注塑机的保压
第24问:注塑成型中的压力参数

第24问:注塑成型中的压力参数有哪些?一、注射压力:1.注射压力定义:是指螺杆(或柱塞)向前移动时,其头部对塑料熔体施加的压力,单位为兆帕(MPa)。
单位换算:1MPa(兆帕)=10.2kgf/cm2(千克力/平方厘米)= 1N/mm2(牛/平方毫米)=10bar(巴)=143.5psi(磅/寸2)2.注射压力对注射成型有何影响:在注射成型中,注射压力主要用来克服熔体在整个注射成型系统中的流动阻力,同时还对熔体起一定的压实作用。
为使熔体在注射成型中有较好的流动性能和充模性能,并保证产品成型质量,必须要选择适中的注射压力。
注射压力于注射速度有部分共同之影响,都是决定在模具内熔体如何能均匀的,彻底地适量地流满各角落。
注射压力太低,产生短射、缺胶、缩水、熔接线明显及强度下降、尺寸小、重量轻、气泡、浮纤、模芯粘模、纹面光亮、生产周期不稳定等不良;注射压力过大,出现涨模、溢料、黏模、内应力残留、变形、破裂、易损坏模具与机台等不良现象,且会引起较大的压力波动、使机器出现过载现象。
3.一般注射压力的控制原则是什么?当塑料流动性差、浇口小、熔体温度较低时,适当选取较大的注射压力。
对于玻璃化温度和熔体粘度较高的塑料,宜用较大的注射压力。
二、何谓射嘴压力?射嘴压力是射嘴腔内的压力。
它大约就是引起塑料熔体流动的压力。
它没有固定的数值,而是随模具填充的难度加大而增高。
射嘴压力、线压力和注射压力之间有直接的关系。
在螺旋式注塑机上,射嘴压力大约比注射压力少大约百分之十左右。
而在活塞式注塑机时压力损失可达到百分之五十。
三、什么是系统压力?与注塑压力有什么区别?油压机的系统压力(bar或kgf/cm2)是注射机台螺杆后端活塞缸中油压的工作压力,此压力作用于螺杆的端面。
一般液压注塑机的系统压力最高设定值为160bar(巴),对应最高注射压力值可从机台的参数表上查到;系统压力只针对油压机而言。
系统压力与注射压力的放大倍数(the intensification ratio,简称R i)的计算:●最大注射压力/机台系统液压:如最高注射压力为2200 kgf/cm2,对应最高系统压力为160bar,则R i其放大系数为:2200÷1.02÷160=13.48。
保压

保压起什么作用保压也就是所谓的二次压.当注塑的时候,注塑的压力是程曲线变化的,而保压则是恒定或有一定斜度的.首先你要搞明白,保压的情况下注塑机也在射胶.当一次压完成后,由于塑胶温度的降低及其内部的内应力,模腔里面的塑胶会发生回流现象.如果没有保压来消除这些力,则产品就会产生缩水甚至不饱模.这是保压的其中一个作用.另外保压可以控制产品的变形量及尺寸的大小.保压太大或太小都不适合.保压太大,产品会出现尺寸大,翘曲甚至粘模.太小的话最直观的就是会产生缩水.至于保压时间,要看产品的肉厚及大小做相应调节.这些需要你自己去实践中摸索.有一点记住.一次压过后熔融的塑胶会在短时间内成型,而保压就在这时间内完成的.具体敲自己摸索摸索关模的低压保护怎么设置低压保护又叫金型保护.不管曲轴还是直压,都应该有.曲轴的低压保护设置相对复杂一些.要先调模厚,然后根据你的模具低压需要的灵敏度来相应的调节位置,压力及时间.我们这边一般低压保护压力设定在3以内,时间1S以内,相对位置就大了点.注塑原理一、何为注塑:所谓注塑就是塑胶材料在注塑机的料筒中经过外部的加热和螺杆的旋转而产生的剪切热对树脂材料进行塑化成熔体后,通过施加一定的压力,把熔体注射到具有一定的形状的型腔中经过冷却定型后所产生的物品就为注塑。
二、注塑的过程,也就是注塑的周期:三、注塑的三大基本要素:机器—包括注塑机、辅机。
模具、材料四、注塑工艺的五大要素:1、温度:A、油温:对于液压机而言是由于机器的不停运作液压油运动摩擦而产生的热能,它是由冷却水来控制,在开机时要确认油温在45℃左右,若油温过高或过低均会影响压力的传递。
B、料温:即炮筒温度,此温度要根据材料和产品的形状和功能去设定,若有文件则根据文件去设定它。
C、模温:此温度也是一个重要的参数,它的高低对于产品的性能影响很大,故设定时一定要考虑产品的功能和结构,同时还要考虑到材料和周期。
2、速度:A、开合模的速度设定,开合模的设定一般是按慢—快—慢的原理,这样设定主要考虑机器、模具、周期去考虑。
注塑机的工作原理

注塑机的工作原理注塑机是一种常见的塑料加工设备,它通过将塑料颗粒加热熔化后,通过一定的压力将熔融塑料注入模具中,冷却固化后得到所需的塑料制品。
下面将详细介绍注塑机的工作原理。
注塑机的工作原理可以分为六个步骤:闭模、进料、射料、保压、冷却和开模。
1. 闭模:首先,注塑机的模具会处于开放状态,当开始工作时,模具会闭合。
闭合后,模具的两个半部分形成一个封闭的腔室,用于注入熔融塑料。
2. 进料:在模具闭合后,注塑机会启动进料系统。
塑料颗粒通过进料斗进入注塑机的加料筒中。
进料筒内部有一个螺杆,当螺杆旋转时,塑料颗粒会被推进到筒内。
3. 射料:当进料筒中的塑料颗粒被推进到一定位置时,注塑机会启动射料系统。
射料系统会将螺杆向前推进,将熔融塑料注入模具的腔室中。
注塑机会根据预设的注射时间和速度来控制射料过程。
4. 保压:一旦注塑机完成射料,它会进入保压阶段。
在保压阶段,注塑机会保持一定的压力,使熔融塑料充分填充模具的腔室,并确保塑料制品的尺寸和形状准确无误。
保压时间和压力会根据不同的塑料材料和制品要求进行调整。
5. 冷却:当保压时间到达设定值后,注塑机会进入冷却阶段。
在冷却阶段,注塑机会停止加热,同时通过冷却系统对模具进行冷却,使熔融塑料迅速固化。
冷却时间会根据不同的塑料材料和制品要求进行调整。
6. 开模:当冷却时间到达设定值后,注塑机会启动开模系统。
开模系统会打开模具,将成型的塑料制品从模具中取出。
注塑机的开模速度和力度需要根据具体的制品要求进行调整。
总结起来,注塑机的工作原理是通过闭模、进料、射料、保压、冷却和开模等步骤来完成塑料制品的注塑成型过程。
这一过程需要精确控制各个参数,如温度、压力和时间等,以确保制品的质量和尺寸符合要求。
注塑机在塑料加工行业中具有广泛的应用,可用于生产各种塑料制品,如塑料容器、零件和玩具等。
注塑压力、保压压力和背压对注塑成型的影响

注塑压力、保压压力和背压对注塑成型的影响
在注塑成型的过程中我们经常会遇到三个压力参数,这几个参数分别是注塑压力、保压压力和背压,这些压力参数设置对注塑成型及制品有什么影响呢?下面由小编为大家介绍一下。
1.注塑压力
注塑压力是指注塑时作用于螺杆头部的熔体压强。
用于克服塑料流经喷嘴、流道、浇口及模腔内的流动阻力,并使型腔压实。
注塑压力的大小与塑料的品种、塑料件的复杂程度、塑料件的壁厚、喷嘴的结构形式、模具浇口的尺寸及注塑件的类型等许多因素有关,通常取
40-200MPa。
2.保压压力
保压压力是指注塑后螺杆并不立即后退,仍继续对前端熔体施加压力。
在保压阶段,模腔能的塑料因为冷却收缩而体积变小,这时若浇口未冻结,螺杆在保压压力的作用下缓慢前进,使塑料继续注射入型腔进行补缩。
一般保压压力≤注射压力。
3.背压
背压又称为塑化压力,是指注塑机螺杆顶部的熔体在螺杆转动后退时所受到的压力。
背压是通过调节注塑液压缸的回油阻力控制的。
背压是注塑成型工艺中很重要的参数,直接影响熔体的充模和塑件的质量。
在下一节内容中,小编会为大家详细地介绍背压的影响,敬请关注。
注塑机低压保护原理
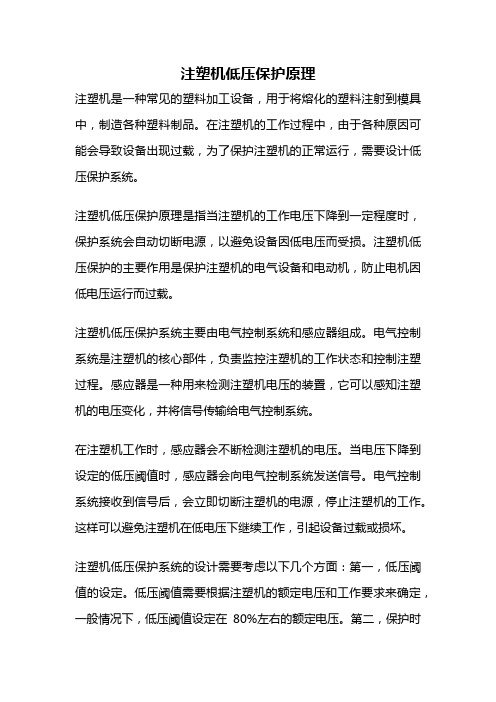
注塑机低压保护原理注塑机是一种常见的塑料加工设备,用于将熔化的塑料注射到模具中,制造各种塑料制品。
