PCBA设计要求
PCBA可制造设计规范
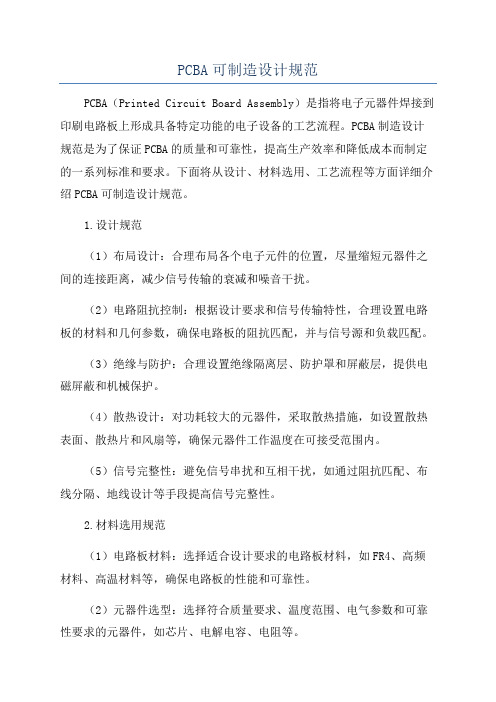
PCBA可制造设计规范PCBA(Printed Circuit Board Assembly)是指将电子元器件焊接到印刷电路板上形成具备特定功能的电子设备的工艺流程。
PCBA制造设计规范是为了保证PCBA的质量和可靠性,提高生产效率和降低成本而制定的一系列标准和要求。
下面将从设计、材料选用、工艺流程等方面详细介绍PCBA可制造设计规范。
1.设计规范(1)布局设计:合理布局各个电子元件的位置,尽量缩短元器件之间的连接距离,减少信号传输的衰减和噪音干扰。
(2)电路阻抗控制:根据设计要求和信号传输特性,合理设置电路板的材料和几何参数,确保电路板的阻抗匹配,并与信号源和负载匹配。
(3)绝缘与防护:合理设置绝缘隔离层、防护罩和屏蔽层,提供电磁屏蔽和机械保护。
(4)散热设计:对功耗较大的元器件,采取散热措施,如设置散热表面、散热片和风扇等,确保元器件工作温度在可接受范围内。
(5)信号完整性:避免信号串扰和互相干扰,如通过阻抗匹配、布线分隔、地线设计等手段提高信号完整性。
2.材料选用规范(1)电路板材料:选择适合设计要求的电路板材料,如FR4、高频材料、高温材料等,确保电路板的性能和可靠性。
(2)元器件选型:选择符合质量要求、温度范围、电气参数和可靠性要求的元器件,如芯片、电解电容、电阻等。
(3)焊接材料:选用适合工艺流程的焊接材料,如无铅焊料、焊膏等,确保焊接质量和可靠性。
3.工艺流程规范(1)印刷:确保PCB板材表面光洁、均匀,印刷厚度均匀一致,避免短路和偏厚现象。
(2)贴片:确保元器件与PCB板材精准对位,减少误差和偏离,避免虚焊、漏焊和偏焊。
(3)回流焊接:控制焊接温度和时间,确保焊点可靠性和焊接质量,避免过热和虚焊。
(4)清洗:清除焊接过程中产生的残留物,如焊膏、金属颗粒等,保证PCBA表面的干净和可靠性。
(5)测试与检验:进行全面的功能测试和质量检验,确保PCBA的功能和质量达到设计要求。
4.环境标准(1)温度和湿度:控制生产环境的温度和湿度,以确保PCBA的稳定性和可靠性。
PCBA可制造性设计

PCBA可制造性设计目录1.目的 (3)2.名词定义 (3)3.PCB设计要求 (3)4.元器件选用 (8)5.器件布局设计要求 (9)6.阻焊、丝印 (17)7.焊盘、焊孔及阻焊层的设计 (19)8.布线、焊盘与印制导线连接 (23)9.测试点的相关规定 (24)10.基准点(Fiducial Mark点) (24)11.拼板设计 (26)12.可装配性设计 (29)1. 目的从可制造性角度对PCB 的设计提出要求,供PCB layout 参考,同时用于指导新产品DFM (Design for manufacturability )评审。
设计无法满足此文档要求时,需经过生产工艺相关同事评估确认。
2. 名词定义Pcb layout :pcb 布局Solder mask :防焊膜面、防焊漆、防焊绿漆 Fiducial Mark :光学定位点或基准点 Via hole :导通孔 SMD :表面贴装器件 THC/THD :通孔插装器件 Mil :长度单位,1mil=0.0254mm3. PCB 设计要求3.1 PCB 外形PCB 外形(含工艺边)为矩形,单板或拼板的工艺边的四角须按半径R=2mm 圆形倒角。
应尽可能使板形长与宽之比为3:2或4:3,以便夹具夹持印制板。
3.2 印制板的可加工尺寸范围适用于全自动生产线的PCB 尺寸为最小长×宽:50mm ×50mm 、最大长×宽:610mm ×460mm 。
设计单板或拼板时,SMT 阶段允许使用最大拼板尺寸为610mm ×460mm ,PCB 单板尺寸较小时,建议拼板尺寸不大于210mm×210mm 。
3.3 传送方向的选择R=2mmPCB 传送方向工艺边为减少焊接时PCB 的变形,对不作拼板的PCB ,一般将其长边方向作为传送方向;对于拼板也应将拼板的长边方向作为传送方向。
但是对于短边与长边之比大于80%的PCB ,可以用短边传送。
PCBA制造质量标准(最)

PCBA制造质量标准(最)PCBA制造质量标准(最完整版)1. 引言本文档旨在规定PCBA(Printed Circuit Board Assembly,印刷电路板组装)制造的质量标准,以确保生产过程的可靠性和一致性。
本标准适用于PCBA制造的各个阶段,包括设计、材料采购、组装和测试。
通过遵循这些标准,可以提高产品质量、减少制造中的错误和缺陷,并满足客户的要求和期望。
2. 设计要求2.1 PCB设计应符合相关行业标准和规范,如IPC-2221、IPC-2222等。
2.2 PCB布线应合理,确保信号完整性和干扰抑制,避免信号串扰和电磁干扰。
