机械制造装备设计-支撑件导轨-PPT文档资料
合集下载
机械制造装备设计-第5章 典型部件设计-支承件、导轨设计-PPT精品文档
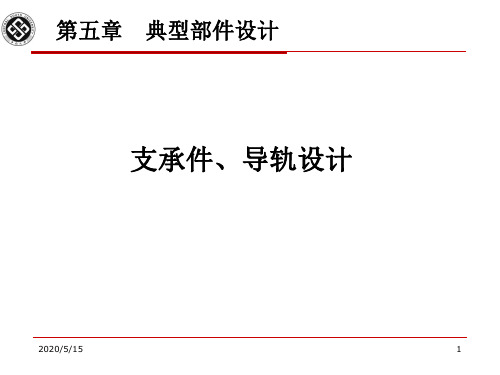
的低阶频率较高,各阶频率不致引起结构共振;不会因薄壁振动 而产生噪声。 热稳定性好。 排屑畅通、吊运安全,并具有良好的结构工艺性。
2019/9/30
2
支承件的结构设计
首先考虑所属机床的类型、布局及常用支承件的形 状。
综合考虑其工艺性。 初步决定其形状和尺寸。 进行有限元计算,求出其静态刚度和动态特性。 修改和完善,选出最佳结构形式,既能保证支承件
201610366直线滚动导轨副1一导轨2一端面挡板3一密封垫4一滚珠5一滑快直线滚动导轨副的工作原理滑块5中装有两组滚珠4两组滚珠各有自己的工作轨道和返回轨道当滚珠从工作轨道滚到滑块中的返回轨道孔返回在导轨条和滑块的滚道内连续地循环滚201610367直线滚动导轨副1一导轨2一端面挡板3一密封垫4一滚珠5一滑快滚动导轨块导轨块2用螺钉固定在动导轨体3上滚动体4在导轨块2与支承导轨5之间滚动并经两端的挡板1和6及返回轨道返回连续作循环运动
2019/9/30
35
导轨应满足的要求
导向精度 承载能力大,刚度好 精度保持性好 低速运动平稳 结构简单、工艺性好
2019/9/30
36
直线运动导轨的截面形状
直线运动导轨的截面形状主要有四种:矩形、三角形、燕尾形和 圆柱形,并可互相组合,每种导轨副之中还有凸、凹之分。
导轨的截面形状
a)矩形导轨 b)三角形导轨 c)燕尾形导轨 d)圆柱形导轨
2019/9/30
37
回转运动导轨的截面形状
圆运动导轨 a)平面环形导轨 b)锥面环形导轨 c) 双锥面导轨
2019/9/30
38
导轨的组合形式
导轨的组合 a)双三角形导轨 b)宽式双矩形导轨 c)窄式双矩形导轨
2019/9/30
2
支承件的结构设计
首先考虑所属机床的类型、布局及常用支承件的形 状。
综合考虑其工艺性。 初步决定其形状和尺寸。 进行有限元计算,求出其静态刚度和动态特性。 修改和完善,选出最佳结构形式,既能保证支承件
201610366直线滚动导轨副1一导轨2一端面挡板3一密封垫4一滚珠5一滑快直线滚动导轨副的工作原理滑块5中装有两组滚珠4两组滚珠各有自己的工作轨道和返回轨道当滚珠从工作轨道滚到滑块中的返回轨道孔返回在导轨条和滑块的滚道内连续地循环滚201610367直线滚动导轨副1一导轨2一端面挡板3一密封垫4一滚珠5一滑快滚动导轨块导轨块2用螺钉固定在动导轨体3上滚动体4在导轨块2与支承导轨5之间滚动并经两端的挡板1和6及返回轨道返回连续作循环运动
2019/9/30
35
导轨应满足的要求
导向精度 承载能力大,刚度好 精度保持性好 低速运动平稳 结构简单、工艺性好
2019/9/30
36
直线运动导轨的截面形状
