淬火钢磨削烧伤
齿轮零件磨削烧伤的危害、检测和预防

齿轮零件磨削烧伤的危害、检测和预防作者:许红平鲁建锋吴伟明徐嘉军来源:《专用汽车》2019年第01期通过淬火类齿轮磨削烧伤的深层次研究,总结出磨削烧伤产生的原因和可能引起的危害,并提出磨削烧伤的各种检测方法:同时对磨削烧伤的防止措施做出了较为全面的分析,对减少齿轮类零件磨削烧伤的问题有着重要的实践意义。
齿轮类零件作为机构中的重要零部件,在渗碳淬火后往往要进行磨削加工。
在磨削加工工艺中,砂轮与零件的接触区会因摩擦产生大量热量,而大部分热量会通过传导进入零件浅表层,容易导致表层金相组织的变化。
若磨削参数设置和砂轮选择不当,在加工的过程中,会引起表层金相组织改变,并出现较大的残余应力,形成“磨削烧伤”[1]。
零件磨削烧伤会使零件表层的耐磨性、耐腐蚀性和接触疲劳强度降低,使用寿命大大降低,严重的情况下会出现裂纹,从而引发质量问题。
本文通过研究淬火类齿轮的磨削烧伤现象,总结和分析了磨削烧伤的种类和危害,提出了针对不同种类烧伤的不同检测方法,并在此基础上探讨了磨削烧伤的预防措施。
磨削烧伤的种类及危害1.磨削烧伤的种类齿轮零件磨削加工的过程中,接触区域的瞬时高温(可达1000℃)使得零件表面的金相组织产生局部变化。
根据磨削烧伤表面组织结构的不同,可以将磨削烧伤分成两类。
1.1回火烧伤当磨削接触区表面层温度显著超过马氏体转变温度,而低于相变临界温度Acl的时候,零件表面马氏体产生回火,转变成硬度较低的索氏体和屈氏体,这种烧伤称为“回火烧伤”,如图1(a)所示。
此时该表面的硬度一般为HRC51-57。
1.2二次淬火烧伤淬火钢的马氏体组织在750℃-800℃以上的磨削高温下转变成奥氏体。
如果冷却速度较低,则会重新变为马氏体,零件表层比原淬火硬度稍有提高,一般在HRC63左右。
但此变质层性能稳定性较差,脆性较高,二次淬火烧伤区域周围通常伴有一圈严重的回火层,如图1(b)所示。
2.磨削烧伤和磨削裂纹磨削烧伤的变质层内存在较大的残余应力,当残余应力超过材料的极限强度时,容易导致裂纹的出现。
磨削烧伤的检测方法

磨削烧伤的检测方法可能形成网状裂纹,它会导致齿面剥落.这当然是绝对不允许的。
用硬度测试法鉴别磨削烧伤的方法,并用超声波硬度计进行了实验,证明该方法简单易行,可以广泛应用于磨削加工中。
磨削烧伤及其常用检查方法在机械类产品中,很多重要零部件如轴承、齿轮、曲轴、凸轮轴、活塞销和万向节等,在热处理之后均需经过磨削加工。
相比之下,磨削时单位切削面积上的功率消耗远远超过其它加工方法,所转化热量的大部分会进入工件表面,因此容易引起加工面金相组织的变化。
在工艺参数、冷却方法和磨料状态选择不当的情况下,工件在磨削过程中极易出现相当深的金相组织变化层(即回火层),并伴随出现很大的表面残余应力,甚至导致出现裂纹,这就是所谓的磨削烧伤问题。
零部件的表面层烧伤将使产品性能和寿命大幅度地下降,甚至根本不能使用,造成严重的质量问题。
为此,生产企业一方面通过执行正确、科学的工艺规范,减轻和避免出现磨削烧伤现象;另一方面,加强对零部件的检验,及时发现不合格工件,并判断正在进行的磨削工艺状况。
但长期以来,对工件表面磨削烧伤的检验,除了最简单的目测法外,就是采用已延续多年的传统方法——酸洗法,即在被检零部件表面涂上酸液或将其浸入盛有按规定配制的酸液槽中。
之后(或在把工件取出后)根据表面呈现的不同颜色,对磨削烧伤的程度作出相应的判断。
一般地说,若色泽没有变化,就表明情况正常;而当颜色变成灰色,则说明已有烧伤情况存在,随着色泽变得越来越深,表示工件表面因温度更高,引起的磨削烧伤更为严重。
酸洗法具体如下:This is only a suggestion from my collegue ( Dino Calvanelli ) to find theburns on the gears此为有关过烧检测的建议:Clean each sample (part) to be inspected (free ofdirt,oil,grease,fingermarks,protective coatings,etc.).清洗产品,确保无灰尘、油污、手印、表面覆盖物等。
磨削烧伤质量分析报告
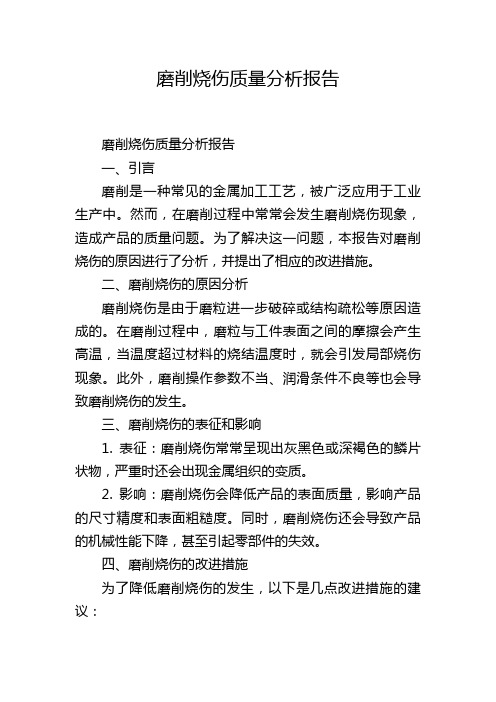
磨削烧伤质量分析报告磨削烧伤质量分析报告一、引言磨削是一种常见的金属加工工艺,被广泛应用于工业生产中。
然而,在磨削过程中常常会发生磨削烧伤现象,造成产品的质量问题。
为了解决这一问题,本报告对磨削烧伤的原因进行了分析,并提出了相应的改进措施。
二、磨削烧伤的原因分析磨削烧伤是由于磨粒进一步破碎或结构疏松等原因造成的。
