钢铁高炉转炉产能计算
3能耗指标体系的分类计算

能耗指标体系的分类钢铁企业能耗指标主要有吨钢综合能耗、吨钢可比能耗、主要产品的工序能耗、主要产品的实物单耗(如炼铁焦比、炼焦煤耗等)以及产值能耗、增加值能耗等等。
能源分析评价指标中,包括企业内部能源加工转换指标和企业损失指标。
按钢铁企业能耗经济技术指标体系可分为:(1)企业级能源技术经济指标:如吨钢综合能耗、万元产值能耗、吨钢耗新水、吨钢电耗、损失率等。
(2)工序级能源技术经济指标:如炼钢工序能耗、炼铁工序能耗等。
(3)耗能设备级能源技术经济指标:加热炉燃耗、高炉焦比、制氧机电耗等。
按钢铁企业能效对标指南中能耗指标体系可分为:(1)综合性指标:如企业级能源消耗总量、工序级能源消耗总量、各类能源介质消耗总量、企业能源亏损量等指标。
(2)单耗性指标:如吨钢综合能耗、企业吨钢可比能耗、工序单位产品能耗。
(3)经济性指标:万元产值能耗、万元增加值能耗等。
2.能耗指标的范围及计算钢铁制造流程是由多个不同的生产工序组成的,前一道工序的产品为下一道工序的原料,这是钢铁工业的特点,由于其复杂性,因此,统计范围和指标定义必须规范,以便于对标,找出节能潜力,提升企业效益。
(1)吨钢综合能耗范围及计算综合能耗是规定的耗能体系在一段时间内实际消耗的各种能源实物量按规定的计算方法和单位分别折算为标准煤后的总和。
吨钢综合能耗(comprehensive energy consumption ):吨钢综合能耗是企业生产每吨粗钢所综合消耗的各种能源自耗总量;也就是每生产一吨钢,企业消耗的净能源量。
其计算公式为:吨钢综合能耗=企业钢产量企业自耗能源量(吨标准煤/吨钢,千克标准煤/吨;tce/t ,kgce/t )式中,企业自耗能源量即报告期内企业自耗的全部能源量。
统计上报按企业全部耗能量。
企业自耗能源量= 企业购入能源量 ± 库存能源增减量 - 外销能源量= 企业各部位耗能量之和 + 企业能源亏损量作为行业对标,吨钢综合能耗的统计范围可按照企业生产流程的主体生产工序(包括原料储存、焦化、烧结、球团、炼铁、炼钢、连铸、轧钢、自备电厂、制氧等动力厂)、厂内运输、燃料加工及输送、企业亏损等消耗能源总量,不包括矿石的采、选工序,也不包含炭素、耐火材料、机修、石灰、精制及铁合金等非钢生产工序的能源消耗量。
炼钢部分各种计算公式汇总

炼钢部分各种计算公式汇总炼钢部分各种计算公式汇总1、转炉装入量装入量=钢坯(锭)单重×钢坯(锭)支数+浇注必要损失钢水收得率(%)-合金用量×合金收得率(%)2、氧气流量Q=V tQ-氧气流量(标态),m 3min 或 m3hV-1炉钢的氧气耗量(标态),m 3; t-1炉钢吹炼时间,min 或h 3、供氧强度 I=Q TI-供氧强度(标态),m3t ·min ;Q-氧气流量(标态),m3min;T-出钢量,t注:氧气理论计算值仅为总耗氧量的75%~85%。
氧枪音速计算α=(κgRT)1/2m/sα—当地条件下的音速,m/s ;κ—气体的热容比,对于空气和氧气,κ=1.4;g —重力加速度,9.81m/s 2;R —气体常数,26.49m/κ。
马赫数计算M=ν/αM —马赫数;ν—气体流速,m/s ;α—音速,m/s 。
冲击深度计算h 冲=K P 00.5·d 00.6ρ金0.4(1+H 枪/d c ·B)h 冲—冲击深度,m ;P 0—氧气的滞止压力(绝对),㎏/㎝2;d 0—喷管出口直径,m ;H 枪—枪位,m ;ρ金—金属的密度,㎏/m 3;d c —候口直径,m ;B —常数,对低粘度液体取作40;K —考虑到转炉实际吹炼特点的系数,等于40。
在淹没吹炼的情况下,H=0,冲击深度达到最大值,即 h max =P 00.5·d 00.6ρ金0.4有效冲击面积计算R=2.41×104(h νmax)2R —有效冲击半径,m ;νmax —液面氧射流中心流速,m/s ;νmax =ν出d 出H ·P 00.404ν出—氧射流在出口处的流速,m/s 。
金属-氧接触面积计算在淹没吹炼时,射流中的金属液滴重是氧气重量的3倍,吹入1m3氧气的液滴总表面积(金属-氧气的接触面积):S Σ=3G 金r 平均·ρ金G 金—1标米3氧气中的金属液滴重量=3×1.43㎏;r 平均—液滴的平均半径,m ;ρ金—金属液的密度,7×103㎏/m 3。
粗钢生产工序能耗计算

②高炉煤气的折标量:当月高气消耗量115.09万立方米×1.30038 (当月煤热值
