棒材四切分问题及解决方法
四切分轧制Ф12mm螺纹钢筋的线差分析及改进措施
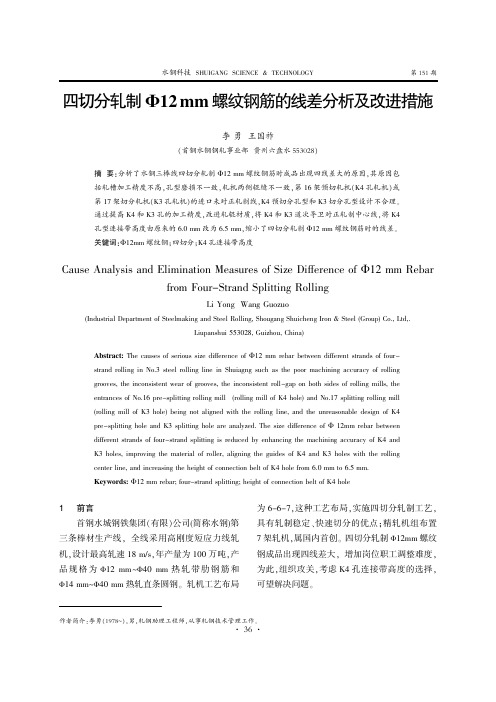
水钢科技SHUIGANG SCIENCE &TECHNOLOGY第151期1前言首钢水城钢铁集团(有限)公司(简称水钢)第三条棒材生产线,全线采用高刚度短应力线轧机,设计最高轧速18m/s,年产量为100万吨,产品规格为Φ12mm ~Φ40mm 热轧带肋钢筋和Φ14mm~Φ40mm 热轧直条圆钢。
轧机工艺布局为6-6-7,这种工艺布局,实施四切分轧制工艺,具有轧制稳定、快速切分的优点;精轧机组布置7架轧机,属国内首创。
四切分轧制Φ12mm 螺纹钢成品出现四线差大,增加岗位职工调整难度,为此,组织攻关,考虑K4孔连接带高度的选择,可望解决问题。
Abstract:The causes of serious size difference of Φ12mm rebar between different strands of four-strand rolling in No.3steel rolling line in Shuiagng such as the poor machining accuracy of rolling grooves,the inconsistent wear of grooves,the inconsistent roll-gap on both sides of rolling mills,the entrances of No.16pre-splitting rolling mill (rolling mill of K4hole)and No.17splitting rolling mill (rolling mill of K3hole)being not aligned with the rolling line,and the unreasonable design of K4pre-splitting hole and K3splitting hole are analyzed.The size difference of Φ12mm rebar between different strands of four-strand splitting is reduced by enhancing the machining accuracy of K4and K3holes,improving the material of roller,aligning the guides of K4and K3holes with the rolling center line,and increasing the height of connection belt of K4hole from 6.0mm to 6.5mm.Keywords:Φ12mm rebar;four-strand splitting;height of connection belt of K4hole作者简介:李勇(1978~),男,轧钢助理工程师,从事轧钢技术管理工作。
四切分技术培训笔记
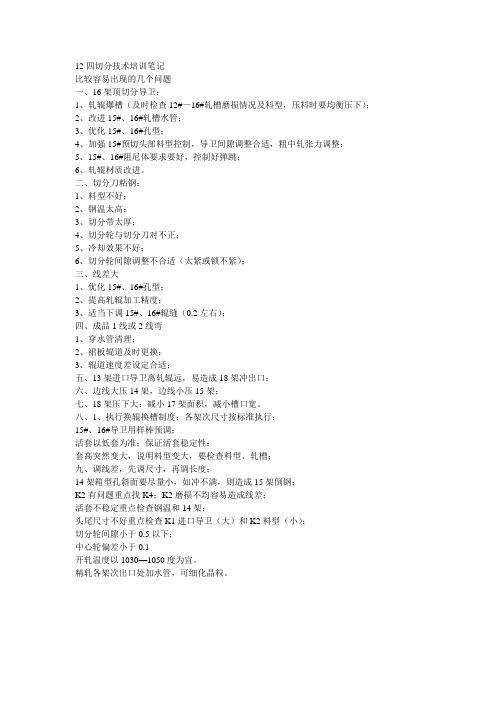
12四切分技术培训笔记比较容易出现的几个问题一、16架顶切分导卫:1、轧辊爆槽(及时检查12#—16#轧槽磨损情况及料型,压料时要均衡压下);2、改进15#、16#轧槽水管;3、优化15#、16#孔型;4、加强15#预切头部料型控制,导卫间隙调整合适,粗中轧张力调整;5、15#、16#阻尼体要求要好,控制好弹跳;6、轧辊材质改进。
二、切分刀粘钢:1、料型不好;2、钢温太高;3、切分带太厚;4、切分轮与切分刀对不正;5、冷却效果不好;6、切分轮间隙调整不合适(太紧或锁不紧);三、线差大1、优化15#、16#孔型;2、提高轧辊加工精度;3、适当下调15#、16#辊缝(0.2左右);四、成品1线或2线弯1、穿水管清理;2、裙板辊道及时更换;3、辊道速度差设定合适;五、13架进口导卫离轧辊远,易造成18架冲出口;六、边线大压14架,边线小压15架;七、18架压下大:减小17架面积,减小槽口宽。
八、1、执行换辊换槽制度;各架次尺寸按标准执行;15#、16#导卫用样棒预调;活套以低套为准;保证活套稳定性;套高突然变大,说明料型变大,要检查料型、轧槽;九、调线差,先调尺寸,再调长度;14架箱型孔斜面要尽量小,如冲不满,则造成15架倒钢;K2有问题重点找K4;K2磨损不均容易造成线差;活套不稳定重点检查钢温和14架;头尾尺寸不好重点检查K1进口导卫(大)和K2料型(小);切分轮间隙小于0.5以下;中心轮偏差小于0.1开轧温度以1030—1050度为宜。
精轧各架次出口处加水管,可细化晶粒。
棒材生产切分工艺的优化与应用
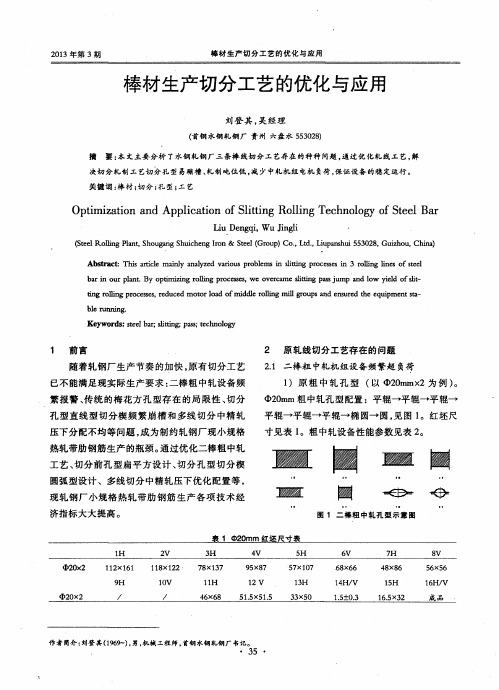
决 切 分 轧 制 工 艺 切 分 孔 型 易 蹦槽 、 轧 制 吨 位低 , 减 少 中轧机 组 电机 负荷 , 保 证 设 备 的稳 定 运行 。 关键词 : 棒材 ; 切分 ; 孔型 ; 工艺
Op t i mi z a t i o n a n d Ap p l i c a t i o n o f S l i t t i n g Ro l l i n g T e c h n o l o g y o f S t e e l B a r
