钢的连续浇铸
炼钢连铸工艺流程介绍
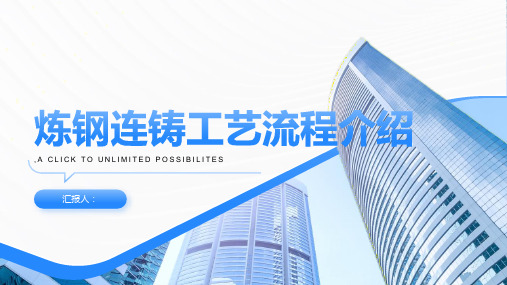
主要方法:采 用脱硫、脱磷、
脱碳等方法
设备:铁水预 处理设备,如 脱硫罐、脱磷
罐等
效果:提高铁 水质量,降低 钢中杂质含量, 提高钢的力学 性能和耐腐蚀
性
转炉炼钢原理:利用高温熔融的钢水与氧气反应,生成铁水与钢渣
转炉炼钢设备:包括转炉、氧枪、钢包等 转炉炼钢过程:将铁水倒入转炉,加入氧气进行反应,生成铁水与钢渣, 然后进行钢渣分离和钢水精炼 转炉炼钢优点:生产效率高,产品质量好,成本低,环保性能好
连铸机的维护:定期检查、维护和 保养,确保连铸机的正常运行
提高生产效率:采用先进的自动化技术,提高生产效率,降低生产成本 节能减排:采用节能环保技术,减少能源消耗,降低环境污染 提高产品质量:采用先进的工艺技术,提高产品质量,满足市场需求 智能化发展:采用先进的智能化技术,实现生产过程的智能化控制,提高生产效率和产品质量
工艺流程:钢液在炉外精炼 设备中进行脱硫、脱氧、脱
碳等处理
优点:提高钢液质量,减少 杂质,降低成本,提高生产
效率
连铸工艺:将钢水连续铸造成钢坯 的工艺
关键技术:连铸机的设计、控制和 维护
连铸机的类型:立式连铸机、卧式 连铸机等
连铸机的工作原理:钢水通过连铸 机,冷却凝固成钢坯
连铸机的控制:温度、速度、压力 等参数的控制
切割速度:根据铸坯尺寸和材质选择合适的 切割速度
切割温度:控制切割温度在1000℃左右, 防止铸坯过热或过冷影响切割质量
切割后处理:切割后对铸坯进行冷却、打 磨等处理,保证铸坯表面光滑、无毛刺
切割质量控制:定期对切割设备进行维护和 校准,确保切割质量稳定可靠。
目的:去除铁 水中的杂质和 气体,提高铁
电炉炼钢原理: 利用电弧热能 熔化废钢和铁 水,生产出钢
钢水罐水平连浇车的连铸工艺流程

初步冷却:钢水在模具中初步冷却,形成固态钢坯的初步形态。
6
模具移动:连浇车带动模具移动,使钢坯逐渐离开浇铸区,进入后续的冷却区域。
7
二次冷却:钢坯在冷却区域进行二次冷却,确保钢坯完全凝固并达到所需的机械性能。
8
钢坯切割:冷却后的钢坯通过切割设备进行定长切割,得到一定长度的钢坯产品。
9
钢坯收集与质检:收集切割好的钢坯,并进行质量检验,确保产品质量符合标准。
连铸工艺做准备。
钢水罐水平连浇车的连铸工艺流程
步骤
工艺流程
1
钢水罐装载:将炼好的钢水倒入钢水罐中,确保钢水温度和质量符合要求。
2
钢水罐运输:将装有钢水的钢水罐运送到连浇车附近,准备进行浇铸。
3
浇铸前准备:检查连浇车及其相关设备是否正常运行,准备好浇铸模具和冷却水等。
4
钢水浇铸:将钢水罐的钢水通过连浇车均匀倒入浇铸模具中,控制浇铸速度和温度。
连铸工艺流程

连铸工艺流程连铸是一种常用的铸造工艺,适用于生产长条状或板状金属材料。
它是通过将熔化的金属直接倒入连续流动的水冷铜板中,使其冷却并形成连续的长条状或板状产品。
连铸工艺具有高效率、低能耗、高品质等优点,广泛应用于钢铁、铝合金等行业。
连铸工艺流程主要包括准备工作、连续浇铸、冷却和切割四个阶段。
首先是准备工作。
这个阶段包括准备熔炉、铜板、铸模、流动水和其他所需设备和材料。
熔炉中加入合适的金属原料,加热使其熔化。
同时,准备好冷却水,并确保其具有足够的流动性和温度适宜。
铜板和铸模是制造连铸机的主要部件,需要进行充分的清洗和检查,以确保表面平整和无缺陷。
接下来是连续浇铸。
将熔化的金属倒入连铸机的铜板中,通过喷头将金属喷向铸模,并使其连续地流动。
连铸机的喷头是一个关键部件,可以调整金属流动的速度和方向,以保证产品的质量。
同时,需要控制好浇注速度和温度,以避免金属过热或过冷,影响产品的性能。
然后是冷却。
在连铸过程中,金属材料与铜板接触,通过快速传热,使金属迅速冷却并凝固。
冷却水通过铜板流过,吸收金属的热量,并保持适宜的温度。
冷却水的流量和温度需要根据不同金属材料进行调整,以确保产品的结晶组织和力学性能。
最后是切割。
冷却后的连铸坯可以根据需要进行切割成适当的长度,以便进一步加工。
切割可以通过割断或切削进行。
割断是指使用切割设备将连铸坯切成所需长度,并去除不良部分。
切削是指使用机械切割工具将连铸坯切割成规定的尺寸和形状。
总之,连铸工艺是一种高效、高品质的铸造工艺,适用于生产长条状或板状金属材料。
其主要流程包括准备工作、连续浇铸、冷却和切割。
通过合理调整浇注速度、温度和冷却设备,可以制造出具有良好结晶组织和优异性能的产品。
连铸工艺的应用范围广泛,为钢铁、铝合金等行业的发展提供了重要的支撑。
连铸技术在钢铁冶炼中的应用

连铸技术在钢铁冶炼中的应用现代钢铁冶炼中的一项关键技术是连铸技术。
