晶粒度评级图
第3章 奥氏体相变

G均匀
r*
*
2 GV GS
G均匀
16 3 3(GV GS ) 2
物理意义:新相核胚的原子团半径(r)必须大于临界半径(r*),系统才 )的阻碍,新相的核胚才能继续长大,完成形核过 能克服势垒( G均匀 程。否则核胚的原子团将重新散开,形核失败。
非均匀形核
3)残留渗碳体的溶解
1.实验现象: 1) F消失时,组织中的Fe3C还未完全转变 2) 测定后发现A中含碳量低于共析成分0.77% 2.原因: Fe-Fe3C相图上ES线斜度大于GS线,S点不在 CA-F与CA-C中点,而稍偏右。所以A中平均碳浓 度,即(CA-F + CA-C)/2低于S点成分。当F全部转 变为A后,多余的碳即以Fe3C形式存在。
σs=σi+Kyd-1/2 σs -屈服强度,σi-抵抗位错在晶粒中运动的 摩擦阻力,Ky-常数, d-晶粒直径
晶粒度 级别图 1-8级
3.4.1 晶粒度概念及晶粒长大现象
一)晶粒度
设N为放大100倍时每平方英寸in2面积内 的晶粒数,则下式中G即为晶粒度。
N=2
G-1
晶粒越细,G越大。 起始晶粒:加热转变终了时所得的A晶粒 实际晶粒:长大到冷却开始时的A晶粒 本质晶粒:930º C保温3~8小时所得的晶粒 1-4级:本质粗晶粒钢,5-8本质细晶粒钢
3.影响P转变为A的因素
温度 形核率与线长大速度随温度升高 而增加 碳含量:A形成速度随C%增加而增加 原始组织 P中Fe3C片厚度和颗粒大小影 响A形成过程及形成速度. 片状大于颗粒状;片层越小,速度越大 合金元素:改变临界点位置、影响C扩散 速度;形成各种碳化物(K)
奥氏体晶粒长大及其控制

*
起始晶粒度:珠光体刚刚转变成奥氏体 的晶粒大小。 实际晶粒度:热处理后所获得的奥氏体 晶粒的大小。 本质晶粒度:度量钢本身晶粒在930℃ 以下,随温度升高,晶粒长 大的程度。
加热速度愈大,过热度就愈大,即奥氏体实际形成温度就愈高,奥氏体的形核率与长大速度之比值I/G增大(表9.1),所以快速加热时可以获得细小的奥氏体起始晶粒。而且,加热速度愈快,奥氏体起始晶粒就愈细小。
*
表9.1 奥氏体的形核率I、长大速度G 与温度的关系
转变温度 (℃)
形核率I (1/mm3·s)
*
(2)晶界推移阻力
图9.12 晶界移动时与第二相粒子的交互作用示意图
1
2
*
在第二相粒子附近的晶界发生弯曲,导致晶界面积增大,界面能升高。弥散析出的第二相粒子愈细小,粒子附近晶界的弯曲曲率就愈大,晶界面积的增大就愈多,因此界面能的增大也就愈多。这个使系统自由能增加的过程是不可能自发进行的。所以,沉淀析出的第二相粒子的存在是晶界推移的阻力。
9.1.4 奥氏体晶粒长大 及其控制
1.奥氏体晶粒度 2.奥氏体晶粒长大原理 3.影响奥氏体晶粒长大的因素
奥氏体化的目的是获得成分均匀和一定晶粒大小的奥氏体组织。多数情况下希望获得细小的奥氏体晶粒,有时也需要得到较大的奥氏体晶粒。因此,为获得所期望的奥氏体晶粒尺度,必须了解奥氏体晶粒的长大规律,掌握控制奥氏体晶粒度的方法。
*
(4)合金元素的影响
钢中加入适量形成难溶化合物的合金元素如Nb、Ti、Zr、V、Al、Ta等,将强烈地阻碍奥氏体晶粒长大,使奥氏体晶粒粗化温度显著升高。上述合金元素在钢中形成熔点高、稳定性强、不易聚集长大的NbC、NbN、Nb(C,N)、TiC等化合物,它们弥散分布于奥氏体基体中,阻碍晶粒长大,从而保持细小的奥氏体晶粒。
晶粒度评级图

金属平均晶粒度评级图—系列图片I无孪晶晶粒100×00级0级
金属平均晶粒度评级图—系列图片I无孪晶晶粒100×0.5级 1.0级
金属平均晶粒度评级图—系列图片I无孪晶晶粒100×1.5级 2.0级
金属平均晶粒度评级图—系列图片I无孪晶晶粒100×2.5级 3.0级
金属平均晶粒度评级图—系列图片I无孪晶晶粒100×3.5级 4.0级
金属平均晶粒度评级图—系列图片I无孪晶晶粒100×
4.5级
5.0级
金属平均晶粒度评级图—系列图片I无孪晶晶粒100×5.5级 6.0级
金属平均晶粒度评级图—系列图片I无孪晶晶粒100×
6.5级
7.0级
金属平均晶粒度评级图—系列图片I无孪晶晶粒100×7.5级8.0级
金属平均晶粒度评级图—系列图片I无孪晶晶粒100×
8.5级9.0级
金属平均晶粒度评级图—系列图片I无孪晶晶粒100×9.5级10.0级。
常用齿轮钢的晶粒度显示方法
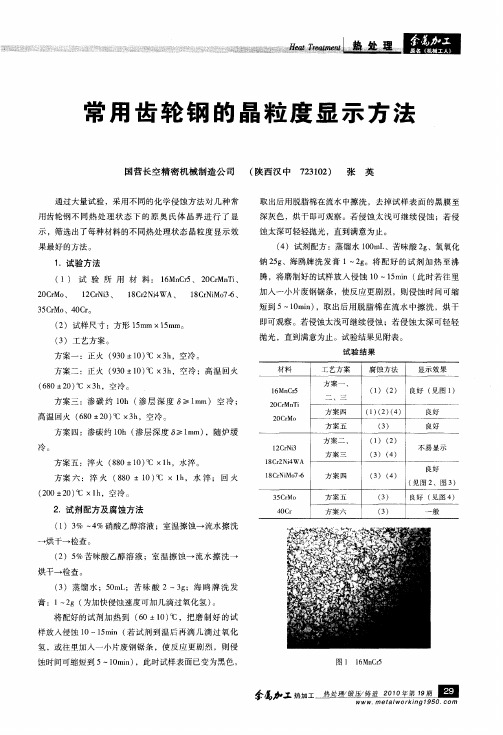
方案 六 :淬 火 ( 8 80±1 o X1 ,水 淬 ;回 火 0) h c
( 0 2 )c×1 ,空冷 。 2 0± 06 3 CMO 5r 4 C 0r
方 案 四 方 案 五 方 案六
( )( ) 3 4 () 3 () 3
抛光 ,直到满意为止。试验结 果见 附表。
试 验 结 果
材 料 1 Mn r 6 C5
2 r n i 0C M T
( )试样尺寸 :方形 1 mlX1 r 2 5 i 5 m。 l a ( )工艺方案 。 3 方案一 :正火 (3 9 0±1 )c× h 0 o 3 ,空冷 。 方 案二 :正火 (3 90±1 ) X3 ,空冷 ;高温 回火 0 ℃ h
常 用 齿 轮 钢 的 晶 粒 度 显 示 方 法
国营长空精密机械制造公 司 ( 陕西汉 中 7 3 0 ) 张 2 12 英
通过大量试验 ,采用不 同的化 学侵蚀方 法对几种 常
取 出后用脱脂棉在流水 中擦洗 ,去掉试样表 面 的黑膜 至
用齿轮钢不 同热 处理 状 态下 的原 奥 氏体 晶界进 行 了显 示 ,筛选出 了每种材料的不同热处 理状态 晶粒度显示 效
用前必须先进行 自身渗碳 ,即使正常生产情 况下 ,停炉 再升温时 ,也应进行炉膛 预渗。这一点至关重要 ,否则
