闭模工艺在船舶行业中的应用
船舶内装设计工艺与材料应用

船舶内装设计工艺与材料应用摘要:船舶内部装饰的宜居性在船舶整体性能中发挥着越来越重要的作用和作用。
良好的舱室布局设计、合理的人机关系、高效的设计工具、科学的设计方法和流程,可以极大地提高船舶室内装饰设计的整体水平和效果。
本文以船舶室内设计原理为基础,以提高船舶室内设计的效果和有效性为出发点。
通过完善完整的室内设计知识体系,改进船舶室内设计的流程和方法,加强室内设计工具的开发和应用,引用新的设计理念,逐步建立规范、科学、合理的室内设计标准,使船舶室内设计在外观上,空间布局装饰效果和人机环境能更好地满足现代船舶的性能需求,满足现代船员对人性化、美观、舒适的海洋生活和工作环境的更高要求,满足人类在海洋工作环境中的心理和生理健康需求。
关键词:船舶;内装设计;工艺;材料应用1船舶室内设计的基本原则1.1适用性和标准化适用性和标准化是船舶内部设计的首要标准。
在这里,内部设计不仅要满足技术规范的要求和IMO、船旗国和船级社的要求,还要实现船舱的最佳使用功能,以满足船舶的性能和要求。
1.2合理性和安全性安全性和合理性是指客舱的设计和布局不仅满足结构组织的合理性和空间布局的要求,还满足机组人员的日常工作、休闲、娱乐等需要,还满足防火、人员疏散、逃生和疏散的安全要求。
1.3舒适和经济舒适性和经济性是船舶室内设计的先进标准。
海事法规也越来越关注海员工作和生活的舒适性。
同时,现代船舶也对船舶内部装修的豪华舒适性提出了越来越高的要求,而经济性是运营船舶的一个重要指标。
因此,在船舶舒适性要求较高的情况下,船舶室内装饰设计应深入优化舱室布局和空间设计,优化各系统的施工工艺,优化材料和设备的选择,具有经济性。
2船舶内装设计工艺与材料2.1船舶内装设计工艺2.1.1模块化工艺模块化技术在船舶内部设计中的应用主要包括:第一,标准化设计。
要求所有节点的标准化设计和系列产品之间的标准化连接。
第二,模块化设计。
模数是指所选的尺寸单位,通常用作比例协调的增值单位。
浅谈船舶合拢工艺
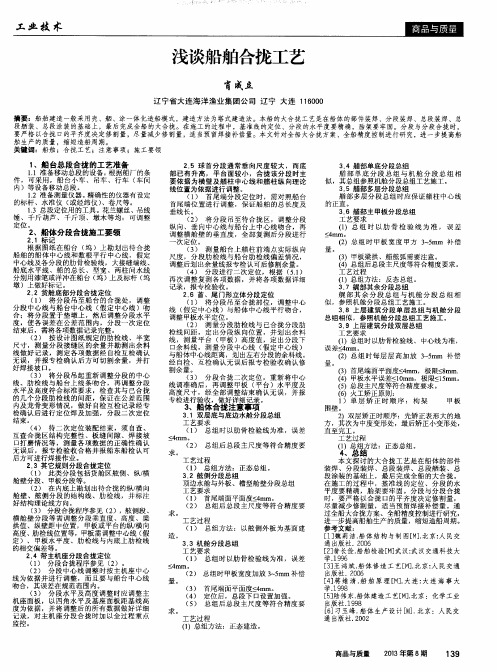
浅谈船舶合拢工艺
肖 成立
辽 宁 省 大 连 海 洋 渔 业 集 团公 司 辽 宁 大 连 1 1 6 0 0 0
摘要 :船舶建造 一般采用 壳 、 舾 、涂 一体 化造 船模 式 ,建造 方法为塔式建造法。本船的大合拢工 艺是在船体 的部件装焊 、分段装焊 、总段装焊、总 段舾装 、总段涂装 的基础上 ,最后完成全船 的大合拢 。在施 工的过程 中,基准线 的定位 、分段 的水平度要精确 ,胎架要牢 固。分段 与分段合拢 时, 要严格 以合拢 口的平 齐度 决定修割量 ,尽量减 少修割量 ,适 当预 留焊接补偿量。本文针对全船大合拢方案 、 全 船精度控制进行研究 , 进 一步提 高船 舶生产 的质量 ,缩 短造船周 期。 关键词 :船舶 ;合拢 工艺;注意事项 ;施工要领
一
3 . 4艏部单底分段总组 艏 部 单底 分 段 总 组 与机 舱 分段 总组 相 似 ,其总组参照机舱分段总组工艺施工 。 3 . 5艏部多层分段总组 艏部 多层分段 总组时应保 证艏柱 中心线 的正直。 3 . 6艏部主甲板分段总组 工 艺 要 求 ( 1 )总 组 时 以肋 骨 检 验 线 为 准 , 误 差
误差_ < 4 mm。
< 4 am 。 r
( 2 )总组 时 甲板 宽度 甲方 3 - 5 mm 补 偿
量。
( 3 )甲板梁拱、艏舷弧需要注意 。 ( 4 )总组后总段主尺度等符合精度要求 。 工 艺 过 程 ( 1 )总 组 方 法 : 反 态 总 组 。 3. 7艉 部 其余 分 段 总组 艉 部 其 余 分 段总 组 与 机舱 分 段 总 组相 似 ,参 照机舱 分段 总组工艺施工。 3 . 8 上层建筑 分段单 层总组 与机 舱分段 总组相似 ,参 照机舱 分段总组工 艺施工 。 3 . 9 上 层 建 筑 分 段双 层 总组 工 艺要 求 ( 1 )总组时以肋 骨检验线、中心线为准 ,
模块化在船舶设计中的应用

