FMEA作业管理规定
FMEA作业规范

德信诚培训网
FMEA作业规范
(WI-DXC-02)
1.目的:
确定与产品相关的开发或制造过程潜在失效模式,评价失效模式对产品或顾客的影响,并找出失效条件的控制变量和能够避免或减少这些潜在失效发生的措施,以降低产品开发时过程与经费,提高产品之质量及可靠度, 进而增强产品之竞争力, 提高顾客满意度。
2.适用范围:
2.1产品设计开发改善(DFMEA)
2.2产品生产过程改善(PFMEA)
3.权责单位:
3.1失效模式及后果分析 (FMEA)制定:工程部/FMEA小组
3.2失效模式及后果分析 (FMEA)审查及评估:FMEA小组
3.3失效模式及后果分析 (FMEA)最后核准:经理
4. 定义:
4.1FMEA:失效模式及效果分析 (Failure Mode and Effect Analysis )的英文简称。
4.2潜在失效模式:在规定条件下(环境、操作、时间),产品参数值不能维持在规定
的上下限之间或
产品不能完成既定功能,甚至危及人身安全或违反政府法规。
4.2.1.它可能是引起下一道工序失效的潜在模式,也可能是上一道工序潜在失效的后
果。
所列出每一个潜在失效模式,前提是假设这种失效可能发生,但不一定非得发生。
4.2.2.FMEA是一个动态和不断完善及发展的文件,它应时刻体现最新的设计改善和相更多免费资料下载请进:好好学习社区。
PFMEA管理规定

4.5.6严重度(S):严重度是指与评估的过程步骤中针对给定的失效模式最严重影响相关的评级等分,他是在一个FMEA范围内的相对评级,评定时无需考虑频度或探测度。
4.5.7频度:频度(O)描述了失效起因在过程中的发生频率,同时考虑了相关的当前的预防控制。
当措施完成时,频度和探测度值将被重新评估,一个新的措施优先级可能要被确定。重新评估应当基于采取的预防和探测措施的有效性,并且新的值基于过程FMEA频度和探测度评级表中的定义。
4.6.6持续改进:
PFMEA是过程的历史记录。初始严重度、频度和探测度(S、O、D)数值需显示可见,或至少可作为历史记录的一部分使用和访问。分析完成后将形成一个储存库,能够记录过程决策和设计改进的进展。
建立日期
版次
文件编号
修订日期
2019.12.23
四、过程FMEA的执行:
4.1过程FMEA步骤一:策划与准备
4.4.1该过程考虑工厂内所有过程均可通过PFMEA进行分析或重新分析。准备阶段的总体优势是将资源集中在优先级最高的过程上。
4.1.2过程策划与准备步骤的主要目标:
①项目识别
②项目计划:目的、时间安排、团队、任务、工具(5T)
4.4.6失效起因:失效起因是指失效模式出现的原因,失效模式是失效起因的结果。
4.4.7失效分析:根据过程步骤,导出失效并从功能分析中创建失效链。
4.4.8失效分析文件化:结构分析、功能分析和失效分析完成后,结构树或电子表格制成多种视图。
批准
审核
作成
第3页共13页
****************公司
3.3生产部职责:
生产部负责提出对生产过程中的生产流程等不合理现象,必要时参与FMEA小组;
FMEA编制作业指导书
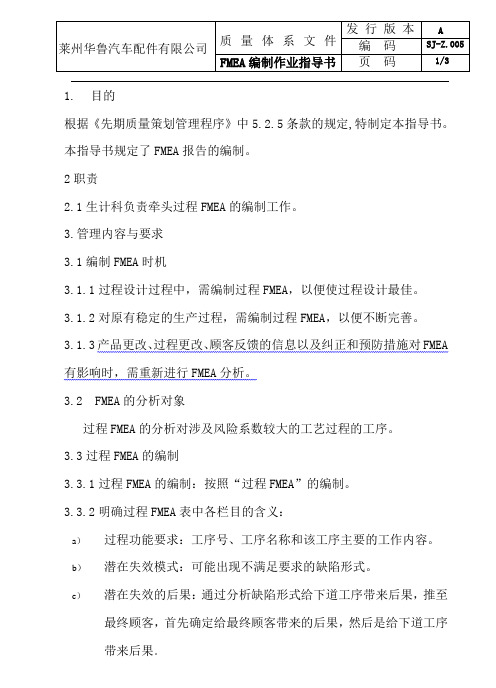
1.目的根据《先期质量策划管理程序》中5.2.5条款的规定,特制定本指导书。
本指导书规定了FMEA报告的编制。
2职责2.1生计科负责牵头过程FMEA的编制工作。
3.管理内容与要求3.1编制FMEA时机3.1.1过程设计过程中,需编制过程FMEA,以便使过程设计最佳。
3.1.2对原有稳定的生产过程,需编制过程FMEA,以便不断完善。
3.1.3产品更改、过程更改、顾客反馈的信息以及纠正和预防措施对FMEA 有影响时,需重新进行FMEA分析。
3.2 FMEA的分析对象过程FMEA的分析对涉及风险系数较大的工艺过程的工序。
3.3过程FMEA的编制3.3.1过程FMEA的编制:按照“过程FMEA”的编制。
3.3.2明确过程FMEA表中各栏目的含义:a)过程功能要求:工序号、工序名称和该工序主要的工作内容。
b)潜在失效模式:可能出现不满足要求的缺陷形式。
