铁水脱硫技术
kr法脱硫工艺介绍PPT

KR法脱硫与喷吹法脱硫工艺特点对比
脱硫剂种类与优、缺点
Mg基(颗粒镁)
优点: (1)反应速度快,脱硫效率高,并且不容易回硫; (2)消耗量小,产生渣量少; (3)脱硫处理时间短,铁水温降小。 缺点: (1)价格昂贵; (2)加工运输贮存、使用都有安全问题, 操控较困难。
铁水KR机械搅拌法脱硫概述
KR (Kambara Reactor)法脱硫,是1963年Nippon Steel为了限制对镁的用量,广烟厂研究发明的。1965年 应用于工业生产。
所谓KR法脱硫,是将浇注耐火材料并经过烘烤的十 字形搅拌头,浸入铁水包熔池一定深度,借其旋转产 生的漩涡,经过称量的脱硫剂由给料器加入到铁水表 面,并被旋涡卷入铁水中使氧化钙基脱硫粉剂与铁水
100 r/ min ), 以防止在加入脱硫剂时出现喷溅。
KR脱硫法搅拌与加料操作
搅拌操作注意事项 (1)确认铁水包中心线对准搅拌头中心线,正 负误差≤50mm。搅拌头的隔热板不能进入到铁水中, 搅拌头叶轮不能出铁水面。 (2)新搅拌头在使用前50次时,必须进行预烤,将搅 拌头叶片浸泡到铁水中烧结3-5min。 (3)铁水液面在控制在3600~4200mm间方可进行 搅拌操作,搅拌过程中注意观察电流值及转速波动情 况和相关信号反应。 (4)每处理完一包铁水要对搅拌头进行检查确认,搅 拌头耐火材料损坏或脱落≥50mm或有槽沟、孔眼、 凹陷情况必须进行热修补后才能使用。 (5)搅拌结束前3min实施必要的均匀减速,但转速
≤ 0.001%S,
约占10%
KR脱硫主体设备及分布
KR法脱硫主体设备
电动翻转检 修平台
铁水脱硫比较分析

铁水脱硫工艺分析简况:近5年来铁水脱硫技术在我国发展很快,“铁水脱硫是转炉使用铁水炼钢不可缺少的工序”,这一点在我国得到了认同,先后增加了50多条(含在建)生产线,入炉铁水的脱硫比已经超过30%(有待核定,1998年仅为22%),目前大中型企业都有了不同型式的铁水预处理生产线,国内铁水预处理(脱硫)技术应用情况见表1表1 铁水预处理(脱硫)简况2 机械搅拌法(KR)、喷吹法脱硫比较1)机械搅拌法(KR)是成熟的生产工艺,日本绝大多数企业采用KR法脱硫,武钢已生产20多年,在消化引进技术的基础上有不少创新,生产技术水平和技术经济指标均较原设计有大幅度的提高,除脱硫铁水产量增长86.8%以外,还自行开发了无碳CaO基脱硫剂取代了CaC2,降低了生产成本。
脱硫处理前后铁水温降△t从过去的40-50℃减至28℃,脱硫效率ηs平均达92.5%,脱硫处理后[S]≤0.005%的罐次比率在98%以上,实际上[S]≤0.002%(ω)时的脱硫剂吨(CaO 基)耗量由8.5kg降至5.00kg以下,2001年脱硫剂平均耗量已降至3.78kg,目前兑入转炉经深脱硫的铁水硫含量平均值已达0.0027%,专用脱硫罐罐龄已达400次以上,主要消耗部件搅拌头使用次数平均已达500次,最多曾达631次,吨铁脱硫处理成本小于20元,铁损约为3%(原文是否有误待核定,是否为0.3%),KR法良好的动力学条件、脱硫效果好、粉剂成本低、无喷溅、无污染等优势使济钢、川威、昆钢、上钢一厂等厂相继采用。
2)喷吹法:八十年代初期我院开始研发用喷吹石灰粉法进行铁水脱硫技术并取得成功,石灰粉铁水脱硫技术先后在天钢等十几个厂应用,1998年我院先后又成功为宝钢设计引进了用混铁车进行铁水三脱复合喷吹技术、为本钢设计引进了“镁基”喷吹脱硫复合喷吹技术、2001年又为太钢设计引进了用铁水罐进行三脱复合喷吹技术以及单吹颗粒镁脱硫技术,喷吹法具有以下优点:●程序喷吹(复合、顺序)技术可以最大限度地利用多种粉剂发挥其在铁水预处理(脱硫)中效果。
kr法脱硫工艺介绍 PPT
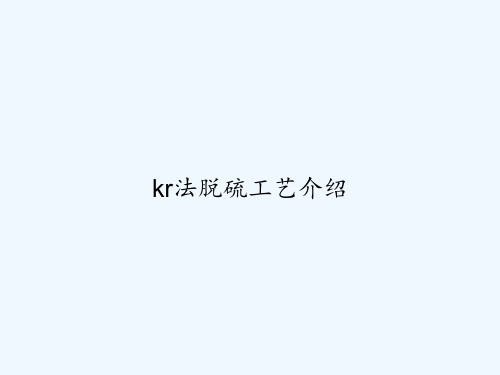
铁水脱硫剂消耗与指标
铁水脱硫主要消耗指标
KR脱硫法搅拌与加料操作
搅拌操作
KR 铁水脱硫时的搅拌速度是根据铁水硫含量、铁 水温度以及搅拌头状况确定的。
铁水温度与含硫量一定值时, 在一定范围内搅拌器转速 越高脱硫效率越高。但搅拌器转速过高, 在搅拌时会造 成脱硫铁水包内铁水严重喷溅, 同时加速搅拌头的磨损。 使用新搅拌头时, 同样的搅拌效果, 设定其转速可比已 经使用一段时间的搅拌器降低10~20r/ min。加入脱 硫剂时搅拌器转速应比正常转速降低2~5r/ min , 在投 料剩余100 kg时, 开始均匀增速到所需的正常转速(80100 r/ min ), 以防止在加入脱硫剂时出现喷溅。
KR脱硫法搅拌与加料操作
搅拌操作注意事项 (1)确认铁水包中心线对准搅拌头中心线,正 负误差≤50mm。搅拌头的隔热板不能进入到铁水中, 搅拌头叶轮不能出铁水面。 (2)新搅拌头在使用前50次时,必须进行预烤,将搅 拌头叶片浸泡到铁水中烧结3-5min。 (3)铁水液面在控制在3600~4200mm间方可进行 搅拌操作,搅拌过程中注意观察电流值及转速波动情 况和相关信号反应。 (4)每处理完一包铁水要对搅拌头进行检查确认,搅 拌头耐火材料损坏或脱落≥50mm或有槽沟、孔眼、 凹陷情况必须进行热修补后才能使用。 (5)搅拌结束前3min实施必要的均匀减速,但转速 不得低于65 r/ min 。 (6)处理后硫含量达不到要求时,当铁水温度 ≥1250℃,方可进行二次脱硫。
其中粒度在0.5-1.0mm之间的比例大于80%,粒 度小于0.3mm和大于1.2mm的比例要求 ≤10%。
铁水预处理脱硫的优点
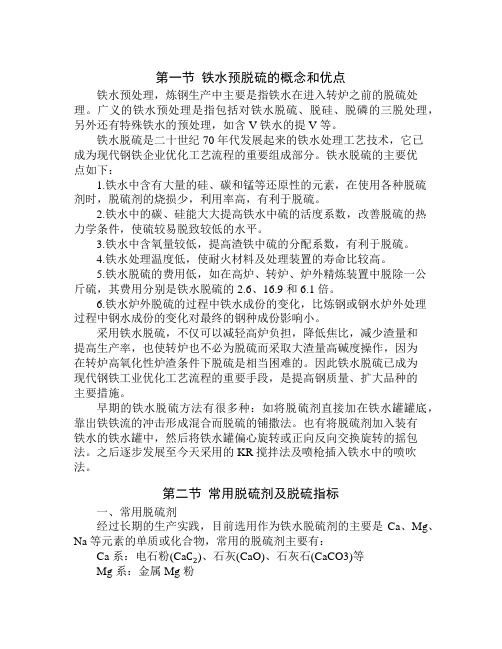
第一节铁水预脱硫的概念和优点铁水预处理,炼钢生产中主要是指铁水在进入转炉之前的脱硫处理。
广义的铁水预处理是指包括对铁水脱硫、脱硅、脱磷的三脱处理,另外还有特殊铁水的预处理,如含V铁水的提V等。
铁水脱硫是二十世纪70年代发展起来的铁水处理工艺技术,它已成为现代钢铁企业优化工艺流程的重要组成部分。
铁水脱硫的主要优点如下:1.铁水中含有大量的硅、碳和锰等还原性的元素,在使用各种脱硫剂时,脱硫剂的烧损少,利用率高,有利于脱硫。
