提高钻孔位置精度的几项措施
提高钻孔精度的方法
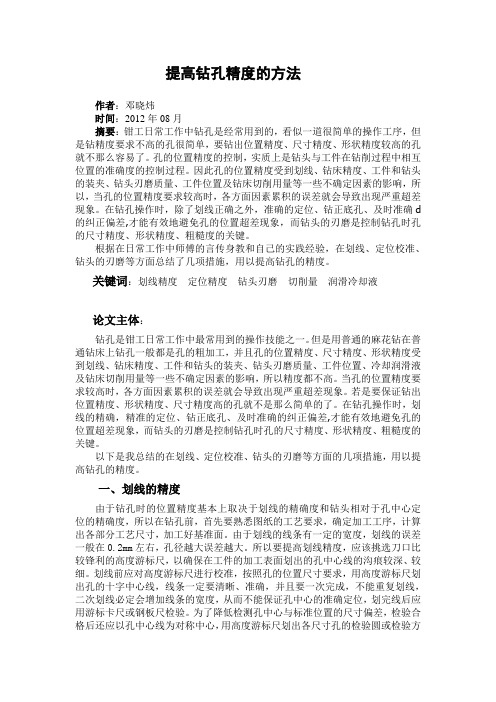
提高钻孔精度的方法作者:邓晓炜时间:2012年08月摘要:钳工日常工作中钻孔是经常用到的,看似一道很简单的操作工序,但是钻精度要求不高的孔很简单,要钻出位置精度、尺寸精度、形状精度较高的孔就不那么容易了。
孔的位置精度的控制,实质上是钻头与工件在钻削过程中相互位置的准确度的控制过程。
因此孔的位置精度受到划线、钻床精度、工件和钻头的装夹、钻头刃磨质量、工件位置及钻床切削用量等一些不确定因素的影响,所以,当孔的位置精度要求较高时,各方面因素累积的误差就会导致出现严重超差现象。
在钻孔操作时,除了划线正确之外,准确的定位、钻正底孔、及时准确d 的纠正偏差,才能有效地避免孔的位置超差现象,而钻头的刃磨是控制钻孔时孔的尺寸精度、形状精度、粗糙度的关键。
根据在日常工作中师傅的言传身教和自己的实践经验,在划线、定位校准、钻头的刃磨等方面总结了几项措施,用以提高钻孔的精度。
关键词:划线精度定位精度钻头刃磨切削量润滑冷却液论文主体:钻孔是钳工日常工作中最常用到的操作技能之一。
但是用普通的麻花钻在普通钻床上钻孔一般都是孔的粗加工,并且孔的位置精度、尺寸精度、形状精度受到划线、钻床精度、工件和钻头的装夹、钻头刃磨质量、工件位置、冷却润滑液及钻床切削用量等一些不确定因素的影响,所以精度都不高。
当孔的位置精度要求较高时,各方面因素累积的误差就会导致出现严重超差现象。
若是要保证钻出位置精度、形状精度、尺寸精度高的孔就不是那么简单的了。
在钻孔操作时,划线的精确,精准的定位、钻正底孔、及时准确的纠正偏差,才能有效地避免孔的位置超差现象,而钻头的刃磨是控制钻孔时孔的尺寸精度、形状精度、粗糙度的关键。
以下是我总结的在划线、定位校准、钻头的刃磨等方面的几项措施,用以提高钻孔的精度。
一、划线的精度由于钻孔时的位置精度基本上取决于划线的精确度和钻头相对于孔中心定位的精确度,所以在钻孔前,首先要熟悉图纸的工艺要求,确定加工工序,计算出各部分工艺尺寸,加工好基准面。
提高钻孔精度的方法
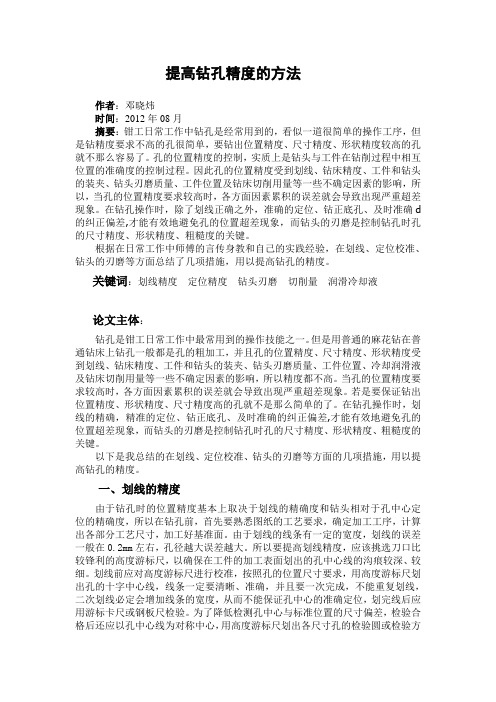
提高钻孔精度的方法作者:邓晓炜时间:2012年08月摘要:钳工日常工作中钻孔是经常用到的,看似一道很简单的操作工序,但是钻精度要求不高的孔很简单,要钻出位置精度、尺寸精度、形状精度较高的孔就不那么容易了。
孔的位置精度的控制,实质上是钻头与工件在钻削过程中相互位置的准确度的控制过程。
因此孔的位置精度受到划线、钻床精度、工件和钻头的装夹、钻头刃磨质量、工件位置及钻床切削用量等一些不确定因素的影响,所以,当孔的位置精度要求较高时,各方面因素累积的误差就会导致出现严重超差现象。
在钻孔操作时,除了划线正确之外,准确的定位、钻正底孔、及时准确d 的纠正偏差,才能有效地避免孔的位置超差现象,而钻头的刃磨是控制钻孔时孔的尺寸精度、形状精度、粗糙度的关键。
根据在日常工作中师傅的言传身教和自己的实践经验,在划线、定位校准、钻头的刃磨等方面总结了几项措施,用以提高钻孔的精度。
关键词:划线精度定位精度钻头刃磨切削量润滑冷却液论文主体:钻孔是钳工日常工作中最常用到的操作技能之一。
但是用普通的麻花钻在普通钻床上钻孔一般都是孔的粗加工,并且孔的位置精度、尺寸精度、形状精度受到划线、钻床精度、工件和钻头的装夹、钻头刃磨质量、工件位置、冷却润滑液及钻床切削用量等一些不确定因素的影响,所以精度都不高。
当孔的位置精度要求较高时,各方面因素累积的误差就会导致出现严重超差现象。
若是要保证钻出位置精度、形状精度、尺寸精度高的孔就不是那么简单的了。
在钻孔操作时,划线的精确,精准的定位、钻正底孔、及时准确的纠正偏差,才能有效地避免孔的位置超差现象,而钻头的刃磨是控制钻孔时孔的尺寸精度、形状精度、粗糙度的关键。
以下是我总结的在划线、定位校准、钻头的刃磨等方面的几项措施,用以提高钻孔的精度。
一、划线的精度由于钻孔时的位置精度基本上取决于划线的精确度和钻头相对于孔中心定位的精确度,所以在钻孔前,首先要熟悉图纸的工艺要求,确定加工工序,计算出各部分工艺尺寸,加工好基准面。
试论如何提高钻孔的加工精度

试论如何提高钻孔的加工精度摘要:结合钻孔的实际要求,合理的提高钻孔加工精度,对于保证钻孔的质量有很大帮助。
然而,在这之前需要详细的分析钻孔容易产生的缺陷及其原因,以此作为提高钻孔加工精度注意事项的依据,才能够保证钻孔加工质量,使其能够合理的运用。
因此,本文就如何提高钻孔的加工精度进行详细的分析和探讨,希望对提高钻孔质量有一定的作用。
关键词:钻孔加工精度钻削钻孔是一项非常基本的、简单的工作,在很多不同类型的工作中都会用到。
尽管钻孔操作非常的简单,但是在进行钻孔的过程中很容易受到某些不良因素的影响而出现错误。
为了最大限度的提高钻孔质量,需要就当前钻孔工作进行详细的分析,找出其中存在的缺陷,采用适合的措施对钻孔进行优化,提高钻孔的加工精度,使钻孔能够有效的应用。