c)潜在失效的后果:通过分析缺陷形式给下道工序带来后果,推至最终顾客,首先确定给最终顾客带来的后果,然后是给下道工序带来后果。
d)潜在失效的起因:造成缺陷形式的原因。
e)现行过程控制:现行对过程所采用的控制方法,包括防错、过程控制和检验。
f)建议措施:经过RPN,认为现行过程控制不足以控制过程,而提出的新的控制方法,包括防错、过程控制和检验。
g)采取措施:经过分析,所落实的新的控制方法。
h)新RPN值:设想采取新的措施的RPN值,如果新的RPN值不能有效降低,应考虑执行其他改进措施。
i)FMEA编号:当前产品的加工过程,编制FMEA的版本次数,由三位数组成,如001,代表针对此过程,第一次编制FMEA。
3.3.3进行RPN分析a)当RPN值小于等于125,一般不采取措施,当出现c)款条件时,按条款c)执行b)当RPN值大于125,小于等于150时,可根据参数的重要性,采取或不采取措施。
c)当严重度大于8,同时频度或可探测度不同时小于及等于3时,应针对比较高的项目采取措施。
FMEA管理规定知识讲解
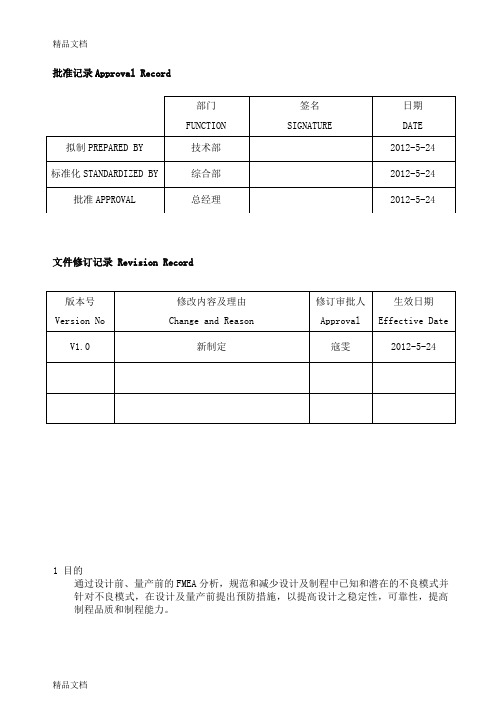
批准记录Approval Record文件修订记录 Revision Record1 目的通过设计前、量产前的FMEA分析,规范和减少设计及制程中已知和潜在的不良模式并针对不良模式,在设计及量产前提出预防措施,以提高设计之稳定性,可靠性,提高制程品质和制程能力。
2 范围设计管制活动、设计变更前/后、制程标准订定及变更前/后的潜在失效模式之作业。
3 定义FMEA(Failure Mode Effects Analysis)失效模式与效应分析。
为一系列统化的分析技术,用以评估某一可能缺点的发生机率,及其发生后造成的影响。
而且针对高风险( RPN,Risk Priority Number )项目,事先评估其制程能力,制订适当的制程管制。
4 职责3.1 技术部:3.1.1 FMEA会议召开,产品保证计划,新产品流程草案主导拟定,FMEA作业制定,主导FMEA会议。
3.1.2 召集组成跨功能小组,小组成员可包括技术、品保、生产及相关人员(必要时可会同客户或供货商),协同进行研讨。
3.2生产部:流程的讨论确认,潜在不良模式收集,潜在不良原因分析,预防措施的拟定、确认、实施。
3.3品管部:FMEA作业所需之相似制程之统计数据的提供,预防措施的监督执行。
3.3管理代表:FMEA文件的核准。
5 适用时期5.1开发初期。
5.2产品投产前期。
5.3整体材料变更时。
5.4制程设备、模/治具大幅变更或购置时。
5.5客户要求时。
5.6以上由技术部主管视情况裁决,是否实施实效模式与效应分析作业。
6 作业流程:流程说明:从制程流程图中,小组成员以脑力激荡后决定欲分析的制程等,用失效模式分析表进行后续的分析.7 作业内容:7.1失效模式分析表使用方法:7.1.1 文件编号:文件号码编号用于做追踪管控。
7.1.2 项目:填入须分析的产品、部件或零组件的名称、编号。
7.1.3 制程/设计责任:填入部门和小组,如果需要,还要包括供货商的名称。
FMEA作业规范(失效模式及影响分析)

失效模式及影響分析(FMEA)1.定義:1) 英文 Failure Mode and Effects Analysis, 縮寫FMEA。
是一種由下而上的歸納式系統分析或流程分析方法,用來評估潛在性的錯誤。
包含找出什麼會造成錯誤,以及會發生錯誤的方法﹝失效模式﹞,決定每個失效模式對系統的影響。
根據經驗分析産品設計與生産工藝中存在的弱點和可能産生的缺陷公及這些缺陷産生的後果與風險,在決策過程中採取措施加以清除。
