火箭弹的表面处理
航空航天领域的材料表面处理技术

航空航天领域的材料表面处理技术航空航天领域是对材料要求极高的工业领域,其材料表面处理技术的发展对于航空航天行业的进步至关重要。
本文将介绍航空航天领域的材料表面处理技术的重要性以及各种处理技术的应用。
一、引言航空航天领域是高度发展和技术密集的工业领域,在此领域中,材料的强度、耐磨损性、防腐蚀性等性能要求非常高。
材料表面处理技术能够改善材料的性能,提高其使用寿命和可靠性。
二、机械加工机械加工是航空航天领域最常用的表面处理技术之一。
通过切削、研磨等机械方法,可以去除材料表面的氧化层、污染物和缺陷,提高表面的光洁度。
同时,机械加工还可以改变材料表面的形状和尺寸,满足航空航天领域对复杂零件的要求。
三、热处理热处理是航空航天领域常用的表面处理技术之一。
通过加热和冷却的方式,改变材料的晶体结构和组织状态,从而改善硬度、强度和耐腐蚀性能。
热处理常用于航空航天领域的金属材料,如铝合金、钛合金等。
四、电化学处理电化学处理是利用电化学反应改变材料表面性质的一种表面处理技术。
在航空航天领域中,常用的电化学处理方法包括电镀、阳极氧化、阳极电泳等。
这些方法可以在材料表面形成一层保护膜,提高表面的耐蚀性和耐磨损性。
五、涂层技术涂层技术是航空航天领域广泛应用的一种表面处理技术。
通过在材料表面涂覆一层特殊的涂层,可以改变材料的性质和特性,如防腐蚀涂层、耐高温涂层等。
涂层技术可以提高材料的耐磨性、耐蚀性和耐高温性,保护航空航天器件在复杂环境中的工作正常。
六、表面涂层表面涂层是航空航天领域常用的一种表面处理技术。
通过在材料表面形成一层保护膜,可以增加材料的机械性能和化学稳定性。
表面涂层可以有效提高材料的抗磨损性、耐蚀性和耐高温性能,延长材料的使用寿命。
七、总结航空航天领域的材料表面处理技术是保证飞行器安全可靠的重要手段。
机械加工、热处理、电化学处理、涂层技术以及表面涂层等各种技术的应用,为航空航天器件的性能提升提供了有效的解决方案。
火箭弹战斗部壳体机械加工工艺要求及夹具研发设计方案
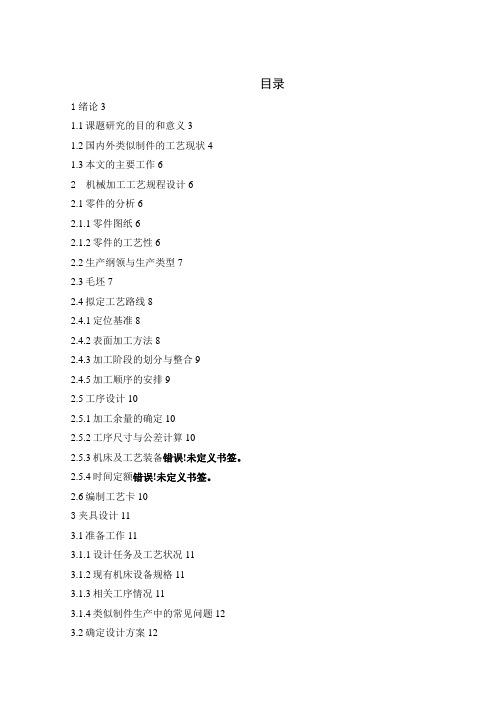
目录1绪论31.1课题研究的目的和意义31.2国内外类似制件的工艺现状41.3本文的主要工作62 机械加工工艺规程设计62.1零件的分析62.1.1零件图纸62.1.2零件的工艺性62.2生产纲领与生产类型72.3毛坯72.4拟定工艺路线82.4.1定位基准82.4.2表面加工方法82.4.3加工阶段的划分与整合92.4.5加工顺序的安排92.5工序设计102.5.1加工余量的确定102.5.2工序尺寸与公差计算102.5.3机床及工艺装备错误!未定义书签。
2.5.4时间定额错误!未定义书签。
2.6编制工艺卡103夹具设计113.1准备工作113.1.1设计任务及工艺状况113.1.2现有机床设备规格113.1.3相关工序情况113.1.4类似制件生产中的常见问题123.2确定设计方案123.2.1多种设计方案123.2.2设计方案的确定错误!未定义书签。
3.3结构草图与相关计算错误!未定义书签。
3.3.1结构草图的改进过程错误!未定义书签。
3.3.2相关计算错误!未定义书签。
3.4总图绘制与校对123.5零件图的绘制与校对133.6本章小结134结论14参考文献15致谢错误!未定义书签。
1绪论1.1课题研究的目的和意义战斗部壳体是火箭弹弹体的重要组成部分。
它的主要功用是用来装载火工品,连接火箭帽、固体发动机等其它部件,并承受它们的载荷[1]。
火箭弹战斗部壳体为内部装载的火工品提供正常工作条件的,如气压、温度、湿度和耐振性等要求;火箭弹产品战争储备量很大,要求全弹各壳体,尤其是战斗部壳体,具有耐储运等特点[2]。
由于战场环境的不断改变,各类型,各用途的火箭弹层出不穷,并由单一用途向多用途,多功能的方向发展,产品更新换代的年限呈减短趋势;近年来随着我国国防战略的转移,军工生产订单呈多品种,小批量的态势[ 3];所以这类产品的加工工艺研究就要强调技术的继承性、设备的通用性。
作为传统加工工艺的机加工在导弹舱体制造中主要有两种方式:1.如空射火箭弹、单兵火箭弹、防空火箭弹等小型火箭弹的机加工多采用厚壁管材作为毛坯,经过机械加工而成[2];2.一些稍大型火箭整体舱体的加工多采用旋压(拉深)毛坯由机加工精加的方式制造,而由于旋压与拉深相比具有模具简单、制造工序少等优点,所以旋压后机加工方式被更多的采用。
表面处理技术在航空航天材料耐腐蚀中的应用案例分析

表面处理技术在航空航天材料耐腐蚀中的应用案例分析表面处理技术在航空航天材料耐腐蚀中的应用案例分析引言:航空航天工业作为高科技产业的代表,对材料性能的要求非常高。
在极端环境中,如高温、高压、高速和强腐蚀等条件下,材料的耐腐蚀性显得尤为重要。
为了增强航空航天材料的耐腐蚀性能,表面处理技术被广泛应用。
本文将通过分析几个真实的案例,探讨表面处理技术在航空航天材料耐腐蚀中的应用。
一、表面处理技术的概述表面处理技术是通过一系列的工艺手段,改善材料表面的物理和化学性质,以达到增强耐腐蚀性的目的。
常见的表面处理技术包括化学镀金、电镀、喷涂、电化学氧化和热处理等。
这些技术不仅可以提高材料的防腐性能,还可以改善材料的耐磨性、耐热性和耐疲劳性等性能。
二、电化学氧化技术在航空航天材料中的应用电化学氧化是一种常用的表面处理技术,通过在材料表面形成多孔的氧化层来提高耐腐蚀性。
对于航空航天材料,如铝合金和镁合金,经过电化学氧化处理后,可以形成均匀且致密的氧化层,从而增加材料的抗腐蚀能力。
以某飞机机身材料为例,该材料为高强度的铝合金,在飞行过程中,受到高温和高湿度等气候条件的侵蚀,容易发生腐蚀现象。
为了增加其耐腐蚀性,采用电化学氧化技术进行表面处理。
在电解液中,通过控制电流密度和电解时间等工艺参数,使得材料表面形成厚度合适的氧化层。
实际应用中,通过电化学氧化处理后的材料,经过腐蚀试验,耐腐蚀性能得到明显改善,可以在恶劣气候下长时间使用而不出现表面腐蚀现象。
三、化学镀金技术在航空航天电子器件中的应用在航空航天电子器件中,由于浸泡性液体的存在,器件表面容易遭受腐蚀。
为了提高电子器件的稳定性和耐腐蚀性,采用化学镀金技术进行表面处理。
化学镀金是一种将金属镀层通过化学反应的方法附着在基体材料表面的过程。
通过在器件表面形成一层金属镀层,可以有效阻止腐蚀介质对器件表面的侵蚀。
某航天卫星中的电子装备,长期工作在太空环境中,面临严峻的腐蚀挑战。
航空航天领域的材料表面处理技术

航空航天领域的材料表面处理技术航空航天领域是科技创新的重要领域之一,而材料表面处理技术在航空航天工程中起着不可忽视的作用。
本文将探讨航空航天领域的材料表面处理技术的应用和发展。
一、材料表面处理技术的意义材料表面处理技术是将各种材料经过一系列工艺加工,改变其表面性能的一种工程技术。
在航空航天领域中,材料表面处理技术的应用意义重大:首先,通过表面处理技术可以提高材料的耐腐蚀性能。
航空航天器在高空、外太空等恶劣环境下飞行,表面会受到各种腐蚀介质的侵蚀,因此需要选用具有良好耐蚀性的材料,并进行适当的表面处理,从而提高其抵抗腐蚀的能力。
其次,材料表面处理技术能够提高材料的抗疲劳性能。
航空航天器在长时间高载荷工作状态下易产生疲劳裂纹,而通过表面处理技术可以增加材料的表面硬度,减少表面裂纹的产生,从而提高材料的抗疲劳性能。
最后,通过表面处理技术可以改善材料的润滑性能。
在航空航天领域中,如发动机润滑系统中的摩擦副、飞机降落装置等都需要具备良好的润滑性能,通过表面处理技术可以在材料的表面形成润滑膜,减少磨损和摩擦。
二、航空航天领域常见的材料表面处理技术1. 电化学氧化电化学氧化是一种利用电解法形成氧化物膜的表面处理技术。
该技术主要适用于铝合金材料,在航空航天领域中被广泛应用。
电化学氧化可以形成一层致密、均匀的氧化膜,提高材料的耐腐蚀性和抗疲劳性能。
2. 化学镀化学镀是通过化学方法将金属沉积在基材表面的一种处理技术。
在航空航天领域中,常用的化学镀技术包括镀铬、镀银等。
这些镀层能够提高材料的耐蚀性、硬度和润滑性能,同时还能够改善材料的外观。
3. 等离子体喷涂等离子体喷涂是一种将材料以等离子体的形式喷射到基材表面的技术。
在航空航天领域中,等离子体喷涂主要用于提高材料的抗磨损性能、隔热性能和润滑性能等。
