FMEA报告编制作业指导书
FMEA作业指导书
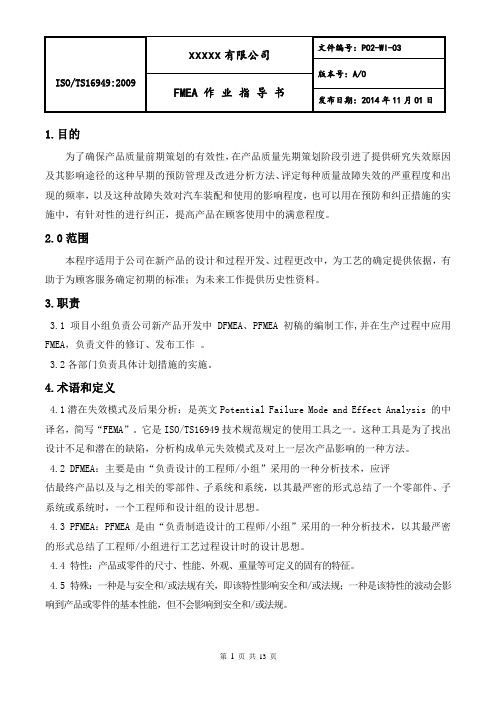
1.目的为了确保产品质量前期策划的有效性,在产品质量先期策划阶段引进了提供研究失效原因及其影响途径的这种早期的预防管理及改进分析方法、评定每种质量故障失效的严重程度和出现的频率,以及这种故障失效对汽车装配和使用的影响程度,也可以用在预防和纠正措施的实施中,有针对性的进行纠正,提高产品在顾客使用中的满意程度。
2.0范围本程序适用于公司在新产品的设计和过程开发、过程更改中,为工艺的确定提供依据,有助于为顾客服务确定初期的标准;为未来工作提供历史性资料。
3.职责3.1 项目小组负责公司新产品开发中DFMEA、PFMEA初稿的编制工作,并在生产过程中应用FMEA,负责文件的修订、发布工作。
3.2各部门负责具体计划措施的实施。
4.术语和定义4.1潜在失效模式及后果分析:是英文Potential Failure Mode and Effect Analysis 的中译名,简写“FEMA”。
它是ISO/TS16949技术规范规定的使用工具之一。
这种工具是为了找出设计不足和潜在的缺陷,分析构成单元失效模式及对上一层次产品影响的一种方法。
4.2 DFMEA:主要是由“负责设计的工程师/小组”采用的一种分析技术,应评估最终产品以及与之相关的零部件、子系统和系统,以其最严密的形式总结了一个零部件、子系统或系统时,一个工程师和设计组的设计思想。
4.3 PFMEA:PFMEA是由“负责制造设计的工程师/小组”采用的一种分析技术,以其最严密的形式总结了工程师/小组进行工艺过程设计时的设计思想。
4.4 特性:产品或零件的尺寸、性能、外观、重量等可定义的固有的特征。
4.5 特殊:一种是与安全和/或法规有关,即该特性影响安全和/或法规;一种是该特性的波动会影响到产品或零件的基本性能,但不会影响到安全和/或法规。
5.内容5.1 FMEA应用的要求5.1.1 新设计、新技术或新过程。
FEMA的范围是全部设计、技术或过程5.1.2对现有设计或过程的修改(假设对现有设计或过程已有FMEA)。
FMEA 作业指导书
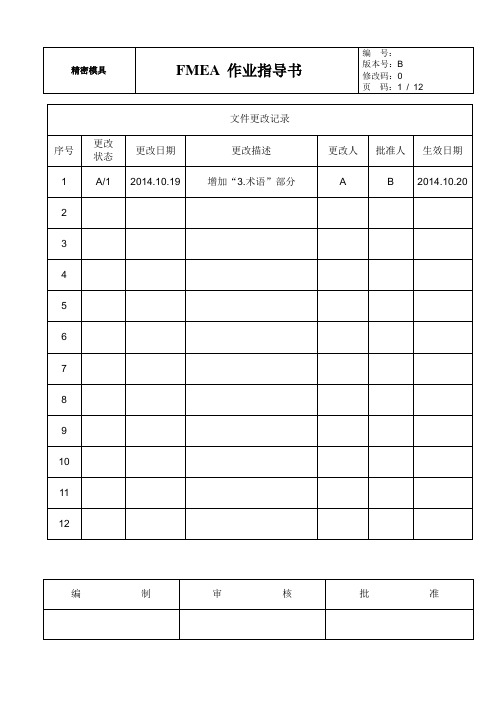
1. 目的:1.1 对新产品进行潜在失效分析,确定可能的失效模式(特别是高风险失效模式),找出可能的失效原因,研究其失效模式对系统产生的影响,为工装设计、制造、品质控制等方面提供依据,并采取相应预防纠正措施;1.2 推动过程改进作为主要目标,重点在防错方法。
2. 范围:2.1 适用于组织开发的所有新产品;2.2 适用于组织所有量产产品,特别是存在高返修费用、召回、不合格和客户抱怨的产品。
3. 术语:3.1 D/P FMEA或PFMEA:Process Potential Failure Mode and Effects Analysis 过程潜在的失效模式及后果分析;3.2 顾客:FMEA中“顾客”的定义通常是指“最终使用者”,然而顾客也可以是随后或下游的制造或装配工序,维修工或政府法规;3.3 防错(POKA-YOKE):是一种消除错误的技术,通常称之为“防止失效”,应作为控制重复性任务或行为的预防性技术,用来消除顾客的忧虑;3.4 变差:由人、设备、材料、方法与环境等原因造成的产品目标值与实际值之间的差异。
变差可分为普通原因变差与特殊原因变差。
普通原因变差是一直在过程中出现的变差,被认为系统是稳定的和可预测的。
特殊原因变差是指过程、产品或服务特性之中那些由“异常”或“外部”事件产生的,在普通原因变差之上或之外的变差,使得过程不可预测。
3.5 过程更改:在过程概念上的更改,是指能够改变过程能力以满足设计要求或产品的耐久性。
4. 职责:4.2 APQP小组负责PFMEA的评审;4.3 生产部技术员负责量产后PFMEA的评审;5. 流程图:(无)6. 内容:6.1 PFMEA的理解:·一种分析技术,用以最大限度地保证从单个部件到总成的所有的制造工序过程中各种潜在的失效模式及其相关起因/机理已得到充分的考虑和论述;·一份动态文件,需要不断的进行修订和评审;·在新产品开发策划阶段,促进对新的或更改的过程进行早期评审和分析,以便预测、解决或监控潜在的过程问题;·D/P FMEA假定所设计的产品能够满足设计要求,因设计的薄弱环节而产生的潜在失效模式可包括在D/P FMEA中,而其后果和避免包括在设计FMEA当中;·D/P FMEA不依靠改变产品设计来克服过程中的薄弱环节,但是他的确要考虑与计划的制造或装配过程有关的产品设计特性,以最大限度的保证产品能够满足顾客的要求和期望;·FMEA信息来源:相关工程技术人员之经验、曾发缺陷经验、顾客抱怨、厂内不良再发防止对策、内部报告、改善报告等。
FMEA编制作业指导书

文件编号JH-GL-GC-046编制工程部批准黄剑1.目的根据《风险和机遇控制程序》里的要求,特制定潜在失效模式作业指导书,本指导书规定了潜在失效模式报告的编制要求及方法。
2.范围适用于公司所有产品FMEA的编制和实施,包含设计、打样、试生产和批量生产阶段。
3.术语DFMEA:设计潜在失效模式。
PFMEA:过程潜在失效模式。
4.职责4.1 研发部负责牵头与设计或变更有关FMEA的编制和修订工作。
4.2 工程部负责牵头过程或工艺改进有关的FMEA的编制和修订工作。
4.3 研发部、生产部、工程部、质管部等都参与到过程与设计FMEA的讨论、制作和修改。
5. 编制和修订FMEA的时机5.1设计过程中需编制设计FMEA,避免出现以往的失误和设计可能出现的误区,以便使设计过程最佳,节约设计成本。
5.2 试生产时需要编制过程FMEA,借鉴以往的最优控制经验,使试生产过程风险可控。
5.3 在试生产结束后升级试生产过程FMEA到量产过程FMEA,总结试生产遇到的问题,增加或优化到量产的过程FMEA中。