3) 分爲設計失效模式分析過程失效分析.過程FMEA是以工藝過程的每道工序爲分析物件; 設計FMEA是以系統或零部件爲分析物件;因此FMEA分析要從系統組成零件列表中或加工工藝流程事確定産品設計專案或過程專案.基本思路:劃分分析物件,確定每一物件的分析內容,研究分析結果及處理措施,製作FMEA分析表;4) FMEA流程分析流程缺陷的名稱潛在失效的後果建議糾正措施想象中可能産生的缺陷失效嚴重度評估缺陷被發現的概率缺陷産生的頻度缺陷産生的原因二.FMEA的分類1) 設計FMEA是由設計主管工程師/4組在設計早期彩的一種分析技術,用來在最大範圍內保證已充分地考慮到和指明各種潛在的失效模式及其相關的起因和理,評估最後的産品以及每個與之相關的系統,系統和零部件,以最嚴密的形式總結了設計思想.2) 在設計階段使用FMEA時常用:a. 有助於對設計要求的評估及對設計方案的相互權衡;b. 建立一套改進設計和開發試驗的優先控制系統;c. 爲推薦和跟蹤低風險的措施提供一個公開的的討論形式;d. 爲將來分析研究現場情況,評價設計時的更改及開發更先進的設計,提供參考;e. 有助於對製造和裝配要求的最初設計;f. 提高在設計開發過程中已考慮潛在失效及其對系統和産品使用影響的可能性;g. 對制定全面,有效的設計試驗計劃和開發專案提供更多資訊;3) 過程FMEA由製造主管工程師/小組,採用的分析技術,用在最大範圍內,保證充分地考慮到並指明失效模式及其相關的後果起因/機理,以最嚴密的形式總工程師結了工藝過程設計的設計思想,與一個工程師在任何製造過程中經常經歷的思維過程是一致的.過程FMEA假設設計的産品會滿足設計要求,它們的影響及避免措施由設計FMEA來解決.主要考慮與製造計劃的製造廠裝配過程有關的産品設計參數,以便最大限度地保證産品能滿足顧客要求和期望.3.FMEA的意義爲設計:生産、質保部門提供共用的資訊資源也爲同類産品的設計提供資料。
FMEA管理规定
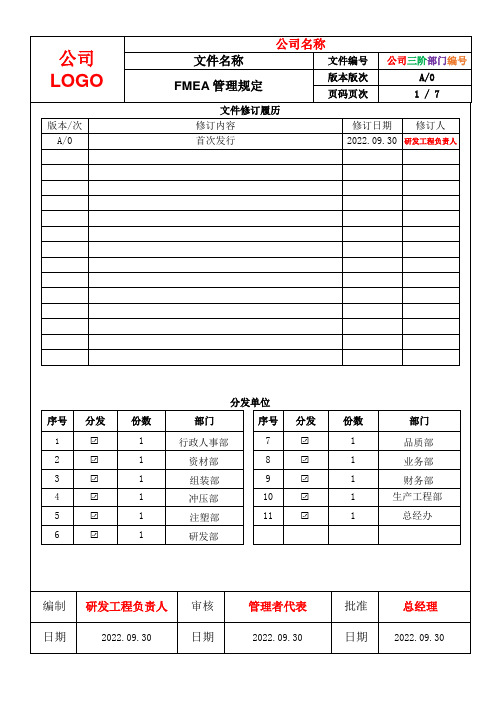
1)功能性:针对产品可靠性测试,有无失效影响。
2)外观:针对行业外观要求、客户外观要求,有无失效影响。
3)制造性:针对制造工艺要求,有无失效影响。
4)合规性:针对所涉及的法律、合约条款,有无失效影响。
5)安全性:针对产品使用的安全要求,有无失效影响。
5.3.8严重度 ( S ):
设计FMEA严重度评价准则
严重度
失效影响:顾客后果
级别
未能符合安全性/合规性
影响产品安全使用/违反所涉及的法律、合约,无预警
10
影响产品安全使用/违反所涉及的法律、合约,有预警
9
基本功能的损失或降级
基本功能损失(不能使用,但不影响安全操作)
8
基本功能降级(可使用,但功能降低)
7
次要功能的损失或降低
次要功能损失(可使用,但舒适性/便利性功能丧失)
5 内容
5.1成立FMEA小组:
5.1.1主导部门召集相关部门,成立FMEA小组。
5.1.2成员要有一定的FMEA工作推进经验。
5.2编制FMEA的时机:
5.2.1设计FMEA在产品的设计开发阶段进行。
5.2.2 过程FMEA在产品的过程设计开发阶段进行。
5.3编制过程:
5.3.1填写FMEA文件的编号,以便查询。
4
中等偏高
从源头进行问题探测
由自动化控制进行工位上失效模式探测。这种自动化控制能探测不符合零件,并自动锁定工位上的零件以防止进一步的操作
3
高
错误(起因)探测和/或问题预防
由自动化控制进行工位上错误(起因)探测。这种自动化控制能探测错误和预防不符合零件的制造
2
非常高
错误(起因)预防
PFMEA作业指导书
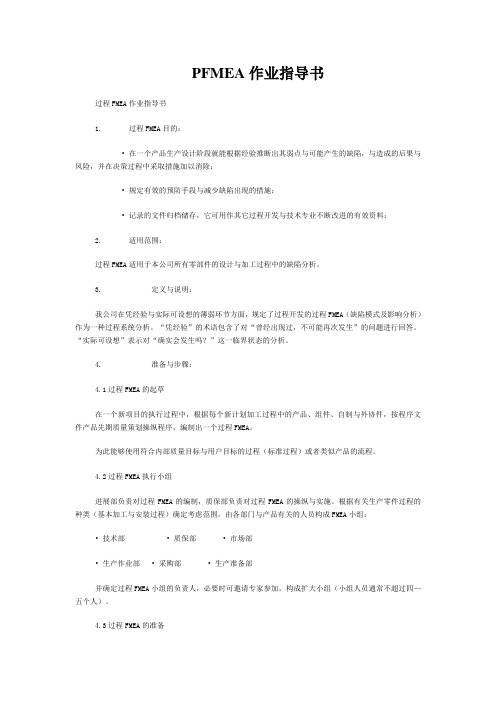
PFMEA作业指导书过程FMEA作业指导书1. 过程FMEA目的:• 在一个产品生产设计阶段就能根据经验推断出其弱点与可能产生的缺陷,与造成的后果与风险,并在决策过程中采取措施加以消除;• 规定有效的预防手段与减少缺陷出现的措施;• 记录的文件归档储存,它可用作其它过程开发与技术专业不断改进的有效资料;2. 适用范围:过程FMEA适用于本公司所有零部件的设计与加工过程中的缺陷分析。
3. 定义与说明:我公司在凭经验与实际可设想的薄弱环节方面,规定了过程开发的过程FMEA(缺陷模式及影响分析)作为一种过程系统分析。
“凭经验”的术语包含了对“曾经出现过,不可能再次发生”的问题进行回答。
“实际可设想”表示对“确实会发生吗?”这一临界状态的分析。
4. 准备与步骤:4.1过程FMEA的起草在一个新项目的执行过程中,根据每个新计划加工过程中的产品、组件、自制与外协件,按程序文件产品先期质量策划操纵程序,编制出一个过程FMEA。
