棒材三切分轧制要点
棒材切分轧制工艺

郭宝峰
学习目标
1、让大家对切分轧制工艺有个初 步的认识。
2、理解切分轧制的概念、意义。 3、了解实际生产过程中的注意事
项。
切分轧制的概念
• 所谓切分轧制,就是在轧制过程中把一根 轧件利用孔型和导卫的作用,轧成具有两 根或两根以上相同形状的并联轧件,再利 用切分设备或轧辊的辊环将并联的轧件沿 纵向切分成两个或两个以上的单根轧件, 这些切分后的轧件有的可直接作为成品, 有的则作为中间坯继续在线同时进行轧制。 根据切分后形成轧件的数目多少,又可分 为二切分、三切分、四切分、五切分等。
四切分工艺概况
切分轧制对温度的要求
• 承钢各线均配备侧进侧出双蓄热步进 式加热炉,坯料165*165*118000,切分 开轧温度控制在1030-1150之间,或高 或低均会引起切分轮故障,即温度低 切分负荷重,切分轴承容易坏,温度 高切分刀容易粘铁,切分终轧温度不 低于850℃。
温度高低对轧制的影响
• 轧机全部使用短应力机型,一般配套120米冷床, 3#剪和冷床距离为120米,即与冷床长度1:1设计。 我们由于地形限制,冷床96米,上冷床距离63米, 这将成为制约提速的关键问题。
切分轧制工艺的意义
1、不同规格产品的生产能力基本均衡。因为 炼钢连铸能力相对稳定,而轧钢能力因为 生产规格不同波动大,特别是小规格棒材 产量低。采用切分工艺可以使多种规格棒 材的轧制能力基本相等,同时,对于轧钢 工序来说,可使加热炉、轧机、冷床及其 它辅助设备的生产能力充分发挥。
• 棒材切分轧机区的设计一般采用18架布置,即 6+6+6,粗中精各6架。粗中轧平立交替无扭轧制, 精轧16、18架平立可转换,轧单线时全部平立交 替无扭轧制。切分时,16、18架为平轧,13架平 辊,14架立轧,15架预切,16架切分,17架成前 扭转后经活套进入18架成品。也有19架的,预切 分为两架。
Ф12mm螺纹钢三切分轧制生产技术攻关

< N ̄ A 镪 ◇◇ - k N
K 6 K 5 K 4 K 3 K 2 K
图 1 (l m x b 2 i 3带肋钢筋精轧孔型 图 n 23精轧料型尺寸 - 我厂 O1m 螺纹钢三切分轧制精轧料型尺寸如表 1 2m 所示 表 1 中1rx 2r 3带 肋钢 筋 精轧 料 型尺 寸 r n
◇ 科技论坛◇
科技 目向导
21 年第 1期 02 8
1mm螺纹钢三切分轧制生产技术攻关 2
罗 祥 琴 f 钢 劳 服 公 司 棒 材 厂 福建 三 -@ 350) 6 0 0
【 要】 摘 本文主要介绍 了三钢劳服公 司棒材 厂 中1f螺纹钢三切分轧制轧制工艺, 2I I l I l 以及在 实际生产过程 中的常见 问 和改进措施 。 题 【 关键词 】 棒材 ; 三切分 ; 技术攻关
注 : 7 型尺 寸 为 3 x 4 m K料 8 3m
3生产过程中出现的问题及解决措施 .
31K . 2产 生 楔 形 料 在 轧制 O1m 螺纹钢时 . 2道 次虽 采用稳 定性较好 的椭 圆孔 . 2m K 仍 易产 生楔形料 . 造成成 品表面折叠 经 K3 切分后 的边线料型呈“ 桃形” K . 2滑动进 口导卫夹板 内腔 为 方形 , 寸为 轧件尺寸 的 1 5 .桃形” 尺 . 倍 “ 2 轧件在 K 进 口中易处于无 2 约束状态 , 图 2 a所示 , 如 () 因此 虽然进 口导 卫与轧槽 对正 , 轧件 中心 却未处于轧槽中心 . K 轧槽轧制后产 生楔 形轧件 : 经 2 针对 K 进 L导 2 I 卫的缺点 . 重新设计 K 2进 口导卫 . 将传统的滑动进 口导卫改为滚 动进 L导卫 , I 调整空 间大大 增加 . 际生产 中把导轮间距 调至与料型尺 寸 实 致 . 图 2 b 所示 , 如 () 轧件 在滚 动进 口导卫 中的中心 与轧槽保 持 一 致. 因此可得到均匀规则 的 K 2的料 型 : 同时 . 由于滚 动进 口导轮 的夹 持作 用 . 可使 K 切分后产生 的切分带旋转至上下侧 . 3 经轧槽加工后 可 消除切分带 . 避免切分带残 留带人 K 道次导致成品折叠 1
导卫的安装与调整(棒材)敬业新

导卫的安装与调整圆钢和螺纹导卫调整:一)单线部分1、所有的进口滚动导卫在调整时,导卫的导辊必须距导卫的轧制中心线(导卫中心线)是一致的,禁止导辊的偏向,那样会产生进口对不准,导辊易损坏,轧件易倒料。
如:12H进口滚动导卫在调整时,导辊的间隙与实际料型的间隙为±10丝左右;也就是说在调整导卫的两个导轮的间隙时,用实际料型来调整,呈现导轮很轻松的跟着样棒转动为最佳。
但是,在左右两边导轮距导卫的本身中心线一致时,间隙适当时,才为最佳。
2、如:12H出口滑动导卫,安装时必须导管铲嘴与轧辊槽的配合间隙为1—1.5mm为最佳,也就是说安装没有与轧辊相摩擦为佳。
也就是说单线的进出口导卫的中心线高必须与轧制线中心高要一致,左右偏向要一致,安装时要三点一线。
3、导卫在装配时,必须正确安装,紧固导卫的所有的紧固件,以防导卫松动,在轧制过程中影响轧制。
二)双线部分:1、16H出口切分导卫的调整。
切分轮的调整要平齐,两个切分轮的调整间隙应为±10丝左右(也就是转动上切分轮带动下切分轮轻松转动就可以了)。
切分刀片应与切分轮、进口夹板在同一条中心线上,叫三点一线。
