棒材切分轧制导卫系统的应用与改进
南钢棒材生产线切分轧制的运用

南钢 棒 材 生产 线 切分 轧 制 的运 用
项 幼 阳 Leabharlann ( 南昌钢铁有限责任公司 , 江西 南 昌 30 1 ) 30 2
摘
要 : 介绍了南钢棒材厂生产 ql In中In @1 mn J2l , 4 l l l m, 6 l螺纹钢材二线切分轧制工艺, 切分孔型
及导卫装嚣的运 用 , 以及切分轧制提高 产量 , 降低成本的效果。
关
键
词 : 棒 材 ; 分 轧制 ; 切 运用 文献标 识码 : B
中图分 类号 : T 3 5 1 G 3 .9
Ap iat fSp itng Ro ln t t r Ro ln n n Na t e pl c i o lti li g a he Ba l g Li e i nse l on i
设 计年 产量 :0万 t 4 。 最 大成 品速 度 :8m s J / 。
2 2 工艺流 程 .
整体年设计能力4 万 t 0 , 全部采用国产化设备 ,0 1 20 年2 1 1 月 83 投产。现主要生产 J m, l m 2m 4 m,
J 6 mm, 2 0 mm , 2 2 mm, 2 5 mm, 2 8 mm , 3 2
・ 5・ 3
3 切分轧制工艺分析 与开发应用
3 1 切 分轧制 .
带连接成一体的两根 轧件 。泼轧件在离开倒数第
三机 架进入 切分 轮导 卫 装 置 后 , 即被 其 中 的两 个 切 分轮 “ 撕开 ” 为两个 单独 的 圆轧 件 也 就是 说 , 切 在
切分轧制是在热轧过程中, 用特殊 的轧辊孔型 和导卫装置或其它切分设备将轧件沿纵 向剖分成 2 条或多条轧件, 从而将延伸系数减小到原来的I2 /, l3 变单条轧制为多条轧制的生产工艺。实现小 / 等, 轧机吃大坯料, 减少轧制道次和轧制时间 , 显著提高 轧机产量 , 降低能耗和成本 。目前螺纹钢切分轧制 主要用 的是特 殊 的轧 辊孑 型加 切分 轮装 黄 。孔型 主 L
棒材切分导卫原理
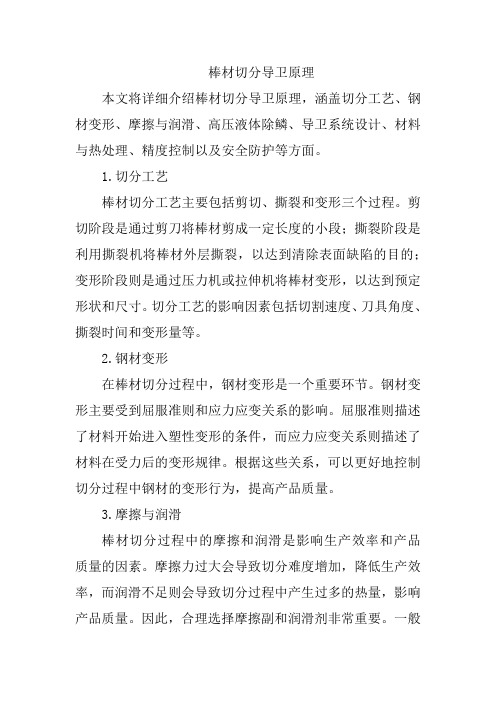
棒材切分导卫原理本文将详细介绍棒材切分导卫原理,涵盖切分工艺、钢材变形、摩擦与润滑、高压液体除鳞、导卫系统设计、材料与热处理、精度控制以及安全防护等方面。
1.切分工艺棒材切分工艺主要包括剪切、撕裂和变形三个过程。
剪切阶段是通过剪刀将棒材剪成一定长度的小段;撕裂阶段是利用撕裂机将棒材外层撕裂,以达到清除表面缺陷的目的;变形阶段则是通过压力机或拉伸机将棒材变形,以达到预定形状和尺寸。
切分工艺的影响因素包括切割速度、刀具角度、撕裂时间和变形量等。
2.钢材变形在棒材切分过程中,钢材变形是一个重要环节。
钢材变形主要受到屈服准则和应力应变关系的影响。
屈服准则描述了材料开始进入塑性变形的条件,而应力应变关系则描述了材料在受力后的变形规律。
根据这些关系,可以更好地控制切分过程中钢材的变形行为,提高产品质量。
3.摩擦与润滑棒材切分过程中的摩擦和润滑是影响生产效率和产品质量的因素。
摩擦力过大会导致切分难度增加,降低生产效率,而润滑不足则会导致切分过程中产生过多的热量,影响产品质量。
因此,合理选择摩擦副和润滑剂非常重要。
一般情况下,选择具有高摩擦系数和良好润滑性能的摩擦副和润滑剂是最佳选择。
4.高压液体除鳞在棒材切分过程中,高压液体除鳞是一种有效的表面处理方法。
通过使用高压水、乳化液或其他液体对棒材表面进行冲洗,可以清除表面的鳞片、氧化皮和其他污染物。
高压液体除鳞不仅可以提高产品的表面质量,还有助于提高刀具的寿命。
在选择清洗剂时,需要考虑到清洗剂的化学性质和压力范围,以确保其能够有效地清除污染物,同时不会对棒材和设备造成损害。
此外,为了确保除鳞效果和生产效率,需要选择合适的密封材料,以保证清洗剂和棒材表面之间的密封性。
5.导卫系统设计棒材切分导卫系统是保证切分过程顺利进行的关键。
导卫系统设计需要考虑的因素包括导卫形式、材料和热处理工艺。
导卫形式主要有滑动式、滚动式和浮动式。
选择合适的导卫形式需要考虑棒材的直径、长度、表面质量以及切分过程中的摩擦和变形等因素。
棒材生产切分工艺的优化与应用
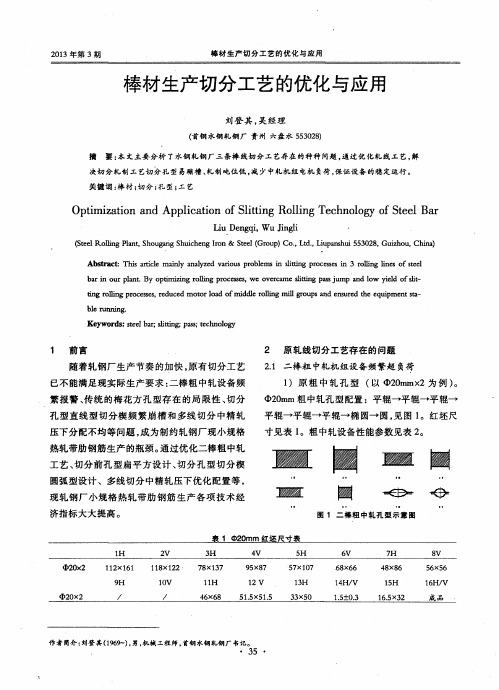
决 切 分 轧 制 工 艺 切 分 孔 型 易 蹦槽 、 轧 制 吨 位低 , 减 少 中轧机 组 电机 负荷 , 保 证 设 备 的稳 定 运行 。 关键词 : 棒材 ; 切分 ; 孔型 ; 工艺
Op t i mi z a t i o n a n d Ap p l i c a t i o n o f S l i t t i n g Ro l l i n g T e c h n o l o g y o f S t e e l B a r
时达 到 1 4 O %( 非 轧件 头 部 ) ; ( 2 )钢坯 加 热 温 度 高, 加 热 炉燃 耗 大 ; ( 3 ) 轧 线 影 响时 间 长 、 机 时 产 量低 、 轧机 作业 率低 。 3 ) 原 因分 析 。( 1 ) 进粗 轧温 度为 9 8 0  ̄ C 时, 粗 中轧 轧 机负 荷见 表 3 。从 表 3中以可 看 出 , 生 产
盈
《# 》 }
图 1 二 棒粗 中轧 孔 型 示 意 图
0 mm 红坯 尺寸 表
作 者 简介 : 刘登其( 1 9 6 9  ̄ ) , 男, 机械工程师 。 首钢水钢轧钢厂书记。 35 ・
・
水 钢 科技 S HU I G A NG S C I E NC E& T E C H N O L O G Y
b a r i n o u r p l nt a . B y o p t i mi z i n g r o l l i n g p r o c e  ̄ e s , we o v e r c a me s l i t t i n g p a s s j u mp a n d l o w y i d d o f s l i t -
