药品生产技术《维生素C的生产》
维生素C的产业概况
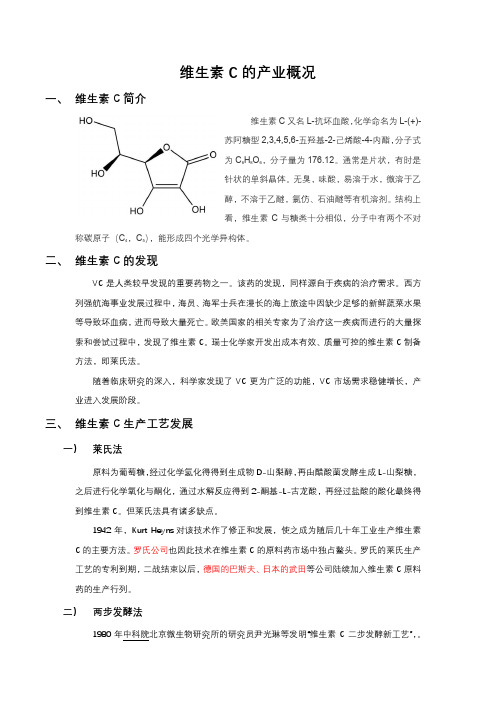
维生素C的产业概况一、维生素C简介维生素C又名L-抗坏血酸,化学命名为L-(+)-苏阿糖型2,3,4,5,6-五羟基-2-己烯酸-4-内酯,分子式为C6H8O6,分子量为176.12。
通常是片状,有时是针状的单斜晶体。
无臭,味酸,易溶于水,微溶于乙醇,不溶于乙醚,氯仿、石油醚等有机溶剂。
结构上看,维生素C与糖类十分相似,分子中有两个不对称碳原子(C4,C5),能形成四个光学异构体。
二、维生素C的发现VC是人类较早发现的重要药物之一。
该药的发现,同样源自于疾病的治疗需求。
西方列强航海事业发展过程中,海员、海军士兵在漫长的海上旅途中因缺少足够的新鲜蔬菜水果等导致坏血病,进而导致大量死亡。
欧美国家的相关专家为了治疗这一疾病而进行的大量探索和尝试过程中,发现了维生素C。
瑞士化学家开发出成本有效、质量可控的维生素C制备方法,即莱氏法。
随着临床研究的深入,科学家发现了VC更为广泛的功能,VC市场需求稳健增长,产业进入发展阶段。
三、维生素C生产工艺发展一)莱氏法原料为葡萄糖,经过化学氢化得得到生成物D-山梨醇,再由醋酸菌发酵生成L-山梨糖,之后进行化学氧化与酮化,通过水解反应得到2-酮基-L-古龙酸,再经过盐酸的酸化最终得到维生素C。
但莱氏法具有诸多缺点。
1942年,Kurt Heyns 对该技术作了修正和发展,使之成为随后几十年工业生产维生素C的主要方法。
罗氏公司也因此技术在维生素C的原料药市场中独占鳌头。
罗氏的莱氏生产工艺的专利到期,二战结束以后,德国的巴斯夫、日本的武田等公司陆续加入维生素C原料药的生产行列。
二)两步发酵法1980年中科院北京微生物研究所的研究员尹光琳等发明“维生素C二步发酵新工艺”,。
此法先将葡萄糖还原成为山梨醇,经过第一次细菌发酵成为山梨糖,再经过第二次细菌发酵转化为KGA(2-keto-gulonicacid),最后异化成为维生素C。
东北制药总厂在1986年左右率先将两部发酵法工艺投入规模化生产(虽然产能只有几百吨,但已显示成本优势),掀开了中国VC企业参与全球角逐的序幕。
维生素C注射液的制备

维生素C注射液的制备***(广西中医学院赛恩斯新医药学院08药学,200831***,南宁,530200)摘要:目的掌握注射剂(小针)的生产工艺流程和操作要点;掌握延缓药物氧化分解的基本方法。
方法维生素C在潮湿状态或者溶液中下容易被氧化,而使药效降低,因此可以加入抗氧化剂;有些溶液中的金属离子在维生素C被氧化的过程中起到催化作用,因此可以加入配合剂将金属离子配合,防止金属离子起到催化作用;溶液的pH也会影响到维生素C的氧化,在pH为5.0 ~ 7.0时,维生素C最稳定,所以可以加入碳酸氢钠调节pH。
为了尽量避免微生物污染,对灌封等关键的操作步骤,生产上多采用层流洁净空气技术,局部灌封处达100级。
结果维生素C注射液本为无色透明液体,但由于实验药品被严重氧化,制得的维生素C为橙黄色。
本品为维生素类药,参与机体的新陈代谢,增加机体的抵抗力,用于防治坏血病,促进创伤及骨折愈合,预防冠心病。
结论维生素C经过经过抗氧化处理和无菌处理后能制得保质期较长的维生素C注射液。
本文就该维生素C注射液的制备及改进方法作出了系统的报告如下。
关键词维生素C注射液;药物氧化分解;处方设计仪器与材料1.1 仪器烧杯,两瓶,电磁炉,水浴锅,注射器,安瓿瓶,熔封器,G3垂熔玻璃漏斗 1.2 材料维生素C,碳酸氢钠,焦亚硫酸氢钠,EDTA-Na2,注射用水,亚甲蓝溶液。
2 实验内容2.1 处方维生素 C 5.2g 碳酸氢钠 2.42g 焦亚硫酸氢钠 0.2g EDTA-Na2, 0.05g 注射用水加至100ml2.2 制法取80%的注射用水,加入EDTA-Na2 ,搅拌混匀,再加入维生素C溶解。
然后分次缓慢加入碳酸氢钠,并搅拌至无泡,加入焦亚硫酸氢钠,并将溶液的pH调节在5 ~ 7之间。
然后将溶液倒入G3垂熔玻璃漏斗中进行过滤,并从滤器上补足注射用水至全量,灌封于2.0ml 安瓿瓶中,放入沸水中灭菌,然后将灭菌的注射液放入10.0g/ml的亚甲蓝溶液中检漏,并剔除废品。
维生素C和K的生产
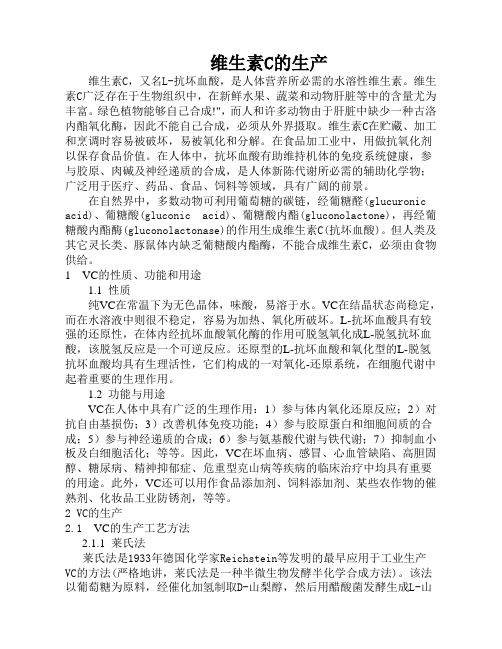
维生素C的生产维生素C,又名L-抗坏血酸,是人体营养所必需的水溶性维生素。
维生素C广泛存在于生物组织中,在新鲜水果、蔬菜和动物肝脏等中的含量尤为丰富。
绿色植物能够自己合成!",而人和许多动物由于肝脏中缺少一种古洛内酯氧化酶,因此不能自己合成,必须从外界摄取。
维生素C在贮藏、加工和烹调时容易被破坏,易被氧化和分解。
在食品加工业中,用做抗氧化剂以保存食品价值。
在人体中,抗坏血酸有助维持机体的免疫系统健康,参与胶原、肉碱及神经递质的合成,是人体新陈代谢所必需的辅助化学物;广泛用于医疗、药品、食品、饲料等领域,具有广阔的前景。
在自然界中,多数动物可利用葡萄糖的碳链,经葡糖醛(glucuronic acid)、葡糖酸(gluconic acid)、葡糖酸内酯(gluconolactone),再经葡糖酸内酯酶(gluconolactonase)的作用生成维生素C(抗坏血酸)。
但人类及其它灵长类、豚鼠体内缺乏葡糖酸内酯酶,不能合成维生素C,必须由食物供给。
1 VC的性质、功能和用途1.1 性质纯VC在常温下为无色晶体,味酸,易溶于水。
VC在结晶状态尚稳定,而在水溶液中则很不稳定,容易为加热、氧化所破坏。
L-抗坏血酸具有较强的还原性,在体内经抗坏血酸氧化酶的作用可脱氢氧化成L-脱氢抗坏血酸,该脱氢反应是一个可逆反应。
还原型的L-抗坏血酸和氧化型的L-脱氢抗坏血酸均具有生理活性,它们构成的一对氧化-还原系统,在细胞代谢中起着重要的生理作用。
1.2 功能与用途VC在人体中具有广泛的生理作用:1)参与体内氧化还原反应;2)对抗自由基损伤;3)改善机体免疫功能;4)参与胶原蛋白和细胞间质的合成;5)参与神经递质的合成;6)参与氨基酸代谢与铁代谢;7)抑制血小板及白细胞活化;等等。
