磨削烧伤的检测方法
磨削烧伤、工件裂纹

磨削烧伤1. 磨削烧伤的分类磨削时,由于磨削区域的瞬时高温(一般为900-1500℃)形成零件层组织发生局部变化,并在表面的某些部分出现氧化变色,这种现象称为磨削烧伤。
磨削烧伤对零件质量性能影响很大,在实际加工过程中应尽量避免。
磨削烧伤有多种不同的分类方法。
根据烧伤外观不同,可分为全面烧伤(整个表面被烧伤)、斑状烧伤(表面上出现分散的烧伤斑点)、均匀线条状烧伤、周期线条状烧伤;按表层显微组织的变化可分为回火烧伤、淬火回火烧伤;还可根据烧伤深度分为浅烧伤(烧伤厚度<0.05mm)、中等烧伤(烧伤层厚度在0.005~0.01mm之间)、深度烧伤(烧伤层厚度>0.01mm)。
在生产中,最常见的是均匀的或周期的线条状烧伤。
由于在磨削烧伤产生时往往伴有表面氧化作用,而在零件表面生成氧化膜。
又因为氧化膜的厚度不同而使其反射光线的干涉状态不同;因此呈现出多种颜色。
所以,人们通常用磨削表面的颜色来判断烧伤的程度。
对钢件来说,随烧伤的加强,颜色一般呈现白、黄、褐、紫、兰(青)的变化。
不同磨削深度下,加工表面的烧伤颜色和氧化膜厚度。
值得注意的是:烧伤颜色仅反映了较严重的烧伤现象,而当零件表面颜色不变时,其表面组织也可能已发生了烧伤变化,这类烧伤通常不易鉴别,所以对零件使用性能危害更大。
目前,人们为了更好地控制烧伤的程度,已根据表面组织的变化时烧伤进行了分级,一般从0-8共分九级,其中,0级最轻,8级烧伤最严重。
1.烧伤产生机理轴承套圈在磨加工中,由于磨粒对工件的切削、刻划和摩擦作用,使金属表面产生塑性变形,由工件内部金属分子间相对位移产生内摩擦而发热;砂轮切削时,相对于工件的速度很高,与工件表面产生剧烈的外摩擦而发热,又因为每颗磨料的切削都是瞬间的,其热量生成也在瞬间,又不能及时传散,所以在磨削区域的瞬时温度较高,一般可达到800~1500℃,如果散热措施不好,很容易造成工件表面的烧伤,也就是在工件的表层(一般有几十微米到击败微米)发生二次淬火及高温回火,破坏了工件表面的组织,肉眼可以看出严重的烧伤。
磨削烧伤检测操作指导书
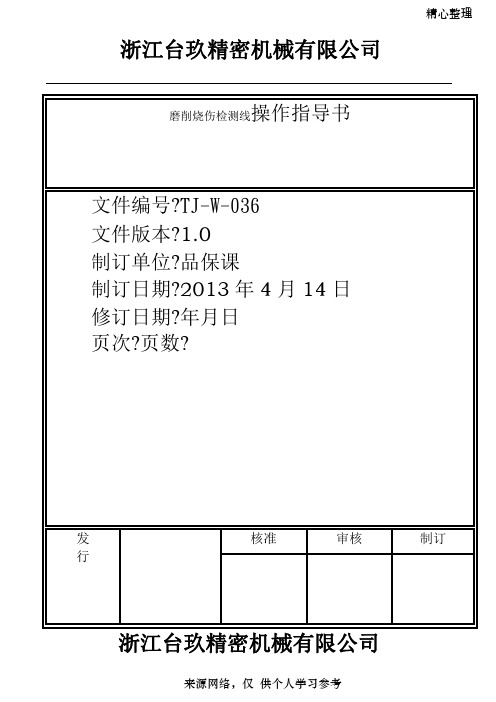
防锈
备注:1.检验必须按池1至池9依次进行检验,时间控制必须符合规定的时间。2.烧伤检验应由经过培训的品保课人员进行。
3.第1池需要加热至50摄氏度以上,所以试验前需加热,试验完成后需关闭开关
2.3检验范围
主要针对蜗杆磨加工工件。即齿部表面烧伤检验。
2.4磨削烧伤检验的判定和记录
A类:无磨削烧伤,表面呈现均匀的灰色.见图2中的无烧伤区域
ph值都须用专门的PH器具或溶度计来检验。
2)浸池定期更换,7、8池12周更换一次;2、4、6池一周更换;1池即洗涤池12周更换
一次;3、5酸池6周更换一次;9浸油池一年更换一次。
当酸溶液更新后,我们需用一件已烧伤的工件来检验腐蚀功能和浸泡时间,并对溶液的腐
蚀效果记录。
品保课
页次/页数
5/7
图1-A级无烧伤
图2B级轻微烧伤
图3D级严重磨削烧伤
图4E级烧伤
2.5检验频率
按客户要求
浙江台玖精密机械有限公司
标题:
腐蚀检测线操作指导书
文件编号
TJ-W-036
文件版本
1.0
制修订日期
2013年4月15日
制订单位
品保课
页次/页数
6/7
2.6磨削烧伤的维护和保养
1)因磨削烧伤线的功能有效性,应每周检验一次,并记录在相应表格中,各池的浓度或
磨削过程中会产生大量的磨削热,一部分被冷却液带走,另一部分被传导入加工件的浅表层内。并使工件表层温度升高。在磨
削热大量产生时会在齿表面形成回火层。当温度达到熔化
温度时,则经冷却液冷却形成二次淬火层,从而形成磨削烧伤。磨削烧伤工件表层会形成回火
层,其表层组织是回火马氏体,会和酸发生腐蚀反应,根据这个原理,我们可以使用硝酸腐蚀
磨削烧伤的检测方法

磨削烧伤的检测方法可能形成网状裂纹,它会导致齿面剥落.这当然是绝对不允许的。
用硬度测试法鉴别磨削烧伤的方法,并用超声波硬度计进行了实验,证明该方法简单易行,可以广泛应用于磨削加工中。
磨削烧伤及其常用检查方法在机械类产品中,很多重要零部件如轴承、齿轮、曲轴、凸轮轴、活塞销和万向节等,在热处理之后均需经过磨削加工。
相比之下,磨削时单位切削面积上的功率消耗远远超过其它加工方法,所转化热量的大部分会进入工件表面,因此容易引起加工面金相组织的变化。
在工艺参数、冷却方法和磨料状态选择不当的情况下,工件在磨削过程中极易出现相当深的金相组织变化层(即回火层),并伴随出现很大的表面残余应力,甚至导致出现裂纹,这就是所谓的磨削烧伤问题。
