设备管理知识
设备管理岗位应知应会知识
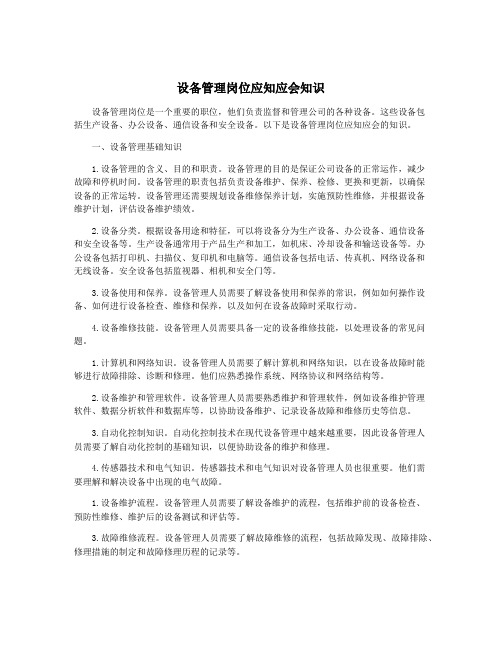
设备管理岗位应知应会知识设备管理岗位是一个重要的职位,他们负责监督和管理公司的各种设备。
这些设备包括生产设备、办公设备、通信设备和安全设备。
以下是设备管理岗位应知应会的知识。
一、设备管理基础知识1.设备管理的含义、目的和职责。
设备管理的目的是保证公司设备的正常运作,减少故障和停机时间。
设备管理的职责包括负责设备维护、保养、检修、更换和更新,以确保设备的正常运转。
设备管理还需要规划设备维修保养计划,实施预防性维修,并根据设备维护计划,评估设备维护绩效。
2.设备分类。
根据设备用途和特征,可以将设备分为生产设备、办公设备、通信设备和安全设备等。
生产设备通常用于产品生产和加工,如机床、冷却设备和输送设备等。
办公设备包括打印机、扫描仪、复印机和电脑等。
通信设备包括电话、传真机、网络设备和无线设备。
安全设备包括监视器、相机和安全门等。
3.设备使用和保养。
设备管理人员需要了解设备使用和保养的常识,例如如何操作设备、如何进行设备检查、维修和保养,以及如何在设备故障时采取行动。
4.设备维修技能。
设备管理人员需要具备一定的设备维修技能,以处理设备的常见问题。
1.计算机和网络知识。
设备管理人员需要了解计算机和网络知识,以在设备故障时能够进行故障排除、诊断和修理。
他们应熟悉操作系统、网络协议和网络结构等。
2.设备维护和管理软件。
设备管理人员需要熟悉维护和管理软件,例如设备维护管理软件、数据分析软件和数据库等,以协助设备维护、记录设备故障和维修历史等信息。
3.自动化控制知识。
自动化控制技术在现代设备管理中越来越重要,因此设备管理人员需要了解自动化控制的基础知识,以便协助设备的维护和修理。
4.传感器技术和电气知识。
传感器技术和电气知识对设备管理人员也很重要。
他们需要理解和解决设备中出现的电气故障。
1.设备维护流程。
设备管理人员需要了解设备维护的流程,包括维护前的设备检查、预防性维修、维护后的设备测试和评估等。
3.故障维修流程。
关于设备管理的基本知识
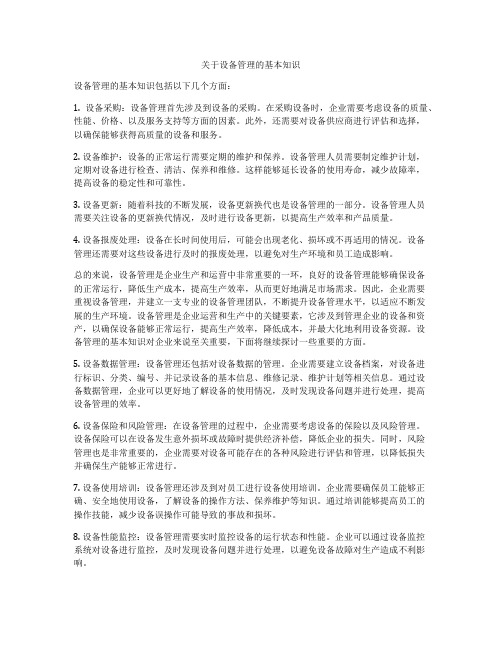
关于设备管理的基本知识设备管理的基本知识包括以下几个方面:1. 设备采购:设备管理首先涉及到设备的采购。
在采购设备时,企业需要考虑设备的质量、性能、价格、以及服务支持等方面的因素。
此外,还需要对设备供应商进行评估和选择,以确保能够获得高质量的设备和服务。
2. 设备维护:设备的正常运行需要定期的维护和保养。
设备管理人员需要制定维护计划,定期对设备进行检查、清洁、保养和维修。
这样能够延长设备的使用寿命,减少故障率,提高设备的稳定性和可靠性。
3. 设备更新:随着科技的不断发展,设备更新换代也是设备管理的一部分。
设备管理人员需要关注设备的更新换代情况,及时进行设备更新,以提高生产效率和产品质量。
4. 设备报废处理:设备在长时间使用后,可能会出现老化、损坏或不再适用的情况。
设备管理还需要对这些设备进行及时的报废处理,以避免对生产环境和员工造成影响。
总的来说,设备管理是企业生产和运营中非常重要的一环,良好的设备管理能够确保设备的正常运行,降低生产成本,提高生产效率,从而更好地满足市场需求。
因此,企业需要重视设备管理,并建立一支专业的设备管理团队,不断提升设备管理水平,以适应不断发展的生产环境。
设备管理是企业运营和生产中的关键要素,它涉及到管理企业的设备和资产,以确保设备能够正常运行,提高生产效率,降低成本,并最大化地利用设备资源。
设备管理的基本知识对企业来说至关重要,下面将继续探讨一些重要的方面。
5. 设备数据管理:设备管理还包括对设备数据的管理。
企业需要建立设备档案,对设备进行标识、分类、编号、并记录设备的基本信息、维修记录、维护计划等相关信息。
通过设备数据管理,企业可以更好地了解设备的使用情况,及时发现设备问题并进行处理,提高设备管理的效率。
6. 设备保险和风险管理:在设备管理的过程中,企业需要考虑设备的保险以及风险管理。
设备保险可以在设备发生意外损坏或故障时提供经济补偿,降低企业的损失。
同时,风险管理也是非常重要的,企业需要对设备可能存在的各种风险进行评估和管理,以降低损失并确保生产能够正常进行。
关于设备管理的基本知识

关于设备管理的基本知识设备管理是指对设备从采购、使用、维护、更新直至报废的全生命周期进行的管理。
以下是关于设备管理的基本知识:1.设备采购设备采购是设备管理的起始环节,也是关键环节之一。
在采购设备时,需要考虑设备的性能、可靠性、效率、成本等多个方面,以确保购买的设备能够满足企业的生产需求并具备合理的投资回报。
在采购过程中,还需要对供应商进行评估和选择,确保购买的设备具备优良的质量和售后服务。
2.设备使用设备使用是设备管理的另一个关键环节。
在使用设备时,需要确保设备的安全性和可靠性,避免因使用不当导致的设备损坏或事故。
同时,还需要对设备进行合理的维护和保养,以延长设备的使用寿命和降低维修成本。
