热镀锌过程锌灰
热镀锌操作流程
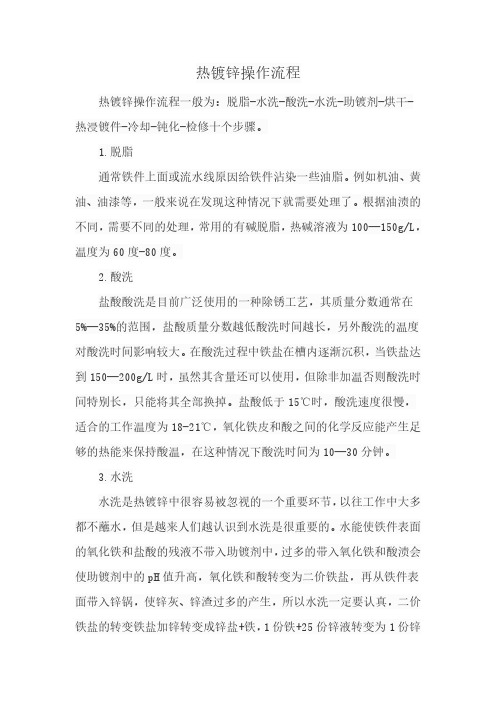
热镀锌操作流程热镀锌操作流程一般为:脱脂-水洗-酸洗-水洗-助镀剂-烘干-热浸镀件-冷却-钝化-检修十个步骤。
1.脱脂通常铁件上面或流水线原因给铁件沾染一些油脂。
例如机油、黄油、油漆等,一般来说在发现这种情况下就需要处理了。
根据油渍的不同,需要不同的处理,常用的有碱脱脂,热碱溶液为100—150g/L,温度为60度-80度。
2.酸洗盐酸酸洗是目前广泛使用的一种除锈工艺,其质量分数通常在5%—35%的范围,盐酸质量分数越低酸洗时间越长,另外酸洗的温度对酸洗时间影响较大。
在酸洗过程中铁盐在槽内逐渐沉积,当铁盐达到150—200g/L时,虽然其含量还可以使用,但除非加温否则酸洗时间特别长,只能将其全部换掉。
盐酸低于15℃时,酸洗速度很慢,适合的工作温度为18-21℃,氧化铁皮和酸之间的化学反应能产生足够的热能来保持酸温,在这种情况下酸洗时间为10—30分钟。
3.水洗水洗是热镀锌中很容易被忽视的一个重要环节,以往工作中大多都不蘸水,但是越来人们越认识到水洗是很重要的。
水能使铁件表面的氧化铁和盐酸的残液不带入助镀剂中,过多的带入氧化铁和酸渍会使助镀剂中的pH值升高,氧化铁和酸转变为二价铁盐,再从铁件表面带入锌锅,使锌灰、锌渣过多的产生,所以水洗一定要认真,二价铁盐的转变铁盐加锌转变成锌盐+铁,1份铁+25份锌液转变为1份锌渣。
4.助镀剂助镀剂是一项重要环节,它不仅可以弥补前几道工序的不足,还可以活化钢件表面,提高镀锌质量,它的好坏直接影响镀层和质量,对锌耗成本有很大影响。
所谓助镀剂是将酸洗后的铁件在一定的铵锌比的助镀剂中形成一种薄的氧化锌铵盐膜。
助镀液的浓度是指氧化锌与氧化铵的比例。
溶剂中的二价铁盐含量、pH值。
温度以及杂质含量等因素都会对助镀效果产生影响。
当助镀剂浓度低于(100g/L)时,镀件产生漏镀;当助镀液浓度低于(100—200g/L)时,由于制件表面附着的盐膜量小,不能有效地活化制件表面,难以获得平滑均匀的镀层;当助镀液浓度高于(400—500g/L)时,由于表面盐膜过厚,不易干透,在铁件入锅时引起锌的飞溅,产生过多的锌灰、更浓的烟尘和厚的锌层;当浓度高于(500g/L)时,制件表面形成内外两层盐膜,下锅时外层盐膜干透里层干不透,当锌液与铁件接触时,会因水的汽化而引起强烈的爆锌。
热浸镀锌的工艺流程
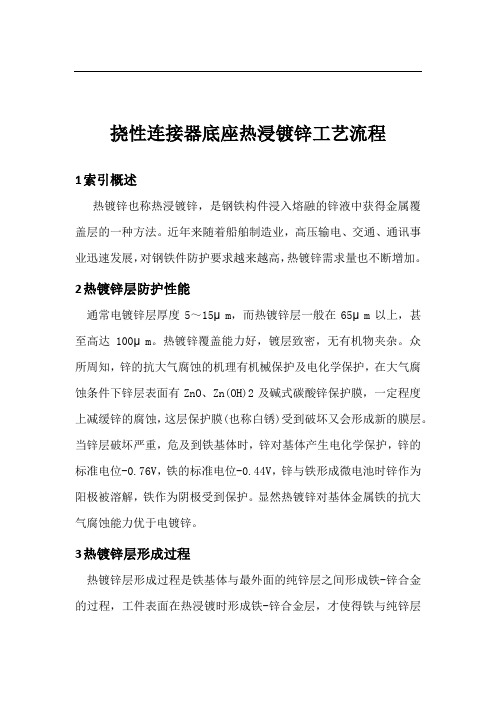
挠性连接器底座热浸镀锌工艺流程1索引概述热镀锌也称热浸镀锌,是钢铁构件浸入熔融的锌液中获得金属覆盖层的一种方法。
近年来随着船舶制造业,高压输电、交通、通讯事业迅速发展,对钢铁件防护要求越来越高,热镀锌需求量也不断增加。
2热镀锌层防护性能通常电镀锌层厚度5~15μm,而热镀锌层一般在65μm以上,甚至高达100μm。
热镀锌覆盖能力好,镀层致密,无有机物夹杂。
众所周知,锌的抗大气腐蚀的机理有机械保护及电化学保护,在大气腐蚀条件下锌层表面有ZnO、Zn(OH)2及碱式碳酸锌保护膜,一定程度上减缓锌的腐蚀,这层保护膜(也称白锈)受到破坏又会形成新的膜层。
当锌层破坏严重,危及到铁基体时,锌对基体产生电化学保护,锌的标准电位-0.76V,铁的标准电位-0.44V,锌与铁形成微电池时锌作为阳极被溶解,铁作为阴极受到保护。
显然热镀锌对基体金属铁的抗大气腐蚀能力优于电镀锌。
3热镀锌层形成过程热镀锌层形成过程是铁基体与最外面的纯锌层之间形成铁-锌合金的过程,工件表面在热浸镀时形成铁-锌合金层,才使得铁与纯锌层之间很好结合,其过程可简单地叙述为:当铁工件浸入熔融的锌液时,首先在界面上形成锌与α铁(体心)固熔体。
这是基体金属铁在固体状态下溶有锌原子所形成一种晶体,两种金属原子之间是融合,原子之间引力比较小。
因此,当锌在固熔体中达到饱和后,锌铁两种元素原子相互扩散,扩散到(或叫渗入)铁基体中的锌原子在基体晶格中迁移,逐渐与铁形成合金,而扩散到熔融的锌液中的铁就与锌形成金属间化合物FeZn13,沉入热镀锌锅底,即为锌渣。
当工件从浸锌液中移出时表面形成纯锌层,为六方晶体。
其含铁量不大于0.003%。
4热镀锌工艺过程及有关说明4.1工艺过程工件→脱脂→水洗→酸洗→水洗→浸助镀溶剂→烘干预热→热镀锌→整理→冷却→钝化→漂洗→干燥→检验4.2有关工艺过程说明4.2.1脱脂可采用化学去油或水基金属脱脂清洗剂去油,达到工件完全被水浸润为止。
热镀锌的危险因素及安全措施
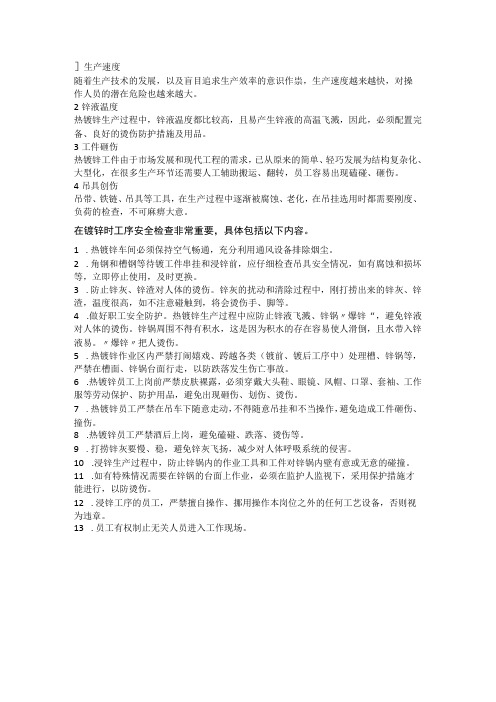
]生产速度随着生产技术的发展,以及盲目追求生产效率的意识作祟,生产速度越来越快,对操作人员的潜在危险也越来越大。
2锌液温度热镀锌生产过程中,锌液温度都比较高,且易产生锌液的高温飞溅,因此,必须配置完备、良好的烫伤防护措施及用品。