5.4 量产中遇到质量问题时或客户投诉质量问题时需不断完善过程FMEA。
5.5产品更改、过程更改、顾客反馈的信息以及纠正和预防措施对FMEA有影响时,需重新进行FMEA分析与修订。
6. FMEA的分析对象FMEA的优先分析对涉及风险系数较大的工艺过程的工序。
7. FMEA 的编制7.1明确设计/过程FMEA表中各栏目的含义:a) 设计/过程功能要求:工序号、工序名称和该工序主要的工作内容。
b) 潜在失效模式:可能出现不满足要求的缺陷形式。
c) 潜在失效的后果:通过分析缺陷形式给下道工序带来后果,推至最终顾客,首先确定给最终顾客带来的后果,然后是给下道工序带来后果。
d) 潜在失效的起因:造成缺陷形式的原因。
e) 现行设计/过程控制:现行对设计/过程所采用的控制方法,包括防错、过程控制和检验。
f) 建议措施:经过RPN,认为现行过程控制不足以控制过程,而提出的新的控制方法,包括防错、过程控制和检验。
FMEA和控制计划编制作业指导书1
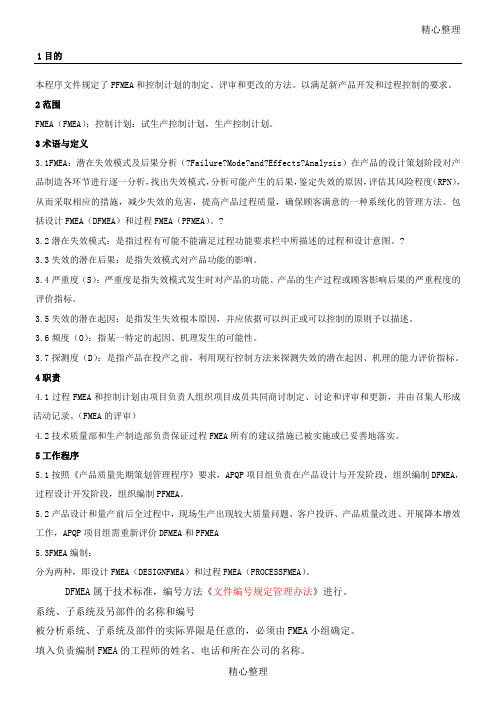
精心整理1目的本程序文件规定了PFMEA和控制计划的制定、评审和更改的方法。
以满足新产品开发和过程控制的要求。
2范围FMEA(FMEA);控制计划:试生产控制计划,生产控制计划。
3术语与定义3.1FMEA:潜在失效模式及后果分析(?Failure?Mode?and?Effects?Analysis)在产品的设计策划阶段对产品制造各环节进行逐一分析,找出失效模式,分析可能产生的后果,鉴定失效的原因,评估其风险程度(RPN),括设计3.23.33.43.53.63.74职责4.1过程4.255.1DFMEA,5.2产品设计和量产前后全过程中,现场生产出现较大质量问题、客户投诉、产品质量改进、开展降本增效工作,APQP项目组需重新评价DFMEA和PFMEA5.3FMEA编制:分为两种,即设计FMEA(DESIGNFMEA)和过程FMEA(PROCESSFMEA)。
DFMEA属于技术标准,编号方法《文件编号规定管理办法》进行。
系统、子系统及另部件的名称和编号被分析系统、子系统及部件的实际界限是任意的,必须由FMEA小组确定。
填入负责编制FMEA的工程师的姓名、电话和所在公司的名称。
填入所分析的设计将要应用和/或影响的车型年/项目(如已知的话)。
填入初次DFMEA应完成的日期,不超过计划的产品批量生产设计发布日期。
填入初稿(第一稿)完成的日期,和最新修订日期。
列出所有确定和/或执行任务的责任部门的名称和个人姓名。
填入被分析项目的名称和其它相关信息。
用尽可能简明的文字说明被分析项目满足设计意图的功能,包括该系统运行环境相关的信息。
指部件、子系统或系统有可能会未达到或不能实现项目/功能栏中所描述的预期功能的情况(如预期项目功能失效)指某一特定的起因/机理在设计寿命内出现的可能性,见表二。
表二:频度(O)的评价准则列出已经完成或承诺要完成的预防措施、设计确认/验证或其它活动,并且这些活动将确保设计对于所考虑的失效模式和/或起因/机理是足够的。
制造和装配过程FMEA作业指导书
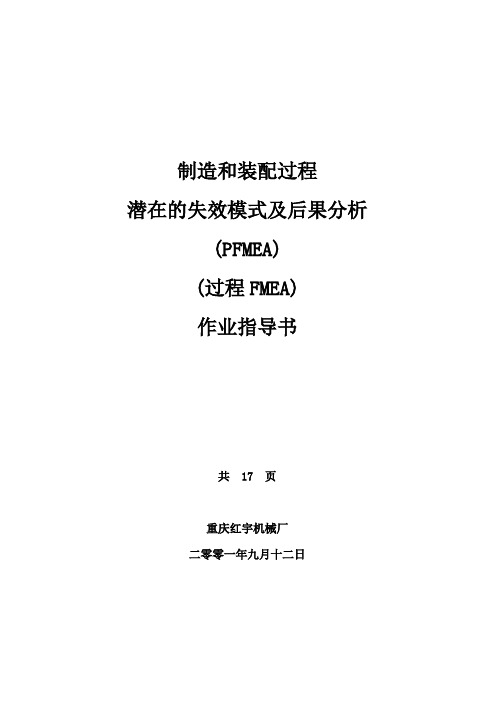
很轻微
生产线破坏轻微,部分产品(少于100%)需要在生产线原工位返工,装配、涂装或卡嗒响等项目不符合要求,很少有顾客能发现缺陷。
2
无
无影响很少
1
13)分级
本栏目是用来对需要附加过程控制的零部件、子系统或系统的一些特殊过程特性进行分级的(如关键、主要、重要、重点等)。如果在过程Байду номын сангаасMEA中确定了某一些分级,应通知设计主管工程师,因为它可能会影响有关确定控制基础上标识的工程文件。
失效发生可能性
可能的失效率
Cpk值
频度数
很高:失效几乎是不可避免的
≥1/2
<0.33
10
1/3
≥0.33
9
高:一般与以前经常反复发生失效过程相似的工艺有关
1/8
≥0.51
8
1/20
≥0.67
7
中等:一般与以前时有失效发生,但不占主要比例的过程相似的工艺有关
1/80
≥0.83
6
1/400
≥1.00
5
1/2000
9
很高
生产线严重破坏,可能100%的产品得报废,车辆/系统无法运行,丧失基本功能,顾客非常不满意。
8
高
生产线破坏不严重,产品需筛选部分(低于100%)报废,车辆/系统能运行,但性能下降,顾客不满意。
7
中等
生产线破坏不严重,部分(低于100%)产品报废(不筛选),车辆/系统能运行,但舒适性或方便性部件性项目失效,顾客感觉不舒服。
过程FMEA的开发
过程FMEA应从整个过程的流程图/风险评定〈见附录C〉开始。流程图应确定与每个过程有关的产品/过程特性参数。如果可能的话,还应根据相应的设计FMEA确定某些产品影响的内容。用于FMEA准备工作中的流程/风险评定图的复制件应伴随FMEA过程。
过程FMEA作业指导书
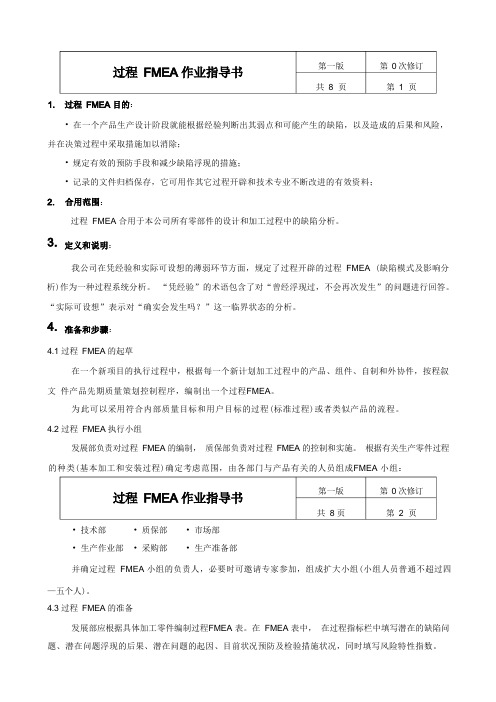
共 8 页:• 在一个产品生产设计阶段就能根据经验判断出其弱点和可能产生的缺陷,以及造成的后果和风险, 并在决策过程中采取措施加以消除;• 规定有效的预防手段和减少缺陷浮现的措施;• 记录的文件归档保存,它可用作其它过程开辟和技术专业不断改进的有效资料;:过程 FMEA 合用于本公司所有零部件的设计和加工过程中的缺陷分析。
:我公司在凭经验和实际可设想的薄弱环节方面,规定了过程开辟的过程 FMEA (缺陷模式及影响分析)作为一种过程系统分析。
“凭经验”的术语包含了对“曾经浮现过,不会再次发生”的问题进行回答。
“实际可设想”表示对“确实会发生吗?”这一临界状态的分析。
:4.1 过程 FMEA 的起草在一个新项目的执行过程中,根据每一个新计划加工过程中的产品、组件、自制和外协件,按程叙文 件产品先期质量策划控制程序,编制出一个过程FMEA 。
