精密和超精密加工技术的发展现状与展望
精密和超精密加工现状与发展趋势
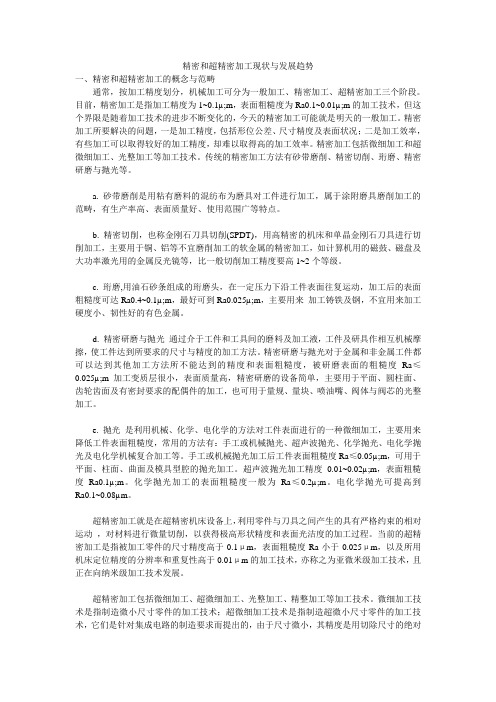
精密和超精密加工现状与发展趋势一、精密和超精密加工的概念与范畴通常,按加工精度划分,机械加工可分为一般加工、精密加工、超精密加工三个阶段。
目前,精密加工是指加工精度为1~0.1µ;m,表面粗糙度为Ra0.1~0.01µ;m的加工技术,但这个界限是随着加工技术的进步不断变化的,今天的精密加工可能就是明天的一般加工。
精密加工所要解决的问题,一是加工精度,包括形位公差、尺寸精度及表面状况;二是加工效率,有些加工可以取得较好的加工精度,却难以取得高的加工效率。
精密加工包括微细加工和超微细加工、光整加工等加工技术。
传统的精密加工方法有砂带磨削、精密切削、珩磨、精密研磨与抛光等。
a. 砂带磨削是用粘有磨料的混纺布为磨具对工件进行加工,属于涂附磨具磨削加工的范畴,有生产率高、表面质量好、使用范围广等特点。
b. 精密切削,也称金刚石刀具切削(SPDT),用高精密的机床和单晶金刚石刀具进行切削加工,主要用于铜、铝等不宜磨削加工的软金属的精密加工,如计算机用的磁鼓、磁盘及大功率激光用的金属反光镜等,比一般切削加工精度要高1~2个等级。
c. 珩磨,用油石砂条组成的珩磨头,在一定压力下沿工件表面往复运动,加工后的表面粗糙度可达Ra0.4~0.1µ;m,最好可到Ra0.025µ;m,主要用来加工铸铁及钢,不宜用来加工硬度小、韧性好的有色金属。
d. 精密研磨与抛光通过介于工件和工具间的磨料及加工液,工件及研具作相互机械摩擦,使工件达到所要求的尺寸与精度的加工方法。
精密研磨与抛光对于金属和非金属工件都可以达到其他加工方法所不能达到的精度和表面粗糙度,被研磨表面的粗糙度Ra≤0.025µ;m加工变质层很小,表面质量高,精密研磨的设备简单,主要用于平面、圆柱面、齿轮齿面及有密封要求的配偶件的加工,也可用于量规、量块、喷油嘴、阀体与阀芯的光整加工。
e. 抛光是利用机械、化学、电化学的方法对工件表面进行的一种微细加工,主要用来降低工件表面粗糙度,常用的方法有:手工或机械抛光、超声波抛光、化学抛光、电化学抛光及电化学机械复合加工等。
精密和超精密加工现状与发展趋势.doc
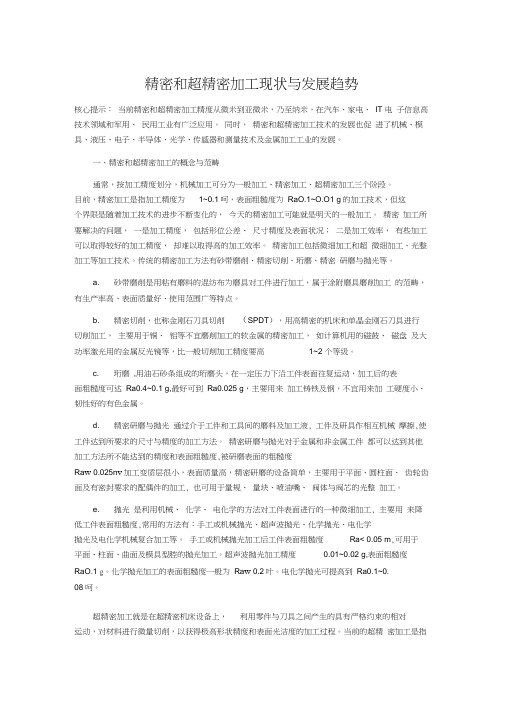
精密和超精密加工现状与发展趋势核心提示:当前精密和超精密加工精度从微米到亚微米,乃至纳米,在汽车、家电、IT 电子信息高技术领域和军用、民用工业有广泛应用。
同时,精密和超精密加工技术的发展也促进了机械、模具、液压、电子、半导体、光学、传感器和测量技术及金属加工工业的发展。
一、精密和超精密加工的概念与范畴通常,按加工精度划分,机械加工可分为一般加工、精密加工、超精密加工三个阶段。
目前,精密加工是指加工精度为1~0.1呵,表面粗糙度为RaO.1~O.O1 g的加工技术,但这个界限是随着加工技术的进步不断变化的,今天的精密加工可能就是明天的一般加工。
精密加工所要解决的问题,一是加工精度,包括形位公差、尺寸精度及表面状况;二是加工效率,有些加工可以取得较好的加工精度,却难以取得高的加工效率。
精密加工包括微细加工和超微细加工、光整加工等加工技术。
传统的精密加工方法有砂带磨削、精密切削、珩磨、精密研磨与抛光等。
a. 砂带磨削是用粘有磨料的混纺布为磨具对工件进行加工,属于涂附磨具磨削加工的范畴,有生产率高、表面质量好、使用范围广等特点。
b. 精密切削,也称金刚石刀具切削(SPDT),用高精密的机床和单晶金刚石刀具进行切削加工,主要用于铜、铝等不宜磨削加工的软金属的精密加工,如计算机用的磁鼓、磁盘及大功率激光用的金属反光镜等,比一般切削加工精度要高1~2 个等级。
c. 珩磨,用油石砂条组成的珩磨头,在一定压力下沿工件表面往复运动,加工后的表面粗糙度可达Ra0.4~0.1 g,最好可到Ra0.025 g,主要用来加工铸铁及钢,不宜用来加工硬度小、韧性好的有色金属。
d. 精密研磨与抛光通过介于工件和工具间的磨料及加工液, 工件及研具作相互机械摩擦,使工件达到所要求的尺寸与精度的加工方法。
精密研磨与抛光对于金属和非金属工件都可以达到其他加工方法所不能达到的精度和表面粗糙度,被研磨表面的粗糙度Ra w 0.025n v加工变质层很小,表面质量高,精密研磨的设备简单,主要用于平面、圆柱面、齿轮齿面及有密封要求的配偶件的加工, 也可用于量规、量块、喷油嘴、阀体与阀芯的光整加工。
超精密加工技术的发展现状
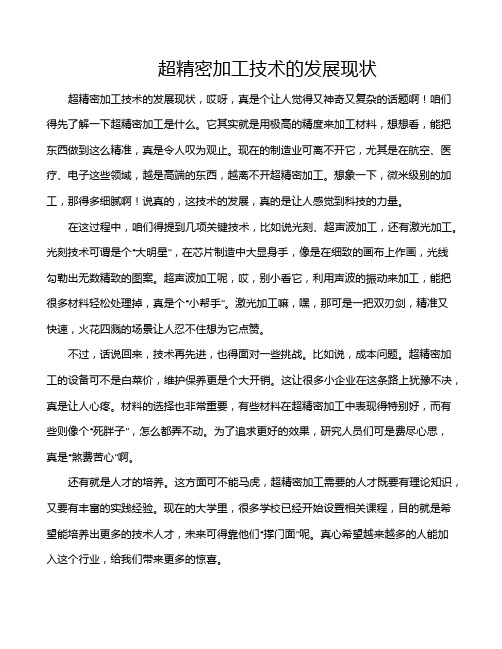
超精密加工技术的发展现状超精密加工技术的发展现状,哎呀,真是个让人觉得又神奇又复杂的话题啊!咱们得先了解一下超精密加工是什么。
它其实就是用极高的精度来加工材料,想想看,能把东西做到这么精准,真是令人叹为观止。
现在的制造业可离不开它,尤其是在航空、医疗、电子这些领域,越是高端的东西,越离不开超精密加工。
想象一下,微米级别的加工,那得多细腻啊!说真的,这技术的发展,真的是让人感觉到科技的力量。
在这过程中,咱们得提到几项关键技术,比如说光刻、超声波加工,还有激光加工。
光刻技术可谓是个“大明星”,在芯片制造中大显身手,像是在细致的画布上作画,光线勾勒出无数精致的图案。