3. 材料选择和采购3.1 PCB材料应符合相关规定,保证电气特性和机械强度的要求。
3.2 元器件应从可靠的供应商处采购,确保质量可靠、符合规格要求,并具备所需的认证和标志。
4. 组装工艺4.1 组装工艺应符合IPC-A-610E等相关标准,确保焊接质量和可靠性。
4.2 使用适当的工艺控制,如温度控制、焊接剂选择和焊接时间控制等,以确保焊接过程的一致性和可靠性。
4.3 组装过程中要保持工作环境卫生,防止污染和杂质的影响。
5. 测试和检验5.1 对PCBA进行功能测试,以确保其符合设计要求和功能规格。
5.2 对元器件进行质量检验,包括外观、尺寸、焊接质量等检查。
5.3 对组装后的PCBA进行可靠性测试,如高低温循环、湿热循环等。
6. 质量记录和跟踪6.1 记录PCBA制造过程的各个环节和参数,以便追溯和质量分析。
6.2 对不合格产品进行追溯和处理,确保问题的解决和防止类似问题再次发生。
7. 文件管理和保密7.1 对PCBA制造相关的文件进行合理分类、管理和保密,确保机密信息不被泄露。
7.2 对设计文件、生产记录和测试数据等进行备份和存档,以便需要时进行查阅和分析。
8. 环境、健康和安全8.1 在PCBA制造过程中,应遵守相关环境、健康和安全法规和标准。
8.2 采取必要的措施,确保员工的工作环境安全和健康,防止事故和职业病的发生。
可制造性需求规范AQ2A-05-R002

< 0.8mm
< 0.8mm
缩短贴片周期、减少短 路,提高直通率
BGA旁边加MARK 标识点
φ1.0mm,圆或方形
依照IPC-7351设 计
依照IPC-7351设计
缩短贴片周期、减少短 路,提高直通率 缩短贴片周期、减少短 路,提高直通率
依照IPC-7351设 计
缩短贴片周期、减少短 路,提高直通率
1.2mm
器件的重量
表贴器件最大重量≤
35g,元件重量与顶部可
吸附面积比小于0.600g/ ㎡.A=器件重量/引脚与 焊盘接触面积,片式器 件A≤0.075g/㎡,翼形引 脚器件A≤0.300g/㎡,J
器件重量符合要求, 利于自动贴片机的生 产,且保证焊接质量, 器件不易脱落。
形引脚器件A≤0.200g/
38
电容及信号接口接 地PAD
39
插件管脚过孔
40
功放IC
41
管脚PAD间距
42
单板可 制造性
43
单板可 制造性
Φ30-50mi
Φ30-50mi
≧ 0.1mm
≧ 0.1mm
缩短装配周期、减少装 配出错率。
缩短装配周期、减少装 配出错率。
按原理图标识重 要的测试点
缩短装配周期、减少装 配出错率。
≧ 5mm
≧ 5mm
≧ 2.0mm 清晰、不得印在 焊盘上 ≧ 5mm
缩短装配周期、减少装 配出错率。 缩短装配周期、减少装 配出错率。 缩短装配周期、减少装 配出错率。 缩短装配周期、减少装 配出错率。 缩短装配周期、减少装 配出错率。
≧ 5mm
缩短装配周期、减少装 配出错率。
椭圆形
椭圆形、泪滴型
产品可制造性通用设计规范-PCBA

产品可制造性通⽤设计规范-PCBA产品可制造性通⽤设计规范-SMT⽂件编号:⼀、PCB外框尺⼨要求:Y)=460mm 12.贴⽚设备最⼩可贴⽚的PCB尺⼨为:50×50mm⼆、PCB的厚度要求:1.可贴⽚最薄的PCB厚度为:0.3mm2.可贴⽚最厚的PCB厚度为:4.0mm三、PCB的线路层数:根据产品的需要,⾃由选择,不影响⽣产。
四、MARK点(基准点)的要求:MARK 点1、MARK 点的数量要求:(见上图)根据PCB 上的拼板数量的多少,来确认MARK 的数量,⼀般1块拼板需要2个以上且⼤⼩、形状⼀样的MARK 点。
拼板数量越多,MARK 点数越多。
2、MARK 点的⼤⼩要求:(见下图)d =1.0mm ,PCB 上的Mark 全部都⼀致;Mark 点周围⽆阻焊层的范围⼤于2mm 。
3、MARK 点的形状:(见上图)⼀般通⽤为圆形。
4、MARK 点的位置要求:MARK 点的位置距离PCB 边缘⾄少5mm 以上,以免机器轨道边夹住。
五、PCB 的拼板要求 1、拼板⽅式:⼀般的情况下,我们建议不要使⽤正、反⾯(即阴阳板)结合的⽅式,采⽤所有A ⾯在TOP边,所有B ⾯在bottom 边,这样不会造成⾼温焊接时,元件脱落的问题发⽣。
见下图:NG OK 推荐使⽤的拼板⽅式这种拼板⽅式容易出现元件脱落⽣产焊接时质量可靠 2、拼板的数量:根据实际拼板的⼤⼩,所有拼板加在⼀起时,不要超过贴⽚机的范围,最好在250mm ×250mm的范围内,⽣产时容易控制质量。
如上图的尺⼨要求。
六、PCB ⼯艺边1、PCB ⼯艺边的宽度要求:⼯艺边的宽度要求为3mm 以上;2、PCB ⼯艺边的数量要求:⼯艺边的数量要求⾄少有2条对称的边;3、PCB ⼯艺边的圆⾓设计:为了防⽌PCB 在机器内传送时出现卡板的现象,要求⼯艺边的⾓为圆弧形的倒⾓。