因此,VC在坏血病、感冒、心血管缺陷、高胆固醇、糖尿病、精神抑郁症、危重型克山病等疾病的临床治疗中均具有重要的用途。
此外,VC还可以用作食品添加剂、饲料添加剂、某些农作物的催熟剂、化妆品工业防锈剂,等等。
实验三 维生素C注射液的制备

H 2O C C C CH 2OH O HO O C H COOHOHHCOOHCOOH C C HOOC OH H CH 2OH实验三 维生素C 注射液的制备一、目的要求1. 掌握注射剂(水针)的制备方法及工艺过程中的操作要点2. 熟悉注射剂成品质量检查标准和检查方法,了解影响成品质量的因素3. 熟悉提高易氧化药物稳定性的基本方法4.了解无菌与灭菌制剂生产工艺中的关键操作二、基本概念和实验原理注射剂系指将药物制成的供注入体内的无菌溶液、乳状液和混悬液以及供临用前配制成溶液或混悬液的无菌粉末。
注射剂的生产车间设施必须符合《药品生产质量管理规范》的要求,注射剂的生产过程包括原辅料的准备、配制、灌封、灭菌、质量检查、包装等步骤。
注射剂的质量要求:无菌、无热原、澄明度合格、使用安全、无毒性无刺激性;稳定性合格,即在贮存期内稳定有效。
注射剂的pH 值应接近血液pH 值,一般控制在4~9范围内,含量合格;凡大量静脉注射或滴注的输液,应调节渗透压与血浆等渗或接近等渗。
维生素C (Vitamin C 或Ascorbic Acid )用于防治坏血病,促进创伤及骨折、预防冠心病等,临床应用十分广泛。
维生素C 在干燥状态下较稳定,但在潮湿状态或溶液中,其分子结构中的烯二醇结构被很快氧化,生成黄色双酮化合物,虽仍有药效,但会迅速进一步氧化、断裂、生成一系列有色的无效物质。
氧化反应式如下:抗坏血酸 去氢抗坏血酸 2,3-二酮-L-古罗糖酸+草酸L-丁糖酸溶液的pH值、氧、重金属离子和温度对Vitamin C的氧化均有影响。
针对Vitamin C溶液易氧化的特点,在注射液处方设计中应重点考虑怎样延缓药的氧化分解,通常采取如下措施:(1)除氧,尽量减少药物与空气的接触,在配液和灌封中通入惰性气体,常用高纯度的氮气和二氧化碳。
(2)加抗氧剂。
(3)调节溶液pH在最稳定pH范围。
(4)加金属离子络合剂。
金属离子对药物的氧化反应有强烈的催化作用,当Vitamin C溶液中含有0.0002mol/L铜离子时,其氧化速反可以增大104倍,故常用依地酸钠或依地酸钙钠络合金属离子。
维生素C片车间工艺设计

维生素C片车间工艺设计一、设计说明书【名称】:维生素C片【药品类别】维生素类及矿物质缺乏症用药【用途】:1.促进骨胶原的生物合成。
利于组织创伤口的更快愈合。
2.改善脂肪和类脂特别是胆固醇的代谢,预防心血管病。
3.促进牙齿和骨骼的生长,防止牙床出血,防止关节痛、腰腿痛。
4.增强肌体对外界环境的抗应激能力和免疫力。
5.充分吸收可以抑制血压上升。
【用法/用量】:每天1次,每次1片,嚼食、口服。
用于成人:1.饮食补充:一日50~100mg。
2.慢性透析病人:一日100~200mg。
3.维生素C缺乏:一次100~200mg,一日3次。
至少服2周。
小儿每日100~300mg,至少服2周。
4.酸化尿:一日口服4~12g,分次服用,每4小时1次。
5.特发性高铁血红蛋白血症:每日300~600mg,分次服用。
【规格】:0.1575g/片,12片/板,2板/小盒,1000盒/箱。
【处方】原料含量(mg/片)每10万片片重(kg)维生素C100.010.0糊精10.0 1.00淀粉20.0 2.00乙醇(50%)25.0 2.5~3.0酒石酸 1.00.1硬脂酸镁 1.50.15【性状】该品为白色或略带淡黄色片。
【药理毒理】维生素C为抗体及胶原形成,组织修补(包括某些氧化还原作用),苯丙氨酸、酪氨酸、叶酸的代谢,铁、碳水化合物的利用,脂肪、蛋白质的合成,维持免疫功能,羟化与羟色胺,保持血管的完整,促进非血红素铁吸收等所必需。
【药代动力学】胃肠道吸收,主要在空肠。
蛋白结合率低。
以腺体组织、白细胞、肝、眼球晶体中含量较高。
人体摄入维生素C每日推荐需要量时,体内约贮存1500mg,如每日摄入200mg维生素C时,体内贮量约2500mg。
肝内代谢,极少量以原形或代谢产物经肾排泄。
当血浆浓度大于14μg/ml时,尿内排出量增多。
可经血液透析清除。
【适应人群】1.过食、偏食、节食者,尤其是果蔬摄入不足者。
2.免疫力低下,易感冒者。
生物发酵技术在医药生产中的应用
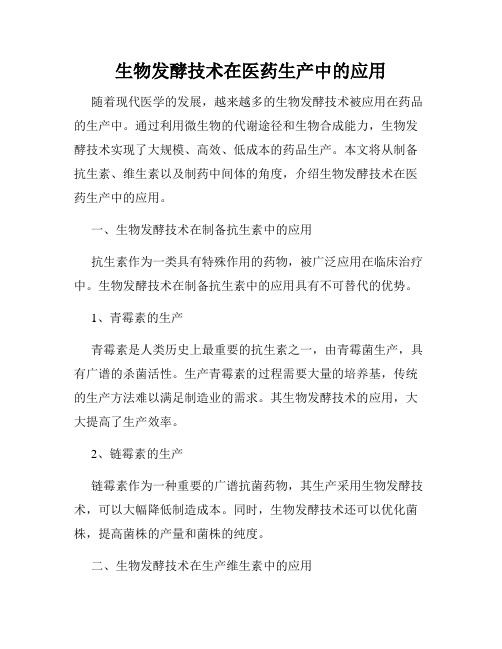
生物发酵技术在医药生产中的应用随着现代医学的发展,越来越多的生物发酵技术被应用在药品的生产中。
通过利用微生物的代谢途径和生物合成能力,生物发酵技术实现了大规模、高效、低成本的药品生产。
本文将从制备抗生素、维生素以及制药中间体的角度,介绍生物发酵技术在医药生产中的应用。
一、生物发酵技术在制备抗生素中的应用抗生素作为一类具有特殊作用的药物,被广泛应用在临床治疗中。
生物发酵技术在制备抗生素中的应用具有不可替代的优势。
1、青霉素的生产青霉素是人类历史上最重要的抗生素之一,由青霉菌生产,具有广谱的杀菌活性。
生产青霉素的过程需要大量的培养基,传统的生产方法难以满足制造业的需求。
其生物发酵技术的应用,大大提高了生产效率。
2、链霉素的生产链霉素作为一种重要的广谱抗菌药物,其生产采用生物发酵技术,可以大幅降低制造成本。
同时,生物发酵技术还可以优化菌株,提高菌株的产量和菌株的纯度。
二、生物发酵技术在生产维生素中的应用维生素是一类具有重要生理功能的有机化合物,对人体健康有着重要的影响。
生物发酵技术在生产维生素方面具有独特的优势。
1、维生素C的生产维生素C是人体必需的一种水溶性维生素,对身体的免疫力、维持组织骨骼的健康等方面有着重要的作用。
生物发酵技术在大规模生产维生素C方面具有较大的优势。
其生产模式主要是采用底物预处理、菌株异源表达等方法,使得维生素C的产率与纯度得到了提高。