一、引言船舶制造业如同其它制造业一样,随着科学技术的发展,市场竞争越来越激烈,竞争的焦点主要体现在:缩短船舶产品建造周期、提高质量和性能以及降低成本,故只有采用先进的造船技术和造船模式方能立于不败之地.由于船舶产品的复杂性和制造规模,使其难以实现批量化生产.船舶制造成本高,投资回收期长、风险大,且制造厂需要满足船东的多样化需求,这种多品种、单件小批生产模式给标准化工作带来了极大的困难,使设计工作量大,制造周期长成了船舶制造业的顽疾.模块化提供了一种有效的解决途径,它可以利用已标准化、系列化的模块,迅速组成整船。
在降低产品开发成本,缩短建造周期的同时,亦能满足客户的个性化需求.此外,模块化技术既便于船舶设备与系统的操作与维护管理,又利于船舶功能的日后修复与改装,大大提高了船舶产品整个生命周期的经济性.目前,模块化造船技术得到了广泛的研究,为全球造船业争相开发应用。
二、模块化造船概述所谓模块,就是可组合成系统的、具有某种功能和接口结构的、典型的通用独立单元.模块是模块化产品的基本组成元素,是一种实体的概念模块化产品设计过程中,通过不同模块的组合和匹配可以产生大量的变型产品,使其具有独特的功能、结构及性能特点和层次.因此,模块化产品设计使企业可以通过组合现有模块或新模块,快速、低成本地生产出能够适应市场和技术变化的产品。
船舶建造是一项庞大的工程,船舶模块相比其它行业的模块也要复杂得多.船舶模块可分为结构模块和功能模块,它们都具有特定的界面、连接尺寸及连接形式,具有独立的功能和良好的通用性.结构模块是指具有尺寸互换性的结构部件,其安装连接部分的几何参数满足某种规定的要求,而能保证通用互换或兼容.如舱壁模块、甲板模块等,不但可以在一艘船的船舱区域通用,还可以在载重量相当的不同船舶的相同区域互换.功能模块是具有相对独立的功能,并具有功能互换性的功能部件,其性能参数和质量参数(常指线性尺寸以外的特性参数)能满足通用互换或兼容的要求.如机舱设备模块、上层建筑的舱室模块、梯道模块等可以在不同船型上通用.通过标准模块的重新组合,有效减少了船舶设计工作量,能快速提供多样化的新船型以适应市场的需求。
消失模工艺流程
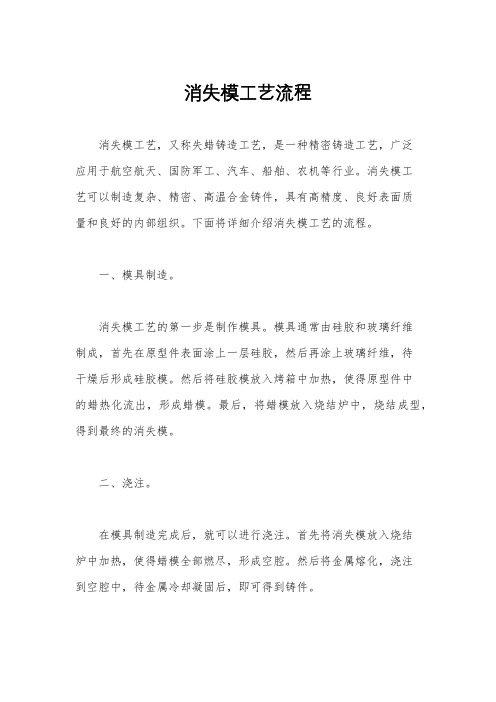
消失模工艺流程消失模工艺,又称失蜡铸造工艺,是一种精密铸造工艺,广泛应用于航空航天、国防军工、汽车、船舶、农机等行业。
消失模工艺可以制造复杂、精密、高温合金铸件,具有高精度、良好表面质量和良好的内部组织。
下面将详细介绍消失模工艺的流程。
一、模具制造。
消失模工艺的第一步是制作模具。
模具通常由硅胶和玻璃纤维制成,首先在原型件表面涂上一层硅胶,然后再涂上玻璃纤维,待干燥后形成硅胶模。
然后将硅胶模放入烤箱中加热,使得原型件中的蜡热化流出,形成蜡模。
最后,将蜡模放入烧结炉中,烧结成型,得到最终的消失模。
二、浇注。
在模具制造完成后,就可以进行浇注。
首先将消失模放入烧结炉中加热,使得蜡模全部燃尽,形成空腔。
然后将金属熔化,浇注到空腔中,待金属冷却凝固后,即可得到铸件。
三、去除模具。
铸件冷却后,需要将模具去除。
首先将铸件放入水中冷却,使得模具收缩,然后用机械或化学方法将模具去除,得到最终的铸件。
四、后处理。
铸件去除模具后,还需要进行后处理。
包括去除表面氧化皮、修磨、热处理等工艺,以提高铸件的表面质量和内部组织。
五、检验。
最后,需要对铸件进行检验。
主要包括外观检验、尺寸检验、化学成分分析、金相组织分析等,以确保铸件符合设计要求。
通过以上流程,消失模工艺可以实现对复杂、精密铸件的生产,具有较高的成型精度和表面质量。
同时,消失模工艺还可以减少后续的加工量,提高生产效率,降低生产成本。
因此,在一些对铸件质量要求较高的领域,消失模工艺得到了广泛的应用和推广。
总之,消失模工艺是一种先进的精密铸造工艺,通过精密模具制造、浇注、去除模具、后处理和检验等环节,可以实现对复杂、精密铸件的生产,具有较高的成型精度和表面质量,是目前铸造行业中的一种重要工艺方法。
玻璃钢船艇闭模灌注成型工艺

动进入模腔浸渍并最终充满模腔 , 并在此状态下 固化
成型。
鉴 于玻 璃 钢 / 合材 料 成 型 时不 需 太 大压 力 的特 复 点, 闭模 成 型工艺 又从 硬质 模具 发展 到 半硬 质 模具 , 即 用 玻璃 钢模具 代替 金属 模 具 ,用干 法成 型 代替 模 塑 料 压制 ,用 常 温 固化 取代 加 热 固化 ,此举 不但 脱 离 了压 机, 降低 了成 本 , 且使 制 品尺 寸 不受 限制 , 玻璃 钢 而 为 船艇 生产开辟 了一条新 的工 艺方 法 。 为进 一步 降低模 具成 本 ,又 开发 了半硬 质 模具 与 弹性膜 材相 结合 的闭模方 式 ,液 体树 脂 借助 抽 真空 形 成 的负压进 入模 腔 , 此谓 灌 注法 (R ) L I。灌 注法 又发 展 了使用 一种 有半 渗 透 陛的特殊 膜 , 只能 通过 空 气 , 它 不
止 , 在 广泛 使 用 。甚至 在 国际船 艇展 览会 上 , 还 一些 国 外 客 商还 特地 表示此 艇 为手工 制作 , 以示 品位很 高 。 事 物 总 是 向前发 展 的 , 糊 工艺 也 同样需 要不 断完 善 、 手 提 高 和发 展 。 国外 玻璃 钢 / 复合 材料 行业对 成 型方法做 了 很 多探 讨 , 开发 了不少 新 的成 型工 艺 , 些玻 璃 钢造 船 一 企 业 也 在 此基 础 上结 合 造 船 特 点 研 发 了一 些 成 型 技 术, 成功 地应 用 于玻璃 钢造船 上 。 如方法 各 异的 闭模 例 成 型法 , 合 于建 造大 尺度船 的预浸渍法 等 。 文仅对 适 本
工艺的基础上又发展了树脂膜灌注工艺 ( F )其使用 R I, 的树 脂为非 液态 , 而是 粘度 较大 的树脂 膜 。 树脂 膜与 将 增强 材料 交替 铺放 于模 具 中 , 闭模后 放人 真 空 烘箱 中 , 树脂在加热下变成流体浸渍增强材。 此法成本很高 , 不
船舶建造工艺的发展现状及改进探讨