为此能够使用符合内部质量目标与用户目标的过程(标准过程)或者类似产品的流程。
4.2过程FMEA执行小组进展部负责对过程FMEA的编制,质保部负责对过程FMEA的操纵与实施。
根据有关生产零件过程的种类(基本加工与安装过程)确定考虑范围,由各部门与产品有关的人员构成FMEA小组:• 技术部• 质保部• 市场部• 生产作业部• 采购部• 生产准备部并确定过程FMEA小组的负责人,必要时可邀请专家参加,构成扩大小组(小组人员通常不超过四—五个人)。
4.3过程FMEA的准备进展部应根据具体加工零件编制过程FMEA表。
在FMEA表中,在过程指标栏中填写潜在的缺陷问题、潜在问题出现的后果、潜在问题的起因、目前状况预防及检验措施状况,同时填写风险特性指数。
质保部应组织FMEA小组讨论改进措施与方案,并根据所记录的数据与每位组员的经验,评定缺陷可能出现的概率与缺陷对用户的影响,必要时补充其它缺陷、后果或者原因。
fmea作业标准(一)

fmea作业标准(一)FMEA作业标准什么是FMEAFMEA是一种常用的风险分析工具,全称为”Failure Mode and Effects Analysis”(故障模式与影响分析),它通过系统性地识别潜在故障模式,评估其对系统性能和可靠性的影响程度,以便采取相应的纠正和预防措施。
FMEA作业标准的重要性FMEA作业标准的制定和遵守对于确保故障预防和产品质量的持续改进至关重要。
它为团队提供了一套规范,帮助实现以下目标:•识别潜在故障模式并进行分析•评估故障可能产生的影响•制定纠正和预防措施•区分关键和不关键故障模式•提高产品性能和可靠性FMEA作业标准的主要内容FMEA作业标准包含以下内容:1.团队组织和联络–成立跨部门的FMEA团队,涵盖所有相关领域的专家–定期召开会议,确保团队有效沟通和协作–指定团队负责人,负责协调和监督整个FMEA过程2.FMEA过程和方法–制定整个FMEA过程的详细步骤和方法–确定故障模式和潜在原因,并对其进行排名和分类–评估故障对系统性能的影响程度–制定纠正和预防措施,确保故障不再发生或影响减弱–确保每个步骤都有详细的记录和跟进3.风险评估和管理–根据故障发生的可能性和影响程度,对故障进行优先级排序–为关键故障模式制定紧急处理计划–根据风险评估结果,制定长期的风险管理计划4.持续改进和经验总结–在FMEA过程中发现的问题和故障模式,应及时改进和纠正–对FMEA作业的经验进行总结和分享,以提高团队的专业知识和技能水平–定期评估和更新FMEA作业标准,确保其与最新的行业标准和法规保持一致FMEA作业标准的好处遵守FMEA作业标准可以带来以下好处:•提高产品质量和可靠性•减少故障发生的可能性和影响•提前预防潜在故障和问题•提高团队协作和沟通效率•加强风险管理和控制能力总之,FMEA作业标准是一个重要的工具和指南,帮助团队在设计、制造和改进过程中识别和管理潜在的故障和风险,以保证产品质量和客户满意度的持续提高。
FMEA作业规范

FMEA作业规范(IATF16949-2016)1.0 目的旨在确定模具设计或产品制造过程中所有的失效模式,及早发现模具设计或产品制造过程中所有的致命性与关键性的失效发生的可能性,以便及早的消除或降低失效发生的机率。
2.0 适用范围适用于本公司所有产品在量产前之模具设计及制程质量之规划时。
3.0 职责和权限3.1 技术部:负责制程质量之PFMEA之制作,组织并主导编写制程质量之PFMEA。
3.2 设计课:负责模具开发和制造PFMEA之制作,组织并主导编写模具开发和制造之PFMEA。
3.3 相关部门:金型部、技管课、生管课、品保部、成型部、营业部、资材课、维修组等单位配合成立跨部门功能小组,参与执行及推动。
3.4 跨部门功能小组:负责PFMEA基本数据之建立、审查、检讨及追踪。
4.0 定义4.1 FMEA:失效模式及效应分析,旨在发现和评价模具设计和制造、产品制造过程中潜在的失效及其失效后果,找到能够避免或减少这些潜在失效发生的措施,并将整个过程文件化的一组系统化的活动。
4.2 潜在的失效模式:指产品可能无法达到设计意图、后续要求或客户预期的可能产品缺失,潜在失效模式的假设为有可能发生却非一定发生。