零部件的表面层烧伤将使产品性能和寿命大幅度地下降,甚至根本不能使用,造成严重的质量问题。
为此,生产企业一方面通过执行正确、科学的工艺规范,减轻和避免出现磨削烧伤现象;另一方面,加强对零部件的检验,及时发现不合格工件,并判断正在进行的磨削工艺状况。
但长期以来,对工件表面磨削烧伤的检验,除了最简单的目测法外,就是采用已延续多年的传统方法——酸洗法,即在被检零部件表面涂上酸液或将其浸入盛有按规定配制的酸液槽中。
之后(或在把工件取出后)根据表面呈现的不同颜色,对磨削烧伤的程度作出相应的判断。
一般地说,若色泽没有变化,就表明情况正常;而当颜色变成灰色,则说明已有烧伤情况存在,随着色泽变得越来越深,表示工件表面因温度更高,引起的磨削烧伤更为严重。
酸洗法具体如下:This is only a suggestion from my collegue ( Dino Calvanelli ) to find theburns on the gears此为有关过烧检测的建议:Clean each sample (part) to be inspected (free ofdirt,oil,grease,fingermarks,protective coatings,etc.).清洗产品,确保无灰尘、油污、手印、表面覆盖物等。
齿轮零件磨削烧伤的危害、检测和预防

⾼温下转变成奥⽒体。
如果冷却速度较低,则会重新变为⻢⽒体,零件表层⽐原淬⽕硬度稍有提⾼,⼀般在HRC 左右。
但此变质层性能稳定性较差,脆性较⾼,⼆次淬⽕烧伤区域周围通常伴有⼀圈严重的回⽕层,如图 (b)所⽰。
磨削烧伤的检测⽅法
⻮轮零件表⾯磨削烧伤后,
降低,甚⾄完全失去⼯作能⼒。
不合格的零件,需要对零件表⾯的磨削烧伤进⾏检测。
(a)回⽕烧伤 ( b)⼆次淬⽕烧伤
图1 磨削烧伤
(a) 磨削裂纹 (b) 磨削裂纹引起的⻮⾯剥落图2 磨削烧伤和磨削裂纹
利⽤钢材不同的⾦相组织对酸蚀有不同的敏感性。
回⽕⻢⽒体酸蚀后呈现灰⾊,如发⽣严重的回⽕烧伤,回⽕⻢⽒体转变为回⽕索⽒体,酸蚀后呈现⿊⾊;如发⽣⼆次淬⽕烧伤,⾦相组织为淬⽕⻢⽒体,酸蚀后呈现⽩⾊。
2.2 酸洗检查的步骤法反应⽐较灵敏,而且数值可靠,应⽤较为⼴泛。
磨削烧伤的预防
磨削烧伤和磨削裂纹均因磨削热过⾼引起,所以预防⽌烧伤和裂纹应该从降低磨削热的⻆度着⼿。
影响磨
(a) 磨削烧伤引起的⻮⾯剥落 (b) 中速轴⻮⾯磨削烧伤并产⽣剥落
图3 ⻮⾯剥落情况图4 ⾏星轮磨削烧伤⻮⾯剥落后造成⻮圈⻮⾯凹坑。
机械加工零件表面烧伤的金相检验

收稿日期:20190628 作者简介:焦丽(1975),女,河北石家庄人,高级工程师 ,主要从事金相检测及零部件的失效分析工作。
Email:1025496268@qq.com
《热处理》 2019年第 34卷 第 4期
·39·
部温度超过工件的回火温度(一般高于 300℃),从 而发生再次回火的现象。宏观表现为,由于不同程 度的氧化膜反射光干涉状态的不同而呈现不同的颜 色。从黄、褐、紫、青 灰 到 黑 色,表 示 氧 化 膜 逐 渐 增 厚,也表明磨削烧伤程度的逐次增大。氧化膜颜色 只是磨削烧伤的一种外观特征,有时因表面受热氧 化或冷却的复杂程度的影响,工件外观并无异常,但 酸蚀后却可见明显的斑状、条状缺陷,或黑或白,可 根据显微组织的特征作进一步验证。磨削烧伤有时 会表现为隐性缺陷,所以隐患更大。
cuttingheatislargeenoughtopermitpartcasetoreachahighertemperature,thustransformationtooccursandto
developacasewherenatureischanged.Inviewoftheabove,themeasurespreventingpartfrom burningmaybe
hardness,moreserious,willcauseparttocrack,eventobescrapped.Inaddition,wireelectrodecuttingislikely
toburnpart,too.Substantially,theburningofpartisconcernedwiththateithergrindingheatorwireelectrode
磨削烧伤检查规定

通常应对有回火显示的零件进行磁粉探伤检验,尤其是渗碳淬火硬化的零件。
7.2. 显微硬度计检查
7.2.1. 7.2.2. 7.2.3.
