熔焊原理-7.1 Ferrite-to-Austenite Transformation in Austenitic Stainless Steel Welds
《熔化焊连接原理》课件

熔化焊的定义
熔化焊是一种通过加热工件将其熔化,并在冷却后形成连接的一种焊接方式。熔化焊可分为电弧焊、激光焊、 等离子焊等多种类型。
熔化焊技术的应用
熔化焊技术具有许多优点,如高强度、高效率和适用于不同材料等。在工业 生产中,熔化焊技术被广泛应用于汽车制造、航空航天和建筑等领域。
可视化演示
熔化焊过程的动画演示
通过动画演示,您将了解到熔化焊的整个过程,从 能量传递到熔池形成的所有细节。
熔化焊接头的X光检测图像展示
通过X光检测图像展示,您将了解到各种焊接缺陷、 接头质量以及焊缝内部结构的情况。
结束语
熔化焊作为一种重要的连接方式,在工业生产中起着关键作用。未来,熔化焊技术将不断发展,并应用于更多 领域,推动着工业的进步。
熔化焊的原理
熔化焊的能量来源包括电弧、激光束和等离子体等。熔化焊的熔池形成原理 与加热源的能量在焊接接头处传递和储存有关。
熔化焊的工艺参数
选择合适的焊接电源和参数对于熔化焊的成功非常重要。此外,选择适当的 焊接材料以及确定合理的焊接工艺参数也是关键。
熔化焊的缺陷与防治
熔化焊过程中可能出现熔池不稳定导致的缺陷,针对这些缺陷,我们需要采取相应的预防和处理措施。同时, 通过焊接接头质量检验方法,确保焊接连接的质量。
高温熔化焊接金属的原理
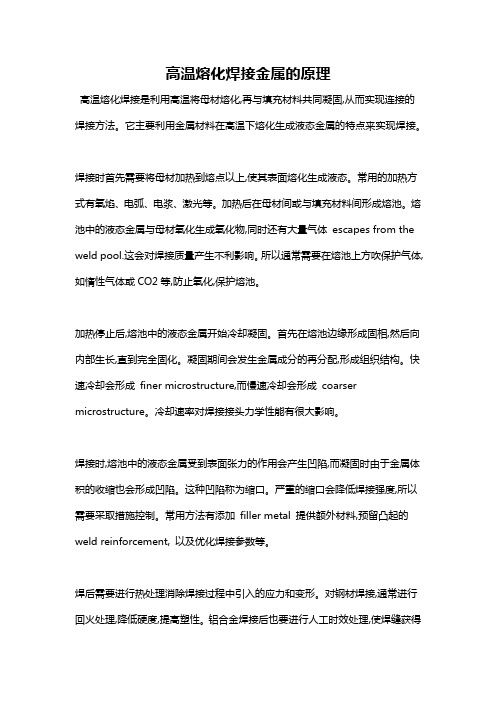
高温熔化焊接金属的原理高温熔化焊接是利用高温将母材熔化,再与填充材料共同凝固,从而实现连接的焊接方法。
它主要利用金属材料在高温下熔化生成液态金属的特点来实现焊接。
焊接时首先需要将母材加热到熔点以上,使其表面熔化生成液态。
常用的加热方式有氧焰、电弧、电浆、激光等。
加热后在母材间或与填充材料间形成熔池。
熔池中的液态金属与母材氧化生成氧化物,同时还有大量气体escapes from the weld pool.这会对焊接质量产生不利影响。
所以通常需要在熔池上方吹保护气体,如惰性气体或CO2等,防止氧化,保护熔池。
加热停止后,熔池中的液态金属开始冷却凝固。
首先在熔池边缘形成固相,然后向内部生长,直到完全固化。
凝固期间会发生金属成分的再分配,形成组织结构。
快速冷却会形成finer microstructure,而慢速冷却会形成coarser microstructure。
冷却速率对焊接接头力学性能有很大影响。
焊接时,熔池中的液态金属受到表面张力的作用会产生凹陷,而凝固时由于金属体积的收缩也会形成凹陷。
这种凹陷称为缩口。
严重的缩口会降低焊接强度,所以需要采取措施控制。
常用方法有添加filler metal 提供额外材料,预留凸起的weld reinforcement, 以及优化焊接参数等。
焊后需要进行热处理消除焊接过程中引入的应力和变形。
对钢材焊接,通常进行回火处理,降低硬度,提高塑性。
铝合金焊接后也要进行人工时效处理,使焊缝获得足够强度。
高温焊接还要注意防止热影响区过热。
HAZ 会产生粗大晶粒,导致强度下降。
严重时可能出现热裂纹。
所以需要控制焊接热输入量,优化焊接参数,并适当进行预热处理。
总之,高温焊接利用金属熔化特性实现连接。
但过程中也伴随着缺陷的产生,如气孔、裂纹、残余应力等。
要获得优良的焊接质量,需要选择合适的焊接方法, filler material, 焊接参数,并辅以符合要求的预热后热处理。
这需要对材料特性,焊接过程及金属学知识有充分理解,才能获得最佳效果。
第一节熔焊原理及过程.
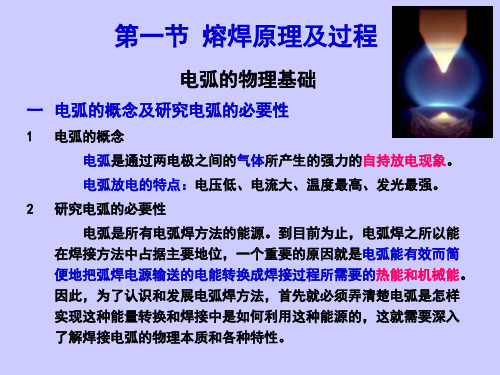
2.电场发射型 1)产生条件:当采用冷阴极(低熔点、沸点材料如铝、铁、铜等)或 虽然采用热阴极但使用较小电流时。原因:不可能加热到很高的温度, 不足以产生较强的热发射来提供弧柱导电所需要的电子流,则在靠近 阴极的区域,正电荷过剩而形成较强的正电场,并使阴极与弧柱之间 形成一个正电性区——阴极区。
3
(二)
阴极区的导电机构
阴极区的任务:向弧柱提供电子流和接收来自弧柱的正离子流,阴 极区的导电机构受气体介质、阴极材料、电流大小影响。
1.热发射型
1) 产生条件:当采用热阴极材料(高熔点、沸点材料如钨、碳)且使用 较大电流时,阴极区可加热到很高的温度,这时阴极主要靠热发射提 供电子流。 2) 特点:几乎不存在阴极区,阴极区不收缩,阴极区的电流密度与弧柱 区也相近,阴极区电压降很小;不存在阴极斑点;在大电流TIG焊时 这种热发射型导电占主导地位。
1
电子发射的基本概念 a. 定义:阴极中的自由电子受到一定的外加能量
作用时,从阴极表面逸出的过程称为电子发射。
b.
