磁弹法检查零部件表面磨削烧伤的新方法
磨削烧伤检测操作指导书
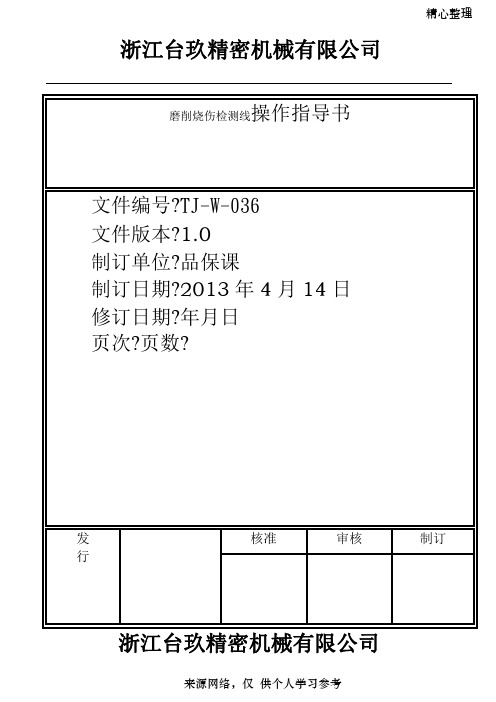
防锈
备注:1.检验必须按池1至池9依次进行检验,时间控制必须符合规定的时间。2.烧伤检验应由经过培训的品保课人员进行。
3.第1池需要加热至50摄氏度以上,所以试验前需加热,试验完成后需关闭开关
2.3检验范围
主要针对蜗杆磨加工工件。即齿部表面烧伤检验。
2.4磨削烧伤检验的判定和记录
A类:无磨削烧伤,表面呈现均匀的灰色.见图2中的无烧伤区域
ph值都须用专门的PH器具或溶度计来检验。
2)浸池定期更换,7、8池12周更换一次;2、4、6池一周更换;1池即洗涤池12周更换
一次;3、5酸池6周更换一次;9浸油池一年更换一次。
当酸溶液更新后,我们需用一件已烧伤的工件来检验腐蚀功能和浸泡时间,并对溶液的腐
蚀效果记录。
品保课
页次/页数
5/7
图1-A级无烧伤
图2B级轻微烧伤
图3D级严重磨削烧伤
图4E级烧伤
2.5检验频率
按客户要求
浙江台玖精密机械有限公司
标题:
腐蚀检测线操作指导书
文件编号
TJ-W-036
文件版本
1.0
制修订日期
2013年4月15日
制订单位
品保课
页次/页数
6/7
2.6磨削烧伤的维护和保养
1)因磨削烧伤线的功能有效性,应每周检验一次,并记录在相应表格中,各池的浓度或
磨削过程中会产生大量的磨削热,一部分被冷却液带走,另一部分被传导入加工件的浅表层内。并使工件表层温度升高。在磨
削热大量产生时会在齿表面形成回火层。当温度达到熔化
温度时,则经冷却液冷却形成二次淬火层,从而形成磨削烧伤。磨削烧伤工件表层会形成回火
层,其表层组织是回火马氏体,会和酸发生腐蚀反应,根据这个原理,我们可以使用硝酸腐蚀
检查零部件表面磨削烧伤的新方法

是在 B N法基础上开发的检测 出现裂纹 ,这就是所谓的磨削烧伤 较确切的评价并予以改进是很困难 图 1 仪器的工作原理示意图。 问题 。 的。
零部件的表面层烧伤将使产品
理论表明, 酸洗法检验只能反
图 l 中,“ a 门”形电感线圈形
性能和寿命大幅度地下降 , 甚至根 映ห้องสมุดไป่ตู้金相组织结构变化引起 的硬度
磨削烧伤及其常用检查方法
众所周知 ,出现磨削烧伤的那 些零部 件,主要 由铁磁 性材 料制 部件 如轴 承 、齿 轮、曲轴、凸轮 传统检查方法虽然简单 易行 , 其磁序 ( 体现 轴 、活塞销和万 向节等,在热处理 但有着很大的局限性,主要是工件 成。在正常情况下 , 之后 均需 经过磨削 加工。相 比之 表面经酸液浸蚀 ,即使为无问题的 在多晶体的磁畴结构里)呈有规则 也不能再予以使用。传统 的排列。但如前所述,磨削烧伤后 下, 磨削时单位切削面积上的功率 零部件 , 消耗远远超过其它加工方法,所转 方法执行的实际上是一种破坏性检 产生的金相组织变化及可能出现的
过程 :由电感线圈引起相应的作用
1 t a m t )标 志oI a ipr e r sc a e I l p与被 检 尽管在汽车行业 中, 不少场合 磨削烧伤的物理表现主要是因 测工件表面的变异状态,如残余应 都可以采用这种以 B N法为基础研 其数值能在仪器的屏幕 制的磨削烧伤测试仪器,但相 比之 表面金相组织结构变化产生回火层 力成 比例 , I l p 所引起 的硬度下降,以及在表面出 上显示 、输 出。但利用 I 来反映 下,对发动机凸轮轴中各挡凸轮 的 现的残余应力 ( 拉应力) 。图 1 所 工件磨削烧伤的程度从本质上来说 检 测是用 的最多 的 。这一方 面是 因 示的检测仪器对它们都能作出敏感 是一种比较测量的方式,为了能够 凸轮乃承重件 , 工作条件差;另一
磨削烧伤与其解决方案

磨削烧伤及其解决方案张国耀(郑州超微磨料具有限公司河南郑州450001)摘要:鉴于磨削过程中工件烧伤的问题一直困扰着产品的质量问题,从磨削烧伤的形成的机理、磨削烧伤的检查方法、磨削烧伤的分级、磨削烧伤的避免措施、磨削烧伤的影响因素、磨削烧伤解决方法。
让我们从基础对磨削烧伤形成认识、到对磨削烧伤的解决方法形成一整套的方案,其中:砂轮的选择在磨削烧伤过程中非常重要。
以避免我们生产中避免烧伤、遇到烧伤而找到合理的解决方法。
适用于外圆磨烧伤、内圆磨烧伤、平面磨烧伤、端面磨烧伤、无心磨烧伤等磨削方式。