直线运动导轨的截面形状主要有四种:矩形、三角形、燕尾形和 圆柱形,并可互相组合,每种导轨副之中还有凸、凹之分。
导轨的截面形状
a)矩形导轨 b)三角形导轨 c)燕尾形导轨 d)圆柱形导轨
2019/9/30
37
回转运动导轨的截面形状
圆运动导轨 a)平面环形导轨 b)锥面环形导轨 c) 双锥面导轨
2019/9/30
38
导轨的组合形式
导轨的组合 a)双三角形导轨 b)宽式双矩形导轨 c)窄式双矩形导轨
《支撑件与导轨设计》课件

设计原则
了解支撑件设计的核心原则, 以实现高效的功能和可靠的 性能。
材料选择
探讨不同材料对支撑件性能 的影响,以实现最佳的设计 方案。
导轨设计
1 种类与用途
了解常见导轨的种类,并了解它们在工业生产中的广泛应用。
2 设计原则
掌握导轨设计的关键原则,以确保其稳定性和可靠性。
3 材料选择
研究不同材料的导轨性能,并选择适合特定应用的材料。
《支撑件与导轨设计》 PPT课件
本次PPT课件将详细介绍工业生产中支撑件与导轨的设计,包括其种类、用途、 设计原则、材料选择以及配合设计等方面内容。
简介
支撑件与导轨是工业生产中至关重要的组成部分。本课程将深入介绍支撑件与导轨的设计原则、材料选择和配 合设计。
支撑件设计
种类与用途
探索支撑件的多样性及其在 工业生产中不同应用领域的 用途。
支撑件与导轨的配合设计
1
配合原理
深入理解支撑件与导轨之间的配合原理,以确保协同工作的顺畅。
2
配合设计技巧
学习如何设计支撑件与导轨的配合方式,以确保其性能和可靠性。
3பைடு நூலகம்
常见问题及解决方法
探讨可能出现的配合问题,并提供解决方案以确保系统的正常运行。
相关应用
在生产生活中的应用
了解支撑件与导轨在工业生产生 活中的各种实际应用场景。
3 未来的展望
支撑件与导轨的设计将在 未来持续发挥重要作用, 我们应该继续研究和创新。
具体案例分析
通过具体案例,深入分析支撑件 与导轨在实际项目中的设计与应 用。
创新性设计的展望
展望支撑件与导轨设计的未来发 展方向,积极推动工业创新。
总结与展望
机械制造装备设计PPT课件-第三章_机床主要部件设计(3)
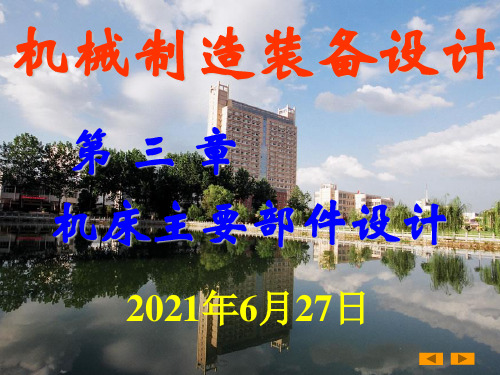
(1)垫片调隙式
用螺钉连接两个螺母的 凸缘,在凸缘间加垫片。
第四节 滚动丝杠螺母副机构
二、滚珠循环方式及轴向间隙调整 1.滚珠循环方式
(1)外循环滚珠丝杠副 如图,丝杠螺母
之外置有插管式回 珠器5,螺母之内 装有挡珠器。
丝杠匀速转动时,挡珠器能迫使滚珠转几圈后,经回珠器返回 入口,完成一个滚动循环,同时准备开始新的循环。
钢珠每一个循环称为一列,每一列内每个导程称为一圈,外循 环每列有1.5圈、2.5圈、 3.5圈,剩下的半圈用作回珠。
第四节 滚动丝杠螺母副机构
2.轴向间隙的调整和施加预紧力的方法 为什么滚珠丝杠轴向间隙要能够调整?怎样调整?
