冷轧轧辊缺陷及预防措施
冷轧带钢边鼓缺陷产生原因与控制措施

冷轧带钢边鼓缺陷产生原因与控制措施全文共四篇示例,供读者参考第一篇示例:冷轧带钢是一种重要的金属材料,广泛应用于建筑、汽车、机械制造等领域。
在生产过程中,冷轧带钢常常会出现边鼓缺陷,影响产品质量。
本文将从冷轧带钢边鼓缺陷的产生原因和控制措施两方面进行探讨。
一、冷轧带钢边鼓缺陷产生原因:1. 轧辊质量不良:轧辊表面粗糙度大、硬度不足或不均匀,会导致轧件表面质量不良,进而引起边鼓缺陷的产生。
2. 轧辊边缘磨损严重:轧辊边缘磨损加剧,造成轧件边部挤压不平整,易产生边鼓缺陷。
3. 轧件冷却不均匀:冷却水量不足或水压不稳定会导致轧件温度分布不均匀,使得边部冷却速度不一致,进而引发边鼓缺陷。
4. 锯切不准确:如果在冷轧带钢的切割过程中,锯切位置不准确或锯切刀具损坏,容易导致边部挤压变形,产生边鼓缺陷。
5. 压下力控制不好:在轧制过程中,如果压下力控制不好,会造成轧辊与轧件之间的挤压不均匀,容易形成边鼓缺陷。
1. 提高轧辊质量:选用优质的轧辊材料,确保轧辊表面光滑、硬度均匀,减少轧辊对轧件表面的损伤。
2. 加强轧辊维护:定期检查轧辊边缘磨损情况,及时更换或修复磨损严重的轧辊,确保轧辊边缘的平整度。
3. 控制冷却工艺:合理设置冷却水量和水压,确保轧件冷却均匀,避免轧件边部出现温差过大的情况。
4. 加强锯切管理:对切割设备进行定期维护保养,确保切割精度和品质,避免因切割不准确导致的边鼓缺陷。
冷轧带钢边鼓缺陷的产生原因复杂多样,需要生产企业在生产过程中严格控制各项工艺参数,加强设备维护保养,提高操作技术水平,才能有效避免边鼓缺陷的产生,确保产品质量。
希望通过本文的介绍,能够对冷轧带钢生产企业提供一定的参考和帮助。
【以上内容仅供参考】。
第二篇示例:冷轧带钢是一种重要的金属材料,广泛应用于各种领域。
但是在生产过程中,冷轧带钢边鼓缺陷是经常出现的一种质量问题,给生产造成了一定的影响。
本文将从边鼓缺陷的产生原因和相应的控制措施进行探讨,希望对相关行业提供一些参考。
冷轧工作辊裂纹及剥落原因及预防

图 4 表层裂纹引起的剥落 海滩痕
图 3 机械裂纹
预防机械裂纹的措施有 3 个。1)确保带钢表面清洁无 异物,减少杂物介入。2)提高轧材表面质量,减少氧化皮残 留。3)加强乳化液检测系统和平衡过滤系统的点检。总之, 通过控制酸洗原料、乳化液指标、轧辊冷却等,可以减少轧 制过程中出现打滑、辊印、局部热擦伤等缺陷,提高板材表 面质量,减少轧机事故停机,同时降低辊耗。
一般情况下,打滑、粘钢等轧制事故,会引起辊身一条 母线上或者辊身局部区域内深度和开口都较大的裂纹,一旦 发生该类事故,则必须马上停止轧制,将轧辊换下,并对事 故辊进行严格的超声波、涡流探伤和磨削处理,必须保证表 面裂纹完全消除,并利用超声波探伤,检测轧辊内部的情况。
伤。4)对每支磨削完成的轧辊采用涡流探伤或表波探伤进行 检测,要确保每支要上机的轧辊不存在任何导致疲劳剥落的 可能性。
1.2 热裂纹
在生产过程中由于辊面局部温升快,最高温度超过轧辊 材质热处理工艺的最终回火温度,冷却后相当于再次回火, 表面硬度下降形成软点区,由于其与周边热膨胀系数不同, 这部分应力叠加,导致薄弱环节产生细小的网状裂纹 [1]。一 般情况下网状裂纹深度较浅,约 1.2 mm 以下(如图 2 所示)。 虽然这些裂纹深度浅,但是如果不及时处理和维护,在后期 的生产轧制中,受到外力、热应力等综合影响,很容易发展 成为如辊面粗化、辊面小掉肉等缺陷,严重时会引起辊面剥 落或断辊,所以一旦发现该类缺陷,在使用过程中重点关注 并及时处理。
2.2 材质缺陷引发的剥落
在制造轧辊的过程中,一些不规则的材料在坯料内有 可能成为轧辊内部残留的夹杂物。这些夹杂物可能是耐火材 料、残渣,也可能是坯料本身的的局部偏析和孔隙等 [3]。这 些内部缺陷,在轧辊使用过程中,都可能成为应力集中的根 源,最终将导致轧辊辊身剥落严重,甚至会出现断辊。轧辊 表层下缺陷引发的剥落,大部分在断裂面上呈现出类似鱼眼 纹,很容易进行辨别,如图 5 所示。可以看出该疲劳是从单 点开始蔓延的,并产生波浪状近似椭圆形的疲劳痕迹。这种 疲劳痕迹只有内部材料缺陷引发的迹象,并没有任何其它剥 落的源头。
冷轧钢带表面常见缺陷及改进措施

目 录一、冷轧卷缺陷辊印 (4)粘结 (5)压痕 (6)锯齿边 (7)树纹 (8)划伤 (9)凹坑 (10)锈-1 (11)锈-2 (12)锈-3 (13)氧化皮 (14)氧化色 (15)污板 (16)振纹 (17)碳化边 (18)边部折皱 (19)脱脂不良 (20)油斑 (21)卷印 (22)擦伤 (23)撞伤 (24)浪形 (25)刀印 (26)中间折皱 (27)燕窝 (28)二、热轧卷缺陷边部开裂 (29)分层 (30)条伸 (31)夹杂 (32)孔洞 (33)缺陷名:辊印(ROLL-MARK)不良代码:12发生形态:1)沿轧制方向有周期性的,板面有点状、块状、条状突起或凹陷进去的有间隔的不良。
2)平整辊印与轧钢辊印的区分:平整辊印伤疤处无粗糙度且发亮;轧钢辊印伤疤处发暗,有一定的粗糙度。
发生原因:1)轧钢辊表面受损2)TM辊表面粘有异物3)ANN不良产生氧化皮后,脱落粘附在TM辊上,TM时产生4)作业各Line其它辊面受损对产品的影响:1)外观不良,加工(冲压)时易发生破裂2)影响镀层效果防止对策:1)需要防止由各种杂质飞入钢带影响辊面质量2)对轧钢及TM工程中工作辊的硬度确认(爆辊)3)ANN保护气体的纯净度保证,防止氧化皮的产生缺陷名:压痕(DENT)不良代码:10发生形态:1)有一定周期性的压痕:异物粘附于发生原因:1)作业line各辊上粘有凸起的异物引起2)钢卷摆放位置有异物,导致产生3)小车压痕4)行车吊钩撞击后产生对产品的影响:对产品的影响:缺陷名:锈-1(RUST)不良代码:01发生形态:1)贯穿与钢带表面不规则或局部存在,多发生原因:ECL机组在生产宽料时,热风燥机烘干不良,加上卷取速度快,钢卷边部残留水迹,ANN后,边部成灰白色锈迹,后工程涂油后成黑色或黑褐色。
缺陷名:锈-2(RUST)不良代码:01发生形态:1)贯穿与钢带表面不规则或局部存在,多发生原因:1)渗透状锈主要是ANN前库和后库,由于下雨漏水和行车漏油造成2)ANN钢卷出炉时,炉罩漏水造成对产品的影响:缺陷名:锈-3(RUST) 不良代码:01 发生原因:1)主要是作业周期太长,(ECL→ANN→TM缺陷名:边部折皱(EDGE-BREAK) 不良代码:15发生形态:发生原因:1)TM在拉矫过程中,当超过屈服点时发生不均匀的塑性变形,开卷时沿开卷方向发生局部屈服。
冷轧生产企业轧辊缺陷产生原因及防范措施