关键词:磨削烧伤烧伤砂轮的选择烧伤解决方法烧伤原理烧伤级别一、定义:磨削时,由于磨削区域的瞬时高温(一般为900-1500℃)到相变温度以上时,形成零件表层金相组织发生变化(大多表面的某些部分出现氧化变色),使表层金属强度和硬度降低,并伴有残余应力产生,甚至出现微观裂纹,这种现象称为磨削烧伤。
二、磨削烧伤机理:当磨削表面产生高温时,如果散热措施不好,很容易在工件表面(从几十um 到几百 um)发生二次淬火及高温回火。
如果磨削工件表面层的瞬间温度超过钢种的AC1 点,在冷却液的作用下二次淬火马氏体,而在表层下由于温度梯度大,时间短,只能形成高温回火组织,这就使在表层和次表层之间产生拉应力,而表层为一层薄而脆的二次淬火马氏体,当承受不了时,将产生裂纹。
三、损伤的原因:(1)热处理的影响a)残余奥氏体磨削时残余奥氏体由于砂轮磨削时产生的热和压力而转变,同时可能伴随出现表面回火和磨削裂纹。
残余奥氏体量应控制在30%以内。
b)渗层碳浓度渗层碳浓度过高,在渗层组织中容易形成网状碳化物或过多的游离碳化物。
由于这种物质极硬,在磨削过程中可能出现局部过热倾向和发生表面回火。
渗层碳浓度过高,会使工件表面产生过多的残余奥氏体.从而导致烧伤和裂纹。
因此,表面碳浓度增加,则降低了磨削性能,一般表面碳浓度应控制在0.75% -0.95%范围以内。
磁粉探伤方法和工艺简介精选文档

磁粉探伤方法和工艺简介精选文档TTMS system office room 【TTMS16H-TTMS2A-TTMS8Q8-磁粉探伤方法和工艺简介射阳县德阳电子有限公司一.剩磁法和连续法1.剩磁法指先将工件磁化,再将磁粉或磁悬液施加到工件表面以检查工件缺陷的方法。
适用于经淬火,调质处理等增强强度或硬度的热处理后的高碳钢和合金钢,不适用于低碳钢和经退火处理或热变形钢材,马氏体不锈钢用剩磁法效果不如连续法。
剩磁法特别适用于批量小件的探伤,此时生产效率高。
2.连续法又称外加法,系指在外加磁场的作用下,将磁粉或磁悬液施加到工件上去进行探伤的方法。
目前该法比较流行的工艺是,先喷洒磁悬液,接着磁化(通电1-3秒),此时仍继续浇注磁悬液,停止浇注后再通电数次,每次秒,中断磁化后观察缺陷,最后退磁。
连续法适用于所有铁磁性材料。
教科书中推荐优先使用剩磁法,实际中多采用连续法。
二.直流磁化和交流磁化1.直流磁化目前已很少采用纯直流电,而采用单相半波或全波,三相半波或全波整流电。
2.交流磁化一般采用工频交流电。
交流磁化时,起作用的是电流的峰值,但一般标示的电流值是有效值。
交流磁化和直流磁化都能检测表面和近表面缺陷,交流磁化对表面缺陷的检测灵敏度高,直流磁化检测表面下的缺陷的能力强一些。
一般说来,电流中包含的脉动成份越大,探测内部缺陷的能力越弱。
直流磁化用于剩磁法时剩磁稳定,交流磁化则剩磁不够稳定,加断电相位控制器可解决此问题(采用过零点断电的方法叫断电相位控制,以防止对工件形成退磁作用)。
直流磁化退磁困难,交流磁化退磁容易。
目前一般推荐使用交流磁化,且多采用连续法,此时一般也加断电相位控制。
使用交流连续磁化,设备结构简单,成本低,磁化效果一般都能满足要求。
也有使用交直流混合磁化的,此时,交流磁化在前,直流磁化在后,以利于退磁。
三.磁化方法1.周向磁化。
指给工件直接通电,或者使电流流过贯穿工件中心孔的导体,旨在工件中建立一个环绕工件的并与工件轴垂直的闭合磁场。
磨削烧伤的检测方法

磨削烧伤的检测方法可能形成网状裂纹,它会导致齿面剥落.这当然是绝对不允许的。
用硬度测试法鉴别磨削烧伤的方法,并用超声波硬度计进行了实验,证明该方法简单易行,可以广泛应用于磨削加工中。
磨削烧伤及其常用检查方法在机械类产品中,很多重要零部件如轴承、齿轮、曲轴、凸轮轴、活塞销和万向节等,在热处理之后均需经过磨削加工。
相比之下,磨削时单位切削面积上的功率消耗远远超过其它加工方法,所转化热量的大部分会进入工件表面,因此容易引起加工面金相组织的变化。
在工艺参数、冷却方法和磨料状态选择不当的情况下,工件在磨削过程中极易出现相当深的金相组织变化层(即回火层),并伴随出现很大的表面残余应力,甚至导致出现裂纹,这就是所谓的磨削烧伤问题。
零部件的表面层烧伤将使产品性能和寿命大幅度地下降,甚至根本不能使用,造成严重的质量问题。
为此,生产企业一方面通过执行正确、科学的工艺规范,减轻和避免出现磨削烧伤现象;另一方面,加强对零部件的检验,及时发现不合格工件,并判断正在进行的磨削工艺状况。