逸出功:电子从阴极表面逸出需要的最低外加
能量。1个电子从金属表面逸出所需要的最低外加能 量称为逸出功 (Wω),单位是电子伏。因电子电量为 常数e,故通常用逸出电压(Uω)来表示,Uω=Wω/e, 单位为V。逸出功的大小受电极材料种类及表面状态
U(V)
暗放电
1000 非自持放电
自持放电 辉光放电
电弧放电
I(A) I/A 10- 4 1
自持放电:当电流大于一定值时,一旦放电开始,气体导电过程本身 就可以产生维持导电所需要的带电粒子。
自持放电类型:暗放电(电池)、辉光放电(日光灯)、电弧放电 (焊接电弧)。
2 气体导电与金属导电的区别
一、熔焊原理
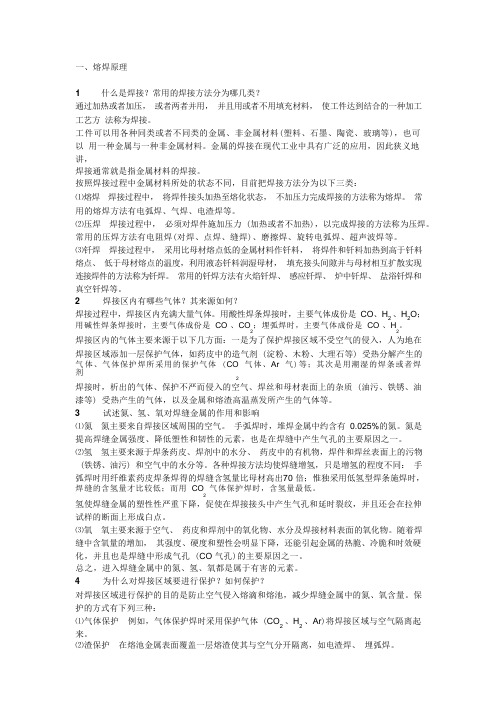
一、熔焊原理1 什么是焊接?常用的焊接方法分为哪几类?通过加热或者加压, 或者两者并用, 并且用或者不用填充材料, 使工件达到结合的一种加工工艺方 法称为焊接。
工件可以用各种同类或者不同类的金属、非金属材料(塑料、石墨、陶瓷、玻璃等),也可以 用一种金属与一种非金属材料。
金属的焊接在现代工业中具有广泛的应用,因此狭义地讲,焊接通常就是指金属材料的焊接。
按照焊接过程中金属材料所处的状态不同,目前把焊接方法分为以下三类:⑴熔焊 焊接过程中, 将焊件接头加热至熔化状态, 不加压力完成焊接的方法称为熔焊。
常 用的熔焊方法有电弧焊、气焊、电渣焊等。
⑵压焊 焊接过程中, 必须对焊件施加压力 (加热或者不加热),以完成焊接的方法称为压焊。
常用的压焊方法有电阻焊(对焊、点焊、缝焊)、磨擦焊、旋转电弧焊、超声波焊等。
⑶钎焊 焊接过程中, 采用比母材熔点低的金属材料作钎料, 将焊件和钎料加热到高于钎料 熔点、 低于母材熔点的温度,利用液态钎料润湿母材, 填充接头间隙并与母材相互扩散实现 连接焊件的方法称为钎焊。
常用的钎焊方法有火焰钎焊、 感应钎焊、 炉中钎焊、 盐浴钎焊和 真空钎焊等。
2 焊接区内有哪些气体?其来源如何?焊接过程中,焊接区内充满大量气体。
用酸性焊条焊接时,主要气体成份是 CO 、H 2 、H 2O ;用碱性焊条焊接时,主要气体成份是 CO 、CO ;埋弧焊时,主要气体成份是 CO 、H 。
2 2焊接区内的气体主要来源于以下几方面:一是为了保护焊接区域不受空气的侵入,人为地在 焊接区域添加一层保护气体,如药皮中的造气剂 (淀粉、木粉、大理石等) 受热分解产生的气体、气体保护焊所采用的保护气体 (CO 气体、Ar 气)等;其次是用潮湿的焊条或者焊剂2焊接时,析出的气体、保护不严而侵入的空气、焊丝和母材表面上的杂质 (油污、铁锈、油 漆等) 受热产生的气体,以及金属和熔渣高温蒸发所产生的气体等。
3 试述氮、氢、氧对焊缝金属的作用和影响⑴氮 氮主要来自焊接区域周围的空气。
金属熔焊原理(共10张PPT)

焊接热源
一、常用的焊接热源 电弧热 、 化学热 、 电阻热 、
摩擦热 、等离子弧 、电子束 、激光 束 、高频 热
二、常用的焊接热源
电弧热 、化学热 、电阻热 、摩擦 热 、等离子弧 、电子束 、激光束 、
高频感应热
三、焊接过程的热效率
在焊接热源作用下金属部分被加热与熔化,同时出现热量的传播和分布的景象。
我们把焊件〔包括母材与填充金 在焊接热源作用下金属部分被加热与熔化,同时出现热量的传播和分布的景象。
三、焊接过程的热效率 有效热功率是热源输出总功率的一部分。
属〕所吸收的热量叫做热源的有效 电弧热 、化学热 、电阻热 、摩擦热 、等离子弧 、电子束 、激光束 、高频感应热
在焊接热源作用下金属部分被加热与熔化,同时出现热量的传播和分布的景象。 1〕焊接热量集中作用在焊件衔接部位,而不是均匀加热整个焊件。
热功率。有效热功率是热源输出总 三、焊接过程的热效率
2〕热作用的瞬时性,焊接时,热源以一定速度挪动,焊件上把焊件〔包括母材与填充金属〕所吸收的热量叫做热源的有效热功率。
我们把焊件〔包括母材与填充金属〕所吸收的热量叫做热源的有效热功率。 电弧热 、化学热 、电阻热 、摩擦热 、等离子弧 、电子束 、激光束 、高频感应热 2〕热作用的瞬时性,焊接时,热源以一定速度挪动,焊件上任一点受热的作用都具瞬时性。 温度场的数学表达式可写作 2〕热作用的瞬时性,焊接时,热源以一定速度挪动,焊件上任一点受热的作用都具瞬时性。
焊接温度场
一、焊接温度场的定义 焊接温度场是指焊接过程中某一瞬时焊上
各点的温度分布。
温度场的数学表达式可写作 T = f (x,y,z ,t)
三、焊接温度场的特点
1、可用图形表示 , 2、等温线或等温面之间互不相交, 有温度梯度。
金属熔焊原理

焊接通过加热或加压,填充或不填充材料使工件产生原子间结合的一种连接方法焊剂:指焊接时能够融化形成熔渣,对融化金属起保护和冶金处理作用的一种颗粒状物质。
焊条:由药皮和焊芯组成的一种溶化电极,供焊条电弧焊使用。
熔渣:焊接过程中焊条药皮或焊剂荣华后,在熔池中参与化学反应而形成覆盖于熔池表面的熔融状金属、非金属氧化物及复合物。
熔合比:熔焊时,被熔化的母材部分在焊道金属中所占的比例称为熔合比焊条的型号:是国家标准中对焊条规定的编号,可用来区分各种焊条熔敷金属的力学性能、化学成分、药皮类型、焊接位置、焊接电流的种类。
热影响区:焊接过程中,母材因受焊接热循环影响而发生组织和力学性能变化的区域焊接区内存在多种气体,气体是通过哪些途径进入的?焊接区内除了外加的惰性保护气体外还有CO,CO2,H2O,O2,H2,N2,的混合物;焊接区内气体一部分是由直接输入或侵入的原始气体,而另一部分是通过物化反应所生成的气体。
酸性焊条和碱性焊条的区别?1.成分不同:酸性焊条皮中含有多量酸性氧化物(TiO2、SiO2 等),碱性焊条药皮中含有多量碱性氧化物(CaO、Na2O等)。
2.酸性焊条能交直流两用,碱性焊条焊接一般用直流电源施焊。
3.酸性焊条药皮组分氧化性强;而碱性焊条药皮组分氧化性弱。
4.酸性焊条工艺性能较好,但焊缝的力学性能,特别是冲击韧度较差,适用于一般低碳钢和强度较低的低合金结构钢的焊接,是应用最广的焊条。
5.碱性焊条脱硫、脱磷能力强,药皮有去氢作用。
碱性焊条的焊缝具有良好的抗裂性和力学性能,但工艺性能较差,一般用直流电源施焊,主要用于重要结构(如锅炉、压力容器和合金结构钢等)的焊接。
使熔池中液态金属运动的主要原因是什么?液态金属的密度差所产生的自由对流运动;表面张力差所引起的强制对流运动;热源的各种机械力所产生的搅拌作用,使熔池处于运动状态。
选择脱氧剂的原则是什么?1.脱氧剂在焊接的高温下对氧的亲和力应比被焊接金属对氧的亲和力大。
焊接的原理
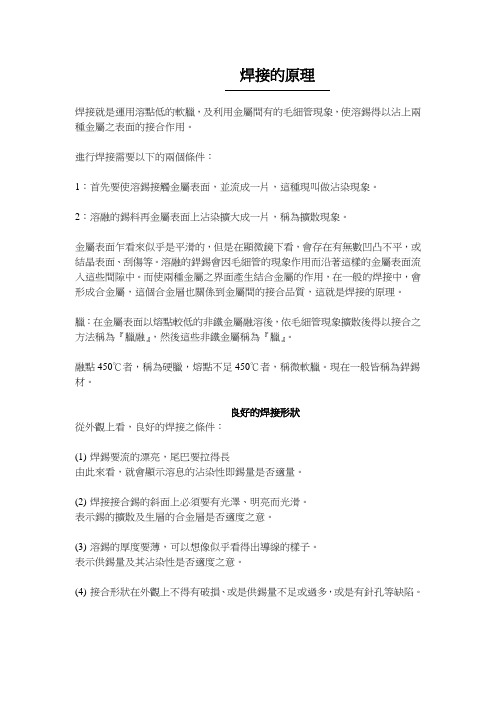
焊接的原理
焊接就是運用溶點低的軟臘,及利用金屬間有的毛細管現象,使溶錫得以沾上兩種金屬之表面的接合作用。
進行焊接需要以下的兩個條件:
1:首先要使溶錫接觸金屬表面,並流成一片,這種現叫做沾染現象。
2:溶融的錫料再金屬表面上沾染擴大成一片,稱為擴散現象。
金屬表面乍看來似乎是平滑的,但是在顯微鏡下看,會存在有無數凹击不平,或結晶表面、刮傷等。
溶融的銲錫會因毛細管的現象作用而沿著這樣的金屬表面流入這些間隙中。
而使兩種金屬之界面產生結合金屬的作用,在一般的焊接中,會形成合金屬,這個合金層也關係到金屬間的接合品質,這就是焊接的原理。
臘:在金屬表面以熔點較低的非鐵金屬融溶後,依毛細管現象擴散後得以接合之方法稱為『臘融』,然後這些非鐵金屬稱為『臘』。
融點450℃者,稱為硬臘,熔點不足450℃者,稱微軟臘。
現在一般皆稱為銲錫材。
良好的焊接形狀
從外觀上看,良好的焊接之條件:
(1)焊錫要流的漂亮,尾巴要拉得長
由此來看,就會顯示溶息的沾染性即錫量是否適量。
(2)焊接接合錫的斜面上必須要有光澤、明亮而光滑。
表示錫的擴散及生層的合金層是否適度之意。
(3)溶錫的厚度要薄,可以想像似乎看得出導線的樣子。
表示供錫量及其沾染性是否適度之意。
(4)接合形狀在外觀上不得有破損、或是供錫量不足或過多,或是有針孔等缺陷。
熔焊的原理及特点
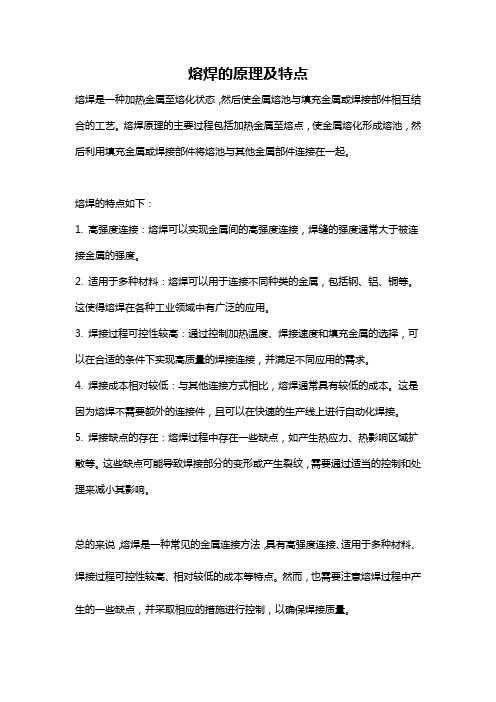
熔焊的原理及特点
熔焊是一种加热金属至熔化状态,然后使金属熔池与填充金属或焊接部件相互结合的工艺。
熔焊原理的主要过程包括加热金属至熔点,使金属熔化形成熔池,然后利用填充金属或焊接部件将熔池与其他金属部件连接在一起。
熔焊的特点如下:
1. 高强度连接:熔焊可以实现金属间的高强度连接,焊缝的强度通常大于被连接金属的强度。
2. 适用于多种材料:熔焊可以用于连接不同种类的金属,包括钢、铝、铜等。
这使得熔焊在各种工业领域中有广泛的应用。
3. 焊接过程可控性较高:通过控制加热温度、焊接速度和填充金属的选择,可以在合适的条件下实现高质量的焊接连接,并满足不同应用的需求。
4. 焊接成本相对较低:与其他连接方式相比,熔焊通常具有较低的成本。
这是因为熔焊不需要额外的连接件,且可以在快速的生产线上进行自动化焊接。
5. 焊接缺点的存在:熔焊过程中存在一些缺点,如产生热应力、热影响区域扩散等。
这些缺点可能导致焊接部分的变形或产生裂纹,需要通过适当的控制和处理来减小其影响。
