高纯生铁生产工艺浅析
高纯生铁的标准

高纯生铁的标准
高纯生铁是指含铁量较高、杂质含量较低的铁制品,通常是铁冶炼的初级产物。
高纯生铁的标准可以涵盖多个方面,包括化学成分、物理性质、生产工艺等。
以下是一般情况下关于高纯生铁的一些可能的标准:
1.化学成分:
含铁量:高纯生铁的含铁量应该较高,通常在99%以上。
杂质含量:标准可能规定其他金属和非金属杂质的最大允许含量,如硫、磷、锰、硅等。
2.物理性质:
密度:标准可能规定高纯生铁的密度范围。
熔点:高纯生铁的熔点通常是较高的,标准可能规定其熔点范围。
3.生产工艺:
生产工艺要求:标准可能规定高纯生铁的生产工艺,确保产品的质量和纯度。
炉温控制:在高温冶炼过程中,可能规定炉温的控制要求,以确保高纯度的铁制品产出。
4.含氧量:
氧含量:标准可能规定高纯生铁中氧的含量,因为氧的存在可能影响其用途。
5.形状和尺寸:
形状:高纯生铁可能以块状或其他规定的形状出现。
尺寸:标准可能规定高纯生铁的尺寸范围,以满足生产和使用的要求。
6.检测方法:
标准通常会指定用于测定含铁量、杂质含量等参数的检测方法,确保测试结果的准确性和可比性。
我国高纯生铁的研制、生产和应用
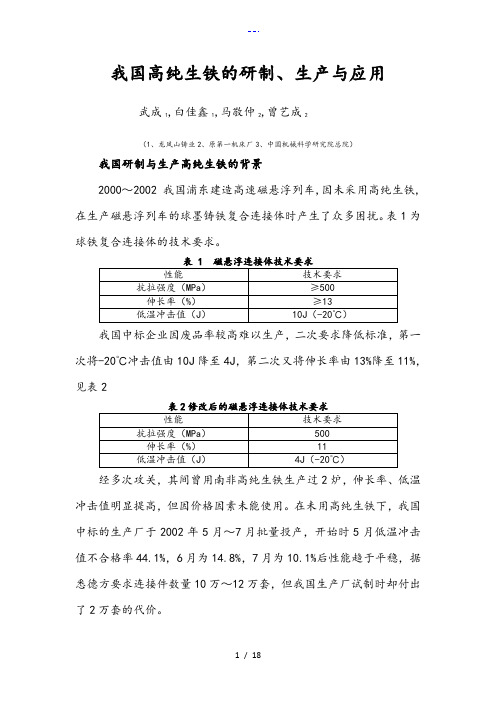
我国高纯生铁的研制、生产与应用武成1,白佳鑫1,马敬仲2,曾艺成 2(1、龙凤山铸业2、原第一机床厂3、中国机械科学研究院总院)我国研制与生产高纯生铁的背景2000~2002我国浦东建造高速磁悬浮列车,因未采用高纯生铁,在生产磁悬浮列车的球墨铸铁复合连接体时产生了众多困扰。
表1为球铁复合连接体的技术要求。
我国中标企业因废品率较高难以生产,二次要求降低标准,第一次将-20℃冲击值由10J降至4J,第二次又将伸长率由13%降至11%,见表2经多次攻关,其间曾用南非高纯生铁生产过2炉,伸长率、低温冲击值明显提高,但因价格因素未能使用。
在未用高纯生铁下,我国中标的生产厂于2002年5月~7月批量投产,开始时5月低温冲击值不合格率44.1%,6月为14.8%,7月为10.1%后性能趋于平稳,据悉德方要求连接件数量10万~12万套,但我国生产厂试制时却付出了2万套的代价。
随着我国高速列车、风力发电、核电、汽车等行业的大发展,对低温铁素体球墨铸铁、等温淬火球墨铸铁ADl、大断面球铁及高性能球铁需求量日益增大。
普通球铁生铁中Si、Mn、P、Ti及其微量元素含量无法满足高端铸件的要求。
高纯生铁的供应已成为高端球铁件发展及进一步提高性能与质量的瓶颈。
高纯生铁的研究与生产已刻不容缓。
2007年中国铸造活动周中,我国学者著文呼吁尽快研制与生产高纯生铁。
从2007年至2010年,我国开始研制高纯生铁,到2010年开始批量生产高纯生铁。
华德机械公司用高纯生铁生产-40℃~-50℃的高铁上的转向架轴箱,电机底座等低温铁素体球铁,为中国客车集团、庞厐巴迪、阿尔斯通、舍佛勒供应低温铁素体轨道产品。
至今生产各类产品2万余套,无一废品。
该公司负责人总结产品质量稳定性问题时说:“采用高纯生铁是保证高性能低温铁素体球铁质量与质量稳定性的基础”。
一、我国生产高纯生铁的工艺特点国外生产高纯生铁的工艺主要是氧化法,以著名的“Sorelmetal”为例,其生产工艺是先将铁矿石和无烟煤混合后置于电弧炉中,经加热,将不同的金属氧化物还原,然后倒入另炉进行氧化吹炼,通过氧化处理,大幅度地脱除了P、Si、Mn、Ti、V、Cr等元素,此法可使各种杂质的含量降至很低,氧化处理的设备可用转炉、反射炉或大型盛铁包。
超高纯铁精矿氢气还原生产纯铁技术研究

超高纯铁精矿氢气还原生产纯铁技术研究以超高纯铁精矿氢气还原生产纯铁技术研究为题,我们将探讨超高纯铁精矿氢气还原生产纯铁的技术研究情况以及其在工业生产中的应用。
铁是一种重要的金属材料,广泛应用于建筑、机械、电子等领域。
高纯度的铁具有更好的物理性能和化学性质,因此在一些特殊领域有着重要的应用价值。
超高纯铁精矿氢气还原生产纯铁技术,就是一种通过氢气还原超高纯度铁精矿,从而获得高纯度铁的方法。
在超高纯铁精矿氢气还原生产纯铁的过程中,首先需要选择合适的铁矿石作为原料。
超高纯铁精矿是一种铁含量较高的矿石,含有少量的杂质。
选择合适的矿石可以有效提高生产纯铁的效率和质量。
接下来,需要将选取的超高纯铁精矿进行预处理。
预处理主要是去除矿石中的杂质和硫化物,以提高还原过程的纯度和效果。
预处理方法包括矿石破碎、磁选和浮选等。
在氢气还原过程中,需要将预处理后的超高纯铁精矿与氢气进行反应。
反应过程中,需要控制温度、气体流速和反应时间等参数,以确保反应的完全性和产物的纯度。
反应完成后,产物中含有高纯度的铁和少量的氧化铁。
产物中的高纯度铁可以通过磁选、浮选和重力选矿等方法进行进一步的分离和纯化。
这些方法可以去除产物中的杂质和氧化铁,从而提高铁的纯度。
在工业生产中,超高纯铁精矿氢气还原生产纯铁技术具有重要的应用价值。
首先,该技术可以获得高纯度的铁,满足一些特殊领域对高纯度铁的需求。
其次,该技术具有环保、节能的特点,不会产生大量的废气和废水。
此外,该技术还可以有效利用矿石资源,提高资源利用率。
