第九章高炉强化冶炼与新技术应用
高炉先进工艺技术

高炉先进工艺技术高炉是冶金工业中非常重要的设备,主要用于炼铁、炼钢和炼铬等过程。
随着科技的不断进步,高炉的先进工艺技术也得到了广泛的应用和发展。
本文将重点介绍几种高炉的先进工艺技术。
首先要介绍的是原料预处理技术。
传统的高炉通常使用矿石和焦炭作为主要原料,但是这些原料存在一些问题,例如矿石含有杂质较多,焦炭燃烧不完全等。
为了解决这些问题,采用了一系列的原料预处理技术,如矿石破碎、磁选和球团矿等。
通过这些技术,可以使原料更加纯净,提高高炉的炉渣质量和产量。
另一个重要的先进工艺技术是炼铁过程的自动化控制技术。
在传统的高炉操作中,需要大量的人工干预和调整,容易出现误差和浪费。
而通过自动化控制技术,可以实现对高炉内温度、压力和炉气成分等的实时监控和调节。
这不仅可以提高工作效率,减少人为错误,还可以保证产品的质量和一致性,降低能源的消耗。
此外,高炉炉渣处理技术也得到了很大的改进和创新。
传统的高炉炉渣通常需要通过人工清理,存在劳动强度大、占用大量时间和资源的问题。
而现在采用了一种叫做湿渣包工艺的技术。
通过在高炉煤气中注入水蒸汽,使炉渣迅速冷却、凝固并变形成固体状。
这样一来,炉渣可以迅速从高炉内部倾倒出来,从而避免了人工清理的过程。
最后还要提到高炉燃烧技术的先进改进。
在传统的高炉中,煤气是通过煤气倒灌的方式进行燃烧的,这样容易产生一些燃烧不完全的问题。
而采用了一种叫做高压煤气喷吹技术的方法,将煤气喷射到高炉内部的炉风中,使燃烧更加充分。
这不仅可以提高高炉的热效率,还可以减少环境污染物的排放。
总之,高炉的先进工艺技术在提高冶金工业生产效率、节约能源和保护环境等方面起到了非常重要的作用。
通过对原料预处理、自动化控制、炉渣处理和燃烧技术的不断改进,可以使高炉的生产过程更加高效、稳定和环保。
相信随着科技的不断进步,高炉的先进工艺技术还会不断地得到更新和发展。
高炉强化冶炼资料重点

是:燃烧产物煤气量增加;喷吹煤粉气
“高”指入炉矿石含 铁品位要高,焦炭、 烧结矿和球团矿强度 要高,烧结矿的碱度 要高。
王瑞祥
高炉炼铁知识9
6.2 精料
入炉矿含铁品位提高1%,炼铁燃料比降低 2%,产量提高3%,渣量减少30kg/t,允许 多喷煤15 kg/t。
原燃料转鼓强度要高。大高炉对原燃料 的质量要求是高于中小高炉。如宝钢要求 焦炭M40为大于88%,M10为小于6.5%,。
2020年10月28日星期三
王瑞祥
高炉炼铁知识2
6、高炉强化冶炼
在高炉冶炼的诸多矛盾中,炉料和煤气
的相向运动是主要的矛盾,炉料和煤气
的相向运动的存在和发展,影响着其他
矛盾的存在和发展,因此,处理好料和
煤气的矛盾,也就是要调整好料和风的
关系。实践证明,通过改善料柱透气性,
改善煤气流分布,从而降低料柱压差,
保证炉况顺行,是使此矛盾相统一的关
键。由此,普遍采用的高炉强化冶炼的
主要措施有:精料、高风温、富氧鼓风、
喷吹燃料、低硅生铁冶炼以及高寿命炉
衬等。 2020年10月28日星期三
王瑞祥
高炉炼铁知识3
6.1 提高冶炼强度
√
2020年10月28日星期三
王瑞祥
高炉炼铁知识4
6.1 提高冶炼强度
2020年10月28日星期三
王瑞祥
高炉炼铁知识26
6.5 喷吹燃料
2020年10月28日星期三
王瑞祥
高炉炼铁知识27
6.5 喷吹燃料
2020年10月28日星期三
王瑞祥
高炉炼铁知识28
6.5 喷吹燃料
2020年10月28日星期三
王瑞祥
高炉强化冶炼详解
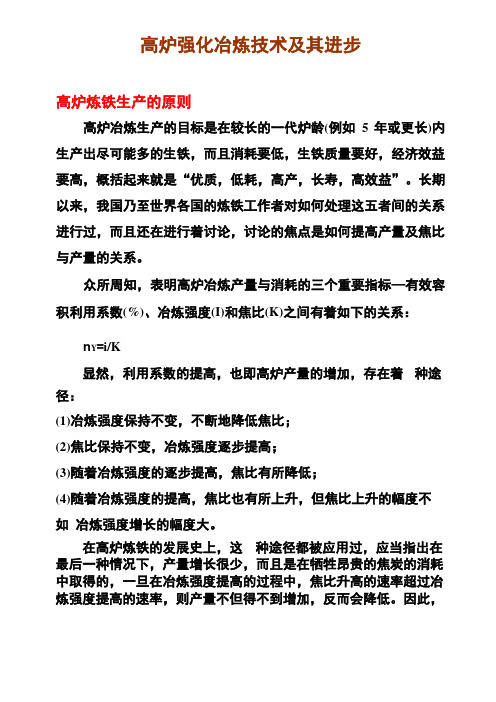
高炉强化冶炼技术及其进步高炉炼铁生产的原则高炉冶炼生产的目标是在较长的一代炉龄(例如5年或更长)内生产出尽可能多的生铁,而且消耗要低,生铁质量要好,经济效益要高,概括起来就是“优质,低耗,高产,长寿,高效益”。
长期以来,我国乃至世界各国的炼铁工作者对如何处理这五者间的关系进行过,而且还在进行着讨论,讨论的焦点是如何提高产量及焦比与产量的关系。
众所周知,表明高炉冶炼产量与消耗的三个重要指标—有效容积利用系数(%)、冶炼强度(I)和焦比(K)之间有着如下的关系:n Y=i/K显然,利用系数的提高,也即高炉产量的增加,存在着种途径:(1)冶炼强度保持不变,不断地降低焦比;(2)焦比保持不变,冶炼强度逐步提高;(3)随着冶炼强度的逐步提高,焦比有所降低;(4)随着冶炼强度的提高,焦比也有所上升,但焦比上升的幅度不如冶炼强度增长的幅度大。
