工艺参数对镀镉层厚度的影响研究
镀铬工艺参数对镀层质量的影响

铬是很易钝化的金属。
以常见金属的钝性系数为例,Cu、Pb、Sn为0〃10,Ni为0〃37,Cr为0〃74,最高为Ti,达2〃44。
即铬比镍易钝化得多。
镀铬用整流电源必须是低纹波的(纹波系数5%以下),且保持波形良好。
因为用纹波系数大的直流电流,在波形的低谷处也可能使铬层钝化,而在钝化的铬上再镀铬,必然灰白,局部钝化则起白斑。
镀铬整流电源可用三相五柱芯十二相整流带乎波电抗器的低纹波可控硅整流器,或者设有足够容量滤波器的高频开关电源。
道理很简单,纹波系数小的直流电是无法用变压器来变压的。
在生产实际中,由整流器也可以造成的镀铬故障。
一般说电镀车间湿度大、酸碱等气体腐蚀性强,常造成整流器等设备发生短路、断路等情况。
镀铬所使用的整流器由于长时间工作在大电流状态下,就更容易发生故障。
所以在处理镀铬故障时,作常规检查仍无法排除故障,同样对整流器作仔细地检查,以防排除电镀故障走弯路。
某厂在镀一批大面积的零件时,镀铬层突然变灰了。
根据故障现象对溶液中各成分和杂质的含量及电流密度、温度等工艺条件进行检查,结果显示没有超越镀铬工艺范围。
用万用表和示波器测量整流器的输出电流和电压的波形。
示波器显示输出电压波形中的纹波系数变大,表明三相交流电经降压、整流到输出的过程中,有某处发生故障致使输出的电压中缺少一相。
在不加电的状态下,仔细检查整流器中的变压器、整流元件、导线、接线柱,没有发现有损坏的现象。
几经周折,终于发现一只整流二极管,由于内部受腐蚀而失效。
断电检测结果二极管完好,但在加电状态下检测电压降,才发现其内部已经断路。
更换整流二极管后试镀,镀铬层质量正常,故障排除。
还有一次在镀一批面积较大的零件时,正常生产2个班后,镀铬层颜色逐渐变暗,深镀能力也越来越差。
针对这种情况,检查镀铬液各成分含量,发现Cr3+含量超过正常值29/L~59/L。
采用加大阳极面积,减小阴极面积的电解法来降低镀液中Cr3+的含量,但通电处理4h后试镀,故障现象依旧。
浅谈不同基体材料对镀层质量及电镀前处理工艺的影响
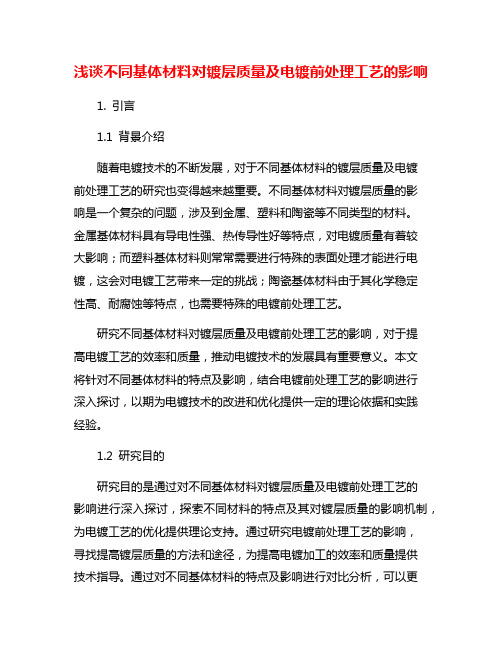
浅谈不同基体材料对镀层质量及电镀前处理工艺的影响1. 引言1.1 背景介绍随着电镀技术的不断发展,对于不同基体材料的镀层质量及电镀前处理工艺的研究也变得越来越重要。
不同基体材料对镀层质量的影响是一个复杂的问题,涉及到金属、塑料和陶瓷等不同类型的材料。
金属基体材料具有导电性强、热传导性好等特点,对电镀质量有着较大影响;而塑料基体材料则常常需要进行特殊的表面处理才能进行电镀,这会对电镀工艺带来一定的挑战;陶瓷基体材料由于其化学稳定性高、耐腐蚀等特点,也需要特殊的电镀前处理工艺。
研究不同基体材料对镀层质量及电镀前处理工艺的影响,对于提高电镀工艺的效率和质量,推动电镀技术的发展具有重要意义。
本文将针对不同基体材料的特点及影响,结合电镀前处理工艺的影响进行深入探讨,以期为电镀技术的改进和优化提供一定的理论依据和实践经验。
1.2 研究目的研究目的是通过对不同基体材料对镀层质量及电镀前处理工艺的影响进行深入探讨,探索不同材料的特点及其对镀层质量的影响机制,为电镀工艺的优化提供理论支持。
通过研究电镀前处理工艺的影响,寻找提高镀层质量的方法和途径,为提高电镀加工的效率和质量提供技术指导。
通过对不同基体材料的特点及影响进行对比分析,可以更深入地了解不同材料在电镀过程中的表现,为选择适合的基体材料提供参考依据,推动电镀工艺的发展和提升。
1.3 研究意义本研究旨在探究不同基体材料对镀层质量及电镀前处理工艺的影响,为电镀行业提供理论支持和实际指导。
具体意义包括:1. 拓展电镀领域的研究范围:通过深入研究不同基体材料对镀层质量的影响,可以为电镀技术的发展提供更多可能性和方向,进一步拓展电镀领域的研究范围。
2. 提高电镀技术的应用价值:准确把握不同基体材料对镀层质量的影响规律,可以有效提高电镀技术的应用价值,实现更高的镀层质量和性能。
3. 优化电镀前处理工艺:研究不同基体材料对电镀前处理工艺的影响,可以为工程领域提供更加适用的处理工艺方案,提高工艺效率和产品质量。
40Cr的电刷镀工艺参数实验研究

行, 而且 更为精 确 , 可 采 用 安 培 小 时 计 的 设 定 值
来 控制单 边厚 度 。因此 , 可根据 式 ( 1 ) 求 得 该 实 验 设 备 的 耗 电 系 数 C, 以 达 到 对 涂 层 厚 度 进 行
盖, 并 根据 自己计 算 的数值 , 通 过按键 增减来 设 定数 值, 当到达设 定 的值 时 , 电源 会 发 出蜂 鸣 的声 音 , 提
醒操 作者 应停 止刷镀 。
感 性 。材 料 规 格 : 棒料 长度 为 6 0 0 m m, 直 径 约 为
7 0 m t n , 实验用 的棒 料见 图 1 。
2 . 2 实验试 剂及 设备 仪器
3 镀层 的厚 度设计及计算
刷镀过 程 中 , 只 有 选 择 合 适 的 镀 层 材 料 和
本 试验 中选用 快 速镍 和快厚 镍 2种 镀液 。根 据
收 稿 日期 : 2 0 1 2—1 0—2 1
基金项 目: 福建省 自然科学基金项 目( 2 0 1 1 J 0 5 1 1 9 ) ; 福建省教育厅资助项 目( J A1 1 1 9 1 )
第1 5版 )
2 0 1 3年 2月
4 0 C r的 电刷 镀 工 艺 参 数 实 验 研 究
李 春 雨
( 1 . 福 州 大学机 械 工程及 自动化 学院 ,福 州 3 5 0 1 0 8 ; 2 . 福 建 工程 学院机械 与 汽车 3 - 程 学院 , 福州 3 5 0 1 0 8 )
能, 而且 能获 得较 高 的强度 和韧性 等综 合机械 性 能 ,
淬火 后 表 面硬 度 可 达 4 5~5 2 H R C 。4 0 C r 是机 械制 造 业使用 最 广泛 的钢之 一 。调质 处理后 具有 良好 的 综 合力学 性 能 , 良好 的低 温 冲击 韧 性 和低 的缺 口敏