÷7000)=149.67吨标煤
③焦炉煤气的折标量:当月焦气消耗量180.02 万立方米×6.20457(当月煤热值
÷7000)=1116.95吨标煤
技术要求(限额准入值) v 当电力折标准煤系数采用等价值0.404kgce/(kw·h)
时,新建或改扩建烧结机生产设备烧结工序单位产 品综合能耗限额准入值应不大于60kgce/t。 v 当电力折标准煤系数从等价值0.404kgce/(kw·h)改 为当量值0.1229 kgce/(kw·h) 时,新建或改扩建烧 结机生产设备烧结工序单位产品综合能耗限额准入 参考值应不大于51kgce/t。
v 本标准适用于钢铁企业进行烧结工序(不含球 团)、高炉工序、转炉工序和电炉工序单位产品 能耗的计算、考核,以及新建设备的能耗控制 。
粗钢生产工序能耗计算
二、标准规范性引用文件
v 下列文件中的条款通过本标准的引用而成为 本标准的条款。凡是注日期的引用文件,其 随后所有的修改单(不包括勘误的内容)或修订 版均不适用于本标准,然而,鼓励根据本标 准达成协议的各方研究是否可使用这些文件 的最新版本。凡是不注日期的引用文件,其 最新版本适用于本标准。
v 企业应定期对粗钢生产的几个主要工序能耗情况进行考核, 并把考核指标分解落实到各基层单位,建立用能责任制度。
v 企业应按要求建立健全能耗统计体系,建立能耗计算和考核 结果的文件档案,并对文件进行受控管理。
v 企业应根据GB 17167的要求配备能源计量器具,并建立能 源计量管理制度。
v 树立系统节能、管理节能的大局意识,从完善工艺操作流程 、提高系统的综合生产能力、产品合格率、设备作业率、利 用系数等方面开展综合节能工作;结合生产工艺改造、扩建 、新建,实现生产设备大型化,提高产能规模。
整合版 转炉炼钢 计算部分

精心整理转炉炼钢部分1.>已知转炉造渣碱度要求为3.0,铁水中含Si为1.2%,石灰有效CaO为70%,试计算吨钢石灰加入量是多少?解:石灰加入量=(2.14[%Si]/%CaO有效)×R×100=(2.14×1.2%/70)×3×1004.>已知在钢液中,元素百分含量(xi):碳0.11%,硅0.21%,锰0.42%,磷0.02%,硫0.03%,铜0.06%,其余成分不计。
各元素含1%对钢液凝固影响值(△ti)为:碳90,硅6.2,锰1.7,磷28,硫40,铜2.6;纯铁凝点为1539℃。
计算Q195的液相线温度(T液)。
解:T液=1539-∑(xi·△ti)=1539-0.11×90-0.21×6.2-0.42×1.7-0.02×28-0.03×40-0.06×2.6=1525℃答:Q195的液相线温度ΔT为1525℃5.>已知:铁水含硅0.80%,硅铁含硅74%,铁水装入量50t,要求配后铁水含硅1.2%,求硅铁配加量(kg)。
解:设:配加的硅铁为Xkg;由硅守恒得出下面方程式:50000×0.008+0.74X=(50000+X)×0.012得:X=274.73kg答:配加的硅铁两位274.73kg。
进入渣中的锰量=5.8-1.53=4.27kg渣量=4.27/3.92%=108.9kg渣量占钢水量的比例=108.9/900=12.1%答:产生的渣量为108.9kg,渣量占钢水量的比例为12.1%8.>根据锰平衡计算转炉渣量。
已知:(1)铁水36t,含锰0.20%;(2)废钢8t,含锰0.45%;(3)散状料带入锰忽略不计;(4)钢水量40t,残锰0.05%;(5)终点炉渣含锰2.20%。
解:(1)锰的带入=铁水带锰+废钢带锰=36×1000×0.20%+8×1000×0.45%=72+36=108kg(2)锰的产出=钢水带锰+炉渣锰=1538-0.45×90-0.27×6.2-0.65×1.7-0.018×28-0.02×40-0.05×2.6=1493℃答:45钢的液相线温度为1493℃。
高炉常用计算公式审批稿