总的来说,熔焊是一种常见的金属连接方法,具有高强度连接、适用于多种材料、焊接过程可控性较高、相对较低的成本等特点。
然而,也需要注意熔焊过程中产生的一些缺点,并采取相应的措施进行控制,以确保焊接质量。
金属熔焊原理
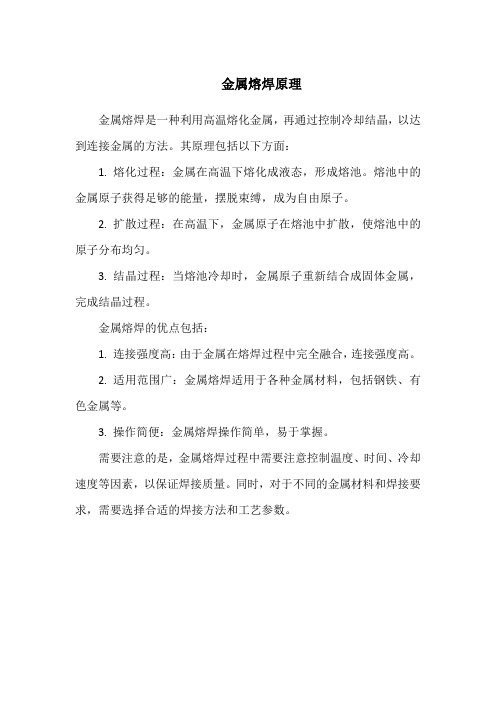
金属熔焊原理
金属熔焊是一种利用高温熔化金属,再通过控制冷却结晶,以达到连接金属的方法。
其原理包括以下方面:
1. 熔化过程:金属在高温下熔化成液态,形成熔池。
熔池中的金属原子获得足够的能量,摆脱束缚,成为自由原子。
2. 扩散过程:在高温下,金属原子在熔池中扩散,使熔池中的原子分布均匀。
3. 结晶过程:当熔池冷却时,金属原子重新结合成固体金属,完成结晶过程。
金属熔焊的优点包括:
1. 连接强度高:由于金属在熔焊过程中完全融合,连接强度高。
2. 适用范围广:金属熔焊适用于各种金属材料,包括钢铁、有色金属等。
3. 操作简便:金属熔焊操作简单,易于掌握。
需要注意的是,金属熔焊过程中需要注意控制温度、时间、冷却速度等因素,以保证焊接质量。
同时,对于不同的金属材料和焊接要求,需要选择合适的焊接方法和工艺参数。
金属熔焊原理

复习题一、1.焊接熔渣的作用有:机械保护作用、改善焊接工艺性能和冶金处理。
2.熔合比是熔焊时,熔化的母材在焊缝金属中所占的百分比。
熔合比越大,则母材的稀释作用越严重。
3.焊接结晶过程有一次结晶和二次结晶。
一次结晶主要是联生结晶,二次结晶组织主要取决于焊缝金属的化学成分和冷却速度。
4.焊接热循环的主要参数有加热速度、最高加热温度、相变温度以上停留时间和冷却速度。
5.氢、淬硬组织和应力三个因素是导致冷裂纹的主要原因。
6.焊缝金属的脱氧方法主要有先期脱氧、沉淀脱氧和扩散脱氧。
7.为了防止硫引起的结晶裂纹及其随含碳量的增加,则Mn/S的比值也应随之增加。
8.冷裂纹的断口从宏观上看,具有发亮的金属光泽,属脆性断裂,并呈人字纹形态发展。
9.在焊条药皮或焊剂中的萤石和有氧化性的氧化物都有去氢作用,但当氧化性的物质过多时,将增加产生 CO气孔的倾向。
二、选择题1.钨极氩弧焊和真空电子束焊的焊接反应区有(B)A熔滴反应区 B熔池反应区C药皮反应区、熔池反应区 D熔滴反应区、熔池反应区2.常用的牌号为H08Mn2SiA焊丝中的“Mn2”表示( C )。
A含锰量为0.02% B含锰量为0.2%C含锰量为2% D含锰量为20%3.埋弧自动焊属于( A )保护。
A渣保护 B气保护 C渣-气联合保护 D渣、气保护4.焊条药皮(焊剂)的氧化性和元素对氧的亲和力越大,合金元素含量对过渡系数的影响( A )A越大 B较小 C越小 D为零6.随着焊缝含( C )量的增加,会引起焊缝金属的热脆、冷脆和时效硬化。
A氢 B氧 C氮D硫7.焊条电弧焊焊时,当焊接电流增大时,则整个熔池的最大深度随之增大,而最大宽度将相对( B )A增大 B减小 C不变 D略大8.在一般情况下,通过焊丝药芯合金化时,过渡系数比通过药皮合金化时( C ) A大 B小 C无明显变化9.焊后消除应力的热处理方法是( A )A退火 B正火 C淬火 D回火10.液化裂纹主要出现在含合金元素较多的高强度钢,( B )和耐热合金的焊件中。
熔化焊加热原理

熔化焊加热原理
熔化焊是一种将金属材料连接在一起的方法,通过加热金属至
其熔点并加入填充材料,使它们冷却后形成一体。
熔化焊的加热原
理是如何实现的呢?我们将在本文中对熔化焊加热原理进行深入探讨。
首先,我们需要了解熔化焊的加热源。
加热源可以是火焰、电弧、激光或电子束等。
这些加热源都能提供足够的能量,使金属材
料达到熔点。
在选择加热源时,需要考虑材料的种类、厚度和加热
速度等因素。
其次,加热过程中需要考虑热传导和热损失。
热传导是指热量
在金属材料中的传播过程,而热损失则是指热量在加热过程中向周
围环境散失的现象。
在熔化焊加热过程中,需要控制加热源的温度
和加热时间,以确保金属材料能够均匀加热至熔点,同时尽量减少
热损失。
另外,填充材料的选择也对熔化焊加热原理产生影响。
填充材
料的熔点和流动性需要与金属材料相匹配,以确保焊接接头的质量。
在加热过程中,填充材料会与金属材料一起熔化,并填充到接头中,
形成坚固的连接。
除了以上因素,加热过程中的气氛环境也需要考虑。
气氛环境可以是惰性气体、氧化性气体或还原性气体等。
不同的气氛环境会对焊接接头的质量产生影响,需要根据具体情况进行选择和控制。
总的来说,熔化焊的加热原理涉及到加热源的选择、热传导和热损失的控制、填充材料的选择和气氛环境的调节等多个方面。
只有在这些因素都得到合理控制的情况下,才能实现高质量的熔化焊接头。
希望本文对熔化焊加热原理有所帮助,谢谢阅读。
安徽熔焊板换阿法拉伐换热器工作原理
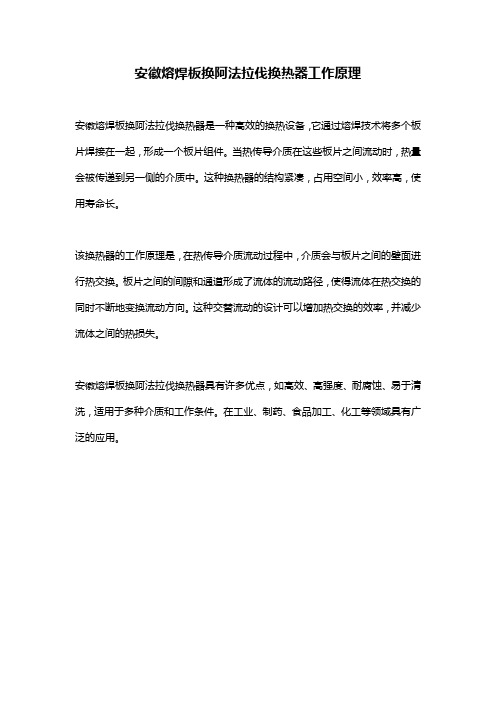
安徽熔焊板换阿法拉伐换热器工作原理
安徽熔焊板换阿法拉伐换热器是一种高效的换热设备,它通过熔焊技术将多个板片焊接在一起,形成一个板片组件。
当热传导介质在这些板片之间流动时,热量会被传递到另一侧的介质中。
这种换热器的结构紧凑,占用空间小,效率高,使用寿命长。
该换热器的工作原理是,在热传导介质流动过程中,介质会与板片之间的壁面进行热交换。
板片之间的间隙和通道形成了流体的流动路径,使得流体在热交换的同时不断地变换流动方向。
这种交替流动的设计可以增加热交换的效率,并减少流体之间的热损失。
安徽熔焊板换阿法拉伐换热器具有许多优点,如高效、高强度、耐腐蚀、易于清洗,适用于多种介质和工作条件。
在工业、制药、食品加工、化工等领域具有广泛的应用。
焊接工作原理

焊接工作原理
焊接是一种将两个或多个金属或非金属材料连接在一起的工艺。
它使用高温来加热材料,使其部分熔化,并在冷却后形成强固的连接。
焊接工作原理基于以下几个关键步骤:
1. 清洁表面:在焊接之前,需要先清洁连接部位的表面,以去除油脂、氧化物和其他杂质,以确保焊接的质量和强度。
2. 加热材料:焊接过程中需要加热要连接的材料。
这可以通过火焰、电子束、激光等不同的方法来完成。
加热材料的目的是使其局部熔化,并为焊接提供足够的热量。
3. 添加填充材料:在加热的过程中,焊工会将填充材料添加到焊缝中。
填充材料有助于填补间隙并提供强度和联结性。
4. 冷却:在将填充材料添加到焊缝后,焊接部位会逐渐冷却,形成一个坚固的连接。
冷却时间取决于所使用的材料和焊接方法。
焊接工作原理的关键是利用高温使材料部分熔化,然后使其冷却并形成强固的连接。
焊接过程中要注意控制温度、填充材料的选择以及焊接技术的正确应用,以确保焊接质量和可靠性。
除了金属材料,焊接还可以应用于连接塑料、玻璃和其他非金属材料。
熔渣焊接原理
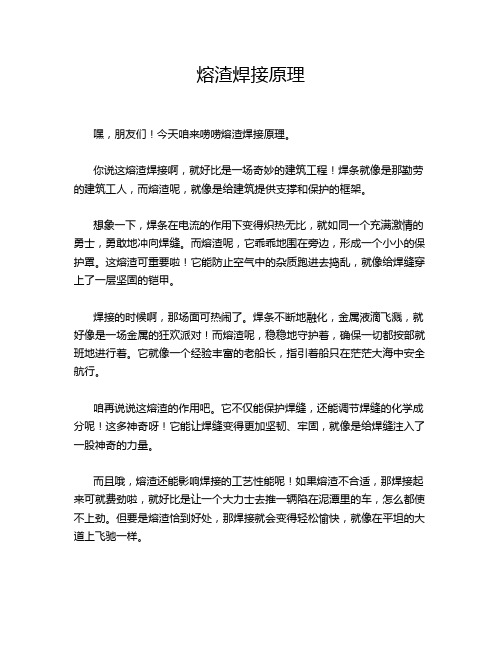
熔渣焊接原理嘿,朋友们!今天咱来唠唠熔渣焊接原理。
你说这熔渣焊接啊,就好比是一场奇妙的建筑工程!焊条就像是那勤劳的建筑工人,而熔渣呢,就像是给建筑提供支撑和保护的框架。
想象一下,焊条在电流的作用下变得炽热无比,就如同一个充满激情的勇士,勇敢地冲向焊缝。
而熔渣呢,它乖乖地围在旁边,形成一个小小的保护罩。
这熔渣可重要啦!它能防止空气中的杂质跑进去捣乱,就像给焊缝穿上了一层坚固的铠甲。
焊接的时候啊,那场面可热闹了。
焊条不断地融化,金属液滴飞溅,就好像是一场金属的狂欢派对!而熔渣呢,稳稳地守护着,确保一切都按部就班地进行着。
它就像一个经验丰富的老船长,指引着船只在茫茫大海中安全航行。
咱再说说这熔渣的作用吧。
它不仅能保护焊缝,还能调节焊缝的化学成分呢!这多神奇呀!它能让焊缝变得更加坚韧、牢固,就像是给焊缝注入了一股神奇的力量。
而且哦,熔渣还能影响焊接的工艺性能呢!如果熔渣不合适,那焊接起来可就费劲啦,就好比是让一个大力士去推一辆陷在泥潭里的车,怎么都使不上劲。
但要是熔渣恰到好处,那焊接就会变得轻松愉快,就像在平坦的大道上飞驰一样。
那怎么才能让熔渣乖乖听话,发挥出它最大的作用呢?这可就需要焊接师傅们的高超技艺和丰富经验啦!他们就像是指挥家,精准地掌控着每一个环节,让熔渣和焊条完美配合。
你说这熔渣焊接是不是很有意思?它虽然看起来普普通通,但其中蕴含的奥秘可不少呢!就像我们生活中的很多事情一样,看似平凡,实则有着非凡的意义。
所以啊,朋友们,可别小看了这熔渣焊接哦!它可是工业领域中不可或缺的一部分呢!它让我们的机器更加牢固,让我们的建筑更加坚固,为我们的生活提供了坚实的保障。
这不就是科技的魅力所在吗?它让我们的生活变得更加美好,更加精彩!原创不易,请尊重原创,谢谢!。
熔焊原理的课件

T=f(x,y,z,t) 式中 T——某瞬时焊件上某点的温度;
x,y,z——焊件上某点的空间坐标 t——时间 把焊件上瞬时温度相同的各点连接在一起,或为一条线或一个面就称为等 温线或等温面。
焊接条件下选取的平均值
低碳钢、低合金 不锈钢
铝
钢
λ
W/(㎝.℃) 0.378-0.504
0.168-0.336 2.65
C
J/(g.℃)
0.625-0.756
0.42-0.50 1.0
cρ
J/(㎝3.℃) 4.83-5.46
3.36-4.2
2.63
α=λ/ cρ ㎝2/s
0.07-0.10