3.设备维护设备维护是设备管理的重要环节之一。
通过对设备进行定期的检修、保养、润滑等工作,可以及时发现和解决设备存在的问题,避免设备出现突发故障。
同时,合理的维护也可以提高设备的效率和可靠性,降低企业的生产成本。
4.设备更新随着技术的不断进步和企业生产需求的不断提高,有时需要对设备进行更新。
在设备更新时,需要考虑设备的性能、效率、可靠性等多个方面,以确保更新的设备能够满足企业的生产需求并具备合理的投资回报。
同时,还需要考虑设备的环保性和节能性,以符合国家的相关政策要求。
5.设备报废当设备已经达到报废条件时,需要对设备进行报废处理。
在报废过程中,需要考虑设备的再利用价值、对环境的影响等多个方面,以选择最合理的报废方式。
同时,还需要对报废的设备进行清理和销毁,以确保不会对企业和环境造成不良影响。
总之,设备管理是一个全生命周期的管理过程,需要从设备的采购、使用、维护、更新直至报废进行全面的管理和考虑。
通过对设备的科学管理,可以提高设备的效率和可靠性,降低企业的生产成本,促进企业的可持续发展。
同时,还需要不断引进先进的管理方法和手段,如数字化管理、智能化管理等,以提高设备管理的效率和精度。
关于设备管理的基本知识

(1)优点:租赁与购买相比,可以减少企业 的长期资本支出,减少贷款利息,及时取得 生产所需设备,并减少设备陈旧过失的风险。 (2)缺点:由于设备租赁只能根据合同规定 取得租赁期内的设备使用权,无权根据生产 需要对设备进行改造;租赁期限有一定要求, 一般不得低于两年;设备租赁的租金总额可 能高于设备购置价格。
优点:充分利用零部件的使用期限,修理费用较低。
缺点:不易做好修理前的准备工作,延长设备停歇时 间。
(二)全员生产维修制(TPM)
日本在学习欧美先进维修经验的基础上,结合本国企 业管理的特色,建立起来的一种较完整的设备管理和 维修制度。
1、基本思想 ①全效益; ②全系统; ③全员参加。 2、主要内容 ①日常点检; ②定期检查; ③计划修理; ④改善性修理; ⑤故障修理; ⑥维修记录分析; ⑦开展“5S”活动
第三节 设备的后期管理
一、设备的合理使用 1、设备的合理配置; 2、适当安排生产任务; 3、协调好设备与操作者的关系; 4、创造良好的设备使用环境; 5、建立和健全设备合理使用的各项规 章制度; 6、教育职工增强正确使用和爱护设备 的意识。
二、设备的磨损与故障规律 (一)设备的磨损理论 1、设备的有形磨损 ①使用磨损 ②自然磨损 ★有形磨损曲线
1、概念:根据零部件的磨损规律和设备的故 障规律,有计划地进行维修,在故障发生之 前修复或更换已磨损或老化的零部件。
2、内容:①日常维护;
②定期清洗换油;
③定期检查;
④计划修理:A、小修
B、中修
C、大修
★设备大修理的经济合理性研究
1、通常零部件所受损耗很不均匀,人们常对部分零 部件进行修理和更换。在一定条件下,修理和更换部 分零部件比重新购置设备要经济得多。
设备管理基础理论知识

设备管理基础理论知识1. 设备生命周期管理:设备管理需要关注设备的整个生命周期,包括设备的采购、安装、维护、更新、报废等各个阶段。
对设备进行全面的生命周期管理能够有效地延长设备的使用寿命,提高设备的利用率,降低设备维护和更换的成本。
2. 设备管理的优化思路:设备管理包括对设备的使用方式、维护方式、更新方式等方面的优化。
通过对设备管理进行优化,可以提高设备的使用效率,减少故障发生率,提高设备的可靠性和安全性。
3. 设备管理的风险管理:设备管理需要关注设备可能出现的各种风险,包括设备失效、设备安全、设备环境等各个方面的风险。
通过对风险的认识和分析,可以制定相应的应对措施,最大限度地减少设备管理过程中的风险。
4. 设备管理的信息化:现代设备管理已经逐渐向信息化方向发展,通过信息化手段可以实现设备管理的自动化、智能化,提高设备管理的效率和准确性。
5. 设备管理的绩效评价:设备管理需要建立适当的绩效评价体系,根据设备管理的目标和指标对设备管理的效果进行评价,及时调整和优化设备管理的策略和方法。
总之,设备管理的基础理论知识是设备管理人员必须要掌握的,只有深刻理解这些基础理论知识,才能更好地实施设备管理工作,提高设备的使用效率和可靠性,降低企业的设备管理成本。
设备管理的基础理论知识是设备管理工作的重要基础,深入了解这些理论知识对于设备管理人员来说至关重要。
在设备管理工作中,需要关注以下几个方面的内容:6. 设备管理的规划:设备管理的规划需要考虑企业的发展战略、市场需求、技术发展趋势等因素,制定适合企业实际情况的设备管理规划。
规划要求对当前设备的使用情况和未来设备需求进行全面的分析和调研,最终确定科学合理的设备管理规划。
7. 设备管理的组织:设备管理需要建立一套科学的、完善的组织体系,明确设备管理的职责和权限,确保设备管理工作的顺利进行。
合理的组织体系可以确保设备管理工作有序进行,有效地协调各个部门之间的工作。
设备管理常用知识总结

一、关于设备故障知识1、故障的含义故障——设备在运行过程中,丧失或降低其规定的功能及不能继续运行的现象。