易形成黑 色组织及表面腐 蚀,导致整炉工 件报废 。 另外 ,因乙醇尿素饱 和 溶液 的滴入 经 常堵 塞滴 孔 ,
图3 1C NM 7 8 r i o- 6
管道要经常用铁棍导通 。
用 ,同时减少 [ 、 [ c] N]原子复 合 ,维持较多 的活性
碳原子数 ,且保持 炉 内碳势 和氮 势 , 充 当活性 [ ] 并 C、
ASTME112中文修订版

金属平均晶粒度测定方法引言本标准规定了金属材料平均晶粒度的基本方法。
由于纯粹以晶粒几何图形为基础,与金属和合金本身无关。
因此,这些基本方法也可以用来测量非金属材料中晶粒、晶体和晶胞的平均尺寸。
如果材料的组织形貌非常接近某一个标准系列评级图,可以使用比较法。
测定平均晶粒度常用比较法,也可以用截点法和面积法。
但是,比较法不能用来测量单个晶粒。
1范围1.1 本标准规定了金属组织的平均晶粒度表示及评定的三种方法——比较法、面积法和截点法。
这些方法也适用于晶粒组织形貌与标准系列评级图相似的非金属材料。
这些方法主要适用于单相晶粒组织,但也适用于多相或多组元试样中特定类型组织的晶粒平均尺寸的测量。
1.2 本标准使用晶粒面积、晶粒直径、截线长度的单峰分布来测定式样的平均晶粒度。
这些分布近似正态分布。
本标准的测定方法不适用于双峰分布的晶粒度。
双峰分布的晶粒度参见标准E1181。
测定分布在细小晶粒基体上个别非常粗大的晶粒的方法参见E 930。
1.3本标准的测量方法仅适用平面晶粒度的测量,也就是试样截面显示出的二维晶度;不适用于试样三维晶粒,即立体晶粒尺寸的测量。
1.4 试验可采用与一系列标准晶粒度图谱进行对比的方法或者在简单模板上进行计数的方法。
利用半自动计数仪或自动图象分析仪测定晶粒尺寸的方法参见E 1382。
1.5本标准仅作为推荐性试验方法,它不能确定受检材料是否接收或适合使用的范围。
1.6 测量数值应用SI单位表示。
等同的英寸-英镑数值,如需标出,应在括号中列出近似值.1.7 本标准没有列出所有的安全事项,只是一些使用的注意事项。
本标准的使用者在使用前应掌握较合适的安全健康的操作规范和使用时限制的规章制度。
1.8 章节的顺序如下:2、参考文献2.1ASTM标准E3 金相试样的制备E7 金相学相关术语E407 金属和合金浅腐蚀的操作E562计数法计算体积分数的方法E691 通过多个实验室比较决定测试方法的精确度的方法E883 反射光显微照相指南E930 截面上最大晶粒的评估方法(ALA晶粒尺寸)E1181双峰分布的晶粒度测试方法E1382 半自动或全自动图像分析平均晶粒度方法2.2 ASTM附件2.2.1 参见附录X23术语3.1 定义-本标准采用的专业术语定义参照E73.2 本标准中特定术语的定义:3.2.1 ASTM晶粒度——G,通常定义如公式(1)N AE=2G-1 (1)N AE为100倍下每平方英寸(645.16mm2)面积内包含的晶粒个数,相当于1倍下每平方毫米面积内包含的晶粒个数乘以15.5倍。
第二节 晶粒度检验

进行研磨和抛光,尽可能完善显示出氧化层奥氏体晶粒。
腐蚀:硝酸酒精,但为了显示清晰,可用15℅盐酸酒精 溶液进行浸蚀。
3、网状铁素体法
C%在0.25%~0.60%碳素钢和合金钢,除 非另有规定,一般在C%<0.35%钢的试样在 900℃±10℃加热, C%>0.35%钢的试样在 860℃±10℃加热,至少保温30min,然后空冷 或水冷。
4)求出晶粒的平均截距 5)按下式换算相应的晶粒度级别:
直线截点法
在晶粒图上,采用一条或数条直线组成测量网格, 选择适当的测量网格长度和放大倍数,以保证最 少能截获约50个截点,根据测量网格截获的截 点数来确定晶粒数。
截点计算;测量线段终点不是截点不予计算;终点 正好接触到晶界时,计为0.5个截点;测量线段 与晶界相切时,计为1个截点,明显地与三个晶 粒汇合点重合时计为1.5个截点。
n=2N-1
若n为放大100倍时每1mm2面积内的晶粒数则
n=2N+3
晶粒越细,n越大,N也越大
一般将N小于4的称为粗晶粒,5~8称为细晶粒,8以上称 为超细晶粒。
起始晶粒度:加热转变终了时所得的奥氏体晶粒的大小。
实际晶粒度:实际加热条件下得到的奥氏体晶粒度或从钢 材上截取试样所测得的晶粒大小) 本质晶粒度:加热(930±10)℃、保温3~8h,冷却,与 标准晶粒度等级图比较,确定的试样的晶粒度,本质晶粒 度代表钢的晶粒长大倾向
(1)对少量的第二相的颗粒测定时可忽略不计, 当单相物质结构处理;
(2)第二相的颗粒与基体相当,或第二相质点 数量少而尺寸又小,且位于初生晶粒的晶界 处,可用比较法;
(3)如果基体晶粒边界清晰可见,且第二相质 点主要存在于基体晶粒之间而不在晶粒内时, 用面积法或截点法测定。
实验一 钢的奥氏体晶粒度的测定及评级方法

实验一钢的奥氏体晶粒度的显示与测定一.实验目的1.熟悉钢的奥氏体晶粒度的显示与测定的基本方法。
学习利用物镜测微尺标定目镜测微尺和毛玻璃投影屏刻度格值。
通过它们间的关系到确定显微镜物镜和显微镜的线放大倍数。
2.熟悉钢在加热时,加热温度和保温时间对奥氏体晶粒大小的影响。
3.测定钢的实际晶粒度。
用直接计算法和弦计算法测量晶粒大小。
用比较法评定晶粒度级别。
二.实验原理金属及合金的晶粒大小与金属材料的机械性能、工艺性能及物理性能有密切的关系。
细晶粒金属的材料的机械性能、工艺性能均比较好,它的冲击韧性和强度都较高,在热处理和淬火时不易变形和开裂。
粒晶粒金属材料的机械性能和工艺性能都比较差,然而粗晶粒金属材料在某些特殊需要的情况下也被加以使用,如永磁合金铸件和燃汽轮机叶片希望得到按一定方向生长的粗大柱状晶,以改善其磁性能和耐热性能。
硅钢片也希望具有一定位向的粗晶,以便在某一方向获得高导磁率。
金属材料的晶粒大小与浇铸工艺、冷热加工变形程度和退火温度等有关。
晶粒尺寸的测定可用直测计算法。