注:切分导卫得进口夹板〈铲嘴〉在与轧辊装配时,必须和轧辊配合间隙为〈1mm〉良好。
2、17H出口扭转导卫〈01-02〉的调整。
在轧制过程中,根据实际轧速,根据实际轧制品种来调整扭转导卫的扭转角度;轧制速度越快,两个扭转轮的间隙越大。
用实际料型测量扭转导卫的扭转角度应为最佳。
在轧制速度越快的情况下,用实际样棒调整的如下α角度越来越小。
一般呈现的角度为15°左右。
(在轧制过程中可以用以下圆棒来调整两辊的间隙。
如:φ22*2的用圆钢22mm来调整;。
)分别用样棒来调整,调整时两个扭转轮跟转就可以,轻松转动不易太紧。
出口扭转导卫呈现的角度图:3、在轧制中(15 –16)架滚动导卫(0930B/C)的导轮,必须左右两边导轮各自两平齐,每两边的导轮距导卫中心线为一致,调整导轮间隙,用实际料型调整导轮,四个导轮跟着转,不要太紧,用实际样棒来调整导辊,如导辊很轻松的在跟着转动,实际料棒在导卫的左右移动又很轻则为最佳(在没有样棒时,调整间隙比实际来料大0.5mm左右).三)二切分轧制:1、在轧制(φ22×2)的轧制工艺,前提条件必须保证轧机左右辊辊缝是一致的,禁止错辊,导卫安装适当。
Ф14棒材生产中三切分轧制技术研究

题 。 但 孔 型 设 计 时 ,还 需 考 虑 预 切 分 与切 分 孔 型 的 配 合 问 题 ,如 配 合 不 当 ,会 造 成 轧 制 过程 中 的调 整 难 度 及 导 卫粘 铁 的现 象 。 ( 3 )立箱孔 立箱孔型延伸系数 很小 ,基本无 宽展 , 起到轧件微调平整 的作用 ,其与前 后孔的配 合很重要 。 根据经验, 其侧壁斜度为 7 。左右,
以达到限制宽展 的 目的 ,立箱孔型 的槽底 宽
应 比来 料 高 小 1 - 2 m m ,如 果 过 大 ,边 孔 会 出
一
现过大的强制性压下 ,导致 出现 中间料型比 两边料型突 出的现象 即 中间料型 的面积比两 边料型大 ,进而导致后续道次料型不好调整 方案一中 1 2 # 料型设计 高度为 2 4 . 6 m m, 而1 3 撑 孔型槽底宽为 2 0 mm,与料型相 比槽底 过窄,咬入 困难 ,且 l 3 孔型限制 了边孔的宽 展, 由 图 8可 以看 出 , 边 孔 最 宽处 为 2 2 . 2 5 mm, 而中间孔不考虑 宽展 已达到 了2 2 . 6 mm,毫无 疑 问会造 成 1 3 料型 中间突出的现象, 而两边 的料 型 明 显 比 中 间 的料 型 偏 大 。 方案二 中 1 2 # 边孔 比 1 3 捍 孔 对 应 位 置 稍 低, 这样 l 3 # 孔 不会 过 多 限制 1 2 # 边孔 的 宽展 , 从而避免造成轧件 向中间孔的流动过 多。 综 合 以 上分 析 , 最 终选 择 了方 案 二 : l 群 - 8 料型与 中1 6两 切分基本相同 , 可减少换孔量 , 1 8 群 、1 9 # 沿用中1 4两 切 分 孔 型 。
切不开,过 小会形成对切分轮的夹持力过 大, 加大切分轮 的负荷 ,一般 在 6 0 。一 6 5 。 :楔子 尖部圆角为 1 ~1 . 5 mm 为好 , 过尖会 加快轧辊 磨损,甚至 掉肉;连接带厚度应 与辊缝接近 , 1 - 2 mm 最好 ;延伸系数在 1 . O 8 ~1 . 1 5 ,并留有 定量的宽展余地 。 工艺布局确 定后 ,初步确 定了两套孔 型 系统,具体情 况如下 : f 1 )预 切 分 孔 第 一 道 预 切分 孔 ( 1 2 撑 ) : 1 2 #  ̄ L 是第一道预切 ,主要作用是可减 小 l 4 牟 孔的变形量,降低 1 4 #  ̄ L 的轧制负荷,减 轻 1 4 #  ̄ L 的变形不均匀性 ,提高轧制稳定性; 同时经过 1 2 # 轧制后的料 型带有 凹槽 , 在进入 1 4 #  ̄ L 时对中性比较好 ,成 品尺寸较均匀。其 延伸系数一般为 1 - 3 ~1 . 4 。 两方案 9 一 1 1 撑 料型 ( 9 撑 都 是 由 4 7 . 8 r m n的 基 圆 放 大辊 缝 ) 。 方案 二设定的料型 比较合理 ,压 下分 配 比较平均 ,l l 的压下量 为 1 2 am左右 ,在轧 r 制过程 中 1 1 # 电流大于 2 O %。 第二道预切分孔 ( 1 4 #) ; 1 4 # ? L 型 的切 分楔进 一步对 初步 压 出凹 陷形状的轧件完成压下 定位 ,并精确 分配 轧 件 的断面面积 。其 变形系数较小 ,延伸系数 般为 1 . 1 . 1 . 2 两种方案中 1 4 #  ̄ L 的 延伸 系数 分别 为 1 . 4 0 7 、1 . 1 9 o ,由此可见方案 一的轧制负荷较 大 ,冲击力大。 方案一中连接带的高度为 4 . 9 am,仅为 r 孔 型 高度 的 0 . 2 5倍 , 且 其 圆 角 半径 为 3 mm, 边孔 与中间孔的连接 比较陡,易导致 1 6 ≠ } 边孔 靠里侧料 型扁平 即边孔型里侧未充满。
轧钢车间三切分轧制总结
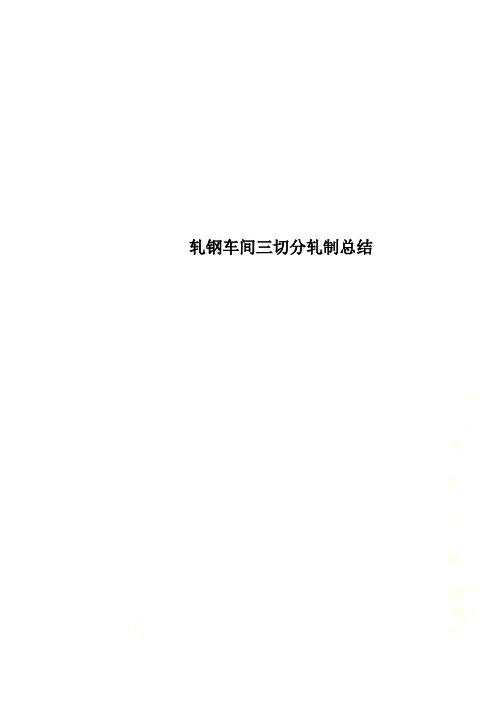
轧钢车间三切分轧制总结轧钢车间三切分轧制总结进入三切分试轧以来,各项操作办法,调整思路都处于摸索阶段,为了更好的保证三切分顺行,现对进阶段摸索出的经验进行总结归纳如下:一、料型控制要点。