但长期以来,对工件表面磨削烧伤的检验,除了最简单的目测法外,就是采用已延续多年的传统方法——酸洗法,即在被检零部件表面涂上酸液或将其浸入盛有按规定配制的酸液槽中。
之后(或在把工件取出后)根据表面呈现的不同颜色,对磨削烧伤的程度作出相应的判断。
一般地说,若色泽没有变化,就表明情况正常;而当颜色变成灰色,则说明已有烧伤情况存在,随着色泽变得越来越深,表示工件表面因温度更高,引起的磨削烧伤更为严重。
酸洗法具体如下:This is only a suggestion from my collegue ( Dino Calvanelli ) to find theburns on the gears此为有关过烧检测的建议:Clean each sample (part) to be inspected (free ofdirt,oil,grease,fingermarks,protective coatings,etc.).清洗产品,确保无灰尘、油污、手印、表面覆盖物等。
磁流变抛光消除磨削亚表面损伤层新工艺
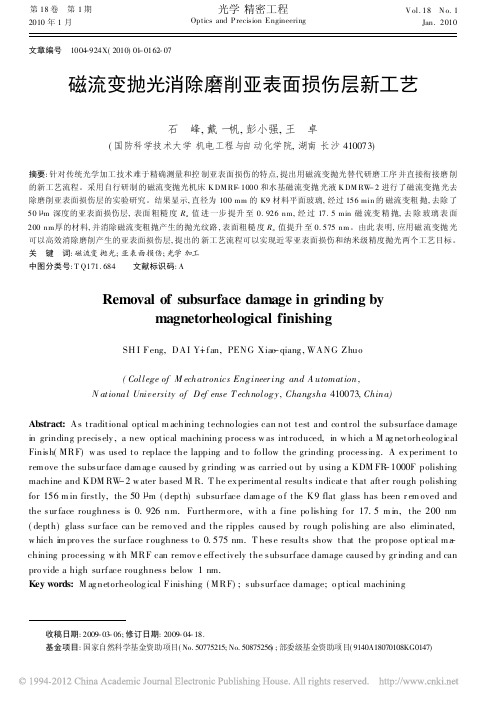
第18卷 第1期2010年1月光学精密工程Optics and P recision EngineeringV ol.18 N o.1 Jan.2010收稿日期:2009-03-06;修订日期:2009-04-18.基金项目:国家自然科学基金资助项目(No.50775215;No.50875256);部委级基金资助项目(9140A18070108KG0147)文章编号 1004-924X(2010)01-0162-07磁流变抛光消除磨削亚表面损伤层新工艺石 峰,戴一帆,彭小强,王 卓(国防科学技术大学机电工程与自动化学院,湖南长沙410073)摘要:针对传统光学加工技术难于精确测量和控制亚表面损伤的特点,提出用磁流变抛光替代研磨工序并直接衔接磨削的新工艺流程。
采用自行研制的磁流变抛光机床K DM RF -1000和水基磁流变抛光液K DM RW -2进行了磁流变抛光去除磨削亚表面损伤层的实验研究。
结果显示,直径为100mm 的K9材料平面玻璃,经过156min 的磁流变粗抛,去除了50L m 深度的亚表面损伤层,表面粗糙度R a 值进一步提升至0.926nm,经过17.5min 磁流变精抛,去除玻璃表面200nm 厚的材料,并消除磁流变粗抛产生的抛光纹路,表面粗糙度R a 值提升至0.575nm 。
由此表明,应用磁流变抛光可以高效消除磨削产生的亚表面损伤层,提出的新工艺流程可以实现近零亚表面损伤和纳米级精度抛光两个工艺目标。
关 键 词:磁流变抛光;亚表面损伤;光学加工中图分类号:T Q171.684 文献标识码:ARemoval of subsurface damage in grinding bymagnetorheological finishingSH I Feng,DAI Y-i fan,PENG Xiao -qiang ,WANG Zhuo (College of M echatronics Engineer ing and A utomation ,N ational University of Def ense T echnology ,Changsha 410073,China)Abstract:As traditional optical m achining techno logies can not test and co ntrol the subsurface damagein grinding precisely ,a new optical machining process w as introduced,in w hich a M ag netorheolog ical Finish(MRF)w as used to replace the lapping and to fo llow the grinding processing.A ex periment to rem ove the subsur face dam ag e caused by g rinding w as carried o ut by using a KDM FR -1000F polishing machine and KDM RW -2w ater based M R.T he ex perimental results