常见的喷涂材料有陶瓷、金属合金等。
三、航空航天领域材料表面处理技术的发展趋势随着航空航天领域的不断发展,材料表面处理技术也在不断创新和发展。
火箭弹战斗部壳体机械加工工艺规程及夹具方案设计书
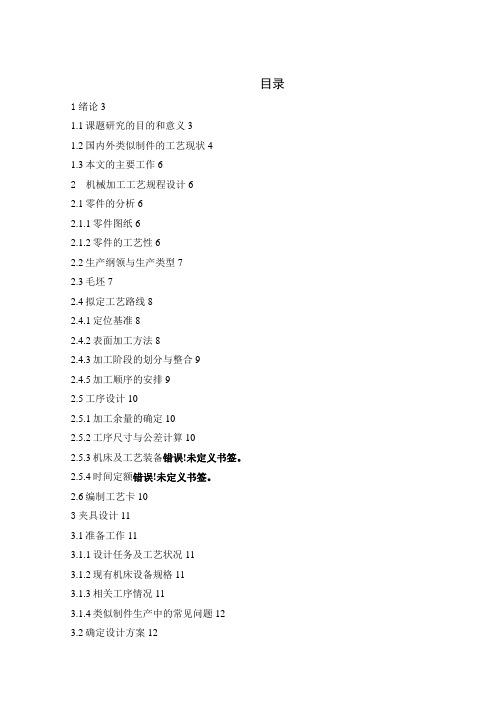
目录1绪论31.1课题研究的目的和意义31.2国内外类似制件的工艺现状41.3本文的主要工作62 机械加工工艺规程设计62.1零件的分析62.1.1零件图纸62.1.2零件的工艺性62.2生产纲领与生产类型72.3毛坯72.4拟定工艺路线82.4.1定位基准82.4.2表面加工方法82.4.3加工阶段的划分与整合92.4.5加工顺序的安排92.5工序设计102.5.1加工余量的确定102.5.2工序尺寸与公差计算102.5.3机床及工艺装备错误!未定义书签。
2.5.4时间定额错误!未定义书签。
2.6编制工艺卡103夹具设计113.1准备工作113.1.1设计任务及工艺状况113.1.2现有机床设备规格113.1.3相关工序情况113.1.4类似制件生产中的常见问题123.2确定设计方案123.2.1多种设计方案123.2.2设计方案的确定错误!未定义书签。
3.3结构草图与相关计算错误!未定义书签。
3.3.1结构草图的改进过程错误!未定义书签。
3.3.2相关计算错误!未定义书签。
3.4总图绘制与校对123.5零件图的绘制与校对133.6本章小结134结论14参考文献15致谢错误!未定义书签。
1绪论1.1课题研究的目的和意义战斗部壳体是火箭弹弹体的重要组成部分。
它的主要功用是用来装载火工品,连接火箭帽、固体发动机等其它部件,并承受它们的载荷[1]。
火箭弹战斗部壳体为内部装载的火工品提供正常工作条件的,如气压、温度、湿度和耐振性等要求;火箭弹产品战争储备量很大,要求全弹各壳体,尤其是战斗部壳体,具有耐储运等特点[2]。
由于战场环境的不断改变,各类型,各用途的火箭弹层出不穷,并由单一用途向多用途,多功能的方向发展,产品更新换代的年限呈减短趋势;近年来随着我国国防战略的转移,军工生产订单呈多品种,小批量的态势[ 3];所以这类产品的加工工艺研究就要强调技术的继承性、设备的通用性。
作为传统加工工艺的机加工在导弹舱体制造中主要有两种方式:1.如空射火箭弹、单兵火箭弹、防空火箭弹等小型火箭弹的机加工多采用厚壁管材作为毛坯,经过机械加工而成[2];2.一些稍大型火箭整体舱体的加工多采用旋压(拉深)毛坯由机加工精加的方式制造,而由于旋压与拉深相比具有模具简单、制造工序少等优点,所以旋压后机加工方式被更多的采用。
火箭弹热防护隔热涂层的选用与设计

火箭弹热防护隔热涂层的选用与设计火箭弹鹽Bfi护蹈翹涂层前选用与设计于互委颖孚耀任淮陇(北方导航控制技术股份有限公司)摘要:新型火箭弹热防护隔热涂层对火箭弹的安全至关重要。
提出了新型火箭弹热防护隔热涂层的选用与设计方法和基本流程。
针对火箭弹热防护实际使用需求,对已有热防护隔热涂层进行调研,从常规性能着手分析和论证,然后进行初步设计、主要性能检测,最后通过专项试验验证完成热防护隔热涂层最终设计。
该热防护隔热涂层选用设计方法已经应用于某一军工型号项目,并得到了有效验证。
利用该方法可以提高火箭弹热防护的研制效率、降低研制成本。
夷键词:火箭弹热防护隔热涂层选用与设计近几年,作为陆军主要作战装备之一的制导冲刷性能好;火箭弹在常规兵器制导化的趋势下,得到了迅速发展。
随着制导与控制技术的发展,火箭弹的射程不断增加,飞行的最大马赫数和飞行时间也不断增大,其承受的热环境日趋恶劣,热流密度的增大导致气动加热冲刷严重。
高速气流的冲蚀使火箭弹表面材料极易受损,从而破坏表面结构并影响舱内仪器的可靠工作,进而影响火箭弹的安全。
因此火箭弹外表面的热防护隔热涂层选用与设计尤为重要,通过何种有效途径和方法能够快捷的选用和设计合适的热防护隔热涂层,是现阶段火箭弹热防护急需解决的问题之一。
1隔热涂层的特点及主要性能指标热防护隔热涂层一般采用喷涂或刷涂的方式涂敷在火箭弹仪器舱或主要部件的外壁以达到隔热的目的,降低热流对火箭弹本体的影响。
对涂层的要求主要有:(1)良好的附着力、抗振动、耐烧蚀,抗(2)低密度、低热导率、高比热容,在燃气及气动高温环境下,热矢量低;(3)在保持良好的隔热效果的同时,需满足火箭弹的气动外形要求;(4)强度较高,抗压、抗划、具有较强的抗冲击性能;(5)环境适应性强,贮存性好;(6)施工工艺性好,质量稳定性和一致性好;(7)经济性好,成本可控。
针对隔热涂层的特点,选取一些指标作为隔热涂层的主要性能技术指标,见表1。
火箭弹战斗部壳体机械加工工艺要求及夹具研发设计方案
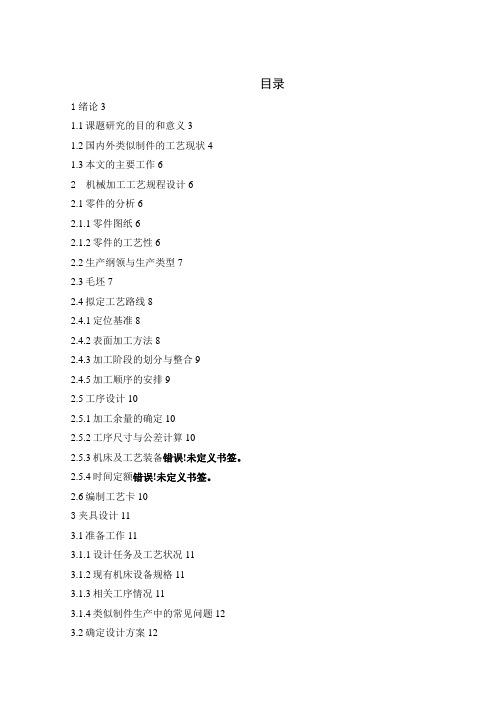
目录1绪论31.1课题研究的目的和意义31.2国内外类似制件的工艺现状41.3本文的主要工作62 机械加工工艺规程设计62.1零件的分析62.1.1零件图纸62.1.2零件的工艺性62.2生产纲领与生产类型72.3毛坯72.4拟定工艺路线82.4.1定位基准82.4.2表面加工方法82.4.3加工阶段的划分与整合92.4.5加工顺序的安排92.5工序设计102.5.1加工余量的确定102.5.2工序尺寸与公差计算102.5.3机床及工艺装备错误!未定义书签。
2.5.4时间定额错误!未定义书签。
2.6编制工艺卡103夹具设计113.1准备工作113.1.1设计任务及工艺状况113.1.2现有机床设备规格113.1.3相关工序情况113.1.4类似制件生产中的常见问题123.2确定设计方案123.2.1多种设计方案123.2.2设计方案的确定错误!未定义书签。
3.3结构草图与相关计算错误!未定义书签。
3.3.1结构草图的改进过程错误!未定义书签。
3.3.2相关计算错误!未定义书签。
3.4总图绘制与校对123.5零件图的绘制与校对133.6本章小结134结论14参考文献15致谢错误!未定义书签。
1绪论1.1课题研究的目的和意义战斗部壳体是火箭弹弹体的重要组成部分。
它的主要功用是用来装载火工品,连接火箭帽、固体发动机等其它部件,并承受它们的载荷[1]。
火箭弹战斗部壳体为内部装载的火工品提供正常工作条件的,如气压、温度、湿度和耐振性等要求;火箭弹产品战争储备量很大,要求全弹各壳体,尤其是战斗部壳体,具有耐储运等特点[2]。
由于战场环境的不断改变,各类型,各用途的火箭弹层出不穷,并由单一用途向多用途,多功能的方向发展,产品更新换代的年限呈减短趋势;近年来随着我国国防战略的转移,军工生产订单呈多品种,小批量的态势[ 3];所以这类产品的加工工艺研究就要强调技术的继承性、设备的通用性。
作为传统加工工艺的机加工在导弹舱体制造中主要有两种方式:1.如空射火箭弹、单兵火箭弹、防空火箭弹等小型火箭弹的机加工多采用厚壁管材作为毛坯,经过机械加工而成[2];2.一些稍大型火箭整体舱体的加工多采用旋压(拉深)毛坯由机加工精加的方式制造,而由于旋压与拉深相比具有模具简单、制造工序少等优点,所以旋压后机加工方式被更多的采用。
宇航应用中常见的表面处理方法综述

宇航应用中常见的表面处理方法综述宋燕,史广芹,董作典,唐旭,韩宝妮(航天科技集团五院西安分院,陕西西安710000)摘要:随着电子行业的快速发展,对元器件的表面处理提出了更高的要求。
首先结合表面处理的定义和目的,介绍了几种表面处理的方法,如机械表面处理、化学表面处理、电化学表面处理和现代表面处理;然后,在此基础上给出了宇航应用中常用的表面处理方法,并分析了各种方法的优缺点和适用性;最后,总结了宇航应用中常见的表面处理的失效模式及其对应的检验方法,对今后表面处理方法的合理选用具有一定的指导性。