2、维生素B的生产维生素B是多种维生素的总称,包括维生素B1、维生素B2、泛酸、烟酸等。
生物发酵技术可以利用微生物的代谢途径和生物合成能力,大规模生产维生素B1、维生素B2等成分。
生物发酵技术的应用,可以大幅降低维生素B类药物的成本,从而使更多的患者受益。
三、生物发酵技术在制药中间体的生产中的应用制药中间体是指通过化学或者生物反应方法制备活性药物的一类基础化学原料。
生物发酵技术在制药中间体的生产中也具有独特的应用价值。
1、磷酸盐缓冲剂的生产生物发酵技术可以通过合成抗生素中产生的有机酸或使用死菌体等方法生产磷酸盐缓冲剂,这些缓冲剂是药品生产中不可缺少的基础原料。
药品维生素c的工艺
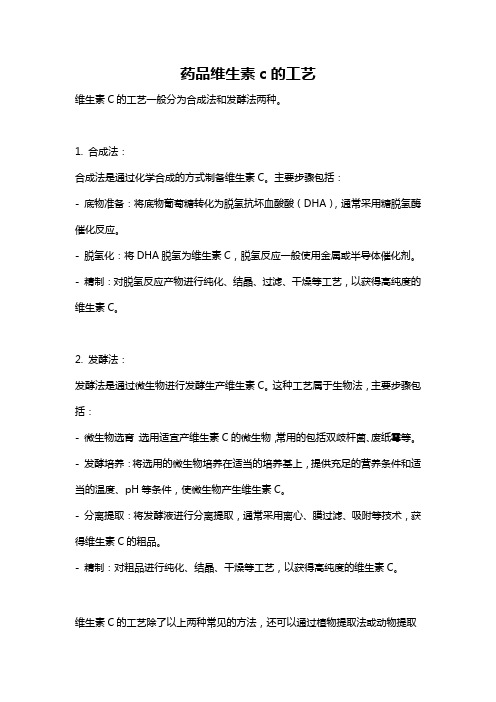
药品维生素c的工艺
维生素C的工艺一般分为合成法和发酵法两种。
1. 合成法:
合成法是通过化学合成的方式制备维生素C。
主要步骤包括:
- 底物准备:将底物葡萄糖转化为脱氢抗坏血酸酸(DHA),通常采用糖脱氢酶催化反应。
- 脱氢化:将DHA脱氢为维生素C,脱氢反应一般使用金属或半导体催化剂。
- 精制:对脱氢反应产物进行纯化、结晶、过滤、干燥等工艺,以获得高纯度的维生素C。
2. 发酵法:
发酵法是通过微生物进行发酵生产维生素C。
这种工艺属于生物法,主要步骤包括:
- 微生物选育:选用适宜产维生素C的微生物,常用的包括双歧杆菌、废纸霉等。
- 发酵培养:将选用的微生物培养在适当的培养基上,提供充足的营养条件和适当的温度、pH等条件,使微生物产生维生素C。
- 分离提取:将发酵液进行分离提取,通常采用离心、膜过滤、吸附等技术,获得维生素C的粗品。
- 精制:对粗品进行纯化、结晶、干燥等工艺,以获得高纯度的维生素C。
维生素C的工艺除了以上两种常见的方法,还可以通过植物提取法或动物提取
法获得。
不同的制备方法会影响维生素C的产率、纯度以及成本等因素。
维生素C的提取

维生素C得提取维生素C就是人类营养中最重要得维生素之一,如果缺乏维生素C它时会产生坏血病,因此又称为抗坏血酸(ascorbic acid)、它对物质代谢得调节具有重要得作用。
近年来,发现它还有增强机体对肿瘤得抵抗力,并具有化学致癌物得阻断作用。
维生素C就是不饱与多羟基物,属于水溶性维生素、抗坏血酸在自然界分布十分广泛,存在于新鲜水果与蔬菜中,尤其就是柠檬果实与一些绿色植物(如青辣椒、菠菜等)中含量特别丰富、抗坏血酸在机体同具有广泛得生理功能,已知体内许多重要物质得代谢反应都需要抗坏血酸得参与。
它就是脯氨酸羟基化酶得辅酶,故有增进胶原蛋白合成得作用。
机体中许多含疏基得酶,需要依赖于作为还原剂得抗坏血酸得保护,使酶分子得疏基处于还原状态,从而维持其催化活性。
由于抗坏血酸得氧化还原作用,它可促进免疫球蛋白得合成,增强机体得抵抗力。
同时还能使氧化型谷胱甘肽转化为还原型谷胱甘肽(简称GSH),而GSH可与重金属结合而排出体外,因此维生素C常用于重金属得解毒、此外,抗坏血酸尚有许多其她生理功能,但其作用机理还不十分清楚、抗坏血酸就是一种不饱与得多羟基内酯化合物,稍有酸味得糖类白色晶体,易溶于水,故属于水溶性维生素。
在溶液中其分子内C2与C3之间得烯醇式羟基上得氢极易解离并释放出H+,而被氧化成脱氢抗坏血酸,氧化后仍具有维生素C得生理活性,但它易分解为二酮古洛糖酸,此化合物不再具有维生素C得生理活性。
维生素C有很强得还原性,在碱性溶液中加热并有氧化剂存在时,易被氧化而破坏。
还原型与氧化型抗坏血酸可以互相转变,在生物组织中自成一氧化还原系统、维生素C具有很强得还原性。
还原型抗坏血酸能还原染料2,6—二氯酚靛酚,本身则氧化为脱氢型。
在酸性溶液中,2,6—二氯酚靛酚呈红色,还原后变为无色。
因此,当用此染料滴定含有维生素C得酸性溶液时,维生素C尚未全部被氧化前,则滴下得染料立即被还原成无色。
一旦溶液中得维生素C已全部被氧化时,则滴下得染料立即使溶液变成粉红色、青椒中维生素得提取方法:维生素C在中性、碱性条件下不稳定,在酸性条件下稳定,因此,弱酸性溶液中可提取维生素 C 。
维生素C的提取
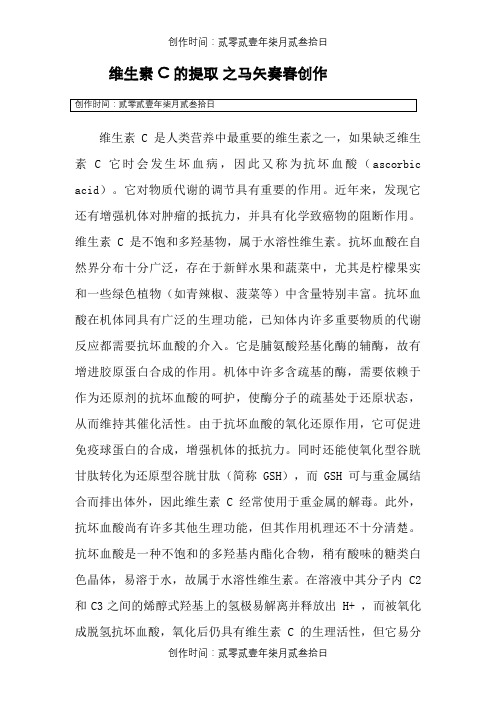
维生素C的提取之马矢奏春创作维生素C是人类营养中最重要的维生素之一,如果缺乏维生素C它时会发生坏血病,因此又称为抗坏血酸(ascorbic acid)。
它对物质代谢的调节具有重要的作用。
近年来,发现它还有增强机体对肿瘤的抵抗力,并具有化学致癌物的阻断作用。
维生素C是不饱和多羟基物,属于水溶性维生素。
抗坏血酸在自然界分布十分广泛,存在于新鲜水果和蔬菜中,尤其是柠檬果实和一些绿色植物(如青辣椒、菠菜等)中含量特别丰富。
抗坏血酸在机体同具有广泛的生理功能,已知体内许多重要物质的代谢反应都需要抗坏血酸的介入。
它是脯氨酸羟基化酶的辅酶,故有增进胶原蛋白合成的作用。
机体中许多含疏基的酶,需要依赖于作为还原剂的抗坏血酸的呵护,使酶分子的疏基处于还原状态,从而维持其催化活性。
由于抗坏血酸的氧化还原作用,它可促进免疫球蛋白的合成,增强机体的抵抗力。
同时还能使氧化型谷胱甘肽转化为还原型谷胱甘肽(简称GSH),而GSH可与重金属结合而排出体外,因此维生素C经常使用于重金属的解毒。
此外,抗坏血酸尚有许多其他生理功能,但其作用机理还不十分清楚。
抗坏血酸是一种不饱和的多羟基内酯化合物,稍有酸味的糖类白色晶体,易溶于水,故属于水溶性维生素。
在溶液中其分子内C2和C3之间的烯醇式羟基上的氢极易解离并释放出 H+ ,而被氧化成脱氢抗坏血酸,氧化后仍具有维生素C的生理活性,但它易分解为二酮古洛糖酸,此化合物不再具有维生素C的生理活性。
维生素C有很强的还原性,在碱性溶液中加热并有氧化剂存在时,易被氧化而破坏。
还原型和氧化型抗坏血酸可以互相转变,在生物组织中自成一氧化还原系统。
维生素C具有很强的还原性。
还原型抗坏血酸能还原染料2,6—二氯酚靛酚,自己则氧化为脱氢型。