时达 到 1 4 O %( 非 轧件 头 部 ) ; ( 2 )钢坯 加 热 温 度 高, 加 热 炉燃 耗 大 ; ( 3 ) 轧 线 影 响时 间 长 、 机 时 产 量低 、 轧机 作业 率低 。 3 ) 原 因分 析 。( 1 ) 进粗 轧温 度为 9 8 0  ̄ C 时, 粗 中轧 轧 机负 荷见 表 3 。从 表 3中以可 看 出 , 生 产
盈
《# 》 }
图 1 二 棒粗 中轧 孔 型 示 意 图
0 mm 红坯 尺寸 表
作 者 简介 : 刘登其( 1 9 6 9  ̄ ) , 男, 机械工程师 。 首钢水钢轧钢厂书记。 35 ・
・
水 钢 科技 S HU I G A NG S C I E NC E& T E C H N O L O G Y
b a r i n o u r p l nt a . B y o p t i mi z i n g r o l l i n g p r o c e  ̄ e s , we o v e r c a me s l i t t i n g p a s s j u mp a n d l o w y i d d o f s l i t -
第1 2 5期
2 ) - 棒 生 产 中存 在 的问题 。( 1 ) 轧制过 程 中
影响棒材定尺率的原因分析及改进措施

影响棒材定尺率的原因分析及改进措施摘要:本文结合轧钢棒材生产过程特点,总结分析了影响棒材定尺率的主要因素,并提出相应的改进措施。
关键词:定尺率;钢坯定重;热装率1 引言螺纹钢占据建筑用钢一半以上的产量,目前也是陕钢集团汉中钢铁有限责任公司主要产品之一,年生产量约160万吨,产品规格主要为Φ12-40mm。
螺纹钢筋通常情况下均以定尺出售,由于棒材在剪切精整过程中会产生较多的非定尺,非定尺材与定尺材每吨有较大差价,且非定尺材的市场需求量少,销售较困难,影响钢材的使用价值,也对成材率有一定影响。
在钢铁企业提质增效、追求效益最大化的情况下,最大程度的降低成本、提高经济效益成为企业提高竞争力、生存发展的关键。
因此提高定尺率是轧钢降低成本的有效措施,可有效增加棒材产品效益,本文总结分析了影响棒材定尺率的主要因素,并提出相应的改进措施。
2 影响棒材定尺率的原因分析2.1 钢坯重量钢坯轧制不同规格螺纹钢后,倍尺飞剪会剪切成固定的长度,同时会产生尾钢,这些尾钢通常就是非定尺。
根据金属平衡,同样重量的钢坯轧制为不同规格的棒材后其非定尺的长短不同,在其他条件不变时,钢坯重量相同,其切后的非定尺长短一定。
所以钢坯重量对定尺率的影响是直接的决定因素【1-2】,钢坯重量稳定性是提升定尺率的前提。
2.2 钢坯热装率钢坯在加热炉中如果氧化烧损和加热温度不一致时,会对轧制过程的延伸率有一定的影响,在轧制工艺参数不变的情况下影响成品长度的变化,从而会影响到非定尺的长短。
一般情况下热坯所轧制成品长度较冷坯较长。
2.3 头尾切损根据金属平衡,轧制过程头尾切损越大,成品的总长度就会相应的变短,可能会使部分定尺变为非定尺。
切损量越小,成材率越高;切损量越稳定,越有利于尾钢长度控制。
因此控制轧制过程的切损量也是提高定尺率的关键因素。
2.4 负差控制在相同钢坯重量的情况下,负偏差对成品长度影响较大,负偏差越大,成品长度越长;负差稳定性越差,成品长度波动越大,尾钢长度越不宜控制,因此负差的稳定控制对定尺率也很关键。
圆钢剪切缺陷原因分析及改进措施

圆钢剪切缺陷原因分析及改进措施圆钢是一种常见的金属材料,广泛应用于机械制造、建筑工程、汽车制造等领域。
在生产过程中,圆钢剪切缺陷是一个常见的问题,不仅会影响产品质量,还可能导致安全事故。
对圆钢剪切缺陷的原因进行分析,并提出改进措施,具有重要的实际意义。
一、圆钢剪切缺陷的原因分析1. 设备问题:圆钢剪切过程中使用的设备如果存在磨损、老化或者不合理的设计,都会导致剪切缺陷的产生。
比如刀具磨损不均匀、切割速度过快等问题都可能引起剪切缺陷。
2. 材料问题:圆钢的质量和性能会直接影响到剪切的效果,如果材料本身存在缺陷或者不符合标准要求,也会导致剪切缺陷的产生。
比如材料硬度不均匀、内部夹杂物等都可能引起剪切不良。
3. 操作问题:操作人员的技术水平和工作细节也是引起剪切缺陷的重要原因之一。
比如操作不规范、工作失误、操作疏忽等都可能导致剪切不良。
4. 环境问题:生产环境的干扰和影响也会对剪切缺陷产生影响。
比如温度、湿度、粉尘等环境因素都可能引起剪切不良。
二、圆钢剪切缺陷的改进措施1. 加强设备维护:定期对剪切设备进行检查和维护,确保刀具的锋利度和机器的正常运行。
对设备进行合理的调整和改进,能够提高剪切的效果。
2. 优化材料选择:对圆钢的材料选择和采购过程进行严格把控,保证材料的质量和性能符合标准要求。
对材料的质量进行检测,排除有缺陷的材料。
3. 加强操作培训:提高操作人员的技术水平和工作细节,确保操作的规范和精准。
对操作人员进行相关知识和技能的培训,提高其对剪切工艺的认识和理解。
4. 控制生产环境:加强生产现场的管理,保证生产环境的整洁、安全和稳定。
对生产环境的温度、湿度等参数进行严格的控制,减少外部环境对剪切的影响。
三、结语圆钢剪切缺陷是一个需要引起重视的问题,只有通过对其产生原因进行深入分析,并采取相应的改进措施,才能够有效地解决这一问题。
通过加强设备维护、优化材料选择、加强操作培训和控制生产环境等措施,可以有效地减少圆钢剪切缺陷的产生,提高产品的质量和安全性。
四切分轧制Ф12mm螺成品勾头冲出口故障的处理
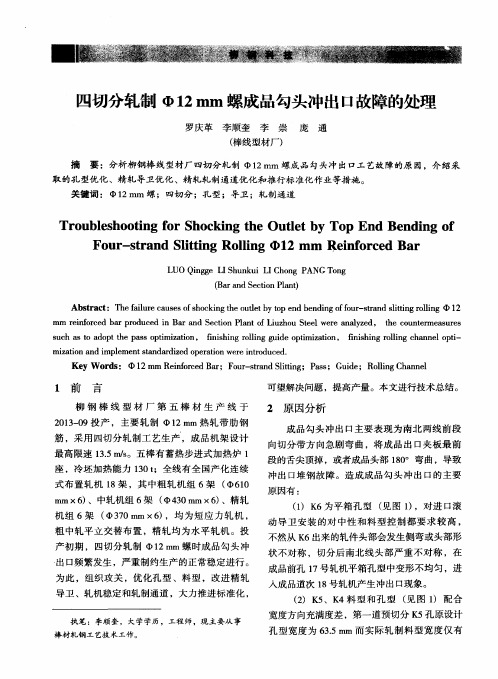
2 原 因分析
成 品勾头冲 出口主要表现为南北两线前段
向切 分 带 方 向急 剧 弯 曲 ,将 成 品 出 口夹 板 最 前
段 的舌 尖顶 掉 ,或者 成 品头部 1 8 0 。 弯 曲 ,导致