在磨削过程中,磨粒与工件表面之间的摩擦会产生高温,当温度超过材料的烧结温度时,就会引发局部烧伤现象。
此外,磨削操作参数不当、润滑条件不良等也会导致磨削烧伤的发生。
三、磨削烧伤的表征和影响1. 表征:磨削烧伤常常呈现出灰黑色或深褐色的鳞片状物,严重时还会出现金属组织的变质。
2. 影响:磨削烧伤会降低产品的表面质量,影响产品的尺寸精度和表面粗糙度。
同时,磨削烧伤还会导致产品的机械性能下降,甚至引起零部件的失效。
四、磨削烧伤的改进措施为了降低磨削烧伤的发生,以下是几点改进措施的建议:1. 选择适当的磨削液。
磨削液能够起到降低摩擦系数和冷却作用,有助于降低磨削烧伤的风险。
同时,应注意磨削液的挥发性和含油量,避免产生刺激性气体和过度润滑。
2. 控制磨削操作参数。
合理选择磨削深度、磨削速度和进给速度等参数,以避免过大的热量积累和高速磨削带来的烧伤风险。
3. 使用适当的磨具。
选择高质量的磨具,减少磨具与工件之间的摩擦,降低磨削烧伤的发生。
4. 加强磨削工艺控制。
对磨削过程进行严格的监控,及时发现磨削烧伤的异常情况,并采取相应的措施进行调整和处理。
五、结论磨削烧伤是磨削过程中常见的质量问题,对产品表面质量和机械性能造成一定的影响。
为了降低磨削烧伤的发生,应选择适当的磨削液,控制磨削操作参数,使用高质量的磨具,并加强磨削工艺的控制。
通过采取上述改进措施,可以有效降低磨削烧伤的发生率,提高产品的质量稳定性和可靠性,进一步提高企业的竞争力和市场占有率。
参考文献:[1] 沈波. 磨削烧伤的预测与控制[D]. 天津: 天津大学, 2007.[2] 苏传远. 磨削烧伤高临界温度及烧伤机理的研究[J]. 石油钻采工艺, 2009, 31(5): 52-53.。
磨削烧伤的小常识
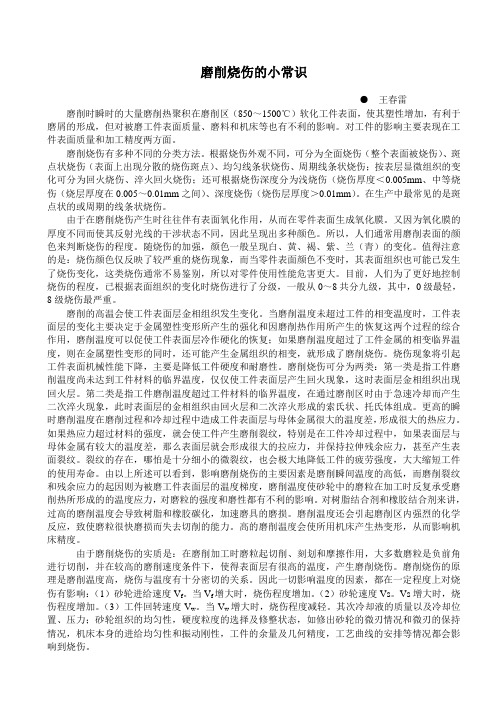
磨削烧伤的小常识●王春雷磨削时瞬时的大量磨削热聚积在磨削区(850~1500℃)软化工件表面,使其塑性增加,有利于磨屑的形成,但对被磨工件表面质量、磨料和机床等也有不利的影响。
对工件的影响主要表现在工件表面质量和加工精度两方面。
磨削烧伤有多种不同的分类方法。
根据烧伤外观不同,可分为全面烧伤(整个表面被烧伤)、斑点状烧伤(表面上出现分散的烧伤斑点)、均匀线条状烧伤、周期线条状烧伤;按表层显微组织的变化可分为回火烧伤、淬火回火烧伤;还可根据烧伤深度分为浅烧伤(烧伤厚度<0.005mm、中等烧伤(烧层厚度在0.005~0.01mm之间)、深度烧伤(烧伤层厚度>0.01mm)。
在生产中最常见的是斑点状的或周期的线条状烧伤。
由于在磨削烧伤产生时往往伴有表面氧化作用,从而在零件表面生成氧化膜。
又因为氧化膜的厚度不同而使其反射光线的干涉状态不同,因此呈现出多种颜色。
所以,人们通常用磨削表面的颜色来判断烧伤的程度。
随烧伤的加强,颜色一般呈现白、黄、褐、紫、兰(青)的变化。
值得注意的是:烧伤颜色仅反映了较严重的烧伤现象,而当零件表面颜色不变时,其表面组织也可能已发生了烧伤变化,这类烧伤通常不易鉴别,所以对零件使用性能危害更大。
目前,人们为了更好地控制烧伤的程度,已根据表面组织的变化时烧伤进行了分级,一般从0~8共分九级,其中,0级最轻,8级烧伤最严重。
磨削的高温会使工件表面层金相组织发生变化。
当磨削温度未超过工件的相变温度时,工件表面层的变化主要决定于金属塑性变形所产生的强化和因磨削热作用所产生的恢复这两个过程的综合作用,磨削温度可以促使工件表面层冷作硬化的恢复;如果磨削温度超过了工件金属的相变临界温度,则在金属塑性变形的同时,还可能产生金属组织的相变,就形成了磨削烧伤。
烧伤现象将引起工件表面机械性能下降,主要是降低工件硬度和耐磨性。
磨削烧伤可分为两类:第一类是指工件磨削温度尚未达到工件材料的临界温度,仅仅使工件表面层产生回火现象,这时表面层金相组织出现回火层。
齿轮零件磨削烧伤的危害、检测和预防

⾼温下转变成奥⽒体。
如果冷却速度较低,则会重新变为⻢⽒体,零件表层⽐原淬⽕硬度稍有提⾼,⼀般在HRC 左右。
但此变质层性能稳定性较差,脆性较⾼,⼆次淬⽕烧伤区域周围通常伴有⼀圈严重的回⽕层,如图 (b)所⽰。
磨削烧伤的检测⽅法
⻮轮零件表⾯磨削烧伤后,
降低,甚⾄完全失去⼯作能⼒。
不合格的零件,需要对零件表⾯的磨削烧伤进⾏检测。
(a)回⽕烧伤 ( b)⼆次淬⽕烧伤
图1 磨削烧伤
(a) 磨削裂纹 (b) 磨削裂纹引起的⻮⾯剥落图2 磨削烧伤和磨削裂纹
利⽤钢材不同的⾦相组织对酸蚀有不同的敏感性。
回⽕⻢⽒体酸蚀后呈现灰⾊,如发⽣严重的回⽕烧伤,回⽕⻢⽒体转变为回⽕索⽒体,酸蚀后呈现⿊⾊;如发⽣⼆次淬⽕烧伤,⾦相组织为淬⽕⻢⽒体,酸蚀后呈现⽩⾊。
