磨削知识复习过程
第12章 磨削
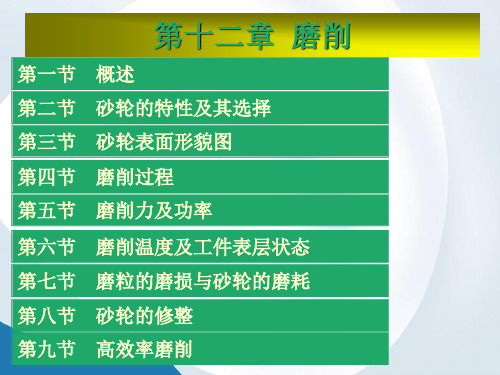
Fn / Ft
1.6~1.9
1.9~2.6
2.7~3.2
Fa / Ft
0.1~0.2 表中Fa为轴向切削分力
说明
材料硬度高时,比值大些
进给速度vf
图12-26 成形磨削时的磨削力与磨削用量的关系 成形磨削时的磨削力Fn、Ft与磨削用量ap、vf的关系
ap增加时,Fn及Ft均增加;
vf增加时,Fn及Ft均有所减小
砂轮的标记:
•P 400×40×127 WA 60
磨料 粒度
• 平行砂轮 外径×厚度×孔径 •L 5 • 硬度 组织号 (m/s)
结合剂
V 35 最高工作线速度
第三节 砂轮表面形貌图
砂轮表面形貌图
有效磨粒切削刃 无效磨粒切削刃
有效磨粒切削刃 只为静态切削刃总 数的5%~12%;
一个磨粒可能有 几个有效切削刃与 工件接触,有60% 的有效切削刃分布 在不同磨粒上面。
第二节 砂轮的特性及其选择
砂轮:由磨料加结合剂用烧结的方法而制 成的多孔物体。
1.磨料:起切削作用, 2.结合剂:把磨料结合起来,使之具有一定 的形状、硬度和强度。
3.气孔:结合剂没有填满磨料之间的全部空
间,因而有气孔存在。
砂轮的特征:
直接担负切削工作。
1. 磨 料
有刚玉系,碳化硅系,碳化硼系,金刚石系,立方氮化硼等 棕刚玉:加工硬度较低的塑性材料,如中、低碳钢和低合 金钢等; 白刚玉:加工硬度较高的塑性材料,如高碳钢、高速钢和 淬硬钢等; 黑碳化硅:加工硬度较低的脆性材料,如铸铁、铸铜等; 绿碳化硅:加工高硬度的脆性材料,如硬质合金、宝石、 陶瓷和玻璃等。
结论
三、 砂轮上的磨削力
可以把磨削力分解为 径向力Fr和切向力Ft
第一章 磨削加工的基本知识

第一章磨削加工的基本知识培训学习目标1.磨削用量包括那几个基本参数?如何计算砂轮圆周速度、工件圆周速度?2.试述切削液的作用、种类及特点。
3.砂轮由哪三要素构成?4.如何选择砂轮硬度?5.如何选择砂轮粒度?6.引起砂轮不平衡的原因是什么?试述平衡砂轮的目的和方法。
一、磨床的基本知识1.磨床工作在制造业中的地位磨削是一种比较精密的金属加工方法,经过磨削的零件有很高的精度和很小的表面粗糙度值。
目前用高精度外圆磨床磨削的外圆表面,其圆度公差可达到0.001mm左右,相当于一个人头发丝粗细的1/70或更小;其表面粗糙度值达到Ra0.025um,表面光滑似镜。
在现代制造业中,磨削技术占有重要的地位。
一个国家的磨削水平,在一定程度上反映了该国的机械制造工艺水平。
随着机械产品质量的不断提高,磨削工艺也不断发展和完善。
2. 普通磨床简介以常用的万能外圆磨床为例,磨床主要由床身、工作台、头架、尾座、砂轮架和内圆磨具等部件组成。
见图1。
磨床还包括液压系统。
(1)床身:磨床的支承。
(2)头架:安装与夹持工件,带动工件旋转,可在水平面内逆时针转90°;(3)内圆磨具:支承磨内孔的砂轮主轴。
(4)砂轮架:支承并传动砂轮主轴旋转,可在水平面±30°范围内转动;(5)尾坐:与头架一起支承工件;(6)滑鞍与横进给机构:通过进给机构带动滑鞍上的砂轮架实现横向进给;(7)横向进给手轮(8)工作台:a.上工作台:上面装有头架与尾坐;b.下工作台:上工作台可绕下工作台在水平面转±10°角度。
3.磨床的型号磨床的种类很多,按GB/T15375-1994磨床的类、组、系划分表,将我国的磨床品种分为三个分类。
一般磨床为第一类,用字母M表示,读作“磨”。
超精加工机床、抛光机床、砂带抛光机为第二类,用2M表示。
轴承套圈、滚球、叶片磨床为第三类,用3M表示。
齿轮磨床和螺纹磨床分别用Y和S表示,读作“牙”和“丝”。
磨工中级工培训第四课
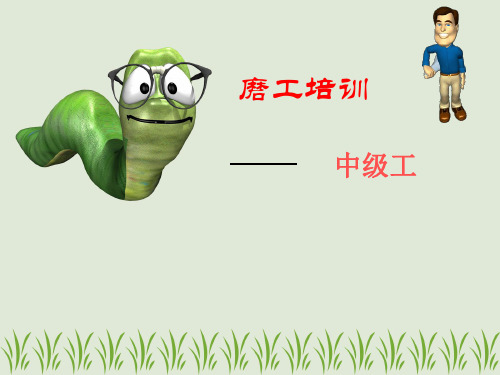
2.用精密角铁装夹
• 特点:精密角铁具有两个互相垂直的工作平面,它的垂 直度为0.005毫米,可达到较高的加工精度. • 适用:适合装夹大小重量都比角铁小的导磁或非磁性垂 直面工件.