座 ,冷 坯 加 热 能 力 1 3 0 t ;全 线 有 全 国产 化 连 续 式布置轧机 1 8架 ,其 性 和 料 型 控 制 都 要 求 较 高 , 不然 从 K 6出来 的轧 件 头部 会发 生侧 弯 或 头部 形 状 不 对 称 ,切 分 后 南 北 线 头 部 严 重 不 对 称 ,在
出 口频繁发生 ,严重制约生产的正常稳定进行。
为 此 ,组织 攻 关 ,优 化 孔 型 、料 型 ,改 进 精 轧 导卫 、轧机 稳定 和轧制 通 道 ,大 力推 进 标 准化 ,
Fo u r - s t r a n d S l i t t i n g Ro l l i n g 01 2 m m Re i n f o r c e d Ba r
L U O Q i n g g e L I S h u n k u i L I C h o n g P A NG T o n g ( B a r a n d S e c t i o n P l nt a )
1 前
言
可 望解决 问题 ,提 高产 量 。本 文进行 技 术总 结 。
柳 钢 棒 线 型 材 厂 第 五 棒 材 生 产 线 于 2 0 1 3 — 0 9投 产 ,主要 轧 制 ①1 2 m m 热 轧 带 肋 钢 筋 ,采 用 四切 分 轧 制 工 艺 生产 ,成 品 机架 设 计
Ke y W o r d s :
圆钢剪切缺陷原因分析及改进措施

圆钢剪切缺陷原因分析及改进措施工业是我国第二产业,在社会经济发展中占据着重要的经济地位。
而钢和铸铁则是工业中应用最广泛的金属材料。
在钢铁具体的生产工艺中,存在着一定的缺陷。
本文对造成圆钢剪切缺陷的原因进行分析,并提出相应的改进措施。
标签:剪切;缺陷;原因;改进措施小棒线是上世纪90年代末投入生产,冷床后使用冷剪将棒材切成不同长度的定尺,在用冷剪进行剪切时,圆钢在剪切端面质量很容易出现诸多类型的剪切缺陷,而其中最重要的剪切缺陷则是圆钢剪切裂纹。
1 小棒线生产工艺简介小棒线采用的坯料断面为150 mm×150mm×9000mm 连铸坯一火成材,或者采用130×150mm×9000mm 轧制坯二火成材工艺。
小棒线生产规格为Φ13mm~Φ60mm直条棒材,定尺的长度是4~12m。
主导产品轴承钢、齿轮钢、弹簧钢、易切削非调质钢、优质碳素结构钢、合金结构钢、锚链及系泊链钢、高压及油井管坯等钢种广泛应用于汽车、工程机械、铁路、石油和矿山、船舶和海洋工程、军工等领域。
全线共18架短应力轧机与4架减定径轧机,并以单线无扭连续布置,最大的轧制速度可达每秒18米;采用12.5*120m 步进式冷床;定尺剪使用450吨冷剪。
2 圆钢剪切缺陷原因分析小棒线出冷床后通过梳形器引导轧件顺利进行孔型剪刃定尺剪切,剪切过程中出现端部剪切质量缺陷,增加了后部处理,容易产生质量隐患,使生产成本、产品形象都产生影响[1]。
2.1 端部剪切弯曲原因分析在剪切低碳钢时如20#钢、20CrMo等,在端部剪切端部容易使端部产生弯曲,此弯曲锯端部长约100~200mm,弯曲度超过4‰,超过国标要求。
矫直机也无法进行矫直,只能通过后部二次锯切进行处理,增加了后续处理成本。
2.2 端部毛刺原因分析首先,由于剪切刀片之间存在过大的缝隙,使得钢材在接受剪切的过程中发生了滑移,进而从缝隙中带出了舌头状的毛刺。
其次,在采用平剪剪切工藝时,受到轧件弯曲的影响,使得压扁的金属体积沿着轧件纵向堆积在了剪刃口处,并最终造成轧件在剪切时发生分离撕裂形成毛刺。
带肋钢筋四切分轧制常见故障及处理措施(酒钢科技)
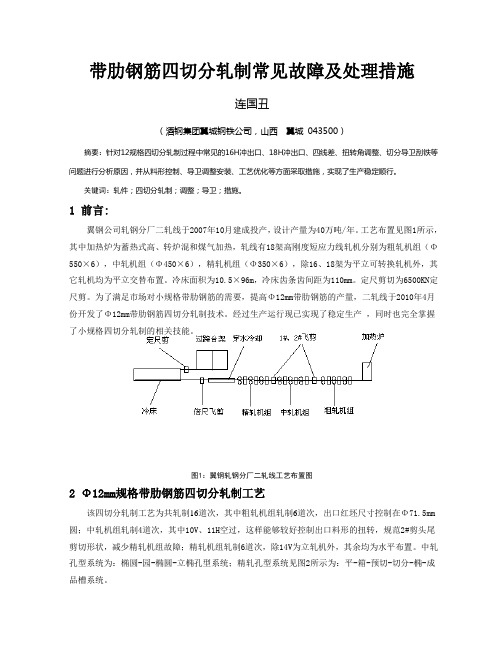
带肋钢筋四切分轧制常见故障及处理措施连国丑(酒钢集团翼城钢铁公司,山西翼城043500)摘要:针对12规格四切分轧制过程中常见的16H冲出口、18H冲出口、四线差、扭转角调整、切分导卫刮铁等问题进行分析原因,并从料形控制、导卫调整安装、工艺优化等方面采取措施,实现了生产稳定顺行。
关键词:轧件;四切分轧制;调整;导卫;措施。
1 前言:翼钢公司轧钢分厂二轧线于2007年10月建成投产,设计产量为40万吨/年。
工艺布置见图1所示,其中加热炉为蓄热式高、转炉混和煤气加热,轧线有18架高刚度短应力线轧机分别为粗轧机组(Φ550×6),中轧机组(Φ450×6),精轧机组(Φ350×6),除16、18架为平立可转换轧机外,其它轧机均为平立交替布置。
冷床面积为10.5×96m,冷床齿条齿间距为110mm。
定尺剪切为6500KN定尺剪。
为了满足市场对小规格带肋钢筋的需要,提高Φ12mm带肋钢筋的产量,二轧线于2010年4月份开发了Φ12mm带肋钢筋四切分轧制技术。
经过生产运行现已实现了稳定生产,同时也完全掌握了小规格四切分轧制的相关技能。
图1:翼钢轧钢分厂二轧线工艺布置图2 Φ12mm规格带肋钢筋四切分轧制工艺该四切分轧制工艺为共轧制16道次,其中粗轧机组轧制6道次,出口红坯尺寸控制在Φ71.5mm 圆;中轧机组轧制4道次,其中10V、11H空过,这样能够较好控制出口料形的扭转,规范2#剪头尾剪切形状,减少精轧机组故障;精轧机组轧制6道次,除14V为立轧机外,其余均为水平布置。
中轧孔型系统为:椭圆-园-椭圆-立椭孔型系统;精轧孔型系统见图2所示为:平-箱-预切-切分-椭-成品槽系统。
图2:精轧机组孔型系统3 常见故障分析:四切分轧制固然能大幅度提升小规格带肋钢筋的产量,但因其工艺的复杂对设备性能,生产准备,导卫安装调整,料形的精准控制,张力调整和钢温等过程控制的要求非常高。
Φ12mm螺纹钢四切分轧制工艺优化

钢等 ,平均每班故 障时间 4 0 m i n 左右 ,严重地