1、中轧来料通条性要好,上下与两旁之差控制在2mm之内,7#机来料避免大头、大尾现象。
2、精轧各道次料型误差控制在0.2mm之内。
3、料型控制关键点:K5料型不能错辊,充满度要好,保证预切分的准确性;K3、K4要保证不错辊,防止轧件扭转,造成切偏或切分不均或冲K3出口。
4、精轧所有架次的轧辊东西辊缝务必做到相等,尤其是K3、K4、K5轧辊的东西辊缝。
5、粗轧三道来料控制在±1mm范围内,对角线差≤2mm。
7#来料控制在±0.5mm范围内,上下与两旁只差≤2mm范围内。
二、导卫调整、安装注意事项。
1、上线前导卫验收、确认工作要到位,对导卫的基本参数、功能要熟练掌握。
2、所有道次的导卫、横梁安装必须遵守“三平一直”的原则,导卫导辊离轧槽的距离严格按照操作工艺要求安装。
K3出口导卫的安装要注意导卫和导卫盒的垂直度,严禁出口导卫装斜,造成K3出口单边飞钢。
3、导卫导辊调整中心线要对称,导辊夹持样棒松紧要合适,防止造成切分不均、切偏、等事故。
4、导卫固定要牢靠:导卫顶丝、握板顶丝、握板锁紧螺丝、握板弹簧等固定要牢靠,防止在轧制中松动,造成轧制不顺。
5、9#机采用出口扭转管,角度要发生变化,一般给30-40度左右,扭转导辊的间隙一般比料型大4—8mm,具体的要结合现场实际情况(9#机出口扭转与扭转的距离、导辊的间隙、扭转的角度有关系)。
6、中、精轧各架次之间的堆拉关系要合适严禁拉钢轧制,尤其是8#、9#、10#之间之间拉钢会造成成品第一刀倍尺尺寸发生变化(东西两线无肋)。
7、8#机东西辊缝差影响成品东西两线差,正常情况下8#机西边辊缝影响成品东边两旁尺寸(西侧辊缝大,成品东侧两旁大。
反之则反。
)在东西两线差不是很大时(东西两旁尺寸差在1mm以内),可以适当的通过调整8#机东西辊缝,保证成品质量,但严禁大幅调整(前提是K3、K4进口对正轧槽)。
棒材三切分轧制工艺实践

1 概论切分轧制技术是把加热后的坯料先轧制成扁坯,然后再利用孔型系统把扁坯加工成两个以上断面相同的并联轧件,并在精轧道次上延纵向将并联轧件切分为断面面积相同的独立轧件的轧制技术。
1.1两线切分轧制技术切分轧制技术的关键是要在连接带上建立足够的拉应力,包括三个阶段:首先,随着变形区的充满,轧制力的水平分力增大,钢料顶部单面承受压力;接着,压力增大到极限后,并联轧件的连接带上产生金属的塑性流动;并联轧件分离后横向移动直至连接带完全破坏,形成分离开的独立轧件。
两线切分轧制工艺最常用的是如图1所示的弧边方——狗骨孔型系统,目前国内应用最多。
两线切分孔型系统如下。
1.2三线切分轧制技术三切分轧制技术是从两线切分轧制技术演化而来的,基本孔型系统如图2。
从图2可以看出,三线切分轧制与两线切分轧制最大的区别在于:两线切分导卫是用一对切分楔对两线并联轧件施加压力,使两线轧件分别横向运动完成切分过程。
三线切分导卫是用两对切分楔对三线并联轧件施加压力,使三线并联轧件两侧的部分分别横向运动,而中间一线不承受压力。
虽然表面现象不一样,但切分的机理仍然是相同的,都是由产生的横向拉应力来完成撕裂连接带的目的。
棒材的三线切分轧制技术自问世以来,替代了两线切分轧制技术应用于Φ10m m 、Φ12m m 及Φ14m m 的小规格产品,迅速地发展成为主流轧制技术,个别生产厂还应用于Φ16mm的螺纹钢产品。
2 工艺条件介绍广钢连轧线是引进20世纪80年代先进水平的达涅利公司棒材生产线,轧制品种为Φ10m m ~Φ40m m 圆钢及带肋钢筋。
用原料为150mm×150m m连铸坯单线生产Φ14mm ~Φ40m m 圆钢和带肋钢筋,1999年棒材三切分轧制工艺实践朱飞标(三一重工股份有限公司 湖南长沙 410000)摘 要:介绍了广钢集团连轧生产线Φ14mm螺纹钢三切分轧制工艺的开发情况,并针对原工艺设备采取了多项措施,如改进料形、精心进行速度调整、严格切分箱装配及安装制度等。
玉钢棒材Ф16mm三切分轧制技术的开发及应用

玉钢棒材Ф16mm三切分轧制技术的开发及应用文章介绍了玉钢棒材厂Ф16mm三切分棒材轧制技术和主要设备概况,并对三切分轧制技术原理进行分析,三切分轧制技术在棒材厂生产应用过程中出现的问题进行优化改进,使该规格产量得到大幅度提升。
标签:三切分轧制技术;孔型;改进优化;产量提升1 前言玉钢棒材厂自2007年4月投产以来,先后引进Ф14mm三切分、Ф12mm四切分、Ф16mm两切分等轧制技术。
经四年多的实践,结合现场工艺设备,于2011年4月提出对Ф16mm带肋钢筋进行三切分轧制技术开发,到2012年2月三切分相对两切分轧制机时产量提高30t/h,平均日产由3100t提高至3650t,从而有效降低生产成本,提高生产率。
2 棒材厂工艺概况棒材厂与炼钢厂相接,可实现铸坯的热送热装,加热炉为蓄热式步进炉,燃料为高炉煤气,设计加热能力150t/h(冷装)。
轧线为18架平立交替布置的短应力高钢度轧机,布置形式为550×4,450×6,350×8,其中16#、18#机架为平立可转换轧机。
粗、中轧后设有1#、2#飞剪,用于切头(尾)和事故碎断,粗轧机组与精轧机组间预留预穿水,精轧机与3#倍尺飞剪间设有淬水线,可生产细晶粒钢筋,不穿水采用空过导槽,冷床为单裙板,可生产Φ12-Φ40热轧带肋钢筋及Φ14-Φ40热轧圆钢,轧机最高轧制速度18m/s。