在注塑机的工作过程中,由于各种原因可能会导致设备出现过载,为了保护注塑机的正常运行,需要设计低压保护系统。
注塑机低压保护原理是指当注塑机的工作电压下降到一定程度时,保护系统会自动切断电源,以避免设备因低电压而受损。
注塑机低压保护的主要作用是保护注塑机的电气设备和电动机,防止电机因低电压运行而过载。
注塑机低压保护系统主要由电气控制系统和感应器组成。
电气控制系统是注塑机的核心部件,负责监控注塑机的工作状态和控制注塑过程。
感应器是一种用来检测注塑机电压的装置,它可以感知注塑机的电压变化,并将信号传输给电气控制系统。
在注塑机工作时,感应器会不断检测注塑机的电压。
当电压下降到设定的低压阈值时,感应器会向电气控制系统发送信号。
电气控制系统接收到信号后,会立即切断注塑机的电源,停止注塑机的工作。
这样可以避免注塑机在低电压下继续工作,引起设备过载或损坏。
注塑机低压保护系统的设计需要考虑以下几个方面:第一,低压阈值的设定。
低压阈值需要根据注塑机的额定电压和工作要求来确定,一般情况下,低压阈值设定在80%左右的额定电压。
第二,保护时间的设定。
保护时间是指注塑机在低压状态下能够继续工作的时间,一般设定为几秒钟到几分钟不等。
第三,报警系统的设计。
当注塑机发生低压保护时,需要及时向操作人员发出报警信号,以便及时处理故障。
注塑机低压保护系统的实现需要依靠先进的电气控制技术。
现代注塑机通常采用PLC(可编程逻辑控制器)作为控制核心,通过编程实现低压保护功能。
PLC具有灵活、可靠的特点,可以根据不同的工艺要求进行编程,实现注塑机的自动控制和保护。
注塑机低压保护原理是为了防止注塑机在低电压下继续工作而导致设备受损。
通过感应器的检测和电气控制系统的控制,可以及时切断注塑机的电源,保护设备的正常运行。
注塑机低压保护系统的设计需要考虑多个因素,包括低压阈值、保护时间和报警系统等。
怎样设置注塑保压

怎样设置注塑保压常常将注塑分为两个阶段:在第一阶段,大部分塑料充入模具中,一般为整个制品体积的0%~99.9%;在第二阶段,压实制品,得到与模具结构和外形相同的制品。
在第二阶段,虽然只有相对较少的塑料熔体充入型腔,然而对制品表面的光洁度,美学外观以及制品尺寸来说非常重要。
在大多数情况下,注塑成型的第二阶段使用压力和时间两个参数。
从科学成型的研究角度,我们将两个因素增加到四个要素:(1)第一阶段向第二阶段转换的方法;(2)保持浇口密封(冻结)或浇口不密封状态下,加工制品;(3)保压时间;(4)保持型腔内的合理压力。
1、转换或许可以这样说,第一阶段向第二阶段转换的控制是成型过程最关键的部分。
能否加工出高质量的制品往往取决于此,而且也常常是塑料加工厂不能从一台设备到另一台设备生产出相同制品的原因。
在大多数应用领域,应尽可能让转换过程短,即不论第一阶段最后是什么压力,都希望能够快速变化到第二阶段压实和保压所需要的压力。
另外,你必须了解设备控制单元是如何正确完成这一转换过程。
遗憾的是在不同设备之间如何判断完成转换还没有统一标准,因此注塑企业需面临四种可能:①加工设备配置控制粘度的转换功能;②设备控制单元具有一个转换用粘度设定值,但它只能让转换时压料杆的速度变慢,却不能控制;③设备没有用于转换的粘度设定值;④第一阶段向第二阶段转换时,设备不能正常运转,出现渐变的粘度倾斜,下降或波摆动。
必须要保证第一阶段向第二阶段转换时迅速而一致。
因此了解注塑机的工作原理对获得所需要的结果非常关键。
对大多数制品,正确的工艺控制来说,第一阶段结束到第二阶段压力设定点的时间应小于0.1秒。
不希望向第二阶段压力转变时出现任何下沉,细而尖的峰,摆动或缓缓滑进第二阶段的压力现象。
下沉会引起流体前锋变得迟疑,造成欠保压或缺料。
细峰或缓慢转变到第二阶段的压力将过度填充型腔,造成飞边。
摆动常造成加工稳定性差。
注塑压力的压力监控器图形与时间的对应关系可作为评估设备响应最好的方式。
各规格注塑机技术参数

各规格注塑机技术参数注塑机是一种用于制造塑料制品的机械设备,主要通过将熔融塑料注入模具中,然后冷却硬化成型,最后取出成品。
不同型号和规格的注塑机具有不同的技术参数,下面将介绍一些常见的注塑机技术参数。
第一个重要的参数是注射容量(注射量),它表示每次注射到模具中的塑料量,单位通常是克(g)或立方厘米(cm³)。
注射容量是根据注射缸和螺杆的直径和行程来计算的,决定了每个周期注塑的质量。
然后是射出压力,它表示材料被注入模具时所需的压力。
通常用千帕(KPa)或兆帕(MPa)来表示。
射出压力取决于注射容量和注射速度,因此注射容量和射出压力之间有一定的关联。
接下来是射出速度,它表示注射材料进入模具的速度。
射出速度是由液压系统控制的,通常用毫米/秒(mm/s)来表示。
射出速度是根据注射时间和注塑机的射出行程来计算的。
注塑机的闭模力也是一个重要的技术参数。
闭模力表示模具在注射材料时需要施加的力量,单位通常是吨(T)。
闭模力的大小取决于模具大小和复杂性,以及注射材料的特性。
另一个重要的参数是射出时间,它表示注射材料进入模具所需的时间。
射出时间是根据射出速度和注射容量来计算的,通常用秒(s)来表示。
接下来是保压时间,它表示注塑材料在模具中保持压力的时间。
保压时间取决于材料的特性和模具的要求,通常用秒(s)来表示。
注塑机的开模力也是一个重要的技术参数。
开模力表示打开模具时所需的力量,单位通常是吨(T)。
开模力的大小取决于模具大小和复杂性。
最后一个重要的参数是机器尺寸,包括注塑机的长度、宽度、高度和重量。
机器尺寸是根据每个型号的注塑机的设计和要求来确定的。
总之,注塑机的技术参数包括注射容量、射出压力、射出速度、闭模力、射出时间、保压时间、开模力和机器尺寸等。
不同的注塑机具有不同的技术参数,根据实际生产需求选择适合的注塑机是非常重要的。
注塑机的保压有什么用

注塑成型各种缺陷的现象及解决方法(一)熔接痕熔接痕是由于来自不同方向的熔融树脂前端部分被冷却、在结合处未能完全融合而产生的。
一般情况下,主要影响外观,对涂装、电镀产生影响。
严重时,对制品强度产生影响(特别是在纤维增强树脂时,尤为严重)。
可参考以下几项予以改善:l)调整成型条件,提高流动性。
如,提高树脂温度、提高模具温度、提高注射压力及速度等。
2)增设排气槽,在熔接痕的产生处设置推出杆也有利于排气。
3)尽量减少脱模剂的使用。
4)设置工艺溢料并作为熔接痕的产生处,成型后再予以切断去除。
5)若仅影响外观,则可改变烧四位置,以改变熔接痕的位置。
或者将熔接痕产生的部位处理为暗光泽面等,予以修饰。
(二)放射纹放射纹(Jetting)1、表观从浇口喷射出,有灰黯色的一股熔流在稍微接触模壁后马上被随后注入的熔料包住。
此缺陷可能部分或完全隐藏在制品内部。
物理原因放射纹往往发生在当熔料进入到模腔内,流体前端停止发展的方向。
它经常发生在大模腔的模具内,熔流没有直接接触到模壁或没有遇到障碍。
通过浇口后,有些热的熔料接触到相对较冷的模腔表面后冷却,在充模过程中不能同随后的熔料紧密结合在一起。
除去明显的表面缺陷,放射纹伴随不均匀性,熔料产生冻结拉伸,残余应力和冷应变而产生,这些因素都影响产品质量。
在多数情况下不太可能只通过调节成型参数改进,只有改进浇口位置和几何形状尺寸才可以避免。
与加工参数有关的原因与改良措施见下表:1、注射速度太快降低注射速度2、注射速度单级采用多级注射速度:慢-快3、熔料温度太低提高料筒温度(对热敏性材料只在计量区)。
增加低螺杆背压与设计有关的原因与改良措施见下表:1、浇口和模壁之间过渡不好提供圆弧过渡2、浇口太小增加浇口3、浇口位于截面厚度的中心浇口重定位,采用障碍注射(三)灰黑斑纹(Grey or black clouding)1、表观灰黑斑纹可能发生在浇口附近,流道的中间和远离浇口的部分。