indicate that after rough polishing for 156m in firstly,the 50L m (depth)subsurface dam age o f the K9flat glass has been r em oved and the sur face roughness is 0.926nm.Furtherm ore,w ith a fine po lishing for 17.5m in,the 200nm (depth)glass sur face can be remo ved and the ripples caused by ro ug h polishing are also eliminated,w hich im pro ves the sur face r oughness to 0.575nm.T hese results show that the pro pose optical m a -chining processing w ith MRF can remov e effectively the subsurface damage caused by gr inding and can pro vide a high surface roughness below 1nm.Key words:M ag netorheolog ical Finishing (MRF);subsurface damage;o ptical machining1引言光学玻璃是无机高分子凝聚态物质,内部呈现短程有序长程无序的非晶态结构。
磨削烧伤的检测方法(5篇)

磨削烧伤的检测方法(5篇)第一篇:磨削烧伤的检测方法磨削烧伤的检测方法可能形成网状裂纹,它会导致齿面剥落.这当然是绝对不允许的。
用硬度测试法鉴别磨削烧伤的方法,并用超声波硬度计进行了实验,证明该方法简单易行,可以广泛应用于磨削加工中。
磨削烧伤及其常用检查方法在机械类产品中,很多重要零部件如轴承、齿轮、曲轴、凸轮轴、活塞销和万向节等,在热处理之后均需经过磨削加工。
相比之下,磨削时单位切削面积上的功率消耗远远超过其它加工方法,所转化热量的大部分会进入工件表面,因此容易引起加工面金相组织的变化。
在工艺参数、冷却方法和磨料状态选择不当的情况下,工件在磨削过程中极易出现相当深的金相组织变化层(即回火层),并伴随出现很大的表面残余应力,甚至导致出现裂纹,这就是所谓的磨削烧伤问题。
零部件的表面层烧伤将使产品性能和寿命大幅度地下降,甚至根本不能使用,造成严重的质量问题。
为此,生产企业一方面通过执行正确、科学的工艺规范,减轻和避免出现磨削烧伤现象;另一方面,加强对零部件的检验,及时发现不合格工件,并判断正在进行的磨削工艺状况。
但长期以来,对工件表面磨削烧伤的检验,除了最简单的目测法外,就是采用已延续多年的传统方法——酸洗法,即在被检零部件表面涂上酸液或将其浸入盛有按规定配制的酸液槽中。
之后(或在把工件取出后)根据表面呈现的不同颜色,对磨削烧伤的程度作出相应的判断。
一般地说,若色泽没有变化,就表明情况正常;而当颜色变成灰色,则说明已有烧伤情况存在,随着色泽变得越来越深,表示工件表面因温度更高,引起的磨削烧伤更为严重。
酸洗法具体如下:This is only a suggestion from my collegue(Dino Calvanelli)to find theburns on the gears此为有关过烧检测的建议:Clean each sample(part)to be inspected(free ofdirt,oil,grease,fingermarks,protective coatings,etc.).清洗产品,确保无灰尘、油污、手印、表面覆盖物等。
一种用于凸轮轴磨削烧伤检测的新方法

一种用于凸轮轴磨削烧伤检测的新方法
朱正德
【期刊名称】《精密制造与自动化》
【年(卷),期】2009(000)003
【摘要】在汽车发动机制造业,凸轮轴、曲轴、气门和活塞销等重要零件的表面磨削烧伤是影响产品质量的一个重要因素.传统的测试方法却难以满足准确、快速检测的要求.对惯用的检测手段进行了简单描述,着重提出了一种新颖、高效的磨削烧伤检测方法--磁弹法.详细介绍了该种方法的工作原理、专用检测仪器的基本结构和组成(以凸轮轴为例),叙述了应用磁弹法时的评定特征值和仪器的定标.