3工件砸伤热镀锌工件由于市场发展和现代工程的需求,已从原来的简单、轻巧发展为结构复杂化、大型化,在很多生产环节还需要人工辅助搬运、翻转,员工容易出现磕碰、砸伤。
4吊具创伤吊带、铁链、吊具等工具,在生产过程中逐渐被腐蚀、老化,在吊挂选用时都需要刚度、负荷的检查,不可麻痹大意。
在镀锌时工序安全检查非常重要,具体包括以下内容。
1.热镀锌车间必须保持空气畅通,充分利用通风设备排除烟尘。
2.角钢和槽钢等待镀工件串挂和浸锌前,应仔细检查吊具安全情况,如有腐蚀和损坏等,立即停止使用,及时更换。
3.防止锌灰、锌渣对人体的烫伤。
锌灰的扰动和清除过程中,刚打捞出来的锌灰、锌渣,温度很高,如不注意碰触到,将会烫伤手、脚等。
4.做好职工安全防护。
热镀锌生产过程中应防止锌液飞溅、锌锅〃爆锌“,避免锌液对人体的烫伤。
锌锅周围不得有积水,这是因为积水的存在容易使人滑倒,且水带入锌液易。
〃爆锌〃把人烫伤。
5.热镀锌作业区内严禁打闹嬉戏、跨越各类(镀前、镀后工序中)处理槽、锌锅等,严禁在槽面、锌锅台面行走,以防跌落发生伤亡事故。
6.热镀锌员工上岗前严禁皮肤裸露,必须穿戴大头鞋、眼镜、风帽、口罩、套袖、工作服等劳动保护、防护用品,避免出现砸伤、划伤、烫伤。
7.热镀锌员工严禁在吊车下随意走动,不得随意吊挂和不当操作,避免造成工件砸伤、撞伤。
8.热镀锌员工严禁酒后上岗,避免磕碰、跌落、烫伤等。
9.打捞锌灰要慢、稳,避免锌灰飞扬,减少对人体呼吸系统的侵害。
10.浸锌生产过程中,防止锌锅内的作业工具和工件对锌锅内壁有意或无意的碰撞。
11.如有特殊情况需要在锌锅的台面上作业,必须在监护人监视下,采用保护措施才能进行,以防烫伤。
热镀锌锌灰锌渣环境报告
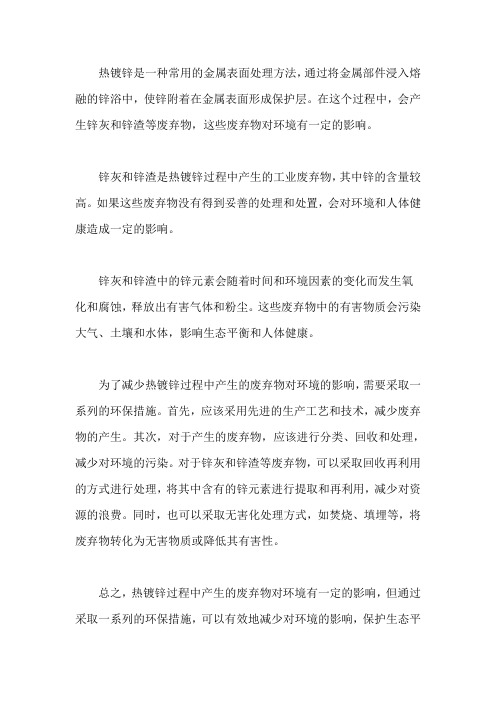
热镀锌是一种常用的金属表面处理方法,通过将金属部件浸入熔融的锌浴中,使锌附着在金属表面形成保护层。
在这个过程中,会产生锌灰和锌渣等废弃物,这些废弃物对环境有一定的影响。
锌灰和锌渣是热镀锌过程中产生的工业废弃物,其中锌的含量较高。
如果这些废弃物没有得到妥善的处理和处置,会对环境和人体健康造成一定的影响。
锌灰和锌渣中的锌元素会随着时间和环境因素的变化而发生氧化和腐蚀,释放出有害气体和粉尘。
这些废弃物中的有害物质会污染大气、土壤和水体,影响生态平衡和人体健康。
为了减少热镀锌过程中产生的废弃物对环境的影响,需要采取一系列的环保措施。
首先,应该采用先进的生产工艺和技术,减少废弃物的产生。
其次,对于产生的废弃物,应该进行分类、回收和处理,减少对环境的污染。
对于锌灰和锌渣等废弃物,可以采取回收再利用的方式进行处理,将其中含有的锌元素进行提取和再利用,减少对资源的浪费。
同时,也可以采取无害化处理方式,如焚烧、填埋等,将废弃物转化为无害物质或降低其有害性。
总之,热镀锌过程中产生的废弃物对环境有一定的影响,但通过采取一系列的环保措施,可以有效地减少对环境的影响,保护生态平
衡和人体健康。
热镀锌工艺中锌渣的形成及其控制

21Metallurgical smelting冶金冶炼热镀锌工艺中锌渣的形成及其控制陈学松(唐山钢铁集团责任有限公司,河北 唐山 063000)摘 要:随着科学技术的不断发展,越来越多的新工艺逐渐应用到热镀锌生产活动当中。
而在热镀锌产品生产过程中,常常伴随着锌渣缺陷,严重影响了产品表面质量,同时还会造成大量的资源浪费,难以满足实际的生产需求,不利于带动我国工业的发展。
因而在现阶段的热镀锌工艺生产活动中,要加强对锌渣形成及其成因的探究,充分了解锌渣形成的原因,并且能够采取积极有效的措,施加强改进,加强热镀锌工艺生产中锌渣生成量控制工作。
基于此,在本次研究中就结合我国大型钢铁厂镀锌线的现场生产作为研究对象,加强对热镀锌板锌渣形成缺陷机理的分析,探究形成原因,并提出相应的工作建议,全面加强锌渣生产量控制,提高镀锌板表面质量。
关键词:热镀锌工艺;锌渣;形成;控制;策略中图分类号:TG174.44 文献标识码:A 文章编号:11-5004(2021)04-0021-2 收稿日期:2021-02作者简介:陈学松,男,生于1994年,汉族,河北唐山人,本科,助理工程师,研究方向:镀锌。
在钢铁行业发展过程中,逐渐加大了热镀锌板的需求量。
而随着人们生活水平的不断提升,人们的生活品质有了明显的提高,对工业生产有了更高的质量要求。
在热镀锌工艺开展过程中,要全面提升整体的施工质量,有效保障其表面的完整性,避免出现点状缺陷等,提升其整体的质量和品质。
在热镀锌工艺使用的过程中,常常会因为锌渣的产生,缩短了锌锅的使用寿命,同时还严重影响产品生产的整体质量。
随着工业的不断发展,在现阶段的热镀锌工艺使用过程中,要全面加强技术创新。
在提升产品表面质量的同时,采用积极有效的办法,保障相应生产活动能够更加高效稳定开展,且能够达到预期的生产目标。
因而在热镀锌产品生产活动中,则需要综合考虑到锌渣的形成对整个生产活动带来的影响,采用更加科学合理的办法,尽可能减少锌渣的生成量。