0.05-0.07 1.001 温度梯度 在不同的方向上有着不同的温度变化率。但是,只有在法线nn的方向上,
温度变化率最大。所以,在法线方向上的温度变化率就是温度梯度。温度梯 度是一个向量,它的方向是在法线上,指向温度增加的方向。 2 温度场的分类
按照焊件上各点温度与时间的关系来分 : 1)稳定温度场 焊件上各点的温度不随时间而变化。即温度场只与焊件各 点的位置有关。其表达试为: T=f (x,y,z ) 2) 非稳定温度场 焊件上各点的温度随时间而变化。前面所分析的焊接温 度场就属于此类。 3)准稳定温度场 当热源温度不变,焊接过程进行了一个阶段以后,焊件传 热达到了饱和状态,形成了暂时稳定的温度场。例如固定热源在补焊缺陷时 就会出现这种情况。对于正常焊接条件的移动热源,在经过一定时间以后, 焊件也会形成准稳定温度场。这时焊件上各点的温度虽然随时间而变化,但 各个点温度能跟随热源一起移动,也就是这个温度场与热源以同样的速度向 前移动着。 按照焊件尺寸和热源性质来分 1)一维温度场 对焊条或焊丝加热,细棒的电阻焊对接,温度场均属于一 维的。 2)三维温度场 对于厚大焊件表面上的堆焊,可以把热源看成一个点,热 的传播是在空间的三个方向上。
- 1、下载文档前请自行甄别文档内容的完整性,平台不提供额外的编辑、内容补充、找答案等附加服务。
- 2、"仅部分预览"的文档,不可在线预览部分如存在完整性等问题,可反馈申请退款(可完整预览的文档不适用该条件!)。
- 3、如文档侵犯您的权益,请联系客服反馈,我们会尽快为您处理(人工客服工作时间:9:00-18:30)。
7.1 Ferrite-to-Austenite Transformation in Austenitic Stainless Steel Welds7.1.1 Primary Solidification ModesThe welds of austenitic stainless steels normally have an austenite (fcc) matrix with varying amounts of δ-ferrite (bcc). A proper amount of δ-ferrite in austenitic stainless steel welds is essential-too much δ-ferrite (≥10 vol %) tends to reduce the ductility, toughness, and corrosion resistance, while too little δ-ferrite (≤5 vol %) can result in solidification cracking.A.Phase DiagramFigure 7.1 The Fe-Cr-Ni ternary system: (a) liquidus surface; (b) solidus surface Figure 7.1 shows the ternary phase diagram of the Fe-Cr-Ni system. The heavy curved line in Figure 7.1a represents the trough on the liquidus surface, which is called the line of twofold saturation. The line declines from the binary Fe-Ni peritecticreaction temperature to the ternary eutectic point at 49Cr-43Ni-8Fe.Alloys with a composition on the Cr-rich (upper) side of this line have δ-ferrite as the primary solidification phase, that is, the first solid phase to form from the liquid. On the other hand, alloys with a composition on the Ni-rich (lower) side have austenite as the primary solidification phase. The heavy curved 1ines on the solidus surface in Figure 7.1b more or less follow the trend of the liquidus trough and converge at the ternary eutectic temperature.Figure 7.2 Schematics showing solidification and postsolidification transformation in Fe-Cr-Ni welds: (a) interdendritic ferrite; (b) vermicular ferrite; (c) lathy ferrite; (d) vertical section ofternary-phase diagram at approximately 70% Fe.The development of weld metal microstructure in austenitic stainless steels is explained in Figure 7.2. The weld metal ferrite can have three different types of morphology: interdendritic (Figure 7.2a), vermicular (Figure 7.2b), and lathy (Figure 7.2c). Figure 7.2d shows a schematic vertical (isoplethal) section of the ternary phase diagram in Figure 7.1, for instance, at 70 wt % Fe and above 1200°C. This has also been called a pseudo-binary phase diagram. The apex (point 1) of the three-phase eutectic triangle (L+γ+δ) corresponds to the intersection between the vertical section and the heavy curved line in Figure 7.1a.The two lower corners (points 2 and 3) of the triangle, on the other hand, correspond to the intersections between the vertical section and the two heavy curved lines in Figure 7.1b.B. Primary Austenite For an alloy on the Ni-rich (left-hand) side of the apex of the three-phase eutectic triangle, austenite (γ) is the primary solidification phase. Thelight dendrites shown in Figure 7.2a are austenite, while the dark particles between the primary dendrite arms are the δ-ferrite that forms when the three-phase triangle is reached during the terminal stage of solidification. These are called the interdendritic ferrite. For dendrites with long secondary arms, interdendritic ferrite particles can also form between secondary dendrite arms.C. Primary Ferrite For an alloy on the Cr-rich (right-hand) side of the apex of the three-phase eutectic triangle, δ-ferrite is the primary solidification phase. The dark dendrites shown in Figure 7.2b are δ-ferrite. The core of the δ-ferrite dendrites, which