玻璃熔窑保温节能技术的发展和存在的问题
玻璃窑炉节能技术路径优化与创新

玻璃窑炉节能技术路径优化与创新玻璃窑炉节能技术路径优化与创新玻璃窑炉是玻璃行业中最耗能的设备之一,如何优化和创新玻璃窑炉的节能技术路径成为了一个重要问题。
下面将从以下几个步骤逐步思考如何进行优化和创新。
第一步:节约玻璃窑炉的燃料消耗玻璃窑炉的主要能源消耗是燃料,因此首先需要思考如何节约燃料的消耗。
一种常见的做法是采用高效燃烧技术,例如预混燃烧技术和循环燃烧技术。
预混燃烧技术可以将燃料和空气充分混合,提高燃烧效率;而循环燃烧技术可以将燃烧产生的废热回收利用,进一步降低能源的消耗。
第二步:提高玻璃窑炉的热效率除了节约燃料消耗外,还可以通过提高玻璃窑炉的热效率来进一步节能。
一种常见的方法是采用高效的热交换器,将燃烧产生的废热回收利用。
此外,可以考虑对玻璃窑炉进行隔热处理,减少热量的散失。
这些措施可以有效提高玻璃窑炉的热效率,降低能源消耗。
第三步:优化玻璃窑炉的操作控制系统除了改进玻璃窑炉的内部结构和设备外,优化操作控制系统也是一个重要方面。
通过引入先进的自动化控制系统,可以实时监测和调整玻璃窑炉的运行状态,以最优的方式控制燃烧过程和热量分配。
这样可以确保玻璃窑炉的运行效率最大化,进一步降低能源消耗。
第四步:引入清洁能源替代传统燃料除了上述的措施外,还可以考虑引入清洁能源来替代传统燃料,进一步减少环境污染和能源消耗。
例如,可以考虑采用天然气、生物质能源或太阳能等清洁能源作为玻璃窑炉的燃料。
这样不仅可以降低碳排放和能源消耗,还可以提高企业的环境形象和可持续发展能力。
综上所述,优化和创新玻璃窑炉的节能技术路径可以通过节约燃料消耗、提高热效率、优化操作控制系统和引入清洁能源等多个方面来实现。
通过科学合理的设计和技术改进,玻璃窑炉的能源消耗将得到有效降低,进一步推动玻璃行业的可持续发展。
我国玻璃炉窑现状及节能技术的发展
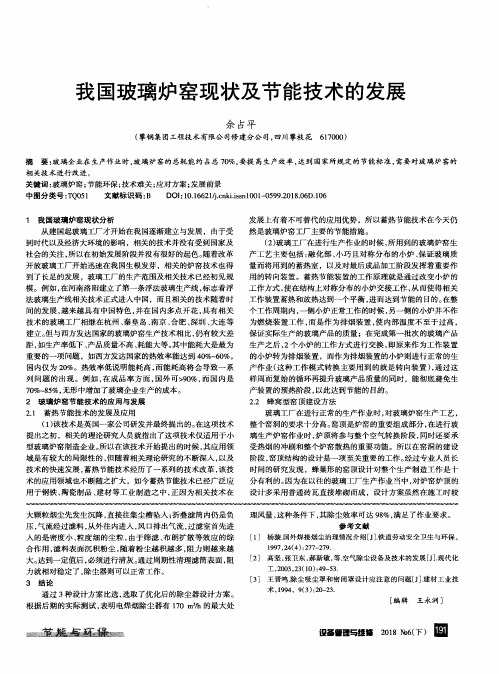
发展上有着不可替代的应 用优 势 ,所 以蓄热节能技术在今天仍 然是玻璃炉窑工厂主要的节能措施 。
(2)玻璃工厂在进行生产作业 的时候 ,所用到 的玻璃炉窑生 产工艺 主要包 括 :融化部 、小巧且对称 分布的小炉 、保证玻璃质 量而将用到 的蓄热室 ,以及对最后成品加工 阶段发挥着重要作 用 的转 向装置 。蓄热节能装置的工作原理就是通过改 变小 炉的 工作方式 ,使在结构上对称分布 的小炉交接工作 ,从 而使得相关 工作装置蓄热和放热达到一个平衡 ,进而达到节能的 目的。在整 个工作周期 内,一侧 小炉正常工作 的时候 ,另一侧 的小 炉并 不作 为燃烧 装置工作 ,而是作 为排烟装置 ,使 内部温 度不至于过高 , 保证实 际生产 的玻璃产 品的质量 ;在完成第一批次的玻璃产品 生产之 后 ,2个小炉 的工作方 式进 行交换 ,即原来作 为工作 装置 的小炉转为排烟装置 ,而作为排烟装置 的小炉则进行正常 的生 产 作业 (这种工作模式 转换主要用 到的就是转 向装置 ),通过这 样 周而复始 的循 环再 提升玻璃产 品质量 的同时 ,能彻底避免生 产装置 的预热 阶段 ,以此达到节能的 目的。 2.2 蜂 窝 型 窑 顶 建设 方 法
为简 ,也 llJ 竹 制 造 成 本 , 玻 璃 炉 窑 q-/ 作 业 时 ,会 因 炉 坝的 鼾 i射 过 小 能 达 到 预 期 的 敞热 效 果 。 2.3 个瓴燃 烧技 术 的 ,皮腱
[2] 高坚 ,张卫 东 ,郝新敏 ,等 .空气 除尘设备及技术 的发展 [J].现代化 工 ,2003,23(10):49—53.