热镀锌生产中锌灰对产品表面质量的影响和解决方法

第12卷 第2期2010年6月 辽宁科技学院学报JOURNAL OF L I A ON I N G I N STI T UTE OF SC I E NCE AND TECHNOLOGY Vol .12 No .2Jun . 2010文章编号:1008-3723(2010)02-0013-02热镀锌生产中锌灰对产品表面质量的影响和解决方法崔凤伟(本溪钢铁集团公司,辽宁本溪117000)摘要:介绍了热镀锌中锌灰产生的原因及对产品质量产生的影响。
阐述了要生产出高表面质量的热镀锌产品,必须首先解决锌灰对设备和产品表面质量所产生的影响,并提出了相应的解决办法。
关键词:热镀锌;锌灰;沉没辊中图分类号:TG356.27 文献标识码:A1 形成锌灰的原因由于锌锅中的锌液被加热至460℃以上,带钢入锌锅温度一般也是在460℃以上,在炉鼻子内的锌液面会有锌蒸汽生成,当升至一定高度后由于与炉鼻子中的水分发生置换反应(方程式1)、与微量的氧发生氧化反应等因素生成氧化锌颗粒,就是我们常说的锌灰,实际产生的锌灰中是纯锌、氧化锌和其他一些杂质的混合物。
Z n +H 2O (气)]高温Z nO +H 2↑(1)在采用立式退火炉的热镀锌生产线中,锌灰缺陷是影响表面质量的主要瓶颈。
由于锌液的蒸发和在炉鼻子中的烟囱效应共同作用,加快了锌液的挥发,加剧了锌灰的产生。
2 锌灰对热镀锌生产带来的影响2.1 对表面质量的影响:锌灰悬浮在炉鼻子中锌液的表面,当带钢进入锌锅时便把锌灰粘到了带钢的表面,在带钢经过锌锅后在带钢表面就产生了粗糙不平的表面。
根据锌灰在液面的分布不同会在带钢的不同位置产生不同形状的锌灰缺陷。
2.2 对设备的影响:被带钢带入锌锅的锌灰还会粘附到沉没辊的表面,造成沉没辊辊印。
这就是为什么出锌锅后带钢下表面锌灰缺陷往往要比上表面严重的原因。
如果锌灰进入到沉没辊、稳定辊、矫正辊的轴与轴套之间还会导致三辊的转动阻力增大,进一步加重了沉没辊辊印,严重的还导致沉没辊划伤和轴套磨损严重甚至磨穿锌灰缺陷是目前产品表面质量提高的主要瓶颈。
热镀锌工艺流程及应用.doc
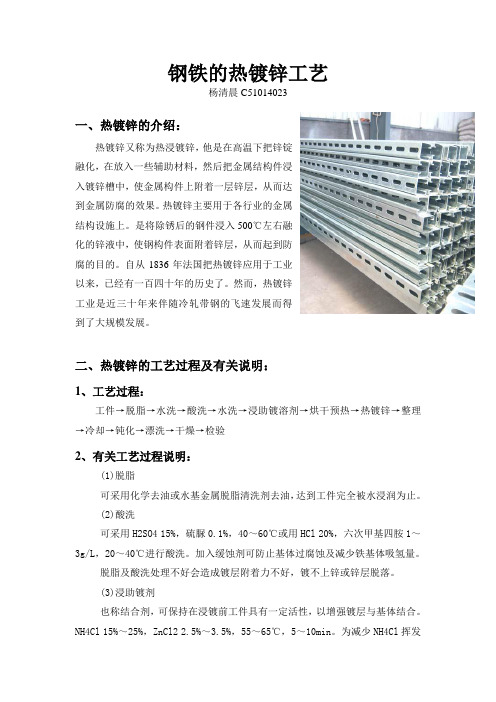
钢铁的热镀锌工艺杨清晨C51014023一、热镀锌的介绍:热镀锌又称为热浸镀锌,他是在高温下把锌锭融化,在放入一些辅助材料,然后把金属结构件浸入镀锌槽中,使金属构件上附着一层锌层,从而达到金属防腐的效果。
热镀锌主要用于各行业的金属结构设施上。
是将除锈后的钢件浸入500℃左右融化的锌液中,使钢构件表面附着锌层,从而起到防腐的目的。
自从1836年法国把热镀锌应用于工业以来,已经有一百四十年的历史了。
然而,热镀锌工业是近三十年来伴随冷轧带钢的飞速发展而得到了大规模发展。
二、热镀锌的工艺过程及有关说明:1、工艺过程:工件→脱脂→水洗→酸洗→水洗→浸助镀溶剂→烘干预热→热镀锌→整理→冷却→钝化→漂洗→干燥→检验2、有关工艺过程说明:(1)脱脂可采用化学去油或水基金属脱脂清洗剂去油,达到工件完全被水浸润为止。
(2)酸洗可采用H2SO4 15%,硫脲0.1%,40~60℃或用HCl 20%,六次甲基四胺1~3g/L,20~40℃进行酸洗。
加入缓蚀剂可防止基体过腐蚀及减少铁基体吸氢量。
脱脂及酸洗处理不好会造成镀层附着力不好,镀不上锌或锌层脱落。
(3)浸助镀剂也称结合剂,可保持在浸镀前工件具有一定活性,以增强镀层与基体结合。
NH4Cl 15%~25%,ZnCl2 2.5%~3.5%,55~65℃,5~10min。
为减少NH4Cl挥发可适当加入甘油。
(4)烘干预热为了防止工件在浸镀时由于温度急剧升高而变形,并除去残余水分,防止产生爆锌,造成锌液爆溅,预热一般为120~180℃。
(5)热镀锌要控制好锌液温度、浸镀时间及工件从锌液中移出的速度。
温度过低,锌液流动性差,镀层厚且不均匀,易产生流挂,外观质量差;温度高,锌液流动性好,锌液易脱离工件,减少流挂及皱皮现象发生,附着力强,镀层薄,外观好,生产效率高;但温度过高,工件及锌锅铁损严重,产生大量锌渣,影响浸锌层质量,锌耗大,甚至无法施镀。
在同一温度下,浸镀时间长,镀层厚。
热镀锌过程中锌渣的形成及其控制

热镀锌过程中锌渣的形成及其控制锌渣的大量产生,不仅会影响产品的表面质量,而且会造成资源浪费,降低锌锅使用寿命。
文章结合国内某大型钢铁厂镀锌线的生产实践,对热镀锌板锌渣缺陷形成机理进行了分析,重点探讨锌渣产生的原因,提出在实际生产中从工艺和设备上采取措施进行控制,减少锌渣的产生,提高镀锌板表面质量。
标签:热镀锌;锌渣;锌锅;底渣1 前言随着钢铁行业的快速发展,市场竞争日趋激烈,用户对镀锌板表面质量的要求也不断提高。
锌渣的产生不仅缩短了锌锅的使用寿命,而且影响产品的表面质量。
人们越来越注重对锌渣的抑制和改善办法的研究。