4.3 潜在的失效效应:指如果失效模式一旦发生,失效模式对客户可能造成的影响或效应。
4.4 严重度(S):对失效模式所造成的失效效应严重程度的评估,如某项缺点一旦发生,则可能对客户产生影响之严重程度。
4.5 发生率(O):指对某一特定失效原因发生导致失效模式产生的发生频率。
4.6 检出率(D):指某项缺点在零件生产或组装中,乃至于在离开制造场所或装配场所之前,能以现行管制方法检测出该缺点的比率。
4.7 风险顺序数(RPN):为严重度、发生率及检出率等三项数字之乘积,亦即为一项纠正缺失的优先排行指数,其数字本身不具有意义。
5.0 参考文件和资料5.1 《FMEA手册》(最新版)6.0 内容7.0 附表7.1 PFMEA表PFM EA表格.d oc。
FMEA作业规范

失效模式清单
失效模式分析
PFMEA 表填写
计算并判定 RPN≤70
分发及存档
定期审核/修正
低
5
能水平有所下降。
在线下返修,不需送往返修部门处理
配 合 和 外 观 / 尖 响 和 卡 嗒 响 项 目 不 舒 或产品可能需要分检,无需报废,但部分产
很低
4
服。多数(75%以上)顾客能发觉缺陷。
品(小于 100%)需返工。
配合和外观/尖响和卡嗒响项目不舒服。50% 或部分产品(小于 100%)可能需要返工,无需
5.3.4风险顺序数(RPN):是指严重度数(S),频度数(O)和不易探测数(D)的乘积 RPN=(S)X(O)X(D)
对过程中那些风险事项进行排序。RPN 取值在"1"到"1000"之间,如果风险顺序值很高
(RPN≧70),严重度高(S≧6) ,工程部门人员必须采取纠正措施,努力减少 RPN 值;产品
5. 作业流程: 5.1 CFT 小组准备有关的资料: a) 初始过程流程图; b) 产品特性数据; c) 类似产品的《PFMEA》数据; d) 产品图纸; e) 产品的《控制计划》; f) 顾客资料及相关的顾客标准; g) 产品环境方面客户特殊要求与欧盟 RoHS/WEEE 等相关法律法规。 5.2 PFMEA 制定: 5.2.1 列出失效模式清单; 5.2.2 根据失效模式,进行分析,分别判定其严重度(S)、频度(O)、可探测度(D),计算其风 险优先级数 RPN 值(RPN=S*O*D) 5.2.3 根据所列失效内容及 S、O、D 判定标准,填写《PFMEA》表;相应标准参考注意事项:5.1、 5.2、5.3 进行; 5.2.4 确定风险顺序(RPN):当严重度(S)≥6,RPN≥70 需采取相应纠正措施,产品如有不同 要求,按客户要求执行。 5.2.5 修订的《PFMEA》分发及存档。 5.2.6 当客诉、工程变更及异常时需重新审核《PEMEA》,根据状况补充及更新相关内容。 5.3 注意事项: 5.3.1 评价准则(S): 注: 小组对评价准则和应有分级规则应意见一致,即使因为个别过程的分析作了修改也应 一致。
公司工厂管理规定办法C-ST-003产品失效模式和影响分析(FMEA)作业办法

工程部
1、PFMEA编号:P□□□□-□□-□□-□□前4位为机种项目编号;5,6位为机种部件编号,数字由01~99循环使用;7,8位为月份;9,10位为年份后两位.例: D0502-01-07-03,代表为0502机种在XXx年3月对其第一个部件进行了PFMEA分析。
2、FMEA小组成员:填入参与FMEA分析的小组成员名单。
14、负责人及预定完成日期:建议对策实施负责单位,个人及预定完成日期。
15、实际改善行动:填写实际改善行动。
《潜在失效模式及失影响分析表》
修订记录
原版次
修订日期
修订内容
核准
审核
制定
XXx有限公司
失效模式和影响分析(FMEA)
作业办法
文件版次
A0
页次
9/11
文件编号
C-ST-003
制定部门
工程部
生效日期
3
研发部
系统可逐级分解直到最基本的零件、构件,一般根据分析目的计划分至某一层级。
4
研发部
1、各功能潜在失效模式。
2、利用因果图从人、机、料、法、环等方面分析失效的可能原因。
3、列举潜在失效影响。
修订记录
原版次
修订日期
修订内容