[3] 王晋 鸣.除尘 吸尘罩 和密 闭罩 设计应 注意 的问题 [J].建 材工业技 术 ,1994,9(3):20—23. [编辑 王永 洲]
玻璃窑炉节能技术发展与应用
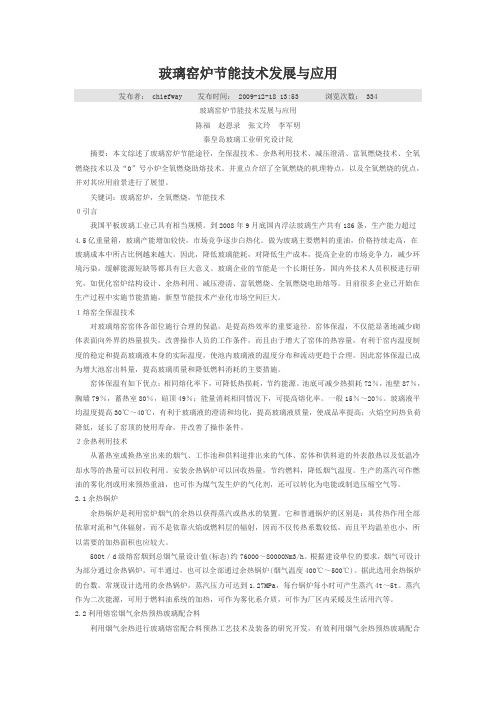
玻璃窑炉节能技术发展与应用发布者: chiefway 发布时间: 2009-12-18 13:53 浏览次数:334玻璃窑炉节能技术发展与应用陈福赵恩录张文玲李军明秦皇岛玻璃工业研究设计院摘要:本文综述了玻璃窑炉节能途径,全保温技术、余热利用技术、减压澄清、富氧燃烧技术、全氧燃烧技术以及“0”号小炉全氧燃烧助熔技术。
并重点介绍了全氧燃烧的机理特点,以及全氧燃烧的优点,并对其应用前景进行了展望。
关键词:玻璃窑炉,全氧燃烧,节能技术0引言我国平板玻璃工业已具有相当规模。
到2008年9月底国内浮法玻璃生产共有186条,生产能力超过4.5亿重量箱,玻璃产能增加较快,市场竞争逐步白热化。
做为玻璃主要燃料的重油,价格持续走高,在玻璃成本中所占比例越来越大。
因此,降低玻璃能耗,对降低生产成本,提高企业的市场竞争力,减少环境污染,缓解能源短缺等都具有巨大意义。
玻璃企业的节能是一个长期任务,国内外技术人员积极进行研究,如优化窑炉结构设计、余热利用、减压澄清、富氧燃烧、全氧燃烧电助熔等。
目前很多企业已开始在生产过程中实施节能措施,新型节能技术产业化市场空间巨大。
1熔窑全保温技术对玻璃熔窑窑体各部位施行合理的保温,是提高热效率的重要途径。
窑体保温,不仅能显著地减少砌体表面向外界的热量损失,改善操作人员的工作条件,而且由于增大了窑体的热容量,有利于窑内温度制度的稳定和提高玻璃液本身的实际温度,使池内玻璃液的温度分布和流动更趋于合理。
因此窑体保温已成为增大池窑出料量,提高玻璃质量和降低燃料消耗的主要措施。
窑体保温有如下优点:相同熔化率下,可降低热损耗,节约能源。
池底可减少热损耗72%,池壁87%,胸墙79%,蓄热室80%,碹顶49%;能量消耗相同情况下,可提高熔化率。
一般15%~20%。
玻璃液平均温度提高30℃~40℃,有利于玻璃液的澄清和均化,提高玻璃液质量,使成品率提高;火焰空间热负荷降低,延长了窑顶的使用寿命,并改善了操作条件。
我国玻璃窑炉的节能

我国玻璃窑炉的节能玻璃窑炉是玻璃工业生产过程中最关键的设备之一,同时也是能耗最高的设备之一、为了提高玻璃窑炉的节能效率,减少能源消耗,我国在玻璃窑炉的设计和运行方面进行了许多改进和创新。
一、窑炉结构优化玻璃窑炉的结构设计对于其能耗和热量利用效率有着重要的影响。
为了降低窑炉的热损失,减少能源消耗,我国通过优化窑炉的结构设计,提高玻璃窑炉的密封性能,减少热量的流失。
同时,采用双层炉壁结构,减少热量传输,进一步提高窑炉的热辐射利用率。
此外,还可以通过使用高效的绝热材料和热工设计,减少窑炉的散热损失,提高热量的利用效率。
二、燃料选择与燃烧优化玻璃窑炉的燃料选择和燃烧控制对于窑炉的能耗影响很大。
为了提高玻璃窑炉的节能效果,我国推广了使用更加清洁和高效的燃料,如天然气等。
与此同时,通过优化燃烧系统,采用先进的燃烧控制技术,控制燃料的供给和燃烧过程,提高燃烧效率,减少燃料的消耗量。
另外,还可以采用余热利用技术,将窑炉燃烧产生的余热用于其他生产环节的加热或热水供应,进一步降低能耗。
三、废热回收与利用玻璃窑炉的高温废气是一个很重要的能源资源,通过回收和利用废热,可以大大提高窑炉的节能效果。
我国在玻璃窑炉的废热回收和利用方面进行了许多研究和应用。
例如,通过安装余热回收装置,将窑炉的排烟中的废热用于热水供应或其他加热工序,可以显著减少能源消耗。
此外,还可以通过废热发电技术,将窑炉废热转化为电能,提高能源利用效率。
四、自动控制与智能化技术玻璃窑炉的自动化控制和智能化技术对于节能效果也有很大的影响。
通过引入先进的自动控制系统和智能化技术,可以实现对窑炉各项参数的精确测量和控制,降低能源的浪费。
例如,采用精确的温度控制系统、自动调节燃烧器的供气量等技术手段,可以提高窑炉的燃烧效率,减少能源的消耗。
另外,通过智能化技术的应用,可以实现对窑炉运行状态的实时监测和优化管理,及时发现和解决能耗问题,进一步提高窑炉的节能效果。
综上所述,我国在玻璃窑炉的节能方面进行了许多探索和实践,通过优化窑炉结构、优化燃料选择和燃烧控制、废热回收与利用以及自动控制与智能化技术的应用,不断提高窑炉的节能效果,减少能源的消耗。
电熔窑炉节能技术优化及应用

电熔窑炉节能技术优化及应用电熔窑炉是一种利用电能作为能源进行熔炼的设备,广泛应用于金属冶炼、玻璃熔化、陶瓷制造等工业领域。
传统的电熔窑炉在高温高能耗的情况下存在能源浪费、环境污染等问题。
为了提高电熔窑炉的能源利用率、降低排放物的产生,节能技术优化及应用显得尤为重要。
1. 燃烧系统优化传统电熔窑炉的燃烧系统存在着燃烧不充分、热量损失大的问题。
通过采用先进的燃烧控制技术和燃料预热技术,可以有效提高燃烧效率,降低燃料消耗和热量损失,从而实现节能降耗的目的。
2. 高效热传递技术利用换热器等设备实现余热回收和热量利用,可以将废气中的热能回收再利用,降低能源消耗。
采用高效隔热材料和热工设计,减小窑炉的散热损失,提高热传递效率,也是提高窑炉能源利用率的重要手段。
3. 智能控制系统智能控制系统可以实时监测窑炉的工作状态,根据熔炼的需要进行智能调节,优化能源利用,提高生产效率。
通过精细化的控制和优化,可以减少窑炉的能源消耗,降低生产成本。
4. 节能设备应用在电熔窑炉中,引入新型节能设备如能量回收设备、超导电磁加热技术等,可以有效提高窑炉能源利用效率。
通过技术改造和设备升级,实现能源的合理利用,减少能源浪费。
1. 炼钢行业钢铁行业是电熔窑炉的重要应用领域,传统的电熔窑炉在炼钢过程中能源消耗较大。
近年来,一些炼钢企业通过优化窑炉的燃烧系统,引入高效的热传递技术和智能控制系统,实现了能源消耗的大幅度降低。