超声波加工呢,哎,别小看它,利用声波的振动来加工,能把很多材料轻松处理掉,真是个“小帮手”。
激光加工嘛,嘿,那可是一把双刃剑,精准又快速,火花四溅的场景让人忍不住想为它点赞。
不过,话说回来,技术再先进,也得面对一些挑战。
比如说,成本问题。
超精密加工的设备可不是白菜价,维护保养更是个大开销。
这让很多小企业在这条路上犹豫不决,真是让人心疼。
材料的选择也非常重要,有些材料在超精密加工中表现得特别好,而有些则像个“死胖子”,怎么都弄不动。
为了追求更好的效果,研究人员们可是费尽心思,真是“煞费苦心”啊。
还有就是人才的培养。
这方面可不能马虎,超精密加工需要的人才既要有理论知识,又要有丰富的实践经验。
现在的大学里,很多学校已经开始设置相关课程,目的就是希望能培养出更多的技术人才,未来可得靠他们“撑门面”呢。
真心希望越来越多的人能加入这个行业,给我们带来更多的惊喜。
说到应用,超精密加工的舞台可大了!像航天器、手术刀、手机的内部零件等等,几乎无处不在。
你看看,航天器上那些复杂的零部件,没有超精密加工,恐怕就飞不起来了!还有手术刀,医生可不能用个普通的刀子,精细的切口直接关系到手术的成功与否,这可是关乎生命的大事啊!而手机的微小零件,哪个能离开超精密加工的加持?所以说,这技术的重要性,不用多说,大家都懂。
精密和超精密加工技术现状和发展趋势

精密和超精密加工技术现状和发展趋势1.引言国际上在超精密加工技术方面处于领先地位的国家有美国、德国和日本发达国家中,美国、日本、德国等在高技术领域(如国防工业、集成电路、信息技术产业等)之所以一直领先,与这些国家高度重视和发展精密、超精密制造技术有极其重要的关系。
由于加工技术水平的发展,精密和超精密加工划分的界限逐渐向前推移,但在具体数值上没有确切的定义。
被加工零件的尺寸精度在 1.0~0.1μm,表面粗糙度Ra在0.1~0.03μm之间的加工方法称为精密加工。
超精密加工当前是指被加工零件的尺寸精度高于0.1μm,表面粗糙度Ra小于0.025μm,以及所用机床定位精度的分辨率和重复性高于0.01μm的加工技术,亦称之为亚微米级加工技术,且正在向纳米级加工技术发展超精密加工技术主要包括:超精密加工的机理,超精密加工的设备制造技术,超精密加工工具及刃磨技术,超精密测量技术和误差补偿技术,超精密加工工作环境条件。
2.发展现状美国是开展研究最早的国家,也是迄今处于世界领先地位的国家。
早在50年代末,由于航天等尖端技术发展的需要,美国首先发展了金刚石刀具的超精密切削技术,并发展了相应的空气轴承主轴的超精密机床,用于加工激光核聚变反射镜、战术导弹及载人飞船用球面、非球面大型零件。
20世纪80年代后期,美国通过能源部“激光核聚变项目”和陆、海、空三军“先进制造技术开发计划”,对超精密金刚石切削机床的开发研究,投入了巨额资金和大量人力,实现了大型零件的微英寸超精密加工。
如美国劳伦斯利弗莫尔国家实验室已经研制出一台大型光学金刚石车床(Large Op tics Diam ond Turn ing Machine, LODTM ), 是一台最大加工直径为1.63m的立式车床,定位精度可达28nm,借助在线误差补偿能力,它已实现了距离超过1m而直线度误差只有±25nm 的加工。
在美国能源部支持下,LLI实验室和Y-12工厂合作,与1983年成功地研制出大型超精密金刚石车床(DTM—3型)。
超精密加工技术在未来机械领域的发展前景概述
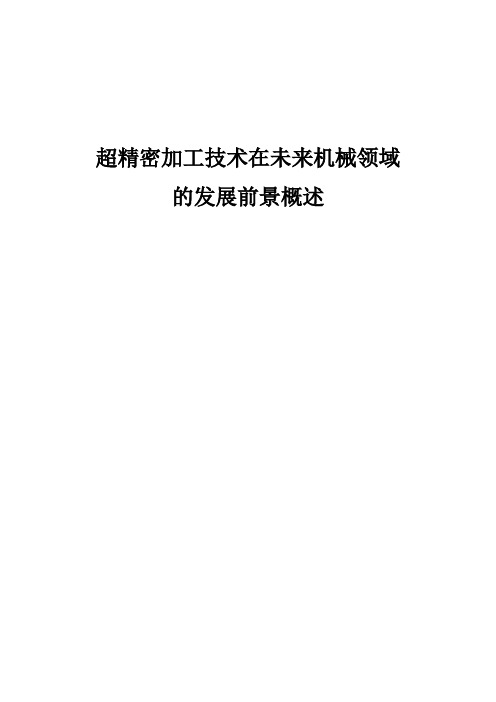
超精密加工技术在未来机械领域的发展前景概述超精密加工技术在未来机械领域的发展前景[前言]近二十年以来机械制造业正以迅猛的发展步伐向精密加工、超精密加工发展,在未来的发展过程中精密加工、超精密加工将成为在国际竞争、市场竞争中取胜的关键技术。
现代制造业之所发要致力于提高加工精度,其主要原因在于提高产品的性能和质量,提高其质量的稳定性和性能的可靠性,促进产品的小型化、功能性强,零件互换性好,产品的装配、调试生产率高,并促进制造装配自动化。
随着制造业的发展,现在的精密机械加工正在从微米、亚微米级工艺发展,在今后的加工中,普通机械加工、精密加工与超精密加工精度可分别达到1μm、0.01μm、0.001μm(即1nm),而且超精密加工正在向原子级加工精度逼进(0.1nm)。
随着极限加工精度的不断提高,为科学技术的发展和进步创造了条件,也为机械冷加工提供了良好的物质手段。
关键词超精密加工发展趋势发展策略后续研发一、引言我们一提到超精密这个词语,就觉得它比较神秘,但跟任何其他复杂的高新技术一样,经过一段时间的熟悉、适应,都会被大众所了解,也就不再是所谓的高科技了,超精密加工也是如此。
实际上,如果拥有超精密的加工设备,并且在其它相关技术和工艺上能匹配,经过一段时间的实践之后,就能很好地掌握它,但这需要一个过程。
超精密加工领域集成了很多IT、机械以及电气控制方面的技术,设备方面的操作和使用也非常复杂,所以,只有在对它有很深的理解之后才能把它用好。
二、正文超精密加工当前是指被加工零件的尺寸和形状精度高于0.1μm,表面粗糙度Ra小于0.025μm,以及机床定位精度的分辨率和重复性高于0.01μm的加工技术,亦称之为亚微米级加工技术,目前正在向纳米级加工技术发展。