值得注意的是,超高纯铁精矿氢气还原生产纯铁技术在实际应用中还存在一些问题和挑战。
例如,反应过程中的温度和气体流速需要精确控制,以确保反应的完全性和产物的纯度。
同时,原料的选择和预处理也对产物的质量和产量有着重要影响。
因此,在实际应用中需要不断优化和改进该技术,以提高生产效率和产物质量。
总结而言,超高纯铁精矿氢气还原生产纯铁技术是一种重要的铁矿石还原方法,可以获得高纯度的铁。
高纯金属制备技术详解

高纯金属制备技术详解高纯金属制备技术详解高纯金属是现代许多高、新技术的综合产物,虽然20世纪30年代便已出现“高纯物质”这一名称,但把高纯金属的研究和生产提高到重要日程,是在二次世界大战后,首先是原子能研究需要一系列高纯金属,而后随着半导体技术、宇航、无线电电子学等的发展,对金属纯度要求越来越高,大大促进了高纯金属生产的发展。
纯度对金属有着三方面的意义。
第一,金属的一些性质和纯度关系密切。
纯铁质软,含杂质的铸铁才是坚硬的。
另一方面,杂质又是非常有害的,大多数金属因含杂质而发脆,对于半导体,极微量的杂质就会引起材料性能非常明显的变化。
锗、硅甲含有微量的m、V族元素、重金属、碱金属等有害杂质,可使半导体器件的电性能受到严重影响。
第二,纯度研究有助阐明金属材料的结构敏感性、杂质对缺陷的影响等因素,并由此为开发预先给定材料性质的新材料设计创造条件。
第三,随着金属纯度的不断提高,将进一步揭示出金属的潜在性能,如普通金属被是所有金属中最脆的金属。
而在高纯时被便出现低温塑性,超高纯时更具有高温超塑性。
超高纯金属的潜在性能的发现,有可能开阔新的应用领域,在材料学方面打开新的突破口,为高技术的延伸铺平道路。
金属的纯度是相对于杂质而言的,广义上杂质包括化学杂质(元素)和物理杂质(晶体缺陷)。
但是,只有当金属纯度极高时,物理杂质的概念才是有意义的,因此生产上一般仍以化学杂质的含量作为评价金属纯度的标准,即以主金属减去杂质总含量的百分数表示,常用N (nine的第一字母)代表。
如99.9999%写为6N,99.99999%写为7N。
此外,半导体材料还用载流子浓度和低温迁移率表示纯度。
金属用剩余电阻率RRR和纯度级R表示纯度。
国际上关于纯度的定义尚无统一标准。
一般讲,理论的纯金属应是纯净完全不含杂质的,并有恒定的熔点和晶体结构。
但技术上任何金属都达不到不含杂质的绝对纯度,故纯金属只有相对含义,它只是表明目前技术上能达到的标准。
超纯净工业纯铁生产工艺研究

超纯净工业纯铁生产工艺研究随着科技的飞速发展,超纯净工业纯铁在众多领域的应用越来越广泛,如电子、能源、航空航天等。
为了满足不同领域对超纯净工业纯铁的需求,研究者们不断探索优化其生产工艺。
本文将对超纯净工业纯铁生产工艺的研究进行详细介绍。
超纯净工业纯铁是指杂质元素含量极低的铁金属,其主要应用于高精度、高要求的场合。
目前,超纯净工业纯铁的生产工艺主要包括电弧熔炼、电子束熔炼、真空感应熔炼等。
然而,在生产过程中,超纯净工业纯铁易受杂质污染,如何提高其生产工艺成为当前研究的热点。
为了提高超纯净工业纯铁的生产工艺,研究者们采用了诸多研究方法。
通过实验设计,研究者们对生产过程中的主要影响因素进行了详细研究,包括原料纯度、熔炼温度、熔炼时间等。
研究者们还采用了数据收集和分析的方法,以获取生产过程中不同阶段的数据,以便对生产工艺进行优化。
同时,在理论研究方面,研究者们结合计算材料学方法,对超纯净工业纯铁的原子结构和电子性质进行了深入研究。
在实验研究方面,通过调整熔炼温度和时间,研究者们成功地提高了超纯净工业纯铁的纯度。
同时,通过对比不同纯度的工业纯铁,研究者们发现,提高原料纯度对超纯净工业纯铁的生产具有重要意义。
在理论研究方面,计算材料学方法为超纯净工业纯铁的原子结构和电子性质提供了精确预测,有助于优化生产工艺。
本文对超纯净工业纯铁生产工艺的研究进行了详细介绍。
通过实验研究和理论研究,研究者们发现提高原料纯度和控制熔炼温度和时间是提高超纯净工业纯铁生产工艺的关键。
随着科技的不断进步,相信超纯净工业纯铁在未来的应用前景将更加广阔。
展望未来,我们期望在超纯净工业纯铁的生产工艺方面取得更多突破性成果。
需要进一步优化生产工艺参数,实现超纯净工业纯铁的大规模生产。
需要加强生产过程中的质量控制,确保产品的一致性和可靠性。
我们还应积极探索新型生产技术,如离子束熔炼、等离子体熔炼等,以满足更高层次的应用需求。
我们还应重视超纯净工业纯铁在环保和能源领域的应用研究。
提升铁水纯度的关键工艺技术分析与研究

提升铁水纯度的关键工艺技术分析与研究在钢铁行业中,铁水纯度的提升对于生产质量和效益具有重要的影响。
随着市场对高质量钢材的需求增加,提升铁水纯度的关键工艺技术变得越来越重要。
本文将分析和研究提升铁水纯度的关键工艺技术,以期对钢铁行业的发展做出贡献。
一、高温炼铁技术高温炼铁技术是提升铁水纯度的关键工艺之一。
采用高炉炼铁技术,可以有效地去除铁水中的硫、磷等有害杂质。
高炉内的高温和还原气氛有利于脱硫,使得铁水中的硫含量大大降低。
此外,高温还可以促进铁水中的杂质与渣相分离,提高产量和纯度。
二、熔炼炉底炼钢技术熔炼炉底炼钢技术是另一种提升铁水纯度的重要方法。