forms at the beginning of solidification, is richer in Cr (point 4), while the outer portions, which form as temperature decreases, have lower chromium contents. Upon cooling into the (δ+γ) two-phase region, the outer portions of the dendrites having less Cr transform to austenite, thus leaving behind Cr-rich “skeletons” of δ-ferrite at the dendrite cores. This skeletal ferrite is called vermicular ferrite. In addition to vermicular ferrite, primary δ-ferrite dendrites can also transform to lathy or lacy ferrite upon cooling into the (δ+γ) two-phase region, as shown in Figure 7.2c.D. Weld Microstructure Figure 7.3a shows the solidification structure at the centerline of an autogenous gas-tungsten arc weld of a 310 stainless steel sheet, which contains approximately 25% Cr, 20% Ni, and 55% Fe by weight. The composition is on the Ni-rich (left) side of the apex of the three-phase eutectic triangle, as shown in Figure 7.4a, and solidification occurs as primary austenite. The microstructure consists of austenite dendrites (light etching; mixed-acids etchant) and interdendritic δ-ferrite (dark etching; mixed-acids etchant) between the primary and secondary dendrite arms, similar to those shown in Figure 7.2a.Figure 7.3b, on the other hand, shows the solidification structure at the centerline of an autogenous gas-tungsten arc weld of a 309 stainless steel sheet, which contains approximately 23 wt% Cr, 14 wt% Ni, and 63 wt % Fe. The composition lies just to the Cr-rich side of the apex of the three-phase eutectic triangle, as shown in Figure 7.4b, and solidifies as primary δ-ferrite. The microstructure consists of vermicular ferrite (dark etching; mixed-acids etchant) in an austenite matrix (light etching; mixed-acids etchant) similar to those shown in Figure 7.2b. In both welds columnar dendrites grow essentially perpendicular to the teardrop-shaped pool boundary as revealed by the columnar dendrites.Kou and Le quenched welds during welding in order to preserve the as-solidified microstructure, that is, the microstructure before post-solidification phase transformations. For stainless steels liquid-tin quenching is more effective than water quenching because steam and bubbles reduce heat transfer. With the help of quenching, the evolution of microstructure during welding can be better studied. Figure 7.5 shows the δ-ferrite dendrites (light etching; mixed-chloride etchant) near the weld pool of an autogenous gas-tungsten arc weld of 309 stainless steel, quenched in during welding with liquid tin before the δ→γtransformation changed it to vermicular ferrite like that shown in Figure 7.3b. Liquid-tin quenching was subsequently used by other investigators to study stainless steel welds.Figure 7.3 Solidification structure at the weld centerline:(a) 310 stainless steel; (b) 309 stainless steel. Magnification 190×.Figure 7.4 The Fe-Cr-Ni pseudo-binary phase diagrams:(a) at 55 wt % Fe; (b) at 63wt % Fe; (c) at 73 wt % Fe.Figure 7.5 Liquid-tin quenched solidification structure near the pool of an autogenous gas-tungsten arc weld of 309 stainless steel. Magnification 70×. Mixed-chloride etchant.7.1.2 Mechanisms of Ferrite FormationInoue et al. studied vermicular and lathy ferrite in autogenous GTAW of austenitic stainless steels of 70% Fe with three different Cr-Ni ratios. It was found that, as the Cr-Ni ratio increases, the ratio of lathy ferrite to total ferrite does not change significantly even though both increase. A schematic of the proposed formation mechanism of vermicular and lathy ferrite is shown in Figure 7.6. Austenite first grows epitaxially from the unmelted austenite grains at the fusion boundary, and δ-ferrite soon nucleates at the solidification front. The crystallographic orientation relationship between the δ-ferrite and the austenite determines the ferrite morphology after the postsolidification transformation. If the