工艺流程如下:连铸坯(冷或热)→上料→入炉→加热→粗轧轧制→1#飞剪切头、切尾(碎断)→中轧轧制→2#飞剪切头、切尾(碎断)→精轧轧制→穿水冷却→3#飞剪倍尺分段→冷床冷却→定尺剪切→横移检查(短尺剔除)→震动收集→打捆→称重→挂牌→入库。
3 Ф16mm三切分轧制技术的应用三切分轧制技术关键在于合理的孔型设计与各道次料形的控制,以及切分导卫装置的选择、线差的稳定性。
3.1 孔型系统轧制道次共16道次(甩11H、12V),中轧轧制后来料为不规则圆形,通过K6道次轧制成扁平轧件,然后进入K5、K4轧制成三狗骨形轧件,经K3切分孔对预切分带进行下压,使切分带控制在0.6mm左右,最后由切分导卫装置将轧件撕开,实现三线轧制,轧件再经K2、K1道次最终轧制为成品(精轧孔型图如上图)。
棒线厂三切分轧制调整操作培训
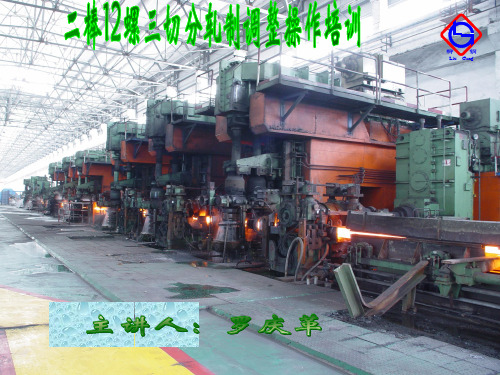
柳
Liu
钢
Gang
• 本次修改的孔型系统的特点: • 1、由一道预切分(K4)改为二道预切分(K4、 K6),目的是减少K4孔的压下量,从而减少K4的 磨损,稳定预切分孔的料形。 • 2、K3孔切分楔由原来比辊环高改为比辊环低,目 的是减少K3崩孔。 • 详见孔型图
轧制料形调整要点
• 1、辊缝设 定要比标准辊缝小0.3mm。 • 2、轧制过程料形调整要根据轧件实 际尺寸与料形标准比较来调整。
•
•
• •
1、由生产技术科制定每个导卫预装标 准尺寸: 1)滑动导卫内腔尺寸及制定允许磨损 最大值。 2)每个滚动导卫辊轮开口度预装标准 及允许偏差。 本项工作在6月10日前完成
2、准备车间要严格按生产技术下发的预装标 准进行预装,管区工程师和生产车间加强 检查验收,凡预装不合格的,责任由准备 车间承担(生产车间调整过的由生产车间 承担)
• • • •
11、两侧线合格,中间线小或大; 12、三线全部合格。 二、料形调整顺序: 1、先保证中间料形符合要求,注意导卫的调 整对中间线的料形不影响,只能通过调整K1、 K2、K3来保证,其它机架料形对中间线料形 影响很小。 • 2、调整中间线料形时,同时兼顾
柳
Liu
钢
Gang
• • • • • • • • •
柳
Liu
钢
Gang
树立信心,排出困难,实现12螺三切分达产攻关 • 1、12螺三切分达产目标:日产2400吨,成材 率大于102.20%。 • 2、攻关的主要措施: • 2.1、料形控制标准化 • 2.2、导卫预装和调整的准确性 • 2.3、采用耐磨性高的轧辊 • 2.4、轧制通道适应性改造 • 2.5、调整工的熟练调整
三切分棒材轧制活套高度差与预切分轧件偏移

Th ea ins p o o p he g f e e c t v a i n o e— s itng e r l to hi f lo ihtdif r n e wih de i to fpr — plti r le pic u i hr e— t a plti r r li o ld e e d r ng t e —sr nd s itng ba o lng
轧
钢
2 0 02
3 活 套 高 度 差 分 析
1 前 言
热 轧带 肋钢 筋 用三 线切 分 工艺 生 产 比用普 通 单 线工 艺 生产具 有 明显 的优 点 , 但生 产时 的 轧制 事 故较 常规 轧制 为 多 。常 见事 故 之一 是 由于 轧件 切 分不均 而 造 成 左 右 两 侧 轧 件 的 活 套 量 偏 离 基 准 ,形 成堆 钢 。经调 查 分析 , 发现 造 成切 分 不均 的 主要原 因是 预 切 分 轧 件 不 能 轧 出 正 确 的 料 型 ,
分 孔型 系 统示 意 图见 图 1 。
惑
严 格 ,仅凭 肉眼观 察很 难 一 次调 整到 位 , 因此给 出活套 高度 差 与轧 件偏 移量 的关 系 ,可 使调 整工
在调 整 时 有 了依据 ,对 指 导和 稳 定 切分 生产 有重 要 的 实际 意 义L 。 1 l
2 孔 型 系统 及 活 套 设 置
致 使轧 件 出现左 右偏 移 。 三 线 切分 生产 对导 卫 的安 装 和孔 型调 整极 为
1 8架 轧机 ,从 第 1 0架 轧机 以后 开 始设 立 式 活套 器 。切 分 轧制 时 立压孔 、预 切分孔 和 切分 孔 分别 设置 在 第 1 4架 、第 1 5架 和 第 1 6架 轧 机 上 , 切
棒线厂三切分轧制调整操作培训共25页文档
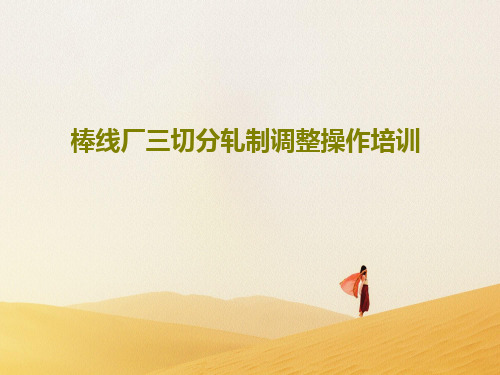
16、云无心以出岫,鸟倦飞而知还。 17、童孺纵行歌,斑白欢游诣。 18、福不虚至,祸不易来。 19、久在樊笼里,复得返自然。 20、羁鸟恋旧林,池鱼思故渊。
▪
26、要使整个人生都过得舒适、愉快,这是不可能的,因为人类必须具备一种能应付逆境的态度。——卢梭
▪
27、只有把抱怨环境的心情,化为上进的力量,才是成功的保证。——罗曼·罗兰
▪Leabharlann 28、知之者不如好之者,好之者不如乐之者。——孔子
▪
29、勇猛、大胆和坚定的决心能够抵得上武器的精良。——达·芬奇
▪
30、意志是一个强壮的盲人,倚靠在明眼的跛子肩上。——叔本华
谢谢!