2.2 酸洗检查的步骤法反应⽐较灵敏,而且数值可靠,应⽤较为⼴泛。
磨削烧伤的预防
磨削烧伤和磨削裂纹均因磨削热过⾼引起,所以预防⽌烧伤和裂纹应该从降低磨削热的⻆度着⼿。
影响磨
(a) 磨削烧伤引起的⻮⾯剥落 (b) 中速轴⻮⾯磨削烧伤并产⽣剥落
图3 ⻮⾯剥落情况图4 ⾏星轮磨削烧伤⻮⾯剥落后造成⻮圈⻮⾯凹坑。
磨削烧伤的因素有哪些?重点考虑这四个方面

磨削烧伤的因素有哪些?重点考虑这四个方面机械加工过程中,在工件的加工区由于切削热会使加工表面温度升高。
当温度超过金相组织变化的临界点时,就会产生金相组织变化。
对于一般的切削加工,切削热大部份被切屑带走,影响不严重。
但对磨削加工而盲,由于其产生的单位面积上的切削热要比一般切削加工大数十倍,故工件表面温度可高达1000℃左右,必然会引起表面层金相组织的变化,使表面硬度下降,伴随产生残余拉应力及裂纹,从而使工件的使用寿命大幅降低,这种现象称为磨削烧伤。
磨削烧伤产生时,工件表面层常会出现黄、褐、紫、青等烧伤色,它们是工件表面由于瞬时高温引起的氧化膜颜色。
影响磨削烧伤的因素有:1. 磨削用量主要包括磨削深度、工件纵向进给量及工件速度。
当磨削深度增大时,工件的表明温度及表层下不同深度的温度都会随之升高,磨削烧伤增加,故磨削深度不可过大;工件纵向进给量的增加使得砂轮与工件的表面接触时间相对减少,散热条件得到改善,磨削烧伤减轻;增大工件速度虽然使磨削区温度上升,但由于热源作用时间减少,金相组织来不及变化,总的来说可以减轻磨削烧伤。
对于增加进给量、工件速度而导致的表明粗糙度增大,一般采用提高砂轮转速及较宽砂轮来补偿。
2. 冷却方法采用切削液带走磨削时的热量可以避免烧伤,但目前适用的冷却方法效果较差,原因是切削液未能进入磨削区。
为了使切削液能较好的进入磨削区起到冷却作用,目前采用的主要方法有内冷却法、喷射法、间断磨削法与古油砂轮等。
内冷却法是将切削液通过砂轮空心主轴引入砂轮的中心腔内,由于砂轮具有多孔性,当砂轮高速旋转时,强大的离心力将切削液沿砂轮空隙向四周甩出,使磨削区直接得到冷却。
3. 工件材料工件材料硬度越高,磨削发热量越多;但材料过软,则易于堵塞砂轮,反而使加工表面温度急剧上升。
工件材料的强度可分为高温强度与常温强度。
高温强度越高,磨削时所消耗的功率越多。
例如在室温时,45钢的强度比20crmo合金钢的强度高65n/mm2,但在600℃时,后者的强度却比前者高180n/mm2,因此20crmo钢的磨削加工发热量比45钢大。
磨削烧伤与其解决方案

磨削烧伤及其解决方案张国耀(郑州超微磨料具有限公司河南郑州450001)摘要:鉴于磨削过程中工件烧伤的问题一直困扰着产品的质量问题,从磨削烧伤的形成的机理、磨削烧伤的检查方法、磨削烧伤的分级、磨削烧伤的避免措施、磨削烧伤的影响因素、磨削烧伤解决方法。
让我们从基础对磨削烧伤形成认识、到对磨削烧伤的解决方法形成一整套的方案,其中:砂轮的选择在磨削烧伤过程中非常重要。
以避免我们生产中避免烧伤、遇到烧伤而找到合理的解决方法。
适用于外圆磨烧伤、内圆磨烧伤、平面磨烧伤、端面磨烧伤、无心磨烧伤等磨削方式。
关键词:磨削烧伤烧伤砂轮的选择烧伤解决方法烧伤原理烧伤级别一、定义:磨削时,由于磨削区域的瞬时高温(一般为900-1500℃)到相变温度以上时,形成零件表层金相组织发生变化(大多表面的某些部分出现氧化变色),使表层金属强度和硬度降低,并伴有残余应力产生,甚至出现微观裂纹,这种现象称为磨削烧伤。
二、磨削烧伤机理:当磨削表面产生高温时,如果散热措施不好,很容易在工件表面(从几十um 到几百 um)发生二次淬火及高温回火。
如果磨削工件表面层的瞬间温度超过钢种的AC1 点,在冷却液的作用下二次淬火马氏体,而在表层下由于温度梯度大,时间短,只能形成高温回火组织,这就使在表层和次表层之间产生拉应力,而表层为一层薄而脆的二次淬火马氏体,当承受不了时,将产生裂纹。
三、损伤的原因:(1)热处理的影响a)残余奥氏体磨削时残余奥氏体由于砂轮磨削时产生的热和压力而转变,同时可能伴随出现表面回火和磨削裂纹。
残余奥氏体量应控制在30%以内。
b)渗层碳浓度渗层碳浓度过高,在渗层组织中容易形成网状碳化物或过多的游离碳化物。
由于这种物质极硬,在磨削过程中可能出现局部过热倾向和发生表面回火。
渗层碳浓度过高,会使工件表面产生过多的残余奥氏体.从而导致烧伤和裂纹。
因此,表面碳浓度增加,则降低了磨削性能,一般表面碳浓度应控制在0.75% -0.95%范围以内。
磨削烧伤检查规定

通常应对有回火显示的零件进行磁粉探伤检验,尤其是渗碳淬火硬化的零件。
7.2. 显微硬度计检查
7.2.1. 7.2.2. 7.2.3.