核准
审核
制定
XXx有限公司
失效模式和影响分析(FMEA)
作业办法
文件版次
A0
修订记录
原版次
修订日期
修订内容
核准
审核
制定
XXx有限公司
失效模式和影响分析(FMEA)
作业办法
文件版次
A0
页次
5/11
文件编号
C-ST-003
FMEA管理规范

FMEA管理规范文件编号:1.目的通过分析、预测设计、过程中潜在的失效,研究失效的原因及其后果,并采取必要的预防措施,避免或减少这些潜在的失效,从而提高产品、过程的可靠性。
2.适用范围适用于公司设计FMEA、过程FMEA活动的控制。
3.职责3.1 产品研发部(R&D)负责组织成立DFMEA(设计FMEA)小组,负责DFMEA活动的管理。
3.2 生产技术部(PE)负责组织成立PFMEA(过程FMEA)小组,负责PFMEA活动的管理。
3.3 产品研发部、生产技术部、品管部、生产部、营销部、采购部等部门指定人员参加DFMEA小组、PFMEA小组。
必要时,由品管部邀请供应商、客户参加。
3.4 DFMEA小组负责制定《DFMEA潜在失效后果严重程度(S)评价标准》、《DFMEA潜在失效模式发生概率(O)评价标准》、《DFMEA潜在失效模式发现难度(D)评价标准》。
3.5 PFMEA小组负责制定《PFMEA潜在失效后果严重程度(S)评价标准》、《PFMEA潜在失效模式发生频度(O)评价标准》、《PFMEA潜在失效模式发现难度(D)评价标准》。
4.工作程序4.1 设计FMEA的开发实施4.1.1 DFMEA实施的时机4.1.1.1 按APQP的计划进行DFMEA。
4.1.1.2 在出现下列情况时,DFMEA小组应在产品零件图纸设计之前进行DFMEA活动:①开发新产品/产品更改;②产品应用的环境发生变化;③材料或零部件发生变化。
4.1.2 DFMEA实施前的准备工作①产品研发部(R&D)牵头成立DFMEA(设计FMEA)小组,生产技术部、品管部、生产部、营销部、采购部等部门指定人员参加DFMEA小组,必要时,由品管部邀请供应商、客户参加。
②在DFMEA活动实施前,DFMEA小组应制定出《DFMEA潜在失效后果严重程度(S)评价标准》、《DFMEA潜在失效模式发生概率(O)评价标准》、《DFMEA潜在失效模式发现难度(D)评价标准》。
FMEA作业指导书
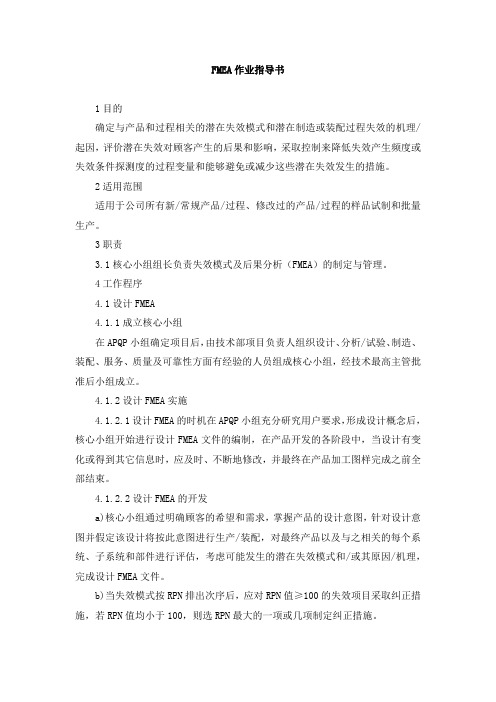
FMEA作业指导书1目的确定与产品和过程相关的潜在失效模式和潜在制造或装配过程失效的机理/起因,评价潜在失效对顾客产生的后果和影响,采取控制来降低失效产生频度或失效条件探测度的过程变量和能够避免或减少这些潜在失效发生的措施。
2适用范围适用于公司所有新/常规产品/过程、修改过的产品/过程的样品试制和批量生产。
3职责3.1核心小组组长负责失效模式及后果分析(FMEA)的制定与管理。
4工作程序4.1设计FMEA4.1.1成立核心小组在APQP小组确定项目后,由技术部项目负责人组织设计、分析/试验、制造、装配、服务、质量及可靠性方面有经验的人员组成核心小组,经技术最高主管批准后小组成立。
4.1.2设计FMEA实施4.1.2.1设计FMEA的时机在APQP小组充分研究用户要求,形成设计概念后,核心小组开始进行设计FMEA文件的编制,在产品开发的各阶段中,当设计有变化或得到其它信息时,应及时、不断地修改,并最终在产品加工图样完成之前全部结束。
4.1.2.2设计FMEA的开发a)核心小组通过明确顾客的希望和需求,掌握产品的设计意图,针对设计意图并假定该设计将按此意图进行生产/装配,对最终产品以及与之相关的每个系统、子系统和部件进行评估,考虑可能发生的潜在失效模式和/或其原因/机理,完成设计FMEA文件。
b)当失效模式按RPN排出次序后,应对RPN值≥100的失效项目采取纠正措施,若RPN值均小于100,则选RPN最大的一项或几项制定纠正措施。
c)执行纠正措施后,计算并记录RPN的结果。
如措施后的RPN级数仍≥100,应考虑采取进一步的措施,并对措施后的RPN再次评审。
4.1.3跟踪负责设计的工程师应负责保证所有的建议措施已被实施或已妥善地落实。