为此可以采用符合内部质量目标和用户目标的过程(标准过程)或者类似产品的流程。
4.2 过程 FMEA 执行小组发展部负责对过程 FMEA 的编制, 质保部负责对过程 FMEA 的控制和实施。
根据有关生产零件过程的种类(基本加工和安装过程)确定考虑范围,由各部门与产品有关的人员组成FMEA 小组:• 技术部• 生产作业部 • 质保部• 采购部 • 市场部• 生产准备部并确定过程 FMEA 小组的负责人,必要时可邀请专家参加,组成扩大小组(小组人员普通不超过四—五个人)。
4.3 过程 FMEA 的准备发展部应根据具体加工零件编制过程FMEA 表。
在 FMEA 表中, 在过程指标栏中填写潜在的缺陷问 题、潜在问题浮现的后果、潜在问题的起因、目前状况预防及检验措施状况,同时填写风险特性指数。
第 0 次修订第 2 页第一版共 8 页第 0 次修订第 1 页第一版质保部应组织 FMEA 小组讨论改进措施和方案,并根据所记录的数据以及每位组员的经验,评定缺 陷可能浮现的概率和缺陷对用户的影响,必要时补充其它缺陷、后果或者原因。
FMEA作业指导书
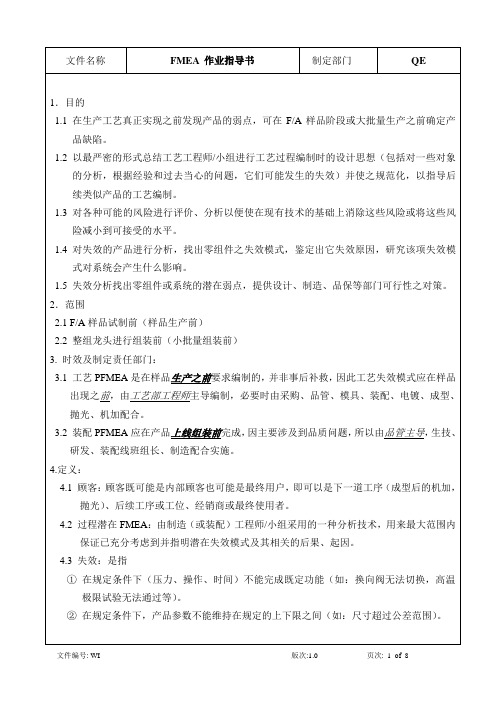
5.8过程功能/要求
填入要被分析的过程或工段(工序)简单的叙述(如:成型、车削、钻孔、攻牙、锁栓轴等)。叙述尽可能与被分析的过程或工序的目的一致;当过程包含多种工段或工序(如:成型、机加、抛光、电镀),存在不同的潜在失效模式时,要逐一分析每工段或工序可能的潜在失效模式列出来。
文件名称
PFMEA编制作业指导书
制定部门
副总室
PFMEA探测度评价准则:
探测性
准则
检查类别
探测方法的推荐范围
探测度
A
B
C
几乎不可能
绝对肯定不可能探测
X
不能探测或没有检查
10
很微小
控制方法可能探测不出来
X
只能通过间接或随机检查来实现控制
9
微小
控制有很少的机会能探测出
X
只通过目测检查来实现控制
8
很小
控制有很少的机会能探测出
注①严重度仅适用于评价后果;②严重度级别降低只能通过修改设计来实现;
文件名称
PFMEA编制作业指导书
制定部门
副总室
PFMEA严重度评价准则:
后果
评定准则:当潜在失效模式导致最终顾客和/或一个客户装配时(OEM件出货)产生缺陷便得出相应的定级结果。最终顾客永远是要首先考虑的;如果两种可能都存在的,采用两个严重度值中较高者。(顾客的后果)
(机加)100%需要返修但返修可能报废一部份
5
很低
配合和外观项目引起不舒服。多数(75%以上)顾客能发觉缺陷。(如:次要面严重撞伤、轻微的色差(需要借助仪器方可识别)、易识别的电镀不良)
(装配)产品可能需要分检,无需报废,但部分产品(小于100%)需要返工
FMEA编制作业指导书
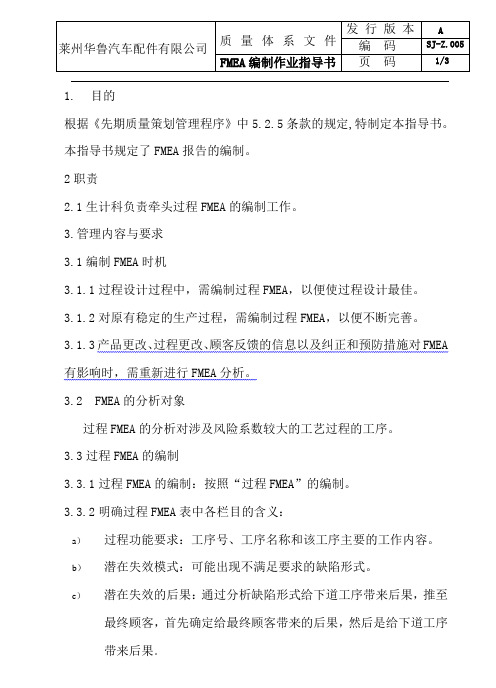
1.目的根据《先期质量策划管理程序》中5.2.5条款的规定,特制定本指导书。
本指导书规定了FMEA报告的编制。
2职责2.1生计科负责牵头过程FMEA的编制工作。
3.管理内容与要求3.1编制FMEA时机3.1.1过程设计过程中,需编制过程FMEA,以便使过程设计最佳。
3.1.2对原有稳定的生产过程,需编制过程FMEA,以便不断完善。
3.1.3产品更改、过程更改、顾客反馈的信息以及纠正和预防措施对FMEA 有影响时,需重新进行FMEA分析。
3.2 FMEA的分析对象过程FMEA的分析对涉及风险系数较大的工艺过程的工序。
3.3过程FMEA的编制3.3.1过程FMEA的编制:按照“过程FMEA”的编制。
3.3.2明确过程FMEA表中各栏目的含义:a)过程功能要求:工序号、工序名称和该工序主要的工作内容。
b)潜在失效模式:可能出现不满足要求的缺陷形式。
c)潜在失效的后果:通过分析缺陷形式给下道工序带来后果,推至最终顾客,首先确定给最终顾客带来的后果,然后是给下道工序带来后果。
d)潜在失效的起因:造成缺陷形式的原因。
e)现行过程控制:现行对过程所采用的控制方法,包括防错、过程控制和检验。
f)建议措施:经过RPN,认为现行过程控制不足以控制过程,而提出的新的控制方法,包括防错、过程控制和检验。
g)采取措施:经过分析,所落实的新的控制方法。
h)新RPN值:设想采取新的措施的RPN值,如果新的RPN值不能有效降低,应考虑执行其他改进措施。
i)FMEA编号:当前产品的加工过程,编制FMEA的版本次数,由三位数组成,如001,代表针对此过程,第一次编制FMEA。
3.3.3进行RPN分析a)当RPN值小于等于125,一般不采取措施,当出现c)款条件时,按条款c)执行b)当RPN值大于125,小于等于150时,可根据参数的重要性,采取或不采取措施。
c)当严重度大于8,同时频度或可探测度不同时小于及等于3时,应针对比较高的项目采取措施。
FMEA和控制计划编制作业指导书1
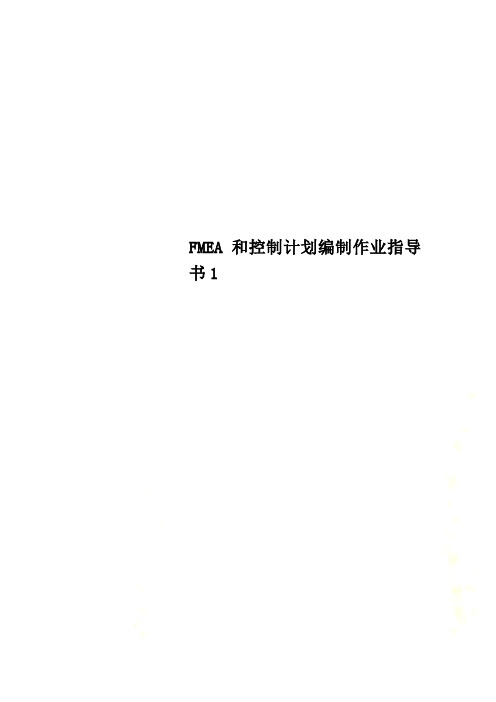
FMEA和控制计划编制作业指导书11目的本程序文件规定了PFMEA和控制计划的制定、评审和更改的方法。
以满足新产品开发和过程控制的要求。
2范围FMEA(FMEA);控制计划:试生产控制计划,生产控制计划。
3术语与定义3.1FMEA:潜在失效模式及后果分析(Failure Mode and Effects Analysis)在产品的设计策划阶段对产品制造各环节进行逐一分析,找出失效模式,分析可能产生的后果,鉴定失效的原因,评估其风险程度(RPN),从而采取相应的措施,减少失效的危害,提高产品过程质量,确保顾客满意的一种系统化的管理方法。
包括设计FMEA(DFMEA)和过程FMEA(PFMEA)。
3.2潜在失效模式:是指过程有可能不能满足过程功能要求栏中所描述的过程和设计意图。
3.3失效的潜在后果:是指失效模式对产品功能的影响。
3.4严重度(S):严重度是指失效模式发生时对产品的功能、产品的生产过程或顾客影响后果的严重程度的评价指标。
