料变形都受到模具的限制,称为闭模式锻造。
成形轧制、辊锻、辗扩等的成形工具与坯料之间有相对的旋转运动,对坯料进行逐点、渐近的加压和成形,故又称为旋转锻造。
锻造用料主要是各种成分的碳素钢和合金钢,其次是铝、镁、铜、钛等及其合金。
材料的原始状态有棒料、铸锭、金属粉末和液态金属。
一般的中小型锻件都用圆形或方形棒料作为坯料。
棒料的晶粒组织和机械性能均匀、良好,形状和尺寸准确,表面质量好,便于组织批量生产。
只要合理控制加热温度和变形条件,不需要大的锻造变形就能锻出性能优良的锻件。
铸锭仅用于大型锻件。
铸锭是铸态组织,有较大的柱状晶和疏松的中心。
因此必须通过大的塑性变形,将柱状晶破碎为细晶粒,将疏松压实,才能获得优良的金属组织和机械性能。
经压制和烧结成的粉末冶金预制坯,在热态下经无飞边模锻可制成粉末锻件。
锻件粉末接近于一般模锻件的密度,具有良好的机械性能,并且精度高,可减少后续的切削加工。
热锻、温锻成型工艺28页PPT
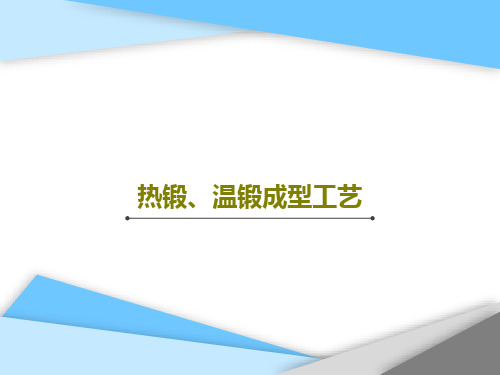
谢谢你的阅读
❖ 知识就是财富 ❖ 丰富你的人生
71、既然我已经踏上这条道路,那么,任何东西都不应妨碍我沿着这条路走下去。——康德 72、家庭成为快乐的种子在外也不致成为障碍物但在旅行之际却是夜间的伴侣。——西塞罗 73、坚持意志伟大的事业需要始终不渝的精神。——伏尔泰 74、路漫漫其修道远,吾将上下而求索。——屈原 75、律是自由的第一条件。——黑格 尔 7、纪律是集体的面貌,集体的声音, 集体的 动作, 集体的 表情, 集体的 信念。 ——马 卡连柯
8、我们现在必须完全保持党的纪律, 否则一 切都会 陷入污 泥中。 ——马 克思 9、学校没有纪律便如磨坊没有水。— —夸美 纽斯
10、一个人应该:活泼而守纪律,天 真而不 幼稚, 勇敢而 鲁莽, 倔强而 有原则 ,热情 而不冲 动,乐 观而不 盲目。 ——马 克思
热锻车间工艺流程

热锻车间工艺流程热锻是一种金属加工工艺,通过加热金属至一定温度后施加一定压力,使金属发生塑性变形,用以制造各种零部件。
热锻车间是进行热锻工艺的地方,工艺流程包括原材料准备、加热、锻造、冷却等环节。
下面是一个详细的热锻车间工艺流程。
首先,原材料准备。
根据产品要求,选择合适的金属材料,如碳素钢、合金钢、铝合金等。
根据产品形状和尺寸,将原材料锯切成合适的长度和宽度,以便后续的加工。
接下来是加热环节。
将原材料放入电炉或火炉中进行加热。
加热温度的选择要根据金属材料的性质和产品要求,通常为材料的再结晶温度或高于再结晶温度。
加热时间也需根据加热温度和材料的厚度和尺寸进行调整,以确保材料均匀加热。
加热后,将材料移入锻压机前的锻模中。
锻模是一种金属工具,用于对金属材料进行形状和尺寸的锻造。
在锻造过程中,需要施加强力压力使材料变形。
锻压机通常由压力机、液压系统和控制系统组成,能够提供足够的压力和控制锻造过程。
在锻造过程中,需要根据产品要求和锻造材料的性质进行合理的锻造温度和锻压时间控制,以确保产品的质量和机械性能。
锻造时的压力和速度也要根据产品的形状和尺寸进行调整,以避免材料的撕裂或过度变形。
锻造完成后,需要进行冷却。
冷却的目的是使金属材料在锻造过程中产生的热量迅速散发,防止材料过热和变形。
冷却方式通常有水淬和自然冷却两种。
对于一些需要保持特定形状的产品,还需要进行定形处理,如回火或正火。
最后,对冷却后的锻件进行清洁和检验。