25
棒材三切分轧制工艺实践
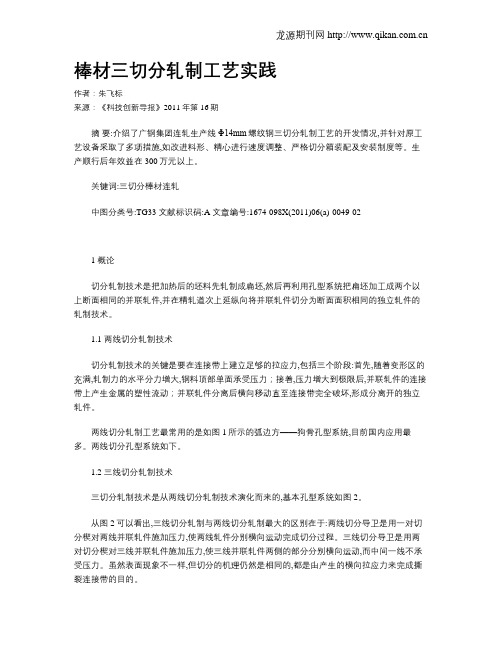
棒材三切分轧制工艺实践作者:朱飞标来源:《科技创新导报》2011年第16期摘要:介绍了广钢集团连轧生产线Φ14mm螺纹钢三切分轧制工艺的开发情况,并针对原工艺设备采取了多项措施,如改进料形、精心进行速度调整、严格切分箱装配及安装制度等。
生产顺行后年效益在300万元以上。
关键词:三切分棒材连轧中图分类号:TG33 文献标识码:A 文章编号:1674-098X(2011)06(a)-0049-021 概论切分轧制技术是把加热后的坯料先轧制成扁坯,然后再利用孔型系统把扁坯加工成两个以上断面相同的并联轧件,并在精轧道次上延纵向将并联轧件切分为断面面积相同的独立轧件的轧制技术。
1.1 两线切分轧制技术切分轧制技术的关键是要在连接带上建立足够的拉应力,包括三个阶段:首先,随着变形区的充满,轧制力的水平分力增大,钢料顶部单面承受压力;接着,压力增大到极限后,并联轧件的连接带上产生金属的塑性流动;并联轧件分离后横向移动直至连接带完全破坏,形成分离开的独立轧件。
两线切分轧制工艺最常用的是如图1所示的弧边方——狗骨孔型系统,目前国内应用最多。
两线切分孔型系统如下。
1.2 三线切分轧制技术三切分轧制技术是从两线切分轧制技术演化而来的,基本孔型系统如图2。
从图2可以看出,三线切分轧制与两线切分轧制最大的区别在于:两线切分导卫是用一对切分楔对两线并联轧件施加压力,使两线轧件分别横向运动完成切分过程。
三线切分导卫是用两对切分楔对三线并联轧件施加压力,使三线并联轧件两侧的部分分别横向运动,而中间一线不承受压力。
虽然表面现象不一样,但切分的机理仍然是相同的,都是由产生的横向拉应力来完成撕裂连接带的目的。
棒材的三线切分轧制技术自问世以来,替代了两线切分轧制技术应用于Φ10mm、Φ12mm 及Φ14mm的小规格产品,迅速地发展成为主流轧制技术,个别生产厂还应用于Φ16mm的螺纹钢产品。
2 工艺条件介绍广钢连轧线是引进20世纪80年代先进水平的达涅利公司棒材生产线,轧制品种为Φ10mm~Φ40mm圆钢及带肋钢筋。
棒材3线切分轧制技术的应用与改进

2 3线切分轧制技术的应用及改进
2.1 切分轧制技术的优点
(1)提高生产率
采用切分轧制不仅可减少轧制道次,减少轧制时间,而且,对棒材轧机,同样架次可采用较大规格的坯料生产较小规格的产品,产量不受影响。如单线生产Φ12、Φ14mm带肋钢筋,由于受总变形量的限制,通常采用小于140mm×140mm的坯料,这不仅增加坯料的规格种类,给炼钢、连铸及轧钢的生产组织带来影响,而且机时产量低。根据棒材轧机140t/h的设计能力,Φ12、Φ14mm带肋钢筋,采用3线切分轧制最合理,机时产量比2线切分提高1倍以上。
③由于3线切分上冷床不顺利,因此改进了拨钢器的设计,使之既能适应1线切分生产,又能满足3线切分生产。
④为精确定位,提高车削精度,设计了连体样板以检验轧槽。在车床上安装了数显表,以精确定位,保证车槽精度,提高配辊的精确度。
⑤由于切分轮设计不合理,第1次生产Φ14mm带肋钢筋时,中线产生大量折叠废品,因而改进了切分轮设计。并针对切分轮不耐磨现象,与生产厂家共同进行多次试验,最后选择了一种新的热作模具钢。
精整区采用裙板辊道上冷床,步进式冷床132.5m×11.5m。出口辊道将钢材送入定尺剪定尺后,由链床送到打包收集区,包装入库。
2.2 产品状况
产品规格共有39个,圆钢规格为Φ14~Φ50mm,带肋钢筋规格为Φ12~Φ40mm。Φ12、Φ14mm带肋钢筋用3线切分技术,Φ16、Φ18mm带肋钢筋用2线切分技术,可根据用户要求生产6~12m任意长度的定尺尺寸范围内的各规格带肋钢筋。
/% 成材率
/% 烧损
/kg.t-1 油耗
/kg.t-1 机时产量
/t.h-1 成本
/元.t-1
12 97.42 95.03 32.00 98.00 61.75 2323.05
Φ18mm热轧带肋钢筋三切分轧制工艺及其控制要点
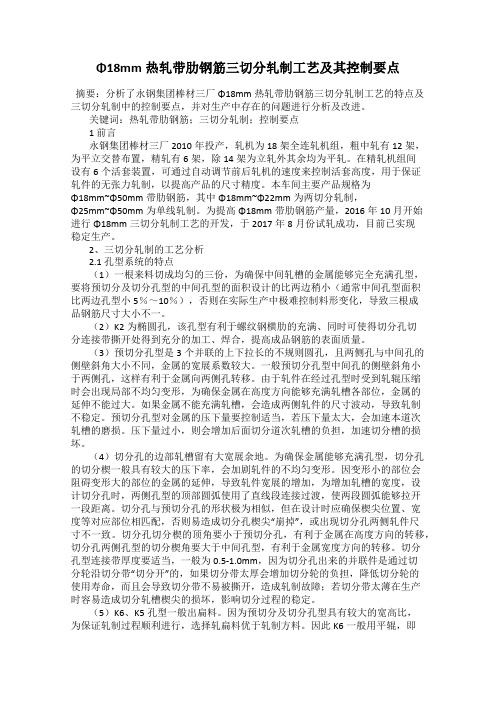
Φ18mm热轧带肋钢筋三切分轧制工艺及其控制要点摘要:分析了永钢集团棒材三厂Φ18mm热轧带肋钢筋三切分轧制工艺的特点及三切分轧制中的控制要点,并对生产中存在的问题进行分析及改进。
