玻璃熔制及熔窑---玻璃熔制过程剖析
玻璃熔制及熔窑---玻璃熔制过程

SiO2 + Al 2 O3 一般工业玻璃:τ = Na 2 O + K 2 O
SiO2 + Al 2 O3 硼酸盐玻璃:τ = 1 Na 2 O + K 2 O + B2 O3 2 SiO2 + Al 2 O3 铅酸盐玻璃:τ = Na 2 O + K 2 O + 0.125PbO
玻璃液的澄清
临界半径rk: 1.微小气泡的形成有利于系统自由焓的降低,促使 核泡长大。 2.核泡的形成,生成新的两相界面,使系统表 面能增大。 排出气泡的方式:半径大于rk的气泡上升排除,小于rk的溶 解消失。 a.多个可见小气泡集合为一个大气泡(由于小气泡相距 气泡 较远较难进行); 长大 的原 b.溶解的气体渗入气泡,使之扩大(实际进行); 因 c. 澄清剂分解的气体渗入气泡或玻璃液。
玻璃液的澄清
玻璃液中可见的气体夹杂物消除的过程,称为玻璃液 1.定义: 的澄清过程。 澄清温度大概为1400℃~1500 ℃
2.玻璃液中气体
种类: (1)来源与种类 a.配合料空隙中带入的空气 b.盐类分解放出的气体 c.易挥发物质挥发及水分蒸发和分解 e.燃料燃烧产物 O2、 N2、CO2、 SO2、 SO3、NO2、 NO、H2O、H2等
浮法玻璃生产技术与设备
第三章 玻璃的熔制及熔窑 ------熔制过程
玻璃的熔制过程
配合料的熔化阶段,约需32min
800℃~900 ℃ 不透明 烧结物 1200 ℃完成 1400~1500 ℃ 透明的 玻璃液
硅酸盐形成阶段
玻璃形成阶段
玻璃液澄清 阶段
干 净 的 玻 璃 液
温度降低200~300 ℃ 均匀的 玻璃液
3 玻璃的熔制及熔(1)讲解

(5)玻璃液冷却阶段 将清澄和均化了的玻璃液均匀降温,使玻璃 液具有成型所需的黏度; 在冷却阶段应不破坏玻璃液的质量; 浮法玻璃冷却阶段结束的温度在1100~ 1050℃左右。
3.1.1 配合料的熔化
(1)配合料的加热及初熔 (2)各种反应简介 多晶转变 盐类分解 水分的逸出 (3)成分的挥发 R2O的挥发 由纯碱引入时:引入量×0.032% 由芒硝引入时:引入量×0.06%
3.1.3 澄清
(1)目的 消除玻璃液中的气泡 (2)玻璃液中的气泡形态和种类 形态:可见气泡、溶解气泡、化学结合的气 体。还有熔体表面上的气体。 种类: CO2、SO2、SO3、N2、O2、H2O、H2
(3) 排泡与去气 澄清是排出玻璃液中的可见气泡; 去气是全部排除玻璃液中的气体,包括化学 结合的气体。
B.二次气泡(灰泡,直径小于0.1mm) ①硫酸盐和其他盐类的继续分解; ②溶解气体的析出; ③耐火材料气泡 ④玻璃液流股间的化学反应; ⑤电化学反应
r=1mm时, 2σ/r =0.6kPa; r<0.01mm时, 2σ/r > 0.06MPa; R= 0.001mm时, 2σ/r= 0.6MPa。 可以看出,表面张力对大气泡的影响可以忽 略,对小气泡的影响则是巨大的。 玻璃液中存在的微小气泡,在温度降低时, 内部的压力急剧增大,使气泡内的气体分压 明显大于玻璃液中气体的分压,从而溶解于 玻璃液中;温度升高时,气泡又会析出。