【总页数】3页(P58-60)
【作者】朱正德
【作者单位】大众动力总成(上海)有限公司,201805
【正文语种】中文
【中图分类】TG8
【相关文献】
1.一种可用于糖厂硫熏强度快速在线检测新方法 [J], 周洋;张立军;黄扬明
2.用于汽车零部件磨削烧伤检测的一种新方法 [J], 朱正德
3.一种用于检测电压暂降的新方法 [J], 蒋素琼
4.一种用于异常用电检测的负荷模式分析新方法 [J], 杨玉锐;程杰;周刚;徐诒玥;吴伟健;吴佳
5.一种应用于运动车辆检测的背景更新方法 [J], 甘玲;潘小雷
因版权原因,仅展示原文概要,查看原文内容请购买。
工件磨削烧伤及其检测、评定方法简析

( V o l k s w a g a n P o w e r t r a i n( S h a n g h a i ) C o . , L t d . , S h a n g h a i 2 0 1 8 0 7 , C h i n a )
Ab s t r a c t : De s c r i p t i o n o f t h e c a u s e a n d h a r mf u l n e s s o f b u r n t p a r t d u e t o g r i n d i n g a s we l l a s
2 0 1 3年 第 2期 第 1 9卷 ( 总第 1 4 3期 )
工件磨 削烧伤及其检测 、 评定 方法简析
朱 正德
( 大众动力总成( 上海) 有限公 司, 上海 2 0 1 8 0 7 )
摘要 阐述 了磨 削烧伤 的成 因与危 害 ,并在对 相应检 测 手段 进 行描 述后 指 出,作为影 响 产 品
Ke y wo r d s : g r i n d i n g b u r n , i n s p e c t i o n me t h o d , ma g n e t o - e l a s t i c i t y , c h a r a c t e r i s t i c v a l u e,
企业虽然对磨削烧伤这一工艺现象的成因及其可能 引起产品质量的影响有所了解 ,但总体来讲 ,无论 在认识上还是在检测 、 评定等具体事宜的处理上都
大有需 要改进 、完 善 、提 升 的必 要 。
c a l i b r a t i o n
1
前言
层 聚集 大量热 量 ,从 而形成 局部 高温 ,以致 磨削 区
磁力探伤和磁力清洗原理

磁力探伤磁力探伤是通过铁磁性材料进行磁化所产生的漏磁场,来发现其表面或近表面缺陷的无损检测方法。
磁力探伤包括磁粉法、磁敏探头法和录磁法。
其中磁粉法是一种相对比较成熟的磁力检验方法,至今已有50多年的发展历史。
并且由于其设备简单,操作方便,检验灵敏度较高,故得到广泛应用。
第一节磁力探伤原理磁力探伤是根据铁磁材料的性质发明的一种无损检测方法,金属材料的焊缝缺陷探伤完全符合磁力探伤条件,所以,焊接生产中的无损检测,磁力探伤是一种重要的方法。
一、磁力探伤的基本原理铁磁性材料制成的工件被磁化后,工件就有磁力线通过。
如果工件本身没有缺陷,磁力线在其内部是均匀连续分布的。
但是,当工件内部存在缺陷时,如裂纹、夹杂、气孔等非铁磁性物质,其磁阻非常大,磁导率低,必将引起磁力线的分布发生变化。
缺陷处的磁力线不能通过,将产生一定程度的弯曲。
当缺陷位于或接近工件表面时,则磁力线不但在工件内部产生弯曲,而且还会穿过工件表面漏到空气中形成一个微小的局部磁场,如图9-1所示。
这种由于介质磁导率的变化而使磁通泄漏到缺陷附近空气中所形成的磁场,称作漏磁场。
通过一定的方法将漏磁场检测出来,进而确定缺陷的位置,包括缺陷的大小、形状和深度等,这就是磁力探伤的原理。
二、影响漏磁场强度的因素1.外加磁场强度对铁磁材料磁化时所施加的外加磁场强度高时,在材料中所产生在磁感应强度也高,这样,表面缺陷阻挡的磁力线也较多,形成的漏磁场强度也随之增加。
2.材料的磁导率材料磁导率高的工件易被磁化,在一定的外加磁场强度下,在材料中产生的磁感应强度正比于材料的磁导率。
在缺陷处形成的漏磁场强度随着磁导率的增加而增加。
3.缺陷的埋藏深度当材料中的缺陷越接近表面,被弯曲逸出材料表面的磁力线越多。
随着缺陷埋藏深度的增加,被逸出表面的磁力线减少,到一定深度,在材料表面没有磁力线逸出而仅仅改变了磁力线方向,所以缺陷的埋藏深度愈小,漏磁场强度也愈大。
4.缺陷方向当缺陷长度方向和磁力线方向垂直时,磁力线弯曲严重,形成的漏磁场强度最大。
工件磨削烧伤及其检测、评定方法简析