closed-packed planes of the δ-ferrite are parallel to those of the austenite, the δ→γ transformation occurs with a planar δ/γ interface, resulting in vermicular ferrite. However, if the so-called Kurdjumov–Sachs orientation relationships, namely, (-110)δ//(-111)γ and [-1-11]δ//[-1-10]γ, exist between the δ-ferrite and the austenite, the transformation occurs along the austenite habit plane into the δ-ferrite dendrites. The resultant ferrite morphology is lathy, as shown in Figure 7.7. For the lathy ferrite to continue to grow, the preferred growth direction <100> of both δ-ferrite and austenite must be aligned with the heat flow direction.Figure 7.6 Mechanism for the formation of vermicular and lathy ferrite.Figure 7.7 Lathy ferrite in an autogenous gas-tungsten arc weld of Fe-18.8Cr-11.2Ni.7.1.3 Prediction of Ferrite ContentSchaeffler first proposed the quantitative relationship between the composition and ferrite content of the weld metal. As shown by the constitution diagram in Figure 7.8, the chromium equivalent of a given alloy is determined from the concentrations of ferrite formers Cr, Mo, Si, and Cb, and the austenite equivalent is determined from the concentrations of austenite formers Ni, C, and Mn. DeLong refined Schaeffler’s diagram to include nitrogen, a strong austenite former, as shown in Figure 7.9. Also, the ferrite content is expressed in terms of the ferrite number, which is more reproducible than the ferrite percentage and can be determined nondestructively by magnetic means. Figure 7.10 shows that nitrogen, introduced into the weld metal by adding various amounts of N2to the Ar shielding gas, can reduce the weld ferrite content significantly. Cieslak et al., Okagawa et al., and Lundin et al. have reported similar results previously.Figure 7.8 Schaeffler diagram for predicting weld ferrite content and solidification mode.Figure 7.9 DeLong diagram for predicting weld ferrite content and solidification mode.Figure 7.10 Effect of nitrogen on ferrite content in gas-tungsten arc welds of duplex stainlesssteel.Figure 7.11 WRC-1992 diagram for predicting weld ferrite content and solidification mode.The WRC-1992 diagram of Kotecki and Siewert, shown in Figure 7.11, was from the Welding Research Council in 1992. It was modified from the WRC-1988 diagram of McCowan et al. by adding to the nickel equivalent the coefficient for copper and showing how the axes could be extended to make Schaeffler-like calculations for dissimilar metal joining.Kotecki added the martensite boundaries to the WRC-1992 diagram, as shown in Figure 7.12. More recent investigations of Kotecki have revealed that the boundaries hold up well with Mo and N variation but not as well with C variation. Balmforth and Lippold proposed the ferritic-martensitic constitution diagram shown in Figure 7.13. Vitek et al. developed a model FNN-1999 using artificial neural networks to improve ferrite number prediction, as shown in Figure 7.14. Twelve alloying elements besides Fe were considered: C, Cr, Ni, Mo, N, Mn, Si, Cu, Ti, Cb, V, and Co. The model is not in a simple pictorial form, such as the WRC-1992 diagram, because it allows nonlinear effects and element interactions.Figure 7.12 WRC-1992 diagram with martensite boundaries for 1, 4, and 10% Mn.Figure 7.13 Ferritic-martensitic stainless steel constitution diagram containing a boundary for austenite formation and with iso-ferrite lines in volume percent of ferrite.Figure 7.14 Experimentally measured ferrite number (FN) versus predicted FN:(a) FNN-1999; (b) WRC-1992.7.1.4 Effect of Cooling RateA. Changes in Solidification Mode The prediction of the weld metal ferrite content based on the aforementioned constitution diagrams can be inaccurate when the cooling rate is high, especially in laser and electron beam welding. Katayama and Matsunawa, David et al., and Brooks and Thompson have compared microstructures that form in slow-cooling-rate arc welds with those that form in high-cooling-rate, high-energy-beam welds. Their studies show two interesting trends. For low Cr-Ni ratio alloys the ferrite content decreases with increasing cooling rate, and for high Cr-Ni ratio alloys the ferrite content increases with increasing cooling rate. Elmer et al.