第1 2 5期
2 ) - 棒 生 产 中存 在 的问题 。( 1 ) 轧制过 程 中
棒材车间自动分钢优化与改进

棒材车间自动分钢优化与改进摘要:自动数支器作为轧钢棒材线生产过程质量控制关键装备,其数支精度直接影响到轧区料型调整和成品尺寸控制,数支错误将给生产过程控制造成干扰,同时精整对多支少支的处理造成作业量增加。
新疆天山钢铁巴州有限公司轧钢厂通过自动分钢系统优化,提升了工作效率,改善了数支准确率和成品包外观质量。
关键词:自动;分钢;优化;效率;质量引言轧钢产线生产能力其根本决定于设备能力。
棒材产线生产,倍尺材在经冷床收集冷却后由定尺剪剪切为定尺材,通过输送辊道和移钢小车输送至收集平台,实现数支分钢和收集。
新疆天山钢铁巴州有限公司轧钢厂棒材产线,精整区域工艺设计配置120米冷床,1.2米输送辊道,850吨冷剪,1号、2号两个收集平台,收集平台设置4段链传输棒把,自动数支分钢系统完成数支和分把。
该产线设计产能60万吨/年,现因工艺优化改进产能达100万吨/年,在工艺优化的同时精整区域匹配了1.5米输送辊道和1200吨定尺剪以承载效率提升后的产能负荷,收集平台区域设备保留原装备能力。
1生产过程现状产能提升后定尺剪剪切的棒把增大,定尺材经输送辊道和移钢小车输送至收集平台后易形成交叉和堆叠,平台链条输送过程定尺材不能拉开间距,钢材重叠缠绕情况不能改善,自动数支分钢系统易出现错误,数支准确率偏低,尤其是在12-16小规格生产过程数支错误率达到10%,每班班需人工数支整改异常支数成品包,造成职工低效劳动工作量增加。
分钢后棒把呈倾斜转态运输至落料收集装置,下落过程两端不同步,收集后的成品包外观呈缠绕扭曲状态,流入市场后严重影响品牌形象。
钢材的扎制一般分为两种:一种是普通扎制,在扎制后按照每捆的实际重量出厂计价;另一种为负公差扎制,在扎制后按照理论计算重量出厂计价。
在两种扎制制度中,由于负公差扎制的理论重量比实际重量大,如φ12 螺纹钢的理论重量比实际重量高出5%以上[1]。
2问题原因分析2.1 收集品台效率低导致前端高效生产的定尺材不能及时数支分把收集打包,前段倍尺材过度冗余,造成冷剪剪切棒把增大,棒把越大收集和数支分钢效果越差,造成恶性循环。
棒材轧制扭转辊的技术改造及运用效果

棒材轧制扭转辊的技术改造及运用效果赵永生杨家勇徐国玉摘要:本文对信钢棒材线粗、中轧的扭转导卫进行了技术改造,从当初的滑动导卫到滚动导卫直到现在的翻钢辊的投入使用进行了综合分析论证,在实际运行中通过轧制实践证明显示出良好的运行效果。
关键词:扭转导卫、翻钢辊、翻钢角度、生产实践一、前言信钢棒材线自02年投产以来,随着生产节奏的加快及操作员水平的提高,粗、中轧扭转导卫已越来越不适应快速连续的生产节奏,由于扭转导卫工艺事故多,调整困难且停机更换时间长,严重地制约着产能的提高,轧钢厂针对现有状况,先后对K16、K14、K12的出口扭转辊进行技术改造,新上线的翻钢辊克服了原扭转导卫的缺陷,不仅扭转到位、过钢量大为提高,而且事故次数大为减少,从而使轧机的日历作业率也得以大幅度的提升。
二、工艺技术分析1、棒材线粗、中轧工艺流程钢坯从加热炉出来后,经过粗轧K17~K13这5座轧机的连轧出了K13后进入粗轧机后辊道,通过中轧机前辊道进入中轧K12,经过中轧四架轧机后进精轧直至出成品上冷床。
由以上轧制工艺流程及各机架的料形尺寸要求可以得出:为了保证轧件在轧制过程中内部结构的均匀性以及为获得各机架的规定料形,在对于平辊轧制过程中必须在偶数辊道上设置相应的扭转机构。
4、出口扭转导卫的结构及工作原理以K14流动导卫为例,其结构简图如下:其工作原理是:轧件从K14出来后(其料形为77×135,横截面为椭圆),经过K14出口导卫时受到上、下扭转辊的支撑作用,且产生了一个力偶,使其发生相向旋转,由此而产生了扭转,到下一架轧机K13咬入之时,轧件头部正好扭转了90℃5、扭转辊的完善过程投产之初,粗、中轧的扭转导卫采用的是夹板式滑动扭转,在实际运行过程中,暴露出磨损严重,扭转不到位(或过多)及产品表面质量缺陷严重等缺陷,于是从2003年开始先后将粗、中轧扭转导卫换装了导辊能随着轧件转动的滚动导卫,该种导卫减少了滑动导卫易易造成的各类缺陷,产品质量也相应地得到了保证,但同时又产生了导辊因受钢温变化、轧件冲击、冷却水等因素的影响而易破碎的问题,除了易诱发工艺事故,增加了换导卫的次数、加大了轧钢工的劳动强度,更因为频繁更换更换造成停机时间长。
导卫说明
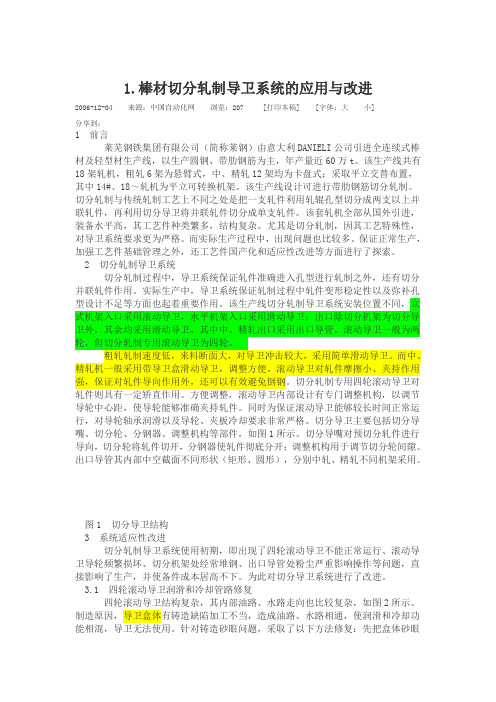
1.棒材切分轧制导卫系统的应用与改进2006-12-04 来源:中国自动化网浏览:207 [打印本稿] [字体:大小]分享到:1 前言莱芜钢铁集团有限公司(简称莱钢)由意大利DANIELI公司引进全连续式棒材及轻型材生产线,以生产圆钢、带肋钢筋为主,年产量近60万t。
该生产线共有18架轧机,粗轧6架为悬臂式,中、精轧12架均为卡盘式;采取平立交替布置,其中14#、18~轧机为平立可转换机架。
该生产线设计可进行带肋钢筋切分轧制。
切分轧制与传统轧制工艺上不同之处是把一支轧件利用轧辊孔型切分成两支以上并联轧件,再利用切分导卫将并联轧件切分成单支轧件。
该套轧机全部从国外引进,装备水平高,其工艺件种类繁多,结构复杂。
尤其是切分轧制,因其工艺特殊性,对导卫系统要求更为严格。
而实际生产过程中,出现问题也比较多。
保证正常生产,加强工艺件基础管理之外,还工艺件国产化和适应性改进等方面进行了探索。
2 切分轧制导卫系统切分轧制过程中,导卫系统保证轧件准确进入孔型进行轧制之外,还有切分并联轧件作用。
实际生产中,导卫系统保证轧制过程中轧件变形稳定性以及弥补孔型设计不足等方面也起着重要作用。