具体见图⽚:圆弧⾓设计⾄少有2条对称的⼯艺边六、焊盘上的过孔(通孔)要求4、元件的焊盘上不允许有通孔存在,否则容易导致⾼温焊接后,焊盘上少锡或者元件虚焊。
PCBA工艺设计规范

PCBA工艺设计规范PCBA(Printed Circuit Board Assembly,印刷电路板组装)是指将已经印制好的电路板上的元器件进行焊接和组装的过程。
PCBA工艺设计规范是制定PCBA工艺流程的一套规范文件,它包括了PCBA设计、焊接、组装、质量控制等方面的要求。
1.PCBA设计规范:-确定电路板尺寸和布局,保证安装的器件数量和尺寸的兼容性。
-设计适当的敷铜和敷焊膏区域,确保焊接质量和连接可靠性。
-合理选择元器件的布局,确保信号线和电源线的有效隔离,降低EMI(电磁干扰)。
-设计保护电路,如电源过压、过流、过热保护等,提高电路的可靠性和稳定性。
2.PCBA焊接规范:-选择适当的焊接技术,如表面贴装技术(SMT)和插件技术(THT)的结合。
-确定焊接方法,如波峰焊、回流焊等,并设置合适的焊接温度和时间。
-控制焊接过程的湿度和灰尘,使用防静电设备,避免静电引起的组装问题。
-做好元器件和焊点的对位和定位,确保焊接准确和稳定。
3.PCBA组装规范:-安装元器件时要遵循正确的顺序和位置,避免错误的插件和短路。
-严格控制焊锡量和焊接质量,避免过量或不足的焊锡引起的问题。
-设置适当的温度和时间,确保焊锡的熔化和固化,保证焊点的牢固性。
-接线、连接和固定要牢固可靠,避免松动和断连导致的电路故障。
4.PCBA质量控制规范:-制定合适的测试方法和测试标准,检测PCBA的性能和质量。
-进行严格的电气测试,包括电阻、电容、电感、短路、开路等参数测试。
-进行功能性测试,测试PCBA连接和元器件的工作状态和可靠性。
-进行环境适应性测试,模拟各种工作环境和应力条件,测试PCBA的稳定性和可靠性。
总之,PCBA工艺设计规范是指导PCBA工艺流程的一套规范文件,它包括了PCBA设计、焊接、组装、质量控制等方面的要求。
通过遵循PCBA 工艺设计规范,可以确保PCBA的焊接和组装质量,提高产品的可靠性和稳定性,降低故障率,满足客户的需求。
pcba应力防止设计 -回复

pcba应力防止设计-回复PCBA(Printed Circuit Board Assembly,印制电路板组装)的应力防止设计是为了保证电路板在使用过程中不会受到应力的破坏,从而提高产品的可靠性和寿命。
本文将从材料选择、设计布局、焊接工艺和产品测试等方面详细介绍PCBA应力防止设计的步骤。
1. 材料选择PCBA的材料选择对于应力防止设计至关重要。
首先要选择具有优良机械性能和热稳定性的材料,如高强度的玻璃纤维增强环氧树脂基板。
此外,要避免使用过硬或脆性材料,以防止应力集中和断裂。
2. 设计布局设计布局是PCBA应力防止设计的重要一环。
首先要合理安排组件和元件的位置,避免过于集中或过于分散,以减少应力的集中和热胀冷缩带来的应力。
其次,要尽量减小板面积,以降低热胀冷缩引起的应力。
同时,在布局时要避免热源与敏感元件的相近位置,防止温度引起的应力对元件的影响。
3. 焊接工艺焊接工艺对于应力防止设计同样至关重要。
应采用合适的焊接工艺,如波峰焊、热风热熔焊等。
同时,要注意控制焊接温度和时间,以防止过高的温度和过长的时间造成PCB板变形和元件的应力损伤。
此外,在焊接工艺中还要合理使用支撑物和限位工具,防止PCB板的弯曲和扭曲。
4. 产品测试产品测试是PCBA应力防止设计的最后一步,能够及时发现潜在的应力问题。
在测试过程中,可以采用视觉检查、X射线检测、热点检测等方法,对PCB板和焊接点进行全面检测。
同时,还可以进行振动测试和温度循环测试,模拟真实工作环境下的应力情况,以验证PCBA设计的可靠性。
综上所述,PCBA应力防止设计需要从材料选择、设计布局、焊接工艺和产品测试等多个方面进行综合考虑。
只有在每个环节都充分考虑应力问题,并采取适当的措施进行防止,才能保证PCBA的质量和可靠性。
这种设计方法不仅可以提高产品的性能和寿命,还可以降低故障率和维修成本,对于提高品牌形象和用户满意度具有重要意义。
PCBA-工艺设计规范

PCBA-工艺设计规范1. 引言本文档旨在规范PCBA(Printed Circuit Board Assembly,印刷电路板组装)的工艺设计,确保生产过程中的高质量和稳定性。
PCBA是电子产品制造中重要的环节之一,正确的工艺设计可以确保产品的可靠性、功能性和性能稳定性。
2. 设计要求在进行PCBA工艺设计时,需要满足以下要求:2.1 设计规范•PCB布线符合设计规范,遵循最佳布局原则,最短路径和最小电流回路原则;•PCB设计必须考虑信号完整性和抗干扰能力;•需要保留适当的物理空间,方便组装和维修。