通过在炉底进行炼钢,可以使得精炼过程更加完善,有效去除铁水中的非金属夹杂物和有害元素。
此外,熔炼炉底炼钢技术还可以提高钢水的温度和溶解度,有利于钢水中含氧量的降低和杂质的排除。
三、连铸连轧技术连铸连轧技术是现代钢铁生产中常用的一种提升铁水纯度的工艺。
这种技术将炉中的铁水直接连续铸造成型,在不断轧制的过程中去除了大部分的杂质和夹杂物。
连铸连轧技术能够有效地降低钢水中的含氧量和含杂质的程度,使得最终产品的纯度得到提升。
四、先进的在线检测技术提升铁水纯度的关键工艺之一是先进的在线检测技术。
通过对铁水进行实时监测和分析,可以及时发现和解决产生高温炼铁过程中的问题,确保炼钢过程的稳定性和质量。
先进的在线检测技术可以帮助生产者更好地控制炼钢过程中的各个环节,从而提高铁水纯度。
五、优化的原料配比和冶炼工艺提升铁水纯度的关键还在于优化的原料配比和冶炼工艺。
合理地选择原料,并对其进行适当搭配,可以减少钢铁生产过程中产生的杂质和夹杂物。
此外,在冶炼工艺上的优化也可以提高铁水的纯度,例如通过增加炉温、延长保温时间等方法,对钢水进行脱硫和脱气,从而提高纯度。
六、精细化管理和智能化控制最后,提升铁水纯度的关键还在于精细化管理和智能化控制。
通过建立全面的生产管理体系和信息化系统,使用智能化的控制技术,可以实现对钢铁生产过程的精细化管理和控制。
生铁炼钢的原理
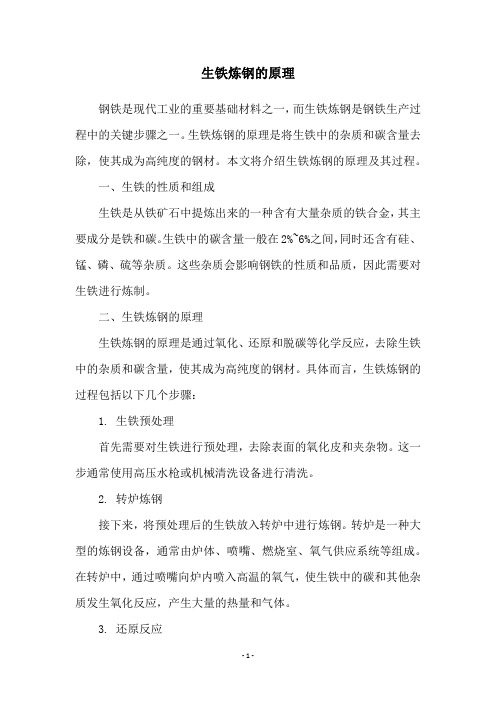
生铁炼钢的原理钢铁是现代工业的重要基础材料之一,而生铁炼钢是钢铁生产过程中的关键步骤之一。
生铁炼钢的原理是将生铁中的杂质和碳含量去除,使其成为高纯度的钢材。
本文将介绍生铁炼钢的原理及其过程。
一、生铁的性质和组成生铁是从铁矿石中提炼出来的一种含有大量杂质的铁合金,其主要成分是铁和碳。
生铁中的碳含量一般在2%~6%之间,同时还含有硅、锰、磷、硫等杂质。
这些杂质会影响钢铁的性质和品质,因此需要对生铁进行炼制。
二、生铁炼钢的原理生铁炼钢的原理是通过氧化、还原和脱碳等化学反应,去除生铁中的杂质和碳含量,使其成为高纯度的钢材。
具体而言,生铁炼钢的过程包括以下几个步骤:1. 生铁预处理首先需要对生铁进行预处理,去除表面的氧化皮和夹杂物。
这一步通常使用高压水枪或机械清洗设备进行清洗。
2. 转炉炼钢接下来,将预处理后的生铁放入转炉中进行炼钢。
转炉是一种大型的炼钢设备,通常由炉体、喷嘴、燃烧室、氧气供应系统等组成。
在转炉中,通过喷嘴向炉内喷入高温的氧气,使生铁中的碳和其他杂质发生氧化反应,产生大量的热量和气体。
3. 还原反应在转炉中,氧气与生铁中的碳和其他杂质反应后,会产生大量的二氧化碳和一氧化碳等气体。
这些气体会与炉内的热铁和石灰石等物质反应,发生还原反应,将生铁中的氧化物还原成纯铁和其他物质。
4. 脱碳在还原反应的同时,生铁中的碳会与氧气反应,生成二氧化碳等气体。
这些气体会从转炉顶部排出,使生铁中的碳含量逐渐降低。
当生铁中的碳含量降至一定程度时,就可以停止氧气喷吹,使炉内的温度逐渐降低,最终得到高纯度的钢材。
三、生铁炼钢的优缺点生铁炼钢是一种重要的钢铁生产工艺,其优点在于可以利用廉价的生铁资源,同时也可以满足各种不同品质和用途的钢材需求。
但是,生铁炼钢也存在一些缺点,比如生铁中的杂质和碳含量较高,需要消耗大量的氧气和能源进行炼制。
同时,生铁炼钢还会产生大量的二氧化碳等废气,对环境造成污染。
四、结论生铁炼钢是一种重要的钢铁生产工艺,其原理是通过氧化、还原和脱碳等化学反应,去除生铁中的杂质和碳含量,使其成为高纯度的钢材。
铸造用高纯生铁的定标及生产要义
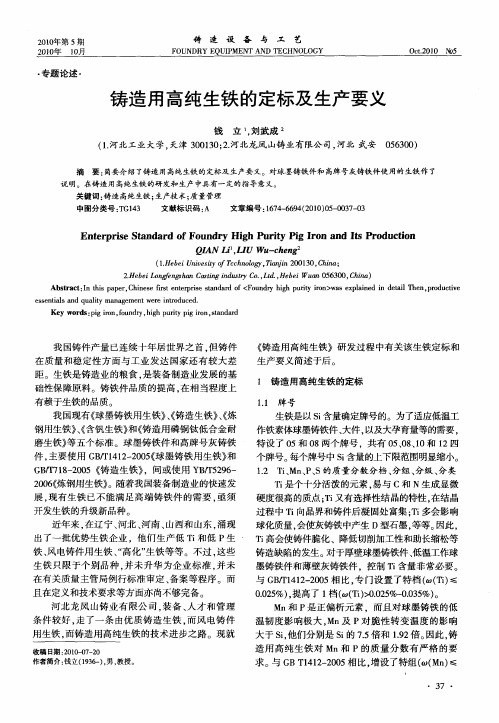
础性保障原料。铸铁件品质 的提高 , 在相当程度上 有赖 于生铁 的 品质 。 我国现有《 球墨铸铁用生铁》 《 、铸造生铁》 《 、炼 钢用生铁》《 、含钒生铁》 铸造用磷铜钛低合金耐 和《 磨 生铁 》 五个 标 准 。球 墨铸铁 件 和 高牌 号灰 铸铁 等 件, 主要使用 G /1 1—0 5 球墨铸铁用生铁》 B 4 2 2 0( T 和 G /7 820 《 造 生铁 》 BT 1—0 5 铸 ,间或 使 用 Y /59 — BT 26 20 ( 0 6炼钢用生铁》 。随着我国装备制造业 的快速发 展, 现有生铁已不能满足高端铸铁件 的需要 , 亟须
Ab t a t I h sp p r Ch n s r t n e p ie s n a d o F u d y h g u i mn wa x l i e n d t i T e p d ci e sr c :n t i a e , i e e f s tr r t d r f< o n rt i e s a t a o v
2 1年第 5 00 期
2 1 年 l月 00 0
铸
造 设
备
与 工
艺
0 t 0 N 5 e. 1 2 0 D
F 0UNDRY E0U P I ME NT AND T HNO OGY EC L
・
专题 论述 ・
铸 造 用 高 纯 生铁 的定 标 及 生产 要义
钱 立 刘 武成 .