各大生产厂家应从生产流程和生产设施方面改进,从而减少镀锌过程里产生的锌渣量,并采取有效方法进行抑制,以减少原料消耗,改善带钢的板面及性能。
本文从热镀锌生产中锌渣的形成机理和减少锌渣的有效措施方面进行探讨。
2 镀锌生产过程锌渣生成的机理无论采取何种措施进行产品的热浸镀锌,通过各种各样的反应、氧化以及腐蚀,锌锅中的液态锌中在所难免的会进入一定数量的铁元素,这一元素与Zn作用就会产出锌渣。
如果我们向锌锅中添加Al,这两种物质也会产生反应产出比重为4.2g/m2的Fe2Al5,由于这一物质的比重比锌液低,因此会浮在液体上部,曾经有人对这种情况进行过计算,镀锌过程中液态Zn中的Fe成分里,钢板溶解造成的损失约百分之七十点五,锌锅的腐蚀约百分之二点二。
铁进入锌液后,一般有83.7%形成底渣,6.1%形成了浮渣,10%附着于镀层。
我们通常所说的浮渣并不应该单单指分量较低的Fe2Al5,它还应该包括ZnO、Al2O3、ZnCl2及NH4Cl,通常进行溶剂法镀锌时会生成后面两种物质。
在连续热镀锌机组正常运转时,产生的浮渣通常由操作者手动通过捞渣勺进行打捞,主要目的就是防止由于锌渣过多而造成的产品表面缺陷等问题,很多大型机组在生产过程中还研制出了专门的捞渣设施及捞渣方法,从而有效提高了产品的表面质量。
生产过程中一定数量的Fe与Zn反应会产生FeZn7,它的熔点为640℃,高于锌液的温度,比重为7.25g/cm3,由于其比重比Zn大,因此会落入锌液底部形成我们通常所说的底渣,不但会造成大量的浪费而且会严重影响带钢的表面及性能。
冷轧热镀锌带钢表面锌灰缺陷形成原因分析及控制
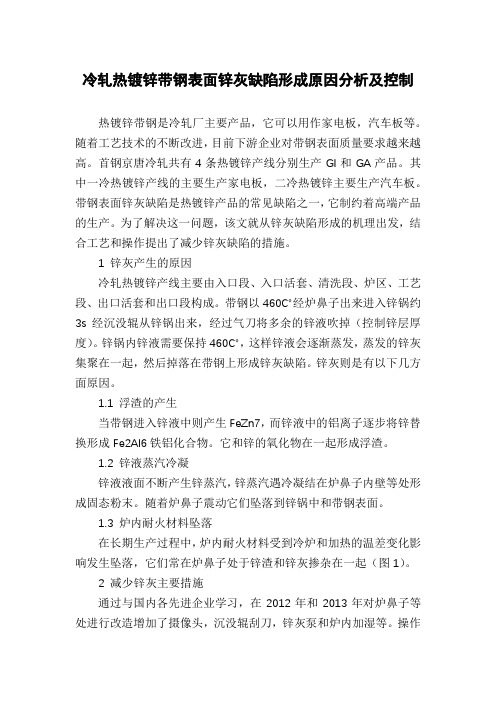
冷轧热镀锌带钢表面锌灰缺陷形成原因分析及控制热镀锌带钢是冷轧厂主要产品,它可以用作家电板,汽车板等。
随着工艺技术的不断改进,目前下游企业对带钢表面质量要求越来越高。
首钢京唐冷轧共有4条热镀锌产线分别生产GI和GA产品。
其中一冷热镀锌产线的主要生产家电板,二冷热镀锌主要生产汽车板。
带钢表面锌灰缺陷是热镀锌产品的常见缺陷之一,它制约着高端产品的生产。
为了解决这一问题,该文就从锌灰缺陷形成的机理出发,结合工艺和操作提出了减少锌灰缺陷的措施。
1 锌灰产生的原因冷轧热镀锌产线主要由入口段、入口活套、清洗段、炉区、工艺段、出口活套和出口段构成。
带钢以460℃经炉鼻子出来进入锌锅约3s经沉没辊从锌锅出来,经过气刀将多余的锌液吹掉(控制锌层厚度)。
锌锅内锌液需要保持460℃,这样锌液会逐渐蒸发,蒸发的锌灰集聚在一起,然后掉落在带钢上形成锌灰缺陷。
锌灰则是有以下几方面原因。
1.1 浮渣的产生当带钢进入锌液中则产生FeZn7,而锌液中的铝离子逐步将锌替换形成Fe2Al6铁铝化合物。
它和锌的氧化物在一起形成浮渣。
1.2 锌液蒸汽冷凝锌液液面不断产生锌蒸汽,锌蒸汽遇冷凝结在炉鼻子内壁等处形成固态粉末。
随着炉鼻子震动它们坠落到锌锅中和带钢表面。
1.3 炉内耐火材料坠落在长期生产过程中,炉内耐火材料受到冷炉和加热的温差变化影响发生坠落,它们常在炉鼻子处于锌渣和锌灰掺杂在一起(图1)。
2 减少锌灰主要措施通过与国内各先进企业学习,在2012年和2013年对炉鼻子等处进行改造增加了摄像头,沉没辊刮刀,锌灰泵和炉内加湿等。
操作人员通过炉鼻子摄像头监控炉内锌灰粉末生成情况,防止炉鼻子内锌灰和锌渣形成过多。
2.1 浮渣清理操作人员利用专用扒渣勺,每班扒渣4次;利用锌灰泵定期对浮渣进行清理;利用检修或更换沉没辊的时间将锌锅降低,炉鼻子处锌渣暴露出来后进行人工扒渣。
2.2 防止锌液蒸汽冷凝为了有效防止锌蒸汽冷凝形成固态锌粉末,各热镀锌产线增加了炉鼻子氮气加湿系统。
热镀锌工艺流程及原理
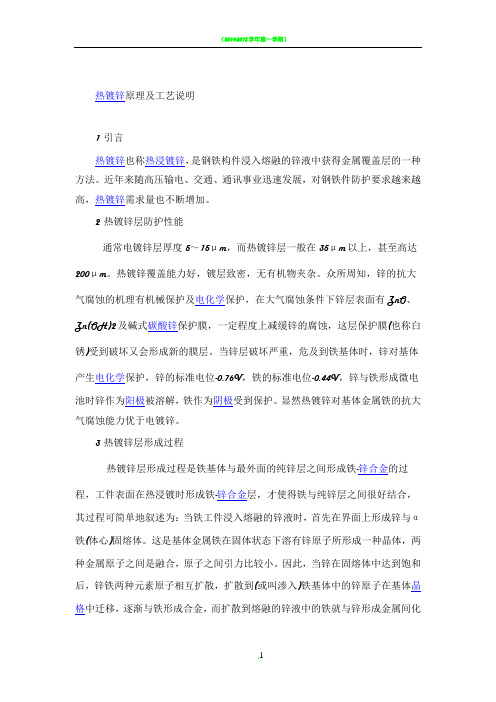
热镀锌原理及工艺说明1 引言热镀锌也称热浸镀锌,是钢铁构件浸入熔融的锌液中获得金属覆盖层的一种方法。
近年来随高压输电、交通、通讯事业迅速发展,对钢铁件防护要求越来越高,热镀锌需求量也不断增加。
2 热镀锌层防护性能通常电镀锌层厚度5~15μm,而热镀锌层一般在35μm以上,甚至高达200μm。
热镀锌覆盖能力好,镀层致密,无有机物夹杂。
众所周知,锌的抗大气腐蚀的机理有机械保护及电化学保护,在大气腐蚀条件下锌层表面有ZnO、Zn(OH)2及碱式碳酸锌保护膜,一定程度上减缓锌的腐蚀,这层保护膜(也称白锈)受到破坏又会形成新的膜层。
当锌层破坏严重,危及到铁基体时,锌对基体产生电化学保护,锌的标准电位-0.76V,铁的标准电位-0.44V,锌与铁形成微电池时锌作为阳极被溶解,铁作为阴极受到保护。
显然热镀锌对基体金属铁的抗大气腐蚀能力优于电镀锌。
3 热镀锌层形成过程热镀锌层形成过程是铁基体与最外面的纯锌层之间形成铁-锌合金的过程,工件表面在热浸镀时形成铁-锌合金层,才使得铁与纯锌层之间很好结合,其过程可简单地叙述为:当铁工件浸入熔融的锌液时,首先在界面上形成锌与α铁(体心)固熔体。