把要检查的部位用 800-1000 号的砂纸磨削 ,尽量少磨,能检查显微硬度即可。 工件要检查的部位不便于进行显微硬度检测,用线切割切下,并镶样。 用显微硬度计检测时,载荷 0.3Kg。对于用线切割切下零件的检验工件 0.05mm 处硬度≥695HV0.3,不允
7. 检验准则
7.1. 目视的外观与分类 未出现回火的零件在清洗和侵蚀后呈现均匀的灰色。局部回火区域在侵蚀后的零件上呈现深灰或黑色。通常,
随着颜色变的越深暗,说明回火烧伤程度越严重。如果在磨削过程中出现严重过热,将导致再硬化,再硬化
区域是一块白色或浅颜色的未回火马氏体,周围是黑色回火面。
所有的磨削后回火,尤其是再硬化的烧伤(即未回火马氏体)会影响零件的寿命,但零件仍可使用。
a)避免直接接触酸碱、溶剂。
b)将酸加入水中或酒精中,防止加反。
c)浸泡箱不用时加盖盖好。
d)遵守可燃和易燃液体储存及使用的安全措施。
有烧伤
无烧伤
机后要检查磨销烧伤。
做好记录。
10. 维护和管理 根据溶液的使用程度或当新配制溶液时,为检验溶液的性能,建议用该溶液侵蚀已知有回火显示的样品零件。
在侵蚀和检验后,该样品应再防锈保护备用,这类样品应定期更换。
根据使用程度,应定期检验溶液的浓度和杂质。
样品和溶液每 7 天更换一次。
11. 安全和环境保护。
磨削烧伤检查规定 1. 目的
保证工件在磨削工序中质量得到保证。 2. 适用范围
本标准规定了用化学侵蚀方法对磨削表面的局部过热进行检验及其分类的标准操作程序和要求,同时硬度法 作为对化学侵蚀方法的校核。 本标准适用于工件在热处理后,进行磨削工序中的检查。对于调质后、高频淬火后、渗碳淬火后的工件都适 用。 本标准不适用氮化零件和不锈钢零件。 化学侵蚀方法对表面硬度的变化的反映比大多数硬度测试方法更为敏感。 表面回火侵蚀检验应在表面磨削后,并在进一步精加工工序之前进行。比如连杆在珩磨前、曲柄销在研磨前。 3. 引用标准 GB/T 17879-1999 齿轮磨削后表面回火的浸蚀检验 4. 设备 4.1. 容器的材料与容器内溶液不得发生反应,也不得损伤被处理的零件。所有容器都应贴上所盛溶液的标签,并 在不用时盖好。本公司采用玻璃烧杯,并用平板玻璃盖好。 4.2. 被检验区域照明 被检验区域应有充分的照明,没有阴影和反射。摧荐被检验区域的光照度应不低于 3200lx。 4.3. 计时装置 应使用适当的计时器(秒表)。保证一组中的所有零件处理过程一致。 4.4. 清洗装置 应采用碱清洗器、蒸汽去油器、溶液清洗装置或相应的清洗装置。 5. 试剂 所有的化学试剂应为工业级或更纯的等级。 5.1. 清洗材料 所有清洗材料应保证能去除所有的污渍、磨粒和油渍,使被检表面可形成不破水膜。不破水膜是指表面用低 于 40℃的清水漂洗干净后,水膜至少应在 15S 内保持不破。 5.2. 硝酸 硝酸密度ρ=1.42Kg/l 5.3. 盐酸 盐酸密度ρ=1.19Kg/l 5.4. 酒精 应使用清洁的、不含油等杂质的甲醇或变性乙醇。 5.5. 水 清洁、无杂质。 5.6. 碱溶液 应使用 4%——6%的氢氧化钠溶液,其 PH≥10。 6. 检验程序 工件清洗→清洗后零件表面应达到能形成不破水膜→侵蚀→检验 6.1. 清洗 a)采用蒸汽清洗。 b)碱洗或超声波清洗。 6.2. 侵蚀 6.2.1. 腐蚀液的配制。
磨削烧伤检查

磨削烧伤检查2#酸洗液配制合成:将5L浓度为69%~71%的工业硝酸缓缓注入酒精中,稀释成100L溶液,搅拌均匀,混合成酸洗溶液。
3#酸洗液配制合成:10L浓度为36%~38%的工业盐酸缓缓注入甲醇中,配制成100L溶液, 搅拌均匀。
4#中和液配制合成:1Kg的碳酸钠加入100Kg水中,搅拌均匀,混合成中和液(碳酸钠与水的重量比为0.01:1)。
加入足够的酚酞指示液,目视观察溶液的中和点(浅粉红色)。
当溶液不在为浅粉红色时,需将溶液废弃。
酸洗程序:1.清洗液:粗磨或精磨完了的零件上残留的可溶乳剂要用1#热水快速漂洗,再放在60~66C°的1#清洗液中清洗至少5分钟。
如果是超精研零件表面有油污时,可先用特殊的1#清洗液清洗煤油清洗后,再按正常程序进行。