超精密加工技术在国际上处于领先地位的国家是美国、英国和日本。
美国是开展超精密加工技术研究最早的国家,也是迄今处于领先地位的国家。
英国的克兰菲尔德精密工程研究所(简称CUPE)享有较高声誉,是当今世界上精密工程的研究中心之一。
超精密加工技术的发展现状与趋势
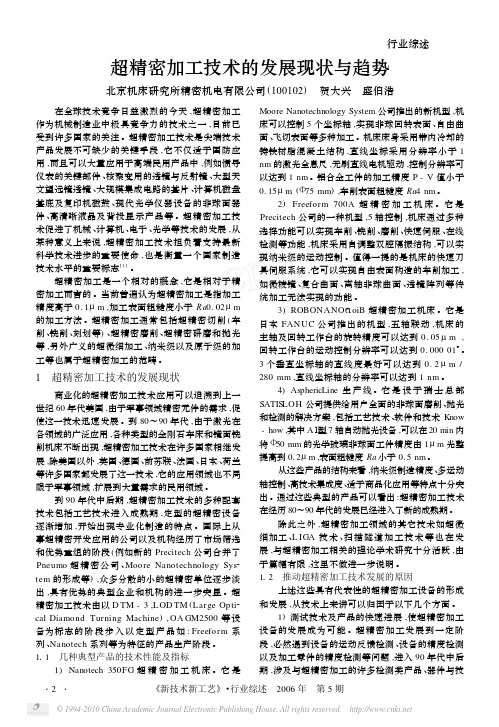
行业综述超精密加工技术的发展现状与趋势北京机床研究所精密机电有限公司(100102) 贺大兴 盛伯浩 在全球技术竞争日益激烈的今天,超精密加工作为机械制造业中极具竞争力的技术之一,目前已受到许多国家的关注。
超精密加工技术是尖端技术产品发展不可缺少的关键手段,它不仅适于国防应用,而且可以大量应用于高端民用产品中,例如惯导仪表的关键部件、核聚变用的透镜与反射镜、大型天文望远镜透镜、大规模集成电路的基片、计算机磁盘基底及复印机磁鼓、现代光学仪器设备的非球面器件、高清晰液晶及背投显示产品等。
超精密加工技术促进了机械、计算机、电子、光学等技术的发展,从某种意义上来说,超精密加工技术担负着支持最新科学技术进步的重要使命,也是衡量一个国家制造技术水平的重要标志[1]。
超精密加工是一个相对的概念,它是相对于精密加工而言的。
当前普遍认为超精密加工是指加工精度高于0.1μm,加工表面粗糙度小于R a0.02μm 的加工方法。
超精密加工通常包括超精密切削(车削、铣削、刻划等)、超精密磨削、超精密研磨和抛光等,另外广义的超微细加工、纳米级以及原子级的加工等也属于超精密加工的范畴。
1 超精密加工技术的发展现状商业化的超精密加工技术应用可以追溯到上一世纪60年代美国,由于军事领域精密元件的需求,促使这一技术迅速发展。
到80~90年代,由于激光在各领域的广泛应用,各种类型的金刚石车床和镜面铣削机床不断出现,超精密加工技术在许多国家相继发展,除美国以外,英国、德国、前苏联、法国、日本、荷兰等许多国家都发展了这一技术,它的应用领域也不局限于军事领域,扩展到大量需求的民用领域。
到90年代中后期,超精密加工技术的多种配套技术包括工艺技术进入成熟期,定型的超精密设备逐渐增加,开始出现专业化制造的特点。
国际上从事超精密开发应用的公司以及机构经历了市场筛选和优势重组的阶段(例如新的Precitech公司合并了Pneumo超精密公司、Moore Nanotechnology Sys2 tem的形成等),众多分散的小的超精密单位逐步淡出,具有优势的典型企业和机构的进一步突显。
精密和超精密加工技术的发展
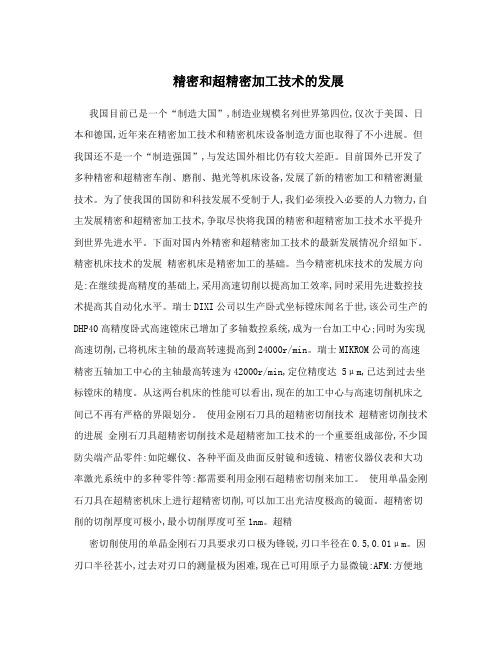
精密和超精密加工技术的发展我国目前已是一个“制造大国”,制造业规模名列世界第四位,仅次于美国、日本和德国,近年来在精密加工技术和精密机床设备制造方面也取得了不小进展。
但我国还不是一个“制造强国”,与发达国外相比仍有较大差距。
目前国外已开发了多种精密和超精密车削、磨削、抛光等机床设备,发展了新的精密加工和精密测量技术。
为了使我国的国防和科技发展不受制于人,我们必须投入必要的人力物力,自主发展精密和超精密加工技术,争取尽快将我国的精密和超精密加工技术水平提升到世界先进水平。
下面对国内外精密和超精密加工技术的最新发展情况介绍如下。
精密机床技术的发展精密机床是精密加工的基础。
当今精密机床技术的发展方向是:在继续提高精度的基础上,采用高速切削以提高加工效率,同时采用先进数控技术提高其自动化水平。
瑞士DIXI公司以生产卧式坐标镗床闻名于世,该公司生产的DHP40高精度卧式高速镗床已增加了多轴数控系统,成为一台加工中心;同时为实现高速切削,已将机床主轴的最高转速提高到24000r/min。
瑞士MIKROM公司的高速精密五轴加工中心的主轴最高转速为42000r/min,定位精度达5μm,已达到过去坐标镗床的精度。
从这两台机床的性能可以看出,现在的加工中心与高速切削机床之间已不再有严格的界限划分。
使用金刚石刀具的超精密切削技术超精密切削技术的进展金刚石刀具超精密切削技术是超精密加工技术的一个重要组成部份,不少国防尖端产品零件:如陀螺仪、各种平面及曲面反射镜和透镜、精密仪器仪表和大功率激光系统中的多种零件等:都需要利用金刚石超精密切削来加工。
使用单晶金刚石刀具在超精密机床上进行超精密切削,可以加工出光洁度极高的镜面。
超精密切削的切削厚度可极小,最小切削厚度可至1nm。
超精密切削使用的单晶金刚石刀具要求刃口极为锋锐,刃口半径在0.5,0.01μm。
因刃口半径甚小,过去对刃口的测量极为困难,现在已可用原子力显微镜:AFM:方便地进行测量。
精密超精密发展趋势
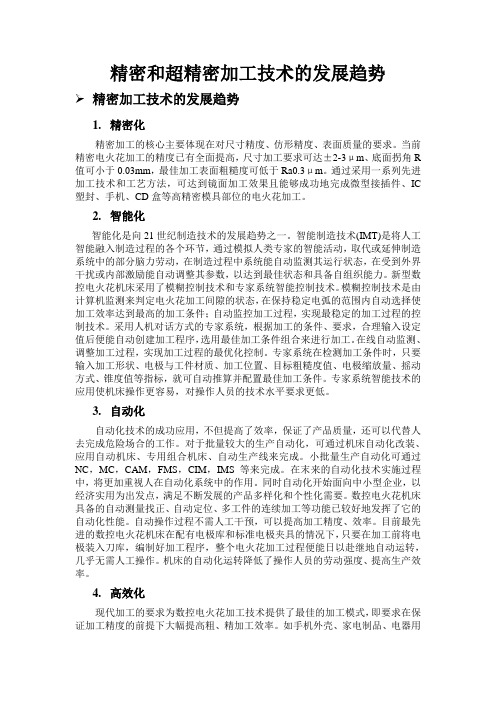
精密和超精密加工技术的发展趋势精密加工技术的发展趋势1.精密化精密加工的核心主要体现在对尺寸精度、仿形精度、表面质量的要求。
当前精密电火花加工的精度已有全面提高,尺寸加工要求可达±2-3μm、底面拐角R 值可小于0.03mm,最佳加工表面粗糙度可低于Ra0.3μm。
通过采用一系列先进加工技术和工艺方法,可达到镜面加工效果且能够成功地完成微型接插件、IC 塑封、手机、CD盒等高精密模具部位的电火花加工。