一、钻孔容易产生的缺陷及原因分析所谓钻孔是指在实体材料上加工孔的方法。
对于机械加工操作工来说是一项简单的基本工作。
然而,钻孔工作容易产生缺陷,降低工作质量。
为了能够最大限度的提高钻孔质量,对钻孔比较容易产生的缺陷及原因进行分析是非常必要的。
以下笔者就钻孔容易产生的缺陷及其原因提出了几点自己的观点。
1.钻孔容易呈现多角度。
钻孔过程中,所应用的钻头容易受到某些因素的影响而出现角度不对称、两切削刃的长短不一等情况,应用此种不标准的钻头就会导致钻孔呈现多个角度的问题。
2.钻孔后孔径超出标准要求。
钻孔过程中所应用的钻孔技术如若出现钻头摆动、两切削刃高度或长短不标准等情况都会使钻孔增大,此种情况的出现对后续的工作影响较大,应当将提高钻孔的加工精度中作为工作重点。
3.钻孔位置出现偏差。
对钻孔工作有一定了解的人都知道,在实体材料上进行钻孔,必须保证钻头与实体材料是垂直的,这样才能够保证钻孔的标准。
然而,钻孔位置出现偏差的情况在钻孔工作确是比较常见的。
导致此缺陷出现的主要原因是工件安装不正确,钻头垂直方向对准的工件位置并不是标准位置,钻孔后就会得到位置出现偏差的钻孔。
提高钻孔精度的小窍门

提高钻孔精度的小窍门作者:胡天卫来源:《职业教育研究》2011年第04期摘要:在钻削加工的实操训练中,应对教学设备和学生技能基础的实际情况认真分析研究,并在找正孔的中心位置、保证工件被加工表面与钻床主轴轴线垂直度及提高麻花钻刃磨质量等方面寻找窍门,给学生掌握钻孔工艺和提高操作技能水平引路。
关键词:钻孔;精度;窍门中图分类号:G712文献标识码:A文章编号:1672-5727(2011)04-0137-02俗话说:“车工怕车细长轴,钳工怕钻孔。
”这句话说明在孔的加工方面保证精度是一件不容易的事。
在孔的加工过程中最容易造成精度误差的因素通常有孔中心偏移、孔的轴线不垂直于工件基准面和钻出孔的孔径有误差。
孔中心的偏移通常是因为孔的中心位置不正确引起的;孔的轴线不垂直基准面通常是在装夹工件时被加工表面与钻床主轴轴线不垂直造成的;孔径的误差则多数是由麻花钻刃磨不好、切削刃长度不等和角度偏差引起的。
如何找正孔的中心位置?如何保证工件被加工表面与钻床主轴轴线的垂直度?如何刃磨好麻花钻?……对一个在校生来说,这些都不容易掌握,既是重点又是难点。
通过多年的教学研究,对解决这些难点,笔者做了有益的尝试,收到了一定成效。
孔中心位置的找正窍门找好中心点,打好样冲眼划中心线时应以工件的两个基准面来划线,不要以为只要保证划线的尺寸不出错,就可以随便选择一个面来划线。
否则,不仅容易累积误差,而且还会给操作者判断样冲眼的位置带来困难。
在打样冲眼时,大家容易考虑到保证样冲轴线和工作平面的垂直度问题,而往往忽视样冲眼究竟该打在什么位置上。
通常情况,操作者很自然地就选择了中心线交叉处的中心位置(如图1a所示)。
事实上,选择的这一点并不是圆的中心。
在实践中,钳工操作通常使用的划线工具(划针、划规、高度游标卡尺等)所划出的线宽至少是0.1mm 左右。
所以,打样冲眼时应考虑这一客观因素。
正确的样冲眼选点应沿着划线基准方向且在圆的两条中心线下缘相交处,如图1b所示。
如何保证钻孔精度
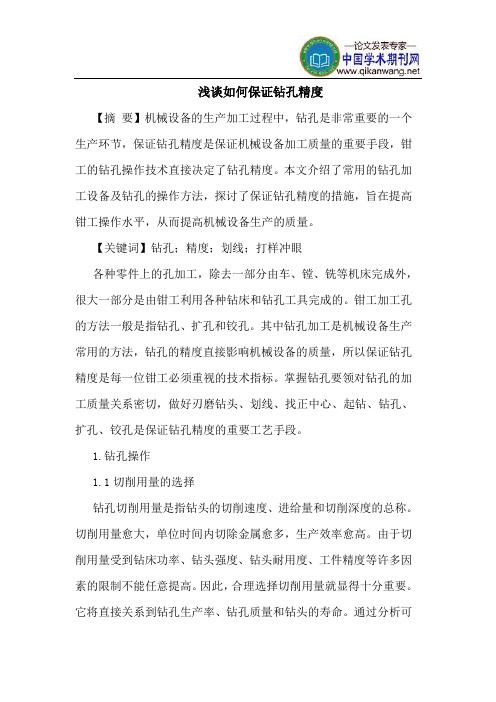
浅谈如何保证钻孔精度【摘要】机械设备的生产加工过程中,钻孔是非常重要的一个生产环节,保证钻孔精度是保证机械设备加工质量的重要手段,钳工的钻孔操作技术直接决定了钻孔精度。
本文介绍了常用的钻孔加工设备及钻孔的操作方法,探讨了保证钻孔精度的措施,旨在提高钳工操作水平,从而提高机械设备生产的质量。
【关键词】钻孔;精度;划线;打样冲眼各种零件上的孔加工,除去一部分由车、镗、铣等机床完成外,很大一部分是由钳工利用各种钻床和钻孔工具完成的。
钳工加工孔的方法一般是指钻孔、扩孔和铰孔。
其中钻孔加工是机械设备生产常用的方法,钻孔的精度直接影响机械设备的质量,所以保证钻孔精度是每一位钳工必须重视的技术指标。
掌握钻孔要领对钻孔的加工质量关系密切,做好刃磨钻头、划线、找正中心、起钻、钻孔、扩孔、铰孔是保证钻孔精度的重要工艺手段。
1.钻孔操作1.1切削用量的选择钻孔切削用量是指钻头的切削速度、进给量和切削深度的总称。
切削用量愈大,单位时间内切除金属愈多,生产效率愈高。
由于切削用量受到钻床功率、钻头强度、钻头耐用度、工件精度等许多因素的限制不能任意提高。
因此,合理选择切削用量就显得十分重要。
它将直接关系到钻孔生产率、钻孔质量和钻头的寿命。
通过分析可知:切削速度和进给量对钻孔生产率的影响是相同的;切削速度对钻头耐用度的影响比进给量大;进给量对钻孔粗糙度的影响比切削速度大。
综上所述可知,钻孔时选择切削用量的基本原则是:在允许范围内,尽量先选较大的进给量,当进给量受到孔表面粗糙度和钻头刚度的限制时,再考虑较大的切削速度。
在钻孔实践中人们已积累了大量的有关选择切削用量的经验,并经过科学总结制成了切削用量表,在钻孔时可参考使用。