船舶建造工艺的发展现状及改进探讨船舶建造工艺是船舶制造业的核心技术之一,它直接影响着船舶的性能、质量和经济效益。
随着科学技术的发展和航运业的需求变化,船舶建造工艺也在不断创新和改进。
本文将就船舶建造工艺的发展现状及改进探讨进行分析和探讨。
一、船舶建造工艺的发展现状1. 传统船舶建造工艺传统船舶建造工艺主要包括钢结构船舶的焊接和钢质船舶的铆接工艺。
这种工艺方式制造成本低、技术成熟、工期短,但随着船舶尺寸的增大和各种外部环境的影响,传统工艺已经不能适应现代船舶需求。
随着数控技术的应用,船舶建造工艺得到了很大发展。
数控切割机、数控焊接机、数控加工中心等设备的应用,提高了船舶建造的精度和效率,降低了材料浪费,减少了劳动力成本,是船舶建造工艺的一大进步。
3. 模块化建造工艺模块化建造工艺是现代船舶建造的一种重要发展方向。
它将船体分割成若干个可以独立制造的模块,然后再将这些模块组装成完整的船体。
模块化建造工艺大大提高了船舶建造的工作效率,缩短了生产周期,降低了船舶建造成本,是目前船舶建造工艺的一个创新突破。
1. 新材料的应用随着碳纤维材料、复合材料、高强度钢材等新材料的发展和应用,船舶建造工艺将迎来新的突破。
这些新材料具有重量轻、强度高、耐腐蚀、抗疲劳等优点,可以大幅提高船舶的性能和经济效益。
2. 自动化技术的应用自动化技术的应用将大大提高船舶建造工艺的效率和精度。
采用机器人进行船舶焊接、涂装、拼装等工艺,可以减少人力成本、提高作业安全性和质量稳定性。
3. 绿色环保工艺随着全球环境保护意识的日益增强,船舶建造工艺也需要进行绿色环保改进。
采用环保材料、节能环保工艺、减少污染排放等做法,将是船舶建造工艺的未来发展方向。
4. 智能化工艺智能化工艺将是船舶建造工艺的重要发展趋势。
通过物联网、大数据、人工智能等技术的应用,实现船舶建造全过程的智能化管理和控制,将大大提高船舶建造的生产效率和质量水平。
结语:船舶建造工艺的发展与变革是不断前进的,新材料的应用、自动化技术的应用、绿色环保工艺、智能化工艺等将是船舶建造工艺的重要发展方向。
复合材料几种闭模成型工艺比较介绍及区别

对于真空注射、RTM、SRIM等三种闭模工艺而言,设备投资以SRIM最高,其次RTM,真空注射最低。这些工艺方法,在加工周期、自动化水平、批量大小等方面,也有一定规律性。
当前,许多国家都对生产环境苯乙烯含量的法定标准,作了严格的规定,例如,英国100ppm;法国50ppm;德国20ppm;瑞典20ppm;挪威 25ppm;荷兰50ppm。为此,积极寻找降低苯乙烯挥发量的方法,已成为玻璃钢业界的一个重要课题。闭模工艺技术,是降低苯乙烯挥发量的一种有效手段。 本文将专门评述几种闭模工艺技术的有关方面。
例如,加工周期以SRIM为最短(约8分钟左右),RTM次之(10~80分钟左右),真空注射成型最长(1个多小时至10多个小时)。自动化水平,以SRIM为最高,它的年生产能力也最高,生产成本中所含劳动力费用最低。
上述这些工艺均采用树脂注射的方法,一个重要的区别,在于增强材料,是在闭合模具以前,还是在树脂浸渍以前,放进模具之中。这对于控制增强材料的含量和定向排列,无疑是一个十分重要的因素RTM、SRIM 工艺,由于采用对模技术,因而对玻璃纤维含量的控制较为有利。必须指出,当采用闭模工艺技术时,所用的树脂也是至关重要的。通常采用真空注射专用树脂,低收缩 RTM 树脂,以及混合型树脂等。
(1)真空注射模塑工艺
该工艺采用树脂注射技术,并辅以真空,以有助于注射过程。通常,有一个可变形的膜,以作为模具的另一面。模具的一半,一般可利用手糊模具或喷射成型模具,只需稍加修改即可使用。这种工艺不需要大量的模具或设备投资,生产批量较大产品质量较高。
船舶建造工艺现代造船模式

船舶建造工艺现代造船模式概述船舶建造工艺现代造船模式是指在船舶制造领域中,采用现代先进技术和工艺,通过系统化、模块化的组织方式进行船舶的建造。
这种模式注重效率、质量和安全,能够提高船舶的建造速度和质量。
模块化建造现代造船模式的核心是模块化建造。
传统的船舶建造方式是采用序列化建造方式,即按照一定的顺序进行建造。
而模块化建造将船舶的结构划分成多个相对独立的模块,这些模块可以独立设计、制造和测试,然后在船坞中组装成船舶的整体结构。
模块化建造可以大幅度提高建造效率和质量,同时也降低了工人的劳动强度和人力成本。
数字化设计现代造船模式还注重数字化设计。
传统的船舶设计是基于手绘图纸进行的,设计师需要消耗大量的时间和精力来制作详细的图纸。
而数字化设计采用计算机辅助设计软件,可以快速地完成船舶的设计工作。
数字化设计不仅能够大大缩短设计周期,还能够减少设计错误和整体成本,提高设计精度和效率。
先进材料应用现代造船模式还借鉴了先进材料的应用。
传统的船舶建造主要使用钢材,而现代造船模式中,逐渐加入了一些新型材料,如复合材料、高强度钢等。
这些先进材料具有重量轻、强度高、抗腐蚀性好等优点,能够提高船舶的载重能力和航行性能。
自动化装备现代造船模式强调自动化装备的应用。
传统的船舶制造过程中,大部分工作都需要人工完成,劳动强度大且效率低下。
现代造船模式中,通过引入自动化装备和机器人技术,能够实现船舶建造过程的自动化和智能化。
例如,使用机械臂进行焊接、激光切割技术进行切割等,都能提高工作效率和质量。
数据化管理现代造船模式强调数据化管理。
在船舶建造过程中,可以通过传感器和监控系统采集大量的数据,然后进行实时监测和分析。
这些数据包括船体结构、材料性能、工人操作等多个方面,能够帮助管理人员及时发现问题和隐患,并采取相应的措施,提高船舶建造的质量和安全性。
现代造船模式带来的优势船舶建造工艺现代造船模式的应用带来了许多优势:1.提高了船舶建造的效率和质量,缩短了建造周期。
模块化技术在船舶建造中的发展趋势及应用