在高炉炼铁的发展史上,这种途径都被应用过,应当指出在最后一种情况下,产量增长很少,而且是在牺牲昂贵的焦炭的消耗中取得的,一旦在冶炼强度提高的过程中,焦比升高的速率超过冶炼强度提高的速率,则产量不但得不到增加,反而会降低。
因此,冶炼强度对焦比的影响,成为高炉冶炼增产的关键。
在高炉冶炼的技术发展过程中,人们通过研究总结出冶炼强度与焦比的关系如图1所示。
图1冶炼强度与产量(I)和焦比(K)的关系美国资料,b 一原西德资料,一前苏联资料在一定的冶炼条件下,存在着一个与最低焦比相对应的最适宜的冶炼强度I适。
当冶炼强度低于或高于I适时,焦比将升高,而产量稍迟后,开始逐渐降低。
这种规律反映了高炉内煤气和炉料两流股间的复杂传热、传质现象。
在冶炼强度很低时,风量及相应产生的煤气量均小,流速低,动压头很小,造成煤气沿炉子截面分布极不均匀,表现为边缘气流过分发展,煤气与矿石不能很好地接触,结果煤气的热能和化学能不能得到充分利用,炉顶煤气中CO,含量低,温度高,而进入高温区的炉料因还原不充分,直接还原发展,消耗了大量宝贵的高温热量,因此焦比很高。
高炉冶炼的改进技术

稳定性,从而提高生铁产品的质量和性能。
铁水质量优化技术
02
通过控制高炉冶炼过程中的各种参数和条件,优化铁水的成分
和性能,提高产品的附加值和市场竞争力。
连铸连轧技术
03
采用连续铸造和轧制技术,提高产品的尺寸精度和表面质量,
满足用户对高质量产品的需求。
04
高炉冶炼改进技术的实施与效果
技术实施方案
优化高炉设计
01
传统高炉
传统高炉采用焦炭作为燃料,具 有较高的燃料消耗和较低的产量 。
02
03
大型化高炉
随着钢铁工业的发展,大型化高 炉逐渐成为主流,其具有更高的 生产效率和更低的成本。
04
02
高炉冶炼的当前问题与挑战
能源消耗与效率问题
总结词
高炉冶炼作为钢铁生产的主要方式,面临着能源消耗大、效率低的问题,亟需改进技术以降低能耗和提高效率 。
高炉冶炼的改进技术
汇报人:可编辑 2024-01-06
目录
• 高炉冶炼技术概述 • 高炉冶炼的当前问题与挑战 • 高炉冶炼的改进技术 • 高炉冶炼改进技术的实施与效果 • 高炉冶炼改进技术的未来展望
01
高炉冶炼技术概述
高炉冶炼的基本原理
还原反应
高炉冶炼通过还原反应将铁矿石中的铁元素 还原出来,通常使用焦炭作为还原剂,同时 需要鼓入大量空气进行燃烧提供热量。
绿色化发展
注重环保和可持续发展,推动 高炉冶炼技术的绿色化发展, 降低能耗和污染物排放。
循环经济
实现高炉冶炼废弃物的循环利 用,推动循环经济的发展,降 低资源消耗和环境负担。
推动高炉冶炼技术与新材料、 新能源等领域的跨界融合创新 ,拓展高炉冶炼技术的应用领 域和价值链。
高炉强化冶炼
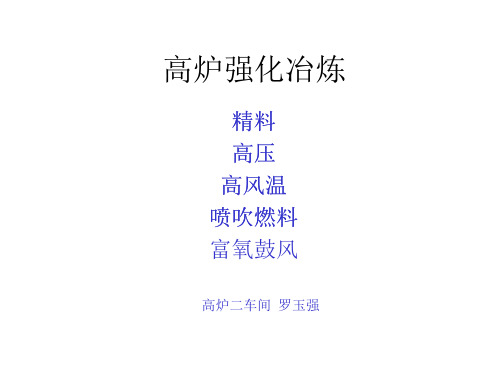
3.提高风温还可加快风口前焦炭的燃烧速度,提高T理,热 量更集中干炉缸,使高温区域下移,中温区域扩大,有利间 接还原发展,直接还原度rd降低。 4.风温的改变也是调剂炉况的重要手段之一。
高炉接受高风温的条件 凡是能降低炉缸燃烧温度和改善料柱透气性的措施,都 有利高炉接受高风温。 1.改善原燃料条件精料是高炉接受高风温的基本条件。只 有原料强度好,粒度组成均匀、粉未少,才能在高温条件下 保持顺行。 2.喷吹的燃料在风口前燃烧时分解、吸热,使理论燃烧温 度降低,高炉容易接受高风温。为了维持风口燃烧区域具有 足够的温度,需要提高风温进行补偿。 3.加湿鼓风时.因水分解吸热要降低理论燃烧温度,相应提 高风温进行热补偿。 4.搞好上下部调剂。保证高炉顺行的情况下才可提高风温。
• • • • • • • • •
(2)高还原性:低FeO、多气孔低温固结型烧结矿 FeO↓1%——K↓1.5%——产量↑1.5% (3)焦炭固定碳含量高:CS = 100 – A – V A↓——焦炭热值↑——渣量↓ (4)熔剂CaO含量高:CaO有效 = CaO – R×SiO2 (5)高强度:冷态强度——转鼓指数 热态强度——烧结矿低温还原粉化RDI 球团矿还原膨胀RSI 焦炭反应性↓ C + CO2 = CO