镀铬工艺技术要求
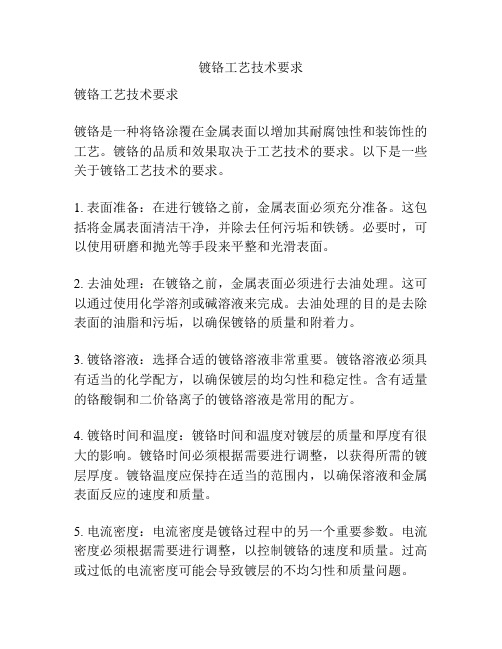
镀铬工艺技术要求镀铬工艺技术要求镀铬是一种将铬涂覆在金属表面以增加其耐腐蚀性和装饰性的工艺。
镀铬的品质和效果取决于工艺技术的要求。
以下是一些关于镀铬工艺技术的要求。
1. 表面准备:在进行镀铬之前,金属表面必须充分准备。
这包括将金属表面清洁干净,并除去任何污垢和铁锈。
必要时,可以使用研磨和抛光等手段来平整和光滑表面。
2. 去油处理:在镀铬之前,金属表面必须进行去油处理。
这可以通过使用化学溶剂或碱溶液来完成。
去油处理的目的是去除表面的油脂和污垢,以确保镀铬的质量和附着力。
3. 镀铬溶液:选择合适的镀铬溶液非常重要。
镀铬溶液必须具有适当的化学配方,以确保镀层的均匀性和稳定性。
含有适量的铬酸铜和二价铬离子的镀铬溶液是常用的配方。
4. 镀铬时间和温度:镀铬时间和温度对镀层的质量和厚度有很大的影响。
镀铬时间必须根据需要进行调整,以获得所需的镀层厚度。
镀铬温度应保持在适当的范围内,以确保溶液和金属表面反应的速度和质量。
5. 电流密度:电流密度是镀铬过程中的另一个重要参数。
电流密度必须根据需要进行调整,以控制镀铬的速度和质量。
过高或过低的电流密度可能会导致镀层的不均匀性和质量问题。
6. 镀铬质量检测:镀铬后,需要对镀层进行质量检测。
这可以通过使用显微镜来检查镀层的均匀性和光滑度。
还可以使用重量和厚度测试来确定镀层的质量和厚度。
7. 表面保护:在完成镀铬后,金属表面需要进行保护以防止腐蚀和损伤。
这可以通过使用适当的清漆或涂层来完成。
这些涂层可以提供额外的耐腐蚀性和保护性,同时也可以增加镀铬层的装饰效果。
综上所述,镀铬工艺技术的要求包括表面准备、去油处理、选择合适的镀铬溶液、控制镀铬时间和温度、调整电流密度、镀铬质量检测和表面保护等。
只有在满足这些要求的情况下,才能获得高质量的镀铬层。
影响镀层厚度和质量的主要因素【详述】
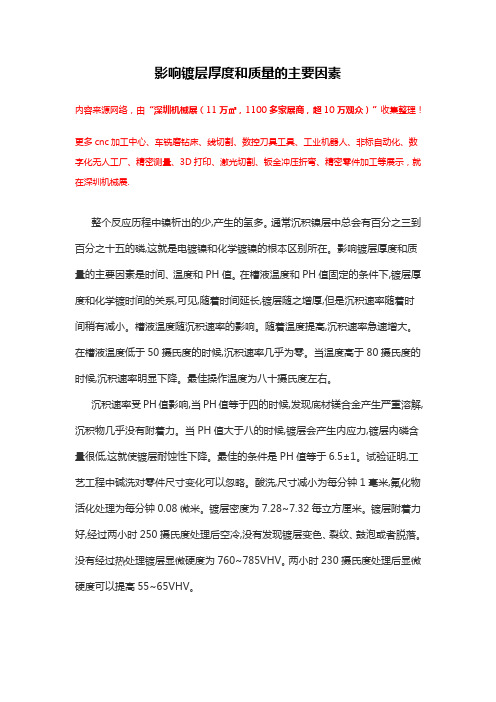
影响镀层厚度和质量的主要因素内容来源网络,由“深圳机械展(11万㎡,1100多家展商,超10万观众)”收集整理!更多cnc加工中心、车铣磨钻床、线切割、数控刀具工具、工业机器人、非标自动化、数字化无人工厂、精密测量、3D打印、激光切割、钣金冲压折弯、精密零件加工等展示,就在深圳机械展.整个反应历程中镍析出的少,产生的氢多。
通常沉积镍层中总会有百分之三到百分之十五的磷,这就是电镀镍和化学镀镍的根本区别所在。
影响镀层厚度和质量的主要因素是时间、温度和PH值。
在槽液温度和PH值固定的条件下,镀层厚度和化学镀时间的关系,可见,随着时间延长,镀层随之增厚,但是沉积速率随着时间稍有减小。
槽液温度随沉积速率的影响。
随着温度提高,沉积速率急速增大。
在槽液温度低于50摄氏度的时候,沉积速率几乎为零。
当温度高于80摄氏度的时候,沉积速率明显下降。
最佳操作温度为八十摄氏度左右。
沉积速率受PH值影响,当PH值等于四的时候,发现底材镁合金产生严重溶解,沉积物几乎没有附着力。
当PH值大于八的时候,镀层会产生内应力,镀层内磷含量很低,这就使镀层耐蚀性下降。
最佳的条件是PH值等于6.5±1。
试验证明,工艺工程中碱洗对零件尺寸变化可以忽略。
酸洗,尺寸减小为每分钟1毫米,氟化物活化处理为每分钟0.08微米。
镀层密度为7.28~7.32每立方厘米。
镀层附着力好,经过两小时250摄氏度处理后空冷,没有发现镀层变色、裂纹、鼓泡或者脱落。
没有经过热处理镀层显微硬度为760~785VHV。
两小时230摄氏度处理后显微硬度可以提高55~65VHV。
在湿度百分之九十五,温度九十五摄氏度的恒温恒湿箱中试验四十八小时,镀层没有任何变化。
该镀层热稳定性优良。
在二百五十摄氏度,真空度为1.33*10-3帕真空箱四十八小时试验,镀层没有变化。
经过热循环试验100次,镀层完好。
化学镀镍层采用高活性酸性溶剂很容易焊接。
如果镀层在空气中长期放置,或者经过热处理,不采用高活性酸性溶剂就很难进行焊接。
镀铬工艺技术分析论文
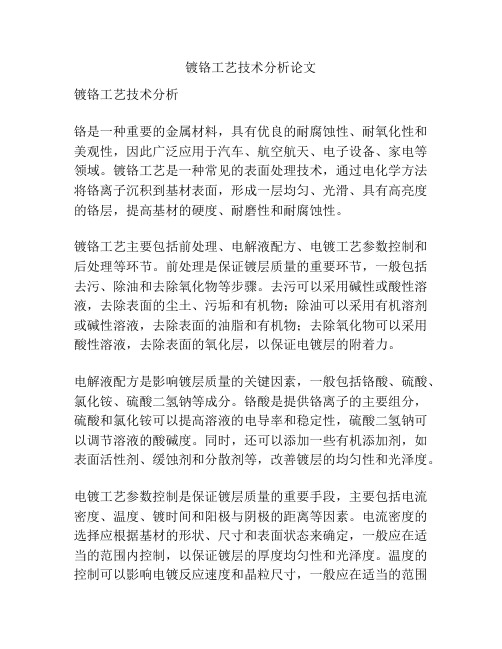
镀铬工艺技术分析论文镀铬工艺技术分析铬是一种重要的金属材料,具有优良的耐腐蚀性、耐氧化性和美观性,因此广泛应用于汽车、航空航天、电子设备、家电等领域。
镀铬工艺是一种常见的表面处理技术,通过电化学方法将铬离子沉积到基材表面,形成一层均匀、光滑、具有高亮度的铬层,提高基材的硬度、耐磨性和耐腐蚀性。
镀铬工艺主要包括前处理、电解液配方、电镀工艺参数控制和后处理等环节。
前处理是保证镀层质量的重要环节,一般包括去污、除油和去除氧化物等步骤。
去污可以采用碱性或酸性溶液,去除表面的尘土、污垢和有机物;除油可以采用有机溶剂或碱性溶液,去除表面的油脂和有机物;去除氧化物可以采用酸性溶液,去除表面的氧化层,以保证电镀层的附着力。
电解液配方是影响镀层质量的关键因素,一般包括铬酸、硫酸、氯化铵、硫酸二氢钠等成分。
铬酸是提供铬离子的主要组分,硫酸和氯化铵可以提高溶液的电导率和稳定性,硫酸二氢钠可以调节溶液的酸碱度。
同时,还可以添加一些有机添加剂,如表面活性剂、缓蚀剂和分散剂等,改善镀层的均匀性和光泽度。
电镀工艺参数控制是保证镀层质量的重要手段,主要包括电流密度、温度、镀时间和阳极与阴极的距离等因素。
电流密度的选择应根据基材的形状、尺寸和表面状态来确定,一般应在适当的范围内控制,以保证镀层的厚度均匀性和光泽度。
温度的控制可以影响电镀反应速度和晶粒尺寸,一般应在适当的范围内控制,以保证镀层的质量和性能。
镀时间的选择应根据基材的要求和工艺实践来确定,一般应在适当的范围内控制,以保证镀层的厚度和附着力。
阳极与阴极的距离的选择应根据镀件的形状、尺寸和表面状态来确定,一般应在适当的范围内控制,以保证镀层的厚度和均匀性。
