6108曲轴机械加工工艺浅析
YC6108ZQ柴油机球铁曲轴疲劳强度及圆角滚压.

YC6108ZQ柴油机球铁曲轴疲劳强度及圆角滚压曲轴是发动机中最重要的零部件之一,工作过程中受力情况非常复杂,工作破坏形式主要是疲劳断裂与磨损,所以,对曲轴疲劳强度的研究是目前曲轴设计研究的一个重要课题。
国内外文献对滚压工艺研究报导明显不足,导致国内厂家滚压工艺参数只能靠经验确定,多数国内厂家依靠进口设备原有的工艺参数,制约了滚压技术的更好应用。
本文对YC6108ZQ柴油机球墨铸铁曲轴滚压工艺强化进行了研究,分析了滚压工艺参数对曲轴疲劳强度的影响规律,为本球铁曲轴工艺参数的改进和优化提供了参考。
本文分析了YC6108ZQ柴油机曲轴各工况下的受力状况;计算了曲轴在各转速下圆角处的不同应力状态;通过试验研究了曲轴材料,包括硬度、强度、延伸率等参数对曲轴疲劳强度的影响规律;研究了曲轴圆角滚压各参数及曲轴圆角结构对曲轴疲强度的影响规律;对曲轴进行了相关的疲劳试验研究;给出了不同滚压力下的疲劳强度极限;得出了YC6108ZQ柴油机球铁曲轴不同疲劳极限值对应的一条最佳残余应力线,以及最佳滚压力值。
本文通过疲劳强度分析和疲劳试验,得到了材料性质和滚压工艺参数对疲劳强度的影响规律,一些结论,如滚压力的提高可在一定范围内可提高曲轴的疲劳强度极限等对实际曲轴的滚压强化生产具有一定的指导意义。
同主题文章[1].各国球墨铸铁标准' [J]. 现代制造工程. 1982.(01)[2].田长浒,陈滌輝,戢家齐. 钒钛球墨铸铁性能试验报告' [J]. 四川大学学报(工程科学版). 1982.(02)[3].白金元. 球墨铸铁拉伸凹模' [J]. 模具工业. 1983.(01)[4].温永泉. 曲轴弯曲疲劳试验的新方法' [J]. 内燃机学报. 1988.(01)[5].罗庆燎. 多种牌号球墨铸铁的生产' [J]. 航空制造技术. 1987.(06)[6].王金廷. 球墨铸铁井管通过鉴定' [J]. 地下水. 1986.(02)[7].郭占哲. 用圆角滚压加工提高曲轴强度' [J]. 车用发动机. 1991.(03)[8].李满良,冯美斌. 圆角滚压球铁曲轴在柴油机中的应用研究' [J]. 汽车工艺与材料. 2002.(Z1)[9].田长浒. 钒钛球墨铸铁耐磨性能的试验研究' [J]. 机械. 1984.(02)[10].铸态QT50—5球墨铸铁科研成果通过省级鉴定' [J]. 华东交通大学学报. 1987.(01)【关键词相关文档搜索】:机械工程; 曲轴; 球墨铸铁; 圆角滚压; 滚压力; 疲劳强度【作者相关信息搜索】:上海交通大学;机械工程;田中旭;蔚兴建;。
曲轴的机械加工工艺

曲轴的机械加工工艺
曲轴的机械加工工艺一般包括以下几个步骤:
1. 钢材修整:使用机械设备将原材料钢坯进行切割、锯割等操作,使得其与曲轴的设计尺寸接近。
同时,还需要进行热处理,使得钢材达到所需的力学性能。
2. 钢材粗加工:通过车床、铣床等机械设备,对钢材进行车削、铣削等操作,使其形成初步的几何轮廓。
3. 曲轴片的制造:将钢材分成若干段,每段分别进行车削、铣削等操作,使得每个曲轴片的几何形状和尺寸符合要求。
4. 吊挂:将曲轴片的上下端面加工成平行和垂直的状态,然后进行悬挂,使得曲轴片的主轴中心线和整体曲轴的主轴中心线重合。
5. 精加工:使用磨床等设备,对曲轴片进行磨削,使其达到设计要求的尺寸和表面粗糙度。
6. 装配:将精加工好的曲轴片进行组装,根据设计要求将各段曲轴片组合在一起,形成完整的曲轴。
7. 检测:对制造好的曲轴进行质量检测,包括尺寸精度、加工粗糙度、内外表
面质量等方面的检查,以确保曲轴符合设计要求。
8. 表面处理:对曲轴进行表面处理,包括防腐蚀处理、表面涂层等,以提高曲轴的耐用性和使用寿命。
以上是曲轴的一般机械加工工艺,具体步骤和操作方式可能会因不同的曲轴类型和加工要求而有所不同。
曲轴加工工艺流程简述
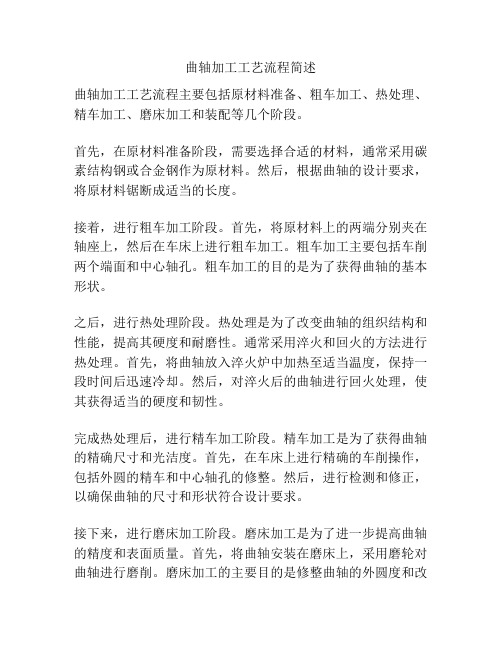
曲轴加工工艺流程简述曲轴加工工艺流程主要包括原材料准备、粗车加工、热处理、精车加工、磨床加工和装配等几个阶段。
首先,在原材料准备阶段,需要选择合适的材料,通常采用碳素结构钢或合金钢作为原材料。
然后,根据曲轴的设计要求,将原材料锯断成适当的长度。
接着,进行粗车加工阶段。
首先,将原材料上的两端分别夹在轴座上,然后在车床上进行粗车加工。
粗车加工主要包括车削两个端面和中心轴孔。
粗车加工的目的是为了获得曲轴的基本形状。
之后,进行热处理阶段。
热处理是为了改变曲轴的组织结构和性能,提高其硬度和耐磨性。
通常采用淬火和回火的方法进行热处理。
首先,将曲轴放入淬火炉中加热至适当温度,保持一段时间后迅速冷却。
然后,对淬火后的曲轴进行回火处理,使其获得适当的硬度和韧性。
完成热处理后,进行精车加工阶段。
精车加工是为了获得曲轴的精确尺寸和光洁度。
首先,在车床上进行精确的车削操作,包括外圆的精车和中心轴孔的修整。
然后,进行检测和修正,以确保曲轴的尺寸和形状符合设计要求。
接下来,进行磨床加工阶段。
磨床加工是为了进一步提高曲轴的精度和表面质量。
首先,将曲轴安装在磨床上,采用磨轮对曲轴进行磨削。
磨床加工的主要目的是修整曲轴的外圆度和改善其表面质量。
最后,进行装配阶段。
将其他零部件,如曲柄杆、连杆等组装到曲轴上,使之成为完整的曲轴装配件。
装配完成后,进行必要的检测和调整,确保曲轴的性能和工作可靠性。
以上就是曲轴加工工艺流程的简要描述。
曲轴的加工工艺复杂,需要经过多个步骤的加工和处理,才能获得高精度和高质量的曲轴产品。
曲轴加工工艺分析
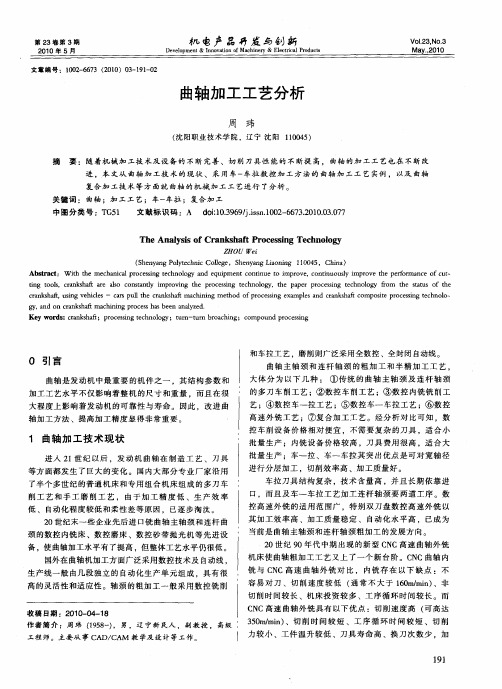
中 图分 类号 :T 5 G1
文 献标 识 码 :A d i O3 6 /.s.0 2 67 .0 00 . 7 o: .9 9ji n1 0 - 6 32 1 .30 l s 7
T eAn lsso a k h f r c sig Te h oo y h a y i fCr n s a P o e s c n lg t n
文章 编 号 : 10 — 6 3 (0 0 3 1 10 0 2 6 7 2 1 )0 - 9 - 2
曲轴 加工工艺分析
周 玮
( 阳 职 业 技 术 学 院 ,辽 宁 沈 阳 1 0 4 ) 沈 1 0 5
摘
要 :随 着机械 加 工技 术及 设 备 的 不断 完善 、切 削刀具 性 能的 不 断提 高 ,曲轴 的加 工 工艺 也在 不 断改
等 方 面都 发 生 了巨大 的变 化 。 国内大 部分 专 业厂 家沿 用 了半个 多世 纪 的普 通 机床 和专 用组 合 机床 组 成 的多 刀车
削工 艺 和 手 工 磨 削 工 艺 , 由于 加 工 精 度 低 、生 产 效 率 低 、 自动 化程 度较 低 和柔性 差 等原 因 ,已逐 步淘 汰 。 2 0世 纪末一 些企 业先 后进 口铣 曲轴 主轴 颈 和连杆 曲 颈 的数控 内铣 床 、数控 磨床 、数控 砂带 抛 光机 等 先进 设
第2 3卷 第 3期
2 1 0 0年 5月
D v lp n & In vt no ciey& Eetia rd cs eeo me t n oai f o Mahn r lcrcl o ut P
机 电产 品 开 发 与刨 新
V1 ,. o 3o .N3 2
May。01 . 2 0
