磨削烧伤检测操作指导书
磨削烧伤

磨削液的供液方法
磨削液对磨削效果的影响不仅取决于磨削液本身的性能,也 取决于磨削液是否可以有效的注入磨削区。常用的供液方法 有: 浇注法、高压冷却、内冷供液法、喷雾法供液法、超声波供 液法、浸渍砂轮。
• 浇注法
浇注法是用低压泵把磨削液输送到冷却喷嘴,借助磨削液 本身的重力作用,浇注到砂轮和工件的接触部位。 优点:简单易行 缺点:砂轮转速较高时,磨削液很难进入到磨削区。
工件温度的上升程度还 随着磨削液流量的变化 而变化。如右图所示, 流量越大,冷却作用越 明显,温度上升幅度则 越小。
• 清洗作用
磨削液侵入磨粒与工件之间,或砂轮的气孔里,将切屑或 脱落破碎的磨粒冲走洗净,避免影响加工精度或机床保养 。 影响因素: 渗透性、流动性、使用压力。 磨削液的主要作用见下图:
这种方法是使磨削液从 砂轮内孔或侧面进入砂轮 体内,依靠砂轮回转时的 离心作用,将磨削液通过 砂轮的气孔甩出。 优点:能有效地将磨削液 送入磨削区,在内圆磨削 时,效果很好。 缺点:由于砂轮气孔很小 ,磨削液必须经过良好的 过滤,否则,砂轮内气孔 易被杂质堵塞。另外,砂 轮周边会甩出磨削液,需 注意保护。
磨削液
• 使用目的
减小磨削力,降低磨削区温度、同时又迅速带走磨削热以 减少工件变形。
• 磨削液的作用
润滑作用、冷却作用、清洗作用。
• 润滑作用
液体渗透到模具与工件的接触区内,形成润滑膜,以减少 界面之间的摩擦,从而达到降低磨削力,减缓磨粒磨损, 延长砂轮寿命的作用。
• 冷却作用
一 迅速吸收热量以减缓工件温度上升,保证工件尺寸精 度,防止表面质量恶化。 二 磨削液使高温下的磨粒急剧冷却,产生热冲击效果, 促进磨粒的自锐作用。 冷却作用与磨削液导热系数、比 热和汽化有密切关系。
磨削烧伤检测操作指导书
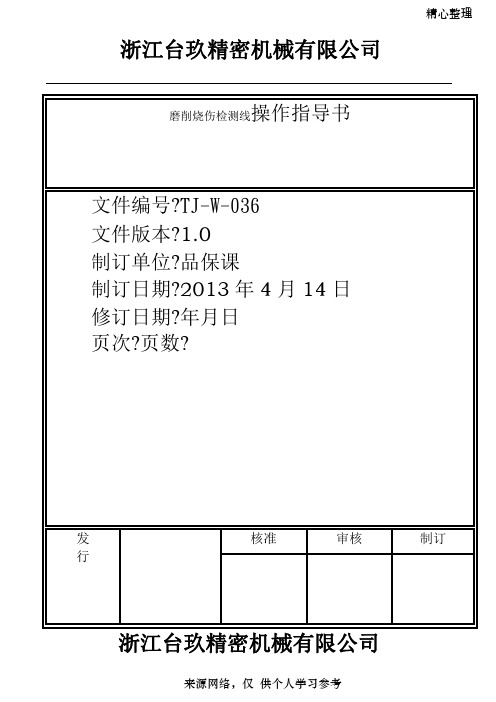
防锈
备注:1.检验必须按池1至池9依次进行检验,时间控制必须符合规定的时间。2.烧伤检验应由经过培训的品保课人员进行。
3.第1池需要加热至50摄氏度以上,所以试验前需加热,试验完成后需关闭开关
2.3检验范围
主要针对蜗杆磨加工工件。即齿部表面烧伤检验。
2.4磨削烧伤检验的判定和记录
A类:无磨削烧伤,表面呈现均匀的灰色.见图2中的无烧伤区域
ph值都须用专门的PH器具或溶度计来检验。
2)浸池定期更换,7、8池12周更换一次;2、4、6池一周更换;1池即洗涤池12周更换
一次;3、5酸池6周更换一次;9浸油池一年更换一次。
当酸溶液更新后,我们需用一件已烧伤的工件来检验腐蚀功能和浸泡时间,并对溶液的腐
蚀效果记录。
品保课
页次/页数
5/7
图1-A级无烧伤
图2B级轻微烧伤
图3D级严重磨削烧伤
图4E级烧伤
2.5检验频率
按客户要求
浙江台玖精密机械有限公司
标题:
腐蚀检测线操作指导书
文件编号
TJ-W-036
文件版本
1.0
制修订日期
2013年4月15日
制订单位
品保课
页次/页数
6/7
2.6磨削烧伤的维护和保养
1)因磨削烧伤线的功能有效性,应每周检验一次,并记录在相应表格中,各池的浓度或
磨削过程中会产生大量的磨削热,一部分被冷却液带走,另一部分被传导入加工件的浅表层内。并使工件表层温度升高。在磨
削热大量产生时会在齿表面形成回火层。当温度达到熔化
温度时,则经冷却液冷却形成二次淬火层,从而形成磨削烧伤。磨削烧伤工件表层会形成回火
层,其表层组织是回火马氏体,会和酸发生腐蚀反应,根据这个原理,我们可以使用硝酸腐蚀
磨削烧伤与其解决方案

磨削烧伤及其解决方案张国耀(郑州超微磨料具有限公司河南郑州450001)摘要:鉴于磨削过程中工件烧伤的问题一直困扰着产品的质量问题,从磨削烧伤的形成的机理、磨削烧伤的检查方法、磨削烧伤的分级、磨削烧伤的避免措施、磨削烧伤的影响因素、磨削烧伤解决方法。
让我们从基础对磨削烧伤形成认识、到对磨削烧伤的解决方法形成一整套的方案,其中:砂轮的选择在磨削烧伤过程中非常重要。
以避免我们生产中避免烧伤、遇到烧伤而找到合理的解决方法。
适用于外圆磨烧伤、内圆磨烧伤、平面磨烧伤、端面磨烧伤、无心磨烧伤等磨削方式。
关键词:磨削烧伤烧伤砂轮的选择烧伤解决方法烧伤原理烧伤级别一、定义:磨削时,由于磨削区域的瞬时高温(一般为900-1500℃)到相变温度以上时,形成零件表层金相组织发生变化(大多表面的某些部分出现氧化变色),使表层金属强度和硬度降低,并伴有残余应力产生,甚至出现微观裂纹,这种现象称为磨削烧伤。