后处理是提高镀层质量和附着力的重要环节,一般包括酸洗、水洗和干燥等步骤。
酸洗可以去除表面的氧化物和污染物,提高镀层的附着力和质量;水洗可以去除酸性溶液残留,同时也可以去除表面的杂质和污染物;干燥可以去除表面的水分和残留溶液,同时也可以提高镀层的光泽度和耐腐蚀性。
镀铬层的性能及影响因素
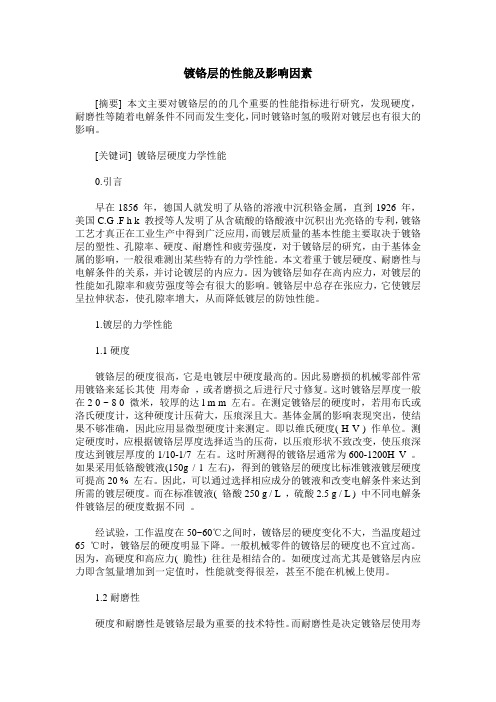
镀铬层的性能及影响因素[摘要] 本文主要对镀铬层的的几个重要的性能指标进行研究,发现硬度,耐磨性等随着电解条件不同而发生变化,同时镀铬时氢的吸附对镀层也有很大的影响。
[关键词] 镀铬层硬度力学性能0.引言早在1856 年,德国人就发明了从铬的溶液中沉积铬金属,直到1926 年,美国C.G .F h k 教授等人发明了从含硫酸的铬酸液中沉积出光亮铬的专利,镀铬工艺才真正在工业生产中得到广泛应用,而镀层质量的基本性能主要取决于镀铬层的塑性、孔隙率、硬度、耐磨性和疲劳强度,对于镀铬层的研究,由于基体金属的影响,一般很难测出某些特有的力学性能。
本文着重于镀层硬度、耐磨性与电解条件的关系,并讨论镀层的内应力。
因为镀铬层如存在高内应力,对镀层的性能如孔隙率和疲劳强度等会有很大的影响。
镀铬层中总存在张应力,它使镀层呈拉伸状态,使孔隙率增大,从而降低镀层的防蚀性能。
1.镀层的力学性能1.1硬度镀铬层的硬度很高,它是电镀层中硬度最高的。
因此易磨损的机械零部件常用镀铬来延长其使用寿命,或者磨损之后进行尺寸修复。
这时镀铬层厚度一般在2 0 ~ 8 0 微米,较厚的达l m m 左右。
在测定镀铬层的硬度时,若用布氏或洛氏硬度计,这种硬度计压荷大,压痕深且大。
基体金属的影响表现突出,使结果不够准确,因此应用显微型硬度计来测定。
即以维氏硬度( H V ) 作单位。
测定硬度时,应根据镀铬层厚度选择适当的压荷,以压痕形状不致改变,使压痕深度达到镀层厚度的1/10-1/7 左右。
这时所测得的镀铬层通常为600-1200H V 。
如果采用低铬酸镀液(150g / l 左右),得到的镀铬层的硬度比标准镀液镀层硬度可提高20 % 左右。
因此,可以通过选择相应成分的镀液和改变电解条件来达到所需的镀层硬度。
而在标准镀液( 铬酸250 g / L ,硫酸2.5 g / L ) 中不同电解条件镀铬层的硬度数据不同。
经试验,工作温度在50~60℃之间时,镀铬层的硬度变化不大,当温度超过65 ℃时,镀铬层的硬度明显下降。
工艺参数对CrNx涂层性能的影响
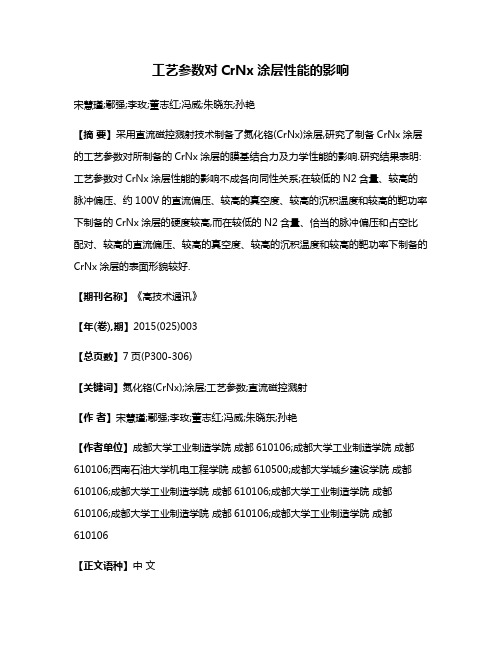
工艺参数对CrNx涂层性能的影响宋慧瑾;鄢强;李玫;董志红;冯威;朱晓东;孙艳【摘要】采用直流磁控溅射技术制备了氮化铬(CrNx)涂层,研究了制备CrNx涂层的工艺参数对所制备的CrNx涂层的膜基结合力及力学性能的影响.研究结果表明:工艺参数对CrNx涂层性能的影响不成各向同性关系;在较低的N2含量、较高的脉冲偏压、约100V的直流偏压、较高的真空度、较高的沉积温度和较高的靶功率下制备的CrNx涂层的硬度较高,而在较低的N2含量、恰当的脉冲偏压和占空比配对、较高的直流偏压、较高的真空度、较高的沉积温度和较高的靶功率下制备的CrNx涂层的表面形貌较好.【期刊名称】《高技术通讯》【年(卷),期】2015(025)003【总页数】7页(P300-306)【关键词】氮化铬(CrNx);涂层;工艺参数;直流磁控溅射【作者】宋慧瑾;鄢强;李玫;董志红;冯威;朱晓东;孙艳【作者单位】成都大学工业制造学院成都610106;成都大学工业制造学院成都610106;西南石油大学机电工程学院成都610500;成都大学城乡建设学院成都610106;成都大学工业制造学院成都610106;成都大学工业制造学院成都610106;成都大学工业制造学院成都610106;成都大学工业制造学院成都610106【正文语种】中文氮化铬(CrNx)涂层硬度高、耐磨性好、摩擦系数低,具有高温抗氧化性和耐腐蚀性能,并且对有色金属及其合金化学惰性好,是加工铝合金、黄铜和镍合金等的理想涂层材料。
氮化铬涂层已经广泛应用在很多领域,近年来越来越受到人们的关注和重视[1-4]。
在机械制造和加工领域,氮化铬涂层的硬度较高,摩擦系数较低,与钢摩擦时,摩擦系数比钢-钢摩擦小20%~30%,比氮化钛-钢摩擦小10%~20%,因为使用中表面容易形成一层稳定致密、硬度高并且结合紧密的氧化层,所以氮化铬涂层作为耐磨涂层已广泛用于一些机械零部件、模具和切削工具的表面强化以增长使用寿命。
化学镀锡工艺参数对沉积速率、镀层厚度及表面形貌的影响

20 40 60 80 100120140160180200 t|rain
图9施镀时间对镀层厚度的影响 对最佳工艺条件下施镀3 h的镀层进行金相显微 分析,计算出镀层的平均厚度为32.72斗m。镀速可达 10.91斗In/h。 由图9可以看出,镀层厚度随沉积时间的延长而 增加,镀层厚度一时间曲线线性良好,说明反应速率接 近一常数。这一规律证实了锡的连续自催化沉积,排 除了浸镀锡的可能性。因为浸镀锡时,基体被镀层完 全覆盖后反应会立即停止,且镀层较薄,一般只有0.5 Ixm左右。 反应初期的置换反应,使得基体铜与镀层间有一 薄铜锡合金层产生,会明显影响锡的沉积速率,导致反 应初期沉积速率低。而施镀30 min之后,锡的沉积速 率加快,说明铜锡合金层对镀速的影响变小,发生锡的 连续自催化反应。
无论是作为可焊性镀层还是作为防护性镀层,镀锡 层都要求有一定的厚度,才能满足其钎焊性能或耐腐蚀 性能的要求。锡的析氢过电位高,自催化活性低,若单独 选用一般的还原剂,无法实现锡的连续自催化沉积。传 统的化学镀锡工艺主要是Ti3+/Ti4+体系和氟硼酸体系, 镀液毒性大,沉积速度慢,镀层薄,镀液稳定性差,镀层不 能满足质量要求。当前的氯化物型化学镀锡多为置换镀