183中国设备工程Engineer ing hina C P l ant中国设备工程 2018.08 (下)经过多年的发展,现代造船业逐渐将模块化造船技术作为目前造船技术发展的新方向,特别是国外的很多国家都已经应用了该项技术。
通过事实证明,模块化技术的使用能够进一步降低生产成本,提高生产效率,加快造船业的发展,因此,模块化技术将成为未来造船业发展的新方向。
在将来,模块化技术也将会得到更为广泛的应用。
1 模块化造船的含义和发展趋势1.1 模块化造船的含义模块化设计是将指定的模块在一定的条件下组装成符合要求的产品,这种设计方法主要是根据不同的任务和要求而进行组装和配制,它能够同时满足不同产品型号和品种的要求,模块化设计具有减少设计周期、提高设计水平、保持船舶系统的先进性、便于产品维修等多种优点。
目前,模块化的设计理念已经被广泛应用在造船业、汽车业等多种领域。
模块化造船是指在船舶建造中,将船舶建造任务进行详细的层层分解。
首先采用一些独立的单元件或标准件,把设备组装成标准化模块,然后通过对各个单元的组装而建造成有特殊功能的集成模块,并将这些具有不同功能的模块上船安装,最后再将这些组建好的模块组合起来,经过一系列的检查和验收后,再由各个模块组合成为一个整体,从而完成船舶建造的所有工作。
目前,由于模块化技术从产品的设计、研发、加工、建造、维修、改装等整个建造阶段,都具有能够提高建造周期、升级灵活、便于安装等功能,而被广泛应用于潜艇、护卫舰等船舶的建造上。
1.2 模块化造船技术的发展趋势随着全球经济的进步和科技的高速发展,造船业也在持续推进,很多先进的新兴技术都被广泛应用到船舶建造领域。
特别是伴随着信息技术、网络技术以及现代生产方式的发展和进步,现代造船业越来越向知识密集型、设备及信息密集型方向转变。
当前造船业最先进的技术主要有船体分道建造、模块化建造、智能控制系统等前沿技术,因此,模块化造船的发展与现代造船技术的发展有着紧密的关系。
采用“闭合模具”技术生产船壳和甲板

件 ,该公 司 开 发 了 新 的 系 列 工具 ,采 用 “ 闭合 模 具 ” 技术 ,生 产 合 成 材 料 的器 具 。有 了这 种创 新 的 技术 ,工 件 的 质量 和 表 面 的 光 洁度 可 以更 好 。 同 时 采 用真 空 注 射 和 灌 输 技 术 ,可 以保 证 树 脂在 各 个 腔 室 里 的 均 匀分 布 ,使
式 注 入 , 因 此 避 免 了 人 与
美 国 亚 特 兰 大 ,2 0 0 6年 船 舶 展 (o tS o 0 6 , 法 国 巴 黎 ,2 0 B a h w 2 0 ) 06 年 1月 1 1日 :P n i c t 司 第 o cnYahs公
一
能力 ,使 工 厂每 天 2 小 时 运 转 。圈 4
里 ,投 资 1 0 7 0万 欧 元 ,从 项 目启 动 以 来 招 收 了 1 0 7
多 人 , 建 立 了 以 前 只 有 汽
20 年 2 o6 4卷 第 6期 一
l 嗣 电舯 7 1
有 害 产 品 接 触 的机 会 。有
害 的有 机 合 成 物 质 ( o c y)
处 在 闭 合 的 环 境 当 中 , 并 在 后 期 经 过 处 理 , 因此 可 以把 有 害 气 体 的排 放 量 减
自己的 工 业 系统 当 中 ,从 而 确 立 了在
船 舶 制 造 业 还 从 未 见 到 过 的 生 产 模 式 。 研 究 工 作 是 由 “ 部 塑 料 工 业 东 区” (i d ls ri eL’ s 完 成 Pe ePat ged E t u )
工艺 。
生 产 和 检 查 模 式 ,可 以 降底 成 本 ,减 少产 品 的开 发 期 限 ,优 化 工 厂 的生 产
船舶闭合模式二级动力定位系统的研究和应用

1 引 言
动力定位系统 ,能在最大环境条件下 ,使船舶 的位置和
能力高 、安全更 可靠 的优点 ,将成为船东优先选择的方 向保持的动力定位系统 ,能在最大环境条件下 ,使船舶
案 。
的位置和航 向保持在限定范围 源自 DP2是指船舶装备一套集控手操和 自动航 向保持 的
2 动 力定位 系统定 义
动力定位系统 ,另外还有一套独立的集控手操和 自动航
动力定位系统的工作原理是 :应用计算机对采集来 的风 、浪 、流等环境参数 ,根据位置参 照系统提供 的位 置 自动地进行计算 ,控制各个 推力器 的推力大小 ,保持 船舶定位不漂移。
断开模式 动力定位系统 的发电机故 障不需要特别分
警或停车等 ),则要求DP控制系统发出减螺距信号给侧 析 ,但合排模 式的动力定位系统是重点分析对象之一 ,
推 ,待备用发 电机起动和并联 ̄I]MSB后才恢 复到正 常螺 调 速器 的命 令信 号 和反馈信 号输 出到主配 电板PMS系
距 ,这个降螺距 的信号 只有几十秒 ,而如果是断开模式 统 ,PMS系统对 电网无功和有功监测和控制 ,判断是否
GUANGDONG SHIPBUILDING 广 东 造船 2016年第 2期 (总第 147期 )
船舶 闭合模式二级动力定 位系统 的研究和应用
王小 林 ,李 美 玲2
(1.广新海事重工股份有限公司 , 111528437;2.广州顺海造船有限公司,广, }H51144O)
自锁式模块脚手架技术在船舶工业领域应用及发展前景

