合成两气氨回收工艺的改进和完善
合成氨装置工艺气余热回收系统存在的问题及改造

合成氨装置工艺气余热回收系统存在的问题及改造陈凤壮【期刊名称】《《天然气化工》》【年(卷),期】2019(044)005【总页数】5页(P102-106)【关键词】合成氨装置; 余热回收; 废热锅炉; 蒸汽预热器【作者】陈凤壮【作者单位】中海石油化学股份有限公司海南东方 572600【正文语种】中文【中图分类】TQ113.2中海石油化学股份有限公司富岛一期拥有一套年产30万t的合成氨装置,1996年建成投产,采用ICI-AMV工艺,主要生产原料为天然气和蒸汽。
装置设计有压力10.8MPa、温度513℃的高压过热蒸汽235t/h,一部分来自工艺气余热回收系统产生,另一部分来自辅助锅炉产生。
工艺气反应热通过余热回收系统对锅炉给水和蒸汽进行加热而回收,该系统由3台高压废热锅炉、2台锅炉给水预热器、1台高压蒸汽预热器和1台高压汽包共7台设备组成(见图1),其整体布局非常紧凑,均由德国BROSIG公司设计和制造。
图1 工艺气余热回收系统设备布置图工艺气余热回收系统总设计蒸汽产量为135t/h,其中1号高压废热锅炉03E001产生高压饱和蒸汽76t/h进入蒸汽预热器03E002内进行初步预热,再送至一段炉对流段蒸汽盘管进一步加热,最终形成高压过热蒸汽汇入高压蒸汽管网。
2018年3月,富岛一期成功对03E001和03E002进行更新改造,两台设备的主要参数见表1。
表1 高压废热锅炉03E001、高压蒸汽预热器03E002设计参数images/BZ_106_1566_1323_1750_1353.pngimages/BZ_106_1761_1328_185 3_1350.pngimages/BZ_106_1910_1323_2126_1353.pngimages/BZ_106_213 6_1328_2231_1350.pngimages/BZ_106_1361_1365_1390_1393.pngimages/ BZ_106_1430_1366_1447_1393.pngimages/BZ_106_1596_1387_1656_1416. pngimages/BZ_106_1787_1387_1846_1416.pngimages/BZ_106_1957_1387_ 2016_1416.pngimages/BZ_106_2125_1387_2185_1416.pngimages/BZ_106_ 1343_1448_1465_1477.pngimages/BZ_106_1557_1464_1632_1486.pngimag es/BZ_106_1634_1460_1693_1489.pngimages/BZ_106_1771_1460_1861_14 89.pngimages/BZ_106_1940_1460_2031_1489.pngimages/BZ_106_2125_14 60_2184_1489.pngimages/BZ_106_1303_1513_1426_1542.pngimages/BZ_1 06_1428_1517_1490_1545.pngimages/BZ_106_1575_1530_2200_1551.pngi mages/BZ_106_1309_1591_1429_1620.pngimages/BZ_106_1432_1595_150 0_1617.pngimages/BZ_106_1602_1595_2188_1616.pngimages/BZ_106_132 5_1655_1447_1684.pngimages/BZ_106_1448_1658_1484_1681.pngimages/ BZ_106_1603_1659_2205_1681.pngimages/BZ_106_1343_1720_1465_1749. pngimages/BZ_106_1531_1724_2216_1746.pngimages/BZ_106_1339_1785_ 1430_1814.pngimages/BZ_106_1431_1786_1470_1814.pngimages/BZ_106_ 1793_1790_1838_1811.pngimages/BZ_106_2090_1789_2170_1818.pngimag es/BZ_106_2180_1785_2218_1818.pngimages/BZ_106_1334_1850_1456_1879.pngimages/BZ_106_1458_1854_1475_1876.pngimages/BZ_106_1684_18 55_2085_1876.png1 存在问题1.1 给水系统跑酸1)跑酸事故的发生。
合成氨氨回收工艺技术改造

综上所述 , 次吹风气余热回收装置技术改 本
造 达到 了预期 目的 , 仅 全 部 回收 了 4台造 气 炉 不 的吹风 气气量 , 实现 了造气 生产 蒸汽 自给 , 明显 还
地 改善 了厂 区 生产 环境 , 现 了吹 风 气 余热 回收 实
装 置 的长周 期 、 安全稳 定运 行
实 际情 况 自行 设计 了 1套氨 回收 装置 。
合成氨 公 司铜 洗 再 生气 、 氨罐 弛放 气 的 回收 装 置 属于 2 0世 纪 7 0年代 小 氮 肥 企 业 的 传 统 回 收 技
术 , 回收率低 ( 3 .7 ) 再 生气 回收 因结垢 氨 仅 74 % , 严重 , 成 回流塔 憋压而 频繁 放空 , 造 回收率 只能达
弛放 气 回收 采用 自冷 方式 , 冷凝 其 中大 部 分 的 氨 以减轻后 工 段 的负 荷 , 回收 的气 氨 送气 氨总 管, 多余 的液 氨送 合 成 氨 冷 器 。氨 自冷 工艺 流程 见图 2 。将 来 自液氨贮 罐 的弛放 气 经过 冷 热交 换 器冷 却降 温后 , 氨冷器进 一 步冷凝 , 送 多余 的液氨 送 合 成氨 冷器 , 回收的气 氨送 气 氨总管 , 冷凝除 去
度 ≥10 o 8 C。随着入 炉蒸汽 温 度 的提 高 和 吹风 阻
表 3 改造 前、 3 h燃煤锅炉运行数据对 比 后 5t /
力的降低 , 吹风 时间减 少 1— , 2s每班 白煤 消耗 下 降 一 。根据 生产 部 门统 计 的数据 , 造 后 余 热 2t 改 回收系统 比改造前 每年 增加 效益 l5万元 以上 5 ( )该 装置 投运 后 , 煤锅 炉负 荷大 幅下 降 , 2 燃 鼓 风机 电流 由原 来 的 30A降为 20A, 汽量 由 2 7 产 原 来的 4 / 2th降 为 3 h 吨氨 烟 煤 消耗 由原 来 3t , / 的 30k 2 g下降 为 20k。3 h锅炉 由原 来 的超 8 g 5t / 负荷运行 变为轻 负荷 运 行 , 锅 炉 长周 期 运 行 奠 为
300kt-a合成氨装置弛放气回收系统优化总结