掌握了这种方法也可对其它组织单元长度进行测定,如铸铁中石墨颗粒的直径;脱碳层深度的测定等。
某些具有晶粒度评定标准的材料,可通过与标准图片对比进行评定。
这种方法称为比较法。
1.奥氏体晶粒度的显示钢在临界温度以上直接测量奥氏体晶粒大小比较困难的,而奥氏体在冷却过程中将发生相变。
一般采用间接的方法显示其原奥氏体晶界,以测定奥氏体晶粒大小。
根据GB6394-86规(4)网状渗碳体法适用于含碳量大于1.0%的过共析钢的奥氏体晶粒度。
方法是:将试样在930±10℃(或特定的温度)下加热保温40min以上(或特定的时间)后以缓慢的速度冷却冷却到600℃,在过共析钢的奥氏体晶界上析出网状渗碳体,以此来显示奥氏体晶粒形貌与大小。
经上述热处理的试样抛光后,应使用硝酸或苦味酸酒精溶液腐蚀。
图1 过共析钢的状渗碳体(×100)在经上述方法之一制备的金相试样上,即可进行奥氏体晶粒度的测定。
晶粒度评级

表1 常用材料使用的标准系列图片
系列图片号
Ⅰ
适
用
范
围
1)铁素体钢的A晶粒(用氧化法、直接淬硬法、F网法、 铁素体钢的A晶粒(用氧化法、直接淬硬法、 网法、 Fe3C网法及其他方法显示 晶粒) 网法及其他方法显示A Fe3C网法及其他方法显示A晶粒) 2)铁素体钢的铁素体晶粒 镁和镁合金、锌和锌合金、 3)铝、镁和镁合金、锌和锌合金、超强合金 1)奥氏体钢的A晶粒(有孪晶的) 奥氏体钢的A晶粒(有孪晶的) 铁素体钢的铁素体晶粒有孪晶的) 2)铁素体钢的铁素体晶粒有孪晶的) 镁和镁合金、镍和镍合金、锌和锌合金、 3)镁和镁合金、镍和镍合金、锌和锌合金、超强合金 铜和铜合金 1)渗碳钢的A晶粒 渗碳钢的A 奥氏体钢的A晶粒(无孪晶的) 2)奥氏体钢的A晶粒(无孪晶的)
F钢与A钢的奥氏体晶粒度 钢与A 形成及显示
对于铁素体钢
奥氏体晶粒的显示方法: 奥氏体晶粒的显示方法:
国家标准GB/T6394-2002《 国家标准GB/T6394-2002《金属平均晶粒 GB/T6394 度测定法》规定可使用渗碳法、氧化法、 度测定法》规定可使用渗碳法、氧化法、 铁素体网法、渗碳体网法、直接淬硬法、 铁素体网法、渗碳体网法、直接淬硬法、 网状珠光体法、相关法、模拟渗碳法等。 网状珠光体法、相关法、模拟渗碳法等。
晶粒数N的计算: 晶粒数N的计算: • 用5000mm2的圆形网置于晶粒图形上; 的圆形网置于晶粒图形上; • 选放大倍数M使网内晶粒数为50个; 选放大倍数M使网内晶粒数为50 50个 • 计算落入数N内和切割数N交,该面积内的晶粒数N 计算落入数N 和切割数N 该面积内的晶粒数N /2) 为: N= N内+( N交/2)-1 计算试样检测面上每mm 内晶粒数n 计算试样检测面上每mm2内晶粒数n: n = M2×N/A 式中: 式中:M—所用的放大倍数 所用的放大倍数 放大M 面积为A N—放大M时,面积为A的网格内晶粒计数 放大 晶粒度级别数: 928lgn晶粒度级别数:G=3.321 928lgn-2.954
钢的奥氏体晶粒度与加热温度的关系(可编辑)
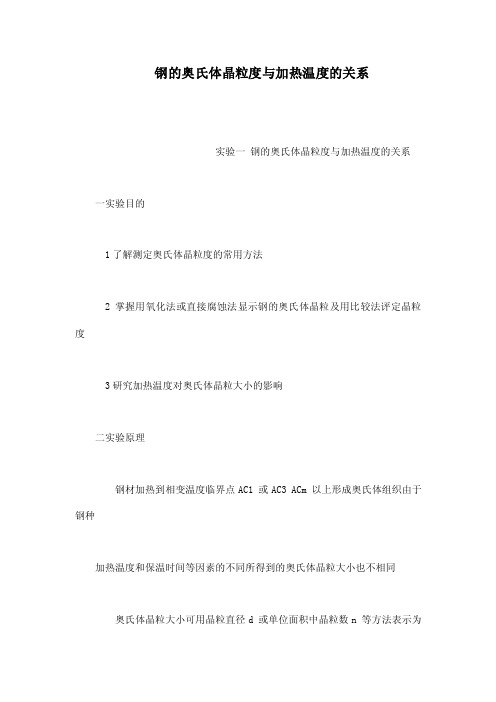
钢的奥氏体晶粒度与加热温度的关系实验一钢的奥氏体晶粒度与加热温度的关系一实验目的1了解测定奥氏体晶粒度的常用方法2 掌握用氧化法或直接腐蚀法显示钢的奥氏体晶粒及用比较法评定晶粒度3研究加热温度对奥氏体晶粒大小的影响二实验原理钢材加热到相变温度临界点AC1 或AC3 ACm 以上形成奥氏体组织由于钢种加热温度和保温时间等因素的不同所得到的奥氏体晶粒大小也不相同奥氏体晶粒大小可用晶粒直径d 或单位面积中晶粒数n 等方法表示为了方便生产上多采用晶粒度来表示晶粒大小奥氏体晶粒的级别G 与晶粒大小的关系是G-1n 22式中 n放大100 倍时每平方英寸645mm 面积内的平均晶粒数目根据奥氏体形成过程和晶粒长大的不同情况奥氏体晶粒度分为起始晶粒度实际晶粒度和本质晶粒度起始晶粒度系指奥氏体刚形成时晶粒的大小实际晶粒度是钢材在某一具体热处理加热条件下所得到的奥氏体晶粒大小而本质晶粒度则是表示晶粒大小的一种尺度对钢来说如不特别指明晶粒度一般是指奥氏体化后的实际晶粒度而实际晶粒度主要受加热温度和保温时间的影响加热温度越高保温时间越长奥氏体晶粒越易长大粗大生产实践表明钢材加热时形成的奥氏体晶粒大小对冷却转变及对钢的力学性能与工艺性能均有很大影响例如粗大的奥氏体晶粒冷却后获得粗大的转变产物这种产物的塑性与韧性比细小的奥氏体晶粒转变产物差而且其屈服点亦较细小奥氏体晶粒转变者为低如果奥氏体晶粒过分粗大钢件在淬火时还易于变形和开裂高碳钢加热时如形成粗大的奥氏体晶粒淬火后残余奥氏体将增多致使刀具的硬度和耐磨性能降低另外细晶粒度的板材易于冲压加工可获得表面光洁的冲压件而粗晶粒的板材冲压时容易开裂冲压成型后的表面亦比较粗糙晶粒度是表示材料性能的重要指标是评定钢材质量的主要依据之一所以生产中常需测定奥氏体晶粒大小以保证产品质量钢中晶粒度的测定分为本质晶粒度和实际晶粒度的测定晶粒度的测定包括两个步骤即晶粒的显示和晶粒尺寸的测定或评级晶粒的显示是晶粒测定的先决条件常用的显示方法如下一奥氏体晶粒的显示1奥氏体本质晶粒的显示奥氏体本质晶粒度是指在930 ±10℃保温一定时间后的奥氏体晶粒大小本质晶粒度可以反映奥氏体晶粒长大倾向根据它能正确估计零件经过热处理后晶粒的大小从而评定零件的力学性能故在生产中常需要测定奥氏体本质晶粒度由于奥氏体在冷却过程中可能已发生相变冷至室温时已不再是奥氏体组织为显示处原奥氏体晶界需采取以下一些方法1 渗碳法渗碳体显示奥氏体晶粒广泛应用于渗碳钢或含碳量≤06的其它类型的钢种本法系采用渗碳热处理方法提高试样表面的含碳量渗碳后的试样表层为过共析成分试样在渗碳后缓慢冷却过程中先共析的渗碳体优先沿原奥氏体晶粒边界析出勾划出了奥氏体晶粒1为了在黑灰色珠光体组织的背景上显露出亮的碳化物渗碳体网常选用下列浸蚀剂腐蚀试样13~4硝酸酒精溶液晶界呈现白色网状碳化物2 