2.酸洗液:将零件浸入2#酸洗液中,并且上下搅动,直到磨削面都变成黑色(不要超过10秒)。
通常腐蚀的时间为3~5秒,如果一定要超过10秒钟零件才能变黑,就要更换溶液。
3.自来水漂洗:将酸洗后的零件立即用流动的自来水冲洗。
4.2#酸洗液:将零件浸入3#酸洗液上下搅动。
通常搅动的时间为10秒钟(但不要超过20秒钟),如果一定要超过20秒钟,就要更换溶液。
5.自来水漂洗:酸洗后的零件用流动的自来水冲洗。
6.中和液:将零件浸入中和液中搅动2~5秒钟。
7.自来水漂洗:将中和后的零件再用流动的自来水冲洗。
8.防锈:酸洗完了的零件应立即浸入专用防锈水中,取出仔细检查烧伤。
9.酸洗检验员检验后,将结果记录在“轴承零件表面酸洗检查记录”中。
酸洗结果的观察及解释:1.中度的灰色:意味着正常的磨加工表面。
2.黑色或深色区域:意味着表面存在再回火烧伤。
3.亮色或白色区域:意味着表面存在再淬火烧伤,在任何情况下均不可接受。
特例:非常浅的表面再淬火烧伤如经过二次酸洗可以除去,则可以接受。
在接受批量前,请再二次酸洗有代表性的产品后,根据结果判定。
4.当目视判断有困难时,可进行二次酸洗。
自制件烧伤零件检测详细过程

自制件烧伤零件检测详细过程磨削烧伤在传动工件的加工工艺过程中不可避免。
这些零件在精磨前一般会经过淬火处理,使表面硬度值达到一定的范围。
但在磨削工艺过程中,由于进给量、冷却液类型和流速、砂轮表面状况等因素综合影响,使得磨削产生的热量并不能总被均匀消散,部分没有消散掉的热量进入金属表面,引起回火现象的发生,更严重的情况还会产生二次淬火现象,使得受影响的部位的硬度值超出合格范围,同时伴随金相硬度的变化,应力场还会朝着有害的方向发展,这就是磨削烧伤的成因。
磨削烧伤的现象一旦发生,烧伤的部位的表面抗疲劳强度就会显著地下降。
这样的工件在服役过程中,会发生逐渐开裂甚至表面脱落的情况,造成整个动力系统的失效。
因此对传动工件进行表面磨削质量的检测非常的重要。
传动的检测磨削烧伤有不同的方法,例如目视法、金相法、硬度法以及酸洗法。
磨削烧伤产生的部位具有一定随机性,因此局部的检测方法会有遗漏的问题发生,所以目视法、金相法以及硬度法在实践过程中一般较少应用,对于要求较高的零件这些方法还会被禁止使用。
酸洗法是传统方法中使用最广泛的一种方法,因为检测形式是将工件整个浸润到酸液中,所有的磨削表面都会被覆盖到,因此从方法上来说发生漏检的情况较少。
但是,酸洗法的判别主要是通过颜色的变化,而颜色的变化判断比较依赖于检测人员的经验,经验的不足通常也会造成一定的误判。
此外随着对土壤环境保护的政策越来越严格,酸洗工艺残留的酸液处理也非常麻烦,导致酸洗方法的应用空间变得逐渐狭窄,甚至逐渐被强制摒弃。
在方法局限和政策限制下,另一种纯物理形式的检测方法,巴克豪森噪声法(磁弹法)受到越来越广泛的认可。
巴克豪森噪声法利用了金属部件的应力场和硬度(金相组织)会影响其本身的磁滞回线效应,然后通过激励并捕捉磁滞回线的变化,来间接定性判断零件表面的硬度分布与应力分布异常与否,进而判断是否有烧伤的发生。
该方法的理论成熟,市场商业化应用也得到全球知名动力系统公司如GE、奔驰、大众、沃尔沃、康明斯以及其供应链的认可。
变速器齿轮齿部磨削烧伤及检测方法对比分析
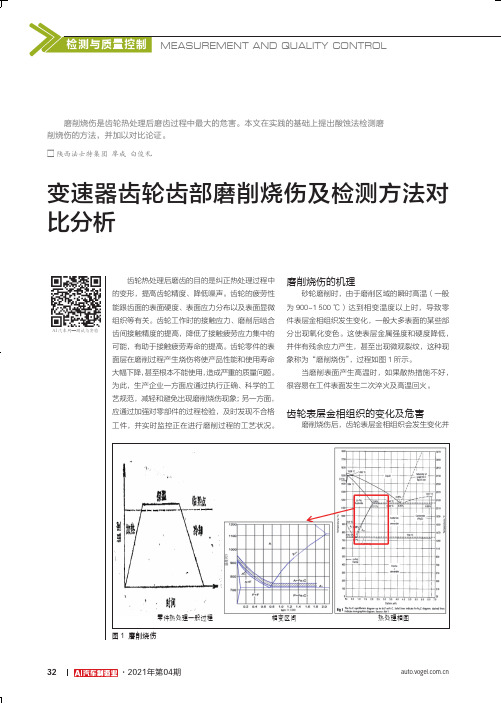
AI汽车网—测试与实验零件热处理一般过程相变区间热处理相图图1 磨削烧伤・2021年第04期・℃,在冷却液的作用下形成二次淬火马氏体,而在表层下,由于温度梯度大,时间短,只能形成高温回火组织,这就会在表层和次表层之间产生拉应力,而表层为一层薄而脆的二次淬火马氏体,当表层承受不了拉应力时,将产生裂纹。
淬火烧伤:当磨削区温度超过相变温度AC1 (30~50) ℃时,工件表层局部区域就会变成奥氏体,随后受到冷却液及工件自身导热的急速冷却作用而在表面极薄层内出现二次淬火马氏体,次表层为硬度大为降低的回火索氏体,这就是二次淬火烧伤。
退火烧伤:如果磨削区温度超过了相变温度,而磨削区域又无冷却液进入,表层金属将产生退火组织,表面硬度将急剧下降,这种烧伤称为退火 烧伤。