300kt-a合成氨装置弛放气回收系统优化总结300kt/a合成氨装置弛放气回收系统优化总结摘要:随着合成氨工业的快速发展,合成氨装置弛放气回收系统的优化迫在眉睫。
本文通过对某300kt/a合成氨装置弛放气回收系统的研究和总结,从操作参数的优化、设备的改进、节能减排以及运行维护等方面进行讨论,并提出相应的优化建议。
一、引言合成氨装置是现代化肥生产中重要的工艺装置之一,但由于弛放气中含有大量氨气及其他有害物质,若直接排放到大气中将会造成环境污染。
因此,对于弛放气回收系统的优化具有十分重要的意义。
二、操作参数的优化1. 压力控制:合成氨装置弛放气的压力过高或过低都会导致气体的泄漏或系统的断气现象。
因此,在气体压力的控制上,应该根据装置的实际情况合理设定压力范围,并定期检测和调整。
2. 温度控制:合成氨装置弛放气在高温下容易引起气体的挥发,增加氨气的浓度,从而增加了环境污染的风险。
因此,在温度控制方面,应采取降低弛放气温度的措施,如增加冷却设备的使用。
三、设备的改进1. 弛放罐的改进:合成氨装置中的弛放罐是弛放气回收系统的核心设备,其工作状态直接影响着气体的回收效果。
为了提高回收效率,可以通过优化弛放罐的结构、增加吸附剂和改变操作方式等措施来改进。
2. 管道的改进:管道是装置中气体输送的重要通道,若管道泄漏会导致气体的浪费和环境污染。
因此,合成氨装置中的管道应定期检查,发现问题及时修复,避免漏气现象的发生。
四、节能减排1. 废气热能的回收利用:合成氨装置中产生的废气含有丰富的热能,可以通过热交换等技术手段回收利用,减少能源的消耗。
2. 尾气脱硫装置的优化:合成氨装置弛放气回收系统中,尾气脱硫装置是减少气体污染的关键设备。
通过优化尾气脱硫系统的工艺和运行参数,可以降低排放的二氧化硫等有害气体的含量。
五、运行维护1. 定期检查和维护:合成氨装置中的弛放气回收系统需要定期检查设备的运行情况,及时发现和处理可能存在的问题,提高装置的稳定性和可靠性。
30万合成氨装置(布朗流程)氨回收系统的改造与运行

锦西天然气化工有限责任公司 (简称锦天化 ) 是以辽东湾海底天然气为原料生产化肥的大型企 业 ,其中合成氨装置采用美国布朗公司的深冷净化 工艺 ,尿素装置采用意大利斯纳姆公司氨汽提工 艺 ,生产规模为合成氨 30万 t/ a,尿素 52万 t/ a。氨 回收系统用于处理回收合成回路排放的弛放气和 少量闪蒸气 (即合成回路排放的尾气 ) 。合成回路 排放尾气主要组分为氢氮气 ,另有设计值为 5. 62% 的氨和微量氩气 。排出弛放气的主要目的是避免 氩气等惰性气体在合成回路中过度累积 ,造成氢氮 气合成为氨的合成率下降 ,回路超压 。氨回收系统 将排放尾气中的氢氮气与氨分离 ,氢氮气返回前工 序重新再利用 ,氨送至成品氨中 。氨回收系统运行
( 1) Ammonia absorber can operate under high load with a releasing gas quantity of 5200~10000 m3 / h, the operative flexibility of system is increased; ( 2) Gas out of absorber can reach em ission requirement of ammonia content less than 1000 ×10 - 6 ; ( 3) No entrainment of liquid in the gas out of absorber; ( 4) It can create econom ic benefitof 355 ×104 Yuan RMB / a due to addition of load; ( 5) It can imp rove the siteenvironment. Key words: synthetic ammonia p lant with a capacity of 30 ×104 t / a; releasing gas; ammonia recovery system; ammonia absorber; substance transfer solid tray ( STST) ; technical reformation
合成氨工艺及节能改造对策

合成氨工艺及节能改造对策摘要:合成氨是一种重要的化学原料,广泛应用于农业、化工和能源等领域。
然而,传统的合成氨工艺存在能源浪费和环境污染的问题。
为了提高合成氨工艺的能源利用效率和减少环境影响,需要进行节能改造和技术创新。
本文探讨了合成氨工艺的基本原理,现有的节能改造技术,并提出未来的发展方向。
关键词:合成氨;节能改造;工艺1合成氨工艺的基本原理合成氨的工艺主要包括催化剂反应、压缩、冷却和分离等步骤。
在传统的哈柏-博斯曼工艺中,通过在高温高压下将氮气与氢气催化反应来合成氨。
这个过程需要大量的能量和催化剂,且产生大量的二氧化碳排放。
为了改善工艺的能源效率和环境友好性,需要进行节能改造。
图1为合成氨工艺流程图。
图1合成氨工艺流程图2现有的节能改造技术2.1催化剂改进研发高效的催化剂是提高合成氨工艺能源效率的关键。
近年来,一些新型的催化剂被开发出来,具有更高的催化活性和选择性。
例如,采用过渡金属催化剂的合成氨工艺可以在较低的温度和压力下进行,从而减少能源消耗。
合成氨工艺中存在一些有害物质,如硫化物、氯化物和氧化物等,它们会中毒催化剂,导致催化活性下降【1】。
因此,改进催化剂的抗中毒性能是关键之一。
通过引入抗中毒组分或者改变催化剂的物理和化学性质,可以增强催化剂对有害物质的抵抗能力,延长催化剂的使用寿命。
2.2压缩技术改进在合成氨工艺中,气体的压缩是一个能量密集型的过程。
通过改进压缩机的设计和运行参数,可以减少能源消耗。
例如,采用多级压缩和高效压缩机可以降低压缩过程中的能量损失。
2.3余热回收在合成氨工艺中,有大量的热量会被废气和冷却水带走。
通过利用余热回收技术,可以将废气和冷却水中的热能回收利用,减少能源的浪费。
例如,采用换热器和蒸汽发生器等设备,可以将废气和冷却水中的热量转化为有用的能源。
2.4改进分离技术在合成氨工艺中,需要将产生的氨与未反应的氮气和氢气进行分离。
传统的分离技术消耗大量的能量传统的分离技术消耗大量的能量,例如通过冷凝和吸附等方法进行气体分离。
氨回收系统问题分析及解决对策