2.智能化智能化是向21世纪制造技术的发展趋势之一。
智能制造技术(IMT)是将人工智能融入制造过程的各个环节,通过模拟人类专家的智能活动,取代或延伸制造系统中的部分脑力劳动,在制造过程中系统能自动监测其运行状态,在受到外界干扰或内部激励能自动调整其参数,以达到最佳状态和具备自组织能力。
新型数控电火花机床采用了模糊控制技术和专家系统智能控制技术。
模糊控制技术是由计算机监测来判定电火花加工间隙的状态,在保持稳定电弧的范围内自动选择使加工效率达到最高的加工条件;自动监控加工过程,实现最稳定的加工过程的控制技术。
采用人机对话方式的专家系统,根据加工的条件、要求,合理输入设定值后便能自动创建加工程序,选用最佳加工条件组合来进行加工。
在线自动监测、调整加工过程,实现加工过程的最优化控制。
专家系统在检测加工条件时,只要输入加工形状、电极与工件材质、加工位置、目标粗糙度值、电极缩放量、摇动方式、锥度值等指标,就可自动推算并配置最佳加工条件。
专家系统智能技术的应用使机床操作更容易,对操作人员的技术水平要求更低。
3.自动化自动化技术的成功应用,不但提高了效率,保证了产品质量,还可以代替人去完成危险场合的工作。
对于批量较大的生产自动化,可通过机床自动化改装、应用自动机床、专用组合机床、自动生产线来完成。
小批量生产自动化可通过NC,MC,CAM,FMS,CIM,IMS等来完成。
在末来的自动化技术实施过程中,将更加重视人在自动化系统中的作用。
精密与特种加工的发展现状与技术展望

精密与特种加工的发展现状与技术展望班级:姓名:学号精密与特种加工的发展现状与技术展望精密与特种加工的发展现状精密加工是指加工精度和表面质量达到极高精度的加工工艺,通常包括精密切削加工和精密磨削加工,加工精度的不断提高对提高机电产品的性能、质量和可靠性,提高装配效率等都有至关重要的作用。
精密和超精密加工已成为当前国际经济竞争的关键技术。
精密工程,微米工程和纳米技术已成为世界技术的制高点,是现代制造技术的前沿,也是明天技术的基础特种加工是将电能、热能、光能、声能和磁能等物理能量或其组合乃至机械能组合直接施加到被加工的部位上,从而实现材料去除的加工方法,也被称为非传统加工技术。
近半个多世纪以来,相继出现了数十种特种加工方法,如电解加工、超声波加工、放电成型加工、激光加工、电子束加工等。
特种加工在难加工材料加工、磨具及复杂面加工、、零件精细加工等领域已成为重要的加工方法或仅有的加工方法。
随着航空航天、核能热能以及微电子工业的发展,产品向高精度、高速度、耐高温、耐高压、耐腐蚀、大功率、小型化和高可靠性方向发展,零件的特殊结构和新材料的应用对制造业提出了更高的要求,特种加工作为跨世纪的先进制造技术的重要组成部分将在21世纪人类社会进步及我国现代化建设中发挥重大作用。
精密加工精密、超精密切削加工所谓精密加工是指加工精度和表面质量达到极高程度的加工工艺。
目前,在工业发达的国家中,一般工厂能掌握的加工精度是1微米,精密工程正在向其终极目标—原子级精度逼近,也就是实现“移动原子”。
精密加工总是与高加工成本联系在一起,在过去它主要应用于军事、航空航天等部门。
近十几年来,随着科学技术发展和人们生活水平的提高,精密加工的产品已经入人民生活的各个领域,工业发达国家已将精密加工机床直接用于产品零件的精密加工,产生了显著的经济效益。
正是精密加工具有优良的特性,因此得到了世界各地的高度重视。
我国必须大力发展精密加工技术,使其为我国的国民经济创造出巨大的经济效益。
第一章 精密和超精密加工技术及发展展望要点

精密与超精密加工技术概述
◆精密加工 —— 在一定的发展时期,加工精度和表面质量 达到较高程度的加工工艺。
超精密加工 —— 在一定的发展时期,加工精度和表面质 量达到最高程度的加工工艺。
◆瓦特改进蒸汽机 —— 镗孔精度 1mm 20 世纪 40 年代 —— 最高精度 1μm 20 世纪 末 —— 精密加工:≤0.1μm,Ra ≤0.01μm(亚微米加工) 超精密加工:≤ 0.01μm ,Ra≤ 0.001μm(纳米加工)
◆微细加工 —— 微小尺寸的精密加工 超微细加工 ——微小尺寸的超精密加工
几种典型精密零件的加工精度
零件 激光光学零件
多面镜 磁头 磁盘 雷达导波管 卫星仪表轴承 天体望远镜
加工精度 形状误差 0.1μm 平面度误差 0.04μm 平面度误差 0.04μm 波度 0.01 ~0.02μm 平面度垂直度误差 < 0.1μm 圆柱度误差 <0.01μm 形状误差 < 0.03μm
• 超精密加工的对象
– 有色金属及合金 – 硬脆材料 – 黑色金属 – 复合材料
中小型精密零件的加工精度
加工零件 (μm)
激光光学零件 磁头 多面镜 磁盘 磁盘 非球面模具
Ra (μm)
0.01~0.006 0.02 0.01~0.02 0.01~0.004 0.01~0.004 0.01
形状精度
0.1
平面度 0.04 平面度 0.04 波度0.02~0.01 波度0.02~0.01
1~0.3
超精密加工的设备
• 美国LLL实验室的 DTM-3、LODTM超 精密金刚石车床
• 英国Cranfield的OAGM2500超精密金 刚石车床
精密和超精密加工技术的新进展