c a s at i e ce rnk h f,us ng v hils— c r ult rn s a a h nn eho r esn x m pe n rn s atc m p iepr esn e h l— asp l hec a k h f m c i ig m t d ofp oc sig e a lsa d c a k h f o os oc sig t c noo t t
6108柴油机曲轴的优化设计毕业设计

6108柴油机曲轴的优化设计毕业设计1 绪论1.1柴油机的发展史和现状1.1.1柴油机的发展史德国狄赛尔(Rudolf Diesel)于1882年提出柴油机的工作原理,第一台四冲程柴油机在1896年制成。
一百多年来,柴油机技术的发展越来越全面,被应用的领域也越来越广泛。
大量的实验研究表明,柴油机是现在产业化应用动力机械中能量利用效率最高、热效率最高和最节能的机型。
柴油机广泛应用于发电、船舶动力、车辆动力、灌溉等领域,特别是在车辆动力方面,柴油机的优势最为明显。
车辆动力的“柴油化”趋势也越来越大。
日本、美国和欧洲100%的重型汽车用柴油机来提供动力。
欧洲33%的轿车和90%的商务车是柴油车。
美国有90%的商务车是柴油车。
而日本38%的商务车是柴油车,9.2%的轿车是柴油车。
随着技术的发展,柴油机将成为主流的车用动力。
柴油机越来越受欢迎是由于其相对于其他机型的优越性,其优越性主要有以下几点:1)大功率的柴油机,卓越的动力性能,压缩比通常为16至22,远高于汽油发动机的压缩比;汽油机功率一般为220千瓦,而通常柴油机功率为380KW,如果使用增压技术,柴油机功率可以得到进一步改善。
从燃烧的方式而言,柴油机燃料通过喷嘴直接喷入燃烧室内然后压缩点火燃烧,不会有提前点火爆燃异常燃烧;柴油机可燃混合物分层混合,这很容易实现稀薄燃烧和分层燃烧;部分负荷运行超过满载,并且没有进气节流损失,柴油机机的性能优于汽油机[1]。
2)柴油机的燃油经济性由于其燃烧方式不同使得它更优越。
一般汽油机的热效率为20~30%,但是柴油机的热效率却可以达到30~40%。
资料表明,以质量为0.8~1.5t 轿车的每百公里油耗为例:汽油机轿车约为5~8.2L,非直喷式柴油机轿车约为4.6~8L,直喷式柴油机轿车约为5~6L,柴油机轿车比汽油机轿车每百公里油耗低30%左右。
3)柴油机的耐久性好,工作可靠性强。
由于点火系统不复杂,避免了油和电路共存的麻烦。
轴的工艺设计分析

轴的工艺设计分析
轴是一种常见的机械零部件,用于传递力和转动运动,承载受力。
在进行轴的工艺设计分析时,需要考虑以下几个方面:
1. 材料选择:轴通常采用金属材料制作,如钢或铸铁等。
在选择材料时,需要考虑轴的工作环境、受力情况以及使用要求,以确保轴具有足够的强度和刚度。
2. 结构设计:轴的结构设计包括轴的直径、长度、圆角半径等参数的确定。
对于承受较大的转矩和受力的轴,通常会采用大直径和短长度的设计,以增加轴的强度和刚度。
3. 加工工艺:轴的加工工艺包括车、铣、镗、磨等工艺。
在进行加工时,需要根据轴的形状、精度要求和加工设备的能力等因素综合考虑,选择合适的加工工艺。
4. 热处理:轴通常需要进行热处理,以改善其机械性能。
常见的热处理方法包括淬火、正火、回火等,根据轴的材料和使用要求选择合适的热处理方法。
5. 表面处理:轴的表面通常需要进行处理,以提高其耐磨性和降低摩擦系数。
常见的表面处理方法包括镀铬、镀镍、喷涂等,根据轴的使用要求选择合适的表面处理方法。
6. 组装和调试:在轴的设计过程中,还需要考虑轴与其他零部件的配合和组装情况。
轴的设计要确保与其他零部件的配合尺寸合适,以保证整个机械系统的正常运行。
在完成轴的加工和表面处理后,还需要进行组装和调试,以确保轴的运转平稳、无杂音。
总之,轴的工艺设计分析需要考虑材料选择、结构设计、加工工艺、热处理、表面处理、组装和调试等多个方面,以确保轴具有良好的强度、刚度和耐磨性,满足机械系统的使用要求。
简谈6108气缸体加工生产线的优与劣
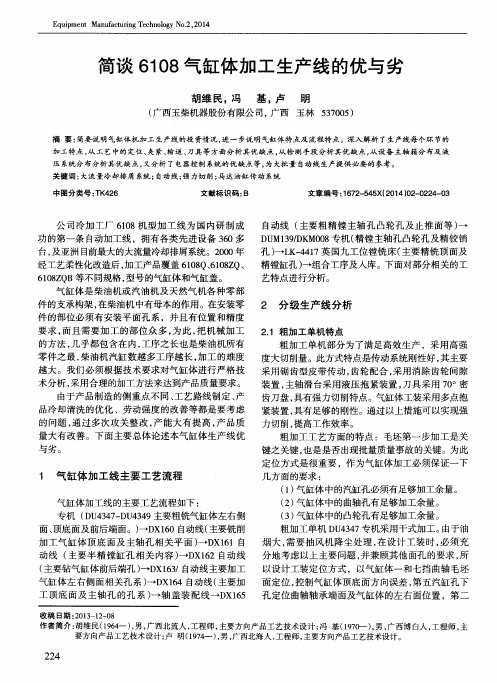
中图分类号 : T K 4 2 6
文献标识码 : B
文章编号 : 1 6 7 2 — 5 4 5 X ( 2 0 1 4 ) 0 2 — 0 2 2 4 — 0 3
公司冷加工厂 6 1 0 8 机型加工线 为国 内研制成 功 的第一条 自动加工线 ,拥有各类先进设备 3 6 0多 台, 及亚洲 目 前最大的大流量冷却排屑系统。2 0 0 0 年 经 工艺 柔性 化改造 后 , 加 工产 品覆 盖 6 1 0 8 Q、 6 1 0 8 Z Q、 6 1 0 8 Z Q B等不 同规格 , 型号的气缸体和气缸盖。 气缸体是 柴油机或汽油机及 天然气机各种零部
Eq u i p me n t Ma n u f a c t u r i n g T 2, 2 01 4
简谈 6 1 0 8气 缸体 加工 生产 线 的优 与劣
胡维 民 , 冯 基 , 卢 明
( 广西玉柴机器股份有限公 司, 广西 玉林 5 3 7 0 0 5 )
收 稿 日期 : 2 0 1 3 — 1 2 — 0 8
作者 简介 : 胡维 民( 1 9 6 4 一) , 男, 广西北 流人 , 工程师 , 主要 方向产 品工艺技术设 计 ; 冯 基( 1 9 7 o _ I ) , 男, 广西 博 白人 , 工程师 , 主 要方 向产 品工艺 技术设计 ; 卢 明( 1 9 7 4 一) , 男, 广西北海人 , 工程 师, 主要方 向产品工艺技术设计 。
摘 要: 简要说 明气缸 体机加 工生产线的投 资情况, 进一步说 明气缸体特 点及流程特点 。深入解析 了生产线每 个环 节的 加 工特点 , 从工艺 中的定位、 夹紧、 输送 、 刀具等方 面分析 其优缺点 , 从 检测手段 分析 其优 缺点 , 从设备 主轴箱分布及 液
曲轴加工工艺优化的分析与实施

曲轴加工工艺优化的分析与实施•核心提示:•针对不同曲轴的淬火涨量不一致,工艺参数控制不统一及检测手段受人为因素影响大的问题,天润曲轴有限公司试验论证了一种新的加工工艺——档心距加工工艺。
该工艺弥补了传统的以止推档侧面为定位基准的加工工艺缺陷,经过换产和大批量生产的验证,不仅大大提高了产品质量和效率,而且有效降低了不合格品率。
在金融危机的影响下,汽车市场竞争日趋激烈,汽车及零部件企业面临严峻的挑战,各大主机厂对曲轴的质量和精度要求越来越严格。
为了满足客户需求,我公司提出“以工艺为龙头”的指导方针,要求改进、优化曲轴加工工艺,进一步提升产品质量和效率,提高客户满意度。
通过对锻钢曲轴加工工艺进行整体优化试验,不仅取得了良好的效果,提高了锻钢曲轴的产品质量,同时还提高了生产线的产能,解决了产量与质量此消彼长的难题。
曲轴加工现状曲轴是发动机的关键零件之一,其结构复杂,生产批量大,品种更换频繁,精度要求高。
主轴连杆颈的尺寸精度为IT6~IT7,圆度≤0.005mm,表面粗糙度Ra0.2~0.4。
因此,一条先进的曲轴生产线不仅要实现柔性换产以面对市场需求,还要满足工艺要求,保证加工精度,最终生产出合格的产品。
锻钢曲轴生产线拥有世界顶级的数控机床、先进的加工工艺及日臻完善的管理制度,不仅大幅提升了曲轴的加工效率,实现了柔性快速换产能力,而且更好地保证了曲轴的加工质量。