在酸性溶液中,2,6—二氯酚靛酚呈红色,还原后变成无色。
因此,当用此染料滴定含有维生素C的酸性溶液时,维生素C尚未全部被氧化前,则滴下的染料立即被还原成无色。
一旦溶液中的维生素C已全部被氧化时,则滴下的染料立即使溶液酿成粉红色。
(完整word)年产3亿片维生素C片剂生产车间 鉴

镇江高等专科学校化学制药课程设计设计题目:年产3亿片维生素C片剂生产工艺课程设计系部:化工系专业:化学制药技术学生姓名: 高祖镜学号: 100305108 起迄日期: 2012年03月21日~ 2012 年05月10日指导教师: # # #教研室主任: # # #目录第一章概述............................................................. - 3 -1。
1片剂介绍.......................................................... - 3 -1.2片剂的特点......................................................... - 3 -1.3片剂的分类......................................................... - 4 -1。
4片剂的规格和质量.................................................. - 4 -1。
5片剂的质量检查.................................................... - 5 -第二章处方设计及工艺................................................... - 7 -2。
1维生素C片简介.................................................... - 7 -2。
2维生素C片处方设计............................................... - 10 -2.3处方分析.......................................................... - 11 -2.4辅料的选择原则.................................................... - 11 -第三章工艺流程........................................................ - 13 -3。
维c
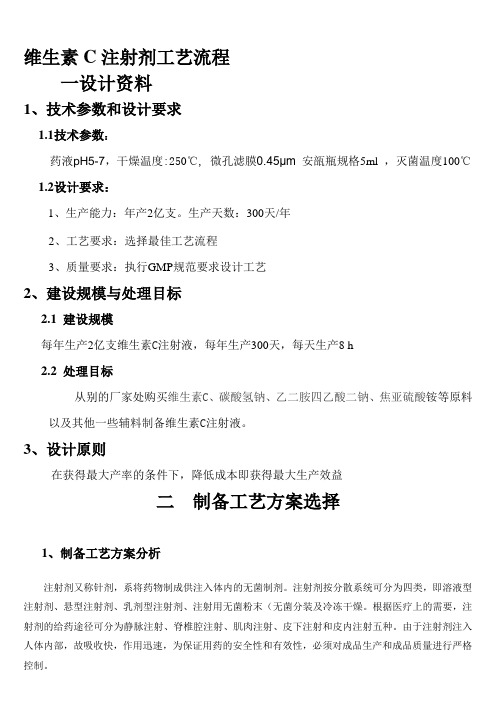
维生素C注射剂工艺流程一设计资料1、技术参数和设计要求1.1技术参数:药液pH5-7,干燥温度:250℃, 微孔滤膜0.45μm安瓿瓶规格5ml ,灭菌温度100℃1.2设计要求:1、生产能力:年产2亿支。
生产天数:300天/年2、工艺要求:选择最佳工艺流程3、质量要求:执行GMP规范要求设计工艺2、建设规模与处理目标2.1 建设规模每年生产2亿支维生素C注射液,每年生产300天,每天生产8 h2.2 处理目标从别的厂家处购买维生素C、碳酸氢钠、乙二胺四乙酸二钠、焦亚硫酸铵等原料以及其他一些辅料制备维生素C注射液。
3、设计原则在获得最大产率的条件下,降低成本即获得最大生产效益二制备工艺方案选择1、制备工艺方案分析注射剂又称针剂,系将药物制成供注入体内的无菌制剂。
注射剂按分散系统可分为四类,即溶液型注射剂、悬型注射剂、乳剂型注射剂、注射用无菌粉末(无菌分装及冷冻干燥。
根据医疗上的需要,注射剂的给药途径可分为静脉注射、脊椎腔注射、肌肉注射、皮下注射和皮内注射五种。
由于注射剂注入人体内部,故吸收快,作用迅速,为保证用药的安全性和有效性,必须对成品生产和成品质量进行严格控制。
注射剂的工艺流程:以溶液型注射剂制备过程为例,其工艺流程如下,注射剂的质量要求:一个合格的注射剂必须是澄明度合格、无菌、无热原、安全性合格(无毒性、溶血性和刺激性)、在贮存期内稳定有效,pH值、渗透压(大容量注射剂)和药物含量应符合要求。
注射液的pH值应接近体液,一般控制在4~9范围内,特殊情况下可以适当放宽,如磺胺嘧啶钠注射液的pH值为9.5~11.0,葡萄糖注射液的pH值为3.2~5.5,葡萄糖氯化钠注射液的pH值为3.5~5.5,注射用奥美拉唑的碱度范围为pH9.0~11.5。
具体注射剂品种的pH值的确定主要依据以下三个方面,首先是满足临床需要,其次是满足制剂制备、贮藏和使用时的稳定性,最后要满足人体生理可承受性。
凡大量静脉注射或滴注的输液,应调节其渗透压与血浆渗透压相等或接近。
维生素C工艺流程
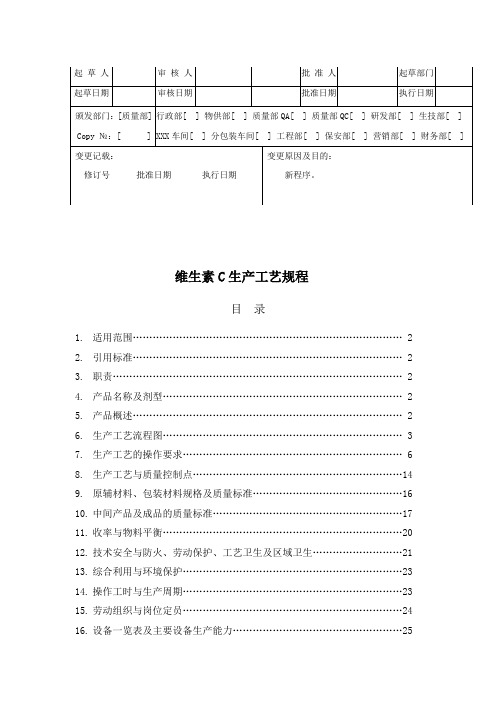
维生素C生产工艺规程目录1.适用范围 (2)2.引用标准 (2)3.职责 (2)4.产品名称及剂型 (2)5.产品概述 (2)6.生产工艺流程图 (3)7.生产工艺的操作要求 (6)8.生产工艺与质量控制点 (14)9.原辅材料、包装材料规格及质量标准 (16)10.中间产品及成品的质量标准 (17)11.收率与物料平衡 (20)12.技术安全与防火、劳动保护、工艺卫生及区域卫生 (21)13.综合利用与环境保护 (23)14.操作工时与生产周期 (23)15.劳动组织与岗位定员 (24)16.设备一览表及主要设备生产能力 (25)17.原材料和技术经济指标 (26)18.附录 (26)1.适用范围本规程规定了流感维生素C合成生产全过程的工艺技术、质量、物耗、安全、工艺卫生、环境保护等内容,经验证合格,符合GMP规范要求。
本工艺规程具有技术法规作用。
本工艺规程适用于流感于维生素C合成的生产全过程,是各部门共同遵循的技术准则。
2.引用标准《中华人民共和国药典》2005年版(第三部)《中国生物制品主要原辅材料质控标准》(2000年版)《药品生产质量管理规范》(1998年修订)《维生素C合成制造和检定规程》批准件3.职责起草:生技部组织相关专业技术人员负责起草。