• (3) 煤气停留时间延长 • 提高炉顶压力,煤气在炉内停留时间延长,有利于还原反 应进行,也有利于焦比降低。 • (4) 有利稳定顺行 • 提高炉顶压力,由于压头损失降低,流速减慢,作用于炉 料的浮力也相应降低,炉料比较容易下降,因而有利于炉 况稳定顺行。 • (5) 除尘器瓦斯灰量减少 • 炉顶压力由常压转为0.08MPa时,炉尘量降了20%~50%, 现代高炉炉顶压力提高到 0.15 ~ 0.25MPa ,炉尘量常低于 10/kg/t。
高炉强化冶炼论文:钢铁企业中的高炉强化冶炼探讨
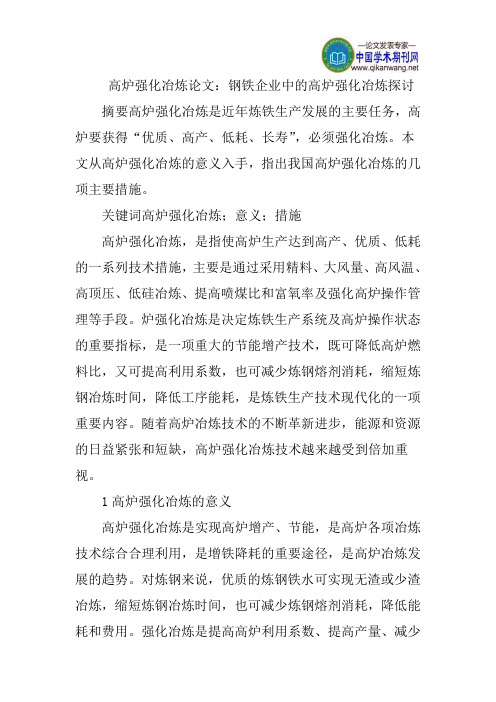
高炉强化冶炼论文:钢铁企业中的高炉强化冶炼探讨摘要高炉强化冶炼是近年炼铁生产发展的主要任务,高炉要获得“优质、高产、低耗、长寿”,必须强化冶炼。
本文从高炉强化冶炼的意义入手,指出我国高炉强化冶炼的几项主要措施。
关键词高炉强化冶炼;意义;措施高炉强化冶炼,是指使高炉生产达到高产、优质、低耗的一系列技术措施,主要是通过采用精料、大风量、高风温、高顶压、低硅冶炼、提高喷煤比和富氧率及强化高炉操作管理等手段。
炉强化冶炼是决定炼铁生产系统及高炉操作状态的重要指标,是一项重大的节能增产技术,既可降低高炉燃料比,又可提高利用系数,也可减少炼钢熔剂消耗,缩短炼钢冶炼时间,降低工序能耗,是炼铁生产技术现代化的一项重要内容。
随着高炉冶炼技术的不断革新进步,能源和资源的日益紧张和短缺,高炉强化冶炼技术越来越受到倍加重视。
1高炉强化冶炼的意义高炉强化冶炼是实现高炉增产、节能,是高炉各项冶炼技术综合合理利用,是增铁降耗的重要途径,是高炉冶炼发展的趋势。
对炼钢来说,优质的炼钢铁水可实现无渣或少渣冶炼,缩短炼钢冶炼时间,也可减少炼钢熔剂消耗,降低能耗和费用。
强化冶炼是提高高炉利用系数、提高产量、减少燃料消耗、降低生铁成本、降低工序能耗的重要因素。
同时,也是改善生铁质量的重要途径。
高炉强化冶炼技术的应用,利用系数的提高、焦比和生铁含硅量的降低是炼铁生产水平的一大进步,是炼铁操作技术的一个新水平,成为近年来引人注目的一项技术。
铁水是氧气顶吹转炉的主要金属料,占装入量的70 %-100 %,铁水的化学热与物理热是氧气顶吹转炉炼钢的主要热源。
铁水含硅量直接关系到转炉炼钢的经济技术指标,是铁钢系统平衡的关键。
随着炼钢技术的飞速发展和新技术的应用,炼钢生产的节奏越来越快,在原燃料供应和资源日趋紧张的条件下,铁前系统明显能力不足,为了进一步满足后续生产的需求,增产节焦,节能降耗,高炉强化冶炼是必然的发展趋势。
2我国高炉强化冶炼的主要措施最近10年来,国内外高炉强化冶炼技术有了新一的进展和突破。
高炉强化冶炼
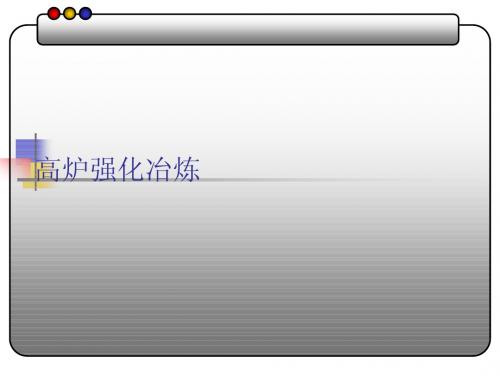
高炉强化冶炼
3、提高热风温度 、
提高热风温度是降低焦比和强化高炉冶炼的重要措施。 采用喷吹技术之后,使用高风温更为迫切。高风温能为提高 喷吹量和喷吹效率创造条件。据统计,风温在950~1350℃ 之间,每提高100 ℃可降低焦比8~20kg ,增加产量2~3%。 当前我国大高炉平均风温在1050~1100 ℃ ,先进高炉可 达1200 ℃,国外高炉风温水平达1300~1350 ℃,日本高炉 1200 1300 1350 的燃料比,1955~1979年间降低了 253kg/t,其中提高风温 的因素占31%。据资料,风温由1000℃提高到1250 ℃ ,焦 比降低22. 5kg/t,增产12.5%。 目前采用高风温已经不是高炉能否接受的问题,而是如何 能提供更高的风温。
“稳” 是指各种原料的化学成分稳定、波 高炉强化冶炼 动小。这是稳定炉况、实现自动控制的先 决条件。
“熟” 是指高炉全部装入烧结矿和球团矿, 熟料率达到100%,尽量不加石灰石入炉。 “小、匀、净” 是对原料的粒度而言。 综上所述,精料对矿石来说,关键是要使
高炉强化冶炼
2、高压操作
提高炉顶煤气压力的操作称为高压操作, 是相对于常压操作而言的。一般常压高 炉炉顶压力(表压)低于30kPa,凡炉顶压 力超过此值者,均为高压操作。它是通 过安装在高炉煤气除尘系统管道上的高 压调节阀组,改变煤气通道截面积,使 其比常压时为小,从而提高炉顶煤气压 力的。由于炉顶压力提高,高炉内部各
高炉强化冶炼