滚珠丝杠副的轴向间隙会造成: ① 滚珠丝杠启动、停止以及受冲击载荷时运动不平 稳; ② 反向时存在空行程,影响传动精度和定位精度。
调整方法: 采用双螺母装置消除轴向间隙。
第四节 滚动丝杠螺母副机构
第三节 导轨设计
④ 燕尾形和矩形导轨的组合
这组导轨调整方便,承载力矩大。广泛用在机床的横梁、立柱、 摇臂导轨中。
第三节 导轨设计
⑤ 双燕尾形导轨
是一种不用辅助导轨副的闭式导轨。导轨高度小,可承受颠覆 力矩。
燕尾导轨是过定位,必须用镶条调整摩擦面的间隙。由于结构 原因,此导轨刚度差,加工、检验、维修不方便。
如图:常用的闭式静压导轨,液压泵产生的压力油,经可变节 流器节流后,通入导轨面油腔A和辅助导轨面油腔B
导轨面的油腔形成一个个独立的液压支承点,在液压的作用下, 动导轨及其运动部件便浮动起来,形成液体摩擦。
第三节 导轨设计
五、低速运动平稳性 1. 爬行现象及产生原因
1)爬行 是进给传动机构的一种低速运动的不均匀现象,即在 传动件以很低的速度匀速转动时,工件台出现速度不均匀的跳跃式 运动,或出现间歇式运动,速度时快时慢,时走时停。
用螺钉连接两个螺母的 凸缘,在凸缘间加垫片。
第四节 滚动丝杠螺母副机构
二、滚珠循环方式及轴向间隙调整 1.滚珠循环方式
(1)外循环滚珠丝杠副 如图,丝杠螺母
之外置有插管式回 珠器5,螺母之内 装有挡珠器。
丝杠匀速转动时,挡珠器能迫使滚珠转几圈后,经回珠器返回 入口,完成一个滚动循环,同时准备开始新的循环。
钢珠每一个循环称为一列,每一列内每个导程称为一圈,外循 环每列有1.5圈、2.5圈、 3.5圈,剩下的半圈用作回珠。
第四节 滚动丝杠螺母副机构
2.轴向间隙的调整和施加预紧力的方法 为什么滚珠丝杠轴向间隙要能够调整?怎样调整?
滚珠丝杠副的轴向间隙会造成: ① 滚珠丝杠启动、停止以及受冲击载荷时运动不平 稳; ② 反向时存在空行程,影响传动精度和定位精度。
调整方法: 采用双螺母装置消除轴向间隙。
第四节 滚动丝杠螺母副机构
第三节 导轨设计
④ 燕尾形和矩形导轨的组合
这组导轨调整方便,承载力矩大。广泛用在机床的横梁、立柱、 摇臂导轨中。
第三节 导轨设计
⑤ 双燕尾形导轨
是一种不用辅助导轨副的闭式导轨。导轨高度小,可承受颠覆 力矩。
燕尾导轨是过定位,必须用镶条调整摩擦面的间隙。由于结构 原因,此导轨刚度差,加工、检验、维修不方便。
如图:常用的闭式静压导轨,液压泵产生的压力油,经可变节 流器节流后,通入导轨面油腔A和辅助导轨面油腔B
导轨面的油腔形成一个个独立的液压支承点,在液压的作用下, 动导轨及其运动部件便浮动起来,形成液体摩擦。
第三节 导轨设计
五、低速运动平稳性 1. 爬行现象及产生原因
1)爬行 是进给传动机构的一种低速运动的不均匀现象,即在 传动件以很低的速度匀速转动时,工件台出现速度不均匀的跳跃式 运动,或出现间歇式运动,速度时快时慢,时走时停。
机械制造技术装备及设计-3-5支撑件设计

第二节 支承件的静刚度与结构设计
一、支承件的静刚度
支承件的变形一般包括三部分:自身变形、局部变形和接触 变形。
1.提高支承件自身刚度 1) 正确选择支承件的截面和尺寸
支承件抵抗自身变形的能力称为支承件的自身刚度,主要决 定于支承件的材料、形状、尺寸和筋板的布置等。
对于同一材料,截面积相当而形状不同时,截面惯性矩相差 很大,合理选择截面可提高支承件自身刚度。
4.内应力
支承件的设计应从结构上和材料上保证其内应力要小,并应 在焊,铸等工序后进行失效处理;
5.其它
支承件还应使排屑通畅,操作方便,调运安全,等。
三、支承件的静力分析
图 4.5-1 普通车床的受力分析
切削力分解为三个分力:Px、Py、Pz作用在 离主轴端部x处直径为d的工件上。根据力的 平衡,求出床头箱支反力,尾架顶尖上的支 反力及主轴端拨盘上的扭矩