2.铁水中的碳、硅能大大提高铁水中硫的活度系数,改善脱硫的热力学条件,使硫较易脱致较低的水平。
3.铁水中含氧量较低,提高渣铁中硫的分配系数,有利于脱硫。
4.铁水处理温度低,使耐火材料及处理装置的寿命比较高。
5.铁水脱硫的费用低,如在高炉、转炉、炉外精炼装置中脱除一公斤硫,其费用分别是铁水脱硫的2.6、16.9和6.1倍。
6.铁水炉外脱硫的过程中铁水成份的变化,比炼钢或钢水炉外处理过程中钢水成份的变化对最终的钢种成份影响小。
采用铁水脱硫,不仅可以减轻高炉负担,降低焦比,减少渣量和提高生产率,也使转炉也不必为脱硫而采取大渣量高碱度操作,因为在转炉高氧化性炉渣条件下脱硫是相当困难的。
因此铁水脱硫已成为现代钢铁工业优化工艺流程的重要手段,是提高钢质量、扩大品种的主要措施。
早期的铁水脱硫方法有很多种:如将脱硫剂直接加在铁水罐罐底,靠出铁铁流的冲击形成混合而脱硫的铺撒法。
也有将脱硫剂加入装有铁水的铁水罐中,然后将铁水罐偏心旋转或正向反向交换旋转的摇包法。
之后逐步发展至今天采用的KR搅拌法及喷枪插入铁水中的喷吹法。
第二节常用脱硫剂及脱硫指标一、常用脱硫剂经过长期的生产实践,目前选用作为铁水脱硫剂的主要是Ca、Mg、Na等元素的单质或化合物,常用的脱硫剂主要有:Ca系:电石粉(Ca C2)、石灰(CaO)、石灰石(CaCO3)等Mg系:金属Mg粉Na系:苏打(Na2CO3)二、常用脱硫剂反应特点1.电石粉碳化钙脱硫反应为用Ca C2脱硫有如下特点:1)在高碳系铁水中,Ca C2分解出的Ca离子与铁水中的硫有极强的亲和力。
常用的几种铁水脱硫工艺的介绍和比较
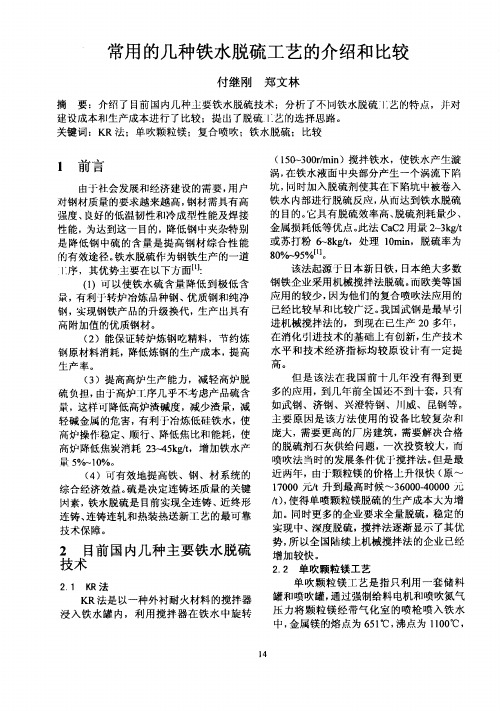
Mg S , 反应 生成 的硫 化镁 在铁水 温度 下早 同 态 ,浸 入渣 q J 。脱硫率 为 8 0 %- -  ̄ 9 0 % J 。 最 初是 2 0 0 0年 武铡 从 鸟克 兰 引进 的 I 艺技术 装备 ,由 J 。 匕具有 一系 列的优 势 , 在 我国应用 得到 迅速发展 。 目前 国内 已经 开 发 出具有 自主 知识 产 权 的铁水 单喷 颗 粒镁 脱 硫 的 I 艺和成 套装备 。 该项 技术 在我 国 已经 得 到 了相 当广泛 的应用 ,设 备达 到近 百 台 套。 2 . 3 复合 喷吹工 艺 复 合 喷吹 。 1 艺 是指 对 分别 装 有 流态 化 石灰 、镁粉 的两个料 罐及两 个喷 吹罐 , 配 以 合适 孔板 直径及氮 气 力参数 , 按 一 定 比例 将 石灰和 镁粉在 喷吹管道 中混 合 , 再经 喷枪 进 入铁 水 中 ,利 用镁 气化 溶 入铁 水 中与 【 S 】 反应 ,生成 Mg S ,经扒渣 去 除 ,达 到铁 水 脱硫 的 目的 。脱硫 率为 8 0 %, -  ̄ 9 0 %L 3 j 。 此项 技 术土 要 从 欧洲 的 霍 高文 和 美 国 的E S M 引进 的,应 用在宝钢 、本钢 、马钢 、 南钢 等企业 。
8 O % ~9 5 %【 ¨
。
该 法起 源 于 日本 新 日铁 , 日本 绝 大多数 钢 铁企 业采 用机 械搅 拌法 脱硫 。 而 欧美 等 国 ( 1 )可 以使铁 水 硫 含 量 降低 到 极 低 含 【 大 1 为他们 的复 合喷 吹法 应用 的 量, 有 利于转 炉 冶炼 品种钢 、 优 质钢 和纯 净 应 用 的较 少 , 我 国武铡 是最 早 引 钢 ,实现钢铁 产 品 的升 级换 代 ,生产 出具 有 已经 比较 早和 比较 广泛 。 进 机 械搅 拌法 的 ,到现 在 已生产 2 0多年 , 高 附加值 的优质 钢材 。 生产技 术 ( 2 )能保 证转 炉炼 钢 吃精 料 ,节 约炼 在消 化 引进技 术 的基础 上有 创新 , 水 平 和技 术 经 济 指标 均 较 原 设计 有 一 定 提 钢 原材料 消耗 ,降低 炼钢 的 生产成 本 , 提 高 高。 生产 率。 但 是 该 法 在 我 国前 十 几 年 没有 得 到 更 ( 3 )提 高高 炉 生产 能力 ,减 轻高 炉脱 只有 硫 负担 , 由于 高炉T 序几 乎不 考虑 产 品硫 含 多的应 用 ,到几 年前全 国还不 到十套 , 如 武钢 、济 铡 、兴 澄特钢 、川威 、 昆铡 等。 景 ,这 样可 降低 高 炉渣碱 度 ,减 少渣 量 ,减 轻碱 金属 的危 害,有利 于冶 炼低 硅铁 水 ,使 主 要 原 因是 该 方法 使 用 的 设备 比较 复 杂 和 需 要解 决合格 高炉 操作 稳定 、顺 行 、降低焦 比和 能耗 ,使 庞 大 ,需要 更高 的厂 房建筑 , 高 炉 降低 焦炭 消耗 2 3 - - 4 5 k g / t ,增 加铁 水产 的脱硫 剂 石灰 供给 问题 ,一次投 资较 大 ,而 喷 吹法 当时 的发展 条件 优于 搅拌法 。 但 是最 罩 5  ̄ / o  ̄ 1 0 %。 F颗粒 镁 的价格 上升很 快 ( 原 ~ ( 4 )可 有效 地提 高铁 、钢 、材 系 统 的 近 两年 ,由 1 7 0 0 0元 / t升 到最 高时候  ̄3 6 0 0 0 — 4 0 0 0 0冗 综 合经 济效 益 。 硫 是 决 定连铸 坯质 量 的关键 / t ) , 使得 单喷 颗粒 镁脱硫 的生产成 本大 为增 素 ,铁水脱硫 是 目前 实现 全连铸 、 近 终 形 稳 定 的 连铸、 连 铸连 轧和热 装热 送 新工 艺 的最可 靠 加 。同时更 多 的企业 要求全 量脱硫 , 实现 中 、 深 度脱 硫 , 搅 拌法 逐渐 显示 了其 优 技 术保障 。 势, 所 以全 国 陆续上机 械搅 拌法 的企 业 已经 2 目前 国内几 种主 要铁 水脱硫 增 加 较快 。 技 术 2 . 2 单 吹颗 粒镁 工艺 单 吹 颗 粒 镁 工艺 是 指 只 利用 一 套 储 料 2 . 1 K R法 通 过 强制给 料 电机 和 喷吹氮 气 K R法 是 以一种 外衬 耐火 材料 的搅 拌器 罐 和喷 吹罐 , 压 力 将 颗 粒镁 经 带 气 化 室 的喷 枪 喷 入铁 水 浸 入 铁 水罐 内 ,利 用搅 拌 器 在 铁 水 中旋 转 中, 金属镁 的熔 点为 6 5 l ℃, 沸点 为 1 1 0 0 ℃,