5苦味酸酒精溶液晶界亦呈现白色网状碳化物3 沸腾的碱性苦味酸钠水溶液苦味酸2g氢氧化钠25g水100mL腐蚀时间为10~25min 晶界网状碳化物呈现黑色本方法对碳化物形成元素过多的钢由于难以形成完整的碳化物网络故不宜采用2 氧化法将预测晶粒度的钢试样加热到奥氏体状态保温一定时间使试样表面受到氧化由于晶界比晶内具有根大的化学活性故奥氏体晶界较晶粒内部更易于氧化适当地保温可使晶界发生氧化而晶粒内部不受影响故使奥氏体晶粒得以清晰地显示氧化法主要有气氛氧化法和熔盐氧化腐蚀法其中以气氛氧化法较为简便应用最多1气氛氧化法将试样两段面先用细砂纸磨光和抛光制成金相试样然后将试样的抛光面向上装入预先加热到860 ±10℃的具有氧化性气氛炉中普通空气炉加热并在该温度保温 1h试样在加热和保温过程中暴露氧化待试样保温后出炉水冷水冷是为了避免铁素体呈块状析出以防铁素体晶界与奥氏体晶界相混淆造成误评再将水冷后的试样仔细研磨和抛光使晶粒表面的氧化膜几乎完全磨去而晶界处的氧化物只部分被磨掉在显微镜下借助晶界处的黑色氧化物即可显示出高温时的奥氏体晶粒大小如用15盐酸酒精溶液或2~4硝酸酒精溶液浸蚀试样磨面则所形成的黑灰色网络将显露得到更为清楚选择试样的奥氏体晶界轻微氧化或轻度脱碳区域观察晶粒度时沿氧化了的奥氏体晶界形成槽形凹沟可在显微镜下清晰地聚焦成线状它与真实的奥氏体本质晶粒度最为接近奥氏体晶粒显示的结果是否清晰准确关键在于试样冷却后的研磨与抛光研磨过少只能看到氧化膜而看不到晶界研磨过多则可能将氧化晶界全部磨掉这样就无法观测奥氏体晶粒大小因此应严格控制研磨量此法的缺点是所显示的往往为保温初期的奥氏体晶粒大小2 熔盐氧化腐蚀法将制备好的金相试样放入预先加热至 930 ±10℃不氧化的碳酸钠盐浴硼砂槽或其它盐浴中加热保温3h 后再转入成分为BaCl2 13NaCl 13CaCl 13 重量比未经脱氧的盐浴中进行腐蚀腐蚀温度为930 ±10℃腐蚀时间为2~5min腐蚀后的试样在煤油后的试样在煤油中冷却然后用冷水洗净酒精冲洗吹干经适宜的抛光在显微镜下放大100 倍进行观察如氧化网络不清晰时可用4苦味酸酒精溶液浸蚀氧化法适用于显示各种钢的奥氏体本质晶粒度尤以中碳钢及中碳合金钢为宜3 网状铁素体法此方法仅适用于亚共析钢对中碳调质碳素钢较为合适而对某些亚共析合金钢即使在很小的冷却速度下铁素体也不呈网状故此法不宜选用将欲测试样加热含C≤035 时为900 ±10℃保温300min当C>035 时为860±10℃保温30min 水冷或空冷在冷却过程中当通过临界温度区域时先共析铁素体优先沿奥氏体晶粒边界析出呈网状分布晶粒内部为珠光体除去试样表面层根据围绕在奥氏体晶粒周围的网状铁素体测定钢的本质晶粒度对接近共析成分的亚共析钢在奥氏体化后可预先缓慢冷却至 700~730℃等温保持十几分钟后在空冷到室温也可得到明显的铁素体网网状铁素体法显示奥氏体晶粒的浸蚀剂可采用3~4硝酸酒精溶液或苦味酸酒精溶液腐蚀后晶界呈白色网状铁素体冷却速度是决定铁素体网勾划出奥氏体晶界质量好坏的关键如果冷却速度过快铁素体网未能布满奥氏体晶界易产生奥氏体晶粒过大的错觉若冷却太慢铁素体堆积成块状也难以显示出奥氏体晶界所以对不同钢种的冷却速度应通过多次试验选择确定24 网状渗碳体法适用于过共析钢的奥氏体晶粒的显示将试样加热到820±10℃保温30~60min 后炉冷到600℃冷却速度约80~100℃h 出炉以保证渗碳体呈网状分布除去试样表面氧化层制成金相试样用3~4硝酸酒精溶液或苦味酸酒精溶液浸蚀此时晶界网状碳化物呈现白色根据碳化物沿奥氏体晶界析出的网络测定钢的奥氏体晶粒度晶粒内部是珠光体5 网状珠光体法一端淬火法适用于淬透性较低的碳素钢和低合金钢以及不能获得完整铁素体或渗碳体网的钢如含碳量接近共析成分的钢实验时可采用Φ20mm ×40mm 的圆柱形试样现将试样加热到900 ±10℃保温1h然后自炉中取出一端淬入水中冷却约入水13~25 长度冷却时不要上下运动只可水平移动试样另一端在空气中冷却由于试样从下端之上端冷却速度逐渐减小因而沿轴向的组织依次由马氏体向珠光体过渡经过这样处理的试样沿纵向磨去约2~3mm 厚以后制成金相试样在淬硬与未淬硬的过渡区则可以找到黑色屈氏体优先沿奥氏体晶界析出的区域在屈氏体网所包围的内部则为灰白色的马氏体根据黑色屈氏体网可以测定钢的晶粒度所用浸蚀剂与网状铁素体法相同6 化学试剂腐蚀法此方法分为直接腐蚀法和马氏体腐蚀法1直接腐蚀法将试样加热到900 ±10℃保温1h 后水冷淬火获得马氏体和贝氏体组织有的钢种还需经过一定温度的回火除去试样表面脱碳层和氧化层制成金相试样选用具有强烈选择性腐蚀的腐蚀剂浸蚀使原奥氏体组织晶界变黑而基体组织腐蚀轻微从而直接显现奥氏体晶粒本法适用于合金化高的能直接淬硬的钢如高淬透性的铬镍钼钢等直接显现奥氏体晶界的腐蚀剂成分与使用条件是①含有05~1烷基苯碘酸钠 100mL 饱和苦味酸水溶液亦可用合成洗衣粉代替烷基苯磺酸钠浸蚀时间依温度不同20~70℃可选用05min 至3h由试验确定如再向此腐蚀剂中加少量医用消毒剂新洁尔灭则能更好控制腐蚀使样品更加清晰②含有 01~015g 十二醇硫酸钠的 100mL 饱和苦味酸水溶液加热到30℃浸蚀约100min 即可上述两种腐蚀剂都可抑制马氏体组织出现促使奥氏体晶界的显示采用直接腐蚀法显示奥氏体晶粒的常用钢种热处理工艺列于表1-1表1-1 直接显示奥氏体晶粒的热处理工艺钢号淬火工艺回火工艺12CrNi3A 930℃保温15~3h 水冷不经回火12Cr2Ni4A20CrNi3A40Cr 或45Cr60 碳钢38CrMoAlA 930℃保温15~3h 水冷 200~250 ℃保温15~30min 空冷18Cr2Ni4WA 4000 ℃保温30min 空冷40CrNiMoA 930℃保温15~3h 油冷不经回火18CrMnTi38CrA30CrMnSiA30CrMnSiNi2A 930℃保温15~3h 水冷 500℃保温300min 空冷30CrMnNi2MoA 600℃保温300min 空冷32 马氏体腐蚀法适用于淬火是得到马氏体的钢先将试样加热到930℃保温3h 后淬火得到马氏体然后再进行150~250℃15min 短时间回火以增加衬度选用适当腐蚀剂浸蚀由于原始奥氏体各晶粒位向不同则各晶粒间马氏体被腐蚀的深浅亦不同借此衬度颜色差异而显示出奥氏体晶粒大小为得到清晰的组织可重复进行抛光和腐蚀此法腐蚀剂可用1g 苦味酸5mL 盐酸100mL 酒精或 1g 氯化铁15mL 盐酸100mL酒精马氏体腐蚀法对粗大奥氏体晶粒较为有效但对细晶粒奥氏体以及钢中存在带状和树枝状偏析腐蚀时会出现混杂图形影响正确测定另外还有真空法高温金相法和氢气脱碳法等但因测试条件所限尚未普遍应用如选用时可参阅有关资料2实际晶粒度的显示测定实际晶粒度时试样直接在交货状态的钢材或零件上切取在切取及制备试样过程中应避免冷热加工的影响试样一般不经任何预先热处理直接测定制备好的试样用适合的腐蚀剂浸蚀而显示晶粒但这种方法因钢的种类化学成分及状态的不同其效果亦有所不同应根据试验实践选择确定对结构钢淬火和调质状态的原奥氏体晶粒的显示常用的腐蚀剂为1 饱和苦味酸水溶液2 结晶苦味酸4g 水100mL加热至沸腾浸蚀时间约15~20s3 饱和苦味酸水溶液海鸥牌洗净剂混合试剂饱和苦味酸水溶液100mL 加海鸥牌洗净剂1g4 饱和苦味酸水溶液加少量新洁尔灭5 10苦味酸乙醚溶液加盐酸1~2 mL对于结构钢在正火和退火后还常测定其铁素体晶粒度其方法是将试样研磨抛光后以5的硝酸酒精溶液腐蚀约15s 后进行观察并与铁素体标准级别图相比较来评定晶粒度对于大多数钢种淬火回火态的原奥氏晶粒的显示以苦味酸为基的试剂较适宜试剂成分为饱和苦味酸水溶液 100mL洗净剂10mL酸微量对不同钢种和不同热处理状态的原奥氏体晶粒的显示只要适当改换微量酸的种类盐酸硝酸和磷酸等和调整微量酸的加入量5~10 滴就可获得良好的效果高速钢淬火后一般均需测定奥氏体晶粒度以间接考察马氏体针的粗细作为判定淬火加热温度高低和工具热处理质量的主要依据从而控制合适的淬火温度另外分析高速钢成品刀具或进行缺陷分析时还需要检验回火后的晶粒度高速钢奥氏体晶界可用4硝酸酒精溶液或表 1-2 所列试剂浸蚀显示然后按晶粒度评级标准图依不同产品和材料确定不同的晶粒度要求表1-2 高速钢晶粒显示试剂成分编号饱和苦味酸水溶液浓硝酸浓盐酸乙醇甲醇海鸥洗净剂Ⅰ 15 1 25 50Ⅱ10 30 595 05Ⅲ 20 10 30 40注Ⅰ号试剂可用以显示淬火回火后的晶界和马氏体形态Ⅱ号试剂可用以显示淬火回4火后的晶界Ⅲ号试剂可用以显示淬火回火后的晶界深腐蚀可显示马氏体形态如果切取及制备试样借腐蚀直接观察难以分辨晶粒边界无法测定原奥氏体晶粒大小时试样可经适当热处理后再进行测定具体试验方法可按有关规定进行二奥氏体晶粒度的评定奥氏体晶粒度的评定有比较法和截点法两种一般多采用比较法1比较法比较法评定晶粒大小是通过与标准评级图相比较来确定晶粒度级别的图1-1 是钢的晶粒度标准级别图选用此法测定晶粒度时是先将制备好的试样在放大100 倍的显微镜下全面观察晶粒然后选择晶粒度具有代表性的视场与标准级别图比较当二者大小相同时试样的晶粒度就是标准级别图上所标定的级别如试样晶粒大小不均匀时若占优势晶粒所占面积不少于视场的 90时则可记录些一种晶粒的级别数否则应用不同级别来表示该钢的晶粒度其中一个级别代表占优势的晶粒级别例如8 级75 4 级25 等当钢的晶粒过大或过小而用100 倍的放大倍数不方便时可改用其它放大倍数观察和评定然后按照表1-3 的关系换算成100 倍下的标准级别表1-3 常用放大倍数下晶粒度级别数间关系表图像的放与标准评级图编号等同图像的晶粒度级别大倍数 No1 No2 No3 No4 No5 No6 No7 No8 No9No1025 -6 -2 -1 0 1 8 3 4 5 650 -1 0 1 2 3 4 7 6 7 8100 1 2 3 4 5 6 5 8 9 10200 3 4 5 6 7 8 9 10 11 12400 5 6 7 8 9 10 11 12 13 14800 7 8 9 10 11 12 13 14 15 16钢的晶粒度标准评级是将钢中晶粒度分为8 级其中1~4 级的属粗晶粒5~8 级的为细晶粒8 级以上称为超细晶粒比较法评定晶粒度简便迅速但不够准确2 截点法当晶粒度测量准确性要求较高或晶粒为椭圆形时一般采用截点法1 等轴晶粒计算法当欲测定的奥氏体晶粒基本上是等轴时可先进行初步观察以确定晶粒的均匀程度然后选择有代表性的部位和适合的放大倍数测定时先用100 倍观察当晶粒过大或过小时可适当缩小或放大显微镜倍数以在80mm 视场直径内不少于50 个晶粒为限再将所选定部位的图像投影在毛玻璃上计算与一条直线相交截的晶粒数目截点数直线要有足够长度L 以使与直线相交截的截点数目不少于 10 个计算时直线端部未被完全交截的晶粒应以一个晶粒计算之选择三条以上不同部位的直线来计算相截的截点数用相截的截点总数Z 除所选用的直线总长度实际长度以mm 计得出弦的平均长度a mm 再以弦的平均长度值根据晶粒级别对照表便可确定钢的晶粒度弦的平均长度为nLdZ Z Z M1 2 35式中M显微镜的放大倍数截点法也可在带有目镜测微尺的显微镜下通过平行移动视场直接观察计数一般也是测Z 个晶粒的总长度再求弦的平均长度a2 非等轴晶粒计算法沿试样的三轴线分别计算出各轴线方向每 1mm 长度的平均节点数量每一轴线方向的平均截点数必须在不少于三条直线下求得3由试样的三个轴线方向得出每1mm 长度的平均截点数量值按下式计算出每 1mm 