二、磨削烧伤机理:当磨削表面产生高温时,如果散热措施不好,很容易在工件表面(从几十um 到几百 um)发生二次淬火及高温回火。
如果磨削工件表面层的瞬间温度超过钢种的AC1 点,在冷却液的作用下二次淬火马氏体,而在表层下由于温度梯度大,时间短,只能形成高温回火组织,这就使在表层和次表层之间产生拉应力,而表层为一层薄而脆的二次淬火马氏体,当承受不了时,将产生裂纹。
三、损伤的原因:(1)热处理的影响a)残余奥氏体磨削时残余奥氏体由于砂轮磨削时产生的热和压力而转变,同时可能伴随出现表面回火和磨削裂纹。
残余奥氏体量应控制在30%以内。
b)渗层碳浓度渗层碳浓度过高,在渗层组织中容易形成网状碳化物或过多的游离碳化物。
由于这种物质极硬,在磨削过程中可能出现局部过热倾向和发生表面回火。
渗层碳浓度过高,会使工件表面产生过多的残余奥氏体.从而导致烧伤和裂纹。
因此,表面碳浓度增加,则降低了磨削性能,一般表面碳浓度应控制在0.75% -0.95%范围以内。
酸浸法检查磨削烧伤

酸浸法简单易懂,一学就会,现介绍如下(包括样品图),本方法与GB/T17879中的方法略有差别,仅供参考:试剂:5%硝酸溶液3%盐酸酒精溶液5%碳酸钠溶液清水无水乙醇步骤:工件放在5%硝酸溶液浸蚀15~30秒→水中清洗20~30秒→3%盐酸酒精溶液浸蚀20~30秒后→水中清洗30秒→立即放入5%碳酸钠溶液中中和1min→无水乙醇中浸入约10秒→取出立即观察磨削表面是否有黑色区域(如附图),黑色区域的多少即为烧伤程度的大小。
至于合格程度可能要双方协议规定或参照GB/T17879-1999 《齿轮磨削后表面回火的浸蚀检验》这一阵忙,上网本是找个别的问题的,即然来了就说说,酸洗磨削烧伤是每个轴承厂必不可少的检验,但真的在下面进行酸洗的又是些工人,而且酸洗成份控制并不容易(随酸洗量的增加,使用时间变化,酸洗液成份要发生变化)我们酸洗的配方与JB1255的略有不同的,用的是1 脱脂无水碳酸钠25-35 g磷酸三钠25-35 g氢氧化钠10-20 g水玻璃2-3 g水1000毫升2 热水清洗水100%3 流动水清洗水100%4 酸洗硝酸15-25ml水 1000ml5 流动冷水洗水100%6 明化1铬酐130-150g硫酸4 g水1000ml7 流动水清洗水100%8 明化2盐酸(d=1.19)100-200ml二氯化锡2g金属锡100-200g水1000ml9 流动冷水洗水100%10 中和无水碳酸钠4-6%水余量11 流动冷水洗水100%12 防锈亚硝酸钠6-8kg无水碳酸钠1-2kg水余量酸洗后烧伤部位呈黑色,无烧伤呈灰色(白烧伤很少见,一般如磨削发生严重操作失误时可能会出现)磁弹仪测烧伤还是很有效的,但有时磁弹值会受附近电磁信号的干扰,还有就是检测位置比较受限,受探头的影响一些位置测不到,特别是内表面,另外测试效率低,测试仅及一条线,不可能所有表面都测到谢谢各位了.我搜索到了一份操作指导书,原文贴出,供大家参考:磨削烧伤痕迹的显示:1 浸蚀溶液配方:4%硝酸酒精浸蚀:工件在溶液中浸蚀2分钟2 清洗工件在清水中清洗2分钟。
磨削烧伤的检测方法

磨削烧伤的检测方法可能形成网状裂纹,它会导致齿面剥落.这当然是绝对不允许的。
用硬度测试法鉴别磨削烧伤的方法,并用超声波硬度计进行了实验,证明该方法简单易行,可以广泛应用于磨削加工中。
磨削烧伤及其常用检查方法在机械类产品中,很多重要零部件如轴承、齿轮、曲轴、凸轮轴、活塞销和万向节等,在热处理之后均需经过磨削加工。
相比之下,磨削时单位切削面积上的功率消耗远远超过其它加工方法,所转化热量的大部分会进入工件表面,因此容易引起加工面金相组织的变化。
在工艺参数、冷却方法和磨料状态选择不当的情况下,工件在磨削过程中极易出现相当深的金相组织变化层(即回火层),并伴随出现很大的表面残余应力,甚至导致出现裂纹,这就是所谓的磨削烧伤问题。
零部件的表面层烧伤将使产品性能和寿命大幅度地下降,甚至根本不能使用,造成严重的质量问题。
为此,生产企业一方面通过执行正确、科学的工艺规范,减轻和避免出现磨削烧伤现象;另一方面,加强对零部件的检验,及时发现不合格工件,并判断正在进行的磨削工艺状况。
但长期以来,对工件表面磨削烧伤的检验,除了最简单的目测法外,就是采用已延续多年的传统方法——酸洗法,即在被检零部件表面涂上酸液或将其浸入盛有按规定配制的酸液槽中。
之后(或在把工件取出后)根据表面呈现的不同颜色,对磨削烧伤的程度作出相应的判断。
一般地说,若色泽没有变化,就表明情况正常;而当颜色变成灰色,则说明已有烧伤情况存在,随着色泽变得越来越深,表示工件表面因温度更高,引起的磨削烧伤更为严重。