为了不影响磨削表面的平面度, 倾斜角度α一般应小于30’。且 此种方法只适用于粗磨。精磨 平面时,磨头主轴必须严格垂 直于工作台,以保证加工精度。
二、电磁吸盘的使用
(1)使用中,当切断电磁吸盘的电源后,工件和电 磁吸盘上仍会保留一部分磁性,即剩磁,因此,工件 不易取下。这时只要将开关转到退磁位置,多次反复 改变线圈中的电流方向,把剩磁去掉,工件就容易取 下。 (2)对于底面积较大的工件,光滑表面间黏附力较 大,,再加上剩磁存在,更不容易取下工件。这时可 根据工件的形状,先用木棒、铜棒或扳手(扳手钳与 工件表面间应垫好铜皮),将工件扳松后再取下。防 止将工件从台面上硬拉下来而拉毛工件表面和吸盘台 面。
五、平面磨床结构
六、平面磨削砂轮的选择
七、平面精度的检验
平面度
透光法、着色法、千分表 千分尺、百分表或千分表 角尺、圆柱角尺、百分表、角铁 角度尺 游标卡尺、千分尺等
平 面 精 度 的 检 验
平行度 垂直度 角度 尺寸精度
八、平面磨削工艺分析
• • • • • • • 1、根据图纸要求选择合适的加工方法 2、确定工件的定位装夹与定位基准 3、选择合适砂轮 4、清擦工作台,修整工件毛边 5、根据工件形状、选择适当的夹具 6、根据工件的精度要求分粗磨和精磨 7、加工工件到图纸要求尺寸及精度
第6章磨削加工

金刚石砂轮
6.2 磨 削 原 理
6.2.1 磨料的形状特征
形状很不规则,但大多呈菱形八面体。顶锥角在80°~ 145°范围内, 但大多数顶锥角为 90°~ 120°。
6.2.2 磨屑形成过程
第6章磨削加工
磨削过程——磨具上的无数个磨粒的微切削刃对工件 表面的微切削过程。
图 6-2 磨粒的切削过程
①当砂轮硬度较高,修整较细,磨削载荷较轻时,易出现钝化型。这时,加工 表而质量虽较好,但金属切除率显著下降。
②当砂轮硬度较低,修整较粗,磨削载荷较重时,易出现脱落型。这时,砂轮 廓形失真,严重影响磨削表面质量及加工精度。
表 6-3 常用结合剂的性能及适用范围
第6章磨削加工
6.1.4 硬度 磨粒在外力作用下从其表面脱落的难易程度。 磨粒容易脱落,砂轮硬度软,反之则硬。 表 6-4 砂轮的硬度等级名称及代号
第6章磨削加工
砂轮硬度的选用原则: ①工件材料越硬,应选用越软的砂轮。 ②磨削面积较大时,磨粒易磨损,应选较软的砂轮。 ③半精磨与粗磨相比,需用较软的砂轮。 ④精磨和成形磨削时,需用较硬的砂轮。
且,径向力Fx最大, 是Fy的2-4倍
图 6-3 磨削力
第6章磨削加工
径向分力 F x 与
砂轮轴、工件的变 形及振动有关,影 响加工精度、质量
6.2.4 磨削温度基本概念 磨削时,切除单位体积切削层所削耗的功率为车、铣等
的10~20倍,且大部分转变为热能,使磨削区形成高温。
⑴磨粒磨削点温度 指磨粒切削刃与切屑点的温度,是磨削中温度 最高的部位,达1000~1400 ℃,它影响加工质量,砂轮磨损。
第 6 章 磨削加工
第6章磨削加工
磨削:用磨具(砂轮、砂带、油石等)对表面加工的方法。 适用难切削的高硬度材料的半、精加工。
磨削过程及磨削原理
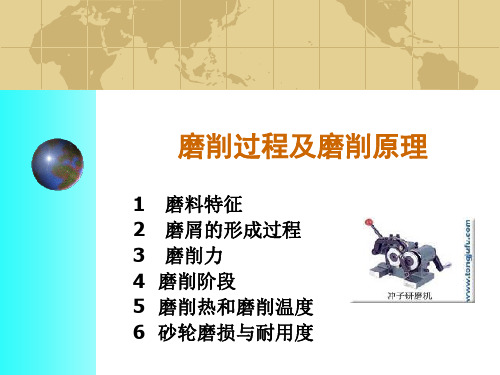
六、砂轮的磨损与耐用度
形态:磨耗磨损(A)、磨粒破碎(B-B) 和脱落磨损(C-C)。 砂轮耐用度:砂轮钝化、变形后加工 质量和效率降低。~用砂轮在两次修 整之间的实际磨削时间度时,工件将发 生颤振,表面粗糙度突然增大,或出 现表面烧伤现象。
由图可知,缩 短初磨阶段和稳定 阶段可提高生产效 率,而保持适当清 磨进给次数和清磨 时间可提高表面质 量。
五 磨削热和磨削温度
1. 磨削温度的基本概念 2. 影响磨削温度的主要因素
砂轮速度V: V ↑→θ↑ 工件速度Vw : Vw ↑→θ↓ 径向进给量fr: fr↑→θ↑ 工件材料: 导热性↓→θ↑ 砂轮硬度与粒度:硬度↓→θ↓ 磨粒大小↑→θ↓
二 磨屑的形成过程
滑擦阶段:磨粒切削厚度非常小,在 工件表面上滑擦而过,工件仅产生弹 性变形。
刻划阶段:工件材料开始产生塑性变 形,磨粒切入金属表面,磨粒的前方 及两侧出现表面隆起现象,在工件表 面刻划成沟纹。磨粒与工件间挤压摩 擦加剧,磨削热显著增加。
切削阶段:随着切削厚度的增加,在 达到临界值时,被磨粒推挤的金属明 显的滑移而形成切屑。
磨削过程及磨削原理
1 磨料特征 2 磨屑的形成过程 3 磨削力 4 磨削阶段 5 磨削热和磨削温度 6 砂轮磨损与耐用度
一 磨料特征
很不规则,大多数呈菱形八面体; 顶尖角大多数为90度~120度,以很大的负前角进行切 削; 磨粒切削刃几乎都存在切削刃钝圆半径; 在砂轮表面分布不均匀,高低也不同。
磨粒常见形状
三 磨削力
➢磨削力的的来源:工件材料产生变形时的抗力和 磨粒与工件间的摩擦力。
➢磨削力的特征: (1) 单位磨削力很大 (2) 径向分力很大---径向力虽不做工,但会使
工件产生水平方向的弯曲,直接影响加工精度。
机械制造业磨削基本知识.

