SMP-P-G012-00物料平衡及产品收率管理规程
GMP体系文件物料平衡管理规程

目的:建立一个物料平衡的工作标准,掌握生产过程中物料平衡,进行严格的收率控制,防止发生差错和出现混药现象。
范围:产品生产过程中的各个关键工序
责任人:岗位操作人员、车间管理人员、质量保证部、生产制造部。
内容:
1、在每个关键工序计算收率,进行物料平衡是避免或及时发现差错与混药的有效方法之一,因此,每个品种关键生产工序的批生产记录(批包装记录)都必须明确规定物料平衡的计算方法,以及根据验证结果确定收率范围。
2、物料平衡计算的基本要求
2.1 物料平衡计算公式:物料平衡=(产出量+尾料量)/(总投入量)× 100%
产出量:生产过程中实际产出量,不包括收集的废品量,生产中取得样品量(检品),丢弃的不合格物料。
尾料量:生产过程中产生的药头数量等。
总投入量:生产过程实际投入的数量。
2.2 在生产过程中如有跑料现象,应及时通知车间管理人员及质量保证部质量监督员,并详细记录跑料过程及数量。
跑料量也应计入物料平衡中,加在实际范围之内。
3、物料平衡计算单位
3.1 固体以重量计算。
3.2 液体以体积或重量计算。
4、数据处理
4.1 凡物料平衡在规定范围之内,经质监员审核,可以递交下道工序。
4.2 凡物料平衡高于或低于合格范围,应立即贴“待查”标志,不能递交下道工序,并填写偏差通知单,通知车间管理人员及质监员按“生产过程偏差处理管理规程”进行调查处理,并如实记录。
4.3 质量保证部会同生产制造部定期对各工序收率及产品的总体物料平衡进行
核算,并进行回顾性验证,为工艺改进、技术革新及技术文件的修订提供参考。
SMP-SC-011 物料平衡及产率管理规程

无。
6变更历史
版本号01:新建文件,2015年5月1日起开始执行。
7附录
无。
4.4物料平衡的评价
4.4.1标准随工艺变化而变化,因此应处于动态管理之中。制剂室可以根据产品质量总结回顾评价既定标准的合理性,必要时进行适当的调整。
4.4.2当生产工艺、可能随之变化,质量管理部应负责组织评价各种工艺变化对物料平衡标准所带来影响的合理性,必要时应进行验证。
(2)分装操作的物料平衡
计算方法:物料平衡=(至贴签量 平均装量+损耗量)/至分装量 100%
限度:100%
(3)贴签操作的物料平衡
计算方法:实际产量=入库量+取样量
物料平衡=(实际产量+损耗量)/至贴签量 100%
限度:100%
4.2产率
计算方法:产率=实际产量/理论产量 100%
限度:95%~105%(普通制剂);90~110%(中药制剂)
4.3物料平衡的审核
4.3.1凡物料平衡在合格范围之内,经生产负责人检查确认后,可以递交下道工序。
4.3.2若物料平衡超出了合格范围,不能递交下道工序。要通知相关管理人员进行评估与调查,并详细记录,具体执行《偏差管理规程》。
4.3.3在进行批放行审核时应对各工序物料平衡情况进行审核,作为评价产品是否合格的重要指标之一。
4.1.2物料平衡的计算
每个工序必须进行物料平衡,药品生产过程中的物料平衡如有显著误差,必须进行调查,确认是否存在潜在质量风险,因此,物料平衡标准也是产品质量的检验性指标。
(1)配制操作的物料平衡
计算方法:物料平衡=(至分装量+取样量+损耗量)/总投料量 100%
限度:95%~105%(普通制剂);90~110%(中药制剂)
SMP-SC-WL010-00物料平衡管理规程
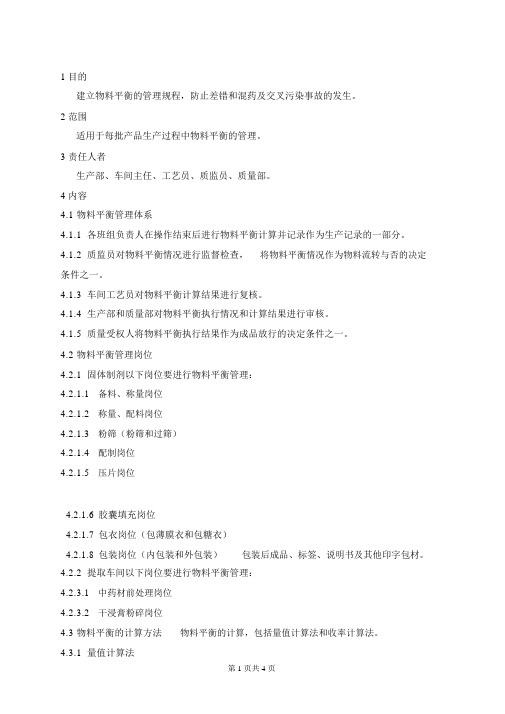
1目的建立物料平衡的管理规程,防止差错和混药及交叉污染事故的发生。
2范围适用于每批产品生产过程中物料平衡的管理。
3责任人者生产部、车间主任、工艺员、质监员、质量部。
4内容4.1 物料平衡管理体系4.1.1 各班组负责人在操作结束后进行物料平衡计算并记录作为生产记录的一部分。
4.1.2 质监员对物料平衡情况进行监督检查,将物料平衡情况作为物料流转与否的决定条件之一。
4.1.3 车间工艺员对物料平衡计算结果进行复核。
4.1.4 生产部和质量部对物料平衡执行情况和计算结果进行审核。
4.1.5 质量受权人将物料平衡执行结果作为成品放行的决定条件之一。
4.2 物料平衡管理岗位4.2.1 固体制剂以下岗位要进行物料平衡管理:4.2.1.1备料、称量岗位4.2.1.2称量、配料岗位4.2.1.3粉筛(粉筛和过筛)4.2.1.4配制岗位4.2.1.5压片岗位4.2.1.6胶囊填充岗位4.2.1.7包衣岗位(包薄膜衣和包糖衣)4.2.1.8包装岗位(内包装和外包装)包装后成品、标签、说明书及其他印字包材。