制 约 了生产 的正 常进行 。为此 ,展开 攻关 ,实 施
Te mp e r a t u r e
1 2 mm Re i n f o r c e d B a r ; Ro l l i n g ; F o u r - s t r a n d S p l i t t i n g ; P r o i f l e ; P a s s ; G u i d e ;
陆文韬等 : l 2 m I I l 螺纹钢 四切分轧制工艺优化
停 机 必 须 检查 K 2孔 型 的磨 损 情 况 ,发 现 缺 陷 , 及 时 换 孔 ;修 改 K 3出 口导 卫 双 刃 切 分 轮 角度 ,
( 3 )轧辊 、导卫方面。轧辊 4线磨损不均 造成后续机架堆钢 ,崩孔引起堆钢 ,K 2 磨损造
LU we n t a o ZHANG Bi n b i n
( B a r a n d S e c t i o n P l a n t )
Ab s t r ac t : The b r a i n s t o r m c o u n t e r me a s u r e s i mpl e me n t e d f o r t he f o u r - s t r a n d s pl i t t i n g r o l l i ng p r o c e s s f o r
中1 2 mm r e i n f o r c e d b a r p r o d u c t i o n w e r e i n t r o d u c e d i n r e s p e c t s o f p r o i f l e o p t i mi z a t i o n , g u i d e i mp r o v e me n t , r o l l e r p a s s r e f o r ma t i o n a n d t e mp e r a t u r e c e n c e t h e r e a c h a b i l i t y o f d e s i g n c a p a c i t y w a s >9 0 %, t h e r o l l i n g s c r a p r a t e w a s r e d u c e d t o 0 . 0 8 % a n d t h e r o l l i n g y i e l d wa s 1 0 3 . 1 %. Ke y W o r d s :
Φ12mm热轧带肋钢筋四线切分轧制工艺存在问题及解决措施

度 是 固定 的 , 而起 套辊起 套后 轧件 高度是 变 化 的 , 导
致 活套起 套后 轧件 经压 辊导 向与 下一架次 进 口导 板 发 生摩 擦 。 () 2 导板 无 冷 却水 , 件 与 导 板 摩 擦 后 导 板 温 轧
度过高 。
( ) D E双 排 导 卫 导 板 上 下 配 合 后 插 入 导 34 4
s i us w o e i r v s ero r n g oo e .
Ke o ds: ot—r ln yW r h olig;fn s i g r li i ih n olng; p o e sp o lm ;m e s r s r c s r b e aue
1
前 言
总第 11 9 期 21 0 1年 第 1 1期
河 北冶金
H EBE M E AL U R GY I T L
Toa l l tl 9
2 01 , u b r 1 1 N m e 1
1 mm 热 轧 带肋 钢 筋 2 四线切 分 轧 制 工 艺存 在 问题 及 解 决 措 施
轴窜 。
造成 切分架 次 出 口堆钢 的 主要 原 因有 切偏 头 、 切分 刀粘 钢等 。
9 . % 。针对 生产 初 期存 在 的粘 钢 、 钢等 问题 进 71 堆 行 了改 进 , 得 了 比较好 的效 果 。 取
2 四 线 切 分 轧 制 原 理
架 , 中 1 、8 2 其 6 1 、0架 为平 立 可转换 轧 机 , 、 粗 中轧 机
组 出 口设 有 1 、 # # 2 飞剪 , 于 轧制 过 程 中切 头 尾 和 用
收 稿 E 期 :0 1 7— O t 2 1 —0 2
的两切 分 , 过 这 两 个 步骤 实 现 四线 切 分 。与 传 统 通 的单 线 轧制工 艺 和二 、 线切 分轧 制工艺 相 比较 , 三 四
Ф12mm螺四切分轧制成品勾头冲出口故障处理分析
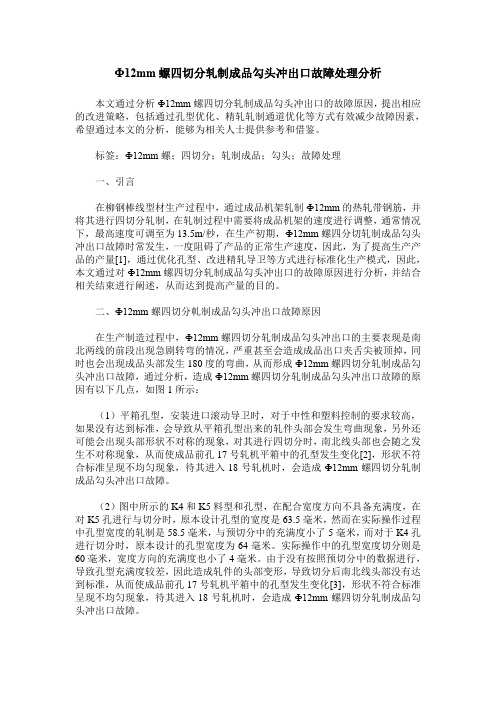
Ф12mm螺四切分轧制成品勾头冲出口故障处理分析本文通过分析Ф12mm螺四切分轧制成品勾头冲出口的故障原因,提出相应的改进策略,包括通过孔型优化、精轧轧制通道优化等方式有效减少故障因素,希望通过本文的分析,能够为相关人士提供参考和借鉴。
标签:Ф12mm螺;四切分;轧制成品;勾头;故障处理一、引言在柳钢棒线型材生产过程中,通过成品机架轧制Ф12mm的热轧带钢筋,并将其进行四切分轧制,在轧制过程中需要将成品机架的速度进行调整,通常情况下,最高速度可调至为13.5m/秒,在生产初期,Ф12mm螺四分切轧制成品勾头冲出口故障时常发生,一度阻碍了产品的正常生产速度,因此,为了提高生产产品的产量[1],通过优化孔型、改进精轧导卫等方式进行标准化生产模式,因此,本文通过对Ф12mm螺四切分轧制成品勾头冲出口的故障原因进行分析,并结合相关结束进行阐述,从而达到提高产量的目的。