关键词:表面处理方法;宇航应用;优缺点分析;失效模式中图分类号:TB 304文献标志码:A文章编号:1672-5468(2019)03-0078-04doi:10.3969/j.issn.1672-5468.2019.03.016Review of Common Surface Treatment Methods inAerospace ApplicationsSONG Yan ,SHI Guangqin ,DONG Zuodian ,TANG Xu ,HAN Baoni(Xi ’an Branch of the Fifth Academy of Astronautics ,Xi ’an 710000,China )Abstract :With the rapid development of the electronics industry ,higher requirements havebeen placed on the surface treatment of components.Firstly ,combined with the definition and purpose of surface treatment ,several surface treatment methods ,such as mechanical surface treatment ,chemical surface treatment ,electrochemical surface treatment ,and modern surface treatment ,are introduced.Then ,based on this ,the surface treatment methods commonly used in aerospace applications are given ,and the advantages and disadvantages and applicability of various methods are analyzed.Finally ,the failure modes of surface treatments commonly used in aerospace applications and their corresponding test methods are summarized ,which has certain guidance for the reasonable selection of surface treatment methods in future.Key words :surface treatment method ;aerospace application ;analysis of advantages and disad -vantages ;failure mode收稿日期:2018-08-14作者简介:宋燕(1988-),女,陕西西安人,航天科技集团五院西安分院工程师,硕士,主要从事宇航元器件质量保证和航天用微波类单机产品应用验证及寿命评估相关工作。
中大口径弹药表面防腐控制
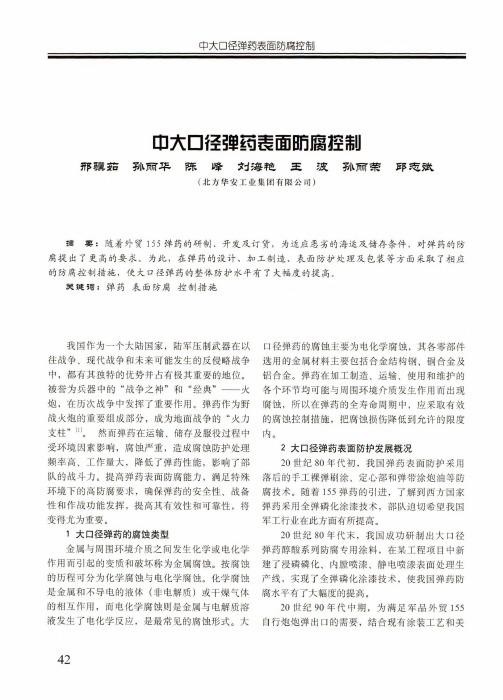
中大□径弾药表面防腐控制B穴口径弹药喪面Bfi腐桎制邢骥茄孙丽华陈峰対海艳王波孙丽荣邱志斌(北方华安工业集团有限公司)摘要:随着外贸155弹药的研制、开发及订货,为适应恶劣的海运及储存条件,对弹药的防腐提出了更高的要求。
为此,在弹药的设计、加工制造、表面防护处理及包装等方面采取了相应的防腐控制措施,使大口径弹药的整体防护水平有了大幅度的提高.笑澤词:弹药表面防腐控制措施我国作为一个大陆国家,陆军压制武器在以往战争、现代战争和未来可能发生的反侵略战争中,都有其独特的优势并占有极其重要的地位。
被誉为兵器中的“战争之神”和“经典”——火炮,在历次战争中发挥了重要作用。
弹药作为野战火炮的重要组成部分,成为地面战争的“火力支柱”山。
然而弹药在运输、储存及服役过程中受环境因素影响,腐蚀严重,造成腐蚀防护处理频率高、工作量大,降低了弹药性能,影响了部队的战斗力。
提高弹药表面防腐能力,满足特殊环境下的高防腐要求,确保弹药的安全性、战备性和作战功能发挥,提高其有效性和可靠性,将变得尤为重要。
1大口径弹药的腐蚀类型金属与周围环境介质之间发生化学或电化学作用而引起的变质和破坏称为金属腐蚀。
按腐蚀的历程可分为化学腐蚀与电化学腐蚀。
化学腐蚀是金属和不导电的液体(非电解质)或干燥气体的相互作用,而电化学腐蚀则是金属与电解质溶液发生了电化学反应,是最常见的腐蚀形式。
大口径弹药的腐蚀主要为电化学腐蚀,其各零部件选用的金属材料主要包括合金结构钢、铜合金及铝合金。
弹药在加工制造、运输、使用和维护的各个环节均可能与周围环境介质发生作用而出现腐蚀,所以在弹药的全寿命周期中,应采取有效的腐蚀控制措施,把腐蚀损伤降低到允许的限度内。
2大口径弹药表面防护发展概况20世纪80年代初,我国弹药表面防护采用落后的手工裸弹刷涂、定心部和弹带涂炮油等防腐技术。
随着155弹药的引进,了解到西方国家弹药采用全弹磷化涂漆技术,部队迫切希望我国军工行业在此方面有所提高。
航空航天材料表面处理技术研究
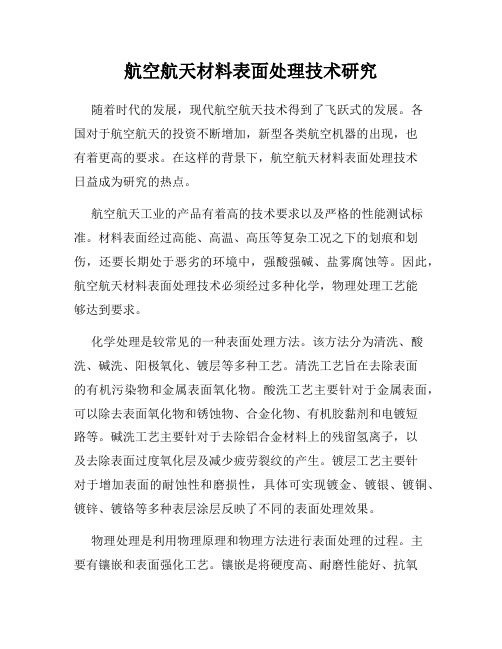
航空航天材料表面处理技术研究随着时代的发展,现代航空航天技术得到了飞跃式的发展。
各国对于航空航天的投资不断增加,新型各类航空机器的出现,也有着更高的要求。
在这样的背景下,航空航天材料表面处理技术日益成为研究的热点。
航空航天工业的产品有着高的技术要求以及严格的性能测试标准。
材料表面经过高能、高温、高压等复杂工况之下的划痕和划伤,还要长期处于恶劣的环境中,强酸强碱、盐雾腐蚀等。
因此,航空航天材料表面处理技术必须经过多种化学,物理处理工艺能够达到要求。
化学处理是较常见的一种表面处理方法。
该方法分为清洗、酸洗、碱洗、阳极氧化、镀层等多种工艺。
清洗工艺旨在去除表面的有机污染物和金属表面氧化物。
酸洗工艺主要针对于金属表面,可以除去表面氧化物和锈蚀物、合金化物、有机胶黏剂和电镀短路等。
碱洗工艺主要针对于去除铝合金材料上的残留氢离子,以及去除表面过度氧化层及减少疲劳裂纹的产生。
镀层工艺主要针对于增加表面的耐蚀性和磨损性,具体可实现镀金、镀银、镀铜、镀锌、镀铬等多种表层涂层反映了不同的表面处理效果。
物理处理是利用物理原理和物理方法进行表面处理的过程。
主要有镶嵌和表面强化工艺。
镶嵌是将硬度高、耐磨性能好、抗氧化性能好、低摩擦系数的金属挤压到基体表面。
表面强化工艺主要包括氮化、碳化、镀膜等。
以飞机起落架上使用的氮化钢为例,将其放进高温、高压的氮气中加热,让氮气分解并在钢材表面沉积形成硬度高的物理膜,来保证其悬挂的坚硬性和抗蚀性。
通过化学和物理处理,可使航空航天材料的表面得到有效的处理和保护,具备更高的防腐蚀性、减少自然环境对材料的损耗,同时确保了产品的可靠性、耐久性、安全性等提高材料表面性能一方面能够增加使用寿命,另一方面能够大幅降低使用成本和维护费用。
在未来,随着科技的进一步发展,航空航天工业的要求会更高,相应的航空航天材料表面处理技术也会得到进一步的研究和发展,为现代航空航天技术的飞跃发展奠定了坚实的基础。
表面处理技术在航天材料中的应用

表面处理技术在航天材料中的应用一、表面处理技术在航天材料中的应用1、引言航天材料是登陆空间过程的基础,表面处理技术在航天材料中的应用,是对航天材料性能的改进和确保,在航天材料中占有重要地位。
现介绍十大表面处理技术,并进行分析。
2、常用的表面处理技术(1)表面处理技术之一:涂层涂层一般指将一层外部附加物置于航天材料上以增加硬度、耐腐蚀性能以及耐磨损性能等。
常用的有氧化处理、氟化处理、碳化处理、涂焊、渗漆、镀(电镀、氧化镀、磷化镀)、复合涂层、熔覆及热浸涂料等。
(2)表面处理技术之二:电解处理电解处理是指用电流对金属表面进行化学变化或物理变化的工艺。
通过电解处理可以改变表面的形貌,增加表面的耐腐蚀性、抗疲劳性、抗冲击性等。
(3)表面处理技术之三:离子轰击离子轰击是指把压缩气体中极其稀薄的氧离子拥挤在管道中,形成低压、高强度的气体离子流,以求达到改善航天材料性能的目的。
通过离子轰击处理,可以提高表面硬度、改善表面抗摩擦性能、抗冲击性及耐腐蚀性能。
(4)表面处理技术之四:电离处理电离处理是指利用电子和离子束引起的电电离,电电离产生的热量可以使表面膜形成液膜,以求达到改善航天材料性能的目的。
(5)表面处理技术之五:电弧处理电弧处理是指利用电弧热量使航天材料的表面产生化学变化,以达到形变、硬化和改善表面抗摩擦性能的目的。
(6)表面处理技术之六:喷涂喷涂是指将填充材料和固化材料凝胶形成的喷雾,通过喷嘴的控制,喷洒到航天材料表面,以改善表面抗摩擦性能、抗冲击性能及耐腐蚀性能。
(7)表面处理技术之七:超声处理超声处理是指利用超高频的声波对航天材料表面进行处理,以求达到增强表面抗摩擦性、抗冲击性及耐腐蚀性能的目的。