4.2.2 提取车间以下岗位要进行物料平衡管理:4.2.3.1中药材前处理岗位4.2.3.2干浸膏粉碎岗位4.3 物料平衡的计算方法物料平衡的计算,包括量值计算法和收率计算法。
理论数(实际投入量)=产成品数+残次品数4.3.2 收率计算法平衡收率=实际值 / 理论值× 100%理论值为实际投入物料量。
实际值为生产过程中实际产出量包括本岗位正品产出量、废品量、零散品量、生产中取样(留样)量。
4.3.3 在生产过程中如有跑料、散装后跌落在地上的物料,要及时通知车间工艺员及车间质监员,详细记录损失数量及事故过程,其损失数计入残次品数之内进行计算。
4.3.4 上工序移交下来的有效物料并经复核的数量,计入下工序计算收率的理论值。
4.3.5 理论投入数与实际产出数二者的正负误差要控制在允许范围内。
4.3.6允许偏差范围根据各产品的特性及加工部位的不同分别制定各岗位平衡允许偏差范围。
【精】GMP物料平衡与收率3
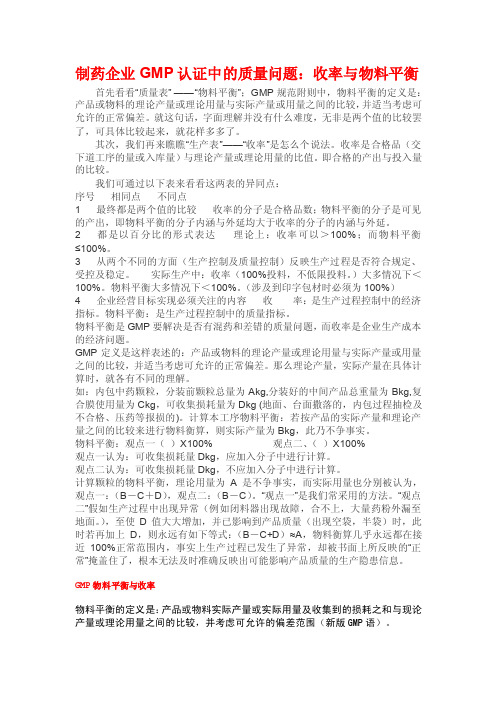
制药企业GMP认证中的质量问题:收率与物料平衡首先看看“质量表” ——“物料平衡”;GMP规范附则中,物料平衡的定义是:产品或物料的理论产量或理论用量与实际产量或用量之间的比较,并适当考虑可允许的正常偏差。
就这句话,字面理解并没有什么难度,无非是两个值的比较罢了,可具体比较起来,就花样多多了。
其次,我们再来瞧瞧“生产表”——“收率”是怎么个说法。
收率是合格品(交下道工序的量或入库量)与理论产量或理论用量的比值。
即合格的产出与投入量的比较。
我们可通过以下表来看看这两表的异同点:序号相同点不同点1 最终都是两个值的比较收率的分子是合格品数;物料平衡的分子是可见的产出,即物料平衡的分子内涵与外延均大于收率的分子的内涵与外延。
2 都是以百分比的形式表达理论上:收率可以>100%;而物料平衡≤100%。
3 从两个不同的方面(生产控制及质量控制)反映生产过程是否符合规定、受控及稳定。
实际生产中:收率(100%投料,不低限投料。
)大多情况下<100%。
物料平衡大多情况下<100%。
(涉及到印字包材时必须为100%)4 企业经营目标实现必须关注的内容收率:是生产过程控制中的经济指标。
物料平衡:是生产过程控制中的质量指标。
物料平衡是GMP要解决是否有混药和差错的质量问题,而收率是企业生产成本的经济问题。
GMP定义是这样表述的:产品或物料的理论产量或理论用量与实际产量或用量之间的比较,并适当考虑可允许的正常偏差。
那么理论产量,实际产量在具体计算时,就各有不同的理解。
如:内包中药颗粒,分装前颗粒总量为Akg,分装好的中间产品总重量为Bkg,复合膜使用量为Ckg,可收集损耗量为Dkg (地面、台面撒落的,内包过程抽检及不合格、压药等报损的)。
计算本工序物料平衡:若按产品的实际产量和理论产量之间的比较来进行物料衡算,则实际产量为Bkg,此乃不争事实。
物料平衡:观点一()X100%观点二、()X100%观点一认为:可收集损耗量Dkg,应加入分子中进行计算。
物料平衡的标准管理规程

物料平衡的标准管理规程一、目的:建立物料平衡的标准管理规程,防止发生差错。
二、适用范围:适用于每批产品生产过程中物料平衡的管理。
三、责任者:生产技术部负责人、操作工人、质量监督员。
四、正文:1 在关键工序计算收率,进行物料平衡是避免或及时发现差错的有效方法。
2 收率计算的基本方法:2.1 收率计算收率=实际值/理论值×100%其中:理论值:为按照所用的原料(包装材料)量,在生产中无任何损失或差错的情况下得出的最大数量;实际值:为生产过程中实际产出量包括本工序正品产出量。
2.2 在生产过程中如有跑料、散装后跌落在地上的物料,应及时通知组长及品管监督员,详细记录损失数量及事故过程,其损失数加在实际值之内进行计算。
2.3上工序移交下来的有效物料并经复核的数量,为下工序计算收率的理论值。
2.4各工序物料平衡计算具体方法:2.4.1 过筛打粉预处理:检查与复核原物料品名、数量、以及其质量情况。
每一个物料,打粉过筛后称重量,并将上述每一种物料经打粉后的损耗率记录在工艺原始记录上。
计算:物料损耗率=(打粉过筛前总重-打粉过筛后总重)/打粉过筛前总重×100%2.4.2制颗粒:检查与复核领入原物料的品名、批号、数量以及质量情况,如发现有异常情况,及时报告品管监督员同意后退回中间站。