内平均截点数N 07n n n纵横法3式中 n每1mm 内平均截点数n 纵纵向上每1mm 长度平均截点数n 横横向上每 1mm 长度平均截点数n 法横向上每 1mm 长度平均截点数07晶粒扁圆度系数由上式计算出n 值根据晶粒级别对照表确定钢的晶粒度三实验设备及材料根据实验所采用的测定奥氏体晶粒度的方法选用所需要的设备和材料 1中温和高温热处理加热炉2 金相显微镜配有目镜测微尺3制备金相试样所需物品砂轮机抛光机砂纸腐蚀剂2~4硝酸酒精溶液或饱和苦味酸水溶液等4 晶粒度标准级别图5试验钢材20CrNi3A 40Cr 45 钢或T8T12CrWMn 等钢试样尺寸圆形试样Φ10~20mm ×15mm或矩形试样10mm×10mm×20mm6图1-1 晶粒度标准级别图四实验内容及步骤采用氧化法或直接腐蚀法显示钢的奥氏体晶粒并用比较法或计算法评定晶粒度级别同时验证加热温度对奥氏体晶粒大小的影响实验步骤如下一分组试验人员按不同加热温度分成若干组试样的加热温度为850℃900℃930℃950℃1000℃1100℃等二试样奥氏体晶粒的显示进行测定奥氏体晶粒度时先选用下列一种方法显示出奥氏体晶粒1氧化法1 每人取试样一块将其两端面研磨并抛光制成金相磨片2 将制备好的试样分别放置于加热到上述规定温度的热处理炉中试样磨面向上并应使加热和氧化均匀一致试样在指定温度保温30min 后取出放入水中冷却3 将冷却后的试样磨面在 04 号砂纸上仔细研磨待磨面磨至大部分发亮时进行抛光为找到一个合适的评级区域可将试样研磨抛光成一个倾斜面10o~15o有时还可配合显微镜观察控制研磨量4 试样抛光后若晶界显示不清晰时可采用浸蚀剂将试样磨面适度浸蚀便可清晰地显示出奥氏体晶界网络2直接腐蚀法1 选用20CrNi3A 或40Cr 等钢制成Φ10mm×10~20mm 圆形或矩形试样2 先将试样放入规定温度的热处理炉中加热加热到温后保温 30min 然后迅速淬入水中冷却以获得马氏体组织3 淬火后的试样磨去脱碳层制成金相试样选用含有 05~1烷基苯磺酸盐的7100mL 苦味酸饱和溶液等腐蚀剂浸蚀由于晶粒边界被腐蚀变黑依次测定奥氏体晶粒度腐蚀时间根据试验条件经试验确定配置腐蚀剂时应煮沸和充分溶解4 为获得更清晰光亮的组织试样可经二次或三次腐蚀抛光重复进行或向腐蚀剂中加少量新结尔灭或将腐蚀剂加热到50~60℃后腐蚀均可3网状铁素体法采用网状铁素体显示亚共析钢的奥氏体晶粒其热处理条件与氧化法相同但是试样预先不需研磨在加热过程中应防止氧化冷却速度应依次不同钢种恰当选择通常对低碳钢可选用油冷中碳钢选用空冷中碳合金钢选炉冷三评级待奥氏体晶粒显示后即可根据试验条件和需要采用比较法或计算法评定试验钢材试样奥氏体晶粒度级别五实验报告要求1写出对实验目的及所选用奥氏体晶粒显示和评级方法原理的简要叙述2 记录及画表格列出全组或全班实验结果并确定本实验用钢奥氏体晶粒度级别3绘出实验用钢或不同实验用钢加热温度与奥氏体晶粒长大关系曲线或比较不同实验用钢奥氏体晶粒长大的倾向性并说明加热温度对奥氏体晶粒大小的影响4 实验结果的分析讨论8实验二钢的淬透性一实验目的1了解钢的淬透性测定方法2 掌握用末端淬透性试验法测定钢的淬透性3研究合金元素等对钢的淬透性的影响二实验原理钢的淬透性是结构钢与工具钢的重要热处理工艺性能之一钢的淬透性对钢材的组织及性能有着十分重要的影响因而钢的淬透性亦是机械零件设计时选择钢种和生产上制定热处理工艺的主要依据之一为了合理地选择和使用工业用钢以及正确地进行钢的热处理对钢的淬透性进行测定和了解具有很大的实际意义一淬透性的本质与评定钢的淬透性也称可淬性是指钢在淬火时能够获得马氏体的能力它是钢材本身固有的一个属性它主要与钢的过冷奥氏体稳定性或钢的临界淬火冷却速度有关淬火是最常用的一种热处理工艺对结构钢和工具钢来说淬火是为了获得马氏体组织零件淬火时表面冷却快愈向心部冷却愈慢如果中心点的冷却速度达到或超过该钢种的临界淬火速度则钢件整个界面均可得到马氏体组织即钢件被淬透而当心部冷却速度小于临界淬火速度时则将在心部出现非马氏体称为未淬透在未淬透的情况下全淬成马氏体的区域就是淬硬层或淬透层钢件经淬火后一般从表面到心部一定深度均可获得马氏体组织这种马氏体组织的深度通常称为淬透层深度或淬硬层深度钢的淬透性反映了钢在淬火时获得马氏体的能力因此通常用标准尺寸试样在一定条件下淬火而得到的淬硬层深度h 或全部淬透的最大直径DC 来表示淬透性大小然而由于不同钢种的淬透性不同故其淬硬层深度以及能淬透的最大直径也不同淬硬层深度及直径愈大表面该钢种的淬透性愈高在实际的淬火钢件中由于从表面到中心各个部位的冷却速度不同因而各部位的组织和性能也就不同从表面全部马氏体组织开始向内依次为屈氏体索氏体珠光体甚至在心部出现铁素体此时显然应以全部马氏体组织或包含有很少量残余奥氏体组织层的深度作为判定淬透性的标准但是实际上当马氏体组织中含有 5~10非马氏体组织时是很难准确分辨出来的在硬度上亦无法测量出来因此现多采用由表面至半马氏体组织即50马氏体和50非马氏体组成的距离为淬透层深度并以此深度作为判定淬透性的标准这是因为半马氏体区域硬度变化显著很容易测量在酸蚀的断面上呈现出明显的明暗分界面见图2-1因此可以认为淬火后的马氏体组织大于50的部分即是被淬透的半马氏体组织的硬度主要与含碳量有关如图2-2 所示实践证明对碳素钢和不具有复杂奥氏体等温转变曲线的低合金钢及中合金钢采用半马氏体作为判定淬透性的标准是没有重大误差的但近年来贾查克Jatezak 等认为在淬火钢中存在 50的非马氏体组织与。
astm 9级 晶粒度 -回复

astm 9级晶粒度-回复ASTM 9级晶粒度简介及其应用ASTM 9级晶粒度是一种用于评估金属材料晶粒尺寸的标准方法,该方法由美国材料和试验协会(ASTM)制定。
晶粒度是指金属材料中晶粒的尺寸和形状的特性,它对金属的力学性能、热处理效果和耐腐蚀性能等都具有重要影响。