2. 玻璃制造业玻璃制造业对电熔窑炉的能耗要求较高,而且排放物易对环境造成污染。
一些玻璃企业通过引入热能回收设备和换热器,在生产过程中充分利用余热,减少了能源消耗和排放物的排放。
3. 金属冶炼业金属冶炼业对电熔窑炉的能源要求也较为严格。
一些金属冶炼企业通过采用超导电磁加热技术和高效的隔热材料,提高了窑炉的能源利用效率,减少了能源消耗和生产成本。
三、电熔窑炉节能技术优化的发展趋势1. 绿色能源应用随着环保意识的不断提高,绿色能源在电熔窑炉中的应用将会逐渐增加。
浅谈玻璃炉窑的节能技术

浅谈玻璃炉窑的节能技术今年的十二五的开局之年,国家为应对环境危机,出台了一系列节能政策,尤其对高耗能产业,国家重拳出击,强制关闭了一些小煤窑,小窑炉等耗能企业。
作为高耗能的玻璃行业,其热量利用率只有35%-45%,其他的热量都排放到大气中,给环境造成了巨大负担。
发生炉煤气,作为玻璃炉窑的主要燃料,是煤炭在缺氧条件下产生的一种煤气。
近年来,随着煤价的不断攀升,煤价在玻璃成本中占的比例越来越大。
因此,降低玻璃能耗,对降低生产成本,提高企业的市场竞争力,减少环境污染,缓解能源短缺等都具有巨大意义。
为了降低成本,目前已有很多玻璃企业已开始在生产过程中实施节能措施,如炉体保温技术、余热利用技术、富氧燃烧技术。
(1)炉体保温技术对玻璃炉窑本体各部位进行合理的保温,如改用导热系数较低的耐火砖、适当增加保温层的厚度、使用性能较好的耐火材料,是提高炉窑热效率的重要途径。
炉窑本体的保温,不仅能显著地减少砌体表面向外界的散量损失,改善操作人员的工作条件,而且由于增大了炉体的热容量,有利于炉内温度制度的稳定和提高玻璃液本身的质量,同时还可以降低燃料的消耗,降低生产成本。
(2)余热利用技术从炉窑烟道排出的烟气,可以通过余热锅炉和空气预热器等换热设备回收其显热,降低排烟损失,提高炉窑的热效率。
通过余热锅炉回收的热量可以生产蒸汽,生产的蒸汽可以作为燃油的雾化剂,也可作为煤气发生炉的气化剂,还可用于工厂采暖和生活用水等。
从空气预热器出来的热空气可以作为玻璃炉窑的助燃空气,这样可以迅速提高炉内温度,改善炉内的燃烧气氛,提高炉窑的热效率,同时也可以达到节约燃料的目的。
(3)富氧燃烧技术富氧燃烧技术是以氧含量高于2l%的富氧空气或纯氧代替空气作为助燃气体的一种高效强化燃烧技术。
其特点在于不论是助燃空气还是燃烧废气体积都有所减少,降低了排烟损失,提高了熔窑的热效率。
研究表明:富氧燃烧技术不仅能够节约大量能源,减少环境污染,而且能提高玻璃的产量、质量,延长熔窑寿命。
建议玻璃生产节能减排建议书
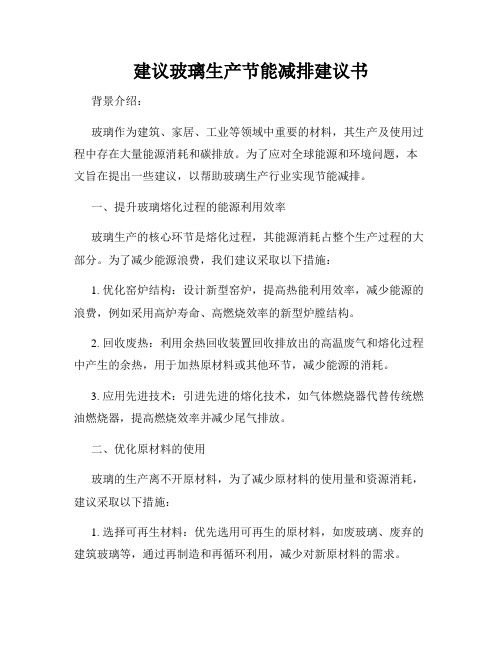
建议玻璃生产节能减排建议书背景介绍:玻璃作为建筑、家居、工业等领域中重要的材料,其生产及使用过程中存在大量能源消耗和碳排放。
为了应对全球能源和环境问题,本文旨在提出一些建议,以帮助玻璃生产行业实现节能减排。
一、提升玻璃熔化过程的能源利用效率玻璃生产的核心环节是熔化过程,其能源消耗占整个生产过程的大部分。
为了减少能源浪费,我们建议采取以下措施:1. 优化窑炉结构:设计新型窑炉,提高热能利用效率,减少能源的浪费,例如采用高炉寿命、高燃烧效率的新型炉膛结构。
2. 回收废热:利用余热回收装置回收排放出的高温废气和熔化过程中产生的余热,用于加热原材料或其他环节,减少能源的消耗。
3. 应用先进技术:引进先进的熔化技术,如气体燃烧器代替传统燃油燃烧器,提高燃烧效率并减少尾气排放。
二、优化原材料的使用玻璃的生产离不开原材料,为了减少原材料的使用量和资源消耗,建议采取以下措施:1. 选择可再生材料:优先选用可再生的原材料,如废玻璃、废弃的建筑玻璃等,通过再制造和再循环利用,减少对新原材料的需求。
2. 节约用料:进一步优化生产工艺,减少材料的浪费,通过提高精确的原材料计量和减少断损,降低用料量。
3. 强化原材料管理:建立严格的原料供应链管理体系,确保原材料的质量和稳定性,减少因材料变质而造成的浪费。
三、推广清洁能源和绿色制造清洁能源的应用和绿色制造是玻璃生产节能减排的关键方面,我们可以从以下方面入手:1. 太阳能和风能:在玻璃生产厂区建设太阳能和风能发电设施,利用可再生能源满足部分生产过程的能源需求,减少对传统能源的依赖。
2. 低碳技术应用:引进低碳技术,如高效冷却系统、绿色照明设备等,减少生产过程中的能源消耗和碳排放。
3. 减少污染物排放:加强废气和废水处理,净化排放物质,确保生产过程中的环境友好和无污染。
四、鼓励创新和合作为了推动玻璃生产行业的节能减排,鼓励创新和加强合作是必不可少的:1. 政策扶持:政府应制定相应的政策和经济激励措施,鼓励企业加大节能减排投资力度,推动技术创新和应用。
玻璃熔窑全氧燃烧技术及发展方向
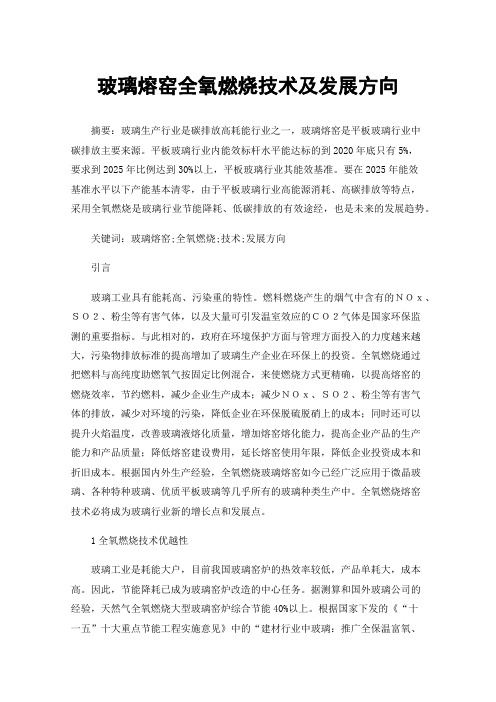
玻璃熔窑全氧燃烧技术及发展方向摘要:玻璃生产行业是碳排放高耗能行业之一,玻璃熔窑是平板玻璃行业中碳排放主要来源。
平板玻璃行业内能效标杆水平能达标的到2020年底只有5%,要求到2025年比例达到30%以上,平板玻璃行业其能效基准。
要在2025年能效基准水平以下产能基本清零,由于平板玻璃行业高能源消耗、高碳排放等特点,采用全氧燃烧是玻璃行业节能降耗、低碳排放的有效途经,也是未来的发展趋势。
关键词:玻璃熔窑;全氧燃烧;技术;发展方向引言玻璃工业具有能耗高、污染重的特性。
燃料燃烧产生的烟气中含有的NOx、SO2、粉尘等有害气体,以及大量可引发温室效应的CO2气体是国家环保监测的重要指标。
与此相对的,政府在环境保护方面与管理方面投入的力度越来越大,污染物排放标准的提高增加了玻璃生产企业在环保上的投资。
全氧燃烧通过把燃料与高纯度助燃氧气按固定比例混合,来使燃烧方式更精确,以提高熔窑的燃烧效率,节约燃料,减少企业生产成本;减少NOx、SO2、粉尘等有害气体的排放,减少对环境的污染,降低企业在环保脱硫脱硝上的成本;同时还可以提升火焰温度,改善玻璃液熔化质量,增加熔窑熔化能力,提高企业产品的生产能力和产品质量;降低熔窑建设费用,延长熔窑使用年限,降低企业投资成本和折旧成本。