该生产线切分轧制导卫系统安装位置不同,立式机架入口采用滚动导卫,水平机架入口采用滑动导卫;出口除切分机架为切分导卫外,其余均采用滑动导卫,其中中、精轧出口采用出口导管。
滚动导卫一般为两轮,但切分轧制专用滚动导卫为四轮。
粗轧轧制速度低,来料断面大,对导卫冲击较大,采用简单滑动导卫。
而中、精轧机一般采用带导卫盒滑动导卫,调整方便。
滚动导卫对轧件摩擦小、夹持作用强,保证对轧件导向作用外,还可以有效避免倒钢。
切分轧制专用四轮滚动导卫对轧件则具有一定矫直作用。
方便调整,滚动导卫内部设计有专门调整机构,以调节导轮中心距,使导轮能够准确夹持轧件。
同时为保证滚动导卫能够较长时间正常运行,对导轮轴承润滑以及导轮、夹板冷却要求非常严格。
切分导卫主要包括切分导嘴、切分轮、分钢器、调整机构等部件,如图1所示。
棒材2号飞剪切头轧废的分析与改进

棒材2号飞剪切头轧废的分析与改进摘要:本文主要针对棒材2号飞剪在切头后,钢头不能正常掉落到下方废料收集装置的原因进行分析。
对剪前热检光栅HMD信号异常、飞剪剪刃导致轧件切头切不开的问题进行改进,着重对剪后导板装置进行了改造,有效的解决了飞剪在切头过程中将钢头带入下游轧机或导槽,阻碍轧件的正常运行,使得下支轧件无法正常轧制造成轧废的问题。
实践证明,采用改造后的剪后导槽生产运行稳定,2号飞剪切头稳定掉落入下方的废料收集装置,降低了轧废,提高了作业率,有效降低了生产成本。
关键词:飞剪、切头1前言二棒生产线为仿一棒Danieli棒材生产线建造,设备全国产化,由18机架平立布置的短应力线轧机组成,分为粗、中、精轧机组,以6+6+6的数量化分,全线轧机成平立交替式布置,其中,精轧机组的16、18架轧机为平立可转换轧机。
轧件在1~10架轧机之间采用微张力轧制技术,10~18架轧机之间采用活套无张力轧制。
装机总容量为31224KW。
一直以165×165mm方坯作为主要原料,设计规格为螺纹钢Φ10-Φ50mm。
目前生产线主要采用切分轧制的生产工艺,主要轧制规格为Ф10-Ф22mm螺纹钢筋。
2生产中存在的问题及原因分析2.1 2号飞剪结构及功能2号飞剪安装在中轧、精轧之间,为回转式飞剪。
其剪切系统由剪前导槽、剪体、剪后导槽、气缸带动的翻板、溜槽等组成。
最大剪切面积2901mm2,剪切速度2.0~9.6米/秒之间。
设计的主要功能为进行棒材的切头、切尾以及出现轧废等事故的碎断。
2.2 2号飞剪切头2号剪切头功能主要是对轧件头部降温较快产生的黑头以及不均匀变形造成的缺陷进行切除,避免切分不均匀造成的轧废。
在切头功能时,热检HMD检测到轧件时,即刻启动计数器记录轧机编码器的脉冲,按照轧辊直径,计算轧件运行过的距离及速度,同时根据剪刃位置及热检到剪切点的距离L,确定启动飞剪的时刻,如果轧件头部到达预定位置,PLC即通过驱动电机运行,启动飞剪按一定的速度曲线完成剪切,剪切完成后,开始制动,并使飞剪复位到一固定位置,准备下一次的剪切[1]。
Φ14棒材生产中三切分轧制技术研究

Φ14棒材生产中三切分轧制技术研究摘要:本文叙述了棒材生产中φ14螺纹钢三切分的工艺选择、调试时出现的问题、改进方案及效果。
关键词:螺纹钢三切分工艺方案1、前言切分轧制是在轧机上利用特殊的轧辊孔型和导卫或者其他切分装置,将原来的一根坯料纵向切成两根以上的轧件,进而轧制多根成品或中间坯的轧制工艺。
采用切分轧制技术可缩短轧制节奏,提高机时产量,显著提高生产效率,降低能耗和成本。
目前切分轧制技术已发展到五切分轧制,且两线切分轧制技术和三线切分轧制技术作为成熟技术已经普遍应用在小规格螺纹钢的生产中。
本文所述棒材厂从2005年开始逐步应用切分轧制技术,现已成功开发了φ14、φ16、φ18螺纹钢二切分、φ12螺纹钢三切分轧制技术。
2010年,为了实现147万吨的年产量目标,棒材厂决定充分发挥切分技术的产能优势,在ф12螺纹钢三切分的基础上实施ф14螺纹钢的三切分轧制。
2、设备配置情况车间的工艺布置为粗轧7架平轧闭口轧机、中轧为平立交替的6架两辊闭口轧机、精轧为平立交替6架预应力轧机。
、3、工艺方案的选择3.1 工艺布局的确定在φ12螺纹三切工艺和φ14螺纹两切分工艺的经验基础上,对一道预切与两道预切的方案进行了比较:如采用一道预切,则预切分孔(k4)的压下和延伸比较大,轧制负荷大、轧制不稳定,且其切分楔处的压下系数远大于槽底的压下系数,造成切分楔处磨损严重;来料进预切分孔时的对中性差,进而导致预切料型进切分孔时不均匀,这样3支成品之间的尺寸不均匀,负差也不易控制。
采用两道预切,可减小k4孔(第二道预切)的变形量,降低k4孔的轧制负荷,减轻其变形不均匀性,提高轧制稳定性;同时带有凹陷部位的来料进k4孔时,容易对中,对轧辊切分楔的冲击较小,成品尺寸较均匀;由于k4变形系数小,故改变k4的压下量对轧件的断面面积影响较小,降低了成品尺寸随k4料型变化而变化的敏感性,提高了轧制的稳定性及料型调整的方便性和精确性。
3.2 孔型设计切分工艺的孔型设计中预切分和切分孔的设计尤为重要,其次是立箱孔型,这几道次的孔型设计,关系到切分轧制是否能成功。
棒材3线切分轧制技术的应用与改进

2 3线切分轧制技术的应用及改进
2.1 切分轧制技术的优点
(1)提高生产率
采用切分轧制不仅可减少轧制道次,减少轧制时间,而且,对棒材轧机,同样架次可采用较大规格的坯料生产较小规格的产品,产量不受影响。如单线生产Φ12、Φ14mm带肋钢筋,由于受总变形量的限制,通常采用小于140mm×140mm的坯料,这不仅增加坯料的规格种类,给炼钢、连铸及轧钢的生产组织带来影响,而且机时产量低。根据棒材轧机140t/h的设计能力,Φ12、Φ14mm带肋钢筋,采用3线切分轧制最合理,机时产量比2线切分提高1倍以上。
③由于3线切分上冷床不顺利,因此改进了拨钢器的设计,使之既能适应1线切分生产,又能满足3线切分生产。