惯性矩是一个物理量,通常被用作述一个物体抵抗扭动,扭转的能力。 惯性矩的国际单位为千克乘以平方米(kg·m2)。
①空心截面的惯性矩比实心的大。因此, 在工艺可能的条件下应尽量减薄壁厚。 一般不用增加壁厚的办法来提高自身刚 度。
②方形截面的抗弯刚度比圆形的大,而 抗扭刚度较低。若支承件所承受的主要 是弯矩,则应取方形或矩形为好。环形 的抗扭刚度比方形、方框形与长框形的 大
图4.5-5 凸缘设计对刚度的影响
• 支承件抵抗局部变形的能力, 称为支承件局部刚度。这种变形 主要发生在载荷较集中的局部结 构处,它与局部变形处的结构和 尺寸等有关。
•合理设置加强筋是提高局部刚 度的有效途径。
二、支承件的结构设计
1.支承件形状和尺寸的确定 1) 卧式床身
卧式床身有3种结构形式:中小型车床床身,是由两端的床 腿支承;对于大型卧式车床镗床、龙门刨床、龙门铣床等的 床身,是直接落地安装在基础上;有些仿形和数控车床,则 是采用框架式床身。
第3章_典型部件设计(主轴、支承件、导轨)ppt课件

提高主轴抗振性 原则:传动力Q引起的主轴弯曲变形要小;
引起主轴前端在误差敏感方向上的位移要小 结论:传动件(最大传动件)尽量靠近前支承
传动件放在两个支承中间靠近前支承,受力 情况好,使用广泛。
3.1.3.3主轴传动件位置的合理布置 (1) 传动件在主轴上轴向位置的合理布置
传动件放在主轴前的悬伸端,主轴刚性好, 主要用于具有大转盘的机床,如立式车床、镗床。
(2) 刚度 主轴组件的刚度K是指其在承受外载荷时抵抗变形的 能力,如图所示,即K=F/y(单位为N/im),刚度的倒数 y/F称为柔度。动刚度指机床在额定载荷下切削时,主轴 组件抵抗变形的能力。 动刚度与静刚度成正比,在共振 区,与阻尼(振动的阻力)近似成正比,故可通过增加 静刚度、增加阻尼比来提高动刚度。 主轴组件的刚度是综合刚度,它与主轴结构尺寸、 所选用的轴承类型和配置及其预紧、支承跨距和主轴前 端悬伸量、传动件的布置方式、主轴部件的制造和装配 质量等有关。
3.1.3.2 推力轴承位置配置形式 (3) 两端配置 缺点:主轴受热伸长后Байду номын сангаас影响主轴轴承的轴
向间隙,必须有消隙机构和热膨胀补偿机构 应用:常用于短主轴,如组合机床主轴
(4) 中间配置 优点:可减少主轴的悬伸量,并使主轴的热 膨胀向后 缺点:前支承复杂,温升大
3.1.3.3主轴传动件位置的合理布置 (1) 传动件在主轴上轴向位置的合理布置 在力Q作用下,主轴上必然存在一个挠度为
3.1.3.2 推力轴承位置配置形式(重点) 切削力→轴向受力→推力轴承 (1) 前端配置 缺点:前支承结构复杂,发热大,温升高 优点:主轴受热后向后延伸,不影响轴向精
度,精度高,可提高主轴部件刚度 应用:高精度机床和数控机床
(2) 后端配置 优点:前支承结构简单,发热小,温升低 缺点:主轴受热后向前延伸,影响轴向精度 应用:普通立式铣床、多刀车床
引起主轴前端在误差敏感方向上的位移要小 结论:传动件(最大传动件)尽量靠近前支承
传动件放在两个支承中间靠近前支承,受力 情况好,使用广泛。
3.1.3.3主轴传动件位置的合理布置 (1) 传动件在主轴上轴向位置的合理布置
传动件放在主轴前的悬伸端,主轴刚性好, 主要用于具有大转盘的机床,如立式车床、镗床。
(2) 刚度 主轴组件的刚度K是指其在承受外载荷时抵抗变形的 能力,如图所示,即K=F/y(单位为N/im),刚度的倒数 y/F称为柔度。动刚度指机床在额定载荷下切削时,主轴 组件抵抗变形的能力。 动刚度与静刚度成正比,在共振 区,与阻尼(振动的阻力)近似成正比,故可通过增加 静刚度、增加阻尼比来提高动刚度。 主轴组件的刚度是综合刚度,它与主轴结构尺寸、 所选用的轴承类型和配置及其预紧、支承跨距和主轴前 端悬伸量、传动件的布置方式、主轴部件的制造和装配 质量等有关。