连铸技术是将液态钢浇注到连续铸机冷却结构上,形成连续的厚板、薄板、管材、工字钢等钢材产品,从而取代了以往钢液在浇铸过程中结晶、凝固而产生的不纯物及疵点,提高了钢材的质量。
连铸技术应用于钢铁冶炼中,提升钢材质量、生产率和经济效益,逐步普及和发展,成为钢铁行业的发展趋势。
一、连铸技术简介连铸是指将钢液在连续铸造机上,通过机械力使钢液流动的同时,紧靠着冷固结构快速凝固并形成的成品钢材。
同时,连铸设备和工艺连续化,无须在冶炼配料和成品钢材之间的中间过程转化步骤,从而提高了钢材质量,减少了能源消耗。
连铸技术的主要优点是:1. 避免了钢液在浇注过程中,由于结晶、凝固而产生的不纯物和疵点,提高了钢材的质量。
2. 减少了钢材制造过程中的能源消耗,同时提高了生产效率。
3. 减少了外观质量的不良因素,提高了铸造钢材的质量。
二、连铸工艺流程连续铸造过程中,首先将液态钢从钢包中送往浇注站,然后将钢液引入下垂式浇注管中,通过支撑装置的各种动作使钢液保持稳定的流动,进入连续铸造机,与冷却结构接触而凝固。
连续铸造过程中,一般采用感应加热方式加热钢水。
加热后的钢水通过调节水冷却器的水流,以达到理想的冷却速度,从而产生所需要的微观组织。
连续铸造机的工作原理是,将钢水通过下垂管输入机器,快速冷却成铜片,然后通过机器的牵引链条拖动,继续冷却、成型、切割制成成品钢材,整个过程实现了连续化生产,极大提升了生产力。
三、连铸技术应用案例1. 小排钢坯连铸小排钢坯连铸技术是近年来发展起来的一种先进的钢铁连铸生产工艺。
它的工艺流程与传统的结构光从钢水到钢坯形成的连铸工艺相同,但采用了先进的成杯技术,将定径后的小排钢坯成杯装载上车架,经热处理后直接送往轧机生产线,大大缩短了连铸生产过程,同时也减少了钢坯形变和凝固的不正常现象,大大提高了钢坯的质量。
2. 大直径碳素钢连铸大直径碳素钢连铸是在特别条件下,通过添加稳定剂、合理调整冷却条件来控制晶粒尺寸,使连铸坯疏松度降低,提高了连铸物质的牢度和成品合格率,在保证钢质量同时,也增加了生产量。
连续浇铸法
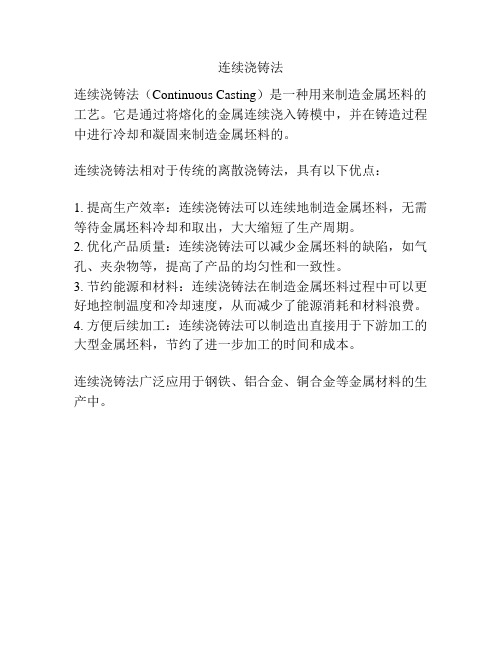
连续浇铸法
连续浇铸法(Continuous Casting)是一种用来制造金属坯料的工艺。
它是通过将熔化的金属连续浇入铸模中,并在铸造过程中进行冷却和凝固来制造金属坯料的。
连续浇铸法相对于传统的离散浇铸法,具有以下优点:
1. 提高生产效率:连续浇铸法可以连续地制造金属坯料,无需等待金属坯料冷却和取出,大大缩短了生产周期。
2. 优化产品质量:连续浇铸法可以减少金属坯料的缺陷,如气孔、夹杂物等,提高了产品的均匀性和一致性。
3. 节约能源和材料:连续浇铸法在制造金属坯料过程中可以更好地控制温度和冷却速度,从而减少了能源消耗和材料浪费。
4. 方便后续加工:连续浇铸法可以制造出直接用于下游加工的大型金属坯料,节约了进一步加工的时间和成本。
连续浇铸法广泛应用于钢铁、铝合金、铜合金等金属材料的生产中。
连铸坯生产工艺

连铸坯生产工艺连铸坯生产工艺是一种将炼钢后的金属浇铸成特定形状和尺寸的制钢工艺。
以下是连铸坯生产工艺的主要步骤:1.炼钢生产炼钢生产是连铸坯生产的第一步。
在这个过程中,铁水被加入到炼钢炉中,并加入碳和其他合金元素,以调整钢的化学成分。
炼钢过程中需要注意安全,避免高温和化学成分对工人健康的影响。
2.连铸浇铸连铸浇铸是将钢水连续地浇铸成特定形状和尺寸的工艺过程。
浇铸时,钢水通过钢包注入结晶器,在结晶器中冷却并形成一定形状的连铸坯。
这个过程中需要注意控制钢水的温度和流量,以保证连铸坯的质量。
3.冷却与切割连铸坯在浇铸完成后需要进行冷却和切割。
冷却过程中,连铸坯被送入冷却塔或水冷装置中,以去除热量并防止变形。
切割则是将连铸坯按照需要的长度和形状进行切割,以便后续加工。
这个过程中需要注意避免连铸坯变形和开裂。
4.矫直与弯曲矫直和弯曲是使连铸坯恢复到原来形状和尺寸的工艺过程。
矫直是将连铸坯的弯曲部分矫直,使其形状更加平整。
弯曲则是将矫直后的连铸坯按照需要的形状进行弯曲。
这个过程中需要注意控制机械力和温度,以避免对连铸坯造成损伤。
5.表面清理表面清理是去除连铸坯表面杂质和缺陷的工艺过程。
清理时可以采用机械方法或化学方法。
机械方法包括磨削、抛光、打毛等,可以去除表面粗糙、划痕等缺陷。
化学方法则是使用酸、碱等化学试剂,去除表面氧化皮、锈蚀等缺陷。
这个过程中需要注意保护工人健康,避免粉尘和化学试剂对环境的影响。
6.质量检测质量检测是确保连铸坯符合质量要求的工艺过程。
检测时可以采用各种仪器和设备,如超声波探伤、X射线探伤、磁粉探伤等,以检测连铸坯内部和表面的缺陷。
这个过程中需要注意控制检测精度和可靠性,以确保产品质量。
7.成品加工成品加工是将连铸坯加工成最终产品或半成品的工艺过程。