二、Ф12mm螺四切分軋制成品勾头冲出口故障原因在生产制造过程中,Ф12mm螺四切分轧制成品勾头冲出口的主要表现是南北两线的前段出现急剧转弯的情况,严重甚至会造成成品出口夹舌尖被顶掉,同时也会出现成品头部发生180度的弯曲,从而形成Ф12mm螺四切分轧制成品勾头冲出口故障,通过分析,造成Ф12mm螺四切分轧制成品勾头冲出口故障的原因有以下几点,如图1所示:(1)平箱孔型,安装进口滚动导卫时,对于中性和塑料控制的要求较高,如果没有达到标准,会导致从平箱孔型出来的轧件头部会发生弯曲现象,另外还可能会出现头部形状不对称的现象,对其进行四切分时,南北线头部也会随之发生不对称现象,从而使成品前孔17号轧机平箱中的孔型发生变化[2],形状不符合标准呈现不均匀现象,待其进入18号轧机时,会造成Ф12mm螺四切分轧制成品勾头冲出口故障。
(2)图中所示的K4和K5料型和孔型,在配合宽度方向不具备充满度,在对K5孔进行与切分时,原本设计孔型的宽度是63.5毫米,然而在实际操作过程中孔型宽度的轧制是58.5毫米,与预切分中的充满度小了5毫米,而对于K4孔进行切分时,原本设计的孔型宽度为64毫米。
棒材摆剪故障原因分析和解决措施

【 Ke y w o r d s ] P e n d u l u m s h e a r , g u i d i n g c o l u m n , b l a d e , b e a i t n g
1 引言
3 存 在 问题
生产效率得到 了很 大提 高。
【 关键词】 摆剪 导柱 剪刃 轴承
Ca u s e An a l y s i s a n d S o l u t i o n s o n Ba r Pe n d u l u m S h e a r Fa u l t
一பைடு நூலகம்
9 一
第3 2 卷2 0 1 4 年第 4 期( 总第 1 7 2 期)
定 时 间后 , 首 先 在 受 力 最 大 和 表 面 强 度 较 弱 的 部
技术改造与改进
( 2 ) 改进锁紧缸油管 , 改进 的方法是将直管部 分改成 u 形, 使圆弧部分紧靠在刀座 的立面上 , 从 而避勉掉下 的钢头砸坏油管 , 改进后油管被 砸断 的设备故障基本杜绝 。 4 . 3 摆 剪导 柱 断、 下 剪胎 裂和连 杆 弯 造成 摆 剪 导 柱 断 、 下 剪 胎 裂 和 连杆 弯 的 原 因 是设备受力不平衡 。如连杆销轴掉未能及 时发现 导致单侧连杆掉 , 地脚螺栓松动严重甚至断裂 , 摆 剪周 围的废钢头清除不及时将拉杆别弯等等 。针 对此设备故障, 采取 以下措施 : ( 1 ) 以保证各部位连接正常为切人点 , 减少 因 销轴掉 、 键 窜出和螺栓松动不能及 时发现导致 的 重大设备故障发生 , 制定精密 的三级点检制度和 具体的点检方案。 ( 2 ) 采取专业技术检测手段 , 定期对摆剪导柱 进行探伤检测 , 防止 内部存在缺 陷发现不及 时造 成设备故 障。要求及时清理废钢头 , 避免外力造 成拉杆变形弯曲。
龙钢公司轧钢厂棒二线Φ16四切分轧制工艺浅析

龙钢公司轧钢厂棒二线Φ16 四切分轧制工艺浅析摘要四线切分轧制技术是在两线和三线切分轧制技术的基础上开发的,该工艺是把加热后的坯料先轧制成扁坯,然后再利用孔型系统把扁坯加工成四个断面相同的并联轧件,并在精轧道次上沿纵向将并联轧件切分为四个尺寸面积相同的独立轧件的轧制技术。
四线切分轧制技术的核心是先完成并联轧件的三切分,再完成并联轧件的两切分,通过这两个步骤实现四切分的目的。
四线切分轧制工艺与传统的单线轧制工艺和二、三线切分轧制工艺相比,在坯料控制、导卫调整、速度控制、轧机准备等方面都有更大的难度。
龙钢公司轧钢厂棒二线Φ16 四切分轧制工艺于 2019 年 8 月开发和投产,至今相关工艺已经逐步成熟,产量相对稳定,为以后的小规格五线及以上切分轧制工艺的开发奠定了基础。
关键词:四线切分;轧制技术;孔型系统一、棒线材切分轧制工艺概述切分轧制原理是在轧制过程中,将轧件用轧辊或者其他设备沿纵向切分成两条或多条轧件的一种轧制方式。
(一)发展过程1.年代初期,加拿大钢铁公司国际公司首先应用和发展切分轧制技术,日本钢管公司 ( N K K ) 于 1977 年 3 月由加拿大钢铁公司引进切分轧制新技术生产棒材 , 经过研究改进 , 在东伸钢铁公司姬路厂建立起切分轧制生产线。
1979 年 N K K 公司向国内大安公司和山口平有限公司等出售切分轧制技术 , 该项技术用于生产棒材。
70 年代初期 , 英国在斯德哥尔摩技术研究所专门的 Triplet 轧机上采用立轧法把板坯变成方坯。
首先是在板坯中间轧一条沟槽 , 然后用火焰将板坯切割成两条,最后轧成方坯。
我国从 50 年代起开始应用切分轧制技术,目前多数还是坯料切分,然后生产成型材和线材 , 切分的方式主要是:辊切切分、切分轮切分,现在已着手研究和应用在连轧机组上,充分发挥切分轧制提高生产率等优势。
(二)工艺特点1.生产率高轧制钢坯时的生产率为:⁄(1-2-1)A = 36001轧制成品时的生产率为:⁄(1-2-2)A = 36001式中:A——轧机生产率,t/h;——坯料重量,t;——轧机利用系数;1——轧制周期,s;——成材率,%。
“四切分轧制”的生产技术要点
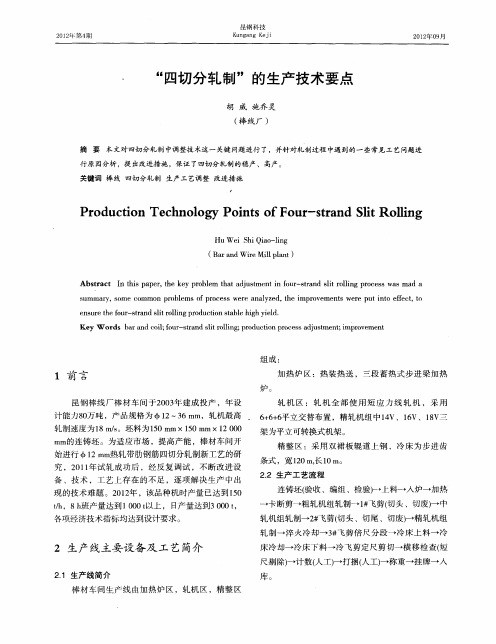
坏 ;2 分刀粘钢 :造成切分刀粘钢主要原因有 :①开 切
轧温度过高 ,切分带形状不规则 ,引起切分刀粘钢 ;
②切分刀被封闭在箱体 内,由于冷却不足 ,刀片两侧
会粘 附氧化铁皮 。③切分箱的安装 必须保证切分 环 、 切分轮 、切分刀三点一线 ,对中 良好 ,若 安装不 正 ,
1 四切 分 生 产 工 艺 相 对 于其 他 钢 种 较 为 复 2 杂 ,对 坯料质 量 、加热温 度及 轧制要 求都 很 高 。特 别 是 轧 制 过 程 中 ,更 是 需 要对 料 形 尺 寸 、轧 制 速 度 、导 卫调整 严格 要求 ,而且 需要 职工过 硬 的操作