列产品的主要特点
1 .先 进 高 效
积 极参 与 了 国际 船 舶 市 场 的竞 争 ,几 十 年 以来 , 我 国船舶 业走 出 了一 条 自强振兴之 路 。 我 国造 船 工 业 紧 紧抓 住 国 际船 舶 景 气 周 期 . 实 现 了 又好 又快 发 展 。据 国外 相 关研 究 统 计 .
进 的 目锁式 模 块 式 脚 手 架技 术 在 得 到充 分 的 消化 吸 收和 结合 中国市 场 的特 点开 发 研制 的 A G系列 D 产 品正 好 顺 应 了船 舶 工业 市 场 发 展 的 需要 ,通 过 同造 船 行 业 内专 家 的 多 次接 触 和 交 流 ,充 分 利 用 外 国专 家 和 中 国行 业 内专 家 的强 大 技 术优 势 。立
A C 自锁式 模 块 脚 手 架技 术 主要 是通 过 预制 D 焊接 生 产 。在横 杆 上 的 C形卡 钩 、楔形 插 销 和 焊
接 在 立 杆 上 的 u形 卡在 重 力 的作 用 下 自动 翻转 且 立 即锁 死 .并 且 通过 斜 杆 上的 T形 锁 销 和 U形 卡
进 行 连 接 ,形 成 几何 不 变 的平 面稳 定 结 构 ,在通 过 对 平 面结 构 的重 复 组 合 .最终 形 成 稳 定 的 空 间 二 维 结构 。 由于 横 杆 上 自动 翻转 系统 的 设 置 。一 三
自锁 式 模 块 脚 手 架 技 术 在 船 舶 工 业 领 域
应 用 及 发 展 前 景
邓
毅
自锁 式模 块 脚 手 架 技 术 即通 过 突 破 传 统脚 手 架 的扣 件 螺栓 紧 固连 接 方式 ,利 用 预 先 铆 、焊 接
在 横 杆 和立 杆 上 以及 斜杆 上 的特 殊 装 置 ,利 用 重 力 楔 形 自锁 的原 理 .将 横 杆 和 立 杆及 斜 杆 连 接 起 来 ,形成 平 面i 角 稳 定结 构 .再将 平 面结 构 进 行 立 体组 合 ,最 终 形成 稳 定 的空 间 结 构 的技 术 该 技 术 的最 主 要 特 点是 其 灵 活 便 捷 的 高效 性 和 稳 定
scrimp成型工艺及其在船舶和基础工程领域的应用
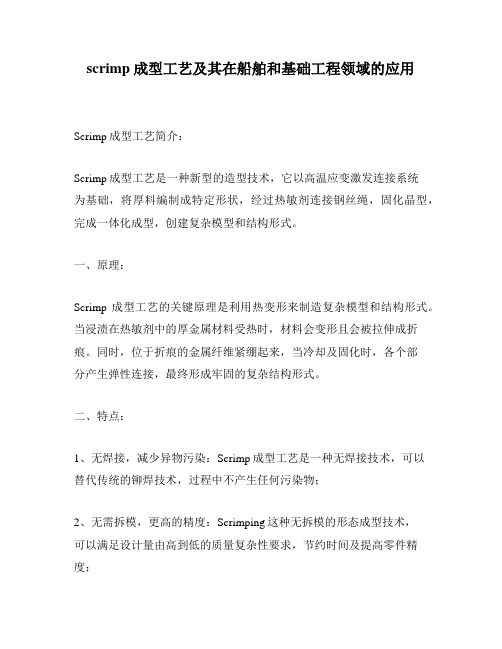
scrimp成型工艺及其在船舶和基础工程领域的应用Scrimp成型工艺简介:Scrimp成型工艺是一种新型的造型技术,它以高温应变激发连接系统为基础,将厚料编制成特定形状,经过热敏剂连接钢丝绳,固化晶型,完成一体化成型,创建复杂模型和结构形式。
一、原理:Scrimp成型工艺的关键原理是利用热变形来制造复杂模型和结构形式。
当浸渍在热敏剂中的厚金属材料受热时,材料会变形且会被拉伸成折痕。
同时,位于折痕的金属纤维紧绷起来,当冷却及固化时,各个部分产生弹性连接,最终形成牢固的复杂结构形式。
二、特点:1、无焊接,减少异物污染:Scrimp成型工艺是一种无焊接技术,可以替代传统的铆焊技术,过程中不产生任何污染物;2、无需拆模,更高的精度:Scrimping这种无拆模的形态成型技术,可以满足设计量由高到低的质量复杂性要求,节约时间及提高零件精度;3、可重复性:Scrimp成型工艺可提供可重复性,能够产生高度可重复性的成型件,从而确保零件的可靠性;4、灵活性:Scrimp成型工艺具备良好的灵活性,可以根据需求进行灵活调整,节约时间和成本;5、精确性:Scrimp成型工艺能够满足不同的设计规范,提高零件的精度,便于高效组装;6、易维护:Scrimp成型件的安全性更高,组装易维护,为客户提供更为可靠的产品和服务。
三、应用:1、船舶:Scrimp成型工艺的精致度高,可以用于制造船舶的复杂舱壁结构;2、基础工程:Scrimp成型工艺可以用于制造桥梁、隔离墙和护栏等基础工程;3、汽车工业:Scrimp成型工艺可以用于汽车钢构架、车身件及轻量化产品复杂模型的生产;4、工业管道:Scrimp成型工艺可用于制造不锈钢及铝合金水管、油管和放血管等;5、飞机材料:Scrimp成型工艺可用于制造飞机上的各种部件,满足性能要求,比如飞行控制、机外外形和机翼等。
四、总结:Scrimp成型工艺是一种使用热变形来制造复杂模型和结构形式的技术,具有无焊接、无拆模、可重复性、高精度及易维护等优点,可以广泛应用于船舶、基础工程、汽车工业、工业管道、飞机材料等行业。
密封件在船舶中的应用