效率。惰性气体含量主要是通过调节合成 回路弛
放 气排 放量 控 制 的。进 入合成 回路 的惰 气 大约有 8 % , 随连续 排 出 的 一 小 股 弛 放 气 和减 压 槽 排 4 是 放气 排 出 系 统 , 者 大 约 占合 成 原 料 气 的 4 二 %。
蒿
蠕
弛放气和减压槽排放气汇合后采取 以水作吸收剂 回收氨 , 其他组 分气体返到加氢脱硫系统 和分子
3℃, 7 然后 回到吸 收塔上 部 , 成 整个循 环 。氨 回 完
收系统 工艺 流程 如 图 1 所示 。
去返氢 和弛 放气返 回阀
过程中, 送到氨合成塔 的气体除氢气和氮气外还
含 有少 量氩 气 , 气来 自前 序工 段 , 参 加氨合 成 氩 不 反应 , 但其 含 量 的高 低 直 接 影 响 到 氨 合成 反 应 的
合 成 工 段 的 弛 放 气 和 减 压 槽 排 放 气 ( . MP 、. ̄ 从 吸 收 塔 底 部 进 入 , 塔 顶 喷 36 a42e) 0 与
洒 下 的洗 涤水逆 流接 触 , 中的氨被 水 吸收 , 气 其 尾
化肥装 置 自原 始 开 车 以来 , 回收 系统 运 行 氨 工况一 直未 达 到设 计 要 求 , 收塔 出 口尾 气 氨含 吸
氨 回收 系统 问题 分 析及 解 决对 策
毛 涛联 王 旭 王 文武
( 重庆建蜂 化肥有限公司 , 重庆 , 80 ) 4 6 1 0
摘要
关键词
通 过分析合成回路回收系统 中存在的 问题 , 出氨 回收系统投用 时间长 、 找 尾气 氨含量超高 和无法
弛放 气 CS 3 T塔板 投用方法
量较高, 造成合成氨系统消耗高 , 同时影响一段炉 和分子 筛 的长期 稳定 运行 。另 外每 次开 车氨 回收
氨回收系统技术改造总结
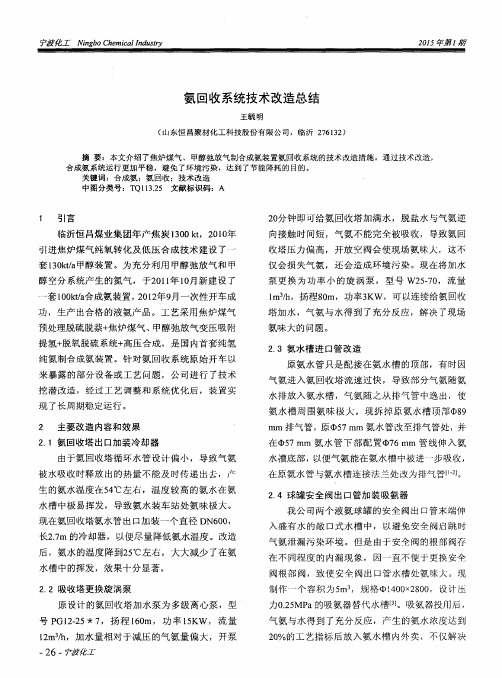
2 . 3 氨水 槽进 口管改造
纯氮 制合 成氨 装 置 。针 对 氨 回 收系 统 原始 开 车 以
来暴 露 的部 分设备 或 工 艺 问题 ,公 司进 行 了技术
挖潜 改造 ,经 过 工艺 调整 和 系统 优 化后 ,装 置实
现 了长周 期稳 定运 行 。
原氨水管只是配接在氨水槽 的顶部 ,有时因
气 氨进 入氨 回收 塔流 速 过快 ,导致 部 分气氨 随氨 水 排放 入氨 水 槽 ,气 氨 随 之从 排气 管 中逸 出 ,使 氨 水 槽 周 围氨 昧 极 人 。现 拆 掉 原 氨水 槽 项 部08 9 mm 排气 管 , 原 05 7 mm 氨水 管 改至排 气 管处 ,并
。
一
套1 0 0 k  ̄ a 合 成氨 装置 , 2 0 1 2 年9 月一 次性 开车 成
l m / h ,扬 程8 0 m,功 率3 KW ,可 以连 续给 氨 回收
塔加 水 ,气 氨 与水 得 到 了充 分 反应 ,解 决 了现场
氨昧 大 的问题 。
功 ,生产 出合格 的液氨 产 品 。工 艺采 用 焦炉 煤 气
被 水 吸收 时释 放 出的 热量 不 能及 时 传递 出去 , 沱
在原 氨水 管 与氨水 槽连 接 法兰 处 改为排气 管l 。 2 . 4 球罐 安全 阀出 口管加 装 吸氨 器 我 公 司两 个液 氨 球罐 的安全 阀出 口管末 端伸
入 盛 有水 的 敞 口式水 槽 中 , 以避 免安 全 阀启跳 时
后 ,氨 水 的温 度 降 N2 5 ℃左 右 ,大 大 减少 了在氨 水槽 中的挥发 ,效 果十 分显 著 。
合成氨生产中两气的合理回收利用

塞的发生;稀氨水浓度大大提高 ,全部 回收利用 , 铜洗再生 自 用氨大部分得到 了回收。铜洗再生气
回收系统 的改造是成 功 的。
改造后每小时 回收稀 氨水 12m ,稀 氨水 . 3 浓度 7 %,每小时回收氨 8 g 4k ,年 回收氨7 4t 3 , 每吨氨价格以 150 0 元计 ,年经济效益约 10 1 万 元;每小 时 回收再生 气 7 0m ,回收后 的再 生 0 3 气作为原料气 ,每吨氨可节约原料煤 3 g 8k ,日 节约原料煤约 1 . t 4 1 ,经济效益显著 。由于不再 有稀 氨水 排放 ,环 境 污 染 问题 得 到 了有 效 遏 制 , 社会效益也相当显著 。
1 2 两气用作燃料的经济分析 . 燃料煤一般以烟煤为主 ,每千克烟煤 的价格
为 01 .8~ 0 2 ,每千 克烟煤的热值为 2 7 .元 252 2 0 J 34 8k 。而两气每立 方米的平均热 值为 9 16k ,两气 的价格在 0 3 元/ 3 9 J .5 m 以上。两者比
~
氨溶气 量是 10m3 8 ,则 合成 弛放气 量 为 27 0 9 m / 。两气合计气量为 62 0 / 。 3h 8 h m3
将回收的两气净化 ( 主要是脱氨和甲烷化) , 作为原料气再返回生产系统使用 。经估算 ,这样
较,1 g 烟煤 的热值是 1 3 k 两气热值的两倍多 , m 而 1k 烟煤 的价格仅为 1m 两气价格 的一半。 g 3 如此看来 ,将两气用作燃料是不经济的。
维普资讯
第 1期
20 0 6年 1月
中 氮
肥
No. 1
M — i d Nir g n u e tl e r g e s S z to e o sF r i z rP o rs e i
合成氨工艺技术的现状及其发展趋势
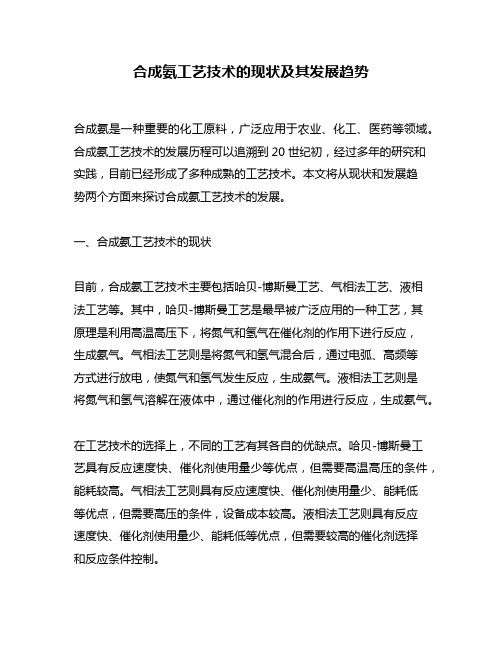
合成氨工艺技术的现状及其发展趋势合成氨是一种重要的化工原料,广泛应用于农业、化工、医药等领域。
合成氨工艺技术的发展历程可以追溯到20世纪初,经过多年的研究和实践,目前已经形成了多种成熟的工艺技术。
本文将从现状和发展趋势两个方面来探讨合成氨工艺技术的发展。
一、合成氨工艺技术的现状目前,合成氨工艺技术主要包括哈贝-博斯曼工艺、气相法工艺、液相法工艺等。
其中,哈贝-博斯曼工艺是最早被广泛应用的一种工艺,其原理是利用高温高压下,将氮气和氢气在催化剂的作用下进行反应,生成氨气。
气相法工艺则是将氮气和氢气混合后,通过电弧、高频等方式进行放电,使氮气和氢气发生反应,生成氨气。
液相法工艺则是将氮气和氢气溶解在液体中,通过催化剂的作用进行反应,生成氨气。
在工艺技术的选择上,不同的工艺有其各自的优缺点。
哈贝-博斯曼工艺具有反应速度快、催化剂使用量少等优点,但需要高温高压的条件,能耗较高。
气相法工艺则具有反应速度快、催化剂使用量少、能耗低等优点,但需要高压的条件,设备成本较高。
液相法工艺则具有反应速度快、催化剂使用量少、能耗低等优点,但需要较高的催化剂选择和反应条件控制。
二、合成氨工艺技术的发展趋势随着科技的不断发展,合成氨工艺技术也在不断地创新和改进。
未来,合成氨工艺技术的发展趋势主要有以下几个方面:1. 绿色化发展随着环保意识的不断提高,绿色化发展已经成为了合成氨工艺技术的重要发展方向。
未来,合成氨工艺技术将更加注重环保和可持续发展,采用更加环保的催化剂和反应条件,减少对环境的污染。
2. 低能耗化发展合成氨工艺技术的能耗一直是制约其发展的重要因素之一。
未来,合成氨工艺技术将更加注重能耗的降低,采用更加节能的反应条件和设备,减少能源的消耗。
3. 高效化发展合成氨工艺技术的效率一直是制约其发展的重要因素之一。
未来,合成氨工艺技术将更加注重效率的提高,采用更加高效的催化剂和反应条件,提高反应速度和产量。
4. 多元化发展合成氨工艺技术的应用领域非常广泛,未来,合成氨工艺技术将更加注重多元化的发展,开发更多的应用领域,满足不同领域的需求。
氨合成工艺方案优化