颗粒制好后,称重量、抽样测含量,必要时可增加测水分。
2.4.2.1 计算总收率:预处理后物料总重量及制粘合剂的固体料(不含配粘合剂所用的液体溶媒)之和为理论值,颗粒干燥后总重量及捕尘器中废料和收集的残料之和为实际值,颗粒总收率=实际干颗粒共重/(本批配料后的总共重量+外加辅料)×100%颗粒损耗率=(制料前总重-实际干颗粒共重)/制粒前总重×100%2.4.2.2 损耗率太大或有问题时,必须查明原因,如检查工序内地面上积粉等可收集部分称重后,再复核计算是否相符,要求将损耗率降低。
如果损耗率是负值,很可能颗粒中水分太高。
物料平衡的管理规程
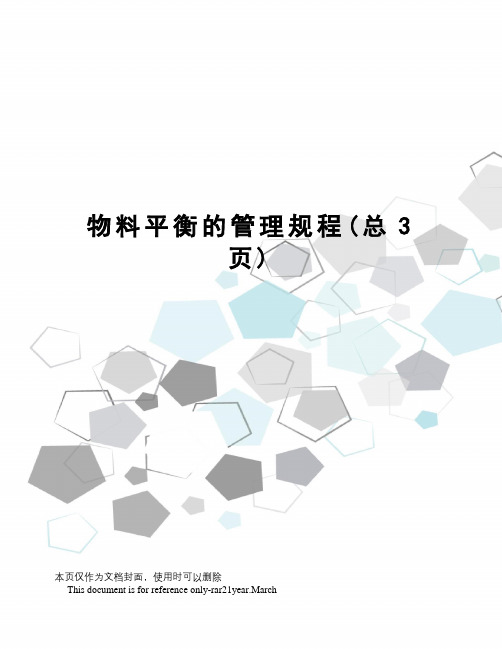
物料平衡的管理规程(总3页)本页仅作为文档封面,使用时可以删除This document is for reference only-rar21year.March建立物料平衡的管理规程。
建立物料平衡的审核标准,掌握生产过程中物料收率变化,防止差错和混药。
2 范围适用于每个批次产品生产过程的关键工序都要进行物料平衡的计算及偏差处理。
3 职责生产技术部部长、生产车间主任、工艺员、操作工,QA监控员。
岗位操作人员负责本岗位平衡的计算,并对计算结果进行判断;生产车间主任负责批平衡收率的计算,工艺员负责各岗位平衡收率的审核及对出现偏差进行分析和说明;QA负责批生产平衡的审核。
4 内容4.1 物料平衡是产品或物料实际产量或实际用量及收集到的损耗之和与理论产量或理论用量之间的比较,并考虑可允许的偏差范围。
4.2 物料平衡的计算是为了防止物料误用和非正常流失4.3 每个品种各关键生产工序的批生产记录(批包装记录)都必须明确规定平衡的计算方法,以及根据验证结果和生产实际确定的平衡限度范围。
4.4 物料平衡计算:产出量+废品量+剩余量物料平衡=×100%(99-100%)投入量投入量:领料的净量。
产出量:为生产过程中实际产出量,包括合格产品和不合格产品。
废品量:过程抛撒受污染后收集的扫地料及检测后不能再使用的产品或料粉。
4.5 物料平衡计算单位:4.5.1 中间产品、成品:中间体采用重量单位(kg);说明书、包装袋、包装盒、包装箱等,分别采用“张”、“只”、“套”、“个”计算。
4.6 结果处理:4.6.1 凡物料平衡在规定平衡限度范围之内,经质量部QA检查确认后,产品可以递交下工序。
4.6.2 凡物料平衡超出规定平衡限度范围的,应立即贴示“待验”标志,产品不得递交下工序,操作工应及时填写《偏差通知单》,通知生产车间主任及QA监控员按《生产过程偏差处理管理规程》中有关偏差处理程序进行调查,采取处理措施,并详细记录。
GMP物料平衡管理规程

页码:文件编号:生效日期: 再版日期:第1页/共2页SMP-PM-01003-1标准管理规程STANDARD MANAGEMENT PROCEDURESubject题目:物料平衡管理规程Issued by颁发部门:质量部Written by起草人:Date日期:Dept. Head Approval 部门主管审核:Date日期:QA Director Approval QA 主管审核:Date日期:Approved by批准:Date日期:Dispense分发:总经理、质量部、生产部、商务部、行政人事部1.目的建立物料平衡的管理规程,严格物料管理,防止物料流失,控制成品率;防止差错和混药事故的发生。
2.适用范围适用于每批产品生产过程中物料平衡的管理。
3.责任者生产部、各生产车间、商务部、质量部相关人员。
4.内容4.1.在每个关键工序计算收率、进行物料平衡,是避免和及时发现差错与混料的有效方法之一。
因此,每个品种各关键生产工序的批生产记录(批包装记录)都必须明确规定收率的计算方法,以及根据验证结果确定的收率合格范围。
4.2.收率计算的基本要求:4.2.1.收率计算:实际值收率=─────────×100%理论值其中:理论值:按照所用的原料(包装材料)量,在生产中无任何损失或差错的情况下得出的最大数量。
实际值:生产过程中实际产出量,包括:本工序产出量、生产中取得样品量(检品)4.2.2.在生产过程中如有跑料现象和可见损耗,应及时通知车间管理人员及QA部门QA检查员,并详细记录跑料可见损耗过程及数量。
跑料和可见损耗数量也应计入物料平衡之中,加在实际值的范围之内。