冷轧生产企业轧辊缺陷产生原因及防范措施轧辊是轧钢生产中的一种大型工具,其性能与质量将直接影响轧机产量和产品质量,其消耗在轧钢生产中占很大比例。
因此,轧辊的使用与管理在冷轧的生产中至关重要。
本文所列舉的冷连轧机为四机架六辊UCM(Universal Crown Mill)轧机,设计产量为152.8万t,其技术从国外成套引进,是目前国内装备水平较高的冷轧机之一。
自投产以后,多次与国内外的轧辊专家进行了技术交流,以提高轧辊的使用和管理水平。
研究冷轧辊缺陷产生的原因,并采取相应的具体措施,以便降低轧辊消耗,对降低成本和稳定生产有着重要的意义。
1冷轧辊缺陷的主要形式当前我们所使用轧辊来自于日立金属、美国电钢、英国轧辊、中国一重、邢台轧辊和常冶轧辊等几家轧辊生产制造厂,其材质为3Cr,5Cr和4CrMo锻钢。
目前出现的轧辊缺陷按照所产生的形态可以分成软点、剥落(爆辊)和内部裂纹等三大类。
1·1 轧辊软点轧辊表面的某些地方会显示出比轧辊表面其它地方硬度值变化较大情况。
通常这些软点区域的硬度值要比基体材料的硬度低20HS。
一般情况下软点区域用肉眼是分辨不出来的,但是经过硝酸酒精腐蚀以后,就会显示出来,呈现一片暗色区域(见图1所示)。
在某些情况下,软点疵瑕也可以保持有硬化情况和回火色(兰色/棕色)。
1·2 轧辊剥落轧辊剥落就是指轧辊辊身的某个区域从辊身上分离出来的现象。
剥落按照产生的原因不同可分成下述几类。
1.2.1 轧辊表面剥落轧辊表面剥落可通过裂纹表面的“破损”轨迹来鉴别。
这种疲劳“破损”轨迹的显著特征是具有典型疲劳痕(海滩纹见图2所示)或在疲劳裂纹面上的“扇形”裂纹流线。
疲劳“破损”轨迹蔓延的方向与轧制时轧辊旋转的方向相反。
1.2.2 接触应力引发的剥落由于轧机的负荷以及轧辊在接触点上的局部挤压,造成的最大组合剪切应力(通常称作“赫兹应力”)位于轧辊表面之下的某个较小区域中。
多处的裂纹可以引发并在赫兹应力超过轧辊的抗拉强度时,在表面之下位置发生弥散,导致剥落的产生,这会通过两种模式发生。
马钢冷轧轧辊缺陷的分析及防范措施

马钢冷轧轧辊缺陷的分析及防范措施冷轧是冶金工业中的重要工艺,以马钢冷轧轧辊为例,由于涉及到温度、压力以及复杂的机械运动,它会极易出现缺陷,严重影响轧件的质量,损害轧、辊膜层的使用寿命,使生产效率大大降低,甚至造成设备损坏,对此,我们必须采取有效的防范措施来解决这个问题。
马钢冷轧轧辊缺陷主要有三大类:表面收缩、表面变形和表面不均匀等。
表面收缩主要是指轧辊表面在装配、加工过程中发生的收缩产生的,其特征是轧辊表面凹陷,严重时甚至可以影响轧制精度,造成轧件质量不达标;表面变形是指轧辊表面在装配、加工过程中发生的变形,其特征是轧辊表面凸起,也可能影响轧件质量;表面不均匀是指轧辊表面装配和加工过程中发生的局部变形的不均匀,使轧辊表面出现比较大的凹凸异常。
要有效地防止和消除轧辊缺陷,必须从技术管理、装配和使用三个方面来采取措施。
首先,应该从技术管理上入手,建立一套完善的技术管理体系。
首要的任务是完善轧辊设计及制造规范,确保相关材料、零部件、设备等都经过严格的质量检查;严格执行加工工艺流程,控制每一步的参数偏差,确保间隙和转动磨损等参数符合要求;完善轧辊维护和日常检测制度,确保轧辊在使用之前能够按照规定完成相关检测,以及形质检测、表面检测和力学检测等,并做好记录。
其次,要注重轧辊的装配。
轧辊装配过程是一个相对比较复杂的操作过程,必须做到完全符合设计标准,特别是轧辊中心钢芯的安装,必须保证严格的对中,以确保轧辊的刚性符合要求;此外,对外罩和安装紧固件也要严格操作,检查是否损坏,以确保无论是外皮还是紧固件都能够牢固地结合在一起。
最后,轧辊还需要合理使用。
轧辊装配完成后,要检查其位置是否准确,特别是轧辊之间的间隙,应注意确认间隙的变化;在轧辊使用过程中,及时对轧辊进行冷却,以减少温度升高带来的变形,同时要避免超载和抗静载,以减少更多的变形;同时,应该定期维护轧辊,确保轧辊在正常工作状态下,以保证长期的使用寿命和质量。
冷轧机轧辊缺陷表现形式及预防措施!