把要检查的部位用 800-1000 号的砂纸磨削 ,尽量少磨,能检查显微硬度即可。 工件要检查的部位不便于进行显微硬度检测,用线切割切下,并镶样。 用显微硬度计检测时,载荷 0.3Kg。对于用线切割切下零件的检验工件 0.05mm 处硬度≥695HV0.3,不允
7. 检验准则
7.1. 目视的外观与分类 未出现回火的零件在清洗和侵蚀后呈现均匀的灰色。局部回火区域在侵蚀后的零件上呈现深灰或黑色。通常,
随着颜色变的越深暗,说明回火烧伤程度越严重。如果在磨削过程中出现严重过热,将导致再硬化,再硬化
区域是一块白色或浅颜色的未回火马氏体,周围是黑色回火面。
所有的磨削后回火,尤其是再硬化的烧伤(即未回火马氏体)会影响零件的寿命,但零件仍可使用。
a)避免直接接触酸碱、溶剂。
b)将酸加入水中或酒精中,防止加反。
c)浸泡箱不用时加盖盖好。
d)遵守可燃和易燃液体储存及使用的安全措施。
有烧伤
无烧伤
机后要检查磨销烧伤。
做好记录。
10. 维护和管理 根据溶液的使用程度或当新配制溶液时,为检验溶液的性能,建议用该溶液侵蚀已知有回火显示的样品零件。
在侵蚀和检验后,该样品应再防锈保护备用,这类样品应定期更换。
根据使用程度,应定期检验溶液的浓度和杂质。
样品和溶液每 7 天更换一次。
11. 安全和环境保护。
磨削烧伤检查规定 1. 目的
保证工件在磨削工序中质量得到保证。 2. 适用范围
本标准规定了用化学侵蚀方法对磨削表面的局部过热进行检验及其分类的标准操作程序和要求,同时硬度法 作为对化学侵蚀方法的校核。 本标准适用于工件在热处理后,进行磨削工序中的检查。对于调质后、高频淬火后、渗碳淬火后的工件都适 用。 本标准不适用氮化零件和不锈钢零件。 化学侵蚀方法对表面硬度的变化的反映比大多数硬度测试方法更为敏感。 表面回火侵蚀检验应在表面磨削后,并在进一步精加工工序之前进行。比如连杆在珩磨前、曲柄销在研磨前。 3. 引用标准 GB/T 17879-1999 齿轮磨削后表面回火的浸蚀检验 4. 设备 4.1. 容器的材料与容器内溶液不得发生反应,也不得损伤被处理的零件。所有容器都应贴上所盛溶液的标签,并 在不用时盖好。本公司采用玻璃烧杯,并用平板玻璃盖好。 4.2. 被检验区域照明 被检验区域应有充分的照明,没有阴影和反射。摧荐被检验区域的光照度应不低于 3200lx。 4.3. 计时装置 应使用适当的计时器(秒表)。保证一组中的所有零件处理过程一致。 4.4. 清洗装置 应采用碱清洗器、蒸汽去油器、溶液清洗装置或相应的清洗装置。 5. 试剂 所有的化学试剂应为工业级或更纯的等级。 5.1. 清洗材料 所有清洗材料应保证能去除所有的污渍、磨粒和油渍,使被检表面可形成不破水膜。不破水膜是指表面用低 于 40℃的清水漂洗干净后,水膜至少应在 15S 内保持不破。 5.2. 硝酸 硝酸密度ρ=1.42Kg/l 5.3. 盐酸 盐酸密度ρ=1.19Kg/l 5.4. 酒精 应使用清洁的、不含油等杂质的甲醇或变性乙醇。 5.5. 水 清洁、无杂质。 5.6. 碱溶液 应使用 4%——6%的氢氧化钠溶液,其 PH≥10。 6. 检验程序 工件清洗→清洗后零件表面应达到能形成不破水膜→侵蚀→检验 6.1. 清洗 a)采用蒸汽清洗。 b)碱洗或超声波清洗。 6.2. 侵蚀 6.2.1. 腐蚀液的配制。
什么是磨削烧伤

完整的解释下,什么是磨削烧伤,磨削烧伤对硬度的影响是什么?对金相组织是什么?怎么样避免磨削烧伤?悬赏分:50 |提问时间:2010-12-10 12:20 |提问者:642347315完整的解释下,什么是磨削烧伤,磨削烧伤对硬度的影响是什么?对金相组织是什么?怎么样避免磨削烧伤?对于实际的操作中Cr5 Cr3冷轧辊辊身淬火后,精磨时的注意项。
我知道问题有点多,也有点难度,有回答尽量回答把,我一定高分献上推荐答案一、磨削烧伤,是指由于磨削时的瞬时高温使工件表层局部组织发生变化,并在工件表面的某些部分出现氧化变色的现象。
二、磨削烧伤会降低材料的耐磨性、耐腐蚀性和疲劳强度,烧伤严重时还会出现裂纹。
淬火钢零件的磨削烧伤主要有良种形式:1、回火烧伤,指当磨削区温度显著地超过钢的回火温度但仍低于相变温度时,工件表层出现回火屈氏体或回火索氏体软化组织的情况。
2、淬火烧伤,当磨削区温度超过相变温度Ac1时,工件表层局部区域就会变成奥氏体,随后受到冷却液及工件自身导热的急速冷却作用而在表面极薄层内出现二次淬火马氏体,次表层为硬度大为降低的回火索氏体,这就是二次淬火烧伤。
三、判别磨削烧伤的方法主要有:1、观色法,随着磨削区温度的升高,工件表面氧化膜的厚度就不同,因而会呈现出黄、草黄、褐、紫等不同的“回火色”。
但表面没有烧伤色并不意味着表层没有烧伤。
此判别法准确性较低。
2、酸洗法,利用钢件不同的金相组织对酸腐蚀有不同的敏感性,以轴承钢为例,正常回火马氏体酸洗后呈灰色,发生二次淬火烧伤时酸洗后呈白色。
生产中常用此法作抽检。
3、金相组织法,通过观察表层金相组织的变化来判别烧伤类别。
此判别法准确度高。
4、显微硬度法,工件表层金相组织变化必然导致其显微硬度的变化,因此,观察其硬度变化,可判断烧伤类别及测定变质层深度。
缺点是需要制作试件。
四、磨削裂纹,在磨削渗碳钢、工具钢、淬火高碳钢、硬质合金等工件时,容易在表层出现细微的裂纹。
不锈钢磨削烧伤的解决方案

(1)储存外观安全状态检测 对试验样储存期间,对试验样的外观进行观察分析,每半 个月对外包装及药卷进行观察,发现外包装未发现变形,药卷 未饱满,证明乳化炸药中的铝粉未发生明显的反应或反应微弱。 (2)储存爆炸性能检测 为了观察试验样品性能变化,存储试验数据如下:
储存性能检测对照表
储存时间
一个月 二个月 三个月 四个月 六个月
[6]汪大立,炸药爆炸理论,淮南工业学院化工系 一九九三年二
月 38~57;268~274.