等级
超软
软
中软
中
中硬
硬
超硬
代号
D
E
F
G
H
J
K
L
M
N
P
Q
R
S
T
Y
选择
磨淬硬钢选用L~N,磨淬火合金钢选用H~K,高表面质量磨削时选用K~L,刃磨硬质合金刀具选用H~J
表5-1 砂轮特性及用途选择4—硬度
5.1.5 砂轮的组织
砂轮结构的紧密或疏松程度
用颗粒、结合剂和气孔三者体积的比例关系来表示
5.1.2 粒度
表示磨料颗粒的大小
1.一般磨粒
粒度号---磨粒刚好可通过的筛网每英寸长度上(25.4mm)上的孔眼数。单位称为“目”。 粒度号越大,磨粒的实际尺寸越小
类别
粒度号
适 用 范 围
磨粒
8# 10# 12# 14# 16# 20# 22# 24# 30# 36# 40# 46# 54# 60# 70# 80# 90# 100# 120# 150# 180# 220# 240#
双斜边砂轮
OSX
磨齿轮及螺纹
双面凹砂轮
PSA
磨外圆,刃磨刀具,无心磨
切断砂轮 (薄片砂轮)
PB
切断及切槽
筒形砂轮
N
端磨平面
杯形砂轮
B
磨平面、内圆,刃磨刀具
碗形砂轮
BW
刃磨刀具,磨导轨
碟形砂轮
D
磨齿轮,刃磨铣刀、拉刀、铰刀
表5-2 常用砂轮的形状、代号及用途举例
有效磨粒切削刃
无效磨粒切削刃
有效磨粒切削刃只为静态切削刃总数的5%~12%; 一个磨粒可能有几个有效切削刃与工件接触,有60%的有效切削刃分布在不同磨粒上面。
机械制造基础--磨削

• 二、粒度 • 磨料的粒度表示磨料颗粒的尺寸大小。 • 颗粒上最大尺寸大于40微米的磨料,用机械筛
分法来决定粒度号,其粒度号数值就是该种颗 粒能通过的筛子每英寸长度上的孔数。因此粒 度号数越大,颗粒尺寸越细 • 颗粒尺寸小于40微米的磨料用显微镜分析法来 测量,其粒度号数即该颗粒最大尺寸的微米数
• 三、结合剂 • 砂轮的结合剂将磨粒粘合起来,使砂轮
具有一定的强度、气孔、硬度和抗腐蚀、 抗潮湿的性能。国产砂轮常用的结合剂 有四种; • 1.陶瓷结合剂(代号A):是由黏土、长 石、滑石、硼玻璃、硅石等陶瓷材料配 制而成。烧结温度为1240°-1280°
• 陶瓷结合剂的特点是粘结强度高,刚性
• 砂轮硬度的选用原则: • 1.工件材料愈硬,应选用愈软的砂轮。这
是因为硬材料易使磨粒磨损,需用较软 的砂轮以使磨钝的磨粒及时脱落。同时 软砂轮空隙较大,容屑性能较好。但是 磨削有色金属(铝、黄铜、青铜等)、 橡胶、树脂等软材料,却也要用较软的 砂轮。这是因为这些材料易使砂轮糊塞; 选用软些的砂轮可使糊塞处较易脱落, 较易露出锋锐新鲜的磨粒来。
一个临届值,即奥氏体化温度时,工件 表面就可能发生烧伤现象,即工件表层 产生氧化膜的回火颜色 工件表面烧伤的表征是: 磨削力增加; 砂轮磨损率增加; 加工表面质量变差。 此时砂轮已到达了必须重新修整的时候。
• • • • •
• 为了减少烧伤现象的发生,可采取减少 • • • •
热量的产生和加速热量的传出的措施: 减小磨削深度; 选用较软的砂轮; 采用大气孔砂轮或表面开槽的砂轮; 把冷却液渗透进磨削区等等。
第十二章 磨削
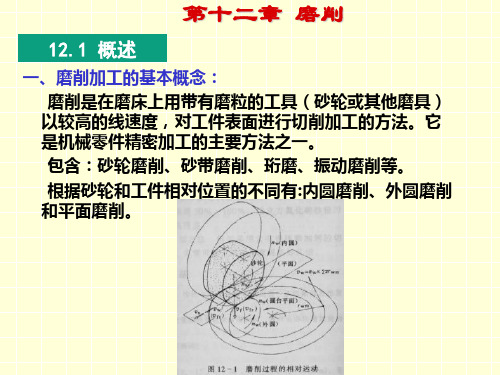
12.3 砂轮表面形貌图
有效磨粒切削刃,无效磨粒切削刃。 测量砂轮表面形貌目前主要用接触法: 1、静态法 2、动态法 3、工件复印法
12.4 磨削过程
一、磨削运动 磨削时,一般有四个运动。 1、主运动 砂轮的旋转运动,主运动的速度 就是砂轮外圆的线速度。 vs=πdsns/1000 2、径向进给运动:砂轮切入工件的运动,其 大小用径向进给量fr表示。又称磨削深度。
• • • •
天然金刚石 人造金刚石 CBN 普通磨料
二、粒度
粒度:磨粒颗粒的尺寸大小。
粗磨粒粒度(颗粒最大尺寸大于40μm ):用机械筛分法,
每平方英寸筛网上孔的数量,如60#,80#。粒度号数越大,
颗粒尺寸越细。
微粉磨粒粒度(颗粒尺寸小于40μm ):用显微镜分析法, 粒度号数即该颗粒最大尺寸的μm数。如W5,W3,W0.5
• 普通磨料固结磨具的标志按国标GB2484-84规定,其书写 顺序为:磨具形状、尺寸、磨料、粒度、组织、结合剂、 最高工作线速度。
国标GB2484-84
国际标准ISO
• 超硬磨料磨具的标志书写顺序为:形状、尺寸、 磨料、粒度、结合剂和浓度等。平行砂轮标志 示例如下:
超硬磨料磨具的结构
• 超硬磨料砂轮一般由磨料层、过渡层和基体组成。
四、磨削循环 一、磨削力的特征 磨削力的来源:一是各个磨粒的切削刃挤压切入工件后,工 件材料发生弹性、塑性变形时所产生的阻力;二是磨粒和结 合剂与工件表面之间的摩擦力。 以外圆纵磨为例,磨削力分解为切向力、法向力和轴向力。