(8)表面处理技术之八:激光处理激光处理是指利用激光能量的影响,改变航天材料表面的形貌,以达到改善表面性能的目的。
(9)表面处理技术之九:化学处理化学处理是指利用化学反应的影响,改变航天材料表面的形貌,以达到改善表面性能的目的。
航空航天材料表面处理技术的研究与应用

航空航天材料表面处理技术的研究与应用随着航空航天技术的不断发展,对材料品质和表面性能的要求越来越高,因此航空航天材料表面处理技术的研究和应用也显得愈加重要。
表面处理技术可以改善材料的外观、机械性能、耐腐蚀性、抗疲劳性、耐热性等方面。
因此,在航空航天领域中,表面处理技术不仅仅是个重要环节,更是提高飞行安全、降低维护成本的必要手段。
在航空航天领域中,除了一些常规的表面处理技术,如喷砂、电镀、喷漆等,还有一些高端、前沿的表面处理技术,如等离子增强化学气相沉积、离子束抛光、离子注入等。
等离子增强化学气相沉积技术是一种利用等离子体在材料表面沉积物质的方法。
这种方法可以在材料表面形成非常均匀,致密,导电的薄膜。
利用这种技术,可以在航空航天中制造各种功能性材料,如防热材料、防腐蚀材料、磨损耐用材料等。
另外,离子束抛光技术也是航空航天领域中非常重要的表面处理技术之一。
这种技术可以通过高能离子的撞击,将材料表面微缩到几纳米甚至更小的尺度,形成非常平滑、致密、无氧化物等的表面。
而这种表面不仅具有均匀性和精细度高,而且还可以提高材料的机械性能、热稳定性、防腐蚀性等多种性能。
离子注入技术也是航空航天领域的重要表面处理技术之一。
这种技术可以通过将离子注入材料表面,而使得材料表面的化学成分和物理性质得到改变,从而提高其性能。
这种技术可以制作出表面淬火、硬化、氮化、碳化等特殊材料,从而极大提高材料的使用寿命和机械性能。
总之,随着航空航天领域的不断发展,我们对于航空航天材料表面处理技术的研究和应用也需要越来越深入,同时还需要不断推陈出新,开发出更加高端、前沿的表面处理技术,以更好地服务于航空航天中的应用。
人工增雪的火箭弹成分
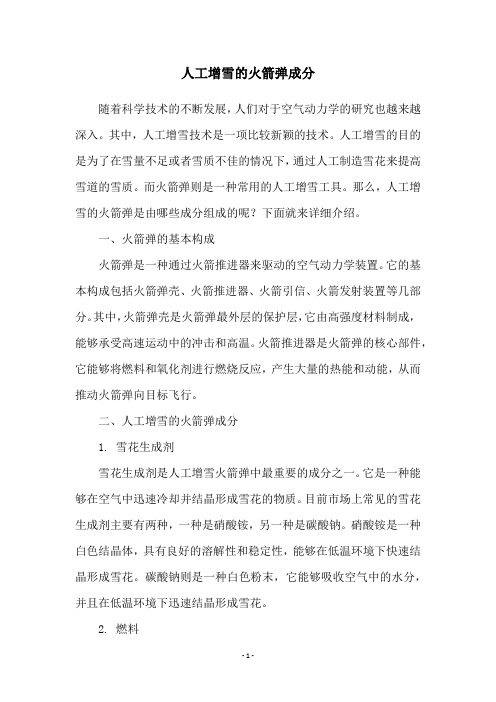
人工增雪的火箭弹成分随着科学技术的不断发展,人们对于空气动力学的研究也越来越深入。
其中,人工增雪技术是一项比较新颖的技术。
人工增雪的目的是为了在雪量不足或者雪质不佳的情况下,通过人工制造雪花来提高雪道的雪质。
而火箭弹则是一种常用的人工增雪工具。
那么,人工增雪的火箭弹是由哪些成分组成的呢?下面就来详细介绍。
一、火箭弹的基本构成火箭弹是一种通过火箭推进器来驱动的空气动力学装置。
它的基本构成包括火箭弹壳、火箭推进器、火箭引信、火箭发射装置等几部分。
其中,火箭弹壳是火箭弹最外层的保护层,它由高强度材料制成,能够承受高速运动中的冲击和高温。
火箭推进器是火箭弹的核心部件,它能够将燃料和氧化剂进行燃烧反应,产生大量的热能和动能,从而推动火箭弹向目标飞行。
二、人工增雪的火箭弹成分1. 雪花生成剂雪花生成剂是人工增雪火箭弹中最重要的成分之一。
它是一种能够在空气中迅速冷却并结晶形成雪花的物质。
目前市场上常见的雪花生成剂主要有两种,一种是硝酸铵,另一种是碳酸钠。
硝酸铵是一种白色结晶体,具有良好的溶解性和稳定性,能够在低温环境下快速结晶形成雪花。
碳酸钠则是一种白色粉末,它能够吸收空气中的水分,并且在低温环境下迅速结晶形成雪花。
2. 燃料燃料是火箭弹推进器中的关键成分之一。
它能够与氧化剂进行燃烧反应,产生大量的热能和动能,从而推动火箭弹向目标飞行。
目前市场上常见的火箭弹燃料主要有三种,一种是硝化棉,另一种是硝化纤维素,还有一种是高能燃料。
硝化棉和硝化纤维素是一种白色粉末,它们具有较高的燃烧速度和燃烧温度,能够产生大量的热能和动能。
而高能燃料则是一种新型的燃料,它具有更高的燃烧速度和燃烧温度,能够产生更大的热能和动能。
3. 氧化剂氧化剂是火箭弹推进器中另一关键成分。
它能够与燃料进行燃烧反应,产生大量的热能和动能,从而推动火箭弹向目标飞行。
目前市场上常见的氧化剂主要有两种,一种是硝酸铵,另一种是过氧化氢。
硝酸铵是一种白色结晶体,具有良好的溶解性和稳定性,能够与燃料进行燃烧反应,产生大量的热能和动能。
火箭弹的装配与验收

火箭弹的装配与验收火箭弹作为一种重要的军事武器装备,其装配与验收十分关键,决定了火箭弹的使用效能和安全性。
本文将从火箭弹装配的步骤和火箭弹验收的标准两个方面进行论述。
一、火箭弹的装配步骤1. 设计和准备在火箭弹装配前,需要进行详细的设计和准备工作。
包括火箭弹的外形尺寸、弹头结构、发动机选型等。
设计人员根据实际需求确定火箭弹的规格和性能指标,为装配过程提供依据。
2. 零部件制造与检验火箭弹是由许多零部件组成的,这些零部件的制造质量直接关系到火箭弹的稳定性和可靠性。
零部件制造过程中需要严格按照技术标准进行操作,并进行必要的质量检验。
对于关键零部件,还需要进行力学性能测试和材料分析等。
3. 组件装配火箭弹组件装配是将各个零部件按指定的顺序进行装配。
这一步骤需要高度专业的技术人员进行操作,确保装配的准确性和稳定性。
过程中应注意各个零部件之间的配合精度,确保装配的精度和质量。
4. 系统调试和测试火箭弹装配完成后,需要进行系统调试和测试。
包括对火箭弹的动力系统、引导系统、通信系统等进行检测和调试,确保各个系统的正常运行。
同时还需要对火箭弹进行静态和动态试验,验证其性能指标是否满足设计要求。
二、火箭弹的验收标准1. 外观检查对火箭弹进行外观检查,包括检查火箭弹外壳是否完好,表面是否有明显的损伤或油漆剥落等。
外观检查是判断火箭弹装配质量的第一步,也是基本的验收要求。
2. 尺寸和重量测量对火箭弹的尺寸和重量进行测量,确认其是否符合设计要求。
尺寸测量包括火箭弹的长度、直径等,重量测量包括火箭弹的空重和总重等。
测量过程中需要使用准确的测量工具和设备。
3. 弹头结构检查对火箭弹的弹头结构进行检查,包括弹头是否完整,装药是否填充到位等。
弹头是火箭弹的重要组成部分,其结构和装填情况直接影响火箭弹的作战效能和安全性。
4. 动力系统测试对火箭弹的动力系统进行测试,包括发动机点火测试和推力测试等。
测试过程中需要确保发动机的正常启动和运行,以及推力输出的稳定性和可靠性。
火箭弹的表面处理
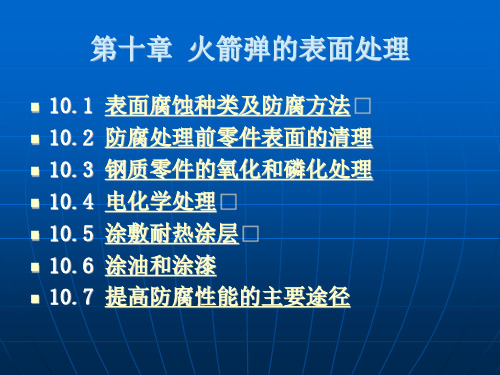
剂应尽量少加,电镀工作应正常,中间不能断电。
2.钝化处理
3.镀锌层的质量检验
下一页 返回
10.4.2 镀铬
一、概述 1.性质及用途 2.镀铬液的种类 二、镀硬铬 1.特点
(1) 镀层厚度要比普通镀铬厚几十至几百倍。(2) 电镀的时间长,电 流密度大。在模具设计时需考虑导入电流的损失。(3) 采用仿形阳极 或辅助阴极,改善镀层分布的均匀性.(4) 镀层需进行除氢处理。
下一页 返回
10.5.2 122 mm火箭弹隔热涂层发生的质量问 题及解决方法
1.
2.解决吸水、吸潮问题 涂层中含有水分是涂层在干燥固化过程中产生气泡、针孔的主要原因
之一。涂层中的水分主要来源于: ① 涂料生产中所用填料含有的水分。生产前应进行烘干处理,去除
水分。 ② 酒精的含水与吸水问题。GT-401涂料所用溶剂为无水酒精, 无水酒精(酒精含量99.5%)也含有少量水分,而且酒精容易吸水。所 以在涂料的生产和使用过程中,不可避免地要吸收部分水。改变涂料 溶剂为高沸点不吸水溶剂是解决涂料吸水的根本方法。 ③ 磷化层含 有一定量的水分,通过试验,涂敷前磷化层在230 ℃温度下,烘干30 min,对减少涂层起泡、针孔有一定效果。
1.有机类 (1) 有机硅树脂类 (2) 其他树脂类涂料 2.无机类耐热隔热涂料 3.涂敷工艺及影响涂敷质量的因素 (1) 涂敷前零件的表面处理 :① 内表面喷砂 ② 零件的磷化处理 ③
磷化层干燥 (2) 涂料的准备 (3) 涂敷 (4) 涂敷层的干燥固化 4.涂敷层的检验 (1) 外观检验 (2) 厚度检验
上一页 下一页 返回
10.1.3 防腐方法选择的原则
(1) (2) 防腐层必须有较好的化学稳定性及抗大气中各种腐蚀介质的侵蚀。
第一章 制造弹箭零件用的材料及毛坯种类的选择