(33) pointed out that in general low Cr-Ni ratio alloys solidify with austenite as the primary phase, and their ferrite content decreases with increasing cooling rate because solute redistribution during solidification is reduced at high cooling rates. On the other hand, high Cr-Ni ratio alloys solidify with ferrite as the primary phase, and their ferrite content increases with increasing cooling rate because the d Æ g transformation has less time to occur at high cooling rates.Elmer et al. studied a series of Fe-Ni-Cr alloys with 59% Fe and the Cr-Ni ratio ranging from 1.15 to 2.18, as shown in Figure 7.15. The apex of the three-phase triangle is at about Fe-25Cr-16Ni. Figure 7.16 summarizes the microstructural morphologies of small welds made by scanning an electron beam over a wide range of travel speeds and hence cooling rates. At low travel speeds such as 0.1-1mm/s, the cooling rates are low and the alloys with a low Cr-Ni ratio (especially alloys 1 and 2) solidify as primary austenite. The solidification mode is either single-phase austenite (A), that is, no ferrite between austenite dendrites or cells (cellular-dendritic A), or primary austenite with second-phase ferrite (AF), that is, only a small amount of ferrite between austenite dendrites (interdendritic F). The alloys with a high Cr-Ni ratio (especially alloys 5-7), on the other hand, solidify as primary ferrite.The solidification mode is primary ferrite with second-phase austenite (FA), that is, vermicular ferrite, lacy ferrite, small blocks of austenite in a ferrite matrix (blocky A), or Widmanstatten austenite platelets originating from ferrite grain boundaries (Widmanstatten A).Figure 7.15 Vertical section of Fe-Ni-Cr phase diagram at 59% Fe showing seven alloys withCr-Ni ratio ranging from 1.15 to 2.18.Figure 7.16 Electron beam travel speed (cooling rate) versus composition map of microstructural morphologies of the seven alloys in Figure 7.15 (A and F denote austenite and ferrite, respectively). The solid lines indicate the regions of the four primary solidification modes, while the dashed lines represent the different morphologies resulting from postsolidification transformation from ferrite to austenite.At very high welding speeds such as 2000mm/s, however, the cooling rates are high and the alloys solidify in only the single-phase austenite mode (A) or the single-phase ferrite mode (F). An example of the former is the alloy 3 (about Fe-24.75Cr-16.25Ni) shown in Figure 7.17a. At the travel speed of 25mm/s (2×103 °C/s cooling rate) the substrate solidifies as primary austenite in the AF mode, with austenite cells and intercellular ferrite. At the much higher travel speed of 2000mm/s (1.5×106°C/s cooling rate) the weld at the top solidifies as primary austenite in the A mode, with much smaller austenite cells and no intercellular ferrite (cellular A). An example of the latter is alloy 6 (about Fe-27.5Cr-13.5Ni) shown in Figure 7.17b. At 25mm/s the substrate solidifies as primary ferrite in the FA mode, with blocky austenite in a ferrite matrix. At 2000mm/s the weld at the top solidifies asprimary ferrite in the F mode, with ferrite cells alone and no austenite (cellular F).Figure 7.16 also demonstrates that under high cooling rates an alloy that solidifies as primary ferrite at low cooling rates can change to primary austenite solidification. For instance, alloy 4 (about Fe-25.5Cr-15.5Ni) can solidify as primary ferrite at low cooling rates (vermicular F) but solidifies as primary austenite at higher cooling rates (intercellular F or cellular