审批:技术总监和质量总监审核,总经理批准。
执行:各级生产质量管理人员及操作人员。
4.产品名称及剂型4.1.产品通用名称:****汉语拼音 :Weishengsu C商品名: ********英文名称:Vitamin C剂型:无菌原料药产品概述:本品为维生素类药。
维生素C参与氨基酸代谢、神经递质的合成、胶原蛋白和组织细胞间质的合成,可降低毛细血管的通透性,加速血液的凝固,刺激凝血功能,促进铁在肠内吸收,促使血脂下降,增加对感染的抵抗力,参与解毒功能,且有抗组胺的作用及阻止致癌物质(亚硝胺)生成的作用。
4.3用途用于用于防治坏血病和各种急慢性传染性疾病及紫癜等辅助治疗,大剂量静脉注射用于克山症,心源性休克时抢救。
维生素c水针剂生产工艺流程图 (2)

维生素C水针剂生产工艺流程图1. 简介在药品生产过程中,维生素C水针剂是一种常见的药品。
维生素C具有抗氧化、免疫调节等作用,通过水针剂的形式可以方便患者进行注射使用。
本文档将介绍维生素C水针剂的生产工艺流程。
2. 原料准备2.1 维生素C原料维生素C原料是生产维生素C水针剂的主要原料。
在原料准备阶段,需要对维生素C原料进行检验,确保其质量符合药典标准。
原料准备中还需要按照配方要求计量维生素C原料的数量。
2.2 辅料准备在生产维生素C水针剂的过程中,还需要使用一些辅料。
辅料可以包括稳定剂、pH调节剂、溶剂等。
辅料的准备需要按照配方要求计量,并确保其质量符合药典标准。
3. 制备工艺3.1 维生素C溶液的制备首先,需要将准备好的维生素C原料进行溶解。
将一定量的溶剂加入反应容器中,然后逐步加入维生素C原料,同时进行搅拌和加热,直至维生素C完全溶解。
在制备过程中,需要控制反应温度和搅拌速度,以确保溶液的均匀性和稳定性。
3.2 辅料的添加在维生素C溶液制备完成后,需要将辅料逐一加入溶液中。
根据配方要求,按照一定的顺序将稳定剂、pH调节剂等辅料加入维生素C溶液中,同时进行搅拌和混合,以确保辅料充分溶解和均匀分布。
3.3 过滤与灭菌在辅料添加完成后,需要对维生素C水针剂的溶液进行过滤处理。
通过使用合适的过滤设备,将溶液进行过滤,去除其中的杂质和微生物。
过滤完毕后,再进行灭菌处理,以确保维生素C水针剂的无菌性。
3.4 充填与包装经过过滤和灭菌处理后的维生素C水针剂溶液需要进行充填和包装。
在充填过程中,将溶液逐一注入注射器或针剂瓶中,并且对充填过程进行精确控制,确保每个单元的充填量符合要求。
充填完成后,对注射器或针剂瓶进行密封和包装,以保证维生素C水针剂的质量。
4. 质量控制在维生素C水针剂的生产过程中,需要进行质量控制,以确保产品质量符合药典标准。
质量控制包括原料、辅料和制剂的检验,生产过程的控制和监测,以及最终产品的检验。
维生素C
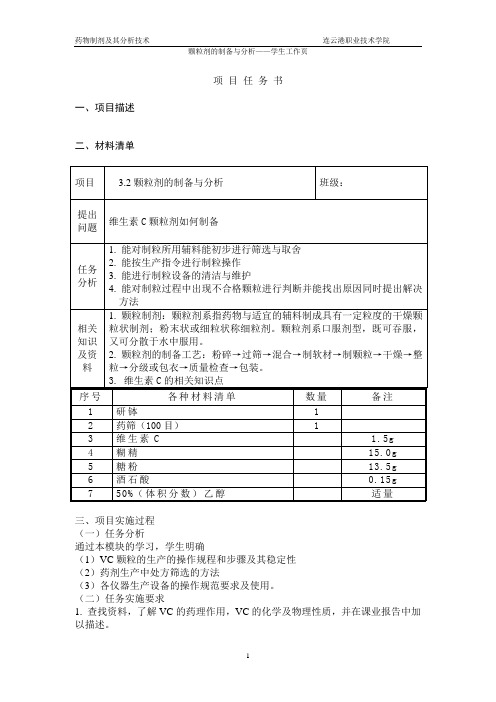
项 目 任 务 书一、项目描述二、材料清单序号 各种材料清单数量 备注 1 研钵1 2 药筛(100目) 1 3 维生素C 1.5g 4 糊精 15.0g 5 糖粉 13.5g 6 酒石酸0.15g 750%(体积分数)乙醇适量三、项目实施过程 (一)任务分析通过本模块的学习,学生明确(1)VC 颗粒的生产的操作规程和步骤及其稳定性 (2)药剂生产中处方筛选的方法(3)各仪器生产设备的操作规范要求及使用。
(二)任务实施要求1. 查找资料,了解VC 的药理作用,VC 的化学及物理性质,并在课业报告中加以描述。
项目 3.2颗粒剂的制备与分析 班级:提出问题维生素C 颗粒剂如何制备任务分析1. 能对制粒所用辅料能初步进行筛选与取舍2. 能按生产指令进行制粒操作3. 能进行制粒设备的清洁与维护4. 能对制粒过程中出现不合格颗粒进行判断并能找出原因同时提出解决方法相关知识及资料 1. 颗粒制剂:颗粒剂系指药物与适宜的辅料制成具有一定粒度的干燥颗粒状制剂;粉末状或细粒状称细粒剂。
颗粒剂系口服剂型,既可吞服,又可分散于水中服用。
2. 颗粒剂的制备工艺:粉碎→过筛→混合→制软材→制颗粒→干燥→整粒→分级或包衣→质量检查→包装。
3. 维生素C 的相关知识点2. 设计药剂处方,其内容包括:确定VC的浓度;选择附加剂,并确定比例和附加剂的使用量。
药剂处方和处方说明为课业报告内容。
3. 思考并设计配制方法,并预先考虑应该注意的事项。
4. 在药物制剂技术实验室完成药剂的配制。
在课业报告中详细描述配制过程。
5. 选择包装容器,并设计药品标签。
6. 将颗粒剂包装,并贴上自己手工绘制的药品标签。
7. 每个小组选一个学生代表将本组的工作情况向其他小组同学介绍。
8、本小组同学集体给本组工作评分,并给其他小组评分。
(三)具体项目任务实施任务一:详述维生素C性质特点以及药理性质物理性质:外观:无色晶体熔点:190 - 192℃沸点:(无)紫外吸收最大值:245nm荧光光谱:激发波长-无nm,荧光波长-无nm;溶解性:水溶性维生素化学性质:分子式:C6H8O6分子量:176.12uCAS号:50-81-7酸性,具有较强的还原性,加热或在溶液中易氧化分解,在碱性条件下更易被氧化,为己糖衍生物。
维生素C的文献
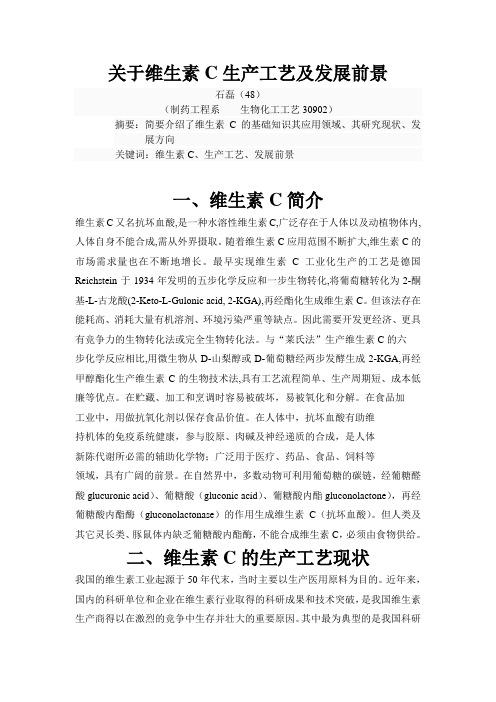
关于维生素C生产工艺及发展前景石磊(48)(制药工程系生物化工工艺30902)摘要:简要介绍了维生素C的基础知识其应用领域、其研究现状、发展方向关键词:维生素C、生产工艺、发展前景一、维生素C简介维生素C又名抗坏血酸,是一种水溶性维生素C,广泛存在于人体以及动植物体内,人体自身不能合成,需从外界摄取。
随着维生素C应用范围不断扩大,维生素C的市场需求量也在不断地增长。
最早实现维生素C工业化生产的工艺是德国Reichstein于1934年发明的五步化学反应和一步生物转化,将葡萄糖转化为2-酮基-L-古龙酸(2-Keto-L-Gulonic acid, 2-KGA),再经酯化生成维生素C。