b. 铝及铝合金 特点:密度小,一定的机械性能,良好的工 艺性能和高的耐腐蚀性。 应用领域:燃烧室、喷管等。 1.包括工业纯铝的热处理不强化型铝合金: 塑性较高,焊接性良好,耐蚀性强,用于载 荷不大的零件; 2.热处理强化型变形铝合金:制造负荷较大 的零件; 3.铸造铝合金:强度、塑性较低,制造负荷 不大、形状复杂的零件。
2. 优质碳素结构钢 按含碳量分类: 高碳钢:经调制处理后,有较好的综合机械性能, 用于承受负荷较大的零件,如中间底,防滑帽等。 中碳钢:经调质或正火使用,用于承受负荷较大而 要求有较高韧性的零件,如喷管,航空炮弹弹体, 曳光管、曳光管螺帽等。 低碳钢:塑性好和变形抗力低,适合于冷压力加 工,常用制作冲裁件、弯曲件、拉伸件等成型零 件,如药包夹、风帽、弹体、支持架、尾翼架等。 另焊接性能好,代替铆接或螺纹连接。
弹箭制造工艺学
第一章 材料及毛坯的选择
制造炮弹和火箭弹零件的材料主要根据两大 性能来选择 使用性能 工艺性能 a) 热冲压:高碳钢 b) 冷挤压:深冲钢 c) 冷冲压:塑性好,变形抗力低 d) 压力铸造:熔点低 此外,选择材料还要根据我国资源情况
1.1 黑色金属材料
a. 碳素结构钢(按用途和性能分) 1. 炮弹钢(热轧碳素钢) 主要用途:榴弹、特种弹以及杀爆火箭弹 战斗部弹体,头螺、底螺等。 材料性能:强度屈服点314~588MPa,塑性 断面收缩率>15% 加工方法:热压力加工(先制造毛坯)和机械 加工。 常用弹体材料:D60,58SiMn,60Si2Mn
d. 钼合金 性能:熔点高(2610℃),良好的高温强度、高温 延展性。最高使用温度可达2000 ℃。可制成板、棒 、 丝、管、带等各种形状。 主要用途:配气阀体、火箭喷管、喷管喉衬等。 e. 钽合金 性能:高强度、高熔点( 2985℃ )、高冲击阻抗 材料。 典型钽合金为钽钨合金:Ta4W和Ta8W。 主要用途:高性能电容器、核反应堆及EFP药型罩 。
基于等离子喷涂法的火箭弹尾翼热障涂层试验研究

基于等离子喷涂法的火箭弹尾翼热障涂层试验研究霍文娟;李龙飞;孔为民;刘巍浩【摘要】针对火箭弹飞行中尾翼遭受气动加热损伤而造成飞行失效的问题,通过分析其尾翼结构特征,设计了适应尾翼工况的热障涂层结构和等离子喷涂制备方法,分析了预处理对热障涂层与基体结合力的影响,以及等离子喷涂工艺参数对热障涂层沉积率的影响,并进行了热障涂层静态和动态测试试验.试验结果表明,该热障涂层与基体的结合强度由10 MPa提高至20 MPa,风洞试验中,热障涂层可以在1800 ℃高温和20 s时间内,克服气动热而不产生剥落.%The empennage suffers from damage for aerodynamic heating at rocket proj ectile flying,and the flying can be failed.Through analyzing the structure of empennage,the thermal barrier coating (TBC)structure and preparation method of plasma spray were designed,which suited for the working conditions of empennage.The influence of pretreatment on binding force of matrix and TBC were ana-lyzed,and the influence of plasma spraying process parameters on deposition rate of TBC was analyzed. The static and dynamic test of TBC was made.Test results show that the bonding strength of the modi-fied TBC with the matrix is increased from 10 MPa to 20 MPa,and TBC can overcome aerodynamic heat without peeling at 1 800 ℃ and in 20 s by the wind tunnel test.【期刊名称】《中北大学学报(自然科学版)》【年(卷),期】2018(039)002【总页数】6页(P200-205)【关键词】热障涂层;尾翼;火箭弹;等离子喷涂【作者】霍文娟;李龙飞;孔为民;刘巍浩【作者单位】晋西工业集团有限责任公司,山西太原030027;晋西工业集团有限责任公司,山西太原030027;中北大学工程训练中心,山西太原030051;晋西工业集团有限责任公司,山西太原030027【正文语种】中文【中图分类】TG156.990 引言随着火箭弹的发展,其飞行速度已经超过3 Ma,受粘性摩擦、速度阻滞和压力变化等,周围环境温度升高,并通过热传导、对流和辐射等方式传导在火箭弹上. 尤其在尾翼结构上,即使飞行时间短暂,气动加热也较严重,会降低尾翼结构材料的强度、刚度和翼面的承载能力,增大变形,结构中温度不均匀会产生热应力,可能使尾翼结构破坏,当驻点温度很高时,迎风面局部材料熔化,翼面破坏. 当尾翼遭受热损伤时,会导致火箭弹稳定性降低,飞行失效. 因此,高速飞行的火箭弹尾翼应采取热防护措施,主要包括采取尾翼耐热结构和热防护层两种方案. 其中,热障涂层(Thermal Barrier Coating, TBC)通过在基体表面涂覆具有高温隔热特性的材料,形成热障涂层,可以降低基体的工作温度[1-2],为火箭弹尾翼克服飞行气动热提供借鉴. 目前,热障涂层广泛应用于航空发动机,陶瓷层材料是6%~8% Y2O3(质量分数)部分稳定ZrO2(YSZ)[3]. 但是在火箭弹领域,鲜有使用热障涂层的相关报道. 本文讨论在尾翼钢制材料表面制备热障涂层防护的方案,尾翼经过热障涂层防护后应保持原有的气动外形,热障涂层的材料应有一定的强度,气动加热后,不应出现裂纹和崩落,隔热效果要优良,质量要小.1 尾翼结构分析尾翼迎风面结构如图 1 所示,迎风面是气动冲刷程度最恶劣,气动加热最为严重的部位,也是尾翼厚度最小,刚度强度最差的部位. 一般根据不同的气动加热程度选用不同的迎风面结构,通常有以下几种形式:① 迎风面金属材料和尾翼其他部位一致的整体结构式尾翼;② 迎风面采用耐高温金属材料并和尾翼其他部位固定连接的分体结构式尾翼;③ 铆接或胶接的蜂窝夹层结构式金属尾翼;④ 非金属尾翼.图 1 尾翼迎风面Fig.1 Windward side of empennage钛合金材料的整体结构式尾翼,飞行中尾翼刚度不足,且钛合金价格昂贵;迎风面为耐高温合金的分体式尾翼结构,制造工艺性差;酚醛树脂压塑成型的非金属尾翼,虽然隔热效果好,但易被高速气流冲刷掉. 本文选用材料为中碳钢的整体结构式尾翼,整体形状为变壁厚(2.5~7 mm)型材,迎风面厚度最小为 2.5 mm. 同时,该火箭弹尾翼不采用耐热结构,而选用尾翼表面涂覆热障涂层以实现飞行中的热防护. 为了提高涂层的可靠性,尾翼形状棱边应进行圆滑过渡,以避免直角造成的涂层应力和崩落,同时增大迎风面大圆角半径,降低飞行阻力并改善涂层制造工艺性.2 热障涂层的制备热喷涂是利用一定的热源将喷涂材料熔融或软化,借助热源本身动力或外加的压缩空气流,使喷涂材料雾化成微粒,形成快速粒子流,然后喷射到基体表面,获得涂层. 不同颗粒对涂层结构的形成发挥不同的作用,熔融及部分熔融大粒子可以直接影响涂层结构[4]. 涂层的结合机理包括涂层与基体的结合以及涂层与涂层的结合. 前者的结合强度称为结合力,后者的结合强度称为内聚力. 喷涂层是由无数变形粒子互相交错呈波浪式堆叠在一起的层状组织结构. 颗粒间不可避免的存在一部分孔隙或空洞,还可能存在氧化物或其他夹杂物[5]. 热障涂层制备工艺主要包括涂层结构设计、涂层成分选择和喷涂方法选择等.2.1 热障涂层结构热障涂层结构主要分为双层、多层[6]和功能梯度结构,其中双层结构的顶层是以ZrO2为主的陶瓷层,起隔热作用;底层为金属粘接层,起改善基体与陶瓷层物理相容性和抗氧化腐蚀的作用,如图 2 所示. 双层结构的热障涂层结构与制备工艺相对简单,耐热性较好,应用最广泛,能实现该尾翼的热防护.