高压操作使炉尘吹出量显著减少, 单位矿石消耗降低,实际焦炭负荷得到 保证,批料出铁量增加,铁的回收率提 高,焦比应有所降低。实践证明,实行 高压操作,不断提高炉顶压力水平,是 强化高炉冶炼,增产节能的一条重要途 径。根据国内外经验,1000m3级高炉, 炉顶压力应达到120kPa左右;2000m3级 高炉,应达到150kPa以上; 3000m3级 高炉,应达到200kPa左右;4000m3级以
高炉炼铁工艺及强化操作

高炉炼铁工艺及强化操作高炉炼铁是指利用高炉将铁矿石还原成铁的工艺。
下面将介绍高炉炼铁的工艺流程和强化操作。
首先是炉料准备。
炉料是指进入高炉的原料,主要包括铁矿石、燃料和熔剂。
铁矿石是炼铁的主要原料,有各种类型,如富含铁的赤铁矿、磁铁矿等。
燃料主要是焦炭,用于提供炉内的热量。
熔剂主要是石灰石,用于与铁矿石中的杂质产生反应,形成易于熔融的铁渣。
然后是炉顶喂料。
炉顶喂料是将炉料逐层从高炉顶部加入,以保持炉内的物料平衡。
铁矿石、焦炭和石灰石按照一定比例加入到高炉顶部,同时还需要加入一定量的还原剂、燃料和助熔剂。
炉料从高炉顶部逐层往下加入,以确保炉内的物料层结构稳定。
然后是高炉操作。
高炉操作是指控制高炉正常运行的一系列操作。
首先是通风。
高炉顶部设有风管,通过风管送入燃料燃烧所需的氧气,维持炉内的高温。
其次是给料。
在正常运行过程中,需要不断地给炉料补料,保持高炉内的物料平衡。
还有是温度和压力的控制。
高炉内的温度和压力需要进行实时监测,以保持高炉内部的平衡状态。
接下来是铁渣处理。
高炉炼铁过程中,铁矿石中的杂质会与熔剂反应形成铁渣。
铁渣是高炉炼铁的副产物,需要进行处理。
铁渣处理主要包括根据铁渣的性质进行分选和利用。
铁渣中的铁石可以回收利用,用于生产水泥等建筑材料。
而其他杂质则需要通过石灰石的熔融和化学反应,形成不溶于炉渣的物质,进一步净化炉渣。
最后是产品收得。
通过高炉炼铁,最终产生的产品是生铁。
生铁是铁矿石还原后的产物,含有较高的碳含量和一些杂质。
生铁需要进行进一步的加工和处理,使其达到市场上的要求。
加工过程中,可以采用转炉炼钢或电炉炼钢技术,将生铁中的杂质进一步去除,得到优质的钢铁产品。
为了提高高炉炼铁的效率和质量,还有一些强化操作可以应用。
比如,在炉料准备过程中,可以根据铁矿石的性质进行选矿和破碎处理,以提高炉内的还原反应速率。
另外,可以在炉顶喂料过程中,适当控制喂料速度和炉料的层次,以保持高炉内的平衡状态。
高炉强化冶炼的手段 -回复

高炉强化冶炼的手段-回复高炉强化冶炼的手段是通过改进和优化高炉冶炼过程,提高炉内矿石的还原和熔化能力,提高产量和质量的一系列措施。
本文将详细介绍高炉强化冶炼的手段,并逐步回答相关问题。
一、高炉强化冶炼的背景和意义高炉是冶炼的核心设备之一,具有熔化矿石、还原金属氧化物、脱硫以及合金添加等多种功能。
强化冶炼手段旨在提高高炉的冶炼效率和产量,降低能耗和环境污染。
这对于钢铁工业的可持续发展和资源节约具有重要意义。
二、高炉强化冶炼的主要手段1. 提高炉料品位高炉强化冶炼的第一步是提高炉料品位。
通过选用高品位的矿石和燃料,减少杂质含量,可以提高高炉的冶炼效率和产量。
2. 优化炉料配比炉料配比是指矿石、焦炭和烧结矿在高炉中的加入比例。
通过合理的炉料配比,可以控制炉内反应的平衡,提高冶炼效果。
优化炉料配比需要根据炉料的化学成分、物理性质和炉渣特性进行科学的设计。
3. 改进炉渣配方炉渣是高炉冶炼过程中的重要组成部分,具有液相和固相两个组成部分。
通过改进炉渣配方,可以提高炉渣的脱硫和吸附能力,减少冶炼过程中的杂质含量。
4. 加强高炉控制高炉控制是高炉强化冶炼的重要环节。
通过采用先进的控制系统和自动化设备,可以实现对高炉冶炼过程的实时监测和精确控制,提高冶炼效率和产品质量。
5. 引入先进技术高炉强化冶炼的另一个重要手段是引入先进的技术和设备。
例如,通过喷吹装置引入高温燃烧气体,可以提高高炉的冶炼温度和热效率;通过炉内预处理,可以改变炉料的物相结构,提高冶炼效果。
三、高炉强化冶炼手段的优势和挑战1. 优势高炉强化冶炼手段可以提高冶炼效率和产量,降低能耗和环境污染。
这可以帮助钢铁企业提高竞争力,降低生产成本,实现可持续发展。
2. 挑战高炉强化冶炼手段的实施面临着技术和经济上的挑战。
从技术上讲,高炉是一个复杂的系统,受多种因素的影响,优化和改进手段需要综合考虑。
从经济上讲,高炉改造需要投入大量资金,并且可能需要长时间才能回收投资。
高炉强化冶炼的手段 -回复