④为精确定位,提高车削精度,设计了连体样板以检验轧槽。在车床上安装了数显表,以精确定位,保证车槽精度,提高配辊的精确度。
⑤由于切分轮设计不合理,第1次生产Φ14mm带肋钢筋时,中线产生大量折叠废品,因而改进了切分轮设计。并针对切分轮不耐磨现象,与生产厂家共同进行多次试验,最后选择了一种新的热作模具钢。
精整区采用裙板辊道上冷床,步进式冷床132.5m×11.5m。出口辊道将钢材送入定尺剪定尺后,由链床送到打包收集区,包装入库。
2.2 产品状况
产品规格共有39个,圆钢规格为Φ14~Φ50mm,带肋钢筋规格为Φ12~Φ40mm。Φ12、Φ14mm带肋钢筋用3线切分技术,Φ16、Φ18mm带肋钢筋用2线切分技术,可根据用户要求生产6~12m任意长度的定尺尺寸范围内的各规格带肋钢筋。
/% 成材率
/% 烧损
/kg.t-1 油耗
/kg.t-1 机时产量
/t.h-1 成本
/元.t-1
12 97.42 95.03 32.00 98.00 61.75 2323.05
棒线轧钢工艺技术创新及优化改造

95科学技术Science and technology棒线轧钢工艺技术创新及优化改造王建荣(酒钢集团榆中钢铁有限责任公司,甘肃 兰州 730104)摘 要:为解决棒线轧钢其质量控制水平低、精度低、成材效率低以及生产效率低等问题,现阶段必须要加强对于棒线轧钢工艺的改造,通过利用导卫系统、剪切工艺以及孔型系统来对棒线轧钢工艺进行创新,通过不断改善创新当前的轧钢工艺,能够确保棒线轧钢的质量,确保棒线轧钢生产的稳定性。
关键词:轧钢;改造;优化中图分类号:TG335.62 文献标识码:A 文章编号:11-5004(2021)15-0095-2收稿日期:2021-08作者简介:王建荣,男,生于1988年,汉族,天水张家川人,本科,助理工程师,研究方向:材料成型。
作为小规格钢,棒线轧钢在生产的过程中,需要耗费大量的资源成本,但是由于产量较低并且质量也不高,所以在市场销售的成果并不理想。
在进行棒线轧钢的生产过程中,最主要的问题就是轧机料型的控制难度较大,所以导致最终的成品其精度较低其孔型的通用性能也较差,而材质其强度不够、导卫结构不合理等一系列问题,导致这种钢材在生产之后销售的效果不佳。
而为了提升钢材质量,优化改进相关生产工艺在现阶段非常有必要。
1 轧钢的简述在钢铁生产过程当中,轧钢技术是极其重要的生产方法。
在钢铁企业当中,通过利用轧钢技术来将钢锭或者钢胚轧制成特定的性质。
在此过程当中,需要采用不断轧制,给予一定的压力挤压才能够实现。
通常情况下,在进行轧钢的生产过程中需要进行多次轧压,基本不存在一次成型。
轧钢技术具有一定的特殊性,在钢材加工的过程中,主要是进行压力作用来加工,这种钢材加工方式和其他一些压力运作方式也是有着相似之处,但是其不同点在于该加工过程对于钢材的质量并不会产生影响,由于在压力作用的时候,钢材其内部质量较为温度,还有就是轧钢技术能够满足各种形状的钢材加工,从而更好的满足不同场景的使用需求,在钢铁生产中通过利用轧钢技术能够有效提升钢铁的性能。
棒线轧钢工艺技术创新及优化改造

棒线轧钢工艺技术创新及优化改造摘要:钢铁是工业建设中利用的重要材料,生产高质量的钢铁并强调生产过程中的能耗控制,这是目前钢铁生产实践中需要重点强调的问题。
就现阶段的分析来看,在节能减排的绿色生产环境下,钢铁的生产需要强调高效率、低成本,必须要进行生产工艺的改造和创新,因此在棒线轧钢的生产中需要不断的应用新技术和工艺来实现对传统工艺的改善。
关键词:棒线轧钢;新技术;应用价值引言钢铁是目前机械制造、工程建设中利用非常普遍的材料,对钢铁的质量生产进行分析与讨论,解决生产实践中存在的具体问题,这于实践而言有突出的现实价值。
就目前的棒线轧钢生产来看,其主要有三个主要的方向,其一是在生产的过程中实现能源的节约,其二是棒线轧钢的生产降低成本,其三是棒线轧钢的生产品质显著提升。
综合棒线轧钢的生产实践做分析可知要实现要让棒线轧钢生产向这三个方向发展,必须要不断的进行新技术、新工艺的应用。
随着计算机技术、智能控制技术等的使用,当前的棒线轧钢生产有了显著的变化,这为棒线轧钢的整体生产实效提升打下了良好的基础。
1.棒线轧钢生产状况分析1.1热轧宽带棒线轧钢生产线热轧宽带棒线轧钢生产线在目前的钢材生产实践中有着非常普遍的利用,这是我国自主研发的,通过对传统中薄板连铸连轧技术的优化而改进的现代棒线轧钢新技术成果。
对热轧宽带棒线轧钢生产工艺的具体利用做分析可知其具有非常显著的完整性,而且在应用实践中具有高效性,在规模化、连续化生产实践中表现出了突出价值。
就生产线的具体利用来看,其工艺流程整体比较的紧凑,能够实现连铸和棒线轧钢工序的有效连接。
简言之,热轧宽带棒线轧钢生产线作为我国配自主研发的棒线轧钢生产工作,在目前的实践应用中表现出了突出价值,所以其应用受到了青睐。
1.2集成宽厚板的生产线集成宽厚板的生产线在目前的棒线轧钢生产实践中也有比较普遍的利用。
就该生产线而言,其构建与我国引进的国外关键棒线轧钢设备有密切的关系。
我国在引进关键棒线轧钢设备之后通过对设备性能和特点的分析,结合了我国棒线轧钢先进技术成果,并在不断探索和研究的基础上最终整合而成了新型的棒线轧钢生产线技术,便是集成宽厚板的生产线。
Φ12螺纹钢四切分轧制技术在棒材厂的应用与改进

Φ12螺纹钢四切分轧制技术在棒材厂的应用与改进摘要:本文叙述了棒材厂φ12螺纹钢生产的工艺选择、试轧时出现的问题和工艺改进以及对切分技术的成果分析和切分技术的展望。
关键词:螺纹钢四切分轧制孔型系统导卫1 前言切分轧制是在轧机上利用特殊的轧辊孔型和导卫或者其他切分装置,将原来的一根坯料纵向切成两根以上的轧件,进而轧制多根成品或中间坯的轧制工艺。
采用切分轧制技术可缩短轧制节奏,提高机时产量,显著提高生产效率,降低能耗和成本。