清洁可以去除锻件表面的氧化物和不纯物质,使其表面得到充分的净化。
检验是确保产品质量的重要环节,包括外观检验、尺寸测量、力学性能测试等。
对于不合格的锻件,需要进行修复或重新制造。
以上是热锻车间的工艺流程。
热锻工艺在制造业中有着广泛的应用,可以制造各种复杂形状和高强度的金属零部件。
随着技术的发展,热锻工艺也在不断进步,新的设备和工艺不断涌现,为金属加工行业提供了更多的选择和机会。
- 1、下载文档前请自行甄别文档内容的完整性,平台不提供额外的编辑、内容补充、找答案等附加服务。
- 2、"仅部分预览"的文档,不可在线预览部分如存在完整性等问题,可反馈申请退款(可完整预览的文档不适用该条件!)。
- 3、如文档侵犯您的权益,请联系客服反馈,我们会尽快为您处理(人工客服工作时间:9:00-18:30)。
二、剪切
在剪切机上进行,剪断直径为200mm以下的钢坯。
特点: 配置自动送料出料机构, 劳动条件好,生产效率高; 提高材料的利用率; 剪切端面质量较差。
三、折断:在水压机或曲柄压力机上进行。(如图9-1)
适用于硬度较高的高 碳钢及高合金钢。加热 温度为300~400℃。
四、砂轮切割 在砂轮切割机上进行。切割直径在40mm以下的金属毛坯。
(3)电阻炉加热
利用电流通过炉内的电热体产生的能量,加热炉内的金属坯料 特点:对毛坯适应范围较大;便于实现保护气体 进行少无氧化加热;热效率低,加热温度受电热 体的限制。
电热体:
金属电热体: 铁铬铝合金(Cr25Al5,Crl7Al5,Crl3Al4) 镍铬合金(Cr20Ni80,Crl5Ni60)
数字化主要体现在对锻造过程和产品品质、成本、效益的预测和可 控程度。
实用中已对汽车发动机连杆精密锻造、汽轮机和压缩机叶片辊锻- 模锻的工艺过程和模具设计制造应用了CADCAM一体化技术,如下图 所示:
计算机辅助设计系统(CAD)和辅助制造系统(CAM )结合,便构成了自动控制集成系统,即由计算机控制的自 动化信息流对锻件的工艺过程设计、锻模的机械加工、装配 、检验和管理进行连续处理,并且发展到以它为中心的锻件 、锻模设计制造和锻造过程模拟(CAE)一体化的自动控制系 统。
扩展阅读:锻造技术发展的未来
1. 数字化塑性成形技术 锻造技术发展的未来是锻造技术数字化。 发达国家重视锻造业的发展,不仅着眼于锻造业在本国工业产值中
所占比例、对国民经济的贡献、就业安排,而且更重视锻造行业为新技 术、新产品的开发和生产提供重要的物质技术,把锻造行业看成是经济 高级化不可缺少的战略性产业。
1.50年代后,锻造生产得到迅速发展。
工艺上:推广了胎模锻造和模锻工艺,采用了高效率、少无切削的特种
锻造工艺,如精密模锻、辊锻和挤压等。基本上掌握了合金钢和大型锻 件的各种锻造技术,如电机转子、护环、立轴、大型高压容器、轧辊等。
设备上:能成系列地制造5kN以下的自由锻锤、12000kN以下的自由锻
造水压机、16kN以下的蒸一空模锻锤、1600kN以下的摩擦压力机和 8000kN以下的热模锻压力机。
加热技术上:无烟节煤炉代替了落后的煤炉,制造了高效薄壁旋转加热
炉和敞焰无氧化加热炉。广泛采用煤气和燃油加热炉及电加热,在先进 的自动化锻压生产线中,感应电加热(中频、工频)成为首选。
其它:提高锻造机械化的操作机和装出料机(包括机械传动、液压传动
锻造技术的发展还必须注意科学化和可控化。