铁水三脱预处理及KR脱硫技术
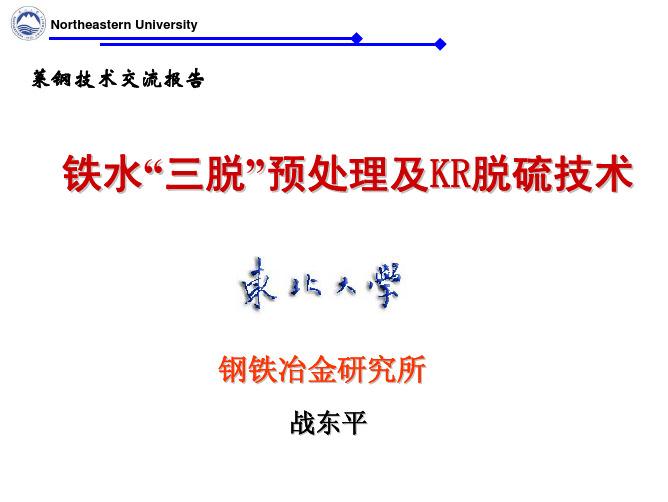
新日铁 君津厂— ORP法
传统“三脱”工艺
Northeastern University
川 崎 千 叶 厂
传统“三脱”工艺
Northeastern University
神 户 钢 铁
加 古 川 厂
传统“三脱”工艺
1-脱硫间 3-脱硫、磷站 5-烟气冷却 7-渣间 9-冷却水 11-来自高炉
◆特殊铁水预处理:针对铁水中的特殊元素进行提纯精炼或
资源综合利用而进行的处理过程,如铁水提钒、提铌、提钨 等。
Northeastern University
为了提高钢的质量,改善高炉和转炉的生产条件,铁水 炉外预处理技术已在世界各国广泛应用。 铁水预处理优点:
1) 铁水炉外脱硫能给高炉减轻负荷,可降低焦比,减 少渣量和提高生产率。
Northeastern University
国外铁水三脱技术的发展
• 40年代:北美一些钢厂曾用氧化铁皮在高炉出铁口年进行 铁水脱硅
• 70年代:以日本为代表的钢铁企业进行铁水三脱研究,并 于80年代初应用于工业生产
• 1982年5月:日本住友公司鹿岛厂 开发的“住友碱精炼 法”—SARP法投产(苏打精炼法)
最短达到37min。宝钢X70、X80管线钢的硫含量最低为3ppm。宝钢无取向电工钢采用RH脱 硫后[S]≤30ppm,最低达到22ppm。本钢AHF(CAS-OB)处理过程可实现40%的脱硫率,该 技术属国内首创。
Northeastern University
科研获奖
在高效精炼技术开发等方面形成了系统创新理论。该 技术的实施为抚钢创造了较大的经济效益,到2004年 底,抚钢新增产值10亿元,新增效益3亿多元。本人项 目执行负责人
KR法铁水脱硫主体设备介绍及有关计算
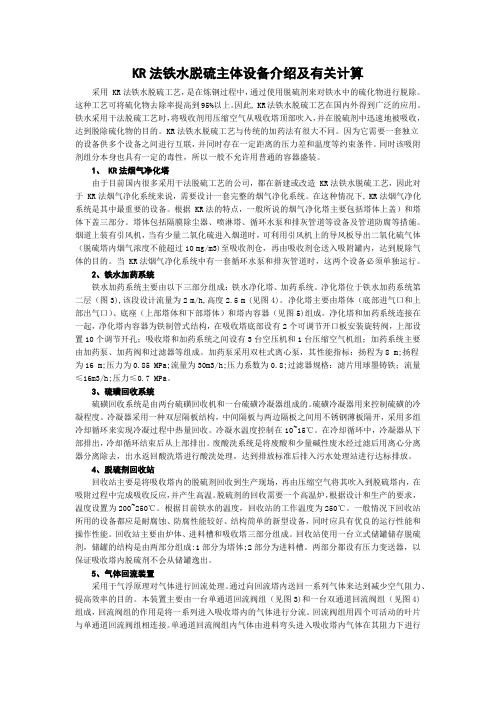
KR法铁水脱硫主体设备介绍及有关计算采用 KR法铁水脱硫工艺,是在炼钢过程中,通过使用脱硫剂来对铁水中的硫化物进行脱除。
这种工艺可将硫化物去除率提高到95%以上。
因此, KR法铁水脱硫工艺在国内外得到广泛的应用。
铁水采用干法脱硫工艺时,将吸收剂用压缩空气从吸收塔顶部吹入,并在脱硫剂中迅速地被吸收,达到脱除硫化物的目的。
KR法铁水脱硫工艺与传统的加药法有很大不同。
因为它需要一套独立的设备供多个设备之间进行互联,并同时存在一定距离的压力差和温度等约束条件。
同时该吸附剂组分本身也具有一定的毒性,所以一般不允许用普通的容器盛装。
1、 KR法烟气净化塔由于目前国内很多采用干法脱硫工艺的公司,都在新建或改造 KR法铁水脱硫工艺,因此对于 KR法烟气净化系统来说,需要设计一套完整的烟气净化系统。
在这种情况下, KR法烟气净化系统是其中最重要的设备。
根据 KR法的特点,一般所说的烟气净化塔主要包括塔体上盖)和塔体下盖三部分。
塔体包括隔膜除尘器、喷淋塔、循环水泵和排灰管道等设备及管道防腐等措施。
烟道上装有引风机,当有少量二氧化硫进入烟道时,可利用引风机上的导风板导出二氧化硫气体(脱硫塔内烟气浓度不能超过10 mg/m3)至吸收剂仓,再由吸收剂仓送入吸附罐内,达到脱除气体的目的。
当 KR法烟气净化系统中有一套循环水泵和排灰管道时,这两个设备必须单独运行。
2、铁水加药系统铁水加药系统主要由以下三部分组成:铁水净化塔、加药系统。
净化塔位于铁水加药系统第二层(图3),该段设计流量为2 m/h,高度2.5 m (见图4)。
净化塔主要由塔体(底部进气口和上部出气口)、底座(上部塔体和下部塔体)和塔内容器(见图5)组成。
净化塔和加药系统连接在一起,净化塔内容器为铁制管式结构,在吸收塔底部设有2个可调节开口板安装旋转阀,上部设置10个调节开孔;吸收塔和加药系统之间设有3台空压机和1台压缩空气机组;加药系统主要由加药泵、加药阀和过滤器等组成。
铁水喷粉脱硫
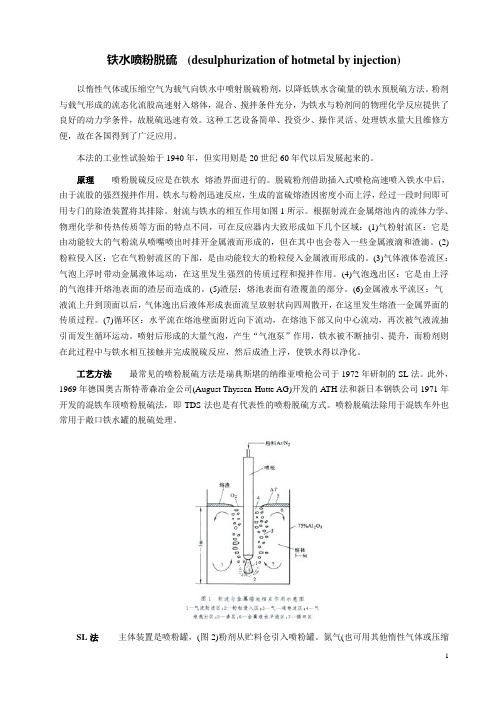
铁水喷粉脱硫(desulphurization of hotmetal by injection)以惰性气体或压缩空气为载气向铁水中喷射脱硫粉剂,以降低铁水含硫量的铁水预脱硫方法。
粉剂与载气形成的流态化流股高速射入熔体,混合、搅拌条件充分,为铁水与粉剂间的物理化学反应提供了良好的动力学条件,故脱硫迅速有效。
这种工艺设备简单、投资少、操作灵活、处理铁水量大且维修方便,故在各国得到了广泛应用。
本法的工业性试验始于1940年,但实用则是20世纪60年代以后发展起来的。
原理喷粉脱硫反应是在铁水--熔渣界面进行的。
脱硫粉剂借助插入式喷枪高速喷入铁水中后,由于流股的强烈搅拌作用,铁水与粉剂迅速反应,生成的富硫熔渣因密度小而上浮,经过一段时间即可用专门的除渣装置将其排除。
射流与铁水的相互作用如图1所示。
根据射流在金属熔池内的流体力学、物理化学和传热传质等方面的特点不同,可在反应器内大致形成如下几个区域:(1)气粉射流区:它是由动能较大的气粉流从喷嘴喷出时排开金属液而形成的,但在其中也会卷入一些金属液滴和渣滴。
(2)粉粒侵入区:它在气粉射流区的下部,是由动能较大的粉粒侵入金属液而形成的。
(3)气体液体卷流区:气泡上浮时带动金属液体运动,在这里发生强烈的传质过程和搅拌作用。
(4)气泡逸出区:它是由上浮的气泡排开熔池表面的渣层而造成的。
(5)渣层:熔池表面有渣覆盖的部分。
(6)金属液水平流区:气--液流上升到顶面以后,气体逸出后液体形成表面流呈放射状向四周散开,在这里发生熔渣一金属界面的传质过程。
(7)循环区:水平流在熔池壁面附近向下流动,在熔池下部又向中心流动,再次被气液流抽引而发生循环运动。
喷射后形成的大量气泡,产生“气泡泵”作用,铁水被不断抽引、提升,而粉剂则在此过程中与铁水相互接触并完成脱硫反应,然后成渣上浮,使铁水得以净化。