将不同温度镀液中施镀1 h的试样进行扫描电镜 分析,其表面形貌见图8。由图8可知,温度为60℃时 镀层颗粒最为细小,排列紧密;为80℃时镀层颗粒大小 适中,排列比较紧密;为90℃时镀层颗粒最大,排列最 为疏松。可以看出,温度越高,沉积的镀层颗粒粒度越 大,优势生长越明显,颗粒的排列越疏松,越不利于镀 层颗粒的连续生长。
乞鹬
V01.42 No.5 May 2009
。钇醐‘魄锄磊,莎k移磊移Z劾静
化学镀锡工艺参数对沉积速率、镀层厚度及表面形貌的影响
工艺参数对三价铬镀铬层粗糙度的影响

e 1 e c t r o d e p o s i t i o n .Th e i n c r e a s e o f t h e c o a t i n g r o u g h n e s s i s t h e mo s t s i g n i f i c a n t wh e n d u t y r a t i o i s 4 O
2 0 1 3年 1 月
电 镀 与 环 保
第3 3 卷第 1 期( 总第 1 8 9 期) ・1 7・
工 艺 参 数 对 三 价 铬 镀 铬 层 粗 糙 度 的 影 响
I n f l u e n c e o f Te c h n o l o g i c a l Pa r a me t e r s o n Ro u g h n e s s o f Cr ( I I I )Co a t i n g
r o ugh ne s s . Pu l s e f r e qu e nc y, d ut y r a t i o a nd a v e r a g i t y a l l h a ve a g r e a t e r i m pa c t o n t he c oa t i ng r o ug hne s s i n pu l s e
Co . ,Lt d .,S h a n g h a i 2 0 1 9 0 0 ,Ch i n a )
摘要: 通 过 单 因素 实验 研 究 了直 流 电镀 和 脉 冲 电镀 的 工 艺 参 数 对 镀 铬 层 粗 糙 度 的 影 响 。 采 用 直 流 电镀 , p H 值 较 低 时 镀 层 粗糙 度 增 大 较 明 显 , 镀 层 粗 糙 度 随 电流 密度 的 增 大 而 增 大 , 基 体 粗 糙 度 对 镀 层 粗 糙 度 也 具 有 较 大 的 影 响 。采 用脉 冲 电镀 , 占
最新影响电镀铬的因素资料

绪论镀铬层是一种高硬度、高耐磨性的镀层,又具有较好的耐热性及良好的化学稳定性。
由于镀铬层的良好性能,在工业上获得了广泛应用。
特别在航空制造业的军民机生产中,占有重要地位。
镀铬层属于单金属电镀。
与其他单金属镀层比较,镀铬过程比较复杂,而且我很多特点。
早镀铬过程中,是有铬酸来提供获得镀层金属所需的铬离子,镀铬所使用的阴极电流密度很高,电流效率低(13%左右),温度与电流密度要严格配合,可以通过改变二者的关系在同一镀液中获得光亮镀层。
镀铬不采用金属铬作为阳极,而是用纤锑合金不溶性阳极,镀铬点解液的分散能力极差。
以上这些,给电镀铬层的质量带来了比较多的影响。
影响镀铬层质量的因素为了获得较为理想的镀层,合理的镀前处理是电镀极为重要的一个环节。
金属零件从原材料到加工成型,不可避免的要与各种油类介质接触。
生产实践证明,油脂清洗不干净是影响镀层质量的重要因素。
同是,金属基体在空气中会生成一层比较致密的氧化膜,只有去除金属基体上的氧化膜,使其表面达到活化状态,才能够进行正常的电镀。
因此,零件表面任何的微量污染,都会降低镀铬层在机体上的附着力。
同时,抛光机体表面也是镀铬前出来及重要的一个工序,它可以是镀铬层更加均匀光亮。
2.镀液各成分的影响铬酐浓度时影响镀铬层的一个重要因素,其含量对溶液的导电性及电流效率有较大影响。
铬酐含量高,导电度增加。
铬酐浓度高则电流效率随之下降,镀层裂纹数量相对减少,意味着防腐蚀能力的提高。
硫酸的影响:硫酸在镀铬溶液中是一种不可缺少的成分。
如果没有酸根的存在,阴极上就不会有铬沉积出来。
但是,重要的并不是硫酸在镀铬液中的绝对喊啦,而是铬酐与硫酸的浓度比。
即:控制在CrO3/H2SO4=100:1镀铬溶液中还应该严格控制三价铬的含量。
三价铬的不足,难以获得你满意的镀层,过多的三价铬会缩小光亮范围,降低溶液的导电性。
3.镀铬液杂质的影响镀铬液中常见的杂质主要有金属阳离子杂志,主要有铁、铜、铅等等。
镀铬厚度 (2)
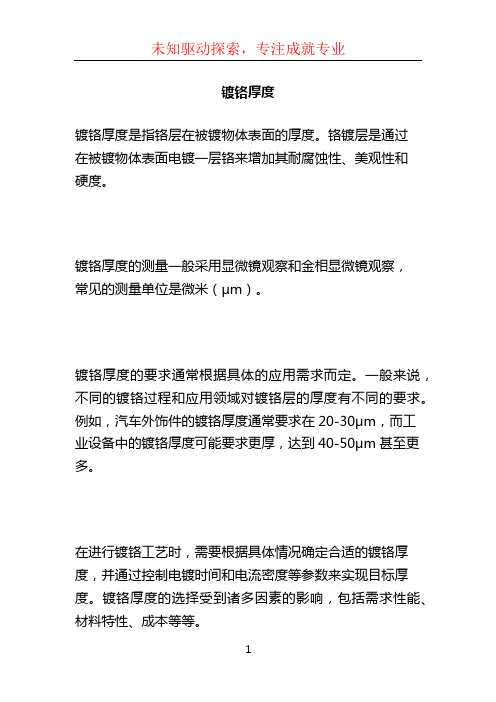
镀铬厚度
镀铬厚度是指铬层在被镀物体表面的厚度。
铬镀层是通过
在被镀物体表面电镀一层铬来增加其耐腐蚀性、美观性和
硬度。
镀铬厚度的测量一般采用显微镜观察和金相显微镜观察,
常见的测量单位是微米(μm)。
镀铬厚度的要求通常根据具体的应用需求而定。
一般来说,不同的镀铬过程和应用领域对镀铬层的厚度有不同的要求。
例如,汽车外饰件的镀铬厚度通常要求在20-30μm,而工业设备中的镀铬厚度可能要求更厚,达到40-50μm甚至更多。
在进行镀铬工艺时,需要根据具体情况确定合适的镀铬厚度,并通过控制电镀时间和电流密度等参数来实现目标厚度。
镀铬厚度的选择受到诸多因素的影响,包括需求性能、材料特性、成本等等。
总之,镀铬厚度是衡量铬镀层质量和性能的重要参数,它直接影响着镀铬件的耐腐蚀性、外观效果和机械性能。
工艺参数对PECVD TiN镀层性能的影响
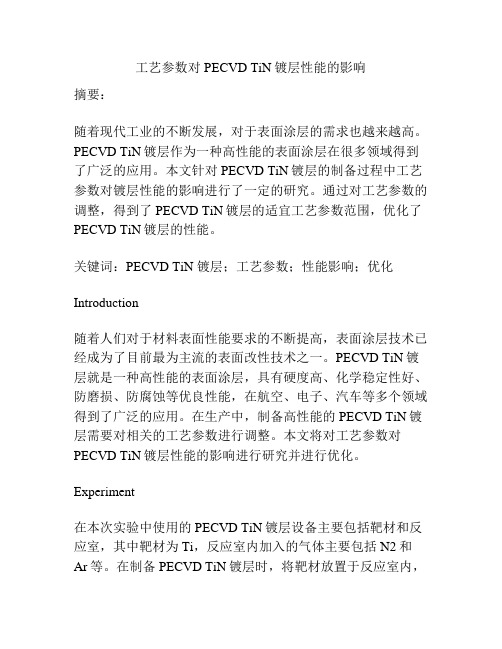
工艺参数对PECVD TiN镀层性能的影响摘要:随着现代工业的不断发展,对于表面涂层的需求也越来越高。
PECVD TiN镀层作为一种高性能的表面涂层在很多领域得到了广泛的应用。
本文针对PECVD TiN镀层的制备过程中工艺参数对镀层性能的影响进行了一定的研究。
通过对工艺参数的调整,得到了PECVD TiN镀层的适宜工艺参数范围,优化了PECVD TiN镀层的性能。
关键词:PECVD TiN 镀层;工艺参数;性能影响;优化Introduction随着人们对于材料表面性能要求的不断提高,表面涂层技术已经成为了目前最为主流的表面改性技术之一。