只能在透明的零件中可看出,并且往往用PMMA,PC 和PS 料制成的产品有此现象。
[精彩]注塑机保压压力操纵
![[精彩]注塑机保压压力操纵](https://img.taocdn.com/s3/m/9b98a4e8900ef12d2af90242a8956bec0975a560.png)
基于C MA C 和P I D 复合控制器的精密注塑机保压压力控制蔡 侃 应 济 陈子辰 王 硕浙江大学,杭州,310027摘要:针对传统P I D 算法对注塑成形过程中保压压力进行控制时存在压力超调㊁静差和时延等问题,建立了注塑过程保压压力的系统数学模型,针对系统特性设计了新型C MA C 和P I D 复合控制器㊂实验结果表明,相对于传统P I D 控制,C MA C 和P I D 复合控制对保压压力的超调㊁静差和时延有显著的改善,制品质量和重复精度得到明显提高㊂关键词:注塑过程;保压压力;神经网络;神经网络;C MA C 和P I D 复合控制中图分类号:T P 273 文章编号:1004 132X (2011)24 2986 04P a c k i n g P r e s s u r eC o n t r o l i naH i g h -a c c u r a c y P l a s t i c I n je c t i o n M o l d i n g M a c h i n eB a s e do nC M A Ca n dP I DC o m po u n dC o n t r o l l e r C a iK a n Y i n g J i C h e nZ i c h e n W a n g Sh u o Z h e j i a n g U n i v e r s i t y ,H a n gz h o u ,310027A b s t r a c t :A i m i n g a t s e r i o u s p r o b l e m s o f c o n t r o l l i n gp a c k i n gp r e s s u r e i n i n j e c t i o nm o l d i n gp r o c e s -s e sw i t h t r a d i t i o n a l P I Da l g o r i t h m ,s u c ha s p r e s s u r eo v e r s h o o t ,s t a t i c e r r o r ,t i m ed e l a y e t c .,am a t h e -m a t i c a lm o d e l o f t h e p a c k i n gp r e s s u r e s y s t e mi n i n j e c t i o n p r o c e s sw a s e s t a b l i s h e d .C o n s i d e r i n g t h e b e -h a v i o r s o f s y s t e m ,an e wc o n t r o l d e v i c ew i t hC MA Ca n dP I Dc o m p o u n dc o n t r o l l e rw a sd e s i gn e d .T h e e x p e r i m e n t a l r e s u l t s s h o wt h a t ,c o m p a r e d t o t r a d i t i o n a lP I Dc o n t r o l ,C MA Ca n dP I Dc o m p o u n dc o n -t r o l i m p r o v e s t h e p r e s s u r e o v e r s h o o t ,s t a t i c e r r o r a n d t i m e d e l a y o f t h e p a c k i n gp r e s s u r e s i g n i f i c a n t l y,a n dm a k e s n o t a b l e p r o g r e s s e s o n q u a l i t y a n d r e p e a t a b i l i t y of p r o d u c t s .K e y w o r d s :i n j e c t i o n m o l d i n gp r o c e s s ;p a c k i n gp r e s s u r e ;n e u r a ln e t w o r k ;C MA Ca n d P I D c o m -po u n d c o n t r o l 收稿日期:2011 01 10基金项目:国家科技支撑计划项目(2007B A F 13B 04)0 引言我国作为塑料制品的生产和消费大国,目前只能提供中低档注塑成形设备,因此发展精密注塑成形是我国注塑机行业的当务之急㊂制约注塑成形设备精度提高的因素很多,注塑过程中的保压控制是核心要素之一㊂一方面,保压压力对制品的收缩㊁翘曲㊁残余应力等有非常重要的影响,另一方面,注塑系统复杂,注塑过程中存在时变㊁非线性等特性且运行环境存在较严重的干扰,难以对保压压力实施精确控制㊂高温熔体充满模腔后,注塑过程进入保压补缩阶段,少量熔体在外部压力作用下缓慢流入模腔以弥补熔体冷却产生的收缩,这个过程持续到浇口封冻为止[1‐2]㊂为了实现保压压力的精确控制,需要解决控制对象和保压压力的检测问题㊂控制对象主要有伺服阀和伺服电机,相对而言,伺服电机控制精度更高㊁能耗更少㊂保压压力的检测位置主要有油缸㊁喷嘴和模腔,若对喷嘴或者模腔压力实施检测,安装压力传感器会破坏结构,影响生产和制品质量;采用超声检测等无损检测存在技术上的难度,离实际应用还有较大距离[3‐4]㊂将液压缸压力作为保压压力的控制参数容易实现,是目前生产和研究中广泛应用的方法㊂在油缸压力控制中,伺服电机的调速特性以及压力从定量泵传递到油缸存在滞后效应等,使得采用传统P I D 算法控制压力曲线时存在超调㊁静差和时延过大等缺陷,同时控制参数K P ㊁K I 和K D 的确定需要丰富的实际经验,否则效率较低㊂采用模糊㊁迭代㊁预测等先进P I D 算法作为保压压力的控制算法,算法计算量较大,难以进行实时控制㊂小脑模型关节控制器(c e r e b e l l a r m o d e la r t i c u l a t i o nc o n t r o l l e r ,C MA C )神经网络具有系统辨识功能,学习速度快,适合复杂动态环境下的非线性实时控制[5‐9]㊂本文在传统的P I D 控制基础上,引入C MA C神经网络,开发出了新型C MA C 和P I D 复合控制器㊂将该控制器在宁波海天塑机集团的MA 900注塑机平台上进行了实时控制实验,并与传统P I D 控制进行了对比㊂1 注塑过程保压压力的系统数学模型M A 900注塑机控制系统采用交流同步伺服电㊃88㊃中国机械工程第22卷第24期2011年12月下半月机直接驱动齿轮定量泵㊂系统可分为三个部分:动力控制部分(上位机㊁控制器和伺服电机),液压传动部分(定量泵㊁溢流阀㊁开关阀和油缸),执行机构(料筒㊁螺杆和模具),具体原理如图1所示㊂图1 注射系统原理图控制器处理指令压力p z和油缸反馈压力p1,发出压力信号p c以控制伺服电机转速n,伺服电机驱动定量泵输出液压油以控制油缸压力,油缸活塞推动螺杆,螺杆挤压料筒内的熔体进入模腔实现补缩,从而控制模腔内熔体压力㊂伺服电机-定量泵数学模型为q