冷轧机轧辊缺陷表现形式及预防措施!许崇山"常州宝菱重工机械有限公司#江苏常州$%&’%()摘要*介绍了轧辊表面缺陷的表现形式#提出了减少和预防轧辊缺陷的措施+关键词*轧辊,冷轧,预防措施中图分类号*-.%/$0/引言冷轧过程中#轧辊对带钢产量1板形质量1吨钢成本消耗三大指标的影响很大2%#$3+冷轧轧辊使用过程中的缺陷#会造成批量产品质量降级甚至报废#造成成材率降低#且可能导致相关设备损坏+因此#国内各冷轧生产厂家都非常注重对轧辊使用的研究#致力于有效降低冷轧轧辊的消耗2$4/3+本文从轧制工艺对轧辊的客观要求出发#从加强轧辊检测1完善轧辊磨削及装配工艺1改善轧制工艺条件1优化轧制工艺参数等多方面提出了轧辊缺陷的预防和消除措施+5轧辊缺陷表现形式及预防措施根据实际生产现场使用情况#轧辊缺陷主要划分为表面缺陷1剥落缺陷和断裂缺陷三大类263+575轧辊表面缺陷表现形式及预防措施轧制过程中#轧辊表面缺陷会明显地转移到带钢表面#直接影响到成品板带的表面质量+常见的轧辊表面缺陷原因分析及预防措施如下*%7%0%轧辊表面夹杂物在轧辊表面用肉眼或借助低倍放大镜可观察到的形状不规则的夹杂物2&3#长度一般在’7’84899范围内+预防措施*控制冶炼锻造加工及热处理等原始状态的关键参数#降低轧辊表面夹杂物的尺寸和数量+%7%7$轧辊表面桔皮轧辊超期服役1在工艺冷却润滑条件相对较差的环境下较长时间工作时#辊身表面会出现粗糙不均的:木纹;状结构#外观形状很像:桔子皮;2&3+有时轧辊过量磨削后也会出现这种特征+预防措施*改善轧制润滑条件#阻碍轧辊表面桔皮缺陷的发展#或适当增加锻造比1合理地缩短轧制周期+%7%7&轧辊表面印痕主要表现为辊面针孔1凹痕1压痕和孔洞#在轧辊表面不规则分布的凹痕#一般呈圆形2&3#最大直径可达&99#深度可达’7’<99#表面状态或轧辊的纹理通常保留在凹痕内#一般是由一些碎片"异物)进入咬入区或轧辊间相互接触摩擦造成的+预防措施*鉴别碎片异物来源1改善工艺润滑冷却条件1提高酸洗卷板的表面质量和剪边质量1增加工作辊表面硬度和淬硬深度1提高工作辊和中间辊和支撑辊之间的硬度差+%7%7=轧辊表面热损伤主要表现为软点和压痕#轧辊表面某个局部区域硬度比正常值低+特殊情况下#热损伤可引起轧辊表面局部的高硬度和回火色+轧辊工作期间#当局部温度超过轧辊制造时的回火温度#辊面便会发生热损伤#受损伤区域的硬度下降+预防措施*避免引发热损伤的一些潜在热源的发生#如磨床砂轮冲刀1轧制时的断带1打滑1轧制事故"缠钢1粘钢)1冷却不均匀1轧制产品规格变化1冷却液温度1轧制速度的变化等#有效降低轧辊表面产生热损伤的几率+对于存在引发热损伤问题几率较高的轧制环境#应当考虑使用硬度较低的轧辊+第&6卷第=期$’’(年<月现代冶金>?@A B C>A D E F F G B H IJ?F0&6K?0=L G H0$’’(!收稿日期*$’’(M’/M%8作者简介*许崇山"%(6%N)#男#工程师+电话*"’8%()<&$8<=//#%&6’%8’&&$6!"!"#轧辊表面热裂纹轧辊表面热裂纹又称应力裂纹$外观上看$热裂纹的形状有沿轧辊轴向的小裂纹%!&&’和龟裂纹两种$冷轧轧辊出现较多的是沿轧辊轴向的小裂纹(通常热裂纹发生在因断带或轧辊粘钢引起的轧辊热损伤最严重的区域内$有时候由于中间辊或支撑辊表面剥落也会引起轧辊表面裂纹(预防措施)避免热损伤和热冲击可以有效降低辊面形成热裂纹缺陷的几率(*"+轧辊剥落缺陷表现形式及预防措施轧辊剥落的起因不一定都来自热损伤和热裂纹区$辊面任何应力集中点都有可能产生疲劳裂纹$如轧辊印痕,清除不彻底的表面裂纹,擦伤等(轧辊剥落按照剥落发生的起始部位划分$可以分为表面起源诱发的轧辊剥落,轧辊材质缺陷引起的次表层剥落,接触应力引起的次表层剥落(!"-"!表面剥落表现为剥落断口有明显的疲劳带$可以通过断口上存留的像沙滩花纹样的延性疲劳纹和扇形断口流线的疲劳带来识别$一个疲劳带的长度范围小到几厘米,大到沿轧辊圆周方向数圈(预防措施)尽量避免轧辊产生应力集中和轧制过载.制定合理的轧辊磨削工艺$保证消除干净上一轧制周期产生缺陷.轧辊磨削后进行涡流探伤和超声波探伤(!"-"-轧辊材质缺陷引起的次表层剥落断口上存在同心疲劳花样%/鱼眼0形状’123$疲劳起自一个点,有疲劳纹,呈椭圆形传播$疲劳纹只与材料内在的缺陷有关(这种疲劳花样不能与表面起源的疲劳相混淆$表面起源的疲劳伴随有疲劳破坏带(预防措施)尽量减少钢锭中的参杂物(!"-"2接触应力引起的次表层剥落由于轧制载荷的作用$在变形区内轧辊会发生弹性压扁$最大剪应力位于辊面下的次表层位置(当剪应力超过轧辊的抗剪切强度时$裂纹在次表层萌生并扩展(预防措施)避免因杂质通过辊缝引起最大综合剪应力超过轧辊本身抗剪切强度.保证轧辊足够的磨削量.缩短轧制周期$减少轧辊应力循环次数.降低轧制力以降低最大综合剪切应力.改进辊身肩部倒角及半径$以减少辊身边缘的应力集中.避免轧制事故如带钢与轧辊间打滑,高速轧制时断带粘钢等(*"4轧辊断裂缺陷表现形式及预防措施!"2"!辊颈断裂辊颈断裂一般表现为疲劳断裂和脆性断裂两种形式(%!’疲劳断裂疲劳断裂按照诱因可分为表面起源,次表面起源和辊颈修复三种形式(表面起源诱发的辊颈疲劳断裂(轧辊有多个起源于表面的棘轮状标记$当采用工作辊传动方式轧制时$工作辊辊颈承受较大的扭转力矩$同时受轧制压力和弯辊力的合力作用$承受一定的弯曲应力$如果施加在辊颈上的合力超过材料的抗拉疲劳强度$周向表面裂纹就会形成$严重时导致辊颈疲劳断裂(次表面起源引起的辊颈疲劳断裂(次表面诱发的辊颈疲劳断裂是从一个材料质量缺陷点%深层固有缺陷’上萌生$或从轧辊结构的某一部分萌生$以椭圆形式从源点开始扩散$可以通过断口上次表层存在的椭圆形疲劳花纹%/鱼眼0形状’来识别(辊颈修复引起的辊颈疲劳断裂(断口上有多个从表面萌生的疲劳/棘轮0标记(轧制过程中会出现工作辊的轴承故障$严重时甚至出现工作辊的轴承抱死$对轧辊辊颈造成一定的修复损伤(前期修复的区域有很大的疲劳倾向(通常修复包括焊接和去掉轧制隐患的挖槽$如果焊缝,母材界面和挖槽的区域接近或处于辊颈上应力高的部位%如辊身5辊颈的圆弧’$集中应力容易超过材料的拉伸疲劳强度(预防措施)避免轧制过程中出现轧辊轴承抱死故障.设计辊型$避免应力集中.提高轧辊材料强度以阻止裂纹的萌生和扩展.设计辊颈时$考虑辊颈所承受的弯曲和扭转载荷$以避免裂纹萌生和扩展.提高轧辊材料强度以阻止裂纹的萌生和扩展.局部修复如焊接界面,凹槽要远离圆弧或辊颈上的应力集中区.使用过程中适当控制道次压下量$降低工作辊承受的扭转力矩(%-’脆性断裂与疲劳断裂产生原因不同$脆性断裂大多是由材质缺陷和轧制过载引起的(轧辊材质缺陷引起的辊颈脆性断裂起源于内部单独一点$断裂不呈现任何疲劳痕迹%疲劳辉纹’(在结晶凝固时$夹杂物%耐火材料,熔渣,局部偏析,疏松等’有可能残存于钢锭中$造成轧辊工作时产生应力集中(轧制过载引起的辊颈断裂一般发生在横向剪切面%呈6#7角’$由表面一点萌生$流线从源点出发$覆#第6期许崇山)冷轧机轧辊缺陷表现形式及预防措施盖整个断口!内部断口在外观上是典型的韧性断裂!断裂源不显现任何疲劳特征"疲劳辉纹#$预防措施%严格控制冶炼过程&减少残存夹杂物&改进热处理工艺&增加辊颈材料强度$’()(*辊身断裂"’#次疲劳断裂疲劳从一个单一点萌生!形成一个伴有疲劳辉纹的椭圆形花纹$深层固有缺陷导致的辊身断裂的危害极大!在轧制状态下!轧辊可能沿轴向完全爆裂或者断裂成几大段$次表层应力集中使局部应力超过疲劳强度!疲劳裂纹萌生并扩展!周围材料的强度逐渐降低到发生疲劳的强度!断裂的最后阶段是瞬时的$预防措施%轧辊磨削后进行超声波探伤!进行检测并跟踪使用情况!及时防止该类缺陷造成的严重事故的发生$"*#脆性断裂辊身脆断是由轧制过载引起的瞬间辊身断裂!一般发生在横向剪切面上"与轴向成+,-角#!断裂裂纹在表面应力最高的一点萌生!在横向剪切面上径向&圆周方向扩展!内部断口在外观上是典型的韧性断口$发生轧制事故时!辊身突然承受很大额外应力!一旦超过辊身材料强度!很容易发生脆断$预防措施%在生产过程中应尽量避免事故的发生.在冶炼过程中要严格控制夹杂物的含量$/应用实例某厂01六辊可逆冷轧机组由于轧辊的使用方法不当!在试生产阶段!出现了大量的轧辊质量缺陷!严重影响了轧后带钢表面质量和板形质量$为此通过轧辊检测设施"包括磁粉探伤&便携式轧辊表面硬度检测仪&超声波控伤等#进行了轧辊缺陷检测!并采取了相应的预防措施$/(2减少轧辊表面缺陷轧辊表面缺陷产生后不断向辊身渗透是导致轧辊裂纹&轧辊剥落和轧辊断裂的主要原因$为此对表面软点&粘结&裂纹等表面缺陷的轧辊进行了深度磨削!把表面缺陷除净后再磨掉3(’344!然后放置*天左右!再进行探伤等轧辊表面检查合格后上机$图’为改进前后轧辊表面缺陷产生几率的对比!由图’可知!改进后轧辊的换辊周期有所延长$/(/预防轧辊剥落通过对正常轧辊疲劳程度变化规律的分析!确卷图!为换辊周期与各种轧辊缺陷发生几率的关系曲线"从左至右分别为换辊周期与表面缺陷#曲线$%&与表面裂纹#曲线’%&与轧辊剥落#曲线(%发生几率的关系曲线)当换辊周期达到带长*+,-以上"橘皮&印痕&热划伤等轧辊表面缺陷产生的几率开始升高"当换辊周期达到带长$.+,-以上"轧辊裂纹产生的几率迅速升高"当换辊周期超过’++,-"轧辊剥落产生的几率超过了带长’+/)为了降低轧辊裂纹&轧辊剥落等缺陷的发生几率"换辊周期应控制在$!+0$.+,-之内)为解决工作辊边部应力集中区剥落问题"对中间辊&支撑辊的两个肩部分别设计加工大圆弧类型复合倒角"降低了轧辊边部因应力集中导致的剥落)123预防轧辊断裂避免工作辊轴承抱死和瞬间过载是预防轧制状态下的工作辊辊身和辊颈断裂#除轧辊本身材质缺陷外%的主要方法"主要措施有以下几点4#$%轧辊轴承及轴承室应定期清洗"保证轴承室的清洁和润滑油路畅通5#’%轴承外套定期倒面"保证磨损均匀)正常情况下"一套四列短圆柱轴承的使用寿命为.06个月"轧制带钢总长度约为7+++0.+++万-"轴承外套倒面时间周期为’个月"每次沿周向旋转*+85 #(%选用进口密封件"保证轴承室密封良好"防止乳化液进入轴承室5#!%对轧机工作辊轴承润滑方式进行改进"改双轴承座并联油雾润滑为单独润滑"降低工作辊轴承故障发生频率和工作辊辊颈断裂事故5 #7%减少轧制状态下的瞬间过载对工作辊的冲击"充分利用轧机的断带保护功能#过负载卸荷和辊缝快速打开%"并以主电机额定电流为负荷上限"减少过负荷冲击造成的轧辊剥落和断辊事故)3结论预防轧辊缺陷的主要措施有4#$%在轧制过程中尽量避免和减少轧制事故5#’%轧辊磨削加工后进行超声波探伤"及时发现轧辊缺陷5#(%改进轧机的工艺润滑及冷却条件5#!%改善酸洗卷板的表面质量"可以有效控制轧辊表面缺陷的产生5#7%制定科学合理的轧辊使用周期&磨削工艺和辊型优化&减少辊面应力过分集中5#.%完善轧辊装配工艺&减少轧制过载"可以有效降低轧辊断裂)参考文献49$:刘以宽"汪光然"严家高;轧辊失效分析9<:;轧钢"$**("#$%4(+=(!;9’:刘德富"尹钟大;冷轧工作辊的早期失效及预防措施9<:;特殊钢"’++("’!#.%4((=(7;9(:陈联满;轧辊辊颈断裂分析9<:;理化检验物理分册"’++$"(>#>%4(+7=(+6;9!:任喜来;冷轧辊的失效分析及其修复9<:;轧钢"’++’"$*#(%4!7=!>;97:?@AB C"DE F G H@CC"I@F J;K L@M;N E O K P O H P M M F E Q@ R P M S H P M M E Q T-E M ME Q@F L K K MU M@Q L V P U K H@L E P Q W K H F X F -@Q X O@R L X H K9<:;Y Q T E Q K K H E Q TZ@E M X H K B Q@M A F E F"’+++">#$%477=.>;9.:B[K W K S P\?Z"]K M P L L E^K L P<;Z@E M X H K@Q@M A F E FP OO P H T K S@Q SE Q S X R L E P QG@H S K Q K SF L K K M R P M S_P H,H P M M F 9<:;Y Q T E Q K K H E Q T Z@E M X H KB Q@M A F E F"’++!"$$#!%4!>7=!6!;9>:杨利坡"周涛"彭艳"等;‘\可逆冷轧机轧辊失效分类及预防9<:;冶金设备"’++7"$7!#.%4$=.;>第!期许崇山4冷轧机轧辊缺陷表现形式及预防措施。
马钢冷轧轧辊缺陷的分析及防范措施