目前棒材φ12mm螺采用三切分轧制工艺,终轧速度为15米/秒,其最高小时产量为57.4支/小时,平均小时产量为50支/小时,平均日产为2380吨/天,与其他规格的平均日产2903—3189吨/天存在较大的差异。
为了更好的发挥切分轧制的经济效益,结合市场对小规格螺纹钢需求量较大的实际,棒材厂决定开展φ12螺纹钢四切分生产工艺改造。
这将大幅度提高小规格产能和生产效率,降低生产成本,提高经济效益。
2 主要设备概况2.1 加热炉加热炉为步进式加热炉,最大加热能力为11Ot/h。
采用钢坯尺寸为150mm ×150mm ×12000mm,重约2075kg。
2.2 轧机一棒轧线上共有20架轧机,粗轧6架550轧机(1-6架)、中轧6架420轧机(7-12架),精轧8架350轧机(7-20架,其中17、18架轧机为平立转换轧机);二棒轧线上共有18架轧机,粗轧6架550轧机(1-6架)、中轧6架420轧机(7-12架),精轧6架350轧机(7-18架),一棒采用平立交替布置,粗、中轧为无扭微张力轧制,精轧采用活套无张力轧制,粗中轧、中精轧之间各有一台飞剪,精轧后设有一台倍尺飞剪。
2.3 冷床冷床为126米齿条步进式冷床,可收集和冷却剪成倍尺的棒材。
2.4 冷剪冷剪剪切能力为850T,可将成排棒材按定尺剪切,剪切范围6~12米。
3 四切分技术的应用与改进四切分轧制,即在轧制过程中通过孔型,将1根轧件轧成具有4个相同形状的并联轧件,再通过切分导卫及孔型将并联轧件沿纵向切分成4个单根轧件。
谢韦尔钢厂切分轧制改造的设计及应用
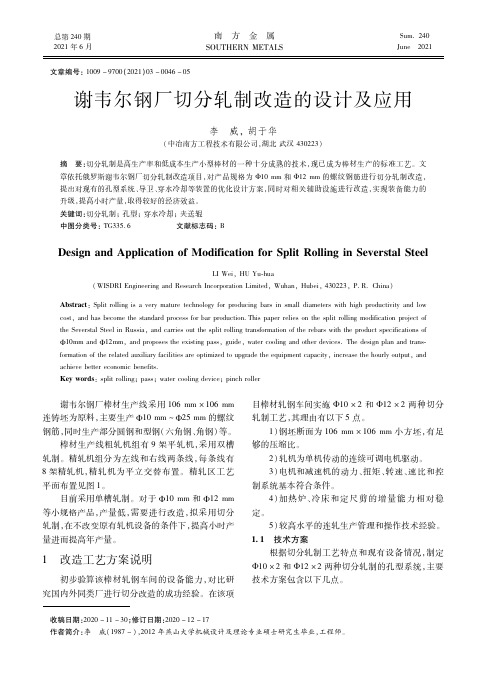
总第240期2021年6月 南 方 金 属SOUTHERNMETALSSum.240June 2021 收稿日期:2020-11-30;修订日期:2020-12-17 作者简介:李 威(1987-),2012年燕山大学机械设计及理论专业硕士研究生毕业,工程师。
文章编号:1009-9700(2021)03-0046-05谢韦尔钢厂切分轧制改造的设计及应用李 威,胡于华(中冶南方工程技术有限公司,湖北武汉430223)摘 要:切分轧制是高生产率和低成本生产小型棒材的一种十分成熟的技术,现已成为棒材生产的标准工艺。
文章依托俄罗斯谢韦尔钢厂切分轧制改造项目,对产品规格为Φ10mm和Φ12mm的螺纹钢筋进行切分轧制改造,提出对现有的孔型系统、导卫、穿水冷却等装置的优化设计方案,同时对相关辅助设施进行改造,实现装备能力的升级,提高小时产量,取得较好的经济效益。
关键词:切分轧制;孔型;穿水冷却;夹送辊中图分类号:TG335.6 文献标志码:BDesignandApplicationofModificationforSplitRollinginSeverstalSteelLIWei,HUYu hua(WISDRIEngineeringandResearchIncorporationLimited,Wuhan,Hubei,430223,P.R.China)Abstract:Splitrollingisaverymaturetechnologyforproducingbarsinsmalldiameterswithhighproductivityandlowcost,andhasbecomethestandardprocessforbarproduction.ThispaperreliesonthesplitrollingmodificationprojectoftheSeverstalSteelinRussia,andcarriesoutthesplitrollingtransformationoftherebarswiththeproductspecificationsofΦ10mmandΦ12mm,andproposestheexistingpass,guide,watercoolingandotherdevices.Thedesignplanandtrans formationoftherelatedauxiliaryfacilitiesareoptimizedtoupgradetheequipmentcapacity,increasethehourlyoutput,andachievebettereconomicbenefits.Keywords:splitrolling;pass;watercoolingdevice;pinchroller 谢韦尔钢厂棒材生产线采用106mm×106mm连铸坯为原料,主要生产Φ10mm~Φ25mm的螺纹钢筋,同时生产部分圆钢和型钢(六角钢、角钢)等。
日钢棒材精轧导卫失效原因分析及解决对策

日钢棒材精轧导卫失效原因分析及解决对策摘要:对2019-2021年日照钢铁棒材精轧区域导卫失效进行统计并分析原因,根据分析结果重点从轴承失效方面找到解决方案,有效减少因导卫轴承失效导致的轧制事故,从而降低生产成本,增加经济效益。
关键词:导卫失效、轴承、对策1 前言日钢棒材精轧区域采用7架短应力轧机,成品轧制速度一般在14m/s左右,K1、K3、K4、K5进口均采用滚动导卫, K2架出口架为扭转导卫,滚动导卫导辊轴承转速较高,且运转环境恶劣,滚动导卫失效事故率较高,因此如何避免滚动导卫在轧制过程中失效对轧线生产顺行至关重要。
2 棒材精轧滚动导卫失效原因分析2.1棒材精轧滚动导卫主要失效部位分析滚动导卫结构如图1所示,导卫主要失效部位如图标注:1、导辊,2、轴承,3、辊轴螺母,4、导辊轴,5,、支臂轴,6、耳轴锁紧系统,7、支臂,8、导板图1滚动导卫主要失效部位2.2 日钢棒材2018-2019年精轧区域滚动导卫失效原因分析导卫失效因轴承原因占比将近50%,前三项失效原因:轴承失效、支臂轴失效、耳轴及锁紧系统失效合计占比达到将近80%。
解决好这三方面的问题基本能够将导卫引起的轧制故障大幅降低。