在工程领域中,准确评估晶粒度对于确定材料的可靠性和适用性至关重要。
ASTM 9级晶粒度的评估方法是通过显微镜观察金属镜面试样的晶粒结构,然后利用一组标准比例图来确定晶粒级别。
这个评估方法的结果通常由两个数字组成:第一个数字表示观察到的晶粒的最大尺寸,第二个数字表示晶粒的数量级。
例如,一个评估结果为9/10的样品意味着晶粒的最大尺寸与标准比例图上的9级相匹配,而晶粒的数量级与标准比例图上的10级相匹配。
ASTM 9级晶粒度方法的应用十分广泛。
在金属材料开发和生产中,评估晶粒度可以帮助确定合适的热处理参数和工艺路线,从而实现理想的材料性能。
晶粒度的评估也可以用于质量控制和产品认证,确保金属制品的质量符合标准要求。
此外,晶粒度还与材料的耐腐蚀性能有关,评估晶粒度可以帮助预测材料在特定环境条件下的腐蚀行为。
实施ASTM 9级晶粒度评估方法需要一定的步骤。
首先,要准备好金属样品,并进行必要的金相制备,例如切割、研磨和腐蚀处理。
然后,将样品放置在显微镜下进行观察,并使用合适的放大倍数以确保能够清晰地看到晶粒结构。
接下来,使用标准比例图与观察到的晶粒进行比较,确定晶粒级别。
最后,记录评估结果,并根据需要进行后续分析和处理。
尽管ASTM 9级晶粒度方法是一种常用的评估方法,但也存在一些局限性。
首先,这种方法对于复杂材料的晶粒结构可能不太适用,因为标准比例图中只包含了有限的晶粒类型。
其次,评估结果受到观察者主观判断的影响,可能存在一定的主观性。
因此,在实施这种评估方法时,需要经过专业培训的人员进行观察和判断,以确保评估结果的准确性和一致性。
总结来说,ASTM 9级晶粒度是一种用于评估金属材料晶粒尺寸的标准方法。
晶粒度图片

45H-200X-11 截点法公式:L= L/M.PL:所使用的测量线段长度(mm), M: 观测用的放大倍数P: 测量直线上的截点L: 测量面上晶粒截距的平均值(查表平均截距一栏)截点的计算: 计算截点时注意:1测量线段终点不是截点不予计算;2 终点正好接触到晶界时,计为0.5个截点;3 测量线段与晶界相切时, 计为1个截点;4 明显的与三个晶粒汇合点重合时,计为1.5个截点;5 在不规则晶粒形状下,测量线在同一晶粒边界不同部位产生的两个截点;后又伸入形成新的截点, 计算截点时应包括新的截点.2 平均晶粒度级别数G的计算:G=6.643856lg(M.P/L) –3.28845H-200X-21 截点法公式:L= L/M.PL:所使用的测量线段长度(mm), M: 观测用的放大倍数P: 测量直线上的截点数L: 测量面上晶粒截距的平均值(查表平均截距)截点的计算: 计算截点时注意:1测量线段终点不是截点不予计算;2 终点正好接触到晶界时,计为0.5个截点;3 测量线段与晶界相切时, 计为1个截点;4 明显的与三个晶粒汇合点重合时,计为1.5个截点;5 在不规则晶粒形状下,测量线在同一晶粒边界不同部位产生的两个截点;后又伸入形成新的截点, 计算截点时应包括新的截点.2 平均晶粒度级别数G的计算:G=6.643856lg(M.P/L) – 3.28845H-200X1 截点法公式:L= L/M.PL:所使用的测量线段长度(mm), M: 观测用的放大倍数P: 测量直线上的截点数L测量面上晶粒截距的平均值(查表平均截距)截点的计算: 计算截点时注意:1测量线段终点不是截点不予计算;2 终点正好接触到晶界时,计为0.5个截点;3 测量线段与晶界相切时, 计为1个截点;4 明显的与三个晶粒汇合点重合时,计为1.5个截点;5 在不规则晶粒形状下,测量线在同一晶粒边界不同部位产生的两个截点;后又伸入形成新的截点, 计算截点时应包括新的截点.2 平均晶粒度级别数G的计算:G=6.643856lg(M.P/L) – 3.28845H-200X-41 截点法公式:L= L/M.PL:所使用的测量线段长度(mm), M: 观测用的放大倍数P: 测量直线上的截点数L测量面上晶粒截距的平均值(查表平均截距)截点的计算: 计算截点时注意:1测量线段终点不是截点不予计算;2 终点正好接触到晶界时,计为0.5个截点;3 测量线段与晶界相切时, 计为1个截点;4 明显的与三个晶粒汇合点重合时,计为1.5个截点;5 在不规则晶粒形状下,测量线在同一晶粒边界不同部位产生的两个截点;后又伸入形成新的截点, 计算截点时应包括新的截点.2 平均晶粒度级别数G的计算:G=6.643856lg(M.P/L) – 3.28845H-200X-51 截点法公式:L= L/M.PL:所使用的测量线段长度(mm), M: 观测用的放大倍数P: 测量直线上的截点数L测量面上晶粒截距的平均值(查表平均截距)截点的计算: 计算截点时注意:1测量线段终点不是截点不予计算;2 终点正好接触到晶界时,计为0.5个截点;3 测量线段与晶界相切时, 计为1个截点;4 明显的与三个晶粒汇合点重合时,计为1.5个截点;5 在不规则晶粒形状下,测量线在同一晶粒边界不同部位产生的两个截点;后又伸入形成新的截点, 计算截点时应包括新的截点.2 平均晶粒度级别数G的计算:G=6.643856lg(M.P/L) – 3.28845H-200X-61 截点法公式:L= L/M.PL:所使用的测量线段长度(mm), M: 观测用的放大倍数P: 测量直线上的截点数L测量面上晶粒截距的平均值(查表平均截距)截点的计算: 计算截点时注意:1测量线段终点不是截点不予计算;2 终点正好接触到晶界时,计为0.5个截点;3 测量线段与晶界相切时, 计为1个截点;4 明显的与三个晶粒汇合点重合时,计为1.5个截点;5 在不规则晶粒形状下,测量线在同一晶粒边界不同部位产生的两个截点;后又伸入形成新的截点, 计算截点时应包括新的截点.2 平均晶粒度级别数G的计算:G=6.643856lg(M.P/L) – 3.28845H -200X-71 截点法公式:L= L /M.PL:所使用的测量线段长度(mm), M: 观测用的放大倍数P: 测量直线上的截点数L测量面上晶粒截距的平均值(查表平均截距)截点的计算: 计算截点时注意:1测量线段终点不是截点不予计算;2 终点正好接触到晶界时,计为0.5个截点;3 测量线段与晶界相切时, 计为1个截点;4 明显的与三个晶粒汇合点重合时,计为1.5个截点;5 在不规则晶粒形状下,测量线在同一晶粒边界不同部位产生的两个截点;后又伸入形成新的截点, 计算截点时应包括新的截点.2 平均晶粒度级别数G的计算:G=6.643856lg(M.P/L) – 3.288。