3.5失效的潜在起因:是指发生失效根本原因,并应依据可以纠正或可以控制的原则予以描述。
3.6频度(O):指某一特定的起因、机理发生的可能性。
3.7探测度(D):是指产品在投产之前,利用现行控制方法来探测失效的潜在起因、机理的能力评价指标。
4职责4.1过程FMEA和控制计划由项目负责人组织项目成员共同商讨制定、讨论和评审和更新,并由召集人形成活动记录。
(FMEA的评审)4.2技术质量部和生产制造部负责保证过程FMEA所有的建议措施已被实施或已妥善地落实。
5工作程序5.1按照《产品质量先期策划管理程序》要求,APQP项目组负责在产品设计与开发阶段,组织编制DFMEA,过程设计开发阶段,组织编制PFMEA。
5.2产品设计和量产前后全过程中,现场生产出现较大质量问题、客户投诉、产品质量改进、开展降本增效工作,APQP项目组需重新评价DFMEA和PFMEA5.3 FMEA编制:分为两种,即设计 FMEA(DESIGN FMEA)和过程 FMEA(PROCESS FMEA)。
FMEA作业指导书

1.目的通过产品设计或过程中可能产生的潜在失效及后果,寻找能避免或减少潜在失效发生的对策措施,从而及时消除实际的或潜在的不合格,最大限度地保证产品质量、降低成本,以满足顾客的要求。
2.适用范围适用于公司新产品、新工艺及其更改,以及由普通变差引起的质量问题对产品设计或工序过程可能造成失效后果的分析和预防。
3.权责3.1.技术部:负责组织设计、过程FMEA,制订相应对策措施。
3.2.模具设计课、生产部、采购课、品质部及相关部门:参与FMEA分析,并承担对策措施中的相应责任。
3.3.各生产部门:负责对策措施的实施。
3.4.项目副总:负责DFMEA、PFMEA对策的核准。
4.定义:4.1.FMEA:Potential Failure Mode and Effects Analysis(潜在失效模式及后果分析).4.2.DFMEA:设计FMEA4.3.PFMEA: 过程FMEA.4.4.RPN: 风险顺序数,RPN=严重度(S)*频度(O)*探测度(D)4.5.CFT:多功能小组4.6.CP: 控制计划5.作业内容5.1.FMEA流程图:无5.2.FMEA准备工作.5.2.1.DFMEA的准备工作.5.2.1.1.新项目评估时,根据客户要求制定,新项目可行性评估报告PPT档或DFMEA,由技术部负责组织,包含模具设计、品质部、生产部门及相关部门的技朮人员成立CFT小组,并指定一人为CFT小组组长,负责主导FMEA并跟进预防措施的施实.5.2.1.2.制定DFMEA 必须从所要分析的系统、子系统及/或零组件的方块图着手,故在制定DFMEA之前由项目工程师制定方块图,以做DFMEA分析时使用,此方块图应说明所要分析的各项目之间的主要关系,并建立一套合符逻辑的分析顺序,制定FMEA时,使用的方块图应附在FMEA中;5.2.2.PFMEA的准备工作5.2.2.1.由技术部负责组织,包含各生产部门,品质部及相关部门人员成立CFT小组,并指定一人为CFT小组组长, 负责主导FMEA并跟进预防措施的施实.5.2.2.2.初始过程流程图已确定,具体参考《产品先期策划与开发控制程序》执行,使用的流程图应附在FMEA中.5.2.2.3.特性矩阵图已确定,具体参考《产品先期策划与开发控制程序》执行.5.2.3.FMEA编号:按照《工程图纸技术文件管理作业指导书》执行。
FMEA作业指导书
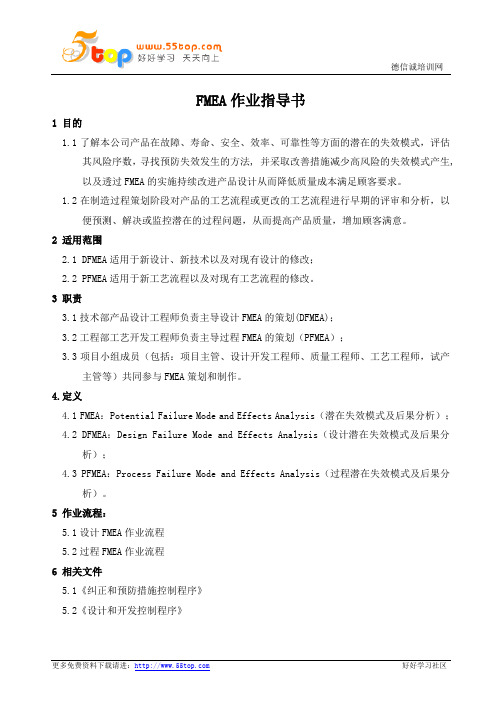
FMEA作业指导书1 目的1.1了解本公司产品在故障、寿命、安全、效率、可靠性等方面的潜在的失效模式,评估其风险序数,寻找预防失效发生的方法, 并采取改善措施减少高风险的失效模式产生, 以及透过FMEA的实施持续改进产品设计从而降低质量成本满足顾客要求。
1.2在制造过程策划阶段对产品的工艺流程或更改的工艺流程进行早期的评审和分析,以便预测、解决或监控潜在的过程问题,从而提高产品质量,增加顾客满意。
2 适用范围2.1 DFMEA适用于新设计、新技术以及对现有设计的修改;2.2 PFMEA适用于新工艺流程以及对现有工艺流程的修改。
3 职责3.1技术部产品设计工程师负责主导设计FMEA的策划(DFMEA);3.2工程部工艺开发工程师负责主导过程FMEA的策划(PFMEA);3.3项目小组成员(包括:项目主管、设计开发工程师、质量工程师、工艺工程师,试产主管等)共同参与FMEA策划和制作。
4.定义4.1 FMEA:Potential Failure Mode and Effects Analysis(潜在失效模式及后果分析);4.2 DFMEA:Design Failure Mode and Effects Analysis(设计潜在失效模式及后果分析);4.3 PFMEA:Process Failure Mode and Effects Analysis(过程潜在失效模式及后果分析)。
5 作业流程:5.1设计FMEA作业流程5.2过程FMEA作业流程6 相关文件5.1《纠正和预防措施控制程序》5.2《设计和开发控制程序》7 相关表单7.1 《设计FMEA资料收集表》7.2 《<设计FMEA表》7.3 《过程FMEA表》。
FMEA作业指导书
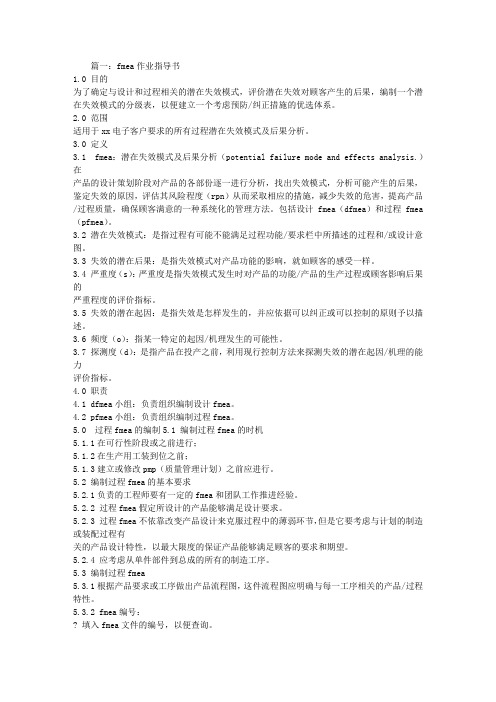
篇一:fmea作业指导书1.0 目的为了确定与设计和过程相关的潜在失效模式,评价潜在失效对顾客产生的后果,编制一个潜在失效模式的分级表,以便建立一个考虑预防/纠正措施的优选体系。
2.0 范围适用于xx电子客户要求的所有过程潜在失效模式及后果分析。