2、故障的类型故障可以不同角度分:1)临时性故障2)永久性故障按故障发生的时间分有以下几种:1)早发性故障2)突发性故障3)渐进性故障4)复合型故障按故障表现形式分有:1)功能故障2)潜在故障按故障产生的原因分有:1)人为故障2)自然故障按故障造成的后果分有:1)致命故障2)严重故障3)一般故障4)轻度故障故障通常采取几种分类法复合并用,如突发性的局部故障;磨损性的危险故障等,由此看出故障的复杂性、严重性和起因等情况。
3、故障的特点1)多样性2)层次性3)多因素和相关性4)延时性5)不确定性6)修复性4、故障管理故障管理是设备管理的核心内容之一。
其目的在于早期发现故障征兆,及时采取措施进行预防和维修。
故障管理的程序和内容包括:1)设备加工工艺和技术培训相结合。
2)制定严禁的设备管理制度和预防性维护制度。
3)熟悉机械设备结构和工作原理,掌握工作性能。
4)配置先进的检查、检测和监测设备,对重要设备和零部件进行实时监测,定期分析,准确掌握设备故障的信息和征兆。
5)根据故障现象和信息及征兆,进行认真科学地分析,确定故障原因、类型、采取最佳的维修策略和维修方案,及时维修过程进行记录。
提供后期统计和借鉴。
6)对常发生或多次重复出现的故障的部位或零件,要重点监测,必要时对其进行系统技术改造。
影响故障产生的主要因素1)制造和修理因素对故障的影响a 零件材料的选择b 零件加工质量c 装配质量2)使用因素对故障的影响a 工作负荷b 工作环境c 设备保养和操作技术二、设备管理的11个指标在企业里,用于度量设备管理好坏的指标很多。
例如设备的完好率,设备的可用率,设备综合效率,设备完全有效生产率,设备故障率,平均故障间隔期,平均修理时间,设备备件库存周转率,备件资金率,维修费用率,检修质量一次合格率,返修率等等。
不同的指标用于度量不同的管理方向。
设备管理知识

1.管理概述1.1设备的定义及范畴:设备是企业的主要生产工具,也是企业现代化水平的重要标志。
设备既是发展国民经济的物质技术基础,又是衡量社会发展水平与物质文明程度的重要尺度。
设备是固定资产的重要组成部分。
国外设备工程学把设备定义为“有形固定资产的总称”,它把一切列入固定资产的劳动资料,如土地、建筑物(厂房、仓库等)、构筑物(水池、码头、围墙、道路等)、机器(工作机械、运输机械等)、装臵(容器、蒸馏塔、热交换器等),以及车辆、船舶、工具(工夹具、测试仪器等)等都包含在其中了。
在我国,只把直接或间接参与改变劳动对象的形态和性质的物质资料才看作设备。
一般认为,设备是人们在生产或生活上所需的机械、装臵和设施等可供长期使用,并在使用中基本保持原有实物形态的物质资料。
1.2设备在工业企业中的地位1)机器设备是现代企业的物质技术基础机器设备是现代企业进行生产活动的物质技术基础,也是企业生产力发展水平与企业现代化程度的主要标志。
没有机器设备就没有现代化的大生产,也就没有现代化的企业。
(2)设备是企业固定资产的主体企业是自主经营、自负盈亏、独立核算的商品生产和经营单位。
生产经营是“将本就利”,这个“本”就是企业所拥有的固定资产和流动资金。
在企业的固定资产总额中,机器设备的价值所占的比例最大,一般都在60%~70%。
而且随着机器设备的技术含量与技术水平日益提高,现代设备既是技术密集型的生产工具,也是资金密集型的社会财富。
设计制造或者购臵现代设备费用的增加,不仅会带来企业固定资产总额的增加,还会继续增大机器设备在固定资产总额中的比重。
设备的价值是企业资本的“大头”,对企业的兴衰关系重大。
(3)机器设备涉及企业生产经营活动的全局企业作为商品的生产、经营单位,必须树立市场观念、质量观念、时间观念、效益观念,以适销对路、物美价廉的产品赢得用户,占领市场,才能取得良好的经济效益,求得企业的生存和发展。
在企业从产品市场调查―组织生产―经营销售的管理循环过程中,机器设备处于十分重要的地位,影响着企业生产经营活动的全局。
设备管理应知应会知识-全员
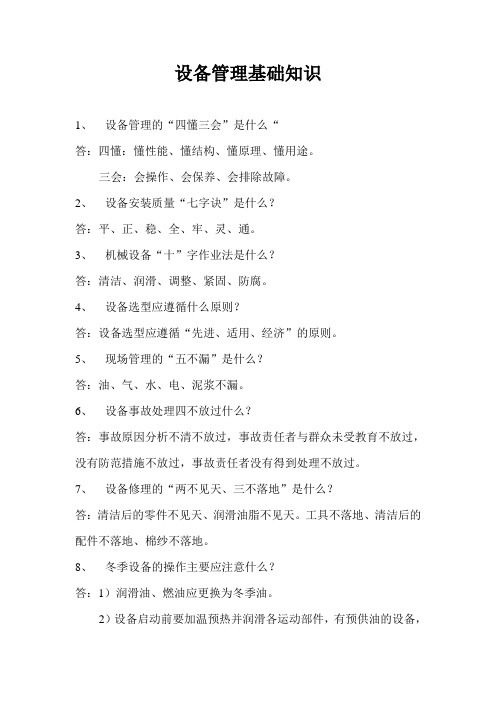
设备管理基础知识1、设备管理的“四懂三会”是什么“答:四懂:懂性能、懂结构、懂原理、懂用途。
三会:会操作、会保养、会排除故障。
2、设备安装质量“七字诀”是什么?答:平、正、稳、全、牢、灵、通。
3、机械设备“十”字作业法是什么?答:清洁、润滑、调整、紧固、防腐。
4、设备选型应遵循什么原则?答:设备选型应遵循“先进、适用、经济”的原则。
5、现场管理的“五不漏”是什么?答:油、气、水、电、泥浆不漏。
6、设备事故处理四不放过什么?答:事故原因分析不清不放过,事故责任者与群众未受教育不放过,没有防范措施不放过,事故责任者没有得到处理不放过。
7、设备修理的“两不见天、三不落地”是什么?答:清洁后的零件不见天、润滑油脂不见天。
工具不落地、清洁后的配件不落地、棉纱不落地。
8、冬季设备的操作主要应注意什么?答:1)润滑油、燃油应更换为冬季油。