根据国内外生产经验,全氧燃烧玻璃熔窑如今已经广泛应用于微晶玻璃、各种特种玻璃、优质平板玻璃等几乎所有的玻璃种类生产中。
全氧燃烧熔窑技术必将成为玻璃行业新的增长点和发展点。
1全氧燃烧技术优越性玻璃工业是耗能大户,目前我国玻璃窑炉的热效率较低,产品单耗大,成本高。
因此,节能降耗已成为玻璃窑炉改造的中心任务。
据测算和国外玻璃公司的经验,天然气全氧燃烧大型玻璃窑炉综合节能40%以上。
根据国家下发的《“十一五”十大重点节能工程实施意见》中的“建材行业中玻璃:推广全保温富氧、全氧燃烧浮法玻璃熔窑,降低烟道散热损失”精神,优化全氧超白压延玻璃生产线熔窑设计是必要的。
玻璃熔窑全氧燃烧技术及发展方向

“十四五”期间,对我国玻璃行业来说,面临着如何将“玻璃熔窑全氧燃烧技术”成果进一步产业化并为行业尽早实现节能减排和碳达峰碳中和,寻找可靠技术措施的重大工程技术问题。
玻璃熔窑全氧燃烧技术最显著的特点一是节能减排,二是提高玻璃质量,目前只有使用重油、天然气等高热值燃料,生产优质玻璃的企业才有动力和需求采用全氧燃烧技术。
通过近年的科研设计和生产实践,玻璃熔窑全氧燃烧技术已经在光伏玻璃、玻璃纤维、玻璃器皿、微晶玻璃等生产领域中广泛应用,其优异的提高玻璃质量、节能减排效果得到了充分验证,但广泛实施浮法玻璃全氧燃烧技术仍然面临着一些重大工程技术和经济问题,总的来说主要需要在以下几个方面开展技术创新:1优化全氧熔窑三维仿真模拟体系通过研究全氧燃烧玻璃熔窑火焰空间和玻璃液流场的三维数学模型,开发界面友好、操作方便、参数设置容易的全氧燃烧浮法玻璃熔窑三维仿真系统,使参与玻璃熔窑设计和仿真的工程技术人员只要输入熔窑结构、燃气布置和相关边界条件等参数,玻璃熔窑三维仿真系统将自动根据使用者提供的设计要求,完成CFD建模、求解和后处理三个步骤。
图1为全氧燃烧数学模拟火焰空间温度分布图。
图1 全氧燃烧数学模拟火焰空间温度分布图进一步形成玻璃原料COD值的快速测定、玻璃的Redox控制、熔体性能、澄清新工艺、火焰空间的数值模拟等理论与关键技术,为全氧燃烧条件下排除玻璃液中的微气泡,保证优质玻璃的熔制提供工艺指导。
2全氧浮法熔窑耐火材料国产化大型全氧浮法熔窑池宽超过11 m,比国内最大的全氧玻壳、玻璃纤维窑池宽30%以上。
到目前为止,国内已经建成了600 t/d、800 t/d规模的全氧燃烧平板玻璃生产线,主要耐火材料也都是国内配套,但要使窑炉达到高质量、长寿命,对大型全氧熔窑的结构安全、关键部位耐火材料的国产化还需要深入研究。
通过总结成功经验,克服存在的不足,持续改进、不断推进全氧玻璃熔窑关键耐火材料的国产化进程。
全氧窑的长宽比是一项重要指标。
我国玻璃熔窑余热发电现状及效果探讨

平板玻璃综合能耗 1 6 ( 标准煤 / 重量箱 ) 7 4
其 中: 浮 法 玻 璃 综 合 能 耗 1 5 - 3 9 ( 标准煤 / 重量箱 )
ห้องสมุดไป่ตู้
1 5 . 9 6
1 4 . 5
1 5 31
1 4 . 1 7
1 4 . 8 6
1 4 . 1 4
表3 2 0 0 9— 2 0 1 2年 我 国玻 璃 能 耗 情 况
2 0 0 9笠 20 1 0笠 2 0 1 1年 2 0 1 2正
在 国家政 策 的引导 下 , 通 过 多年 的努 力 , 我 国平 板 玻 璃 行业 取 得 了长足 的进 步 , 产 量 已连 续 2 4年 位 居 世 界第 一 。2 0 1 2 年 全 国生 产 平 板玻 璃 7 6 0 1 1 万 重
产量 / 万 重量 箱 增速 / %
6 0 2 2 4 0 . 9 2
6 6 0 8 2 9 . 7 2
7 8 5 1 1 7 6 0 1 1 1 8 . 8 1 — 3 . 1 8
中空窑时, 同时配套建设 了高温余 热发 电机组 , 称 为
“ 水 泥 干法 中空 余热 发 电窑”;1 9 2 6年启 新水 泥 厂也 建成 中空 窑余 热发 电站 。
准 。这 些政 策 的 出台以及标 准 的发 布实施 , 对 抑制 低 水 平 重 复建 设 , 改 善优 化 行 业 结构 , 推 进 行业 的节 能 减 排发 挥 了重要作 用 。 2 0 1 2年 全 行业 能 耗 约 1 1 2 9 . 5万 吨标 准 煤 , 平 板
统, 水泥窑产量一般大于 7 0 0 t / d , 单 台水泥窑余 热发
玻璃熔窑全氧燃烧技术应用过程中存在的问题及分析

材料科学与工程玻璃熔窑全氧燃烧技术应用过程中存在的问题及分析谢东恒2,姜宏1,2*(1.海南大学,海南省特种玻璃重点实验室,海南 海口570228;2.特种玻璃国家重点实验室,海南 澄迈571924)摘要:本文首先介绍了玻璃熔窑全氧燃烧技术特点,其次对其在实际应用过程中遇到的问题进行了总结,然后对全氧燃烧技术应用于玻璃熔窑的投资、运营成本进行测算,并针对玻璃熔窑实际生产中的关键工艺技术难题(如玻璃液表面泡沫多与澄清困难等)进行了系统研究分析,提出解决方法并成功将其运用在国内某条浮法玻璃熔窑生产线上。