负责设计的工程师可采用以下几种方式来保证所关注的问题得到明确,所建议的测试得到实施:●保证设计要求达到得到实现;●评审工程图样和规范;●确认这些已反映在装配/生产文件之中;●评审过程FMEA和控制计划。
FMEA作业规范

1.目的
在设计新产品的制造工程时,为了防止有可能出现的品质的问题在各工程中发生,总结过往的所有的经验,找出对策,实施改善,为了进行品质能够得到保障而规定《工程FMEA》的实行、管理,在工程设计阶段,对所研究项目的正确性进行确认,防止问题点再度发生。
2.适用范围
适用于公司内部的工程FMEA作成,使用及改进。
3.职责
APQP小组负责对工程FMEA的作成、实施、改善以及品质部负责将相关内容反映到工程类文件。
4.时期
(1)新制品制作时期前实施(控制计划);
(2)工程FMEA变更时(改善对策引起);
5.标准
5.1作成
⑴工程FMEA是使用被指定的格式作成的,当客户有要求格式时,要按客户要求实施;作成时,根据需要将下述内容记入:
⑵符合下列项目时,记入纠正处理栏里:
①危险优先度(RPN)在100分以上时,需要采取措施改进;(RPN=S*0*D)
②严重度的在9或10分时,要对频度或检出的难易度(探测度)降低到1分点;
③当客户有要求严重度、频度及探测度的评价分数时,则按客户要求执行;
④评价标准见附件一、二
5.2工程FMEA制作的输入资料:。
FMEA作业管理规定

很高
控制几乎肯定能探测出
X
X
在工位上的误差探测(自动测量并自动停机),不能通过有差异的零件。
2
很高
肯定能探测出
X
由于有关项目已通过过程/产品设计采用了防错措施,有差异的零件不可能产出。
1
检验类别: A.防错B.量具C.人工检验
少
设计控制有较少的机会能找出潜在的起因/机理及后续的失效模式
6
中等
设计控制有中等到的机会能找出潜在的起因/机理及后续的失效模式
5
中上
设计控制有中上多的机会能找出潜在的起因/机理及后续的失效模式
4
多
设计控制有较多的机会能找出潜在的起因/机理及后续的失效模式
3
很多
设计控制有很多的机会能找出潜在的起因/机理及后续的失效模式
2
几乎肯定
设计控制几乎肯定能找出潜在的起因/机理及后续的失效模式
1
6、支持性文件
TM-QP710-1《产品质量先期策划控制程序》、TM-QP423《文件控制程序》及《FMEA参考手册》
7、附件(包括表1、表2和表3)
QR710-1-15【潜在失效模式及后果分析(DFMEA)】
QR710-1-29【潜在失效模式及后果分析(PFMEA)】
9
很高
车辆/项目不能工作(丧失基本功能)。
或100%的产品可能需要报废,或者车辆/项目需在返修部门返修1个小时以上。
8
高
车辆/项目可运行但性能水平下降,
顾客非常不满意。
或产品需要进行分检、一部分(小于100%)需报废,或车辆/项目在返修部门进行返修的时间在小时之间。
7
中等
车辆/项目可运行但舒适性/便利性项目不能运行,顾客不满意。
FMEA作业办法

3.1管理辦法制訂:生產技術部.
3.2管理辦法執行:品保部.生技單位.工程單位.製造單位.設備課.
3.3管理辦法核准:廠內最高主管
4.作業重點
4.1只要定義是新產品開始就必須做FMEA(如附件一)。
4.2特別要把焦點集中在將會爆發問題上
4.3 FMEA檢討的不僅在於機能有關部份,也應考量故障模式對所有構成要素可能帶來的影響
香港太空梭高傳真資訊科技股份有限公司
電子事業處
SPACE SHUTTLE(H.K) HI-TECH CO.,LTD
標題
FMEA作業辦法
版本/版次
A/0
編號
CWF-M08
制訂部門
生產技術部
制訂日期
2003/產品的故障及改善安全性.
2.適應範圍:新產品先前之預防及產品發生異常分析.
5.4.2評估前考量
5.4.2.1之前的作業是否採用相同方式或類似方式
5.4.2.2原物料是否為新廠商
5.4.2.3之前是否有發生類似狀況
5.4.2.4工治具及機器設備是否有變更
5.4.2.5環境是否有改變
5.5評估故障模式影響的嚴重度
給予影響度評估(容易影響的5分,不易影響的1分),分配適當的分數
5.作業內容.
5.1故障模式.