3.1.3.2 推力轴承位置配置形式 (3) 两端配置 缺点:主轴受热伸长后Байду номын сангаас影响主轴轴承的轴
向间隙,必须有消隙机构和热膨胀补偿机构 应用:常用于短主轴,如组合机床主轴
(4) 中间配置 优点:可减少主轴的悬伸量,并使主轴的热 膨胀向后 缺点:前支承复杂,温升大
3.1.3.3主轴传动件位置的合理布置 (1) 传动件在主轴上轴向位置的合理布置 在力Q作用下,主轴上必然存在一个挠度为
3.1.3.2 推力轴承位置配置形式(重点) 切削力→轴向受力→推力轴承 (1) 前端配置 缺点:前支承结构复杂,发热大,温升高 优点:主轴受热后向后延伸,不影响轴向精
度,精度高,可提高主轴部件刚度 应用:高精度机床和数控机床
(2) 后端配置 优点:前支承结构简单,发热小,温升低 缺点:主轴受热后向前延伸,影响轴向精度 应用:普通立式铣床、多刀车床
机械制造装备设计支撑件导轨PPT课件

4.双燕尾形导轨
• 两个燕尾平面同时起导向及压板作用 • 一根镶条:调整各接触面的间隙 • 不能承受过大的颠覆力矩,摩擦损失较大 • 用于要求层次多、尺寸小、调整间隙方便和移动速度不大的场合 • 如CA6140刀架、B6050滑枕导轨等
第50页/共87页
第31页/共87页
(4)低速运动平稳
• 保证在作低速运动或微量位移时运动始终平 稳。
•将降低定位精 度
• 影响因素:导轨的结构和润滑
动、静摩擦系数的差值
度等
传动导轨运动的传动系统的刚
第32页/共87页
(5)结构简单、工艺性好
• 在可能的情况下,应尽量使导轨结构简单,便于制造和维护 • 对于刮研导轨,应尽量减少刮研量 • 对于镶装导轨,应做到更换容易
第40页/共87页
(二)回转运动导轨的截面形状
平面环形导轨 锥面环形导轨
第41页/共87页
1.平面环形导轨
• 平面环形导轨: • 制造容易,热变形后导轨仍能接触,只能承受轴向力,不能承
受径向力,需与带径向滚动轴承的主轴相配合,来承受径向力 • 摩擦损失小,精度高,目前用得较多。 • 适用于大直径的工作台和转盘,如滚齿机、立式车床导轨等。
(二)提高动态特性
1.改善阻尼特性 2.采用新材料制造支承件
第21页/共87页
四、提高支承件结构性能的措施
(三)提高热稳定性
1.控制温升 2.采用热对称结构 3.采用热补偿装置
第22页/共87页
第八节 导 轨设计
第23页/共87页
一、导轨的功用和应满足的基本要 求( 一 ) 导 轨 的 功 用 和 分 类
性 • 受力和变形分析、结构设计,初步决定形状和
尺寸
相关主题
- 1、下载文档前请自行甄别文档内容的完整性,平台不提供额外的编辑、内容补充、找答案等附加服务。
- 2、"仅部分预览"的文档,不可在线预览部分如存在完整性等问题,可反馈申请退款(可完整预览的文档不适用该条件!)。
- 3、如文档侵犯您的权益,请联系客服反馈,我们会尽快为您处理(人工客服工作时间:9:00-18:30)。
(二)提高动态特性
1.改善阻尼特性 2.采用新材料制造支承件
四、提高支承件结构性能的措施
(三)提高热稳定性
1.控制温升 2.采用热对称结构 3.采用热补偿装置
第八节 导轨设计
一、导轨的功用和应满足的基本要求
(一)导轨的功用和分类
• 功用:承载和导向 • 在外力作用下,能准确地沿着一定的方向运动 • 动导轨——运动的一方 • 支承导轨——不动的一方 • 只有一个自由度 • 直线或回转运动
滚柱导轨 按滚动体
滚针导轨
3)按结构形式分
开式导轨——依靠外载荷和部件自重,使 两导轨面在全长上保持贴合的导轨
闭式导轨——用压板作为辅助导轨面保证 主导轨面贴合的导轨
(二)导轨应满足的基本要求
