企业精益生产培训(上)
精益生产培训课程
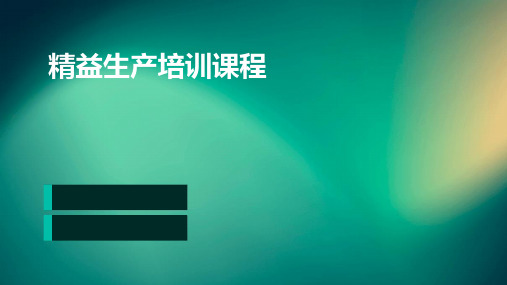
05 精益生产在中国的挑战与 机遇
市场环境与竞争态势
市场竞争激烈
随着中国制造业的快速发展,市 场竞争日趋激烈,企业需要不断 提升生产效率和产品质量以保持 竞争优势。
客户需求多样化
客户需求日益多样化,要求企业 具备快速响应市场变化的能力, 这需要企业引入精益生产理念, 实现个性化定制和柔性生产。
技术创新与人才培养
应用
在产品设计、生产和运营过程中, 绘制价值流图有助于企业了解产品 开发和生产流程中的瓶颈和浪费。
5S管理
定义
5S管理是一种现场管理方法,包 括整理(Sort)、整顿 (Straighten)、清扫
(Sweep)、清洁(Sanitize) 和素养(Sustain)五个方面。
目的
提高工作效率,减少浪费,保证 生产安全。
应用
03
在库存管理中,拉动系统有助于降低库存成本,减少浪费和降
低库存风险。
03 精益生产的实施步骤
明确目标与期望
01
确定企业实施精益生产的目标, 如降低成本、提高效率、优化流 程等。
02
明确企业高层对精益生产的期望 ,确保各部门对目标的理解和认 同。
价值流分析
对企业生产流程进行全面的价值流分 析,包括从原材料采购到产品交付的 整个过程。
质量管理
本田公司注重质量管理,通过严格的质量控制和持续改进,确保产 品的高品质。
创新与研发
本田公司在汽车技术方面不断创新,推出了一系列具有影响力的产 品和技术。
海尔集团
海尔管理模式
海尔集团采用独特的管理模式,注重流程优化、快速响应和持续 改进,实现了高效、低成本的生产和服务。
全球化战略
海尔集团积极推进全球化战略,通过收购、兼并与合作等方式拓 展海外市场,提高国际竞争力。
精益生产班组培训试题一答案

精益班组技能大赛培训测试题单位:班组:姓名:得分:一、单项选择题(每题1分,共10分)1.企业开展精益工作的切入点是(A)。
A 。
现场5S改善B。
作业标准化C。
合理化建议 D 。
TPM工作2。
集团公司现场精益管理揭示板主要管理(C )项内容。
A。
六 B .八 C 。
九 D 。
十3。
(A)是5S活动的核心,也是5S活动的最终目的。
A 。
素养B。
清洁 C.安全 D.三定4. TPM是以(C )为观察点进行思考。
A.制造现场; B。
生产人员; C.设备及物流; D。
产品质量5。
以下不属于看板分类的是(A )A。
管理看板B。
传送看板 C. 生产看板 D. 临时看板6。
精益生产线布置时对设备的要求描述错误的是(D)A。
小型化的设备 B. 设备的管线要整齐并有柔性C。
物品在加工时的出入口要一致化D。
设备要落脚生根7。
推行设备U型布置的要点包括设备布置的流水线化、站立式作业、(A)、人与设备分离。
A。
培养多能工 B. 单能工C。
生产节拍 D. 生产任务8。
控制生产速度的指标是( B)A. 设备B。
生产节拍 C. 库存 D. 材料9.“拉动”一词是指(B )A。
上工序带动下工序B。
下工序带动上工序C。
上、下工序同步进行 D. 以上皆不是10. 流动思想的最终目标是实现( D )A. 零库存B。
拉动式生产 C. 单个流 D. 完全消灭整个生产过程中的停顿二、多项选择题(每题2分,共20分,多选、错选不得分.)1.精益生产的两大支柱是( B C ).A. 6SB. 准时化C。
自働化D。
标准化2.准时化是由哪三种思想观念组成(ABC)A。