锻造生产不再是简单的坯件供应,要发展为零件、部件 供应,还可以在产品初步设计阶段,针对零件的可生产性, 提供快速分析手段,形成将设计思想转化为产品原型零件, 直至市场效果的快速评估系统。做到“设计、制造、营销” 一体,协同实现对市场需求的快速响应。
锻造技术的发展已不仅是单纯锻造成形技艺的推陈出新 ,而是各种新材料、传感技术、信息技术、自动控制技术、 液压技术、表面技术与锻造原理的融合。锻造技术将实现低 噪音、少污染、对改善人类居住和工作环境有利。
第三节 锻前加热的目的及方法
锻前加热目的: 提高金属塑性,降低变形抗力,使金属易于流动成形,即坯
料易于变形,并获得具有良好的组织和力学性能的锻件。 加热方法:
火焰加热(燃料加热)、 电加热 少无氧化加热
一、火焰加热
利用燃料在火焰加热炉内燃烧产生高温气体,通过对流、辐射 把热能传给毛坯表面,再由表面向中心热传导而使金属毛坯加热。
2.锻压设备与锻压工艺技术的未来发展趋势
国家锻压加工能力主要体现为锻压设备能力与锻压工 艺过程技术能力。锻压设备能力包括自有锻造设备能力、模 锻设备能力、环形件輾扩锻造能力和板材成形设备能力。
1) 锻压设备的大型化发展趋势 由于锻压生产需要巨大的变形力,对大型零件的锻造离
不开重型锻压设备,成形力在100 MN(万吨级)以上。 从某种意义说,重型锻压设备及其所能锻造的大型零件
在实际应用中采用三维模拟技术,对涡旋盘流动控制成形过程 进行的模拟,如下图:
图1.11 涡旋盘控制成形(FCF)工艺过程的三维模拟
锻造过程模拟技术(CAE)通过引入计算机技术等高新技 术,架起了联系材料科学基础理论与热加工工程实际的桥梁 ,使基础学科的理论能够直接定量地指导锻造过程,改变锻 造过程设计中长期依赖经验的落后状况。它使工艺设计由经 验判断走向定量分析,使锻造过程由“技艺”发展为真正的 工程科学,是信息化提升传统工艺过程水平的一个重要体现 。
以低电压(一般为2~15V)大电流直接通过金属坯料,由
坯料自身电阻在通过电流时产生的热量加热金属坯料。
优点: 速度快、烧损少、加热范
围不受限制、热效率高、耗 电少、成本低、设备简单、 操作方便、使用于长坯料的 整体或局部加热的优点。 缺点:
对坯料的表面粗糙度和形 状尺寸要求严格。加热温度 的测量和控制也比较困难。
第九章 热锻工艺概述
热锻工艺特点 热锻原材料及下料方法 锻前加热的目的及方法
热锻温度范围的确定 钢在加热中特点
锻造: 利用外力,通过工具或模具使金属毛坯产生塑性变形, 从而获得具有一定形状、尺寸和内部组织的工件的一种压力 加工方法。 锻造为机械制造工业中提供毛坯,一般是承受力的重要机械
按不同电流频率,感应电加热分为: 高频加热(f=105~106Hz) 中频加热(f=500~10000Hz) 工频加热(f=50Hz)
优点: 速度快、质量好、温度易控制、烧损少、易实现机械
化。适于精密成形的加热。 缺点:
投资费用高,加热的坯料尺寸范围窄、电能消耗大。
(2)接触电加热 (如图9-3)
零件。
锻造优越性: (1) 获得一定形状的金属零件;
(2)改善金属的原来组织,提高 金属的力学性能和物理性能。
一、锻造工艺的重要性
(1)国防工业飞机上的锻压件质量占85%,坦克上的锻压件质量占70 %;大炮、枪枝的大部分都是锻件。
(2)机床制造工业各种机床上的主要零件,如主轴、传动轴、齿轮和 切削刀具等。
优点:燃料来源方便、加热炉修造容易、加热费低、适 应性强。
缺点:劳动条件差,加热速度慢,热效率低 加热质量和炉温难以控制。