酸洗法具体如下:This is only a suggestion from my collegue ( Dino Calvanelli ) to find theburns on the gears此为有关过烧检测的建议:Clean each sample (part) to be inspected (free ofdirt,oil,grease,fingermarks,protective coatings,etc.).清洗产品,确保无灰尘、油污、手印、表面覆盖物等。
磨削作业指导书SOP

磨削作业指导书SOP
目的
本文档旨在提供磨削作业的详细指导,确保安全和高效地进行磨削作业。
适用范围
本指导书适用于所有从事磨削作业的员工。
安全要求
1. 在进行磨削作业前,员工必须穿戴个人防护装备,包括护目镜、手套和防护服。
2. 严禁穿戴松散的衣物或饰品,在作业时应将长发束起或戴头巾。
3. 确保磨削设备和工作区域的安全,包括检查设备的安全传感器、刀盘的磨损程度和保持工作区域的整洁。
操作指南
1. 首先,检查磨削设备的工作状态和连续性。
2. 将待加工的物体正确固定在磨削设备上,并调整加工角度和加工参数。
3. 启动磨削设备并确保加工物体的稳定性和精准性。
4. 在进行磨削过程中,注意观察磨削效果和加工物体的状态,及时调整操作和参数。
5. 磨削完成后,停止设备并将磨削物体移开。
6. 清理工作区域,包括清除磨屑和保养磨削设备。
故障处理
1. 如果设备出现故障或异常情况,请立即停止操作,并通知相关维修人员。
2. 在维修人员到达之前,严禁私自拆卸设备或进行维修操作。
紧急情况处理
1. 在发生紧急情况时,立即停止设备并按照应急计划执行。
2. 如果发生人身伤害,请及时寻求医疗帮助。
操作纪录和报告
1. 所有磨削作业都应记录操作人员、时间和作业类型。
2. 如出现异常情况、故障或事故,应立即上报相关部门,并详细记录事发经过和处理过程。
以上为磨削作业指导书的主要内容,请所有从事磨削作业的员工严格遵守本指导书的要求和操作流程。
如有任何疑问,请随时咨询相关负责人。
磨削烧伤的检测方法(5篇)

磨削烧伤的检测方法(5篇)第一篇:磨削烧伤的检测方法磨削烧伤的检测方法可能形成网状裂纹,它会导致齿面剥落.这当然是绝对不允许的。
用硬度测试法鉴别磨削烧伤的方法,并用超声波硬度计进行了实验,证明该方法简单易行,可以广泛应用于磨削加工中。
磨削烧伤及其常用检查方法在机械类产品中,很多重要零部件如轴承、齿轮、曲轴、凸轮轴、活塞销和万向节等,在热处理之后均需经过磨削加工。
相比之下,磨削时单位切削面积上的功率消耗远远超过其它加工方法,所转化热量的大部分会进入工件表面,因此容易引起加工面金相组织的变化。
在工艺参数、冷却方法和磨料状态选择不当的情况下,工件在磨削过程中极易出现相当深的金相组织变化层(即回火层),并伴随出现很大的表面残余应力,甚至导致出现裂纹,这就是所谓的磨削烧伤问题。
零部件的表面层烧伤将使产品性能和寿命大幅度地下降,甚至根本不能使用,造成严重的质量问题。
为此,生产企业一方面通过执行正确、科学的工艺规范,减轻和避免出现磨削烧伤现象;另一方面,加强对零部件的检验,及时发现不合格工件,并判断正在进行的磨削工艺状况。
但长期以来,对工件表面磨削烧伤的检验,除了最简单的目测法外,就是采用已延续多年的传统方法——酸洗法,即在被检零部件表面涂上酸液或将其浸入盛有按规定配制的酸液槽中。
之后(或在把工件取出后)根据表面呈现的不同颜色,对磨削烧伤的程度作出相应的判断。
一般地说,若色泽没有变化,就表明情况正常;而当颜色变成灰色,则说明已有烧伤情况存在,随着色泽变得越来越深,表示工件表面因温度更高,引起的磨削烧伤更为严重。
酸洗法具体如下:This is only a suggestion from my collegue(Dino Calvanelli)to find theburns on the gears此为有关过烧检测的建议:Clean each sample(part)to be inspected(free ofdirt,oil,grease,fingermarks,protective coatings,etc.).清洗产品,确保无灰尘、油污、手印、表面覆盖物等。
磨削烧伤检查规定

通常应对有回火显示的零件进行磁粉探伤检验,尤其是渗碳淬火硬化的零件。
7.2. 显微硬度计检查
7.2.1. 7.2.2. 7.2.3.