但该法存在能耗高、消耗大量有机溶剂、环境污染严重等缺点。
因此需要开发更经济、更具有竞争力的生物转化法或完全生物转化法。
与“莱氏法”生产维生素C的六步化学反应相比,用微生物从D-山梨醇或D-葡萄糖经两步发酵生成2-KGA,再经甲醇酯化生产维生素C的生物技术法,具有工艺流程简单、生产周期短、成本低廉等优点。
在贮藏、加工和烹调时容易被破坏,易被氧化和分解。
在食品加工业中,用做抗氧化剂以保存食品价值。
在人体中,抗坏血酸有助维持机体的免疫系统健康,参与胶原、肉碱及神经递质的合成,是人体新陈代谢所必需的辅助化学物;广泛用于医疗、药品、食品、饲料等领域,具有广阔的前景。
在自然界中,多数动物可利用葡萄糖的碳链,经葡糖醛酸glucuronic acid)、葡糖酸(gluconic acid)、葡糖酸内酯gluconolactone),再经葡糖酸内酯酶(gluconolactonase)的作用生成维生素C(抗坏血酸)。
但人类及其它灵长类、豚鼠体内缺乏葡糖酸内酯酶,不能合成维生素C,必须由食物供给。
二、维生素C的生产工艺现状我国的维生素工业起源于50年代末,当时主要以生产医用原料为目的。
近年来,国内的科研单位和企业在维生素行业取得的科研成果和技术突破,是我国维生素生产商得以在激烈的竞争中生存并壮大的重要原因。
关于维生素C生产工艺的综述
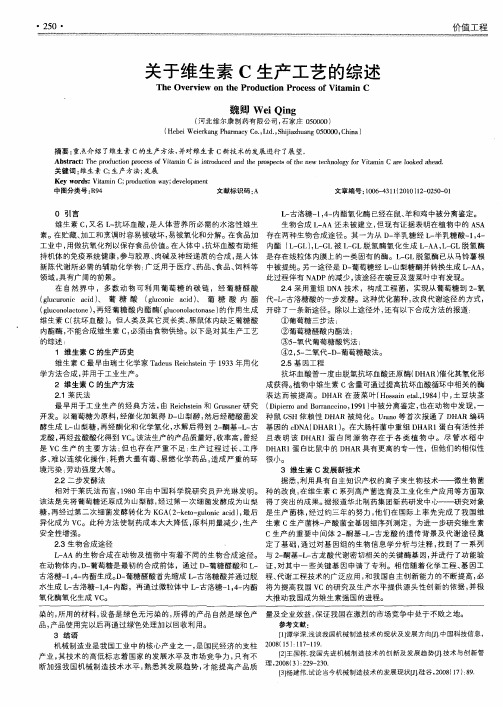
关键词 : 生素 c 生产 方法 ; 展 维 ; 发
K e wo ds y r :Via n C: rdu t n wa d v lpme tmi p o ci y; e eo o nt
中图分类号 : 9 R4
文献标识码 : A
文章编号:0 6 4 1 (0 0)2 0 5 — 1 10 — 3 12 1 1— 2 0 0
在 自然 界中 ,多数 动物 可利 用葡 萄糖 的碳链 ,经 葡糖 醛 酸 24采 用 重 组 D A 技 术 ,构 成 工 程菌 ,实 现从 葡萄 糖 到 2 氧 . N 一 (lc rnc c 、 葡 糖 酸 (l o i c ) 葡 糖 酸 内 酯 代一 一 g uoi i u a d) g cnc i 、 u a d L 古洛糖酸 的一步发酵。这种优化菌种 , 良代谢途径 的方式 , 改 (lcn l t e , g oo c n )再经 葡糖 酸 内酯酶(lcnlc ns ) u ao guooat ae 的作用 生成 开辟 了一条新途径 。除以上途径外 , o 还有以下合成方法的报道 : 维 生素 c 抗坏血酸 ) ( 。但人类及其 它灵长类、 豚鼠体 内缺 乏葡糖 酸 葡 萄糖 三 步 法 ; 内酯 酶 , 能合 成 维 生 素 C 必 须 由食 物 供 给 。以下 是对 其 生 产 工 艺 不 , ②葡萄糖醛酸 内酯法 ;
是 V 生 产 的 主 要 方 法 ; 也 存 在 严 重 不 足 : 产 过 程 过 长 、 序 D A 蛋 白比鼠中的 D A C 但 生 工 H R1 H R具有更高的专一性 ,但他们的相似性 多、 以连续化操作 ; 费大量有毒 、 难 耗 易燃化学药品 , 造成 严重的环 很 小 。 境 污 染 ; 动 强 度 大等 。 劳 22二步 发 酵 法 . 3 维 生 素 C 发 展新 技 术 据悉, 利用具 有 自主知识产权 的离子束生物技术——微 生物菌
(完整版)维生素c注射剂工艺流程
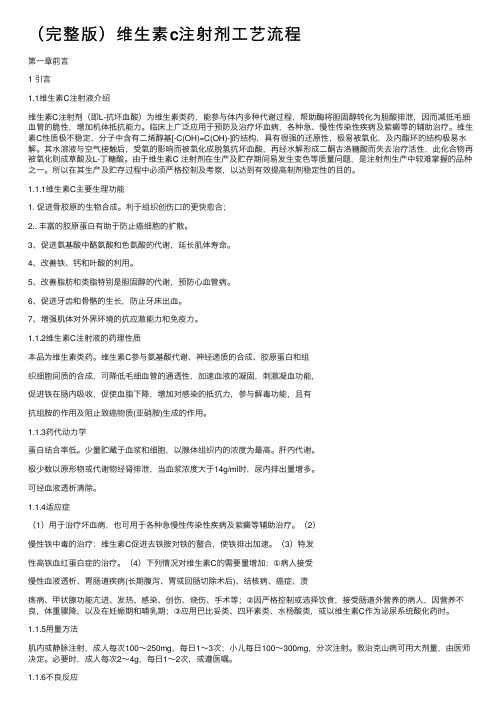
(完整版)维⽣素c注射剂⼯艺流程第⼀章前⾔1 引⾔1.1维⽣素C注射液介绍维⽣素C注射剂(即L-抗坏⾎酸)为维⽣素类药,能参与体内多种代谢过程,帮助酶将胆固醇转化为胆酸排泄,因⽽减低⽑细⾎管的脆性,增加机体抵抗能⼒。
临床上⼴泛应⽤于预防及治疗坏⾎病,各种急、慢性传染性疾病及紫癜等的辅助治疗。
维⽣素C性质极不稳定,分⼦中含有⼆烯醇基[-C(OH)=C(OH)-]的结构,具有很强的还原性,极易被氧化,及内酯环的结构极易⽔解。
其⽔溶液与空⽓接触后,受氧的影响⽽被氧化成脱氢抗坏⾎酸,再经⽔解形成⼆酮古洛糖酸⽽失去治疗活性,此化合物再被氧化则成草酸及L-丁糖酸。
由于维⽣素C 注射剂在⽣产及贮存期间易发⽣变⾊等质量问题,是注射剂⽣产中较难掌握的品种之⼀。
所以在其⽣产及贮存过程中必须严格控制及考察,以达到有效提⾼制剂稳定性的⽬的。
1.1.1维⽣素C主要⽣理功能1. 促进⾻胶原的⽣物合成。
利于组织创伤⼝的更快愈合;2.. 丰富的胶原蛋⽩有助于防⽌癌细胞的扩散。
3、促进氨基酸中酪氨酸和⾊氨酸的代谢,延长肌体寿命。
4、改善铁、钙和叶酸的利⽤。
5、改善脂肪和类脂特别是胆固醇的代谢,预防⼼⾎管病。
6、促进⽛齿和⾻骼的⽣长,防⽌⽛床出⾎。
7、增强肌体对外界环境的抗应激能⼒和免疫⼒。
1.1.2维⽣素C注射液的药理性质本品为维⽣素类药。
维⽣素C参与氨基酸代谢、神经递质的合成、胶原蛋⽩和组织细胞间质的合成,可降低⽑细⾎管的通透性,加速⾎液的凝固,刺激凝⾎功能,促进铁在肠内吸收,促使⾎脂下降,增加对感染的抵抗⼒,参与解毒功能,且有抗组胺的作⽤及阻⽌致癌物质(亚硝胺)⽣成的作⽤。
1.1.3药代动⼒学蛋⽩结合率低。
少量贮藏于⾎浆和细胞,以腺体组织内的浓度为最⾼。
肝内代谢。
极少数以原形物或代谢物经肾排泄,当⾎浆浓度⼤于14g/ml时,尿内排出量增多。
可经⾎液透析清除。
1.1.4适应症(1)⽤于治疗坏⾎病,也可⽤于各种急慢性传染性疾病及紫癜等辅助治疗。
脂质体维生素c原料生产

脂质体维生素c原料生产
脂质体是一种由磷脂双分子层包裹的微粒,其结构和细胞膜类似,可以用于有效地输送各种药物和营养成分。
在近年来的研究中,脂质
体被广泛应用于维生素C原料的生产中,其具有突出的优势。
首先,脂质体维生素C原料的生产具有高效率的特点。
脂质体可
以提高维生素C的稳定性,防止其与外界环境接触导致氧化,从而提
高维生素C的质量和纯度。
此外,脂质体还能够增加维生素C在体内