关键词:全氧燃烧;玻璃熔窑;工艺控制;成本测算Problems and Analysis in the Application of the Oxy-fuel Combustion Technology in Glass FurnaceXIE Dong-heng 2, JIANG Hong 1,2*(1. Key Laboratory of Hainan Special Glass, Hainan University, Haikou, Hainan 570228, China; 2.State Key Laboratory of Special Glass, Dengmai, Hainan 571924, China)Abstract: This paper firstly introduces the technical characteristics of oxy-fuel combustion in glass melting furnace,secondly, it summarizes the problems encountered in practical application, and then estimates the investment and operating cost of oxy-fuel combustion in glass melting furnace. The key technological problems (such as froth and clarification of glass frit) in the actual production of glass melting furnace are systematically studied and analyzed, and solutions are put forward and successfully applied in a domestic float glass melting furnace production line.Key words: Oxy-fuel combustion; Glass furnace; Process control; Cost estimation0 引 言众所周知,传统的玻璃熔窑都是以空气作为助燃气体,采用空气助燃是导致高污染、高能耗的重要原因[1]。
浮法玻璃熔窑制氧机富氧燃烧节能技术应的几个关键问题

浮法玻璃熔窑制氧机富氧燃烧节能技术应的几个关键问题随着全球能源危机的加剧,燃料价格的不断上涨,玻璃生产的成本越来越高。
因而,玻璃熔窑的节能降耗研究是一个具有重大战略意义的课题。
我国平板玻璃工业已具有相当规模,每年浮法玻璃生产线消耗重油200万吨以上,燃料成本占玻璃生产成本已由30%上升为40%左右,严重影响着行业的经济效益。
因此,玻璃行业对节能技术的需求非常迫切。
近年来,随着玻璃熔窑节能降耗技术研究的深入,开发节能玻璃配方、优化玻璃熔窑结构、改善玻璃熔窑控制技术、加强玻璃熔窑保温和余热利用等实现玻璃熔窑节能手段的研究已相当成熟。
在此背景下,要实现熔窑进一步的节能降耗,富氧燃烧技术应运而生。
特别是近几年来,富氧燃烧技术得到了迅猛发展,成为当今玻璃行业中最活跃的研究课题之一。
该技术推广应用也必将为浮法玻璃生产行业带来可观的经济效益及社会效益。
秦皇岛玻璃工业研究设计院承担且完成了国家发改委重点科技攻关项目“浮法玻璃熔窑富氧燃烧节能技术的研究开发”,并已于2008年在秦皇岛组织召开了该项目验收会。
经参会专家质询、讨论,验收组一致同意该项目通过验收。
现提出若干关键问题,供大家参考。
富氧燃烧技术应用过程中的关键问题1.富氧燃烧工艺路线的设计富氧燃烧工艺路线的设计大致如下:富氧气体收集系统→气体混合系统→富氧调节系统→富氧换向系统→富氧预热系统→气体流量调节分配系统→富氧喷嘴→玻璃熔窑。
不同的玻璃厂实施富氧燃烧,其工艺路线会略有不同,主要根据其气保车间的结构(单高还是双高)而定。
主要设备如下:富氧气体收集装置、气体混合装置、换向系统、富氧预热设备、富氧喷嘴以及相应的管道和阀门。
2.富氧气体的收集大部分采用单高空分法制氮的浮法玻璃厂气保车间所产生的富氧气体都是直接排放到空气中。
富氧燃烧技术就是利用这些被浪费的富氧气体,添加富氧气体收集系统,将富氧气体收集起来。
本系统不会对气保车间有任何影响,也不会影响到玻璃生产线的正常生产。
电熔窑炉节能技术优化及应用

电熔窑炉节能技术优化及应用电熔窑炉是制备化工原料、金属材料以及玻璃等工业产品的重要设备之一。
在熔炼过程中,电熔窑炉的能耗一直是一个很大的问题。
为了解决这一问题,节能技术的研发和应用已经成为电熔窑炉行业的研究热点。
本文将着重探讨电熔窑炉节能技术的优化及应用。
一、电熔窑炉节能技术的现状电熔窑炉节能技术的研究主要包括两方面,一是优化熔炼工艺,减少能源损耗;二是改进设备结构,提高能源利用率。
在电熔窑炉节能技术的研究中,优化熔炼工艺是关键。
通过优化熔炼工艺,可以有效减少电熔窑炉的能耗。
对电熔窑炉内部的炉料配比、炉温控制、熔炼周期等方面进行优化,可以降低电熔窑炉的能耗。
还可以通过改进电熔窑炉的操作方式,提高生产效率,从而减少能源消耗。
改进电熔窑炉的设备结构也是提高能源利用率的重要途径。
采用高效的燃料燃烧技术、增加热能回收装置、优化电熔窑炉内部结构等,可以大幅度提高电熔窑炉的能源利用率,从而实现节能减排的目的。
1. 优化炉料配比和炉温控制在电熔窑炉的生产过程中,通过对炉料配比和炉温控制进行优化,可以达到节能减排的目的。
炉料配比的优化可以提高炉料的利用率,减少能源的浪费。
通过精确控制炉温,可以避免炉温过高或过低造成的能源损耗,提高电熔窑炉的能源利用率。
2. 改进操作方式改进电熔窑炉的操作方式也是节能的重要途径。
通过优化电熔窑炉的操作流程,减少停机时间,提高生产效率,从而减少电熔窑炉的能源消耗。
3. 采用高效的燃料燃烧技术在电熔窑炉的设计和制造中,采用高效的燃料燃烧技术可以有效减少能源的消耗。
通过改进燃烧器的结构,提高燃料的燃烧效率,可以降低电熔窑炉的燃料消耗,实现节能减排的目的。
电熔窑炉节能技术的应用已经成为电熔窑炉行业的发展方向。
通过应用节能技术,可以有效降低电熔窑炉的能耗,提高生产效率,降低生产成本,从而为企业带来更好的经济效益。
1. 提高能源利用率通过应用节能技术,可以提高电熔窑炉的能源利用率,减少能源的浪费。
电熔窑炉节能技术优化及应用

电熔窑炉节能技术优化及应用电熔窑炉是一种用于金属、陶瓷、玻璃等材料熔化和成型的重要设备,广泛应用于工业生产中。