將引起故障的不良現象的特徵加以分門別類
5.2探討故障模式發生時的影響
站在作業人員的立場,考量上述故障模式發生時,究竟導致怎樣不良的故障
5.3探討故障的原因及故障的發生
故障的原因或發生狀況應儘可能記載完整,簡潔,方能循此建立因應對策
5.4評估故障模式發生難易度
5.4.1給予難易度評估(容易發生的5分,不易發生的1分),分配適當的分數
FMEA指导书作业办法

1.目的对公司的FMEA活动程序化、规范化,降低设计和制造风险,以有效预防质量问题的发生,促进效益的提高;适用于公司对所有新产品、新过程、更改过的产品过程及应用或环境有变化时沿用零件进行设计FMEA和过程FMEA活动。
2.适用范围适用于公司所有的新产品、新过程、更改过的产品过程及应用或环境有变化时沿用零件进行DFMEA和PFMEA活动。
3.职责3.1工程部:负责在产品设计和过程开发活动之前组织项目小组人员进行分析研究、制作、修改DFMEA。
3.2制造工程部:负责在产品设计和过程开发活动之前组织项目小组人员进行分析研究、制作、修改PFMEA。
3.3 品质部:负责对FMEA的活动进行跟踪检查,确保FMEA所采取的措施得到落实执行;对FMEA现行的控制方法所提到的检测、试验等方法的可行性负责。
3.4 生产单位:负责对PFMEA活动的具体实施。
4.定义4.1 潜在失效模式及后果分析FMEA: 在产品的设计阶段和过程设计阶段,对构成产品的子系统、零件、对构成过程的各道工序逐一进行分析,找出所有潜在的失效模式,并分析其可能的后果,从而预先采取必要的措施,以提高产品的质量和可靠性的一种系统化的活动。
DFMEA:设计失效模式及后果分析PFMEA:过程失效模式及后果分析4.2 严重度(S):是潜在失效模式发生时对下序零件、子系统、系统或顾客影响后果的严重程度的评价指标。
4.3 级别:对零件、子系统或系统的产品特殊特性分级(如关键、主要、重要、重点等),它们可能需要附加的过程控制。
4.4 频度(O): 频度是指某一特定失效起因或机理发生的频率。
4.5探测度(D):探测度是指在零部件离开制造工序或装配工位之前,用现行设计控制方法来探测潜在失效起因或机理的能力的评价指标。
4.6 风险顺序数(RPN):风险顺序数是严重度(S)、频度数(O)和探测数(D)的乘积,是对设计风险性的度量。
即RPN=SXOXD5. 流程图流程图作业概要权责单位相关记录当有新产品或更改的产品以及重要的过程更改时,项目负责人主导组成项目小组,明确各小组成员的职责收集资料,完成FMEA 的输入信息1. 小组根据产品过程流程图结合以往经验通过潜在的失效模式及后果分析表进行分析识别; 2.根据零部件或过程特性,对特定作业列出每一个潜在的失效模式。
- 1、下载文档前请自行甄别文档内容的完整性,平台不提供额外的编辑、内容补充、找答案等附加服务。
- 2、"仅部分预览"的文档,不可在线预览部分如存在完整性等问题,可反馈申请退款(可完整预览的文档不适用该条件!)。
- 3、如文档侵犯您的权益,请联系客服反馈,我们会尽快为您处理(人工客服工作时间:9:00-18:30)。
文件名称:FMEA作业管理规定
编号:TM-G023-04/A
版本:A
核准:日期: 审查:日期: 拟案:日期:
有限公司
表1.推荐的PFMEA严重度评价准则
注:
①若有特殊特性的过程,其严重程度数(S)不能低于8,需要
采取整改措施;
②若涉及安全或法律法规,其严重程度数(S)不能低于9,需
要采取整改措施。
表2. 推荐的带有PpK值的PFMEA频度评价准则
可能性可能的失效率Ppk 频度
很高:失效待续发生≥100/1000件<0.55 10 50/1000件≥0.55 9
高:失效经常发生20/1000件≥0.78 8 10/1000件≥0.86 7
中等:失效偶尔发生5/1000件≥0.94 6 2/1000件≥1.00 5 1/1000件≥1.10 4
低:失效较少发生0.5/1000件≥1.20 3 0.1/1000件≥1.30 2
极低:失效不大可能发生≤0.01/1000件≥1.67 1 表3.推荐的PFMEA探测度评价准则
探测性准则
检查类别
探测方法的推荐范围探测度A B C
几乎不可能绝对肯定不可能
探测
X 不能探测或没有检查。
10
很微小控制方法可能探
测不出来
X 只能通过间接或随机检查来实现控制。
9
微小控制有很少的机
会能探测出
X 只通过目测检查来实现控制。
8
很小控制有很少的机
会能探测出
X 只通过双重目测检查来实现控制。
7
小控制可能能探测
出
X X 用制图的方法,如SPC(统计过程控制)来实现控制。
6
中等控制可能能探测
出
X
控制基于零件离开工位后的计量测量,或者零件离
开工位后100%的止/通测量。
5
中上控制有较多机会
可探测出
X X
在后续工位上的误差探测,或在作业准备时进行测
量和首件检查(仅适用于作业准备的原因)。
4
高控制有较多机会
可探测出
X X
在工位上的误差探测,或利用多层验收在后续工序
上进行误差探测:供应、选择、安装、确认,不能
接受有差异的零件。
3
很高控制几乎肯定能探
测出
X X
在工位上的误差探测(自动测量并自动停机),不能
通过有差异的零件。
2
很高肯定能探测出X 由于有关项目已通过过程/产品设计采用了防错措
施,有差异的零件不可能产出。
1
检验类别: A.防错 B.量具C.人工检验。