这是基体金属铁在固体状态下溶有锌原子所形成一种晶体,两种金属原子之间是融合,原子之间引力比较小。
因此,当锌在固熔体中达到饱和后,锌铁两种元素原子相互扩散,扩散到(或叫渗入)铁基体中的锌原子在基体晶格中迁移,逐渐与铁形成合金,而扩散到熔融的锌液中的铁就与锌形成金属间化合物FeZn13,沉入热镀锌锅底,即为锌渣。
当工件从浸锌液中移出时表面形成纯锌层,为六方晶体。
其含铁量不大于0.003%。
4 热镀锌工艺过程及有关说明4.1 工艺过程工件→脱脂→水洗→酸洗→水洗→浸助镀溶剂→烘干预热→热镀锌→整理→冷却→钝化→漂洗→干燥→检验4.2 有关工艺过程说明(1)脱脂可采用化学去油或水基金属脱脂清洗剂去油,达到工件完全被水浸润为止。
(2)酸洗可采用H2SO4 15%,硫脲0.1%,40~60℃或用HCl 20%,乌洛托品3~5g/L,20~40℃进行酸洗。
热镀锌工艺
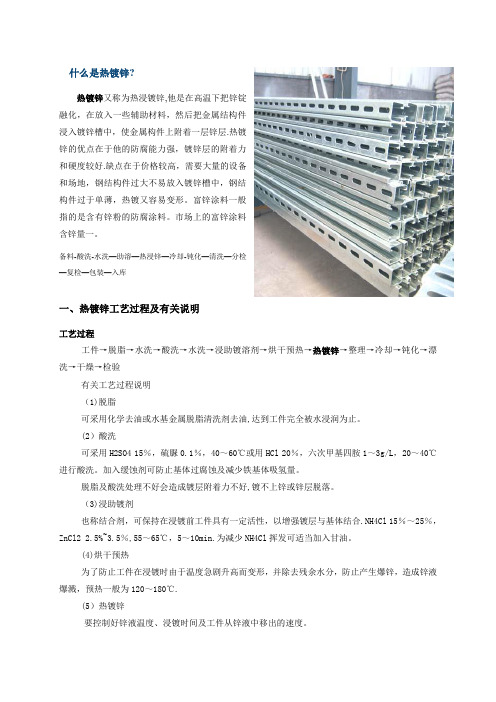
什么是热镀锌?热镀锌又称为热浸镀锌,他是在高温下把锌锭融化,在放入一些辅助材料,然后把金属结构件浸入镀锌槽中,使金属构件上附着一层锌层.热镀锌的优点在于他的防腐能力强,镀锌层的附着力和硬度较好.缺点在于价格较高,需要大量的设备和场地,钢结构件过大不易放入镀锌槽中,钢结构件过于单薄,热镀又容易变形。
富锌涂料一般指的是含有锌粉的防腐涂料。
市场上的富锌涂料含锌量一。
备料-酸洗-水洗—助溶—热浸锌—冷却-钝化—清洗—分检—复检—包装—入库一、热镀锌工艺过程及有关说明工艺过程工件→脱脂→水洗→酸洗→水洗→浸助镀溶剂→烘干预热→热镀锌→整理→冷却→钝化→漂洗→干燥→检验有关工艺过程说明(1)脱脂可采用化学去油或水基金属脱脂清洗剂去油,达到工件完全被水浸润为止。
(2)酸洗可采用H2SO4 15%,硫脲0.1%,40~60℃或用HCl 20%,六次甲基四胺1~3g/L,20~40℃进行酸洗。
加入缓蚀剂可防止基体过腐蚀及减少铁基体吸氢量。
脱脂及酸洗处理不好会造成镀层附着力不好,镀不上锌或锌层脱落。
(3)浸助镀剂也称结合剂,可保持在浸镀前工件具有一定活性,以增强镀层与基体结合.NH4Cl 15%~25%,ZnCl2 2.5%~3.5%,55~65℃,5~10min.为减少NH4Cl挥发可适当加入甘油。
(4)烘干预热为了防止工件在浸镀时由于温度急剧升高而变形,并除去残余水分,防止产生爆锌,造成锌液爆溅,预热一般为120~180℃.(5)热镀锌要控制好锌液温度、浸镀时间及工件从锌液中移出的速度。
温度过低,锌液流动性差,镀层厚且不均匀,易产生流挂,外观质量差;温度高,锌液流动性好,锌液易脱离工件,减少流挂及皱皮现象发生,附着力强,镀层薄,外观好,生产效率高;但温度过高,工件及锌锅铁损严重,产生大量锌渣,影响浸锌层质量,锌耗大,甚至无法施镀。
在同一温度下,浸镀时间长,镀层厚。
不同温度,要求同样的厚度时,高温浸镀所需时间长。
真空冶炼炉处理热镀底锌情况介绍

真空冶炼炉处理热镀底锌情况介绍我国是产锌大国,锌产量位居世界首位。
据统计,目前我国用于热镀的锌量为100余万吨。
在钢铁热镀锌过程中,锌镀层平均厚度为0.3~2.0毫米、锌附着量60~150克/平方厘米,锌的直接利用率一般在60%左右,其余则形成底锌(渣)和锌灰,一般底锌占20%左右,其中底锌由于被镀钢铁件经过酸洗后残留在镀件表面尚未漂洗干净的铁盐与热镀锌合金里锌生成的锌铁化合物,混杂有少量的铝和铅等杂质,一般为FeZn7、FeZn5 等。
表三:热镀锌的底锌、锌灰产量(公斤/吨镀件)表四:热镀锌行业底锌成分 %目前国际国内采用的蒸馏处理工艺也不同,可分为2大类:一类是生产再生金属锌锭或锌粉;另外一类是生产化工产品(氧化锌、氯化锌等锌盐),表五是目前热镀底锌的处理回收方法情况:表五:常用热镀底锌、锌灰回收方法生产工艺流程根据我们了解掌握的热镀底锌再生利用情况,再结合我公司的实际情况,我们选择是表五里的方法3 ,结合国内大学多年的研究专利成果,我们引进该所的真空冶金炉的最新技术,而且吸收了一些公司曾经成功使用真空炉处理类似物料的成功经验,以国内热镀锌厂的锌底渣为生产原料,综合回收该渣里的有用成分,变废为宝、资源综合回收再生利用,响应国家目前大力提倡的循环经济的号召。
生产工艺流程为:小块底锌→干燥→压力成型→真空炉蒸馏→锌蒸汽→冷却→锌液→铸锭→商品锌锭工艺说明:1.利用锌与铁、铝、铜等金属的熔点和沸点的不同差异,基于在一定状态下饱和蒸气压的差异, 在同一蒸馏温度和一定的真空下,蒸气压大的金属就会优先挥发, 蒸气压小的金属就会少挥发或者不挥发从而达到分离回收的目的。
2.在真空状态下,由于没有氧气成分存在,金属就不容易被氧化,特别是锌,最容易在高温条件下快速成为氧化锌。
3.蒸馏生产方法简单,灵活实用,投资节约,效益好。
锌灰是什么?锌灰的工作原理是什么?