• 机床导轨的质量在一定程度上决定了— — 机床的加工精度 工作能力 使用寿命
纵向肋板——主要提高抗弯刚度 横向肋板——主要提高抗扭刚度 斜向肋板——兼有提高抗弯刚度和抗扭刚 度的效果
T型肋板:主要提高水平面抗弯刚度,对提 高垂直面抗弯刚度和抗扭刚度作用不明 显。多用在刚度要求不高的床身上。
C图的肋板在垂直面和水平面的抗弯刚度都 比A图好。
W型布置能较大的提高水平面的抗弯、抗 扭刚度。
铁的牌号应根据导轨的要求选择 • 如果导轨是镶装上去的,或者支承件上没有导轨
,则一般可采用HT150 • 如果支承件由型钢和钢板焊接,则常用Q235AF或
,如果导轨与支承件铸为一体,则铸 铁的牌号应根据导轨的要求选择
• 如果导轨是镶装上去的,或者支承件上没有导轨 ,则一般可采用HT150
• 采用钢筋混凝土可节约大量钢材,降低成本。 但钢筋混凝土支承件的变形、侵蚀、导轨与支 承件连接刚度不足等问题,有待进一步研究解 决。
四、提高支承件结构性能的措施
(一)提高支承件的静刚度和固有频率
根据支承件受力情况合理地选择支承件的材料、截 面形状和尺寸、壁厚,合力地布置肋板和肋条, 提高结构整体和局部的弯曲刚度和扭转刚度。
(二)钢板焊接结构
• 如果支承件由型钢和钢板焊接,则常用Q235AF或 Q275钢
(三)支承件的其它材料
• 预应力钢筋混凝土支承件(主要为床身、立柱、 底座等)近年来有较大的发展。混凝土的比重 是钢的1/3,弹性膜量是钢的1/10~1/15, 阻尼高于铸铁,适合于制造受载均匀,截面积 大、抗振性要求较高的支承件。
• 内部空间可存放切削液、润滑液、液 压油的油箱、电动机
(二)支承件应满足的基本要求基本要求
1)足够的刚度和较高的刚度/重量比
要求在规定的最大载荷作用下,变形量不得 超过一定的数值。
重量占机床总重量的80%以上,应尽量减轻 支承件的重量。
2)较好的动态特性
包括较大的动刚度和阻尼; 与其它部件相配合,使整机的各阶固有频率 不致与激振频率重合而产生共振; 不会发生薄壁振动而产生噪声等。
密机床 (3)重力和切削力必须同时考虑的大型和重型机
床
(一)机床的类型、布局和支承件的形状
2. 机床的布局形式对支承件形状的影响 3. 支承件的形状
箱型类、板块类、梁类
(二)支承件的截面形状和选择
最小重量条件下,最大静刚度 • 支承件主要是承受力矩、扭矩以及弯扭复合载荷 • 自身刚度主要考虑——弯曲刚度和扭转刚度 • 在弯、扭载荷作用下,支承件的变形与截面的抗
D图自由排屑,提高刚度。
肋条——配置与某一内壁上,主要为减小局部变 形和薄壁振动,用来提高支承件的局部刚度
(四)合理选择支承件的壁厚
减轻机床重量,壁厚根据工艺上的可能选择得薄些 。 C =(2L+B+H)/3
三、支承件的材料
• 支承件的重量在机床总重量中占有很大比重,因 此必须合理选择材料。
• 支承件的材料,主要为——铸铁和钢 • 铸铁支承件,如果导轨与支承件铸为一体,则铸
3)应具有较好的热变形特性,使整机的热变 形较小或热变形对加工精度的影响较小
由于摩擦热、切削热等产生热变形和热应力
在铸造、焊接和粗加工过程中,会形成内应 力,使支承件变形。
热变形和内应力都将破坏部件间的相互位置关 系和相对运动轨迹,影响加工精度。
4)应该排屑畅通、吊运安全,并具有良好的 工艺性以便于制造和装配。
导轨可按下列性质分类:
• 1)按工作性质可分为: 主运动导轨、进给运动导轨、调位导轨
• 调位导轨只用于调整部件之间的相对位置,在 加工时没有相对运动
• 例如车床尾架用的导轨
2)按摩擦性质分
滑动导轨
滚动导轨
• 滑动导轨:混合摩擦导轨 边界摩擦导轨 液体动压导轨
按两导轨面间 的摩擦状态
液体静压导轨
• 滚动导轨:滚珠导轨
刚度比方形低 3)封闭截面的刚度远远大于开口截面的刚度,特