马钢冷轧轧辊缺陷的分析及防范措施今天,随着工业的发展,越来越多的重要工业用钢,如马钢板材,在冷轧过程中,轧辊是一个非常重要的部件,随着轧辊的日益快速的寿命,轧辊的缺陷也会带来不利影响。
本文将从分析原因和防范措施两方面来探讨马钢冷轧轧辊缺陷的问题,为提高冷轧轧辊的使用寿命和质量提供参考。
一、马钢冷轧轧辊缺陷的分析1、损坏原因由于轧辊会在马钢冷轧过程中长期受到扭矩、温度、压力等不均匀的外界考验,而轧辊中各种元素的问题也会导致轧辊疲劳损坏,从而出现缺陷,如表面裂纹、磨损和烧伤等。
2、实际表现轧辊缺陷以表面裂纹为主,由此可知表面失效正是轧辊缺陷产生的原因之一,根据不同的裂纹形态,可以推断出轧辊的损伤原因,如圆柱形裂纹、锥形裂纹、Y字型裂纹等。
二、马钢冷轧轧辊缺陷的防范措施1、优化轧辊设计优化轧辊设计,使得轧辊具有较大的强度,同时增加轧辊表面的耐磨性,减少轧辊表面的损坏,使轧辊的使用寿命更长。
2、降低轧辊温度应控制轧辊的表面温度,并在较低的温度范围内进行轧制,以减少轧辊表面的烧伤,提高轧辊的使用寿命。
3、均匀保护润滑剂应给轧辊表面均匀的润滑,以确保轧辊的表面,同时保持充足的润滑剂分布,以减少轧辊噪声,平滑运行,减少轧辊磨损损坏,提高轧辊的使用寿命。
4、改善马钢材质应均匀改善马钢坯料的碳素含量,改善马钢冷硬度,使冷轧材料更加均匀,减少冷轧过程中烧伤、磨损等,提高冷轧轧辊使用寿命。
综上所述,马钢冷轧轧辊缺陷的分析及防范措施应及早采取有效的措施,以提高冷轧轧辊的使用寿命和质量,促进行业的健康发展。
首先,应优化轧辊的设计,降低轧辊温度,提供良好的润滑剂保护,同时改善马钢材质,以改善冷轧工艺,减少轧辊缺陷产生的可能。
冷轧产品缺陷及预防

5欠酸洗 英:Under pickled
【定义与特征】 钢带表面残留着未酸洗掉的氧化铁皮,呈横向的黑色条纹(类似
“抬头纹”的横向黑色细纹),形成带状或片状分布在钢板表面 上。用手摸,手上将粘有黑色的污物。 【原因分析】 热带的表面氧化铁皮经酸洗槽后,未清除干净,残留在带钢表面
震纹的特点是厚度波动,它是机架发生共振产 生的。
【鉴别与判定】
肉眼或打磨后判定,不易与其他缺陷混
淆。
9乳化液斑 英:Emulsion marks
【定义与特征】
是残留在钢带表面的裂化乳化液,随机的分布在钢带表面,形状不规 则,颜色发暗。
【原因分析】
乳化液痕迹是残留在带钢表面的乳化液发生裂化作用,由于退火过程 中残余的乳化液没有被完全蒸发,即带钢上多余的乳化液没有被吹净。
卷轴印:垂直钢板轧制方向的有周期的 横纹。
平整勒印:平整过程中产生的羽毛状的 花纹,分布在局部或整个钢带。
平整横楞:沿钢带宽度方向有明暗相间 的条纹。
折皱:是在钢带的边部连续出现的桔皮状皱 纹。
横折印:在钢带的边部(极少数在钢板中间 的某一部位也有发生)连续出现象等号一样 的折线。在钢板边部长短不一的折线,垂直 或与钢板轧制方向成45度角。
粘结:是有曲线形状的应变条纹,可分布在 钢带边部、中部、二肋任何部位。
表面碳黑:冷轧钢带经罩式炉退火后,钢带外圈或 端面有黑色粉状物,有时可擦掉。
对流板印:冷轧钢带经罩式炉退火后,在钢卷端部 出现的碳黑或焦油残留。
碳化边:颜色呈黑灰色,用手擦不掉,碳与基板发 生化学反应,不溶于酸,又称蛇形迹。一般分布在 钢卷(退过火)的两边,连续或间断分布。
马钢冷轧轧辊缺陷的分析及防范措施

马钢冷轧轧辊缺陷的分析及防范措施
调整轧辊缺陷主要涉及轧辊的设计成形等工艺指标,以满足冷轧要求的功能、精度和
结构。
钢铁厂在设计轧辊时,应当特别注意轧辊成型工艺过程中发生轧辊缺陷。
马钢冷轧
轧辊缺陷的具体表现主要体现在轧辊表面存在肉眼可见的凹凸疵点,局部残余焊料不充分,铸造的物理性能和力学性能较差等问题。
如何防止和减少马钢冷轧轧辊缺陷,目前主要采用如下措施:
首先,应确保轧辊材料的质量。
钢铁厂在选择轧辊材料时应该严格按照要求,以满足
冷轧材料的使用寿命和功能。
同时,轧辊材质的选择也应参考轧制条件,比如速度、温度、能量等参数。
其次,选择合适的轧辊成形工艺来减少缺陷。
无论是采用成型机还是手工操作,在轧
辊成形工艺的过程中,应坚持微小改变原则,尽量保持轧辊的精度,并观察成形过程中产
生的残余焊料,从而减少轧辊缺陷。
同时,搭配合理的润滑来提高轧辊耐磨性。
轧辊运行中,要保证轧辊机体和轴承各部
件能正常润滑。
正确的润滑模式和润滑油定期更换,可减少机械式的磨损,减轻轧辊的磨耗,有效的防止轧辊缺陷的产生。
此外,保证轧辊安装对接质量也是必不可少的一环。
钢铁厂在轧辊的安装时,应确保
轧辊的质量,安装的时候要避免过度的倾斜、圆弧不平等现象,并且在安装时尽量减少人
工操作,以免造成损伤。
总之,轧辊缺陷的具体归因原因无法一概而论,要想减少马钢冷轧轧辊缺陷,就需要
从多个角度出发,避免在设计、选择材料、工艺成形、安装对接过程出现现象,做到安全
结构、成本有效,提高轧辊的品质和可靠性。
浅析冷轧机轧辊缺陷表现形式及预防措施

浅析冷轧机轧辊缺陷表现形式及预防措施摘要:在冷轧轧辊使用的过程中,如果轧辊本身存在缺陷,会导致质量降级,甚至产品直接报废,严重时将导致轧机断带、堆钢,此类事故处理时间长,严重影响轧机生产效率。
目前我国很多的生产厂家对轧辊出现的缺陷问题非常的重视,他们通过对轧辊的研究,力图有效的降低轧辊的消耗,保证轧机产能和成材率。
本文就冷轧机轧辊常见的缺陷问题进行分析,提出了具体的问题的预防措施。
关键词:冷轧机;轧辊缺陷;表现形式;预防措施某钢冷轧厂在轧机投产初期,如果轧辊表面出现缺陷,会给整个生产带来很大的困扰,对产品的生产节奏和质量都有一定的影响。
一般来说轧辊的表面缺陷包括很多种,包括振纹、螺旋纹、刀花、裂纹等,以上缺陷对产品的表面都有一定的影响。
一、振纹进行带钢轧制的过程中,在带钢的表面,经常有一种与带钢运动方向垂直、明暗相间的条纹出现,这种现象就叫做带钢振纹。
通过多次的实践我们发现,产生的振纹多数原因是由于轧辊的原因,轧辊的振纹复制在了带钢的表面。
1.轧辊振纹的产生原因一般来说,轧辊的振纹产生是有其自身的原因的,进行生产的过程中,砂轮主轴的不断振动会导致轧辊振纹的产生,此时产生的振纹呈螺旋状,在轧辊的表面分布;砂轮脱粒不良、砂轮形状不良也可能导致轧辊振纹的出现,呈螺旋状,分布在其表面;通常情况下,我们可以通过对砂轮和轧辊的转速对振纹的间距进行测算,然后与实际存在的进行相互比较,这样对砂轮振纹就可以进行准确的判断,由于轧辊托架(托瓦)的接触不良引发的轧辊振纹,振纹以平行于轧辊母线的形式分布在轧辊表面;由于尾座顶尖形状不良而引发的轧辊振纹,振纹的分布是平行于轧辊母线的;因头架转动不良引发的轧辊振纹,振纹的分布是平行于轧辊母线的;砂轮头架的振动和床头箱的振动之间产生共振引起的轧辊振纹,以平行于母线的形式分布在轧辊表面。
2.轧辊振纹的消除方法对轧辊振纹进行消除,首先对不正常的振源要进行消除,对振纹的明显形式进行分析,选择合适的磨削方式,对明显的振纹要从粗磨开始,不明显的则从半粗磨开始。
马钢冷轧轧辊缺陷的分析及防范措施