2.2 硬件要求•PCB材料应符合相关标准要求,具有良好的导电性和绝缘性能;•PCB层数应根据实际需求来确定,同时考虑信号层和电源层的布局;•组件的选择要符合相关标准和规定,能够满足产品的功能需求。
2.3 工艺要求•PCBA整个生产过程应遵守相关工艺标准和规范,确保产品质量;•SMT(Surface Mount Technology,表面贴装技术)组装必须符合IPC(Association Connecting Electronics Industries)相关标准;•焊接工艺应确保焊点质量,防止焊接缺陷和冷焊等问题。
3. 设计流程PCBA的工艺设计流程如下:3.1 PCB设计•根据产品需求,制定PCB的尺寸、层数和布局;•完成原理图设计、布线和走线规划;•使用专业的PCB设计软件进行PCB布局和布线。
3.2 元器件选型•根据产品要求和性能需求,选取合适的元器件;•选择符合规范的供应商,确保元器件的可靠性和稳定性。
3.3 SMT组装•进行SMT贴片工艺流程,包括钢网制作、贴片、回焊等;•严格控制贴片工艺参数,确保元器件正确、牢固地焊接。
3.4 机械组装•将PCB组装到产品中,包括固定和连接电路板;•在组装过程中要注意防止静电、引脚弯曲等问题。
3.5 焊接和测试•进行焊接工艺,包括手工焊接和波峰焊接;•对焊接后的PCBA进行功能测试和质量检验,确保产品符合设计要求。
pcba制造工艺标准

pcba制造工艺标准
PCBA(Printed Circuit Board Assembly)制造工艺标准是一套关于PCB板生产和组装的规范和流程。
以下是一些常见的PCBA制造工艺标准:
1. 设计规范:这包括了PCB的设计规则,如线宽、线距、孔径、焊盘尺寸等。
这些规则是为了确保PCB的设计可以满足生产要求。
2. 制造流程:这包括了PCB的制造和组装流程。
例如,铜箔电镀、干膜成像、紫外激光雕刻、电镀钻孔、丝网印刷、热转印、波峰焊等。
3. 质量检测:这包括了PCB的质量检测标准和方法。
例如,视觉检测、显微镜检测、X射线检测、功能性测试等。
4. 环境要求:这包括了PCB制造和组装的环境要求。
例如,温度、湿度、空气净化等。
5. 安全要求:这包括了PCB的安全要求。
例如,防静电措施、防火措施等。
6. 可持续性:这包括了PCB的可持续性要求。
例如,环保材料的使用、能源效率等。
以上只是一部分常见的PCBA制造工艺标准,具体的工艺标准可能会根据不同的制造商和产品的具体要求有所不同。
pcba 散热设计原则

pcba 散热设计原则PCBA是印刷电路板组装的简称,其散热设计是保证电子设备正常运行的关键之一。
本文将从PCBA散热设计的原则出发,详细介绍如何有效地进行散热设计,以确保电子设备的稳定性和可靠性。
一、合理布局是基础PCBA上的元器件密度较高,合理的布局对于散热至关重要。
首先,需要将散热元件和发热元件合理分布在整个电路板上,以增加散热效果。
其次,要避免高功率元件相互靠近,应将它们分散开来,以减少热量的集中释放,从而降低温度。
二、选择合适的散热材料散热材料的选择直接影响着散热效果。
常见的散热材料有铜基板、铝基板和陶瓷基板等。
铜基板具有良好的导热性能,适用于大功率散热;铝基板重量轻,适用于小功率散热;陶瓷基板具有良好的绝缘性能,适用于高频电路的散热。
根据具体的应用需求选择合适的散热材料,以提高散热效果。
三、合理设计散热结构在PCBA的散热结构设计中,应注意以下几点。
首先,要合理设计散热片的形状和尺寸,以增加散热面积。
其次,要选择合适的散热风扇,以增加空气流通量。
此外,还可以考虑使用热管、热界面材料等辅助散热结构,以提高散热效果。
四、增加散热通道在PCBA的散热设计中,要合理增加散热通道,以增强空气对PCBA 的冷却效果。
可以通过设置散热孔、散热槽等方式,增加空气流通的路径,从而加速热量的传导和散发。
五、优化供电系统设计供电系统的设计也会影响PCBA的散热效果。
首先,要合理选择供电元件,避免过度发热。
其次,要优化供电电路,减少电流的损耗,以降低功率元件的温度。
此外,还可以采用分区供电的方式,将高功率元件和低功率元件分开供电,以减少热量的集中释放。
六、合理控制环境温度PCBA的散热效果还与环境温度密切相关。
在实际应用中,应合理控制PCBA所处的环境温度,避免过高或过低的温度对PCBA的散热造成不利影响。
可以通过合理的通风设计、温度控制系统等手段,提供稳定的工作环境。
七、定期检测和维护PCBA的散热设计不仅仅是一次性的工作,还需要定期检测和维护。
pcba外观 标准
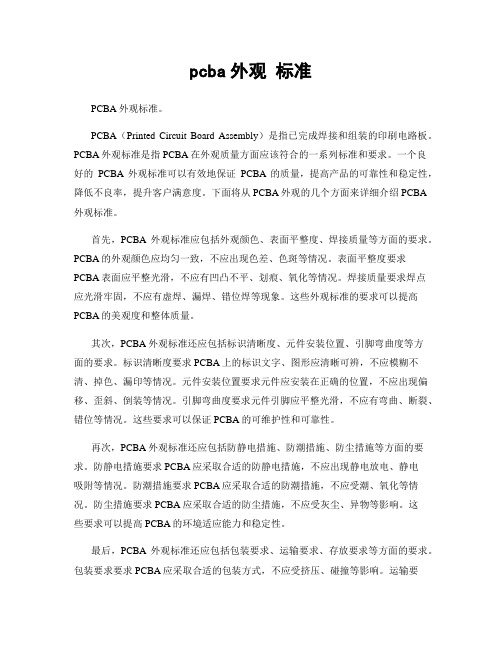
pcba外观标准PCBA外观标准。