加工时可以采用各种机械加工方法和热处理方法,如车削、铣削、钻孔、热轧、冷拔等,以得到需要的形状和性能。
这个过程中需要注意提高加工效率和精度,降低成本。
炼钢连铸工艺流程的介绍
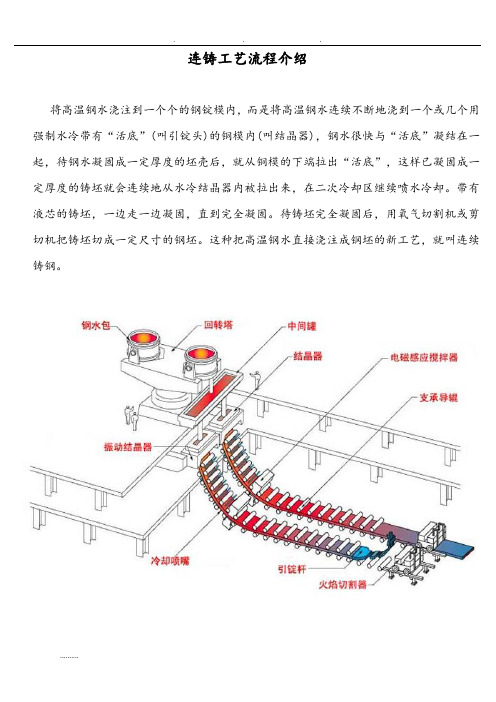
连铸工艺流程介绍将高温钢水浇注到一个个的钢锭模内,而是将高温钢水连续不断地浇到一个或几个用强制水冷带有“活底”(叫引锭头)的铜模内(叫结晶器),钢水很快与“活底”凝结在一起,待钢水凝固成一定厚度的坯壳后,就从铜模的下端拉出“活底”,这样已凝固成一定厚度的铸坯就会连续地从水冷结晶器内被拉出来,在二次冷却区继续喷水冷却。
带有液芯的铸坯,一边走一边凝固,直到完全凝固。
待铸坯完全凝固后,用氧气切割机或剪切机把铸坯切成一定尺寸的钢坯。
这种把高温钢水直接浇注成钢坯的新工艺,就叫连续铸钢。
【导读】:转炉生产出来的钢水经过精炼炉精炼以后,需要将钢水铸造成不同类型、不同规格的钢坯。
连铸工段就是将精炼后的钢水连续铸造成钢坯的生产工序,主要设备包括回转台、中间包,结晶器、拉矫机等。
本专题将详细介绍转炉(以及电炉)炼钢生产的工艺流程,主要工艺设备的工作原理以及控制要求等信息。
由于时间的仓促和编辑水平有限,专题中难免出现遗漏或错误的地方,欢迎大家补充指正。
连铸的目的: 将钢水铸造成钢坯。
将装有精炼好钢水的钢包运至回转台,回转台转动到浇注位置后,将钢水注入中间包,中间包再由水口将钢水分配到各个结晶器中去。
结晶器是连铸机的核心设备之一,它使铸件成形并迅速凝固结晶。
拉矫机与结晶振动装置共同作用,将结晶器内的铸件拉出,经冷却、电磁搅拌后,切割成一定长度的板坯。
连铸钢水的准备一、连铸钢水的温度要求:钢水温度过高的危害:①出结晶器坯壳薄,容易漏钢;②耐火材料侵蚀加快,易导致铸流失控,降低浇铸安全性;③增加非金属夹杂,影响板坯内在质量;④铸坯柱状晶发达;⑤中心偏析加重,易产生中心线裂纹。
钢水温度过低的危害:①容易发生水口堵塞,浇铸中断;②连铸表面容易产生结疱、夹渣、裂纹等缺陷;③非金属夹杂不易上浮,影响铸坯内在质量。
二、钢水在钢包中的温度控制:根据冶炼钢种严格控制出钢温度,使其在较窄的范围内变化;其次,要最大限度地减少从出钢、钢包中、钢包运送途中及进入中间包的整个过程中的温降。
转炉炼钢的五大工艺制度

转炉炼钢的五大工艺制度引言:转炉炼钢是一种常见的冶炼工艺,通过炼钢炉中高温条件下的氧气吹吹炼,将铁水和废钢等原料加工成高质量的钢材。
为了提高炼钢效率和质量,转炉炼钢采用了多种工艺制度。
本文将介绍转炉炼钢的五大工艺制度,包括氧枪喷吹工艺、钢包倾吊工艺、渣氧平衡工艺、碱性炉温保护工艺和连续浇铸工艺。
一、氧枪喷吹工艺氧枪喷吹工艺是转炉炼钢的核心工艺之一。
该工艺通过氧气喷吹,使铁水中的杂质和不良元素在高温条件下被氧化和吹出,从而提高钢材的纯度和质量。
在氧枪喷吹工艺中,需要控制氧气的流量和喷吹位置,以确保各种元素的氧化速率和炉温的控制。
二、钢包倾吊工艺钢包倾吊工艺是转炉炼钢的关键环节之一。
在钢包倾吊过程中,将经过炼钢炉炼制的钢水倾倒到钢包中,然后再将钢包倾倒到连铸坑中进行连铸。
倾吊时需要注意钢水的温度控制和倾吊速度,以确保钢水的质量和均匀性。
三、渣氧平衡工艺渣氧平衡工艺是转炉炼钢中用于控制渣铁比和氧气利用率的重要工艺。
通过合理控制渣铁比,可以提高转炉炼钢的冶炼效率和钢材质量。
同时,通过优化氧气利用率,可以减少能耗和炼钢成本。
渣氧平衡工艺需要根据具体炼钢情况进行调整,以达到最佳的效果。
四、碱性炉温保护工艺转炉炼钢中的高温条件对炉衬的腐蚀和寿命造成了严重挑战。
为了保护炉衬,常采用碱性炉温保护工艺。
该工艺通过添加适量的碱性物质,形成一层保护性的渣膜,减少炉衬的腐蚀和磨损。
碱性炉温保护工艺的成功应用,延长了转炉炼钢炉衬的使用寿命,降低了生产成本。
五、连续浇铸工艺连续浇铸工艺是转炉炼钢生产线的最后一个环节,也是实现高效率生产和优质钢材的关键。
在连续浇铸中,将炼制好的钢水连续地注入到均质的结晶器中,并通过提拉辊、冷却器等设备进行快速冷却和连续成形。
这种工艺既提高了钢材的质量,又提高了生产效率,逐渐成为转炉炼钢的主流工艺。
结论:转炉炼钢的五大工艺制度,即氧枪喷吹工艺、钢包倾吊工艺、渣氧平衡工艺、碱性炉温保护工艺和连续浇铸工艺,共同构成了转炉炼钢生产线的关键环节。
连续铸钢技术项目设计方案

连续铸钢技术项目设计方案1.1 连铸技术的发展概况连续铸钢是钢铁冶金领域内发展最快、最受重视和最为成功的技术之一,其原因在于连铸技术具有显著的技术经济优越性,是钢铁生产流程中结构优化的重要环节。
转炉的发明者亨利·贝塞麦(Herry Bessemer)于1846年首先提出了连续浇注的概念并于1857 年获得专利权。