当前,曲轴的质量主要通过机加工和热处理的过程控制来保证,其途径大致有以下三种:1. 人为检测:指通过专业质检人员(或操作人员自检、互检)对每道工序按照工艺要求进行在线测量,及时调整工艺参数,避免不合格产品周转到下道工序或出现批量废品。
2. 设备控制:指依靠较高设备精度保证当前工序的加工精度,是保证尺寸精度、形状精度和位置精度的有效方式,也是先进曲轴加工生产线的标志之一。
3. 工艺保障:工艺是机加工过程中将曲轴毛坯转化成成品的“法律”准绳,是产品质量的根本保证,也是提高加工效率的前提。
曲轴加工工艺
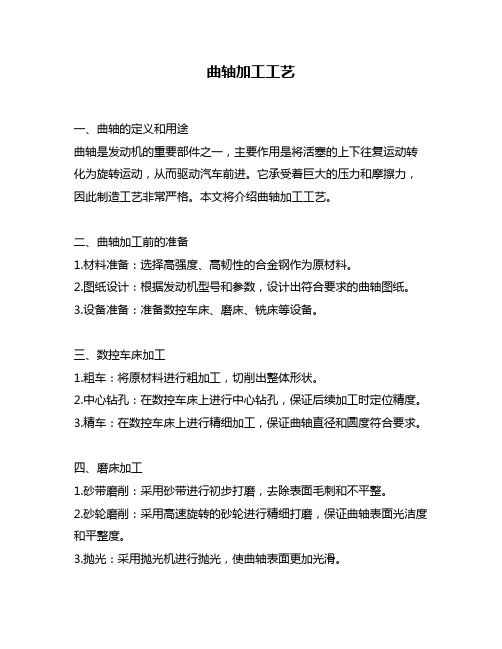
曲轴加工工艺一、曲轴的定义和用途曲轴是发动机的重要部件之一,主要作用是将活塞的上下往复运动转化为旋转运动,从而驱动汽车前进。
它承受着巨大的压力和摩擦力,因此制造工艺非常严格。
本文将介绍曲轴加工工艺。
二、曲轴加工前的准备1.材料准备:选择高强度、高韧性的合金钢作为原材料。
2.图纸设计:根据发动机型号和参数,设计出符合要求的曲轴图纸。
3.设备准备:准备数控车床、磨床、铣床等设备。
三、数控车床加工1.粗车:将原材料进行粗加工,切削出整体形状。
2.中心钻孔:在数控车床上进行中心钻孔,保证后续加工时定位精度。
3.精车:在数控车床上进行精细加工,保证曲轴直径和圆度符合要求。
四、磨床加工1.砂带磨削:采用砂带进行初步打磨,去除表面毛刺和不平整。
2.砂轮磨削:采用高速旋转的砂轮进行精细打磨,保证曲轴表面光洁度和平整度。
3.抛光:采用抛光机进行抛光,使曲轴表面更加光滑。
五、铣床加工1.铣槽:在铣床上对曲轴进行铣槽,以便安装汽缸连杆。
2.钻孔:在铣床上对曲轴进行钻孔,以便安装销子和油路。
六、渗碳处理将曲轴放入渗碳炉中,在高温高压下进行渗碳处理,增强曲轴表面硬度和耐磨性。
七、质量检测1.外观检测:检查曲轴表面是否平整、无裂纹、无气泡等缺陷。
2.尺寸检测:使用三坐标测量仪等设备对曲轴尺寸进行精确测量。
3.硬度检测:使用硬度计对曲轴硬度进行测试。
八、总结以上就是曲轴加工的详细流程。
为了保证曲轴的质量和使用寿命,每个环节都必须严格按照工艺要求进行操作。
只有这样,才能生产出符合要求的优质曲轴,为汽车行业的发展做出贡献。
曲轴零件的机械加工工艺及夹具设计概述

曲轴零件的机械加工工艺及夹具设计概述曲轴是一种常见的发动机零件,它是将活塞通过连杆和拐角转化为旋转力量的重要机械零件。
曲轴旋转时承受着很大的惯性力和工作负荷,要保证曲轴的精度和强度,必须对其进行高精度的机械加工和精心设计的夹具。
本文将对曲轴零件的机械加工工艺及夹具设计进行详细的概述。
一、曲轴零件的机械加工工艺曲轴的机械加工工艺一般有以下步骤:1、毛坯加工:根据设计图纸的要求,选择合适的毛坯材料进行切削加工,制成粗加工后的曲轴毛坯。
2、中心线定位:将曲轴毛坯放在加工中心,通过调整夹具和自动控制系统,确保曲轴旋转轴线与加工中心的旋转轴线一致,保证加工精度。
3、粗加工:采用车床、铣床等机床进行粗加工,主要是将毛坯外形和基准面加工到设计要求的尺寸、形状和位置精度。
4、回火处理:为了提高曲轴的强度和韧性,需要对粗加工后的曲轴进行回火处理,调整材料的组织结构。
5、精加工:采用高精度的数控车床、磨床等机床进行精加工,对曲轴进行外圆、内孔、轴承座和油孔等核心部件的细加工和研磨,使其达到设计和使用要求的加工精度和表面光洁度。
6、表面处理:为了保护曲轴表面和提高其装饰性和耐蚀性,可以在曲轴表面经过电镀、喷涂、镀铬等工艺处理。
二、曲轴零件的夹具设计曲轴是一种中空、复杂零件,加工时不仅要保证零件的精度和表面质量,还要考虑到加工过程中对曲轴的变形、热变形和工艺损伤等因素的影响。
因此,曲轴的夹具设计是影响曲轴加工精度和效率的关键因素之一。
根据曲轴零件的特点,夹具的设计应该遵循以下原则:1、夹紧稳定:夹紧力应均匀分布,避免在加工过程中产生不均匀的受力和变形,损伤曲轴表面。
2、可调性强:夹具应具有可调性,能够适应不同型号和规格的曲轴加工,保证加工精度,提高生产效率。
3、刚性高:夹具应具有高的刚性和稳定性,使曲轴在加工过程中不会产生颤振和爆炸危险,保证加工质量。
4、操作简便:夹具的操作应简单、方便,能够快速装夹和卸夹,提高生产效率。
曲轴加工的工艺浅析
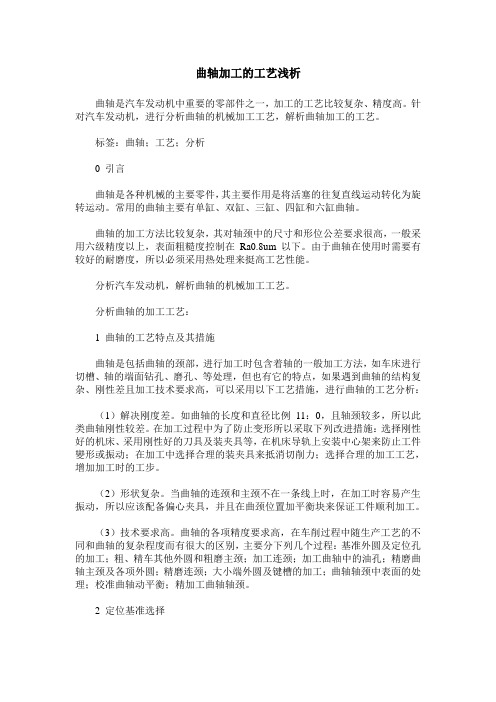
曲轴加工的工艺浅析曲轴是汽车发动机中重要的零部件之一,加工的工艺比较复杂、精度高。
针对汽车发动机,进行分析曲轴的机械加工工艺,解析曲轴加工的工艺。
标签:曲轴;工艺;分析0 引言曲轴是各种机械的主要零件,其主要作用是将活塞的往复直线运动转化为旋转运动。
常用的曲轴主要有单缸、双缸、三缸、四缸和六缸曲轴。
曲轴的加工方法比较复杂,其对轴颈中的尺寸和形位公差要求很高,一般采用六级精度以上,表面粗糙度控制在Ra0.8um以下。
由于曲轴在使用时需要有较好的耐磨度,所以必须采用热处理来挺高工艺性能。
分析汽车发动机,解析曲轴的机械加工工艺。
分析曲轴的加工工艺:1 曲轴的工艺特点及其措施曲轴是包括曲轴的颈部,进行加工时包含着轴的一般加工方法,如车床进行切槽、轴的端面钻孔、磨孔、等处理,但也有它的特点,如果遇到曲轴的结构复杂、刚性差且加工技术要求高,可以采用以下工艺措施,进行曲轴的工艺分析:(1)解决刚度差。
如曲轴的长度和直径比例11:0,且轴颈较多,所以此类曲轴刚性较差。
在加工过程中为了防止变形所以采取下列改进措施:选择刚性好的机床、采用刚性好的刀具及装夹具等,在机床导轨上安装中心架来防止工件變形或振动;在加工中选择合理的装夹具来抵消切削力;选择合理的加工工艺,增加加工时的工步。
(2)形状复杂。
当曲轴的连颈和主颈不在一条线上时,在加工时容易产生振动,所以应该配备偏心夹具,并且在曲颈位置加平衡块来保证工件顺利加工。
(3)技术要求高。
曲轴的各项精度要求高,在车削过程中随生产工艺的不同和曲轴的复杂程度而有很大的区别,主要分下列几个过程:基准外圆及定位孔的加工;粗、精车其他外圆和粗磨主颈;加工连颈;加工曲轴中的油孔;精磨曲轴主颈及各项外圆;精磨连颈;大小端外圆及键槽的加工;曲轴轴颈中表面的处理;校准曲轴动平衡;精加工曲轴轴颈。
2 定位基准选择(1)粗基准的选择。
装夹时保证中心孔与主颈毛坯外圆面的在同一轴线上,粗基准一般选择主颈的外圆。
曲轴的加工工艺过程
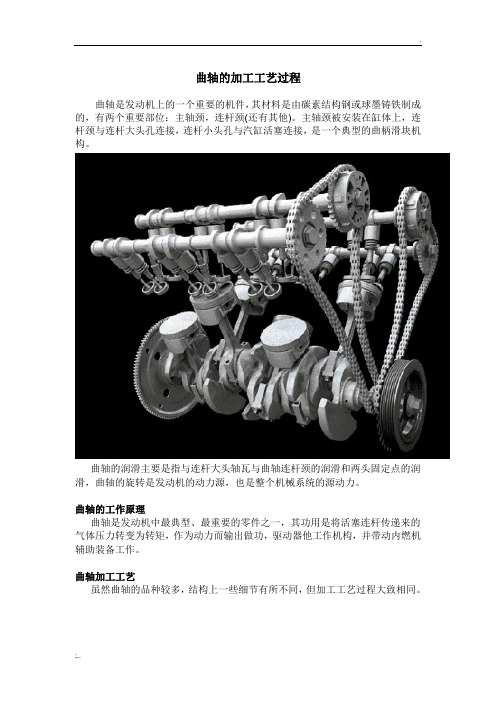
曲轴的加工工艺过程曲轴是发动机上的一个重要的机件,其材料是由碳素结构钢或球墨铸铁制成的,有两个重要部位:主轴颈,连杆颈(还有其他)。
主轴颈被安装在缸体上,连杆颈与连杆大头孔连接,连杆小头孔与汽缸活塞连接,是一个典型的曲柄滑块机构。
曲轴的润滑主要是指与连杆大头轴瓦与曲轴连杆颈的润滑和两头固定点的润滑,曲轴的旋转是发动机的动力源,也是整个机械系统的源动力。
曲轴的工作原理曲轴是发动机中最典型、最重要的零件之一,其功用是将活塞连杆传递来的气体压力转变为转矩,作为动力而输出做功,驱动器他工作机构,并带动内燃机辅助装备工作。
曲轴加工工艺虽然曲轴的品种较多,结构上一些细节有所不同,但加工工艺过程大致相同。
主要工艺介绍(1)曲轴主轴颈及连杆颈外铣加工在进行曲轴零件加工时,由于圆盘铣刀本身结构的影响,刀刃与工件始终是断续接触,有冲击。
因此,机床整个切削系统中控制了间隙环节,降低了加工过程中因运动间隙产生的振动,从而提高了加工精度和刀具的的使用寿命。