我 国铸 件产 量 已连续 十年居 世 界之 首 , 铸件 但
在 质 量 和稳 定 性 方 面 与工 业 发 达 国家还 有 较 大 差
《 铸造用高纯生铁》研发过程 中有关该生铁定标和 生 产要义 简述 于后 。
1 铸 造 用高纯 生铁 的定标
浅谈纯净钢生产技术
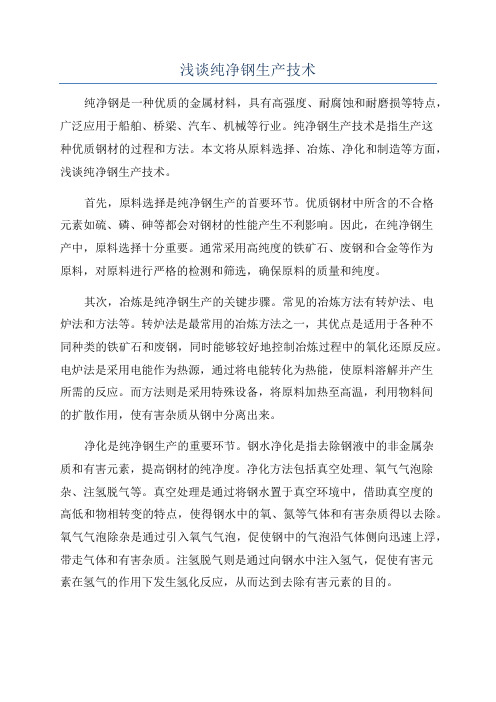
浅谈纯净钢生产技术纯净钢是一种优质的金属材料,具有高强度、耐腐蚀和耐磨损等特点,广泛应用于船舶、桥梁、汽车、机械等行业。
纯净钢生产技术是指生产这种优质钢材的过程和方法。
本文将从原料选择、冶炼、净化和制造等方面,浅谈纯净钢生产技术。
首先,原料选择是纯净钢生产的首要环节。
优质钢材中所含的不合格元素如硫、磷、砷等都会对钢材的性能产生不利影响。
因此,在纯净钢生产中,原料选择十分重要。
通常采用高纯度的铁矿石、废钢和合金等作为原料,对原料进行严格的检测和筛选,确保原料的质量和纯度。
其次,冶炼是纯净钢生产的关键步骤。
常见的冶炼方法有转炉法、电炉法和方法等。
转炉法是最常用的冶炼方法之一,其优点是适用于各种不同种类的铁矿石和废钢,同时能够较好地控制冶炼过程中的氧化还原反应。
电炉法是采用电能作为热源,通过将电能转化为热能,使原料溶解并产生所需的反应。
而方法则是采用特殊设备,将原料加热至高温,利用物料间的扩散作用,使有害杂质从钢中分离出来。
净化是纯净钢生产的重要环节。
钢水净化是指去除钢液中的非金属杂质和有害元素,提高钢材的纯净度。
净化方法包括真空处理、氧气气泡除杂、注氢脱气等。
真空处理是通过将钢水置于真空环境中,借助真空度的高低和物相转变的特点,使得钢水中的氧、氮等气体和有害杂质得以去除。
氧气气泡除杂是通过引入氧气气泡,促使钢中的气泡沿气体侧向迅速上浮,带走气体和有害杂质。
注氢脱气则是通过向钢水中注入氢气,促使有害元素在氢气的作用下发生氢化反应,从而达到去除有害元素的目的。
最后,制造是纯净钢生产的最后一步。
制造过程中,主要包括热处理、轧制和加工。
热处理是将钢材加热至一定温度,然后通过快速冷却的方法,使钢材获得理想的力学性能。
轧制是将钢坯通过轧机进行塑性变形,使得钢材在尺寸和形状上得到满足需求的改变。
加工是将轧制后的钢材进行切割、焊接、打孔等工艺,制成最终的产品。
综上所述,纯净钢生产技术是一个复杂而严谨的过程。
原料选择、冶炼、净化和制造都是非常重要的环节,需要严格按照标准进行操作。
钢铁加工工艺流程分析
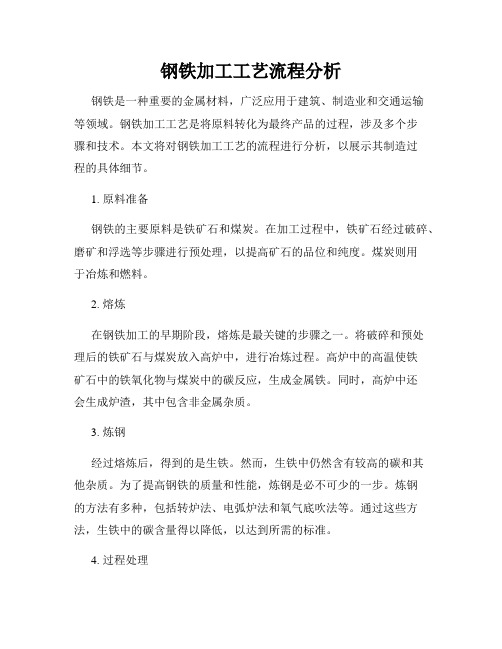
钢铁加工工艺流程分析钢铁是一种重要的金属材料,广泛应用于建筑、制造业和交通运输等领域。
钢铁加工工艺是将原料转化为最终产品的过程,涉及多个步骤和技术。
本文将对钢铁加工工艺的流程进行分析,以展示其制造过程的具体细节。
1. 原料准备钢铁的主要原料是铁矿石和煤炭。
在加工过程中,铁矿石经过破碎、磨矿和浮选等步骤进行预处理,以提高矿石的品位和纯度。
煤炭则用于冶炼和燃料。
2. 熔炼在钢铁加工的早期阶段,熔炼是最关键的步骤之一。
将破碎和预处理后的铁矿石与煤炭放入高炉中,进行冶炼过程。
高炉中的高温使铁矿石中的铁氧化物与煤炭中的碳反应,生成金属铁。
同时,高炉中还会生成炉渣,其中包含非金属杂质。
3. 炼钢经过熔炼后,得到的是生铁。
然而,生铁中仍然含有较高的碳和其他杂质。
为了提高钢铁的质量和性能,炼钢是必不可少的一步。
炼钢的方法有多种,包括转炉法、电弧炉法和氧气底吹法等。
通过这些方法,生铁中的碳含量得以降低,以达到所需的标准。
4. 过程处理经过炼钢后,得到的是纯净的钢水。
然而,钢水中仍然存在非金属杂质和气体。
为了去除这些杂质,需要进行一系列的过程处理。
其中包括钢水调温、脱氧、除杂、脱硫等。
通过这些处理,可以使钢铁的成分和性能得到进一步改善。
5. 连铸连铸是钢铁加工的关键环节之一,也是最后一个工艺步骤。
在连铸过程中,钢水被注入连铸机中,经过冷却和凝固,形成连续的铸坯。
连铸可以生产各种形状和规格的钢材,如圆钢、方钢和板材等。
同时,连铸还可以控制钢材的组织和性能,确保其质量和可靠性。
6. 后续加工连铸获得的铸坯经过冷却和固化后,可以进行后续加工。
后续加工包括热轧、冷轧、锻造、焊接等工艺。
通过这些工艺,可以将铸坯转化为所需的最终产品,如钢板、管材和结构件等。
同时,后续加工还可以对钢铁的性能进行进一步调整和提升。
7. 检验和质量控制在钢铁加工的每个环节,都需要进行严格的检验和质量控制。
通过检验,可以确保钢铁的质量和性能符合标准要求。
一种4n级高纯铁及其火法工业化生产方法