从那时以来,近一个世纪的时间里,世界上的一些冶金工作者在连续浇铸技术方面进行了有益的探索,上世纪三十代,德国人容汉斯开创性的提出结晶器振动法,浇注铜铝合金获得成功,使有色合金的连续铸造应用于生产,金属(铜、铝)的连续铸造获得了工业应用。
但钢液的连续浇铸却始终没有获得工业化[1]。
钢的连铸取得突破性进展是由1945 年,容汉斯(S.Junghans)及其合作者罗西(I.Rossi)采用了振动式结晶器代替以前的固定式结晶器,解决了固定式结晶器拉坯漏钢的难题,钢水的连铸才首次获得成功。
1950 年容汉斯和曼内斯曼(Mannesmann)公司合作,建成了世界上第一台能浇铸 5 t 钢水的连铸机[2]。
钢水连铸获得巨大成功的另一重要的技术关键是英国人哈里德(Halliday)提出的“负滑脱(Negative Slip)”的概念。
“负滑脱”能够有效地防止了凝固壳与结晶器的粘结和更好地改善润滑。
20 世纪40 年代,德国建成了第一台浇注钢水的实验性连铸机。
连铸技术在20 世纪50 年代初开始步入工业应用阶段,70 年代以后钢的连铸技术迅速发展,80 年代连铸技术日臻完善,一个国家的连铸技术水平的高低己成为衡量其钢铁工业现代化程度的重要标志。
20 世纪90 年代,随着钢的连铸技术的日益成熟,连铸技术又有新的重大发展。
从那时以来,薄板坯连铸(连轧)技术在世界上获得了重大发展;薄带连铸技术也受到广泛重视,进行了深入研究;高效连铸技术随之出现,并获得了迅速发展。
今天,钢的连铸技术无论从深度和广度上,都远远超过了20 世纪80年代的水平。
13.1 钢的连续浇铸
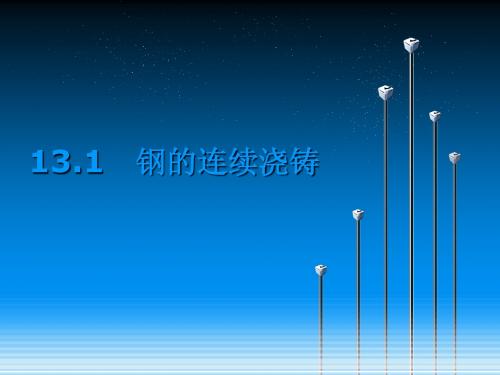
(4)生产过程机械化、自动化程度高。设备和操作水平的提高,采用全过程的计
算机管理,不仅从根本上改善了劳动环境,还大大提高了劳动生产率。 (5)提高质量,扩大品种。几乎所有的钢种均可以采用连铸工艺生产。如超纯净
度钢、硅钢、合金钢、工具钢等约500多个钢种都可以用连铸工艺生产,而且质量
很好。
Your company slogan
连铸机等。
Your company slogan
13.1.3
连铸机的基本机型及其特点
Your company slogan
13.1.3
连铸机的基本机型及其特点
Your company slogan
13.1.3
连铸机的基本机型及其特点
按结晶器是否移动可以分为两类:一类是固定式结晶器(包括固定振动结晶器 )的各种连铸机,如立式连铸机、立弯式连铸机、弧形连铸机、椭圆形连铸机、水 平式连铸机等。这些机型已经成为现代化连铸机的基本机型,如图13-2所示。另— 类是同步运动式结晶器的各种连铸机,如图13-3所示。这类机型的结晶器与铸坯同 步移动,铸坯与结晶器壁间无相对运动,因而也没有相对摩擦.能够达到较高的浇
曾遇到过。因此,要在炼钢领域实现连铸生产,要做的最重要的一项开拓性工作
是如何提高一台连铸机的浇铸能力,最关键的是浇铸速度。1913年,瑞典人皮尔 逊提出结晶器以可变的频率和振幅做往复振动的想法。1933年德国人容汉斯(
S.Junghans)真正将这一想法付诸实施。
Your company slogan
铸速度,适合于生产接近成品钢材尺寸的小断面或薄断面的铸坯,即近终形连铸。
如双辊式连铸机、单辊式这铸机、双带式连铸机、单带式这铸机。轮带式连铸机等 。这些也是正在开发中的连铸机机型。 按铸坯断面形状可分为:方坯连铸机、圆坯连铸机、板坯连铸机、异型连铸机 、方/板坯兼用型连铸机等。按钢水的静压头可分为:高头型、低头型和超低头型
连续铸钢工艺教程

连续铸钢工艺教程1.连铸工艺连铸工艺介绍连铸全称连续铸钢,与模铸不同,它不是将高温钢水浇铸到一个个的钢锭模内,而是将高温钢水浇注到一个或几个用强制水冷、带有“活底”(叫引锭头)的铜模内(叫结晶器),钢水很快与“活底”凝结在一起,待钢水凝固成一定厚度的坯壳后,就从铜模的下端拉出“活底”,这样已凝固成一定厚度的铸坯就会连续不断地从水冷结晶器内被拉出来,,在二次冷却区继续喷水冷却,带有液芯的铸坯一边走一边凝固,直到完全凝固,待铸坯完全凝固后,用氧气切割或剪切机把铸坯切成一定尺寸的钢坯。
连铸是连接炼钢和轧钢的中间环节,是炼钢生产的重要组成部分,连铸生产的正常与否,不但会影响到炼钢生产任务的完成,还会影响到轧材的质量和成材率。
一台连铸机主要由大包回转台、中间包、中间包车、结晶器、结晶器振动装置、二次冷却装置、拉坯矫直装置、切割装置和出坯辊道等部分组成。