(2)曲轴主轴颈及连杆颈磨削跟踪磨削法是以主轴颈中心线为回转中心,一次装夹依次完成曲轴连杆颈的磨削加工(也可用于主轴颈磨削),磨削连杆轴颈的实现方式是通过CNC控制砂轮的进给和工件回转运动两轴联动,来完成曲轴加工进给。
跟踪磨削法采用一次装夹、在一台数控磨床上依次完成曲轴主轴颈和连杆颈的磨削加工,能有效地减少设备费用,降低加工成本,提高加工精度和生产效率。
(3)曲轴主轴颈、连杆颈圆角滚压机床应用滚压机床是为了提高曲轴的疲劳强度。
据统计资料表明,球墨铸铁曲轴经圆角滚压后的曲轴寿命可提高120%~230%;锻钢曲轴经圆角滚压后寿命可提高70%~130%。
滚压的旋转动力来源于曲轴的旋转,带动滚压头中的滚轮转动,而滚轮的压力是由油缸实施的。
发动机主要受力零件曲轴其疲劳破坏最常见的是金属疲劳破坏,即弯曲疲劳破坏和扭转疲劳破坏,前者的发生概率大于后者。
弯曲疲劳裂纹首先产生在连杆轴颈(曲柄销)或主轴颈圆角处,然后向曲柄臂发展。
YC6108Q曲轴双面磨削自动化磨床的设计与开发

烟台大学硕士学位论文YC6108Q曲轴双面磨削自动化磨床的设计与开发姓名:曲世金申请学位级别:硕士专业:机械制造及其自动化指导教师:方世杰20100401摘 要本文“YC6108Q曲轴双面磨削自动化磨床的设计与开发”,是受文登天润曲轴股份有限公司委托,制定针对曲轴双面磨削自动化磨床的总体设计方案并完成自动化磨床整体设计的应用项目。
本课题设计过程中,在充分考察调研基础上,查阅大量文献资料,综合运用机械设计、电控、机电一体化等多种理论技术,来解决实际问题。
在设计过程中,充分考虑到人的因素,不仅满足机械设计的基本功能要求,而且充分将人体工程学的设计理念应用其中,降低工人的劳动强度、改善工人的工作环境,充分体现新时代条件下“以人为本”的设计思想;同时,该课题研究成果可以为企业带来更大的经济效益,具有广阔的应用前景。
首先,结合企业的实际生产加工状况,提出曲轴双面磨削自动化磨床的整体设计方案。
其次,基于自动化磨床整体设计方案,分别完成刀具磨削工作系统的设计、工件进给系统的设计、夹具系统的设计以及电动机的选择。
本文根据磨削及机械设计原理,结合机电一体化知识,着重对上述三个系统功能模块开展创新性设计,按照三个系统功能模块的结构设计原理,对曲轴双面磨削自动化磨床的三个系统功能模块进行分析设计依据、论证设计方案、阐述设计过程;根据各系统功能模块的设计原理、企业的实际生产要求等多方面因素来确定部件的选择和参数的设定,例如步进电机,既要满足机械设计要求,又要方便电气设计时进行控制。
再次,基于Pro/Engineer设计软件完成自动化磨床在三维环境下,刀具磨削工作系统、工件进给系统、夹具系统的三维建模设计和自动化磨床整体虚拟装配。
最后,对曲轴双面磨削自动化磨床的整体设计进行深一步的说明,指出该自动化磨床具备一定的加工通用性,可以通过系统软件升级来完成YC6108Q型号曲轴的改进型或相近型及不同型号曲轴的磨削加工任务。
关键词:曲轴;双面磨削;自动化磨床;Pro/EngineerABSTRACTThis “The design and development of YC6108Q crankshaft double-sided grinding automatic grinding machine”, is subject to the text beyond the bounds Wendeng Tianrun Crankshaft Co., Ltd. was commissioned to both develop the overall design program of crankshaft double-sided grinding automatic grinding machine and complete the overall design of the automation grinder. This is a application project.In the design tasks of this topic, in the full investigation and study was based on access to a large number of literature, the integrated use of mechanical design, electric control, mechanical and electrical integration of a variety of theoretical techniques to solve practical problems. In the design process, fully taking into account the human factor, not only to meet the basic functions of mechanical design requirements and to fully integrate the application of ergonomic design concepts which reduce labor intensity and improve the working environment of workers to fully reflect the conditions of a new era under the “people-oriented” design ideas; the same time, the subject of research results can lead to greater economic benefits for the enterprise, has broad application prospects.First of all, combined with the actual production and processing enterprise situation and recommended the overall design of crankshaft double-sided grinding automatic grinding machine.Secondly, based on the overall design of automatic grinding machine program, to complete the work of system design tool, workpiece feed system design, fixture system design and motor choice. Based on the grinding and mechanical design principles, combined with knowledge of mechanical and electrical integration, focusing on these three systems function modules to carry out innovative design, functional modules in accordance with the structure of the three systems design principle