PECVD TiN镀层就是一种高性能的表面涂层,具有硬度高、化学稳定性好、防磨损、防腐蚀等优良性能,在航空、电子、汽车等多个领域得到了广泛的应用。
在生产中,制备高性能的PECVD TiN镀层需要对相关的工艺参数进行调整。
本文将对工艺参数对PECVD TiN镀层性能的影响进行研究并进行优化。
Experiment在本次实验中使用的PECVD TiN镀层设备主要包括靶材和反应室,其中靶材为Ti,反应室内加入的气体主要包括N2和Ar等。
在制备PECVD TiN镀层时,将靶材放置于反应室内,并在正常气氛下施加电场,使靶材表面出现等离子体,并将气体注入反应室中,在等离子体的作用下进行化学反应,生成PECVD TiN镀层。
在此基础之上,进行以下实验:实验一:探究Ar气流对PECVD TiN镀层的影响。
在实验中,通过对反应室内Ar气流量进行调整,探究不同Ar气流量对PECVD TiN镀层的表面形貌、硬度和厚度等性能指标的影响。
实验二:探究N2气流对PECVD TiN镀层的影响。
在实验中,通过对反应室内N2气流量进行调整,探究不同N2气流量对PECVD TiN镀层的表面形貌、硬度和厚度等性能指标的影响。
实验三:探究靶材温度对PECVD TiN镀层的影响。
在实验中,通过控制反应室内的靶材温度,探究不同温度对PECVD TiN镀层的表面形貌、硬度和厚度等性能指标的影响。
冲压模具电镀镀铬层的厚度
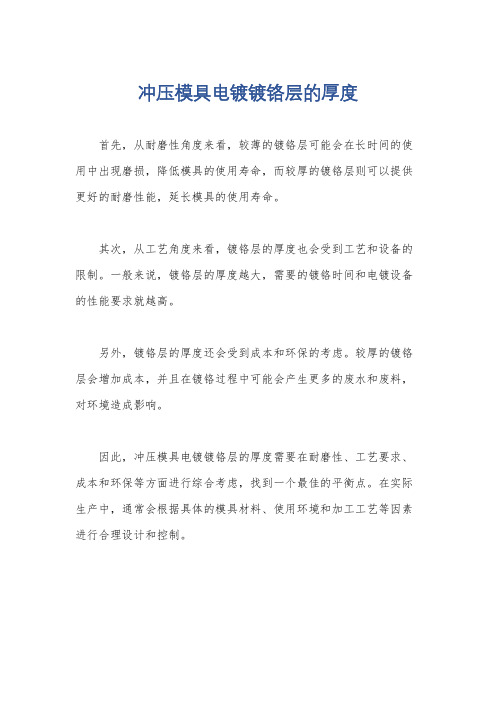
冲压模具电镀镀铬层的厚度
首先,从耐磨性角度来看,较薄的镀铬层可能会在长时间的使用中出现磨损,降低模具的使用寿命,而较厚的镀铬层则可以提供更好的耐磨性能,延长模具的使用寿命。
其次,从工艺角度来看,镀铬层的厚度也会受到工艺和设备的限制。
一般来说,镀铬层的厚度越大,需要的镀铬时间和电镀设备的性能要求就越高。
另外,镀铬层的厚度还会受到成本和环保的考虑。
较厚的镀铬层会增加成本,并且在镀铬过程中可能会产生更多的废水和废料,对环境造成影响。
因此,冲压模具电镀镀铬层的厚度需要在耐磨性、工艺要求、成本和环保等方面进行综合考虑,找到一个最佳的平衡点。
在实际生产中,通常会根据具体的模具材料、使用环境和加工工艺等因素进行合理设计和控制。
电镀工艺厚度
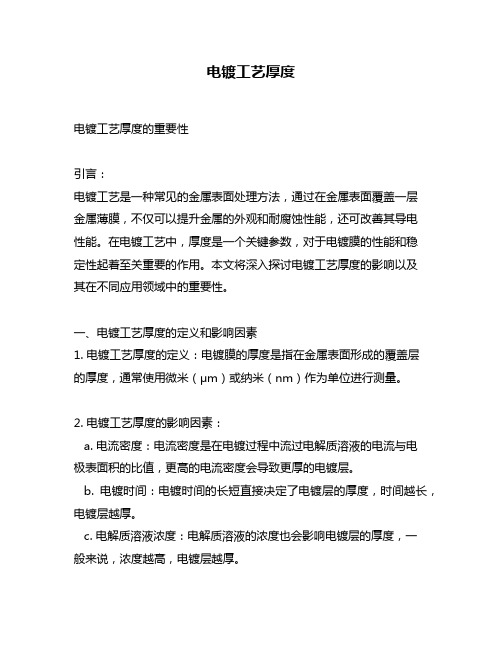
电镀工艺厚度电镀工艺厚度的重要性引言:电镀工艺是一种常见的金属表面处理方法,通过在金属表面覆盖一层金属薄膜,不仅可以提升金属的外观和耐腐蚀性能,还可改善其导电性能。
在电镀工艺中,厚度是一个关键参数,对于电镀膜的性能和稳定性起着至关重要的作用。
本文将深入探讨电镀工艺厚度的影响以及其在不同应用领域中的重要性。
一、电镀工艺厚度的定义和影响因素1. 电镀工艺厚度的定义:电镀膜的厚度是指在金属表面形成的覆盖层的厚度,通常使用微米(μm)或纳米(nm)作为单位进行测量。
2. 电镀工艺厚度的影响因素:a. 电流密度:电流密度是在电镀过程中流过电解质溶液的电流与电极表面积的比值,更高的电流密度会导致更厚的电镀层。
b. 电镀时间:电镀时间的长短直接决定了电镀层的厚度,时间越长,电镀层越厚。
c. 电解质溶液浓度:电解质溶液的浓度也会影响电镀层的厚度,一般来说,浓度越高,电镀层越厚。
d. 金属基材的表面形态:基材表面的形态也会对电镀层的厚度产生影响,粗糙的表面会导致电镀层不均匀。
二、电镀工艺厚度的重要性1. 外观和装饰性能:电镀工艺的厚度对金属制品的外观效果至关重要,适当的厚度可以给制品带来深度和光泽,提升其装饰性能。
2. 耐腐蚀性能:适当的电镀工艺厚度可以为金属制品提供优秀的耐腐蚀性能,有效延长其使用寿命。
3. 电导率:电镀层通常具有较好的导电性能,适当的厚度可以提高金属制品的导电性能,广泛应用于电子行业和电器制造业。
三、电镀工艺厚度在不同应用领域中的重要性1. 汽车制造业:在汽车制造业中,电镀工艺的厚度对于保护车身免受腐蚀的作用至关重要,同时也能为汽车外观增添豪华感和吸引力。
2. 电子行业:电镀层在电子行业中的应用广泛,适当的厚度可以提高电子元器件的导电性能和稳定性,降低电阻和能耗。
3. 家具制造业:电镀工艺可以赋予家具制品金属质感,增加其价值和品质感。
适当的厚度可以提升家具制品的金属感,使其更显高档。
总结和回顾:电镀工艺厚度是电镀过程中一个重要的参数,影响着电镀层的性能和稳定性。
浅议提高板类带孔件镀铬表面质量的方法

浅议提高板类带孔件镀铬表面质量的方法近年来,随着家居装饰行业的发展和人们对商品质量要求的提高,板类带孔件镀铬表面质量的要求也越来越高。
在板类带孔件镀铬表面质量的提高方面,有许多方法可以采用,如控制镀铬工艺参数、改善基材表面处理等,本文将对提高板类带孔件镀铬表面质量的方法进行浅议。
一、控制镀铬工艺参数在镀铬过程中,控制工艺参数对提高板类带孔件镀铬表面质量至关重要。
其中包括控制镀液配方、电镀温度、电镀时间、电镀电流密度等。
通过合理的控制镀液的配方,可以保证电镀层的均匀性和致密性,从而提高镀铬层的表面质量。
而电镀温度、电镀时间、电镀电流密度等参数的控制也都可以影响镀铬层的厚度和质量,因此需要根据实际情况进行合理的调控。
还需要注意镀铬前的基材处理工艺,例如去油脱脂、酸洗、活化等工艺过程的控制,这些都是影响镀铬表面质量的重要因素。
只有通过合理的工艺参数控制,才能保证板类带孔件镀铬表面质量的提高。
二、改善基材表面处理除了控制镀铬工艺参数外,改善基材表面处理也是提高板类带孔件镀铬表面质量的关键。
在基材表面处理过程中,要保证基材表面的平整度和光洁度,排除基材表面的油污和杂质等,以保证镀铬层的附着力和表面质量。
在实际生产中,可以采用机械抛光、化学抛光、酸洗等方式对基材表面进行处理,以保证镀铬层的表面质量。
还可以采用一些钝化剂或者活化剂对基材表面进行处理,以改善镀铬层的致密性和表面质量。