在连铸生产时通常用天车将钢包吊至大包回转台,然后大包转台将钢包旋至浇注位,经大包底部水口把钢水注入到中间包内,打开中间包塞棒后,钢水流入到下口用引锭杆堵塞并能上下振动的结晶器中,钢水沿结晶器周边冷凝成坯壳,当结晶器下端出口处坯壳有一定厚度时,带有液芯并和引锭杆连在一起的铸坯在拉矫装置的作用下,离开结晶器,沿着二冷段的支撑结构下移,与此同时铸坯被二次冷却装置进一步冷却并继续凝固,当引锭装置进入拉矫机后脱去引锭装置,铸坯在全部凝固或带有液芯的状态下被矫直,随后在水平位置被切割成定尺长度,经出坯辊道运送到规定地点,上述整个过程在实际生产中是连续进行的。
连铸的主要设备1.3.1钢包回转台钢包回转台设置在电炉、精炼同一跨,它的本体是一个具有两个钢包支撑架的转臂,绕回转台中心回转,钢包回转台工作时,出钢跨一侧的天车将盛满钢水的钢包吊放到支撑架上,然后回转台旋转180o,将钢包转到连铸跨中间包上方的浇注位进行浇注,浇注完毕,再把空包转出的同时,又把另一个盛满钢水的钢包旋转到浇注位置,这样就可以快速更换钢包,实现多炉连浇。
(八)钢的浇注
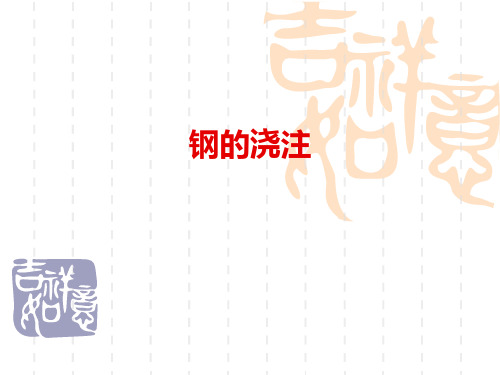
3、浇注方法的选用 (根据钢锭大小、钢种特点和生产条件等合理选择) ①对表面质量要求严格的的钢采用下注法(如:不锈钢、硅钢、轧制薄钢) ②对内部质量要求较高的钢采用上注法(如轴承钢、炮钢) ③对体积收缩大、线性收缩性小的高碳钢宜采用上注法 ④对体积收缩小、线性收缩性大的低碳钢宜采用下注法 ⑤小钢锭适合于下注法 ⑥沸腾钢适于下注,半镇静钢适于上注
( a)
( b)
图14—1 上注法和下注法 a—上注法;b —下注法 1一塞棒;2一钢包,3——水口;4一钢锭模;5一底盘;6一中注管;7—汤道
2、铸锭工艺
铸锭工艺流程: 清理盛钢桶→干燥盛钢桶→选择水口→清除中注管夹杂物(下注法)→ →清除汤道砖内杂物(下注法)→底板清理→安装保温帽→浇注 →钢锭处理(生产准备→浇注钢锭→钢锭处理)。 钢锭浇注:镇静→选择合理的浇注温度和浇注速度→保护浇注→操作 镇静作用:①使钢液脱氧和合金化完全,成分进一步均匀; ②使脱氧产物和其他外来夹杂物充分上浮排出,以纯净钢质; ③均匀钢液温度。
坑铸 (全部作业在铸锭跨内进行)
根据浇注系统的摆放位置 车铸 (脱模、整模等均在另外的
厂房内进行)
根据钢液由盛钢桶注入钢锭模的方式
上注法 下注法
钢的浇注
2、上注法和下注法 ①下注法:优点:表面质量好、有利于钢种气体向上排出,同时浇注多支钢锭 缺点:夹杂物多,不能补缩,内部质量差 ②上注法:优点:内部质量好 缺点:飞溅,浇注支数少
3、连铸坯结构特点
细小的等轴晶带、柱状晶带、粗大等轴晶带。
与钢锭相比其特点为: (1)因冷却强度大,因此激冷层较钢锭厚,晶粒也细小,且可以得到铸坯特 的无侧枝的细柱状晶; (2)铸坯始终处于强制冷却状态,柱状晶比较发达,容易造成穿晶结构; (3)铸坯比钢锭组织致密。
钢的连续浇铸讲解
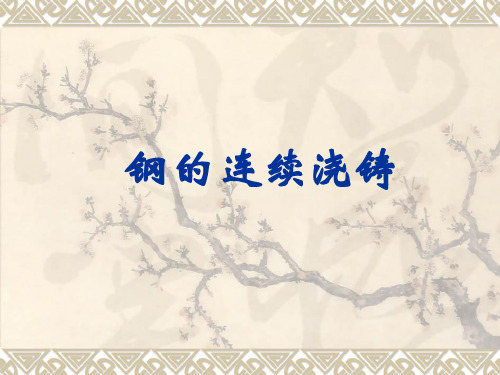
降低了能源消耗
采用连铸工艺比传统工艺可节能1/4-1/2。
生产过程机械化、自动化程度高
设备和操作水平的提高,采用全过程的计算机管理,不仅 从根本上改善了劳动环境,还大大提高了劳动生产率。
提高质量,扩大品种
几乎所有的钢种均可以采用连铸工艺生产,如超纯净度钢、 硅钢、合金钢、工具钢等约500多个钢种都可以用连铸工艺 生产,而且质量很好。
1.2连铸的发展史
1.2.1 早期尝试
美国亚瑟(B.Atha)(1866年)和德国土木 工程师达勒恩(R.M.Daelen)(1877年)最早提出 以水冷、底部敞口固定结晶器为特征的常规连铸 概念。前者采用一个底部敞开、垂直固定的厚壁 铁结晶器并与中间包相连,施行间歇式拉坯;后 者采用固定式水冷薄壁铜结晶器、施行连续拉坯、 二次冷却,并带飞剪切割、引锭杆垂直存放装置。 1920~1935年间,连铸过程主要用于有色金属, 尤其是铜和铝的领域。
1.2.2 40年代连续铸钢的试验开发
在40年代钢的连铸试验开发主要集中在美 国和欧洲。
虽然振动式结晶器是钢得以顺利连铸的 开创性的技术关键,但真正有效防止坯壳与 结晶器粘结的突破性进展的技术贡献,应当 归功于英国人哈里德(Halliday)提出的 “负滑脱”概念,这有改善润滑、减轻粘结 的优点,更便于实现高速浇铸。
1.3 连铸机的机型及其特点
按结晶器是否移动可以分为两类:一类是固定式结 晶器(包括固定振动结晶器)的各种连铸机,如立 式连铸机、立弯式连铸机、弧形连铸机、椭圆形连 铸机、水平式连铸机等;另一类是同步运动式结晶 器的各种连铸机。这种机型的结晶器与铸坯同步移 动,铸坯与结晶器壁间无相对运动,适合于生产接 近成品钢材尺寸的小断面或薄断面的铸坯,如双辊式 连铸机、双带式连铸机、单辊式连铸机、单带式连 铸机,轮带式连铸机等。
炼钢厂连铸工艺流程

炼钢厂2#连铸机工序简介
利用天车将钢包吊起放置在连铸钢包回转台准备浇铸作业.