的生物可利用度,使其更有效地发挥作用。
其次,脂质体维生素C原料的生产具有良好的生物相容性。
脂质
体是由天然磷脂构成,和人体细胞膜的组成相似,不会对人体产生毒
副作用。
这一特点使得脂质体制剂能够更好地被人体吸收和利用,减
少了不良反应的发生。
此外,脂质体维生素C原料的生产过程相对简单,不需要复杂的
设备和技术。
只需要将维生素C与磷脂混合搅拌,经过适当的处理和
改进,即可得到高质量的脂质体维生素C原料。
这一简单的生产过程
使得脂质体维生素C的制备成本较低,更加适合大规模工业化生产。
在实际应用中,脂质体维生素C原料可以用于多种领域。
例如,
可以将其应用于保健品和药品中,用于提高人体免疫力、预防感冒和
治疗慢性疾病。
此外,脂质体维生素C原料还可以用于化妆品中,起
到美白、抗氧化和抗衰老的作用。
总之,脂质体维生素C原料的生产具有高效率、良好的生物相容性和简单的制备过程的优势。
在今后的发展中,我们应进一步完善脂质体维生素C的生产技术,推动其在各个领域的广泛应用,为人类健康事业做出更大的贡献。
- 1、下载文档前请自行甄别文档内容的完整性,平台不提供额外的编辑、内容补充、找答案等附加服务。
- 2、"仅部分预览"的文档,不可在线预览部分如存在完整性等问题,可反馈申请退款(可完整预览的文档不适用该条件!)。
- 3、如文档侵犯您的权益,请联系客服反馈,我们会尽快为您处理(人工客服工作时间:9:00-18:30)。
生产案例二维生素C发酵维生素C在国外,1938年开始工业化生产,主要用作保健品及食品添加剂。
一般采用采用莱氏化学法。
生产流程图如下:在国内,开始工业化生产有30多年历史,主要作为药用。
采用自行开发的发酵法,分为发酵,提取,转化三个步骤。
1、发酵过程:2、提取过程:3、转化过程:莱氏法的优点是生产工艺成熟,总收率能到达60%〔对D-山梨醇计〕,优级品率为100%,但生产中为使其它羟基不受影响,需用丙酮保护,使反响步骤增多,连续操作有困难,且原料丙酮用量大,苯毒性大,劳动保护强度大,并污染环境。
由于存在上述问题,莱氏法工艺已逐步被两步发酵法所取代。
两步发酵法也是以葡萄糖为原料,经高压催化氢化、两步微生物〔黑醋菌、假单孢杆菌和氧化葡萄糖酸杆菌的混合菌株〕氧化,酸〔或碱〕转化等工序制得维生素C。
这种方法系将莱氏法中的丙酮保护和化学氧化及脱保护等三步改成一步混合菌株生物氧化。
因为生物氧化具有特异的选择性,利用适宜的菌将碳上羟基氧化,可以省去保护和脱保护两步反响。
此法的最大特点是革除了大量的有机溶剂,改善了劳动条件和环境保护问题,近年来又去掉了动力搅拌,大大地节约了能源。
我国已全部采用两步发酵法工艺,淘汰了莱氏法工艺。
第一节L-山梨糖的制备一、菌种制备黑醋菌是一种小短杆菌,属革兰氏阴性菌〔G-〕,生长温度为30~36℃,最适温度为30~33℃。
培养方法:将黑醋菌保存于斜面培养基中,每月传代一次,保存于0~5℃冰箱内。
菌种从斜面培养基移入三角瓶种液培养基中,在30~33℃振荡培养48h,合并入血清瓶内,糖量在100mg/ml以上,镜检菌体正常,无杂菌,可接入生产。
二、发酵液制备种子培养分为一、二级种子罐培养,都以质量浓度为16%~2021D-山梨醇投料,并以玉米浆、酵母膏、泡敌、碳酸钙、复合维生素B、磷酸盐、硫酸盐等为培养基,在pH5.4~5.6下于12021温30min灭菌,待罐温冷却至30~34℃,用微孔法接种。
在此温度下,通入无菌空气〔1VVM〕,并维持罐压0.03~0.05MPa 进行一、二级种子培养。
当一级种子罐产糖量大于50mg/ml〔发酵率达40%以上〕,二级种子罐产糖量大于70mg/ml〔发酵率在50%以上〕,菌体正常,即可移种。
三、发酵罐发酵以2021右D-山梨醇为投料浓度,另以玉米浆、尿素为培养基,在pH5.4~5.6,灭菌消毒冷却后,按接种量为10%接入二级种子培养液。
在31~34℃,通入无菌空气〔0.7VVM〕,维持罐压0.03~0.05Mpa等条件下进行培养。
当发酵率在95%以上,温度略高〔31~33℃〕、pH在7.2左右,糖量不再上升时即为发酵的终点。
四、发酵液处理将发酵液过滤除去菌体,然后控制真空度在0.05MPa以上,温度在60℃以下,将滤液减压浓缩结晶即得L-山梨糖。
第二节2-酮基-L-古龙酸的制备一、菌种制备将保存于冷冻管的假单孢杆菌和氧化葡萄糖酸杆菌菌种活化,别离及混合培养后移入三角瓶种液培养基中,在29~33℃振荡培养24h,产酸量在6~9mg/ml,pH值降至7以下,菌形正常无杂菌,再移入血清瓶中,即可接入生产。
二、发酵液制备先在一级种子培养罐内参加经过灭菌后的辅料〔玉米浆、尿素及无机盐〕和醪液〔折纯含山梨糖1%〕,控制温度为29~30℃,发酵初期温度较低,通入无菌空气维持罐压为0.05MPa,pH6.7~7.0,至产酸量达合格浓度,且不再增加时,接入二级种子罐培养,条件控制同前。
作为伴生菌的芽孢杆菌开始形成芽孢时,产酸菌株开始产生2-酮基-L-古龙酸,直到完全形成芽孢和出现游离芽孢时,产酸量达顶峰〔5mg/ml以上〕为二级种子培养终点。
三、发酵罐发酵供发酵罐用的培养基经灭菌冷却后,参加至山梨糖的发酵液内,接入第二步发酵菌种的二级种子培养液,在温度30℃,通入无菌空气下进行发酵,为保证产酸正常进行,往往定期滴加灭菌的碳酸钠溶液调pH值,使保持7.0左右。
当温度略高〔31~33℃〕,pH 在7.2左右、二次检测酸量不再增加,残糖量0.5mg/ml以下,即为发酵终点,得含古龙酸钠的发酵液。
此时游离芽孢及残存芽孢杆菌菌体已逐步自溶成碎片,用显微镜观察已无法区分两种细菌的差异,整个产酸反响到此也就结束了。
所以,根据芽孢的形成时间来控制发酵是一种有效的方法。
在整个发酵期间,保持一定数量的氧化葡萄糖酸杆菌〔产酸菌〕是发酵的关键。
整个发酵过程可分为产酸前期、产酸中期和产酸后期。
产酸前期主要是菌体适应环境进行生长的阶段。
该阶段产酸量很少,为了提高发酵收率应尽可能缩短产酸前期。
产酸前期长短与底物浓度、接种量、初始pH及溶氧浓度等有关。