把要检查的部位用 800-1000 号的砂纸磨削 ,尽量少磨,能检查显微硬度即可。 工件要检查的部位不便于进行显微硬度检测,用线切割切下,并镶样。 用显微硬度计检测时,载荷 0.3Kg。对于用线切割切下零件的检验工件 0.05mm 处硬度≥695HV0.3,不允
7. 检验准则
7.1. 目视的外观与分类 未出现回火的零件在清洗和侵蚀后呈现均匀的灰色。局部回火区域在侵蚀后的零件上呈现深灰或黑色。通常,
随着颜色变的越深暗,说明回火烧伤程度越严重。如果在磨削过程中出现严重过热,将导致再硬化,再硬化
区域是一块白色或浅颜色的未回火马氏体,周围是黑色回火面。
所有的磨削后回火,尤其是再硬化的烧伤(即未回火马氏体)会影响零件的寿命,但零件仍可使用。
a)避免直接接触酸碱、溶剂。
b)将酸加入水中或酒精中,防止加反。
c)浸泡箱不用时加盖盖好。
d)遵守可燃和易燃液体储存及使用的安全措施。
有烧伤
无烧伤
机后要检查磨销烧伤。
做好记录。
10. 维护和管理 根据溶液的使用程度或当新配制溶液时,为检验溶液的性能,建议用该溶液侵蚀已知有回火显示的样品零件。
在侵蚀和检验后,该样品应再防锈保护备用,这类样品应定期更换。
根据使用程度,应定期检验溶液的浓度和杂质。
样品和溶液每 7 天更换一次。
11. 安全和环境保护。
磨削烧伤检查规定 1. 目的
保证工件在磨削工序中质量得到保证。 2. 适用范围
本标准规定了用化学侵蚀方法对磨削表面的局部过热进行检验及其分类的标准操作程序和要求,同时硬度法 作为对化学侵蚀方法的校核。 本标准适用于工件在热处理后,进行磨削工序中的检查。对于调质后、高频淬火后、渗碳淬火后的工件都适 用。 本标准不适用氮化零件和不锈钢零件。 化学侵蚀方法对表面硬度的变化的反映比大多数硬度测试方法更为敏感。 表面回火侵蚀检验应在表面磨削后,并在进一步精加工工序之前进行。比如连杆在珩磨前、曲柄销在研磨前。 3. 引用标准 GB/T 17879-1999 齿轮磨削后表面回火的浸蚀检验 4. 设备 4.1. 容器的材料与容器内溶液不得发生反应,也不得损伤被处理的零件。所有容器都应贴上所盛溶液的标签,并 在不用时盖好。本公司采用玻璃烧杯,并用平板玻璃盖好。 4.2. 被检验区域照明 被检验区域应有充分的照明,没有阴影和反射。摧荐被检验区域的光照度应不低于 3200lx。 4.3. 计时装置 应使用适当的计时器(秒表)。保证一组中的所有零件处理过程一致。 4.4. 清洗装置 应采用碱清洗器、蒸汽去油器、溶液清洗装置或相应的清洗装置。 5. 试剂 所有的化学试剂应为工业级或更纯的等级。 5.1. 清洗材料 所有清洗材料应保证能去除所有的污渍、磨粒和油渍,使被检表面可形成不破水膜。不破水膜是指表面用低 于 40℃的清水漂洗干净后,水膜至少应在 15S 内保持不破。 5.2. 硝酸 硝酸密度ρ=1.42Kg/l 5.3. 盐酸 盐酸密度ρ=1.19Kg/l 5.4. 酒精 应使用清洁的、不含油等杂质的甲醇或变性乙醇。 5.5. 水 清洁、无杂质。 5.6. 碱溶液 应使用 4%——6%的氢氧化钠溶液,其 PH≥10。 6. 检验程序 工件清洗→清洗后零件表面应达到能形成不破水膜→侵蚀→检验 6.1. 清洗 a)采用蒸汽清洗。 b)碱洗或超声波清洗。 6.2. 侵蚀 6.2.1. 腐蚀液的配制。
磨削烧伤检查

磨削烧伤检查2#酸洗液配制合成:将5L浓度为69%~71%的工业硝酸缓缓注入酒精中,稀释成100L溶液,搅拌均匀,混合成酸洗溶液。
3#酸洗液配制合成:10L浓度为36%~38%的工业盐酸缓缓注入甲醇中,配制成100L溶液, 搅拌均匀。
4#中和液配制合成:1Kg的碳酸钠加入100Kg水中,搅拌均匀,混合成中和液(碳酸钠与水的重量比为0.01:1)。
加入足够的酚酞指示液,目视观察溶液的中和点(浅粉红色)。
当溶液不在为浅粉红色时,需将溶液废弃。
酸洗程序:1.清洗液:粗磨或精磨完了的零件上残留的可溶乳剂要用1#热水快速漂洗,再放在60~66C°的1#清洗液中清洗至少5分钟。
如果是超精研零件表面有油污时,可先用特殊的1#清洗液清洗煤油清洗后,再按正常程序进行。
2.酸洗液:将零件浸入2#酸洗液中,并且上下搅动,直到磨削面都变成黑色(不要超过10秒)。
通常腐蚀的时间为3~5秒,如果一定要超过10秒钟零件才能变黑,就要更换溶液。
3.自来水漂洗:将酸洗后的零件立即用流动的自来水冲洗。
4.2#酸洗液:将零件浸入3#酸洗液上下搅动。
通常搅动的时间为10秒钟(但不要超过20秒钟),如果一定要超过20秒钟,就要更换溶液。
5.自来水漂洗:酸洗后的零件用流动的自来水冲洗。
6.中和液:将零件浸入中和液中搅动2~5秒钟。
7.自来水漂洗:将中和后的零件再用流动的自来水冲洗。
8.防锈:酸洗完了的零件应立即浸入专用防锈水中,取出仔细检查烧伤。
9.酸洗检验员检验后,将结果记录在“轴承零件表面酸洗检查记录”中。
酸洗结果的观察及解释:1.中度的灰色:意味着正常的磨加工表面。
2.黑色或深色区域:意味着表面存在再回火烧伤。
3.亮色或白色区域:意味着表面存在再淬火烧伤,在任何情况下均不可接受。
特例:非常浅的表面再淬火烧伤如经过二次酸洗可以除去,则可以接受。
在接受批量前,请再二次酸洗有代表性的产品后,根据结果判定。
4.当目视判断有困难时,可进行二次酸洗。
磨削烧伤检测方法