密封件在船舶中的应用
密封件在船舶中有着广泛的应用,主要涉及以下几个方面:
1. 轴系密封:船舶的推进系统、辅助机械和舵机等设备都需要轴系进行传动。
在这些设备的轴系中,密封件被用来防止水、润滑油和气体等介质泄漏。
常见的轴系密封件包括油封、水封和机械密封等。
2. 舱室密封:舱室密封主要用于船体的水密和气密分隔。
这些密封件可以防止水进入船内的生活区和设备舱室,同时也可以保证船内的空气密闭,防止外部气体进入。
3. 管道密封:在船舶的管道系统中,密封件被用来连接各个部件并防止介质泄漏。
常见的管道密封件包括法兰、垫圈和接头等。
4. 动力系统密封:船舶的动力系统包括发动机、泵和压缩机等设备。
在这些设备中,密封件被用来防止润滑油、冷却水和其他液体的泄漏。
同时,也用于气体和蒸汽管道的密封。
5. 液压系统密封:液压系统在船舶中被广泛应用于舵机、起锚机和装卸货物的设备。
在这些液压系统中,密封件是关键的部件之一,可以保证油或其他液体的密封性。
6. 防腐和防污密封:船舶长期在海上航行,会受到海水的侵蚀和海洋生物的附着。
为了防止这些问题,船舶的底部和某些设备的外表面会涂上防污和防腐涂料。
这些涂料的涂抹需要使用到密封材料,以保证涂料的长期有效性。
总的来说,密封件在船舶中发挥着重要的作用,可以保证船舶的正常运行和延长使用寿命。
船舶建造模块化工艺流程优化
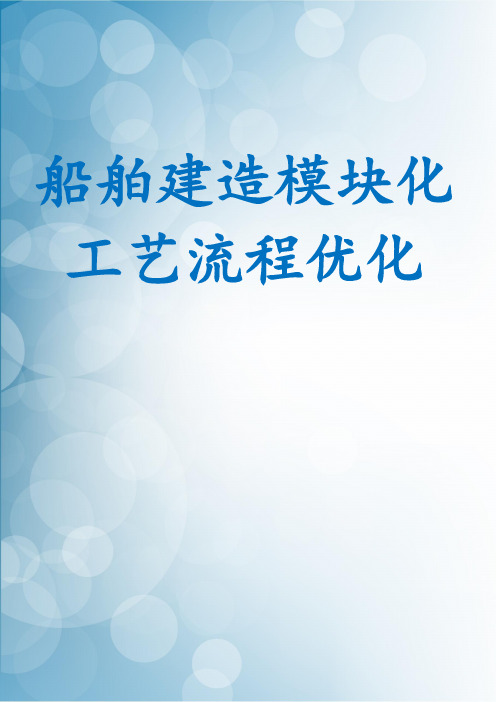
船舶建造模块化工艺流程优化一、船舶建造模块化工艺流程概述船舶建造作为一项复杂的工程活动,其工艺流程的优化对于提高建造效率、降低成本以及提升船舶性能具有重要意义。
模块化工艺流程,即通过将船舶建造过程分解为若干个相对的模块,每个模块在特定的制造区域进行生产,最后再将这些模块组装成完整的船舶。
这种工艺流程优化方法,不仅能够提高生产效率,还能够减少建造过程中的资源浪费,提高船舶建造的灵活性和可持续性。
1.1 模块化工艺流程的核心理念模块化工艺流程的核心理念在于将复杂的建造任务分解为简单的、可重复的模块化任务。
这种分解不仅有助于提高生产效率,还有助于提高建造质量,因为每个模块可以在专门的制造环境中进行生产,从而确保每个模块的建造质量。
1.2 模块化工艺流程的优势模块化工艺流程的优势主要体现在以下几个方面:- 提高生产效率:通过模块化生产,可以并行进行多个模块的建造,从而缩短整个船舶的建造周期。
- 降低建造成本:模块化生产可以减少建造过程中的资源浪费,如材料、能源和人力等。
- 提高建造质量:每个模块在特定的制造环境中进行生产,可以更好地控制建造质量。
- 增强灵活性:模块化工艺流程可以根据市场需求和设计变更灵活调整生产计划。
- 促进技术创新:模块化生产鼓励技术创新,因为每个模块都可以采用最新的技术和材料。
二、船舶建造模块化工艺流程的关键技术船舶建造模块化工艺流程的实施需要依赖于一系列关键技术,这些技术包括但不限于设计优化、制造技术、物流管理、质量控制和信息技术等。
2.1 设计优化技术设计优化是模块化工艺流程的基础,它涉及到船舶的整体设计和模块划分。
设计优化的目标是确保每个模块的设计既满足功能要求,又便于制造和组装。
这通常需要采用先进的设计软件和方法,如计算机辅助设计(CAD)、计算机辅助工程(CAE)和模块化设计原则。
2.2 制造技术制造技术是实现模块化工艺流程的关键,它包括材料加工、部件制造和模块组装等。
制造技术需要不断更新和改进,以适应模块化生产的需求。
江南驶来数字船——老牌军工企业基于模型的数字造船体系构建与实施

管理创新丨M a n a g e m e n t I n n o v a t i o n江南驶来数字船—-老牌军工企业基于模型的数字造船 体系构建与实施文/江南造船(集团)有限责任公司■关键词:数字造船江南造船体验式设计智能制造以大型舰船为代表的巨系统工程,其零件数量达千万级,传统研制模式无法满足高质量研制需要,必须以大体系思维,依靠信息技术和数字技术创新驱动,构建先进平台和基于模型的数字造船体系。
围 绕中船集团战略部署.江南造船(集 团)有限责任公司(简称江南造船)突破了传统以二维图纸为中心的研制模式,开创了船舶行业以三维模型为核心的研制方法,创新了一种“体验式”数字造船新模式,提升了 船舶精准设计、精确建造和精细化管理水平,形成了一整套涵盖各专业的船舶数字化研制流程和体系。
深化总体思路,建立体系框架江南造船首先制定了“战略引 领,立足全局;一把手工程,型号 引领;系统谋划,分步实施;解放思想,创新突破”的推进方针,形成了“三轴四面”总体推进思路;基于单一数字模型核心思想,对数字造船总体框架进行了设计,从顶层指导基于模型的数字造船体系构建与实施。
以船舶业务流程(合同设计、基本设计、详细设计、生产设计、工艺设计、建造、工程管理)为主线,对船舶总体、跨专业以及船体、管系/风管、电气、外舾装、内装的各专业,全面运用基于单一数字模型、系统工程、轻量化设计、体验式设计、智能设计等新的理念方法,结合船舶行业业务实际进行流程再造,以工程应用为导向持续推进优化,如图I所示。
在船舶领域,由于行业特性和历史传承,设计与制造相对分离。
总体所进行总体设计时,一般较少从建造角度考虑如何合理、髙效;到了总装厂,需要再进行生产设计,重新进行三维建模。
通过基于模型的数字造船体系构建,将工艺信息、几何信息、管理信息全部加载到模型上去,让模型更为“丰满”。
以前在设计阶段,要对舱室的空间可达性、可操作性、可维修性,以及声场、气流场、光场、温度场等舒适性指标进行逐一分析,每项分析都要单独再建模型,耗费大量精力。
模具在船舶制造业的应用