工件磨削烧伤及其检测、评定方法简析朱正德【摘要】阐述了磨削烧伤的成因与危害,并在对相应检测手段进行描述后指出,作为影响产品质量的一项重要因素,现有测试方法已难以满足准确、快速检测的要求.介绍了一种新颖、高效、实用的“磁弹法”的工作原理,以及在此基础上研制的专用仪器,尤其叙述了借助磁弹法检测工件磨削烧伤时的评定指标和仪器的特征值定标.最后还就诸多工艺因素对磨削烧伤的影响做了相关分析.【期刊名称】《柴油机设计与制造》【年(卷),期】2013(019)002【总页数】4页(P36-39)【关键词】磨削烧伤;检测手段;磁弹法;特征值mp和定标【作者】朱正德【作者单位】大众动力总成(上海)有限公司,上海201807【正文语种】中文近期在汽车行业内进行的一次调研表明,多数企业虽然对磨削烧伤这一工艺现象的成因及其可能引起产品质量的影响有所了解,但总体来讲,无论在认识上还是在检测、评定等具体事宜的处理上都大有需要改进、完善、提升的必要。
不同于其他方式的切削加工,磨削广泛应用于零件的精密加工。
由于被磨削金属层较薄,产生的切屑也少,加之砂轮的导热性差,因此仅有不到10%的热量可以被切屑带走,而大约60%~90%的热量会传入工件。
这样就在很短的时间内在磨削表层聚集大量热量,从而形成局部高温,以致磨削区区域温度可达800~1 000℃甚至更高,从而在表面形成极大的温度梯度。
在磨削热量、磨削力二者的综合作用下,引起了零件表层的金相组织变化,并产生残余应力,而这就是所谓磨削烧伤的成因。
铁磁性材料的工件一般在磨削加工前都需经历热处理这道工序,借助在工件表面形成马氏体组织,将能够提供足够的硬度。
而磨削区的高温和很大的温度梯度会使金相组织发生变化,主要是因为只要当温度一旦超过马氏体转变的温度,就会产生回火或退火现象引起金相组织转变,而这会直接导致工件表面硬度不同程度的下降。
另一方面,磨削过程中工件表面温度的急剧上升,以及之后开始的冷却直至最后冷却,会引起零件表层的热胀冷缩,造成自工件表面至内部的各层产生各异的残余应力。
烧伤介绍及解决办法

产生的冷硬化的共同作用下发生分解,引起相变,形成较大的组织应力。
(3) 渗层碳浓度
渗层碳浓度过高,在渗层组织中容易形成网状碳化物或过多的游离碳化物。由于这种物质极硬,在磨削过程中可能出现局部过热倾向和发生表面回火。
其硬度比原来的回火马氏体的高,在它的下层,因冷却较慢,出现了硬度比原先的回火马氏体低的回火组织(索氏体或托氏体),
这种烧伤称为淬火烧伤。
3、退火烧伤
如果磨削区温度超过了相变温度,而磨削区域又无冷却液进入,表层金属将产生退火组织,表面硬度将急剧下降,
这种烧伤称为退火烧伤
(1) 碳化物的大小、数量、分布及形态。
如果渗碳层碳化物的颗粒大、数量多、分布不均匀,特别是形成网状或角状,将会导致材质的脆性增加。
(2) 残余奥氏体量过多。
若渗碳后淬火温度过高,就会使奥氏体晶粒粗大和奥氏体内含碳量过高,这样就会导致形成粗大的片状马氏体和过多的残余奥氏体。
磁弹法
(1)工作原理
磁弹法即BN法(Barkhansen Noise Method),是以1919年发现的物理学Barkhansen效应为基础开发的一种测试方法,它能有效地
对磨削烧伤进行测试。近年来,利用磁弹法研制的测试仪器已在零部件表面磨削烧伤检测中逐步得到应用,并充分显现出优越性。
②砂轮
⑴砂轮选择
在保证齿面粗糙度的前提下,磨料粒度应尽量选择大一些 ,以达到较高的去除量比率;渗碳钢硬度高,砂粒易磨钝,
为了避免砂粒磨钝而产生大量磨削热,砂轮硬度宜选软些,这样可以使磨钝了的磨粒及时脱落 ,保持砂轮经常有锐利的磨粒在工作 ,
磁弹性法检测技术的应用研究——特种钢制轴承套圈磨削烧伤检测技术
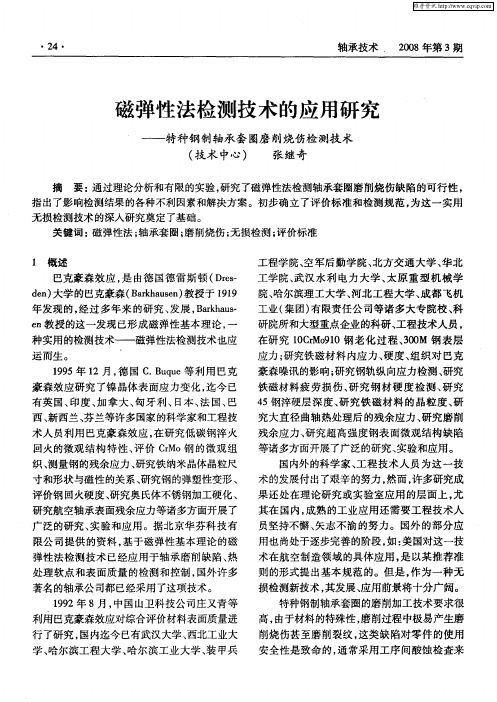
种实用的检测技术——磁弹性法检测技术也应
运而 生 。
19 9 5年 l 2月 , 国 C B qe等 利 用 巴克 德 .uu
豪森效应研究 了镍 晶体表面应力变化, 迄今 已 有英 国 、 度 、 拿 大 、 牙 利 、1本 、 国、 印 加 匈 3 法 巴
无 损 检测 技术 的深入 研究 奠定 了基础 。
关键 词 :磁弹性 法 ; 轴承套 圈 ; 削烧伤 ; 磨 无损 检测 ; 评价标 准
I 概 述
工程学 院 、 军 后 勤学 院、 方 交 通 大学 、 北 空 北 华 工学 院 、 武汉 水 利 电 力 大 学 、 原 重 型 机 械 学 太 院 、 尔滨理 工 大 学 、 哈 河北 工 程 大 学 、 都 飞 机 成
西、 新西 兰 、 兰 等许多 国家 的科学 家和工 程技 芬
究 大直 径 曲轴 热 处理 后 的残余 应 力 、 研究 磨 削
术人员利用 巴克豪森效应 , 在研究低碳钢淬火 回火 的微 观 结 构 特 性 、 价 CMo钢 的 微 观 组 评 r