回火烧伤:指当磨削区温度显著地超过钢的回火温度但仍低于相变温度时,工件表层出现回火屈氏体或回火索氏体软化组织的情况。
磨削烧伤的检测方法目前磨削烧伤的检测方法有:观色法、酸蚀法、显微硬度法、金相检测法和磁弹法(巴克豪森噪声法)。
我公司根据实际需求,结合加工工艺流程,选用的是酸蚀法检测磨削烧伤。
酸蚀方法(硝酸溶液酸蚀法)步骤包括::预清洗→预加热→酸浸腐蚀(硝酸+甲醇溶液)→冲洗→脱水→漂白(盐酸+甲醇溶液)→冲洗→中和→冲洗→脱水→防锈等11个步骤。
方法每次酸蚀检测磨削烧伤前需要配制酸蚀溶液,配制好溶液之后需要用酸碱中和滴定的方法检测酸蚀溶液酸的体积百分比浓度。
二次回火区的颜色为浅褐色至黑色,即颜色深于正常酸蚀表面的均匀灰色;再次淬火区颜色为浅灰色至白色,周围有浅褐色至黑色边界;最终对其进行烧伤等级评定。
烧伤等级评定是根据磨削烧伤的面积和磨削烧伤的程度进行判定,分为4个等级,分别是A 、B 、、E ,如图2~5近期,客户推荐使用方法蚀,抗渣剂溶液酸蚀法包括预清洗→预加热→硝酸Computed Tomograp hy 无损测量工业CT 解决方案Optical H igh Speed Scann ing 高速光学扫描测量解决方案Mobile Measuring ARM便携式测量解决方案Shopflo or CMM 车间坐标测量解决方案3D Digital Solution 数字化解决方案Automotive Solution 汽车测量解决方案3D M et ro lo gy三坐标测量技术T 展位号E2-B 101水溶液腐蚀(硝酸+水+抗渣剂溶液)→烘干→冲洗→防锈等6的灰色,取出后进行冲洗,中和,再冲洗,脱水,烘干之后采用目测方法对零件表面进行检查,评Anti-Smut 100是用于硝酸刻蚀溶液的一种抗渣添加剂产品特性•在硝酸蚀刻时抑制零件表面附着渣子•在硝酸里非常稳定•易溶进溶液•非常好的润湿性应用•Anti-Smut 100推荐用于各种硝酸蚀刻溶液(例如:高强度合金钢零件的蚀刻检验)•Anti-Smut 100抗渣剂需在室温下溶入蚀刻溶液,并进行轻微的手动搅拌,以便使其混合均匀•回火蚀刻溶液的典型成分如下:0.3% ~5% v/v 硝酸3% ~5% 抗渣剂其余为水表 Anti-Smut 100特性恷㱷⌍⠕★㓟㿦ḣ䟧䯉⍇㽯䕼共澳恷㱷⌍⠕★ 䐞㿦ḣ䟧䯉䊯孠⍇䅆䆵淐共◡♖恷㱷⌍䧮晡㓟㿦ḣ䟧䯉澳恷㱷⌍䧮晡 䐞㿦ḣ䟧澳䯉䊯孠淐共≯媯澳澳㓟㿦ḣ䟧䯉澳㓟㿦ḣ䟧䯉澳恷㱷⌍⠕★㓟㿦ḣ䟧䯉⍇㽯䕼共澳恷㱷⌍⠕★ 䐞㿦ḣ䟧䯉䊯孠⍇䅆䆵淐共◡♖恷㱷⌍䧮晡㓟㿦ḣ䟧䯉澳恷㱷⌍䧮晡 䐞㿦ḣ䟧澳䯉䊯孠淐共≯媯澳澳㓟㿦ḣ䟧䯉澳㓟㿦ḣ䟧䯉澳㿦ḣ䟧䯉澳澳澳恷㱷⌍⠕★㓟㿦ḣ䟧䯉⍇㽯䕼共澳恷㱷⌍⠕★ 䐞㿦ḣ䟧䯉䊯孠⍇䅆䆵淐共◡♖恷㱷⌍䧮晡㓟㿦ḣ䟧䯉澳恷㱷⌍䧮晡 䐞㿦ḣ䟧澳䯉䊯孠淐共≯媯澳澳㓟㿦ḣ䟧䯉澳㓟㿦ḣ䟧䯉澳㿦ḣ䟧䯉㿦ḣ䟧䯉恷㱷⌍⠕★㓟㿦ḣ䟧䯉⍇㽯䕼共澳恷㱷⌍⠕★ 䐞㿦ḣ䟧䯉䊯孠⍇䅆䆵淐共◡♖恷㱷⌍䧮晡㓟㿦ḣ䟧䯉澳恷㱷⌍䧮晡 䐞㿦ḣ䟧澳䯉䊯孠淐共≯媯澳澳㓟㿦ḣ䟧䯉澳㓟㿦ḣ䟧䯉澳㿦ḣ䟧䯉㿦ḣ䟧䯉图2 A 级图4 C 级图3 B 级图5 D 级。
磨削烧伤检查规定

a)避免直接接触酸碱、溶剂。
b)将酸加入水中或酒精中,防止加反。
c)浸泡箱不用时加盖盖好。
d)遵守可燃和易燃液体储存及使用的安全措施。
有烧伤
无烧伤
许表面硬度出现严重的低头现象。对于高频或调质后的零件,检测后显微硬度转换为洛氏硬度应不低于
没有磨削时的表面硬度,但应低于没有磨削时的表面硬度加 4HRC。 8. 回火侵蚀的去除
回火侵蚀后的颜色,采用珩磨去除。
9. 检验人员及检验频次 检验人员车间质检员。
按照工艺(修砂轮的频次)检查,每 2 小时检查 1 件,砂轮更换、设备维修、操作工更换、异常停机重新开
机后要检查磨销烧伤。
做好记录。
10. 维护和管理 根据溶液的使用程度或当新配制溶液时,为检验溶液的性能,建议用该溶液侵蚀已知有回火显示的样品零件。
在侵蚀和检验后,该样品应再防锈保护备用,这类样品应定期更换。
根据使用程度,应定期检验溶液的浓度和杂质。
样品和溶液每 7 天更换一次。
11. 安全和环境保护。
酒精
浸泡并干燥 去水
零件应浸泡足够的时间,以使零
4.