工艺方法最常见的喷粉脱硫方法是瑞典斯堪的纳维亚喷枪公司于1972年研制的SL法。
此外,1969年德国奥古斯特蒂森冶金公司(August Thyssen-Hutte AG)开发的A TH法和新日本钢铁公司1971年开发的混铁车顶喷粉脱硫法,即TDS法也是有代表性的喷粉脱硫方式。
铁水脱硫经济性分析

铁水炉外脱硫的经济性分析钢铁工业技术的发展已经证明:高炉——铁水预处理(脱硫)——顶底复合转炉炼钢——炉外精炼(钢水二次精炼)——连铸——热送热装连续轧制,是高效、优质、低耗工艺路线。
铁水预处理能减轻高炉冶炼的负担,使转炉炼钢使用精料,而且为保证转炉扩大品种、提高钢质量,实现少渣炼钢,提高生产效率,改善技术经济指标奠定了基础。
一、铁水炉外脱硫对高炉的优势高炉为了保证生铁脱硫的要求,高炉不得不采用保守的操作方法,即采用高炉温、高碱度、大渣量操作,导致焦比高、产量低,高炉高产低耗的目标难以实现。
采用铁水炉外脱硫后,对高炉的优势如下:1、降低高炉生产成本,高炉实行低碱度操作可减少石灰消耗量、减少渣量、降低炉渣碱度、降低高炉焦比、减轻高炉负担并且增加高炉铁水产量;2、放宽了高炉铁水含硫量的限制,促进高炉平稳操作,提高了高炉生产率;3、有利于高炉排出碱金属氧化物Na2O、K2O,减少高炉结瘤,有利于冶炼低硅铁,使高炉稳定、顺行。
因此,铁水炉外脱硫是优化高炉工艺的关键技术,也是高炉增产降耗的重要技术手段。
高炉炉渣碱度、焦比与产量关系图由上图可见,高炉炼铁的炉渣碱度由1.2降到1.1,铁水硫含量由0.045%上升到0.06%,焦比降低10公斤/吨铁,铁产量增加5%。
二、铁水炉外脱硫对转炉的优势1、铁水脱硫预处理后,可得到含硫低的铁水,扩大了转炉冶炼的钢种范围;2、铁水脱硫预处理后,可以缩短转炉、精炼工序的冶炼周期;3、铁水脱硫预处理后,进一步保证了连铸工序生产顺行和连铸坯的质量;4、铁水脱硫预处理后,低硫铁水炼钢能减少石灰加入量和渣量,使铁的收得率提高约0.6个百分点。
转炉炼钢的铁水含硫量与炉渣碱度、渣量、渣中铁量及铁收得率关系图由上图可见,转炉炼钢的铁水含硫量降低,炉渣碱度、渣量及石灰消耗降低,渣中铁量增加,铁收得率降低。
三、铁水炉外脱硫的经济效益铁水脱硫在高炉内热力学条件好,但动力学条件差;在转炉内脱硫其热力学条件差(氧化性气氛),动力学条件好;无论高炉与转炉内,其脱硫条件都不完善,因此,脱硫成本高。
kr法脱硫工艺介绍
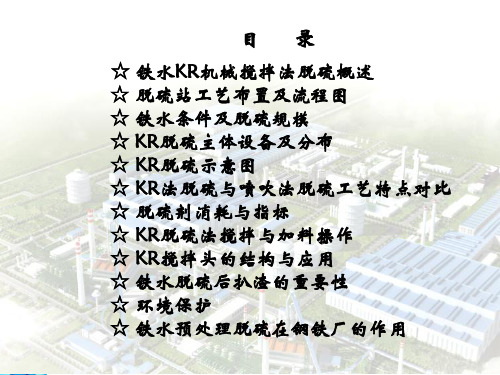
脱硫站工艺布置及流程图
Ningxia Medical University
铁水脱硫站工艺布置
在转炉加料跨(DE跨) 11#~14#柱间建设3座脱硫站, 每座脱硫站采取搅拌和扒渣同 工位的生产方式。加料、脱硫、 设备维修在脱硫位操作平台上 进行,搅拌头采用更换方式, 搅拌头热修补在操作维护平台 上进行。脱硫渣罐车与铁水包
搅拌系统画面
Ningxia Medical University
KR搅拌脱硫示意图
备料加料系统画面
Ningxia Medical University
KR搅拌脱硫示意图
液压系统画面
Ningxia Medical University
KR法脱硫与喷吹法脱硫工艺特点对NUninivg比exirasiMtyedical
(2)消耗量小,产生渣量少; (3)脱硫处理时间短,铁水温降小。
缺点: (1)价格昂贵; (2)加工运输贮存、使用都有安全问题, 操控较困难。
CaO基(石灰粉)
优点: (1)有较强的脱硫能力; (2)脱硫产物疏松,扒渣方便,对包衬侵蚀轻; (3)资源广,价格低,易加工, 使用安全。
缺点: (1)耗量大,渣量大; (2) 流动性差,在料罐中易“架桥”堵塞; (3)极易吸潮,降低反应效果,且使运输、贮存较为困难。
程式如下:[Mg]+[S]=[MgS]
喷吹法不足是,动力学条件差。 有研究表明,在都使用CaO基脱硫剂的情况下,KR法的脱硫率
是喷吹法的四倍。
KR法脱硫与喷吹法脱硫工艺特NU点ninivgex对irasiMty比edical
脱硫剂种类与优、缺点
Mg基(颗粒镁)
优点: (1)反应速度快,脱硫效率高,并且不容易回硫;
铁水脱硫方法

铁水脱硫是钢铁生产过程中的一项重要技术,旨在降低铁水中的硫含量,以保证钢铁产品的质量。
硫在钢铁中以硫化物的形式存在,会降低钢的纯净度,影响其机械性能,特别是对于海洋平台、汽车板等高品质钢材的生产,要求铁水中的硫含量必须严格控制。
常见的铁水脱硫方法有以下几种:
1. 机械搅拌法(KR法):通过机械搅拌器使铁水旋转,并喷入脱硫剂,如CaO或MgO,通过搅拌使脱硫剂与硫化物反应,实现脱硫。
2. 喷吹法:利用喷枪将粉末状的脱硫剂直接喷入铁水中,脱硫剂与铁水中的硫化物发生反应,从而降低硫含量。
3. 气体搅拌法:将含有硫的气体通入铁水中,通过气体的搅拌作用,使硫化物与气体充分混合并排出。
4. 悬浮法:将含硫化合物的悬浮液通入铁水中,通过悬浮液的吸附作用将硫分从铁水中分离出来。
5. 压入法:将含硫气体或液体通过压力直接压入铁水中,使其与铁水充分接触并达到脱硫效果。
以上方法中,机械搅拌法(KR法)因其效率高、控制参数灵活而被广泛应用。
此外,还有利用摇包、搅拌时间、转速等参数进行优化的方法,以及对脱硫剂的加入速度和量进行控制的技术,以提高脱硫效率和降低成本。
铁水预处理技术2

2013-7-22 铁水预处理技术 23
三种铁水预脱硅流程:
2013-7-22 铁水预处理技术 6
炉外脱硫的好处体现在:
高炉: 减轻脱硫负担,稳定、顺行、降低焦比
转炉:解放生产率,冶炼优质钢和合金钢 (高附加值钢种、低硫或极低硫钢)
预脱硫是目前实现全连铸、近终形连铸连轧和 热装热送新工艺的最经济、最可靠的技术保障。
企业:提高铁、钢、材系统的综合经济效益, 提高市场竞争能力。
铁水预处理技术
2013-7-22
12
(4) 镁 (Mg)系:
种类:
① 镁焦(Magcoke); ② 镁合金(MgFeSi); ③ 覆膜镁粒:其惰性保护膜占重量的3%~10%; ④ 覆膜混合镁粒:含Mg30%~80%,余为惰性物质。
镁的脱硫机理: 镁和[S]有很强亲合力,
[Mg ] + [S] ==== MgS(固) Mg(气) + [S] ==== MgS(固)
2013-7-22 铁水预处理技术 7
3)发展铁水预处理(脱硫)的必要性与紧迫性 是脱硫反应化学冶金学合理性的必要
高炉:动力学条件差,脱硫要付出代价 高炉脱硫:高炉温、焦比高、产量低 转炉:热力学条件不好,几乎无脱硫能力 炉外:可创造良好的热力学和动力学条件
是钢材市场竞争力紧迫性的必要 是企业工艺结构调整、产品发展需求的必要
8.3 铁水预处理脱硅
1 )铁水预脱硅发展背景及现状
热加工论坛—颗粒镁铁水脱硫技术
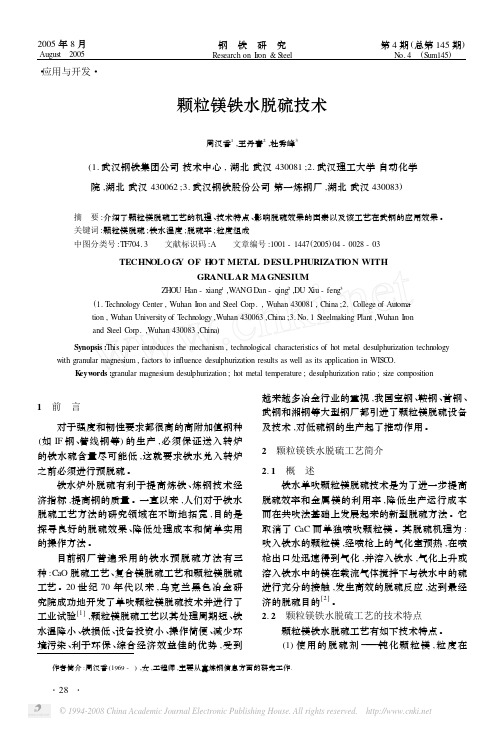
2005年8月August 2005钢 铁 研 究Research on Iron &S teel第4期(总第145期)N o.4 (Sum145)・应用与开发・颗粒镁铁水脱硫技术周汉香1,王丹青2,杜秀峰3(1.武汉钢铁集团公司技术中心,湖北武汉430081;2.武汉理工大学自动化学院,湖北武汉430062;3.武汉钢铁股份公司第一炼钢厂,湖北武汉430083) 摘 要:介绍了颗粒镁脱硫工艺的机理、技术特点、影响脱硫效果的因素以及该工艺在武钢的应用效果。
关键词:颗粒镁脱硫;铁水温度;脱硫率;粒度组成中图分类号:TF704.3 文献标识码:A 文章编号:1001-1447(2005)04-0028-03TECHN OLOG Y OF H OT META L DESU LPHURIZATION WITHGRANU LAR MAGNESIU MZH OU Han -xiang 1,W ANG Dan -qing 2,DU X iu -feng 3(1.T echnology Center ,Wuhan Iron and S teel C orp.,Wuhan 430081,China ;2.C ollege of Automa 2tion ,Wuhan University of T echnology ,Wuhan 430063,China ;3.N o.1S teelmaking Plant ,Wuhan Iron and S teel C orp.,Wuhan 430083,China )Synopsis :This paper introduces the mechanism ,technological characteristics of hot metal desulphurization technology with granular magnesium ,factors to in fluence desulphurization results as well as its application in WISC O.K eyw ords :granular magnesium desulphurization ;hot metal temperature ;desulphurization ratio ;size composition作者简介:周汉香(1969-),女,工程师,主要从事炼钢信息方面的研究工作.1 前 言对于强度和韧性要求都很高的高附加值钢种(如IF 钢、管线钢等)的生产,必须保证送入转炉的铁水硫含量尽可能低,这就要求铁水兑入转炉之前必须进行预脱硫。
1#KR铁水脱硫技术操作规程
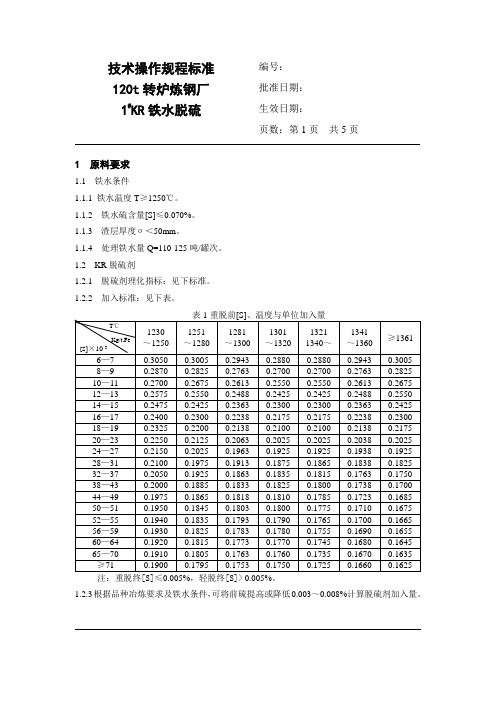
1 原料要求1.1 铁水条件1.1.1 铁水温度T ≥1250℃。
1.1.2 铁水硫含量[S]≤0.070%。
1.1.3 渣层厚度σ<50mm 。
1.1.4 处理铁水量Q=110-125吨/罐次。
1.2 KR 脱硫剂1.2.1 脱硫剂理化指标:见下标准。
1.2.2 加入标准:见下表。
注:重脱终[S]≤0.005%,轻脱终[S]> 0.005%。
1.2.3根据品种冶炼要求及铁水条件,可将前硫提高或降低0.003~0.008%计算脱硫剂加入量。
技术操作规程标准 120t 转炉炼钢厂 1#KR 铁水脱硫编号: 批准日期: 生效日期:页数:第1页 共5页编号:页数:第2页共5页1.2.4 KR脱硫剂:CaO基脱硫剂1.2.4.1 重量配比:活性石灰88-90% 萤石12-10%1.2.4.3 要求新鲜、干净、干燥、不得粉化变质。
2 扒渣操作2.1 脱硫铁水罐由牵引车运载至扒渣位置后,由主控台将罐倾斜至扒渣角度(以铁水不能溢出为准),然后进行扒渣操作。
2.2 接通扒渣机电源并选择好手动或自动操作方法(扭动转换操作手柄)。
2.3 启动前,要确认清楚手动(ISW)或自动(3PL)灯光显示和紧急停车手动按扭的位置;压缩空气的入口压力达到0.6-0.8MPa、操作压力>0.45 MPa;扒渣机小车前端极限设在零位、后退端极限应设在拾位上,否则不允许运转。
2.4 调整大臂高度,先试扒后再调整适宜高度进行正式扒渣作业(扒渣机的前后行程5-6米,高度调整为0.9米,左右旋转角度为12.5度)。
2.5 当罐内铁水中带有大于600kg的渣块时,原则上不能强行扒渣,应将铁水返回到混铁炉。
2.6 前渣扒至铁水裸露≥1/3且无块砣状渣块漂浮;后渣扒至铁水裸露≥2/3,直兑及入低混扒至铁水裸露≥3/4。
2.7 回落铁水缶,关停扒渣操作,将指令送至现场卷场操作人员。
3 卷场操作3.1 运行前必须检查主操作台电源转换开关,确认钢丝绳及抱闸正常,进行试运转后方能使用。
铁水预处理-脱硫

【本章学习要点】本章学习铁水预处理脱硫的优点,常用脱硫剂种类及其反应特点,脱硫生产指标,KR法脱硫的生产工艺流程和脱硫的基本操作,混铁车喷吹脱硫的工艺特点和工艺操作。
第一节铁水预脱硫的概念和优点铁水预处理,炼钢生产中主要是指铁水在进入转炉之前的脱硫处理。
广义的铁水预处理是指包括对铁水脱硫、脱硅、脱磷的三脱处理,另外还有特殊铁水的预处理,如含V铁水的提V等。