图 2 热障涂层结构Fig.2 Structure of thermal barrier coating2.2 热障涂层材料2.2.1 陶瓷涂层(工作层)热障涂层中的陶瓷涂层是尾翼克服气动加热的工作层,应具备以下性质:① 耐高温;② 低密度;③ 良好的抗热冲击性能;④ 相对较低的热导率;⑤ 高的化学稳定性;⑥ 较高的热膨胀系数. 目前,使用最广泛的陶瓷材料Y2O3部分稳定ZrO2(YSZ)具有高的热膨胀系数(最接近金属)和低的热导率(金属的1/10)[6-7],其XRD图谱如图 3 所示.图 3 陶瓷粉末(ZrO2)XRD图谱Fig.3 XRD spectrum of ceramic powder ZrO2 2.2.2 金属粘接层如果将氧化锆ZrO2直接喷涂在金属基体上,会导致涂层的脱落,不能起到任何防护作用,这是因为氧化锆ZrO2与金属基体的热膨胀系数不匹配,为解决上述问题,通常在金属基体和陶瓷涂层之间增加一层具有一定厚度的金属粘接层. 金属粘接层是热障涂层中的关键结构[7-8]. 金属粘接层材料一般选用MCrAlY(M为Ni 或NiCo)合金,这种材料的粘接层不仅能满足粘接要求,还能提高金属基体的抗氧化腐蚀性能.金属粘接层(NiCr)粉末XRD图谱如图 4 所示.图 4 金属粘接层(NiCr)粉末XRD图谱Fig.4 XRD spectrum of metal bonding layer powder NiCr2.3 热障涂层制备方法热障涂层的制备方法主要有等离子喷涂法(APS)、电子束物理气相沉积法(EB-PVD)、化学气相沉积法(CVD)3种. 本文采用等离子喷涂法[9],在等离子喷涂过程中,影响喷涂沉积率及质量的工艺参数很多,主要有:喷涂功率、送粉距离、送粉量、气体流量等,工艺参数之间互相影响.1) 表面预处理. 其工艺主要包括表面净化和表面粗化. 表面净化主要用于除去所有尾翼喷涂区域的油渍、砂粒等污垢,这些污垢严重影响涂层和金属基体的结合.去除污垢后的表面应小心保护,避免二次污染. 涂层与金属基体之间是依靠“撞击”来结合的,喷涂表面粗化的目的是粗糙金属基体表面,有利于涂层的附着.2) 大气等离子喷涂. 大气等离子喷涂简称等离子喷涂,通过等离子喷枪来实现. 喷枪的喷嘴(阳极)和电极(阴极)分别接电源的正、负极,喷嘴和电极之间通入工作气体,借助高频火花引燃电弧,将气体加热并使之电离,产生等离子弧,气体热膨胀由喷嘴喷出高速等离子射流. 送粉器将粉末从喷嘴内或外送入等离子射流中,粉末被加热到熔融或半熔融状态,被射流加速后以一定的速度喷射到经预处理的基体表面形成涂层. 等离子喷涂可以制备具有耐磨、耐腐蚀、耐高温氧化、隔热等性能的涂层. 采用等离子电弧的高温热源,可减少孔隙、夹杂物等涂层制备中的缺陷.3) 喷涂功率控制. 等离子射流作为粒子加热、加速的媒介,喷涂功率决定等离子射流. 如果喷涂功率过小,则粉末熔融不好、不充分,粉末碰撞工件时变形不充分,并有较多的粉末反弹损失,降低了沉积效率,且涂层与基体结合不牢;反之,虽然粉末融化和撞击变形良好,但粉末受热氧化腐蚀太多. 喷枪是完成等离子喷涂过程的核心设备之一,不同型号的喷枪具有自身的特点及要求,功率参数应满足其所用设备的要求.4) 送粉距离控制. 喷枪送粉距离决定粉末颗粒在等离子射流中的起点,起点位置发生改变后,粒子加热、加速历程随之变化,影响其达到基体前的温度、速度,从而使涂层性能发生改变. 喷涂距离过大,粒子温度、速度均下降导致结合力、沉积效率下降;反之,粒子温度、速度高导致基体、粒子出现高温氧化,影响涂层性能.5) 送粉量控制. 送粉量必须与功率相适应,送粉量过大,会出现粉末熔融不充分,造成夹生、层片粘接状况不佳,导致喷涂效率过低;送粉量过小,粉末氧化严重,造成基体温度过高,同样导致喷涂效率过低.6) 气体流量控制. 等离子喷涂所用气体分两种,一种称为主气,气体流量大小直接影响等离子焰流的流速和热焓. 如果流量过高,气体不仅会带走等离子射流中的更多热量,而且会使喷涂粒子速度加快,减少了在等离子焰流中的时间,导致喷涂粒子不能达到变形所需要的熔融或半熔融状态,使得涂层组织疏松,孔隙率增加;相反,流量过低会降低喷涂粒子速度,容易引起喷嘴和阴极烧损.3 试验研究3.1 基体表面净化及粗糙度对涂层质量的影响根据实验分析基体表面粗糙度及净化表面对涂层质量的影响,以制定合理的工艺,实验结果如表 1 所示.在静态烧蚀试验中,方案1和2的涂层剥落, 如图 5 所示. 可以得到如下结论:增大粗糙度能大幅提高金属粘接层与金属基体的结合强度,当Ra≥8.0 μm,结合强度可达到 22 MPa;净化表面方式中,超声波水洗不如空气吹效果好. 通过选择合理的表面粗化参数和表面净化方式,使得尾翼热障涂层与基体的结合强度由10 MPa(当8.0 μm≥Ra≥5.0 μm) 提高至20 MPa.表 1 方案1~3的尾翼状态Tab.1 Empennage conditions of scheme from oneto three方案基体表面粗糙度Ra/μm结合强度/MPa备注1≤5.05~825.0~8.09~123≥8.018~22采用超声波水洗、空气吹图 5 热障涂层剥落示意图Fig.5 Peeling of thermal barrier coating3.2 喷涂参数对沉积效率的影响热障涂层沉积效率试验是将100 g涂层粉末全部喷涂在一块经过表面预处理且重量确定的钢板上,该涂层粉末的沉积率就是钢板喷上粉末后的总重量与钢板重量的差值和钢板重量的百分比,试验示意图如图 6 所示. 沉积率高可提高涂层的致密性,降低孔隙率,改善涂层性能. 在该尾翼涂层中沉积率为40%较好.图 6 沉积率试验示意图Fig.6 Diagram of deposition rate test3.2.1 喷涂功率的影响通过试验,分析相同参数下不同的喷涂功率对涂层沉积率的影响,以制定合理的喷涂功率. 试验方案见表 2.表 2 方案1~6的喷涂参数Tab.2 Spraying process parameters of scheme from one to six方案粉末功率/kW距离/mm送粉量/(g·min-1)123NiCr底粉20253010040456ZrO2面粉35404510040测量钢板的增重可以得出:方案3的沉积率最高,即NiCr底粉喷涂功率选用30 kW;方案5的沉积率最高,即ZrO2面粉喷涂功率选用40 kW.3.2.2 喷涂距离的影响分析相同参数下不同的喷涂距离对沉积率的影响,以制定合理的喷涂距离. 试验方案见表 3.表 3 方案7~12的喷涂参数Tab.3 Spraying process parameters of scheme from seven to twelve方案粉末功率/kW距离/mm送粉量/(g·min-1)789NiCr 底粉3010011012040101112ZrO2面粉4010011012040测量钢板的增重可以得出:方案9的沉积率最高,即NiCr底粉喷涂距离选用120 mm;方案11的沉积率最高,即ZrO2面粉喷涂距离选用110 mm.3.2.3 送粉量的影响分析相同参数下不同的送粉量对沉积率的影响,以制定合理的送粉量. 试验方案见表 4.表 4 方案13~18的喷涂参数Tab.4 Spraying process parameters of scheme from thirteen to eighteen方案粉末功率/kW距离/mm送粉量/(g·min-1)131415NiCr底粉30120303540161718ZrO2面粉40110303540测量钢板的增重得出:方案13的沉积率最高,即NiCr底粉送粉量选用30g/min;方案18的沉积率最高,即ZrO2面粉送粉量选用40 g/min.3.3 最佳喷涂参数根据以上试验研究,本文尾翼热障涂层等离子喷涂参数确定如表 5 所示.表 5 最佳喷涂参数Tab.5 The best praying process parameters粉末功率/kW距离/mm送粉量/(g·min-1)NiCr底粉3012030ZrO2面粉40110403.4 静态试验采用自制的氧乙炔加热装置模拟加热环境,即热流随时间变化,被加热的尾翼热障涂层处于静止状态,并通过热电偶测试尾翼涂层迎风面上、中、下3处的表面温度,须达到1 950 ℃的高温,加热时间持续60 s,空冷30 min. 通过尾翼地面烧蚀试验表明,涂层没有裂纹、剥落,如图 7 所示.