脱色
盐酸 50% (容积)
件上呈现出均匀的棕灰色。脱色 10 秒(10-20 秒) 时间应重复试验以确定确切时
间。
5
漂洗
水
8秒
去酸
6
中和
碱性溶液 PH≥10 20 秒(10-60 秒) 浸入后搅动零件
7
漂洗
水
8秒
去碱
8
酒精浸泡
酒精
浸泡并干燥 去水
9
通常应对有回火显示的零件进行磁粉探伤检验,尤其是渗碳淬火硬化的零件。
7.2. 显微硬度计检查
巴克豪森噪音法检测磨削烧伤原理

磁弹法检测零部件磨削烧伤原理概述一、什么是磨削烧伤?磨削烧伤是指机械零部件如齿轮、轴承套圈、凸轮轴、曲轴、飞机起落架、喷油嘴等在经过磨削工艺处理时,由于磨削产生的热量进入零部件的表层,产生回火层,致使零部件的表面硬度下降产生软点,同时产生相应的拉应力,而大大降低产品的使用寿命甚至是不合格产品,统称为磨削烧伤。
用酸洗法显示的磨削烧伤状况二、磨削烧伤与零部件材质的关系目前会产生磨削烧伤的部件,多为铁磁性材料,即这类材料都可以被磁化。
对于存在的极小部分非铁磁性材料部件产生的烧伤问题不在磁弹法的讨论范围内。
根据磁弹法理论,这类材料在正常情况都由叫“磁畴”的小区域构成:每一个小多边形,我们称之为磁畴如上图所示,在无外加磁场和加工处理的情况下,铁磁性材料的内部磁矩都整齐排列,但方向不同,整个材料的磁力矢量和为零,对外不显示磁性。
当铁磁性材料在经过磨削加工处理过程中,由于磨削产生的高温传导到工件表面(一般情况是浅浅的一层,不超过1mm),致使某些区域产生回火层,工件出现软点。
对应于磁矩来说,就是原来“有序”的排列经过磨削处理,都变得“无序”,无序的程度根据磨削的程度而不同,就是磨削越厉害的地方,这种无序的程度就越强。
磁矩的无序化示意图因此,磨削烧伤的严重程度通过磁畴和磁化机理,就可以跟磁序相对应起来。
三、铁磁性材料的磁化机理通过上面的叙述我们知道,铁磁性材料在无任何外加影响下不显示磁性,因为虽然各个磁畴内的磁矩有磁极,但磁畴内的磁矩方向又各异,导致矢量和为零,所以不显示磁性。
但如果有外加磁场的情况下,结果就会发生变化。
通过外加磁场,我们可以将所有的磁畴内的磁矩方向进行纠正,变得和外加磁场的磁力方向一致,就使其变得“有序”了。
磁矩经过外加磁场的作用变得有序磁化过程示意图在磁化过程中,有一种力的作用,我们称之为“矫顽力”,对于无序程度较低的磁矩,磁化时需要的矫顽力较小,无序程度较高的磁矩,需要的矫顽力则较大。
因此,磨削烧伤的严重程度,我们又可以和磁化过程中需要的矫顽力大小来对应。
酸浸法检查磨削烧伤
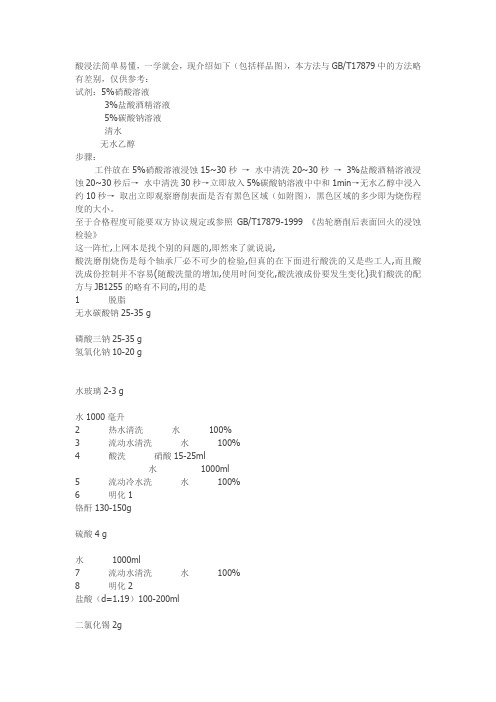
酸浸法简单易懂,一学就会,现介绍如下(包括样品图),本方法与GB/T17879中的方法略有差别,仅供参考:试剂:5%硝酸溶液3%盐酸酒精溶液5%碳酸钠溶液清水无水乙醇步骤:工件放在5%硝酸溶液浸蚀15~30秒→水中清洗20~30秒→3%盐酸酒精溶液浸蚀20~30秒后→水中清洗30秒→立即放入5%碳酸钠溶液中中和1min→无水乙醇中浸入约10秒→取出立即观察磨削表面是否有黑色区域(如附图),黑色区域的多少即为烧伤程度的大小。
至于合格程度可能要双方协议规定或参照GB/T17879-1999 《齿轮磨削后表面回火的浸蚀检验》这一阵忙,上网本是找个别的问题的,即然来了就说说,酸洗磨削烧伤是每个轴承厂必不可少的检验,但真的在下面进行酸洗的又是些工人,而且酸洗成份控制并不容易(随酸洗量的增加,使用时间变化,酸洗液成份要发生变化)我们酸洗的配方与JB1255的略有不同的,用的是1 脱脂无水碳酸钠25-35 g磷酸三钠25-35 g氢氧化钠10-20 g水玻璃2-3 g水1000毫升2 热水清洗水100%3 流动水清洗水100%4 酸洗硝酸15-25ml水 1000ml5 流动冷水洗水100%6 明化1铬酐130-150g硫酸4 g水1000ml7 流动水清洗水100%8 明化2盐酸(d=1.19)100-200ml二氯化锡2g金属锡100-200g水1000ml9 流动冷水洗水100%10 中和无水碳酸钠4-6%水余量11 流动冷水洗水100%12 防锈亚硝酸钠6-8kg无水碳酸钠1-2kg水余量酸洗后烧伤部位呈黑色,无烧伤呈灰色(白烧伤很少见,一般如磨削发生严重操作失误时可能会出现)磁弹仪测烧伤还是很有效的,但有时磁弹值会受附近电磁信号的干扰,还有就是检测位置比较受限,受探头的影响一些位置测不到,特别是内表面,另外测试效率低,测试仅及一条线,不可能所有表面都测到谢谢各位了.我搜索到了一份操作指导书,原文贴出,供大家参考:磨削烧伤痕迹的显示:1 浸蚀溶液配方:4%硝酸酒精浸蚀:工件在溶液中浸蚀2分钟2 清洗工件在清水中清洗2分钟。
- 1、下载文档前请自行甄别文档内容的完整性,平台不提供额外的编辑、内容补充、找答案等附加服务。
- 2、"仅部分预览"的文档,不可在线预览部分如存在完整性等问题,可反馈申请退款(可完整预览的文档不适用该条件!)。
- 3、如文档侵犯您的权益,请联系客服反馈,我们会尽快为您处理(人工客服工作时间:9:00-18:30)。
磨削烧伤的检测方法可能形成网状裂纹,它会导致齿面剥落.这当然是绝对不允许的。