1.2操作方法操作方法的正确与否,将直接影响钻孔的质量和操作安全。
按划线位置钻孔:工件上的孔径圆和检查圆均需打上样冲眼作为加工界线,中心眼应打大一些。
钻孔时先用钻头在孔的中心锪一小窝(占孔径的1/4左右),检查小窝与所划圆是否同心。
钳工实训中提高钻孔质量的方法探讨

钳工实训中提高钻孔质量的方法探讨钻孔加工是钳工技能操作中不可缺少的重要内容之一,正确掌握钻孔要领是保证加工质量的关键。
本文从三个方面阐述了提高钻孔质量的方法,刃磨钻头是提高钻孔质量的关键,划线、钻孔、扩孔是保证钻孔精度的重要工艺手段。
标签:钳工技能钻孔找正孔加工技能在钳工操作生涯中是应用最广泛的技能之一。
而且在单件小批量零件生产过程中,钻孔质量的高低有时直接决定零件的合格与否。
钻孔加工教学的好坏,对一个钳工的技能培养至关重要。
要想钻提高孔的加工精度,需要在钻头的刃磨、找正、定心、装夹等方面对被培训者进行强化培训。
经过多年的钳工技能培训教学,笔者摸索出了一套提高钻孔质量的培训方法。
1.影响钻孔的质量因素分析1.1 操作技术的影响因素1.1.1麻花钻刃磨精度的影响因素两主切削刃长度不等;两主切削刃和钻头轴心线组成的顶角φ不相等;钻头横刃未修磨短。
1.1.2划线精度的影响因素划线时重复划线,利用高度游标划线,每条线条的宽度大约为0.3~0.5mm。
重复划线导致线条过宽,造成划线精度降低,钻孔定心不准。
划线量具精度影响,划线高度游标使用年限久后前端划线部分会产生磨损,精度降低,划针宽度增大,造成划线精度降低。
而且由于读数的视线偏差影响,也会造成读数误差。
划线基准选择不当,划线基准与尺寸基准不重合,造成基准不重合误差。
1.1.3装夹精度的影响因素零件装夹不正,与钻床轴线不垂直,造成钻心偏离中心位置或者产生斜孔。
1.1.4找正、定心能力的提高由于初学者操作熟练程度的影响,找正、定心精度不高,导致钻孔精度不高。
1.2设备精度的影响因素1.2.1钻床精度的影响因素钻床主轴的径向跳动误差超差,造成钻孔时钻头摆动,影响钻孔时的定位精度。
【3】1.2.2装夹夹具精度的影响因素技能培训钻孔时,采用通用夹具进行装夹钻孔的情况较多。
通用夹具的制造精度、装配精度影响钻孔的位置精度。
当通用夹具的装夹面与钻床主轴的平行度偏差较大时,将会造成孔歪斜,甚至产生废品。
提高钻孔精度的小窍门
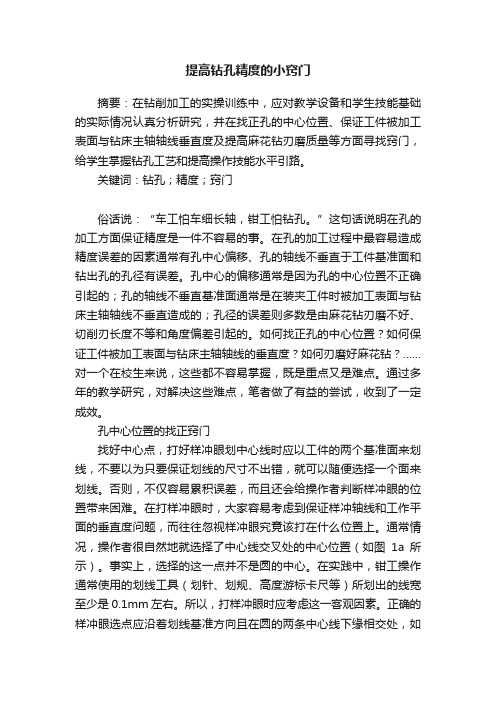
提高钻孔精度的小窍门摘要:在钻削加工的实操训练中,应对教学设备和学生技能基础的实际情况认真分析研究,并在找正孔的中心位置、保证工件被加工表面与钻床主轴轴线垂直度及提高麻花钻刃磨质量等方面寻找窍门,给学生掌握钻孔工艺和提高操作技能水平引路。
关键词:钻孔;精度;窍门俗话说:“车工怕车细长轴,钳工怕钻孔。
”这句话说明在孔的加工方面保证精度是一件不容易的事。
在孔的加工过程中最容易造成精度误差的因素通常有孔中心偏移、孔的轴线不垂直于工件基准面和钻出孔的孔径有误差。
孔中心的偏移通常是因为孔的中心位置不正确引起的;孔的轴线不垂直基准面通常是在装夹工件时被加工表面与钻床主轴轴线不垂直造成的;孔径的误差则多数是由麻花钻刃磨不好、切削刃长度不等和角度偏差引起的。
如何找正孔的中心位置?如何保证工件被加工表面与钻床主轴轴线的垂直度?如何刃磨好麻花钻?……对一个在校生来说,这些都不容易掌握,既是重点又是难点。
通过多年的教学研究,对解决这些难点,笔者做了有益的尝试,收到了一定成效。
孔中心位置的找正窍门找好中心点,打好样冲眼划中心线时应以工件的两个基准面来划线,不要以为只要保证划线的尺寸不出错,就可以随便选择一个面来划线。
否则,不仅容易累积误差,而且还会给操作者判断样冲眼的位置带来困难。
在打样冲眼时,大家容易考虑到保证样冲轴线和工作平面的垂直度问题,而往往忽视样冲眼究竟该打在什么位置上。
通常情况,操作者很自然地就选择了中心线交叉处的中心位置(如图1a所示)。
事实上,选择的这一点并不是圆的中心。
在实践中,钳工操作通常使用的划线工具(划针、划规、高度游标卡尺等)所划出的线宽至少是0.1mm 左右。
所以,打样冲眼时应考虑这一客观因素。
正确的样冲眼选点应沿着划线基准方向且在圆的两条中心线下缘相交处,如图1b所示。
选择有正确锥度的样冲打眼保证所使用的样冲有正确的锥度对初钻时的钻头定位是十分重要的。
在打样冲眼时千万别小看这个问题,更不应该随便在砂轮机上刃磨几下样冲就打眼了。
谈提高钻孔位置精度的方法

周刊谈提高钻孔位置精度的方法赵东坡(淮海技师学院,江苏宿迁223800)摘要:在加工孔的过程中,控制定位精度,本质上即为一个孔的理想位置与实际位置间差值方面的动态控制过程。
钳工 钻孔位置通常具有较高的精度要求,且在控制上仅能以手工方式来完成,所以加工精度在某种程度上受到操作者钳工钻孔技能 等诸多主观性因素的影响。
本文结合对钳工钻孔位置精度造成影响的相关因素,就如何有效克服与规避钻孔位置度误差这一 难题,通过多次的实验与论证,不断改进、改善钻孔的方法与工艺,深入剖析了对钻孔位置精度造成影响的各类因素,以期对孔 的位置精度施加有效控制。