V=Vηp K Gτs+1p c(1)式中,q V为定量泵出口体积流量;V为排量;ηp为机械效率;K G为伺服电机增益系数;τ为时间常数;s为传递函数的复数变量㊂开关阀在保压过程中阀芯打开,相当于通路㊂液压缸为非对称缸,其进油腔流量连续性方程为q1=A1d x d t+V10+A1xβe d p1d t(2)式中,q1为油缸进油腔流量;x为活塞位移;V10为油缸进油腔初始体积;A1为进油腔活塞面积;βe为油液体积弹性膜量㊂油缸泄油腔直接连通油箱,腔内油液压力为零㊂熔融塑料在料筒中的运动是非牛顿流动,并可认为是轴向环形C o u e t t e流动,由此得出保压过程中螺杆所受的黏性摩擦力:F s=2πη0R1-n n(l0+x)[(s-1)v xk1-s r-1]n(3)式中,η0为聚合物黏滞系数;R n为喷嘴半径;n为聚合物熔融的幂率指数;k r为螺杆半径和料筒半径之比;l0为螺杆长度;v x为活塞速度㊂由于模腔熔体的温度㊁密度和P V T曲线难以获得,因此将喷嘴处反压力F p简化为F p=B v x+k x(4)式中,B为阻尼系数;k为比例系数㊂料筒前端熔体压力与喷嘴压力相近,故料筒对熔体的反压力F L为F L=(A L-A p)p p(5)式中,A L为料筒前端横截面积;A p㊁p p分别为喷嘴横截面积㊁熔体压力㊂对油缸负载即执行机构做力平衡分析,有A1p1=F s+F L+A p p p(6)忽略泄漏对系统的影响,泵的出口流量即为油缸进油腔流量㊂将式(1)代入式(2),再进行L a p l a c e变换,得s p1(s)=βeV10+A1x0Vηp K Gτs+1p c(s)-βe A1V10+A1x0X(s)s-βeA1(q10-A1v x0)(V10+A1x0)2X(s)(7)式中,x0㊁v x0分别为活塞初始位移㊁初始速度;q10为油缸进油腔初始流量㊂将式(3)~式(5)代入式(6)再进行L a p l a c e 变换得mX(s)s2=A1p1(s)-A L(B s+k)X(s)-a v x0X(s)-a(L0+x0)n X(s)s(8)a=2πη0R1-n n(s-1k1-s r-1)nv n-1x0式中,m为活塞和螺杆的质量之和㊂联立式(7)㊁式(8),消去X(s)可得系统模型: p1(s)p c(s)=b m s2+bc s+b dτm s4+(m+τc)s3+(c+τe)s2+(e+τf)s+fb=βe Vηp K GV10+A1x0,c=B A L+a n(l0+x0)d=k A L+a v x0,e=d+A21βeV10+A1x0f=βe A21(q10-A1v x0)(V10+A1x0)2上述模型为开环传递函数,通过控制算法计算处理指令压力和油缸压力,从而实现对系统的闭环控制㊂2 C MA C和P I D复合控制器设计针对系统非线性和时变等特性,引入神经网络对系统进行辨识㊂C MA C是一种模拟小脑功能的神经网络模型,是一种表达复杂非线性函数的表格查询自适应神经网络㊂C MA C神经网络结构如图2所示㊂C MA C神经网络和P I D复合控制的核心思想是:当系统开始运行时,置学习参数w=0,此时,系统由P I D控制器进行控制;每一控制周期结束后,将C MA C神经网络输出与总控制输出进行比较,修正权重,进入学习过程㊂随着C MA C 神经网络的不断学习,C MA C神经网络产生的输出控制量逐渐逼近控制器总输出,而P I D产生的输出的控制量逐渐减小为零,最终实现C MA C神经网络对系统的辨识,利用系统信息来进行控制优化,实现控制性能的改善㊂㊃98㊃基于C MA C和P I D复合控制器的精密注塑机保压压力控制 蔡 侃 应 济 陈子辰等图2 C M A C神经网络结构图针对P I D控制中压力跟随曲线超调㊁波动的特点,同时消减干扰信号,对指令压力u z做低通滤波处理㊂由于受处理器所限,同时高阶滤波会增大时延,因此本控制器采用一阶低通滤波,传递函数设为1/(εs+1)(ε为决定滤波截止频率的参数),离散化后得到指令信号u(h)(表示第h次指令信号的离散值):u(h)=-d e n(2)u(h-1)+n u m(1)(u z(h)+u z(h-1))式中,d e n㊁n u m分别表示离散传递函数的分母㊁分子㊂C MA C神经网络采用有导师的学习算法,实现前馈控制,P I D控制实现反馈控制,以保证系统的稳定性,且抑制扰动㊂C MA C神经网络和P I D 复合控制结构如图3所示㊂图中,u z(h)为输入信号,u p(h)为常规控制器P I D的输出,u n(h)为C MA C产生的相应输出㊂图3 C MA C神经网络和P I D复合控制流程图控制器运算包括以下4个阶段:(1)将指令信号u(h)作为C MA C控制器的输入㊂(2)经过局部泛化,将输入向量映射到概念存储器中㊂将输入空间S在区间[S m i n,S m a x]上分成N+2C个量化间隔:o1,o2, ,o C=S m i no j=o j-1+Δo j j=C+1, ,C+No N+C+1,o N+C+2, ,o N+2C=S m a x式中,o j为输入空间分割后的量化间隔;S m i n和S m a x为输入的最大值和最小值;C为C MA C网络的泛化参数㊂(3)C MA C神经网络实现映射的方法为,当S j在区间[o j,S j+C]中时,二进制选择向量a i的值为1,否则为0㊂C MA C神经网络学习算法采用δ学习规则调整权值,权值调整指标为E(h)=12C e(h)2=12C(u n(h)-u(h))2式中,e(h)为误差㊂由梯度下降法,权值调整如下:Δw(h)=-η∂E(h)∂w=ηu(h)-u n(h)C a i=ηu p(h)C a i w(h)=w(h-1)+Δw(h)+α(w(h)-w(h-1))式中,η为网络学习速率;α为惯性量㊂梯度下降法存在容易陷入局部最优解和收敛速度慢的缺点,本文采用变步长梯度下降法予以改进,即步长采用自适应学习策略:η(h+1)=η(h)-λΔe(h)e(h)其中,λ为步长调整参数,根据误差变化值Δe(k)自动调整,当Δe(k)<0时,误差减小,此时步长增大以提高搜索速度;当Δe(k)>0时,误差增大,此时步长减小以减慢搜索速度㊂(4)将实际存储器单元中的权值相加作为网络输出值,由此信号去控制伺服电机㊂将上述滤波算法㊁P I D算法和C M A C神经网络算法分别写成C语言子程序,在主程序中调用,将程序在K e i l开发软件中调试完毕㊂外围电路根据要求设计完毕后,即可将程序下载到A D u C841芯片中,再根据实验效果调整算法中的参数㊂3 注塑过程保压压力实验为验证C MA C神经网络控制的实际效果,本文以A D公司A D u C841微控制器为核心,自行设计开发了C MA C和P I D复合控制器,然后将其应用到海天MA900型注塑机平台上㊂实验流程如图4所示㊂图4 实时控制系统流程图实时控制器集成了A/D㊁C MA C和D/A模块㊂利用A D u C841微控制器片内的A/D模块实时读取上位机指令,控制器计算处理指令压力和反馈压力,信号经D/A转换后发往伺服电机(图㊃09㊃中国机械工程第22卷第24期2011年12月下半月4中由伺服控制器代指),从而控制油缸压力㊂实验制品为薄圆盘,注塑材料选用聚丙烯㊂保压过程中系统采样周期为1m s㊂参考实际生产中注塑保压工艺,实验中保压压力设置为阶梯状的五段曲线,压力值分别为2M P a ㊁4M P a ㊁6M P a㊁4M P a ㊁2M P a ,每段时长为2s㊂第一组实验采用P I D 控制器,第二组实验采用C MA C 和P I D 复合控制器㊂选取稳定状态下保压压力跟随曲线,如图5所示㊂分析实验保压压力曲线可得表1㊂图5 