页码:文件编号:生效日期: 再版日期:第2页/共2页SMP-PM-01003-1标准管理规程STANDARD MANAGEMENT PROCEDURESubject题目:物料平衡管理规程Issued by颁发部门:质量部4.2.3.如若实际收率在规定的收率范围内,即视为物料平衡合格,一般收率应在97%-101%之间。
GMP质量体系010物料平衡管理规程

物料平衡管理规程
1. 目的:建立物料平衡管理规程,防止差错和混淆。
2 范围:生产车间的关键工序。
3 责任:操作工、过程监控员、车间负责人、质量负责人、生产负责人对本规程的实
施负责。
4 内容:
4.1 物料平衡是指产品或物料的理论产量或理论用量与实际产量或用量之间的比较,并
适当考虑可允许的正常偏差。
4.2 每批产品生产结束后,由车间对物料进行平衡计算,及时发现差错与混药。
4.2.1 物料平衡的计算:
%100⨯=
理论值
实际值
物料平衡
注:实际值:为生产中实际产出量。
包括本工序产出量(合格品);收集的废品量;
生产中的样品量(检品、留样观察品)。
理论值:按照生产指令所用的原料、包装材料量,在生产过程中无任何损失
或差错的情况下得出的理论数量。
4.3 需要进行物料平衡计算的主要工序;见下表:
物料平衡表:
4.4 数据的处理:
4.4.1 物料平衡率高于或低于合格范围,不能递交下工序,通知过程监控员及质量部有关
人员进行调查,采取处理措施,并详细记录。
4.4.2 质量负责人对各工序物料平衡进行检查,为工艺改进、技术标准文件的修订提供参
考。
SMP-产品质量档案管理规程

标准管理文件STANDARD FILE MANAGEMENT审批分发部门一、目的:规范产品质量档案管理,规定归档时间和内容,使产品质量具有可追溯性。
二、适用范围:本规程适用于公司内所有产品的档案资料管理。
三、定义:不涉及四、职责:QA档案管理员对产品档案进行收集、整理、保管。
五、规程内容:1 本公司生产所有产品均要建立产品质量档案,将产品质量技术资料、检测数据等积累存档,为质量管理和检验工作提供决策依据。
2 产品质量档案的内容2.1 产品简介:包括产品名称、规格、批准文号、批准日期、处方或结构式、简要工艺流程、工艺处方、原辅材料消耗定额、适应症或功能主治等。
2.2 产品质量标准沿革,主要原辅料、中间产品、成品、包装材料、标签等质量标准、检验方法变更情况资料。
2.3 历年来与国内外同类产品的对比情况。
2.4 历年来产品留样复验情况、留样观察及产品稳定性试验资料,每年均要有数据和书面总结。
2.5 质量指标完成情况。
2.6 质量标准变更:变更申请表、药品监督管理部门的批准件等资料,对比试验资料等。
2.7 生产历史及大事记录,记述生产重大工艺改进情况。
2.8 提高产品质量的科研报告摘要,包括:工作总结、数据资料、方法、效果、质量改进文字资料。
2.9 历年来产品质量重大事故分析记录及处理情况。
2.10 用户访问意见、退货、产品收回、紧急召回等情况,每年记录归档。
2.11 包装规格要求、标签、说明书箱头文字、尺寸、材质标准、变更文字说明、变更后资料。
2.12 市级以上药检所抽检的检验报告书,进口产品口岸药检所检验报告书。
3 归档要求3.1 质量档案随时发生随时归档,不受时间限制。
3.2 立卷必须遵循文件材料的自然形成规律和保持文件材料之间的有机联系这一原则,主要按专业,按时间组卷。
3.3 产品质量标准文件及资料、记录等应一并归档,平时在形成归档资料时,必须印有统一格式,选择质量较好的纸张,用电脑打印,或用碳素笔书写,不得复写或用铅笔、圆珠笔书写。
物料、产品审核放行管理规程
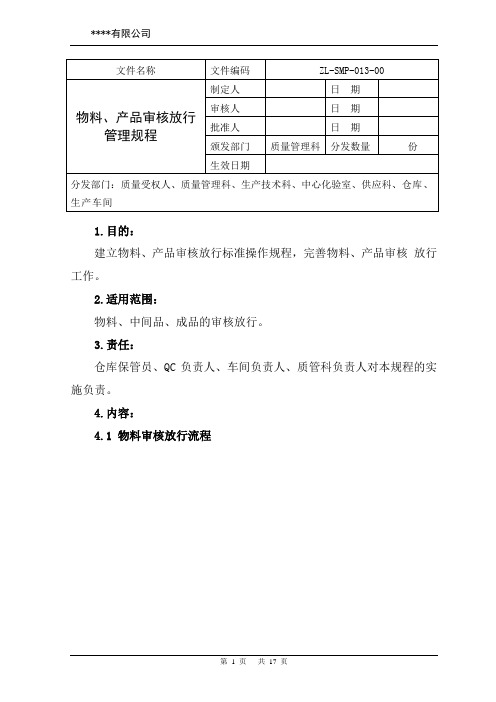
1.目的:建立物料、产品审核放行标准操作规程,完善物料、产品审核放行工作。
2.适用范围:物料、中间品、成品的审核放行。
3.责任:仓库保管员、QC负责人、车间负责人、质管科负责人对本规程的实施负责。
4.内容:4.1 物料审核放行流程4.2 成品审核放行流程4.3 各级放行人员职责仓库负责对入库物料进行初验。
◆化验室负责检验过程和检验结果的审核。
◆生产车间负责产品生产过程的审核。
◆质管科质量审核员负责物料、产品放行前的审核。
◆转受权人负责所用物料、包装材料的审核结果评估和批准放行。
◆质量受权人负责产品的审核结果评估和批准放行。
4.4 物料审核放行程序◆物料进厂,供应科及时填写《来货通知单》,仓库按《物料接收管理规程》对来货进行初验、贮存,并做好初验记录。
◆初验合格后填写《请验单》,交化验室取样检验,不合格物料拒收。