高炉强化冶炼的手段-回复高炉强化冶炼是指通过技术手段和工艺改进,提高高炉的冶炼效率和产品质量的方法。
随着钢铁工业的不断发展,高炉强化冶炼成为提高生产效益的关键环节。
本文将从高炉炉缸结构、喷吹系统优化、配料技术改进和高炉操作方法优化四个方面进行讨论,一步一步回答高炉强化冶炼的手段。
一、改进高炉炉缸结构高炉炉缸是高炉内部最重要的部件之一,对冶炼过程起着至关重要的作用。
为了提高高炉的冶炼效果,可以通过改进高炉炉缸结构来优化冶炼环境。
1. 提高炉肩的强度和耐火材料质量:炉肩是高炉炉缸的上部,负责承受高炉内部冶炼压力和冶炼物料的侵蚀。
提高炉肩的强度和耐火材料质量,可以减少炉缸的磨损和炉缸壁的腐蚀。
2. 优化炉缸形状:改进高炉炉缸的形状,可以提高炉缸内的流动性和物料的混合程度。
例如,采用锥形炉缸可以增加物料和煤粉的混合速度,提高冶炼效果。
3. 设置降温装置:在高炉炉缸中适当设置降温装置,可以降低炉缸内的温度,减少冶炼过程中的烧损和能耗。
二、优化喷吹系统喷吹系统是高炉冶炼过程中供气和喷吹燃料、冶炼物料的关键设备,对高炉冶炼效率和质量起着重要作用。
为了提高喷吹系统的效率,可以进行以下优化:1. 改进喷吹煤粉粒度:煤粉是高炉冶炼过程中的主要燃料,煤粉的粒度对燃烧效果有着直接影响。
适当调整和控制煤粉的颗粒大小,可以提高煤粉的燃烧速度和燃烧效率。
2. 优化喷吹风速和角度:喷吹风速和角度的调整对物料的混合和煤粉的燃烧有着重要影响。
通过改变喷吹风口的结构和位置,调整喷吹风速和角度,可以提高冶炼反应的强度和均匀性。
3. 定期清理和维护喷吹系统:定期清理和维护喷吹系统是保证喷吹效果和正常运行的重要手段。
清理喷吹风口和喷吹管道的积灰和结焦物,可以减少堵塞和爆破的风险,提高喷吹效果和稳定性。
三、改进配料技术高炉焦炭、铁矿石和熔剂是高炉冶炼过程中的主要原料,通过改进配料技术可以提高冶炼效率和产品质量。
1. 优化焦炭配比:焦炭是高炉冶炼过程中的主要还原剂和热源,优化焦炭配比可以提高冶炼温度和还原效果。
炼铁高炉强化冶炼实践

炼铁高炉强化冶炼实践作者:任毅刚来源:《科学与财富》2019年第29期摘要:重钢股份根据钢材市场行情,决定对2座2500m3高炉,1座1750 m3高炉进行强化冶炼,提高产量,使高炉各项经济指标得到改善,高炉利用系数逐步提高。
关键词:高炉;强化冶炼;实践一、概况重钢股份1#高炉有效容积2500 m3,设有30个风口,无渣口,3个铁口,环形出铁场,3个铁口连续放铁方式,从投产以来2011—2015年期间因为原料紧张,钢材行情市场低迷,高炉压产,控制产量,冶炼强度偏低,消耗高。
2017年开始随着钢材市场行情好转,公司对生产的3座高炉逐步提产,强化高炉冶炼,各项经济技术指标大大改善。
下表是1#高炉2015年12月和1018年1月主要技术经济指标的比较詳表。
二、强化冶炼的措施1、实施精料方针,为高炉强化冶炼创造好条件1)改善烧结配比,优化烧结工艺,改善烧结矿质量,提高高炉入炉烧结矿的品位。
目前公司在制造部资源室专门有主管烧结矿配比的主管专家。
针对重钢烧结粉矿的品种多,来料复杂,成份波动大,冶金性能不稳定的特点,每天对成品烧结矿的强度,全铁,碱度进行实时跟踪,对影响烧结矿强度的因素及时作出调整,目前烧结矿的质量得到明显提高,为保证高炉长期稳定顺行提供保证。
烧结矿转鼓指数由75左右提升至目前77.5左右,烧结矿含铁品位由53.5%,提高到57.8%,1#高炉综合入炉矿品位从53.75%提高到57.9%。
2)加强高炉入炉原燃料的筛分工作为了减少粉矿入炉,因块矿粉末多,较湿,不容易筛透的特点,入炉块矿采取由物运部先期在料场第一次筛分,拉至高炉槽下进行第二次筛分,大大改善块矿的筛分效果。
3)提高焦炭质量,满足高炉强化冶炼的需要焦炭是高炉冶炼的重要燃料,随着高炉冶炼强度的不断提高,焦炭作为料柱骨架的作用越来越重要。
所以对焦炭的转鼓强度、热强度、反应性要求也越来越高。
公司专门成立配煤组,实时分析跟踪焦炭质量,采购优质洗煤,寻求最佳配煤比,加强焦化工序的工艺操作,焦炭质量明显改善。
高炉强化冶炼工艺
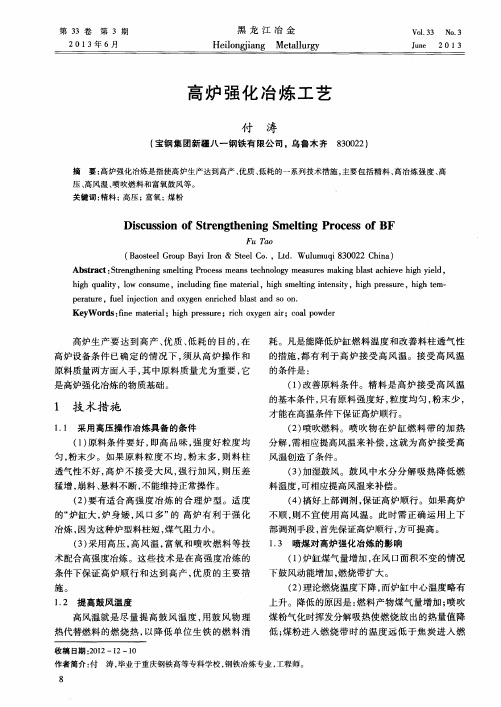
p e r a t u r e , f u e l i n j e c t i o n a n d o x y g e n e n i r c h e d b l a s t a n d S O o n .