保压过程实验曲线表1 实验保压过程压力值分析上升阶段超调(%)上升阶段时延(s )静差(M P a )波动(M P a )下降阶段超调(%)下降阶段时延(s)P I D 控制290.050.90.660.30复合控制无0.070.20.380.08 两组实验稳定状态下的制品如图6所示㊂观察制品,第一组制品(图6a)浇口处有熔体大量溢出,同时边缘有少量飞边,边缘触感粗糙;第二组制品(图6b)没有熔体溢出,没有飞边,边缘圆滑㊂(a )传统P I D 控制(b )C MA C 和P I D 复合控制图6 实验制品比较分析制品质量,用样本与平均值的偏差的平方和来求重复精度,可得表2㊂表2 实验制品重量分析平均质量(g)最重与最轻之差(g)重复精度(%)传统P I D 控制11.8870.255.96C MA C 和P ID 复合控制11.3260.121.87综上所述,采用传统P I D 控制,保压压力上升超调严重,静差较大,保压压力下降严重滞后,制品重复精度较低,且制品存在缺陷,而采用C MA C 和P ID 复合控制使得制品质量有很大的提高,适用于精密注塑控制㊂4 结语本文建立了注塑过程保压压力的数学模型,开发设计了新型C MA C 和P I D 复合控制器㊂C MA C 神经网络对系统的辨识功能消减了伺服电机调速特性和液压系统压力特性的影响,与传统P I D 控制的实验结果比较表明,C MA C 和P I D复合控制可以极大地改善保压压力超调㊁静差和时延,制品质量有很大程度的提高㊂正在完善控制器的其他性能,计划取代原控制器而应用到宁波海天塑机集团精密注塑机中㊂参考文献:[1] K a m a lM R ,K u oY ,D o a nP H.T h e I n j e c t i o n M o l d -i n g B e h a v i o r o fT h e r m o p l a s t i c s i nT h i nR e c t a n gu l a r C a v i t i e s [J ].P o l y.E N G.S c i .,1975,15(12):863.[2] 陈曦.基于质量的注塑过程建模方法研究[D ].杭州:浙江大学,2001.[3] Z h a n g L i .AS e l f -e n e r g i z e dS e n s o r f o rW i r e l e s s I n -j e c t i o n M o l dC a v i t y P r e s s u r e M e a s u r e m e n t :D e s i gn a n dE v a l u a t i o n [J ].J .o fD y n a m i cS y s t e m s ,M e a s -u r e m e n t ,a n dC o n t r o l ,2004,126:309‐318.[4] C a oB i n .O n-l i n e U l t r a s o n i c M o n i t o r i n g o f I n j e c -t i o n M o l d i n g a n dD i eC a s t i n g P r o c e s s e s [D ].M o n t -r e a l ,Q u e b e c ,C a n a d a .M c G i l lU n i v e r s i t y,1996.[5] A l b u sJS .A N e w A p p r o a c ht o M a n i p u l a t e rC o n -t r o l :t h e C e r e b e l l a r M o d e l A r t i c u l a t i o n C o n t r o l l e r(C MA C )[J ].J .o fD y n a m i cS ys t e m s ,M e a s u r e m e n t a n dC o n t r o l ,1975,97(3):220‐227.[6] 刘金琨.先进P I D 控制MA T L A B 仿真[M ].北京:电子工业出版社,2004.[7] A l b u s J S .M o d e l i n g a n dC o n t r o l o f a nE l e c t r o -h y -d r a u l i c I n je c t i o n M o d e l i n g Ma c h i n ew i t hS m o o t h e d F i l l -t o -P a c kT r a n s i t i o n [J ].J .o f M a n u f a c t u r i n gS c i e n c e a n dE n g i n e e r i n g,2003,125:154‐163.[8] 钟民军,胡世峰,史铁林.双层混合隔振系统的C MA C 和P I D 复合控制研究[J ].中国机械工程,2008,19(13):1547‐1551.[9] 阮晓钢.神经计算科学[M ].北京:国防工业出版社,2006.(编辑 苏卫国)作者简介:蔡 侃,男,1986年生㊂浙江大学机械系现代制造工程研究所硕士研究生㊂研究方向为注塑成形过程控制与检测技术㊂应 济,男,1964年生㊂浙江大学机械系现代制造工程研究所副研究员㊂陈子辰,男,1950年生㊂浙江大学机械系现代制造工程研究所教授㊂王 硕,男,1984年生㊂浙江大学机械系现代制造工程研究所博士研究生㊂㊃19㊃基于C MA C 和P I D 复合控制器的精密注塑机保压压力控制蔡 侃 应 济 陈子辰等。
注塑机的保压有什么用

注塑成型各种缺陷的现象及解决方法(一)熔接痕熔接痕是由于来自不同方向的熔融树脂前端部分被冷却、在结合处未能完全融合而产生的。
一般情况下,主要影响外观,对涂装、电镀产生影响。
严重时,对制品强度产生影响(特别是在纤维增强树脂时,尤为严重)。
可参考以下几项予以改善:l)调整成型条件,提高流动性。
如,提高树脂温度、提高模具温度、提高注射压力及速度等。
2)增设排气槽,在熔接痕的产生处设置推出杆也有利于排气。
3)尽量减少脱模剂的使用。
4)设置工艺溢料并作为熔接痕的产生处,成型后再予以切断去除。
5)若仅影响外观,则可改变烧四位置,以改变熔接痕的位置。
或者将熔接痕产生的部位处理为暗光泽面等,予以修饰。
(二)放射纹放射纹(Jetting)1、表观从浇口喷射出,有灰黯色的一股熔流在稍微接触模壁后马上被随后注入的熔料包住。
此缺陷可能部分或完全隐藏在制品内部。
物理原因放射纹往往发生在当熔料进入到模腔内,流体前端停止发展的方向。
它经常发生在大模腔的模具内,熔流没有直接接触到模壁或没有遇到障碍。
通过浇口后,有些热的熔料接触到相对较冷的模腔表面后冷却,在充模过程中不能同随后的熔料紧密结合在一起。
除去明显的表面缺陷,放射纹伴随不均匀性,熔料产生冻结拉伸,残余应力和冷应变而产生,这些因素都影响产品质量。
在多数情况下不太可能只通过调节成型参数改进,只有改进浇口位置和几何形状尺寸才可以避免。
与加工参数有关的原因与改良措施见下表:1、注射速度太快降低注射速度2、注射速度单级采用多级注射速度:慢-快3、熔料温度太低提高料筒温度(对热敏性材料只在计量区)。
增加低螺杆背压与设计有关的原因与改良措施见下表:1、浇口和模壁之间过渡不好提供圆弧过渡2、浇口太小增加浇口3、浇口位于截面厚度的中心浇口重定位,采用障碍注射(三)灰黑斑纹(Grey or black clouding)1、表观灰黑斑纹可能发生在浇口附近,流道的中间和远离浇口的部分。