3.0 定义3.1 fmea:潜在失效模式及后果分析(potential failure mode and effects analysis.)在产品的设计策划阶段对产品的各部份逐一进行分析,找出失效模式,分析可能产生的后果,鉴定失效的原因,评估其风险程度(rpn)从而采取相应的措施,减少失效的危害,提高产品/过程质量,确保顾客满意的一种系统化的管理方法。
包括设计fmea(dfmea)和过程fmea (pfmea)。
3.2 潜在失效模式:是指过程有可能不能满足过程功能/要求栏中所描述的过程和/或设计意图。
3.3 失效的潜在后果:是指失效模式对产品功能的影响,就如顾客的感受一样。
3.4 严重度(s):严重度是指失效模式发生时对产品的功能/产品的生产过程或顾客影响后果的严重程度的评价指标。
3.5 失效的潜在起因:是指失效是怎样发生的,并应依据可以纠正或可以控制的原则予以描述。
3.6 频度(o):指某一特定的起因/机理发生的可能性。
3.7 探测度(d):是指产品在投产之前,利用现行控制方法来探测失效的潜在起因/机理的能力评价指标。
4.0 职责4.1 dfmea小组:负责组织编制设计fmea。
4.2 pfmea小组:负责组织编制过程fmea。
5.0 过程fmea的编制5.1 编制过程fmea的时机5.1.1在可行性阶段或之前进行;5.1.2在生产用工装到位之前;5.1.3建立或修改pmp(质量管理计划)之前应进行。
5.2 编制过程fmea的基本要求5.2.1负责的工程师要有一定的fmea和团队工作推进经验。
5.2.2 过程fmea假定所设计的产品能够满足设计要求。
FMEA作业指导书
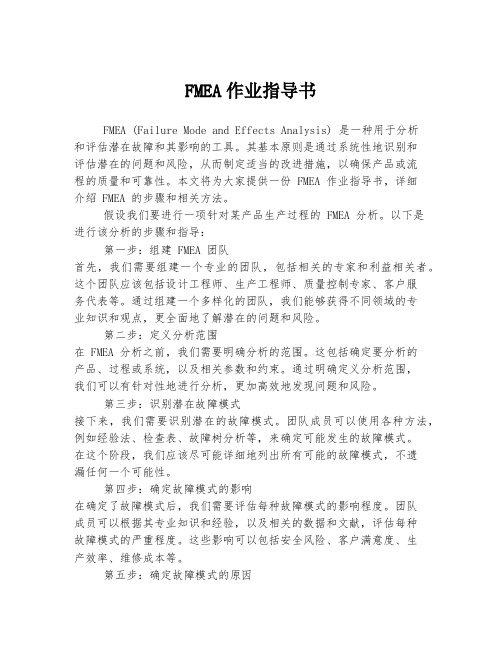
FMEA作业指导书FMEA (Failure Mode and Effects Analysis) 是一种用于分析和评估潜在故障和其影响的工具。
其基本原则是通过系统性地识别和评估潜在的问题和风险,从而制定适当的改进措施,以确保产品或流程的质量和可靠性。
本文将为大家提供一份 FMEA 作业指导书,详细介绍 FMEA 的步骤和相关方法。
假设我们要进行一项针对某产品生产过程的 FMEA 分析。
以下是进行该分析的步骤和指导:第一步:组建 FMEA 团队首先,我们需要组建一个专业的团队,包括相关的专家和利益相关者。
这个团队应该包括设计工程师、生产工程师、质量控制专家、客户服务代表等。
通过组建一个多样化的团队,我们能够获得不同领域的专业知识和观点,更全面地了解潜在的问题和风险。
第二步:定义分析范围在 FMEA 分析之前,我们需要明确分析的范围。
这包括确定要分析的产品、过程或系统,以及相关参数和约束。
通过明确定义分析范围,我们可以有针对性地进行分析,更加高效地发现问题和风险。
第三步:识别潜在故障模式接下来,我们需要识别潜在的故障模式。
团队成员可以使用各种方法,例如经验法、检查表、故障树分析等,来确定可能发生的故障模式。
在这个阶段,我们应该尽可能详细地列出所有可能的故障模式,不遗漏任何一个可能性。
第四步:确定故障模式的影响在确定了故障模式后,我们需要评估每种故障模式的影响程度。
团队成员可以根据其专业知识和经验,以及相关的数据和文献,评估每种故障模式的严重程度。
这些影响可以包括安全风险、客户满意度、生产效率、维修成本等。
第五步:确定故障模式的原因一旦确定了故障模式的影响程度,我们就需要找出造成该故障模式的原因。
团队成员可以使用原因分析工具,如鱼骨图、5W1H 分析等,来确定故障模式的潜在原因。
这些原因可以包括人为错误、设计缺陷、材料问题、操作不当等。
第六步:确定当前的控制措施在已经识别了故障模式和其潜在原因后,我们需要确定当前已经采取的控制措施。
FMEA作业指导书
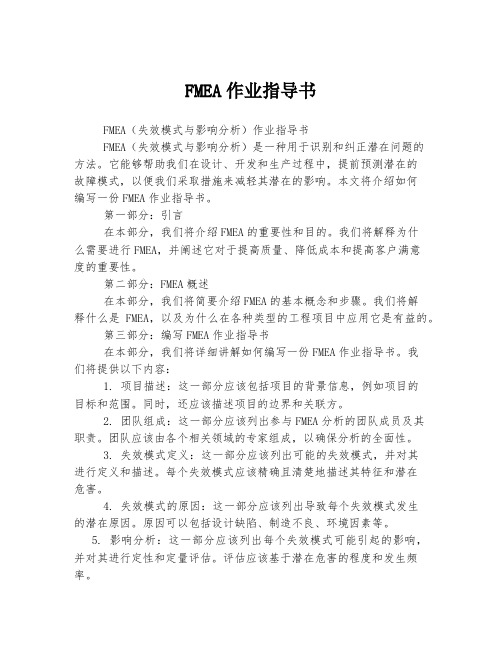
FMEA作业指导书FMEA(失效模式与影响分析)作业指导书FMEA(失效模式与影响分析)是一种用于识别和纠正潜在问题的方法。
它能够帮助我们在设计、开发和生产过程中,提前预测潜在的故障模式,以便我们采取措施来减轻其潜在的影响。
本文将介绍如何编写一份FMEA作业指导书。
第一部分:引言在本部分,我们将介绍FMEA的重要性和目的。
我们将解释为什么需要进行FMEA,并阐述它对于提高质量、降低成本和提高客户满意度的重要性。
第二部分:FMEA概述在本部分,我们将简要介绍FMEA的基本概念和步骤。
我们将解释什么是FMEA,以及为什么在各种类型的工程项目中应用它是有益的。
第三部分:编写FMEA作业指导书在本部分,我们将详细讲解如何编写一份FMEA作业指导书。
我们将提供以下内容:1. 项目描述:这一部分应该包括项目的背景信息,例如项目的目标和范围。
同时,还应该描述项目的边界和关联方。
2. 团队组成:这一部分应该列出参与FMEA分析的团队成员及其职责。
团队应该由各个相关领域的专家组成,以确保分析的全面性。
3. 失效模式定义:这一部分应该列出可能的失效模式,并对其进行定义和描述。
每个失效模式应该精确且清楚地描述其特征和潜在危害。
4. 失效模式的原因:这一部分应该列出导致每个失效模式发生的潜在原因。
原因可以包括设计缺陷、制造不良、环境因素等。
5. 影响分析:这一部分应该列出每个失效模式可能引起的影响,并对其进行定性和定量评估。
评估应该基于潜在危害的程度和发生频率。
6. 风险评估:这一部分应该根据影响分析,对每个失效模式的风险进行评估。
评估结果应该以可视化的方式展示,以便团队成员更好地理解。
7. 风险控制措施:这一部分应该列出针对每个失效模式采取的风险控制措施。
措施可以包括改进设计、制定新的工艺规程、加强监控等。
8. 跟踪计划:这一部分应该描述针对潜在故障模式的跟踪计划。
计划应包括责任人、跟踪频率和跟踪方法,以确保控制措施的有效性。
FMEA作业指导书
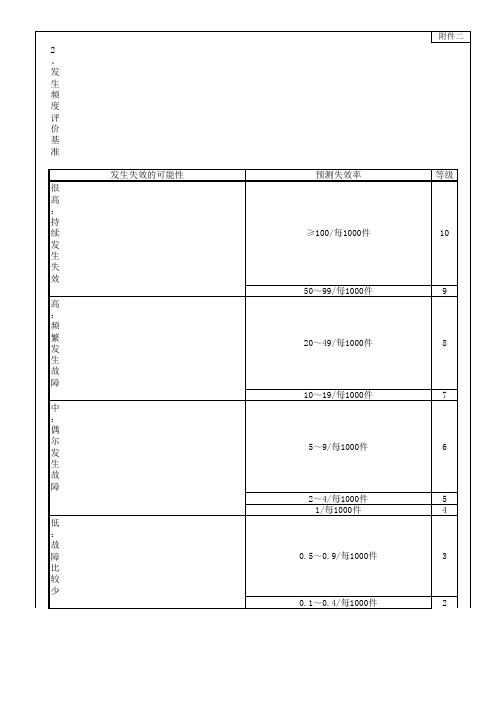
等级
10
9 8 7 6 5 4 3 2
更
低
:
不
可
能 发
0.1以下/每1000件