C H I N A
V E N T U R E
C A P I T A L
103
科技技术应用|TECHNOLOGY APPLICATION
磨削效果和成本的优势。而其它三种磨粒单独测试磨削效果也 不明显,烧伤现象无明显改善。如果利用微晶刚玉和单晶刚玉 各自的特性,将这二种磨料混合使用;再而为减小磨削时砂轮 的粘附阻塞,保证光洁度的情况下应选用较粗粒度的砂轮。粗 精磨选用 80 号粒度,又可满足表面粗糙度的要求。
爆速 ×103m/s 4.1 4.2 4.0 3.9 4.0 3.9 3.7 3.6 3.4 3.4
生产样 猛度 mm
16.5 15.4 14.0 13.8 12.5
殉爆 cm
[5]2/2 [4]2/2 [4]2/2 [3]2/2 [3]2/2
爆速 ×103m/s 4.4 4.3 4.3 4.2 4.2 4.2 4.1 4.2 4.1 4.0
一、分析
要了解问题所在,找到解决方法,必须先知道造成磨削烧 伤的机理和不锈钢的特性。
简单地说,磨削加工过程中,所有消耗的能量几乎转为磨 削热。磨削区的温度很高,可达 1000℃~ 1500℃。如果冷却 不及时,会造成磨粒耗损及磨屑熔着现象更甚造成工件加工表 层金相组织发生变化或破坏,造成热损伤,产生回火或二次淬 火层,这就是所说磨削烧伤。
什么是回火烧伤

什么是回火烧伤,淬火烧伤,退火烧伤?有什么区别时间:2013-03-28来源:济世康民网作者:济世康民网点击: 1444 次
满足谜底
当切削热使被加工外貌的温度高出相变温度后,表层金属的金相组织将会产生变革。
1. 磨削烧伤
当被磨工件外貌层温度到达相变温度以上时,表层金属产生金相组织的变革,使表层金属强度和硬度低落,并伴有残余应力发生,甚至呈现微观裂纹,这种现象称为磨削烧伤。
在磨削淬火钢时,大概发生以下三种烧伤:
回火烧伤
假如磨削区的温度未高出淬火钢的相变温度,但已高出马氏体的转变温度,工件表层金属的回火马氏体组织将转酿成硬度较低的回火组织(索氏体或托氏体),这种烧伤称为回火烧伤。
淬火烧伤
假如磨削区温度高出了相变温度,再加上冷却液的急冷浸染,表层金属产生二次淬火,使表层金属呈现二次淬火马氏体组织,其硬度比本来的回火马氏体的高,在它的基层,因冷却较慢,呈现了硬度比原先的回火马氏体低的回火组织(索氏体或托氏体),这种烧伤称为淬火烧伤。
退火烧伤
假如磨削区温度高出了相变温度,而磨削区域又无冷却液进入,表层金属将发生退火组织,外貌硬度将急剧下降,这种烧伤称为退火烧伤。
磨削烧伤、磨削裂纹及控制措施
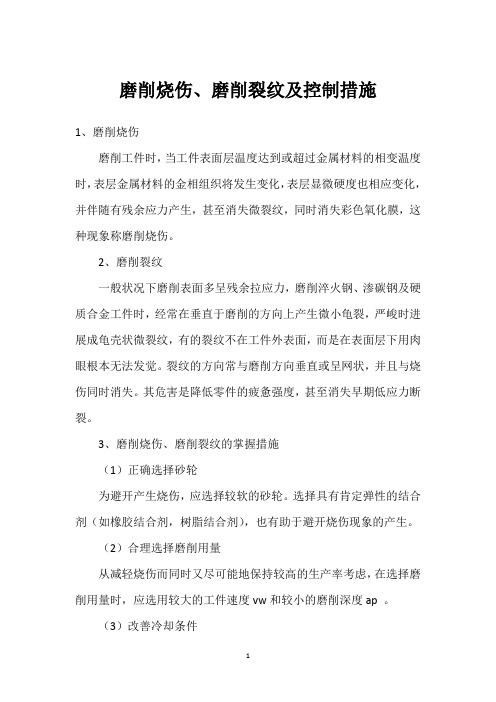
磨削烧伤、磨削裂纹及控制措施1、磨削烧伤磨削工件时,当工件表面层温度达到或超过金属材料的相变温度时,表层金属材料的金相组织将发生变化,表层显微硬度也相应变化,并伴随有残余应力产生,甚至消失微裂纹,同时消失彩色氧化膜,这种现象称磨削烧伤。
2、磨削裂纹一般状况下磨削表面多呈残余拉应力,磨削淬火钢、渗碳钢及硬质合金工件时,经常在垂直于磨削的方向上产生微小龟裂,严峻时进展成龟壳状微裂纹,有的裂纹不在工件外表面,而是在表面层下用肉眼根本无法发觉。
裂纹的方向常与磨削方向垂直或呈网状,并且与烧伤同时消失。
其危害是降低零件的疲惫强度,甚至消失早期低应力断裂。
3、磨削烧伤、磨削裂纹的掌握措施(1)正确选择砂轮为避开产生烧伤,应选择较软的砂轮。
选择具有肯定弹性的结合剂(如橡胶结合剂,树脂结合剂),也有助于避开烧伤现象的产生。
(2)合理选择磨削用量从减轻烧伤而同时又尽可能地保持较高的生产率考虑,在选择磨削用量时,应选用较大的工件速度vw和较小的磨削深度ap 。
(3)改善冷却条件① 采纳高压大流量法此法不但可以增加冷却作用,而且也增加了对砂轮的冲洗作用,使砂轮不易堵塞。
② 安装带空气挡板的喷嘴此法可以减轻高速回转砂轮表面处的高压附着气流作用,使磨削液能顺当喷注到磨削区。
③ 采纳磨削液雾化法或内冷却法采纳特地装置将磨削液雾化,使其带走大量磨削热,增加冷却效果;也可采纳内冷却砂轮,其工作原理如图所示。