只能在透明的零件中可看出,并且往往用PMMA,PC 和PS 料制成的产品有此现象。
注塑压力曲线变化
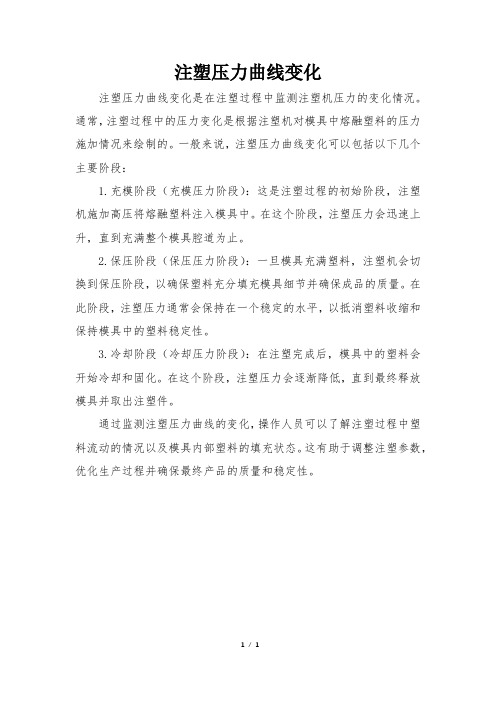
注塑压力曲线变化
注塑压力曲线变化是在注塑过程中监测注塑机压力的变化情况。
通常,注塑过程中的压力变化是根据注塑机对模具中熔融塑料的压力施加情况来绘制的。
一般来说,注塑压力曲线变化可以包括以下几个主要阶段:
1.充模阶段(充模压力阶段):这是注塑过程的初始阶段,注塑机施加高压将熔融塑料注入模具中。
在这个阶段,注塑压力会迅速上升,直到充满整个模具腔道为止。
2.保压阶段(保压压力阶段):一旦模具充满塑料,注塑机会切换到保压阶段,以确保塑料充分填充模具细节并确保成品的质量。
在此阶段,注塑压力通常会保持在一个稳定的水平,以抵消塑料收缩和保持模具中的塑料稳定性。
3.冷却阶段(冷却压力阶段):在注塑完成后,模具中的塑料会开始冷却和固化。
在这个阶段,注塑压力会逐渐降低,直到最终释放模具并取出注塑件。
通过监测注塑压力曲线的变化,操作人员可以了解注塑过程中塑料流动的情况以及模具内部塑料的填充状态。
这有助于调整注塑参数,优化生产过程并确保最终产品的质量和稳定性。
1/ 1。
注塑保压时间

在研究塑料制品注塑成型的过程中,常常将注塑分为两个阶段:在第一阶段,大部分塑料充入模具中,一般为整个制品体积的90%~99.9%;在第二阶段,压实制品,得到与模具结构和外形相同的制品。
在第二阶段,虽然只有相对较少的塑料熔体充入型腔,然而对制品表面的光洁度,美学外观以及制品尺寸来说非常重要。
在大多数情况下,注塑成型的第二阶段使用压力和时间两个参数。
从科学成型的研究角度,我们将两个因素增加到四个要素:(1)第一阶段向第二阶段转换的方法;(2)保持浇口密封(冻结)或浇口不密封状态下,加工制品;(3)保压时间;(4)保持型腔内的合理压力。
1、转换或许可以这样说,第一阶段向第二阶段转换的控制是成型过程最关键的部分。
能否加工出高质量的制品往往取决于此,而且也常常是塑料加工厂不能从一台设备到另一台设备生产出相同制品的原因。
在大多数应用领域,应尽可能让转换过程短,即不论第一阶段最后是什么压力,都希望能够快速变化到第二阶段压实和保压所需要的压力。
另外,你必须了解设备控制单元是如何正确完成这一转换过程。
遗憾的是在不同设备之间如何判断完成转换还没有统一标准,因此注塑企业需面临四种可能:①加工设备配置控制粘度的转换功能②设备控制单元具有一个转换用粘度设定值,但它只能让转换时压料杆的速度变慢,却不能控制③设备没有用于转换的粘度设定值④第一阶段向第二阶段转换时,设备不能正常运转,出现渐变的粘度倾斜,下降或波摆动。
必须要保证第一阶段向第二阶段转换时迅速而一致。
因此了解注塑机的工作原理对获得所需要的结果非常关键。
对大多数制品,正确的工艺控制来说,第一阶段结束到第二阶段压力设定点的时间应小于0.1秒。
不希望向第二阶段压力转变时出现任何下沉,细而尖的峰,摆动或缓缓滑进第二阶段的压力现象。
下沉会引起流体前锋变得迟疑,造成欠保压或缺料。
细峰或缓慢转变到第二阶段的压力将过度填充型腔,造成飞边。
摆动常造成加工稳定性差。
注塑压力的压力监控器图形与时间的对应关系可作为评估设备响应最好的方式。
保压

保压起什么作用保压也就是所谓的二次压.当注塑的时候,注塑的压力是程曲线变化的,而保压则是恒定或有一定斜度的.首先你要搞明白,保压的情况下注塑机也在射胶.当一次压完成后,由于塑胶温度的降低及其内部的内应力,模腔里面的塑胶会发生回流现象.如果没有保压来消除这些力,则产品就会产生缩水甚至不饱模.这是保压的其中一个作用.另外保压可以控制产品的变形量及尺寸的大小.保压太大或太小都不适合.保压太大,产品会出现尺寸大,翘曲甚至粘模.太小的话最直观的就是会产生缩水.至于保压时间,要看产品的肉厚及大小做相应调节.这些需要你自己去实践中摸索.有一点记住.一次压过后熔融的塑胶会在短时间内成型,而保压就在这时间内完成的.具体敲自己摸索摸索关模的低压保护怎么设置低压保护又叫金型保护.不管曲轴还是直压,都应该有.曲轴的低压保护设置相对复杂一些.要先调模厚,然后根据你的模具低压需要的灵敏度来相应的调节位置,压力及时间.我们这边一般低压保护压力设定在3以内,时间1S以内,相对位置就大了点.注塑原理一、何为注塑:所谓注塑就是塑胶材料在注塑机的料筒中经过外部的加热和螺杆的旋转而产生的剪切热对树脂材料进行塑化成熔体后,通过施加一定的压力,把熔体注射到具有一定的形状的型腔中经过冷却定型后所产生的物品就为注塑。
二、注塑的过程,也就是注塑的周期:三、注塑的三大基本要素:机器—包括注塑机、辅机。
模具、材料四、注塑工艺的五大要素:1、温度:A、油温:对于液压机而言是由于机器的不停运作液压油运动摩擦而产生的热能,它是由冷却水来控制,在开机时要确认油温在45℃左右,若油温过高或过低均会影响压力的传递。
B、料温:即炮筒温度,此温度要根据材料和产品的形状和功能去设定,若有文件则根据文件去设定它。
C、模温:此温度也是一个重要的参数,它的高低对于产品的性能影响很大,故设定时一定要考虑产品的功能和结构,同时还要考虑到材料和周期。
2、速度:A、开合模的速度设定,开合模的设定一般是按慢—快—慢的原理,这样设定主要考虑机器、模具、周期去考虑。
注塑机参数设置

注塑机参数设置有读者问:注塑时注射速度,位置,压力都怎么设置?保压的压力怎么确定?我们的经验所知,一般的简单的小产品,可先设置一段高速高压,使用位置切换,调位置打出约90%完整度的产品,保压速度也用高速,保压压力设置在注射压力的一半左右或略高,保压时间从1s往上加,选择产品单重稳定的时间为保压时间。
背压可以根据机台选择一个经验值。
简单产品一般一段高速成型就OK了,但是对模具和设备要求比较高。
一般情况下还要以这个为基础,调整第二段或者多段工艺。
如果开模没有考虑到产品变形或者排气做的不好,还需要调节模温,使用低速,低压工艺等。
试模是一个调试的过程,具体问题还要具体分析。
一般情况下都是打到产品的90%,之后就是加保压,这样就需要你知道此产品的计量的前提下找切换位置,至于速度就要根据产品的材料来确定了,ABS料要低速低压,尼龙料要高速高压,总之要考虑材料的流动性、产品骨位的多少,当然必要时最好用模温机来改善模温,让材料在模腔的流动性有所改善。
保压的作用是保证产品的美观的前提下调节局部尺寸,俗话说“一保二压三稳定”就是这个道理,第一段保产品最后一段保料头。
有些产品骨位太多、太深,这就需要准确的知道哪一段管这里,调节位置和速度来走满!其实都需要经验,注塑上有句话:没有谁多牛多牛,就看你考虑的是不是全面,找没找到问题的关键点!一、压力由注塑机的压力系统(油泵)或司服马达所提供的动作压力,主要运用于注射装置、熔胶装置、开锁模装置、顶出装置、射台装置,抽芯装置等各动作程序,在注塑机的控制面板输入相关参数后由处理器将其转换成各程序动作的信号,从而控制各个动作程序的执行所需的压力。
压力设定原则为:克服该动作阻力的相应力度,但为配合动作的速度需相应调整其参数值。
二、速度配合上述的压力来完成各动作程序所需活动速度(系统液压油的流量),速度的基本等级区分:缓流0.1-10、慢速11-30、中速31-60、高速61-99。
1. 射胶速度的控制,应用于不同的制品结构及用料来设置大小数值,在此暂不区分(工程/通用塑料,结晶/非结晶塑料,高温/低温塑料,软胶/硬胶塑料)容易混淆视听,作个比较易懂的解释,射胶速度是注塑成型中比较难控制的工艺要素,不象其他的工艺要素都有标准的数据可供参考(后续会作详细的介绍)。
在注塑成型中,你是如何“转换保压”的?