B.新气泡的产生 澄清好的玻璃液一般不能再次产生气泡。 原因是: 新生气泡的半径r≈0,需要克服的
2σ/r≈∞。
(8)影响澄清的因素
A.配合料中的气体率 一般15~20% B.澄清温度 温度高,黏度小,有利于澄清;熔窑温度受 耐火材料的限制。 C.窑压 微正延长澄清时间 B.提高澄清温度 C.搅拌 D.鼓泡 E .加澄清剂(最常用)
玻璃的熔制过程

硅酸盐形成和玻璃形成
6. 含有着色剂和乳浊剂的配合料的加热反应-1
着色剂可能发生氧化还原变化,或者与其它组份生成化合物和 固熔体以及参加硅酸盐生成的反应。
铁的氧化物 Fe2O3+CO → 2FeO + CO2 Fe2O3 ←→ 2FeO + 0.5O2
Fe2O3 + 6HCl → 2FeCl3 +3H2O 锰的氧化物
从三价变为五价,在800℃和1200℃之间,绝大多数As在玻璃中以As2O5存在,
当温使度玻高璃于1液20沸0℃腾时,搅A拌s2O,5又鼓重泡新,分解利为用As玻和A璃s2对O3流放出氧气,物又由理五澄价清变到法
硅酸盐形成和玻璃形成
3. 三组份配合料的硅酸盐和玻璃形成
SiO2+Na2SO4+CaCO3配合料(通常称芒硝配合料)
Na2SO4分解比较困难,所以必须在有碳或其它还原剂存在时,才能加速反应。 SiO2+Na2SO4+CaCO3+C配合料加热发生的反应过程如下:
硅酸盐形成和玻璃形成
4. 四组份配合料的硅酸盐和玻璃形成
4MnO2 → 2Mn2O3 + O2 Mn2O7 → 2Mn2O3 + 2O2 Mn2O3 → 2MnO + 0.5O2
硅酸盐形成和玻璃形成
6. 含有着色剂和乳浊剂的配合料的加热反应-2 铜的氧化物
钴的氧化物 乳浊剂反应
硅酸盐形成和玻璃形成
7. 配合料组份在加热时的挥发
挥发性比较大的有硼酸、硼酸盐、氧化铅、 砷的化合物、氧化锑和氯化物等。碱和氧化 锌也具有显著的挥发率,氟化物和硒的挥发 率非常大。
之后,配合料基本熔化成为液相,过剩的石英颗粒 继续熔化于熔体中,液相不断扩大,直至最后全部 固相转化为玻璃相,成为含有大量气泡、不均匀的 透明玻璃液。
玻璃的熔制过程
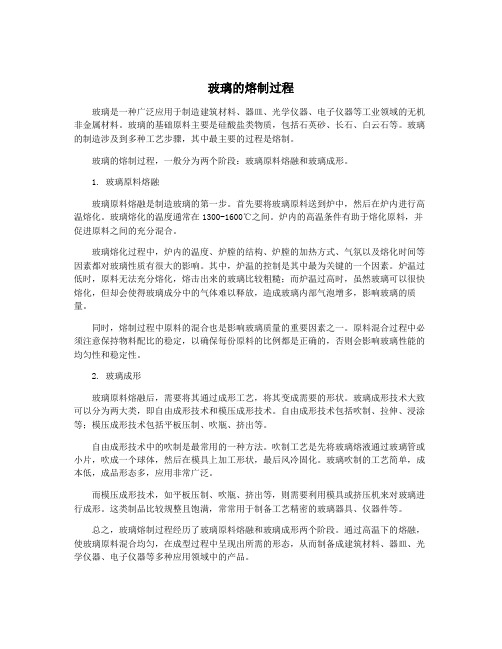
玻璃的熔制过程玻璃是一种广泛应用于制造建筑材料、器皿、光学仪器、电子仪器等工业领域的无机非金属材料。
玻璃的基础原料主要是硅酸盐类物质,包括石英砂、长石、白云石等。
玻璃的制造涉及到多种工艺步骤,其中最主要的过程是熔制。
玻璃的熔制过程,一般分为两个阶段:玻璃原料熔融和玻璃成形。
1. 玻璃原料熔融玻璃原料熔融是制造玻璃的第一步。
首先要将玻璃原料送到炉中,然后在炉内进行高温熔化。
玻璃熔化的温度通常在1300-1600℃之间。
炉内的高温条件有助于熔化原料,并促进原料之间的充分混合。
玻璃熔化过程中,炉内的温度、炉膛的结构、炉膛的加热方式、气氛以及熔化时间等因素都对玻璃性质有很大的影响。
其中,炉温的控制是其中最为关键的一个因素。
炉温过低时,原料无法充分熔化,熔击出来的玻璃比较粗糙;而炉温过高时,虽然玻璃可以很快熔化,但却会使得玻璃成分中的气体难以释放,造成玻璃内部气泡增多,影响玻璃的质量。