连铸封好引锭,设备及辅助设施满足浇注条件,将中间包车开到浇注位,连铸浇铸首先打开钢包滑动水口,钢流正常后套上浸入式水口,待中间罐面升至开浇位时,大包测温,开启中间包塞棒,钢流流入结晶器,待正常时套上浸入式水口,液面超过浸入式水口下端后即开始加入保护渣,结晶器开始振动,拉矫机开始拉坯操作,启动结晶器电磁搅拌。
铸坯拉出结晶器后在足辊区就开始冷却,直到铸坯导向段的前
段。
铸坯喷水冷却可防止发生漏钢事故,保证在切割前达到全凝状态,铸坯头部到达末端电磁搅拌位置时启动末端电磁搅拌。
全凝的高温铸坯由引锭杆牵引穿过拉矫机时被连续矫直,引锭装置抬起将铸坯坯头与引锭头脱脱离,引锭杆由存放装置快速提升后存放在辊道上方.被矫直的高温铸坯由中间辊道支承引导送入火焰切割区,首先切下坯头,然后按定尺切割铸坯。
定尺铸坯由输出辊道输入升降辊道后,碰到固定挡板挡发出信号,将铸坯停在升降辊道上。
天车将铸坯吊下辊道堆垛缓冷或入坑缓冷,精整工段对铸坯进行检查精整,精整后的铸坯由天车吊往轧钢部。
铸坯热送时,天车直接将高温铸坯由升降辊道吊运至轧钢部.。
连铸工作中的注意事项总结
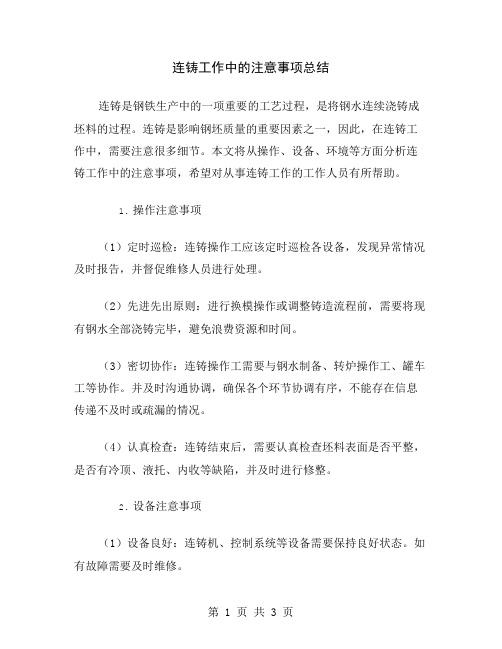
连铸工作中的注意事项总结连铸是钢铁生产中的一项重要的工艺过程,是将钢水连续浇铸成坯料的过程。
连铸是影响钢坯质量的重要因素之一,因此,在连铸工作中,需要注意很多细节。
本文将从操作、设备、环境等方面分析连铸工作中的注意事项,希望对从事连铸工作的工作人员有所帮助。
1.操作注意事项(1)定时巡检:连铸操作工应该定时巡检各设备,发现异常情况及时报告,并督促维修人员进行处理。
(2)先进先出原则:进行换模操作或调整铸造流程前,需要将现有钢水全部浇铸完毕,避免浪费资源和时间。
(3)密切协作:连铸操作工需要与钢水制备、转炉操作工、罐车工等协作。
并及时沟通协调,确保各个环节协调有序,不能存在信息传递不及时或疏漏的情况。
(4)认真检查:连铸结束后,需要认真检查坯料表面是否平整,是否有冷顶、液托、内收等缺陷,并及时进行修整。
2.设备注意事项(1)设备良好:连铸机、控制系统等设备需要保持良好状态。
如有故障需要及时维修。
(2)精度保障:连铸机的精度决定了坯料的质量。
检查设备的精度是否达到生产要求,定期检查和维护精度要求较高的设备。
(3)密封措施:连铸机需要保证密封性,以防止水外泄,同时也可以提高浇注坯料的成形率。
(4)防溅措施:连铸机在工作时,钢水容易产生溅射,危害工作人员的安全。
因此,需要在设备周围设置防护措施,严格使用安全操作规程。
3.环境注意事项(1)温度控制:连铸环境的温度和湿度对坯料的质量影响很大,因此,需要定期检查环境的温度、湿度等参,保持合适的生产环境。
(2)通风设施:连铸操作现场应该设置通风设施,排除对操作人员的有害气体和粉尘,保护工作人员的健康。
(3)卫生清洁:操作现场应该保持干净,及时清理铸造后产生的钢渣、灰尘、污水等,保持操作现场清洁、整洁。
(4)绿色环保:钢铁生产是一个重要的污染源,环境保护是社会的共同责任。
在连工作中,应该合理使用资源,减少废弃物的产生,建立可持续的绿色生产模式。
连铸工作中需要注意的事项有很多,从操作、设备、环境等方面,都需要保持高度的警惕性。
新编连续铸钢手册 01第一篇 总论

表 1-3 20 世纪 70 年代大型转炉炼钢厂实现全连铸工厂
国别 工厂名
投产 年份
美国
麦克劳斯公司特 伦顿厂
1969
机型 铸机数 流 弧形 4 双流
铸坯断面 mm 230×(910~1524)
转炉 年产量 数量×吨位 万 t
5×110t 240
法国
敦刻尔克厂二转 炉车间
1972
弧形
3 双流
250×1650
追溯连铸技术发展的进程,大致可以分为以下几个阶段。
1.1 世界连续浇铸技术的发展经历 1.1.1 连续浇铸方法的提出
最早提出将液态金属连续浇铸成形的设想可追溯到 19 世纪 40 年代,1840 年美国的塞 勒斯(G.. E. Sellers),1843 年莱恩(J. Laing)以及 1846 年英国的贝赛麦(H. Bessemer)提 出了各种连续浇铸有色金属的方法,贝赛麦获得用双辊法浇铸可锻铸铁的专利(1856 年), 在 20 世纪 30 年代以前连续浇铸只是在有色金属中应用,例如低熔点金属铅、锌,也有用于 浇铝、铜的。
表 1-2 世界主要工业国 1970-1980 年间连铸坯产量与连铸比上升情况
国家
连铸增长
1970 年
连铸坯产量 万t
连铸比 %
1980 年
连铸坯产量 万t
连铸比 %
连铸坯平均年增长量 万t
连铸比平均年增长 %
日本 527 5.6 6627.1 59.5 610.0 5.39
德国 372.6
8.3 2016.2 46.0 164.4 3.77