A).Another interesting point seen in the same figure is that at high cooling rates alloy 5 can solidify in the fully ferritic mode and undergoes a massive (diffusionless) transformation after solidification to austenite (massive A). Under very high cooling rates there is no time for diffusion to occur.Figure 7.17 Microstructure of the low-cooling-rate substrate (2 × 103°C/s) and thehigh-cooling-rate electron beam weld at the top: (a) alloy 3 in Figure 7.15; (b) alloy 6.B. Dendrite Tip Undercooling Vitek et al. attributed the change solidification mode, from primary ferrite to primary austenite, at high cooling rates to dendrite tip undercooling. Brooks and Thompson explained this under-cooling effect based on Figure 7.18. Alloy C0solidifies in the primary ferrite mode at low cooling rates. Under rapid cooling in laser or electron beam welding, however, the melt can undercool below the extended austenite liquidus (C Lg), and it becomes thermodynamically possible for the melt to solidify as primary austenite. The closer C0 is to the apex of the three-phase triangle, the easier sufficient undercooling can occur to switch the solidification mode from primary ferrite to primary austenite.Figure 7.18 Vertical section of Fe-Cr-Ni phase diagram showing change in solidification fromferrite to austenite due to dendrite tip undercooling.Kou and Le made autogenous gas–tungsten arc welds in 309 stainless steel, which has a composition close to the apex of the three-phase triangle, as shown in Figure 7.4b.At 2mm/s (5ipm) welding speed, primary ferrite was observed across the entire weld (similar to that shown in Figure 7.3b). At a higher welding speed of 5mm/s (12ipm), however, primary austenite was observed along the centerline, as shown in Figure 7.19. Electron probe micro-analysis (EPMA) revealed no apparent segregation of either Cr or Ni near the weld centerline to cause the change in the primary solidification phase. From Equation (6.3) the growth rate R = Vcosα,where α is the angle between the welding direction and the normal to the pool boundary. Because of the teardrop shape of the weld pool during welding (Figure 2.15), α drops to zero and R increases abruptly at the weld centerline. As such, the cooling rate (GR) increases abruptly at the weld centerline, as pointed out subsequently by Lippold.Elmer et al. calculated the dendrite tip undercooling for the alloys in Figure 7.16 under various electron beam travel speeds. An undercooling of 45.8°C was calculated at the travel speed of 175mm/s, which is sufficient to depress the dendrite tip temperature below the solidus temperature (Figure 7.15). This helps explain why alloy 4 can change from primary ferrite solidification at low travel speeds to primary austenite solidification at much higher travel speeds.Figure 7.19 Weld centerline austenite in an autogenous gas-tungsten arc weldof 309 stainless steel solidified as primary ferrite.7.1.5 Ferrite Dissolution upon ReheatingLundin and Chou observed ferrite dissolution in multiple-pass or repair austenitic stainless steel welds. This region exists in the weld metal of a previous deposited weld bead, adjacent to but not contiguous with the fusion zone of the deposited bead under consideration. Both the ferrite number and ductility are lowered in this region, making it susceptible to fissuring under strain. This is because of the dissolu tion of δ-ferrite in the region of the weld metal that is reheated to below the γ-solvus temperature. Chen and Chou reported, in Figure 7.20, a significant ferrite loss in a 316 stainless steel weld subjected to three postweld thermal cycles with a 1250°C peak temperature, which is just below the γ + δ two-phase region of about 1280-1425°C.Figure 7.20 Effect of thermal cycles on ferrite content in 316 stainless steel weld: (a) as welded;(b) subjected to thermal cycle of 1250°C peak temperature three times after welding.。