马钢冷轧轧辊缺陷的分析及防范措施
马钢冷轧轧辊缺陷是指在马钢冷轧工艺中,轧辊表面由于调试不当或操作不当而产生的缺陷。
这些缺陷会导致板材质量下降,影响板材的生产效率,甚至会给马钢冷轧生产过程带来严重的危害。
原因分析:
1.轧辊的表面质量问题:马钢轧辊表面的质量可能存在缺陷,如轧辊表面的磨损、氧化、缺少材料、缺陷和污垢等。
2.操作不当:由于操作者技术水平不高,或者没有按照正确的操作流程操作而引起的轧辊缺陷。
3.调试不当:轧辊和上下轧机架之间调试不当,会导致轧辊表面出现缺陷。
4.机械问题:由于冷轧机械部件的老化或损坏,会导致轧辊出现缺陷。
预防措施:
1.加强轧辊的质量检验:仔细检查轧辊表面的质量,及时发现轧辊表面的缺陷,及时更换损坏的轧辊。
2.强操作人员培训:定期举办操作培训,增强操作人员操作技能,避免操作出现问题。
3.合理调试轧辊和上下滚机架:轧辊和上下滚机架之间要保持合理的间隙,以减少轧辊表面的缺陷。
4.定期检测机械部件:定期检查机械部件的磨损情况,及时维修或更换损坏的部件,保证冷轧工艺的正常运行。
综上所述,只有全面加强轧辊的质量检验、定期培训操作人员、合理调试轧辊和上下滚机架,以及定期检测机械部件,才能有效的防止轧辊出现缺陷。
市场上出现的马钢冷轧轧辊缺陷问题,主要可以归结为前述4个因素,解决这些原因才能有效解决轧辊缺陷问题。
同时,此外,还要建立严格的工艺和操作规程,避免生产环节出现偏差,以确保轧辊表面质量。
大家一定要深入了解马钢冷轧轧辊缺陷的原因,切实落实上述防范措施,以保证冷轧轧辊表面的高标准,有效提升马钢冷轧生产效率,为满足市场需求打下坚实的基础,确保冷轧轧辊的质量和可靠性。
马钢冷轧轧辊缺陷的分析及防范措施

马钢冷轧轧辊缺陷的分析及防范措施
马钢冷轧轧辊的缺陷,严重影响了冷轧的质量,引起了工厂的重大损失。
因此,对这种缺陷的分析和防范措施的研究及实施具有十分重要的意义。
马钢冷轧轧辊缺陷主要有两类:局部失效缺陷和整体失效缺陷。
局部失效缺陷主要包括凹陷,纹路,毛刺等问题,这些缺陷大多是由轧辊表面的杂质、局部的温度、表面的生锈等对轧辊表面造成的破坏和形变产生的。
整体失效缺陷分为抗拉强度下降、表面质量下降、热阻力减小等。
其中,抗拉强度下降是由轧辊陈旧、热锻桩热处理之后无法维持原始结构状态、熔炼时组织状态差等引起;表面质量下降是由于熔化时产生的粒度不均匀和凝固后的机械损伤所导致;热阻力减小主要是因为热处理中铝合金和铁合金的熔炼凝固状态的变化所导
致的。
要防止马钢冷轧轧辊的缺陷,首先要加强冷轧材料的检测,明确冷轧材料的标准,以保证轧辊的质量。
第二要提高操作技术,明确轧辊加工的步骤,合理布置机械化设备,减少轧辊的损伤和缺陷的形成。
第三要提高热处理工艺,准确控制熔炼温度,熔炼组织,凝固组织,热处理温度和实际时间,保证热处理过程中组织状态及抗拉强度等参数符合规范要求。
最后,设备要定期检验和更新,确保设备能够按设计要求运行,避免缺陷的发生。
马钢冷轧轧辊缺陷的防范措施,要求我们必须加强对轧辊的管理,避免缺陷的产生。
同时,还要求设备的检修和更新,确保轧辊的正常
工作。
此外,还要定期对冷轧工艺进行审查和改进,以确保热处理过程中组织状态及抗拉强度等参数符合规范要求。
只有这样,才能保证马钢冷轧轧辊的质量,确保生产过程的高效安全。
马钢冷轧轧辊缺陷的分析及防范措施

马钢冷轧轧辊缺陷的分析及防范措施
马钢冷轧轧辊缺陷已成为冷轧工艺中的一个严重问题,严重影响操作和生产效率,并影响质量。
本文旨在分析轧辊缺陷及其发生原因,以及探讨有效防范措施。
1、轧辊缺陷分析
轧辊缺陷是指轧辊磨损,型面凹陷,表面裂纹,焊接部失效等现象。
它们的存在会影响轧辊的正常使用,影响冷轧过程的质量,缩短轧辊的使用寿命,并增加维修成本。
在实际生产中,轧辊缺陷常见原因主要有:
(1)轧辊质量不合格:因结构设计不合理,选用和制备材料不合格,加工工艺不合格等原因,提高了轧辊缺陷的可能性。
(2)轧辊磨损:由于滚压过程中的轧辊振动、局部过热、轧件本身结构不均匀等原因,导致轧辊表面磨损等缺陷的产生。
(3)焊接失效:由于焊接技术不足或焊缝质量不合格等原因,造成焊缝失效或断裂,从而使轧辊表面出现缺陷。
2、防范措施
(1)增强轧辊质量控制:在轧辊的设计、加工、焊接、组装等各个方面都应严格把关,加强对轧辊质量的控制,以确保轧辊质量稳定,减少轧辊缺陷。
(2)提高滚压过程控制:应采用合理的滚压参数,加强对滚压压力、温度及轧件材料等的控制,适当减小滚压力,以降低滚压过程中轧辊的磨损,防止轧辊损坏。
(3)加强焊接质量控制:应按照焊接技术标准,严格把关焊接技术操作,确保焊接缝的质量符合要求,避免轧辊出现焊接失效的缺陷。
3、结论
轧辊缺陷是影响工艺效率和产品质量的主要因素,应采取有效的措施来防范和消除其存在。
针对轧辊缺陷的发生,应加强轧辊的质量控制,提高滚压过程的控制,加强焊接质量控制,以最大程度地减少轧辊缺陷及其造成的损失。
冷轧-涂镀产品质量缺陷及改正措施