1
生
任
何
故
障
3 、 检 出 难 易 度 ( 探 测 度 ) 评 价 基 准
检出
几乎不可能
基准
的确是不能检验出来
检出方法 ABC
检出方法的范围
○ 不能检验出来,或不能检查
2 、 发 生 频 度 评 价 基 准
发生失效的可能性 很 高 : 持 续 发 生 失 效
高 : 频 繁 发 生 故 障
中 : 偶 尔 发 生 故 障
低 : 故 障 比 较 少
附件二
预测失效率
≥100/每1000件
50~99/每1000件 20~49/每1000件 10~19/每1000件 5~9/每1000件 2~4/每1000件
7
通过类似SPC(统计技术管理)那样的管理图
○ ○ 法来管理
6
有关外观等项目要进行目视确认
部品从作业场所出来后的变数的测定,或是将
部品从作业场所拿出来后,以实行的GO/NO-GO
○
规类调查为基准对部品100%进行管理。
5
对于稍微复杂的外观等项目,由经过充分培训
的作业员来确认
中上
通过管理检验出来的 可能性高
过;
3
对于较简单的外观等项目,由接受过充分培训
的作业员进行两次目视检查,稍微复杂的机能
项目要进行三次检查。
在作业场所内进行错误检查(自控制系统的自 动检测),不良品不能通过
2
机械制造公司FMEA作业指导书(失效模式)

机械制造公司FMEA作业指导书(失效模式)机械制造公司FMEA作业指导书(失效模式)1目的:使相关人员掌握FMEA的编写方法及如何运用FMEA来预防和改进缺陷2范围:2.1新产品量产前2.2材料变更时2.3生产设备及工装新购及变更时2.4工艺变更时3定义:3.1FMEA:失效模式与效应分析3.2DFMEA:设计失效模式与效应分析3.3PFMEA:过程失效模式与效应分析4职责FMEA的编制与修改均由多方论证小组完成5程序说明5.1说明5.1.1本公司无产品设计开发责任。
所有产品均按按客户的图纸/规范/相关标准书生产的,5.1.2厂部应尽可能地从客户处得到DFMEA,以作为本公司编制PFMEA时作参考之用5.2PFMEA的表格格式5.2.1采用美国三大汽车之标准格式,多方论证小组根据本公司实际情况可将标准格式稍作修改。
具体见附件一5.3编制PFMEA的资料来源5.3.1客户的DFMEA5.3.2过程流程图(若无,则参考类似产品的过程流程图)5.3.3客户的图纸/规范等5.3.4本公司以往类似产品的PFMEA或经验5.3.5本公司以往客户抱怨或客户退货资料5.3.6本公司类似产品的不良率统计资料5.3.7设备及工装运行不良之统计资料5.4RPN的接收准则5.4.1RPN=S×O×D其中RPN为风险顺序数,S为严重程度数,O为频度数,D为不可探测度数5.4.2当RPN>100时,必须采取改进措施5.4.3当S≥6且100>RPN>60时,必须采取改进措施5.5严重程度数(S)之判定准则5.5.1严重程度数之判定准则见附件二5.5.2若有特殊特性之过程,其严重程度数(S)不能低于95.6频度数(O)之判定准则5.6.1频度数(O)之判定准则见附件三5.7不可探测度数(D)之判定准则5.7.1不可探测度数(D)之判定准则见附件四5.8PFMEA之修改5.8.1多方论证小组在量产时应定期对相应产品的PFMEA作修改,修改所需之资料见5.8.25.8.2PFMEA修改时,可参考以下资料a.该产品量产后之不良统计资料,这将涉及到(O)的改变b.该产品交付顾客后的顾客抱怨及退货资料,这将涉及到(O)和(D)的改变c.该产品量产时之设备与工装之运行不良之统计,因设备及工装运行不良将影响到产品的不良,这将影响到(O)及(D)的改变d.其它将影响RPN值改变的资料5.8.3PFMEA变化后,将影响控制计划、检查标准书及作业标准书的变化,所以多方论证小组将相应之控制计划、检查标准书和作业标准书进行修改,且按《文件与资料控制程序》的规定执行。
FMEA作业指导书
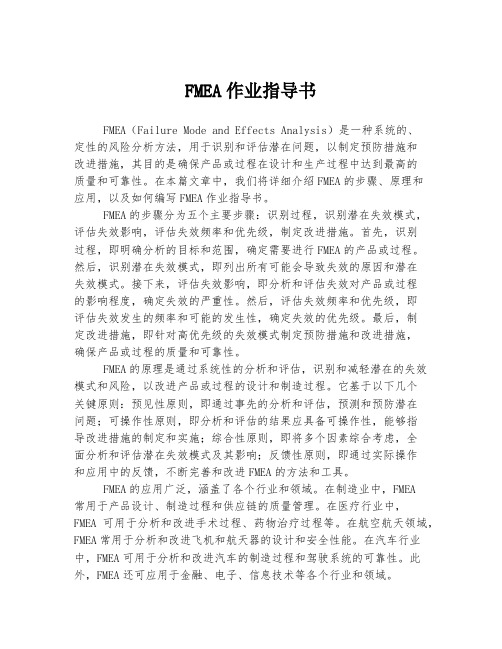
FMEA作业指导书FMEA(Failure Mode and Effects Analysis)是一种系统的、定性的风险分析方法,用于识别和评估潜在问题,以制定预防措施和改进措施,其目的是确保产品或过程在设计和生产过程中达到最高的质量和可靠性。
在本篇文章中,我们将详细介绍FMEA的步骤、原理和应用,以及如何编写FMEA作业指导书。
FMEA的步骤分为五个主要步骤:识别过程,识别潜在失效模式,评估失效影响,评估失效频率和优先级,制定改进措施。
首先,识别过程,即明确分析的目标和范围,确定需要进行FMEA的产品或过程。
然后,识别潜在失效模式,即列出所有可能会导致失效的原因和潜在失效模式。
接下来,评估失效影响,即分析和评估失效对产品或过程的影响程度,确定失效的严重性。
然后,评估失效频率和优先级,即评估失效发生的频率和可能的发生性,确定失效的优先级。
最后,制定改进措施,即针对高优先级的失效模式制定预防措施和改进措施,确保产品或过程的质量和可靠性。
FMEA的原理是通过系统性的分析和评估,识别和减轻潜在的失效模式和风险,以改进产品或过程的设计和制造过程。
它基于以下几个关键原则:预见性原则,即通过事先的分析和评估,预测和预防潜在问题;可操作性原则,即分析和评估的结果应具备可操作性,能够指导改进措施的制定和实施;综合性原则,即将多个因素综合考虑,全面分析和评估潜在失效模式及其影响;反馈性原则,即通过实际操作和应用中的反馈,不断完善和改进FMEA的方法和工具。
FMEA的应用广泛,涵盖了各个行业和领域。
在制造业中,FMEA常用于产品设计、制造过程和供应链的质量管理。
在医疗行业中,FMEA可用于分析和改进手术过程、药物治疗过程等。
在航空航天领域,FMEA常用于分析和改进飞机和航天器的设计和安全性能。
在汽车行业中,FMEA可用于分析和改进汽车的制造过程和驾驶系统的可靠性。