图 7 尾翼地面烧蚀试验结果Fig.7 Test result of empennage ablation in the ground3.5 动态试验在高速风洞中模拟气动加热温度和气流速度,但由于气流密度小,动压小,只能模拟部分冲刷情况. 有研究表明,直径大于30 μm的粒子能对尾翼造成明显的冲蚀磨损[10]. 动态试验表明,在1 800 ℃高温和20 s时间内,热障涂层状态完好,如图 8 所示.图 8 地面热风洞试验结果Fig.8 Test result of hot wind tunnel in the ground4 结论等离子喷涂制备的尾翼热障涂层解决了火箭弹飞行中尾翼气动加热工作失效的问题,通过工程化研究,试验结果表明:1) 通过选择合理的表面粗化参数和表面净化方式,使得尾翼热障涂层与基体的结合强度由10 MPa 提高至20 MPa.2) 动态风洞试验中,热障涂层可以在1 800 ℃ 时,时间20 s内,克服气动热,热障涂层无剥落,尾翼整体无变形,承载能力提高.3) 合理的尾翼结构有助于提高热障涂层的附着力,改善涂层性能.参考文献:[1] 周洪,李飞,何博,等. 等离子喷涂热障涂层的隔热性分析[J]. 中国有色金属学报, 2007, 17(10): 1609-1615.Zhou Hong, Li Fei, He Bo, et al. Analyses on thermal barrier effects of zirconia based thermal barrier coatings[J]. The Chinese Journal of Nonferrous Metals, 2007, 17(10): 1609-1615. (in Chinese)[2] 何箐,汪瑞军,邹晗,等. 不同结构8YSZ热障涂层对CMAS沉积物的防护作用[J]. 中国表面工程, 2016, 29(4): 86-95.He Qing, Wang Ruijun, Zou Han, et al. Protective effects of 8YSZ TBCs with different microstructures against CMAS deposits[J]. China Surface Engineering, 2016, 29(4): 86-95. (in Chinese)[3] 袁小虎,郭洪波, 彭徽,等. Gd2Zr2O7陶瓷的高温热物理性能及Gd2Zr2O7-8YSZ双涂层制备[J]. 复合材料学报, 2013, 3(5): 138-143.Yuan Xiaohu, Guo Hongbo, Peng Hui, et al. High temperature thermo-physical properties of and preparation of a novel thermal barrier coating Gd2Zr2O7-8YSE[J]. Acta Materiae Compositae Sinica, 2013, 3(5): 138-143. (in Chinese)[4] 邓子谦,刘敏,毛杰,等. 等离子喷涂-物理气相沉积射流中粒子状态和分布[J]. 中国表面工程, 2017, 30(3): 81-88.Deng Ziqian, Liu Min, Mao Jie, et al. State and distribution of particles in jet of plasma spray-physical vapor deposition[J]. China Surface Engineering, 2017, 30(3): 81-88. (in Chinese)[5] 钱苗根. 现代表面技术[M]. 第2版. 北京:机械工业出版社, 2016.[6] 王娇,邓畅光,邓姝皓,等. CeO2-Y2O3- ZrO2热障涂层的组织结构及隔热性能[J]. 中国表面工程, 2015, 28(1): 29-35.Wang Jiao, Deng Changguang, Deng Shuhao, et al. Microstructures and thermal insulation capability of CeO2-Y2O3-ZrO2 thermal barrier coatings[J]. China Surface Engineering, 2015, 28(1): 29-35. (in Chinese) [7] 付超,孔魏凯,廖文俊,等. 应用于燃气轮机的热障涂层技术的研究现状[J]. 装备机械, 2014(3): 12-18.Fu Chao, Kong Weikai, Liao Wenjun, et al. Research on thermal barrier coating technology of gas turbine[J]. Equipment Machnery, 2014(3): 12-18. (in Chinese)[8] 张志强,宋文兴,陆海鹰. 热障涂层在航天发动机涡轮叶片上的应用研究[J].航空发动机, 2011, 37(2): 38-42.Zhang Zhiqiang, Song Wenxing, Lu Haiying. Application fo thermal barrier coating on aeroengine turbine blade[J]. Aeroengine, 2011, 37(2):38-42. (in Chinese)[9] 吴子健. 热喷涂技术与应用[M]. 北京:机械工业出版社, 2016.[10] 袁福河,张佳平,程玉贤,等. 我国航空发动机用几种涂层技术的差距及未来发展[J]. 航空制造技术, 2016, 59(1/2): 40-44.Yuan Fuhe, Zhang Jiaping, Cheng Yuxian, et al. Gap and future in technologies of coaings for aeroengine in China[J]. Aeronautical Manufacturing Technology, 2016, 59(1/2): 40-44. (in Chinese)。
- 1、下载文档前请自行甄别文档内容的完整性,平台不提供额外的编辑、内容补充、找答案等附加服务。
- 2、"仅部分预览"的文档,不可在线预览部分如存在完整性等问题,可反馈申请退款(可完整预览的文档不适用该条件!)。
- 3、如文档侵犯您的权益,请联系客服反馈,我们会尽快为您处理(人工客服工作时间:9:00-18:30)。
氧化铁红、铅铬黄、体质颜料等研磨后,加入催干剂,并以200号溶 剂汽油及二甲苯调配而成。 (2) 面漆:C04-64草黄醇酸半光磁漆。该漆是用中油度醇酸树脂与颜 料及体质颜料调制后,加入催干剂,用有机溶剂调配而成。 3.火箭部外表面涂漆
1.喷砂 喷砂是指使制件表面受到喷射砂粒的冲击而进行清理、除锈或粗化的
过程。 2.抛丸 将金属制件和铁丸共装在抛丸清理滚筒内进行清理出光的过程,称为
抛丸。 3.滚光 滚光在清理滚筒内进行,用于小型零件清除氧化皮、铁锈和毛刺等。
如火箭弹的质量调节板、盖片、药包夹体等冷冲件,成型后毛刺较多, 在表面处理前进行滚光清理,效良好。
上一页 下一页 返回
10.2.3 酸洗
1.钢铁零件酸洗 为了确保酸洗效果,在选择酸洗配方、操作及溶液维护过程中,必须
注意以下几点: (1) 要根据零件锈蚀程度选择酸洗配方。 (2) 酸的 溶度与温度对腐蚀速度影响很大。 (3) 搅拌对酸洗速度和质量影响 很大,搅拌不当,大量的铁盐及杂质会沉积在金属零件表面,使局部 酸洗不匀,而影响酸洗速度及质量。 (4) 要控制酸洗时间,严格防 止零件过腐蚀。 (5) 酸洗液中铁盐的含量直接影响酸洗效果,当酸 的溶度很低和酸洗初始阶段,铁盐的存在会加速腐蚀。 2. 为了确保酸洗效果,操作及溶液维护过程中必须注意以下几点: (1) 要根据锈蚀情况选择酸洗时间,严防过腐蚀。 (2) 酸洗温度常控制 在30 ℃左右。 (3) 新配的酸洗液一般常采用废零件预先处理一下, 这样会消耗掉含量过多的那一种酸,使比例更为恰当。 (4) 铜及铜 合金零件应采用单独的酸洗溶液。
返回
10.4.1 镀锌
一、概述
1. 影响镀层质量的因素 :(1) 锌碱比 (2) 添加剂 (3) 温度 (4) 电 流密度 (5) 阳极
2.故障处理
二、镀锌后处理
1.