关键词:热轧带肋钢筋;三切分轧制;控制要点1 前言永钢集团棒材三厂2010年投产,轧机为18架全连轧机组,粗中轧有12架,为平立交替布置,精轧有6架,除14架为立轧外其余均为平轧。
在精轧机组间设有6个活套装置,可通过自动调节前后轧机的速度来控制活套高度,用于保证轧件的无张力轧制,以提高产品的尺寸精度。
本车间主要产品规格为Φ18mm~Φ50mm带肋钢筋,其中Φ18mm~Φ22mm为两切分轧制,Φ25mm~Φ50mm为单线轧制。
为提高Φ18mm带肋钢筋产量,2016年10月开始进行Φ18mm三切分轧制工艺的开发,于2017年8月份试轧成功,目前已实现稳定生产。
2、三切分轧制的工艺分析2.1 孔型系统的特点(1)一根来料切成均匀的三份,为确保中间轧槽的金属能够完全充满孔型,要将预切分及切分孔型的中间孔型的面积设计的比两边稍小(通常中间孔型面积比两边孔型小5%~10%),否则在实际生产中极难控制料形变化,导致三根成品钢筋尺寸大小不一。
(2)K2为椭圆孔,该孔型有利于螺纹钢横肋的充满、同时可使得切分孔切分连接带撕开处得到充分的加工、焊合,提高成品钢筋的表面质量。
(3)预切分孔型是3个并联的上下拉长的不规则圆孔,且两侧孔与中间孔的侧壁斜角大小不同,金属的宽展系数较大。
一般预切分孔型中间孔的侧壁斜角小于两侧孔,这样有利于金属向两侧孔转移。
由于轧件在经过孔型时受到轧辊压缩时会出现局部不均匀变形,为确保金属在高度方向能够充满轧槽各部位,金属的延伸不能过大。
如果金属不能充满轧槽,会造成两侧轧件的尺寸波动,导致轧制不稳定。
预切分孔型对金属的压下量要控制适当,若压下量太大,会加速本道次轧槽的磨损。
压下量过小,则会增加后面切分道次轧槽的负担,加速切分槽的损坏。
棒材三切分轧制工艺实践

截面积
辊缝
延伸 系数 1 3 .9
1. l 39
(11 11 11 ×11) 11 13 12xl2 0 6
1 4X l 4 1 l
( mm) ( l) s q i n n l l8 6 8
1 2 1. 27 8
迅 速 地 发 展 成 为 主 流 轧 制 技 术 , 别生 产 个 厂 还 应 用 于 1 rm的螺 纹 钢 产 品 。 6 a
l
2
箱
相
55 6
44 5
1 5
l 2
2工 艺条 件介绍
广 钢 连 轧 线 是 引进 2 世 纪 8 年 代 先 进 0 O 水 平 的 达 涅 利 公 司棒 材 生 产 线 , 制 品 种 轧 为 中 l mm ~中4 mm圆钢 及 带 肋 钢 筋 。 O 0 用 原料 为 I 0 m ×1 0 r 5a mm连铸 坯单 线 生 产 中 5 l mm ~ 4 mI 钢 和 带 肋 钢 筋 , 9 9年 4 0 n圆 19
建立足 够的拉应力 , 括三个阶段 : 先 , 包 首 随 着 变 形 区 的 充 满 , 制 力 的 水 平 分 力 增 轧
件 , 在 精 轧 道 次 上 廷 纵 向 将 并 联 轧 件 并 切 分 为 பைடு நூலகம் 面 面 积 相 同 的 独 立 轧 件 的 轧 制
技 术 。
大, 钢料 顶 部 单 面 承 受 压 力 ; 着 , 力 增 接 压 大 到 极 限 后 , 联 轧 件 的 连 接 带 上 产 生 金 并 属 的 塑性 流 动 ; 联 轧 件 分 离 后 横 向移 动 并 直 至 连 接 带 完 全破 坏 , 成 分 离 开 的 独 立 形
三切分轧制技术的应用与分析
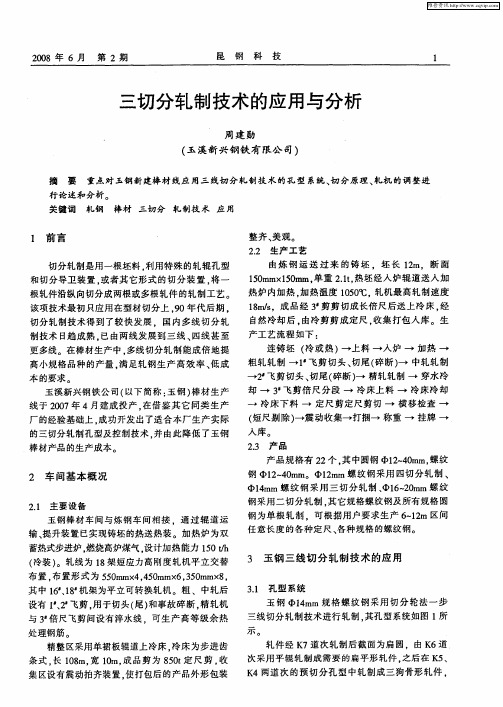
- +冷床 下 料 定 尺 剪 定 尺剪 切 横移 检 查
线 于 20 0 7年 4月建 成 投 产 . 在借 鉴 其 它 同类 生 产
厂 的经验 基础上 . 功开发 出 了适 合 本厂 生 产 实际 成
( 短尺 剔 除 ) 震 动 收 集 打 捆- ÷称重 挂 牌
入库。
23 产 品 -
轧 件基 本不 产 生 宽展 ,最 后 由切 分 孔 型 出 E 的 三 l
切 分孔型 系统 主要 由成 品前 6 次组成 . 架 包括 平 辊 孔 ( 6 , 方 形 孔( ) 铃 形d (4、 分 孔 K )扁 , 哑 : K )切 L
( 3、 品前 孔( 2、 品孔( ) K )成 K )成 K1。切分孔 型 系统设
的三切分轧制孔型及控制技术. 由此降低 了玉钢 并 棒材 产 品的生产 成本 。
产 品规 格有 2 2个 . 中圆钢 1 ~ 0 m, 纹 其 24 r 螺 a
2 车 间 基本 概 况
21 主要 设 备 .