of the automatic grinding machine crankshaft grinding three double-sided systems analysis and design based on functional modules, demonstration design, set design process; system function modules of the various design principles, the enterprise's actual production requirements, and other factors to determine the choice of components and parameters settings, such as stepper motors, it is necessary to meet mechanical design requirements, but also facilitate the design of electrical control.Again, based on Pro / Engineer design software to complete automation of grinding machine in three-dimensional environment, the tool system of work, the workpiece feed system, fixture design system, three-dimensional modeling and automation, grinding the whole virtual assembly.Finally, double-sided grinding crankshaft grinding machine automation of the overall design of deep-step instructions, pointing out that the automatic grinding machine with a certain degree of processing versatile, and can be accomplished through the system software upgrades improved version of the crankshaft YC6108Q model or similar type and different models of crank shaft the grinding task.Key words: crankshaft; double-sided grinding; automatic grinder; Pro / Engineer烟台大学学位论文原创性声明和使用授权说明原创性声明本人郑重声明:所呈交的学位论文,是本人在导师的指导下,独立进行研究工作所取得的成果。
6108曲轴机械加工工艺浅析

6108曲轴机械加工工艺浅析罗仁芝(湘潭职业技术学院,湖南湘谭 411102)摘要:曲轴是活塞式发动机的主要零部件之一,加工工艺复杂、要求高。
结合YC6105QC柴油发动机,深入分析了6108曲轴的机械加工工艺,并对曲轴机加工发展方向进行了初步探讨。
关键词:6108曲轴工艺工序分析中图分类号:TH162+.1 文献标识码:B 文章编号:1008-8415[2006] -01-0039-04一、引言曲轴是活塞式发动机的主要零部件之一,用来将活塞的往复运动转变为旋转运动。
根据发动机气缸的数目,曲轴一般分单缸、双缸、三缸、四缸和六缸曲轴。
如六缸发动机曲轴6108(见图1)有7个主颈和6个连颈,连颈分别位于三个互成120°角的平面内。
曲轴的加工工艺复杂,特别是轴颈有很高的尺寸和形位公差要求,一般按6级精度制造,粗糙度不高于Ra0.8μm。
轴颈表面需要热处理以提高其耐磨性,常用的热处理形式为氮化和高频淬火。
本曲轴的材料为QT850-3。
近年来,球墨铸铁和稀土球墨铸铁得到了广泛的运用,其特点为:可铸性好,有较高的强度和较小的缺口敏感性,有较好的减振性及耐磨性。
本文结合YC6105QC柴油发动机,主要对6108曲轴的机械加工工艺进行分析。
二、6108曲轴工艺分析主一连1主二连2主三连3主四连4主五连5主六连6主七图一 6108曲轴示意图图1 6108曲轴示意图(一)6108曲轴特点及工艺措施6108曲轴(见图1)是带有曲拐的轴,它仍具有轴的一般加工规律,如铣两端面、钻中心孔、车、磨及抛光等,但也有它的特点,包括形状复杂、刚度差及技术要求高,应采取相应的工艺措施,分析如下:1、刚度差6108曲轴的长径比较大(L/d=11),又具有6个连颈,因此刚度较差。
为防止变形,在加工过程中应当采取下列措施:选用有较高刚度的机床、刀具及夹具等,并用中心架来增强刚性,从而减少变形和振动;采用具有两边传动或中间传动的刚度高的机床来进行加工,可以减少扭转变形、弯曲变形和振动;在加工中尽量使切削力的作用互相抵消;合理安排工位顺序以减少加工变形;增设校直工序。
曲轴加工工艺流程

曲轴加工工艺流程曲轴是内燃机的重要零部件之一,它承受着发动机高速旋转时的巨大转矩,因此曲轴的加工工艺流程显得尤为重要。
下面将详细介绍曲轴加工的工艺流程。
首先,曲轴的加工从原材料的准备开始。
通常情况下,曲轴的原材料是优质的合金钢,这种材料具有较高的强度和硬度,能够满足曲轴在高速旋转时的要求。
在原材料准备阶段,需要对原材料进行质量检测,确保原材料符合加工要求。
接下来是曲轴的粗加工。
粗加工包括车削、铣削、钻削等工艺,通过这些工艺可以初步将原材料加工成曲轴的初步形状。
在粗加工过程中,需要严格控制加工尺寸和表面粗糙度,以确保后续加工的顺利进行。
然后是曲轴的热处理工艺。
热处理是提高曲轴强度和硬度的重要工艺环节,通过淬火、回火等热处理工艺,可以使曲轴具有良好的力学性能和耐磨性能。
接着是曲轴的精密加工。
精密加工是曲轴加工工艺流程中的关键环节,包括磨削、抛光等工艺。
通过精密加工,可以使曲轴的尺寸精度达到要求,并且提高曲轴的表面质量,减小表面粗糙度,提高曲轴的耐磨性能。
最后是曲轴的检测和组装。
在曲轴加工完成后,需要进行严格的检测,包括尺寸检测、硬度检测、表面质量检测等,确保曲轴的质量达到要求。
随后进行曲轴的组装,将曲轴与连杆、曲轴箱等零部件进行组装,组装完成后进行整体质量检测,确保曲轴的装配质量。
综上所述,曲轴的加工工艺流程包括原材料准备、粗加工、热处理、精密加工、检测和组装等环节,每个环节都至关重要,需要严格控制加工工艺,确保曲轴的质量和性能达到要求。
曲轴作为内燃机的关键零部件,其加工质量直接影响到发动机的性能和可靠性,因此曲轴加工工艺流程的重要性不言而喻。
曲轴加工工艺分析
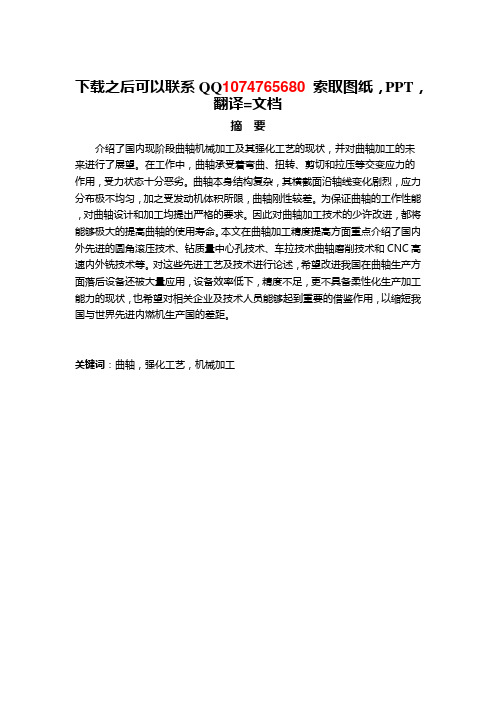
下载之后可以联系QQ1074765680索取图纸,PPT,翻译=文档摘要介绍了国内现阶段曲轴机械加工及其强化工艺的现状,并对曲轴加工的未来进行了展望。
在工作中,曲轴承受着弯曲、扭转、剪切和拉压等交变应力的作用,受力状态十分恶劣。
曲轴本身结构复杂,其横截面沿轴线变化剧烈,应力分布极不均匀,加之受发动机体积所限,曲轴刚性较差。
为保证曲轴的工作性能,对曲轴设计和加工均提出严格的要求。