关键词:孔的位置精度;扩孔;钻孔;麻花钻钻孔加工乃为工具钳工人员必须熟练掌握与应用的基 本技能,是整个钳工实习教学当中的关键内容,同时还是操 作实训考核的核心项目。
对于那些具有不高的钻精度要求 的钻孔,则比较简单,但是要想钻出具有较高形状精度、尺寸 精度及位置精度的孔,便不是一件容易的事情。
1、正确回线在进行画线前,首先要做的便是熟悉图纸,查看评分标 准、技术要求及图形标注;对完成加工的工件进行检查,对于 基准平面而言,需满足平面度<0.02mm,对于相邻基准平 面垂直度,需使其<0.02mm。
另外,结合工件外形加工尺 寸,将钻孔的实际位置尺寸计算出来;依据钻孔相应位置尺 寸要求,选择那些拥有比较锋利刀头的高度尺,将孔位置的 十字中心线准确画出,便于在实际加工表面上,能够得到比 较深的孔中心线沟痕;要求具有比较准确、清晰的线条,当所 画的线条越细时,则表明具有越高的精度。
接下来便是打样 冲眼,首先需要运用样冲移动时孔中心线沟痕对其所具有的 阻力作用,将样冲眼打制的正确位置确定下来。
为了能够将 理想位置与目测孔中心之间所存在的尺寸偏差最大化减小,需要将以孔中心线为轴心与中心的检验圆或者是检验方格 画出来,将其当做试钻孔时的检查线,便于试钻孔操作时对 钻孔的位置进行修正与检查。
提高钻孔精度的加工方法

提高钻孔精度的加工方法作者:许杰来源:《教育界》2011年第08期普通钻床高精度孔加工,通常是用钻、铰孔的方法来保证孔的精度。
在长期生产实践中我们摸索出一种钻孔精度介于钻孔和铰孔之间的钻孔方法,其尺寸精度可达IT7级,表面粗糙度可达Ra3.2~0.8。
这种方法操作简单,易于掌握,能适应各种金属材料,在小批量生产及修理或是作为较高精度孔的前加工方法,精钻孔方法在实践中得到较好的应用。
现将这一方法介绍如下:一、加工方法钻精孔的钻头虽然和普通钻头不同,但也不能一次直接完成所要钻的孔。
精钻孔于铰孔加工工艺方法相似,在普通钻床上用标准钻头先钻出小于公称直径的底孔,留加工余量0.1~1mm,然后再用改良后的精孔钻头进行孔加工。
二、钻头的改良精孔钻钻头,在普通麻花钻头的基础上,应作以下改良:1.磨出第二个顶角2Φ1≤65°,新形成的两主切削刃长3~4mm,并且将它和两副切削刃的连接处用油石磨出r=2.0-2.5mm的过渡圆角,两个新的切削刃要求对称,从而使之形成粗精加工的联合切削刃,形成梯次加工。
2.磨窄刃带或磨出副后角α=6°~8°,并保留刃带宽度f=0.1~0.2mm,修磨长度为4~5mm,以减少表面的摩擦。
3.磨出负刃倾角,一般负刃倾角入=-10°~-15°,使得削流向非加工表面。
4.后角不宜过大,一般α=6°~10°,以减少钻孔时产生的振动。
5.切削刃的前后面需用油石研磨,其表面粗糙度达到Ra0.2。
其改良钻头切削角度见右图:三、加工特点精钻孔与钻孔,铰孔的不同:1.精钻孔时切削的梯次加工减少了切削的厚度和变形,负荷较轻,振动也大为减小。
2.精钻孔切削量小,切削阻力大大减小,前工序产生的缺陷容易纠正,有利于孔加工几何精度的保证。
3.精钻孔头磨损较小,能保持原有的锋利,降低成本。
4.精钻孔可提高刀具的修光能力,改善散热条件,降低孔的表面粗糙度。
浅谈提高钻孔位置精度的有效方法

交流平台浅谈提高钻孔位置精度的有效方法文/张冠兰摘 要:钻孔是钳工必须掌握和应用的一项基本技能。
它是整个钳工实习教学的核心内容,也是操作训练考核的核心工程。
因此,对于相关操作者来说,不仅要有一定的操作技能,还需要有丰富的加工技能。
然而,在实际钻孔作业中,往往存在定位过度的情况。
目前,许多专家和实践工作者对如何有效地控制钳工钻孔的定位精度进行了全面、深入、系统的研究和探讨。
本文参考他们的有益经验、方法和思想,通过笔者实际操作、反复探索和思考,总结出成果和信息。
关键词:钻孔 钳工 加工工艺一、影响钻孔定位精度的因素分析影响钻削位置精度的主要因素有工件夹紧、钻头、加工工艺、刀具设备、麻花钻的磨削和麻花钻的结构。
1.麻花钻结构特点对钻孔精度的影响(1)麻花钻的基本结构特征,即一个水平刃和两个切削刃。
对于水平刃,在实际的钻削操作中,可以相应地增加轴向张力;此外,横刃与轴线会存在不对称现象,如果有这样的情况,就会导致实际的切削位。
当有左右摆动时,不能准确对中,所以会直接影响到孔的对应位置。
(2)麻花钻钻头的切削性能较差。
在钻削操作开始时,所有位于核心位置的切削刃将以直接的方式参与切削。
当切削阻力过大时,钻芯将出现不同程度的偏斜。
(3)麻花钻属于细长杆,刚性差。
此外,它的指向性差,容易弯曲,这会影响孔的位置精度。
(4)标准麻花钻本身有一定的加工误差,对钻削精度有一定影响。
在实际钻孔作业中,应尽量采用各种零件的尺寸精度和公差要求以及接近钻头的要求。
2.钻孔工艺对孔加工定位精度的影响(1)麻花钻本身的结构特点,在很大程度上决定了麻花钻的缺点,即摆动大、易弯曲、刚性差、导向不良、定心不稳定。