2)设备启动前要加温预热并润滑各运动部件,有预供油的设备,要先使用预供油泵,待润滑油的压力上升到一定数值后方可启动。
3)注意防冻。
不加防冻液的设备停用时要及时放净冷却水。
10、钻机有哪八大系统?答:1、起升系统2、旋转系统3、循环系统4、动力设备5、传动系统6、控制系统7、底座8、辅助设备11、润滑系统按质换油有什么好处?答:可使机构传动系统处在良好的润滑状态下运转,并能够节约能源12、对发动机使用的软化水如何处理?答:主要采用离子交换的方法,利用软化水处理装置除去钙镁盐,降低硬度后再加入3~4‰百克灵801B型13、什么是设备管理的三定?答:定人、定机、定岗14、什么叫润滑工作的“五定”“三过滤“?答:五定:(1)定点(2)定质(3)定量(4)定期(5)定人三过滤:(1)入库过滤(2)发放过滤(3)加油过滤15、防冻液的主要功能?答:1、较低的冰点。
2、较高的沸点3、良好的抗腐蚀性能4、良好的安定性。
16、润滑脂的主要性能?答:1、稠度2、塑性3、机械安定性好4、析油率低、胶体安定型好5、良好的高低温性能6、抗水性7、极压性8、水分9、防腐防锈性17、油品的管理使用应做到什么?答:品质把关、专罐专储,专罐专输、沉淀过滤、密闭输送、对路实用、定期化验、按质换油、再生利用。
设备管理知识设备管理知识

设备管理知识设备管理知识1.管理概述1.1如何理解设备的含义?设备是人们在生产或生活上所需的机械、装置和设施等可供长期使用,并在使用中基本保持原有实物形态的物质资料,是固定资产的主要组成部分。
国外设备工程学把设备定义为“有形固定资产的总称”,它把一切列入固定资产的劳动资料,如土地、建筑物(厂房、仓库等)、构筑物(水池、码头、围墙、道路等)、机器(工作机械、运输机械等)、装置(容器、蒸馏塔、热交换器等),以及车辆、船舶、工具(工夹具、测试仪器等)等都包含在其中了。
在我国,只把直接或间接参与改变劳动对象的形态和性质的物质资料才看作设备。
1.2什么是生产设备?生产设备是指直接或间接参加生产过程的设备,它是企业固定资产的主要组成部分。
从这一定义出发,生产设备必须是直接作用于加工对象,使之改变物质形态或化学成份,而转化为一定的工业产品的设备或辅助完成产品加工的设备。
1.3什么是生产技术装备素质?6 M9 U- S% i3 y: w' X$ L! d生产技术装备是生产设备、试验设备、仪器仪表与工艺装备(包括刀具、夹具、量具、模具、检具和工位器具等)的总称。
生产技术装备的素质是指在技术进步条件下,技术装备适应企业生产和技术发展的内在品质,也就是指企业技术装备水平的高低和技术状况的优劣。
通常包括以下几项:(1)工艺适用性、(2)质量稳定性、(3)技术先进性、(4)运行可靠性、(5)机械化、自动化程度。
1.4完好设备的要求是什么?完好设备的要求一般说来有以下四条:①设备性能良好:机械设备精度、性能能满足相应水平产品的生产工艺要求;动力设备功能达到原设计或法定运行标准;运转无超温、超压和其他超额定负荷现象。
②设备运转正常:零部件齐全,磨损、蚀耗程度不超过规定技术标准;操纵和控制系统,计量仪器、仪表、液压、气压、润滑和冷却系统,工作正常可靠。
8 N0 g9 u) V" I4 N# d: m9 Z③消耗原材料、燃料、油料、动能等正常,基本无漏油、漏水、漏气(汽)、漏电现象,外表清洁整齐。
设备管理基本知识

2、针对性强;
3、适应性广;
4、经济性好。
对设备员的基本要求
责任心强,对设备参数、内部结构要熟悉
维 备修 件设 和备 分, 析Ev设损al备坏ua员的tio必原n须因on在,ly现并. 场寻,找确 预认 防更 对换 策的 eated withCAo熟 对sppy悉 车orsi设 间ge.h备 特Stl部 种2id0e下设0s4发备f-o2的要r0.1管关N1E理注ATs制p3o度.5s和eCP操litey作nLt规tPd程r.of等ile 5.2.0
2.1 设备选型与购置
★设备部采购设备必须有申报部门的申请报告, 且经厂级领导签字确认 。
申请报告的内容必须包含与设备相关的全部参
数。 Evaluation only.
eated with★A设sp备os部e.根Sl据ide申s 请fo报r .告NE中T的3相.5关C参lie数nt进Pr行of设ile备5选.2.0 Co型py。right 2004-2011 Aspose Pty Ltd.
部现场验收Ev人al员ua和tio使n用on部ly门. 负责人签字、经 eated with A设sp备os部e.主Sl管ide领s导fo签r .字NE后T方3可.5入C库lien。t Profile 5.2.0
★Co经py验ri收gh,t 2质00量4、-2数01量1 A、s性po能se、P技ty术L条td件. 和图
前修复或更Ev换a已lua磨ti损on或o老nly化. 的零部件。
eated withA2s、p内os容e.S:li①de日s f常or维.N护E;T 3.5 Client Profile 5.2.0
Copyright 2②00定4期-20清1洗1 A换s油po;se Pty Ltd.