PCBA(Printed Circuit Board Assembly)是指已完成焊接和组装的印刷电路板。
PCBA外观标准是指PCBA在外观质量方面应该符合的一系列标准和要求。
一个良好的PCBA外观标准可以有效地保证PCBA的质量,提高产品的可靠性和稳定性,降低不良率,提升客户满意度。
下面将从PCBA外观的几个方面来详细介绍PCBA 外观标准。
首先,PCBA外观标准应包括外观颜色、表面平整度、焊接质量等方面的要求。
PCBA的外观颜色应均匀一致,不应出现色差、色斑等情况。
表面平整度要求PCBA表面应平整光滑,不应有凹凸不平、划痕、氧化等情况。
焊接质量要求焊点应光滑牢固,不应有虚焊、漏焊、错位焊等现象。
这些外观标准的要求可以提高PCBA的美观度和整体质量。
其次,PCBA外观标准还应包括标识清晰度、元件安装位置、引脚弯曲度等方面的要求。
标识清晰度要求PCBA上的标识文字、图形应清晰可辨,不应模糊不清、掉色、漏印等情况。
元件安装位置要求元件应安装在正确的位置,不应出现偏移、歪斜、倒装等情况。
引脚弯曲度要求元件引脚应平整光滑,不应有弯曲、断裂、错位等情况。
这些要求可以保证PCBA的可维护性和可靠性。
再次,PCBA外观标准还应包括防静电措施、防潮措施、防尘措施等方面的要求。
防静电措施要求PCBA应采取合适的防静电措施,不应出现静电放电、静电吸附等情况。
防潮措施要求PCBA应采取合适的防潮措施,不应受潮、氧化等情况。
防尘措施要求PCBA应采取合适的防尘措施,不应受灰尘、异物等影响。
这些要求可以提高PCBA的环境适应能力和稳定性。
最后,PCBA外观标准还应包括包装要求、运输要求、存放要求等方面的要求。
包装要求要求PCBA应采取合适的包装方式,不应受挤压、碰撞等影响。
运输要求要求PCBA在运输过程中应采取合适的保护措施,不应受震动、摔落等影响。
存放要求要求PCBA在存放过程中应采取合适的保存方式,不应受潮、日晒等影响。
PCBA_工艺设计规范

PCBA_工艺设计规范PCBA(Printed Circuit Board Assembly,印刷电路板焊接)工艺设计规范是指在PCB装配过程中,对工艺过程和相关参数进行规定和约束的技术文档。
它是确保电子产品质量可靠性和一致性的重要保障。
一、厂房环境要求1.温度:工作环境温度应控制在25℃左右,温度波动不得超过±3℃。
2.湿度:相对湿度控制在45%~75%之间。
3.空气净化:要采取空气过滤设备,保持空气质量良好,控制灰尘粒子数量。
4.静电防护:采取静电防护措施,如地板导电材料、静电防护垫和接地电阻等,确保装配过程中防止静电的积累和释放。
二、贴片工艺规范1. 定位精度:贴片元件的定位精度应符合IPC-A-610标准,通常为±0.1mm。
2.焊接温度曲线:根据焊接材料和元件特性,制定相应的焊接温度曲线,确保焊接过程中温度的控制和适应不同元件的要求。
3. COB(Chip On Board)工艺:对于COB工艺,应控制好胶水剂量,保证芯片和PCB之间的紧密粘接,避免因胶水存在过多而引起的电气性能问题。
4.包装:对于贴片元件的包装材料和方法,应选择符合相关标准的防潮袋进行包装,以确保元件质量不受环境湿度的影响。
三、波峰焊工艺规范1.焊接温度:根据焊接材料和元件特性,制定相应的焊接温度曲线,控制焊接温度在合适的范围内。
2.波峰高度:根据PCB板的厚度和元件的焊盘高度,设置合适的波峰高度,确保焊接质量。
3.焊盘设计:根据元件的引脚结构和大小,合理设计焊盘的形状和尺寸,确保焊接时元件能够正确定位并与焊盘良好接触。
4.焊接时间:控制焊接时间,确保焊点能够充分熔化和润湿,并且避免因焊接时间过长而引起的元件损坏。
四、手工焊接工艺规范1.焊锡面积:手工焊接时,焊锡面积应符合IPC-A-610标准,确保焊点质量可靠。
2.焊接温度:控制手工焊接温度在合适的范围内,以避免过高温度对元件和PCB的损害。
3.焊锡量:手工焊接时,要控制好焊锡的量,确保焊点充分连接,避免过多或过少的焊锡对焊点可靠性的影响。
pcba加工工艺要求
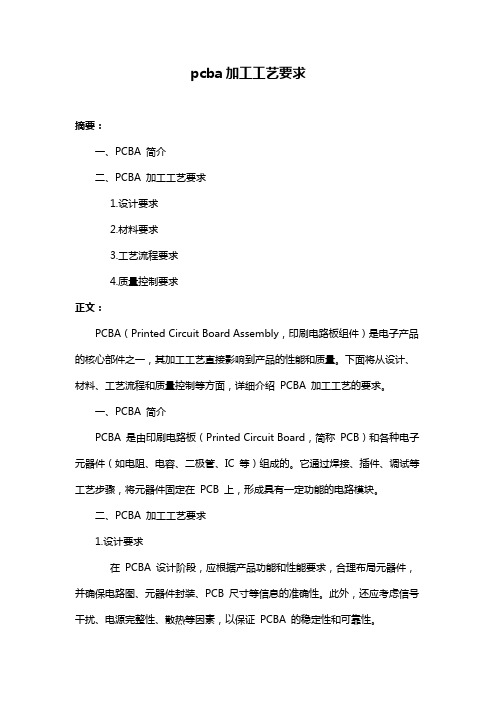
pcba加工工艺要求摘要:一、PCBA 简介二、PCBA 加工工艺要求1.设计要求2.材料要求3.工艺流程要求4.质量控制要求正文:PCBA(Printed Circuit Board Assembly,印刷电路板组件)是电子产品的核心部件之一,其加工工艺直接影响到产品的性能和质量。
下面将从设计、材料、工艺流程和质量控制等方面,详细介绍PCBA 加工工艺的要求。
一、PCBA 简介PCBA 是由印刷电路板(Printed Circuit Board,简称PCB)和各种电子元器件(如电阻、电容、二极管、IC 等)组成的。