由于磨粒上的切削刃为负前角,所以法向分力Fn远大于 切向分力Ft。轴向分力Fa最小。
以磨粒率表示的磨具组织及其应用范围
组织号 磨粒率 (%) 0 62 1 60 2 58 3 56 4 54 5 52 6 50 7 48 8 46
磨削工培训讲学
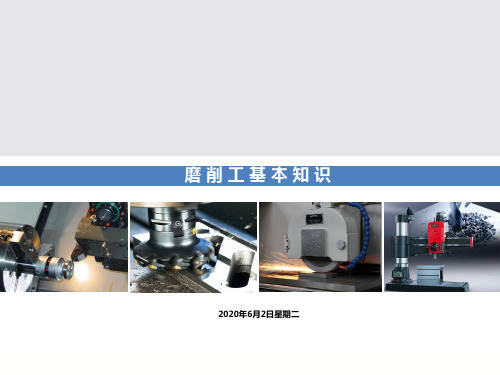
6—立柱;7—撞块;8—工作台;9—砂轮垂直进给手轮;10—床身
二、常用磨床介绍
3、普通内圆磨床 如图3所示为普通内圆磨床,它可以加工零件上的通孔、不通孔、阶台和 端面等。
图3 M2110型内圆磨床 1— 床身;2—工作台;3—头架;4—砂轮架;5—滑板座
砂轮是一种特殊的切削刀具。磨削是通过分布在砂轮表面的磨粒进行切 削的,每颗磨粒相当于一把车刀,整个砂轮即相当于刀齿极多的铣刀。在砂 轮高速旋转时,凸出的具有尖棱的磨粒从工件表面上切下细微的切屑,不太 凸出或磨钝了的磨粒只能在工件表面上划出小的沟纹,比较凹下的磨粒则和 工件表面产生滑动摩擦,后两种磨粒在磨削时产生微尘。因此,磨削除和一 般刀具的切削过程有共同之处(切削作用)外,还具有刻划和修光作用。
一、磨削加工工艺简介
磨削加工的主要特点如下: (1) 磨削加工的精度较高。由于加工余量小,磨削时磨粒细微并有修光
作用,磨削后工件的精度可达IT7~IT6级,表面粗糙度Ra为1.6~0.2μm;如 采用高精度磨削,则精度可达IT5级以上,表面粗糙度Ra为0.1~0.012μm。
(2)磨削可以加工一般刀具难以加工甚至无法加工的硬质材料。如淬硬 钢、硬质合金和陶瓷等。
还可以使用机床附设的内圆磨头来磨削内圆柱面、内圆锥面等。
图1 万能外圆磨床 1-床身;2-头架;3-工作台;4-内圆磨具;5-砂轮架;6-尾座;7-控制箱
二、常用磨床介绍
2、平面磨床 如图6-2所示是M7120型平面磨床,砂轮主轴的轴线与工作台面平行,工
件安装在矩形电磁吸盘上,并随工作台作纵向往复运动,其运动速度即为工件 的直线进给速度,砂轮除高速旋转外,还能作瞬间的横向进给运动。
磨削培训第一章2

• Rt、Rw—分别为砂轮和工件的半径 • m—单位面积上的磨粒数 • e—未变形切屑的宽度与平均厚度的比值
30
■磨削表面质量
磨削表面粗糙度公式的讨论:
Rmax 2 Rw Rt Vw 2Vc m e 2 Rw Rt
3 2 1 3
m ,Rmax Vc 或Vw ,使Vw/Vc的比值减小, Rmax Rt , Rmax ;同理, Rw , Rmax 砂轮宽度B大时,e值 ,可减小Rmax 磨粒切削刃高度的等高性越好、磨粒越细, Rmax 径向进给量越小, Rmax 磨削振动越小, Rmax
加速磨削热传出: 除了适当提高工件速度和轴向进给量外, 选择合适的磨削用量和适当的光磨时间
主要是采用有效的冷却方法:采用喷雾 冷却、高压冷却和内冷却
●磨削表面质量形成要素:磨削力、磨削热和被磨工 件
33
§8 砂轮的磨损与修整
砂轮的磨损(工作面 尺寸变化)
磨耗磨损(摩擦所致)
破碎磨损(磨粒/结合剂破碎)
§2
砂轮的特性和选择
主要起切削作用 主要起容屑和冷却作用
■砂轮的构成:砂轮是由磨料加结合剂烧制而成 的。
主要起粘接作用
常用的磨削工具:
1
■砂轮特性
砂轮特性五要素:磨料、粒度、结合剂、硬度、 组织及尺寸形状
(1)磨料:其选择主要取决于工件材料的硬度 应具备的条件:硬度高、红硬性好;有一定的强度和韧
磨削加工工件表面层 的温度分布,是指沿 工件表面层深度方向 温度的变化,它与加 工表面变质层的生成 机理、磨削裂纹和工 件的使用性能有关。
砂轮磨削区温度和磨粒磨削 点温度图
28
■磨削热与磨削温度
砂轮的特性与选择和磨削的基础知识
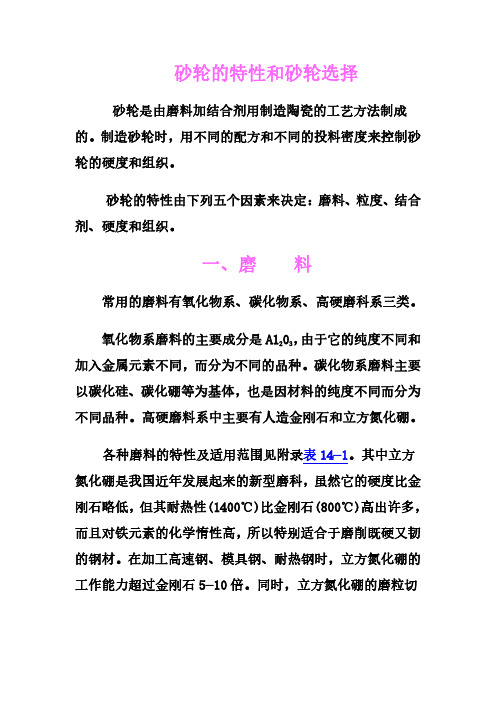
砂轮的特性和砂轮选择砂轮是由磨料加结合剂用制造陶瓷的工艺方法制成的。
制造砂轮时,用不同的配方和不同的投料密度来控制砂轮的硬度和组织。
砂轮的特性由下列五个因素来决定:磨料、粒度、结合剂、硬度和组织。
一、磨料常用的磨料有氧化物系、碳化物系、高硬磨科系三类。
氧化物系磨料的主要成分是A1203,由于它的纯度不同和加入金属元素不同,而分为不同的品种。
碳化物系磨料主要以碳化硅、碳化硼等为基体,也是因材料的纯度不同而分为不同品种。
高硬磨料系中主要有人造金刚石和立方氮化硼。
各种磨料的特性及适用范围见附录表14—1。
其中立方氮化硼是我国近年发展起来的新型磨科,虽然它的硬度比金刚石略低,但其耐热性(1400℃)比金刚石(800℃)高出许多,而且对铁元素的化学惰性高,所以特别适合于磨削既硬又韧的钢材。
在加工高速钢、模具钢、耐热钢时,立方氮化硼的工作能力超过金刚石5—10倍。
同时,立方氮化硼的磨粒切削刃锋利,在磨削时可减小加工表面材料的塑性变形,因此,磨出的表面粗糙度比用一般砂轮小。