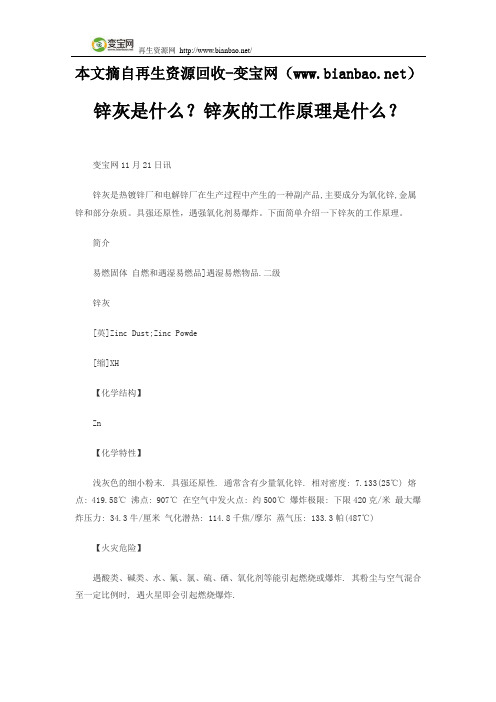
本文摘自再生资源回收-变宝网()锌灰是什么?锌灰的工作原理是什么?变宝网11月21日讯锌灰是热镀锌厂和电解锌厂在生产过程中产生的一种副产品,主要成分为氧化锌,金属锌和部分杂质。
具强还原性,遇强氧化剂易爆炸。
下面简单介绍一下锌灰的工作原理。
简介易燃固体自燃和遇湿易燃品]遇湿易燃物品.二级锌灰[英]Zinc Dust;Zinc Powde[缩]XH【化学结构】Zn【化学特性】浅灰色的细小粉末. 具强还原性. 通常含有少量氧化锌. 相对密度: 7.133(25℃) 熔点: 419.58℃沸点: 907℃在空气中发火点: 约500℃爆炸极限: 下限420克/米最大爆炸压力: 34.3牛/厘米气化潜热: 114.8千焦/摩尔蒸气压: 133.3帕(487℃)【火灾危险】遇酸类、碱类、水、氟、氯、硫、硒、氧化剂等能引起燃烧或爆炸. 其粉尘与空气混合至一定比例时, 遇火星即会引起燃烧爆炸.【处置方法】干砂、干粉;禁止用水和泡沫锌灰锌渣是热镀锌厂和电解锌厂在生产过程中产生的一种副产品,主要成分为氧化锌,金属锌和部分杂质.其中氧化锌和金属锌都有着较高的经济价值,但是必须把它们分离开才能使用.传统的处理工艺和设备污染大,回收率低,工作效率差,工作环境恶劣,处理成本高.很难达到国家环保要求.因此一般是卖给求购锌灰的商家,因为他们有专门的锌灰分离机来提取锌灰,今天我们就来认识一下锌灰分离机的工作原理:锌灰分离机工作原理:锌灰分离机由粉碎和分离及除尘三大部分组成,锌灰进入分离机后受到机械力的作用其中的金属受力变形但重量不会改变,在机器的底部被排出,杂质和氧化锌由于性质的不同受力被粉碎成很细的微粉被风机抽走排入分离器,在分离器内细粉被收集,气体被排入除尘器,经过除尘器的过滤,干净气体排入大气中.收集到的金属锌即可入炉熔炼成锌锭,细粉可直接销售或加工下游产品.更多锌灰资讯关注变宝网查阅。
本文摘自变宝网-废金属_废塑料_废纸_废品回收_再生资源B2B交易平台网站;变宝网官网网址:/newsDetail373541.html网上找客户,就上变宝网!免费会员注册,免费发布需求,让属于你的客户主动找你!。
热镀锌工艺流程及原理
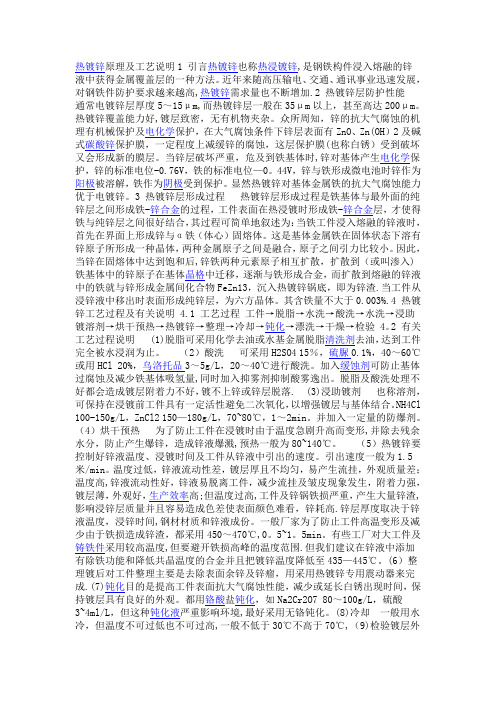
热镀锌原理及工艺说明1 引言热镀锌也称热浸镀锌,是钢铁构件浸入熔融的锌液中获得金属覆盖层的一种方法。
近年来随高压输电、交通、通讯事业迅速发展,对钢铁件防护要求越来越高,热镀锌需求量也不断增加.2 热镀锌层防护性能通常电镀锌层厚度5~15μm,而热镀锌层一般在35μm以上,甚至高达200μm。
热镀锌覆盖能力好,镀层致密,无有机物夹杂。
众所周知,锌的抗大气腐蚀的机理有机械保护及电化学保护,在大气腐蚀条件下锌层表面有ZnO、Zn(OH)2及碱式碳酸锌保护膜,一定程度上减缓锌的腐蚀,这层保护膜(也称白锈)受到破坏又会形成新的膜层。
当锌层破坏严重,危及到铁基体时,锌对基体产生电化学保护,锌的标准电位-0.76V,铁的标准电位—0。
44V,锌与铁形成微电池时锌作为阳极被溶解,铁作为阴极受到保护。
显然热镀锌对基体金属铁的抗大气腐蚀能力优于电镀锌。
3 热镀锌层形成过程热镀锌层形成过程是铁基体与最外面的纯锌层之间形成铁-锌合金的过程,工件表面在热浸镀时形成铁-锌合金层,才使得铁与纯锌层之间很好结合,其过程可简单地叙述为:当铁工件浸入熔融的锌液时,首先在界面上形成锌与α铁(体心)固熔体。
这是基体金属铁在固体状态下溶有锌原子所形成一种晶体,两种金属原子之间是融合,原子之间引力比较小。
因此,当锌在固熔体中达到饱和后,锌铁两种元素原子相互扩散,扩散到(或叫渗入)铁基体中的锌原子在基体晶格中迁移,逐渐与铁形成合金,而扩散到熔融的锌液中的铁就与锌形成金属间化合物FeZn13,沉入热镀锌锅底,即为锌渣.当工件从浸锌液中移出时表面形成纯锌层,为六方晶体。
其含铁量不大于0.003%.4 热镀锌工艺过程及有关说明 4.1 工艺过程工件→脱脂→水洗→酸洗→水洗→浸助镀溶剂→烘干预热→热镀锌→整理→冷却→钝化→漂洗→干燥→检验 4。
2 有关工艺过程说明 (1)脱脂可采用化学去油或水基金属脱脂清洗剂去油,达到工件完全被水浸润为止。
(2)酸洗可采用H2SO4 15%,硫脲0.1%,40~60℃或用HCl 20%,乌洛托品3~5g/L,20~40℃进行酸洗。
热镀锌过程锌灰
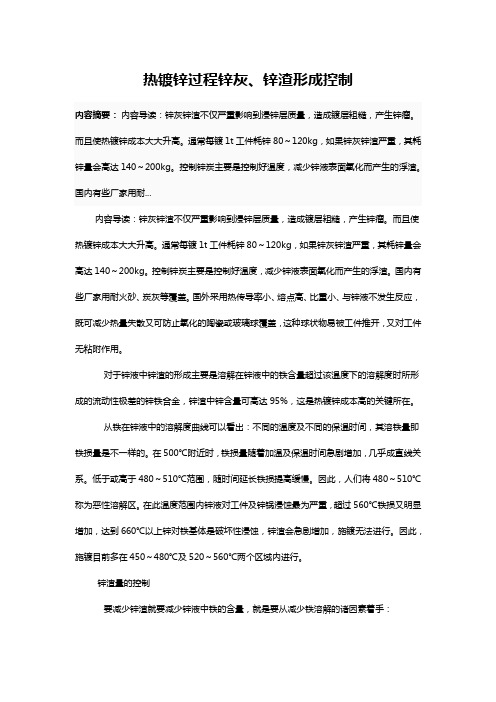
热镀锌过程锌灰、锌渣形成控制内容摘要:内容导读:锌灰锌渣不仅严重影响到浸锌层质量,造成镀层粗糙,产生锌瘤。
而且使热镀锌成本大大升高。
通常每镀1t工件耗锌80~120kg,如果锌灰锌渣严重,其耗锌量会高达140~200kg。
控制锌炭主要是控制好温度,减少锌液表面氧化而产生的浮渣。
国内有些厂家用耐...内容导读:锌灰锌渣不仅严重影响到浸锌层质量,造成镀层粗糙,产生锌瘤。
而且使热镀锌成本大大升高。
通常每镀1t工件耗锌80~120kg,如果锌灰锌渣严重,其耗锌量会高达140~200kg。
控制锌炭主要是控制好温度,减少锌液表面氧化而产生的浮渣。
国内有些厂家用耐火砂、炭灰等覆盖。
国外采用热传导率小、熔点高、比重小、与锌液不发生反应,既可减少热量失散又可防止氧化的陶瓷或玻璃球覆盖,这种球状物易被工件推开,又对工件无粘附作用。
对于锌液中锌渣的形成主要是溶解在锌液中的铁含量超过该温度下的溶解度时所形成的流动性极差的锌铁合金,锌渣中锌含量可高达95%,这是热镀锌成本高的关键所在。
从铁在锌液中的溶解度曲线可以看出:不同的温度及不同的保温时间,其溶铁量即铁损量是不一样的。
在500℃附近时,铁损量随着加温及保温时间急剧增加,几乎成直线关系。
低于或高于480~510℃范围,随时间延长铁损提高缓慢。