冷轧薄板之所以说是精品,一个主要的原因就是冷轧薄板对表面质量的严格要求,。
在可整以个说冶金行业中,冷轧薄板对表面质量是要求最高最严其,是宽而薄的冷轧钢带产品和对冲压成型性能有严格要求的产品。
这也是下游工序如涂漆、涂镀、冲压成型的要求,如宝钢经多轮攻关并3开、O发5板,就是为了向汽车创造厂家供应高级表面质量要求的冷轧产一。
而言,冷轧产品的表面质量按表面缺陷情况分为普通表面质量、较高级表面质量和高级表面质量三个的,定义在相关的标准中有规。
表列出冷轧产品可能浮现的表面缺陷的种类及可能产生的工序及原因,所当列然缺,陷不一定彻底,产生原因及工序也不一定彻底正确,这有待于在今后的实际生产中逐渐补充完善。
序号缺陷名称产生缺陷的可能工序冷轧钢板与钢带表面缺陷一、表面缺陷(一)、钢板与钢带不允许存在的缺陷1 气泡炼钢可能的产生原因炼钢时产生气泡,在热轧时又未焊合,酸洗冷轧后暴露在外2 3 45 6 78 9 1011 裂纹结疤或者结瘤拉裂夹杂折叠分层黑膜或者黑带乳化液斑点波纹和折印倒刺或者毛刺炼钢、热轧与冷轧及各加工工序酸洗与冷轧冷轧、镀锌与平整炼钢热轧、冷轧炼钢、热轧与冷轧酸洗冷轧与平整酸洗剪切过程由于炼钢热应力、轧制形变或者加工致应力集中造成酸洗未洗尽氧化皮,轧制时镶嵌于表面形成结疤张力过大、张力波动过大以及张力不稳定等原因造成炼钢原因轧制时呈粘性流动的金属被再次轧制后镶嵌于板材表面炼钢时成份偏析以及组织偏析、大块夹杂等原因造成并最终在轧制过程中表现为分层酸洗后烘干效果不好造成乳化液残留于钢带表面所致过酸洗等(待查)剪刃不锋利、上下剪刃错开角度大、剪刃角度不许等原因造成(二)、允许存在的且根据其程度不同来划分不同表面质量等级的缺陷12 34 麻点划痕擦伤兰色氧化色冷轧、光整与平整各工序及搬运吊装过程等搬运、吊装过程冷轧与平整轧制时塑性基体金属粘附于高速转动的轧辊表面所致由于轧制磨擦力使基体金属升温从而造成基体发蓝,特别是带钢边部更易于形成此缺陷5 浅黄色酸洗色酸洗6 轧辊压痕冷轧、光整与平整7 划伤搬运、吊装过程8 凹坑冷轧(三)、其他表面质量缺陷1 粘接罩式退火2 表面碳黑罩式退火3 生锈与腐蚀钢卷存放以及运输过程4 欠酸洗酸洗5 过酸洗酸洗二、板形缺陷1 切斜酸轧、精整等2 镰刀弯冷轧、光整与平整浪形(细分为单3 边浪、双边浪、冷轧、光整与平整中浪、斜浪等)4 瓢曲热轧、冷轧、光整与平整三、卷型缺陷1 塔型卷曲过程2 鼓包卷曲过程3 鼓耳卷曲过程四、尺寸缺陷1 厚度超差轧制过程2 宽度短尺切边过程3 长度超差钢板分切过程热镀锌钢板与钢带表面缺陷1 锌粒热镀锌过程2 厚边热镀锌过程酸洗后未烘干造成轧辊原因轧辊原因以及表层夹杂被轧出基体表面等原因形成凹坑由于在全氢气氛下长期加热造成钢卷表面残铁粉被还原为铁而造成,此外粘接还与卷取张力以及冷却速度等有关在全氢高温气氛下,钢铁表面残存轧制油发生分解形成碳黑沉积于钢卷表面防锈油质量不好或者未涂防锈油或者涂油量不足等,或者是存放环境湿度高等原因造成表现为还有氧化铁皮未洗掉表现为基体表面可见清晰轧制纹路指钢卷或者钢带切边时切斜带钢两边轧制力不平衡,轧制力响应时间滞后或者辊缝不均匀(辊缝调节不好)或者原料密度与硬度不均匀等造成原料密度与硬度不均匀、轧制时轧制力以及弯辊力调节响应不快或者不许、带钢张力波动过大等所致,此外上下轧辊辊径相差大也会造成浪形原料厚度方向上密度或者硬度不均匀,造成钢板上下两面塑性不均匀造成,卷取机卷曲精度不高造成钢带边部超薄并在连续卷曲过程中形成钢卷鼓起对于镀锌卷,如存在边部超厚,则可能卷取时钢卷两端鼓起轧制控制不许等切边不许或者原料边部缺陷原因控制精度原因等底渣被机械搅起或者因为锌液温度高而浮起,从而附着在镀锌板面上,并在冷却过程中形成锌铁化合物FeZn10气刀的角度调整不佳,造成对吹从而形成绕流;此外由于边部气流向外散失一部份使喷吹压力不够,也会造成厚边缺陷在冷却相变过程中,如果锌铁合金层迅速长大3 4 5 6 7 8 910111213141516171819 灰色镀锌层气刀条痕锌突起贝壳状表面条状花纹锌浪气刀刮痕颤动条痕沉没辊锌疤卷取皱纹光整花钝化斑点白锈粗糙度不合要求浪边镀层划伤钢基划伤热镀锌过程热镀锌过程热镀锌过程热镀锌过程热镀锌过程热镀锌过程热镀锌过程热镀锌过程热镀锌过程镀锌带钢卷取过程光整过程钝化过程存放运输过程热镀锌过程热镀锌从而使表面纯锌层消失,即没有锌的结晶花纹从而显现为灰色.普通认为,如果钢i 含量大于0。
马钢冷轧轧辊缺陷的分析及防范措施
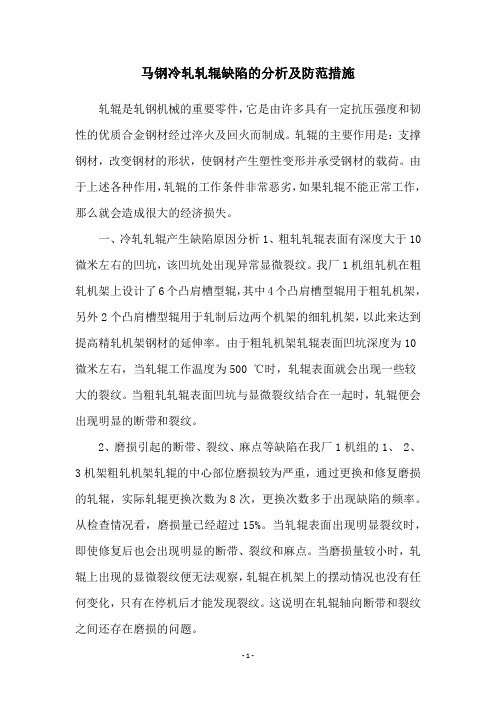
马钢冷轧轧辊缺陷的分析及防范措施轧辊是轧钢机械的重要零件,它是由许多具有一定抗压强度和韧性的优质合金钢材经过淬火及回火而制成。
轧辊的主要作用是:支撑钢材,改变钢材的形状,使钢材产生塑性变形并承受钢材的载荷。
由于上述各种作用,轧辊的工作条件非常恶劣,如果轧辊不能正常工作,那么就会造成很大的经济损失。
一、冷轧轧辊产生缺陷原因分析1、粗轧轧辊表面有深度大于10微米左右的凹坑,该凹坑处出现异常显微裂纹。
我厂1机组轧机在粗轧机架上设计了6个凸肩槽型辊,其中4个凸肩槽型辊用于粗轧机架,另外2个凸肩槽型辊用于轧制后边两个机架的细轧机架,以此来达到提高精轧机架钢材的延伸率。
由于粗轧机架轧辊表面凹坑深度为10微米左右,当轧辊工作温度为500 ℃时,轧辊表面就会出现一些较大的裂纹。
当粗轧轧辊表面凹坑与显微裂纹结合在一起时,轧辊便会出现明显的断带和裂纹。
2、磨损引起的断带、裂纹、麻点等缺陷在我厂1机组的1、 2、3机架粗轧机架轧辊的中心部位磨损较为严重,通过更换和修复磨损的轧辊,实际轧辊更换次数为8次,更换次数多于出现缺陷的频率。
从检查情况看,磨损量已经超过15%。
当轧辊表面出现明显裂纹时,即使修复后也会出现明显的断带、裂纹和麻点。
当磨损量较小时,轧辊上出现的显微裂纹便无法观察,轧辊在机架上的摆动情况也没有任何变化,只有在停机后才能发现裂纹。
这说明在轧辊轴向断带和裂纹之间还存在磨损的问题。
3、过热引起的内部裂纹、麻点、缩孔等缺陷钢水温度超过800 ℃时,轧辊内部便会产生气泡,在钢坯被拉入加热炉时,气泡被拉入钢坯内部,由于气泡的不稳定性,当轧辊冷却时,便会发生显著的收缩,收缩量与轧辊直径的平方根成正比。
当轧辊直径增大时,则收缩量也增大,最终导致轧辊纵向开裂。
通过研究发现,从2号机架轧辊纵向裂纹发生的部位观察,随着轧辊直径的减小,轧辊的表面尺寸呈现增大的趋势。
4、其他因素导致的缺陷在生产过程中,轧辊的弯曲和划伤等都会导致表面缺陷。
马钢冷轧轧辊缺陷的分析及防范措施