经过严格过滤的磨削液由锥形套1经空心主轴法兰套2引入砂轮的中心腔3内,由于离心力的作用,磨削液经由砂轮内部有径向小孔的薄壁套4的孔隙甩出,直接浇注到磨削区。
图内冷却砂轮结构1-锥形盖2-主轴法兰套3-砂轮中心腔4-薄壁套。
磨削烧伤及预防措施
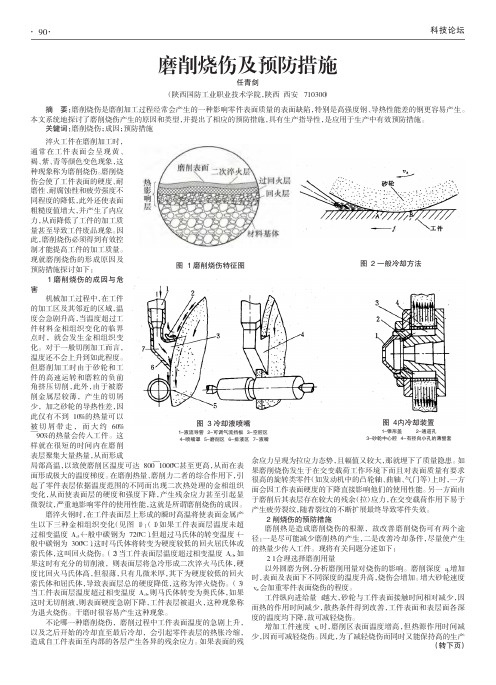
[3]朱正德.工件磨削烧伤及其检测、评定方法简析[J].柴油机设计与
另外在使用砂轮时可以在砂轮圆周上开槽,使砂轮间断磨削, 制造,2013,19(2):36-39.
工件受热时间短,金相组织来不及转变,同时又改善了散热条件,对 [4]刘高群,杨洪平.磨削烧伤研究[J].航空精密制造技,2011,47(2):54-
图 4 内冷却装置
1- 锥形盖 2- 通道孔 3- 砂轮中心腔 4- 有径向小孔的薄璧套
表层聚集大量热量,从而形成
余应力呈现为拉应力态势,且幅值又较大,那就埋下了质量隐患。如
局部高温,以致使磨削区温度可达 800 ̄1000℃甚至更高,从而在表 果磨削烧伤发生于在交变载荷工作环境下而且对表面质量有要求
防止烧Байду номын сангаас效果良好。
56.
2.3 冷却条件
[5] 郭 长 永 . 磨 削 烧 伤 的 成 因 及 预 防 措 施 [J] 科 技 信 息 ,2011,19:513 -
采用切削液带走磨削区的热量可以避免烧伤。目前通用的冷却 513.
方法效果较差,由于高速旋转的砂轮表面上产生强大气流层,实际
作者简介:任青剑(1960-),男,本科,陕西国防工业职业技术学院,
过相变温度 Ac3(一般中碳钢为 720℃),但超过马氏体的转变温度(一 径:一是尽可能减少磨削热的产生,二是改善冷却条件,尽量使产生
般中碳钢为 300℃),这时马氏体将转变为硬度较低的回火屈氏体或 的热量少传入工件。现将有关问题分述如下:
索氏体,这叫回火烧伤。(2)当工件表面层温度超过相变温度 Ac3,如
对于硬度太高的砂轮,钝化砂粒不易脱落,容易产生烧伤,因此 [2]黄新春,张定华,姚倡锋,任敬心.超高强度钢 AerMetloo 磨削烧伤研
渗碳淬火齿轮磨削烧伤成因分析及改善措施
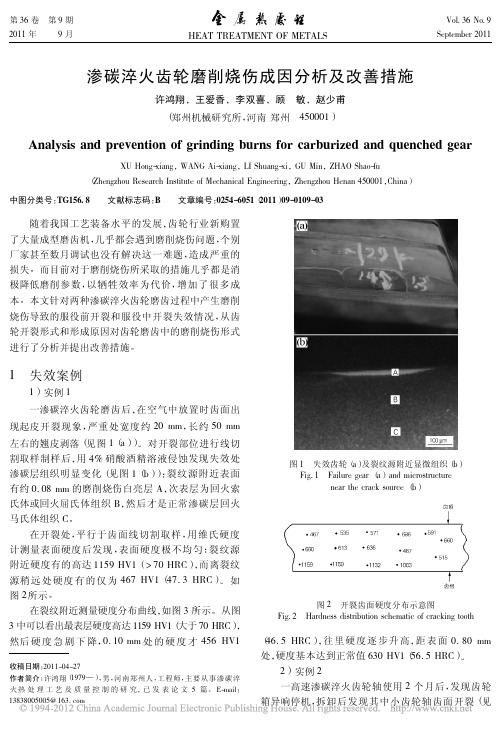
110
第 36 卷
图 3 失效齿轮裂纹源处硬度分布曲线 Fig. 3 Hardness distribution curve in crack
source of the failure gear
图 5 失效齿轮裂纹源附近硬度分布 Fig. 5 Hardness distribution curve in crack
source of the failure gear
图 4 ) 。在 裂 纹 附 近 取 样,4% 硝 酸 酒 精 溶 液 侵 蚀。 经金相分析,裂 纹 源 附 近 表 面 无 明 显 白 亮 层,但 有 约 0. 6 mm 左右深的变质层,组织为回火索氏体或回火屈 氏体 A,然后为回火马氏体组织 B,见图 4( b) 。
第 36 卷 第 9 期 2011 年 9 月
HEAT TREATMENT OF METALS
Vol. 36 No. 9 September 2011
渗碳淬火齿轮磨削烧伤成因分析及改善措施
许鸿翔,王爱香,李双喜,顾 敏,赵少甫 ( 郑州机械研究所,河南 郑州 450001)
Analysis and prevention of grinding burns for carburized and quenched gear
大一淬火剂有限公司 广东世创金属科技有限公司 江苏丰东热技术股份公司 科威嘉尼( 北京) 科技有限公司 天龙科技炉业( 无锡) 有限公司 武汉华敏测控技术有限公司 一汽普雷特科技股份公司 张家港市创典炉窑配套风机厂 浙江海盐华辰工业炉有限公司 郑州科创电子有限公司 日本领先科技设备株式会社 意大利 TAV 真空炉有限公司 北京赛维美高科技有限公司 赛科沃克( 天津) 工业炉有限公司 东莞市震霖实业有限公司 湖南省中南炉业有限公司特殊钢厂 昆山同和热处理工业炉有限公司 天津市宝尔发电热材料有限公司 上海开信机械制造有限公司 南京新光英炉业有限公司 上海中加电炉有限公司 上海宝华威热处理设备有限公司