水 平 。料形控 制是 四切分 生产 工艺 中最 为重要 的环 节 ,料 型 的控 制 又牵涉 到轧制 温度 、速度 、导 卫 、
H i h Q a—i u We S i i —n olg
( a n r lpa t B r dWi Mi ln ) a e l
Ab ta t nti p p r tek ypo lm a du t n nfu - t n l ol gpo e sw sma sr c I hs a e, h e rbe t t j s h a me t o r sr dsi rln rc s a da i a t i
行 原 因分析 ,提 出改进措施 ,保证 了四切分轧制的稳产 、高产。
关 键 词 棒 线 四切 分 轧制 生产 工 艺调 整 改 进 措 施
Pr u to c no o y Po n so o r。ta d S i Rol od c i n Te h l g i t fF u ‘sr n l l ng - t i
带肋钢筋四切分轧制常见故障及处理措施

带肋钢筋四切分轧制常见故障及处理措施
连国丑
【期刊名称】《酒钢科技》
【年(卷),期】2013(000)004
【摘要】针对12mm规格四切分轧制过程中常见的16H冲出口、18H冲出口、四线差、扭转角调整、切分导卫刮铁等问题进行分析原因,并从料形控制、导卫调整安装、工艺优化等方面采取措施,实现了生产稳定顺行。
【总页数】4页(P78-81)
【作者】连国丑
【作者单位】酒钢集团宏兴股份公司翼城钢铁公司山西翼城043500
【正文语种】中文
【中图分类】TG335.62
【相关文献】
1.带肋钢筋四切分轧制孔型系统分析 [J], 唐丽娟
2.Φ12mm热轧带肋钢筋四线切分轧制工艺存在问题及解决措施 [J], 祖超;史盼盼
3.φ12 mm热轧带肋钢筋四切分轧制开发实践 [J], 蒋子龙;夏洪林;吴豪
4.Φ16mm热轧带肋钢筋低温控轧四切分轧制技术开发 [J], 李俊芳
5.Φ12螺四切分轧制常见故障及处理措施 [J], 孙海潘
因版权原因,仅展示原文概要,查看原文内容请购买。
Φ12螺纹钢四切分轧制技术在棒材厂的应用与改进

Φ12螺纹钢四切分轧制技术在棒材厂的应用与改进摘要:本文叙述了棒材厂φ12螺纹钢生产的工艺选择、试轧时出现的问题和工艺改进以及对切分技术的成果分析和切分技术的展望。
关键词:螺纹钢四切分轧制孔型系统导卫1 前言切分轧制是在轧机上利用特殊的轧辊孔型和导卫或者其他切分装置,将原来的一根坯料纵向切成两根以上的轧件,进而轧制多根成品或中间坯的轧制工艺。
采用切分轧制技术可缩短轧制节奏,提高机时产量,显著提高生产效率,降低能耗和成本。
目前棒材φ12mm螺采用三切分轧制工艺,终轧速度为15米/秒,其最高小时产量为57.4支/小时,平均小时产量为50支/小时,平均日产为2380吨/天,与其他规格的平均日产2903—3189吨/天存在较大的差异。
为了更好的发挥切分轧制的经济效益,结合市场对小规格螺纹钢需求量较大的实际,棒材厂决定开展φ12螺纹钢四切分生产工艺改造。
这将大幅度提高小规格产能和生产效率,降低生产成本,提高经济效益。
2 主要设备概况2.1 加热炉加热炉为步进式加热炉,最大加热能力为11Ot/h。
采用钢坯尺寸为150mm ×150mm ×12000mm,重约2075kg。
2.2 轧机一棒轧线上共有20架轧机,粗轧6架550轧机(1-6架)、中轧6架420轧机(7-12架),精轧8架350轧机(7-20架,其中17、18架轧机为平立转换轧机);二棒轧线上共有18架轧机,粗轧6架550轧机(1-6架)、中轧6架420轧机(7-12架),精轧6架350轧机(7-18架),一棒采用平立交替布置,粗、中轧为无扭微张力轧制,精轧采用活套无张力轧制,粗中轧、中精轧之间各有一台飞剪,精轧后设有一台倍尺飞剪。
2.3 冷床冷床为126米齿条步进式冷床,可收集和冷却剪成倍尺的棒材。
2.4 冷剪冷剪剪切能力为850T,可将成排棒材按定尺剪切,剪切范围6~12米。
3 四切分技术的应用与改进四切分轧制,即在轧制过程中通过孔型,将1根轧件轧成具有4个相同形状的并联轧件,再通过切分导卫及孔型将并联轧件沿纵向切分成4个单根轧件。
∮14mm四切分轧制工艺的开发与应用

∮14mm四切分轧制工艺的开发与应用棒材厂张 月摘要本文通过对∮14mm四切分轧制工艺技术的研究与应用。
提高了小规格螺纹钢筋的产能,降低了生产成本,增强了产品的市场竞争力。
对螺纹钢的多线切分技术的推广具有较好的借鉴作用。
1 前言∮14mm四切分轧制工艺是在热轧过程中将轧件利用孔型的作用,轧成四个并联轧件,再利用切分设备(轧辊、导卫、切分轮等)把并联的轧件沿纵向切分成四根单体轧件,然后再轧成成品钢材。
一块钢坯在大部分道次中都是单根轧制,仅在最后几道次中进行四线轧制,然后切分成四根棒材。
本文对∮14mm四切分轧制技术进行自主开发和应用,积累多线切分轧制经验。
2 工艺概况涟钢棒二线共计有19架轧机,纵列式全连轧布置,其中1-4#轧机为Φ550闭口式轧机,5-8#轧机为Φ450闭口式轧机,9-12#轧机为Φ450短应力线轧机,13-19#轧机为Φ350短应力线轧机。
1-13#轧机为无孔型平立交替布置(∮14mm四切分轧制12#轧机空过)。
目前轧制品规∮12-∮22规格,坯料为150×150×12000mm连铸坯,末架最高速度13.5m/s,年生产能力100万吨。
保证中间坯头部被除鳞,同时对加热炉热负荷进行调整,提高均热段热负荷,或对均热段采用间拔操作方式,保证烧嘴在额定负荷下运行。