模具在船舶制造业的应用摘要船舶制造是一项复杂而精密的工艺,其中模具在加工过程中扮演着关键的角色。
本文将探讨模具在船舶制造业中的应用,包括模具的种类、制作方法以及优势和挑战。
通过深入了解模具的应用,可以更好地理解船舶制造领域的制造流程和技术创新。
1. 引言船舶制造业是一项重要的工业领域,对于国家的经济发展和海上交通起着关键作用。
在船舶制造过程中,模具起到了至关重要的作用,它们不仅能够提高生产效率,还可以保证产品质量和一致性。
本文将从模具的概念、种类、制作方法以及在船舶制造业中的应用等方面进行探讨。
2. 模具的概念和种类模具是用于制造物体的工具或设备,通过模具可以使产品在制造过程中形成固定的几何形状。
在船舶制造业中,常用的模具有以下几种:•焊接模具:用于焊接船体结构的模具,在船舶制造的各个阶段都会用到焊接模具,具有高度的适应性和可塑性,能够满足各种船型和结构的要求。
•压力模具:用于对金属板材进行压力成形的模具,通过压力的加入可以使金属板材变形成所需的形状,常用于船体板材的成形和冷弯加工。
•注塑模具:用于塑料成型的模具,在船舶制造业中,注塑模具主要用于制作内部管道和管件等零件,具有成本低、生产效率高的优势。
•精密模具:用于制造高精度零部件的模具,常用于船舶的导航仪器、电子设备等关键零部件的制作。
3. 模具的制作方法模具的制作方法多种多样,常用的制作方法有以下几种:•开模:通过模具切割成型材料,常用于金属板材的制作,可以根据设计要求进行切割、冲孔和折弯等操作,用于制作各种套筒、支架和连接件等。
•铣削:通过铣床将材料加工成所需形状的模块,精度高、加工效率高,常用于制作精密模具和复杂零部件。
•焊接:通过焊接多个零件组合成所需形状,常用于制作大型焊接模具和船体结构的组装。
•注塑:通过注塑机将熔化的塑料注入模具中,在特定的压力和温度条件下冷却成型,常用于制作塑料模具和零部件。
4. 模具的优势和挑战在船舶制造业中,模具的应用带来了许多优势,但也面临一些挑战。
消失模铸造工艺

消失模铸造工艺消失模铸造工艺是一种非常有效的金属铸造技术。
它结合了传统的消失模铸造工艺和高科技的装备来提高铸件的质量,降低制造成本。
消失模铸造工艺是在固定模具内倒入合金铸造件,在铸造过程中消失模具会因为热量膨胀而逐渐破碎。
它的优点是不需要像传统的铸造工艺那样把模具分解,可以提高铸件的精度。
消失模铸造工艺的基本原理是在固定模具上倒入铸件,当铸件在高温环境下熔化时,模具会随着铸件的膨胀而被破坏。
模具的材料可以根据铸件的要求选择,有时会选择比较软的材料,如木头、橡胶或织物,这样模具就可以被更快地破坏。
消失模铸造工艺主要用于铸造大型、大型、复杂形状的件,如汽车发动机曲轴和活塞、汽车框架等。
这种技术可以使铸件达到较高的精度,它还可以提高生产效率,减少冗余劳动。
消失模铸造工艺在汽车、船舶、飞机、机械设备、家用电器等制造行业中都得到了广泛应用。
消失模铸造工艺的过程主要包括模具设计、模具材料选择、模具加工、铸件倒入、熔化等几个过程。
首先是完成模具的设计,然后选择合适的模具材料,模具材料必须具有足够的抗拉强度,能抵抗高温压力,以及抵抗铸件的熔化。
接下来就是模具的加工,完成模具的结构,然后进行安装,安装完成后就可以进行铸件的铸造,倒入熔融金属,熔融的金属在模具内会迅速膨胀,从而破坏模具,当金属冷却完全时,模具就会完全消失,产出符合要求的铸件。
消失模铸造工艺有很多优点,如铸件精度高、成本低、生产效率高等。
但是,由于消失模铸造工艺模具设计和加工非常复杂,因此制作模具需要有专业的技术人员进行设计,并且模具材料必须具有足够的抗拉强度,这就要求模具的制作和维护要精确精致,容易受到外界的影响,所以这种技术也会遇到一些困难。
总之,消失模铸造工艺是一种高精度、高效率、低成本的金属铸造技术,已经广泛应用于汽车、船舶、机械设备制造行业。
然而,由于消失模铸造工艺模具设计和加工相对复杂,并且模具材料也要求高,因此也会带来一些挑战。
未来,在技术不断发展的同时,消失模铸造工艺必将取得更好的发展,它必将给汽车、船舶、机械设备制造行业带来更大的效益。
代理模型技术及其在船舶板架强度和稳定性计算中的应用