生产流程化 B.确定符合人需求数量的节拍时间C。
后道工序领取 D.均衡化生产3.定置管理的类别(ABCDE )A.全系统定置管理B.区域定置管理C.职能部门定置管理 D。
仓库定置管理 E。
特别定置管理4.加强企业基础管理的主要抓手是(A B C).A。
精益化生产B。
精细化管理 C.合理化建议 D .TPM工作5.一表三票包括下列哪项内容(ABCD )A .标准作业票 B.工序能力算定表C。
精益生产培训课件(PPT 72页)
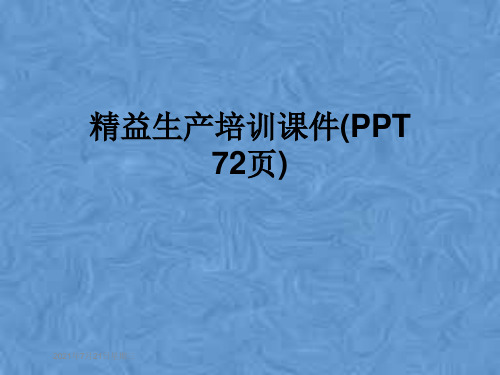
素养
• 定义:人人依规矩行事,工作的每 分钟、每个环节都具备良好的思维 方式。
• 目的:提升人的品质,使每个人都 成为对任何工作都持认真态度 的 优秀管理者和员工。
5S活动开展原则
• 1、自我管理 • 2、持之以恒 • 3、小处着眼
• 实例
返回
推行精益重在坚持
维持
改 善
改善和维持 循环
整顿
• 定义:要的东 西依规矩定位, 摆放整齐,并 明确表明。
• 目的:不浪费 时间寻找需要 的物品
整顿
是对整理后的东西的整顿。
• 定位摆放
物各有位,物在其位
• 定量摆放
过目知数,控制库
• 目视管理
标识清晰,一目了然
• 取用方便
提高效率,保证质量
整顿推行要点
• 1、将整理后的货架、场所空间进行重新规 划使用。
库存的浪费
• 后果: 1、过多的库存,使资金都积压在原材料, 企业的利润有相当一部分被货款利息吃掉了。 2、库存过多,会产生锈蚀变质, 3、增加人去清点、整理
库存的浪费
后果
增加利息负担 占用场地厂房 管理人员增加 入出库的搬运 处锈等工作浪费 长时间失效的浪费
最大的问题: 完全掩盖了工 厂里的问题。
• 精益生产的基本思想 • 2.1 一大目标:低成本、高效率、高
质量地进行生产,消除生产中的一切浪 費 • 2.2两大支柱:准时化、自働化 • 2.3一大基础:改善活動
精益的5项原则
• 1 价值观(Value) 2 价值流(Value Stream) 3 流动(Flow) 4 拉动(Pull) 5 尽善尽美(Perfection)
动作的浪费
• 根源:
精益生产知识培训

整顿
常有的问题
❖ 刚开始大家摆放整齐,可是不知从谁,从什么 时候开始,慢慢又乱了
❖ 识别的手法只有自己看的懂,别人看不懂,识 别手法不统一,有和没有一样
❖ 摆放位置转移,今天换一个地方,明天又换一 个地方,很多人来不及知道
❖ 一次搬入现场的物品太多,摆放的地方都没有
38
整顿
整顿实施方法-油漆作战-
◆ 防呆防错;
◆ 标准化作业;
◆ 智能化、自动化替代人工作业.。。。.
工厂七大浪费之五
➢3.3.6动作的浪费
工厂八大浪费之六
任何不增加产品或服务价值的人员和设备的动作
工厂十二个动作的浪费
1.两手空闲
具体操作中,出现两只手均无事可做的时间段的浪费。
2.单手空闲 3.作业动作停止
具体操作中,出现单只手均无事可做的时间段的浪费。 具体操作中,因操作顺序不合理等原因导致动作出现停顿的浪费。
9.不明技巧
不了解作业技巧而导致的时间浪费 。
10.伸臂动作
超出“经济动作”范围而导致的浪费。
11.弯腰动作
超出“经济动作”范围而导致的浪费。
12.重复/不必要动作
因操作顺序设置不合理,导致重复的或者不必要的各种动作浪费 。
多余动作
◆ 寻找
◆ 收回
◆ 去拿
◆ 行走
消除多余动作的方法
◆ IE工具--5M分析(人、机、料、法、测).