According to the professional article, … Nital (nital solution (HNO3 in ethanol))etching in proof of grinding burning”, since ca. 1983 we have carried out the burning etching in our plant.In the following years, the process steps have been modified as following:1. Clean / Degrease with ultrasonic and tenside cleaning agent by 60±5°C2. Wash in water bath by 60±5°C ca. 4 min3. Etch in 2% alcoholic nitric acid 2.5-3.0 min4. Wash in water bath by room temperature ca. 0.5 min5. Etch in 3% alcoholic hydrochloric acid 2.5-3.0 min6. Wash in water bath by room temperature ca. 0.5 min7. Neutralize in 4% hydrous ammoniac solution 1-2 min8. Wash in water bath by room temperature ca. 0.5 min9. Dry with compressed air10. Conserve按照专业条款,硝酸乙醇腐蚀液(硝酸乙醇腐蚀液(HNO3 in乙醇))中浸泡的齿轮来检查磨削烧伤,从1983年开始我们在工厂就开始做磨削烧伤的检测。
磨削烧伤实验报告
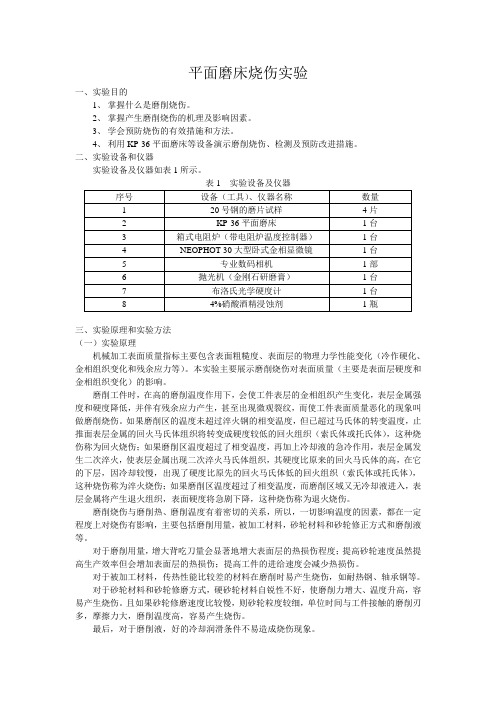
平面磨床烧伤实验一、实验目的1、掌握什么是磨削烧伤。
2、掌握产生磨削烧伤的机理及影响因素。
3、学会预防烧伤的有效措施和方法。
4、利用KP-36平面磨床等设备演示磨削烧伤、检测及预防改进措施。
二、实验设备和仪器实验设备及仪器如表1所示。
三、实验原理和实验方法(一)实验原理机械加工表面质量指标主要包含表面粗糙度、表面层的物理力学性能变化(冷作硬化、金相组织变化和残余应力等)。
本实验主要展示磨削烧伤对表面质量(主要是表面层硬度和金相组织变化)的影响。
磨削工件时,在高的磨削温度作用下,会使工件表层的金相组织产生变化,表层金属强度和硬度降低,并伴有残余应力产生,甚至出现微观裂纹,而使工件表面质量恶化的现象叫做磨削烧伤。
如果磨削区的温度未超过淬火钢的相变温度,但已超过马氏体的转变温度,止推面表层金属的回火马氏体组织将转变成硬度较低的回火组织(索氏体或托氏体),这种烧伤称为回火烧伤;如果磨削区温度超过了相变温度,再加上冷却液的急冷作用,表层金属发生二次淬火,使表层金属出现二次淬火马氏体组织,其硬度比原来的回火马氏体的高,在它的下层,因冷却较慢,出现了硬度比原先的回火马氏体低的回火组织(索氏体或托氏体),这种烧伤称为淬火烧伤;如果磨削区温度超过了相变温度,而磨削区域又无冷却液进入,表层金属将产生退火组织,表面硬度将急剧下降,这种烧伤称为退火烧伤。
磨削烧伤与磨削热、磨削温度有着密切的关系,所以,一切影响温度的因素,都在一定程度上对烧伤有影响,主要包括磨削用量,被加工材料,砂轮材料和砂轮修正方式和磨削液等。
对于磨削用量,增大背吃刀量会显著地增大表面层的热损伤程度;提高砂轮速度虽然提高生产效率但会增加表面层的热损伤;提高工件的进给速度会减少热损伤。
对于被加工材料,传热性能比较差的材料在磨削时易产生烧伤,如耐热钢、轴承钢等。
对于砂轮材料和砂轮修磨方式,硬砂轮材料自锐性不好,使磨削力增大、温度升高,容易产生烧伤。
且如果砂轮修磨速度比较慢,则砂轮粒度较细,单位时间与工件接触的磨削刃多,摩擦力大,磨削温度高,容易产生烧伤。
磨削烧伤安全操作规程

磨削烧伤安全操作规程1. 前言磨削工作中,磨盘会在高速旋转的情况下与工件接触,产生高温和摩擦力。
因此,进行磨削作业时必须遵守安全操作规程,以确保工作场所的安全,并减少可能发生的磨削烧伤事故。
2. 个人防护在进行磨削作业之前,必须正确佩戴个人防护装备,包括但不限于: - 眼部防护:佩戴符合标准的安全眼镜或面罩,以保护眼睛免受磨削粉尘和碎片的伤害。
- 呼吸道防护:戴上适合的口罩或呼吸器,以避免吸入磨削产生的粉尘和有害气体。
- 手部防护:佩戴防护手套,以防止手部磨损或烧伤。
- 身体防护:穿戴合适的工作服,避免裸露皮肤,以免受到磨削产生的碎片和溅射物的伤害。
3. 设备检查在使用磨削设备之前,必须进行设备检查,确保设备处于良好工作状态。
以下是设备检查的一些关键步骤: - 磨盘:检查磨盘是否有破损、裂纹或变形,如果有则需要更换。
- 磨削机:检查机器的冷却系统是否正常工作,确保水流或冷却液充足,以防止过热和磨削机损坏。
- 电源和电缆:检查电源和电缆是否正常,无裸露的导线和损坏的绝缘层。
4. 工作区域准备在进行磨削作业之前,必须进行适当的工作区域准备: - 清理:确保工作区域干净整洁,没有杂物和障碍物。
清除工作台上的其他物品,以确保磨削作业时不会干扰工作。
- 照明:确保工作区域有足够的光照,以便进行准确的磨削操作,并避免磨盘和工件之间的接触问题。
5. 安全操作在进行磨削作业时,必须遵循以下安全操作规程: - 正确操作:根据设备说明书或培训指导,正确操作磨削机和附件。
不得超负荷使用机器和磨削工具。
- 压力控制:使用适当的压力进行磨削,避免施加过大压力,以免引发磨削烧伤事故。
- 方向控制:始终将磨削工具和工件保持在适当的磨削角度。
不要改变工具和工件的磨削方向,以免引发不稳定和磨削过热。
- 加工时间控制:适当控制磨削时间,以免磨盘过热,损坏工件或引发磨削烧伤事故。
- 均匀磨削:保持均匀的磨削压力和速度,避免不均匀磨削导致过热和工件破损。
钢管有限公司管修磨及修磨后检验作业指导书.doc