传统的电熔窑炉在生产过程中存在能源消耗大、环境污染严重等问题。
为了解决这些问题,科研人员不断探索和优化电熔窑炉的节能技术,提高其能源利用效率,并推动其在实际生产中的应用。
本文将就电熔窑炉节能技术的优化及应用进行介绍和探讨。
一、传统电熔窑炉存在的问题传统的电熔窑炉通常采用电阻加热的方式,能源消耗大,效率低下。
而且在熔炼过程中产生的高温烟气和废气会对环境造成严重污染,加重大气污染和温室效应。
由于高温条件下的熔融过程,传统的电熔窑炉易产生热能的散失和物料的不均匀熔化,导致能源的浪费和生产成本的增加。
二、电熔窑炉节能技术的优化为了解决传统电熔窑炉存在的问题,科研人员提出了一系列的节能技术,并进行了不断的优化和改进。
1. 高效节能加热元件传统的电熔窑炉通常采用电阻丝、电石墨等作为加热元件,能量利用率低。
现代电熔窑炉开始采用高效的陶瓷电阻加热元件,利用其快速加热、均匀加热等优点,提高了加热效率,降低了能源消耗。
2. 高效节能的炉体结构设计传统的电熔炉炉体设计不科学,导致能量的大量散失。
现代熔窑炉开始采用双层炉体结构,有效减少了热能的散失,提高了能源的利用效率。
3. 废热回收技术在熔炼过程中产生的高温烟气和废气能够通过废热回收技术进行利用,例如通过换热器、热回收装置等将废热回收,再次利用,降低了能源消耗和环境污染。
4. 智能控制系统引入智能控制系统,通过温度、压力等参数的实时监测和控制,保证电熔窑炉在最佳状态下工作,提高了生产效率和能源利用效率。
三、电熔窑炉节能技术的应用优化的电熔窑炉节能技术已经开始在实际生产中得到了应用,并取得了显著的效果。
1. 金属熔炼行业金属熔炼是电熔窑炉的主要应用领域之一,传统的金属熔炼工艺能源消耗大,而且产生大量废气和废渣,严重污染环境。
采用优化的电熔窑炉节能技术后,能源消耗大大降低,废气和废渣得到有效处理和利用,环境污染得到了有效控制。
玻璃窑炉发展现状

玻璃窑炉发展现状
近年来,玻璃窑炉的发展取得了显著的进展。
为了满足不断增长的市场需求和节能减排的要求,玻璃窑炉逐渐迈向智能化、高效化和环保化的方向发展。
首先,智能化技术的应用使得玻璃窑炉的生产过程更加自动化、智能化。
传统的玻璃窑炉操作过程中需要大量的人工参与,容易出现人为操作失误。
而通过引入先进的自动控制系统,玻璃窑炉的温度、压力、时间等参数可以实现精确控制,从而提高生产效率和产品质量。
其次,高效化技术的应用使得玻璃窑炉的能源利用率大幅提升。
传统的玻璃窑炉存在着大量的能量浪费现象,如烟气中的热能未能充分利用。
而通过多级回热、余热利用等技术手段,可以有效提高玻璃窑炉的能源利用效率,降低能源消耗。
另外,环保化技术的应用使得玻璃窑炉的尾气排放得到有效控制。
玻璃窑炉的生产过程中会产生大量的废气、废水和固体废弃物,给环境造成严重污染。
而通过引入多级净化、脱硫、脱硝等技术,可以有效去除尾气中的有害物质,提高环境治理水平。
总的来说,玻璃窑炉的发展正朝着智能化、高效化和环保化的方向不断迈进。
随着技术的进步和创新,相信玻璃窑炉的发展前景将更加广阔。
玻璃窑炉如何更好的节能

玻璃窑炉如何更好的节能玻璃窑炉如何更好地节能引言:玻璃工业是一个能源消耗较大的行业,其中窑炉是主要能耗设备之一。
由于其高温作业和长时间运行,玻璃窑炉的能耗占据了整个生产线的重要比例。
因此,如何降低玻璃窑炉的能耗,节约能源成为玻璃工业的一项重要任务。
本文将就玻璃窑炉如何更好地节能进行探讨。
一、优化玻璃窑炉设计窑炉的设计是节能的关键。
具体而言,可以通过改善窑炉的结构和燃烧系统来降低能耗。
1. 优化窑炉结构:合理的窑炉结构可以减少能量损失。
例如,采用双层窑炉结构,可以减少外部热辐射对内部材料的热损失。
此外,增加窑炉的隔热层厚度,可以减少热能散失。
2. 改进燃烧系统:优化燃烧系统可以提高燃料利用率,减少能耗。
可以采用先进的燃烧技术,如预混燃烧技术、过热空气燃烧技术等。
除此之外,还可以采用余热回收技术,将燃烧产生的热能转化为工艺过程所需的热能,进一步提高能源利用效率。
二、控制燃料选择选择合适的燃料可以降低窑炉的能耗。
下面介绍几种常用的燃料选择。
1. 天然气:天然气作为一种清洁、高效的燃料,具有燃烧稳定、热值高的特点。
将燃烧系统调整为适合天然气燃烧的状态,可以减少能耗,降低环境污染。
2. 生物质能源:生物质能源是一种可再生能源,如木屑、秸秆等。
通过将生物质能源与传统燃料混合使用,可以减少对传统燃料的依赖,并且减少温室气体的排放。
3. 光伏发电:光伏发电是利用太阳能转化为电能的技术。
将光伏发电与传统燃料相结合,可以减少对传统燃料的使用,降低玻璃窑炉的能耗。
三、有效控制窑炉运行参数科学合理地控制窑炉的运行参数,可以降低能耗。
1. 温度控制:合理控制窑炉的温度可以减少能量的浪费。
通过准确、稳定地控制窑炉温度,避免过高或过低的温度,可以提高玻璃生产的质量,并减少能耗。
2. 空气流动控制:窑炉的空气流动对玻璃生产起着重要的作用。
通过调整窑炉内的空气流动速度和方向,可以提高燃烧效率,减少能耗。
3. 玻璃成分控制:合理控制玻璃的配方和成分比例,可以降低生产过程中的能耗。
浮法玻璃熔窑的节能技术及其发展
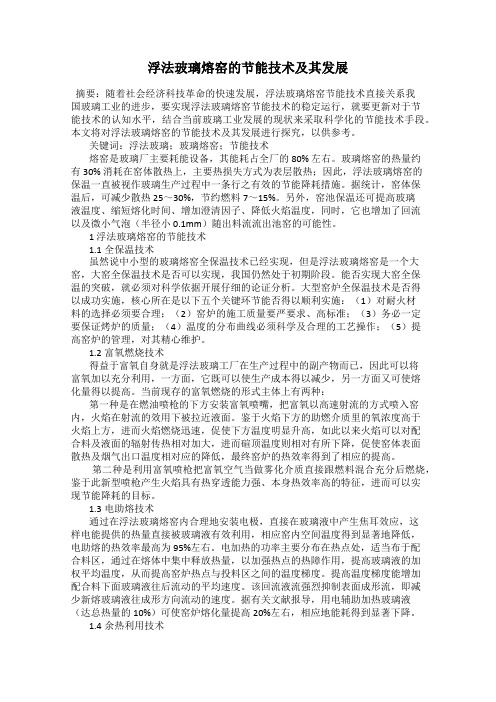
浮法玻璃熔窑的节能技术及其发展摘要:随着社会经济科技革命的快速发展,浮法玻璃熔窑节能技术直接关系我国玻璃工业的进步,要实现浮法玻璃熔窑节能技术的稳定运行,就要更新对于节能技术的认知水平,结合当前玻璃工业发展的现状来采取科学化的节能技术手段。
本文将对浮法玻璃熔窑的节能技术及其发展进行探究,以供参考。
关键词:浮法玻璃;玻璃熔窑;节能技术熔窑是玻璃厂主要耗能设备,其能耗占全厂的80% 左右。
玻璃熔窑的热量约有 30% 消耗在窑体散热上,主要热损失方式为表层散热;因此,浮法玻璃熔窑的保温一直被视作玻璃生产过程中一条行之有效的节能降耗措施。
据统计,窑体保温后,可减少散热 25~30%,节约燃料7~15%。