设备管理基础知识

设备管理基础知识1、设备管理三定:定人、定机、定岗位2、设备生产维护的四项要求整齐、安全、清洁、润滑良好。
3、设备的维护保养的主要工作检修、保养、维护性修理。
4、设备三全管理:全面管理;全员管理;全过程管理5、设备选型三原则:技术上先进;经济上合理;生产上适用6、设备管理三级网络体系:一级:公司级;二级:车间级;三级:班组级7,设备检修和维护三严:严格执行检修计划和检修规程;严把备件质量关;严格抓好检修质量和完工验收关8,安全运行三个坚持:坚持交接班制度;坚持持证上岗;坚持抓好安全、工艺和劳动三纪9,三级保养:日常维护保养(日保);一级保养(月保);二级保养(年保)10,设备的5个条件:①完成任务好、安全、出勤率高;②设备性能好、零件、部件完整齐全;③设备马力达到规定要求;④搞好设备清洁、润滑、扭紧、调整和防腐;⑤设备使用和管理基础资料齐全、准确11,设备操作三好、四懂、四会①三好:管好、用好、修好②四懂:懂原理、懂构造、懂性能、懂用途③四会:会使用、会保养、会检查、会排除故障12,设备修理二不见天、三不落地①二不见天:油料不见天,清洗过的机件不见天②三不落地:油料、机件、工具三不落地13,设备使用5项纪律:①凭操作证使用设备,遵守安全操作规程;②经常保持设备清洁,并按规定加油;③遵守设备交接班制度;④管好工具、附件、不得遗失;⑤发现异常现象,应立即停车检查14,设备管理八字方针:安全、可靠、经济、合理15,设备三验收:开箱验收、试运行验收、最终验收16,设备检查五字操作法:看、查、摸、听、闻17,润滑五定:定人、定部位、定时间、定品种、定油量18,润滑三过滤:①从领油大桶到贮油箱为一级过滤;②从贮油箱到油壶为二级过滤;③从油壶到各润滑部位为三级过滤19,三位一体点检:①岗位操作员的日常点检;②专业点检员的定期点检;③专业技术人员的精密点检20,修理的四个一次成功:一次解体、一次备料、一次组装、一次验收成功21、设备三检制:操作手自检;修理工配合的互检;检验员的专职检查22、设备修保使用中的四不漏:不漏电、不漏油、不漏气、不漏水23、设备管理管理发展的三个阶段:事后维修阶段,预防性定期修理阶段,综合性管理阶段。
设备管理的基本知识
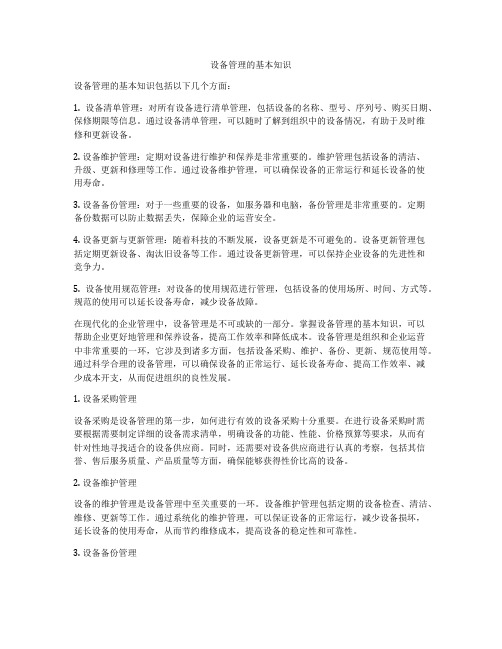
设备管理的基本知识设备管理的基本知识包括以下几个方面:1. 设备清单管理:对所有设备进行清单管理,包括设备的名称、型号、序列号、购买日期、保修期限等信息。
通过设备清单管理,可以随时了解到组织中的设备情况,有助于及时维修和更新设备。
2. 设备维护管理:定期对设备进行维护和保养是非常重要的。
维护管理包括设备的清洁、升级、更新和修理等工作。
通过设备维护管理,可以确保设备的正常运行和延长设备的使用寿命。
3. 设备备份管理:对于一些重要的设备,如服务器和电脑,备份管理是非常重要的。
定期备份数据可以防止数据丢失,保障企业的运营安全。
4. 设备更新与更新管理:随着科技的不断发展,设备更新是不可避免的。
设备更新管理包括定期更新设备、淘汰旧设备等工作。
通过设备更新管理,可以保持企业设备的先进性和竞争力。
5. 设备使用规范管理:对设备的使用规范进行管理,包括设备的使用场所、时间、方式等。
规范的使用可以延长设备寿命,减少设备故障。
在现代化的企业管理中,设备管理是不可或缺的一部分。
掌握设备管理的基本知识,可以帮助企业更好地管理和保养设备,提高工作效率和降低成本。
设备管理是组织和企业运营中非常重要的一环,它涉及到诸多方面,包括设备采购、维护、备份、更新、规范使用等。
通过科学合理的设备管理,可以确保设备的正常运行、延长设备寿命、提高工作效率、减少成本开支,从而促进组织的良性发展。
1. 设备采购管理设备采购是设备管理的第一步,如何进行有效的设备采购十分重要。
在进行设备采购时需要根据需要制定详细的设备需求清单,明确设备的功能、性能、价格预算等要求,从而有针对性地寻找适合的设备供应商。
同时,还需要对设备供应商进行认真的考察,包括其信誉、售后服务质量、产品质量等方面,确保能够获得性价比高的设备。
2. 设备维护管理设备的维护管理是设备管理中至关重要的一环。
设备维护管理包括定期的设备检查、清洁、维修、更新等工作。
通过系统化的维护管理,可以保证设备的正常运行,减少设备损坏,延长设备的使用寿命,从而节约维修成本,提高设备的稳定性和可靠性。
设备管理基础知识
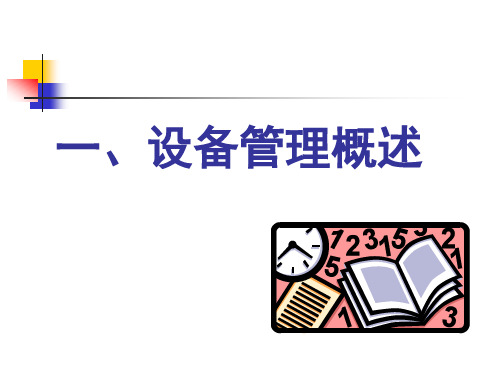
日常维护保养
保养人:操作工人
要点: 班前检查 加油润滑 随手清洁
处理异常 班后维护 真实记录
坚持不懈 周末养护
日常维护保养规范
三级维护保养制
日常维护保养(日保) 一级保养(一保)
一级保养
保养人:操作工人(主)+维修工人(辅)
要 点:定期计划 重点拆解 清洗检查
生; 可以延长设备的使用寿命; 可以提高设备的使用效率。
1. 如何正确合理使用设备?
合理配置;
合理配置设备
配套性; 平衡性; 适当柔性。
1. 如何正确合理使用设备?
合理配置; 合理安排生产;
1. 如何正确合理使用设备?