氨合成工艺方案优化一、背景介绍氨合成工艺是制取氨的关键步骤,也是工业生产中的重要环节。
传统的氨合成工艺存在能量消耗高、催化剂寿命短、产品纯度低等问题,因此需要进行方案优化以提高效率和降低成本。
二、优化方案一:催化剂改进当前常用的氨合成催化剂是铁钼催化剂,具有较高的活性和稳定性。
然而,这种催化剂在高温高压条件下容易失活。
为了解决这个问题,可以考虑以下两个方面的改进措施:1. 催化剂载体选择:优选载体材料,如氧化铝或硅胶,具有较高的比表面积和孔隙度,能够提供更多的活性中心,增强催化剂的吸附能力和稳定性。
2. 催化剂改性:通过添加少量的促进剂(如钾、铜等),可以改善催化剂的抗毒性能和抗结晶性能,延长催化剂的使用寿命。
三、优化方案二:工艺参数调整除了改进催化剂,调整氨合成的工艺参数也可以有效提高合成效率和产品质量。
以下是可以考虑的优化方案:1. 反应温度优化:适当提高反应温度可以提高氨的产率,但过高的温度会导致催化剂失活。
因此,需要在催化剂活性和稳定性之间进行权衡,选择最适合的反应温度。
2. 反应压力控制:在一定范围内增加反应压力可以提高氨的产率,但过高的压力会增加设备投资和运行成本。
因此,需要在经济性和产率之间进行平衡,确定最佳的反应压力。
3. 气体流速调节:合理控制气体流速可以保证反应物料的充分混合和传质,提高反应效率。
同时,需要避免过高的流速造成催化剂颗粒磨损和压降增大。
4. 反应物料配比优化:通过合理调整氮气和氢气的配比,可以提高氨的选择性和产率。
优化配比同时还可以减少废料的产生,降低生产成本。
四、优化方案三:废热利用在氨合成过程中,会产生大量的废热。
合理利用废热可以提高能源利用效率,降低生产成本。
以下是一些常见的废热利用方式:1. 热交换器:将反应过程中产生的废热与进料气体进行换热,减少能量损失。
2. 余热发电:对高温高压废热进行发电,回收部分能量。
3. 蒸汽回收:将废热用于蒸汽产生,替代传统的锅炉加热方式。
合成氨工艺分析及节能改造

合成氨工艺分析及节能改造【摘要】合成氨生产的消耗主要包括原料消耗和燃料消耗两部分,基于降低合成氨工艺能耗的理念,本文对合成氨的工艺流程进行分析,并提出煤化学合成氨的节能措施,以期为相关人员或工程提供参考。
【关键词】合成氨;工艺;节能0引言节能是我国未来发展的重要组成部分,从目前氨在煤合成厂的应用,结合近几年的节能因素,探究煤合成氨的能耗这种新型的节能技术,对我国合成氨工艺的未来发展提供更优化的方法,因此主要对合成氨装置的节能措施进行讨论和分析。
1 合成氨工艺流程分析1.1 原料气处理氨合成过程的第一步是生产富含氮气和氢气的气体。
天然气、重蒸汽、石脑油和焦炉煤气被用作生产氢气的原料,这些原料暴露在高温下,与水蒸气发生化学反应,生成含有一氧化碳和氢气的合成气,这也是产气的主要过程,而气态碳氢化合物和石脑油则用于生产合成气,二次蒸汽是主要用于生产合成气,也是主要工艺。
这种原料制氢的用途另外,制氮的主要原料是空气,空气可以通过物理稀释或其他化学方法得到纯氮低温提取纯氮生产氮气的化学方法是在空气中燃烧碳,空气中的含有的二氧化碳进行有效地释放,从而获得高纯度氮气。
1.2 原料气净化在合成氨工艺中,原料气生产完成后必须对原料气进行净化。
原料气处理分为以下几个过程:一是一氧化碳转化转化,原料气中的一氧化碳含量比较高,所以这些一氧化碳必须全部转化为氢气和二氧化碳。
一氧化碳转化的生产能耗很高,因此需要采取适当的方法降低能耗,控制生产成本,避免能源损失。
二是原料气脱碳脱硫,脱碳脱硫工艺主要采用物理吸收和化学吸收的方法,去除原料气中多余的碳和硫,防止催化剂中毒等问题。
脱碳和脱硫过程中需要对二氧化碳进行高效回收利用,由于二氧化碳是生产碳酸氢胺的重要物质,可以生产纯碱和尿素,因此必须将二氧化碳充分回收并用于减冰,避免浪费资源,节能环保。
此外,干法脱硫和湿法脱硫、脱碳脱硫过程中可采用两种不同的脱硫方法。
尤其是采用干法脱硫时,主要采用固体脱硫剂来达到脱硫目的,但脱硫剂无法回收,因此通常用于精细脱硫作业。
合成氨装置排放性气氨的回收利用及改造情况