一种4n级高纯铁及其火法工业化生产方法
高纯铁是指纯度较高的铁材料,其中杂质含量较低。
下面是一种4n级高纯铁的工业化生产方法:
1. 原料准备:选用优质的铁矿石作为原料,同时需要进行矿石的破碎和磁选等预处理,以获得更纯净的铁矿石。
2. 高温还原:将经过预处理的铁矿石与还原剂(如焦炭)一同加入高炉中,通过高温还原反应将铁矿石中的氧气和杂质还原出来,生成高纯度的铁块。
3. 提纯:得到的高纯铁块需要进行进一步的提纯过程。
一种常用的方法是将高纯铁块放入真空炉中,在高温下进行真空脱气和脱硫的处理,同时控制炉内的气氛,使得杂质被脱除。
还可以通过电解或氩气灌注等方式进一步提高纯度。
4. 锻造和加工:提纯后的高纯铁块可以进行锻造和加工,以满足不同的应用需求。
通过锻造可以改善高纯铁的力学性能和微观结构。
5. 最终检测和包装:对加工后的高纯铁进行最终的检测,以确保其达到4n级纯度要求。
通过合适的包装方式将高纯铁产品包装好,以便于储运和使用。
需要注意的是,高纯铁的制备过程中需要严格控制各个环节的工艺参数,包括温度、压力、气氛等。
同时,工业化生产还需要考虑成本和效率,需要进行工艺优化和设备改进。
这只是一
种可能的高纯铁工业化生产方法,实际生产中可能会根据具体情况进行不同的调整和改进。
我国铸造用高纯生铁的现状与建议

生 产 出了高纯生 铁 ,并取 得 了专利 。该厂高 炉容积
小 ,铁 液大 部分供本 企业 生产铸 件 ,外供 量不 多 。因
此 ,我 国 当前 生产高 纯生铁 的主 流方法是方 法二 。现 有 两 家 企业 生产 铸 造 用 高 纯 生 铁 ,并 有 企 业 标 准 ,
2 1年 的产销量 约 l万t 00 2 。此外 ,尚有 几家企业 的产品
绵铁 中有脉 石带来 的杂质 ,电弧 炉 冶炼要 多 加石 灰 , 耗 电多 ,加之 增碳量 大 的缘 故 ,使 这种方 法 的生产成
本 较高 。用 固体料 间断生产 ,生产率低 ,产量不 大。 综上 可见 ,方 法三 没有价 格优势 ,产量 低 ,很难 实 现规模化 生产 。2 世 纪8 年代 ,我 国有些单 位 已掌 0 0 握第 一种方 法 ,但未 予实 施 。前 几年 ,有工厂 用方法
废钢 中 留存 的微量元 素对铸铁 组织 的影响 。因此 ,高 端铸铁对生铁炉 料的要求 ,主要着 眼于其 中S 、Mn 、P
和有害微量元素的含量 。 在分 析 了低 温用 高韧 性球 墨铸铁件 、等 温淬火球
3 对 生产 铸 造 用 高 纯 生铁 的建 议
()对 用方法二生 产铸 造用 高纯生铁 的企 业来说 , 1
Mo n b b i T 、A 、B、A 等 各 自含 量 的 、S 、S 、P 、B 、 e s 1 最大 值 ,且规 定 了T和上 述 1个 微 量元素 总和 的含量 j 1
不 应 大 于 01 。 . %
2 铸 造用 高 纯 生铁 的三 种 生产 方 法
()方法 一 。以钒钛 磁铁矿 精 粉为原 料 ,由高 炉 1
的含 量在7 %~ 4 3 8 %,炉料 中F 的收得 率低 。此外 ,海 e
高纯生铁冶炼
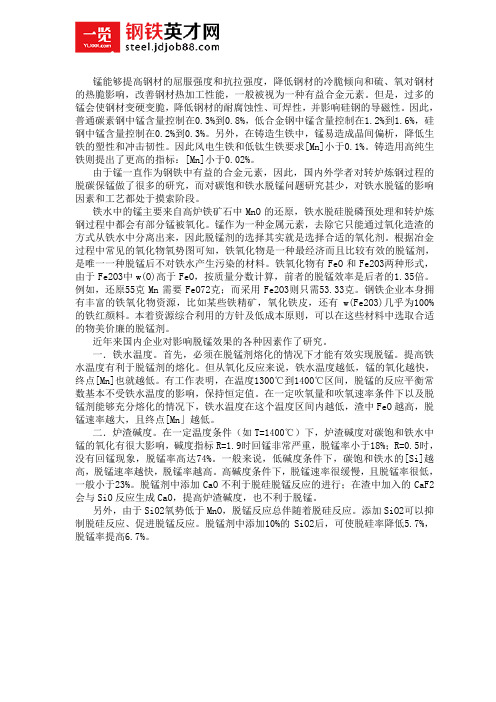
锰能够提高钢材的屈服强度和抗拉强度,降低钢材的冷脆倾向和硫、氧对钢材的热脆影响,改善钢材热加工性能,一般被视为一种有益合金元素。
但是,过多的锰会使钢材变硬变脆,降低钢材的耐腐蚀性、可焊性,并影响硅钢的导磁性。
因此,普通碳素钢中锰含量控制在0.3%到0.8%,低合金钢中锰含量控制在1.2%到1.6%,硅钢中锰含量控制在0.2%到0.3%。
另外,在铸造生铁中,锰易造成晶间偏析,降低生铁的塑性和冲击韧性。
因此风电生铁和低钛生铁要求[Mn]小于0.1%。
铸造用高纯生铁则提出了更高的指标:[Mn]小于0.02%。
由于锰一直作为钢铁中有益的合金元素,因此,国内外学者对转炉炼钢过程的脱碳保锰做了很多的研究,而对碳饱和铁水脱锰问题研究甚少,对铁水脱锰的影响因素和工艺都处于摸索阶段。
铁水中的锰主要来自高炉铁矿石中MnO的还原,铁水脱硅脱磷预处理和转炉炼钢过程中都会有部分锰被氧化。
锰作为一种金属元素,去除它只能通过氧化造渣的方式从铁水中分离出来,因此脱锰剂的选择其实就是选择合适的氧化剂。
根据冶金过程中常见的氧化物氧势图可知,铁氧化物是一种最经济而且比较有效的脱锰剂,是唯一一种脱锰后不对铁水产生污染的材料。
铁氧化物有FeO和Fe2O3两种形式,由于Fe2O3中w(O)高于FeO,按质量分数计算,前者的脱锰效率是后者的1.35倍。
例如,还原55克Mn需要FeO72克;而采用Fe2O3则只需53.33克。