在相同切削条件下,立方氮化硼砂轮加工所得的表面层为残余压应力,而氧化铝砂轮加工的表面层为残余张应力(参看图14—1)。
所以用立方氮化硼砂轮所加工出的零件,其使用寿命要高些。
由此可见,立方氮化硼是一种很有前途的磨料。
二、粒度粒度表示磨粒的大小程度。
以磨粒刚能通过的一号筛网的网号来表示磨粒的粒度。
例如60粒度是指磨粒刚可通过每英寸长度上有60个孔眼的筛网。
当磨粒的直径小于40μm时,这些磨粒称为微粉。
它的粒度以微粉的尺寸大小来表示。
如尺寸为28μm的微粉,其粒度号标为W28。
磨粒粒度及其尺寸范围见表14—2。
磨粒粒度对磨削生产率和加工表面粗糙度有很大的影响。
一般来说,粗磨用颗粒较粗的磨粒,精磨用颗粒较细的磨粒。
当工件材料软、塑性大和磨削面积大时,为避免堵塞砂轮,也可采用较粗的磨粒。
常用的砂轮粒度及其应用范围见表14—3。
三、结合剂结合剂的作用是将磨粒粘合在一起,使砂轮具有必要的形状和强度。
磨削方法与步骤

磨削方法与步骤
一、操作步骤
1、合上电源,启动油泵,打开气阀,机床设置在调整状态。
2、用合格试件调整偏心及支承夹角(偏心往右上偏10丝左右,
夹角在90-105度)。
3、调整修整位置,使用手轮把砂轮横移至合金笔位置,慢速手摇
进给,使砂轮刚好接触合金笔,确定砂轮修整位置,并把数据输入参数内。
4、复位,机床在原位状态下,砂轮开,进入长修状态,进行修整。
5、砂轮关,设置调整状态,将砂轮移入工件,慢速手摇进给,使
砂轮接触工件,确定快趋位,并在参数栏内设置快趋量进给量及进给速度(在将砂轮移入的过程中,工件须激磁转动)。
6、机床在全自动状态下进行加工。
二、加工余量参考
粗磨余量130丝左右,一次半精磨余量80丝,二次半精磨余量40丝,精磨加工至尺寸。
三、粗磨分段
假设粗磨余量130丝,并分13段进行磨削,则每段为10丝磨削余量,进行设置,每进给1丝,砂轮来回磨削一次。
砂轮共来回磨削10次,进行一次砂轮修整,如此循环,直至粗磨完成。
四、精磨分段
方法同上。
说明:
工艺卡上的为原来的工艺,除二平面外,内外径均需在新设备3MK2010上加工。
磨削加工工艺过程及主要工序

磨削加工工艺过程及主要工序
磨削加工是通过摩擦和剪切作用在工件表面上去除一定厚度的材料,以逐步达到工件
表面的精度、光洁度。
在工业生产中,磨削加工广泛应用于机械制造、航空航天、军工制
造等领域,是制造精密零部件不可少的一个步骤。
1. 磨削前准备工作:包括检查磨料和磨具等加工工具的状况,将不良的磨料和磨具
清除,并确认加工工件和加工参数等。
2. 粗磨工序:将工件表面的大颗粒物和粗糙度去除,提高表面平整度和加工性能。
粗磨主要使用粒度较粗的磨料和磨具,磨削过程中会产生较多的热量和磨屑,需要采取冷
却液进行冷却。
3. 半精磨工序:对工件进行中等精度的修整和平滑,精度一般可以达到0.01mm左右。
半精磨使用粒度较细的磨料和磨具进行加工,在与工件接触的磨具上涂覆润滑油,减少磨
料与磨具之间的摩擦和磨损。
5. 抛光工序:对工件表面进行细微处理,有效提高表面亮度和平滑度。
抛光工序使
用细粒度的抛光料和抛光棉进行加工,加工速度较慢但效果很好,加工表面不会有明显的
划痕或损伤。
6. 清洗和除油:不同的磨削工艺需要使用不同的清洗和除油方法,常用的方法有机洗、水洗和气动喷洗等。
清洗时要注意不能让残留的磨料和油污对工件表面造成二次污
染。
磨削加工的基础知识
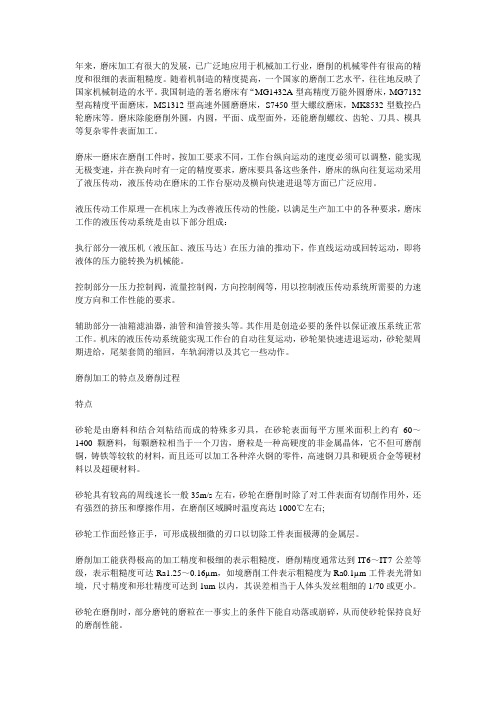
年来,磨床加工有很大的发展,已广泛地应用于机械加工行业,磨削的机械零件有很高的精度和很细的表面粗糙度。
随着机制造的精度提高,一个国家的磨削工艺水平,往往地反映了国家机械制造的水平。
我国制造的著名磨床有“MG1432A型高精度万能外圆磨床,MG7132型高精度平面磨床,MS1312型高速外圆磨磨床,S7450型大螺纹磨床,MK8532型数控凸轮磨床等。
磨床除能磨削外圆,内圆,平面、成型面外,还能磨削螺纹、齿轮、刀具、模具等复杂零件表面加工。
磨床—磨床在磨削工件时,按加工要求不同,工作台纵向运动的速度必须可以调整,能实现无极变速,并在换向时有一定的精度要求,磨床要具备这些条件,磨床的纵向往复运动采用了液压传动,液压传动在磨床的工作台驱动及横向快速进退等方面已广泛应用。
液压传动工作原理—在机床上为改善液压传动的性能,以满足生产加工中的各种要求,磨床工作的液压传动系统是由以下部分组成:执行部分—液压机(液压缸、液压马达)在压力油的推动下,作直线运动或回转运动,即将液体的压力能转换为机械能。
控制部分—压力控制阀,流量控制阀,方向控制阀等,用以控制液压传动系统所需要的力速度方向和工作性能的要求。