如果撤除职场里不需要的物品的话,就能腾出空间来。
通道及职场应画区域划分线,物品放置场所也应画线。
·区域划分线 把作业区域与通道、车道及通路分开的线
·放置场所线 在地上画出表示放置场所位置的线
要统一具体的颜色、线的幅度及标示的规则
精益生产管理培训(1)

如何提高劳动利用率
提高直接劳动利用率
1. 一人负责多台机器 2. 建立工作标准化 3. 安装自动检测装置
提高间接劳动生产率
消除产品价值链中不能增值的间接活动 后,如库存、检验、返工等环节,它们 所引发的间接成本便会显著降低,劳动 生产率也会提高
案例分析
某企业的生产车间接到任务,要生产一 组产品,需要经过铣、钻、磨、装配和 打包等六道工序,每周生产3200件,所 有这些产品的加工过程相似,需要的工 人相同。该企业每周工作5天,每天工作 8小时。
LP在管理方法上的特点
•组织扁平化,减少非直接生产人员 •生产均衡化和同步化 •零库存和柔性生产 •全面质量管理(TQM),实现零缺陷 •减少任何浪费 •准时生产(JIT)
拉动式准时化生产(JIT)
以最终用户的需求为生产起点 强调物流平衡,追求零库存 看板生产 生产中的节拍可由人工干预,控制 采用拉动式生产,生产中的计划与调度 实际上由各个生产单元自己完成
80units / h 1.78 45units / h
(取2个工作台,尚有生产能力剩余)
铣、钻、磨:这几道工序有长有短,必 须平衡各道工序的劳动利用率。
设置一个微型加工单元,把铣、钻、磨 有机地结合起来,并且只要一个工人完 成这三项操作。
完成这三道工序所需时间为170秒。每小 时可完成21.2单位的产品。
生产指定产品每道工序的单位加工时间:
工序 加工时间(秒)工序 加工时间(秒)
铣(M) 80
装配线1 80
钻(D) 30
装配线2 180
磨(P) 60
包Hale Waihona Puke 30现对其进行精益化改造 经调查: 1.铣、钻、磨床尚有剩余生产能力,因
精益生产管理培训资料

TAKT
0
10
20
30
40
50
60
TAKT
0
10
20
30
40
50
60
TAKT
0
10
20
30
40
50
60
TAKT
0
10
20
30
40
50
60
TAKT
0
10
20
30
40
50
60
TAKT
0
10
20
30
40
50
60
TAKT
0
10
20
30
40
50
60
TAKT
0
10
20
30
40
50
60
TAKT
0
10
20
30
40
50
60
TAKT
0
10
20
30
40
50
60
3、多技能员工
“U”型单元 - 低速生产状态
6
5
4 7
3 8
2 9
10
1
TAKT
0 10 20 30 40 50 60
1. 多技能工一人多岗制
业务内容
1 图纸理解度
2 上下合模
3 钳工基础
4
组装
5
冲压操作
6
缺点对策
7 成型性调整
8
精度调整
。。。。。。
6、以均衡化适应市场的多样化
迅速适应需求变化的生产 准时生产(仅按能销售的数量生产)
每月的适应
每日的适应
精益生产(TPS)培训教材

丰田生产管理方式第一次授课§1—1.企业经营与成本:利润=售价—成本为了提高利润:(1)提高售价 (售价由市場規律决定,提高售价就会卖不出去)「售价=成本+利润」⇒成本主义是行不通的(2)降低成本(成本的三要素:经费、劳务费、材料费)利润=售价—成本(3) 企业不断降低成本的方法彻底的消除浪費,从而降低成本,提高利润。
§1-2.物品製造和成本:* 成本的3要素:材料费、劳务费、管理费*分析成本才能发现哪些是不必要的成本:1.生产出的不良品2.过多的库存3.设备在等待4.不必要的物流5.不必要的作业6.员工在等待等等……*降低成本的方法:①排除浪费②降低原材料采购的价格③降低费用的开支④提高效率⑤缩短生产周期⑥排除人的浪费§ 1-3.什么是丰田生产方式:何谓丰田生产方式:丰田生产方式就是以彻底排除浪费为目标,致力于降低成本,如何做的便宜等一切车间的实践活动的统称。
它是从大批量的生产方式转变为JUST IN TIME(将必要的东西,仅仅是必要的量,在必要的时候进行生产)的生产方式.在最短的生产期间内,挑战由于自动化而实现省人化,到设备的最适化所采用的手法的总称。
§ 1-4.什么是丰田生产方式:丰田生产方式的两大支柱:(1)丰田佐吉翁的带“イ”旁的自动化即:问题显在化的看得見管理+自动化,不是单纯的把人的工作交给机器去做,而是能自动检测不良,发现不良时能自动停止,不向下工程提供不良品.(2)丰田喜一郎的“Just in time”即:“必要的物品、在必要的時候、按必要的量生産”。