钢 1 ~ 0 m。 1 rm螺 纹 钢 采用 四切 分 轧 制 、 24m 2 a 1rm 螺 纹 钢 采 用 三 切 分 轧 制 、 1  ̄ 0 m 螺 纹 4 a 62m 钢 采用 二切 分 轧制 . 它规 格螺 纹钢及 所有 规格 圆 其 钢 为单 根 轧 制 .可 根据 用 户要 求生 产 6 1 m区 问 -2
浅析三切分轧制技术在棒材轧机上的应用

表现在 :a 轧件出 K () 3易跑偏。( ) b 轧件在 K l后至 3 飞 剪问 易堆 钢 。对 产生 上 述 现 象 #
的原 因进 行 了分析 , 提 出解 决措施 。 并
4 1轧件 出 l . ( 3易跑偏 原 因分 析及 改进措 施 原 因分 析 a 由于 、 4 I . K 、5孔型设计 中存在不合理 <
能保证 3 m 支f4 m带肋钢筋能顺利通过导槽。 1
5 三切分轧制时应注意的事项
a料形 尺 寸 的 控制 。严 格 按 工 艺要 求 , . 控制 好各 道次 料 形 的尺 寸 , 特别 要 注 意 保 证 K 、 3孔 有 很 好 的 充满 度 , 又不 能 有 “ 4K 但 明 显” 的耳子 出现 。 因此保 持 料形 尺 寸的 相对 稳 定是 轧制 的关 键 , 轧 制稳 定 后 杜绝 人 为 在
精 轧系 统孔型 的特点 : aK . 7为椭 圆孔 ,6孔 为无 孔 型 ( 叫平 K 或
2 主要设备概况
棒材 厂 的棒 材 二 线 于 20 0 1年 4月 建 成
投产, 年设 计 能力 为 6 O万 吨 。共 2 O架轧 机 。
轧孔) 。其中 K 孔若用“ 6 平箱” 孔型, 则在实 际生 产 中易 出耳 子 , 会影 响进 入 下一 道 的 则
成 品轧制 工艺 。切 分轧制 能提 高小规 格带肋 钢筋 的产量 , 同时也能 缩短轧 线 、 有效 节约 能 源、 降低 生 产 成 本 。切 分 轧 制 有 “ 切 二 ” 一 、
“
一
冷床 为步进 齿条式 , 10 宽 1.m。 长 2m, 15
3 三切5S ̄ 的孔型系统的选择及特 kLJ
在f4 m带肋钢筋进行三线切分轧制 , r 1a
∮12三线切分轧制技术研究与探讨
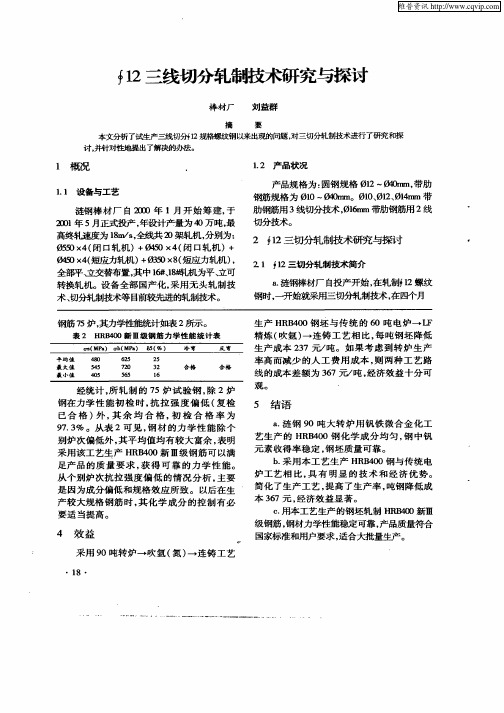
2 f2三切分轧制技术研究与探讨 1
2 1 f2三切分 轧制技术简 介 1
×( 4 拗
车 6)+ 『 脚 L
x ( 应 力车 E) 8 夏 『 , L
4 效 益
采用 9 O吨转 炉 一 吹 氩 ( ) 连 铸 工 艺 氮 一
・
元 素收得 率稳定 , 钢坯质量 可靠 。 b 采 用 本 工艺 生 产 HR 40钢 与传 统 电 . B0 炉 工艺 相 比 , 有 明显 的 技 术 和 经 济 优 势 。 具 简 化 了 生 产 工 艺 , 高 了生 产 率 , 钢 降 低 成 提 吨 本 37元 , 济 效 益 显 著 。 6 经 c用本 工艺 生 产 的 钢坯 轧 制 H B 0 . R 40新 Ⅲ 级 钢筋 , 钢材力学性能稳定可靠 , 产品质量符合 国家标准和用户要求 , 适合大批量生产。
1 ・ 8
维普资讯
的轧 制 过 程 中 , 过 改 进 , 经 基 本 掌 握 该 技 经 已
术。
接, 立箱 孔后 面轧 机全 部水 平放置 , I 从 ( 3开 始 切 分 , 要 用 切 分 轮 切 分 , 2出 口后 轧 件 主 l (
产 品规 格 为 : 圆钢 规 格 02~00 ̄ , 1 4r 带肋 钢筋 规 格 为 O 0~ 1 切分 技术 。 。O0 02 O4 n 1、 1、 1nn带 肋钢 筋用 3线切分 技术 , 6 n O1nn带肋钢筋用 2线
涟钢 棒 材 厂 自 2O OO年 1月 开 始 筹 建 , 于 20 01年 5月正 式投 产 , 年设 计 产量为 4 吨 , o万 最
棒材三切分轧制工艺实践和控制要点

棒材三切分轧制工艺实践和控制要点本文结合生产实际,分析并比较了三切分轧制工艺的特点及三切分轧制中的控制要点,针对生产实践中遇到的问题提出了适当改进建议。
标签:棒材;三切分轧制;工艺实践;控制要点1 Φ16mm规格棒材三切分轧制工艺实践(1)孔型轧机设计。
外径为十六规格三分切轧制应用六道粗轧加之四道中轧加之六道精轧合计为十六道次。
整体轧机中第一架和第九架应该是无孔型轧制、第十架为圆孔型,中轧来料是不规则的圆形。
参照二切分轧制技术的生产实践,三切分应该应用切分轮法。