在扩孔时,只有最周边的切削刃,为了减少阻力,在铰孔时没有十字刃切削,此时钻头可以浮动和定心。
因此,先钻后扩孔工艺和方法不仅能保证扩孔后的位置精度,而且即使存在误差,也能通过扩孔和纠偏的方法消除误差。
(2)在实际钻孔作业中,首先使用直径为3mm 的钻头或直径为2.5mm的中心钻头。
提高钳工实习钻孔位置精度的几种方法

提高钳工实习钻孔位置精度的几种方法作者:王秀娟来源:《教育界》2011年第10期【摘要】使用钻床钻出精度不高的孔很容易,但要钻出精度较高的钻孔却比较困难。
工厂里有句俗话:车工怕车杆,钳工怕打眼,指的就是钻孔的位置精度难以掌握,钳工实习教学大纲要求孔位置的误差≤±0.1㎜。
随着经济社会的进步和科学技术的发展,钳工已被细化分流成了好几类,可钻孔仍然是所有钳工练习的重点和难点,是必须掌握和最常用的基本操作技能之一。
用钻床钻出精度不高的孔很容易,但要钻出精度较高的孔就比较困难。
工厂里有句俗话:车工怕车杆,钳工怕打眼。
指的就是孔的位置精度难以掌握,钳工实习教学大纲要求孔位置的误差≤±0.1㎜。
在钳工实习中经常使用Φ6.7㎜、Φ7.8㎜、Φ8㎜等规格的钻头钻孔。
学徒工对孔的位置精度掌握不够,超差比较大。
根据我多年工作实践经验,现以孔位置误差≤±0.1㎜为例,谈谈提高钻孔位置精度的几项措施。
1.准确画线钻孔前,首先应熟悉图样要求,加工好工件的基准,一般的基准平面度≤0.04㎜,相邻基准垂直度≤0.04㎜。
按孔尺寸要求,用高度尺画出孔位置的十字中心线,要求线条清晰准确,线条越细精度越高。
由于画线的一般精度可达0.25~0.5㎜,所以画完后,要用游标卡尺或钢板尺进行检验。
初学者对画线后检验做得不够,拿着画错线的工件进行钻孔,根本保证不了孔的位置精度,特别是参加考试时担心干不完,往往画完就钻,等发现错了已经晚了,因此,要养成画线后检查的习惯。
2.画检验方格或检验圆画正确后还应画出以孔中心线为对称中心的检验方格或检验圆,作为试钻的检查线,以便钻孔时检查和借正钻孔位置。
一般可画出几个大小不一的检验方格或检验圆,小的检验方格或检验圆略大于钻头横刃,大一点的检验方格或检验圆则略大于钻头直径。
3.打样冲眼画出相应的线后应认真打样冲眼,先打一小点,在十字中心线的不同方向仔细观察样冲眼是否在十字的交叉点上,最后把样冲眼打正、打圆、打大,以便准确落钻定心,这是提高钻孔位置精度的重要环节。
保证孔系位置精度的方法
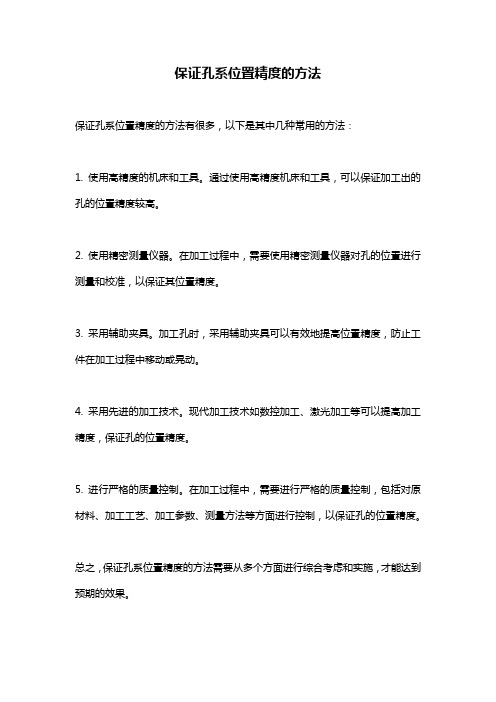
保证孔系位置精度的方法
保证孔系位置精度的方法有很多,以下是其中几种常用的方法:
1. 使用高精度的机床和工具。
通过使用高精度机床和工具,可以保证加工出的孔的位置精度较高。
2. 使用精密测量仪器。
在加工过程中,需要使用精密测量仪器对孔的位置进行测量和校准,以保证其位置精度。
3. 采用辅助夹具。
加工孔时,采用辅助夹具可以有效地提高位置精度,防止工件在加工过程中移动或晃动。
4. 采用先进的加工技术。
现代加工技术如数控加工、激光加工等可以提高加工精度,保证孔的位置精度。
5. 进行严格的质量控制。
在加工过程中,需要进行严格的质量控制,包括对原材料、加工工艺、加工参数、测量方法等方面进行控制,以保证孔的位置精度。
总之,保证孔系位置精度的方法需要从多个方面进行综合考虑和实施,才能达到预期的效果。
钳工用什么方法可以提高钻孔精度

对于钳工来说,钻孔是一项重要的基本操作技能,因此,钻孔精度的提高,是他们需要时刻关注的问题。
在实际生产中,造成钻孔精度差的原因主要有是因为划线精度不高、钻头刃磨质量较差以及钻孔时没有找正或找正不准等等,下面我们就来根据提高钻孔精度的问题进行讨论。
提高钻孔精度可以从以下几个方面考虑。
1、刃磨好钻头要想钻出好精度的孔,首先应该做的就是磨好钻头,刃磨的钻头不仅要保证顶角、后角以及横刃斜角,两主切削刃长度相等且对称钻头中心线对称、两主后刀面光滑。
同时对于不同的情况,适当修磨棱边、前刀面、分屑槽等也是很必要的。
2、精确划线精确划线,是保证尺寸准确的基础,所以在实际生产中,我们经常会使用到高度尺来精确划线,为保证线条的清晰均匀。
同时还要注意划线基准面的选择,基准面要加工精确,还要保证本身的平面度以及相邻面的垂直度。
3、正确装夹·直径在6mm以下的孔:精度要求不高,可以使用手钳夹紧工件进行钻孔。
·直径在6—10mm的孔:工件规则平整,可用平口钳夹持,保持工件表面与钻床主轴垂直。
·直径较大的孔:必须将平口钳用螺栓压板固定。
·直径在10mm以上的孔:应用压板夹紧的方法进行钻孔。
4、准确找正装夹完成后,要进行找正,找正有静态找正与动态找正两方面:·静态找正:在钻床启动之前进行找正,使钻床主轴中心线与工件十字线交点对正。
这种方法适用于新手,容易掌握但是相对的精度较低。
·动态找正:在钻床启动后进行找正,在找正的同时,把一些不确定因素均考虑在内。
这种方法虽然钻孔精度较高,但是对于操作者的要求也很高。