它通过焊接、插件、调试等工艺步骤,将元器件固定在PCB 上,形成具有一定功能的电路模块。
二、PCBA 加工工艺要求1.设计要求在PCBA 设计阶段,应根据产品功能和性能要求,合理布局元器件,并确保电路图、元器件封装、PCB 尺寸等信息的准确性。
此外,还应考虑信号干扰、电源完整性、散热等因素,以保证PCBA 的稳定性和可靠性。
2.材料要求(1)PCB 材料:PCB 应选用符合标准的原材料,如FR-4、CEM-3 等,以保证其机械强度、电气性能和耐热性。
(2)元器件:元器件应选择符合国家标准的正品,并确保其型号、参数等信息与设计要求一致。
3.工艺流程要求(1)制板:根据设计文件制作PCB,并进行相应的工艺处理,如钻孔、镀铜、化学镍金、阻焊等。
(2)元器件加工:对元器件进行焊接、插件、清洗等处理,使其符合PCBA 组装要求。
(3)组装:将加工好的元器件按照设计要求组装到PCB 上,并进行焊接、固定、调试等操作。
(4)检验:对组装好的PCBA 进行外观、尺寸、性能等方面的检验,确保其质量符合要求。
4.质量控制要求(1)检验标准:参照国家相关标准和行业规范,对PCBA 的质量进行检验。
(2)检验方法:采用自动化或手动检验方法,对PCBA 进行全检或抽检。
(3)不合格品处理:对检验出的不合格品,应分析原因并采取相应措施进行整改,确保产品质量和性能。
PCBA Layout设计参考手册

一、PCB-LAYOUT 基本规范参考备注朝前垂输送带夹持边.输送带需)PAD 如最外则零件文字框依两 其文字框外缘以粗线标示在文字框的极性零件标示极性后文字框外缘不可互相接或邮票孔须距正上方平行板边的积L或邮票孔须距正上方垂直板边的积零件文字框外缘或邮票孔须距左右方平行板边的积零件文字框外缘或邮票孔须距左右方垂直板边的积零件文字框外缘邮票孔与周围突出板边零件的文字框须其跨越部份的的机构图必 TOOLING 于完成孔宽度Hole Y;W; Via 内必须盖绿并不能有锡珠残留在此区域的: :正面及背面零件面标示.二、锡偷 LAYOUT RULE 建议规范备注的最后一排零的角落朝后的位置ENG则锡偷的b)三、PCB LAYOUT 建议规范备注锡面测试点的边缘距过板前方的大铜箔距PAD mil)选 大绿漆成本垒板型VIA选用所用为零件脚截尺寸如右的游戏杆长方向与的摆设位置请勿摆与其余基材180过锡的大铜W此白框但不可被零件置件后压此文以利计算机其,用不同的喷锡样mil)25*25时不知道哪些机种故制造单位在生产时帮忙修改由技术中心机种光学点修由下.,附耳文字框长度50四、零件选用 建议规范6 mil. 其零件塑料顶部与10, 其零件塑料顶部正胶单位≧须有定位及两个防呆,须有一个定位防零件的零件脚左右偏移的位置度亦即左右偏移中心线各允许Connector五、零件包装建议规范六、光学点Layout 位置1. Index B 光学点距板边位置必要大于2. Index N 光学点距板边位置必要大于3. 不管新、旧机种, 对角线必须各有一个光学点, 其距离愈长愈好.4. 不管新、旧机种, 其对角线之光学点位置必须不对称.PCB 长边 PCB 短边SMT 进板方向 | a 1 - a 2 | ≧200 mil 或 | b 1 - b 2 | ≧200 milPCB 长边 PCB 短边 SMT 进板方向5.当机种变更版本时, 其对角线之一个或二个光学点位置必须挪动, 其间距(a i’, b I’)与前一版本(a i , b i)必须| a i-a i’ | ≧200 mil 或| b i-b i’ | ≧200 mil; 但若改版幅度不大时, 可在对角线光学点的其中一个旁标示直径100mil的白点, 白点位置随版本变化而改变, 以利辨别.。
PCBA 工艺设计规范
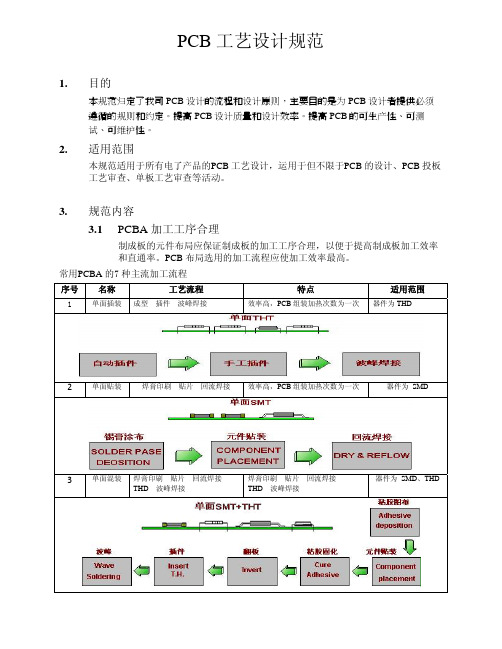
元器件种类的增多而导致SMT机器送料站位的不 够
阴阳板:将AB面的元器件分布在同一面板上。
家族式拼板的优势
阴阳板的劣势
减少了板的数量,有利于采购 减了WIP存货
增加了回流焊接难度 元器件种类的增多而导致SMT机器送料站位的不 够
) 减少了Tooling 成本为PCB制造 及SMT装配 制造周期缩短,也缩短的品质反馈周 期
3.3.1.2 基准点的类型 这里有两种类型,一种是“PCB 基准点”,另外一种根椐不同元器件的需要而设的“元件基准 点”
1)PCB 基准点 A. 对于单板的 Layout,建议使用三个基准点来作为角度、线性及非线性失真的补偿,如果 PCB 板的元件间距或脚间距有小于 50mil pitch 的就必须要使用三个基准点; B. 三个基准点位于 PCB 板上的三个角落位置; C. 在 PCB 长度及对角线的范围之内,三个基准点的距离应尽量最大.