由德国人德伦提出立式连铸机的雏形和 S. 容汉斯的结晶器振动技术组合。在 1933 年 容汉斯在德国建成一台浇铸黄铜的立式连铸机,并取得成功。1943 年容汉斯又建了一台浇 钢的试验机组,第二次世界大战结束,世界各主要工业国都对连铸技术进行研究,在 1946~ 1947 年间,第一批连续铸钢试验装置分别建于美国的巴布考克和威尔考克斯公司(Babcock & Wilcox)、英国的劳莫尔公司(Low Maor)、日本尼崎钢管厂,以后奥地利的布雷坦费尔 德钢厂、英国钢铁学会(BISRA)和美国阿·勒德隆(Alleghenyludlum)钢公司都建设了试 验设备。在此基础上,第一台生产型立式连续铸钢机于 1950 年在德国曼内斯曼(Mannesman) 建成。随后,1951 年原苏联红十月冶金厂建成一台浇铸不锈钢的立式半连续铸机,往后英 国巴路厂(Barrow)、加拿大阿特拉斯厂都建造立式连铸机,中国也于 1958 年在重庆第三钢 铁厂建成一台工业生产用双流矩形坯立式连铸机,当时德国、苏联是建设立式连铸机的积极 者。
炼钢厂连铸工艺流程
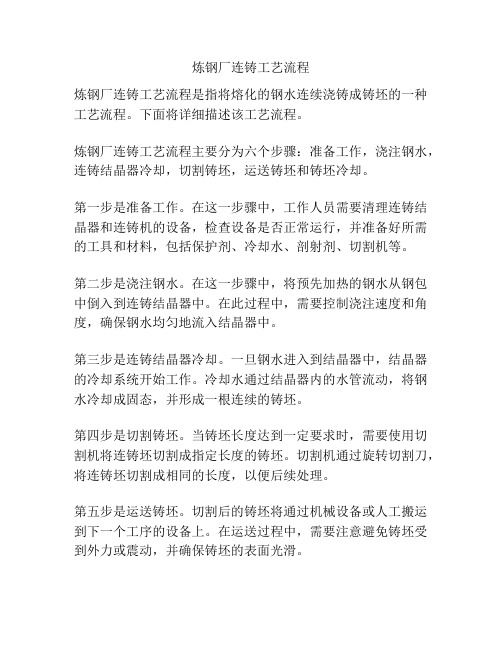
炼钢厂连铸工艺流程炼钢厂连铸工艺流程是指将熔化的钢水连续浇铸成铸坯的一种工艺流程。
下面将详细描述该工艺流程。
炼钢厂连铸工艺流程主要分为六个步骤:准备工作,浇注钢水,连铸结晶器冷却,切割铸坯,运送铸坯和铸坯冷却。
第一步是准备工作。
在这一步骤中,工作人员需要清理连铸结晶器和连铸机的设备,检查设备是否正常运行,并准备好所需的工具和材料,包括保护剂、冷却水、剖射剂、切割机等。
第二步是浇注钢水。
在这一步骤中,将预先加热的钢水从钢包中倒入到连铸结晶器中。
在此过程中,需要控制浇注速度和角度,确保钢水均匀地流入结晶器中。
第三步是连铸结晶器冷却。
一旦钢水进入到结晶器中,结晶器的冷却系统开始工作。
冷却水通过结晶器内的水管流动,将钢水冷却成固态,并形成一根连续的铸坯。
第四步是切割铸坯。
当铸坯长度达到一定要求时,需要使用切割机将连铸坯切割成指定长度的铸坯。
切割机通过旋转切割刀,将连铸坯切割成相同的长度,以便后续处理。
第五步是运送铸坯。
切割后的铸坯将通过机械设备或人工搬运到下一个工序的设备上。
在运送过程中,需要注意避免铸坯受到外力或震动,并确保铸坯的表面光滑。
第六步是铸坯冷却。
切割后的铸坯将放置在冷却区域,通过自然冷却将温度降低到适合后续处理的温度。
冷却时间的长短和冷却方式根据不同的钢种和工艺要求而有所不同。
以上就是炼钢厂连铸工艺流程的详细描述。
通过这个工艺流程,炼钢厂能够将熔化的钢水高效地连续浇铸成铸坯,为后续的热轧、冷轧等工序提供优质的原材料。
同时,对于保证钢水质量和铸坯质量,以及提高生产效率和产品质量都起到了重要的作用。
连铸浇钢工艺流程简图
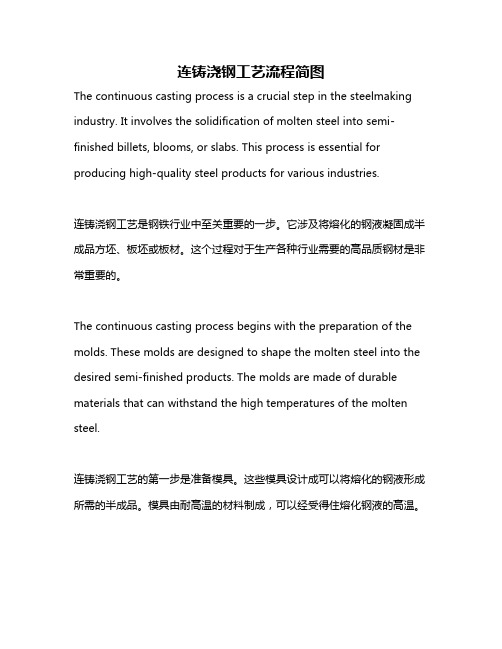
连铸浇钢工艺流程简图The continuous casting process is a crucial step in the steelmaking industry. It involves the solidification of molten steel into semi-finished billets, blooms, or slabs. This process is essential for producing high-quality steel products for various industries.连铸浇钢工艺是钢铁行业中至关重要的一步。
它涉及将熔化的钢液凝固成半成品方坯、板坯或板材。
这个过程对于生产各种行业需要的高品质钢材是非常重要的。
The continuous casting process begins with the preparation of the molds. These molds are designed to shape the molten steel into the desired semi-finished products. The molds are made of durable materials that can withstand the high temperatures of the molten steel.连铸浇钢工艺的第一步是准备模具。
这些模具设计成可以将熔化的钢液形成所需的半成品。
模具由耐高温的材料制成,可以经受得住熔化钢液的高温。
Once the molds are ready, the molten steel is poured into the molds through a tundish, a container that regulates the flow of molten steel. As the molten steel enters the molds, it begins to solidify and take the shape of the molds. This is a critical stage of the process, as it determines the quality and shape of the final steel products.一旦模具准备好,熔化的钢液通过浇注槽注入到模具中,浇注槽是一种调节熔化钢液流动的容器。