辅助部分—油箱滤油器,油管和油管接头等。
其作用是创造必要的条件以保证液压系统正常工作。
机床的液压传动系统能实现工作台的自动往复运动,砂轮架快速进退运动,砂轮架周期进给,尾架套筒的缩回,车轨润滑以及其它一些动作。
磨削加工的特点及磨削过程特点砂轮是由磨料和结合刘粘结而成的特殊多刃具,在砂轮表面每平方厘米面积上约有60~1400颗磨料,每颗磨粒相当于一个刀齿,磨粒是一种高硬度的非金属晶体,它不但可磨削铜,铸铁等较软的材料,而且还可以加工各种淬火钢的零件,高速钢刀具和硬质合金等硬材料以及超硬材料。
砂轮具有较高的周线速长一般35m/s左右,砂轮在磨削时除了对工件表面有切削作用外,还有强烈的挤压和摩擦作用,在磨削区域瞬时温度高达1000℃左右;砂轮工作面经修正手,可形成极细微的刃口以切除工件表面极薄的金属层。
第四章:磨削

第4章磨削磨削是以砂轮或其它磨具对工件进行精加工和超精加工的切削加工方法。
在磨床上采用各种类型的磨具为工具,可以完成内外圆柱面、平面、螺旋面、花键、齿轮、导轨和成形面等各种表面的精加工。
它除能磨削普通材料外,尤其适用于一般刀具难以切削的高硬度材料的加工,如淬硬钢、硬质合金和各种宝石等。
磨削加工精度可达IT6~IT4,表面粗糙度Ra 可达1.25—0.01μm,甚至可达0.008μm。
磨削主要用于零件的精加工,目前也可以用于零件的粗加工甚至毛坯的去皮加工,可获得很高生产率。
除了用各种类型的砂轮进行磨削加工外,还可采用做成条状、块状(刚性的)、带状(柔性的)磨具或用松散的磨料进行磨削。
加工方法主要有珩磨、砂带磨、研磨和抛光等。
砂轮的磨削过程实际上是磨粒对工件表面的切削、刻划和滑擦三种作用的综合效应。
磨削中,磨粒本身也由尖锐逐渐磨钝,使切削作用变差,切削力变大。
当切削力超过粘合剂强度时,圆钝的磨粒脱落,露出一层新的磨粒,形成砂轮的“自锐性”。
但切屑和碎磨粒仍会将砂轮阻塞。
因而,磨削一定时间后,需对砂轮进行修整。
4.1 砂轮4.1.1 砂轮的特性与选择砂轮是用各种类型的结合剂把磨料粘合起来,经压坯、干燥、焙烧及修整而成的,具有很多气孔,用磨粒进行切削的磨削工具。
决定砂轮特性的五个要素分别是:磨料、粒度、结合剂、硬度和组织。
1.磨料普通砂轮所用的磨料主要有刚玉、碳化硅和超硬磨料三类,按照其纯度和添加的元素不同,每一类又可分为不同的品种。
表4-1列出了常用磨料的名称、代号、主要性能和用途。
表4-1 常用的磨料的性能及适用范围2.粒度粒度是指砂轮中磨粒尺寸的大小。
粒度有两种表示方法:(1)用筛选法区分的较大磨粒,主要用来制造砂轮,粒度号以筛网上每英寸长度的筛孔数来表示。
例如,60号粒度表示磨粒能通过每英寸(25.4mm)长度上有60个孔眼的筛网。
粒度号为4~240,粒度号越大,颗粒尺寸越小。
(2)用显微镜测量尺寸区分的磨粒称微粉,主要用于研磨,以其最大尺寸前加W表示。
磨削1
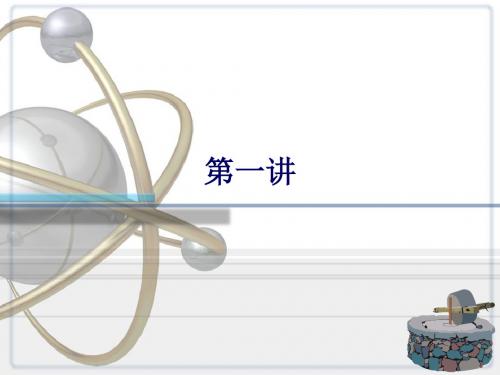
w w 4
平面磨削时:
2Lnt vw 1000
式中,nw为工件转速r/min;nt为工作台往复运动频率s-1; L为工作台行程mm。
2、砂轮的组成及特性
砂轮磨削 固结 磨具
磨 料 加 工
固结 磨料 加工
油石研磨 精密珩磨
涂覆 磨具
研磨 抛光
砂带磨削 砂带研抛
游离磨料 加工
2、砂轮的组成及特性
2.8 结合剂种类
(2)树脂结合剂(代号B)通常为酚醛树脂或环氧树脂。 特点:强度高、弹性好;耐热性和耐腐蚀性差、磨损快气孔 率小易堵塞等;该结合剂制成的砂轮,用作切断和切槽, 对热敏工件作精加工等 (3) 橡胶结合剂(代号R)主要是人造橡胶。 特点:比树脂结合剂更具强度和弹性,允许切削速度 65m/s, 比树脂结合剂 45m/s 更高;耐热性更差,气孔更少;通常 用作无心磨导轮、切断切槽砂轮以及抛光用砂轮。 (4) 金属结合剂(代号 M) 常用青铜作结合剂,主要用于 金刚石砂轮。 特点:这种结合剂制成的砂轮型面保持性好、强度高、有一 定韧性,但自砺性差;主要用作粗、精磨硬质合金,磨削 与切断光学玻璃、宝石、陶瓷与半导体材料等。
有色金属及塑 料、橡胶等非 金属以及热敏 合金
2.7 砂轮形状
•
•
•
根据机床结构与磨削加工的需要,砂轮制成各种形状 与尺寸。下表是常用的几种砂轮形状、尺寸、代号及 用途。 砂轮的外径应尽可能选得大些,以提高砂轮的圆周速 度,这样对提高磨削加工生产率与表面粗糙度有利。 此外,在机床刚度及功率许可的条件下,如选用宽度 较大的砂轮,同样能收到提高生产率和降低粗糙度的 效果,但是在磨削热敏性高的材料时,为避免工件表 面的烧伤和产生裂纹,砂轮宽度应适当减小。
- 1、下载文档前请自行甄别文档内容的完整性,平台不提供额外的编辑、内容补充、找答案等附加服务。