磨削烧伤的成因

机 械 管 理 开 发
M ECH ANI CAL M ANAGEMENT AND DEVELOPM ENT
21年1 01 0月
0e .01l t2
磨削烧伤的成 因
李 晓文
( 中国重汽大同齿轮有限公司 技术中心 , 山西 大同 070 30 6)
铁素体和珠光体 , 工件表面的硬度急剧下降 , 工件表层 退 火 , 种 现象 称 为 退火 烧 伤 。在 干 磨 时容 易产 生 这 这 种 烧 伤 。磨 削时 , _ 表 层 温 度超 过 相 变 温度 A 。回 ]件 , 火 马 氏体 组 织 逐渐 转 变 为奥 氏体 组 织 , 使用 磨 削 液 在 急 冷条 件下 , 则表 面形 成二 次淬 火马 氏体 , 二次淬 火 马 氏体组织 很 薄 , 度较 回火 马 氏体 高 , 硬 这种烧 伤称 为淬 火 烧 伤 。磨 削 加 工 时 , 件 表 面 未 超 过 A .但 超 过 工 , 300, 时 马 氏体转 变 为 回火 托 氏体 , 种烧 伤 称为 0 =这 【 这 回火 烧 伤 。 在 30o以 下 一 般 不 发 生 晶 相 结 构 的 转 0 C 变 , 以不 产生 烧伤 问题 。 所
1 磨 削原理 磨 削热使 工 件 表层 的金相 结 构 产生 变 化 、 面层 表 的硬 度改变 , 会影 响零 件 的使用性 能 , 同时 工件 表面呈 现氧化 膜 的颜色 , 这种 现象 称为磨 削烧 伤 。 磨 削也 是 一种 切 削 , 轮 表 面上 的每个 磨 粒 可 近 砂 似看 作微 小 刀齿 , 出 的磨粒 尖 棱 可认 为 是微 小 的切 突 削刃 ; 削 时 , 突 出的磨粒 , 磨 较 可获 得较 大 的切削 厚度 , 从而切 下切 屑 ; 突 出或磨钝 的磨 粒 , 不 只在工 作 表面刻 划 出细 小 的沟痕 , 工件材 料则 被挤 向磨 粒两 旁 , 沟痕 在 两边 隆起 ; 凹下 的磨 粒 , 较 既不 切 削 又不 刻 划工 件 , 只 是 从工 件 表 面滑 擦 而过 ” 因 而磨 削过 程 既 有切 削 , , 又 有 刻划 和 划擦 。此 时 , 被磨 工 件材 料 受 到磨 削力 的作 用, 产生塑性变形 , 晶格扭 曲 、 使 晶粒 被拉长 、 呈纤维 化 , 表 面层 硬化 增 加 , 面产 生 压应 力 , 面硬 度 提 使 表 表 高, 耐磨性 增强 , 塑性 降低 。磨 削表 面一方 面受 到力 的 作用 , 一方 面会 受到磨 削热 的作 用 , 对塑 性变 形或 加 热 工硬 化 会有 很 大影 响 , 使 塑性 变 形产 生 恢 复 和再 结 会 晶, 这种 现 象称 之 为软 化 , 果磨 削热加 大 , 如 就有 可 能 产生烧 伤 。
磨削烧伤检查规定

a)避免直接接触酸碱、溶剂。
b)将酸加入水中或酒精中,防止加反。
c)浸泡箱不用时加盖盖好。
d)遵守可燃和易燃液体储存及使用的安全措施。
有烧伤
无烧伤
许表面硬度出现严重的低头现象。对于高频或调质后的零件,检测后显微硬度转换为洛氏硬度应不低于
没有磨削时的表面硬度,但应低于没有磨削时的表面硬度加 4HRC。 8. 回火侵蚀的去除
回火侵蚀后的颜色,采用珩磨去除。
9. 检验人员及检验频次 检验人员车间质检员。
按照工艺(修砂轮的频次)检查,每 2 小时检查 1 件,砂轮更换、设备维修、操作工更换、异常停机重新开
机后要检查磨销烧伤。
做好记录。
10. 维护和管理 根据溶液的使用程度或当新配制溶液时,为检验溶液的性能,建议用该溶液侵蚀已知有回火显示的样品零件。
在侵蚀和检验后,该样品应再防锈保护备用,这类样品应定期更换。
根据使用程度,应定期检验溶液的浓度和杂质。
样品和溶液每 7 天更换一次。
11. 安全和环境保护。
酒精
浸泡并干燥 去水
零件应浸泡足够的时间,以使零
4.