钢铁企业本身拥有丰富的铁氧化物资源,比如某些铁精矿,氧化铁皮,还有w(Fe2O3)几乎为100%的铁红颜料。
本着资源综合利用的方针及低成本原则,可以在这些材料中选取合适的物美价廉的脱锰剂。
近年来国内企业对影响脱锰效果的各种因素作了研究。
一.铁水温度。
首先,必须在脱锰剂熔化的情况下才能有效实现脱锰。
提高铁水温度有利于脱锰剂的熔化。
但从氧化反应来说,铁水温度越低,锰的氧化越快,终点[Mn]也就越低。
有工作表明,在温度1300℃到1400℃区间,脱锰的反应平衡常数基本不受铁水温度的影响,保持恒定值。
一种4n级高纯铁及其火法工业化生产方法
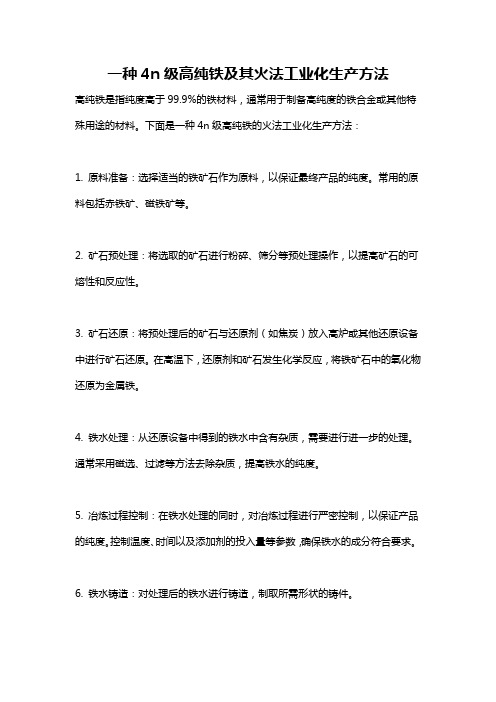
一种4n级高纯铁及其火法工业化生产方法
高纯铁是指纯度高于99.9%的铁材料,通常用于制备高纯度的铁合金或其他特殊用途的材料。
下面是一种4n级高纯铁的火法工业化生产方法:
1. 原料准备:选择适当的铁矿石作为原料,以保证最终产品的纯度。
常用的原料包括赤铁矿、磁铁矿等。
2. 矿石预处理:将选取的矿石进行粉碎、筛分等预处理操作,以提高矿石的可熔性和反应性。
3. 矿石还原:将预处理后的矿石与还原剂(如焦炭)放入高炉或其他还原设备中进行矿石还原。
在高温下,还原剂和矿石发生化学反应,将铁矿石中的氧化物还原为金属铁。
4. 铁水处理:从还原设备中得到的铁水中含有杂质,需要进行进一步的处理。
通常采用磁选、过滤等方法去除杂质,提高铁水的纯度。
5. 冶炼过程控制:在铁水处理的同时,对冶炼过程进行严密控制,以保证产品的纯度。
控制温度、时间以及添加剂的投入量等参数,确保铁水的成分符合要求。
6. 铁水铸造:对处理后的铁水进行铸造,制取所需形状的铸件。
7. 检验和精炼:对铸件进行检验,检测铸件的纯度和性能,并根据需要进行精炼处理以提高产品的纯度和品质。
常用的精炼方式包括真空冶炼、气氛冶炼等。
8. 成品包装:对最终产品进行包装和标识,以便储存和销售。
以上是一种常见的4n级高纯铁的火法工业化生产方法,具体的操作细节和设备配置可能会因厂家和地点而有所不同。
高纯生铁冶炼(图)
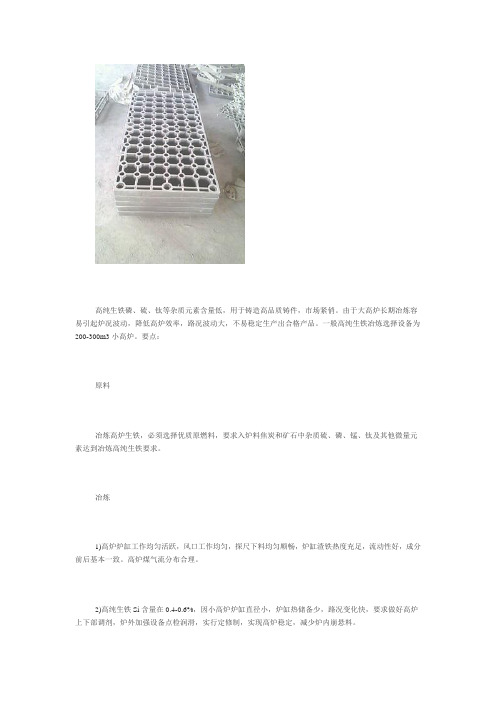
高纯生铁磷、硫、钛等杂质元素含量低,用于铸造高品质铸件,市场紧俏。
由于大高炉长期冶炼容易引起炉况波动,降低高炉效率,路况波动大,不易稳定生产出合格产品。
一般高纯生铁冶炼选择设备为200-300m3小高炉。
要点:
原料
冶炼高炉生铁,必须选择优质原燃料,要求入炉料焦炭和矿石中杂质硫、磷、锰、钛及其他微量元素达到冶炼高纯生铁要求。
冶炼
1)高炉炉缸工作均匀活跃,风口工作均匀,探尺下料均匀顺畅,炉缸渣铁热度充足,流动性好,成分前后基本一致。
高炉煤气流分布合理。
2)高纯生铁Si含量在0.4-0.6%,因小高炉炉缸直径小,炉缸热储备少,路况变化快,要求做好高炉上下部调剂,炉外加强设备点检润滑,实行定修制,实现高炉稳定,减少炉内崩悬料。
3)适当提高炉渣碱度。
炉渣二元监督控制在1.14-1.18,Ls一般在35-40,能将生铁中硫控制在≤0.02%。
4)冶炼低硅铁,有利于抑制Ti还原,高炉Si含量在0.4-0.6%,Ti在高炉内还原率35-38%。
5)P在高炉内几乎全部还原,因此欲控制出铁含P量,需严格控制炉料带入的含P量。
3、煤气流控制
运用高炉上下部调剂手段,缩小风口面积,提高风速,来保持炉缸工作均匀活跃,控制气流合理分布。
.4、提高风温
提高风温能使高温区下移,有利于冶炼高纯生铁,风温控制在1150℃左右。
5、精准操作
实行标准化操作,要求Si偏差≤0.013%,严格工艺制度,实现精准操作。
我国高纯生铁的生产和应用情况
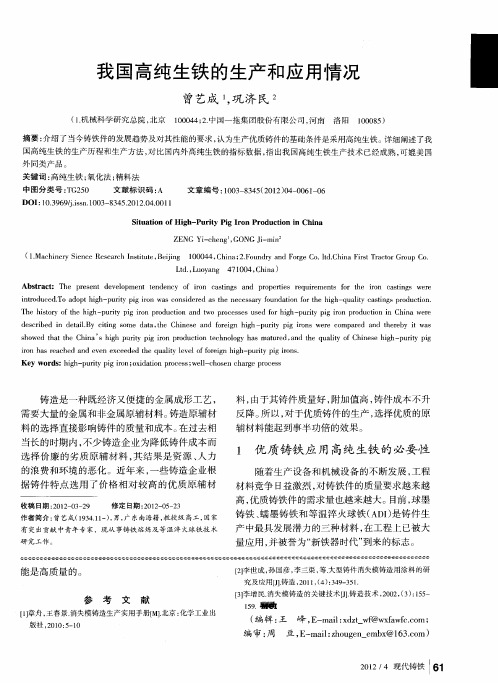
DOI 1.9 9 .s.0 3 8 4 .0 2 40 1 :03 6  ̄i n10 — 3 5 1 . . 1 s 2 0 0
Siuato ofH ih-Purt g r o t in g iy Pi I on Pr duc i n Chi ton i na
ZE — h n ’ GO NG Yi c e g , NG i mi J- n
Ld , u y n 4 1 0 , hn ) t.L o a g 7 0 4 C i a
Ab t a t T e r s n d v lp n tn e c o r n a t g a d r p ris e u r me t o t e r n a t g w r s r c : h p e e t e eo me t e d n y f i c si s n p o e t r q i o n e e n s r h io c s n s e e f i