高炉常用计算公式 YKK standardization office【 YKK5AB- YKK08- YKK2C- YKK18】炼铁用计算公式1、根据焦炭负荷求焦比焦比=1000/(负荷×综合品位)=矿批/(负荷×理论焦比)2有效容积利用系数=每昼夜生铁产量/高炉有有效容积3焦比=每昼夜消耗的湿焦量×(1-水分)/每昼夜的生铁产量4理论出铁量=(矿批×综合焦比)/=矿批×综合品位×不考虑进去渣中的铁量因为焦炭也带入部分铁5富氧率=-×富氧量/60×风量=×富氧量/风量6煤比=每昼夜消耗的煤量/每昼夜的生铁含量7 综合焦比=焦比+煤比×8 综合燃料比=焦比+煤比+小块焦比9 冶炼强度=每昼夜消耗的干焦量/高炉有效容积10 矿比=每昼夜加入的矿的总量/每昼夜的出铁量11 风速=风量(1-漏风率)/风口总面积漏风率20%12 冶炼周期=(V有 -V炉缸内风口以下的体积)/(V球+V烧+V矿)×88%=(V球+V烧+V矿)×88%13 综合品位=(m烧×烧结品位+m球×球品位+m矿×矿品位)/每昼夜加入的矿的总量14 安全容铁量=×ρ铁×1/4πd2hh取风口中心线到铁口中线间高度的一半15 圆台表面积=π/2(D+d)体积=π/12×h×(D2+d2+Dd)16 正方角锥台表面积S=a2 +b2 +4( a+b/2)hV=h/3(a2+b2+ab)=h/3(S1+S2+√S1S)17、圆锥侧面积M=πrl=πr√r2+h2体积V=1/3πr2h18、球S=4πr2=πd2V=4/3πr3=π/6d319、风口前燃烧1kg碳素所需风量(不富氧时)V风=24×1/+ f为鼓风湿度20、吨焦耗风量V风=(+)×1000×85%f为鼓风湿度 85%为焦炭含碳量21、鼓风动能(1)E=(764I2-3010I+3350)dE-鼓风动能 I-冶炼强度(2)E=1/2mv2=1/2×Q×r风/(60gn)v风实2Q-风量 r风-风的密度 g= n-风口数目22、石灰的有效容剂性CaO有效=CaO熔-SiO2×R23、洗炉墙时,渣中CaF2含量控制在2%-3%,洗炉缸时可掌控在5%左右,一般控制在%每批料萤石加入量X=P矿×TFe×Q×(CaF2)/([Fe]×N)P矿-矿批重 TFe-综合品位 [Fe]-生铁中含铁量Q-吨铁渣量 (CaF2)-渣中CaF2含量 N-萤石中CaF2含量24、风口前燃烧1kg碳素的炉缸煤气量V煤气=(+)/(+)××C风C风-风口前燃烧的碳素量,kg25、理论出渣量渣量批=QCaO批/CaO渣渣量批-每批炉料的理论渣量,tQCaO批-每批料带入的CaO量,tCaO渣-炉渣中CaO的含量,%25、喷吹煤粉热滞后时间t=V总/(V批×n)V总-H2参加反应区起点处平面(炉身温度1100℃~1200℃处)至风口平面间的容积,m3V批-每批料的体积,m3n-平均每小时的下料批数,批/h26、高炉某部位需要由冷却水带走的热量称为热负荷,单位表面积炉衬或炉壳的热负荷称为冷却强度Q=CM(t-t0)×103Q-热负荷 kJ/hM-冷却水消耗量,t/hC-水的比热容,kJ/(kg.℃)t-冷却水出水温度℃t0-冷水进水温度,℃。
(完整word版)高炉产能换算
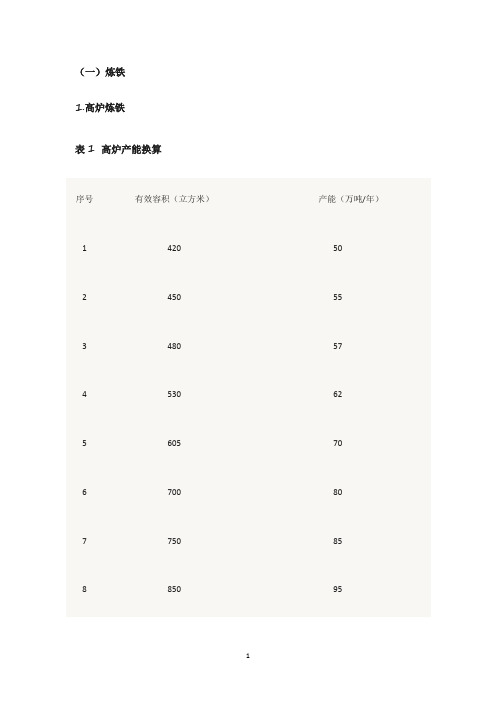
(一)炼铁1.高炉炼铁表1 高炉产能换算序号有效容积(立方米)产能(万吨/年)14205024505534805745306256057067008077508588509591080104 101200113 111250115 121280118 131350122 141500133 151580137 161780152 171860158 182000170 192200187202260193 212380203 222500213 232580215 242650221 252750229 262800234 272850238 283200267 293800304 304000320314350347 324747379 335500439 345800463备注:高炉有效容积在上表中两档之间的,按插值法计算其产能。
2.非高炉炼铁表2 非高炉炼铁设备产能换算序号工艺及型号产能(万吨/年)一熔融还原1COREX1000,C2000,C300030,80,1502FINEX示范厂,FINEX300060,1503Hismelt示范厂80二直接还原1竖炉产能根据设备具体型号换算2回转窑3转底炉(二)炼钢1.转炉表3 转炉产能换算序号公称容量(吨)普钢产能(万吨/年)特钢产能(万吨/年)13560422407048345805445085555559060 6609566 76510072 87010577 97511083 108012088 119012599 12100130100 131******** 14135150135 151********1615017015017180200162182********19210220189202502502252126028023422300300270备注:1、上表中普钢亦包括低合金钢和优钢。