用硬度测试法鉴别磨削烧伤的方法,并用超声波硬度计进行了实验,证明该方法简单易行,可以广泛应用于磨削加工中。
磨削烧伤及其常用检查方法在机械类产品中,很多重要零部件如轴承、齿轮、曲轴、凸轮轴、活塞销和万向节等,在热处理之后均需经过磨削加工。
相比之下,磨削时单位切削面积上的功率消耗远远超过其它加工方法,所转化热量的大部分会进入工件表面,因此容易引起加工面金相组织的变化。
在工艺参数、冷却方法和磨料状态选择不当的情况下,工件在磨削过程中极易出现相当深的金相组织变化层(即回火层),并伴随出现很大的表面残余应力,甚至导致出现裂纹,这就是所谓的磨削烧伤问题。
零部件的表面层烧伤将使产品性能和寿命大幅度地下降,甚至根本不能使用,造成严重的质量问题。
为此,生产企业一方面通过执行正确、科学的工艺规范,减轻和避免出现磨削烧伤现象;另一方面,加强对零部件的检验,及时发现不合格工件,并判断正在进行的磨削工艺状况。
但长期以来,对工件表面磨削烧伤的检验,除了最简单的目测法外,就是采用已延续多年的传统方法——酸洗法,即在被检零部件表面涂上酸液或将其浸入盛有按规定配制的酸液槽中。
之后(或在把工件取出后)根据表面呈现的不同颜色,对磨削烧伤的程度作出相应的判断。
一般地说,若色泽没有变化,就表明情况正常;而当颜色变成灰色,则说明已有烧伤情况存在,随着色泽变得越来越深,表示工件表面因温度更高,引起的磨削烧伤更为严重。
酸洗法具体如下:This is only a suggestion from my collegue ( Dino Calvanelli ) to find theburns on the gears此为有关过烧检测的建议:Clean each sample (part) to be inspected (free ofdirt,oil,grease,fingermarks,protective coatings,etc.).清洗产品,确保无灰尘、油污、手印、表面覆盖物等。
Etch sample by immersing for 15/30" in a 5% solution (by volume) of Nitric acid in distilled water or alcohol.将产品浸在5%(体积比)的溶液(硝酸:水或硝酸:酒精)中腐蚀15至30秒,Rinse the sample in water (warm water preferable).Then rinse in acetone oralcohol.在温水中漂洗/冲洗产品,然后用丙酮或酒精中漂洗/冲洗。
Re-etch the sample by immersing for 15/30" in a 3% solution (by volume) ofHydrochloric acid in acetone or alcohol.再将产品浸在3%(体积比)的溶液(盐酸:丙酮或盐酸:酒精)中腐蚀15至30秒,Uniformly agitate the solution to avoid a spotty etching condition.均匀的摇动溶液以避免片面的点腐蚀。
If immersion is not convenient,etch with a cotton swab.Immediately after the second etch,rinse the sample in water.第二次腐蚀后立即在水中漂洗/冲洗产品。
If the part is to be used or preserved ,neutralize any remainingacid by immersing in a weak alkaline solution suchas 5% solution of sodium bicarbonate in water.如产品需使用或保存,用弱碱溶液中和残留的酸质,如5%的碳酸钠溶液。
Finally ,rinse the sample in alcohol and dry with an air blast.最后,用酒精漂洗/冲洗产品并用空气吹干。
Repetition of the above sequence may be necessary to develop propercontrast.为获得最合适的检测状态,有必要重复上述步骤。
Etch times are for general cases;longer times may be required to obtain accurate results.腐蚀次数基于一般状态;为获得准确的结果,需要更长的次数。
Examine the sample for tempering and rehardening under adeguatelight.在明亮的灯光下检测产品。
Low power magnification (up to 10x) may be used to aid the examination.使用低倍放大以帮助检测Areas of the tooth surface where overheating has occurred ,appear brown or black on a light brown or graybackground.在褐色或灰色灯光下,齿面过烧的部分将显示为棕褐色或黑色。