这些基材表面处理工艺的改善,对于提高板类带孔件镀铬表面质量具有非常重要的作用。
三、选择合适的镀铬工艺对于板类带孔件镀铬来说,选择合适的镀铬工艺也是非常重要的。
在实际生产中,可以根据具体的板类带孔件的形状和要求,选择不同的镀铬工艺,以保证镀铬层的均匀性和质量。
例如对于复杂形状的板类带孔件,可以采用旋转镀、喷镀等镀铬工艺,以保证镀铬层的均匀性和质量。
还可以根据板类带孔件的具体要求,选择硬镀铬、半亮镀铬、亮镀铬等不同的镀铬工艺,以满足不同客户的需求。
工艺条件对镀层性能的影响

工艺条件对镀层性能的影响①脉冲参数的影响采用脉冲电流镀金的作用主要是细化晶粒和增加镀层中硬颗粒的含量。
在脉冲导通时间内突发性的瞬时高电流产生大的极化,使得成核速率远大于晶粒生长速率,因而晶粒变细,而在断通状态,阴极周围存在的杂质和气体得以分到溶液中去,从而使得镀层结晶更细致,孔隙少,纯度高。
控制脉冲电流密度在O.1—2. 5A/dm2,脉冲通断比在(1:5)一(1:8)范围内可获得较为理想的镀金层。
②添加剂的影响氰化物镀金若电镀时间稍长,厚度大于O.5J真m,镀层就会发暗,去金属光泽,这时就需要添加光亮剂。
纯金镀层较软,显微硬度一般在HV70~90,但金饰件如首饰、项链或纪念章等又要求镀釜层自较高的硬度,能耐磨,所以镀金液中往往还需添加增硬组【电镀设备厂】分。
其他添加剂如辅助络合剂可以增大极化,细化晶粒,还有p冲剂、除杂剂等。
研制出的N-I型镀金光亮剂和N-2型增硬剂用于低氰镀金,好的效果。
磷酸二氢钾的加;入也可显著改善低电流密度区的光亮效果。
其中光亮剂的添加范围经实验确定在4~8mL/L 为宜。
加入增硬剂后,镀层硬度可提高到IHV180左,且随着电流密度的加大,有利于硬化组分的共沉积,因而硬度提高。
硬化组分的加人,实际上使镀金成了合金电镀,影响到金沉积的结晶过程,使得镀层结晶颗粒变细,提高了镀层的光泽和硬度,所以也能改善镀层的耐磨性。
脉冲电流的作用便是增加硬分的含量,同时也能细化晶粒。
增硬剂的添加量以lOmL/L左右为宜。
③施镀温度的影响试验中发现施镀温度在40~50℃之间都能获得良好的镀疫层,但从节能和工艺性能考虑,选择45℃左右为佳。
④pH的影响本配方镀液的pH在9~10之间,电镀一定时间后,pH会有所变化。
当pH低于9时,镀层粗糙发暗,色泽不均匀,而pH高于10. 5时,镀层光亮度会F降,所以需加入一定量的辅助络合剂和磷酸二氢钾以稳定镀液pH。
⑤阴极电流密度的影响生产中,施镀电流密度范围在O.1~3A/dm2为宜。
电镀设备影响镀铬层质量的分析

电镀设备中的镀铬是一个主要生产单元,镀层的密度、均匀性影响产品的质量。
设备、镀液和工艺技术是影响电镀质量的关键环节,而设备运行和维护的质量则直接影响工艺的实现。
在长期的电镀生产实践中,根据生产现场积累的经验,记录了一些因设备配置或者使用不当导致的影响生产和电镀工艺实现的典型故障实例,对其中的一些关于镀铬生产线仪表、母排、辅助阳极的故障加以分析,供同行参考。
为便于分析,在本文的故障分析中,均假定电镀电源、仪表本体、输电母线本体、镀铬工艺和镀液、电镀电极的材质均为完好无故障状态。
1.铜母排连接错误生产实例1)故障现象新电镀生产线运行保修期内(运行二十天)出现三处直流电压示值不一致,影响设备最终交接。
三处电压表分别装设在整流电源本体、直流母排入工房首端位置、镀槽旁。
前两处示值相同,镀槽处的电压表示值低2V。
在设备安装完毕的交接中没有出现此问题。
2)故障原因分析及排除方法发现母排正负极均出现较大电阻,运行中滴水法检查,发现母排在几处螺栓对接点出现过热现象,为电压损失点所在。
打开连接部位,细砂纸打磨氧化层并涂抹导电膏,将螺栓更换为铜螺栓,重新连接,故障排除。
在电路的设计中应使铜母排对接部分大于其宽度,铜母体表面也可以采用镀锡层,以避免氧化。
滴水法查母排过热点,是应用于低压大电流母排的一种简便的、不停电查线路过热点的方法。
就是用冷水点滴在铜母排上观察其温度变化。
2·阳极形状设计不当生产实例:1)故障现象在镀铬生产线进行铜管结晶器镀铬。
铜管结晶器内部一端为不规则弧线形状。
镀铬工艺中,结晶器为阴极,石墨为阳极。
试镀过程中,出现铜管结晶器弧形尾端局部铬层过厚或局部没有镀层。
2)故障原因分析及排除方法电镀工艺人员和设备维护人员从设备、镀铬工艺和镀液配方、电镀电极的材质等多方面进行调试,均未解决问题。
经综合分析故障现象,提出将石墨阳极做成仿形阳极,使阴极表面各部位与阳极的距离比较接近,改善了阴极表面电流分布的均匀性。
电镀工艺厚度
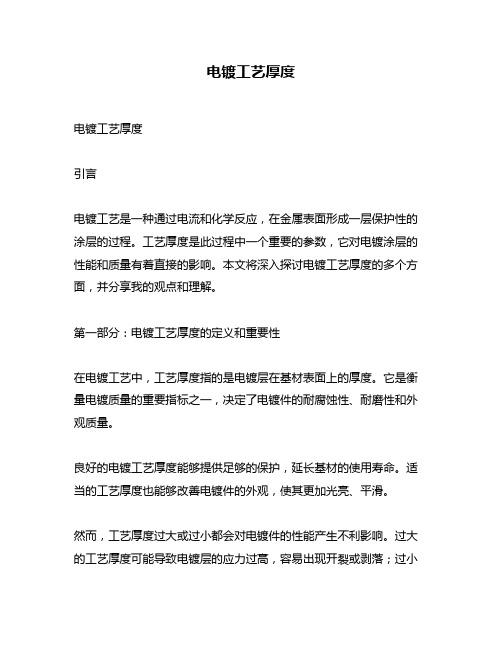
电镀工艺厚度电镀工艺厚度引言电镀工艺是一种通过电流和化学反应,在金属表面形成一层保护性的涂层的过程。
工艺厚度是此过程中一个重要的参数,它对电镀涂层的性能和质量有着直接的影响。
本文将深入探讨电镀工艺厚度的多个方面,并分享我的观点和理解。
第一部分:电镀工艺厚度的定义和重要性在电镀工艺中,工艺厚度指的是电镀层在基材表面上的厚度。
它是衡量电镀质量的重要指标之一,决定了电镀件的耐腐蚀性、耐磨性和外观质量。
良好的电镀工艺厚度能够提供足够的保护,延长基材的使用寿命。
适当的工艺厚度也能够改善电镀件的外观,使其更加光亮、平滑。
然而,工艺厚度过大或过小都会对电镀件的性能产生不利影响。
过大的工艺厚度可能导致电镀层的应力过高,容易出现开裂或剥落;过小的工艺厚度则容易导致电镀层的质量不稳定,影响电镀件的使用寿命。
第二部分:影响电镀工艺厚度的因素1. 电镀时间和电流密度:电镀时间和电流密度是决定工艺厚度的关键因素之一。
一般来说,电镀时间越长,厚度越大;电流密度越大,厚度也越大。
然而,在实际生产中,需要根据具体情况进行优化,以确保工艺厚度在可控范围内。
2. 电镀液成分:电镀液的成分也会对工艺厚度产生影响。
不同的电镀液配方会有不同的工艺厚度范围。
通过调整电镀液中的添加剂和浓度,可以控制工艺厚度的变化。