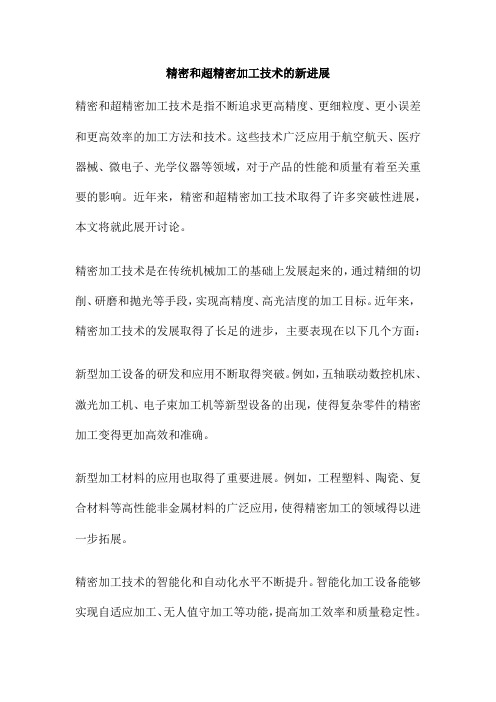
精密和超精密加工技术的新进展精密和超精密加工技术是指不断追求更高精度、更细粒度、更小误差和更高效率的加工方法和技术。
这些技术广泛应用于航空航天、医疗器械、微电子、光学仪器等领域,对于产品的性能和质量有着至关重要的影响。
近年来,精密和超精密加工技术取得了许多突破性进展,本文将就此展开讨论。
精密加工技术是在传统机械加工的基础上发展起来的,通过精细的切削、研磨和抛光等手段,实现高精度、高光洁度的加工目标。
近年来,精密加工技术的发展取得了长足的进步,主要表现在以下几个方面:新型加工设备的研发和应用不断取得突破。
例如,五轴联动数控机床、激光加工机、电子束加工机等新型设备的出现,使得复杂零件的精密加工变得更加高效和准确。
新型加工材料的应用也取得了重要进展。
例如,工程塑料、陶瓷、复合材料等高性能非金属材料的广泛应用,使得精密加工的领域得以进一步拓展。
精密加工技术的智能化和自动化水平不断提升。
智能化加工设备能够实现自适应加工、无人值守加工等功能,提高加工效率和质量稳定性。
超精密加工技术是指比精密加工技术更为精细、精确的加工方法和技术。
随着科技的不断进步,超精密加工技术的应用越来越广泛,主要包括以下几个方面:超精密加工技术广泛应用于微电子领域。
微电子产业对于芯片的精度和光洁度要求极高,超精密加工技术能够实现高精度、高效率的微米级加工,对于提升微电子产业的发展水平和竞争力具有重要意义。
超精密加工技术在光学仪器领域也有着广泛的应用。
光学仪器对于透镜、反射镜等光学元件的精度和表面质量要求极高,超精密加工技术能够实现高精度、高稳定性的光学元件加工,对于提高光学仪器的性能和精度具有重要作用。
再次,超精密加工技术在航空航天领域也有着重要的应用。
航空航天领域对于零件的精度和可靠性要求极为严格,超精密加工技术能够实现高精度、高稳定性的零件加工,对于提升航空航天领域的产品质量和性能具有重要意义。
近年来,精密和超精密加工技术的研究和应用不断取得新的进展,在新型加工设备、新型加工材料和智能化加工等方面都取得了重要突破。
精密和超精密加工现状与发展趋势.doc

精密和超精密加工现状与发展趋势核心提示:当前精密和超精密加工精度从微米到亚微米,乃至纳米,在汽车、家电、IT电子信息高技术领域和军用、民用工业有广泛应用。
同时,精密和超精密加工技术的发展也促进了机械、模具、液压、电子、半导体、光学、传感器和测量技术及金属加工工业的发展。
一、精密和超精密加工的概念与范畴通常,按加工精度划分,机械加工可分为一般加工、精密加工、超精密加工三个阶段。
目前,精密加工是指加工精度为1~0.1μm,表面粗糙度为Ra0.1~0.01μm的加工技术,但这个界限是随着加工技术的进步不断变化的,今天的精密加工可能就是明天的一般加工。
精密加工所要解决的问题,一是加工精度,包括形位公差、尺寸精度及表面状况;二是加工效率,有些加工可以取得较好的加工精度,却难以取得高的加工效率。
精密加工包括微细加工和超微细加工、光整加工等加工技术。
传统的精密加工方法有砂带磨削、精密切削、珩磨、精密研磨与抛光等。
a. 砂带磨削是用粘有磨料的混纺布为磨具对工件进行加工,属于涂附磨具磨削加工的范畴,有生产率高、表面质量好、使用范围广等特点。
b. 精密切削,也称金刚石刀具切削(SPDT),用高精密的机床和单晶金刚石刀具进行切削加工,主要用于铜、铝等不宜磨削加工的软金属的精密加工,如计算机用的磁鼓、磁盘及大功率激光用的金属反光镜等,比一般切削加工精度要高1~2个等级。
c. 珩磨,用油石砂条组成的珩磨头,在一定压力下沿工件表面往复运动,加工后的表面粗糙度可达Ra0.4~0.1μm,最好可到Ra0.025μm,主要用来加工铸铁及钢,不宜用来加工硬度小、韧性好的有色金属。
d. 精密研磨与抛光通过介于工件和工具间的磨料及加工液,工件及研具作相互机械摩擦,使工件达到所要求的尺寸与精度的加工方法。
精密研磨与抛光对于金属和非金属工件都可以达到其他加工方法所不能达到的精度和表面粗糙度,被研磨表面的粗糙度Ra≤0.025μm加工变质层很小,表面质量高,精密研磨的设备简单,主要用于平面、圆柱面、齿轮齿面及有密封要求的配偶件的加工,也可用于量规、量块、喷油嘴、阀体与阀芯的光整加工。
超精密加工技术的发展现状
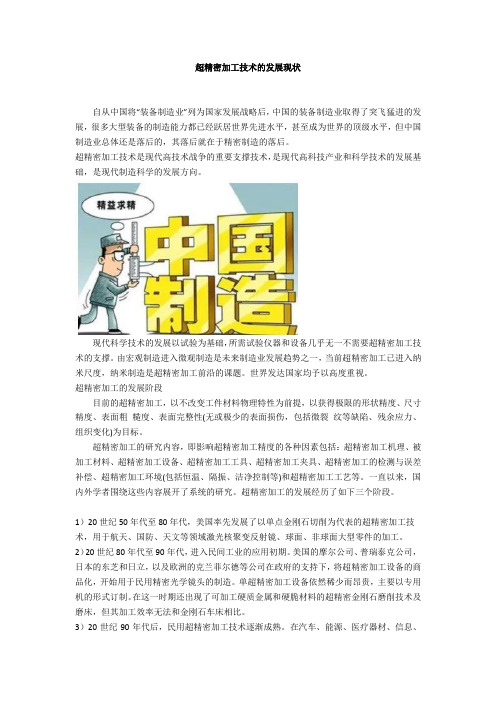
超精密加工技术的发展现状自从中国将“装备制造业”列为国家发展战略后,中国的装备制造业取得了突飞猛进的发展,很多大型装备的制造能力都已经跃居世界先进水平,甚至成为世界的顶级水平,但中国制造业总体还是落后的,其落后就在于精密制造的落后。
超精密加工技术是现代高技术战争的重要支撑技术,是现代高科技产业和科学技术的发展基础,是现代制造科学的发展方向。
现代科学技术的发展以试验为基础,所需试验仪器和设备几乎无一不需要超精密加工技术的支撑。
由宏观制造进入微观制造是未来制造业发展趋势之一,当前超精密加工已进入纳米尺度,纳米制造是超精密加工前沿的课题。
世界发达国家均予以高度重视。
超精密加工的发展阶段目前的超精密加工,以不改变工件材料物理特性为前提,以获得极限的形状精度、尺寸精度、表面粗糙度、表面完整性(无或极少的表面损伤,包括微裂纹等缺陷、残余应力、组织变化)为目标。