另外,窑池保温还可提高玻璃液温度、缩短熔化时间、增加澄清因子、降低火焰温度,同时,它也增加了回流以及微小气泡(半径小 0.1mm)随出料流流出池窑的可能性。
1 浮法玻璃熔窑的节能技术1.1全保温技术虽然说中小型的玻璃熔窑全保温技术已经实现,但是浮法玻璃熔窑是一个大窑,大窑全保温技术是否可以实现,我国仍然处于初期阶段。
能否实现大窑全保温的突破,就必须对科学依据开展仔细的论证分析。
大型窑炉全保温技术是否得以成功实施,核心所在是以下五个关键环节能否得以顺利实施:(1)对耐火材料的选择必须要合理;(2)窑炉的施工质量要严要求、高标准;(3)务必一定要保证烤炉的质量;(4)温度的分布曲线必须科学及合理的工艺操作;(5)提高窑炉的管理,对其精心维护。
1.2富氧燃烧技术得益于富氧自身就是浮法玻璃工厂在生产过程中的副产物而已,因此可以将富氧加以充分利用,一方面,它既可以使生产成本得以减少,另一方面又可使熔化量得以提高。
当前现存的富氧燃烧的形式主体上有两种:第一种是在燃油喷枪的下方安装富氧喷嘴,把富氧以高速射流的方式喷入窑内,火焰在射流的效用下被拉近液面。
鉴于火焰下方的助燃介质里的氧浓度高于火焰上方,进而火焰燃烧迅速,促使下方温度明显升高,如此以来火焰可以对配合料及液面的辐射传热相对加大,进而碹顶温度则相对有所下降,促使窑体表面散热及烟气出口温度相对应的降低,最终窑炉的热效率得到了相应的提高。
- 1、下载文档前请自行甄别文档内容的完整性,平台不提供额外的编辑、内容补充、找答案等附加服务。
- 2、"仅部分预览"的文档,不可在线预览部分如存在完整性等问题,可反馈申请退款(可完整预览的文档不适用该条件!)。
- 3、如文档侵犯您的权益,请联系客服反馈,我们会尽快为您处理(人工客服工作时间:9:00-18:30)。
14l
带来的效益结果却差异不同。主要表现在: l、对玻璃窑炉强化保温的系统知识认识不足。 玻璃企业往往在设计和建造时期对玻璃窑炉保温系统知识的认识不足,导致在窑炉使用中后期 能耗异常上升,甚至烧损修补时并未真正认识到:保温的结构和材料的选择决定了这种现实。我们 认为玻璃熔窑保温节能效果的持续稳定关键在于保温的结构和材料,保温结构的关键在于实现真正 有效的密封。在此前提下,稳定保温节能效果在于保温材料的选择。首先:做好玻璃窑炉的密封是 玻璃窑炉保温节能的关键,当不进行密封或是密封不严,就会产生沿砖缝窜火,尤其在保温中加剧 了烧损速度,烧损造成保温层揭掉、随着窑炉的运行,这种情况会越来越严重,造成大量的热量损 失.密封既是个选材问题,又是个结构问题,二者都以满足强化保温使用要求为目的。实施强化保 温主要问题之一是设置严格而有效的密封结构,它的主要功能是确保砌体之间和碹砖与密封层形成 严密的整体结构,这种经过严格密封的砌体,既起到了密封保温作用,还起到了增加整体结构强度 的作用。其次:密封施工操作是实现窑体强化保温的重要环节,必须严格按着施工程序、操作方法
依据:
2、
特种高效耐火隔热系列材料和具有特殊功能的密封系列材料的研究开发成功以及优质硅砖
的投入使用,为熔窑碹项实施强化保温创造了可行的先决条件。 研究结果表明,在满足某些条件下.可以对熔制钠钙玻璃熔窑的硅砖碹项进行强化保温,并且 应该进一步加大保温力度。因此。我公司八十年代中期在全国率先提出了熔窑大碹密封与强化保温 建议与论证喁J,并且在轻工行业青岛晶华玻璃厂马蹄窑推广使用成功的基础上【引,又提出了大型平板 窑实施强化保温的研究开发课题,1989年在秦皇岛耀华集团一厂九机窑进行了强化保温首次使用试 验,取得了大型熔窑大碹强化保温的成功经验。1992年4月通过了河北省科委技术鉴定,鉴定结论
140
术现已在世界各地的50多座窑炉应用,降低热损失率达75—90%【2l。前苏联开发一种磷酸盐珠光体的 新型隔热材料,其特点是容重轻(800-1lOOKg/cm3),导热率低(0.45Kcal/m2.℃-h),是玻璃熔 窑有效的隔热材料之一,在熔化部碹顶上使用,可使表面温度降低至120-135"C.隔热保温效率有 了明显提高【3l。“Lubisol”技术在中国90年代秦皇岛耀华国家示范线浮法窑建设中被引进,使用 一个窑期后因造价昂贵和国内保温技术和材料发展,成为孤例。 国内玻璃窑炉的强化密封保温技术走过了艰难推广道路,主要原因是从理论和技术角度特别是 对玻璃熔窑硅砖碹顶实施强化隔热保温的争议,当时许多业内业内专家认为,对硅砖碹顶进行强化 保温会使热负荷增大,蚀损加剧,影响大碹的使用寿命:还有人认为,硅砖碹顶保温要适中,不宜 提高保温力度,硅砖碹项的承受能力是有限的,进一步加大保温力度,会使大碹使用的安全性和可 靠性不能得到保证;较为普遍地认为,国内生产的硅砖不能满足强化保温使用要求,要进行大碹强 化保温,要求从国外进口优质硅砖:甚至有业内权威在其培训班中认为玻璃生产企业.窑炉密封无 用、保温无用,玻璃生产企业应该注重的是产量和质量而不是能耗的高低等等.在能耗并不为国家 和企业重视的年代里其难度更是可想而知。 应该指出,尤其窑炉硅砖碹顶实旄强化保温之所以得以实施并取得成功,是借助于两项独立的 研究成果: l、对熔窑大碹硅砖使用后的损毁机理的研究‘4・5・6¨。,它为大碹实施强化保温提供了重要的理论
l ห้องสมุดไป่ตู้9
b、熔窑碹顶实施强化保温之后,外表面温度显著降低,保温效果特别明显,经第一阶段的强化保温 降低到1340.1千卡/米2・小时,即减少了7117千卡/米2・小时,散热损失降低84.15%,达到了强 化保温减少散热损失要求。 c、进一步提高保温力度,使其外表面温度达到现在实施中的最低水平,即外表面温度降至80"C, 热损失降为793.8千卡/米2・小时,散热损失降低9096以上,这是目前世界先进水平。 在计算节能价值时,我们取重油发热值为9500Kcal/Kg,重油进厂价格(包括装运费)按每吨 2500元人民币计算。 从热损失计算结果可见,碹项进行强化保温之后节能效果显著,与不保温相比: 当散热损失减少数量为7117千卡/米2・小时。