气含量高,需要打开惰气冷却器顶部放空阀排掉其 中的惰 气,同时F } 1 于系统 内惰气 含量高导致 出口压
力高 ,大 多数 情 况 下需 现 场 手动 打 开 出 口安 全 阀旁 路 阀泄 压 以满 足工 艺要 求 。这 两 股气 氨 均排 放 至低 温 甲醇 洗 硫化 氢 吸 收塔 顶 部放 空 管 ,严 重污 染 周边 环境 的 大气 质量 。
1 . 4 低 温 甲醇 洗冰 机 系统气 氨排 放
低 温 甲醇洗 冰机在 开 车过 程 中 ,由于系统 内惰
压缩 机 缸 体 内部 的一 级 密封 气 量 3 4 4 m (1 4 l ×2+ 3 l ×2) 。氮 气 易 压缩 并 不 断在 冷 冻 系统 中累积 ,造
成 冷冻 系 统 压 力上 升较 快 ,导致 一 级 氨 闪蒸 槽 安 全 阀在 l 0 5 . J 过 临 界 的 过 程 中 起 跳 。 为 了避 免 氨 闪 蒸
于东北 石油大学化学工程与T艺专业,现从 事技术管
理工作。
2 0 1 7 年. 第6 期
鄢小林.合成氨装置排放性气氨的回收利用及改造情况
表 1 1 O 5 一 J ~级 密封气设计参数
一 3 7一
项目
低 压缸 非驱 动端 低 压缸 驱 动端 高 压缸 非驱 动端
染 环境 。 1 。 2 氨 压缩 机 ( 1 0 5 一 J) 开 车过 程 中的气 氨排 放 1 0 5 一 J 原 轴 端 密 封 为 机 械 密 封 ,机 组 运 行 过 程 中 密 封 油 易 向压 缩 机 缸 体 内 泄 漏 ,影 响 成 品 氨 的
氨回收装置技术改造及运行

统存在的压力波动大、 液位控制不住 、 精馏工况不稳定 、 产品回收困难 常运行时, 氨库压力稳定 , 吸收塔负荷能够 自动调节, 压力和液位基本保 系 等一系列问题得到了全面解决 。 现该装置对全部贮罐气进行气氨回收操 液氨产量明显增加。 ’ 3 蒸氨塔 自动放空调节阀更换膜头。 . 2 根据工艺要求, 当蒸氨塔超压 作 , 时, 系统会 自动放空 , 以保证安全生产。但由于原设计放空位置不合理 , 由改造前的月平均回收液氨 6 吨增加到了 17吨, 4 2 改造获得成功。 在装置实际安装过程中, 我公司对其进行了改进 , 将该放空接至冷凝器 同时由于产量提高, 单位产品较改造前节约蒸汽量 3%以上 , 0 气氨回收 9 %以上。 5 与液氨贮罐平衡管处。 装置投产后, 满足了工艺放空要求, 但由此却造成 率在 9. 现该装置存在的问题是 , 设备露天设置 , 冬季运行时气温低 , 造成大 自动放空调节阀由于背压太小( = . a无法投入使用 。 AP 0 2MP ) 0 一旦系统 蒸汽消耗量明显增加。同时该装置多次出现由于仪表管线冻 出现波动 , 蒸氨 迢压, 便不能迅速做出反应 , 严重威胁着安全生产。迫 量热损失 , 停车检修隋况。 不得已只好降低蒸氨塔操作压力, 低负荷运行 。于是对该 白调阀更换了 结 ,
持 匿定 。
2工艺 流程
来 自氨库的贮罐气, 经减压阀减压后 , 从氨吸收塔的下部人塔 , 与从 塔中段氢回收来的氨水和上段喷淋下来的稀氨水逆流接触 , 气体中的氨 被水吸收生成浓氨水。 经水洗后的尾气经减压阀减压后送人气柜做燃料 图 1 氨 回 收装 置 工 艺 流 程 图 气使用。氨吸收塔中生成的浓氨水凭借压差, 经氨水换热器加热后从蒸 氨塔中部人塔。在蒸氨塔中浓氨水被循环水冷凝成液氨, 一部分回流至 蒸氨塔顶, 其余部分作为产品流人液氨储罐。在蒸氨塔中蒸出氨后的稀 氨水送至氨水换热器 , 加热吸收塔来的浓氨水后 , 经水冷却器进一步冷 却, 经氨水循环泵加压后从氨吸收塔的上段入塔 , 氨水在系统 内循环。 为 保证塔液位正常, 设有稀氨水排放阀。 . 蒸氨塔所需热量由进人再沸 此外, 器的蒸汽提供。工艺流程见图 1 。 3生产 运行 情况及 问题 改进 氨回收装置 自 19 年 1 月投入使用后陆续暴露出一些问题。主 96 0 要表现为:吸收塔压力波动大, 乱 液位控制不住 ;蒸氨塔自动放空由于调 b . 图 2蒸氨塔回凌管改选 节阀膜头背压小 , 不能投入使用 , 限制了生产负荷的提高 ;蒸氨塔塔顶 c . 系统开车后 自动放空投人使用 , 解决了安全隐患 , 生产负荷得以提 回流设计不合理 , 比过大, 回流 产品产量少 , 液氨在塔内循环 , 蒸汽消耗 膜头。 高。限于以上原因, 该装置一直在较低负荷下运行 , 贮罐气仍有大量放 高 。 3 蒸氨塔塔顶回流管线改造。由于蒸氨塔塔顶回流管线设计时无 - 3 空, 不仅浪费了大量气氨, 同时也污染了环境。针对这一情况, 我公司对 液封 , 并且产品液氨引出位置高于回流管近 1 图 2结果造成回流管 米( ) 系统存在的问题进行了改进 , 具体包括以下几个方面。 3 稳定吸收塔压力。氨吸收塔操作压力的稳定是氨回收装置稳定 阻力远小于收氨管阻力。虽然设计 匕 . 1 在回流管上设一截止阀 , 但仍然不 产品液氨少的问题。于是通过对回流管线进 运行的前提条件。我公司氨吸收塔压力控制有两方面调节, 一是氨库来 能解决液氨回流量不稳定, 对原管线进行了改造 , 增加了高度为 1 米 的 U型液封 , . 5 同时将 的贮罐气压力调节 , 二是尾气排放压力调节。 具体操作为, 给定吸收塔操 行核算, 作压力 , 当吸收塔压力低于给定值时, 氨库来贮罐气调节 阀打开向吸收 收氨管线引出位置下移到 U型弯的最低处( 2o 图 ) 改造后 由于液封的作 增大了液氨回流阻力, 液氨产量明显增加。同时由于回流比适合 , 精 塔充压, 反之停 l E 充压; 当去气柜压力低于给定值时, 尾气排放 自调阀打 用, 单位产品能耗大幅度降低。 开, 吸收塔向气柜充压 , 从而保证吸收塔压力稳定。采用这样的控制方 馏工况得到改善, 式, 其弊端在于, 以吸收塔压力稳定为调节原则 , 必然造成氨库压力波 3 尾气排放管线增加放空管。 . 4 氨回收装置 自投运以来 , 一直未能满 主要是由于原设计不合理 , 限制了系统只能在低负荷下运行。 动 。而对于我公 司尿素生产 ,要求 氨库压力必须平稳 ,且不能低 于 负荷运行, 21 a因此为保证氨库去尿素压力稳定 , . , MP 只好将贮罐气压力调节阀改 但还是—个客观原因, 就是氨回收尾气排放设计时只考虑送气柜做燃料 为手动操作, 给生产带来极大不便。 直接表现为吸收塔压力控制不住 , 气使用。但由于我公司实际隋况, 液 气柜过高时, 不允许放空, 目的是保证 空分装置正常生产 , 避免 C H化合物超标 。因而当气柜过高时, — 氨回收 位经常大幅度波动 , 生产无法正常进行。 针对这一隋况, 经过认真分析 , 并吸取操作上的经验 , 对吸收塔压力 只能减负荷运行 , 多余的贮罐气则通过氨库放空放掉 , 致使大量气氨 白 的控制方式进行了改进。将贮罐气压力调节, 取压点位置 由阀后位移至 白浪费。于是对氨回收尾气排放管线进行了改造 , 增加一旁路引至氨库 当气柜高时, 通过该管线将多余尾气放掉, 氨回收装置保证正常生 阀前, 目的是把保证氨库压力平衡作为氨回收装置i 生产的前提。当 放空 。 亍 确保了对全部 氨库压力高于工艺指标时, 阀门打开, 氨库向吸收塔释放贮罐气。 同时将 产。尾气排放管线的改造提高了氨回收装置的操作弹性 , 尾气压力调节阀取压点 由阀后移至阀前, 并更换调节阀膜头, 当吸收塔 贮罐气中的气氨进行回收。 操作压力高于给定值时 , 尾气排放阀打开 , 向气柜排气 , 从而保证吸收塔 4改造效果及问题讨论 我公司氨回收装置 自投运以来经过两年多的调试和技术改造 , 原有 压力稳定。 吸收塔压力控制方式经过改进后 , 收到了明显效果。 当装置正
合成氨含氨废气氨回收技术项目建议书