2、上表中特钢主要是指合金钢,不锈钢属于特钢,但不锈钢产能需按其冶炼工艺综合计算。
高炉,转炉单位产品能耗先进值计算公式
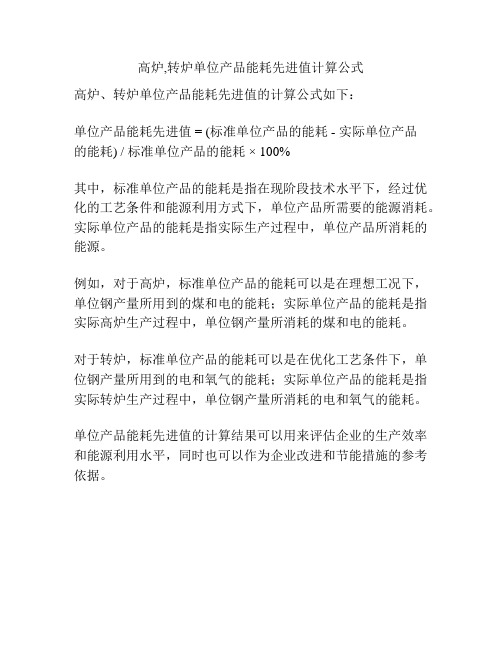
高炉,转炉单位产品能耗先进值计算公式
高炉、转炉单位产品能耗先进值的计算公式如下:
单位产品能耗先进值 = (标准单位产品的能耗 - 实际单位产品
的能耗) / 标准单位产品的能耗 × 100%
其中,标准单位产品的能耗是指在现阶段技术水平下,经过优化的工艺条件和能源利用方式下,单位产品所需要的能源消耗。
实际单位产品的能耗是指实际生产过程中,单位产品所消耗的能源。
例如,对于高炉,标准单位产品的能耗可以是在理想工况下,单位钢产量所用到的煤和电的能耗;实际单位产品的能耗是指实际高炉生产过程中,单位钢产量所消耗的煤和电的能耗。
对于转炉,标准单位产品的能耗可以是在优化工艺条件下,单位钢产量所用到的电和氧气的能耗;实际单位产品的能耗是指实际转炉生产过程中,单位钢产量所消耗的电和氧气的能耗。
单位产品能耗先进值的计算结果可以用来评估企业的生产效率和能源利用水平,同时也可以作为企业改进和节能措施的参考依据。
高炉炼铁技术关于计算内容大全

高炉炼铁技术关于计算内容大全
1.炉料配比计算:
高炉的炉料配比是指将各种原料按一定比例混合,形成炉料,以满足
高炉内冶炼的要求。
炉料配比计算需要考虑铁矿石的品位、配加量、还原
性能等因素。
根据不同的炉况和冶炼目标,可以通过计算确定最佳的炉料
配比。
2.铁矿石还原率计算:
铁矿石还原率是指在高炉内,铁矿石中铁的还原程度,一般用还原率
来表示。
铁矿石还原率的计算需要考虑还原剂的种类、配加量、还原反应
的温度、压力等因素。
可以通过测定高炉内不同位置的铁矿石成分和炉渣
成分,来计算铁矿石的还原率。
3.高炉燃烧计算:
高炉燃烧计算主要是针对炉顶燃烧系统进行的,包括风口、鼓风机、
燃料气等相关参数的计算。
通过计算一系列参数,可以确定合适的鼓风量、燃料气使用量,以实现高炉内燃烧过程的最佳效果。
4.炉渣成分计算:
高炉冶炼过程中,炉渣是一种重要的冶炼剂。
炉渣成分计算可以通过
测定高炉内炉渣中的各种成分来实现。
炉渣成分的计算需要考虑各种原料
的配加量、还原反应的程度等因素,以确保炉渣成分符合冶炼的要求。
5.高炉出铁量计算:
高炉出铁量是指高炉每天或每小时生产的铁水量。
高炉出铁量的计算需要考虑炉顶风量、炉渣成分、炉渣重量、料温等因素。
通过测定高炉出铁口的温度和流量,可以计算出高炉出铁量。
以上是高炉炼铁技术中一些常见的计算内容,这些计算内容是为了优化高炉冶炼过程,提高冶炼效率和质量,减少能耗和环境污染而进行的。
高炉炼铁技术的计算内容综合考虑了多个因素,通过科学的计算方法,可以更好地指导高炉运行和冶炼生产。
高炉产能换算
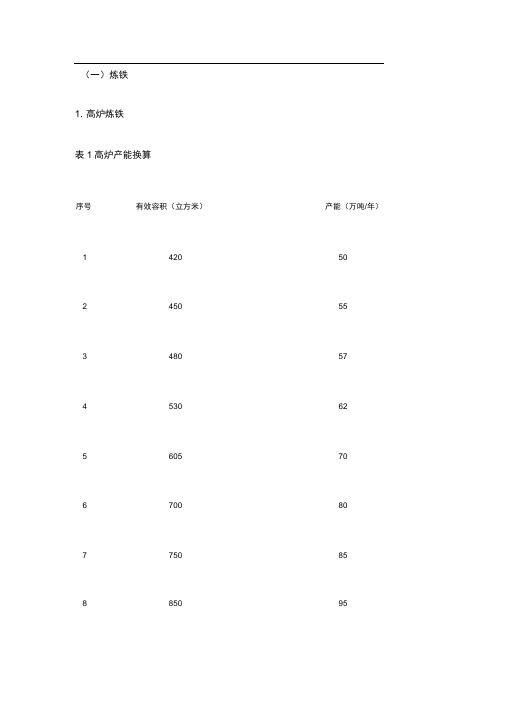
(一)炼铁1. 高炉炼铁表1高炉产能换算序号有效容积(立方米)产能(万吨/年)1 420 502 450 553 480 574 530 625 605 706 700 807 750 858 850 959 1080 10410 1200 11311 1250 11512 1280 11813 1350 12214 1500 13315 1580 13716 1780 15217 1860 15818 2000 17019 2200 18720 2260 19321 2380 20322 2500 21323 2580 21524 2650 22125 2750 22926 2800 23427 2850 23828 3200 26729 3800 30430 4000 32031 4350 34732 4747 37933 5500 43934 5800 463 备注:高炉有效容积在上表中两档之间的,按插值法计算其产能。