我 国高纯 生铁 的生产和应用情况
曾艺成 1巩 济 民 2 ,
(. 械科学研究总院 , 京 1 机 北 104 ;. 一 拖 集 团 股 份有 限公 司 , 南 0 0 4 2中国 河 洛阳 10 8 ) 0 0 5
摘要 : 介绍了当今铸铁件 的发展趋势及对其性能 的要求 , 为生产优质铸件的基础条件是采用高纯生铁 。 认 详细阐述了我
1 优 质 铸 பைடு நூலகம் 应 用 高 纯 生铁 的 必要 性
io sr a he nd e e x e de h uaiy lve ff r in hih—p it g io . r n ha e c d a v n e c e d t e q lt e lo o eg g ur y pi r ns Ke y wor :hih— rt g io o i to o e s; l—c os n c r e p o e s ds g pu iy pi r n; xdai n pr c s we l h e ha g r c s
高纯度金属材料的制备技术研究

高纯度金属材料的制备技术研究随着科技的不断发展,金属材料在现代工业中扮演着越来越重要的角色。
随着金属材料应用领域的不断拓展,对于金属材料纯度的要求也越来越高。
在这种情况下,高纯度金属材料的制备技术逐渐成为研究的热点之一。
高纯度金属材料是指金属材料中不含杂质或者含杂质极少,达到了特定技术要求的材料。
它不仅不易氧化、腐蚀,而且具有较高的物理化学性质。
因此,高纯度金属材料在航空、航天、电子、半导体、化工、医疗等高科技领域得到广泛应用。
目前,高纯度金属材料的制备技术主要有以下几种:1. 物理法物理法是指通过物理方法分离和提纯金属,比如熔融法、凝固法、蒸发法、溅射法等。
在这些制备技术中,熔融法是应用最广泛的一种。
它是将金属加热至熔点以上,使其熔化后在特定条件下高温冷却,从而得到高纯度的金属。
这种制备方式可以避免化学反应,从而降低杂质含量,提高金属的纯度。
2. 化学法化学法主要是通过化学反应分离和提纯金属,比如溶剂萃取法、离子交换法、化学还原法、电解法等。
这种制备方式主要是在金属与杂质之间特定的化学反应条件下研究提纯,提高金属的纯度。
化学法可以选择特定的化学试剂来将杂质与金属分离,来达到特定的提纯目的。
在实际生产中,以上两种方法单独应用不能完全满足高纯度金属材料的制备需求,需要综合使用不同的方法来提高金属的纯度。
同时,确定合适的制备工艺对提高金属材料的纯度也具有重要意义。
因为制备过程涉及到多种因素,如硅化物的纯度、制备温度的控制、硅脉冲转炉的设计以及气相、液相、固相反应等,因此,制备高纯度金属材料的过程比较复杂。
其中,在金属熔融过程中悬浮不同大小和杂质含量的气包是提高金属成品质量的关键。
因此,控制和降低金属熔池中气体的含量是非常重要的。
除此之外,在高温下,金属容易与氢气或氧气等反应并形成气体,这也是制备高纯度金属材料时要注意的问题之一。
在制备过程中用适当的气氛,可以有效地防止这种情况发生。
同时,在制备过程中,需要进行多次人工搅拌和过滤处理,以降低金属中杂质的含量。
- 1、下载文档前请自行甄别文档内容的完整性,平台不提供额外的编辑、内容补充、找答案等附加服务。
- 2、"仅部分预览"的文档,不可在线预览部分如存在完整性等问题,可反馈申请退款(可完整预览的文档不适用该条件!)。
- 3、如文档侵犯您的权益,请联系客服反馈,我们会尽快为您处理(人工客服工作时间:9:00-18:30)。
高纯生铁生产工艺浅析
近年来,随着我国汽车、风电、船舶、化工、高速列车等行业的发展,对优质铸铁件、等温淬火球铁件(ADI)、大断面球铁件及特殊性能要求的球铁件需求量不断提高,与国内的铸造生铁普遍存在的钛、磷含量偏高和杂质、微量元素超标等形成突出的矛盾,很多高端铸造企业不得不从加拿大等国进口高纯生铁来满足生产要求,制约着我国由铸造大国向铸造强国迈进的步伐。
河北龙凤山铸业有限公司等企业为加快推进高纯生铁的研制,充分利用当地的优质的原燃料优势,摸索生产工艺,已形成大批量生产高纯生铁的能力,填补了国内的空白,形成了符合实际的企业产品标准,为国内装备制造业的发展提供基础性原料保障。
下面就结合河北龙凤山铸业有限公司的生产实际,对高纯生铁生产工艺进行探讨和分析。
一、我国铸铁的标准体系
现有《球墨铸造用生铁》、《铸造生铁》、《炼钢用生铁》、《含钒生铁》、《铸造用磷铜钛合金耐磨生铁》等五个标准。