* 由大野耐一汇集成“丰田生产方式”§ 1—5.丰田生产方式的目的:1、丰田生产方式的目的:彻底消除浪费为目标,致力于降低成本。
具体地説是追求以下四項為零:①Lead time為0 ―→缩短加工周期(加工时间+停滞时间=工場内的加工周期)②工数的浪费為0―→进行动作和作业的改善③设备的浪费為0―→设备减少+小型化+最适合化④品质的浪费為0―→加工时进行检查,发现不良立即停止例: <加工周期〉加工时间:停滞时间丰田 1 : 300优良企业 1 : 5000亏损企业 1 : 100002、培养发现浪费的眼睛:*发现浪费的第一步就是到现场!!!§ 2-1.车间改善的必要性:§ 2-2.车间的浪费:1、浪费的定义:不能产生利润的行为.首先最重要的是要认识浪费:增加成本的各个要素“一旦认为是浪费,就立刻废除"这种姿态对于在职场里工作的我们来说非常重要*怎样排除动作的浪费:1.明确取放顺序2.明确是左手还是右手拿取方便3.物品不要放得过远4.工具不要迟延§ 2-3.时效分析*标准与改进由于有称为“标准"的比较基准,问题就明确了,由于问题明确了,就有了改进和提高效率·评价1.评价将作业者进行的作业速度与标准速度进行比较,用百分比表示的数值2.评价的目的a、用于标准时间根据时效研究,修正所得的时间值并作成作业标准时间值找到指导作业\改进作业的着眼点具备了效率评价能务,则明白了标准作业速度;明确了指导作业的要点产生向目标靠拢的愿望b、评价训练:观看训练用电影\录像,培养评价工作能力考虑作业的困难程度,是仅用手来进行的作业,还是使用整个身体来进行的作业以100%作业标准速度若感到比标准速度快,则有105,110,120等大数值若感到比标准速度慢,则有95,90,85等小值反复训练\修正自己的基准,争取在一定时间内,对一定的作业能正确评价的工作能力。
精益生产培训资料
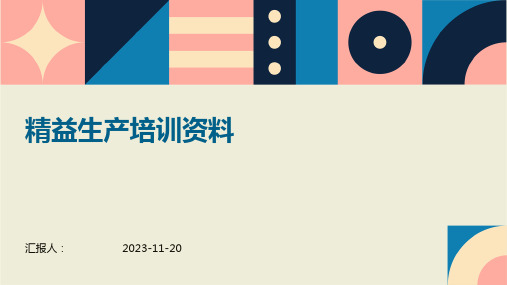
FMEA旨在提前发现并解决潜在问题,防止故障发生,提高产品和过程 的可靠性和安全性。
03
实施步骤
包括识别潜在故障模式、评估故障影响、确定故障优先级、制定纠正措
施和持续改进。
03
精益生产实施步骤
精益诊断与评估
价值流分析
通过对产品生产的整个过程进行 详细的价值流分析,识别出生产 过程中的浪费和不增值环节。
法,实现精益生产的持续提升。
04
成功实施精益生产的关键要素
领导层的支持与承诺
领导层的坚定支持
精益生产的成功实施需要领导层对精益理念和目标的充分理解和坚定支持。领导层应积极倡导精益生 产,为员工树立榜样,推动精益生产的深入实施。
资源承诺
领导层需要为精益生产投入足够的资源,包括人力、物力、财力等,确保精益生产项目的顺利推进。
起源
精益生产起源于20世纪80年代的丰田 生产方式(TPS),由丰田公司创立 。后来逐渐发展成为一种广泛应用于 各种行业和企业的生产管理方法。
精益生产的核心原则
消除浪费
精益生产追求零浪费,通过识别 并消除生产过程中的各种浪费, 如过度生产、等待、运输、不良 品等,提高效率和资源利用率。
持续改进
精益生产强调持续改进,通过员工 参与、团队合作、问题解决等方法 ,不断优化生产过程和管理方式, 实现长期的竞争优势。
现场调研
深入生产现场,了解实际生产状 况,包括设备布局、物料流动、 人员操作等,找出存在的问题和 改进点。
制定精益战略
确定目标
明确精益生产的目标,如提高生产效率、降低成本、缩短交货期等,为制定战 略提供方向。
制定计划
根据诊断与评估结果,制定具体的精益生产实施计划,明确改进项目、时间表 和责任人。
精益生产培训(精选)
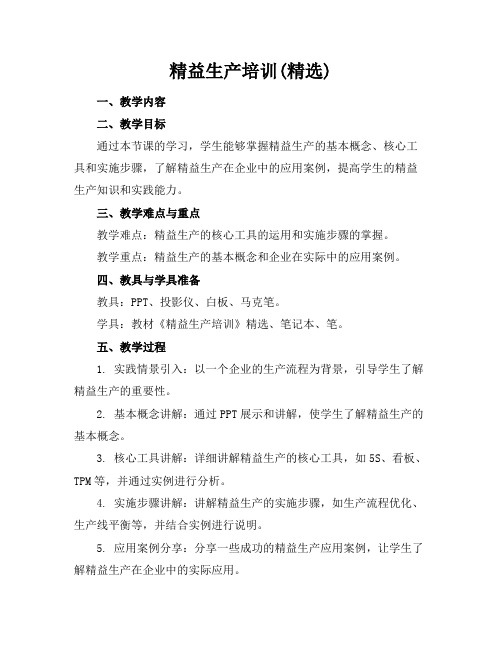
精益生产培训(精选)一、教学内容二、教学目标通过本节课的学习,学生能够掌握精益生产的基本概念、核心工具和实施步骤,了解精益生产在企业中的应用案例,提高学生的精益生产知识和实践能力。
三、教学难点与重点教学难点:精益生产的核心工具的运用和实施步骤的掌握。
教学重点:精益生产的基本概念和企业在实际中的应用案例。
四、教具与学具准备教具:PPT、投影仪、白板、马克笔。
学具:教材《精益生产培训》精选、笔记本、笔。
五、教学过程1. 实践情景引入:以一个企业的生产流程为背景,引导学生了解精益生产的重要性。
2. 基本概念讲解:通过PPT展示和讲解,使学生了解精益生产的基本概念。
3. 核心工具讲解:详细讲解精益生产的核心工具,如5S、看板、TPM等,并通过实例进行分析。