钢管修磨及修磨后检验作业指导书Steel pipe grinding and after grinding testing Operating instructions编制人Prepared by 李学精Li Xucjing编制日期Preparation date2013.10.20Oct.20,h,2013审核人/Fl期Reviewed by/date 刘建辉、邓世荣/2013.10.21Liu Jianhui/ Oct.21,h,2013批准人/日期Approved by/datc阳恩虎/2013.10.21Yang Enhu/ Oct.21th,2013牛效H期Effective date 版本号/修订码Ver./Rev.2013.10.22Oct.22sl,2()13A/01范围Scope本作业指导书规定了经探伤不合格的钢管的修磨要求、对修磨点的检测要求和修磨后钢管的更探的要求。
木作业指导书适用于我公司所有•产品。
本作业指导书未规定修磨人员和检验人员的安全防护要求, 这些要求参照我公司的相关规定执行。
The operating instructions define the grinding requirements for the NDT failed testing pipe, testing requirements for grinding position after grinding and the retest requirements for the pipe that have been grindedThe operating instructions apply to al 1 our products. The operating instructions are not required the security requirements of grinding and inspection personnel which refer to company's relevant regulations.2参考标准Reference specificationAPT 5CT APT 5L API 5DP DCM-SU-5272-A PPI-SU-1051-E3检测标准Test specification ASTM E 709 ISO 10893-54修磨及检验过程Grinding and inspection process4. 1在修濟台架处准备好许J桝机、超声波测厚仪、磁轨式磁粉探伤机等:Prepare the grinder,ultrasonic thickness tester, yoke-type magnetic particle inspection machine in the grinding rack.4. 2根据探伤不合格报告或探伤缺陷的标记找到待修磨处;Find the grinding position according to thefailure reports or the marking of NDT defect4. 3 用角磨机磨削待修磨处,找出缺陷;Grinding the pipe wi th grinding machine to locate defects 4.4对缺陷处进行修磨,修磨时角磨片与钢管的夹角不超过15°,以保证修磨区域闘滑过度,倾度大于4:1 On the defect of grinding, grinding and grinding angle corner tube is less than15 °, to ensure the grinding zone are smooth, incl ination is greater than 4:14. 5修磨过程中目视观察缺陷确认缺陷已去除干净;Make sure the vi sual defects have been removedduring the grinding process4. 6 (客户或产品标准要求时)对修磨处进行磁粉探伤,确认缺陷已去除干净;(Customer or productspec required) MPT on grinding section, confirm the defects have been removed;4. 6. 1磁粉探伤准备工作preparation for MP14. 6. 1. 1 nJ'见光照度检查:检测修磨台架处的可见光照度,可见光照度应大于5001ux,每班至少进行一次;Visible light ilium in ation exam in ation: detection grinding bench at visible il luminal i on,visible 1ight illumination should be greater than 5001ux, test at least once per shift;4. 6. 1.2磁悬液浓度检查:用黑磁粉配制磁悬液,磁悬液浓度应在1.2-2.4ml/100ml,每班至少进行一次;Magnetic suspension concentration check: use black powder formulated with magnetic suspension, magnetic suspension concentration should 1. 2-2. 4nil/100ml, test at least once per shift4. 6. 1.3磁轨提升力检查:磁辄提升力应大于45N,每班至少进行一次;Yoke lifting power check: yokelifting power should be greater than 45N, test at 1 east once per shift;4. 6. 1. 