为了防止锌层起泡,操作中应注意以下几点: (1) 采用工艺规定的
金属清洗剂,对弹性零件清洗,效果较好,可代替180号航空汽油。
第十章 火箭弹的表面处理
10.1 表面腐蚀种类及防腐方法 10.2 防腐处理前零件表面的清理 10.3 钢质零件的氧化和磷化处理 10.4 电化学处理 10.5 涂敷耐热涂层 10.6 涂油和涂漆 10.7 提高防腐性能的主要途径
10.1 表面腐蚀种类及防腐方法
10.1.1 金属表面腐蚀的种类 10.1.2 防腐方法 10.1.3 防腐方法选择的原则
上一页 返回
10.7 提高防腐性能的主要途径
正确地选择防腐层,是使火箭弹金属零件不被腐蚀的主要途径。此外, 还要从零件材料的选用、结构的设计及产品的包装方法等多方面考虑, 才能提高火箭弹的整体防腐能力,使之在长期储存后仍能正常使用。
1.正确选择零件材料和涂镀层 2.正确选择零部件的保护层 3.注意后处理 4. (1)非密封包装:即经过表面处理的火箭弹,直接装入木箱包装。此种
上一页 下一页 返回
10.2.2 除油
1.有机溶剂除油 2.金属清洗剂除油 3.化学除油 :为了确保化学除油效果,在选择除油规范及溶液维护过程中,
必须注意以下几点: (1) 要正确选择除油液成分。 (2) 要适当控制除油 温度,以确保安全除去皂化和非皂化类油污。 (3) 油污严重的工件,应 先用有机溶剂除油后再进行化学除油。 (4) 当除油效果不好时,应及时 补充材料,必要时应更换溶液。 (5) 为了保证除油效果,在没有条件搅 拌溶液的情况下,除油过程中应经常上下移动工件。 4.电化学除油:在选择除油液配方、操作及溶液维护过程中,必须注意以 下几点:(1) 电化学除油时,一个电极是工件,另一个电极可选用不锈钢 板或铁板。阴极除油不能用铁板作阳极,因为铁板阳极的溶解会污染电解 液。(2) 电极接触要好,接触不良会产生电火花,引起爆鸣。(3) 表面活 性剂不可使用高泡的,否则过多的泡沫会覆盖在液面或溢出槽外。当液面 泡沫较厚时,应先切断电源,然后放进或取出零件。(4) 提高电流密度, 可以相应提高除油速度和改善深孔除油质量,但电流密度过高,不仅形成 大量的碱雾,污染工房里的空气,还可能腐蚀零件。(5) 提高温度可以降 低溶液的电阻,从而节约电能,但温度过高不仅消耗了大量的热能,污染 工房里的空气,恶化劳动条件,还可能造成零件的腐蚀。
剂应尽量少加,电镀工作应正常,中间不能断电。
2.钝化处理
3.镀锌层的质量检验
下一页 返回
10.4.2 镀铬
一、概述 1.性质及用途 2.镀铬液的种类 二、镀硬铬 1.特点
(1) 镀层厚度要比普通镀铬厚几十至几百倍。(2) 电镀的时间长,电 流密度大。在模具设计时需考虑导入电流的损失。(3) 采用仿形阳极 或辅助阴极,改善镀层分布的均匀性.(4) 镀层需进行除氢处理。
(1) 应力腐蚀 金属材料在拉伸应力作用下,处在腐蚀介质的环
境下所发生的腐蚀即为应力腐蚀。应力腐蚀的结果往往出现裂纹、甚
(2) 电偶腐蚀 凡是有不同电极电位的金属相互接触,并在一定
的介质中所发生的电化学腐蚀即属电偶腐蚀。
(3) 缝隙腐蚀 金属与金属或金属与非金属材料接触时,即使是
采用紧配合,仍然有可能存在间隙,当腐蚀液渗入缝隙中产生化学腐
上一页 返回
10.3 钢质零件的氧化和磷化处理
10.3.1 钢质零件的氧化处理 10.3.2 钢质零件的磷化处理
返回
10.3.1 钢质零件的氧化处理
1. 碱性氧化处理成膜机理 2.工艺流程 : 碱液去油 →热水洗 →冷水洗 →酸洗 →冷水洗 →中和 →冷水洗
→热水洗 →氧化处理 →氧化液回收 →热水洗 →冷水洗 →皂液封 闭 →清洗 →热风吹干 →浸油、擦去多余油 →包装 3. (1) 浸皂处理 (2) 浸油 4.不合格氧化膜的退除
上一页 返回
10.2 防腐处理前零件表面的清理
10.2.1 机械处理 10.2.2 除油 10.2.3 酸洗
下一页 返回
10.2.1 机械处理
机械处理指通过机械方法对金属制件进行表面清理的方法。包括:磨 光、抛光、喷砂、喷丸、滚光等。火箭弹零部件的表面处理主要用于 防腐,因此表面清理一般用喷砂、滚光等方法,很少用磨光、抛光等 方法。
(1) 非金属覆盖层:主要指各种涂料防护层,即通过一定的涂敷方法把 油基漆和树脂基漆,涂在金属表面上,经固化形成涂层,保护金属免 被腐蚀。如火箭弹生产中采用的铁红醇酸底漆、军黄醇酸面漆、军绿
(2) 金属覆盖层:利用电解作用使耐蚀性较好的金属或合金沉积在金 属制件表面,形成均匀、致密、结合力良好的金属层。
5.发蓝时常见的故障,可能原因及处理方法
下一页 返回
10.3.2 钢质零件的磷化处理
1.磷化液中各种成分的作用及影响磷化膜质量的因素 2.常见疵病及其消除方法 3.磷化膜皂化填充 4.磷化膜的质量检验
上一页 返回
10.4 电化学处理
10.4.1 镀锌 10.4.2 镀铬 10.4.3 铝和铝合金的阳极氧化
1.有机类 (1) 有机硅树脂类 (2) 其他树脂类涂料 2.无机类耐热隔热涂料 3.涂敷工艺及影响涂敷质量的因素 (1) 涂敷前零件的表面处理 :① 内表面喷砂 ② 零件的磷化处理 ③
磷化层干燥 (2) 涂料的准备 (3) 涂敷 (4) 涂敷层的干燥固化 4.涂敷层的检验 (1) 外观检验 (2) 厚度检验
上一页 下一页 返回
10.1.1 金属表面腐蚀的种类
按腐蚀机理分类,通常把金属腐蚀划分为两大类:化学腐蚀和电化学 腐蚀。
化学腐蚀:是指在没有电流的情况下,金属与周围介质发生化学作用 而引起的腐蚀。
电化学腐蚀:是指金属与电解质溶解液接触时由电化学作用而引起的 腐蚀,这是由于形成了“微电池”而引起的。电化学腐蚀是金属与周 围介质(如潮湿的空气、海水、土壤、电解质溶液等)发生电化学作用 而引起的。
2.工艺流程 :碱水洗 →碱液去油 →热水洗 →冷水洗 →酸洗 →冷 水洗 →电化学除油 →热水洗 →冷水洗 →弱腐蚀 →冷水洗 →温水 洗 →镀铬 →镀铬液回收 →热水洗 →烘干 →检验
3. 4.镀后除氢处理 5.不合格镀层的退除
上一页 下一页 返回
10.4.3 铝及铝合金的阳极氧化
1.概述 2.氧化膜的结构 3.各种因素对氧化膜性能的影响 :(1) 硫酸 (2) 温度 (3) 电流密度
下一页 返回
10.5.2 122 mm火箭弹隔热涂层发生的质量问 题及解决方法
1.
2.解决吸水、吸潮问题 涂层中含有水分是涂层在干燥固化过程中产生气泡、针孔的主要原因
之一。涂层中的水分主要来源于: ① 涂料生产中所用填料含有的水分。生产前应进行烘干处理,去除
水分。 ② 酒精的含水与吸水问题。GT-401涂料所用溶剂为无水酒精, 无水酒精(酒精含量99.5%)也含有少量水分,而且酒精容易吸水。所 以在涂料的生产和使用过程中,不可避免地要吸收部分水。改变涂料 溶剂为高沸点不吸水溶剂是解决涂料吸水的根本方法。 ③ 磷化层含 有一定量的水分,通过试验,涂敷前磷化层在230 ℃温度下,烘干30 min,对减少涂层起泡、针孔有一定效果。
蚀,金属的腐蚀便会加快。
除上述局部腐蚀形式外,还有沟状腐蚀、水线腐蚀、刀口腐蚀等局部
上一页 下一页 返回
10.1.2 防腐方法
火箭弹的零件较多,所以防腐较一般榴弹要求高,每个零件都要进行 防腐处理。其原理是用耐蚀性较强的金属或非金属来覆盖耐蚀性较弱 的金属,将主体金属与腐蚀介质隔离开以达到防腐的目的。
(2) 电化学除油采用阳极去油,温度在90~95 ℃,电流密度在5 A
/dm2
Cu2 等金属杂质污染,严重时要更换,或
除铜后再进行1~2 min阳极去油。 (3) 酸浸蚀尽量采用浓的新盐
酸,酸中绝不能有 Cu2,否则更换。 (4) 工件浸蚀后入镀槽时,在