合成氨生产含氨废气氨回收技术项目建议书一、项目概述随着国家日益高度重视保护生态环境,氮肥行业走清洁生产之路已势在必行!其中,氮肥生产过程的含氨废气氨回收技术已迅速发展,如:华东理工大学的高效化废气氨回收(为下文方便简称HDGXH)专利技术已大量用于几十家氮肥生产企业,取得显著的经济效益和社会效益。
中科院与山东济宁蓝光化工科技有限公司共同开发的“无动力氨回收”(为下文方便简称SDWDL)专利技术也已问世,已在山东海化集团金星化肥厂进行工业化试验并取得很好效果。
上述两项氮肥生产过程含氨废气氨回收技术为氮肥生产企业实现污水零排放,同时为企业带来可观的经济效益和社会效益。
二、国内现状和发展趋势氮肥生产企业要实现污水零排放的环保目标,首要解决好氨氮问题是前提。
国内含氨废气氨回收技术从简单地单元回收制成氨水再转化为碳酸氢铵到综合回收提浓再解吸生产尿素;发展到氨水提浓后蒸氨再冷凝和利用含氨废气多级减压冷凝(SDWDL技术)直接获得液氨。
几种氨回收技术国内氮肥生产企业都有采用,目前多数应用前两种回收技术,其中应用HDGXH此种技术最为普遍。
后两种技术尚处于工业化试验阶段。
从现在了解试验的相关信息情况看,可以预见,后两种技术将共存互补、合二为一,达到低成本、高效益、标本兼治、干净彻底之功效。
并最终取代现存的其它方式的氨回收技术!但就近期而言,HDGXH技术以其投资少、技术成熟的特点仍然是氮肥生产企业可以选择的一项有价值的专利技术。
三、主要内容和创新点(一)HDGXH技术此技术包括氨合成驰放气冷凝分离技术,可使合成驰放气中70%的氨呈液态被回收,而30%的氨以(约320tt)高浓度氨水被完全回收。
放空气高压净氨后氨水直接送合成等压氨回收塔提浓。
铜洗再生气回收技术是采用低阻力高效浮阀塔板,软水一次直流多级等温吸收直接获将近100tt的氨水,再经合成等压氨回收塔提浓为200tt以上的氨水。
(二)SDWDL技术此技术在不需要任何外置动力或能量的情况下,将氨合成驰放气(放空气)中的氨利用下列技术全部转化为液态氨,可直接销售或用于生产尿素产品。
氨气合成工艺参数优化提升收率

氨气合成工艺参数优化提升收率在氨气合成工艺中,参数的优化是提高产率的重要手段。
通过合理调整工艺参数,可以改善反应过程中的能量利用效率、增加反应速率,从而提高氨气的合成收率。
本文将讨论如何优化氨气合成的工艺参数,以达到提升收率的目的。
一、反应温度的优化反应温度是氨气合成中一个关键的参数。
反应速率通常随着温度的升高而增加,但是温度过高会导致反应副产物的生成增加,产率降低。
因此,需要在不产生过多副产物的前提下,选择适当的反应温度来达到最佳收率。
在实际操作中,通过控制反应温度可以实现收率的优化。
首先,可以进行多次实验,逐渐调整反应温度,观察收率的变化。
根据实验结果,确定一个最佳温度范围。
其次,可以利用自动控制系统来实时监测反应温度并进行调整,以保持最佳温度的稳定。
二、反应压力的优化反应压力对氨气合成的收率同样有着重要影响。
一般来说,增加反应压力可以促进气体的吸附和反应物的接触,有利于提高反应速率。
然而,过高的压力会增加设备投资和能耗,不利于工业生产。
因此,在设计合成工艺时需综合考虑投资和能耗等因素,选择适当的反应压力。
通过控制设备的操作参数,可以将压力维持在最佳范围内。
此外,在氨气合成过程中,也可以将反应温度与压力进行联合调节,以进一步提高收率。
三、反应物配比的优化反应物的配比对氨气合成的收率有着重要的影响。
适当的反应物配比可以改善反应的平衡,提高反应速率,从而增加收率。
在实验中,可以通过改变反应物的摩尔比例,观察收率的变化,并找到一个最佳的配比。
在工业生产中,需要密切监测反应物的进料比例,并进行实时调整以维持最佳配比。
同时,定期开展工艺优化研究,进一步改进配比方案,以提高氨气合成的收率。
四、催化剂的选择与用量合适的催化剂对氨气合成过程的效率和收率同样具有重要影响。
选择适当的催化剂可以提高反应速率并改善选择性,从而增加合成氨的收率。
在工业生产中,需要综合考虑催化剂的成本、活性和寿命等因素,选择最合适的催化剂。
合成氨工艺年终总结范文(3篇)