◆化验室接到请验单,及时到仓库取样,取样严格按照4《取样管理规程》进行,并对检品按内控质量标准、检验操作规程进行检验、记录。
检验结果异常按《OOS调查处理管理规程》进行处理,检验结果确认后,出具检验报告,填写《批检验过程审核表》,交QC负责人进行审核签字后,将检验记录和《批检验过程审核表》交给质量管理科审核员,同时在《记录送审登记表》上登记备查。
◆QC负责人对检验记录进行审核,并对检验过程和检验结果的正确性作出判断,审核内容有:●取样操作符合规定,取样记录完整准确,样品按规定储存条件存放,请验单完备;●检验是严格依照经过验证的分析方法的规定进行的,有法定标准的按法定标准进行检验,不再进行验证;●所有的检验均完成,检验记录内容完整,检验结果己复核,检验报告单打印内容及签章完整,内容和结论准确,记录内容和报告单内容相一致;●记录中计算过程经复核无误,复核人签字齐全。
记录中的原始图谱齐备,有检验人签名及日期,原始数据图谱与记录数据相一致;●检验过程中是否存在试液、仪器、对照品、执行SOP等方面的偏差;●检品己按规定的数量和保存位置进行了留样。
物料平衡管理规程

物料平衡管理规程一、目的:建立物料平衡的工作标准,掌握生产过程中物料平衡变化,防止差错和混淆二、范围:所有生产过程的关键工序,物料平衡率的计算处理。
三、责任者:生产部经理、车间主任、操作人员、车间工艺员、QA四、正文1.物料平衡是指产品或物料的实际产量或用量与理论产量或用量之间的百分比,并适当考虑可允许的偏差范围。
生产过程的各个关键工序在生产过程完成后计算收得率和物料平衡是避免并及时发现差错和混淆的有效方法。
2.物料平衡率可接受标准的制定工艺验证结束后,统计三批的物料平衡率结果,制定试行的物料平衡率。
一年生产结束后,生产部统计该年的正常生产结果,以统计结果作为物料平衡率的标准。
为工艺改进、技术革新及文件的修订提供依据。
3.操作人员计算物料平衡的依据为批生产记录(批包装记录)规定的物料平衡计算方法及根据验证结果确定的物料平衡合格范围。
各工序物料平衡计算应填写物料平衡记录。
4.物料平衡计算的基本方法实际值4.1物料平衡=────×100%理论值——理论值:根据投料量和原料、产品的分子量计算而得。
——实际值:为生产过程中实际加工产出量。
4.2在生产过程中如有跑料现象,应及时通知车间管理人员及质量保证部QA,并详细记录跑料过程及数量。
跑料数量也应计入物料平衡之中,加在实际值的范围之内。
4.3每个工段均需进行物料平衡和计算收率4.4各工序物料平衡计算是根据投料量,产出量及分子量等数据计算得出。
4.5物料平衡时计算单位:4.5.1固体以重量(公斤)计算。
4.5.2液体以体积(升)计算或重量(公斤)计算。
4.6数据处理4.6.1物料平衡应在合格范围之内,由现场QA确认。
4.6.2凡物料平衡高于或低于合格范围,按《偏差管理规程》处理。
4.6.3质量保证部应定期对各工序收率及产品的总体物料平衡进行回顾,为工艺改进,技术革新及技术标准文件的修订提供参考。
物料平衡与收率管理规程
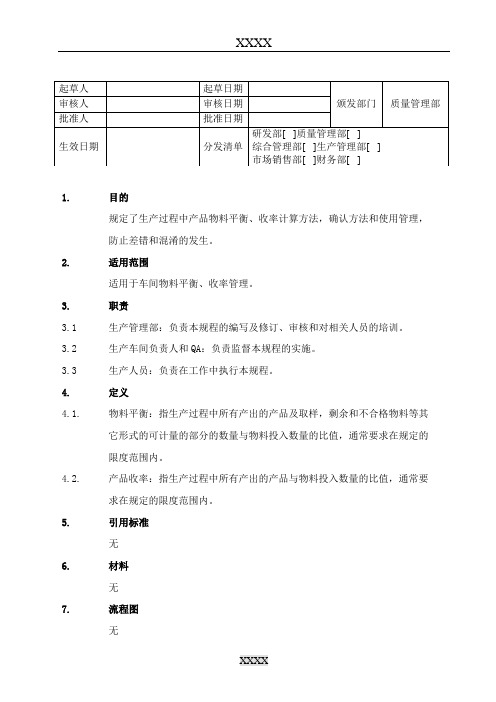
1.目的规定了生产过程中产品物料平衡、收率计算方法,确认方法和使用管理,防止差错和混淆的发生。
2.适用范围适用于车间物料平衡、收率管理。
3.职责3.1 生产管理部:负责本规程的编写及修订、审核和对相关人员的培训。
3.2 生产车间负责人和QA:负责监督本规程的实施。
3.3 生产人员:负责在工作中执行本规程。
4.定义4.1.物料平衡:指生产过程中所有产出的产品及取样,剩余和不合格物料等其它形式的可计量的部分的数量与物料投入数量的比值,通常要求在规定的限度范围内。
4.2.产品收率:指生产过程中所有产出的产品与物料投入数量的比值,通常要求在规定的限度范围内。
5.引用标准无6.材料无7.流程图无8.内容8.1.物料平衡管理8.1.1.物料平衡的计算方法是:本工序产品+取样品+不合格品+剩余物料物料平衡 = ——————————————————×100%本工序投料量8.1.2.物料平衡限度的确定方法8.1.2.1.产品在一批生产结束,统计各工序的物料平衡值,三批确认批生产数据作为临时的物料平衡限度。
8.1.2.2.生产管理部应对同一产品同一岗位上20个正常批次生产的数据进行统计,确定该产品在该工序的物料平衡接受限度。
8.1.2.3.使用20个正常批产品进行统计的方法,可以用于为一个新产品确定物料平衡接受限度,也可以用于对已有的产品物料平衡限度进行检查和修改。