织、 测量 钢 的残余应 力 、 研究铁 纳米 晶体 晶粒尺
评价钢 回火硬度、 研究奥 氏体不锈钢加工硬化、
研究 航 空轴 承表 面残余 应力 等诸 多方面开 展 了 广 泛 的研究 、 验 和 应 用 。据北 京华 芬 科 技 有 实
限公司提供 的资料 , 基于磁弹性基本理论的磁 弹性 法检 测 技 术 已经 应 用于 轴 承磨 削缺 陷、 热
行 了研 究 , 内迄 今 已有武汉 大学 、 国 西北工 业大 学、 哈尔 滨工 程 大 学 、 尔滨 工 业 大学 、 甲兵 哈 装
- 1、下载文档前请自行甄别文档内容的完整性,平台不提供额外的编辑、内容补充、找答案等附加服务。
- 2、"仅部分预览"的文档,不可在线预览部分如存在完整性等问题,可反馈申请退款(可完整预览的文档不适用该条件!)。
- 3、如文档侵犯您的权益,请联系客服反馈,我们会尽快为您处理(人工客服工作时间:9:00-18:30)。
磁弹法检查零部件表面磨削烧伤的新方法
作者:大众动力总成有限公司朱正德
磨削烧伤及其常用检查方法
在机械类产品中,很多重要零部件如轴承、齿轮、曲轴、凸轮轴、活塞销和万向节等,在热处理之后均需经过磨削加工。
相比之下,磨削时单位切削面积上的功率消耗远远超过其它加工方法,所转化热量的大部分会进入工件表面,因此容易引起加工面金相组织的变化。
在工艺参数、冷却方法和磨料状态选择不当的情况下,工件在磨削过程中极易出现相当深的金相组织变化层(即回火层),并伴随出现很大的表面残余应力,甚至导致出现裂纹,这就是所谓的磨削烧伤问题。
零部件的表面层烧伤将使产品性能和寿命大幅度地下降,甚至根本不能使用,造成严重的质量问题。
为此,生产企业一方面通过执行正确、科学的工艺规范,减轻和避免出现磨削烧伤现象;另一方面,加强对零部件的检验,及时发现不合格工件,并判断正在进行的磨削工艺状况。
但长期以来,对工件表面磨削烧伤的检验,除了最简单的目测法外,就是采用已延续多年的传统方法——酸洗法,即在被检零部件表面涂上酸液或将其浸入盛有按规定配制的酸液槽中。
之后(或在把工件取出后),根据表面呈现的不同颜色,对磨削烧伤的程度作出相应的判断。
一般地说,若色泽没有变化,就表明情况正常;而当颜色变成灰色,则说明已有烧伤情况存在,随着色泽变得越来越深,表示工件表面因温度更高,引起的磨削烧伤更为严重。
传统检查方法虽然简单易行,但有着很大的局限性,主要是工件表面经酸液浸蚀,即使为无问题的零部件,也不能再予以使用。
传统方法执行的实际上是一种破坏性检查。
从以上描述可知,酸洗法本质上属于定性检查,难以对磨损烧伤程度做出定量的说明。
鉴于上面两点,采取传统方法时,只能采用抽检的方式,且样本很小,欲对所执行的工艺过程作出较确切的评价并予以改进是很困难的。
理论表明,酸洗法检验只能反映因金相组织结构变化引起的硬度下降这种情况,对于工件表面存在的残余应力则无法反映,放在全面揭示磨削烧伤的程度上显得不足。
另一方面,由于使用了酸液,企业增加了消除环境污染的负担;传统检查方法的规范化可靠性水平较低,更难以制定可操作性强的评定标准。
一种新颖、高效的磨削烧伤检测方法——磁弹法
1. 工作原理
磁弹法即BN法(BarkhansenNoise Method),是以1919年发现的物理学Barkhansen效应为基础开发的一种测试方法,它能有效地对磨削烧伤进行测试。
近年来,利用磁弹法研制的测试仪器已在零部件表面磨削烧伤检测中逐步得到应用,并充分显现出优越性。
众所周知,出现磨削烧伤的那些零部件,主要由铁磁性材料制成。
在正常情况下,其磁序(体现在多晶体的磁畴结构里)呈有规则的排列。
但如前所述,磨削烧伤后产生的金相组织变化及可能出现的很大残余应力都将引起磁畴结构内的磁序变化。
Barkhansen效应指出,矫顽(磁)力,即改变被颠倒极性所需要的磁场强度是与铁磁性材料晶格结构错位和残余应力等的程度有关的。
利用BN法探测被检零部件表面磨削烧伤的机理就在于此。
图1是在BN法基础上开发的检测仪器的工作原理示意图。
图1 BN法检测仪器工作原理示意图
图1a中,“门”形电感线圈形成的磁场在被测钢件中所产生的效应取决于工件表面磨削烧伤的实际状况,而由此在工件周围所形成的磁场又会使测头在测试区域的感应线圈中产生相应的电信号,而这一信号直接与工件磨削烧伤的程度有关。
图1b是据此研制的测试仪器的组成框图,箭头反映了整个工作过程:由电感线圈引起相应的作用磁场,通过被检工件,进而在传感头中产生对应的检测信号(称为B 信号),该B信号经过放大和滤波等处理环节,最后被显示和输出。
磨削烧伤的物理表现主要是因表面金相组织结构变化产生回火层所引起的硬度下降,以及在表面出现的残余应力(拉应力)。