2. 非高炉炼铁表2非高炉炼铁设备产能换算序号工艺及型号产能(万吨/年)-一-熔融还原1 C0REX100Q C2000,C3000 30,80,1502 FINEX 示范厂,FINEX3000 60,150直接还原3 Hismelt示范厂801 竖炉2 回转窑3 转底炉(二)炼钢1. 转炉表3转炉产能换算1 35 60 422 40 70 483 45 80 544 5085 55产能根据设备具体型号换算序号 公称容量(吨) 普钢产能(万吨/年) 特钢产能(万吨/年)直接还原5 55 90 606 60 95 667 65 100 728 70 105 779 75 110 8310 80 120 8811 90 125 9912 100 130 10013 120 140 12014 135 150 13515 140 160 14016 150 170 15017 180 200 16218 200 210 18019 210 220 18920 250 250 22521 260 280 23422 300 300 270备注:1、上表中普钢亦包括低合金钢和优钢。
钢铁行业能源平衡计算介绍

钢铁企业能源综合平衡一、钢铁企业能源综合平衡概述(一)钢铁企业能源综合平衡的定义钢铁企业能源综合平衡是以钢铁企业为对象的能源平衡,包括各种能源收入与支出的平衡,消耗与有效利用及损失的能源数量平衡。
钢铁企业能源综合平衡所指的能量平衡范围,是指在生产活动中消耗的一次能源和二次能源所提供的能量,工质和物料所携带的能量,以及在企业内部进行能源转换和传输过程中损失能量的综合系统平衡。
在平衡计算中,都是将各种形式的能量按它们的等价热量值折合成热能这一主要利用形式,所以往往又将钢铁企业能源综合平衡称为钢铁企业热平衡。
钢铁企业能源综合平衡并不是只限于能源和能量的统计分析和数量平衡这一狭义的技术经济范围,而是通过这方面的工作,广义地对钢铁企业能源管理的组织体制,用能方针和政策,企业的耗能设备乃至生产工艺流程等进行分析,提出企业近期技术改进措施和远景规划。
钢铁能源综合平衡统计是综合平衡统计的重要组成部分,是一项综合性很强的系统工程。
从微观到宏观,从单项到综合,从局部到整体,从个别能源流转环节到全部能源系统流程,形成了一个完整的能源平衡体系。
(二)钢铁企业能源综合平衡的意义钢铁企业能源综合平衡遵循输入能量等于输出能量这一基本法则,就一定时期内企业能源的购入、加工转换、输送、分配、储备、使用等整个能源系统流程进行平衡分析,就能源系统内各运行环节的特征和相互之间的联系,以及能源经济运行中所形成的总量、效益之间的制约和平衡状况。
(三)能量平衡体系能量收、支的项目是随着所选体系不同而异的,所以在进行能量平衡时必须首先确定研究的体系,它可以是一个设备,也可以是一个工序,还可以是一个分厂,乃至整个企业。
在选好体系之后,用框图代表所选的体系,而将进入和排出体系的所有各项能量用箭头标在方框的四周,这就构成了我们所研究的能量平衡模型,绘制模型图的习惯方法一般是:1.由工质(工艺流体、物料或半成品)所带入能量Q带入画在方框的左侧。
2.由外界供给的能量Q供入画在方框的下方。
高炉、非高炉炼铁,转炉、电炉炼钢产能换算方法

高炉、非高炉炼铁,转炉、电炉炼钢产能换算方法(一)炼铁1.高炉炼铁表1 高炉产能换算序号有效容积(立方米)产能(万吨/年)1 420 502 450 553 480 574 530 625 605 706 700 807 750 858 850 959 1080 10410 1200 11311 1250 11512 1280 11813 1350 12214 1500 13315 1580 13716 1780 15217 1860 15818 2000 17019 2200 18720 2260 19321 2380 20322 2500 21323 2580 21524 2650 22125 2750 22926 2800 23427 2850 23828 3200 26729 3800 30430 4000 32031 4350 34732 4747 37933 5500 43934 5800 463备注:高炉有效容积在上表中两档之间的,按插值法计算其产能。