Ke y Wo r d s : i f n e ma t e i r a l ;h i g h p r e s s u r e ;r i c h o x y g e n a i r ;c o a l p o w d e r
Ab s t r a c t : S t r e n g t h e n i n g s me l t i n g P r o c e s s me a n s t e c h n o l o g y me a s u r e s ma k i n g b l a s t a c h i e v e h i g h y i e l d,
高 炉生 产 要 达 到 高 产 、 优质 、 低 耗 的 目的 , 在 高 炉设备 条 件 已确 定 的情 况 下 , 须 从 高 炉 操 作 和 原料 质 量两方 面人手 , 其 中原 料质 量 尤 为 重要 , 它 是 高炉 强化 冶炼 的物 质基 础 。
耗。凡是能降低炉缸燃料温度和改善料柱透气性
的措施 , 都 有 利 于 高 炉 接 受 高 风 温 。接 受 高 风 温 的条件 是 :
( 1 ) 改善原料条件 。精料是高炉接受高 风温
的基本条 件 , 只有 原料 强度 好 , 粒度均匀 , 粉末 少 ,
1 技 术措 施
1 . 1 采用 高压操 作 冶炼具 备 的条 件 ( 1 ) 原料 条 件 要 好 , 即高 品 味 , 强 度好 粒度 均 匀, 粉 末少 。如 果 原 料 粒 度 不 均 , 粉末多 , 则 料 柱 透 气性 不好 , 高炉不接受大风 , 强行加风 , 则 压 差 猛增 , 崩料 、 悬 料 不断 , 不 能维持 正 常操作 。 ( 2 ) 要有 适合 高 强 度 冶 炼 的合 理 炉 型 。适 度 的“ 炉 缸大 , 炉身矮 , 风 口多 ” 的 高 炉有 利 于 强 化 冶炼 , 因 为这种 炉型料 柱 短 , 煤 气 阻力小 。 ( 3 ) 采 用高 压 , 高风温 , 富 氧 和 喷 吹 燃 料 等 技
高炉强化冶炼的措施和实践

高炉强化冶炼的措施和实践孙宝银(黑龙江西钢集团炼铁总厂)高炉强化冶炼是提高高炉效率的有效途径,优化高炉操作、实施精料方针、铁前工序系统挖潜等差不多上高炉强化冶炼的有效措施。
1 优化高炉操作1.1合理操作炉型合理操作炉型是高炉操作参数长期稳固的结果,是各种操作制度长期相对稳固而形成的炉型;合理的操作炉型反过来又会促使高炉炉况稳固顺行、高炉生产高效,为高炉强化冶炼提供有利条件;对此,高炉工作者应重视高炉的日常操作与爱护,系统考虑阻碍高炉操作的内外部条件,确定适宜的高炉生产节奏,在分析炉况波动时应以高炉操作炉型是否合理为重点,利用因果分析法来调剂高炉操作参数,使高炉操作参数适应高炉操作炉型的需求。
1.2适宜鼓风动能鼓风动能直截了当阻碍高炉炉缸的工作状态,适宜的鼓风动能能够保证煤气流初始分布相对合理,炉缸工作稳固活跃,渣铁性能良好;对此,高炉工作者应界定适宜的风速,合理的风口面积,稳固的风口回旋区,确定适宜的高炉炉腹煤气量指数,为高炉强化冶炼提供较为科学的依据。
1.3改进装料制度高炉强化冶炼后,送风参数需进行相应的调整,调整送风参数后必须改进相应的装料制度,以保证煤气流分布的相对合理稳固,防止显现局部煤气流过分进展,阻碍高炉冶炼的正常进程;对此,高炉工作者应积极探讨与实践各种装料制度对高炉炉况的阻碍,优化装料制度来适应高炉强化冶炼需求,确保高炉内煤气流分布合理、软熔带相对稳固,物料的物理变化和化学反应正常运行,提高高炉稳固顺行的周期。
1.4改善炉渣性能高炉炉渣的性能直截了当反映出高炉的热制度,炉渣温度、炉渣的流淌性、炉渣的色泽能够给高炉工作者的炉况判定提供依据,炼好铁必须先应炼好渣,炉渣变黑是炉缸工作不理想及炉凉的征兆;对此,高炉工作者应重视入炉料的成分操纵,对炉渣的四元碱度实时进行监控,通过及时调整高炉热制度等措施,在保证高炉脱硫的基础上,界定适宜的炉渣操作碱度,为炉况长期稳固顺行制造有利的条件。
1.5强化细节操作高炉强化冶炼、高效生产需要对高炉的各种操作制度制定细节化的治理考核细则,针对显在的和潜在的问题,采取有效的措施来加以操纵,对原料系统以时刻为轴线进行分仓入炉、交错振料,制定预防炉凉的警示,以稳固率为轴线对焦化工序、烧结工序、竖炉工序、选矿工序等的稳固率进行严格操纵,高炉操作应不断向细节化操作转变,强化高炉工作者的业务技能培训,以便提高高炉工作者对炉况的掌控和驾驭能力。
强化冶炼技术在涟钢7 #高炉的应用

( i y a rn& SeL G op C . La u nIo n t ru o, e
,L u 4 7 0 ,C ia o c 10 9 hn )  ̄
ABSI A CT: Th r ce s mma i e h n e sf d s l n r c c o b a tf r a e i . R e a t l u i rz s t e i t n i e me t g p a t e f r 7 l s u n c n i i i L a g n . a so t n t e e fn a a e n o i t v n f e d c n e t i n r w in a g By me n fsr g n d e m n g me t o o e u l e h i t n n a o tn - r a o
由于强化加强对烧结矿槽下筛分系统的管理通过冶炼的需要在保证高炉顺行前提条件下对对槽下筛筛面棒条等方面的改进和管理以及炉料结构作了优化配入高品位的南非块巴对筛分速度和料流量控制保证筛分效果