因此对曲轴加工技术的少许改进,都将能够极大的提高曲轴的使用寿命。
本文在曲轴加工精度提高方面重点介绍了国内外先进的圆角滚压技术、钻质量中心孔技术、车拉技术曲轴磨削技术和CNC高速内外铣技术等。
对这些先进工艺及技术进行论述,希望改进我国在曲轴生产方面落后设备还被大量应用,设备效率低下,精度不足,更不具备柔性化生产加工能力的现状,也希望对相关企业及技术人员能够起到重要的借鉴作用,以缩短我国与世界先进内燃机生产国的差距。
关键词:曲轴,强化工艺,机械加工The Crankshaft Process AnalysisAbstractThe article the current situation of the machine consolidation of slider shaft in contemporary phase at home and abroad, and envision the future of shaft proceessing.During the operation it withstands the reversal stress and join forces from bending, reversing,shearing, andcompressing in adverse environment. Slider shaft is complicatedly structured and its cross section taode place so drastic changes along the Stem line that the allowable strss is uneqully distrbuted .what’s most.engine volume is V ery limitet,all of which lead to poor hardness and rigidity. To guarantee its working p Performance, strict requirments are placed on the designing and manufacturing So a li ttle improvement of machining techniques will dramatically raise its durability. As to improving its processing accuracy, this thesis emphasizes on the advancd foreign and domestic technology such as circular angle rolling ,quality-centered hole punching ,maching and strtching, shaft grinding and milling, and CNC-motivated high-speed milling ets. Though the abov statement and demonstration, it’s expected that our status quo can be change that backward device is still widly used with low woking effciency and inaccuracy, and lack of producing and processing flexibility .Besides this, important experrience and lesons can be drawn by correspondent enterprses and professionals to shorten the distans between advaned engine producers and our country.Key words: Crankshaft ; Strengthening Processes ; Mechanical processing1目录1 绪论 (23)2 曲轴加工工艺过程简述 (24)3 国内外曲轴加工技术现状 (27)3.1曲轴的强化工艺技术 (27)3.1.1 曲轴圆角的应力集中及解决途径 (28)(1)改进圆角结构 (28)(2)采用圆角强化工艺 (28)3.1.2 氮化处理 (32)3.1.3 喷丸处理 (32)3.2曲轴的机械加工技术 (33)3.2.1 加工质量中心孔技术 (33)3.2.2 曲轴车削技术 (34)3.2.3 数控内铣铣削工艺 (34)3.2.4 CNC高速外铣工艺 (35)3.2.5 曲轴车-拉工艺 (36)3.2.6 数控车-拉工艺 (36)3.2.7 曲轴油道孔加工枪钻工艺 (37)3.2.8 曲轴磨削工艺 (37)4 国内外曲轴加工技术展望 (38)5 结束语 (38)谢辞 (38)参考文献 (39)21 绪论不管在发达国家还是自发展中国家,机械制造业水平都是一国生产力的体现。
曲轴的机械加工分析
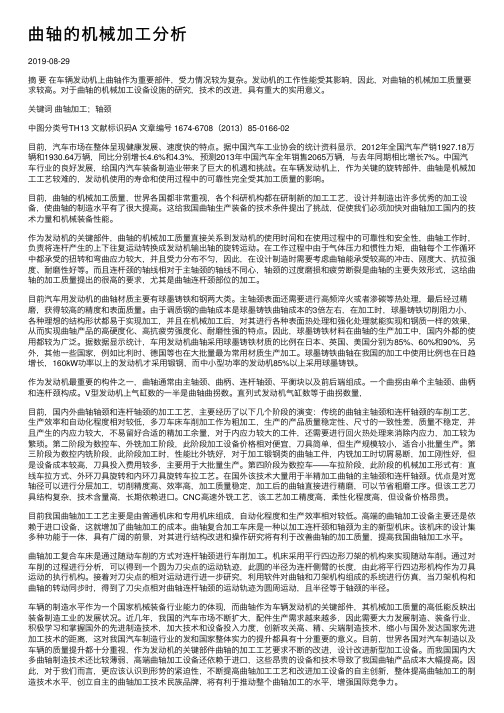
曲轴的机械加⼯分析2019-08-29摘要在车辆发动机上曲轴作为重要部件,受⼒情况较为复杂。
发动机的⼯作性能受其影响,因此,对曲轴的机械加⼯质量要求较⾼。
对于曲轴的机械加⼯设备设施的研究,技术的改进,具有重⼤的实⽤意义。
关键词曲轴加⼯;轴颈中图分类号TH13 ⽂献标识码A ⽂章编号 1674-6708(2013)85-0166-02⽬前,汽车市场在整体呈现健康发展、速度快的特点。
据中国汽车⼯业协会的统计资料显⽰,2012年全国汽车产销1927.18万辆和1930.64万辆,同⽐分别增长4.6%和4.3%,预测2013年中国汽车全年销售2065万辆,与去年同期相⽐增长7%。
中国汽车⾏业的良好发展,给国内汽车装备制造业带来了巨⼤的机遇和挑战。
在车辆发动机上,作为关键的旋转部件,曲轴是机械加⼯⼯艺较难的,发动机使⽤的寿命和使⽤过程中的可靠性完全受其加⼯质量的影响。
⽬前,曲轴的机械加⼯质量,世界各国都⾮常重视,各个科研机构都在研制新的加⼯⼯艺,设计并制造出许多优秀的加⼯设备,使曲轴的制造⽔平有了很⼤提⾼。
这给我国曲轴⽣产装备的技术条件提出了挑战,促使我们必须加快对曲轴加⼯国内的技术⼒量和机械装备性能。
作为发动机的关键部件,曲轴的机械加⼯质量直接关系到发动机的使⽤时间和在使⽤过程中的可靠性和安全性,曲轴⼯作时,负责将连杆产⽣的上下往复运动转换成发动机输出轴的旋转运动。
在⼯作过程中由于⽓体压⼒和惯性⼒矩,曲轴每个⼯作循环中都承受的扭转和弯曲应⼒较⼤,并且受⼒分布不匀,因此,在设计制造时需要考虑曲轴能承受较⾼的冲击、刚度⼤、抗拉强度、耐磨性好等。
⽽且连杆颈的轴线相对于主轴颈的轴线不同⼼,轴颈的过度磨损和疲劳断裂是曲轴的主要失效形式,这给曲轴的加⼯质量提出的很⾼的要求,尤其是曲轴连杆颈部位的加⼯。
⽬前汽车⽤发动机的曲轴材质主要有球墨铸铁和钢两⼤类。
主轴颈表⾯还需要进⾏⾼频淬⽕或者渗碳等热处理,最后经过精磨,获得较⾼的精度和表⾯质量。
发动机曲轴机加工工艺浅析
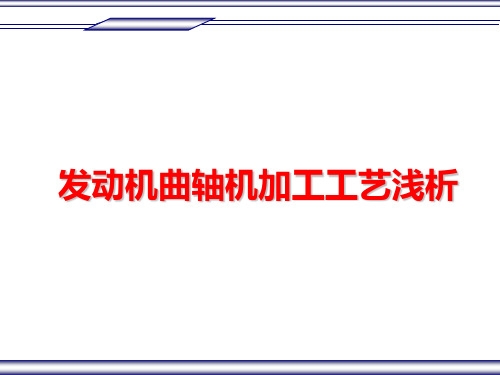