4. 实施步骤讲解:讲解精益生产的实施步骤,如生产流程优化、生产线平衡等,并结合实例进行说明。
5. 应用案例分享:分享一些成功的精益生产应用案例,让学生了解精益生产在企业中的实际应用。
6. 随堂练习:布置一些与精益生产相关的练习题,让学生进行思考和巩固。
7. 作业布置:布置一些有关精益生产的作业,让学生在课后进行深入学习和思考。
六、板书设计板书设计主要包括精益生产的基本概念、核心工具、实施步骤和应用案例等内容,用简洁明了的语言和图示展示给学生。
七、作业设计作业题目:1. 请简述精益生产的基本概念。
2. 请列举出精益生产的核心工具。
3. 请解释一下精益生产的实施步骤。
4. 请分享一个你了解的精益生产在企业中的应用案例。
答案:1. 精益生产是一种以消除浪费为核心的生产方式,旨在提高生产效率和质量,降低成本。
2. 精益生产的核心工具包括5S、看板、TPM、SMED等。
3. 精益生产的实施步骤包括生产流程优化、生产线平衡、标准化作业等。
4. 精益生产在企业中的应用案例可以是某汽车制造公司通过实施精益生产,提高了生产效率和质量,降低了成本。
八、课后反思及拓展延伸课后反思:本节课通过实践情景引入、基本概念讲解、核心工具讲解、实施步骤讲解、应用案例分享等环节,使学生了解了精益生产的基本概念、核心工具和实施步骤,并通过随堂练习和作业布置,让学生巩固所学知识。
精益生产培训
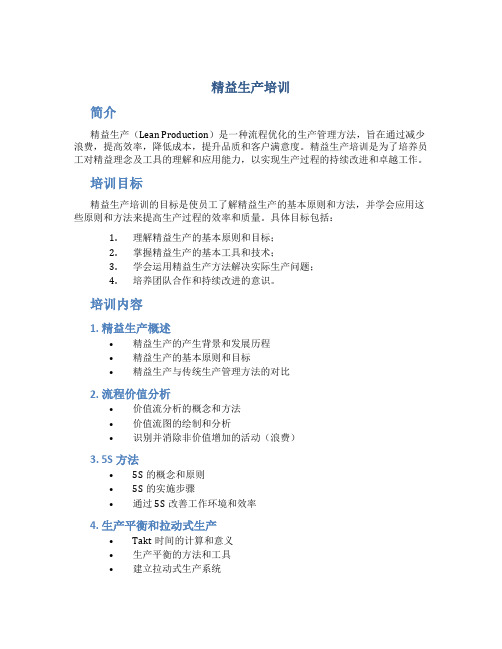
精益生产培训简介精益生产(Lean Production)是一种流程优化的生产管理方法,旨在通过减少浪费,提高效率,降低成本,提升品质和客户满意度。
精益生产培训是为了培养员工对精益理念及工具的理解和应用能力,以实现生产过程的持续改进和卓越工作。
培训目标精益生产培训的目标是使员工了解精益生产的基本原则和方法,并学会应用这些原则和方法来提高生产过程的效率和质量。
具体目标包括:1.理解精益生产的基本原则和目标;2.掌握精益生产的基本工具和技术;3.学会运用精益生产方法解决实际生产问题;4.培养团队合作和持续改进的意识。
培训内容1. 精益生产概述•精益生产的产生背景和发展历程•精益生产的基本原则和目标•精益生产与传统生产管理方法的对比2. 流程价值分析•价值流分析的概念和方法•价值流图的绘制和分析•识别并消除非价值增加的活动(浪费)3. 5S方法•5S的概念和原则•5S的实施步骤•通过5S改善工作环境和效率4. 生产平衡和拉动式生产•Takt时间的计算和意义•生产平衡的方法和工具•建立拉动式生产系统5. 连续流•连续流生产的原理和优势•批量生产与单件生产的对比•通过连续流生产提高生产效率和质量6. 总生产维护•总生产维护的概念和目标•预防性维护和改进性维护的方法•提高设备可靠性和稳定性的措施7. 问题解决和持续改进•PDCA循环的原理和应用•问题解决的方法和工具•培养团队的改进习惯和持续改进文化培训方法精益生产培训采用多种教学方法,包括理论讲座、案例分析、团队讨论和实践演练等。
培训将结合实际生产场景进行,以便员工能够将所学的理论知识应用到实际工作中。
培训还将组织学员参与小组项目,通过解决实际问题来培养团队合作和持续改进的能力。
培训效果评估为了评估培训效果,将在培训结束后进行考核。
考核内容包括理论知识的理解和应用以及解决实际问题的能力。
考核形式包括书面测试、实际操作和小组项目评估等。
通过考核,可以评估培训的有效性,并对培训内容和方法进行改进。
精益生产培训教材(PPT 41页)
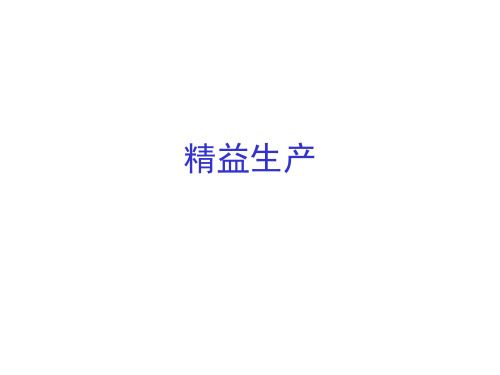
The Job
工 作
Time Fluctuation 时间波动
Job Element Sheet 工作要素单
Element 1 要素 1
Job Element Sheet 工作要素单
Element 2 要素 2
Job Element Sheet 工作要素单
Element 3 要素 3
Job Element Sheet 工作要素单
TIME FLUCTUATION WORKSHEET 时间波开工作单 JOB ELEMENT SHEET 工作要素单 TIME MEASUREMENT SHEET 时间测量单
STANDARDISED OPERATIC THEET 标准作业单
Quality Process Sheet
Department/ Welding 05
精益生产
课程内容
• 定义 • 产生与开展 • 特点与优越性 • 核心内容与生产要素 • 标准化介绍 • 最终目的
什么是精益生产?