铁水脱硫是二十世纪70年代发展起来的铁水处理工艺技术,它已成为现代钢铁企业优化工艺流程的重要组成部分。
铁水脱硫的主要优点如下:1.铁水中含有大量的硅、碳和锰等还原性的元素,在使用各种脱硫剂时,脱硫剂的烧损少,利用率高,有利于脱硫。
2.铁水中的碳、硅能大大提高铁水中硫的活度系数,改善脱硫的热力学条件,使硫较易脱致较低的水平。
3.铁水中含氧量较低,提高渣铁中硫的分配系数,有利于脱硫。
4.铁水处理温度低,使耐火材料及处理装置的寿命比较高。
5.铁水脱硫的费用低,如在高炉、转炉、炉外精炼装置中脱除一公斤硫,其费用分别是铁水脱硫的2.6、16.9和6.1倍。
6.铁水炉外脱硫的过程中铁水成份的变化,比炼钢或钢水炉外处理过程中钢水成份的变化对最终的钢种成份影响小。
采用铁水脱硫,不仅可以减轻高炉负担,降低焦比,减少渣量和提高生产率,也使转炉也不必为脱硫而采取大渣量高碱度操作,因为在转炉高氧化性炉渣条件下脱硫是相当困难的。
因此铁水脱硫已成为现代钢铁工业优化工艺流程的重要手段,是提高钢质量、扩大品种的主要措施。
早期的铁水脱硫方法有很多种:如将脱硫剂直接加在铁水罐罐底,靠出铁铁流的冲击形成混合而脱硫的铺撒法。
也有将脱硫剂加入装有铁水的铁水罐中,然后将铁水罐偏心旋转或正向反向交换旋转的摇包法。
之后逐步发展至今天采用的KR搅拌法及喷枪插入铁水中的喷吹法。
第二节常用脱硫剂及脱硫指标一、常用脱硫剂经过长期的生产实践,目前选用作为铁水脱硫剂的主要是Ca、Mg、Na等元素的单质或化合物,常用的脱硫剂主要有:Ca系:电石粉(CaC2)、石灰(CaO)、石灰石(CaCO3)等Mg系:金属Mg粉Na系:苏打(Na2CO3)二、常用脱硫剂反应特点1.电石粉碳化钙脱硫反应为用CaC2脱硫有如下特点:1)在高碳系铁水中,CaC2分解出的Ca离子与铁水中的硫有极强的亲和力。
铁水脱硫理论

铁水脱硫理论、生产知识培训之一1、铁水脱硫的意义硫对绝大部分钢种都是非常有害的,降低钢中的硫含量,有利于提高钢的机械、工艺等性能,以满足市场需要。
在铁水中进行脱硫已成为现代钢铁工业优化工艺流程的重要手段。
2、什么是铁水预处理?铁水预处理是指铁水兑入炼钢炉之前,为脱硫或脱硅、脱磷而进行的处理过程。
3、铁水脱硫的优点:(1)铁水中碳、硅等元素含量高,氧含量低,有利于脱硫。
(2)脱硫剂利用率高,脱硫效率高,脱硫速度快。
(3)提高炼铁和炼钢的生产能力,节约工序能耗,降低成本。
(4)提高了钢铁企业钢材的综合经济效益。
4、铁水脱硫的主要方法有哪些有(1)投入法(2)铁水容器搅拌脱硫法(3)采用搅拌器的机械搅拌法(4)喷吹法5、KR搅拌脱硫法有哪些优、缺点?KR脱硫搅拌能力强,可将铁水硫含量脱至很低,缺点是设备复杂,铁水温降大。
6、简叙KR搅拌脱硫的方法:KR搅拌脱硫,是采用一个浇筑有耐火材料外衬的十字搅拌器,插入到铁水罐中进行旋转搅拌,使铁水产生旋涡,将投入到铁水液面的脱硫剂卷入并与铁水充分混合发生脱硫反应。
7、铁水脱硫常用的脱硫剂有哪些?生产中,铁水脱硫常用的脱硫剂有电石粉(CaC2)、石灰粉(CaO)、石灰石粉(CaCO3)、苏打粉(Na2CO3)、金属镁等。
8、CaC2脱硫剂有哪些优点?(1)有很强的脱硫能力(2)铁水温降小(3)不易回硫(4)对铁水容器的耐火材料衬浸蚀较轻9、CaC2脱硫剂有哪些缺点?(1)易燃易爆,运输储存困难(2)加工生产能耗高,价格贵(3)对环境产生污染10、用CaC2 脱硫,其脱硫反应是放热反应还是吸热反应?其脱硫反应是放热反应。
11、CaC2脱硫剂极易吸潮,并产生乙炔气体(C2H2)。
12、CaC2脱硫剂安全使用要点:(1)乙炔浓度控制在0.5%以下(2)氮气露点低于-10°C。
(3)设备系统发生CaC2泄漏,要立即联系修复。
(4)泄漏CaC2要及时清理。
(5)储料间严禁水,火。
金属冶炼脱硫工艺
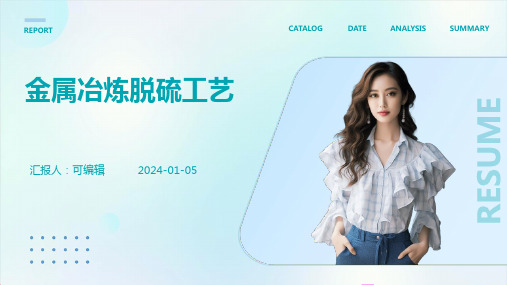
利用还原剂将有色金属冶炼过程中的 硫化物还原成单质硫,再通过分离、 回收等手段去除。该技术具有成本低 、操作简单等优点,但脱硫效率较低 ,需要多次循环处理。
贵金属冶炼脱硫技术
离子交换法
利用离子交换剂吸附贵金属冶炼过程中的硫化物,再通过洗涤、再生等手段去除。该技术具有选择性好、处理效 果好等优点,但成本较高、操作复杂。
反应模型建立
建立反应模型,模拟和预测脱硫过 程,指导工艺优化。
04
REPORT
CATALOG
DATE
ANALYSIS
SUMMAR Y
06
金属冶炼脱硫工艺的环 境影响与可持续发展
工艺的环境影响评价
空气污染
01
金属冶炼过程中产生的硫化物和烟尘等污染物,对大气环境造
成严重污染。
水体污染
02
脱硫工艺过程中产生的废水含有重金属离子和硫化物等有害物
吸附脱硫技术
利用吸附剂将稀有金属冶炼过程中的硫化物吸附在表面,再通过洗涤、再生等手段去除。该技术具有 脱硫效率高、操作简单等优点,但吸附剂的制备和再生较为困难。
REPORT
CATALOG
DATE
ANALYSIS
SUMMAR Y
05
脱硫工艺的优化与改进
工艺参数优化
温度控制
通过调整反应温度,优化脱硫效果,提高脱 硫率。
燃料中硫分
冶炼过程中使用的煤炭、焦炭等燃料可能含有硫分,燃烧后会产生 硫氧化物。
添加剂或杂质
在金属冶炼过程中,可能使用含有硫的添加剂或原料中含有其他含 硫杂质。
硫对金属的影响
降低金属纯度
硫是金属冶炼的有害杂质之一,会降低金属的纯度和质量。
热脆性
铁水预脱硫
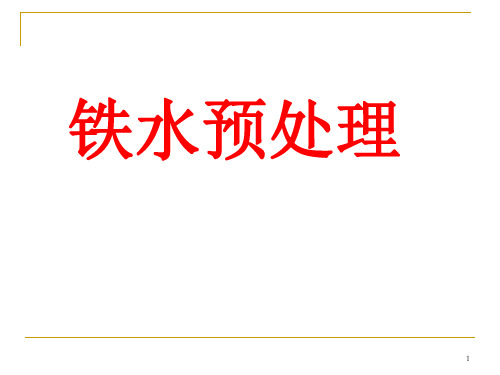
习题
6.铁水预处理脱硫剂包括( A.石灰 A.石灰 A.石灰 A.CaO B.苏打 B.苏打 B.苏打 B.CaC2 C.电石 C.电石 C.电石 C.Na2CO3 7.铁水预处理脱硫剂( )。 D.金属镁 D.金属镁 )扒渣容易。
8.铁水预处理加入脱硫剂(
9.铁水预处理采用(
)造成温度降低。
D.金属镁 D.Mg )脱硫剂扒渣效率最高。
特点
特点
常见方法:
KR法、DO法、RS法和NP法
常见方法:
KR铁水脱硫
由搅拌器和脱硫剂输送装置等 部分组成。 搅拌器头部是一个“十”字形叶轮, 内骨架为钢结构,外包砌耐火 泥料。 搅 拌 器 以 150~300r/min 速 度 旋 转 搅 动 铁 水 , 1~1.5min 以 后 , 使铁水形成旋涡,加入脱硫剂, 通过搅动,铁水与脱硫剂密切 接触,充分混合作用。
12、(单选)铁水预处理脱硫剂石灰的主要成分是(A
D.Mg )。 13、(单选)KR缩写在冶金中代表( D A.炼铁直接还原 C.连铸一种新设备
)。
习题
14、铁水炉外脱硫原理是:使用与硫的亲和力比铁与硫的亲和 力大的元素并生成稳定的和不溶于铁液的硫化物。( ) 15、常用的铁水炉外脱硫剂有碳化钙、石灰、金属镁和苏打。 ( ) 16、铁水预处理( A.CaO B.CaC2 )脱硫剂在液面深处脱硫效果好。 C.Na2CO3 )。 D.Mg
16
KR铁水脱硫
采用CaO-CaF2-CaC2系 脱硫剂; 脱硫剂作用时间长; 大约12min脱硫反应可基 本达到平衡; 脱硫处理时间较喷粉工艺 缩短5min; 脱硫效率提高20-35% 左右。
- 1、下载文档前请自行甄别文档内容的完整性,平台不提供额外的编辑、内容补充、找答案等附加服务。
- 2、"仅部分预览"的文档,不可在线预览部分如存在完整性等问题,可反馈申请退款(可完整预览的文档不适用该条件!)。
- 3、如文档侵犯您的权益,请联系客服反馈,我们会尽快为您处理(人工客服工作时间:9:00-18:30)。
铁水脱硫技术的研究进展摘要:介绍了近几年我国铁水脱硫预处理技术的应用发展情况及达到的效果。
对铁水脱硫预处理的不同工艺、不同技术装备作了对比介绍,分析了不同处理工艺和不同装备的特点,提出了脱硫工艺的选择思路。
关键字:铁水;脱硫;扒渣;脱硫剂Abstract:China's desulphurization pretreatment technology development and achieve results in recent years are Introduced. Hot metal desulphurization pretreatment different process, technology and equipment are compared. Analyzed the different treatment processes and the characteristics of different types of equipment as well as proposed desulfurization process of selection idea.key wods: hot metal; desulphurization;slag skimming; Desulfurizer硫在生铁中是有害元素,它促使铁与碳的结合,使铁硬脆,并与铁化合成低熔点的硫化铁,使生铁产生热脆性和减低铁液的流动性。
对大多数钢种,硫都能使其加工性能和使用性能变坏。
一般钢种要求含硫量不得超过0.05%,优质钢种要求含硫量不得超过0.02^0.03,超低硫钢要求含硫量小于0 .005%。
20世纪50~60年代世界上有的钢厂由于铁水含硫高(大于0.08%),而对铁水脱硫进行了研究和应用。
70年代由于二次世界石油危机使生产成本大幅提高,世界钢产量1978年突破7亿t后到1982年下降到6.46亿t,这时,汽车工业为减重节能对钢材性能提出了更高要求。
因此,70~80年代以降低成本、提高质量和开发品种为主的新工艺、新技术得到广泛研究和迅速应用,连铸和炉外精炼技术发展很快。
在西欧60年代后期、日本70年代初期对铁水预处理研究工作的基础上,于70年代后期用于生产,80年代在发达国家获得广泛应用,并成为钢铁生产中必不可少的工序,完善钢铁生产工艺最有效的技术之一〔3〕、生产低硫磷(〔S〕、〔P〕不大于0.015%)和超低硫磷钢(〔S〕、〔P〕不大于0.005%)的必要手段,是实现经济炼钢的必要前提。
我国武钢、太钢、宝钢、攀钢和宣钢等非常重视铁水预处理技术,70年代后期就引进了这一技术并进行了研究,80年代陆续投入生产。
以后又有十几个钢铁企业做了大量工作,但由于长期以来突出产量,忽视质量品种,直到1998年我国铁水预处理比才达22%左右。
我们由钢铁大国向钢铁强国的转变过程中,铁水预处理技术必然会获得应有的地位,取得重大发展。
对大多数钢种,硫都能使其加工性能和使用性能变坏。
一般钢种要求含硫量不得超过0.05%,优质钢种要求含硫量不得超过0.02%,超低硫钢要求含硫量小于0 .005%。
目前,由于铁矿石和焦炭以及喷吹燃料含硫量高,只靠高炉和转炉冶炼难以达到低硫钢和超低硫钢要求的含硫指标。
为了解放高炉,减轻转炉负担,铁水予脱硫具有现实意义。
近一、二十年,许多冶金工作者在铁水脱硫剂的研制和铁水脱硫方法的改进方面,做了大量的试验研究工作。
本文是在这一基础上,从冶金反应的热力学和动力学角度,进一步对铁水脱硫反应进行了分析讨论。
目前,广泛使用的铁水脱硫方法,一是通过浸人铁水申的喷枪往铁水中喷人脱硫剂的喷射脱硫法,另一种是在铁水巾转动用耐火材料制的搅拌叶轮,将脱硫剂与铁水充分搅拌混合进行脱硫的KR法。
在设备费用方面,以构造简单的喷射法比较便宜,但此法一旦喷人的脱硫剂浮到铁水液面上就几乎不再发生反应,以致会残留大最未起反应的生石灰,脱硫剂单位消耗量相当大。
而KR 法则由于不断搅拌使铁水与脱硫剂充分混合,故有生石灰利用效率高并可将铁水脱硫到硫含量很低的优点。
1喷射法喷射法是利用惰性气体为载体将脱硫粉剂喷入铁水中,使细小的脱硫剂尽可能均匀的分散在铁水中,载气形成气泡搅动铁水,从而大大提高脱硫速度、脱硫率和脱硫剂利用率。
CaCZ(电石粉)。
其优点有:①有很强的脱硫能力;②脱硫反应是放热反应,有利于减少温降;③消耗量少,渣量少;脱硫产物疏松,扒渣方便,对铁水罐内衬侵蚀轻。
缺点有:①极易吸潮劣化,降低反应效果,且使运输、贮存困难;②价格昂贵,成本高。