此外,FMEA还可应用于金融、电子、信息技术等各个行业和领域。
FMEA作业指导书
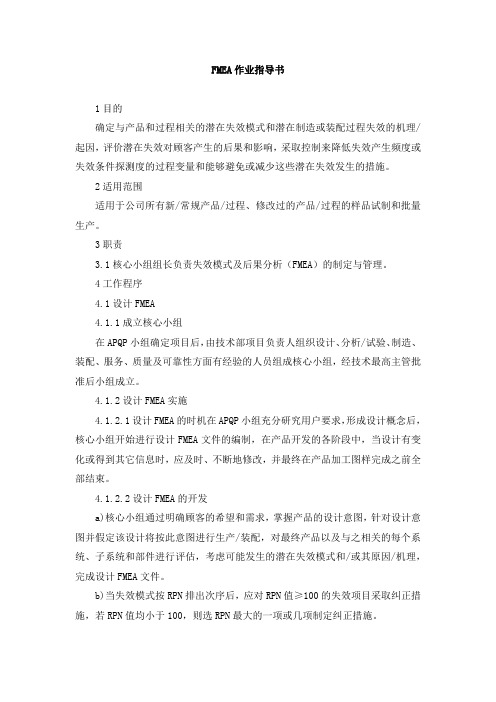
FMEA作业指导书1目的确定与产品和过程相关的潜在失效模式和潜在制造或装配过程失效的机理/起因,评价潜在失效对顾客产生的后果和影响,采取控制来降低失效产生频度或失效条件探测度的过程变量和能够避免或减少这些潜在失效发生的措施。
2适用范围适用于公司所有新/常规产品/过程、修改过的产品/过程的样品试制和批量生产。
3职责3.1核心小组组长负责失效模式及后果分析(FMEA)的制定与管理。
4工作程序4.1设计FMEA4.1.1成立核心小组在APQP小组确定项目后,由技术部项目负责人组织设计、分析/试验、制造、装配、服务、质量及可靠性方面有经验的人员组成核心小组,经技术最高主管批准后小组成立。
4.1.2设计FMEA实施4.1.2.1设计FMEA的时机在APQP小组充分研究用户要求,形成设计概念后,核心小组开始进行设计FMEA文件的编制,在产品开发的各阶段中,当设计有变化或得到其它信息时,应及时、不断地修改,并最终在产品加工图样完成之前全部结束。
4.1.2.2设计FMEA的开发a)核心小组通过明确顾客的希望和需求,掌握产品的设计意图,针对设计意图并假定该设计将按此意图进行生产/装配,对最终产品以及与之相关的每个系统、子系统和部件进行评估,考虑可能发生的潜在失效模式和/或其原因/机理,完成设计FMEA文件。
b)当失效模式按RPN排出次序后,应对RPN值≥100的失效项目采取纠正措施,若RPN值均小于100,则选RPN最大的一项或几项制定纠正措施。
c)执行纠正措施后,计算并记录RPN的结果。
如措施后的RPN级数仍≥100,应考虑采取进一步的措施,并对措施后的RPN再次评审。
4.1.3跟踪负责设计的工程师应负责保证所有的建议措施已被实施或已妥善地落实。
负责设计的工程师可采用以下几种方式来保证所关注的问题得到明确,所建议的测试得到实施:●保证设计要求达到得到实现;●评审工程图样和规范;●确认这些已反映在装配/生产文件之中;●评审过程FMEA和控制计划。
- 1、下载文档前请自行甄别文档内容的完整性,平台不提供额外的编辑、内容补充、找答案等附加服务。
- 2、"仅部分预览"的文档,不可在线预览部分如存在完整性等问题,可反馈申请退款(可完整预览的文档不适用该条件!)。
- 3、如文档侵犯您的权益,请联系客服反馈,我们会尽快为您处理(人工客服工作时间:9:00-18:30)。
生产线破坏不严重,产品需要100%返工,车辆 低 或系统能运行,但有些舒适性或方便性项目性能
下降,顾客有些不满意
很低
生产线破坏不严重,产品经筛选,部分(少于 100%)需要返工,配合、外观或尖响、卡嗒响 等项目不符合要求,多数顾客发现有缺陷
生产线破坏较轻,部分(少于100%)产品需要
严重度 数 10 9 8 7 6 5 4
很高
生产线严重破坏,可能100%的产品得报废,车 辆/系统无法运行,丧失基本功能,顾客非常不满 意
生产线破坏不严重,产品需筛选部分(低于 高 100%)报废,车辆能运行,但性能下降,顾客
不满意
中等
生产线破坏不严重,部分(低于100%)产品报 废(不筛选),车辆/系统能运行,但舒适性或方 便性项目失效,顾客感觉不舒适
FMEA报告编制作业指导书 1、 目的: 为了防止发生缺陷,消除或减少潜在失效发生,更好地指导FMEA报 告的编制,特制定本作业指导书。
二、编制FMEA的时机 1、 产品设计时,需编制DFMEA,以便使产品设计最佳; 2、 过程设计时,需编制PFMEA,以便使过程设计最佳; 3、 对原有稳定生产的过程,需编制PFMEA,以便不断完善。
系统、子系统、或零部件有可能未达到设计意图的形式;
11)潜在失效的后果:填入失效的后果对系统功能或顾客的影响; 12)严重度数(S):指发生潜在失效模式对下序零件、子系统、系统
或顾客影响的严重程度。评估分为1到10,可参照附表取值;
13)分级(重要程度):填入产品特性分级符号(如关键、安全、重 要等);
14)潜在失效的起因/机理:填入发生潜在失效模式的原因,典型的失效 起因可能包括但不限于:规定的材料不对、设计寿命估计不当、应 力过大、润滑不足、维修保养说明书不当、环境保护不够、计算错 误等;
15)频度数:指具体的失效起因/机理发生的频率,评估分为1到10,取 值可参照附表。通过设计更改来消除或控制一个或更多的失效起因/ 机理是降低频度数的唯一途径;
设计控制有中上多的机会能够找出潜在原因/ 中上 机理及后续的失效模式
不易探测 度数 10 8 7 6 5
4
多
设计控制有较多的机会能够找出潜在原因/机 理及后续的失效模式
3
很多
设计控制有很多机会能够找出潜在原因/机理 及后续的失效模式
2
几乎肯定
设计控制几乎肯定能够找出潜在原因/机理及 后续的失效模式
1/400 1/2000
1/15000
1/150000
≤1/1500000
Cpk <0.33 ≥0.33 ≥0.51 ≥0.67 ≥0.83 ≥1.00 ≥1.17 ≥1.33
≥1.50
≥1.67
频度数
10 9 8 7 6 5 4 3
2
1
不易探测度(D)
探测性
评价准则:在下一个或后续工艺前,或零部 件离开制造或装配工位之前,利用过程控制
轻微 在生产线上其它工位返工,配合、外观或尖响、 卡嗒响等项目不符合要求,有一半顾客发现有缺
3
陷
生产线破坏轻微,部分(少于100%)产品需要
很轻微 在生产线上其它工位返工,配合、外观或尖响、
2
卡嗒响等项目不符合要求,很少顾客发现有缺陷
无 无影响
1
频度(O): 失效发生的可能性
很高:失效几乎是不可避免的
有警告 这是一种非常严重的失效形式,是在具有失效预 的严重 兆的前提下所发生的,并影响到行车安全或违反 危害 了政府的有关章程
很高 车辆(或系统)不能运行,丧失基本功能
高