3.2.6.3 若PCB 上有大面积开孔 >4mm 的地方,在设计时要先将孔补全,以避免波峰焊接时造成漫锡和 板变形,补全部分和原有的PCB 部分要以单边几点连接,在波峰焊后将之去掉(图18)
項 項目
次 1 一般 PCB 過板方向定義:
9 PCB 在 SMT 生產方向為短邊過迴 焊爐(Reflow), PCB 長邊為 SMT 輸 送帶夾持邊.
3. 规范内容
3.1 PCBA 加工工序合理
制成板的元件布局应保证制成板的加工工序合理,以便于提高制成板加工效率 和直通率。PCB 布局选用的加工流程应使加工效率最高。
常用PCBA 的7 种主流加工流程
序号 名称
工艺流程
特点
适用范围
1
单面插装 成型—插件—波峰焊接
pcba控制板 产品标准

PCBA控制板产品标准一、产品概述PCBA控制板作为电子产品的核心组成部分,承担着控制和管理整个系统的功能。
本文将对PCBA控制板产品的标准进行详细介绍,以确保产品的质量和可靠性。
二、外观要求1. 尺寸规格:PCBA控制板的尺寸需符合设计要求,并保证与整体设备的配套性;2. 材料颜色:PCBA控制板主要采用绿色阻焊油墨作为表面覆盖层,确保表面平整、光滑、一致性良好;3. 接口布局:PCBA控制板的接口布局应合理,易于连接和布线,并遵循相关标准;4. 标识标注:PCBA控制板应有清晰的产品标识、型号、生产日期等信息,并确保标识不易磨损。
三、电性能指标1. 工作电压:PCBA控制板的工作电压范围应符合设计要求,并能稳定工作在规定范围内;2. 电流负载能力:PCBA控制板应具备足够的电流负载能力,能够满足设备正常运行所需的电流要求;3. 信噪比:PCBA控制板在信号传输过程中应保持较低的信噪比,以确保信号的准确性和稳定性;4. 通讯速率:PCBA控制板的通讯速率应满足实际需求,并确保通讯稳定可靠。
四、功能要求1. 控制功能:PCBA控制板应具备精确的控制功能,能够准确完成系统指令的执行;2. 保护功能:PCBA控制板应具备多种保护功能,如过载保护、过热保护、短路保护等,以确保系统的安全运行;3. 扩展性能:PCBA控制板应具备一定的扩展性能,能够适应不同的扩展需求;4. 故障检测与诊断:PCBA控制板应能够自动检测故障,并给出相应的诊断信息,以提高故障排除的效率。
五、可靠性要求1. 耐高温性:PCBA控制板应具备良好的耐高温性能,能够在高温环境下长时间稳定工作;2. 抗震性:PCBA控制板应具备一定的抗震性能,能够在振动环境下正常工作;3. 防尘防水性:PCBA控制板应具备一定的防尘防水能力,以确保在复杂环境下正常工作;4. 寿命要求:PCBA控制板的设计寿命要求应符合行业标准,并能满足用户的实际需求。
pcba 方案

PCBA方案概述PCBA(Printed Circuit Board Assembly)是指将电子元器件焊接到印刷电路板上的过程,是电子产品制造的重要环节之一。
PCBA方案是根据产品需求设计出的针对特定PCB的工艺流程和工程文件,用于指导PCBA制造过程。
本文将介绍pcba方案的主要内容和流程,包括设计原则、节点定义、BOM清单、焊接工艺和测试流程等。
设计原则在制定PCBA方案时,需要遵循以下设计原则: 1. 确定PCB的尺寸和布局,使之满足产品的功能需求和外观要求。
2. 根据电路复杂性和功耗要求,选择合适的层数和线宽线距。
3. 选择适当的元器件包型和封装形式,使之便于焊接和维修。
4. 尽量减少电路板上的线路和元器件,以提高可靠性和减少成本。
节点定义PCBA方案中的节点定义是制定工艺流程的关键步骤之一。
在确定节点之前,需要分析产品的功能需求、重要性和难度,以合理安排工艺流程。
常见的节点定义包括以下几个方面: 1. 插件焊接:将插件元器件通过波峰焊或手工焊接到PCB上。
2. 表面贴装:将SMT元器件通过自动贴装机精确地贴装到PCB上。
3. 钢网印刷:使用钢网印刷机将焊膏均匀地印刷在PCB上。
4. 回流焊接:将装有元器件的PCB送入回流焊炉进行焊接。
5. 软硬件调试:对焊接完成的PCBA进行软硬件调试以验证功能是否正常。
BOM清单BOM(Bill of Materials)清单是PCBA方案中的必备文档,用于记录电子产品所需的所有部件和元器件,并提供准确的型号、规格和数量信息。
一个典型的BOM清单通常包含以下列项:- 序号:标识部件在清单中的序号。
- 部件名称:部件的通用名称或型号。
- 规格/描述:部件的规格说明或描述。
- 制造商:部件的制造商或供应商信息。
- 供应商:从哪个供应商购买该部件。
- 数量:需要采购或使用的部件数量。
- 单位成本:部件的单价。
- 备注:其他相关说明或特殊要求。