曲轴粗加工也可以先进行内铣(或外铣)主轴颈和连杆轴颈,去除大部 分余量,释放应力再进行车车拉主轴颈和连杆轴颈,这样对减小曲轴的粗加 工变形更为有利,经过车车拉后,曲轴相当于进行了粗磨,获得了较高的轴 向尺寸和轴颈尺寸精度。
以下就曲轴粗加工各类工艺优缺点及适用范围列表,在曲轴粗加工工艺 确定时以作参考。
设备 卧式加工中心 曲轴连杆颈铣床 卧式加工中心 卧式加工中心
沟槽滚压及校直机床 数控多轮磨床 数控连杆颈磨床 法兰面加工机床 卧式加工中心 去毛刺机机器人 动平衡机 曲轴砂带抛光机 磁力探伤机 清洗机 外径分组打刻机
3 曲轴部分加工设备简介
3.1 车车拉机床 车车拉设备一次设定能完成所有同心圆的车削,并在同一
连杆颈的磨削分为粗磨和精磨,连杆颈的尺寸精度、形位公差是靠连杆颈 精磨工序来保证的,连杆颈的精磨工序是曲轴生产中保证曲轴质量的最重要 工序。
曲轴是否粗磨或半精磨与曲轴粗加工工艺选择和曲轴自身精度要求有较大 关系。
国内磨削工艺一般分为粗磨、精磨。国外曲轴加工,大多数厂家都是一 次精磨到位。而在我国曲轴的技术条件中,中间主轴颈对1-7主轴颈的跳动要 求十分严格。以6缸机为例:通常为0.02-0.03mm(感应淬火曲轴)或0.05mm (软氮化曲轴),这就对曲轴主轴颈加工的要求更加严格。以钢质曲轴为例, 经中频感应淬火后进行圆角滚压并校直,通常使跳动量控制在0.15-0.20mm之 间,经重新修整中心孔后,使其跳动量控制在0.075-0.10mm之间,通常跳动 量超过0.08mm,一次磨削就难以达到0.025-0.03mm跳动量要求。如果增加一 次半精磨(粗磨),使其跳动量控制在0.05-0.08mm范围内,再经一次精磨可 以稳定控制其中间主轴颈对1-7主轴颈跳动量要求。相对而言,4缸机曲轴加 工情况要好一些,可以省略半精磨主轴颈工序,直接精磨。
曲轴加工工艺及设备

曲轴加工工艺及设备一、介绍曲轴是发动机中最重要的零部件之一,它的性能直接影响到发动机的整体性能。
曲轴的加工过程复杂,需要经过多道工序才能完成。
本报告将就曲轴的加工工艺、设备、工装等方面进行阐述,并对曲轴加工中的关键技术进行解释和探讨。
二、加工工艺1.毛坯制造曲轴的毛坯制造方式有铸造、锻造和粉末冶金等。
其中,铸造是最常用的毛坯制造方式,可以将熔融的金属注入模具中,冷却后形成毛坯。
锻造是将金属坯料放入模具中,在高压下形成毛坯。
粉末冶金是将金属粉末与粘合剂混合,压制成形后进行烧结,形成毛坯。
2.车削加工车削加工是曲轴加工的基础,可以去除毛坯的剩余材料,形成曲轴的基本形状和尺寸。
在车削加工中,常用的设备有车床和数控车床。
3.铣削加工铣削加工是曲轴加工的重要工序之一,可以去除曲轴上的多余材料,形成曲轴的轮廓和孔。
在铣削加工中,常用的设备有数控铣床和加工中心。
4.钻孔和铰孔钻孔和铰孔是曲轴加工的关键工序之一,可以形成曲轴的孔。
在钻孔和铰孔中,常用的设备有钻床和铰床。
5.热处理热处理是曲轴加工的必要工序之一,可以提高曲轴的硬度和韧性。
在热处理中,常用的工艺有淬火、回火和渗碳等。
三、加工设备1.车床车床是曲轴加工的基础设备,可以完成曲轴的外圆、端面和螺纹等加工。
常用的车床有普通车床和数控车床。
1.铣床铣床是曲轴加工的重要设备,可以完成曲轴的轮廓和孔等加工。
常用的铣床有数控铣床和加工中心。
1.钻床和铰床钻床和铰床是曲轴加工的关键设备,可以完成曲轴的孔加工。
常用的钻床和铰床有数控钻床和数控铰床。
1.热处理设备热处理设备是曲轴加工的必要设备之一,可以提高曲轴的硬度和韧性。
常用的热处理设备有炉、渗碳炉和淬火炉等。
四、工装1.刀具刀具是曲轴加工的重要工具之一,可以切除材料。
常用的刀具有车刀、铣刀、钻头和铰刀等。
2.量具量具是曲轴加工的重要工具之一,可以测量工件的尺寸和形状。
常用的量具有卡尺、千分尺、内径千分尺和塞尺等。
3.工装夹具工装夹具是曲轴加工的重要工具之一,可以固定工件,防止工件移动或变形。
- 1、下载文档前请自行甄别文档内容的完整性,平台不提供额外的编辑、内容补充、找答案等附加服务。
- 2、"仅部分预览"的文档,不可在线预览部分如存在完整性等问题,可反馈申请退款(可完整预览的文档不适用该条件!)。
- 3、如文档侵犯您的权益,请联系客服反馈,我们会尽快为您处理(人工客服工作时间:9:00-18:30)。
6108曲轴机械加工工艺浅析罗仁芝(湘潭职业技术学院,湖南湘谭 411102)摘要:曲轴是活塞式发动机的主要零部件之一,加工工艺复杂、要求高。
结合YC6105QC柴油发动机,深入分析了6108曲轴的机械加工工艺,并对曲轴机加工发展方向进行了初步探讨。
关键词:6108曲轴工艺工序分析中图分类号:TH162+.1 文献标识码:B 文章编号:1008-8415[2006] -01-0039-04一、引言曲轴是活塞式发动机的主要零部件之一,用来将活塞的往复运动转变为旋转运动。
根据发动机气缸的数目,曲轴一般分单缸、双缸、三缸、四缸和六缸曲轴。
如六缸发动机曲轴6108(见图1)有7个主颈和6个连颈,连颈分别位于三个互成120°角的平面内。
曲轴的加工工艺复杂,特别是轴颈有很高的尺寸和形位公差要求,一般按6级精度制造,粗糙度不高于Ra0.8μm。
轴颈表面需要热处理以提高其耐磨性,常用的热处理形式为氮化和高频淬火。
本曲轴的材料为QT850-3。
近年来,球墨铸铁和稀土球墨铸铁得到了广泛的运用,其特点为:可铸性好,有较高的强度和较小的缺口敏感性,有较好的减振性及耐磨性。
本文结合YC6105QC柴油发动机,主要对6108曲轴的机械加工工艺进行分析。
二、6108曲轴工艺分析主一连1主二连2主三连3主四连4主五连5主六连6主七图一 6108曲轴示意图图1 6108曲轴示意图(一)6108曲轴特点及工艺措施6108曲轴(见图1)是带有曲拐的轴,它仍具有轴的一般加工规律,如铣两端面、钻中心孔、车、磨及抛光等,但也有它的特点,包括形状复杂、刚度差及技术要求高,应采取相应的工艺措施,分析如下:1、刚度差6108曲轴的长径比较大(L/d=11),又具有6个连颈,因此刚度较差。
为防止变形,在加工过程中应当采取下列措施:选用有较高刚度的机床、刀具及夹具等,并用中心架来增强刚性,从而减少变形和振动;采用具有两边传动或中间传动的刚度高的机床来进行加工,可以减少扭转变形、弯曲变形和振动;在加工中尽量使切削力的作用互相抵消;合理安排工位顺序以减少加工变形;增设校直工序。
2、形状复杂连颈和主颈不在同一根轴线上,在连颈加工中易产生不平衡的现象,应配备能迅速找正连颈的偏心夹具,且应加平衡块。
3、技术要求高6108曲轴的技术要求是很高的,其机械加工工艺过程随生产纲领的不同和曲轴的复杂程度而有很大的区别,但一般均包括以下几个主要阶段:定位基准的加工;粗、精车和粗磨各主颈及其它外圆;车连颈;钻油孔;精磨各主颈及其他外圆;精磨连颈;大、小头及键槽加工;轴颈表面处理;动平衡;超精加工各轴颈。
可以看出,主颈或连颈的车削工序都与磨削工序分开,往往中间安排一些不同的加工面或不同性质的工序。
粗加工后会发生变形,因此常把粗、精加工分开,并在切削力较大的工序后面安排校直工序,以保证加工精度。
为了减小切削力所引起的变形,保证精加工的精度要求,精磨各轴颈时,一般采用单砂轮依次磨削。
轴颈的加工要求高,主颈和连颈采用多次加工,使加工余量越来越小,切削力逐渐降低;同时由于粗、精加工工序分开进行,后工序就有可能消除前工序的误差,最终获得很高的精度和很低的粗糙度。