别是抗扭刚度
• 在两壁之间起连接作用的内壁 ——肋板 • 肋板功用——把作用于支承件局部地区的载荷
传递给其它壁板,从而使整个支承件各壁板能 比较均匀的承受载荷 • 当支承件不能采用全封闭截面时,常常布置肋 板来提高支承件的自身刚度
肋板布置的三种基本形式
二、支承件的结构设计
• 考虑机床的类型、布局及常用支承件的形状 • 满足机床工作性能的前提下,综合考虑其工艺性 • 受力和变形分析、结构设计,初步决定形状和尺
寸
• 有限元计算,求出静态刚度和动态特性, 再修改和完善
(一)机床的类型、布局和支承件的形状
1. 机床的类型
(1)以切削为主的中小型机床 (2)以移动件的重力和热应力为主的精密和高精
机械制造装备设计-支撑件导轨
一、支承件的功能和应满足的基本要求
• 支承件——床身、立柱、横梁、摇臂、 底座、箱体和升降台等尺寸及重量较大 的零件(大件)
(一)支承件的功能
• 支承机床各部件,承受切削力、重力 、惯性力、摩擦力等静态力和动态力
• 保证各部件之间的相对位置精度和运 动部件的相对运动轨迹的准确关系。
弯惯性矩和抗扭惯性矩有关。 • 材料和截面积相同而形状不同时,截面惯性矩相
差很大。
(二)支承件的截面形状和选择
1)空心截面的刚度都比实心的大 2)圆(环)形截面的抗扭刚度比方形好,而抗弯
刚度比方形低 3)封闭截面的刚度远远大于开口截面的刚度,特
别是抗扭刚度
(三)支承件肋板和肋条的布置
1)空心截面的刚度都比实心的大 2)圆(环)形截面的抗扭刚度比方形好,而抗弯
1.改善阻尼特性 2.采用新材料制造支承件
四、提高支承件结构性能的措施
(三)提高热稳定性
1.控制温升 2.采用热对称结构 3.采用热补偿装置
第八节 导轨设计
一、导轨的功用和应满足的基本要求
(一)导轨的功用和分类
• 功用:承载和导向 • 在外力作用下,能准确地沿着一定的方向运动 • 动导轨——运动的一方 • 支承导轨——不动的一方 • 只有一个自由度 • 直线或回转运动
滚柱导轨 按滚动体
滚针导轨
3)按结构形式分
开式导轨——依靠外载荷和部件自重,使 两导轨面在全长上保持贴合的导轨
闭式导轨——用压板作为辅助导轨面保证 主导轨面贴合的导轨
(二)导轨应满足的基本要求
• 机床导轨的质量在一定程度上决定了— — 机床的加工精度 工作能力 使用寿命
纵向肋板——主要提高抗弯刚度 横向肋板——主要提高抗扭刚度 斜向肋板——兼有提高抗弯刚度和抗扭刚 度的效果
T型肋板:主要提高水平面抗弯刚度,对提 高垂直面抗弯刚度和抗扭刚度作用不明 显。多用在刚度要求不高的床身上。
C图的肋板在垂直面和水平面的抗弯刚度都 比A图好。
W型布置能较大的提高水平面的抗弯、抗 扭刚度。
铁的牌号应根据导轨的要求选择 • 如果导轨是镶装上去的,或者支承件上没有导轨
,则一般可采用HT150 • 如果支承件由型钢和钢板焊接,则常用Q235AF或
,如果导轨与支承件铸为一体,则铸 铁的牌号应根据导轨的要求选择
• 如果导轨是镶装上去的,或者支承件上没有导轨 ,则一般可采用HT150
• 采用钢筋混凝土可节约大量钢材,降低成本。 但钢筋混凝土支承件的变形、侵蚀、导轨与支 承件连接刚度不足等问题,有待进一步研究解 决。
四、提高支承件结构性能的措施
(一)提高支承件的静刚度和固有频率
根据支承件受力情况合理地选择支承件的材料、截 面形状和尺寸、壁厚,合力地布置肋板和肋条, 提高结构整体和局部的弯曲刚度和扭转刚度。
(二)钢板焊接结构
• 如果支承件由型钢和钢板焊接,则常用Q235AF或 Q275钢
(三)支承件的其它材料
• 预应力钢筋混凝土支承件(主要为床身、立柱、 底座等)近年来有较大的发展。混凝土的比重 是钢的1/3,弹性膜量是钢的1/10~1/15, 阻尼高于铸铁,适合于制造受载均匀,截面积 大、抗振性要求较高的支承件。