3. 基材表面处理:基材表面的处理也影响着电镀工艺厚度的均匀性和稳定性。
合适的表面处理能够提高电镀涂层与基材的结合力,避免厚度不均匀的问题。
第三部分:控制工艺厚度的方法为了获得理想的电镀工艺厚度,以下是一些常用的控制方法:1. 优化电镀工艺参数:通过合理调整电镀时间、电流密度和电镀液成分,以达到所需的工艺厚度。
2. 使用控制设备:现代化的电镀设备通常配备了实时监测和控制功能,可以自动控制电镀工艺参数,从而实现工艺厚度的精确控制。
3. 进行检测和测量:定期对电镀层进行检测和测量,可以及时发现和解决工艺厚度偏差的问题。
常用的测量方法包括金相显微镜、X射线荧光光谱仪等。
镀铬厚度_精品文档
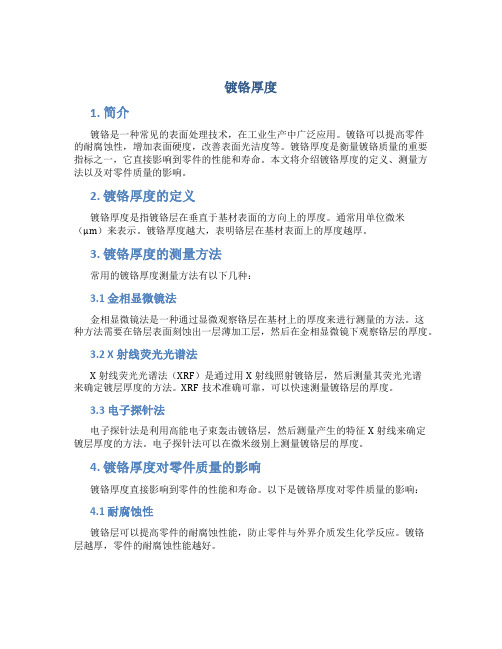
镀铬厚度1. 简介镀铬是一种常见的表面处理技术,在工业生产中广泛应用。
镀铬可以提高零件的耐腐蚀性,增加表面硬度,改善表面光洁度等。
镀铬厚度是衡量镀铬质量的重要指标之一,它直接影响到零件的性能和寿命。
本文将介绍镀铬厚度的定义、测量方法以及对零件质量的影响。
2. 镀铬厚度的定义镀铬厚度是指镀铬层在垂直于基材表面的方向上的厚度。
通常用单位微米(μm)来表示。
镀铬厚度越大,表明铬层在基材表面上的厚度越厚。
3. 镀铬厚度的测量方法常用的镀铬厚度测量方法有以下几种:3.1 金相显微镜法金相显微镜法是一种通过显微观察铬层在基材上的厚度来进行测量的方法。
这种方法需要在铬层表面刻蚀出一层薄加工层,然后在金相显微镜下观察铬层的厚度。
3.2 X射线荧光光谱法X射线荧光光谱法(XRF)是通过用X射线照射镀铬层,然后测量其荧光光谱来确定镀层厚度的方法。
XRF技术准确可靠,可以快速测量镀铬层的厚度。
3.3 电子探针法电子探针法是利用高能电子束轰击镀铬层,然后测量产生的特征X射线来确定镀层厚度的方法。
电子探针法可以在微米级别上测量镀铬层的厚度。
4. 镀铬厚度对零件质量的影响镀铬厚度直接影响到零件的性能和寿命。
以下是镀铬厚度对零件质量的影响:4.1 耐腐蚀性镀铬层可以提高零件的耐腐蚀性能,防止零件与外界介质发生化学反应。
镀铬层越厚,零件的耐腐蚀性能越好。
4.2 表面硬度适当的镀铬厚度可以增加零件的表面硬度,提高零件的抗磨损能力和机械强度。
4.3 表面光洁度镀铬层可以改善零件表面的光洁度,使零件表面更加光滑、亮丽。
4.4 尺寸影响过厚或过薄的镀铬层会对零件的尺寸产生影响,可能导致零件的尺寸不合格。
5. 结论镀铬厚度是衡量镀铬质量的重要指标之一。
合理的镀铬厚度可以提高零件的耐腐蚀性、表面硬度和光洁度等性能。
根据实际需要,选择合适的镀铬厚度对提高零件质量至关重要。
以上就是关于镀铬厚度的介绍,包括定义、测量方法及对零件质量的影响。
了解镀铬厚度的重要性,有助于提高对镀铬质量的认识和控制。
- 1、下载文档前请自行甄别文档内容的完整性,平台不提供额外的编辑、内容补充、找答案等附加服务。
- 2、"仅部分预览"的文档,不可在线预览部分如存在完整性等问题,可反馈申请退款(可完整预览的文档不适用该条件!)。
- 3、如文档侵犯您的权益,请联系客服反馈,我们会尽快为您处理(人工客服工作时间:9:00-18:30)。
科技创新导报 Science and Technology Innovation Herald
18
航空航天科学技术
DOI:10.16660/ki.1674-098X.2018.01.018
工艺参数对镀镉层厚度的影响研究
翟敏 安浩
(航空工业西飞热表处理厂 陕西西安 710089)
摘 要:本文通过溶液浓度、电流密度、电镀时间等方面研究镀层厚度与电镀工艺参数之间的关系,结果表明:当槽液中各组分达到某个最佳范围时,零件镉层厚度比较均匀;随着电流密度的增大,电镀时间的增长,镀层厚度先增大后几乎不变,但是镀层外观粗糙,有局部烧焦的现象。
关键词:能量参数 镀层厚度 研究分析
中图分类号:V250 文献标识码:A 文章编号:1674-098X(2018)01(a)-0018-02
航空类产品对抗腐蚀要求较高,电镀镉层是主要的抗海洋大气腐蚀镀层,镀层不易开裂剥落,因此在航空,航海及国防工业中得到了广泛的应用。
在海洋和高温大气环境中,镉镀层对钢铁是阳极性镀层,并且氰化镀镉溶液具有较大的阴极极化作用,从氰化镀镉溶液中得到的镀层平滑、细致。
含有光亮剂的氰化镀镉溶液可获得光亮镀层,其孔隙率小,耐蚀性高,主要用于抗拉轻度低的结构钢零件中。
目前西飞公司在表面处理生产中采用了氰化镀镉工艺,任务量非常大,溶液的消耗很快,在生产过程中很容易出现镀镉层的厚度不均匀、镀层质量较差等问题。
为了解决这种情况,本文通过赫尔槽试验并采用正交实验的方法,综合评定优化了各组份的最佳范围,以及电镀时采用的电流密度、电镀时间等工艺参数并对各影响因素进行了系统的分析,找出影响镀镉层厚度的因素。
1 试验
1.1 溶液浓度对镀层厚度的影响
氰化镀镉槽液由氰化钠、氧化镉、氢氧化钠和光亮剂四种组份组成,氰化钠在镀液中是络合剂,除了与氧化镉作用生成络盐外,在溶液中保持一定量的游离氰化物能保证阳极的正常溶解,补充镉离子的消耗,稳定溶液并提高阴极极化作用,改善溶液的分散能力。
氧化镉是电镀液的主盐,在其他条件相同时,阴极电流密度范围随镉含量的降低而降低。
氢氧化钠在电镀液中是导电盐,一是防止主盐和络合剂的水解;二是增加溶液的导电能力,有益于提高溶液的分散能力,改善镀层组织,使镀层光亮,细致。
在电流密度为1.5A/d m 2,电镀时间为25m i n,我们通过控制其中三种组份含量不变,逐渐改变其中一种组份含量的镀液进行赫尔槽试验。
通过测量试片镀层厚度,最终将多次试验结果进行正交,得出各组份的最佳含量范围。
以此为基础我们做了大量的工艺试验,最终得到了电镀镉溶液各组份镀层厚度影响的关系图(见图1)。
氰化物含量过低,镀层均镀能力差,阳极容易钝化,不
易溶解,过高会降低允许的阴极电流密度范围的上限制和阴极电流效率,阴极附近析出大量气泡,镉镀层难以析出,对分散能力和沉积速度均有不良影响。