8.1.3.物料平衡限度的确定程序8.1.3.1.生产经理、QA负责共同确定各个产品在各生产工序的物料平衡接受限度。
8.1.3.2.当需要采取对20个正常批产品用统计的方法来确定某一物料接受限度时,生产管理部负责数据的收集和计算,然后由生产经理和QA审核确定。
8.1.3.3.产品在各个生产工序的物料平衡限度,应印在该工序的批记录上。
8.1.4.物料平衡限度的使用当某一生产工序的工作结束后,生产操作人员要按照批记录中的要求,计算物料平衡,并填写在批记录中。
物料平衡管理规程

题目:物料平衡管理规程文件编号:FSD-WI-PM-003页数: 1 /2编制人:编制日期:年月日颁发部门:品保部审核人:审核日期:年月日批准人:批准日期:年月日生效日期:2014年06月01日分发部门:生产部、品保部分发号:1.目的:建立物料的平衡限度核查,掌握生产过程中主要物料收率变化及使用情况,进行严格的收率控制和物料平衡,防止差错和混淆。
2.范围:每个批次产品生产过程的关键工序和关键物料(即A类物料)都要进行物料平衡核查。
3.职责:生产部操作人员对本规程负责、品保部对本规程的实施负监督检查责任。
4.内容:4.1在每个主要工序计算收率、进行关键物料平衡是避免和发现差错与混淆的有效方法之一。
因此,每个品种的批生产记录(批包装记录)都必须明确规定收率和物料平衡的方法。
4.2收率计算公式:收率=实际值/理论值×100%其中:理论值:为按照所用的原料(包装材料)量,在生产中无任何损失或差错的情况下得出的最大数量。
实际值:为生产过程中实际产出量的总和,包括:本工序产出量(包括取样量)和收集的废品量。
4.3在生产过程中如有跑料现象,应及时通知生产部及品保部,并详细记录跑料过程及数量。
跑料数量也应计入物料平衡之中,加在实际值的范围之内。
4.4需进行收率计算的工序为:分装、组装。
4.5物料平衡时,收率计算单位可根据具体情况以体积、数量为单位计算,以简洁、有效为原则。
关键物料包括配制所用原料。
贴签和外包装岗位的物料平衡公式为:领用量=实际使用量+报废量+退回量(或剩余量)。
4.6根据各产品生产工艺,在批记录中规定各产品的物料平衡,各产品收率应在规定范围内才算合格,否则按《异常情况处理报告单》进行处理。
4.7偏差处理:凡收率高于或低于规定范围,应立即贴示“待验”标志,不能递交下到工序,并填写《异常情况处理报告单》,通知生产部经理及品保部,查明原因,在得出合理解释,确认无潜在质量事故后,方可按正常产品处理,并详细记录过程。
物料平衡管理规定
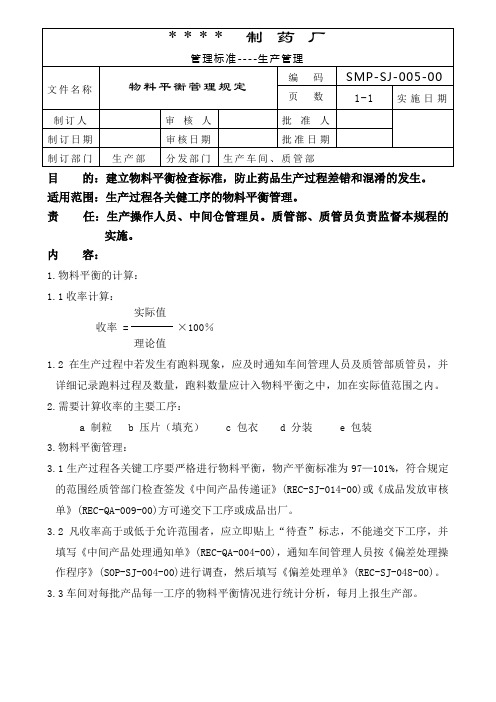
目的:建立物料平衡检查标准,防止药品生产过程差错和混淆的发生。
适用范围:生产过程各关健工序的物料平衡管理。
责任:生产操作人员、中间仓管理员。
质管部、质管员负责监督本规程的实施。
内容:
1.物料平衡的计算:
1.1收率计算:
实际值
收率 = ×100%
理论值
1.2在生产过程中若发生有跑料现象,应及时通知车间管理人员及质管部质管员,并详细记录跑料过程及数量,跑料数量应计入物料平衡之中,加在实际值范围之内。
2.需要计算收率的主要工序:
a 制粒
b 压片(填充)
c 包衣
d 分装
e 包装
3.物料平衡管理:
3.1生产过程各关键工序要严格进行物料平衡,物产平衡标准为97—101%,符合规定的范围经质管部门检查签发《中间产品传递证》(REC-SJ-014-00)或《成品发放审核单》(REC-QA-009-00)方可递交下工序或成品出厂。
3.2凡收率高于或低于允许范围者,应立即贴上“待查”标志,不能递交下工序,并填写《中间产品处理通知单》(REC-QA-004-00),通知车间管理人员按《偏差处理操作程序》(SOP-SJ-004-00)进行调查,然后填写《偏差处理单》(REC-SJ-048-00)。
3.3车间对每批产品每一工序的物料平衡情况进行统计分析,每月上报生产部。
物料平衡审核及管理规程

文件制修订记录1.0目的建立物料平衡的审核及管理规程,掌握生产过程中物料平衡及收率变化,进行严格的物料平衡及收率控制,防止差错和混药。
2.0范围关键岗位的物料平衡计算及审核3.0责任技术开发部部长、车间主任、质量管理部监控员、技术员、班长、操作工4.0管理内容4.1 在每个关键岗位计算收率、进行物料平衡计算是避免或及时发现差错与混药的有效方法之一。