第1篇一、前言合成氨工艺作为我国化工行业的重要组成部分,近年来在我国得到了迅速发展。
为了进一步提高合成氨生产效率、降低生产成本、提高产品质量,我国合成氨行业在技术创新、设备升级、管理优化等方面取得了显著成果。
本篇总结将回顾2021年合成氨工艺的发展情况,分析存在的问题,并对2022年工作进行展望。
二、2021年合成氨工艺发展回顾1. 技术创新(1)合成氨催化剂研究取得突破。
2021年,我国合成氨催化剂研究取得了重要进展,新型催化剂的研制成功降低了合成氨生产成本,提高了合成氨产率。
(2)反应器优化设计。
通过对合成氨反应器进行优化设计,提高了反应器内传热、传质效率,降低了能耗。
(3)循环流化床合成氨技术。
循环流化床合成氨技术具有高效、低能耗、低污染等特点,得到了广泛关注。
2. 设备升级(1)合成塔大型化。
随着合成氨生产规模的不断扩大,合成塔的大型化成为趋势。
2021年,我国成功研制出大型合成塔,提高了合成氨产量。
(2)压缩机性能提升。
为满足合成氨生产需求,压缩机性能得到了显著提升,降低了能耗。
(3)能源回收利用设备。
能源回收利用设备在合成氨生产中的应用,提高了能源利用率,降低了生产成本。
3. 管理优化(1)安全生产管理。
加强安全生产管理,提高了合成氨生产的安全性。
(2)环保管理。
加大环保投入,降低了合成氨生产过程中的污染物排放。
(3)人才培养。
加强人才培养,提高了合成氨生产技术水平。
三、2021年合成氨工艺存在的问题1. 原料供应不稳定。
合成氨生产对原料需求量大,原料供应不稳定导致生产波动。
2. 能耗较高。
合成氨生产过程中的能耗较高,降低了企业盈利能力。
3. 催化剂性能有待提高。
尽管我国合成氨催化剂研究取得突破,但与国际先进水平相比,催化剂性能仍有待提高。
4. 污染物排放仍需降低。
合成氨生产过程中,污染物排放对环境造成一定影响,需进一步降低排放。
四、2022年合成氨工艺工作展望1. 加强原料供应保障。
氨合成工艺优化节能降耗

氨合成工艺优化节能降耗氨是重要的化工原料,广泛应用于农业、化肥、医药等各个领域。
然而,传统的氨合成工艺存在能耗高、环境污染等问题。
因此,优化氨合成工艺,实现节能降耗成为迫切的需求。
本文将探讨氨合成工艺优化的关键技术和方法,并分析其在节能降耗方面的应用前景。
一、氨合成工艺现状氨合成的工艺一般采用哈伯-博仑过程。
该过程通过催化剂促使氮气和氢气发生反应生成氨气,但该工艺存在以下问题:1. 能耗高:哈伯-博仑过程中,氮气和氢气以高温高压的条件下进行反应,能耗较高。
2. 产物纯度低:传统工艺中,合成氨的产物中往往含有大量的惰性气体和杂质,需要经过多道分离与纯化步骤。
3. 环境污染:传统氨合成工艺中使用的催化剂存在重金属的含量,容易造成环境污染。
二、氨合成工艺优化的技术和方法为了优化氨合成工艺,降低能耗、提高产能和产物纯度,我们可以采用以下技术和方法:1. 催化剂的改良:改良催化剂的设计和制备,可以提高催化剂的催化活性和选择性,降低反应温度和压力。
2. 反应条件的优化:通过调节反应温度、压力、气体流速等条件,可以提高催化剂的利用率,减少能量损耗。
3. 原料气体的净化:采用先进的气体净化技术,将原料气体中的杂质和惰性气体去除,提高产物纯度。
4. 催化剂的再生与循环利用:通过催化剂的再生和循环利用,减少催化剂的使用量,降低生产成本。
5. 氨合成流程的整合与改进:通过对氨合成反应流程的整合和改进,优化反应步骤,减少能量损耗。
三、氨合成工艺优化的应用前景氨合成工艺优化在节能降耗方面具有广阔的应用前景。
通过改良催化剂和优化反应条件,可以将反应温度和压力降低至适宜的范围,从而降低能耗,提高能源利用效率。
此外,通过净化原料气体和循环利用催化剂,可以提高产物纯度,减少分离与纯化步骤,进一步降低生产成本。
氨合成工艺优化还可以减少环境污染。
采用环保催化剂和先进的气体净化技术,可以降低重金属的含量,减少对环境的污染。
综上所述,氨合成工艺优化是实现节能降耗的重要途径。
化工合成氨工艺的化学质量平衡优化与控制策略

化工合成氨工艺的化学质量平衡优化与控制策略化学工业是现代社会的重要支柱之一,而合成氨又是化学工业中的重要原料之一。
合成氨广泛应用于农业、化肥、医药和塑料等领域。
在合成氨的生产过程中,实现化学质量平衡优化和控制是提高生产效率和质量的关键。
本文将探讨化工合成氨工艺的化学质量平衡优化与控制策略。
1. 工艺的化学质量平衡优化合成氨的生产过程主要包括氮气和氢气的储备与净化、合成气的合成、合成氨的制备以及产品的分离与制取等环节。
在每个环节中,化学质量平衡优化都起到至关重要的作用。
1.1 氮气和氢气的储备与净化在合成氨的生产中,氮气和氢气是必要的原料。
因此,确保氮气和氢气的质量是化学质量平衡优化的重要环节。
首先,需要对原料进行储备,并通过净化处理去除杂质。
常用的净化方法包括吸附剂和膜分离等技术,以保证氮气和氢气的纯度和质量达到要求。
1.2 合成气的合成合成气是合成氨的关键中间体,其化学质量直接影响着合成氨的质量。
优化氮气和氢气的配比和反应条件是实现合成气化学质量平衡的关键。
通过调节氮气和氢气的流量、压力和温度等参数,确保合成气中氮、氢的比例和气体纯度达到最佳状态,以提高合成氨的产率和质量。
1.3 合成氨的制备合成氨的制备过程是合成氨工艺的核心环节。
在制备过程中,需要控制温度、压力和催化剂的使用量等因素,以保证化学反应的选择性和产率。
此外,在制备过程中,还需要控制反应前后气体的流动速度,以确保化学反应达到平衡,降低副产物的生成。
1.4 产品的分离与制取在合成氨的生产中,需要对合成氨和副产物进行分离与制取。
通过合理选择分离技术,如吸附、蒸馏和结晶等方法,可以实现合成氨与副产物的有效分离,进一步提高合成氨的纯度和质量。
2. 控制策略的优化化学质量平衡优化需要有效的控制策略的支持。
在化工合成氨工艺中,采用先进的控制策略可以提高生产过程的稳定性和灵活性。
2.1 反应温度的控制反应温度是合成氨反应的重要参数之一。
通过精确控制反应温度,可以控制反应速率和副产物的生成。
合成氨尾气全回收实现生产的清洁化