合理配置; 合理安排生产; 加强工艺管理;
加强工艺管理
定周期:确定点检的周期(检查点在生产和 安全上的重要性以及生产工艺特点并结合维 修经验)
定法:确定点检方法(点检要求) 定人:确定点检人员(按照不同点检分类) 定表:确定点检表格
点检作业表
例
年月
日
设备编号: 设备名称: 检查者: 审核:
检查项目 允许状态 月 日 月 日 月 日 月 日
观察镜破损
要途径 设备管理是企业长远发展的重要条
件
4. 设备管理的主要任务
保持设备完好; 充分发挥设备效能; 提高企业技术装备的素质;
企业技术装备的素质:
设备素质
设备的完好率 设备的综合效率 现代化程度 自动化程度 技术水平
4. 设备管理的主要任务
保持设备完好; 充分发挥设备效能; 提高企业技术装备的素质; 取得良好的投资效益。
冷 水 观察镜水锈
装 冷却水
置
冷却水管
无裂纹及破损 无水锈 充足 不泄漏
设备管理基础知识

及时检修和精心维护设备
掌握时机、及时改造和更新设备
设备日常管理
四.设备的前期管理------选型
1.设备选择考虑的技术因素
生产性(满足生产提高生产率的程度) 可靠性(在现实条件下,所能发挥出的功效程度) 安全性(设备安全生产的保障性能) 节能性(对能源利用的性能) 耐用性(自然寿命) 维修性(可维修的难易呈递或性质) 互换性(各部件及元器件互换的可能性) 成套性(配套辅机、生产线等的协调) 可调整性(设备可进行适应性调整的可能性) 环境保护性(对周边环境、操作人的影响)
八.设备完好标准
1.零部件完整齐全,质量符合要求
• • • • • • • 主辅机的零部件完整齐全 安全防护装置灵敏可靠 设备基础及机座稳固,地脚螺栓及各连接螺栓整齐紧固 各传动齿轮啮合正常,齿厚磨损不超标 管线、管件、阀门、支架等安装合理,牢固可靠,标识分明 电气控制系统、通讯系统及各部位仪表齐全、灵敏、准确 零部件磨损不超标,产成品能满足生产工艺要求
设备管理基础知识
一.概念
1.设备—企业用于创造利润的有形固定资产总称
为设备。 2· 广义的设备管理—指从前期的需求调查、设 计开发、制造、安装、调试、试生产、运行维 护到最后报废的全寿命周期的整个过程中有效 运用设备机能实现企业目的的活动。 3.狭义的设备管理—指在完成设备安装后,在 设备使用过程中进行的设备维护活动。
2.经济性评价
投资回收期(回报率) 费用换算(一次性投资、使用过程中的维修费 用等)
五.设备的更新与改造
1.设备磨损的性质
有形磨损(物理磨损—磨损、腐蚀等) 无形磨损(精神磨损---由于新技术的同类产品出现使 设备贬值)
2.设备寿命
2024版设备管理知识培训PPT课件

故障诊断技术意义
提高设备可靠性,减少故障停机 时间,降低维修成本,保障生产
安全。
常见故障类型及原因分析
机械故障
由于设备运动部件的磨损、断裂、变形等原因引起的故障。
电气故障
由于电气设备绝缘损坏、电路短路、元器件损坏等原因引起的故障。
热力故障
由于设备过热或过冷引起的故障,如轴承过热、密封件泄漏等。
指标计算。
环境评估
03
评估更新改造对环境的影响,确保符合环保要求。
更新改造方案制定
方案设计
根据需求分析和技术经济评估结果,制定详细的更新改造方案。
设备选型
选择符合技术经济要求的设备型号和供应商。
工程实施计划
制定工程实施计划,明确时间节点、责任人和任务分工。
实施效果评价
技术效果评价
评估更新改造后设备的技术性能提升情况。
调试过程检查要点
检查设备安装情况
调试设备电气系统
检查设备各部件是否安装到位、紧固可靠。
检查电气系统接线是否正确、可靠,调试电 气控制功能。
调试设备机械系统
调试设备整体性能
检查机械系统运转是否平稳、无异响,调试 机械传动精度。
对设备进行整体性能调试,确保设备各项功 能正常。
投产运行注意事项
01
操作前培训
设备运行不稳定
检查设备各部件紧固情况、机械传动精度及 电气控制功能,调整相关参数。
设备安全装置失效
立即停机检查,修复或更换失效的安全装置。
设备维护保养不到位
加强设备维护保养工作,定期检查、更换易 损件,确保设备正常运行。
04
设备维护保养计划制 定
维护保养目的和意义
01
设备管理基础知识
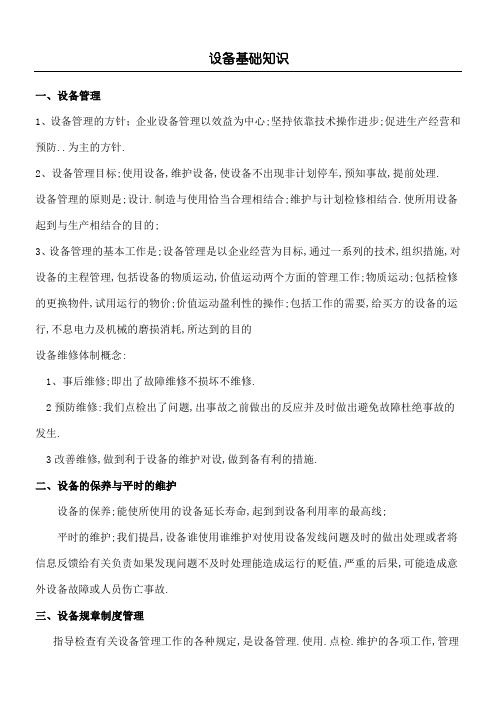
设备基础知识一、设备管理1、设备管理的方针;企业设备管理以效益为中心;坚持依靠技术操作进步;促进生产经营和预防..为主的方针.2、设备管理目标;使用设备,维护设备,使设备不出现非计划停车,预知事故,提前处理.设备管理的原则是;设计.制造与使用恰当合理相结合;维护与计划检修相结合.使所用设备起到与生产相结合的目的;3、设备管理的基本工作是;设备管理是以企业经营为目标,通过一系列的技术,组织措施,对设备的主程管理,包括设备的物质运动,价值运动两个方面的管理工作;物质运动;包括检修的更换物件,试用运行的物价;价值运动盈利性的操作;包括工作的需要,给买方的设备的运行,不息电力及机械的磨损消耗,所达到的目的设备维修体制概念:1、事后维修;即出了故障维修不损坏不维修.2预防维修:我们点检出了问题,出事故之前做出的反应并及时做出避免故障杜绝事故的发生.3改善维修,做到利于设备的维护对设,做到备有利的措施.二、设备的保养与平时的维护设备的保养;能使所使用的设备延长寿命,起到到设备利用率的最高线;平时的维护;我们提昌,设备谁使用谁维护对使用设备发线问题及时的做出处理或者将信息反馈给有关负责如果发现问题不及时处理能造成运行的贬值,严重的后果,可能造成意外设备故障或人员伤亡事故.三、设备规章制度管理指导检查有关设备管理工作的各种规定,是设备管理.使用.点检.维护的各项工作,管理包括管理制度,技术标准,工作,操作管理的约束.规章制度有以下几点;1、设备使用维护管理的办法:做到谁使用谁维护的定义.2、设备检修管理办法:做到做到预警汇报,填写好设备隐患记录,纳入检修的依据.3、设备备件管理办法:仓库的备件换件填写与备件工作志,做进、出换件的依据,确保下次备推上进库的准确性.4、设备的润滑管理方法:认真点检各传动机构,是否缺油的点检,及时加油维护,减少机械的有形磨损.5、设备工作考核与奖惩办法:是点检与维护的精心度,得到的理论与实践责任心的工作状态.6、技术培训的目标:提高职工的专业技术为目的,努力提高各项工作的业务水平.7、设备事故管理办法:设备故障、事故的分析,设备发生事故后,要及时调查分析、研究,召开分析会并做好调查分析记录,做到举一反三的厂会精神.。