Areas where untempered martensite has formed appear as white areassurrounded by black,tempered areas.未回火的马氏体处会形成白色区域,并被黑色的回火区域包围。
传统检查方法虽然简单易行,但有着很大的局限性,主要是工件表面经酸液浸蚀,即使为无问题的零部件,也不能再予以使用。
传统方法执行的实际上是一种破坏性检查。
从以上描述可知,酸洗法本质上属于定性检查,难以对磨损烧伤程度做出定量的说明。
鉴于上面两点,采取传统方法时,只能采用抽检的方式,且样本很小,欲对所执行的工艺过程作出较确切的评价并予以改进是很困难的。
理论表明,酸洗法检验只能反映因金相组织结构变化引起的硬度下降这种情况,对于工件表面存在的残余应力则无法反映,故在全面揭示磨削烧伤的程度上显得不足。
另一方面,由于使用了酸液,企业增加了消除环境污染的负担;传统检查方法的规范化可靠性水平较低,更难以制定可操作性强的评定标准。
一种新颖、高效的磨削烧伤检测方法——磁弹法(1)工作原理磁弹法即BN法(Barkhansen Noise Method),是以1919年发现的物理学Barkhansen效应为基础开发的一种测试方法,它能有效地对磨削烧伤进行测试。
近年来,利用磁弹法研制的测试仪器已在零部件表面磨削烧伤检测中逐步得到应用,并充分显现出优越性。
众所周知,出现磨削烧伤的那些零部件,主要由铁磁性材料制成,在正常情况下,其磁序(体现在多晶体的磁畴结构里)呈有规则的排列。
但如前所述,磨削烧伤后产生的金相组织变化及可能出现的很大残余应力都将引起磁畴结构内的磁序变化。
Barkhausen效应指出,矫顽(磁)力,即改变被颠倒极性所需要的磁场强度是与铁磁性材料晶格结构错位和残余应力等的程度有关的。
利用BN法探测被检零部件表面磨削烧伤的机理就在于此。
在BN法基础上开发的检测仪器的工作原理中,“门”形电感线圈形成的磁场在被测钢件中所产生的效应取决于工件表面磨削烧伤的实际状况,而由此在工件周围所形成的磁场又会使测头在测试区域的感应线圈中产生相应的电信号,而这一信号直接与工件磨削烧伤的程度有关。
测试仪器的工作过程:由电感线圈引起相应的作用磁场,通过被检工件,进而在传感头中产生对应的检测信号(称为B信号),该B信号经过放大和滤波等处理环节,最后被显示和输出。
磨削烧伤的物理表现主要是因表面金相组织结构变化而产生的回火层所引起的硬度下降,以及在表面出现的残余应力(拉应力)。
检测仪器对它们都能作出敏感的反映。
随着被检工件表面硬度值Rc由高向低变化,检测仪器输出的相应B信号幅值将由小到大,即硬度低对应的检测信号高,硬度高对应的检测信号低。
由仪器对表面残余应力的反应可见,当残余应力由小到大,即由负(压应力)向正(拉应力)变化时,检测仪器输出的相应B信号幅值将由低向高变化。
(2)评定特征值mp及其定标上述由仪器特殊设计的激磁电路和传感装置产生的检测信号,乃是Barkhansen磁弹法效应的一种量化表达,以特征值mp(magnetoelastic parameter)标志。
mp与被检测工件表面的变异状态,如残余应力成比例,其数值能在仪器的屏幕上显示、输出。
但利用mp来反映工件磨削烧伤的程度从本质上来说是一种比较测量的方式,为了能够真正地对其做准确的定量描述,还必须解决“定标”的问题。
定标包括二项内容:①确定不合格品的界限。
有目的地制作一批样品,其中包括有一些磨削烧伤程度不同的工件,利用酸洗法按用户的评定标准对它们作出不同的判断后,将介于合格/不合格临界状态的若干工件通过仪器求得相应的mp值,然后取其平均值作为不合格的界限;②进行校准。
校准就是找出特征值mp与采用酸洗法确认的磨削烧伤程度之间的相关性。
具体来说,就是需确定一个相关系数MAGN,并利用仪器控制面板上的拨盘予以设置,MGAN值的范围从0到99,一般尾数取5或0。
为此,可在前面的样品中找二根表面状态差异较大的工件,选定工件上的某一位置,在检测仪器上的MGAN取值间隔为5或10时,以静态方法读出二组对应的mp 值,如MGAN为30时在二个工件上测出2个mp值,在MGAN为40时又得到2个,直到MGAN=90。
两两相减后必然能得到一个最大值,以这时的MGAN值作为相关系数,在面板上予以设置。
注意:在实际执行“定标”时,也可先利用第一项中的样件求得相关系数MGAN,然后再找出不合格品界限。
否则,在前一项操作中,会由于任意设置的MGAN(一般取50或60)给界限值带来一些偏差。
应用实例尽管在汽车行业中,不少场合都可以采用这种以BN法为基础研制的磨削烧伤测试仪器,但相比之下,对发动机凸轮轴中各挡凸轮的检测是用的最多的。
这一方面是因凸轮乃承重件,工作条件差;另一方面是由于凸轮圆周方向不同曲率半径的特点可能会造成磨削过程中表面状态的差异,在这种情况下,出现磨削烧伤的机率会增大。
磨削烧伤测试仪器是一种高效率半自动检测设备,很适合于在批量生产条件下的汽车发动机厂、内燃机厂使用。