图6 中间坯头部/尾部异常高温3.5 半段爬坡型温度曲线图6 半段爬坡型温度曲线该类异常曲线下,异常点比正常温度低50℃以上,温度异常范围在板坯长度的一半以上,可以发生在板坯头部也可以发生在尾部。
产生的原因为某根水封槽缺水,造成吸冷风,或某侧烧嘴空/煤手阀与另一侧阀门开度严重不一致所导致。
4 结语通过对影响蓄热式加热炉纵向温度均匀性的分析和研究,提出加热质量的过程控制措施:a. 将加热炉换向阀故障个数列入加热炉关键过程控制参数,将换向阀故障个数控制在2个以下(单座加热炉)。
b. 对蓄热小球质量进行严格把控,保证其抗热振性和抗渣性。
浅析唐钢棒材厂四线切分轧制技术

圆形 轧件进 平辊 时不 会产 生不 均匀 变形 。中轧 机 新 增加 的第 1 # 机与精 轧 机 1 # 机 的距离 缩短 到 9 4轧 5轧
m, 而且 由于 1 # L 的孔 型 为 立 箱形 , 4  ̄机 采用 小 压 下
量, 主要 作用 是 使 1 # 辊 加 工 出 来 的 鼓 形 断 面 轧 3平
DI SCUS ON SI ABOUT FOUR —L E PLI S TD ROLL玎 G G D TAN G TEEL S
Ni a g e g,G e Ya o u Li n p n d ng, Ya g Ba h ng n oz o
( . te l n l,Ta g h n Io n te mp n No 2S elRol g Mi i l n sa rn a dS e l Co a y,He e rn a d Se lGru b i o n te o p,T n s a ,He I a gh n — bi030 e , 6 0 0)
虽 然表面 现象 都 是 切 分架 次 堆 钢 , 是 导 致 切 但
分架 次堆 钢频 繁 的原 因有多种 。按 照切 分架 次堆 钢
的原 因分类 , 有如 下几 种 :
3 2 1 切 分 架 次钢 料 形状 不 好 ..
与三线切分 轧制相 比 , 四线 切分轧制 对轧辊 的精 度要 求更高 。在 现有 条件允许 的前提下 , 为最 大限度
在 K 3孔 ( 分孔 型 ) 工 成 断 面积 相 同 的 并 联 轧 切 加
9’
件, 连接 带厚 度一 般 为 1 0 mm, . 经过 切 分 导 卫 的加 工分 成 四条独 立 的轧件 , K 在 2孔加工 成 四条扁椭 形
Ф12mm螺四切分轧制工艺的优化
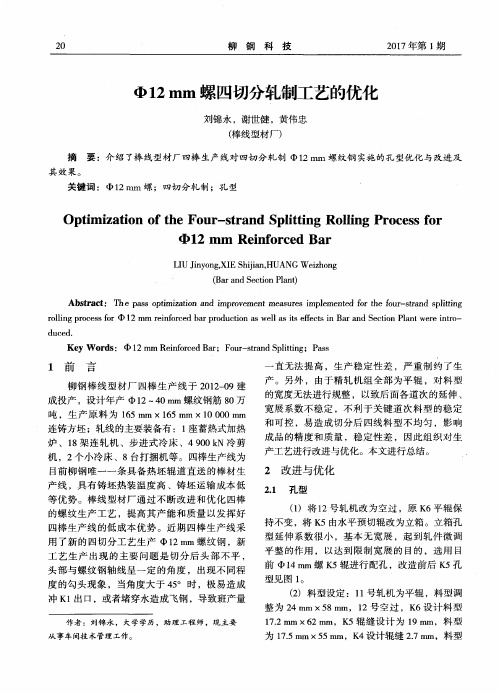
其 效果 。 关键 词 :
Op t i mi z a t i o n o f t h e Fo u r - s t r a n d S p l i t t i n g Ro l l i n g Pr o c e s s f o r
1 2 mm Re i n or f c e d Ba r
2 0 1 7年第 1 期
刘锦永等:中 1 2 m m螺四切分轧制工 艺的 优化
2 1
度 均 匀 性 ,轧 制 温 度 控制 以 2号 飞 剪 处 温 度 为
准 ,控制在 1 0 4 0℃ ±1 0℃;上冷床温度 :6 9 0 ℃~ 7 0 0℃。三是开展轧制线对 中,重点对活套 架 进 出 口导槽 ,喇 叭 口 ,导 卫 进 出 口安 装 ,K1
1 前
言
直 无 法 提 高 ,生 产 稳 定 性 差 ,严 重 制 约 了生
柳 钢 棒 线 型材 厂 四棒 生 产 线 于 2 0 1 2 — 0 9建 成 投产 ,设计 年 产 1 2~ 4 0 m m 螺纹 钢筋 8 0万
吨 ,生 产 原 料 为 1 6 5 mm ×1 6 5 mm ×1 0 0 0 0 m m
( 2 ) 料型设 定 :1 1 号 轧机 为 平辊 ,料 型调
整为 2 4 mm×5 8 m m,1 2号 空 过 ,K 6设 计 料 型 1 7 . 2 m m×6 2 m m,K 5辊缝 设 计 为 1 9 mm,料 型 为1 7 . 5 mm×5 5 m m,K 4设计 辊缝 2 . 7 mm,料 型
出 口至 穿 水 管 进 口 ( 空 过竹 节 管 导 槽 ) 水 平 校
对 ,避 免 与 K l出 口不水平 造 成钢 头 碰对 盖板 或
- 1、下载文档前请自行甄别文档内容的完整性,平台不提供额外的编辑、内容补充、找答案等附加服务。
- 2、"仅部分预览"的文档,不可在线预览部分如存在完整性等问题,可反馈申请退款(可完整预览的文档不适用该条件!)。
- 3、如文档侵犯您的权益,请联系客服反馈,我们会尽快为您处理(人工客服工作时间:9:00-18:30)。
棒材四切分问题及解决方法
编写作者:邱世浦
一切分刀粘钢
切分刀粘钢是指切分轧制生产过程中,切分刀两侧或一侧粘渣,最终导致切分故障的
现象,切分刀粘钢的原因主要有以下几个方面;
1.开轧温度过高。
如果开轧温度过高,在精轧区切分过程中,切分楔处压下量非常
大时,因急剧变形产生大量的热,造成局部金属温度迅速升高和切分带形状不规矩,
引起切分刀粘钢。
2.来料过大或过小,切分轧制遵循斧头原理,来料必须与16架切分楔处角度匹配。
15料形过大或过小,都会造成切分困难,导致切分带过大,轧件前进过程中,切分带与切分刀发生摩擦,引起粘钢。
3.切分轮切偏或没对准轧槽。
切分导卫安装,必须保证切分楔,切分轮,切分刀三
点一线,
对中良好,如果安装不正,导致料与切分轮不能对正而切偏,造成切分带过大,与切
分刀发生摩擦,引起粘钢。
4. 切分刀冷却不好,切分导卫必须保证充分冷却,尤其是切分刀,正常生产过程中因坯料,轧槽磨损等原因,造成轧件表面带细小氧化铁皮,切分带形状不规矩,与切分