因此,人们将480~510℃称为恶性溶解区。
在此温度范围内锌液对工件及锌锅浸蚀最为严重,超过560℃铁损又明显增加,达到660℃以上锌对铁基体是破坏性浸蚀,锌渣会急剧增加,施镀无法进行。
因此,施镀目前多在450~480℃及520~560℃两个区域内进行。
锌渣量的控制要减少锌渣就要减少锌液中铁的含量,就是要从减少铁溶解的诸因素着手:⑴施镀及保温要避开铁的溶解高峰区,即不要在480~510℃时进行作业。
⑵锌锅材料尽可能选用含碳、含硅量低的钢板焊接。
含碳量高,锌液对铁锅浸蚀会加快,硅含量高也能促使锌液对铁的腐蚀。
目前多采用08F优质碳素钢板。
带钢表面锌灰产生的机理及控制措施

239管理及其他M anagement and other带钢表面锌灰产生的机理及控制措施马 林(唐山钢铁集团高强汽车板有限公司,河北 唐山 063000)摘 要:本文通过对连续热镀锌生产中带钢表面锌灰缺陷产生的机理进行分析与研究,得出了温度、稳定性、炉鼻子“烟囱效应”及震动是导致带钢表面粘附锌灰的主要原因的结论,并提出了有针对性的措施,在一定程度上有效减轻了带钢表面锌灰缺陷,提高了产品质量。
关键词:连续热镀锌;锌灰;锌灰泵;锌液温度中图分类号:TG335.56 文献标识码:A 文章编号:11-5004(2021)08-0239-2 收稿日期:2021-04作者简介:马林,男,生于1987年,汉族,河北唐山人,本科,工程师,研究方向:冷轧及涂镀产品质量控制。
连续热镀锌生产中,影响带钢表面质量的因素有很多,例如光整、拉矫、钝化等,而在这其中,起决定性作用的是锌锅,它是整个镀锌线的核心部分。
由于其本身原因或者控制不合理,将产生一些难以避免的缺陷,主要有锌灰、锌渣、硌窝、划伤等,而这其中影响比较大、比较常见的就是锌灰。
锌灰缺陷造成了表面质量的降判,成为影响生产高质量的镀锌板的一大难题。
本文结合生产实际,分析研究了锌灰产生的机理,对原有措施进行了一些规范、改进,以期达到减少锌灰的目的。
1 产生机理镀锌生产中使用的镀液温度基本维持在460℃左右(Zn 的熔点420℃),在此温度下,炉鼻子内的锌液面会发生在低于Zn 沸点(907℃)下的蒸发过程。
当蒸发的锌蒸汽升至一定高度后就会与炉鼻子内的水蒸汽(一方面来自于炉鼻子加湿,一方面来自H 2的还原反应)发生置换反应Zn+H 2O====ZnO+H 2生成ZnO,或者与微量的O 2发生氧化反应生成ZnO,形成锌灰。
实际生产中的锌灰是指包括ZnO 在内的、纯锌及其他一些杂质的混合物。
由于炉鼻子的烟囱效应,将锌灰“抽”到炉鼻子上部或者退火炉张力室、均衡段,进而加速了炉鼻子内锌液的蒸发,导致锌灰的大量产生[1],如图1所示。
热镀锌过程

热镀锌过程嘿,咱今儿就来唠唠热镀锌这档子事儿!你说这热镀锌啊,就好比给铁家伙们穿上一层厚厚的超级铠甲!为啥这么说呢?你想想啊,那些铁制品,暴露在外面,风吹日晒雨淋的,多可怜啊,没几天就锈迹斑斑了。
可一旦经过热镀锌这么一处理,哇塞,那可就大不一样啦!就像一个灰姑娘摇身一变成了美丽的公主。
热镀锌的过程那可是相当有趣呢!首先呢,得把那些铁制品洗得干干净净的,就跟咱人洗澡似的,得把身上的脏东西都洗掉。
这一步可不能马虎,要是洗不干净,那后面的效果可就大打折扣啦。
洗完了澡,接下来就该进“大澡堂子”啦,也就是镀锌池。
这镀锌池里的锌液啊,就像是一池神奇的魔法药水。
铁制品们在里面泡一泡,游一游,出来的时候就披上了一层银光闪闪的锌衣。
你说神奇不神奇?这时候可能有人会问啦,那这锌衣能管多久啊?嘿嘿,这锌衣可结实啦,能保护铁制品好长好长时间呢!只要不是故意去破坏它,用上好些年都没问题。
而且啊,热镀锌可不仅仅是给铁制品穿上一层保护衣这么简单。
它还能让这些铁家伙变得更漂亮呢!原本灰扑扑的,一下子就变得亮晶晶的,多好看呀!你说咱生活中哪里没有热镀锌的影子呢?那些铁栅栏、电线杆、桥架啥的,好多都是经过热镀锌处理的呢。
它们默默地守护着我们的生活,风吹雨打都不怕。
咱再想想,如果没有热镀锌这技术,那得有多少铁制品早早地就报废啦?那得浪费多少资源啊!所以说,热镀锌这技术可真是太重要啦!咱平常可能不会特别注意到这些热镀锌的制品,但它们真的无处不在,为我们的生活提供着坚实的保障。
就像那些默默付出的人一样,虽然不起眼,但却不可或缺。
热镀锌,看似简单的一个过程,却蕴含着大大的能量和智慧。
它让铁制品变得更耐用、更美观,也让我们的生活更加美好。
所以啊,咱可得好好感谢这热镀锌技术,让我们的世界变得更加精彩!这就是热镀锌,一个神奇又实用的过程,你说棒不棒?原创不易,请尊重原创,谢谢!。
镀锌板表面锌灰成因及控制
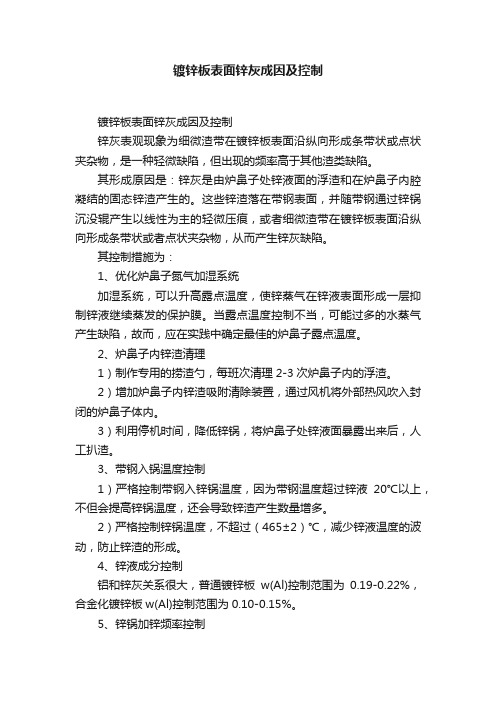
镀锌板表面锌灰成因及控制
镀锌板表面锌灰成因及控制
锌灰表观现象为细微渣带在镀锌板表面沿纵向形成条带状或点状夹杂物,是一种轻微缺陷,但出现的频率高于其他渣类缺陷。
其形成原因是:锌灰是由炉鼻子处锌液面的浮渣和在炉鼻子内腔凝结的固态锌渣产生的。
这些锌渣落在带钢表面,并随带钢通过锌锅沉没辊产生以线性为主的轻微压痕,或者细微渣带在镀锌板表面沿纵向形成条带状或者点状夹杂物,从而产生锌灰缺陷。
其控制措施为:
1、优化炉鼻子氮气加湿系统
加湿系统,可以升高露点温度,使锌蒸气在锌液表面形成一层抑制锌液继续蒸发的保护膜。
当露点温度控制不当,可能过多的水蒸气产生缺陷,故而,应在实践中确定最佳的炉鼻子露点温度。
2、炉鼻子内锌渣清理
1)制作专用的捞渣勺,每班次清理2-3次炉鼻子内的浮渣。
2)增加炉鼻子内锌渣吸附清除装置,通过风机将外部热风吹入封闭的炉鼻子体内。
3)利用停机时间,降低锌锅,将炉鼻子处锌液面暴露出来后,人工扒渣。
3、带钢入锅温度控制
1)严格控制带钢入锌锅温度,因为带钢温度超过锌液20℃以上,不但会提高锌锅温度,还会导致锌渣产生数量增多。