马钢冷轧轧辊缺陷的分析及防范措施马钢冷轧轧辊是冷轧原料从准备到成品时核心设备中重要的部件,质量良好的轧辊是冷轧厂提高产量和质量、提高竞争力的重要因素。
但是,因市场竞争压力大,冷轧厂仍存在质量问题,其中轧辊缺陷在一定程度上影响了产量和质量。
因此,对轧辊缺陷的分析及有效的防范措施至关重要。
马钢冷轧轧辊缺陷的主要表现形式是表面磨损和内部裂纹,其中表面磨损又可分为热蚀、冷蚀和磨损等类型,内部裂纹则是由于轧辊表面磨损引起的接触应力积聚而产生。
轧辊缺陷会降低轧辊表面粗糙度,一般会导致冷轧厂产量和质量下降,用料变动大,质量不稳定等问题出现。
基于上述分析,为了有效防治马钢冷轧轧辊缺陷,应重点围绕以下几点措施:首先,加强冷轧轧辊的精磨。
轧辊表面的磨损程度直接影响轧道质量,因此,冷轧厂应定期进行精磨,以提高轧辊表面的精度和光洁度,使轧辊表面磨损减少。
其次,优化冷轧轧辊表面处理工艺。
轧辊表面处理工艺包括渗碳、热处理、热喷涂和涂油等,合理的表面处理工艺可以有效缩小轧辊表面的粗糙度,延长轧辊的使用寿命,减少轧辊表面磨损。
再次,加强轧辊定期维护和保养。
轧辊温度、压力和滑动速度等,都会影响轧辊的表面磨损程度,因此,轧辊需要定期维护和保养,以保持轧辊正常工作,减少轧辊表面磨损。
最后,定期检查轧辊表面结构和断口。
定期检查轧辊温度、压力和滑动速度等情况,以及轧辊内部结构和断口的变化,及时发现和处理轧辊缺陷,可以有效避免轧辊表面磨损及裂纹扩大的情况出现。
总之,马钢冷轧轧辊缺陷是影响冷轧厂产量和质量的重要因素。
为此,应重点围绕加强冷轧轧辊的精磨、优化冷轧轧辊表面处理工艺、加强轧辊定期维护和保养以及定期检查轧辊表面结构和断口,结合实际情况采取有效措施,以预防轧辊缺陷的出现,提高冷轧厂的产量和质量。
冷轧带钢常见缺陷
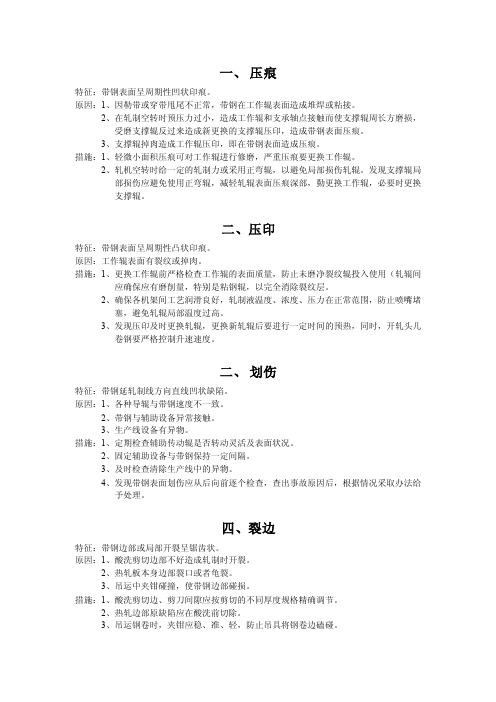
一、压痕特征:带钢表面呈周期性凹状印痕。
原因:1、因勒带或穿带甩尾不正常,带钢在工作辊表面造成堆焊或粘接。
2、在轧制空转时预压力过小,造成工作辊和支承轴点接触而使支撑辊周长方磨损,受磨支撑辊反过来造成新更换的支撑辊压印,造成带钢表面压痕。
3、支撑辊掉肉造成工作辊压印,即在带钢表面造成压痕。
措施:1、轻微小面积压痕可对工作辊进行修磨,严重压痕要更换工作辊。
2、轧机空转时给一定的轧制力或采用正弯辊,以避免局部损伤轧辊。
发现支撑辊局部损伤应避免使用正弯辊,减轻轧辊表面压痕深部,勤更换工作辊,必要时更换支撑辊。
二、压印特征:带钢表面呈周期性凸状印痕。
原因:工作辊表面有裂纹或掉肉。
措施:1、更换工作辊前严格检查工作辊的表面质量,防止未磨净裂纹辊投入使用(轧辊间应确保应有磨削量,特别是粘钢辊,以完全消除裂纹层。
2、确保各机架间工艺润滑良好,轧制液温度、浓度、压力在正常范围,防止喷嘴堵塞,避免轧辊局部温度过高。
3、发现压印及时更换轧辊,更换新轧辊后要进行一定时间的预热,同时,开轧头几卷钢要严格控制升速速度。
二、划伤特征:带钢延轧制线方向直线凹状缺陷。
原因:1、各种导辊与带钢速度不一致。
2、带钢与辅助设备异常接触。
3、生产线设备有异物。
措施:1、定期检查辅助传动辊是否转动灵活及表面状况。
2、固定辅助设备与带钢保持一定间隔。
3、及时检查清除生产线中的异物。
4、发现带钢表面划伤应从后向前逐个检查,查出事故原因后,根据情况采取办法给予处理。
四、裂边特征:带钢边部或局部开裂呈锯齿状。
原因:1、酸洗剪切边部不好造成轧制时开裂。
2、热轧板本身边部裂口或者龟裂。
3、吊运中夹钳碰撞,使带钢边部碰损。
措施:1、酸洗剪切边、剪刀间隙应按剪切的不同厚度规格精确调节。
2、热轧边部原缺陷应在酸洗前切除。
3、吊运钢卷时,夹钳应稳、准、轻,防止吊具将钢卷边磕碰。
五、热划伤特征:带钢沿轧制线方向无规律的条状凹痕。
原因:1、轧辊和热带温度过高。
锻钢冷轧工作辊常见辊面缺陷及预防措施
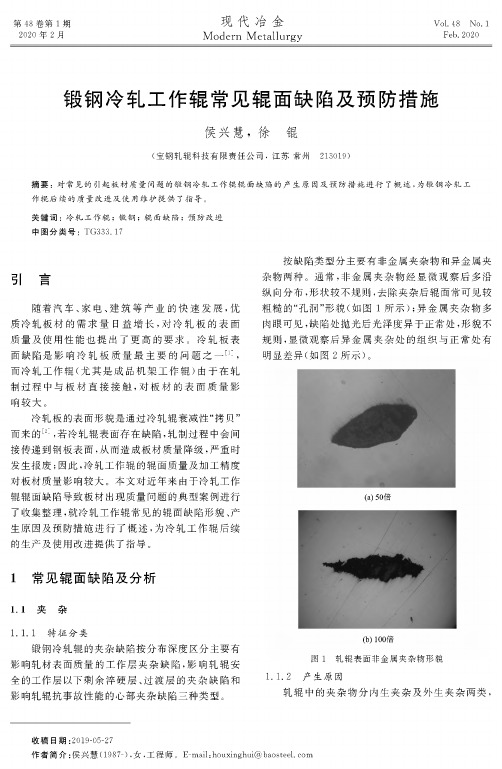
第48卷第1期2020年2月Vol.48No.1Feb.2020现代冶金Modern Metallurgy锻钢冷轧工作辊常见辊面缺陷及预防措施侯兴慧,徐锟(宝钢轧辊科技有限责任公司,江苏常州213019)摘要:对常见的引起板材质量问题的锻钢冷轧工作辍辍面缺陷的产生原因及预防措施进行了概述,为锻钢冷轧工作辍后续的质量改进及使用维护提供了指导。
关键词:冷轧工作辍;锻钢;辍面缺陷;预防改进中图分类号:TG333.17引言随着汽车、家电、建筑等产业的快速发展,优质冷轧板材的需求量日益增长,对冷轧板的表面质量及使用性能也提出了更高的要求。
冷轧板表面缺陷是影响冷轧板质量最主要的问题之一&1',而冷轧工作辊(尤其是成品机架工作辊)由于在轧制过程中与板材直接接触,对板材的表面质量影响较大。
冷轧板的表面形貌是通过冷轧辊衰减性“拷贝)而来的⑵,若冷轧辊表面存在缺陷,轧制过程中会间接传递到钢板表面,从而造成板材质量降级,严重时发生报废;因此,冷轧工作辊的辊面质量及加工精度对板材质量影响较大。
本文对近年来由于冷轧工作辊辊面缺陷导致板材出现质量问题的典型案例进行了收集整理,就冷轧工作辊常见的辊面缺陷形貌、产生原因及预防措施进行了概述,为冷轧工作辊后续的生产及使用改进提供了指导。
1常见辊面缺陷及分析!1夹杂1.1.1特征分类锻钢冷轧辊的夹杂缺陷按分布深度区分主要有影响轧材表面质量的工作层夹杂缺陷,影响轧辊安全的工作层以下剩余淬硬层、过渡层的夹杂缺陷和影响轧辊抗事故性能的心部夹杂缺陷三种类型。
按缺陷类型分主要有非金属夹杂物和异金属夹杂物两种。
通常,非金属夹杂物经显微观察后多沿纵向分布,形状较不规则,去除夹杂后辊面常可见较粗糙的“孔洞”形貌(如图1所示);异金属夹杂物多肉眼可见,缺陷处抛光后光泽度异于正常处,形貌不规则,显微观察后异金属夹杂处的组织与正常处有明显差异(如图2所示)%(a)50倍(b)100倍图1轧辊表面非金属夹杂物形貌1.1.2产生原因轧辊中的夹杂物分内生夹杂及外生夹杂两类,收稿日期:2019-05-27作者简介:侯兴慧(1987-),女,工程师。
冷轧轧辊缺陷及预防措施
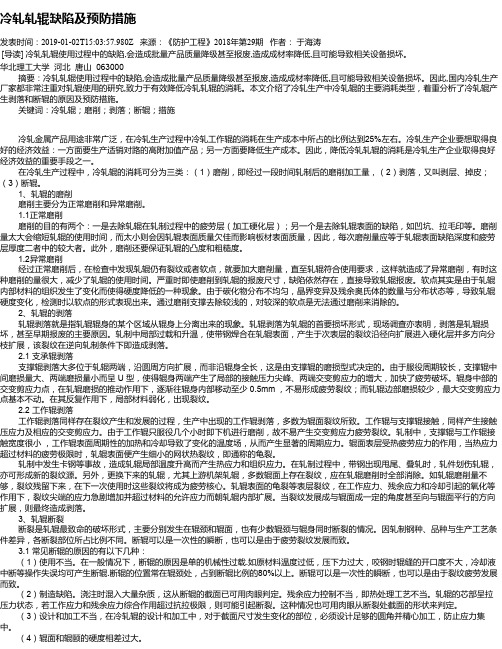
冷轧轧辊缺陷及预防措施发表时间:2019-01-02T15:03:57.980Z 来源:《防护工程》2018年第29期作者:于海涛[导读] 冷轧轧辊使用过程中的缺陷,会造成批量产品质量降级甚至报废,造成成材率降低,且可能导致相关设备损坏。
华北理工大学河北唐山 063000摘要:冷轧轧辊使用过程中的缺陷,会造成批量产品质量降级甚至报废,造成成材率降低,且可能导致相关设备损坏。
因此,国内冷轧生产厂家都非常注重对轧辊使用的研究,致力于有效降低冷轧轧辊的消耗。
本文介绍了冷轧生产中冷轧辊的主要消耗类型,着重分析了冷轧辊产生剥落和断辊的原因及预防措施。
关键词:冷轧辊;磨削;剥落;断辊;措施冷轧金属产品用途非常广泛,在冷轧生产过程中冷轧工作辊的消耗在生产成本中所占的比例达到25%左右。
冷轧生产企业要想取得良好的经济效益:一方面要生产适销对路的高附加值产品;另一方面要降低生产成本。
因此,降低冷轧轧辊的消耗是冷轧生产企业取得良好经济效益的重要手段之一。
在冷轧生产过程中,冷轧辊的消耗可分为三类:(1)磨削,即经过一段时间轧制后的磨削加工量,(2)剥落,又叫剥层、掉皮;(3)断辊。
1、轧辊的磨削磨削主要分为正常磨削和异常磨削。
1.1正常磨削磨削的目的有两个:一是去除轧辊在轧制过程中的疲劳层(加工硬化层);另一个是去除轧辊表面的缺陷,如凹坑、拉毛印等。
磨削量太大会缩短轧辊的使用时间,而太小则会因轧辊表面质量欠佳而影响板材表面质量,因此,每次磨削量应等于轧辊表面缺陷深度和疲劳层厚度二者中的较大者。