2.3日钢棒材滚动导卫失效的要因分析2.3.1 轴承失效分析日钢棒材所有滚动导卫轴承主要有30202、30203、30304、30204、33205、32303等圆锥辊子轴承,均为进口著名品牌,质量可靠,轴承失效应从轴承工作环境方面入手。
2.3.1.1轴承缺油现有润滑系统为油气润滑,在装配新上线导辊时加少量耐高温锂基脂以防止轴承运转初期未形成油膜保护。
成品架导卫运转速度较高,供油压力偏低、供油管路不通及导卫制造精度不高有漏油点均会造成润滑不到位,当轴承缺油时轴承内部则会摩擦加剧,运行温度升高,相对运动表面就会发生高温变色,润滑油发黑,轴承滚珠颜色发黄,为缺油后高温变色特征。
2.3.1.2 轴承载荷过大轴承载荷过大主要由下面几个原因造成(1)轧件头部大或者料型偏大,而导卫的导辊间距不能随之变化。
棒线轧钢工艺技术创新及优化改造

山西冶金SHANXI METALLURGY Total 188No.6,2020DOI:10.16525/14-1167/tf.2020.06.51总第188期2020年第6期棒线轧钢工艺技术创新及优化改造谈群峰(山东钢铁股份有限公司莱芜分公司,山东济南271104)摘要:莱钢为改善棒线轧钢质量控制水平降低、成材效率降低、精度不高、生产效率等等特征现象,积极改造棒线轧钢工艺,因此使用孔型系统进行改造,还使用导卫系统、剪切工艺优化等进行创新,这些技术运用在棒线轧钢工艺当中,质量得到保证,而且市场需求大,生产稳定。
关键词:轧钢改造优化中图分类号:TG335.62文献标识码:A文章编号:1672-1152(2020)06-0131-02收稿日期:2020-07-24作者简介:谈群峰(1973—),男,中级工程师,毕业于哈尔滨理工大学热能与动力工程专业,本科,主要从事工艺技术管理工作。
棒线轧钢属于一种小规格钢,此种类型的钢在投产之后,由于需要投入大量成本,成本低且产量无法释放,再加上质量不能得到保证,因此没有市场。
这种轧钢生产之后最突出的问题是轧机料型控制难度很大,而且成品精度很低,孔型通用性能差,需要频繁更换,导卫结构不够合理、材质强度低等特征导致此钢在生产之后,没有市场还消耗了大量材料。
为提高产品质量,为企业发展创造出合理的品牌,改造生产工艺,有很现实的必要。
1棒线轧钢生产工艺某企业生产棒线轧钢,生产线产品规格为D 20~80mm ,生产中使用的机械设备有粗轧机、预精轧、精轧机、减定径机组成,机组之间设置事故碎断剪刀,在减定径机组设置了在线测径仪器。
中棒使用半连轧工艺制作,其中粗轧、中轧使用脱头轧制,预精轧机组之间设置了活套加强机组的灵活性,还能实现无张力轧制。
减定径机组使用西门子奥钢预应力轧机,材质为WC 等高耐磨材质。
根据生产需要,安排不同的方式进行生产,其中根据多个工艺生产的具体情况,使用不同的生产工艺,具体的生产工艺按照标准化来进行[1]。
棒材轧制中降低工艺故障提高作业率的方法和措施
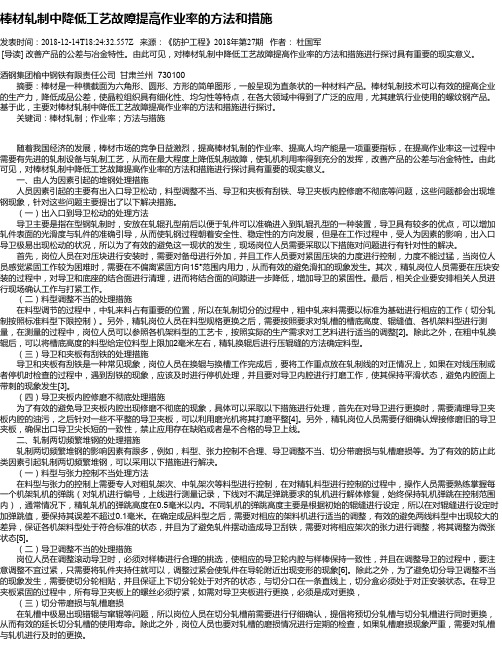
棒材轧制中降低工艺故障提高作业率的方法和措施发表时间:2018-12-14T18:24:32.557Z 来源:《防护工程》2018年第27期作者:杜国军[导读] 改善产品的公差与冶金特性。
由此可见,对棒材轧制中降低工艺故障提高作业率的方法和措施进行探讨具有重要的现实意义。
酒钢集团榆中钢铁有限责任公司甘肃兰州 730100 摘要:棒材是一种横截面为六角形、圆形、方形的简单图形,一般呈现为直条状的一种材料产品。
棒材轧制技术可以有效的提高企业的生产力,降低成品公差,使晶粒组织具有细化性、均匀性等特点,在各大领域中得到了广泛的应用,尤其建筑行业使用的螺纹钢产品。
基于此,主要对棒材轧制中降低工艺故障提高作业率的方法和措施进行探讨。
关键词:棒材轧制;作业率;方法与措施随着我国经济的发展,棒材市场的竞争日益激烈,提高棒材轧制的作业率、提高人均产能是一项重要指标,在提高作业率这一过程中需要有先进的轧制设备与轧制工艺,从而在最大程度上降低轧制故障,使轧机利用率得到充分的发挥,改善产品的公差与冶金特性。
由此可见,对棒材轧制中降低工艺故障提高作业率的方法和措施进行探讨具有重要的现实意义。
一、由人为因素引起的堆钢处理措施人员因素引起的主要有出入口导卫松动,料型调整不当、导卫和夹板有刮铁、导卫夹板内腔修磨不彻底等问题,这些问题都会出现堆钢现象,针对这些问题主要提出了以下解决措施。
(一)出入口到导卫松动的处理方法导卫主要是指在型钢轧制时,安放在轧辊孔型前后以便于轧件可以准确进入到轧辊孔型的一种装置,导卫具有较多的优点,可以增加轧件表面的光滑度与轧件的准确引导,从而使轧钢过程朝着安全性、稳定性的方向发展,但是在工作过程中,受人为因素的影响,出入口导卫极易出现松动的状况,所以为了有效的避免这一现状的发生,现场岗位人员需要采取以下措施对问题进行有针对性的解决。
首先,岗位人员在对压块进行安装时,需要对备母进行外加,并且工作人员要对紧固压块的力度进行控制,力度不能过猛,当岗位人员感觉紧固工作较为困难时,需要在不偏离紧固方向15°范围内用力,从而有效的避免滑扣的现象发生。
导卫的安装与调整(棒材)敬业新

导卫的安装与调整圆钢和螺纹导卫调整:一)单线部分1、所有的进口滚动导卫在调整时,导卫的导辊必须距导卫的轧制中心线(导卫中心线)是一致的,禁止导辊的偏向,那样会产生进口对不准,导辊易损坏,轧件易倒料。
如:12H进口滚动导卫在调整时,导辊的间隙与实际料型的间隙为±10丝左右;也就是说在调整导卫的两个导轮的间隙时,用实际料型来调整,呈现导轮很轻松的跟着样棒转动为最佳。
但是,在左右两边导轮距导卫的本身中心线一致时,间隙适当时,才为最佳。
2、如:12H出口滑动导卫,安装时必须导管铲嘴与轧辊槽的配合间隙为1—1.5mm为最佳,也就是说安装没有与轧辊相摩擦为佳。