4 探伤灵敏度检查Detection sensitivity check:将 A 型30/100 试片(shim type 430)紧贴到钢管上,将磁辄沿钢管圆周方向放置在钢管上,使试片处于两个磁轨中部,按下磁化开关对钢管进行磁化,同时往试片处喷淋磁悬液,然后结束喷淋再结束磁化,观察试片上的磁痕显示,此吋应能清楚地观察到沿钢管轴向的1条直线和2断弧线显示(分别对应试片上的十字和圆周的轴向部分);再将轨沿钢管轴向方向放置在钢管上,重复磁化喷淋过程,此时应能清塑地观察到沿钢管轴向的1条直线和2断弧线显示(分别对应试片上的十字和圆周的周向部分);Stickthe A-type 30/100 specimens (shim type 430) onto the tube closely, then placed the yoke along the circumferential direction of pipe, so that the specimen is in two yoke central.Press the magneti/tion switching and start the magnetization of the pipe, at the same time to spray the magnetic suspension concentration and then exit the spray and magnetization in sequence. Observe the magnetized mark, It can be observed clearly that there is one straight 1 ine and two fault arc along the circumferential directi on (Corresponding to cross and the axial of circle section on specimens) then placed the yoke along the axial direction of pipe, so that the specimen is in two yoke central. Repeat the spay and magnetization process. Tt can be observed clearly the di splay of that axis 1 straight and 2 fault arc along the pipe axial directi on (Correspond ing to cross and the circumferential of circle section on specimens)探伤灵敏度检查应在每次接班时和交班时各进行1次;Detection sensitivity checks shall be taken once at during the job transfer and job handle over to next shift respectively4. 6. 2磁粉探伤MPI4. 6. 2. 1,将磁辘放置在钢管上,使修懒处于两个磁辄中部使磁辘的连线与缺陷长度方向大致垂直,按下磁化开关对钢管进行磁化,同时往试片处喷淋磁悬液,然后结束喷淋再结束磁化,观察修磨处是否有磁痕显示,若有磁痕显示则表明缺陷未修磨干净,需重新修磨再磁粉探伤确认;若无磁痕显示则表明缺陷已修磨干净,可进行下步操作;The magnetic yoke placed on the steel pipe, the grinding position in the two magnetic yoke and the connection with the central defect length direction of the yoke is roughly vertical, press the magnetization switch to magnctize the steel pipe, at the same time to spray magnetic suspending liquid, then stop and end magnotization, observe the grinding position if there is the magnetic mark. Tf magnetic mark exist show that defects have not been grinded clearly, need to be re-grinding and magnetic particle inspection confirmation; if there is no magnetic marks suggest that defects have been grinding clean, which can be used in the next operation; 4. 7对修磨处进行超声波测厚,确认剩余壁厚大于产晶标准规定的最小壁厚,否则该支钢管应报废。
酸浸法检查磨削烧伤
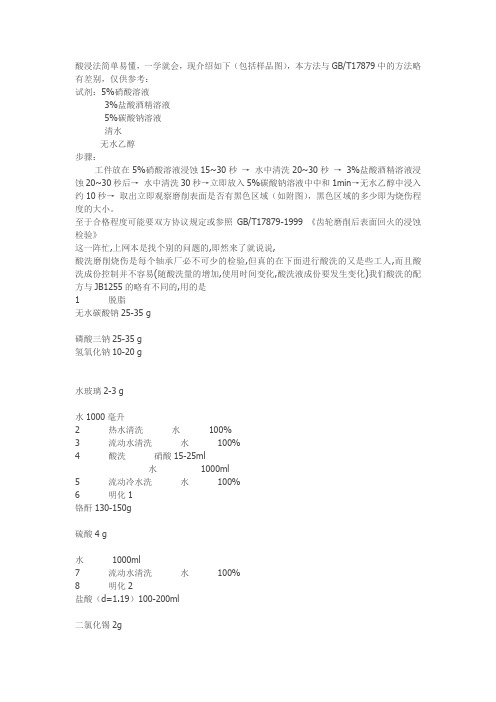
酸浸法简单易懂,一学就会,现介绍如下(包括样品图),本方法与GB/T17879中的方法略有差别,仅供参考:试剂:5%硝酸溶液3%盐酸酒精溶液5%碳酸钠溶液清水无水乙醇步骤:工件放在5%硝酸溶液浸蚀15~30秒→水中清洗20~30秒→3%盐酸酒精溶液浸蚀20~30秒后→水中清洗30秒→立即放入5%碳酸钠溶液中中和1min→无水乙醇中浸入约10秒→取出立即观察磨削表面是否有黑色区域(如附图),黑色区域的多少即为烧伤程度的大小。