应用范围:大、中、小型坯料。
二、电加热
通过把电能转化为热能的方法来加热金属毛 坯。有:
感应电加热 接触电加热 电阻炉加热 盐浴炉加热
(1)感应电加热
坯料放入通过交变电流的螺旋线圈内,利用电磁感应发热 直接加热。
常见的下料方法:
一、锯削 1、圆盘锯:锯盘的最大直径可达2m,锯切的棒料直径在750mm 以下。
2、弓形锯: 锯切的棒料直径100mm以下。直径特别小的棒料,可 成捆地锯断。
3、高速带锯:一种较先进的下料设备,生产效率高,且 毛坯形状规则。
特点: 切口断面平整,尺寸准确; 生产率较低,有锯口损失; 锯条和锯盘的损耗比较大。
二、锻造的分类及特点
(一)锻造的分类
(1)按金属变形时的温度:热锻、温锻和冷锻;
(2)根据工作时所受作用力的来源分:手工锻造、机器锻造。
手工锻造:用手锻工具依靠人力在铁砧上进行的。 机器锻造:现代锻造生产的主要方式,在各种锻造设备上进行。
(3)根据所用设备和工具的不同还可分成四类:
自由锻造:把加热好的金属毛坯放在自由锻造设备的平砧之间或简单
3)锻压设备和工艺过程技术的可持续发展—绿色制造 绿色制造是一个综合考虑环境影响和资源效率的现代制造
模式,其目标是使产品在整个生命周期中对环境影响最小,资 源利用率最高。锻压生产决定了锻压设备和工艺过程对资源的 消耗大,对环境的污染比较严重。
锻压设备在制造领域中扮演着越来越重要的角色,因此锻 压生产实现绿色制造的意义和经济效果尤为突出。锻压设备是 装备制造业中体现制造能力的重要手段,在国家重大工程项目 和汽车工业中起着举足轻重的作用。
(3)电力工业发电设备中的主要零件,如水轮机主轴、透平叶轮、转 子、护环等。(4)交通运输工业机车上的锻压件质量占60%、汽车上的锻 压件质量占80%、轮船上的发动机曲轴和推力轴等主要零件也是锻件。
(5)农业拖拉机、收割机等农业机械上的许多主要零件也都是锻件, 如拖拉机上就有560多种锻件。
(6)日常生活用品如锤子、斧头、小刀、钢丝钳等亦均是锻制而成。
我国锻压设备和锻压工艺技术应该向大型化、自动化、精 密化和绿色锻造方向发展。
我国开发热精锻、冷锻和温锻技术的一些典型 应用实例:
前轴的精密辊锻-整体模锻生产过程:
生产线布置鸟瞰
1000mm自动辊锻机精密成型辊锻 25MN( 2500吨)螺旋压力机弯曲——终锻成形
精密辊锻-整体模锻各道工艺过程的产品
挤压 精密模锻 环形件辗压 辊锻 斜轧 横轧 径向锻造 多向锻造 粉末锻造
(二)锻造工艺的特点
1.锻造能改善金属的组织,提高金属的力学性能和物 理性能。 2.节约金属材料和切削加工工时。 3.具有较高的劳动生产率。 4.锻造有很大的灵活性。
三、我国锻造主产的发展概况及今后发展的方向和任务
和混合传动的)。
发展结果:锻造行业形成具有自己特点的体系。
2.锻造发展方向:
在提高劳动生产率和锻件质量、降低成本和改善工人劳动条件 的前提下,广泛采用机械化、自动化和先进工艺。使锻件的形状和尺 寸及表面质量上最大限度地与产品零件相接近,以达到少无切削加工 的目的。
3.目前我国锻造行业的任务:
(1)提高大型锻件与合金钢锻件的质量和锻造生产的机械化与自动化 程度。 (2)进一步推广模锻,发展大型、先进的模锻设备,扩大模锻生产, 提高模锻件在整个锻件中占的比重。 (3)根据热源条件,发展煤气、天然气、油、电等先进的加热技术。 (4)大力推厂锻造少无切削工艺,发展高效、精密锻压设备。