第3 9卷 第 3期
2 1 年 6月 01
金 属 材 料 与 冶 金 工 程
ME TAL M ATE AL RI S AND METALL URGY ENGI NEE NG RI
KEY ol S:lr e s e ls fr a e a maeil d fe ;o eai n W ag i db at u n c ;r w tra 1 p r t z n a u o
涟 钢 7 高 炉有 效 容 积 为 32 om3 目前 是 o , 湖 南 省 内最 大高 炉 。 于 2 0 0 9年 l 0月 7日点 火 开 炉 ,设 有 4个 铁 1 ,3 2 2个 风 口 。并 罐 式 无 料 1 钟 炉顶 ,3座卡 鲁金式 顶燃 式热 风 炉 ,干法 旋 风 煤 气 除 尘 ,烧 结 矿 分 级 入 炉 等 新 技 术 新 设 备 。 投 产 一 年来 。通 过 逐 步 提 高 人 炉原 料 质 量 ,逐
高炉强化冶炼

→煤气热能、化学能利用不充分
→焦比升高
I> I适时:煤气流速过大
中心过吹或管道行程
△P↑
炉况恶化→焦比↑
适宜冶炼强度和焦比的关系
I适是随冶炼条件的改善不断增大的
1
2
冶炼条件改善
3
焦
比
4
5
适宜的 冶炼强度
各类因素之间关系的分析
1) 产量和消耗之间的关系 2) 效益与产量、消耗之间的关系 3) 产量与高炉寿命、效益之间的关系 4) 产量与质量之间的关系
还原、软化熔融等。
散料堆中的粒度分布情况
炉料性质对布料的影响(A)
炉料的粒度
(不同粒度的混合料)
大块炉料易于滚落到堆角 由于堆角处料层薄,相对透气性好;
小块炉料则多集中在堆尖 由于堆尖处料层厚,相对透气性差。
高炉炉顶装料设备
料车- - 钟式
P·W- -无钟式
影响炉顶装料状况的因素
固定因素 a、布料设备参数 1、布料器形式 2、炉喉高度和直径 3、大钟与炉喉间隙 4、大钟倾角及速度 5、无钟炉顶参数 b、炉料特性
(一般:下部调剂的反应较快)
6.2 高炉操作制度
高炉四大操作制度
装料制度 送风制度 造渣制度 热制度
3) 造渣制度
★ 控制炉渣各种理化性能的总称
包括
熔化温度、粘度、炉渣成分、 熔化滴落区间、 脱硫性、排碱 性、表面性能等
控制造渣过程和终渣性能
6.2 高炉操作制度
高炉四大操作制度
装料制度 送风制度 造渣制度 热制度
高炉炼铁生产的原则
各类因素之间关系的分析
1) 产量和消耗之间的关系 2) 效益与产量、消耗之间的关系 3) 产量与高炉寿命、效益之间的关系 4) 产量与质量之间的关系
炼铁高炉冶金技术的应用
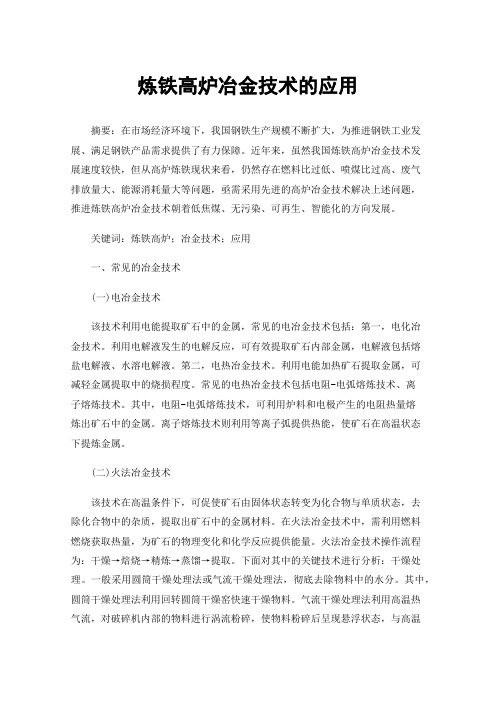
炼铁高炉冶金技术的应用摘要:在市场经济环境下,我国钢铁生产规模不断扩大,为推进钢铁工业发展、满足钢铁产品需求提供了有力保障。
近年来,虽然我国炼铁高炉冶金技术发展速度较快,但从高炉炼铁现状来看,仍然存在燃料比过低、喷煤比过高、废气排放量大、能源消耗量大等问题,亟需采用先进的高炉冶金技术解决上述问题,推进炼铁高炉冶金技术朝着低焦煤、无污染、可再生、智能化的方向发展。
关键词:炼铁高炉;冶金技术;应用一、常见的冶金技术(一)电冶金技术该技术利用电能提取矿石中的金属,常见的电冶金技术包括:第一,电化冶金技术。
利用电解液发生的电解反应,可有效提取矿石内部金属,电解液包括熔盐电解液、水溶电解液。
第二,电热冶金技术。
利用电能加热矿石提取金属,可减轻金属提取中的烧损程度。
常见的电热冶金技术包括电阻-电弧熔炼技术、离子熔炼技术。
其中,电阻-电弧熔炼技术,可利用炉料和电极产生的电阻热量熔炼出矿石中的金属。
离子熔炼技术则利用等离子弧提供热能,使矿石在高温状态下提炼金属。
(二)火法冶金技术该技术在高温条件下,可促使矿石由固体状态转变为化合物与单质状态,去除化合物中的杂质,提取出矿石中的金属材料。
在火法冶金技术中,需利用燃料燃烧获取热量,为矿石的物理变化和化学反应提供能量。
火法冶金技术操作流程为:干燥→焙烧→精炼→蒸馏→提取。
下面对其中的关键技术进行分析:干燥处理。
一般采用圆筒干燥处理法或气流干燥处理法,彻底去除物料中的水分。
其中,圆筒干燥处理法利用回转圆筒干燥窑快速干燥物料。
气流干燥处理法利用高温热气流,对破碎机内部的物料进行涡流粉碎,使物料粉碎后呈现悬浮状态,与高温气流充分接触,快速去除物料水分;焙烧处理。
焙烧技术包括氧化焙烧、盐化焙烧、还原焙烧、烧结处理等技术,在火法冶金技术的实际应用中,以氧化处理和还原处理技术应用最为广泛;精炼处理。
采用化学方法或物理方法去除矿石中的杂质,其中,化学方法为碱性反应、氧化反应等,物理方法为熔析方法、精馏方法等。
- 1、下载文档前请自行甄别文档内容的完整性,平台不提供额外的编辑、内容补充、找答案等附加服务。
- 2、"仅部分预览"的文档,不可在线预览部分如存在完整性等问题,可反馈申请退款(可完整预览的文档不适用该条件!)。
- 3、如文档侵犯您的权益,请联系客服反馈,我们会尽快为您处理(人工客服工作时间:9:00-18:30)。
• 2)当I达到一定值后,则随I的增加,煤气流速增大, 煤气在炉内停留时间减小,煤气能利用变差,焦比升 高。在不改善原料条件下,若I过高,则会导致压差明 显升高,引起高炉难行或悬料,破坏高炉顺行,焦比 升高。
相结合(高风温是提高喷吹量、提高喷吹效率的重要 措施);2)在无喷吹条件下,可采用加湿鼓风技术。