此外,磨削还要保证轧辊的凸度和粗糙度。
1.2异常磨削经过正常磨削后,在检查中发现轧辊仍有裂纹或者软点,就要加大磨削量,直至轧辊符合使用要求,这样就造成了异常磨削,有时这种磨削的量很大,减少了轧辊的使用时间。
严重时即使磨削到轧辊的报废尺寸,缺陷依然存在,直接导致轧辊报废。
软点其实是由于轧辊内部材料的组织发生了变化而使得硬度降低的一种现象。
- 1、下载文档前请自行甄别文档内容的完整性,平台不提供额外的编辑、内容补充、找答案等附加服务。
- 2、"仅部分预览"的文档,不可在线预览部分如存在完整性等问题,可反馈申请退款(可完整预览的文档不适用该条件!)。
- 3、如文档侵犯您的权益,请联系客服反馈,我们会尽快为您处理(人工客服工作时间:9:00-18:30)。
浅谈冷轧轧辊缺陷及预防措施
摘要:介绍了冷轧生产中冷轧辊的主要消耗类型,着重分析了冷轧辊产生剥落和断辊的原因及预防措施。
关键词:冷轧辊磨削剥落断辊措施
冷轧金属产品用途非常广泛,在冷轧生产过程中冷轧工作辊的消耗在生产成本中所占的比例达到25%左右。
冷轧生产企业要想取得良好的经济效益:一方面要生产适销对路的高附加值产品;另一方面要降低生产成本。
因此,降低冷轧轧辊的消耗是冷轧生产企业取得良好经济效益的重要手段之一。
在冷轧生产过程中,冷轧辊的消耗可分为三类:(1)磨削,即经过一段时间轧制后的磨削加工量,(2)剥落,又叫剥层、掉皮;(3)断辊
1、轧辊的磨削
磨削主要分为正常磨削和异常磨削。
1.1正常磨削
磨削的目的有两个:一是去除轧辊在轧制过程中的疲劳层(加工硬化层);另一个是去除轧辊表面的缺陷,如凹坑、拉毛印等。
磨削量太大会缩短轧辊的使用时间,而太小则会因轧辊表面质量欠佳而影响板材表面质量,因此,每次磨削量应等于轧辊表面缺陷深度和疲劳层厚度二者中的较大者。
此外,磨削还要保证轧辊的凸度和粗糙度。
1.2异常磨削
经过正常磨削后,在检查中发现轧辊仍有裂纹或者软点,就要加大磨削量,直至轧辊符合使用要求,这样就造成了异常磨削,有时这种磨削的量很大,减少了轧辊的使用时间。
严重时即使磨削到轧辊的报废尺寸,缺陷依然存在,直接导致轧辊报废。
软点其实是由于轧辊内部材料的组织发生了变化而使得硬度降低的一种现象。
由于碳化物分布不均匀,晶界变异及残余奥氏体的数量与分布状态等,导致轧辊硬度变化,检测时以软点的形式表现出来。
通过磨削支撑去除较浅的,对较深的软点是无法通过磨削来消除的。
2、轧辊的剥落
轧辊剥落就是指轧辊辊身的某个区域从辊身上分离出来的现象。
轧辊剥落为轧辊的首要损坏形式,现场调查亦表明,剥落是轧辊损坏,甚至早期报废的主要原因。
轧制中局部过载和升温,使带钢焊合在轧辊表面,产生于次表层的裂纹沿径向扩展进入硬化层并多方向分枝扩展,该裂纹在逆向轧制条件下即造成剥落
2.1 支承辊剥落
支撑辊剥落大多位于轧辊两端,沿圆周方向扩展,而非沿辊身全长,这是由支撑辊的磨损型式决定的。
由于服役周期较长,支撑辊中间磨损量大、两端磨损量小而呈 u 型,使得辊身两端产生了局部的接触压力尖峰、两端交变剪应力的增大,加快了疲劳破坏。
辊身中部的交变剪应力点,在轧辊磨损的推动作用下,逐渐往辊身内部移动至少 0.5mm ,不易形成疲劳裂纹;而轧辊边部磨损较少,最大交变剪应力点基本不动。
在其反复作用下,局部材料弱化,出
现裂纹。
见图1
2.2 工作辊剥落
工作辊剥落同样存在裂纹产生和发展的过程,生产中出现的工作辊剥落,多数为辊面裂纹所致。
工作辊与支撑辊接触,同样产生接触压应力及相应的交变剪应力。
由于工作辊只服役几个小时即下机进行磨削,故不易产生交变剪应力疲劳裂纹。
轧制中,支撑辊与工作辊接触宽度很小,工作辊表面周期性的加热和冷却导致了变化的温度场,从而产生显著的周期应力。
辊面表层受热疲劳应力的作用,当热应力超过材料的疲劳极限时,轧辊表面便产生细小的网状热裂纹,即通称的龟裂,见图2。
轧制中发生卡钢等事故,造成轧辊局部温度升高而产生热应力和组织应力。
在轧制过程中,带钢出现甩尾、叠轧时,轧件划伤轧辊,亦可形成新的裂纹源。
另外,更换下来的轧辊,尤其上游机架轧辊,多数辊面上存在裂纹,应在轧辊磨削时全部消除。
如轧辊磨削量不够,裂纹残留下来,在下一次使用时这些裂纹将成为疲劳核心。
轧辊表面的龟裂等表层裂纹,在工作应力、残余应力和冷却引起的氧化等作用下,裂纹尖端的应力急剧增加并超过材料的允许应力而朝轧辊内部扩展。
当裂纹发展成与辊面成一定的角度甚至向与辊面平行的方向扩展,则最终造成剥落。
3、轧辊断裂
断裂是轧辊最致命的破坏形式,主要分别发生在辊颈和辊面,也有少数辊颈与辊身同时断裂的情况。
因轧制钢种、品种与生产工艺
条件差异,各断裂部位所占比例不同。
断辊可以是一次性的瞬断,也可以是由于疲劳裂纹发展而致。
3.1 常见断辊的原因的有以下几种:
(1)使用不当。
在一般情况下,断辊的原因是单的机械性过载.如原材料温度过低,压下力过大,
咬钢时辊缝的开口度不大,冷却液中断等操作失误均可产生断辊.断辊的位置常在辊颈处,占到断辊比例的80%以上。
断辊可以是一次性的瞬断,也可以是由于裂纹疲劳发展而致。
(2)制造缺陷。
浇注时混入大量杂质,这从断辊的截面已可用肉眼判定。
残余应力控制不当,即热处理工艺不当。
轧辊的芯部呈拉压力状态,若工作应力和残余应力综合作用超过抗拉极限,则可能引起断裂。
这种情况也可用肉眼从断裂处截面的形状来判定。
(3)设计和加工不当,在冷轧辊的设计和加工中,对于截面尺寸发生变化的部位,必须设计足够的圆角并精心加工,防止应力集中。
(4)辊面和辊颐的硬度相差过大。
(5)辊颈的直径过小,强度不够。
3.2 常见辊颈的断裂位置在轧机上、下辊辊身与辊颈的过渡区处。
辊颈断裂的横向断口形貌有多种形状:锥面状断口,平整且断裂面垂直于辊身轴线的断口或与轴线呈的断口等。
典型的横向断口如图3所示。
该断口形貌呈锥面状,并可分为a、b、c三个断面。
其中a断面已经被乳化液污染,b、c面呈新断面,b断面有明显的
放射状纹棱,并指向a面。
4、预防措施
根据以上的分析,为了防止因缺陷造成轧辊报废,减少非正常的辊耗应采取几点措施:
(1)冷轧辊不能在有表面裂纹的状态下使用。
当轧辊轧制一定数量的带钢后,表面有可能出现轻微裂纹,如不及时发现和修磨,就会导致轧辊的表面剥落,影响产品质量。
这就要求轧机操作者要及时检查,按规定进行换辊。
(2)采用合理的轧制工艺。
要合理选择轧制力、张力和压下量,尽量避免轧机事故,如带钢打滑和缎带等。
轧机操作者应将带钢过度变形的地方先进行矫正。
(3)保证轧机的冷却和润滑系统的正常工作。
轧机在轧制过程中会产生大量的热量,而且轧辊与带钢之间也有很大的摩擦力,如果没有足够的冷却和润滑能力,轧辊表面和带钢的温度就会迅速升高,这样就很容易产生热划伤和粘连。
(4)预热轧辊,消除应力。
新冷轧辊投入使用前和每次磨削后使用时,必须进行预热,在轧辊达到110~100摄氏度时,可以消除大部分的表面应力。
轧辊上机后,要缓慢加速一对轧辊预热。
(5)冬季要对刚换下来的轧辊就行保温,均匀冷却,防止温差过大引起应力变化。
(6)正确磨削。
每次磨削要保证轧辊表面的加工硬化层完全去除,同时保证粗糙度,刚换下来的轧辊要在应力消除后再进行加工。
(7)对事故辊要进行探伤检查。
目前所用的探伤手段有涡流、磁粉和超声波探伤,前两种主要检测表面缺陷,超声波探伤可以发现内部的缺陷。
根据不同的情况,采取不同的探伤方法或者几种探伤方法同时检测,确保轧辊质量。
结论
通过对已出现轧辊缺陷的分析,初步掌握轧辊的缺陷,采取积极有效的预防措施,减少由轧辊缺陷引起的事故,减少轧辊的消耗,释放冷轧产能、增加经济效益。
参考文献:
[1] 刘德富,尹钟大. 冷轧工作辊的早期失效及预防措施[j]. 特殊钢. 2003(06)
[2] 宋淼. 冷连轧轧辊缺陷形成及相应措施[j]. 冶金设备. 2008(s1)。