因此,每个品种各关键生产岗位的批生产记录都必须明确规定收率和物料平衡计算方法,以及根据验证结果确定的合格范围限度。
4.2收率及物料平衡计算的基本要求:4.2.1 收率计算:实际值收率= ×100%理论值其中:理论值:按照所用的原料(包装材料)量,在生产中无任何损失或差错的情况下得出的最大数量。
实际值:生产过程中实际产出量。
收率是进行成本核算的重要基础数据。
4.2.2 物料平衡计算:产成品+不合格品+取样量物料平衡率= ×100%理论产品数物料平衡是指生产过程中所有产出可见产品(或中间产品)及其它形式产出与初始物料投入数量的比值。
4.2.3 在生产过程中如有跑料现象,应及时通知车间技术员及质量管理部监控员,并详细记录跑料过程及数量。
4.3 各岗位收率及物料衡算4.3.1 提取工艺各岗位收率及物料衡算4.3.1.1 中药材前处理收率及物料平衡4.3.1.1.1 收率净药材重量中药材前处理收率= ×100%投料总重量4.3.1.2 净药材粉碎岗位:4.3.1.2.1 收率粉碎后药粉重量粉碎收率= ×100%净药材投料量4.3.1.2.2 物料衡算粉碎后药粉重量+废弃量物料平衡率= ×100%净药材投料量4.3.1.3 净药材提取、浓缩岗位:4.3.1.3.1 收率清膏重量收率= ×100%净药材投料量4.3.1.4 膏粉混合岗位:4.3.1.4.1 收率混合后膏粉重量混合收率= ×100%膏粉总投料量4.3.1.4.2 物料衡算混合后膏粉重量+废弃量物料平衡率= ×100%膏粉总投料量4.3.1.5 膏粉干燥岗位:4.3.1.5.1 收率干燥后干粉重量干燥收率= ×100%膏粉总投料量4.3.1.5.2 物料衡算干燥后干粉重量+废弃量物料平衡率= ×100%膏粉总投料量4.3.1.6 粉碎岗位:4.3.1.6.1 收率粉碎后药粉重量粉碎收率= ×100%领入药粉重量4.3.1.6.2 物料衡算粉碎后药粉重量+废弃量物料平衡率= ×100%领入药粉重量4.3.2 制剂各岗位收率及物料衡算4.3.2.1 制粒、干燥岗位:4.3.2.1.1 收率干颗粒重量干颗粒收率= ×100%投料重量4.3.2.1.2 物料衡算干颗粒重量+废弃量物料平衡率= ×100%投料重量4.3.2.2 整粒岗位:4.3.2.2.1 收率整粒后颗粒重量整粒收率= ×100%干燥后颗粒重量4.3.2.2.2 物料衡算整粒后颗粒重量+废弃量物料平衡率= ×100%干燥后颗粒重量4.3.2.3 批混岗位:4.3.2.3.1 收率批混后重量收率= ×100%领入重量4.3.2.3.2 物料衡算批混后重量+废弃量+取样量物料平衡率= ×100%领入重量4.3.2.4 压片4.3.2.4.1 收率压片后合格素片重量压片收率= ×100%领入颗粒重量4.3.2.4.2 物料衡算压片后合格素片重量+取样量+废弃量物料平衡率= ×100%领入颗粒总重量4.3.2.5 包衣岗位:4.3.2.5.1 收率糖衣片总重量×片芯系数包衣收率= ×100%领入片芯总重量4.3.2.5.2 物料衡算糖衣片总重量×片芯系数+废弃量物料平衡率= ×100%领入片芯总重量片芯平均重量片芯系数= ×100%糖衣片平均重量4.3.2.6 胶囊充填岗位:4.3.2.6.1 收率充填后胶囊总重量(1—空心胶囊系数)+尾料量胶囊充填收率= ×100%领入药粉重量4.3.2.6.2 物料衡算充填后胶囊总重量(1—空心胶囊系数)+废弃量+尾料量物料平衡率= ×100%领入药粉重量空胶囊平均重量空心胶囊系数= ×100%充填后胶囊平均重量4.3.2.7 灌封岗位:4.3.2.7.1 收率合格品数量灌封收率= ×100%理论灌封数量4.3.2.7.2 物料衡算合格品数量+不合格品数量+取样量物料平衡率= ×100%理论灌封数量配制量理论灌封数量=理论装量4.3.2.8 灯检岗位4.3.2.8.1 收率合格品数量灯检收率= ×100%领入数量4.3.2.8.2 物料衡算合格品数量+废弃量物料平衡率= ×100%领入数量4.3.2.9 铝塑包装4.3.2.9.1 收率热合后总重量(1—空铝塑板系数)铝塑包装收率= ×100%充填后胶囊重量或糖衣片重量4.3.2.9.2 物料衡算热合后总重量(1—空铝塑板系数)+废弃量物料平衡率= ×100%充填后胶囊重量或糖衣片重量空铝塑板平均重量空铝塑板系数= ×100%成品板平均重量4.3.2.10 成品包装4.3.2.10.1 收率包装产出量成品包装收率= ×100%成品包装理论产量投料量成品包装理论产量=规格4.3.2.10.2 物料衡算产出量+取样量+不合格品数量物料平衡率= ×100%成品包装理论产量4.3.2.11 标签物料衡算使用数+废品数+剩余数物料平衡率= ×100%领用数注:废品数包括已打印批号且未使用的数量。