较高的镉含量能提高允许的阴极电流密度范围上限值,镉含量过高时,会降低阴极极化作用,使镀层结晶粗大,镀液的均镀能力下降。
氢氧化钠含量过高,电流效率降低,电解液碱度增大,镀层发暗并带黑条纹,容易起泡;氢氧化钠含量过低,电解液导电性差,沉积层分布不均匀。
氢氧化钠在规定范围内可增加电解液的导电性,防止游离氰化物的水解,提高游离氰化物的相对含量。
1.2 电流密度以及电镀时间对镀层厚度的影响
电沉积过程中,电镀时间过短往往因为电镀不充分而导致平均沉积速率很小,电镀时间过长镀液中有效成分大量消耗平均沉积速率也不理想,因此选择一个合适的电镀时间可以有效利用电镀液,也可以生成表面粗糙度低的镀层。
电流密度增加可以加快阴极阳离子的还原,成核速度逐渐增加,晶界逐渐模糊;但电流密度过大时阳离子容易集中在高电流密度区域,被还原金属来不及扩散,在高密度区域
图1 槽液中主盐浓度与膜层厚度的关系
图2 不同电流密度与镀层厚度的关系
表1 不同电流密度下电镀至8~12μm所需时间电流密(A/dm 2) 1.52 2.535 6.4时间(min)
25
22
18
/
18
15
科技创新导报 Science and Technology Innovation Herald
19
(上接17页)
快速生长导致晶粒之间界面明显,表面不平整。
故选择合适的电流密度对电镀膜层的质量影响比较大。
不同电流密度条件下零件电镀膜层的厚度不同,由于原始记录采用的电流密度为1.5A/d m 2、以及3A/d m 2电镀时间又各异,所以固定电镀时间为18m i n,通过改变电流密度,测量镀层厚度,最终得出电流密度与镀层厚度的关系图如图2所示。
由图2可以看出,随着电流密度以及电镀时间的增长,镀镉层厚度先增大后基本保持不变,但是镀层质量变差,镀层粗糙并且局部烧焦。
所以为了满足实际生产要求,需要找出优化的电流密度以及电镀时间,结果如表1所示。
2 结论
(1)通过单因素和正交实验研究,找到光亮氰化镀镉液的最佳控制点,最终确定了氰化镀镉液维护控制在氰化钠:110~120g/L,氧化镉:28~30g/L,氢氧化钠:15~17g/L,光亮剂:1.2%(初配时)时,零件镉层厚度比较均匀。
(2)随着电流密度的增大,电镀时间的增长,镀层厚度先增大后几乎不变,但是镀层外观粗糙,有局部烧焦的现象。
所以选择合适的电流密度以及电镀时间至关重要。
参考文献
[1] 董占东.控制锌层厚度的一种有效方法[J ].轧钢,2010,27(3):56-58.
[2] 周斌.镀镉工艺改进[J].材料保护,2001,12(34):42.[3] 黄平,陈端杰.无氰镀镉工艺研究及应用[J].新技术新工艺,2008(11):17-18.
[4] 王贺贺,姚敢英,上官帖,等.助镀剂中氯化镍对热浸镀锌层增重、厚度及形貌结构的影响[J].材料保护,2014,4(47):8-10.
2 故障分析
(1)故障原因:BTB1故障,不能正常吸合。
(2)故障现象有两个状态。
①飞机电源系统转换到APU发电机后,Bus transfer switch 在Auto位,左Transfer bus off灯亮,地面低流量音响警告报警。
②飞机电源系统转换到APU发电机后,Bus transfer sw itch 在OFF位,左Transfer bus of f灯亮,地面低流量音响警告无报警。
(3)具体分析:参考S SM 21-27-31/21 S SM 24-32-11。
设备冷却正常供气扇由115V XFR bus 2供电;设备冷却正常排气扇由115V XFR bus 1供电。
供气风扇低流量传感器由28V DC BUS 2供电;排气风扇低流量传感器由28V DC BUS 1。
当故障发生后,BTB1不能正常吸合,115V XFR bus 1断电,同样的28V DC BUS 1也断电,而115V XFR bus 2和28V DC BUS 2供电正常。
而设备冷却电门都设置在正常位,此时供气扇工作正常,而排气风扇不工作。
当Bus Tra ns fer s w it ch置AUTO位,而此时28V DC BUS 1断电,且28V DC BUS 2供电正常,那么R9 DC bus tie relay自动吸合,将28V DC BUS 1与28V DC BUS 2并联供电。
此时设备冷却的供气和排气低流量传感器供电电源都正常。
由于设备冷却排气风扇不工作,排气管路内的空气流量立即减少,空气温度会在几分钟内明显上升,而此时排气低流量传感器电源工作正常,探测数据到达警告值后,系统会产生低流量音响警告。
当Bus Transfer switch置OFF位,那么R9 DC bus tie relay会始终保持断开状态,将28V DC BUS 1与28V DC BUS 2隔离。
此时排气风扇低流量传感器供电电源断电,无论排气管路是否有低流量情况,传感器都不会输出警告信号。
3 结论
(1)类似故障原因主要集中在GCU和BTB。
可以首先考虑对串GCU或者拔掉GCU跳开关使GCU进入故障安全模式来隔离故障。
(2)GCU故障可能性较大,随着改装的进行GCU可靠性大大提高。
由于BT B进行了改装,辅助触点由原来的接线片连接方式,更改为现在的插钉连接方式,这个可能会对BTB部件可靠性有所影响。
参考文献
[1] 波音公司,B737-600/700/800/900飞机维修手册D633A101-SHC[Z].2014.
[2] 737NG -F T D -32-05007 O p e r at or E x p e r ie nc e R e q u e s t e d P o s t S 138 P/N 426H E 13-8 I n c o r p o r a t i o n [E B /O L ].h t t p s ://w w ,2005-11-15.
[3] 波音公司,B737-600/700/800/900飞机系统原理手册D280A282-SHG[Z].2014.。