5、认真检测在钻孔的过程中,误差是一定会存在的。
为了减少误差,需要从各方面来采取措施。
在采取这些措施后,还需要对孔的精度及时进行检测,确保孔的精度准确性,以便及时采取措施进行补救。
浅述钻孔精度“六关”提高法

C OCCUPATION2012 0894案例ASES浅述钻孔精度“六关”提高法文/阮强志所谓钻孔就是在实体材料上加工出孔的方法。
操作起来并不是很复杂,但要保证孔的形状精度、位置精度和尺寸精度并没那么容易。
一般来说,用普通的麻花钻在普通钻床上钻孔,其钻孔精度只能达到IT10~IT11,表面粗糙度为Ra 50~12.5μm。
按照钳工实习教学大纲的要求,中级钳工钻孔位置误差应小于±0.10mm,表面粗糙度为Ra 3.2μm;高级钳工的钻孔位置误差应小于±0.05mm,表面粗糙度为Ra 1.6μm。
因此,将普通手工钻孔的位置精度提高到小于±0.05mm、表面粗糙度为Ra 1.6μm,或者要钻出形状精度高,位置、尺寸精度高的孔不是件容易的事。
一、准确把握好“划线关”划线正确与否,是钻孔对错的关键。
因此,钻孔前,首先应熟悉图样要求。
加工好工件的基准;一般基准的平面度≤0.04mm,相邻基准的垂直度≤0.04mm。
按钻孔的位置尺寸要求,使用高度尺划出孔位置的十字中心线,要求线条清晰准确。
线条越细,精度越高。
由于划线的线条总有一定的宽度,而且划线的一般精度可达到0.25~0.5mm,所以划完线以后要使用游标卡尺进行检验。
如若学生对于划线后检验做得不够,拿着划错线的工件进行钻孔,则根本无法保证孔的位置精度。
因此,要教育学生养成划完线后进行检验的好习惯。
二、熟练掌握好钻头“刃磨关”钻头是钻孔好坏、精度高低的根本保证,选择钻头直径要合理,熟悉钻头的几何尺寸、熟练掌握钻头的手工刃磨方法是学生钻孔技能的基础。
1.标准麻花钻刃磨对于标准麻花钻要磨出一支理想的钻头,就要正确理解和判断钻头上的各种几何参数,如顶角、横刃斜角、前角、后角等。
刃磨的操作要领很多,教师辅导刃磨时要反复讲解并操作示范,在学生具有感性认识和理性认识的基础上,进行主切削刃刃磨练习,反复训练目测判断120°、60°、10~14°、55°等特定角度。
如何提高钻孔精度

如何提高钻孔精度作者:平中甫来源:《科技视界》2013年第30期钻孔是钳工实习课中的重要课题也是学生不好掌握的课题之一。
俗话说:“车工怕车杆儿,钳工怕钻眼儿”。
这也是很多专业人员在长期的工作中的体会,因为很多因素都可能对钻孔的精度造成直接的影响,例如:钻头的刃磨工件的装夹转速的大小等等都会直接影响到钻孔的精度。
那么在钻孔中如何做才能提钻孔的质量,笔者就从以下几个方面谈谈自身的看法。
1 提高钻头的刃磨质量在钻削过程中钻头质量的好坏直接影响到孔的精度。
标准麻花钻刃磨时两切削面要交替刃磨及时观察切削刃的长度,对于初学的学生来说通过旋转来观察比对两刃的长度是很难发现切削刃是否一致,通过自己的总结有两方面比较直观来检查切削刃的长度:(1)在同一位置分别用两切削刃来划线观察两线高低,如果重合说明两切削刃长度相等。
(2)用专用的角度样板来测量刀刃的长度,最好是有刻度。
通过这两种方法就能很直观解决初学者刃磨钻头时两切削刃不等的问题。
2 工件的划线划线时工件涂上涂色剂,按钻孔位置划线,在孔中心位置打上样冲眼,量出半径尺寸,画圆,对于较大的孔时应多画出几个大小不一的圆,以便检查和借正钻孔位置。
对于精度要求较高的孔时,避免因样冲偏离中心时要画出几个大小不等的方格,钻孔时来检查和借正钻孔位置。
3 打样冲眼样冲一般是用45钢车削或磨削成40到60度的锥体然后淬火后才能使用,如果手工磨制的样冲圆锥度误差大钻头定心精度低。
打样冲眼时,先打一个小点,从四周观察冲点是否在十字线正中间,确认后把冲点加大,以便起钻时钻头定心准确。
4 试钻试钻就是在钻孔之前对钻床速度和进给量的确定和钻头精度的检验,包括钻孔的直径的精度孔壁的粗糙度等等的检验。
5 工件的装夹装夹工件时,工件和平口钳要擦拭干净,工件夹紧后检验工件是否与钻床主轴垂直,对于钻直径大于10毫米的孔,平口钳一定要上紧固螺钉或者使用压板,避免钻削时平口钳震动过大,影响钻孔精度。
6 起钻起钻时先用钻头在打样冲位置钻一个小坑,观察钻心是否在孔的中心位置,对于精度要求高的孔,要用中心钻先钻定位,然后再用麻花钻钻孔。
钳工作业中提高自由钻孔位置精度探讨

钳工作业中提高自由钻孔位置精度探讨摘要:钻孔工艺是钳工必备的一项基本操作技能,自由钻孔位置精度的合理控制对于零部件加工会产生直接的影响,严重时还会危及到工程建设质量。
由于受到多种因素的影响,在钻孔加工的过程中还普遍存在着位置度超差的情况,因此需要对其问题予以高度的重视,并进一步加大钳工作业过程中自由钻孔位置精度控制的技能训练,使得钳工较好的掌握加工要求,掌握孔和孔位置精度的控制方法。
关键词:自由钻孔;位置精度;提高对策钳工作业中,在板料上通过划线进行钻孔加工,是一项重要的操作技能,是钳工技能考核内容的一个重要组成部分,作业人员必须熟练掌握。