2)严格控制锌锅温度,不超过(465±2)℃,减少锌液温度的波动,防止锌渣的形成。
4、锌液成分控制
铝和锌灰关系很大,普通镀锌板w(Al)控制范围为0.19-0.22%,合金化镀锌板w(Al)控制范围为0.10-0.15%。
5、锌锅加锌频率控制
锌液面下降,会造成炉鼻子内部浮渣黏附在炉鼻子内墙上,因此要根据锌液消耗速度合理制定加锌频率,防止锌液面上下波动过大而使浮渣在炉鼻子内壁越聚越多。
热镀锌工艺
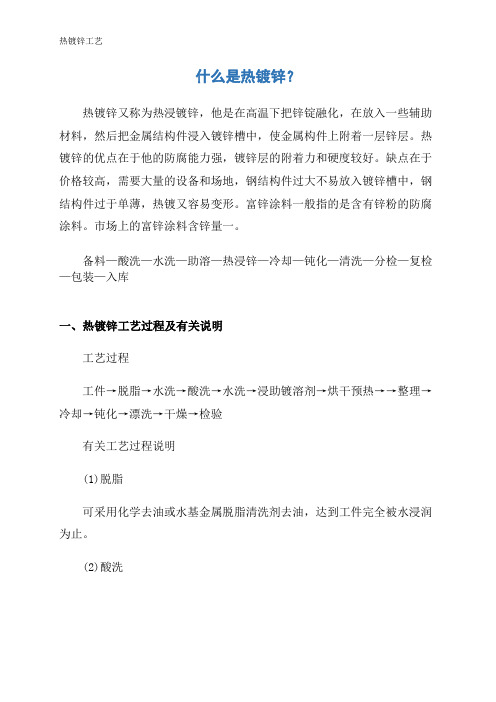
什么是热镀锌?热镀锌又称为热浸镀锌,他是在高温下把锌锭融化,在放入一些辅助材料,然后把金属结构件浸入镀锌槽中,使金属构件上附着一层锌层。
热镀锌的优点在于他的防腐能力强,镀锌层的附着力和硬度较好。
缺点在于价格较高,需要大量的设备和场地,钢结构件过大不易放入镀锌槽中,钢结构件过于单薄,热镀又容易变形。
富锌涂料一般指的是含有锌粉的防腐涂料。
市场上的富锌涂料含锌量一。
备料—酸洗—水洗—助溶—热浸锌—冷却—钝化—清洗—分检—复检—包装—入库一、热镀锌工艺过程及有关说明工艺过程工件→脱脂→水洗→酸洗→水洗→浸助镀溶剂→烘干预热→→整理→冷却→钝化→漂洗→干燥→检验有关工艺过程说明(1)脱脂可采用化学去油或水基金属脱脂清洗剂去油,达到工件完全被水浸润为止。
(2)酸洗可采用H2SO4 15%,硫脲0.1%,40~60℃或用HCl 20%,六次甲基四胺1~3g/L,20~40℃进行酸洗。
加入缓蚀剂可防止基体过腐蚀及减少铁基体吸氢量。
脱脂及酸洗处理不好会造成镀层附着力不好,镀不上锌或锌层脱落。
(3)浸助镀剂也称结合剂,可保持在浸镀前工件具有一定活性,以增强镀层与基体结合。
NH4Cl 15%~25%,ZnCl2 2.5%~3.5%,55~65℃,5~10min。
为减少NH4Cl挥发可适当加入甘油。
(4)烘干预热为了防止工件在浸镀时由于温度急剧升高而变形,并除去残余水分,防止产生爆锌,造成锌液爆溅,预热一般为120~180℃。
(5)热镀锌要控制好锌液温度、浸镀时间及工件从锌液中移出的速度。
温度过低,锌液流动性差,镀层厚且不均匀,易产生流挂,外观质量差;温度高,锌液流动性好,锌液易脱离工件,减少流挂及皱皮现象发生,附着力强,镀层薄,外观好,生产效率高;但温度过高,工件及锌锅铁损严重,产生大量锌渣,影响浸锌层质量,锌耗大,甚至无法施镀。
在同一温度下,浸镀时间长,镀层厚。
不同温度,要求同样的厚度时,高温浸镀所需时间长。
一般厂家为了防止工件高温变形及减少由于铁损造成锌渣,都采用450~470℃,0.5~1.5min。
- 1、下载文档前请自行甄别文档内容的完整性,平台不提供额外的编辑、内容补充、找答案等附加服务。
- 2、"仅部分预览"的文档,不可在线预览部分如存在完整性等问题,可反馈申请退款(可完整预览的文档不适用该条件!)。
- 3、如文档侵犯您的权益,请联系客服反馈,我们会尽快为您处理(人工客服工作时间:9:00-18:30)。
热镀锌过程锌灰、锌渣形成控制
内容摘要:内容导读:锌灰锌渣不仅严重影响到浸锌层质量,造成镀层粗糙,产生锌瘤。
而且使热镀锌成本大大升高。
通常每镀1t工件耗锌80~120kg,如果锌灰锌渣严重,其耗锌量会高达140~200kg。
控制锌炭主要是控制好温度,减少锌液表面氧化而产生的浮渣。
国内有些厂家用耐...
内容导读:锌灰锌渣不仅严重影响到浸锌层质量,造成镀层粗糙,产生锌瘤。
而且使热镀锌成本大大升高。
通常每镀1t工件耗锌80~120kg,如果锌灰锌渣严重,其耗锌量会高达140~200kg。
控制锌炭主要是控制好温度,减少锌液表面氧化而产生的浮渣。
国内有些厂家用耐火砂、炭灰等覆盖。
国外采用热传导率小、熔点高、比重小、与锌液不发生反应,既可减少热量失散又可防止氧化的陶瓷或玻璃球覆盖,这种球状物易被工件推开,又对工件无粘附作用。
对于锌液中锌渣的形成主要是溶解在锌液中的铁含量超过该温度下的溶解度时所形成的流动性极差的锌铁合金,锌渣中锌含量可高达95%,这是热镀锌成本高的关键所在。
从铁在锌液中的溶解度曲线可以看出:不同的温度及不同的保温时间,其溶铁量即铁损量是不一样的。
在500℃附近时,铁损量随着加温及保温时间急剧增加,几乎成直线关系。
低于或高于480~510℃范围,随时间延长铁损提高缓慢。
因此,人们将480~510℃称为恶性溶解区。
在此温度范围内锌液对工件及锌锅浸蚀最为严重,超过560℃铁损又明显增加,达到660℃以上锌对铁基体是破坏性浸蚀,锌渣会急剧增加,施镀无法进行。
因此,施镀目前多在450~480℃及520~560℃两个区域内进行。
锌渣量的控制
要减少锌渣就要减少锌液中铁的含量,就是要从减少铁溶解的诸因素着手:
⑴施镀及保温要避开铁的溶解高峰区,即不要在480~510℃时进行作业。
⑵锌锅材料尽可能选用含碳、含硅量低的钢板焊接。
含碳量高,锌液对铁锅浸蚀会加快,硅含量高也能促使锌液对铁的腐蚀。
目前多采用08F优质碳素钢板。
其含碳
0.087%(0.05%~0.11%),含硅≤0.03%,并含有能抑制铁被浸蚀的元素镍、铬等。
不可用普通碳素钢,否则耗锌量大,锌锅寿命短。
也有人提出用碳化硅制作熔锌槽,虽然可解决铁损量,但造型工艺也是一个难题。
⑶要经常捞渣。
先将温度升高至工艺温度上限以便锌渣与锌液分离,然后降至工艺温度以下,使锌渣沉于槽底后用勺捞取。
落入锌液中镀件也要及时打捞。
⑷要防止助镀剂中铁随工件带入锌槽,助镀剂使用一定时间就有红褐色含铁的化合物生成,要定期滤去。
助镀剂pH值维护在5左右为好
⑸镀液中铝少于0.01%会加快沉渣的生成,适量铝不仅提高锌液的流动性,增加镀层亮度,而且有利于减少锌渣、锌灰。
少量铝浮在液面对减少氧化有益,过多影响镀层质量,产生缺斑现象。
⑹加热、升温要均匀,防止爆烧及局部过热。