2020/9/1
12
• 第五节 喷吹燃料
2020/9/1
4
• 因此,在一定的冶炼条件下,有一个适宜的I 值 ,此 时风量与料柱透气性相适应,K较低,超过或低于这个 值,都会使K增加。因此应不断改善原料条件和冶炼条 件,提高操作水平,使适宜的I值向更高的方向发展, 以获得低的焦比和高的利用系数。
• 高炉强化冶炼的基本方针:以精料为基础,以节能为 中心,改善煤气能利用,选择适宜的冶炼强度,最大 限度地降低焦比和燃料比,有效地提高利用系数。
• 三、合理炉料结构
2020/9/1
6
• 第三节 高压操作
• 高压操作:提高炉顶煤气压力的操作。一般炉顶压力 超过0.03MPa均称为高压操作。它是通过安装在煤气除 尘系统管道上的高压阀组,改变煤气通道面积,从而 提高炉顶煤气压力。
• 高压操作是随着高炉大型化以及炉顶设备的改进而得 到实现和提高,是高炉强化冶炼的主要手段。
• 3、增加调剂炉况手段,为高炉大型化创造条件。
• 高压操作使燃烧带缩小,因此,高压应与大风量、大 喷吹等配合使用。同时,高压后,鼓风机动能消耗增 加,回收炉顶煤气剩余压力能对降低能耗、降低生铁 成本有重要意义。
2020/9/1
9
•
第四节 高风温
• 热风作用:是降低高炉焦比、增加产量的重要措施, 而且还有利增强炉渣脱硫能力,从而提高生铁质量、
第九章 高炉强化冶炼与新技术应用
• 第一节 高炉强化冶炼的方向 • 第二节 精料 • 第三节 高压操作 • 第四节 高风温 • 第五节 喷吹燃料 • 第六节 富氧鼓风 • 第七节 加湿鼓风与脱湿鼓风
2020/9/1
1
• 第一节 高炉强化冶炼的方向
• 高炉操作者的任务就是在给定条件下达到“高产、优 质、低耗、长寿”的目的。
补偿喷吹燃料和炉缸热量不足,以及稳定风口燃烧带 温度,为喷吹燃料创造有利条件。
• 风温水平:
• 风温水平与提高风温降低焦比的关系:
• 风温水平 -800 800-900 900-1000 +1000
• 降焦 % 4.0 3.5
3.0
2.0-2.5
•
(每提高100℃风温降焦幅度)
2020/9/1
10
• 一、提高风温对焦比影响
2020/9/1
2
• 从右图I与K的关系可以 看出:
• 1)在一定原料条件下, K先随I的提高而降低, 当I达到一定值后,K随I 的增加而增加,且存在 一个适宜的I,此时K最 低。
• 2)随着原料条件的改善, 适宜的I值提高而焦比K 随之降低。
图1 焦比与冶强的关系
2020/9/1
3
• 解释I与K的这种关系,要从顺行和炉内煤气能利用二 个方面来分析:
2020/9/1
8
• 2、焦比降低 • 1)高压操作改善了煤气流分布,促进炉况稳定顺行和
炉温稳定,降低煤气流速,煤气与矿石接触时间增加 等。
• 2)产量提高,单位生铁热损失减少。 • 3)压力提高,CO2+C=2CO反应开始温度提高,间接
还原区扩大。
• 4)高压不利SiO2等直接还原反应的进行,有利抑制Si 等的还原。
• 2、随风温提高,高炉热量利用系数随之增大。这是因为 鼓风带入的物理热直接作用于高炉高温区,热价值高于焦 炭燃烧放热。
• 3、风温提高,焦比降低,单位生铁煤气量减少,炉顶煤 气温度降低,炉顶煤气带走热量减少。
• 4、风温提高,高温区下移,间接还原区扩大。
• 5、风温提高,焦比降低,若I不变,则产量增加,单位生 铁热损失减少。
• 从提高高炉生产能力看,主要从三个方面:1)扩大炉 容;2)降低休风率;3)强化冶炼。
• 强化冶炼:在顺行基础上,使高炉在单位时间内能鼓 入更多的风量(氧量),提高冶炼强度,以便获得高 的利用系数和低的焦比。
• 从利用系数(ηV)与冶炼强度(I)和焦比(K)的关 系式: ηV=I/K 可以看出,要想提高ηV,一是要提高冶炼强度(I), 二是要降低焦比(K)。
• 目前高炉冶炼而言,rd 值偏高,碳素消耗取决于热量消耗 而非还原剂消耗,故风温提高,焦比降低。但如上所述, 随风温水平提高,提高风温降低焦比幅度减小,原因如下:
• 1、鼓风带入物理热替代部分焦炭燃烧放热,使焦比降低, 但随风温提高,焦比降低,单位生铁鼓风量减小,鼓风带 入物理热相对减小,故降低焦比幅度减小。
2020/9/1
11
• 二、提高风温对顺行影响 • 提高风温对高炉顺行有不利影响,这是因为: • 1、风温提高,高温区PSiO增大(SiO大量挥发),引起
料柱透气性变差,严重时会导致难行。
• 2、风温提高,燃烧带温度增加,煤气体积膨胀,引起 压差升高,对顺行不利。
• 三、接受高风温条件 • 1、精料 • 2、与其它技术措施配合使用:1)高风温与喷吹燃料
• 高炉强化冶炼主要采取措施:精料、高压、高风温、 富氧鼓风、大喷吹、脱湿鼓风和自动控制等。
2020/9/1
5
•
第二节 精料
• 精料是高炉强化冶炼的物质基础。
• 一、精料基本内容
• 基本内容;高、稳、熟、小、匀、净
• 高:
• 稳:•熟•Fra bibliotek小:• 匀:
•净
• 二、提高人造富矿的高温冶金性能——还原后强度、 还原性、软熔性
• 生产实践证明:炉顶压力提高0.01MPa,产量提高 2~3%,焦比降低0.5~1.0%。
• 高压操作现状:
• 高压操作作用:
• 1、强化冶炼作用
• 炉顶压力提高,炉内煤气体积减小,流速降低,压差 减小,有利提高冶炼强度,提高产量。
2020/9/1
7
图2 冶强与顶压的关系
图3 压差与顶压及冶强的关系