所谓钻孔,就是在实体工件上加工出孔的方法。
操作起来并不是很复杂,首先按钻孔的位置尺寸要求,划出孔位的十字中心线,并打上中心样冲眼,然后将工件装夹好,再选择合适的钻头和钻床转速,即可进行钻孔。
但在没有专用钻具的情况下,自由钻孔要达到图纸上要求的较高的孔距精度,就不那么容易了,在钳工钻孔作业的过程中,往往会出出现各种情况的定位不准确现象。
如何有效地避免和消除孔位超差现象,是自由钻孔中孔位精度控制的关键。
在机床精度、工件和钻头的装夹、钻头刃磨质量及机床切削用量的调整得到有效保证的基础上,划线正确、钻正底孔、及时准确借正,是保证孔位精度的基础。
一、自由钻孔及其位置精度影响因素钻孔,实际上就是在实体工件之上采取多种方法加工出孔的工艺。
对于钻孔的流程而言,首先需要按照钻孔位置的尺寸要求在孔位上划出十字中心线,其次打中心样冲眼,在装夹工件之后再利用适合的钻头和钻床转速进行钻孔。
钻孔对其位置精度具有较高的要求,通常情况下,中级钳工自由钻孔的位置误差应<±0.10mm,而高级钳工自由钻孔的位置误差则需要控制在≤±0.05mm的范围当中。
从钳工自由钻孔位置精度的影响因素来看,集中体现在以下几点。
1.麻花钻的结构特点是造成自由钻孔位置精度误差较大的主要因素,横刃相对轴线位置的不对称使得钻头切入时易发生摆动,导致定心不准确2.钻孔加工工艺方法是影响其位置精度的另一重要因素,若在扩孔时将没有将工件固死在钻床工作台之上则无法保证位置的准确性。
浅谈提高钻孔位置精度的方法

浅谈提高钻孔位置精度的方法发表时间:2011-08-05T16:54:30.640Z 来源:《职业技术教育》2011年第6期供稿作者:施荣[导读] 划出检查孔位置精度的“检查圆”和“检查框”。
在孔加工时,可以根据工作实际需要选择这两种找正基准。
施荣(江苏省南通职业大学技师学院江苏南通226001)摘要:钻孔是钳工专业一项重要基本操作技能之一,要求对学生进行系统的技能技巧训练,掌握加工要求较高的孔及孔系位置精度的方法。
关键词:钻孔方法孔距精度技能训练俗话说“钳工怕眼(钻孔),车工怕杆(车细轴)”,由此可见,钻孔是钳工专业一项重要的又比较难掌握的基本操作技能之一。
在实际批量生产中,加工位置精度要求较高的孔及孔系一般都采用工装夹具、钻模夹具等方法来加工以保证精度的。
而在单件生产中,特别是在钳工应会考核和操作比赛中,是不可能采用钻模加工来保证钻孔位置精度的,只能通过划线、找正等其它一些方法来保证钻孔位置的精度。
下面介绍一下我在多年的钳工实习教学、培训和技能比武中用来提高钻孔精度、保证钻孔位置精度的几种方法。
一、保证提高划线精度的几种方法和注意事项划线精度的高低是确保加工钻孔位置精度的一个重要前提,因此在划线时应做好以下几方面的工作,以提高划线精度:(1)采用高度游标划线尺划出加工孔的加工位置线。
用高度游标划线尺划线,首先应检查高度尺的示值误差是否在规定的精度误差范围内,以保证所划线条的尺寸准确;其次还应检查高度游标划线尺的划线刃口是否锋利,以确保所划线条清晰均匀。
(2)保证工件划线基准面无毛刺和达到形位精度要求,保证划线平板的精度,保持平板工作表面无毛刺、灰尘、杂质等,以免影响划线精度。
(3)如果孔加工的位置尺寸在图纸上没有直接标注出来,则需要通过相关尺寸的换算才能得到。
因此在尺寸换算时,必须保留小数点后三位数,保证尺寸换算的准确性,提高划线精度。
(4)正确使用样冲。
样冲眼的作用是为钻孔或划圆弧起定心作用的,因此,对刃磨样冲的要求是非常高的,要求样冲头必须磨得圆而尖和有足够的硬度。
- 1、下载文档前请自行甄别文档内容的完整性,平台不提供额外的编辑、内容补充、找答案等附加服务。
- 2、"仅部分预览"的文档,不可在线预览部分如存在完整性等问题,可反馈申请退款(可完整预览的文档不适用该条件!)。
- 3、如文档侵犯您的权益,请联系客服反馈,我们会尽快为您处理(人工客服工作时间:9:00-18:30)。
提高钻孔位置精度的几项措施
【摘要】:在钳工操作考核中钻孔是一项重要的内容,分数占整个考核的1/5,所以控制好钻孔精度是钳工必须掌握的基本技能。
本文主要阐述了钳工操作过程中一些能有效提高钻孔位置精度,使钻孔达到所要求位置精度的方法和经验。
【关键词】:钻孔;精度;钳工
【中图分类号】g710
我们都知道在机械设备上零件、构件、部件之间的连接许多是靠孔来保证的,绝大多数的孔是钳工钻孔加工出来的。
钻孔是钳工最常用的操作技能,也是钳工实习教学的重点和难点。
俗话说:“钳工怕打眼,车工怕长轴”。
在钻床上钻精度不高的孔很容易,但要钻出精度较高的孔却绝非易事。
钳工实习教学大纲要求孔位置误差≤±0.10mm,学生对这种较高位置精度的钻孔不易掌控,通常位置精度超差比较大。
孔的位置精度的控制受到划线、机床精度、工件和钻头的装夹、钻头刃磨质量、工件位置及机床切削用量的调整等一些不确定因素的影响,所以,当孔的位置精度要求较高时,就会导致出现严重超差现象。