连续铸钢工艺教程
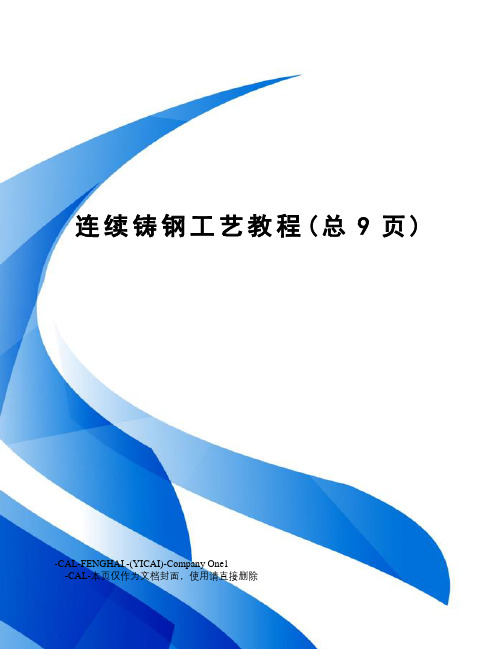
连续铸钢工艺教程(总9页) -CAL-FENGHAI.-(YICAI)-Company One1-CAL-本页仅作为文档封面,使用请直接删除连续铸钢工艺教程1.连铸工艺1.1连铸工艺介绍连铸全称连续铸钢,与模铸不同,它不是将高温钢水浇铸到一个个的钢锭模内,而是将高温钢水浇注到一个或几个用强制水冷、带有“活底”(叫引锭头)的铜模内(叫结晶器),钢水很快与“活底”凝结在一起,待钢水凝固成一定厚度的坯壳后,就从铜模的下端拉出“活底”,这样已凝固成一定厚度的铸坯就会连续不断地从水冷结晶器内被拉出来,,在二次冷却区继续喷水冷却,带有液芯的铸坯一边走一边凝固,直到完全凝固,待铸坯完全凝固后,用氧气切割或剪切机把铸坯切成一定尺寸的钢坯。
连铸是连接炼钢和轧钢的中间环节,是炼钢生产的重要组成部分,连铸生产的正常与否,不但会影响到炼钢生产任务的完成,还会影响到轧材的质量和成材率。
一台连铸机主要由大包回转台、中间包、中间包车、结晶器、结晶器振动装置、二次冷却装置、拉坯矫直装置、切割装置和出坯辊道等部分组成。
在连铸生产时通常用天车将钢包吊至大包回转台,然后大包转台将钢包旋至浇注位,经大包底部水口把钢水注入到中间包内,打开中间包塞棒后,钢水流入到下口用引锭杆堵塞并能上下振动的结晶器中,钢水沿结晶器周边冷凝成坯壳,当结晶器下端出口处坯壳有一定厚度时,带有液芯并和引锭杆连在一起的铸坯在拉矫装置的作用下,离开结晶器,沿着二冷段的支撑结构下移,与此同时铸坯被二次冷却装置进一步冷却并继续凝固,当引锭装置进入拉矫机后脱去引锭装置,铸坯在全部凝固或带有液芯的状态下被矫直,随后在水平位置被切割成定尺长度,经出坯辊道运送到规定地点,上述整个过程在实际生产中是连续进行的。
1.3连铸的主要设备1.3.1钢包回转台钢包回转台设置在电炉、精炼同一跨,它的本体是一个具有两个钢包支撑架的转臂,绕回转台中心回转,钢包回转台工作时,出钢跨一侧的天车将盛满钢水的钢包吊放到支撑架上,然后回转台旋转180o,将钢包转到连铸跨中间包上方的浇注位进行浇注,浇注完毕,再把空包转出的同时,又把另一个盛满钢水的钢包旋转到浇注位置,这样就可以快速更换钢包,实现多炉连浇。
- 1、下载文档前请自行甄别文档内容的完整性,平台不提供额外的编辑、内容补充、找答案等附加服务。
- 2、"仅部分预览"的文档,不可在线预览部分如存在完整性等问题,可反馈申请退款(可完整预览的文档不适用该条件!)。
- 3、如文档侵犯您的权益,请联系客服反馈,我们会尽快为您处理(人工客服工作时间:9:00-18:30)。
钢的连续浇铸
连续铸钢是用连铸机浇铸、冷却、切割而直接得到铸坯的工艺,它是连接炼钢和热轧的环节。
主要设备由钢包、中间包、结晶器、结晶振动装置、二次冷却和铸坯导向装置、拉坯矫直装置、切割、出坯装置等组成的。
1 、浇铸过程:将盛钢水的钢包吊到连铸机上部,钢水通过钢包底部的水口流到中间包,钢水进入结晶器内,钢水从四周逐步冷却凝固,温度下降,当钢水开始进入结晶器时,在结晶器下段用引锭杆塞住,当出结晶器时,有二次冷却装置靠许多喷头喷出雾壮水进行冷却。
在用夹紧辊拉出,完全凝固后,切割成板坯,送热轧厂。
设备:A 、钢包。
是用于盛放钢水并进行精炼的容器。
B 、中间包。
位于钢包与结晶器之间,起到稳流、减压、储钢、分流等作用。
它的容量为钢包的20 一40%。
C 、结晶器是连铸的“心脏”,钢水在结晶器内冷却初步凝固成一定厚度的铸坯外形,并被连续从结晶器下口拉出,进入二冷区。
D ,二次冷却。
铸坯出结晶器到完全凝固的过程称二次冷却,通过喷水或喷雾气冷却。
E ,拉坯矫直装置。
对板坯矫直。
F ,切割。
把板坯切割成规定的尺寸。
2 、薄板坯连铸连轧技术
薄板坯连铸连轧是20 世界80 年代末开发成功的技术,特点是:A ,板坯厚度小。
厚度在20 一80mm ,冷却快。
B ,拉速快,一般在sm / min 。
C ,流程短。
传统的厚板坯一般是热送或冷却后送热轧板坯库,编组后进加热炉加热后再轧制,由于炼钢和热轧是二个独立的部门,生产不连续。
而薄板坯连铸连轧,是将连铸机与连轧机连成一条线,钢水由薄板坯连铸机生产一定规格的板坯,随即进入在线的加热炉进行少量的加热,即可进入连轧机轧制。
这样缩短了生产周期、减少设备投资。
但比表面积大,散热快,•缺陷的产生几率高。
主要工艺有:德国西马克(SMS )的CSP (漏斗形结晶器)技术,德国德马克(MOH )的ISp (平板直弧形结晶器)技术。
我国从西马克引进了CSp 生产线,分别在珠江钢厂、邯郸钢厂、包钢、唐钢、本钢的企业。