中文E112平均晶粒度标准讲解

中⽂E112平均晶粒度标准讲解⾦属平均晶粒度测定⽅法1 范围1.1 本标准规定了⾦属组织的平均晶粒度表⽰及评定⽅法。
这些⽅法也适⽤晶粒形状与标准系列评级图相似的⾮⾦属材料。
这些⽅法主要适⽤于单相晶粒组织,但经具体规定后也适⽤于多相或多组元和试样中特定类型的晶粒平均尺⼨的测量1.2 本标准使⽤晶粒⾯积、晶粒直径、截线长度的单峰分布来测定式样的平均晶粒度。
这些分布近似正态分布。
本标准的测定⽅法不适⽤于双峰分布的晶粒度。
双峰分布的晶粒度参见标准E1181。
测定分布在细⼩晶粒基体上个别⾮常粗⼤的晶粒的⽅法参见E930。
1.3本标准的测量⽅法仅适⽤平⾯晶粒度的测量,也就是试样截⾯显⽰出的⼆维晶度,不适⽤于试样三维晶粒,即⽴体晶粒尺⼨的测量。
1.4 试验可采⽤与⼀系列标准晶粒度图谱进⾏对⽐的⽅法或者在简单模板上进⾏计数的⽅法。
利⽤半⾃动计数仪或者⾃动分析晶粒尺⼨的软件的⽅法参见E1382。
1.5本标准仅作为推荐性试验⽅法,它不能确定受检材料是否接收或适合使⽤的范围。
1.6 测量数值应⽤SI单位表⽰。
等同的英⼨-英镑数值,如需标出,应在括号中列出近似值.1.7 本标准没有列出所有的安全事项。
本标准的使⽤者英建⽴适合的安全健康的操作规范和使⽤局限性。
1.8 章节的顺序如下:2、参考⽂献2.1ASTM标准E3 ⾦相试样的准备E7 ⾦相学有关术语E407 微蚀⾦属和合⾦的操作E562计数法计算体积分数的⽅法E691 通过多个实验室⽐较决定测试⽅法的精确度的⽅法E883 反射光显微照相指南E930 截⾯上最⼤晶粒的评估⽅法(ALA晶粒尺⼨)E1181双峰分布的晶粒度测试⽅法E1382 半⾃动或全⾃动图像分析平均晶粒度⽅法2.2 ASTM附件2.2.1 参见附录X23 术语3.1 定义-参照E73.2 本标准中特定术语的定义:3.2.1 ASTM晶粒度——G,通常定义为公式(1)N AE为100倍下⼀平⽅英⼨(645.16mm2)⾯积内包含的晶粒个数,也等于1倍下⼀平⽅毫⽶⾯积内包含的晶粒个数,乘以15.5倍。
晶粒度评级图

金属平均晶粒度评级图—系列图片I无孪晶晶粒100×
00级0级
金属平均晶粒度评级图—系列图片I无孪晶晶粒100×
0.5级 1.0级
金属平均晶粒度评级图—系列图片I无孪晶晶粒100×
1.5级
2.0级
金属平均晶粒度评级图—系列图片I 无孪晶晶粒 100×
2.5级
3.0级
金属平均晶粒度评级图—系列图片I无孪晶晶粒100×
3.5级
4.0级
金属平均晶粒度评级图—系列图片I无孪晶晶粒100×
4.5级
5.0级
金属平均晶粒度评级图—系列图片I无孪晶晶粒100×
5.5级
6.0级
金属平均晶粒度评级图—系列图片I无孪晶晶粒100×
6.5级
7.0级
金属平均晶粒度评级图—系列图片I无孪晶晶粒100×
7.5级8.0级
金属平均晶粒度评级图—系列图片I无孪晶晶粒100×
8.5级9.0级
金属平均晶粒度评级图—系列图片I无孪晶晶粒100×
9.5级10.0级。
钢实际晶粒度的显示和评定方法

钢实际晶粒度的显示和评定方法 cyh(2010-07-27 18:25:01) 杨桂珠(中国工程物理研究院机械制造工艺研究所,绵阳621900)摘要:对不同热处理状态下的60Si2MnA钢和0Cr17Ni14Cu4Nb钢试样进行了试验和摸索,获得了这两种材料在常规热处理状态下的实际晶粒度的显示方法,即60Si2MnA钢用饱和苦味酸+3%~5%洗涤剂+新洁尔灭水溶液侵蚀0Cr17Ni14CuNb钢用高锰酸钾(0.5~1g)+硫酸(8~12ml)+水(90~115ml)热蚀。
晶粒显现清晰,解决了60Si2MnA钢和0Cr17Ni14Cu4Nb 钢晶界显示和晶粒度评定的难题。
关键词:0Cr17Ni14Cu4Nb钢60Si2MnA钢晶粒度评定方法1 引言许多钢材的晶界难以侵蚀,随着热处理状态的不同,侵蚀晶界的条件也多变。
因此,迅速腐蚀和清晰显示晶界,找出影响侵蚀条件的因素及规律为人们所关注。
在对60Si2MnA钢和0Cr17Ni14Cu4Nb钢反复试验的基础上,根据钢材热处理状态变化对金相侵蚀条件的影响和国家相关标准,从试验方法入手,并进行了粗略的理论分析,找到了显示60Si2MnA钢和0Cr17Ni14Cu4Nb 钢晶粒度的方法。
2 试验方法显示晶粒度应采用比显示显微组织弱得多的侵蚀剂。
显示实际晶粒度时,应尽量降低试剂的电化学腐蚀能力。
试样经过磨制抛光后侵蚀,抛光织物必须用丝绒,抛光剂用水或油剂金刚石研磨膏(粒度为W2.5~3.5)。
根据0Cr17Ni14Cu4Nb和60Si2MnA钢的特性,经过优化,选用的侵蚀剂见表1。
组织和晶界观测在德国MM6大视场显微镜上进行。
3试验结果3.1 0Cr17Ni14Cu4Nb钢不锈钢侵蚀一般均可采用草酸电解,但该种钢电解十几分钟或更长时间晶界都不受腐蚀,显微镜下只能观察到一些腐蚀坑。
用试剂1对固溶时效状态下的0Cr17Ni14Cu4Nb钢进行试验,室温下擦拭试样表面2s,组织先显示出来,随之部分晶界也显示出来,因组织干扰大,无法评定晶粒度,见图1a。