(2)CaO(石灰粉)。
其优点有:①有较强的脱硫能力;②脱硫产物疏松,扒渣方便,对罐衬侵蚀轻;③资源广,价格低,易加工.使用安全。
缺点有:①耗量大,渣量大;②流动性差,在料罐中易“架桥”堵塞;③极易吸潮劣化,降低反应效果,且使运输、贮存较为困难。
(3)NaZCO3(苏打)。
其优点有:①有很强的脱硫能力;②脱硫的同时还能脱磷;③处理后渣中的苏打呈水溶性,可回收利用。
缺点有:①在1250℃以上易挥发、分解,铁水温降大,污染环境;②对罐衬侵蚀严重;③来源短缺,成本高。
(4)Mg。
优点有:①脱硫能力很强,反应快,渣量少;②沸点低,在铁水中气化,形成气泡,增强脱硫效果;③可溶于铁水,有利于脱硫和防止回硫。
缺点有:①在高温下气化,难于加入铁水中;②价格高,处理成本高。
由于铁水常用脱硫剂各有优点和不足,故将它们组合起来,取长补短,形成高效复合脱硫剂成了当今脱硫剂研制开发的重点。
随着铁水脱硫技术的不断发展,脱硫剂的研制与应用呈现两个基本趋势:一是以石灰基为主的脱硫剂;二是发展配加石灰、电石、焦炭等的金属镁脱硫剂。
为改善环境,在复合脱硫剂中配加工业废渣(如转炉渣)也将越来越受到重视。
在脱硫剂的选购及使用上,将不再单纯迫求高脱硫率,而是更多地考虑消耗、渣铁分离的难易程度等技术经济指标以及综合经济效益。
为了降低铁水处理成本,进行了喷吹纯镁工艺的技术改造。
该工艺系统由贮料罐、喷吹给料罐、喷枪架、喷枪、称量装置、输送管道、阀门及控制系统组成,贮料罐、喷枪架及辅助的扒渣、除尘设施都利用原有设备,喷吹罐体积小(容积约0.53 m3),现有平台空间及结构载荷能适应新工艺技术改造的需要,工艺技术改造的工程量不大,改造工期仅一个多月,改造期间基本不影响正常生产。
2001年底投入使用,在生产中不断进行优化改进。
(1)建立喷吹模型。
通过对脱硫率、铁水条件、脱硫深度、载气流量、喷吹强度等数据整理分析,建立了喷吹模型,实现了计算机自动控制喷吹操作,不断优化操作程序,脱硫终点目标命中率达到86 %。
(2)喷枪的改进。
优选耐材材质,改进制作程序,对气化室内壁喷脱渣涂料,气化室内铁渣容易清理脱落,避免内腔受损,很好地解决了内壁粘渣问题,使喷枪处理频率和劳动强度大为降低,喷枪寿命平均120次,比原工艺提高2.43倍。
同时保证了气化室内腔正常形状尺寸,镁得以充分气化,促进脱硫反应。
(3)优化操作模式,提高实用性。
由于喷吹强度低,前渣对脱硫操作影响不大,除有大块高炉渣需扒除外,取消扒前渣工序。
为解决脱硫后渣稀少,扒除操作困难问题,开发了粘渣操作工艺,基本满足了快速扒除干净的要求,提高了操作实用性KR搅拌式脱硫法是日本新日铁广烟制铁所于1963年开始研究、1965年应用于工业生产的一种铁水炉外脱硫技术。
这种脱硫方法是以一个外衬耐火材料的搅拌器浸入铁水罐内进行旋转搅动铁水,使二以水产生旋涡同时加入脱硫剂使其卷入铁水内部进行充分反应,从而达列铁水脱硫的目的。
它具有脱硫效率高,脱硫剂耗少、铁水温降小、作业时间短,金属损耗低以及耐火材料消耗低等特点。
首先,将从高炉区域运输到炼钢车间的1270~1350℃铁水通过铁水罐倾翻车运输至喷吹处理位置,测温、取样分析铁水中初始硫含量,然后根据钢种要求的目标硫含量确定其Mg粉和CaO粉的喷吹量,下降喷枪通过助吹气体将两者粉剂在喷吹管道内按比例混合后喷入铁水中,在喷吹的过程中,铁水也被助吹的气体搅拌从而使脱硫剂和铁水中的[S]充分接触生产硫化物夹杂物,通过扒渣机将上浮至铁水表明的脱硫渣扒除。
最后,开出铁水罐倾翻车,将处理后的铁水直接兑入炼钢转炉内。
喷吹铁水预处理因其明显的经济价值,已经引起了各个钢铁企业的重视,可以肯定在未来的几年内该技术将会成为炼钢前必不可少的一道工序,所以该技术在国内有着广阔的发展空间。
铁水复合喷吹脱硫工艺、设备简单,占地少,投资省。
并且该工艺具有温降小、不易回硫、良好的反应动力学条件和处理时间短等优点。
而且我国的镁资源相当丰富,大量使用镁基脱硫是我国钢铁工业难得有利条件。
因此,复合喷吹铁水脱硫方式是值得推广和普遍采用的高效脱硫技术。
2 KR法KR脱硫工艺对脱硫处理前、后的铁水均要进行扒渣作业,以保证脱硫效率。
其扒渣作业由扒渣机按自动或手动两种控制方式进行。
扒渣机使用压缩空气作动力,压力为0.55一0.7MPa(表压),气体耗量为14m3/min(最大操作耗量),空压机设计选用螺杆式,能力为27.sma/min,压力0.7MPa,马达容量160kw,自带后冷却器及贮气罐等设备。
扒渣机扒渣时前后行程为3m(最大6m),行进速度为1.0~1.sm/s(可调),通常使用0.5一1.0m/s,扒渣板上下行程900mm,可用千斤顶调整高度,其调整范围为1000m,。
扒渣板由16mm厚的普通钢板制成,其尺寸为450又400X16mm。
此外,为扒除铁水罐边部的熔渣,扒渣机前端的机械手可以左右旋转,旋转角度为士12.5。
使用的专用铁水罐容量为100t,每一处理周期扒渣两次(高炉铁水渣和脱硫渣),每次作业时间5一10mhi。
扒渣作业通常采用手动控制。
当铁水面外露约2邝以上时,扒渣操作即停止。
扒渣机的扒渣能力约60okg。
2.搅拌器搅拌器是KR脱硫装置中的重要部件,它是由棒芯及十字型的叶片组成。
其表面分别炼钢门1·涂一层不同理化性能的浇注耐火材料。
搅拌器的外形尺寸示意如图,搅拌器在铁水脱硫处理过程中要承受高温铁水、熔渣的冲刷、浸蚀、急冷急热等物理及化学作用。
因此搅拌器用的浇注料及耐火涂料要具有耐高温、耐冲刷、耐浸蚀、耐热震等性能。
同时耐火涂料(修补用料)还要具有粘结性好、热硬性好、修补方便、使用次数多等特点。
搅拌器的使用次数与所用脱硫剂的种类有关。
原引进专利中采用CaC:作脱硫剂,搅拌器使用次数一般为90一100次。
在使用过程中视搅拌器损坏部位和程度予以修补,使用后期修补次数较多。
一般铁水脱硫处理,用耐火材料衬里,实际上使用42%A1203含量的粘土质的时候很多,在这种情况下,碳化钙脱硫处理后,长时间持续与耐火材料衬里接触,会充分发生上述反应,因此要考虑耐火材料衬里必须用高铝质耐火材料林换。