• 精益生产是 通过系统结构、人员组织、运行方式和市 场供求等方面的变革,使生产系统能很快适应用户需 求不断变化,并能使生产过程中一切无用、多余的东 西被精简,最终到达包括市场供销在内的生产的各方 面最好的结果。
Worksheet
#
5-140
Opr
WGL
Page__1__ of__1__
Sup
Maint
Eng
3302246
QC QUICK
CHANGE OVER
VISUAL FACTORY
FORD Total Prod.T
F
M
Maint.
P
ERROR PROOFING D
精益生产培训教材

3 Shifts TAKT Time CT = C/O Time = DT = Scrap / Rework = # Operators WIP =
# Material Handlers Max Size 2 Shifts 0 Overtime
分析当前状态 设计将来状态
C/O Time = DT = Scrap = WIP =
课程一: 课程一:
精益生产概论
精益生产的发展历史
福特生产系统 •生产线大量生产 •大批量标准化产品 •工人掌握单一技术 丰田生产系统(TPS) 丰田生产系统(TPS) (TPS •JIT生产(按客户需求品种和数量准时生产) •拉动生产 •强调生产数量和库存数量与市场匹配 •按照客户需求定制产品
精益生产的发展历史
消除浪费的四步骤
第一步: 第一步: 了解什么是浪费 了解什么是浪费
第二步: 第二步: 识别工序中哪里存在浪费 识别工序中哪里存在浪费
第四步: 第四步: 实施持续改进措施 实施持续改进措施, 持续改进措施, 重复实施上述步骤
第三步: 第三步: 使用合适的工具来消除 使用合适的工具来消除 已识别的特定浪费
精益生产既是一种以最大限度地减少企业生产所占用的资 源和降低企业管理和运营成本为主要目标的生产方式,同 源和降低企业管理和运营成本为主要目标的生产方式, 时它又是一种理念,一种文化。实施精益生产就是决心追 时它又是一种理念,一种文化。 求完美的历程,也是追求卓越的过程。 求完美的历程,也是追求卓越的过程。
1985年美国麻省理工学院组织了世界上14个国家的专家、 学者,花费了5年时间,耗资500万美元,对日本等国汽车 工业的生产管理方式进行调查研究后总结出来的生产方式, 在日本称为丰田生产方式。
精益生产培训资料全

部品配置方法变更 只需移动手
原则2 动作要最短距离 皮带拉
制品要到作业者手的近处
原则4 取送材料利用重力和机械力
作业台
滑台
部品 B0X
自动滑入 包装箱内
4.2.4 动作要方便
原则1 动作利用重力和其他力量 利用孔 的大小
大
中
小
原则3 动作的方向和其变换要圆滑
动作的急变时不合适的
二、现场七大浪费
浪费
1. 过量生产 2. 库存 3. 搬运 4. 作业本身 5. 等待 6. 多余动作 7. 不良
2.1 过量生产
?生产多于下游客户所需 Making More Than Needed ?生产快于下游客户所求 Making Faster Than Needed
2.2 在库的浪费
1.2 大量生产方式
20世纪初,美国福特公司创建了世界上第一条汽车 生产流水线:以流水线形式生产大批量、少品种的产品, 以规模效应带动成本降低,并由此带来价格上的竞争力 特点是:
单一化:连续19年只生产黑色T型车 标准化:设备、零件、工装模具、工具 节拍化:按节拍组织生产 专一化:分解为7600工序,每个工人只承担
任何超过加工必 须的物料供应
2.3 搬运的浪费
不符合精 益生产的 一切物料 搬运活动
2.4 作业本身
对最终产品或服务 不增加价值的过程
2.5 作业本身
任何不增加产品或服务价值的 人员 和 设备的动作
2.6 等待的浪费
当两个关联要素间 未能完全同步时 所产生的空闲时间
7、不良的浪费
为了满足顾客的 要求而对产品或服 务进行返工!