产酸中期是菌体大量积累产物的时期。
产酸中期的时间主要决定于产酸前期菌体的生长的好坏和中期的溶氧浓度控制,也与pH值等有关。
因此适宜的操作条件可获得较大的产酸速率和较长的发酵中期,从而可提高发酵收率。
产酸后期,菌体活性下降,产酸速率变小,同时局部酸发生分解,引起酸浓度下降。
生产上由于要求发酵液中残糖浓度小于0.5mg/ml,不可能提前终止发酵,所以在此期间应采取措施,设法延长菌体活性,使之继续产酸。
影响发酵产率的因素主要有以下几点:(1)山梨糖初始浓度在一定的温度〔30℃〕、压力〔表压0.05Mpa〕和pH〔6.7~7.0〕和溶液氧浓度〔10% ~60%〕下存在一个极限浓度,此极限浓度为80mg/ml。
当山梨醇浓度大于该浓度时,将抑制菌体生长,表现为产酸前期长,产酸速率变小,使发酵产率下降。
从生产角度考虑,希望得到尽可能高的酸浓度,也即要求山梨糖初始浓度越高越好。
因此,较适宜的初始浓度为80mg/ml左右。
在产酸中期,菌体生长正常时,高浓度的山梨糖对发酵收率影响不大。
因此,在发酵过程中滴加山梨糖或一次补加山梨糖均能提高发酵液中产物浓度。
(2)溶氧浓度在发酵过程中,溶氧不但是菌体生长所必需的条件,而且又是反响物之一。
在菌体生长阶段,高溶氧能使菌体很好地生长,而在中期,那么应控制一定的溶氧浓度以限制菌体的过渡生长,防止过早衰老,从而延长菌体的生产期。
中期溶氧浓度越高,产酸速率越大,但产酸中期越短,这对整个发酵过程是不利的。
因此,生产上一般前期处于高的溶氧状态;中期溶氧以3.5~6.0mg/ml为宜;后期耗氧减少,大多数情况下溶氧浓度会上升。
(3)pH值发酵过程中如pH降至6.4是不利的,如能通过连续的调节使pH维持于6.7~7.9间对发酵是有利的。
.四、2-酮基-L-古龙酸的提取2-酮基-L-古龙酸是将2-酮基-L-古龙酸钠用离子交换法经过两次交换,去掉其中Na+而得。
一次、二次交换中均采用732阳离子交换树脂。
(1)工艺过程a.一次交换将发酵液冷却后用盐酸酸化,调至菌体蛋白等电点,使菌体蛋白沉淀。
静置数小时后去掉菌体蛋白,将酸化上清液以2~3m3/h的流速压入一次阳离子交换柱进行离子交换。
当回流到pH3.5时,开始收集交换液,控制流出液的pH值,以防树脂饱和,发酵液交换完后,用纯水洗柱,至流出液古龙酸含量低于1mg/ml以下为止。
当流出液到达一定pH值时,那么更换树脂进行交换,原树脂进行再生处理。
b.加热过滤将经过一次交换后的流出液和洗液合并,在加热罐内调pH至蛋白质等电点,然后加热至70℃左右,加0.3%左右的活性炭,升温至90~95℃后再保温10~15min,使菌体蛋白凝结。
停搅拌,快速冷却,高速离心过滤得清液。
c.二次交换将酸性上清液打入二次交换柱进行离子交换,至流出液的pH1.5时,开始收集交换液,控制流出液pH1.5~1.7,交换完毕,洗柱至流出液古龙酸含量在1mg/ml以下为止。
假设pH>1.7时,需更换交换柱。
d.减压浓缩结晶先将二次交换液进行一级真空浓缩,温度45℃,至浓缩液的相对密度达1.2左右,即可出料。
接着,又在同样条件下进行二级浓缩,然后参加少量乙醇,冷却结晶,甩滤并用冰乙醇洗涤,得2-酮基-L-古龙酸。
如果以后工序使用碱转化,那么需将2-酮基-L-古龙酸进行真空枯燥,以除去局部水分。
(2)考前须知及“三废处理〞a.调好等电点是凝聚菌体蛋白的重要因素。
b.树脂再生的好坏直接影响2-酮基-L-古龙酸的提取。
标准为进出酸差小于1%、无Cl-。
c.浓缩时,温度控制在45℃左右较好,以防止跑料和碳化。
d.结晶母液可再浓缩和结晶甩滤,加以回收以提高收率;废盐酸回收后可再用于第一次交换。
第三节粗品维C的制备由2-酮基-L-古龙酸〔简称古龙酸〕转化成维C的方法目前已从酸转化开展到碱转化、酶转化,使维C生产工艺日趋完善。
一、酸转化①反响原理见莱氏法生产粗维C酸转化的反响原理。
②工艺过程配料比为2-酮基-L-古龙酸:38%盐酸:丙酮=1:0.4〔W/ W〕:0.3〔W/ W〕。
先将丙酮及一半古龙酸参加转化罐搅拌,再参加盐酸和余下的古龙酸。
待罐夹层满水后开蒸汽阀,缓慢升温至30~38℃关汽,自然升温至52~54℃,保温约5h,反响到达高潮,结晶析出,罐内温度稍有上升,最高可达59℃,严格控制温度不能超过60℃。
反响过程中为防止泡沫过多引起冒罐,可在投料时参加一定量的泡敌作消泡剂。
剧烈反响期后,维持温度在50~52℃,至总保温时间为2021开冷却水降温1h,参加适量乙醇,冷却至-2℃,放料。
甩滤0.5h后用冰乙醇洗涤,甩干,再洗涤,甩干3h左右,枯燥后得粗维C。
③影响因素盐酸浓度低,转化不完全;浓度过高,那么分解生成许多杂质,使反响物色深,一般盐酸浓度为38%。
转化反响中需参加一定量丙酮,以溶解反响中生成的糠醛,防止其聚合,保持物料中有一定浓度的糠醛,从而防止抗坏血酸的进一步分解生成更多的糠醛。
二、碱转化(1)反响原理 先将古龙酸与甲醇进行酯化反响,再用碳酸氢钠将2-酮基-L-古龙酸甲酯转化成钠盐,最后用硫酸酸化得粗维C 。
反响过程如下:2-酮基-L-古龙酸甲酯维生素C 钠盐粗维生素C(2)工艺过程a.酯化 将甲醇、浓硫酸和枯燥的古龙酸参加罐内,搅拌并加热,使温度为66~68℃,反响4h 左右即为酯化终点。
然后冷却,参加碳酸氢钠,再升温至66℃左右,回流10h 后即为转化终点。
再冷却至0℃,离心别离,取出维生素C 钠盐,母液回收。
b.酸化 将维C 钠盐和一次母液干品、甲醇参加罐内,搅拌,用硫酸调至反响液pH 为2..2~2.4,并在40℃左右保温1.5h ,然 OH H CH 2OH H H HO C C C C HO COOH O + CH 3OH 浓[酯化]H 2SO 466~68℃[转化]33OH H 2OHH H HO CC C C HO COOCH 3O C O C C C C CH 2OH HO HO NaO H H COCC CC CH 2OHHO HO HO H HO后冷却,离心别离,弃去硫酸钠。