脱色
盐酸 50% (容积)
件上呈现出均匀的棕灰色。脱色 10 秒(10-20 秒) 时间应重复试验以确定确切时
间。
5
漂洗
水
8秒
去酸
6
中和
碱性溶液 PH≥10 20 秒(10-60 秒) 浸入后搅动零件
7
漂洗
水
8秒
去碱
8
酒精浸泡
酒精
浸泡并干燥 去水
9
通常应对有回火显示的零件进行磁粉探伤检验,尤其是渗碳淬火硬化的零件。
7.2. 显微硬度计检查
汽车渗碳淬火齿轮磨削烧伤的研究_吕红明

目前 CBN 砂轮也应用广泛, 其热稳 定性好, 磨削 温度低, 且本身硬度、强度仅次于金刚石, 磨削力小, 能 磨出较高的表面质量。另外, 采用有一定弹性的结合 剂, 如橡胶、树脂等, 也能改善砂轮磨削条件。当由于 某种原因导致切屑力增大时, 这样的结合剂能使砂轮 的磨粒产生一定的弹性退让, 使切屑深度自动减小, 避 免烧伤。
第 33 卷 第 3 期
汽车渗碳淬火齿轮磨削烧伤的研究
1 09
件表层硬度虽然很高, 但紧接着二次淬火烧伤层是严 重回火层, 其硬度突然下降 HV( 150~ 200) 。残余应力 从压应力很快转化为拉应力, 严重烧伤表面在磨削后 拉应力可达 736MPa, 中等烧伤在磨削后为( 373~ 392) MPa; 轻微烧伤为 49MPa。而在应力向拉应力转变的过 渡层内, 很容易产生不易察的显微裂纹, 在反复载荷的 作用下, 将影响齿轮的疲劳强度和使用寿命, 导致齿面 过早地磨损和点蚀, 甚至造成齿轮早期失效。另外由 于残余拉应力的作用, 往往是会沿着烧伤边缘产生磨 削裂纹, 故避免烧伤是防止磨削裂纹的先决条件。
3 影响齿面磨削烧伤的主要因素
对于渗碳淬火齿轮而言, 影响齿面磨削烧伤的主 要因素是磨削热的产生和磨削热的传出。其中, 影响 磨削热产生的是砂轮和磨削参数, 而影响磨削热传出 的是切削液及渗层碳浓度[ 6] 。 3. 1 砂轮
砂轮选的太硬, 磨钝了的磨粒不能及时脱落即自 锐性不好, 使磨削力增大、温度升高, 容易造成齿面烧 伤[ 7] 。砂轮粒度号太大( 磨粒太小) , 组织太紧, 容易引 起砂轮堵塞, 产生大量的磨削热引起烧伤。没有经常 修整砂轮, 砂轮太钝, 也易引起表面烧伤。 3. 2 磨削条件
- 1、下载文档前请自行甄别文档内容的完整性,平台不提供额外的编辑、内容补充、找答案等附加服务。
- 2、"仅部分预览"的文档,不可在线预览部分如存在完整性等问题,可反馈申请退款(可完整预览的文档不适用该条件!)。
- 3、如文档侵犯您的权益,请联系客服反馈,我们会尽快为您处理(人工客服工作时间:9:00-18:30)。
10804020136 张庆宇
一、磨削烧伤机理:
磨削烧伤,是指由于磨削时的瞬时高温使工件表层局部组织发生变化,并在工件表面的某些部分出现氧化变色的现象。
当磨削表面产生高温时,如果散热措施不好,很容易在工件表面(从几十um到几百um)发生二次淬火及高温回火。
如果磨削工件表面层的瞬间温度超过钢种的AC1点,在冷却液的作用下二次淬火马氏体,而在表层下由于温度梯度大,时间短,只能形成高温回火组织,这就使在表层和次表层之间常山拉应力,而表层为一层薄而脆的二次淬火马氏体,当承受不了时,将产生裂纹。
磨削烧伤会降低材料的耐磨性、耐腐蚀性和疲劳强度,烧伤严重时还会出现裂纹。
淬火钢零件的磨削烧伤主要有良种形式:
二、在磨削淬火钢时,可能产生以下3种烧伤:
1.回火烧伤
如果磨削区的温度未超过淬火钢的相变温度,但已超过马氏体的转变温度,止推面表层金属的回火马氏体组织将转变成硬度较低的回火组织(索氏体或托氏体),这种烧伤称为回火烧伤。
2.淬火烧伤
如果磨削区温度超过了相变温度,再加上冷却液的急冷作用,表层金属发生二次淬火,使表层金属出现二次淬火马氏体组织,其硬度比原来的回火马氏体的高,在它的下层,因冷却较慢,出现了硬度比原先的回火马氏体低的回火组织(索氏体或托氏体),这种烧伤称为淬火烧伤。
3.退火烧伤
如果磨削区温度超过了相变温度,而磨削区域又无冷却液进入,
表层金属将产生退火组织,表面硬度将急剧下降,这种烧伤称为退火烧伤。
在曲轴成形磨削中,多属于此种烧伤。
三、判别磨削烧伤的方法主要有:
1)观色法
随着磨削区温度的升高,工件表面氧化膜的厚度就不同,因而会呈现出黄、草黄、褐、紫等不同的“回火色”。
但表面没有烧伤色并不意味着表层没有烧伤。
此判别法准确性较低。
2)酸洗法
利用钢件不同的金相组织对酸腐蚀有不同的敏感性,以轴承钢为例,正常回火马氏体酸洗后呈灰色,发生二次淬火烧伤时酸洗后呈白色。
生产中常用此法作抽检。
3)金相组织法
通过观察表层金相组织的变化来判别烧伤类别。
此判别法准确度高。
4)显微硬度法
工件表层金相组织变化必然导致其显微硬度的变化,因此,观察其硬度变化,可判断烧伤类别及测定变质层深度。
缺点是需要制作试件。
四、消减磨削烧伤与裂纹的工艺途径
1、正确选用砂轮,例如可采用颗粒较粗、较软、组织较疏松的砂轮;砂轮磨损后应及时修整。
若砂轮的粒度越细、硬度越高时自砺性差,则磨削温度也增高。
砂轮组织太紧密时磨屑堵塞砂轮,易出现烧伤。
砂轮钝化时,大多数磨粒只在加工表面挤压和摩擦而不起切削作用,使磨削温度增高,故应及时修整砂轮。
2、改善磨削时的冷却条件,如采用内冷却方法;设法使冷却液渗透到磨削区中。
3、合理选择磨削用量,例如提高工件的转速,采用较小的径向进给量。
减小磨削深度可以减少工件表面的温度,故有利于减轻烧伤。
增加工件速度和进给量,由于热源作用时间减少,使金相组织来不及变化,因而能减轻烧伤,但会导致表面粗糙度值增大。
一般采用提高砂轮速度和较宽砂轮来弥补。
4、提高工件转速可以减少烧伤发生的机率,原因是减少磨削厚度和传热时间,利于磨屑带走热量
5、冷却液的浓度;
6、冷却液的喷溅流量及喷溅部位。