超精密加工的研究内容,即影响超精密加工精度的各种因素包括:超精密加工机理、被加工材料、超精密加工设备、超精密加工工具、超精密加工夹具、超精密加工的检测与误差补偿、超精密加工环境(包括恒温、隔振、洁净控制等)和超精密加工工艺等。
一直以来,国内外学者围绕这些内容展开了系统的研究。
超精密加工的发展经历了如下三个阶段。
1)20世纪50年代至80年代,美国率先发展了以单点金刚石切削为代表的超精密加工技术,用于航天、国防、天文等领域激光核聚变反射镜、球面、非球面大型零件的加工。
2)20世纪80年代至90年代,进入民间工业的应用初期。
美国的摩尔公司、普瑞泰克公司,日本的东芝和日立,以及欧洲的克兰菲尔德等公司在政府的支持下,将超精密加工设备的商品化,开始用于民用精密光学镜头的制造。
单超精密加工设备依然稀少而昂贵,主要以专用机的形式订制。
在这一时期还出现了可加工硬质金属和硬脆材料的超精密金刚石磨削技术及磨床,但其加工效率无法和金刚石车床相比。
3)20世纪90年代后,民用超精密加工技术逐渐成熟。
国外超精密加工技术的现状和发展趋势

国外超精密加工技术的现状和发展趋势1. 引言在当今世界,超精密加工技术已经成为了制造业的重要组成部分。
随着科技的不断发展,国外的超精密加工技术也取得了长足的进步。
本文将从多个角度对国外超精密加工技术的现状和发展趋势进行评估和探讨。
2. 现状分析超精密加工技术是指在微米或纳米级别进行加工的技术,其精度和表面质量要求非常高。
当前,国外一些先进制造业发达国家,如日本、德国和美国等,都在超精密加工技术领域具有举足轻重的地位。
这些国家的企业和研究机构不断推动着超精密加工技术的发展,不断推陈出新,取得了许多创新成果。
3. 技术发展趋势未来,国外超精密加工技术将朝着更高精度、更复杂形状、更多材料的加工方向发展。
随着人工智能、大数据和物联网等新一代信息技术的不断涌现,超精密加工技术将更加智能化、数字化和柔性化。
新型材料、纳米技术的应用,也将极大地拓展超精密加工技术的应用范围。
4. 我的观点我认为,国外超精密加工技术的快速发展将为全球制造业带来深远影响。
随着超精密加工技术在航空航天、医疗器械、电子器件等领域的广泛应用,将极大地推动相关产业的发展。
超精密加工技术的不断突破也将为人类社会带来更多便利和可能性。
5. 总结国外超精密加工技术的现状和发展趋势令人振奋。
技术不断创新,应用领域不断拓展,为制造业注入了新的活力。
我对超精密加工技术的未来充满信心,相信它将在全球范围内发挥越来越重要的作用。
通过本文的介绍和分析,相信您已经对国外超精密加工技术的现状和发展趋势有了更深入的了解。
希望本文能够为您带来一些启发和思考,并对您在相关领域的学习和工作有所帮助。
超精密加工技术在国外的发展已经取得了显著的进步,但仍有许多挑战和机遇。
在不断推动超精密加工技术的发展的国外也在积极探索新的技术路径和应用领域,以应对日益复杂的市场需求和竞争压力。
国外超精密加工技术在材料加工和表面处理方面取得了重大突破。
随着新型材料的广泛应用和纳米技术的发展,超精密加工技术已经能够处理更多种类的材料,包括金属、陶瓷、复合材料等。
超精密加工的发展与展望
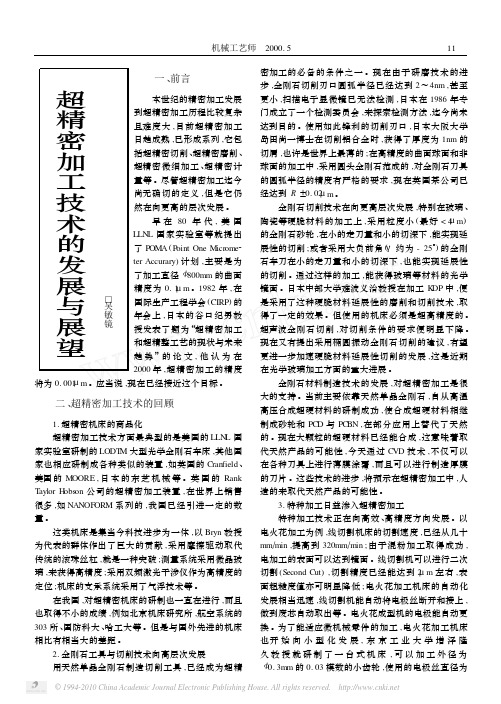
□吴敏镜 超精密加工技术的发展与展望 一、前言本世纪的精密加工发展到超精密加工历程比较复杂且难度大,目前超精密加工日趋成熟,已形成系列,它包括超精密切削、超精密磨削、超精密微细加工、超精密计量等。
尽管超精密加工迄今尚无确切的定义,但是它仍然在向更高的层次发展。
早在80年代,美国LLN L 国家实验室等就提出了POMA (P oint One Microme 2ter Accurary )计划,主要是为了加工直径<800mm 的曲面精度为0.1μm 。
1982年,在国际生产工程学会(CIRP )的年会上,日本的谷口纪男教授发表了题为“超精密加工和超精整工艺的现状与未来趋势”的论文,他认为在2000年,超精密加工的精度将为0.001μm 。
应当说,现在已经接近这个目标。
二、超精密加工技术的回顾1.超精密机床的商品化超精密加工技术方面最典型的是美国的LLN L 国家实验室研制的LODT M 大型光学金刚石车床,其他国家也相应研制成各种类似的装置,如英国的Cran field 、美国的MOORE ,日本的东芝机械等。
英国的Rank T aylor H obs on 公司的超精密加工装置,在世界上销售很多,如NANOFORM 系列的,我国已经引进一定的数量。
这类机床是集当今科技进步为一体,以Bryn 教授为代表的群体作出了巨大的贡献,采用摩擦驱动取代传统的滚珠丝杠,就是一种突破;测量系统采用微晶玻璃,来获得高精度;采用双频激光干涉仪作为高精度的定位;机床的支承系统采用了气浮技术等。
在我国,对超精密机床的研制也一直在进行,而且也取得不小的成绩,例如北京机床研究所,航空系统的303所、国防科大、哈工大等。
但是与国外先进的机床相比有相当大的差距。
2.金刚石工具与切削技术向高层次发展用天然单晶金刚石制造切削工具,已经成为超精密加工的必备的条件之一。