SMP-P-G012-00物料平衡及产品收率管理规程
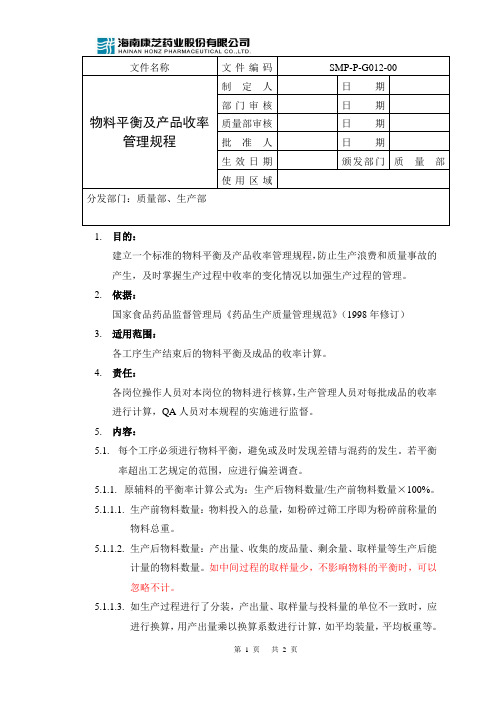
1.目的:建立一个标准的物料平衡及产品收率管理规程,防止生产浪费和质量事故的产生,及时掌握生产过程中收率的变化情况以加强生产过程的管理。
2.依据:国家食品药品监督管理局《药品生产质量管理规范》(1998年修订)3.适用范围:各工序生产结束后的物料平衡及成品的收率计算。
4.责任:各岗位操作人员对本岗位的物料进行核算,生产管理人员对每批成品的收率进行计算,QA人员对本规程的实施进行监督。
5.内容:5.1.每个工序必须进行物料平衡,避免或及时发现差错与混药的发生。
若平衡率超出工艺规定的范围,应进行偏差调查。
5.1.1.原辅料的平衡率计算公式为:生产后物料数量/生产前物料数量×100%。
5.1.1.1.生产前物料数量:物料投入的总量,如粉碎过筛工序即为粉碎前称量的物料总重。
5.1.1.2.生产后物料数量:产出量、收集的废品量、剩余量、取样量等生产后能计量的物料数量。
如中间过程的取样量少,不影响物料的平衡时,可以忽略不计。
5.1.1.3.如生产过程进行了分装,产出量、取样量与投料量的单位不一致时,应进行换算,用产出量乘以换算系数进行计算,如平均装量,平均板重等。
文件名称物料平衡及产品收率管理规程文件编码SMP-P-G012-00 5.1.1.4.由于有收集不到的废品量,以及平均装量的局限性,因此物料平衡有一定的范围,平衡率的范围在工艺规程中明确规定。
5.2.成品收率的计算:(成品数量+取样量)/投料量×100%,计算时,必须将相关单位进行换算。
5.3.每批产品应在生产作业完成后,作物料平衡检查。
做物料平衡的岗位有:粉碎岗位、称量配料岗位、总混岗位、压片岗位、胶囊充填岗位、包装岗位、分装岗位等。
6.培训:6.1.培训时间:0.5小时6.2.培训部门:生产部6.3.受训人员:生产部全体人员、QA检查员。
- 1、下载文档前请自行甄别文档内容的完整性,平台不提供额外的编辑、内容补充、找答案等附加服务。
- 2、"仅部分预览"的文档,不可在线预览部分如存在完整性等问题,可反馈申请退款(可完整预览的文档不适用该条件!)。
- 3、如文档侵犯您的权益,请联系客服反馈,我们会尽快为您处理(人工客服工作时间:9:00-18:30)。
1.目的:
建立一个标准的物料平衡及产品收率管理规程,防止生产浪费和质量事故的产生,及时掌握生产过程中收率的变化情况以加强生产过程的管理。
2.依据:
国家食品药品监督管理局《药品生产质量管理规范》(1998年修订)
3.适用范围:
各工序生产结束后的物料平衡及成品的收率计算。
4.责任:
各岗位操作人员对本岗位的物料进行核算,生产管理人员对每批成品的收率进行计算,QA人员对本规程的实施进行监督。
5.内容:
5.1.每个工序必须进行物料平衡,避免或及时发现差错与混药的发生。
若平衡
率超出工艺规定的范围,应进行偏差调查。
5.1.1.原辅料的平衡率计算公式为:生产后物料数量/生产前物料数量×100%。
5.1.1.1.生产前物料数量:物料投入的总量,如粉碎过筛工序即为粉碎前称量的
物料总重。
5.1.1.2.生产后物料数量:产出量、收集的废品量、剩余量、取样量等生产后能
计量的物料数量。
如中间过程的取样量少,不影响物料的平衡时,可以
忽略不计。
5.1.1.3.如生产过程进行了分装,产出量、取样量与投料量的单位不一致时,应
进行换算,用产出量乘以换算系数进行计算,如平均装量,平均板重等。
文件名称物料平衡及产品收率管理规程文件编码SMP-P-G012-00 5.1.1.4.由于有收集不到的废品量,以及平均装量的局限性,因此物料平衡有一
定的范围,平衡率的范围在工艺规程中明确规定。
5.2.成品收率的计算:(成品数量+取样量)/投料量×100%,计算时,必须将
相关单位进行换算。
5.3.每批产品应在生产作业完成后,作物料平衡检查。
做物料平衡的岗位有:
粉碎岗位、称量配料岗位、总混岗位、压片岗位、胶囊充填岗位、包装岗位、分装岗位等。
6.培训:
6.1.培训时间:0.5小时
6.2.培训部门:生产部
6.3.受训人员:生产部全体人员、QA检查员。