2.非高炉炼铁表2 非高炉炼铁设备产能换算序号工艺及型号产能(万吨/年)一熔融还原1 COREX1000,C2000,C3000 30,80,1502 FINEX示范厂,FINEX3000 60,1503 Hismelt示范厂80二直接还原1 竖炉产能根据设备具体型号换算2 回转窑3 转底炉(二)炼钢1.转炉表3 转炉产能换算序号公称容量(吨)普钢产能(万吨/年)特钢产能(万吨/年)1 35 60 422 40 70 483 45 80 544 50 85 555 55 90 606 60 95 667 65 100 728 70 105 779 75 110 8310 80 120 8811 90 125 9912 100 130 10013 120 140 12014 135 150 13515 140 160 14016 150 170 15017 180 200 16218 200 210 18019 210 220 18920 250 250 22521 260 280 23422 300 300 270备注:1、上表中普钢亦包括低合金钢和优钢。
高炉炼铁计算范文

高炉炼铁计算范文高炉炼铁是针对生铁矿石的还原和焦化过程,通过高温和化学反应将生铁矿石中的金属铁还原出来,从而得到享有广泛用途的铁。
炼铁过程中的一些重要参数和计算方法如下:1.原料配比(矿石与煤炭配比):高炉的原料主要包括生铁矿石和焦炭,它们的配比会影响到铁的产量和铁质的质量。
一般来说,煤炭与生铁矿石的质量比称为煤矿比(C/S)。
2.高炉配料量:高炉配料量是指在一定时间内进入高炉的原料总质量。
根据配料的不同,可以分为炉料重和矿料重。
炉料重是指每小时进入高炉的焦炭、燃料和矿石的总质量;矿料重是指每小时进入高炉的矿石的质量。
3.炉渣成分:炉渣是高炉炼铁过程中产生的副产物,它包含了一定的硅、铝、镁等氧化物。
炉渣中的成分直接影响到高炉的冶炼过程和炉渣的特性。
根据炉渣中SiO2、FeO、MgO和Al2O3的含量,可以计算出炉渣的碱度和熔融性指数。
4.高炉炼铁过程计算方法:高炉炼铁过程中的一些重要计算包括还原速度、冶炼强度、料线稠度、炉温、气体收入、铁液性能、产量和消耗等。
还原速度计算:高炉中还原过程通常可由还原比(C/O)来衡量,还原速度可用动力学公式刻画。
冶炼强度计算:冶炼强度=炉温×电解质浓度,是高炉冶炼的一个重要指标。
料线稠度计算:料线稠度=料层厚度/料层表面积,料线稠度的测量和调整对高炉冶炼具有重要意义。
炉温计算:炉温是指高炉内部的温度,它对高炉的冶炼过程和铁液的流动性有很大影响。
气体收入计算:高炉内的气体收入量直接影响到高炉的冶炼效果,常见的气体有高炉煤气、炉渣气、空气等。
铁液性能计算:铁液的物理性质,如粘度、密度、表面张力等,是高炉冶炼的重要指标。
产量和消耗计算:高炉的铁水产量和原料消耗是衡量高炉冶炼效果的重要指标。
高炉炼铁计算涉及的内容较多,以上只是其中一部分。
在实际操作中,操作人员需要根据高炉的运行状况和原料质量,结合配比、炉渣成分等参数进行综合考虑和计算。
这些计算结果可以为高炉运行提供重要的参考依据,进而调整和优化高炉的操作方式,以达到最佳的冶炼效果。
转炉炼钢工序能耗计算与分析
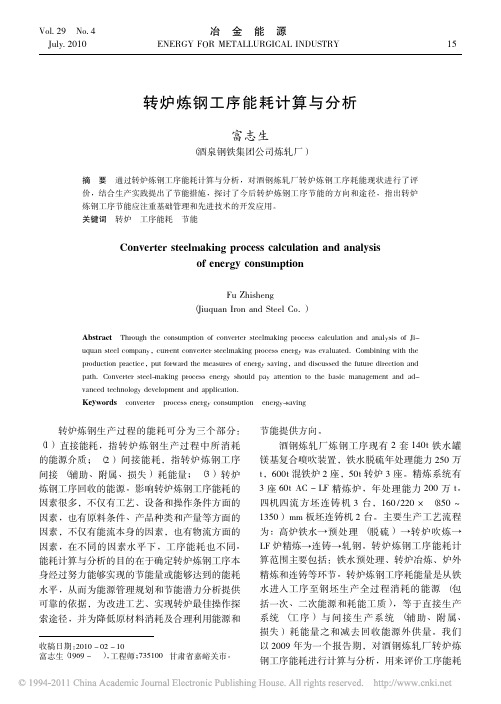
所占比例 18. 68% 7. 69% 20. 01% 0. 19% 0. 76% 5. 19% 27. 89% 16. 82% 2. 77% 100. 00% 59. 59% 40. 41% 100. 00%
氧气消耗与转炉吹炼过程有关,提高操作水平, 降低氧气消耗的潜力较大; ( 3) 电力和氮气消 耗尽管所占比例也不低,通过科学管理、生产工 艺优化与生产合理组织,也会有较大幅度下降; ( 4) 氩气的消耗在炼钢能源消耗中所占比例较 小,但随着高附加值、高难度产品比例的增加而 增加; ( 5) 转炉出口烟气总热量约 1112 × 108 kJ / t, 其中 81. 18% 为潜热,显热为 18. 12% ,属于二 次能源范围,折合 3818kgce / t。显然回收转炉煤 气、蒸汽等二次能源是实现负能炼钢的关键要 素,随意放散不仅白白浪费了大量能源,还会由 于 CO 有毒而造成公害[1]。
3 转炉炼钢工序能耗评价
3. 1 降低氧气消耗是转炉降低直接耗能的重要 措施
转炉炼钢工序的氧气消耗占能源消耗总量的 18. 68% 。降低氧气消耗应该在转炉操作工艺上 采取严格的控制措施: ( 1) 降低出钢温度,严 禁出高温钢; ( 2) 提高一次拉碳率,保证转炉 终点成分、温度的双命中; ( 3) 严禁用氧气吹 刷烟罩等。这些措施使转炉的氧气消耗由 2003 年 57m3 / t 降低到 2009 年 49. 48m3 / t,降低转炉 炼钢工序能耗约 1kgce / t。 3. 2 吨钢煤气回收量的多少对转炉工序能耗高