外径十六规格三分切轧制要运用”狗骨型孔型系统”,也就是精轧运用六机架:十三号机架用平型辊、十四号机架用立箱、孔型,十五号机架用三狗骨头型,十六号机架是切分孔型,十七号机架是平椭,经过十八架机架轧制出螺纹钢筋成品。
(2)孔型轧机原理。
1)十四号机架设计。
理论上十四号机架立箱、孔型为十五号机架夯实了矩形的标准尺寸,否则将影响十五号机架预期切孔的三孔充满度,十四号机架料型天地宽度尺寸主要参照十五号机架边线的充满度和十四号机架料型天地的平整度。
高度尺寸主要参考十五号机架的下压量和中线充满度。
在辊径确定、其余参照不更改的条件下,轧件宽展决定压下率的大小。
当压下率和轧件的宽高之比小于零点四,轧件与轧辊触面产生变形,轧件产生双鼓型侧面。
轧件变形程度的压下率在百分之十以下,轧件表面产生变形,当压下率在百分之二十以上,中心部分由于渗透产生变形。
当压下率在百分之三十以上,接触面积部分小于中心部分变形。
2)十五号机架设计。
十五号机架预切孔型的作用是:切分楔完成对扁钢轧件的压下定位,并精准确定分配轧件的断面积,从而减轻切分孔型的负担,切实加强切分的均匀性和稳定性。
十四号机架出口轧件料型是不规则的矩形,合理设计十五号机架三线孔型,确保这个孔型轧制之后的轧件每截面积相等或者控制在相差数最小。
保证靠两边轧件不产生耳子,反之,在但影响下道工序的咬入,还能够使下道轧机在作业是产生折叠,甚至堆钢(俗称“挤王八”)。
- 1、下载文档前请自行甄别文档内容的完整性,平台不提供额外的编辑、内容补充、找答案等附加服务。
- 2、"仅部分预览"的文档,不可在线预览部分如存在完整性等问题,可反馈申请退款(可完整预览的文档不适用该条件!)。
- 3、如文档侵犯您的权益,请联系客服反馈,我们会尽快为您处理(人工客服工作时间:9:00-18:30)。
棒材三切分轧制
为顺利完成Φ12*3、Φ14*3三切分螺纹钢轧制调试工作,特提出工艺要求如下:
1、原料工严把原料质量关,杜绝有肉眼可见缺陷的钢坯入炉。
2、看火工按工艺规程要求,严格控制钢坯出炉温度,既要防止钢坯高温氧化甚至脱碳现象,影响钢材性能,又要防止低温钢轧制损坏设备甚至造成轧制事故。
3、导卫的调整与安装
3.1 导卫在上线前必须对油路、水路、轴承等进行检查,确保油路、水路畅通,零部件完好,并对导卫加油。
3.2导卫上线前的调整应坚持以下原则:①、粗轧滚动导卫的开口度比标准料型大2—4mm 为宜;中轧滚动导卫的开口度比标准料型大1—2mm为宜;精轧滚动导卫的开口度比标准料型大0.1—0.5mm为宜。
②、15、16架双排轮前面两个辊的开口度必须与后边两个辊的开口度一致。
调整时可先调前面两个辊的开口度与后边两个辊的开口度一致,然后再调内支撑臂后端的调整螺丝左右两个螺丝可同时、同步改变前后两组辊的开口度。
④、切分导卫切分轮间隙应调整适当,控制在0.3—0.5mm,以用手转动其中一个轮子时,另一个轮子也能转动,且无明显阻力为宜。
⑤、要特别注意切分刀片中心线必须与切分轮两切分刃在同一直线上,并与铲嘴内孔中心线吻合。
⑥、铲嘴在设计时已经考虑到来料与轧槽形状,在现场安装时铲嘴离轧槽的距离控制在1—2mm。
⑦、分料盒离切分轮越近越好。
⑧、扭转导卫的扭转角控制在30。
—35。
范围内。
3.3导卫在安装时尤其是15、16架进口导卫,必须保证导卫中心线与孔型中心线相吻合,以保证切分开的料型尺寸上的一致性。
4、轧辊在安装时必须保证轧辊装配的正确性以及轧机安装前轧辊轴承的加油工作;保证轧辊安装时上下轧槽的对正、磨槽以及轧辊两端辊缝的一致性,要求精轧机两边辊缝差小于0.1mm。
5、必须保证各机架孔型中心线对正轧制线,以防止轧槽偏磨,保证料型的正确性。
6、料型控制
6.1轧制过程中的料型控制严格执行《工艺技术规程》要求。
6.2第一次轧制前,中轧、13、14、15架必须各试轧2—3根小样,并测试各架次料型尺寸,要特别注意考虑小样与正常轧制时轧件尺寸及变形条件的差别。
6.3在小样试完并符合要求后,成品机架以10m/s的速度全线贯穿一根,要求使用1#剪碎断头部4米及尾部3米,岗位工注意测量各道次红坯尺寸及17、18架间轧件的扭转角度。
6.4在轧制过程中,必须控制好13架出口料型厚度及14架出口料型宽度。
6.5轧制过程中钢温应控制在1050—1150℃
7、轧制过程中1#剪必须切头、尾。
8、轧制初始阶段应投入活套。
9、保证裙板平直以及上位与下位的准确性。
10、调整倍尺剪时,必须保证倍尺剪剪臂原位水平及剪切位置的垂直,以防止倍尺轧件的头尾弯曲。
11、试生产前,冷床输入辊道中有问题的辊子和电机应换完。
12、利用检修时间调整对齐辊道,保证对齐辊道平直;3#台操作工应选择合适的对齐辊道速度。