球墨铸铁件和高牌号灰铸铁件主要使用《球墨铸造用生铁》和《铸造生铁》两个国家标准,间或使用《炼钢用生铁》行业标准;有关高纯生铁生产企业制订的高纯生铁企业产品标准。
二、高纯生铁工艺控制的原则
根据国内外有关的研究资料和市场用户需求,高纯生铁化学成分的要求包括控制碳、硅、锰、硫、磷、钛六个常规元素;对高端铸件有影响的微量元素及其极限值;微量元素的含量总和,重点在于控制钛、锰、磷、硫四个元素,关键是控制钛、磷的含量。
钛易与碳、氮生成显微硬度很高的化合物,又有选择性结晶的特性,使钛向晶界及铸件后凝固处富集,并影响球化质量等,钛高会使铸件脆化、降低切削加工性能和助长缩松等铸造缺陷的产生。
磷和锰是正偏析元素,对球墨铸造的低温韧度影响极大,对脆性转变温度的影响分别是硅的7.5倍和1.92倍。
合理确定铬、钒、钼、锡、锑、铅、铋、碲、砷、硼和铅十一个微量元素的最大值,各微量元素的含量总和以形式良好铸铁件性能。
河北龙凤山铸业有限公司的钛和上述十一个微量元素的含量总和不应大于0.1%,11个微量元素最大值是:
三、高纯生铁的生产工艺
目前国外主要采用高炉还原+另炉氧化吹炼的方法,但在不使用特殊原料(钒钛磁铁矿)的条件下,不适合采用此工艺。
钛是干扰球化元素,实际生产中【Ti】和【Si】同步还原,呈强相关性,控
制高炉铁水含【Si】量的途径:控制焦炭、煤的灰分和原料中的SiO2含量,降低焦比;改善炉料结构,合理布料促使煤气合理分布,控制滴落带高度,减少铁水吸硅量;增加炉缸渣中氧化性物质,促进铁水脱硅反应。
在充分利用企业设备、优质原燃料和人员技术的基础上,摸索研究,采取“精料+高炉精细作业+炉外专项处理”的技术路线,用高炉直接冶炼出高纯生铁,主要的生产工艺为:
1.降低焦炭灰分和TiO2,降低烧结矿中SiO2和TiO2,降低焦比。
通过对优质原材料的选用、配比和增加必要的细化分选工序,最大限度降低钛元素含量。
2.选择合理的炉料结构。
以高碱烧结矿占比65—70%,酸性球团矿占比30—35%,碱度为1.9—2.0(倍);增加装入料热流化,改善矿石高温冶金性能,提高炉料本身自熔温度,增加烧结矿中MgO含量。
3.装料控制。
根据高纯生铁质量要求和出铁量,总料批确定按每小时6.5—7批料控制,连续4小时料批不能超规定批数上限;提前2小时根据炉温、料速与铁量关系预测下2小时负荷情况,稳定炉温;严禁空料线作业,分装入炉;合理布料,实现合理煤气流分布范围尽量缩小。
4.送风控制。
为使生铁含Si量稳定,风量控制在1750—1850m/min;密切关注各风口部位反映的参数作细节把握,压差反应快;考虑白天与黑夜环境温差对炉温的影响,夜里风温比白天高30℃左右。
5.热制度管理。
稳定炉温【Si】含量控制0.4±0.1%,铁水物理热>1470℃-1520℃;严禁含Si跳号波动,降低风口区温度减少SiO生成;冷却设备发现漏水及时控制更换,不影响炉缸的炉温。
6.造渣管理。
入炉碱度以炉渣R2≥1.15(倍),R3≥1.4(倍);炉渣流动性要好,脱硫能力强,MgO含量≥12%,Al2O3≤14%。
7.喷煤管理。
视炉况反应、料速计算,按综合负荷加减喷煤量,喷枪均匀喷煤,堵枪要及时处理。
8.实行高顶压控制。
800m3高炉顶压控制在150kpa,既提高炉内压力,抑制SiO生成,又能降煤气流速,提高利用率,降低焦比。
9.出铁量控制。
铁口深度≥1800mm,保证铁口堵泥耐冲刷力强、透气性好,无潮泥,出铁顺畅,按时出铁。
10.炉外处理。
高炉采取低【Si】作业法,以获低【Ti】铁水,由于不同牌号铁水有时需炉外增硅,由喂料机按计算量进行孕育;在铁水罐中,根据所需的脱【Si】量,以氮气为载体进行喷Mg粒操作,搅拌铁水,脱气、浮渣和均匀化学成分;以液面渣量多少决定是否捞渣,由捞渣机完成;浇锭时,使用高效孕育剂
进行随流孕育,若白口没有完全消除,启动第二孕育装置进行补加,孕育剂加入时,应稳定均匀,孕育剂流要正对铁水流。
高纯生铁锭外观洁净,断口均匀呈细灰粒状,金相分析,石墨组织均呈A型石墨形态,细小,分布均匀。
高纯生铁在我国应用有着广泛的空间,需要针对不同用户的特定需求,严格炉料控制,强化工艺管理,细化工艺参数,总结生产经验,生产出符合要求的优质高纯生铁,实现批量替代进口,切实提高铸造生铁的附加值,推进我国高端铸件的全面发展。
参考文献:
[1]李克瑞、曾艺成、张忠仇:《优质生铁和高纯生铁—球铁稳定生产的基础》,2007年中国铸造活动周论文集,355-362;
[2]李传栻:《如何面对铸造生铁中干扰元素的影响》;铸造纵横,2009(2);
[3]钱立:《企标之我见》,第八届全国铸铁及熔炼学术会议暨先进球化处理方法研讨会论文集,2010.7,160,162。