代理模型技术及其在船舶板架强度和稳定性计算中的应用代理模型技术是一种基于物理模型的数值计算方法,通过将复杂的物理现象简化成一个简单结构的模型来进行计算。
在船舶板架强度和稳定性计算中,代理模型技术可以有效地降低计算成本和提高计算效率。
本文将介绍代理模型技术的原理和应用,并探讨其在船舶板架强度和稳定性计算中的具体应用。
代理模型技术的原理是通过建立一个简化的模型来代替复杂的物理系统,通过与原系统的关系函数来模拟系统的行为。
代理模型可以是一个简单的数学模型、一个统计模型或者一个机器学习模型。
通过代理模型技术,可以降低计算成本,提高计算效率,并且更容易处理原系统中的不确定性和复杂性。
在船舶板架强度和稳定性计算中,代理模型技术可以用来简化复杂的结构力学问题。
例如,可以利用代理模型来模拟船舶结构在不同载荷条件下的变形情况,并进一步计算板架的强度和稳定性。
代理模型还可以用来优化船舶设计,在设计过程中提供关键参数和指导,帮助设计人员快速做出决策。
在实际应用中,代理模型技术可以与传统的有限元方法相结合,形成一种混合模拟技术。
通过在有限元模型中嵌入代理模型,可以在不损失精度的前提下显著减少计算时间和资源,提高计算效率。
此外,代理模型还可以通过参数优化等方法来优化设计结果,提高船舶结构的强度和稳定性。
总的来说,代理模型技术在船舶板架强度和稳定性计算中具有重要的应用前景。
通过采用代理模型技术,可以降低计算成本、提高计算效率,并且更容易处理原系统中的不确定性和复杂性。
代理模型技术可以与传统的有限元方法相结合,形成一种混合模拟技术,为船舶设计和分析提供更强大的工具和方法。
未来,代理模型技术将在船舶结构设计与分析领域发挥更重要的作用。
- 1、下载文档前请自行甄别文档内容的完整性,平台不提供额外的编辑、内容补充、找答案等附加服务。
- 2、"仅部分预览"的文档,不可在线预览部分如存在完整性等问题,可反馈申请退款(可完整预览的文档不适用该条件!)。
- 3、如文档侵犯您的权益,请联系客服反馈,我们会尽快为您处理(人工客服工作时间:9:00-18:30)。
•注意搭接和对接。纤维的搭接一般铺层设计里面都有规定搭接宽度,而 且是尽量错开搭接位置。芯材的对接一般要尽量减少缝隙,泡沫和轻木可 以用塑料钉枪,强芯毡一类可以缝制。
解读
材料铺放有什么讲究?
•管路铺设多种多样,不应拘泥于单一方式。从形式上来说,可以 按照图片中的鱼骨形状(发散型)或者多段平行的导流管路,以 及相互结合(甲板多)。主要按照产品的形状和铺层变化。
船侧折角位置架桥
干 区
平行排布,一般会有开 闭顺序,接力棒的形式
鱼骨形,一般导入效率较高, 开闭操作少,干区风险稍大
•比较厚的铺层,在真空导入工艺中,往往存在上下表面的浸润差 距。通过在玻璃平板上的充分试验,可以调整辅助材料铺放和工 艺操作,避免做船出现表面树脂浸透,但是底部铺层出现局部干 区的问题。
•制品样板可以测试力学性能,验证铺层设计
•舱板可以跟试验相结合
完成铺层材料及辅助材料铺放
解读
材料铺放有什么讲究?
闭模工艺相比传统手糊,可使船体铺层结构更致密。在等强度设计中, 发挥巨大优势,减轻产品重量。 更强、更轻、更快、更小驱动力(发动力马力)、更省油、
3. 改变劳动密集型现状
管理者们一直在苦恼的事情
可以依葫芦画瓢
二、案例解读如何真空导入造船?
1. 真空导入工艺做游艇
案例:24米比赛级帆船(环氧碳纤维铺层,局部有泡沫三明治结构) 地点:斯洛维尼亚
酸酐类固化剂易引起皮炎,而经口毒性比较小。胺类固化剂毒性是比较强的, 芳香胺毒性比脂肪胺大。对皮肤和黏膜有刺激性,可引起过敏。不容易通过 肝脏代谢。以间苯二甲胺为例,大鼠经口LD50: 930mg/kg
Why?
2. 提高产品质量性能
手糊做船容易出现的缺陷: 1. 树脂二次积层时的界面粘接不够牢固,会影响耐疲劳性 2. 积层中容易存在气泡和架桥,防水性差 3. 局部富树脂,偏重 4. 不同批次产品不稳定
•如果做了手糊过渡层,最好是搭建施工梯架,防止预脱模
•当铺层结构缺少导流介质,树脂流速较慢,往往采用比较密集一些的管 路铺设,和大面积的导流网,这样会需要比较多的树脂。如果是铺层中有 芯材提供导流效果,导流网和导流管可以极大简化。
•真空袋膜的拼接与打折。真空袋膜如果没有足够的长宽,或者局部打折 不充分,都可能导致抽真空时被过度拉伸,易发生破裂。
Personal Resin Injector (RTM) 10
2
G.25 2.36 20.02
37.91 2.65
需要减少接触的物质
环氧稀释剂
活性稀释剂缩水甘油醚类化合物的毒性,主要表现在对皮肤的刺激上,容易 产生过敏。以正丁基缩水甘油醚(501)为例,口服-大鼠 LD50: 2050 mg/kg; 环氧固化剂
Sample Job Group Type
Building n
Area Gelcoat Booth
2
3
Area Lamination Area
3
12
Area RTM Area
10
3
Personal Gun operator (small
2
2
parts)
Personal Roller (Deck)
3
14
分段三、模具。越大的产品需要保压的时间越长
分段四、模具注射口 → 树脂桶
解读
什么时候结束导入?
停止导树脂: 树脂差不多要全部浸透时,剩余部分可在树脂凝胶时间内浸满的 情况下,一般可以提供停止导树脂,来减少树脂的浪费并控制产 品重量。但实际往往因为局部的干区,无法提前停掉树脂,要一 直抽到结束。
•相比手糊,真空导入做船要注意的模具因素?
•(合模)密封性。船底往往会采用对开模,双体船还会用三片模。 翻边防止变形,做好密封条。
•耐热冲击性。真空导入集中放热,还有真空压力,容易在模具表 面形成布纹和芯材印记。
做船前样板测试
舱板做真空导入
解读
做船前平板试验的重要性
•不同的铺层以及不同的树脂以及施工温度都会对流速产生影响, 收集不同条件下的真空导入工艺树脂流速资料,可以对导流管路 设计起到很大的参考作用。
国内排放标准: GB14554-93
控制 项目
单位
一级
苯乙烯 Mg/m3 3.0
二级
新扩改建 现有
5.0
7.0
三级
新扩改建 现有
14
19
苯乙烯 styrene
美国海军2006年7月在华盛顿一游艇厂检测数据 检测设备:
Pac III Drager 便携式气体监视器 XS EC 有机蒸汽感应器(专门测苯乙烯)
搭建简易模,并完成表面的积 层处理,使之达到真空导入工 艺要求
解读
为什么用简易模做真空导入?
•这么大的比赛用船型,一般订单比较少,开复合材料阴模成本非 常高,周期非常长。用简易模具是比较经济、高效的办法。
•产品表面是做后喷漆处理,对于模具表面的平整和光亮度不是非 常严格。阴模处理过程中不好找平找顺的缺点,不会有太大影响。
一、 为什么采用闭模工艺造船?
1. 减少有害化学物质接触,改善工作环境
主要VOC (挥发性有机化合物): 苯乙烯
LD50:5000 mg/kg(大鼠经口);LC50:34.5 g/m3,2 h(小鼠吸入) LC50:26.0 g/m3,4 h(大鼠吸入) 刺激呼吸道,影响皮肤、神经、肝肺等
美国职业安全健康研究所制定的允许暴露限制NIOSH REL:50 mg/m3 (每天最多暴露10小时,每周最多暴露40小时)
闭模工艺在船舶行业中的应用
内容概要
复合材料船舶的传统制造工艺主要采用手糊、喷射成型,都 属于敞模工艺
本次交流谈及的闭模工艺造船是:
真空导入 湿法真空袋压
RTM
LRTM
内容概要
WHY? HOW? WHAT?
一、 为什么采用闭模工艺造船?
二、案例解读如何真空导入造船? 三、闭模工艺造船其他应用简介
四、常见问题探讨FAQ 五、闭模造船发展畅想
①② ③④
树脂浸透区域
船底真空导入
解读
什么情况下可以开始导入树脂? 前提:1. 树脂原料是否计算好,准备充分?
2. 凝胶时间在可控范围之内,太短太长都不行(考虑堆积 放热、环境温度因素)
分段检查密封性,做保压测试,使用真空检漏仪查漏气点 分段一、真空泵 → 树脂收集器
分段二、树脂收集器 → 模具抽气口