图1所示的检测仪器对它们都能作出敏感的反映(见图2)。
图2a中的横坐标表示硬度值Rc,而纵坐标表示输出的B 信号幅值。
随着被检工件表面硬度值Rc由高向低变化,检测仪器输出的相应B 信号幅值将由小到大,即硬度低对应的检测信号高,硬度高对应的检测信号低。
仪器对表面残余应力的反应见图2b,从中可见,当残余应力由小到大,即由负(压应力)向正(拉应力)变化时,检测仪器输出的相应B信号幅值将由低向高变化。
图2 BN法检测仪器能够敏感反映出磨削烧伤的硬度及残余应力变化
2. 评定特征值mp及其定标
上述由仪器特殊设计的激磁电路和传感装置产生的检测信号,乃是Barkhansen 磁弹法效应的一种量化表达,以特征值mn(magnetoelastic parameter)标志。
mp 与被检测工件表面的变异状态,如残余应力成比例,其数值能在仪器的屏幕上显示、输出。
但利用mp来反映工件磨削烧伤的程度从本质上来说是一种比较测量的方式,为了能够真正地对其做准确的定量描述,还必须解决“定标”的问题。
定标包括二项内容:①确定不合格品的界限。
有目的地制作一批样品,其中包括有一些磨削烧伤程度不同的工件,利用酸洗法按用户的评定标准对它们作出不同的判断后,将介于合格/不合格临界状态的若干工件通过仪器求得相应的mp值,然后取其平均值作为不合格的界限;②进行校准。
校准就是找出特征值mp与采用酸洗法确认的磨削烧伤程度之间的相关性。
具体来说,就是需确定一个相关系数MAGN,并利用仪器控制面板上的拨盘予以设置,MGAN值的范围从0到99,一般尾数取5或0。
为此,可在前面的样品中找二根表面状态差异较大的工件,选定工件上的某一位置,在检测仪器上的MGAN取值间隔为5或10时,以静态方法读出二组对应的mp值,如MGAN为30时,在二个工件上测出2个mp值,在MGAN为40时又得到2个,直到MGAN=90。
两两相减后必然能得到一个最大值,以这时的MGAN值作为相关系数,在面板上予以设置。
注意:在实际执行“定标”时,也可先利用第一项中的样件求得相关系数MGAN,然后再找出不合格品界限。
否则,在前一项操作中,会由于任意设置的MGAN(一般取50或60)给界限值带来一些偏差。
应用实例
尽管在汽车行业中,不少场合都可以采用这种以BN法为基础研制的磨削烧伤测试仪器,但相比之下,对发动机凸轮轴中各挡凸轮的检测是用的最多的。
这一方面是因凸轮乃承重件,工作条件差;另一方面是由于凸轮圆周方向不同曲率半径的特点可能会造成磨削过程中表面状态的差异,在这种情况下,出现磨削烧伤的机率会增大。
图3为该仪器示意图,它是一种高效率半自动检测设备,很适合于在批量生产条件下的汽车发动机厂、内燃机厂使用。
首先,针对不同的凸轮轴,需配备一根精确加工的轴向定位器,其纵向开有一排缺口,每个缺口对应一个被检凸轮。
在开始测量前,必须仔细调整其在机体上的位置,在确保传感器支臂嵌入任一缺口时,测头正好对准相应凸轮,此时就可以利用带捏手的螺钉,把轴向定位器固定在机体上。
操作者在启动设备后,被测工件即在驱动顶尖带动下开始旋转,此时,操作者只要简单地提起传感器支臂上的手柄,使传感器沿着机身上的一圆柱导轨移动,当到达第一个被检凸轮时,轻轻地放入手柄。
在手柄嵌入定位器缺口的同时,测头在测力弹簧作用下压在凸轮表面,随着工件的回转实施动态检测。
期间,连续输出的BN信号会在设备一侧的控制柜显示屏上以曲线形式呈现。
当完成一周的测试后,操作者再次提起传感器支臂上的手柄,使测头脱离第一个被检凸轮,移动至下一个进行测量,直到全部凸轮测毕,返回起点。
1.机体
2.传感器和交臂
3.驱动顶尖
4.死顶尖(尾架)
5.轴向定位器
6.尾架手柄
7.轴向定位器固定捏手8.导向销9.限位螺丝10.停止挡块
图3 BN法磨削烧伤测试仪器示意图
尽管只是一台半自动设备,但操作便捷,效率很高,检查一个工件,如一根四缸发动机的凸轮轴,包括装卸也不到2分钟。
目前,以磁弹法原理为基础研制的这类新型磨削烧伤检测仪器已经产品化,在很多行业得到了成功的应用。
针对不同被测工件的特征和各个用户的需要,这类新型检测仪器可设计、制造成不同的型式,有逐点测量的静态方式,也有上述那种连续动态测量方式。
至于仪器能探测的深度,取决于实际被检工件材料的导电率、导磁率以及所确定的激磁频率。
仪器都配两种激磁频率,3-15kHz和70~200kHz。
按磁弹法原理研制的这类新型仪器的检查深度一般范围为0.01~1.5mm,但通常工件表面磨削烧伤发生的深度是0.02~0.2mm。
国内在这方面虽刚刚起步,但已经采用的场合除了上述汽车发动机行业的凸轮轴外,还有轴承行业中的套圈,显示了相当广阔的前景。
(end)。