4.2 动作分析改善
为了消除动作中的浪费,以如下 4个观点为基准,研究改善方法,做出好的方案。
精益生产管理培训课件(1)

1.2 认识浪费
又有7个零的指标 ➢ 零切换 ➢ 零库存 ➢ 零浪费 ➢ 零故障 ➢ 零停滞 ➢ 零不良 ➢ 零灾害
48
1.3 精益生产方式的基础
必须掌握企业浪费现况 必须有系统的进行精益生产项目 必须掌握各种可用的技术(通过培训) 必须有清楚的目标/指标 必须先有投资和最高领导者支持
45
1.2 认识浪费
亦有专家提出 1. 切换浪费 2. 库存浪费 3. 成本浪费 4. 不良浪费 5. 故障浪费 6. 停滞延误浪费 7. 事故浪费
46
1.2 认识浪费
企业提出更多不同的口号或指标,如 5S零生产 1. 零切换时间 → 多品种生产 2. 零不良率 → 高质量 3. 零浪费 → 低成本 4. 零延误 → 短交期 5. 零工伤 → 安全第一
LEAN这个英文形容词,是瘦,不肥的意思,是描 述一个人体的状态. MANUFA CTURING这个英文名词是制造的意思. LEAN MANUFACTURING是不肥的/瘦的制造. 不肥的/瘦的,就是在形容一个制造是没有 “多
余的” ,“不需要的”组成部份.
7
1.1 精益生产方式概论
思考题(1) 制造MANUFACTVRING与生产PRODUCTION
37
1.1.3 品质控制的工具
矩阵图 矩阵图
箭形图 PDPC图
找出问题的各种原因的相互影响
为控制一个工作项目而绘制的工 作计划表和应变计划表
38
1.2 认识浪费
浪费的定义是“不在预算中的消耗”及“可 以节省的和不必要的消耗”.
浪费英语是WASTE,是不能“产生收益的支 出或成本”或“所支出或成本不单不能带来 收益,而且更带来损失及破坏”.
课程内容 第一天 1.0 精益生产方式概论 1.2 认识浪费 1.3 精益生产方式的基础 1.4 精益生产的导入
- 1、下载文档前请自行甄别文档内容的完整性,平台不提供额外的编辑、内容补充、找答案等附加服务。
- 2、"仅部分预览"的文档,不可在线预览部分如存在完整性等问题,可反馈申请退款(可完整预览的文档不适用该条件!)。
- 3、如文档侵犯您的权益,请联系客服反馈,我们会尽快为您处理(人工客服工作时间:9:00-18:30)。
在三到五年的时间里
生产时间减少 90% 库存减少 90% 生产效率提高 60% 到达客户手中的缺陷减少 50% 废品率降低 50% 与工作有关的伤害降低 50% ……否则,要检查一下你在哪里做错了!
-《精益思想》, Womack & Jones
11
业绩对比
项目 地区 日本
55
停线的责任 领班:生产力改进;成本降低 主管:生产控制,作业标准,质量控制, 培 训,安全, 经理:目标方针,资源配备,系统优化
高层管理 中层管理 基层管理
作业人员
17
The Attitude to Quality 对待质量问题的心态
People CAN and WILL make inadvertent mistakes!
60
北美
6
82
欧洲
6.5
97
生产率(辆/人/年)
质量(缺陷/100辆车)
场地(平方英尺/车/年
库存(8个样件,天) 团队(占劳动力%) 工种轮换(0-无 4-高) 建议数/年/雇员 缺勤率 自动化(组装)
5.7
0.2 69 3.0 61.6 5.0 1.7
7.8
2.9 17 0.9 0.4 111.7 1.2
3
精益思想的要点
“精益”释义:
精益 - 形容词:无肉或少肉,少脂肪或无脂肪, 文体或措词简练
反义词: 肥胖的,多肉的,过重的,不结实的,过分 肥胖的,丰满的,粗短的,肥大的,软的
精益生产: 通过消除企业所有环节上的不增值活动,来达到 降低成本、缩短生产周期和改善质量的目的
4
What is Lean Manufacturing 什么是精益生产-五个原则
Evaluate
实施跟踪
评价推广
22
Quality Is Not Only The Result 质量:不仅仅是“结果面”的质量
“结果面”的质量:客户对产品和服务的满意
度 “过程面”的质量:从订单到发货一切过程的 工作心态和质量
下个工序是 客户!!!