和质量要求进行。
2、对玻璃窑体强化保温的部位局限。 目前国内玻璃窑炉中相对建材行业浮法窑炉保温部位情况好于轻工瓶罐行业窑炉,在有些玻璃企 业中认为碹项和蓄热室墙体保温就是保温,真正实现整个窑体如池底、小炉、甚至烟道全面密封保 温还有待提高。 3、对密封保温材料重要性和施工质量重要性认识不足. 在玻璃企业中对窑炉耐火材料的认识一直以来都是重视关键部位耐火材料,如电熔砖、碹顶硅 砖及蓄热室内格子体等大宗耐火材料,把砌筑泥浆、密封耐火材料、保温耐火材料当成“辅材”, 这样造成结果是对材料选择相对随意,以价格高低唯选择条件,对质量的要求和把控不严。窑炉砌 筑施工和密封保温施工的质量水平是目前存在主要问题,以上情况造成砌体透气烧损后,不但承担 材料的损失、修补费用,而且造成能耗的更大损失。近几年我公司从承担越来越多的窑炉异常损坏 的修补中,可以明显感觉到这种损失对玻璃企业效益带来的明显损失。 国外玻璃窑炉相对国内玻璃窑炉从窑炉的结构而言并无明显的优势,相反国内尤其是轻工玻璃 马蹄焰窑炉近年来的不断窑炉结构创新,甚至走在世界前列。但是在耐火材料的质量、砌筑、使用 的稳定规范等方面的差异,在使用结果上产生了明显差距。正是这种不稳定和不规范使也使得玻璃 窑炉的强化保温技术在实践中走出了自己的路子,那就是严格有效的窑炉密封是取得稳定保温效果 的前提,在这种技术思路情况下,从理论、结构、材料、施工操作逐渐形成了完善的系统。迄今为 止,我公司在全国210余座不同类型的玻璃熔窑推广了密封强化保温技术,其中约有90座是大型平 板窑(六座国外浮法窑炉),降低热损失90%以上,从2005年皮尔金顿(常熟)浮法线对我公司窑 炉密封材料通过英国本部详细研究和评估后采用,到2007年英国皮尔金顿兄弟公司考利西尔浮法线 采用,以及国内自行设计,至今仍在使用,窑龄11年的厦门明达500d/t浮法二线系统采用密封保 温结构和材料效果看,无疑确定了这种技术的可靠和价值。 应该特别指出,对玻璃熔窑实施强化保温不仅可以节省大量热能和燃料,而且对整个玻璃熔化 工艺产生重大影响:强化保温蓄积的热量大约是未进行保温的二倍半,这些热量对减少窑内温度波 动,提高炉料热均匀性具有重要作用。众所周知,保持窑炉温度的高温稳定对玻璃熔化过程,即获 取均匀的玻璃是非常重要的。如碹项对配合料和玻璃液的热辐射是熔化能量的主要来源,强化保温 碹项保持稳定的高温加速了熔化过程,提高了熔化率和熔化质量。因此,强化保温是节约能源,提
式中凡决定于散热表面位置的系数,
当散热面为向上的平壁时,肛2.8
因此,窑项向环境的散热损失,可由(1)和(2)两式计算求出。 l、保温前(即不进行保温时),碹项散热损失为: ql-Q,(t。厂t。)=27.55(327—20)=8457.8千卡/米2・小时 2、碹顶实施强化保温,前期取外表面平均温度1 10"C,其散热损失为:
与国内玻璃工业窑炉保温技术相比,国外玻璃工业窑炉保温技术发展相对保守和缓慢,在我国
全引进的轻工玻璃窑炉如:广州ACL生产线线和上海耀华皮金顿浮法线的窑炉保温在十余年来,以 及新的窑期内并无变化,采用的结构仍然是以轻质保温砖为主。80年代未美国一条浮法玻璃窑炉首 先采用“Lubisol”的隔热保温材料,当隔热材料厚度在200m左右时,热损失率降低了75%以上【¨. Lubisol工程公司是保加利亚一家生产玻璃熔窑碹项整体隔热材料的专业公司,该公司的材料及技
q i=Q
2(tf2一t。)=14.89(110-20)=1340.1千卡/米2・小时
3、碹项实施强化保温,外表面温度降为80"C,其散热损失为:
q后=Q
3(tf3一t。)=13.23(80—20)=793.8千卡/米2・小时
从以上计算结果可以看出: a、熔窑碹项在不保温的情况下,散热损失十分严重,每平方米每小时散热量高达8457.8千卡。
【千卡/米2.小时】——(1)
其中:qt一每平方米窑壁散热损失(千卡/米2.小时) t.-一窑炉壁外表面温度(℃)
t。一周围空气的温度(℃)
a
t~窑炉外壁与周围空气之间的对流,辐射换热系数【千卡/米2・℃・小时】
当窑炉周围空气为自由运动时,Q。值可用下列公式计算:
Q。孔瓜+盥竺盘!眦a。肥鼬,
‰一fcr
玻璃熔窑保温节能技术的发展和存在的问题
高峰 (太原高科耐火材料有限公司
山西太原030006)
玻璃窑炉是玻璃工业能源消耗的关键热工设备,其能耗占全厂的80%左右,玻璃窑炉的节能降 耗是整个玻璃工业节能的关键,搞好玻璃窑炉的节能降耗是提高玻璃企业经济效益的主要手段。当
能源成为企业沉重负担因素时,就会使能耗高、成本高企业处于更加艰难的处境,生存和利润决定
了企业对窑炉能耗的关注,也使得各种提高玻璃窑炉节能技术应用的更加普遍,从近20年专注于玻 璃窑炉保温节能工作的实践,笔者认为强化窑体全保温并长期稳定的保持窑炉密封保温效果是玻璃 工业节能最有效、最直接的途径之一。 一、强化窑体全保温并长期稳定的保持窑炉密封保温效果是玻璃窑炉节能的最有效的途径。 从玻璃窑炉的熟效率分析,使得占整个热消耗三分之一的窑体散热减少,是显而易见的节能方 式,以窑炉熔窑碹项为例,通过以下对散热量和节能价值计算可以得出以下数据。 表面散热的数据分析根据实际测试结果,保温前外表面温度取平均温度327‘C:保温后外表面 温度前期取平均温度1 10"C,后期降为80"C;周围空气温度取全年平均室温20"C。 对连续式操作的玻璃熔窑,通过窑体向外散失的热量,属于稳定热流。按传热学原理,这种散 热可用下式进行计算: q1=Q-(t.t—t.)
每平方米每天节省重油数量为:—71百17矿x
24=17.98Kg,
折合44.95元;
每平方米全年节省重油数量为:—71—17弋x商2菇4x—3—65=6562.6翰,折合16406.50元:
当散热损失降为793.8千卡/米2・小时,热损失减少7664千卡/米2・小时。