也就是说单线的进出口导卫的中心线高必须与轧制线中心高要一致,左右偏向要一致,安装时要三点一线。
3、导卫在装配时,必须正确安装,紧固导卫的所有的紧固件,以防导卫松动,在轧制过程中影响轧制。
二)双线部分:1、16H出口切分导卫的调整。
切分轮的调整要平齐,两个切分轮的调整间隙应为±10丝左右(也就是转动上切分轮带动下切分轮轻松转动就可以了)。
切分刀片应与切分轮、进口夹板在同一条中心线上,叫三点一线。
注:切分导卫得进口夹板〈铲嘴〉在与轧辊装配时,必须和轧辊配合间隙为〈1mm〉良好。
2、17H出口扭转导卫〈01-02〉的调整。
在轧制过程中,根据实际轧速,根据实际轧制品种来调整扭转导卫的扭转角度;轧制速度越快,两个扭转轮的间隙越大。
用实际料型测量扭转导卫的扭转角度应为最佳。
在轧制速度越快的情况下,用实际样棒调整的如下α角度越来越小。
一般呈现的角度为15°左右。
(在轧制过程中可以用以下圆棒来调整两辊的间隙。
如:φ22*2的用圆钢22mm来调整;。
)分别用样棒来调整,调整时两个扭转轮跟转就可以,轻松转动不易太紧。
出口扭转导卫呈现的角度图:3、在轧制中(15 –16)架滚动导卫(0930B/C)的导轮,必须左右两边导轮各自两平齐,每两边的导轮距导卫中心线为一致,调整导轮间隙,用实际料型调整导轮,四个导轮跟着转,不要太紧,用实际样棒来调整导辊,如导辊很轻松的在跟着转动,实际料棒在导卫的左右移动又很轻则为最佳(在没有样棒时,调整间隙比实际来料大0.5mm左右).三)二切分轧制:1、在轧制(φ22×2)的轧制工艺,前提条件必须保证轧机左右辊辊缝是一致的,禁止错辊,导卫安装适当。
棒材螺纹钢生产线滚动导卫的装配与故障的分析

棒材螺纹钢生产线滚动导卫的装配与故障的分析柳州钢铁股份有限公司棒线型材厂摘要:本文针对棒材螺纹钢生产上的滚动导卫,简要介绍了滚动导卫的结构与安装注意事项,然后详细分析了生产线上滚动导卫常见的故障,并提供了相应的解决方法。
关键词:滚动导卫螺纹钢故障分析引言棒材螺纹钢是众多钢铁企业的重要产品,广泛应用于各种建筑中,一直以来在国内有着很大的市场。
导卫是棒材螺纹钢生产线上的重要部件,可分为滑动导卫与滚动导卫。
它安装在轧机的进出口,用来引导轧件准确地进出轧辊的轧槽。
滚动导卫结构相对滑动导卫复杂,但是稳定性相对较高,能实现轧件切分和扭转等功能,是棒材螺纹钢多切分轧制中不可或缺的重要组成部分。
1 滚动导卫的结构与装配滚动导卫通常由盒体、支撑臂、销轴、预导板、导辊和导辊轴组成。
导辊通过导辊轴固定在支撑臂上,支撑臂通过销轴固定到盒体上,导板通过紧固螺杆固定到盒体上,所有部件组装在起成为一个导卫总成。
将滚动导卫的全部零件组装成一个导卫总成需要注意以下几点:(1)零件质量检查。
首先检查外观无明显质量缺陷,然后使用尺子和样板检查零件的尺寸是否符合工艺参数要求。
最后检查各个零件的螺孔与螺牙是否完好,各种油路和水路是否畅通。
(2)导辊轴承安装。
安装轴承之前,要先保证导辊轴承位的干净与光滑平整,还要检查轴承的型号是否与导辊相符合,并检查轴承外观是否完好,质量有无缺陷等等。
然后使用铜棒或者铜锤把轴承外圈打入导辊轴承位。
如果轴承采用的是干油润滑,接着给导辊轴承外圈与内圈分别涂抹干油脂。
之后把轴承内圈放进外圈里面。
轴承安装到位后,给轴承安装防尘盖。
(3)导辊安装。
导辊轴承安装好之后,接着就要把导辊安装到导卫的支撑臂上。
导辊不能直接放到支撑臂上,而是需要分别在导辊两个轴承防尘盖外面各放置一块止推垫片。
然后把导辊轴分别穿过支撑臂上端、导辊上垫片、导辊、导辊下垫片和止推垫片下端,接着装上导辊轴螺母。
导辊安装的工艺要求是:导辊能自由转动而不发生轴向窜动。
中大棒生产线滚动导卫导轮的使用及优化
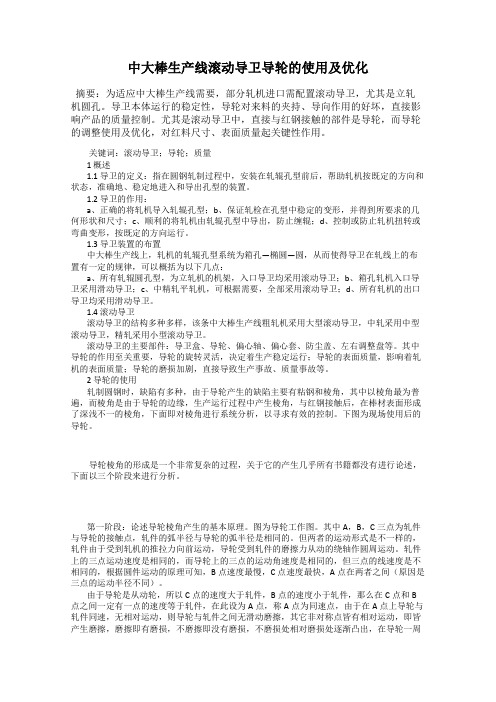
中大棒生产线滚动导卫导轮的使用及优化摘要:为适应中大棒生产线需要,部分轧机进口需配置滚动导卫,尤其是立轧机圆孔。
导卫本体运行的稳定性,导轮对来料的夹持、导向作用的好坏,直接影响产品的质量控制。
尤其是滚动导卫中,直接与红钢接触的部件是导轮,而导轮的调整使用及优化,对红料尺寸、表面质量起关键性作用。
关键词:滚动导卫;导轮;质量1 概述1.1 导卫的定义:指在圆钢轧制过程中,安装在轧辊孔型前后,帮助轧机按既定的方向和状态,准确地、稳定地进入和导出孔型的装置。
1.2 导卫的作用:a、正确的将轧机导入轧辊孔型;b、保证轧检在孔型中稳定的变形,并得到所要求的几何形状和尺寸;c、顺利的将轧机由轧辊孔型中导出,防止缠辊;d、控制或防止轧机扭转或弯曲变形,按既定的方向运行。
1.3 导卫装置的布置中大棒生产线上,轧机的轧辊孔型系统为箱孔—椭圆—圆,从而使得导卫在轧线上的布置有一定的规律,可以概括为以下几点:a、所有轧辊圆孔型,为立轧机的机架,入口导卫均采用滚动导卫;b、箱孔轧机入口导卫采用滑动导卫;c、中精轧平轧机,可根据需要,全部采用滚动导卫;d、所有轧机的出口导卫均采用滑动导卫。
1.4 滚动导卫滚动导卫的结构多种多样,该条中大棒生产线粗轧机采用大型滚动导卫,中轧采用中型滚动导卫,精轧采用小型滚动导卫。
滚动导卫的主要部件:导卫盒、导轮、偏心轴、偏心套、防尘盖、左右调整盘等。
其中导轮的作用至关重要,导轮的旋转灵活,决定着生产稳定运行;导轮的表面质量,影响着轧机的表面质量;导轮的磨损加剧,直接导致生产事故、质量事故等。
2 导轮的使用轧制圆钢时,缺陷有多种,由于导轮产生的缺陷主要有粘钢和棱角,其中以棱角最为普遍,而棱角是由于导轮的边缘,生产运行过程中产生棱角,与红钢接触后,在棒材表面形成了深浅不一的棱角,下面即对棱角进行系统分析,以寻求有效的控制。
下图为现场使用后的导轮。
导轮棱角的形成是一个非常复杂的过程,关于它的产生几乎所有书籍都没有进行论述,下面以三个阶段来进行分析。