23
To The Defects, I Will Say No!No!!No!!! 对待缺陷,三不政策
5
Life Cycle Cost In Different System 不同系统中的成本
大规模生产模式下的 精益生产系统之产品
产品生命周期成本
生命周期成本
$/ piece
$/piece
销售价格
销售价格
V
产量
V
产量
6
Lean Manufacturing And Automation 精益生产与自动化
20
The Continuous Improvement Tool 改善的工具: SDCA – PDCA
- Plan - Do - Check - Action
改 进 A C A S C D P D
A
C
P
D
A S
C D
- Standardize - Do - Check - Action
21
时 间
2
市场竞争及全球化
Marketing Competition and Globalization
Shorter lead time and on time delivery
快速并准时交货 Grow the mix,special configurations 需求品种增加,特殊定制 Maintain / improve quality and reduce price 不断改进质量及降低销售价格 Total life cycle of product becoming shorter and shorter 产品的生命周期越来越短 No boundary,business globalize village 无国界,业务“地球村”
If one person makes a mistake – ANYONE can! ONE mistake out the door is too many!!
Mistakes CAN be eliminated and MUST be eliminated for us to
become COMPETITIVE!!!
加 工
检 验 及 返 工
成 品 存 储
成 品 发 运
货 款 回 收
制造周期
交付周期
8
精益思想:从增值比率看改善空间
增值比率 =
X 100% 制造周期(Manufacturing cycle time) 增值时间(Value added time)
增值时间:站在客户立场看制造过程中的增值动作和时间 如:改变形状、改变性能、组装、包装等
每年发生两万起药物处方错误
每天发生50起新生婴儿掉在地上的事件
每小时发生两万起支票帐户的错误
一个人出现三万二千次心跳异常
19
Standards Is The Foundation 标准是改进的基础
为什么要标准化? - 代表最好的、最容易的和最 安全的方法 - 提供了一种衡量绩效的手段 - 表现出因果之间的联系
What Shall We Talk…? 内容安排
精益生产系统简介 质量、成本和交货周期 现场管理及班组建设 价值流分析 运行效率 柔性生产单元 看板拉动和精益供应链 精益指标和推行策略
1
Key Points for Manufacturing System 制造系统要点
产品生命周期成本
直接员工 投资
精益的通俗定义
自动化程度
灵巧的双手
全自动
7
LEAN
本 成
间接员工 质量
质量 间接员工
精益思想:关注流程
企业的生产流程包括:订单处理、物料计划、采购下单、 供应商备料、运输、来料检验、存储、搬运、加工、检验 和返工、过程等待、成品库存、发运、货款回收等环节
订 单 处 理 采 购 下 单 供 应 商 备 料 运 输 来 料 检 验 原 料 存 储 搬 运 和 等 待
2
Quality,Cost and Delivery 质量、成本和交货期
对待质量的心态和改进工具
成本的构成及控制手法 流动的物流和信息流是缩短
交货期的保障
生产管理的任务
Quality 质量 Cost 成本
SQDC
Safety 安全、士气 Delivery 交货
16
生产管理者的职责
组长:质量及不合格品的注意;生产线
新的方法 利润 =销售价格 – 成本
29
降低成本的优势:范例
通过管理使制造成本下降20%,而增加114% !
当前状况 增加销售50% 削减支出50% 降低成本20%
销售 成本 毛利
$ 100,000 - 80,000 20,000
zz
25
错误有八种不同的类型
健忘
误解产生的错误
疏忽的错误
迟钝的错误
识别错误
新手错误
缺少标准的错误
蓄意的错误
26
防错十大原理
1. 断根原理 2. 保险原理
6. 隔离原理 7. 复制原理
3. 自动原理
4. 相符原理
8. 层别原理
9. 警告原理 10. 缓和原理
5. 顺序原理
Value 价值
Perfect 完美
站在客户 的立场上
Value Stream 价值流
没有任何事物 是完美的 不断改进
Lean Manufacturing 精益生产
从接单到发货 过程的一切活动
Demand Pull 需求拉动
BTR-按需求生产
象开发的河流 一样通畅流动
Flow 流动
降低成本, 改善质量, 缩短生产周期
DON’T ACCEPT 不接受!
DON’T MAKE 不制造!! DON’T DELIVEfing 差错预防
Preventing or detecting errors at the source FMEAs provide basis for error proofing 在源头预防或探测差错 失效模式分析是差错预防的基础
• Large batches of • Focused on total elimination similar products of waste • Inflexible • Ongoing efforts machinery to improve • Manufacture of Quality, goods by process Productivity, and • 大批量少品种 Responsiveness • 工序式生产 • Recognition of • 设备大难组合 employee abilities • 消除浪费 • 不断改进 • 员工参与
人们可能而且也会在无意中做出错误
如果一个人会犯错误,那么任何人都会犯错误
一个错误出门,带来麻烦多多 为使我们更有竞争力,错误必须消除而且也能消除
18
The Attitude to Quality 对待质量问题的心态
99.9%的正确率意味着什么?
每天北京机场有一次飞机着陆是不安全的
1997 IWeek Survey of 2,900 manufacturers 1998 IWeek Survey of 2,100 additional manufacturers 10
The Competition Advantage Of A Lean Enterprise
精益企业的竞争优势
Agile 敏捷生产组织
• Remove constraints to respond to customer demand through the entire supply pipeline (supplier-customer) • Capable plants linked to lean concepts • 改善整个价值链 • 节点上连着精益工 厂