设备管理基础知识

。 • 据统计,机械设备失效中,磨损失效约占80%左右。 擦和减少磨损的一种手段
五、设备的润滑
设备使用的“润滑五定”
①定点:确定每台设备的润滑部位和润滑点。 ②定时:按规定的时间取样化验、加油、换油和清洗储油箱。 ③定质:各润滑点按指定的润滑油、脂牌号加油。 ④定量:各润滑点按规定的油量加油。 ⑤定人:明确每个润滑点加油换油责任者。
二、设备的前期管理
3、设备的验收
• 设备开箱验收: a) 检查设备各部件在运输过程有无缺损。 b) 清点核对附件、备件、工具、技术资料、图纸是否齐全。 c) 填写【设备开箱验收单】,查无问题方能办理入库手续。 d) 设备管理员将设备图纸以及所有的技术资料收集整理归档。 • 设备验收: ★验收程序:新增设备, 由资产管理部组织相关单位进行验收,并填写《竣工验收单》,由参加现 场验收的相关单位人员签字确认。 ★经验收,质量、数量、性能、技术条件和图纸符合合同及技术协议要求,现场验收后使用单位 方可投入使用,如存在问题,立即向设备部门主管领导汇报,同时报生产厂家协商解决,验收人 员必须做好验收纪要。
三、设备的使用
设备使用的“四项要求”: (1)整齐 (2)清洁 (3)润滑 (4)安全
工具、工件放置整 齐,安全防护装置 齐全,线路管道完 整。
设备清洁,环境干 净,各滑动面无油 污、无碰伤。
按时加油换油,油 质符合要求,油壶、 油枪、油杯齐全, 油毡、油线、油标 清洁,除 故障及一切危险因 素,预防事故。
四、设备的点检
2、 点检准备------
由设备管理部门负责
定点: 确定点检设备关键部位,薄弱环节
定项: 确定点检项目即检查内容(技术水平匹配,仪器仪表配套)
定标: 确定点检检查项目的判定标准(设备技术要求、实践经验)
- 1、下载文档前请自行甄别文档内容的完整性,平台不提供额外的编辑、内容补充、找答案等附加服务。
- 2、"仅部分预览"的文档,不可在线预览部分如存在完整性等问题,可反馈申请退款(可完整预览的文档不适用该条件!)。
- 3、如文档侵犯您的权益,请联系客服反馈,我们会尽快为您处理(人工客服工作时间:9:00-18:30)。
设备管理知识设备管理知识发布于:2013-5-6 16:59:26 被浏览617次【打印】【关闭】一、设备管理1.生产和设备管理一般称人[Man], 设备[Machine], 原材料[MATERIAL]为生产3要素(3M)。
除此之外,还有工作方法[Method],测量(Measurement),环境(Environment)3个要素,这些并称为生产6要素(5M1E)。
生产要素是指生产的输入,而生产的输出是生产量[P:Production], 质量[Q:Quality],成本[C:Cost], 交期[D:Delivery], 安全环境卫生[S: Safety, Environment, Health], 作业士气[M: Morale]等6要素。
2.设备管理的发展过程事后维护(BM : Breakdown Maintenance)设备负责人为中心的故障后再维护预防维护(PM : Preventive Maintenance)通过预防维护为中心的设备维护管理,追求经济性改善维护(CM : Corrective Maintenance)设备负责人追求提高设备性能维护预防(MP : Maintenance Prevention)总结维护信息,设计不发生故障的设备生产维护(PM : Productive Maintenance)设备负责人对设备全寿命周期进行管理,追求经济性全面PM(TPM : Total Productive Maintenance)生产、开发、销售、采购、管理等全员参与的生产维护4.设备管理广义的设备管理是指对设备寿命周期全过程的管理,从规划、选型、购置、安装、验收、调试、使用、保养、维修、改造直至报废为止的全过程,是通过有效利用设备,提高企业的生产力的管理活动。
狭义的设备管理指购置完毕后的维护活动的管理,即,设备保全管理。
5.开动时间和非开动时间为了测量维护时间,需要对设备相关时间进行分类与定义。
这个时间大体上分类为设备实际开动的开动时间(Uptime)和非开动时间(Downtime)。
时间开动时间非开动时间实际维护时间准备/换装/调试时间管理延误时间事后维护定期维护预防维护改良维护开动时间: 设备为了完成任务实际运转时间。
非开动时间: 设备不执行实际任务的所有时间。
实际维护时间:为了故障修复实施的维护时间。
准备/换装/调整时间: 虽然已完成维护,但为了设备正常开动进行的准备或调试的时间(包括为了生产其他产品进行的更换模具等准备时间)管理延误时间: 故障报告,零部件供应,等待审批等,因管理(行政)问题引起的延误时间。
6.设备维护的类型(1) 预防维护和人的身体相比较时,相当于定期体检。
“预防维护是为了维持设备的健康状态,防止故障的发生,通过日常维护防止劣化的发生,通过定期检查或设备诊断测量劣化程度,早期修复劣化的维护活动”。
改良维护改良维护是不断地利用先进的工艺方法和技术,改正设备的某些缺陷和先天不足,提高设备的先进性、可靠性及维修性,提高设备的利用率。
事后维护事后维护是故障停止或性能发生下降后实施维修的维护方法。
在几十年前(上世纪50~60年代)为止,设备管理正是处于这种事后维修的时代。
虽然当时没有预防的概念,但现在已经在原有概念的基础上发展成为,即使发生故障也有措施手段和考虑经济性、防止故障时间对其他设备影响的事后维护。
定期维护考虑设备的开动率或开动条件,通过确定的周期实施定期点检,发现异常、即时维修、修复、改良的维护手段。
是以周、月、季度、半期、年等事前确定的时间实施分解修理及点检的维护。
日常维护每日实施的维护保养。
是从作业前、后的设备状态开始,将脏污、螺丝松动、润滑状态等,按照一定标准,使用点检表实施记录、维护,当发现异常时,即时修理、修复。
7.设备管理的目的(1) 完成生产计划[Productivity]将设备始终维持在最理想状态为前提条件,为了将规定的产品在规定的时间内,输出最大限度的产量,如何对设备状态进行维护是设备管理的主要课题。
- 例如,如何在短时间内更换模具?- 如何缩小设备停止时间?(2) 提高质量[Quality]产品的好与坏决定于设备状态。