- 2、"仅部分预览"的文档,不可在线预览部分如存在完整性等问题,可反馈申请退款(可完整预览的文档不适用该条件!)。
- 3、如文档侵犯您的权益,请联系客服反馈,我们会尽快为您处理(人工客服工作时间:9:00-18:30)。
磨削知识磨削加工和砂轮1.磨削加工1-1 磨削加工的位置磨削加工是机械作业的一个领域,在磨削加工方面是使用砂轮对车刀、刀具等磨削工具进行加工的方法。
表1 机械作业法的分类1-2 磨削加工的概念1-2-1 磨削加工的定义磨削加工一般使用高速旋转的砂轮,利用构成这个砂轮的极硬的微细磨料来切削加工物的加工方法。
1-2-2 磨削加工的特点以及缺点磨削加工与切削加工相比,具有以下特点。
(1)能够很容易的切削使用切削工具所不能切削的硬质或脆性材料。
砂轮的切刃是非常硬的矿物质的粒子,能够很容易的加工超硬合金和陶瓷器具。
(2)能够很容易的得到要求的加工面粗糙度以及精度。
构成砂轮的一个一个切刃很小,并在高速旋转下使用,切屑极小。
即,比使用切削工具得到的加工面的粗糙度好,尺寸精度也好。
(3)加工率极好砂轮的周速度为10 – 80m/s,比切削工具的速度高数倍到数十倍。
因此,一个一个的切屑很细微,而且加工率极好。
(4)切刃的自锐作用在使用中,砂轮由于切刃的磨损,而导致切削阻力增大,磨料裂开或脱落,产生新的切刃和气孔。
因此,不象一般的切削工具那样需要重新研磨。
(5)因为磨削点的温度高,是导致烧裂的原因磨削作业中,磨削点的温度很容易超过1000℃,这是磨削加工的一个大缺点。
因此,为了不使产生烧裂现象,需要使用性能良好的磨削液进行充分的冷却。
(6)使用高速旋转的砂轮由于砂轮是高速旋转的,所以万一损坏的话,具有产生重大灾害的危险性。
因此,需要充分考虑包括工作人员以及工作环境在内的安全性。
1-2-3 磨削加工的分类在磨削加工的分类方面,存在各种各样的考虑方法,如果根据它的的作业方法分类,包括如下几种。
(1)圆筒磨削 ---------------------- 纵向进给磨削方式(Traverse Cut) (Cylindrical Grinding) 横向进给磨削方式--斜置横向进给磨削方式(Plunge Cut) (Angular Slide Plunge Cut)纵向进给磨削横向进给磨削斜置横向进给磨削(2)内面磨削(Internal Grrinding) 普通式(Plain type)行星式(Planetary type)无心式–集结式普通式行星式无心式 (砂轮轴公转形)集结式(3)无心磨削(Centerless Grinding) 纵向进给法 (Through Feed)横向进给法 (Infeed)切向送进法 (Tangential Feed)纵向进给法横向进给法切向进给法(4) 平面磨削(Surface Grinding)卧轴矩形工作台使用平行砂轮卧轴圆形工作台立轴矩形工作台使用杯形、环形、立轴圆形工作台扇形砂轮卧轴矩形工作台纵向进给贯穿磨法使用薄片砂轮(两头平面磨削) 运载式卧轴矩形工作台卧轴圆形工作台立轴矩形工作台卧轴矩形工作台立轴圆形工作台纵向进给贯穿磨法运载式(5)工具磨削(Tool Grinding) 车刀、钻头、铣刀、滚刀、推刀、插齿刀、立铣刀车刀磨削钻头磨削铣刀磨削滚刀磨削推刀磨削插齿刀磨削立铣刀磨削2.砂轮2-1 砂轮的构成砂轮是由磨料、粘合剂、气孔3要素构成的。
根据场合,有时要添加填充剂、添加剂、以及特殊处理。
磨料…作为切刃切削加工物粘合剂…保持磨料的结合气孔…切屑的排泄道、冷却作用2-2 决定砂轮性质的5个主要因素砂轮的性质或性能主要由以下5个主要因素决定。
磨料的种类…磨料的品种(氧化铝质磨料、碳化硅质磨料)粒度…磨料的大小(粗号、中号、细号、粉末)结合度…磨料的保持力(极软、软、中、硬、极硬:粘合剂的量)组织…砂轮中的磨料的容积比例(密、中、粗 =多孔性砂轮)粘合剂的种类…保持磨料的材料的种类(陶瓷、热固树脂、橡胶、氧化镁)2-3 磨料的种类和特点作为砂轮切刃的磨料使用天然磨料和人造磨料。
现在全部使用人造磨料。
表2 人造磨料的种类(JIS)氧化铝质 Al2O3かっ色氧化铝质白色氧化铝质粉碎形氧化铝质淡红色氧化铝质氧化锆氧化铝质AWAHAPAZ碳化硅 SiC黑色碳化硅绿色碳化硅CGC 表3 クレノートン的使用磨料クレノートン记号用途氧化铝质AL2O3 A、57A 一般钢铁自由磨削、生钢材精密磨削用SHA、68AZS、ZF、ZN自由磨削用STA、76A 不锈钢钢材自由磨削用WA、38A 一般淬火钢材精密磨削用RA、PW、85ADA、32A、80A合金钢、工具钢、淬火钢材等难磨削材的精密磨削用16A、19A、23A、35A特殊精密磨削用SG、SGF、TG 精密磨削用碳化硅SiC C、37C 非铁、非金属、铸铁磨削用 GC、39C 超硬合金磨削用表4 磨料的化学成分和物理性质碳化硅表5 磨料和其它材料的硬度比较2-4 粒度(Grain Size)粒度表示的是磨料的大小,用25.4mm(1英寸)四方的旧目数表示。