现在由于研磨技术的进步,金刚石切削刃口圆弧半径已经达到2~4nm ,甚至更小,扫描电子显微镜已无法检测,日本在1986年专门成立了一个检测委员会,来探索检测方法,迄今尚未达到目的。
超精密制造技术的进展与发展趋势
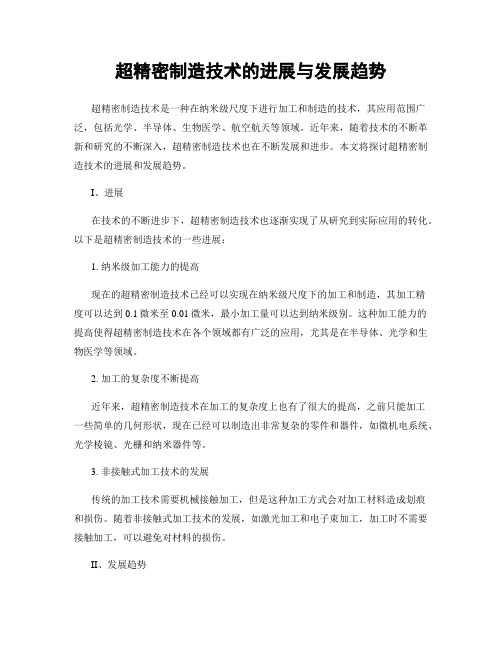
超精密制造技术的进展与发展趋势超精密制造技术是一种在纳米级尺度下进行加工和制造的技术,其应用范围广泛,包括光学、半导体、生物医学、航空航天等领域。
近年来,随着技术的不断革新和研究的不断深入,超精密制造技术也在不断发展和进步。
本文将探讨超精密制造技术的进展和发展趋势。
I、进展在技术的不断进步下,超精密制造技术也逐渐实现了从研究到实际应用的转化。
以下是超精密制造技术的一些进展:1. 纳米级加工能力的提高现在的超精密制造技术已经可以实现在纳米级尺度下的加工和制造,其加工精度可以达到0.1微米至0.01微米,最小加工量可以达到纳米级别。
这种加工能力的提高使得超精密制造技术在各个领域都有广泛的应用,尤其是在半导体、光学和生物医学等领域。
2. 加工的复杂度不断提高近年来,超精密制造技术在加工的复杂度上也有了很大的提高,之前只能加工一些简单的几何形状,现在已经可以制造出非常复杂的零件和器件,如微机电系统、光学棱镜、光栅和纳米器件等。
3. 非接触式加工技术的发展传统的加工技术需要机械接触加工,但是这种加工方式会对加工材料造成划痕和损伤。
随着非接触式加工技术的发展,如激光加工和电子束加工,加工时不需要接触加工,可以避免对材料的损伤。
II、发展趋势超精密制造技术的发展趋势主要包括以下几个方面:1. 改善加工精度虽然目前超精密制造技术可以在纳米级尺度下进行加工和制造,但是仍然存在一些难以解决的问题,如加工误差、表面粗糙度等。
未来的发展方向应该是更进一步地提高加工精度,将加工误差降到最低,同时也要解决表面质量的问题,使得制造出的产品亮度更高,表面更光滑。
2. 降低加工成本目前超精密制造技术的加工成本较高,这限制了其在工业领域的应用。
未来的发展方向应该是降低加工成本,提高生产效率和效益。
这可以通过改进生产工艺和材料、降低超精密设备的制造成本等方面实现。
3. 开发新的加工材料超精密制造技术的加工材料对材料的要求非常高,要求材料的均匀性和纯度都非常高。
超精密加工的发展和展望

超精密加工的发展和展望精密和超精密制造工程是适应前沿高技术发展需求而发展起来的。
它是一个国家重要经济和技术实力的体现,是其它高新技术实施的基础。
超精密制造技术是当前各个工业国家发展的核心技术之一,各技术先进国家在高技术领域(如国防工业、集成电路、信息技术产业等)之所以一直领先,与这些国家高度重视和发展超精密制造技术有极其重要的关系。
超精密制造技术是随着测量技术的发展而发展的。
Renishaw、Heidenhain及SONY等公司发展了分辨率均可以达到1nm的测量元件;美国HP公司、英国Taylor、美国zygo等公司的测量仪器均可以满足纳米测量的需求。
超精密制造技术在国际上已经得到广泛应用。
与国防工业有关的如人造卫星用的姿态轴承和遥测部件、被送入太空的哈勃望远镜(HST)、飞机发动机转子叶片等;与集成电路(IC)有关的硅片加工(要求硅片的加工表面粗糙度Ra一般小于2nm,精度要求达0.1nm);此外光刻设备和硅片加工设备的精度要求到亚微米和纳米级。
仪表的精度、激光陀螺仪的平面反射镜的精度、红外制导的反射镜等,其表面粗糙度均要求达到纳米级。
另外,光学非球曲面零件面形制造精度要求已达λ/(30—50),表面粗糙度要求≤0.5nm。
1、超精密制造技术的发展状况1962年美国Union Carbide公司研制出首台超精密车床。
在美国能源部支持下,LLI实验室和Y—12工厂合作,与1983年成功地研制出大型超精密金刚石车床(DTM—3型)。
该机床可加工直径¢2100mm,多路激光干涉测量系统分辨率为2.5nm。
1984年,LLL实验室成功地研制出LODTM大型金刚石车床。
该机床可加工的最大直径为¢1625mm x500mm,重量1360kg。
采用的双频激光测量系统分辨率为0.7nm,其主轴静态精度为:径向跳动≤25nm,轴向窜动≤51nm。
LLL实验室这两台机床是目前公认的国际上水平最高的超精密机床。
CUPE(Cranfield Unit for Precision Engineering)研制的Nanocenter超精密车床已批量生产,其主轴精度≤50nm,加工工件的面形精度≤0.1μm。
精密与超精密加工技术现状和发展展望

精密与超精密加工技术现状和发展展望精密加工技术是一种在当今制造业中非常重要的技术,它的发展与制造业的发展息息相关。
精密加工技术是通过对材料进行高精度的加工来制造出各种精密零部件,这些精密零部件被广泛应用于汽车、航空航天、医疗器械、电子产品等各个领域。
现阶段,精密加工技术已经取得了很大的进步,各种高精度的加工设备和加工工艺层出不穷。
在这些技术发展的基础上,超精密加工技术应运而生。
超精密加工技术是一种相对于精密加工技术更加高端、更加精密的加工技术,它可以实现对材料的超高精度加工,甚至可以达到纳米级的精度。
这种技术对于一些特殊材料的加工非常重要,比如硬质合金、钢、陶瓷等材料。
超精密加工技术的发展展望是非常乐观的。