高炉总年产量的计算

1 高炉总年产量的计算据铸造生铁与炼钢生铁的换算系数1:1.15,得: 本高炉全年的生铁任务P=500×85%+500×15%×1.15 =425+86.25=511.25(万 t /a ) 2 高炉有效容积的确定高炉有效容积可按下述步骤确定:(1)确定高炉全年的生铁任务。
已知本设计P=511.25(万 t /a ) (2)计算高炉日产量这p P=-η)(1/365M P式中 M -高炉座数,座,本设计为2; η-高炉休风率,%,本设计取2%。
则:高炉的日产量P=-η)(1/365M P=98%2×36525.511⨯=0.715(万t) =71500(t)(3)计算高炉有效容积V uV u =IKp p ⨯=n 式中 K -每吨生铁的焦比,t/t ,本设计取0.52;I -冶炼强度,t/(m 3×d),本设计取1.3。
则高炉的有效容积 V u =I K p p ⨯=n = 5.27150=2860(m 3) 3 高炉内型尺寸确定高炉内型各部位的尺寸确定如下: (1) 炉缸1) 炉缸直径(d/m )。
d=0.32×V u 0.45=0.32×28600.45=0.32×35.92=11.49(m) 取d=11.5(m)。
2)炉缸高度。
①渣口高度(h z /m ):h z =1.27 2C N pb ×d T⨯⨯⨯⨯γ 式中 b -生铁产量波动系数,本设计取1.25;p -生铁日产量,t;N -昼夜出铁次数,取12;C -渣口下部炉缸容积利用系数,为0.55~0.6,炉容大、渣量大时选取较低值, 本设计取为0.58;T γ-铁水密度,一般取7.2~7.4,本设计取为7.3; d -炉缸直径。
则: h z =1.27 2C N pb ×d T⨯⨯⨯⨯γ =1.27 211.5×7.3×0.58×127150×1.2×=1.69(m ) 取h z=1.7(m )。
高炉炼铁工序能耗计算方法

1);高炉炼铁工序能耗计算方法日前,中国钢铁企业网特邀专家顾问王维兴就高炉炼铁工序能耗计算方法作了以下解 析:1. 高炉炼铁工序能耗计算统计范围 原燃料供给:矿槽卸料、称量料斗和计量、料车或皮带上料、仪表显示和控制、照明等 用电;空调用电、冬季取暖用蒸汽等能源用量。
高炉本体:焦炭(包括小块焦) 、煤粉、电力、蒸汽、压缩空气、氧气、氮气、水(新 水、软水等)等。
渣铁处理:炉渣处理用电和水,冲渣水余热要进行回收利用。
鼓风:分电力鼓风或气动鼓风。
鼓风能耗一般占炼铁总能耗的10% 1m?风需要用能耗0.030kgce/ m?.正常冶炼条件下,高炉消耗 1吨燃料,需要2400m?的风量。
热风炉:要求漏风率 <2%漏风损失应<5%总体热效率为0%风温大于1200 C ,寿命 大于 25年。
烧炉用高炉煤气折标煤系数 0.1143kgce/m 3; 转炉煤气折标煤系数 0.2286kgce/m 3;焦炉煤气折标煤系数 0.6kgce/m 3。
热风炉用电力和其它能源工质:蒸汽、压缩空气、水等。
煤粉喷吹:煤粉制备干燥介质,宜优先采用热风炉废气; 用电力、氮气、蒸汽、压缩空气、空调和采暖用能等。
设计喷煤能力要大于 180kg/t.碾泥:用电力和其它能源工质。
除尘和环保:主要是电力(大企业环境保护用电力占炼铁用电的30%左右)、水等。
,铸铁机:电力、水等。
扣除项目:回收利用的高炉煤气,热值按实际回收量计算; TRT 余压发电量(电力0.1229kgce/kwh ) 2. 炼铁工序能耗计算方法炼铁工序能耗=(C+l+E-R )日式中:T-合格生铁产量,铸造铁产量要用折算系数进行计算(见表表】合格甥折合翔主衙拟C-焦炭(干全焦,包括小块焦)用量。
折热量,28435kJ。
标煤量0.9714kgce/t焦炭.I-喷吹煤折热量,20908kJ ;折标煤量0.7143kgce/t原煤。
E-加工能耗(煤气、电、耗能工质等)折标煤量:煤气折标煤系数见热风炉栏目。
产能换算表.doc

附1产能换算表1一、钢铁(一)炼铁1.高炉炼铁表1 高炉产能换算序号有效容积(立方米)产能(万吨/年)1 420 502 450 553 480 574 530 625 605 706 700 807 750 858 850 959 1080 10410 1200 11311 1250 11512 1280 11813 1350 12214 1500 13315 1580 13716 1780 15217 1860 15818 2000 17019 2200 18720 2260 19321 2380 20322 2500 2131该表主要用于产能置换。