车辆(或系统)能运行,但性能下降,顾客不满 意
中等
车辆(或系统)能运行,但舒适性或方便性部件 不能工作,顾客感觉不舒服
低
车辆(或系统)能运行,但舒适性或方便性项目 性能下降,顾客感觉有些不舒服
三、FMEA的分析对象 1、DFMEA的分析对象主要为产品的特殊特性的设计参数; 2、PFMEA的分析对象主要为涉及特殊特性的工序。
四、DFMEA的编制 1、 DFMEA的编制是集体努力的结果,参加部门应包括但不限于 产品设计、装配、制造、材料、质量、售后服务;
2、 DFMEA是一份动态文件,应在一个设计概念最终形成之时或 之前开始,而且,在产品开发各阶段中,当设计有变化或得
子系统可空白,只填入所分析的零件名称和零件号;
3) 设计责任:填入技术开发部; 4) 编制者:填入负责FMEA编制工作的人员姓名及联系电话; 5) 年型/车型:填入零件适用的车型,若不知,此栏空白; 6) 关键日期:填入FMEA初次预定完成的日期; 7) FMEA日期:填入编制FMEA原始稿的日期及最新修订的日
很低
配合、外观或尖响、卡嗒响等项目不符合要求, 大多数顾客发现有缺陷
轻微
配合、外观或尖响、卡嗒响等项目不符合要求, 有一半顾客发现有缺陷
很轻微
配合、外观或尖响、卡嗒响等项目不符合要求, 但很少有顾客发现有缺陷
无 无影响
严重度 10
9 8 7 6 5 4 3 2 1
频度(O): 失效发生可能性
很高:失效几乎是不可避
10)潜在的失效模式:指过程可能发生的不满足过程要求或设计意图的 形式,是对某具体工序不符合要求的描述;
11)潜在的失效后果:指失效模式对顾客的影响,顾客可以是下一 道工序、后续工序、代理商、车主;
12)严重程度数:指潜在失效模式对顾客的影响后果的严重程度的评价 指标,仅适用于失效的后果。评估分为1到10,可参照附表取值;
程控制方法,或统计过程控制SPC,也可以是过程评价; 17)不可探测度数:用现行过程控制方法来探测潜在失效起因/机理 能力的评价指标。评估分为1到10,取值可参照附表; 18)风险顺序数RPN:指严重度数、频度数和不易探测度的乘积, 是对过程风险性的度量;
19)建议措施: RPN≤90时,可不采取措施,填写“无”;当严重度数(S)>8或 RPN≥125时,需采取纠正措施; 20)责任及目标完成日期:填写负责建议措施的人员及其部门,以 及预计完成的日期;
5
中上
现行控制方法找出失效模式的可能性中等偏 上
4
高 现行控制方法找出失效模式的可能性高
3很高 现行控制方法找出失Fra bibliotek模式的可能性很高
2
几乎肯定 现行工艺控制方法几乎肯定能找出失效模式
1
潜在的失效模式及后果分析
(设计FMEA)
系统工程
期;
8) 主要参加人员:填入主要参加人员的姓名及其部门; 9) 项目/功能:填入被分析项目要满足设计意图的功能,包括该
系统运行的环境信息(如说明温度、压力、湿度范围),如
果该项目有多种功能,且有不同的失效模式,应把所有功能
都单独列出;
10)潜在失效模式:对一个特定项目及其功能,列出每一个潜在失效模 式。前提是这种失效可能发生,但不是一定发生。潜在失效模式指
1
严重度(S): 后果
PFMEA推荐的评价准则 评定准则:后果的严重度
无警告 可能危害机器或装配操作者。潜在失效模式严重 的严重 影响车辆安全运行和/或包含不符合政府法规项, 危害 严重程度很高。失效发生时无警告
有警告 可能危害机器或装配操作者。潜在失效模式严重 的严重 影响车辆安全运行和/或包含不符合政府法规项, 危害 严重程度很高。失效发生时有警告
13)级别:指过程特性分级(如关键、主要、重要等),填入特殊 特性工序符号;
14)潜在的失效原因/机理:指失效发生的原因,并依据可以纠正或 控制的原则来描述;
15)频度数:指具体的失效起因/机理发生的频率,评估分为1到10, 取值可参照附表;
16)现行过程控制:是对尽可能阻止失效模式的发生,或探测将发生的 失效模式的控制的描述;这些控制方法可以是象防错夹具之类的过
中国最大的资料库下载
2、PFMEA是一份动态文件,应在生产工装准备之前,在过程可行 性分析阶段或之前开始,而且要考虑以单个零件到总成的所有制 造工序。在新车型或零件项目的制造计划阶段,对新工艺或修订 过的工艺进行早期评审和分析能够促进预测、解决或监控潜在过 程问题;
3、PFMEA是假定所有设计的产品会满足设计要求,因设计缺陷所 产生的失效模式不包含在PFMEA中。它们的影响及避免措施由 DFMEA来解决;
4、明确PFMEA表中各栏目的含义
1)PFMEA编号:按《技术文件编号方法》42QS5.2.1规定,一般由 综合工艺员给号;
2)项目名称:填入零件的名称、编号; 3)过程责任部门:填入技术开发部和主要生产分厂; 4)编制:填入负责编制工作的人员姓名及联系电话; 5)车型年/车辆类型:填入零件适用的车型,若不知,此栏空白; 6)关键日期:填入初次FMEA预定完成的日期; 7)FMEA日期:填入编制FMEA原始稿的日期及最新修订的日期; 8)主要参加人:列出主要参加人的姓名及其所在部门; 9)过程功能/要求:简单描述被分析的过程或工序,尽可能简单地说 明该工艺过程或工序的目的;
到其它信息时,应及时、不断地修改,并最终在产品图样完
成之前全部结束;
3、 明确DFMEA表格中各栏目的含义 1) FMEA编号:按《技术文件编号方法》42QS5.2.1规定,一般
由综合工艺员给号;
2) 系统、子系统或零部件的名称及编号:注明适当的分析级别 并填入所分析系统、子系统或零部件的名称、编号。系统、
可能的失效率 ≥1/2
频度数 10
免的
1/3
9
1/8
8
高:反复发生的失效
1/20
7
1/80
6
中等:偶尔发生的失效
1/400
5
1/2000
4
1/15000
3
低:相对很少发生的失效
1/150000
2
极低:失效不太可能发生
≤1/1500000