(二)定位基准选择1、粗基准的选择为了保证中心孔钻在主颈毛坯外圆面的轴线位置上,选用主颈的外圆面为粗基准。
同时为了保证所加工的基准面的轴向尺寸,选用第四主颈两侧扇板面为轴向粗基准。
2、辅助粗基准的选择在扇板上铣出两个工艺平面即是加工连颈时所用的辅助粗基准。
3、精基准的选择加工主颈及与其同轴心的轴颈外表面时,以中心孔为精基准。
加工连颈时,用加工的法兰和小头的外圆及连颈1外圆作为精基准基面,这样便于保证技术要求。
此外,轴向定位基准采用第四主颈的两个台阶面,与设计基准一致。
(三)6108曲轴工艺过程若某公司年产6108曲轴20000支,材料为QT850-3,毛坯为铸件。
工艺过程编制如下:(见表1)完善的工艺技术条件是为了满足产品的技术要求,故工艺技术条件应切实可行,便于操作。
分析如下:1、铣端面工序有两个作用:保证曲轴的总长;保证中心孔的质量。
若端面不平,则中心钻上两个切削刃的受力不均,钻头引偏而折断。
这也是“先面后孔”原则的具体应用。
2、中心孔的重要性:中心孔除影响曲轴的质量分布外,它的重要性还在于它是曲轴加工的重要精基准,直接影响曲轴的加工精度,因此中心孔必须满足其质量要求。
但工件经过粗加工后,中心孔的精度往往不可避免地受到影响,所以在精加工之前,必须对中心孔进行修研,确保符合其技术要求。
可用油石或橡胶砂轮修研。
3、打中心孔是采用找出曲轴的几何中心来代替质量中心,是以毛坯的外表作为基准。
毛坯外表光洁圆整,则打出的中心孔位置误差就小。
4、按照S1-206车床的工装结构,必须先粗车和粗磨主颈四。
主颈四是加工长度尺寸的一个基准,其两侧扇板的厚度应分均匀,否则极易使整根曲轴的轴向尺寸发生偏移,即单边,致使曲轴各扇板厚度不一而致废。
5、因曲轴刚度差,故车主轴颈的工序,采用前后刀架同时横向进给的S1-206一次加工成型的机床,必须注意刀排分布应合理,车刀应常换常磨,进刀量应适中。
6、车小头孔、平端面工序不容忽视。
因为小头是与起动爪相连的部位,在用人力起动发动机时,小头传递大力矩,所以首先要保证小头的有效深度,其次小头孔倒角应圆整光滑,角度正确,以保证精磨小头时外圆跳动合格,否则就应重新精修小头孔倒角。
7、钻大头孔工序。
孔太深会影响第七主轴颈及法兰的强度,太浅会影响内装黄油的空间和装轴承的轴向位置。
8、铣定位面。
为了使车连颈时角度分布均匀,按照铸造毛坯六缸曲轴的角度均布原理去掉铸造余量,故必须铣好定位面。
不论定位面向那边有所偏移,都会严重改变铸件曲轴工序余量的均匀分布,严重偏移的致使连颈加工不足而致废。
9、车连颈时按照S1-217的结构分成车连颈1、6,车连颈2、5,车连颈3、4三道工序。
S1-217是成型车床,刀排分布合理、车刀的成型正确、进刀量适中、定位面紧靠都直接影响到产品能否达到工艺技术要求。
故中心距、长度、宽度尺寸和圆弧、外圆尺寸等的调整必须在车床进入稳定加工状态后才可进行,避免工艺系统热变形影响太大。
10、粗磨连颈是一道重要工序。
粗磨连颈要进行曲轴120°的三等分,保证中心高尺寸。
磨床首尾两端偏心夹具的移动会引起主连轴颈中心高的变化,应仔细调整至合适之处反锁固定。
此外若中心架调整不恰当会引起曲轴变形而致中心高超差,而砂轮进刀太快则会引起角度偏移,甚至曲轴断裂。
11、国家颁布的《曲轴技术条件》明确规定,每根曲轴必须经磁力探伤并且执行严格的磁力探伤标准,它是曲轴加工过程中唯一可较直观地检查曲轴浅表层质量的工序;注意探伤后曲轴必须退磁。
12、钻斜油孔使用的是专用钻床。
此工序主要保证钻斜油孔的角度和它的进出口位置。
斜油道的作用是在轴颈与轴瓦相对运动时提供润滑油,如果油孔口偏移,那么进入轴瓦油道的润滑油减少,造成发动机整体燃油经济性下降,甚至有可能造成早期磨损,轴瓦抱死等严重事故。
所以,在加工时首先要保证直油道与斜油道交接口足够大,其次要保证直油道在轴颈方向不偏移,因此对斜油孔钻模应常予检查。
钻头进入到与直油孔口交接处应减慢进刀速度,避免钻头折断。
13、精磨主轴颈时应把两顶尖孔倒角处抹干净,去掉砂粒、油泥,确保加工基准——中心孔的精度,必要时修研。
精磨开始前,要提前启动机床,使砂轮运转一定时间后,利用修整器把砂轮的厚度和圆弧修整。
修好圆弧后应用圆弧规检查,看圆弧是否和两侧面相切,如不相切,要检查表面修整器是否有偏心或其它问题,问题找出并解决后再重新修圆弧至合格。
砂轮的圆周表面要修细致,否则不能保证磨削后轴颈的粗糙度而形成螺旋纹印。
因为曲轴较长,必须用中心架作为一个辅助支撑,进入精磨后,先磨一个轴颈至合适尺寸(留至比成型尺寸大0.1~0.2mm),使支中心架有一个合适的基准面。
为了使整根曲轴在加工运转时的刚性和紧固性增强,可采用V型夹具来装夹曲轴主颈一、主颈七位置。
测量时,应千分尺和表架上的千分表结合起来使用。
14、小头精磨一般单独安排一道工序。
此工序主要是小头跳动和小头长度尺寸易超差。
加工前应先用百分表检查主颈一跳动,若超差,则应重新修正小头中心孔倒角,直到跳动合格。
15、钻法兰孔采用多工步的加工方法。
各丝孔相互之间的位置度由钻模和钻套保证,销孔的位置度由可调定位销保证。
此工序易出现的质量问题是法兰各孔漏攻丝和攻丝深度不够。
16、在万能铣床上铣键槽是用V型夹具支撑,连颈1的外径靠在可调定位销上定位。
键槽的对称度是从两个方面要求,一是对连1轴颈中心线的对称度,二是对主轴颈的对称度。
对称度是通过调动V型夹具和定位销来保证的。
17、油孔口抛光工序相当重要,因为如果油孔口有毛刺,则会刮伤轴瓦,造成早期拉毛现象;如果油孔口有尖角,则曲轴运转时应力集中形成裂纹影响其使用寿命;特别是如果主油道口与斜油道口交接处过渡不圆整,粗糙度低,更容易形成应力集中。
18、随着技术的发展,曲轴动不平衡的要求越来越严格,动不平衡量越小,曲轴工作时运转越平稳,噪音越小,磨损越少,寿命越长。
三、曲轴机加工发展方向随着我国数控机床的不断增加,曲轴粗加工将广泛采用数控车床、数控内铣床、数控车拉床等先进设备对主轴颈、连杆轴颈进行数控车削、内铣削、车-拉削加工,以有效减少曲轴加工的变形量。
曲轴精加工将广泛采用CNC控制的曲轴磨床对其轴颈进行精磨加工,此种磨床将配备砂轮自动动平衡装置、中心架自动跟踪装置、自动测量、自动补偿装置、砂轮自动修整、恒线速度等功能要求,以保证磨削质量的稳定。
为满足曲轴日益提高的加工要求,对曲轴磨床提出了很高的要求。
现代曲轴磨床除了要有很高的静态、动态刚度和很高的加工精度外,还要求有很高的磨削效率和更多的柔性。
近年来,更要求曲轴磨床具有稳定的加工精度,为此,对曲轴磨床的工序能力系数规定了Cp≥1.67,这意味着要求曲轴磨床的实际加工公差要比曲轴给定的公差小一半。
随着现代驱动和控制技术、测量控制、CBN (立方氮化硼)砂轮和先进的机床部件的应用,为曲轴磨床的高精度、高效磨削加工创造了条件。
一种称之为连杆颈随动磨削的工艺。
正是体现了这些新技术综合应用的具体成果。
这种随动磨削工艺可显著地提高曲轴连杆颈的磨削效率、加工精度和加工柔性。
在对连杆颈进行随动磨削时,曲轴以主轴颈为轴线进行旋转,并在一次装夹下磨削所有连杆颈。
在磨削过程中,磨头实现往复摆动进给,跟踪着偏心回转的连杆颈进行磨削加工。
要实现随动磨削,X轴除了必须具有高的动态性能外,还必须具有足够的跟踪精度,以确保连杆颈所要求的形状公差。
CBN砂轮的应用是实现连杆颈随动磨削的重要条件。
由于CBN砂轮耐磨性高,在磨削过程中砂轮的直径几乎是不变的,一次修整可磨削600~800条曲轴。