在注塑成型中,你是如何“转换保压”的?在注塑成型中,注射和保压是共存的,对于刚刚接触成型调试和模流的初学者都会疑问,“产品注射满了,保压该如何加呢”?其实,保压并没有具体的数值,都是根据自己的生产经验进行设定,而且每个人的思路不同,设定的数值都会有些差异,以下是我在调试时,所理解保压的使用方法。
一、转换保压的控制方式在注塑成型中,当熔体注射动作完成后,熔体会因为材料冷凝收缩、定型的特性,模腔内部会留有空间,当螺杆保持一定的压力,继续向模腔内施加压力注射溶体,就会弥补填充收缩后剩下的空间,即转入的就是保压。
保压的参数设定对产品的质量有大的影响,在保压的作用下,模腔的熔体得到补缩和压实。
在调试时如果保压过大,会导致浇口附近内应力过大,应力开裂、产品脱模拉伤,周期时间长等问题;如果保压过小会导致产品缩水、气泡、表面凹凸不平等缺陷发生,调试产品时保压参数的常用的设定方式:1、先低后高的保压设定在注射结束后,熔体会由于惯性的作用,螺杆还会注入一些熔体,而前段保压压力设定低、增加停顿时间,接触到模芯的材料会冷凝固化,避免熔体过度填充而引起的缺陷;后段采用较高的保压压力控制浇口附近熔体的冷凝,补偿产品缩水,还可以控制产品形变。
2、由高逐渐下降的保压设定前段保压用于快速补缩接触到模芯还没有注射后冷凝的熔体,对于调试产品重量和尺寸有很大效果;后段保压冷凝定形,用于逐渐释放产品的残余应力的作用。
二、转换保压的位置确定查看注塑机的检测画面和注塑机的压力表都可以查看到保压的转换位置,也就是注塑机起压的地方至降压的地方。
在我刚开始学习成型调试的时候,老师傅告诉我:“产品快打满了(95%),一点点加保压,看产品外形变化,表面是否缩水、变形、达到重量、寸法要求?”对于保压该如何设定位置点,还是在需要根据生产情况,了解材料的流动性、产品的寸法和重量要求、以及形变、模具结构等原因,才能找出合适的转换保压位置。
但是也有的产品不需要转换保压,比如我曾经接触的同一系列的使用PP材料进行填充的产品,在换产开机调试的时候需要喷脱模剂,否则就筋位塞料、卸模拆解模具。
保压时间和保压压力对注塑制品厚度分布的影响

表 3 制品最厚处与最薄处厚度值之差
The effe ct of pa cking pre ssure a nd pa cking time on thickne ss distribute of inje ction molding parts
Q iu Bin, Li Wei
(Me chanic al and elec trica l e ngine e r institute ,Jia ngxi Unive rsity
inje c tion molding parts is inve stigate d by te st. The conclusions will he lpful for de s ign of pla stiy W
j
,
,
,
f
72
2006 / 1 1
品的最厚处与最薄处的差值最小;多级保压可以获得 比常压保压更均匀的制品厚度分布。
图 6 聚丙烯制品在不同位置的厚度随保压压力的变化
制品厚度最大值与最小值之差见表 3。
参考文献 1 北京化工大学、华南理工大学合编.塑料机械设计.第 2 版.中国 轻工业出版社,1995。 2 王喜顺,彭玉成.注射成型中冷却阶段 的研究.模 具工业.1999, (4):40
of S cie nce a nd Te chnology, Jia ngxi Ganzhou, 341000)
Abstra ct: Introduce the pa cking pha se of inje ction molding .the e ffe ct of pac king pre ss ure a nd pac king time on thickne ss distribute of
注塑机压力单位

注塑机压力单位注塑机压力单位是指在注塑过程中所施加的压力,是影响注塑产品质量的重要因素之一。
正确的压力控制可以确保注塑产品的尺寸精度和结构牢固性。
在注塑机中,常用的压力单位有:牛顿(N)、兆帕(MPa)、巴(bar)和千克力(kgf)等。
下面将逐一介绍这些压力单位的特点和应用。
首先是牛顿(N),牛顿是国际单位制中力的单位,常用于描述物体所受到的外力大小。
在注塑机中,牛顿通常用于表示注射压力和保压力。
注射压力是注塑机在注塑过程中向模具内注射熔融塑料所施加的压力,而保压力是指在注塑完成后,为了使注塑产品的尺寸稳定,需要施加的保持压力。
牛顿作为一个基本力单位,具有较好的可读性和易于计算的特点,广泛应用于注塑机的控制系统中。
其次是兆帕(MPa),兆帕是国际单位制中压力的单位,常用于描述材料的强度和刚度。
在注塑机中,兆帕通常用于表示注射压力和保压力的大小。
与牛相比,兆帕具有更大的数值范围,可以精确描述较大的压力值。
兆帕的使用需要将压力值转换为力值,再与面积进行计算,因此在一些需要对压力进行精确控制和计算的注塑应用中,更常使用兆帕作为压力单位。
再次是巴(bar),巴是国际单位制中压力的单位,常用于表示气体压力和液体压力。
在注塑机中,巴通常用于表示液体的压力,例如液压系统中的油压。
巴的使用较为广泛,因为注塑机中的液压系统是重要的动力源,对压力的精确控制要求较高。
巴的计算相对简单,可以直接表示压力值,而不需要进行额外的转换。
因此,在液压注塑机中,巴是常见的压力单位之一。
最后是千克力(kgf),千克力是国际单位制中力的单位,常用于描述物体的质量和重力。
在注塑机中,千克力通常用于表示注射压力和保压力的大小。
与牛顿类似,千克力也是一个基本力单位,具有较好的可读性和易于计算的特点。
千克力的使用需要将压力值转换为力值,再与面积进行计算,因此在一些需要对压力进行精确控制和计算的注塑应用中,也会使用千克力作为压力单位。
综上所述,注塑机压力单位有牛顿、兆帕、巴和千克力等。
- 1、下载文档前请自行甄别文档内容的完整性,平台不提供额外的编辑、内容补充、找答案等附加服务。
- 2、"仅部分预览"的文档,不可在线预览部分如存在完整性等问题,可反馈申请退款(可完整预览的文档不适用该条件!)。
- 3、如文档侵犯您的权益,请联系客服反馈,我们会尽快为您处理(人工客服工作时间:9:00-18:30)。
保持压力的设定是为使树脂在冷却的过程中不致产生回流,且能继续补充因树脂冷却收缩而不足的空间,而得到最佳的模具复制效果。
保持压力设定过高,易造成毛边、过度充填浇口附近的应力集中等不良现象,保持压力设定过低,又易造成收缩太大、尺寸不安定等现象。
保持压力必须伴随保压切换点及保压时间设定方为有效。
保压不足时会导致:1.凹陷;2.气泡;3.收缩率增加;4.成形品尺寸变小;5.尺寸的波动性变大;6.由于熔胶回流导致内层配向。
过大的保压则会造成:1.注道(Sprue)区域的应力;2.脱模困难;3.外皮层的拉伸应力。
保压时间阶段逐次降低保压可(多段保压):1.减少翘曲、降低从浇口到末端的成形品区域之收缩变异;2.减少内应力;3. 减少能源损耗。
保压时间的设定是为控制保压产生作用的时间,保压时间设定不足将使产品发生尺寸、重量不安定。
但保压时间设定太长,又会影响成形效率。
适当的保压时间是维持到浇口凝固的时间即可,同时保压大小与保压时间的适当配合,可使程序式保压控制发挥最大效用。
保压系为了射出终了时密封注道及因体积收缩的补偿,因此保压必须高于内部残留的压力。
保压时间设定如果在最大有效保压时间之前停止,亦即保压时间过短,则可能产生下列之结果:1.凹陷;2.气泡;3.重量不足;4.尺寸较小;5.由于熔胶之回流产生内部配向。
;6.更高的翘曲,尤其在半结晶性的材料;7.更大尺寸波动;8.收缩率增加设定有效的保压时间至少须到注道固化,一般约为冷却时间的30%即够.通常将注射压力的控制分成为一次注射压力、二次注射压力(保压)或三次以上的注射压力的控制。
压力切换时机是否适当,对于防止模内压力过高、防止溢料或缺料等都是非常重要的。
模制品的比容取决于保压阶段浇口封闭时的熔料压力和温度。
如果每次从保压切换到制品冷却阶段的压力和温度一致,那麽制品的比容就不会发生改变。
在恒定的模塑温度下,决定制品尺寸的最重要参数是保压压力,影响制品尺寸公差的最重要的变量是保压压力和温度。
例如:在充模结束后,保压压力立即降低,当表层形成一定厚度时,保压压力再上升,这样可以采用低合模力成型厚壁的大制品,消除塌坑和飞边。