因此,始终监控、记录设备状态,识别影响质量的因素,将不合格防范于未然是设备维护最重要的目的之一。
(3)降低成本[Cost]应以最少的维护费用发挥最大的效果,但要注意的是,维护费用与投资额成反比例关系。
抑止初期投资会导致设备生命周期中的维护费用的增大。
遵守交期[Delivery]即使会发生因企业管理矛盾引发的交期延误,但从维护的立场上看时,应致力于建立保证设备始终在高效运转、发挥设备最大的能力、严格遵守规定交期的设备维护体系。
(5) 防止灾害[Safety]没有履行好维护职责时,会引发安全上的问题。
为了确保安全性,应严格遵守维护规则。
(6) 提高工作士气[Morale]是指如何赋予与建立设备爱心的问题。
应形成鼓励和赞扬自己(操作)的设备,自己维护的企业文化。
8.TPM的理解TPM(Total Productive Maintenance)的意思就是是“全员生产维修”,这是日本人在70年代提出的,是一种全员参与的生产维修方式,其主要点就在“生产维修”及“全员参与”上。
TPM旨在通过改善人和设备的素质来改善企业的素质,从而最大提高设备的综合效率,实现企业的最佳经济效益。
TPM的特点TPM的特点就是三个“全”,即全效率、全系统和全员参加。
全效率:指设备寿命周期费用评价和设备综合效率。
目标使设备处于良好的技术状态,获得最好的设备输出——产量、质量、成本、交货期等,支出最少的寿命周期费用,即低投入,高产出。
全系统:指从设计制造到投入使用的全过程管理。
全员参加:指设备的采购、使用、维修等所有部门都要参加,尤其注重的是操作者的自主维修。
TPM的目标TPM的首要目的就是要事先预防、并消除设备的六大损失。
做到零故障、零不良、零浪费和零灾害,在保证生产效益最大化的同时,实现费用消耗的合理化。
TPM的含义:以达到设备综合效率最高为目标。
以设备一生为对象的全系统的预防维修。
涉及设备的采购、使用、维修部门。
从最高领导到一线员工全员参与。
1:10:100法则关于产品质量与成本的关系问题,企业界有一个著名的“1:10:100”成本法则。
意思是说,假如某件产品在生产前发现一项欠缺并加以弥补,仅需1元钱;如果该缺陷在生产过程中被发现,需花10元钱的代价来弥补;如果此缺陷在市场上被消费者发现,则需花上100倍甚至上千倍的代价来弥补。
TPM要求将设备的操作人员也当作设备维修中的一项要素,那种“我只负责操作”的观念在这里不再适用了。
而例行的日常维修检查、少量的调整作业、润滑以及个别部件的更换工作都成了操作人员的责任。
操作人员也应在维修过程中扮演显著角色。
改变维修思维和方法故障只是冰山一角冰山下面:生锈、螺丝松动,变形,油路堵塞,异物飞入,裂纹,弯曲,固定不良,发热,振动,异常声音等等。
好多微小缺陷造成中缺陷大缺陷故障1:29:300事故法则1∶29∶300是指安全事故发生的规律,即每330起生产安全事件中,会发生1起重伤或死亡事故,29起轻伤事故,300起无伤害事件。
称作1:29:300的事故法则,又称作“海因里希法则”,即在发生330次事故中,有300次未造成伤害、有29次造成轻伤害、有1次造成重伤害。
设备损失结构和效率化2.1设备的6大LOSS①突发故障损失②准备换装·调试损失③减速损失④暂停损失⑤质量(不合格)损失⑥开工损失(初期收得率低)2.2.设备综合效率指标设备综合效率化是最大限度发挥设备能力,确保质量·生产力·生产效率。
但是,从现实情况上看,因为存在各种损失及浪费,设备能力没有被最大限度的释放出来。
a) 设备综合效率的计算公式(1) 设备综合效率设备综合效率= 时间开动率×性能开动率×合格率①时间开动率= (负荷时间-停止时间)/负荷时间②性能开动率= 净(实质)开动率×速度开动率生产数量×实际生产周期净(实质)开动率= ----------------------负荷时间–停止时间理论生产周期速度开动率= -------------实际生产周期③合格率= 合格数量/总数量b) 设备综合效率的计算– (例)• 1天负荷时间10H×60M = 600M准备·换装40M调试20M,故障30M• 1天的生产数量25个• 理论生产周期15M/个• 实际生产周期18M/个• 合格率98%* 时间开动率= (600-40-50)/600=85%* 速度开动率= 15/18=83%* 净(实质)开动率= (25X18)/(600-90)=88%* 性能开动率= 0.83x0.88=73%* 合格率= 98%◎设备综合效率= 0.85X0.73X0.98=60%* 提高设备综合效率,就是充分发挥和保持设备的固有能力,使人和机器达到最佳配合状态。
* 达到80%是优秀企业的标志2.3提高设备效率的方案[1] 正确测量设备6大损失发生量* 明确测量项目,方法,基准,周期,负责人等[2] 测量6大损失对设备综合效率影响的程度* 明确控制目标,充实趋势控制[3] 为了提高开动率, 性能开动率, 提高合格品率,确切实施问题和重点项目的分析* 每当脱离目标时,进行原因分析,全力以赴于再发防止对策[4] 各项目设定正确、确切的目标与活动方向* 以瓶颈(Buttle Neck)工序设备为重点,实施改进[5] 提供与提高综合效率、降低费用、提高收益等方面的相关性* 发行周报/月报,促进全体人员的关心3. 设备改进的基本概念3.1浪费的改进开动率水平确认和消除浪费的目的6大损失和改进目标3.2设备6大损失的改进方法1) 故障损失的对策对于故障损失,需要研究如何提高设备的可靠性与如何缩短发生故障到修复为止的消耗时间。
故障“0”化是可以在不需要太多投资(一时的投资)下实现的。
为此,首先要改变BM( 事后维护)思维的错误认识(故障是不可避免的)。
b) 故障“0”化的方法c) 降低故障损失(2)准备·换装·调试损失的对策最近各个公司也在研究(零准备作业: 10分以内完成作业交接), 但还有很多待解决的项目。
通过外准备、缩短·消除内准备的时间等IE研究,虽然可以看到在各个方面缩短时间的成果,但依旧存在关于调试时间的问题。
调试是很难涉足的领域,一般都处于研究不足的状态,也存在盲目排斥的现象。
但如果想缩短调试时间,首先应评估调试的结构,确定缩短时间的项目。
目标应定为“最小化”。
一般在准备时间中,调试占50~60%左右,做为对策,最重要的是分析有效程度,其步骤如下。