至于合格程度可能要双方协议规定或参照GB/T17879-1999 《齿轮磨削后表面回火的浸蚀检验》这一阵忙,上网本是找个别的问题的,即然来了就说说,酸洗磨削烧伤是每个轴承厂必不可少的检验,但真的在下面进行酸洗的又是些工人,而且酸洗成份控制并不容易(随酸洗量的增加,使用时间变化,酸洗液成份要发生变化)我们酸洗的配方与JB1255的略有不同的,用的是1 脱脂无水碳酸钠25-35 g磷酸三钠25-35 g氢氧化钠10-20 g水玻璃2-3 g水1000毫升2 热水清洗水100%3 流动水清洗水100%4 酸洗硝酸15-25ml水 1000ml5 流动冷水洗水100%6 明化1铬酐130-150g硫酸4 g水1000ml7 流动水清洗水100%8 明化2盐酸(d=1.19)100-200ml二氯化锡2g金属锡100-200g水1000ml9 流动冷水洗水100%10 中和无水碳酸钠4-6%水余量11 流动冷水洗水100%12 防锈亚硝酸钠6-8kg无水碳酸钠1-2kg水余量酸洗后烧伤部位呈黑色,无烧伤呈灰色(白烧伤很少见,一般如磨削发生严重操作失误时可能会出现)磁弹仪测烧伤还是很有效的,但有时磁弹值会受附近电磁信号的干扰,还有就是检测位置比较受限,受探头的影响一些位置测不到,特别是内表面,另外测试效率低,测试仅及一条线,不可能所有表面都测到谢谢各位了.我搜索到了一份操作指导书,原文贴出,供大家参考:磨削烧伤痕迹的显示:1 浸蚀溶液配方:4%硝酸酒精浸蚀:工件在溶液中浸蚀2分钟2 清洗工件在清水中清洗2分钟。
- 1、下载文档前请自行甄别文档内容的完整性,平台不提供额外的编辑、内容补充、找答案等附加服务。
- 2、"仅部分预览"的文档,不可在线预览部分如存在完整性等问题,可反馈申请退款(可完整预览的文档不适用该条件!)。
- 3、如文档侵犯您的权益,请联系客服反馈,我们会尽快为您处理(人工客服工作时间:9:00-18:30)。
品保课
页次/页数
4/7
表1
浸池
过程
浸池成分
浓度
温度℃
PH值
时间
各部分作用
1
热去脂
碱性去油脂剂
(4-5)%
》50
>10
>15分钟
去油脂
2
冷冲洗
氢氧化钠水溶液
(4-6)%
25
10-11.5
3分钟
去油脂
3
酸蚀
硝酸水溶液
(2-4)%
室温
<7
5-8秒
腐蚀
4
冷冲洗
氢氧化钠水溶液
(4-6)%
室温
11-12.5
ph值都须用专门的PH器具或溶度计来检验。
2)浸池定期更换,7、8池12周更换一次;2、4、6池一周更换;1池即洗涤池12周更换
一次;3、5酸池6周更换一次;9浸油池一年更换一次。
当酸溶液更新后,我们需用一件已烧伤的工件来检验腐蚀功能和浸泡时间,并对溶液的腐
蚀效果记录。
B类:轻微烧伤,磨削烧伤不连续,较窄的浅色显示;此类磨削烧伤降低表面硬度不显著。见图2
D类:较重的磨削烧伤,磨削烧伤连续较宽的深色显示。此类磨削烧伤降低表面硬度10HV或更多,如图3
E类:重新硬化,重新硬化的区域为白斑,周围是黑色的D级区域。这些白斑是未回火马氏体,对腐蚀没反应,见图4
国标中,根据磨削烧伤的面积,磨削烧伤又分为3等级,B类分级见表2
页次/页数
2/7
修订履历
修订日期
修订页次
原版本
新版本
修订摘要
标题:
磨削烧伤检测线操作指导书
文件编号
TJ-W-036
文件版本
1.0
制修订日期
2013年4月14日
制订单位
品保课
页次/页数
3/7
1.目的:规定渗碳钢工件做磨削烧伤检查的过程和责任以及对检测结果的判定和记录
2.检验流程
2.1磨削烧伤检验的方法
浙江台玖精密机械有限公司
磨削烧伤检测线操作指导书
文件编号TJ-W-036
文件版本1.0
制订单位品保课
制订日期2013年4月14日
修订日期年月日
页次页数
发
行
核准
审核
制订
浙江台玖精密机械有限公司
标题:
磨削烧伤检测线操作指导书
文件编号
TJ-W-036
文件版本
1.0
制修订日期
2013年4月15日
制订单位
品保课
品保课
页次/页数
5/7
图1-A级无烧伤
图2 B级轻微烧伤
图3 D级严重磨削烧伤
图4 E级烧伤
2.5检验频率
按客户要求
浙江台玖精密机械有限公司
标题:
腐蚀检测线操作指导书
文件编号
TJ-W-036
文件版本
1.0
制修订日期
2013年4月15日
制订单位
品保课
页次/页数
6/7
2.6磨削烧伤的维护和保养
1)因磨削烧伤线的功能有效性,应每周检验一次,并记录在相应表格中,各池的浓度或
磨削过程中会产生大量的磨削热,一部分被冷却液带走,另一部分被传导入加工件的浅表层内。并使工件表层温度升高。在磨
削热大量产生时会在齿表面形成回火层。当温度达到熔化
温度时,则经冷却液冷却形成二次淬火层,从而形成磨削烧伤。磨削烧伤工件表层会形成回火
层,其表层组织是回火马氏体,会和酸发生腐蚀反应,根据这个原理,我们可以使用硝酸腐蚀
表2表面烧伤级别
级别
回火表面积的最大百分比%
B1
10
B2
25
B3
无限制
蜗杆烧伤的验收和判废准则:A类合格,B1、B2、B3需提交客户仲裁。D、E类烧伤则判废
浙江台玖精密机械有限公司
浙江台玖精密机械有限公司
标题:
腐蚀检测线操作指导书
文件编号
TJ-W-036
文件版本
1.0
制修订日期
2013年4月15日
制订单位
1-3分钟
防锈
备注:1.检验必须按池1至池9依次进行检验,时间控制必须符合规定的时间。2.烧伤检验应由经过培训的品保课人员进行。
3.第1池需要加热至50摄氏度以上来自所以试验前需加热,试验完成后需关闭开关
2.3检验范围
主要针对蜗杆磨加工工件。即齿部表面烧伤检验。
2.4磨削烧伤检验的判定和记录
A类:无磨削烧伤,表面呈现均匀的灰色.见图2中的无烧伤区域
的方法检验。这里我们采用浸池的方式进行。
2.2磨削烧伤检测线的结构和检验流程
烧伤检测线的结构如图。检验流程见表1,检验的步骤按池1到池9进行。各池的化学成分及浸泡时间见表1
图1:烧伤检测线结构
浙江台玖精密机械有限公司
标题:
腐蚀检测线操作指导书
文件编号
TJ-W-036
文件版本
1.0
制修订日期
2013年4月15日
5秒
去酸
5
酸蚀
盐酸水溶液
(2-4)%
室温
<7
30-60秒
脱色
6
冷洗
氢氧化钠溶液
(4-6)%
室温
11-12.5
5秒
去酸
7
中和
碳酸钠水溶液
(4-6)%
室温
10-11.5
3分钟
中和酸
8
冷洗
碳酸钠水溶液
(4-6)%
室温
10-11.5
5秒
去碱
9
吹风机
去水
10
浸油
防锈油
----------
室温
----------