保压压力及速度通常是塑料充填模腔时最高压力及速度的50%~65%,即保压压力比注射压力大约低0.6~0.8MPa。
由于保压压力比注射压力低,在可观的保压时间内,油泵的负荷低,固油泵的使用寿命得以延长,同时油泵电机的耗电量也降低了。
***压力注射既能使制件顺利充模,又不会出现熔接线、凹陷、飞边和翘曲变形。
对于薄壁制件、多头小件、长流程大型制件的模塑,甚至型腔配置不太均衡及合模不太紧密的制件的模塑都有好处。
在注塑过程里,溶体因为冷却而收缩,但由于螺杆要继续缓慢地向前移动,使料管中的熔体继续注入型腔,以补充制品收缩的需要,称之为保压.说白了就是防止产品收缩的,用保压的话产品生产也比较稳定.保压还可以调整产品尺寸的大小,又不会出现熔接线,凹陷,飞边和翘曲变形.其实保压和注射都是一个意思,就是用力把螺杆往前推,只不过注射过程中,以注射速度为设定,以最大注射压力为上限的推动,在保压过程中,是以注射压力为设定,以最大保压速度为上限的推动.注塑机分段成型,优点是可以分段调节原料进入模具的速度以及压力,这样一些较为复杂结构的产品可以降低不良率。
同时也可以保护模具内的小镶件,例:在原料进入模具的时候,遇到小的镶件的时候降低速度以及压力,这个镶件就不容易损坏分段保压可以减少产品凹陷等,主要优点也是减少不良的产生注塑机保压在什么情况下最起作用?注塑机具有能一次成型外型复杂、尺寸精确或带有金属嵌件的质地密致的塑料制品,被广泛应用于国防、机电、汽车、交通运输、建材、包装、农业、文教卫生及人们日常生活各个领域。
注射成型工艺对各种塑料的加工具有良好的适应性,生产能力较高,并易于实现自动化。
在塑料工业迅速发展的今天,注塑机不论在数量上或品种上都占有重要地位,其生产总数占整个塑料成型设备的20%--30%,从而成为目前塑料机械中增长最快,生产数量最多的机种之一。
据有关资料统计,1996--1998年我国出口注塑机8383台(套),进口注塑机42959台(套),其中1998年我国注塑机产量达到20000台,其销售额占塑机总销售额的42.9%。
注塑机的工作原理与打针用的注射器相似,它是借助螺杆(或柱塞)的推力,将已塑化好的熔融状态(即粘流态)的塑料注射入闭合好的模腔内,经固化定型后取得制品的工艺过程。
注射成型是一个循环的过程,每一周期主要包括:定量加料—熔融塑化—施压注射—充模冷却—启模取件。
取出塑件后又再闭模,进行下一个循环。
注射成型是一个循环的过程,每一周期主要包括:定量加料—熔融塑化—施压注射—充模冷却—启模取件。
取出塑件后又再闭模,进行下一个循环。
一般注塑机包括注射装置、合模装置、液压系统和电气控制系统等部分。
注射装置:它的主要作用是使塑料均匀地塑化成熔融状态,并以足够的压力和速度将熔料注射入模具中。
它主要由塑化部件(机筒、螺杆或柱塞、喷嘴等)、料斗、螺杆传动装置(油马达等)、注射油缸、注射座移动油缸等组成。
合模装置:它是保证成型模具可靠的闭合和实现启闭模动作以及取出制品的部件。
由于熔料以很高的压力注入模腔中,为了锁紧模具而不致使制品产生飞边或影响制品质量,就要对模具施加足够的锁紧力(即合模力)。
合模装置主要包括固定模板、移动模板、后墙板、连接前后模板用的拉杆、合模油缸、顶出油缸、调模装置等组成。
液压系统和电气控制系统:它是保证注塑机按工艺过程预定的要求(如压力、速度、温度、时间等)和动作程序准确有效的进行工作而设置的动力和控制系统。
一般螺杆式注塑机的成型工艺过程是:首先将粒状或粉状塑料加入机筒内,并通过螺杆的旋转和机筒外壁加热使塑料成为熔融状态,然后机器进行合模和注射座前移,使喷嘴贴紧模具的浇口道,接着向注射缸通人压力油,使螺杆向前推进,从而以很高的压力和较快的速度将熔料注入温度较低的闭合模具内,经过一定时间和压力保持(又称保压)、冷却,使其固化成型,便可开模取出制品(保压的目的是防止模腔中熔料的反流、向模腔内补充物料,以及保证制品具有一定的密度和尺寸公差)。
注射成型的基本要求是塑化、注射和成型。
塑化是实现和保证成型制品质量的前提,而为满足成型的要求,注射必须保证有足够的压力和速度。
同时,由于注射压力很高,相应地在模腔中产生很高的压力(模腔内的平均压力一般在20~45MPa之间),因此必须有足够大的合模力。
由此可见,注射装置和合模装置是注塑机的关键部件。
注塑机的动作程序关门→合模→喷嘴前进→注射→保压→预塑→松退→喷嘴后退→冷却→开模→顶出→退针→开门。
注塑机操作项目:注塑机操作项目包括控制键盘操作、电器控制系统操作和液压系统操作三个方面。
分别进行注射过程动作、加料动作、注射压力、注射速度、顶出型式的选择,料筒各段温度的监控,注射压力和背压压力的调节等对塑料制品的评价主要有三个方面,第一是外观质量,包括完整性、颜色、光泽等;第二是尺寸和相对位置间的准确性;第三是与用途相应的物理性能、化学性能、电性能等。
这些质量要求又根据制品使用场合的不同,要求的尺度也不同。
制品的缺陷主要在于模具的设计、制造精度和磨损程度等方面。
但事实上,塑料加工厂的技术人员往往苦于面对用工艺手段来弥补模具缺陷带来的问题而成效不大的困难局面。
生产过程中工艺的调节是提高制品质量和产量的必要途径。
由于注塑周期本身很短,如果工艺条件掌握不好,废品就会源源不绝。
在调整工艺时最好一次只改变一个条件,多观察几回,如果压力、温度、时间统统一起调的话,很易造成混乱和误解,出了问题也不知道是何道理。
调整工艺的措施、手段是多方面的。
例如:解决制品注不满的问题就有十多个可能的解决途径,要选择出解决问题症结的一、二个主要方案,才能真正解决问题。
此外,还应注意解决方案中的辨证关系。
比如:制品出现了凹陷,有时要提高料温,有时要降低料温;有时要增加料量,有时要减少料量。
要承认逆向措施的解决问题的可行性。
注塑机的工艺过程一般分为锁模、射胶、熔胶、保压、冷却、开模等几个阶段,各个阶段需要不同的工作压力和流量。
对于油泵马达而言,注塑过程是处于变化的负载状态。
在定量泵的液压系统中,油泵马达始终以恒定的转速提供恒定的流量,多余的液压油通过溢流阀回流,此过程称为高压节流。
据统计高压节流造成的能量损失高达25-60%。
同时,由于液压长期的全速循环流动,与液压件、机械件的剧烈磨擦,造成油温过高、噪音过大、机械寿命缩短的现象。
在注塑机工序一个完整的过程中,各种型号的注塑机,它的工序过程是相同的,大致是五个工序过程(见图1)。
从图1可知注塑机不同的工序过程中压力和时间是这样分布的:(1)送模具过程:压力低,时间较短。
(2)合模具过程:左右两个模具相接直至完全闭合,压力略高,时间不长。
(3)保压过程:送料至模腔,直到成型,固化。
压力较高,时间较长,约占一件产品制造时间的40—60%。
(4)脱模具过程:加工成型,开启模具,脱模,取出加工件。
压力略高,时间不长。
(5)退模具过程:加工件取出,模具后退原位,进行辅助工作后,待再次加工。
压力低,时间较短。
对同一台注塑机,加工不同的塑料件,其压力(P)与时间(t)长短是各不相同的。
由于加工件模具的复杂性,使用不同的塑料,一个加工件的总用料量,有否嵌件等有关。
具体参数设定,一般由工程技术人员经过测试后才能确定。
三.注塑机节能的原理及可行性分析1.理论原理油泵的输出功率:pt=p×Qt=p×v×n (1)油泵的理论转矩:Tt=1/2π×p×V (2)P为压力,Qt为流量,V为油泵排量,n为油泵的转速,将(2)式代入(1)式得:Pt=2π×Tt×n(3)如果忽略机械能到液压能转换过程中的能量损失,则可近似认为油泵的输出功率等于电机的输出转矩与电机转速的乘积。
因此可以看出,当系统要求低流量时,系统需要的功率其实是非常低的。
但是实际情况却是,由于电动机始终运行在工频50HZ状态上,并不能根据实际的需求来降低其转速,从而减小流量。
因此多余的液压油只能通过比例流量阀流回油箱,造成能源的白白浪费。
2、油泵变频调速节电运行从图1注塑机的P=f(t)工序过程中看出,在不同时间段,它的主油泵压力是变化的,而且起伏较大,这就存在节能的可能性,且潜力较大。
据统计,注塑机节电率一般可达25%-60%。
众所周知注塑机未使用变频器时,主泵的电动机始终恒速运行,是极不经济的运行的方式。
采用注塑机节电控制器,将控制比例流量阀的电流信号(0-1A),按每个生产工艺阶段设定的流量比例,得到0-1A的比例信电表去打开电磁阀的比例开度,以提供系统所需的压力。