因此,数字越大磨料的大小越细碎。
表6显示的是磨料的标称粒度和它的的平均直径。
表6 磨料的标称粒度和平均直径2-5 结合度(Grade)结合度显示的是保持磨料的粘合剂的保持力。
在磨削作业中左右磨料切刃的自锐作用。
一般用字母表示。
接近A的软,接近Z的硬。
表7 结合度标称和记号标称极软软中硬极硬记号 A B C D E FG H I J K L M NOP Q R S T U V W X Y Z正常磨削和异常的状态2-6 组织(Struoture)组织显示的是砂轮的固定容积中所占磨料的比例。
表8 组织号码和磨料率(JIS)组织0 1 2 3 4 5 6 7 8 9 10 11 12 13 14 磨料率%62 60 58 56 54 52 50 48 46 44 42 40 38 36 34(允许差:±1.5%)2-7 粘合剂(Bond)表9显示的是粘合剂的种类和用途。
表9 粘合剂的种类和用途(1)表9 粘合剂的种类和用途(2)表10 利用磨削盘等构造规格(第14条)的周速度区别尺寸限制表(单位:mm)备注:1.在这个表里,Df表示的是凸缘的直径,R表示的是凹处的圆内半径。
2.在这个表里没有规定的尺寸可以任意使用。
2-9 最高使用周速度表11表示的周速度称为「普通周速度」。
另外,超过表11 的周速度称为「高速度」。
表11 砂轮的普通使用周速度的限度(单位:m/s)砂轮的种类粘合剂为无机质粘合剂为有机质平行砂轮没有加固一般用33 50超重磨削用-63螺纹磨削用以及沟槽磨削用63 63曲柄轴以及凸轮轴磨削用45 50 有加固直径在100mm以下,厚度在25mm以下-80直径在100mm以上205mm以下,厚度在13mm以下-72 其它尺寸-50单锥形、双锥形、单凹形、双凹形、安全形、碟形、以及磨具用碟形33 50楔形一般用33 50 螺纹磨削用以及沟槽磨削用63 63带槽形一般用33 50 曲柄轴以及凸轮轴磨削用45 50环形以及环形的扇形30 35 杯形以及碗形30 40 圆盘形以及圆盘形的扇形33 45偏置形(直径在230mm以下,厚度在10mm以下)没有加固-57 有加固-72切断没有加固-63 有加固-802-10 形状、缘形(Type and Face)2-11 高速砂轮的特别表示表12 色调最高使用轴速度区别色调JIS R 6241以上,45m/s以下兰色系统45m/s以上,60m/s以下黄色系统60m/s以上红色系统(1)(2)备注: 1.色带的宽度设定为20mm。
2.(2)的场合的色带的外径要比凸缘径大。
2-12 尺寸允许差表13 允许差(单位:mm)外径厚度凹径缘厚(D)尺寸允许差(T)尺寸允许差(P)持续允许差(W)尺寸允许差未满50 ±0.5未满25 ±0.5 未满25+0.5未满50 +1.5-0.550以上未满255 ±1.025以上未满125+1.00 25以上未满50±1.0255以上未满510 ±2.0125以上未满225+2.050以上+2.0-0.5 50以上±2.0510以上±3.0225以上+3.0(单位:mm)孔径尺寸允许差(H)一般磨削机械磨削没有轴衬带轴衬普通速度高速度未满50.80 +0.40+0.10+0.30+0.30H1250.80以上未满76.20 +0.60+0.10 76.20以上+0.40H12 H112-13 平衡度(平衡)砂轮的平衡度2-14 劳动安全卫生规则(砂轮的罩子)第117条旋转中的砂轮存在给工作人员带来危险的隐患时,事业者必须设置罩子。
但是,直径不满50毫米的砂轮,不在此范围内。
(砂轮试运转)第118条事业者在当天开始工作前,必须进行1分钟以上的试运转,更换砂轮时必须进行3分钟以上的试运转。
(超过砂轮的最高轴速度时,禁止使用)第119条事业者不可以使用超过其最高使用周速度的砂轮。
(禁止使用砂轮的侧面)第120条事业者不可以使用以使用侧面为目的的砂轮以外的砂轮侧面。
(抛光轮的罩子)第121条事业者必须要给抛光盘(使用布抛光、软木等的抛光盘除外)的抛光研磨需要部分以外的部分设置罩子。
2-15 标准表示法下面表示的是砂轮的尺寸规格。
3.正确砂轮的选择方法为了取得良好的磨削结果,选择适当的砂轮是很重要的。
但是,要满足所要求的加工精度,达到效率好、砂轮磨损少的需要非常困难。
因此,在砂轮选择时,明确着眼点,是基本的姿态。
相对于每个作业,砂轮的选择请考虑的砂轮选择表。
砂轮选择的必要条件选择正确砂轮的基本思考方法按照表14。
另外,为了提高磨削效果,请务必活用下面的调查表。
表14。