• 内部空间可存放切削液、润滑液、液 压油的油箱、电动机
(二)支承件应满足的基本要求基本要求
1)足够的刚度和较高的刚度/重量比
要求在规定的最大载荷作用下,变形量不得 超过一定的数值。
重量占机床总重量的80%以上,应尽量减轻 支承件的重量。
2)较好的动态特性
包括较大的动刚度和阻尼; 与其它部件相配合,使整机的各阶固有频率 不致与激振频率重合而产生共振; 不会发生薄壁振动而产生噪声等。
密机床 (3)重力和切削力必须同时考虑的大型和重型机
床
(一)机床的类型、布局和支承件的形状
2. 机床的布局形式对支承件形状的影响 3. 支承件的形状
箱型类、板块类、梁类
(二)支承件的截面形状和选择
最小重量条件下,最大静刚度 • 支承件主要是承受力矩、扭矩以及弯扭复合载荷 • 自身刚度主要考虑——弯曲刚度和扭转刚度 • 在弯、扭载荷作用下,支承件的变形与截面的抗
D图自由排屑,提高刚度。
肋条——配置与某一内壁上,主要为减小局部变 形和薄壁振动,用来提高支承件的局部刚度
(四)合理选择支承件的壁厚
减轻机床重量,壁厚根据工艺上的可能选择得薄些 。 C =(2L+B+H)/3
三、支承件的材料
• 支承件的重量在机床总重量中占有很大比重,因 此必须合理选择材料。
• 支承件的材料,主要为——铸铁和钢 • 铸铁支承件,如果导轨与支承件铸为一体,则铸
3)应具有较好的热变形特性,使整机的热变 形较小或热变形对加工精度的影响较小
由于摩擦热、切削热等产生热变形和热应力
在铸造、焊接和粗加工过程中,会形成内应 力,使支承件变形。
热变形和内应力都将破坏部件间的相互位置关 系和相对运动轨迹,影响加工精度。
4)应该排屑畅通、吊运安全,并具有良好的 工艺性以便于制造和装配。
导轨可按下列性质分类:
• 1)按工作性质可分为: 主运动导轨、进给运动导轨、调位导轨
• 调位导轨只用于调整部件之间的相对位置,在 加工时没有相对运动
• 例如车床尾架用的导轨
2)按摩擦性质分
滑动导轨
滚动导轨
• 滑动导轨:混合摩擦导轨 边界摩擦导轨 液体动压导轨
按两导轨面间 的摩擦状态
液体静压导轨
• 滚动导轨:滚珠导轨
刚度比方形低 3)封闭截面的刚度远远大于开口截面的刚度,特
别是抗扭刚度
• 在两壁之间起连接作用的内壁 ——肋板 • 肋板功用——把作用于支承件局部地区的载荷
传递给其它壁板,从而使整个支承件各壁板能 比较均匀的承受载荷 • 当支承件不能采用全封闭截面时,常常布置肋 板来提高支承件的自身刚度
肋板布置的三种基本形式
二、支承件的结构设计
• 考虑机床的类型、布局及常用支承件的形状 • 满足机床工作性能的前提下,综合考虑其工艺性 • 受力和变形分析、结构设计,初步决定形状和尺
寸
• 有限元计算,求出静态刚度和动态特性, 再修改和完善
(一)机床的类型、布局和支承件的形状
1. 机床的类型
(1)以切削为主的中小型机床 (2)以移动件的重力和热应力为主的精密和高精
机械制造装备设计-支撑件导轨
一、支承件的功能和应满足的基本要求
• 支承件——床身、立柱、横梁、摇臂、 底座、箱体和升降台等尺寸及重量较大 的零件(大件)
(一)支承件的功能
• 支承机床各部件,承受切削力、重力 、惯性力、摩擦力等静态力和动态力
• 保证各部件之间的相对位置精度和运 动部件的相对运动轨迹的准确关系。
弯惯性矩和抗扭惯性矩有关。 • 材料和截面积相同而形状不同时,截面惯性矩相
差很大。
(二)支承件的截面形状和选择
1)空心截面的刚度都比实心的大 2)圆(环)形截面的抗扭刚度比方形好,而抗弯
刚度比方形低 3)封闭截面的刚度远远大于开口截面的刚度,特
别是抗扭刚度
(三)支承件肋板和肋条的布置
1)空心截面的刚度都比实心的大 2)圆(环)形截面的抗扭刚度比方形好,而抗弯