刀摩擦粘在两边,如果冷却效果不好,就会越粘越多,最终导致冲出导卫堆钢,和下
游轧机无法调整。
5. 切分刀间距不合适,轧件进入切分盒后,成一定的角度,如切分刀间距未设定好,就会出现轧件件与切分刀发生摩擦而粘钢。
6. 切分孔型设计不合理,15,16架孔型系统设计非常重要,切分角设计必须匹配。
7.轧机刚性差,弹跳大,料形控制差。
8.切分刀长度不合适,三切分更为明显,离切分轮过近造成排渣不方便,引起粘钢。
9.切分轮角度设计不合理,切分不顺利。
10. 12到18架料形没有控制好,料发生便斜扭转,过大过小,头大尾大造成粘刚。
11.钢坯自身有问题有夹杂气泡开花。
12.关键架次轧槽老化或蹦槽。
13.关键架次导卫梁和导卫未对正轧制中心。
14.各架次张力没控制好或刚温不稳定。
15. 导板或导板磨损过度或导卫导槽装配有问题。
切分刀粘钢解决方案。
1. 按工艺要求控制好钢温,在满足主电机负荷的情况下,钢温应控制在1000到1050摄氏度,最好不要超过1100摄氏度。
2. 严格按工艺要求控制好料型尺寸,粗轧六架料型尺寸偏差控制在±0.5 mm以内,中轧尺寸偏差控制在±0.3mm以内,精轧尺寸偏差控制在0.2 mm以内。
预切分和切分架次料型应严格按工艺要求控制。
保证切分架次的充满度。
3. 切分导卫安装要精确,保持切分刀,切分轮,切分槽在同一直线上,同时加强切分导卫及轧槽的冷却,及时观察料型的转钢程度。
4,设计人员对孔型要做好设计校对工作。
4.切分刀的间距是一定的,仔细检查切分刀间距是否合适。
5.按要求控制好各道次料型。
6.及时做好轧线在线检查。
正确安装导卫及导卫梁。
二.切分轧制线四线差问题。
切分轧制工艺虽然有效提高了作业率,使产量大幅度上升,但是受钢温波动,轧槽磨损,孔型系统设计,导卫安装,轧槽加工精度等各方面因素影响,每根轧件尺寸都不可能完全一样,即存在线差,若在获得较高经济效益的同时,又要求保证钢材质量,这就要求必须通过各种手段来缩小各线差距。
线差产生的主要原因有以下几个方面;
1. 预切分15架或切分16架进口导卫没对正轧线,偏向一侧,此时来料被切分后偏向的一侧由于断面积大,导致此线成品尺寸大。
2. 孔型磨损不一致。
由于轧槽冷却不一致,前道次料形不规矩或导卫孔型设计等各方面因素影响,磨损严重的一线断面积就会增大,造成成品尺寸的。
3. 两侧辊缝不一致。
在换辊调试时,由于15—18架两侧辊缝控制不一致,辊缝大的一侧孔型面积就大,从而导致成品存在差异。
4. 轧槽加工精度不高。
这主要与轧辊材质,制修车间成型刀具磨损及修复精度,加工方式有关。
5. 12---16架次料形控制有问题。
切分生产非常注重12—16架次料形的匹配,匹配不好就会造成线差。
6. 线差的主要原因一般集中表现为K4轧槽老化问题,和K3K4导卫对正问题,以及K6料形变化问题。
四线差的解决方法
1.准确安装导卫。
在换辊前要预调好导卫,确保各方位对中,并固定好。
2.改进15,16架冷却水管,加强冷却效果,生产过程中做好点检。
3.换辊时点动轧机,用同样的焊条测两侧辊缝,偏差控制在0.1mm以内。
4.改进轧辊材质,15,17,18采用高速钢轧辊。
联系加工部门提高加工精度。
5.严格按工艺要求控制好各道次料形,按要求用样棒调整导卫间隙。
三.18架顶出口故障
切分轧制生产过程中,18架顶出口故障发生较为常见,是制约四切分生产的一个主要故障点,主要表现为内侧或外侧两线钢前端向切分带方向急剧弯曲,将导管的舌尖顶掉,或弯曲180度从出口冲出来卡在导槽内堆钢。
产生这种现象的主要原因有以下几个方面;
1. 孔型设计存在缺陷,主要是孔型设计时参数的分配存在问题,造成调整难度过大,对职工整体素质和操作水平要求极高。
2. 17架孔型槽口设计过大,切分带无法很好加工。
3. 料形控制不准确。
15架充满度不好,或16架料形过小,切分后两线前端严重不对称,在17架变形不均匀,且对切分带加工不好,进入18架产生顶出口现象,或者12—16架料形过大,18架变形剧烈且不均匀,造成顶出口现象。
4. 15架16架导卫间隙控制不合适对中性不好,轧件前端弯曲在切分时切偏,造成头部尺寸过大或过小,经17架后,造成18架顶出口。
5. 切分带处温度较高,在18架不易脱槽。
6. 导卫设计有问题或18架出口内腔尺寸过大,离轧辊相对较远,不能有效阻止18架头部形状变化。
7. 18架轧机导卫,导卫梁未按要求装配对正。
8. 17架料形与进口导板安装配合不好。
9. 切分导卫未按要求装配,或切分轮偏心方向不对或方向不统一。
10. 前面架次间转钢,尤其12—13架之间。
11. 17架出口扭转角度没调好。
12. 轧槽磨损严重。
13. 切分轮和切分导卫设计问题。
14. 连接轴间隙太大。
18架顶出口故障的解决方案
1.优化孔型系统,重新分配各道次压下量。
确定生产工艺。
2.摸索最佳工艺,重点是加热参数,各架次料形尺寸,各架次速度及电流参数,形成标准在各班组严格执行。
3.提高轧机导卫装配水平,重点做好精轧15-16架轧机导卫的装配,确保轧机刚性及轴向稳定性。
严格做好导卫预调及安装工作。
4.对切分带进行重点冷却。
5.改进18架导卫形式和内腔尺寸,控制在一定范围,使舌尖尽量靠近变形区,提高导向性。
6. 17架料形与进口导板安装应遵循以下原则;17架孔型未充满时,导板不易偏向切分带。
17架孔型充满时,导板应偏向切分带反方向.
7.及时检查轧辊磨损情况。
8.改变导卫形式。
l还有三号剪信号,穿水,孔型设计,初中轧张力控制,精轧调整,导卫设计,标注制定,料形控制
QQ2298345698搜索。