车规 pcba 防雷击要求

车规 pcba 防雷击要求
以下是车规 PCBA 防雷击要求的一些关键方面:
1. 接地设计:良好的接地设计是防止雷击损害的关键。
车规 PCBA 应采用多点接地,确保电流能够快速地通过接地系统导入地面,从而减少电路板上的电压差。
2. 过压保护:车规 PCBA 应配备适当的过压保护元件,如 TVS(Transient Voltage Suppressor,瞬态电压抑制器)、MOV(Metal Oxide Varistor,金属氧化物压敏电阻)等。
这些元件可以在雷击发生时快速响应,将过电压限制在安全范围内,保护电路板上的敏感元件。
3. 绝缘设计:车规 PCBA 中的电路应保持良好的绝缘性能,以防止雷击时电流泄漏或击穿。
电路板的布线应合理,避免高压线路与低压线路之间的交叉和干扰。
4. 电磁兼容性:车规 PCBA 应满足电磁兼容性要求,以减少雷击时产生的电磁干扰对其他电子设备的影响。
这包括合理的布线、屏蔽措施和滤波设计等。
5. 可靠性测试:车规 PCBA 在投入使用前应经过严格的可靠性测试,包括雷击模拟测试、静电放电测试等。
这些测试可以确保车规 PCBA 在恶劣的环境条件下能够正常工作,提高其抗雷击能力。
总之,车规 PCBA 的防雷击要求是非常严格的,需要在设计、制造和测试过程中充分考虑各种因素,以确保汽车电子系统在遭受雷击时能够保持正常运行,保障乘客的安全。
- 1、下载文档前请自行甄别文档内容的完整性,平台不提供额外的编辑、内容补充、找答案等附加服务。
- 2、"仅部分预览"的文档,不可在线预览部分如存在完整性等问题,可反馈申请退款(可完整预览的文档不适用该条件!)。
- 3、如文档侵犯您的权益,请联系客服反馈,我们会尽快为您处理(人工客服工作时间:9:00-18:30)。
深圳中宇元一数码科技有限公司A-MAX Technology(China) Ltd
PCBA设计要求
序
号
设计改善要求图示描述
1 咪头接地脚,USB接地脚,负极弹弓焊
盘都需要采用网孔连接大地,或其它方
法,因其接触面大,散热快,这样便于焊
接,提高生产效率。
(必须修改)
焊盘设计形状
如图2,3所示
2 耳插应改为DIP型,增强其附着力。
(建议修改)
3 若为贴片耳插,则需加大焊盘,另在焊盘中间增加贯穿孔,以增强其拉力和焊接可靠性;或者贴片耳插引脚翘起45度,PCBA在加锡时也可增强其附着力;在结构上骨位顶住耳插。
(必须修改)
4 侧面按键焊盘需加大,增强附着力。
(必须修改)
5 晶振尽量改用假贴片或贴片型,若不能用贴片,但需留有足够空间摆放,以免烫坏和压坏晶振。
(必须修改)
6 多彩LED焊盘间距应保持在3MM以上且周围尽量少有元件。
电池线焊盘距离应大于5mm
(必须修改)
7 芯片和FLASH不要在SD卡座下面,便于维修。
8 若以使用OLED旧机型应增加定位孔便于
啤机,提高生产效率.
(必须修改)
有定位孔定位
准确
9 CONT引脚与旁边的元件不能太近,便于维修。
(建议修改)
10 所有直经4.0咪头引脚改为2.0mm长度,
直经6.0咪头引脚改为2.5mm长度.
(建议修改)
来料长2.0mm
减少焊后要剪
脚时间
11 要求所有LED支架需有定位柱,防止LCD 显示斜。
(建议修改)
12 所有象收音5767封装IC,需在中间开有
焊盘,且焊盘面积需有9㎟以上,形状不
定,以增强其附着力,防止空焊和脱落
(增加焊盘必须修改,焊盘大小建议修改参数)
图1 图2
L ≥3mm
电池L≥5mm
L
旁边尽量少排元件
两端加定位孔
L=2.0mm
L
图4 NG 图5 OK
图3
图6
图7
图8
13 尽量不使用TAB OLED,用COF OLED或者其它替换.若使用TAB OLED需增加FPC或者是小板连接,导致重复多个工序,增加生产成本;若用COF OLED可以减少几个工序,直接连接在主板上,用Socket或者Hot Bar,或者是手工焊接。
(必须修改)
14 所有后焊元件焊盘周围尽量不要有元件,
便于员工操作提高生产效率。
(必须修改)
焊接件附近元
件越少越易焊
15 弹簧的选取及定型应尽可能用易稳定(可
贴板),圈数少易分离(负极弹簧)的才易
于作业,便于提高生产效率。
(建议修改)
间距大则易分
离,减少员工取
弹簧焊接时要
分开的时间
16 LCD框架设计尽可能可扣住LCD(不影
响装壳情况下);减去老是贴双面胶
纸(增加辅料及工时)及因胶纸粘不
牢过一段时间后LCD翘起造成LCD
黑点等不良(增加不良品)。
(建议修改)
可平贴PCB
圈数少间距
大,易分离
图9
图11
TAB
扣位
LCD
扣位
支架。