- 1、下载文档前请自行甄别文档内容的完整性,平台不提供额外的编辑、内容补充、找答案等附加服务。
- 2、"仅部分预览"的文档,不可在线预览部分如存在完整性等问题,可反馈申请退款(可完整预览的文档不适用该条件!)。
- 3、如文档侵犯您的权益,请联系客服反馈,我们会尽快为您处理(人工客服工作时间:9:00-18:30)。
棒材切分轧制导卫系统的应用与改进
2006-7-12 11:39:18未知来源供稿
1 前言
莱芜钢铁集团有限公司(简称莱钢)由意大利DANIELI公司引进的全连续式棒材及轻型材生产线,以生产圆钢、带肋钢筋为主,年产量近60万t。
该生产线共有18架轧机,粗轧6架为悬臂式,中、精轧12架均为卡盘式;采取平立交替布置,其中14#、18~轧机为平立可转换机架。
该生产线设计可进行带肋钢筋切分轧制。
切分轧制与传统轧制在工艺上的不同之处是把一支轧件利用轧辊孔型切分成两支以上的并联轧件,再利用切分导卫将并联轧件切分成单支轧件。
该套轧机全部从国外引进,装备水平高,其工艺件种类繁多,结构复杂。
尤其是切分轧制,因其工艺的特殊性,对导卫系统的要求更为严格。
而在实际生产过程中,出现的问题也比较多。
为了保证正常生产,除了加强工艺件的基础管理之外,还在工艺件国产化和适应性改进等方面进行了探索。
2 切分轧制导卫系统
在切分轧制过程中,导卫系统除了保证轧件准确地进入孔型进行轧制之外,还有切分并联轧件的作用。
在实际生产中,导卫系统在保证轧制过程中轧件变形的稳定性以及弥补孔型设计的不足等方面也起着重要作用。
该生产线切分轧制的导卫系统根据安装位置不同,立式机架入口采用滚动导卫,水平机架入口采用滑动导卫;出口除切分机架为切分导卫外,其余均采用滑动导卫,其中中、精轧出口采用出口导管。
滚动导卫一般为两轮,但切分轧制的专用滚动导卫为四轮。
粗轧轧制速度低,来料断面大,对导卫的冲击较大,采用简单的滑动导卫。
而中、精轧机一般采用带导卫盒的滑动导卫,调整方便。
滚动导卫对轧件摩擦小、夹持作用强,除了保证对轧件的导向作用外,还可以有效地避免倒钢。
切分轧制专用的四轮滚动导卫对轧件则具有一定的矫直作用。
为了方便调整,滚动导卫内部设计有专门的调整机构,以调节导轮的中心距,使导轮能够准确地夹持轧件。
同时为保证滚动导卫能够较长时间正常运行,对导轮轴承的润滑以及导轮、夹板的冷却要求非常严格。
切分导卫主要包括切分导嘴、切分轮、分
钢器、调整机构等部件,如图1所示。
切分导嘴对预切分轧件进行导向,切分轮将轧件切开,分钢器使轧件彻底分开;调整机构用于调节切分轮间隙。
出口导管根据其内部中空截面的不同形状(矩形、圆形),分别在中轧、精轧的不同机架采用。
[img]20067121137199832.gif[/img]
图1 切分导卫结构
3 系统的适应性改进
切分轧制导卫系统在使用初期,即出现了四轮滚动导卫不能正常运行、滚动导卫导轮频繁损坏、切分机架处经常堆钢、出口导管处粉尘严重影响操作等问题,直接影响了生产,并使备件成本居高不下。
为此对切分导卫系统进行了改进。
3.1 四轮滚动导卫润滑和冷却管路的修复
四轮滚动导卫结构复杂,其内部油路、水路的走向也比较复杂,如图2所示。
由于制造原因,导卫盒体有铸造缺陷并且加工不当,造成油路、水路相通,使润滑和冷却功能相混,导卫无法使用。
针对铸造砂眼问题,采取了以下方法修复:先把盒体砂眼处镗孔,然后镶套,将油路、水路隔开;同时,采取钻孔镶入销子的方法对其它水路与油路相通处进行修复。
[img]200671211372872025.gif[/img]
图2 四轮滚动导卫油、水路结构
3.2 轴承防尘盖的设计加工
原设计中,滚动导卫的轴承多数不带密封。
在轧制过程中,导轮直接夹持高温轧件进行高速旋转,一方面使润滑脂很快流失,另一方面氧化铁皮、冷却水等侵入轴承内部,使滚动体产生滑动摩擦,产热大而烧坏轴承,进而影响了导轮的使用寿命。
经详细分析导轮、轴承的工作状态并考虑轴承外圈的尺寸,设计出三种防尘盖用于滚动导卫。
防尘盖外径小于轴承外圈外径1mm,内径略大于导轮轴直径。
在导轮旋转过程中,防尘盖外沿压在轴承外圈上,随导轮一起旋转,既能封住轴承内部润滑脂不向外溢出,保证润滑效果;又能防止外部氧化铁皮等杂物落入轴承内部。
3.3 切分导卫的改进
针对切分轧制时切分导卫频繁粘钢进而造成堆钢的问题,进行了分析,认为是由于切分导嘴设计不合理造成的。
原设计两片切分导嘴之间留给红钢通过的空间偏小,切分导嘴分料棱与红钢接触过于紧密。
而红钢塑性好,表面摩擦系数大,冷却水又不充足,经过一段时间后,摩擦脱落物逐渐积累,发生粘钢,进而堆钢。
为此,重新设计了切分导嘴,将分料棱改为圆弧过渡,增大过钢空间。
在切分导嘴上开出冷却水路,强制冷却导嘴。
改造实施后,切分导嘴粘钢现象大大减少。
针对随后出现的切分轮严重粘钢的问题,通过改造切分轮压紧碟簧和加强维护,减少了过钢时切分轮的弹跳。
3.4 水封器的设计加工
轧制过程中,车间内弥漫着大量的粉尘,直接影响对红钢运行状态的观察,同时影响环境卫生、危害职工身体健康。
粉尘主要集中在轧制区,特别是轧机出口导管处。
分析认为是由于轧制力大和轧制温度高,大量粉末状氧化铁皮弥散形成的。
原设计未考虑除尘装置,各机架后也没有足够的安装空间。
为解决此问题,利用一定压力的轧机冷却水在出口导管处形成水帘,吸收粉尘,粉尘随水排入地沟进入沉淀池沉淀,即“水封除尘”。
如图3所示,针对圆导管,设计了一种分离式水封器。
对于出口半管,利用其壁厚空间,直接在侧壁上打通主水路和喷水孔,实现水封除尘。
[img]200671211375157320.gif[/img]
图3 水封器主体示意图
根据现场生产的实际情况,从熟悉导卫结构入手,进行针对性分析并迅速解决问题,取得了事半功倍的效果。
同时,通过对导卫系统的适应性改进,使工艺件的使用效果最大限度地处于受控范围内,大大降低了备件消耗,有效地保证了正常生产的需要。