根据多年钳工教学经验,现以孔位置误差≤±0.10mm为例,谈谈提高钻孔位置精度的几项措施:
一、做好钻孔准备
1、划线要准
钻孔前,应按钻孔的位置尺寸要求,划出表示孔位置的对称中心
线,要求线条清晰准确(线条越细越好,其精度越高)。
并划出检查圆或检查方格,作为钻孔检查线,以便钻孔时检查和借正钻孔位置。
2、冲眼要正
打中心冲眼应先打一小点,在十字中心线的不同方向仔细观察,中心冲眼应在对称中心线的交叉点上,最后把中心冲眼用力打正打圆,以便准确落钻定心。
3、工件装夹要紧
擦拭干净机床台面、夹具表面、工件基准面,将工件夹紧,要求装夹平整、牢靠,便于观察和测量。
同时应注意工件的装夹方式,以防工件因装夹而变形。
4、钻头装夹要短
钻头的夹柄装入钻夹部分应不少于15mm,钻头露出部分要尽可能短,以提高钻头的刚性和强度,从而有利于钻孔位置精度的保证。
5、钻头中心对准冲眼中心要准
对正样冲眼,钻头中心与样冲眼的对正有两种方法:一是用手转动钻夹头,并移动平口钳或转动台钻的工作台,使中心钻与样冲眼对正。
二是比较规整的工件尽可能处于浮动状态,依靠钻削力的拉动使工件位置产生微量的移动,让钻头与样冲眼自动对中。
二、钻孔操作
1、试钻
钻孔前必须先试钻:使钻头横刃对准孔中心样冲眼钻出一浅坑,
然后目测该浅坑位置是否正确,并要不断纠偏,使浅坑与检验圆或检验方格同轴。
2、钻孔
钳工实习钻孔一般以手动进给操作为主,当试钻达到钻孔位置精度要求后,即可进行钻孔。
手动进给时,进给力量不应使钻头产生弯曲现象,以免孔轴线歪斜。
钻小直径孔或深孔时,要经常退钻排屑,以免切屑阻塞而扭断钻头,并注意冷却润滑。
三、钻孔偏斜后的补救
按照上面所述方法,经过一段时间的练习后,对钻孔位置精度的把握有很大改善,但由于划线、试钻中修正偏差等操作都不可避免的存在着误差,要达到图纸上要求的较高的孔距精度,仍不那么容易,在钳工锉配课题练习中,还是失分较多。
下面根据本人在工作时的体会,总结以下几种修复补救的方法:
1、如果工件外形没有加工余量时,可以选用修孔法:所谓修孔法,就是将加工偏斜的孔修正到所需要的位置。
对于孔位超差>0.10的孔,可采取圆锉修正技术去除多余的偏移余量后再配以钻孔加以解决。
例如:
如上图所示,工件的外形已加工好,要保证图纸上要求的孔距尺寸,可先划出孔的中心线并打中心冲眼,再用φ5mm钻头钻孔,测量孔距,若超出图纸要求的孔距误差,就要对孔进行修锉。
如上图,若用φ5mm钻头钻孔后,测得孔中心到基准面的距离为9.8mm和10.1mm。
即长度方向孔距小了0.2mm,宽度方向孔距大了
0.1mm。
这时只要将孔的右面锉去0.4mm,即孔横向直径锉到φ
5.4mm;再将孔的下面锉去0.2mm,即孔纵向直径锉到φ5.4mm。
注意应将孔锉至基本椭圆,所选的修锉圆锉直径略小于原底孔直径,直径过大或等于底孔直径,圆锉插不进底孔内或修锉时锉削困难;过小易修锉成梨形状,使扩孔钻头切削力不对称,钻孔时产生新的孔位偏移。
如上图所示,去除多余的偏移余量后,然后再用φ6mm的钻头扩孔,检测孔距,如仍存在误差,重复上述方法进行修锉孔,若孔距已符合要求,则可用φ7.8mm钻头扩孔,最后用φ8h7铰刀铰孔即可。
一般经两次修锉孔后,能准确的保证图纸上的孔距要求。
修锉法控制孔位精度技术,由于影响因素较多,实际上是一个循序渐进、精度逐步提高的过程,特别是误差偏大时,特别适用。
2、如果工件外形还有加工余量时,可以选用修边法:这种方法适用于孔位精度要求高且工件外形可以加工或有加工余量的情况。
可以直接将孔加工完,然后以孔为基准加工工件外形尺寸,直到孔的位置尺寸达到公差要求。
例如:
加工上图中工件,工件外形有加工余量。
为了很好的保证孔距的精度要求,可先按图纸要求划出孔中心线并打中心冲眼,再用φ5mm 钻头钻孔,φ7.8mm钻头扩孔,倒角,最后用φ8h7铰刀铰孔。
然后检测孔距是否符合要求,若存在误差(一般总会存在一定的误差),可通过锉削平面a和平面b来保证孔距要求。
使用这种方法时,可能会出现这样情况:孔钻铰好后,检测孔距时,发现孔距已
偏小,即已没有锉削余量。
为了避免这种情况出现,在钻孔前要注意划线和打中心冲眼的准确性,也可有意识的略偏离a、b面一些,以保证钻好孔后有锉削修整余量。
又如图所示,加工正六面体工件,要求孔到多边形各面距离相等,这类工件如果先加工好外形再钻孔,一般很难保证孔到各面距离相等。
若采用先钻孔铰孔再加工锉削面,则较容易保证孔中心到各边的距离。
加工方法为:先划出孔的中心线并打中心冲眼,再用
φ5mm钻头钻孔,φ7.8mm钻头扩孔,倒角,最后用φ8h7铰刀铰孔,然后锉削各面。
测
量时,将φ8mm标准圆柱塞入孔中,用百分表测量圆柱到各面的距离,保证孔到各面的距
离相等。
这两种方法都能有效的保证图纸上的孔距要求,且加工速度快,在钻孔加工过程中,针对工件的不同情况,可灵活选用,也可两种方法结合在一起使用。
以上是本人对钳工实习教学中钻孔内容的一点心得体会,通过在实际教学中的应用,教学效果良好,可保证学生对钻孔操作技能的熟练掌握。