合成氨尾气全回收实现生产的清洁化发布时间:2021-07-28T10:49:02.367Z 来源:《基层建设》2021年第13期作者:张振印郭伟[导读] 摘要:伴随着我国经济的发展,化工企业也有了很大突破。
山东润银生物化工股份有限公司山东泰安 271509摘要:伴随着我国经济的发展,化工企业也有了很大突破。
随着我国化工企业的发展,环保节能是目前化工企业主要发展趋势。
废气利用是节能环保的重要手段之一,对于合成氨生产企业尤其如此。
合成氨生产中可产生大量废气,如氢气、一氧化碳等。
做好废气利用工作能够为企业带来经济效益以及节能效益。
文章在阐述合成氨生产中废气利用的必要性的基础上,从提取甲醇、提取氢气等角度具体分析了合成氨生产中的废气利用,希望为合成氨生产企业的废气利用提供参考意见。
关键词:合成氨;尾气;回收;清洁化引言合成氨装置尾气的综合利用是企业节能降耗和提高经济效益的主要措施,也是企业治理“三废”、实现装置达标排放的首要目标之一。
合成氨尾气的回收利用包括两个部分:一是尾气中氨的回收,二是尾气中氢气的回收。
由于氨、氢回收工艺不同,合成氨尾气的综合利用可选择不同的组合形式。
采用软水洗除氨和变压吸附提氢回收氢气(变压吸附装置释放出来的解吸气送一段炉燃烧)的工艺路线,对合成氨尾气进行综合利用,取得了较好的经济效益和社会效益。
1合成氨生产行业的发展需求在众多行业中,经过调查可知合成氨生产行业属于耗能较高、污染较重的行业,这主要是由于合成氨生产的过程中主要以能源材料为原材料,在合成过程中对能源的需求更大,一般来说,在合成氨生产行业中能源成本的投入要将近生成总成本的七成,从国内能源的消耗来看,约有3%的能源用于合成氨生产行业。
除此之外,合成氨生产中氧气的需求高,在生产过程中易形成二氧化氮、二氧化硫等对环境污染严重的污染气体,从而对环境造成一定的影响。
因此,在当前能源紧缺,环境污染严重的背景下,加强对合成氨生产过程中的废气利用是行业可持续健康发展的保障,帮助合成氨生产企业成功转型为节能、环保企业,以促进企业的转型升级。
- 1、下载文档前请自行甄别文档内容的完整性,平台不提供额外的编辑、内容补充、找答案等附加服务。
- 2、"仅部分预览"的文档,不可在线预览部分如存在完整性等问题,可反馈申请退款(可完整预览的文档不适用该条件!)。
- 3、如文档侵犯您的权益,请联系客服反馈,我们会尽快为您处理(人工客服工作时间:9:00-18:30)。
艺, 这样不仅可减少气氨过剩而开冰机n l ,  ̄s 而且 ' - J 又多 了一种 新产 品 。
改 造后 两气 工艺 见 图 2 。
原 2套装置合成工段均为 1 0 m标塔 0m 0 生产 , 均为满 负荷运行。2 0 05年 9月 1装 置大
修, 合成工段新增 1 只 l 0 m矮塔与 o 0 0m 0 l 0 0 m m标塔并联运行 , 合成装置能力 明显提高 , 合成
2 2套 装置 合成 工段 补气 连通
时调整产品结构来增加收益 , 实现利润最大化。 20 03年 3 , 月 为了适应产 品结 构调整 , 必须 把水 、 、 汽 氨平衡作 为工作重点 , 改造传统 的两气
回收工 艺 ( 图 1 。把 两 气 改 为 产 无 硫 氨 水 工 见 )
2 5 0 严宏 顺 王春 华 ) 250
1 2 套装置合成二出总管连通
l装 置变换 工 段 超 负荷 运 行 , 际 操 作 压 力 实 0 9 P 左右 ; 装置变换工段轻负荷, .0M a 2 实际操
合成 两气 氨 回收 工艺 的改 进和 完善
本 公 司是 生 产 碳铵 、 氨 、 液 甲醇 、 硫 氨水 等 无 产品 的小氮 肥企 业 , 在市 场 经济价 格波 动下 , 随 可
作压力只有 07 P 。在两系统饱和塔前加了 l .5M a 根 D 6 m连通管 , 1装置向 2装置送气 , g5m 由 1 装置变换工段操作压力降至 O 8 P 左右, 装 .5M a 2 置操作压力达 0 8 P .0M a左右, 既减轻 了 l装置 变换工段超负荷运行问题 , 又提高了 2装置变换 工段的生产能力。
塔一进压力降至 2 . P , H 含量 l% , 2 5 0M aC 8 而 系统 合 成 塔 一 进 压 力 达 3 . P , H 含 量 O5M aC l%。将 2 2 套合成工段补充气管道进行连 通 , 由 2装置向 l 装置送气 , 装置合 成塔一进压力升 l 至2 . P , H 含量 l% ; 装置合成塔一进压 65M aC 2 8
维普资讯
2 l
来的 8 3 m改为 内端 8 3 m, = 0m = 5m 外端 6= 8 2 m 铸造时增大筋板根部 的圆角 , m, 避免产生应力 集中现象。
连通管 , 当单系统装置停车检修 , 可以从另一套系 统装置补气充压提前开车。 3 2 套装置 C O 压缩工段一人总管连通 l尿素装置生产尿素能力4 0t 左右, 1 2 d / 而 装置氨及 C O 都有富余 ; 2 尿素装置生 产能力可 达 50t 0 d以上 , 2装置 的氨及 C : / 而 O 不能满足。 将 2套系统 的 C O 压缩 一人总 管用 1 D 20 根 g5
力降至 2 . M )、 l 含量 l% 。在开机台数不 95 1 c{ a 3
变的情 况 下 , 产 N lI /1同时 增 加 补 气 增 H 近 1 1 1 ,
右稀氨水用于水处理再生阴床。 这样公 司 每 天 可收 获 20~ 3 t 2 20t无硫 氨水
l 。 行 2 多来 , 市 场 价 格 高 , 公 司带 了 t运 2 年 因 给
( 安徽 临泉化 工股份 有 限公 司 2 60 陈子 育 张 34 0 优 势互补 充分 发挥 装置 潜力 建)
m m管道连通 , 很好地平衡 了 2套尿素装 置生产
负荷。 4 2 套装置氢回收管道连通 由于公司 2 套装置共用 1 l 00m 气柜, 只 0 0
合成触媒因使用时间不同 , 活性有差异 , 对气体成
姜堰市化肥有限责任公司为年产合成氨 l0 8 k、 t 尿素 30 k 的化 肥生产企业 , 0 t 现有 2套合 成 氨、 尿素生产装置。由于 2 套装 置部分工段装置 能力有差异 , 单套装置运行时, 有的工段超负荷运 行, 有的工段轻负荷运行 。针对这一现状在双系 统之问增加了部分连通管道 , 在充分发挥 2套装 置潜 力上 取得 了很好 的效 果 。 分的要求不尽相同。为解决这一矛盾 , 2套提 将 氢装 置氢 回收管 道连通 , 以双 系统送 气 , 可 基本 可 以满足 2 套装置氢氮比的调节。 使用以上连通管道 , 2套系统 装置得到了 使 很好的互补 , 投入不大 , 却充分发挥了现有装置的 潜力 , 取得了良好的经济效益。 ( 苏省姜堰 市化 肥 有限责 任公 司 江
③ 装配时, 保证 心轴平 面贴实 , 面和 C B平
平面的间隙在 00 0 1 m .5— .0m 。 3 改造效果 目前 我公 司 4台 6 5 M 0型 压缩 了 2 年多, 到现 在为止还没有出现过一级活塞破裂问题。
一
l 炼 - 匝 囵 H 稀 水I 匝 Iq 成 气 圆 氨 - 台 两 精 -
图 1 两气 回 收 工 艺 流 程
改造过程中新增 l 1/ 的小柱塞泵 , 台 h t 给系 统补加软水 , 且水 、 气氨平衡 , 出系统气 体氨含量
合格 。 改造 后 可 得 无 硫 氨 水 1 / 2td和 l / 5td左
维普资讯
2 2
① 氟 放气 放空气
3 咖 n/ ( 0 C 标寿) d lo / 3 o I m
修理或 更换。由于该空 压机排气 温度 接近 10 7
净 氟 塔
℃, 加之气阀与气缸盖配合间隙很小, 排气阀在损 坏时极难从气缸盖中取出。拆卸气阀顺序是先拆