随着科学技术的不断进步,各种先进的加工设备和工艺将不断涌现。
在这种趋势下,超精密加工技术将会得到更加广泛的应用。
在汽车工业中,超精密加工技术可以用于制造高压油泵的零部件,提高汽车发动机燃油的利用率;在医疗器械领域,超精密加工技术可以用于制造各种医疗器械的零部件,提高医疗器械的精度和安全性。
在未来的发展中,我们还可以看到超精密加工技术将会在航空航天领域得到更广泛的应用。
超精密加工技术可以制造出更加轻巧和高强度的航空零部件,提高航空器的性能和安全性。
超精密加工技术在电子产品领域也有很大的潜力,它可以制造出更小巧、更精密的电子元件,提高电子产品的性能和可靠性。
精密加工技术和超精密加工技术的发展是非常重要的。
它们直接关系到制造业的发展和产品的质量。
相信随着科学技术的不断进步,这些技术将会取得更大的突破,为各个领域带来更多的创新和发展。
精密与超精密加工技术的现状和发展展望精密加工技术是制造业中至关重要的一环,它的发展与制造业的发展密不可分。
精密加工技术通过对材料进行高精度的加工,制造出各种精密零部件,广泛应用于汽车、航空航天、医疗器械、电子产品等各个领域。
当前,精密加工技术已取得了长足的发展,各种高精度加工设备和工艺不断涌现。
精密和超精密加工技术及其发展展望(精密加工)
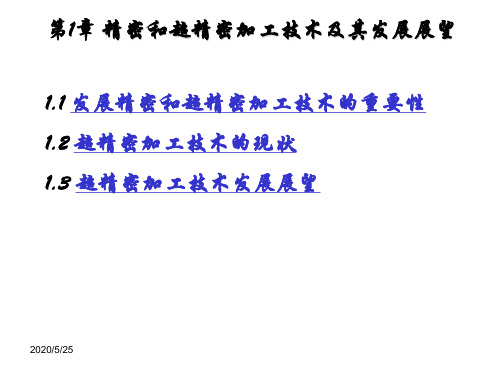
1.2 超精密加工技术的现状
4 加工工具
加工工具主要是指刀具、磨具及刃磨技术。用 金刚石刀具超精密切削,值得研究的问题有:金刚 石刀具的超精密刃磨,其刃口钝圆半径应达到2~ 4nm,同时应解决其检测方法,刃口钝圆半径与切 削厚度关系密切,若切削的厚度欲达到10nm,则刃 口钝圆半径应为2nm。
表面粗糙度可用电感式、压电晶体式表面形貌仪等
进行接触测量,或用光纤法、电容法、超声微波法和 隧道显微镜法进行非接触测量;
表面应力、表面变质层深度、表面微裂纹等缺陷,
可用X光衍射法、激光干涉法等来测量。检测可采取 离线的、在位的和在线的三种方式。
2013-9-22
1.2 超精密加工技术的现状
5 检测与误差补偿
在非传统加工中,出现了电子束、离子束、激
光束等高能加工、微波加工、超声加工、刻蚀、电 火花和电化学加工等多种方法,特别是复合加工, 如磁性研磨、磁流体抛光、电解研磨、超声珩磨等 ,在加工机理上均有所创新。
2013-9-22
1.2 超精密加工技术的现状
2 被加工材料
用精密和超精密加工的零件,其材料的化学成 分、物理力学性能、加工工艺性能均有严格要求。 例如,要求被加工材料质地均匀,性能稳定,无外 部及内部微观缺陷;其化学成分的误差应在10-2 ~ 10-3数量级,不能含有杂质;其物理力学性能,如拉 伸强度、硬度、延伸率、弹性模量、热导率和膨胀 系数等应达到10-5~10-6数量级;材料在冶炼、铸造 、辗轧、热处理等工艺过程中,应严格控制熔渣过 滤、辗轧方向、温度等,使材质纯净、晶粒大小匀 称、无方向性,能满足物理、化学、力学等性能要 求。
国家(中小零件加工) 。
我国的超精密加工技术在70年代末期有了长足
超精密加工技术的发展与展望
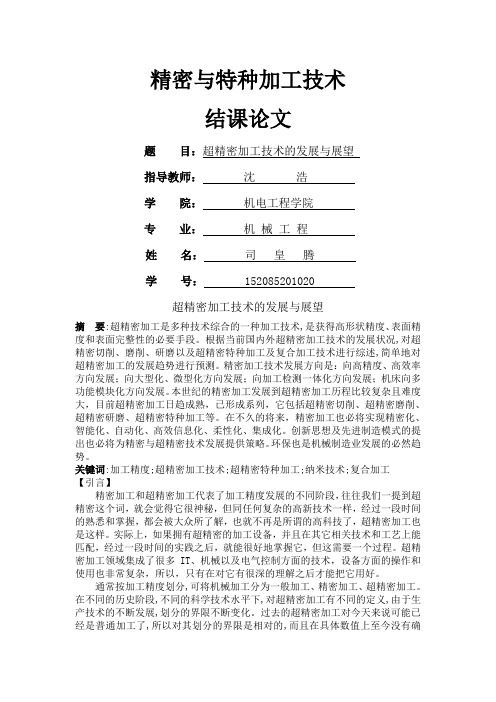
精密与特种加工技术结课论文题目:超精密加工技术的发展与展望指导教师:沈浩学院:机电工程学院专业:机械工程姓名:司皇腾学号: 152085201020超精密加工技术的发展与展望摘要:超精密加工是多种技术综合的一种加工技术,是获得高形状精度、表面精度和表面完整性的必要手段。
根据当前国内外超精密加工技术的发展状况,对超精密切削、磨削、研磨以及超精密特种加工及复合加工技术进行综述,简单地对超精密加工的发展趋势进行预测。
精密加工技术发展方向是:向高精度、高效率方向发展;向大型化、微型化方向发展;向加工检测一体化方向发展;机床向多功能模块化方向发展。
本世纪的精密加工发展到超精密加工历程比较复杂且难度大,目前超精密加工日趋成熟,已形成系列,它包括超精密切削、超精密磨削、超精密研磨、超精密特种加工等。
在不久的将来,精密加工也必将实现精密化、智能化、自动化、高效信息化、柔性化、集成化。
创新思想及先进制造模式的提出也必将为精密与超精密技术发展提供策略。
环保也是机械制造业发展的必然趋势。
关键词:加工精度;超精密加工技术;超精密特种加工;纳米技术;复合加工【引言】精密加工和超精密加工代表了加工精度发展的不同阶段,往往我们一提到超精密这个词,就会觉得它很神秘,但同任何复杂的高新技术一样,经过一段时间的熟悉和掌握,都会被大众所了解,也就不再是所谓的高科技了,超精密加工也是这样。
实际上,如果拥有超精密的加工设备,并且在其它相关技术和工艺上能匹配,经过一段时间的实践之后,就能很好地掌握它,但这需要一个过程。
超精密加工领域集成了很多IT、机械以及电气控制方面的技术,设备方面的操作和使用也非常复杂,所以,只有在对它有很深的理解之后才能把它用好。
通常按加工精度划分,可将机械加工分为一般加工、精密加工、超精密加工。
在不同的历史阶段,不同的科学技术水平下,对超精密加工有不同的定义,由于生产技术的不断发展,划分的界限不断变化。
过去的超精密加工对今天来说可能已经是普通加工了,所以对其划分的界限是相对的,而且在具体数值上至今没有确切的界限。