23 2580 21524 2650 22125 2750 22926 2800 23427 2850 23828 3200 26729 3800 30430 4000 32031 4350 34732 4747 37933 5500 43934 5800 463备注:高炉有效容积在上表中两档之间的,按插值法计算其产能。
2.非高炉炼铁表2 非高炉炼铁设备产能换算序号工艺及型号产能(万吨/年)一熔融还原1 COREX1000,C2000,C3000 30,80,1502 FINEX示范厂,FINEX3000 60,1503 Hismelt示范厂80二直接还原1 竖炉产能根据设备具体型号换算2 回转窑3 转底炉(二)炼钢1.转炉表3 转炉产能换算序号公称容量(吨)普钢产能(万吨/年)特钢产能(万吨/年)1 35 60 422 40 70 483 45 80 544 50 85 555 55 90 606 60 95 667 65 100 728 70 105 779 75 110 8310 80 120 8811 90 125 9912 100 130 10013 120 140 12014 135 150 13515 140 160 14016 150 170 15017 180 200 16218 200 210 18019 210 220 18920 250 250 22521 260 280 23422 300 300 270备注:1、上表中普钢亦包括低合金钢和优钢。
- 1、下载文档前请自行甄别文档内容的完整性,平台不提供额外的编辑、内容补充、找答案等附加服务。
- 2、"仅部分预览"的文档,不可在线预览部分如存在完整性等问题,可反馈申请退款(可完整预览的文档不适用该条件!)。
- 3、如文档侵犯您的权益,请联系客服反馈,我们会尽快为您处理(人工客服工作时间:9:00-18:30)。
钢铁高炉转炉产能计算
钢铁产业是国民经济的重要支柱之一,而钢铁高炉和转炉是钢铁制造的两种主要生产工艺。
在计算钢铁高炉和转炉的产能时,需要考虑多个因素。
本文将围绕“钢铁高炉转炉产能计算”进行阐述。
一、高炉产能计算
高炉是将熔铁矿石还原成铁的设备,它的产能计算是衡量钢铁企业生产能力的主要指标之一。
高炉产能计算采用的是理论炼铁量(理论渣量)和实际产量相比较的方法。
理论炼铁量是指高炉在确定的条件下炼铁的能力,它与高炉的炉容、炉渣成分、理论风量、燃料比等因素有关。
计算公式如下:理论炼铁量(t)= 炉容(m³)× 密度(t/m³)× 处理铁矿石含铁量(%)÷ 炼铁系数
在计算理论炼铁量时,需要考虑到高炉的实际运转情况,根据高炉的调定情况确定一个合理的炼铁系数,其数值通常在0.22-0.28之间。
实际产量是指高炉在生产过程中实际获得的铁量。
实际产量与高炉的运行维护、设备状况、人员素质等因素有关。
实际产量的计算公式如下:
实际产量(t)= 铁水重量(t)÷ 矿渣重量(t)× 块矿含铁量(%)
二、转炉产能计算
转炉是将铁水中的碳与氧反应,从而去除碳和其他杂质,得到纯净钢的设备。
转炉产能的计算依据是炉容、炉口冷却水质量、炉料特性、氧气喷吹速度等因素。
转炉的产能计算有两种方法:一种是利用进出站统计数据进行计算,另一种是直接读取转炉系统的控制参数进行计算。
利用进出站统计数据进行计算,需要记录进站净矿、废钢的重量和成分、钢水得铁量、焦炭、喷吹氧气的用量和成分等信息,根据这
些信息进行计算即可。
直接读取转炉系统的控制参数,需要将转炉的各项实时控制参数,如氧气流量、煤气流量、水流量、料量、温度、压力等参数实时读取,然后在计算机上进行数据处理,得到产量等相关指标。
三、综合考虑
在实际生产中,钢铁企业还需要综合考虑高炉和转炉的产能,制
定生产计划。
生产计划需要根据市场需求、原料储备、设备状况等多
种因素制定,并在生产过程中进行动态调整。
企业还需要为今后的生
产进行规划,确保生产线的合理布局和产能的合理配置。
以上是钢铁高炉转炉产能计算的介绍。
生产计划是钢铁生产过程
中的关键环节,合理的产能计算和生产计划,对于钢铁企业的持续稳
定发展具有十分重要的意义。