同时,熔制过程中原料的混合也是影响玻璃质量的重要因素之一。
原料混合过程中必须注意保持物料配比的稳定,以确保每份原料的比例都是正确的,否则会影响玻璃性能的均匀性和稳定性。
2. 玻璃成形玻璃原料熔融后,需要将其通过成形工艺,将其变成需要的形状。
玻璃成形技术大致可以分为两大类,即自由成形技术和模压成形技术。
自由成形技术包括吹制、拉伸、浸涂等;模压成形技术包括平板压制、吹瓶、挤出等。
自由成形技术中的吹制是最常用的一种方法。
吹制工艺是先将玻璃熔液通过玻璃管或小片,吹成一个球体,然后在模具上加工形状,最后风冷固化。
玻璃吹制的工艺简单,成本低,成品形态多,应用非常广泛。
而模压成形技术,如平板压制、吹瓶、挤出等,则需要利用模具或挤压机来对玻璃进行成形。
这类制品比较规整且饱满,常常用于制备工艺精密的玻璃器具、仪器件等。
总之,玻璃熔制过程经历了玻璃原料熔融和玻璃成形两个阶段。
通过高温下的熔融,使玻璃原料混合均匀,在成型过程中呈现出所需的形态,从而制备成建筑材料、器皿、光学仪器、电子仪器等多种应用领域中的产品。
第八章玻璃的熔制与窑炉.
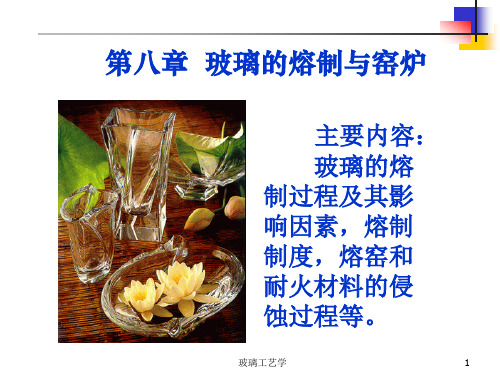
11
铅硅酸盐玻璃
1 Na 2O K 2O PbO 8 其中:氧化物—各氧化物在玻璃中的重量百分数; —表示玻璃相对难熔的特征值; 与值相应的熔化温度
SiO 2
值
6
1450~1460
5.5
1420
4.8
1380~1400
4.2
1320~1340
熔化温度℃
注意:常数是一经验值,确定熔制温度时,此常数不能认 为是唯一的决定因素,它未考虑如粒度、温度等因素。
玻璃工艺学
12
2、石英颗粒的大小 鲍特维金公式:
K 1r
3
—玻璃形成的时间(分钟); r-石英颗粒的原始半径(厘米); K1-与玻璃组成和温度有关的常数; 3、熔制温度 bt 索林诺夫经验公式: a e —玻璃形成时间(小时); a、b—常数(与玻璃组成、原料粒度有关)。对窗玻璃, a=101256, b=0.00815; e—自然常数 t—熔融体温度(℃)
三、玻璃的形成阶段
(一)玻璃形成阶段的反应: 溶解:石英砂粒表面的SiO2进入液相; 扩散:溶解的SiO2向周围熔体扩散,速度最慢;
(二)玻璃形成动力学 玻璃熔制过程中玻璃形成速度与玻璃组成、砂粒大小、熔制 温度等有关。 1、玻璃组成: 沃尔夫(M.Volf)提出如下玻璃熔化速度常数的方程式。
SiO 2 Al 2O 3 一般工业玻璃 Na2O K 2O SiO 2 Al 2O 3 硼硅酸盐玻璃 1 Na 2O K 2O B 2O 3 2
玻璃工艺学
13
四、玻璃的澄清阶段
玻璃液的澄清过程是玻璃熔化过程中极其重要的一环,它与
玻璃工艺学 6
2.多组分反应:除了包括单组分和双组分的加热反应特点外, 还包括含自身反应特点,如复盐的反应;形成低共熔物,使得熔制 温度低,所以组成越多,熔制温度越低;硅酸盐的生成等。 如:生成CO2的来源有碳酸盐的单组分分解、碳酸盐生成硅酸 盐的反应、复盐的分解等。 因此配合料的加热反应基本上是单组分和多组分加热反应的综 合。
玻璃熔制及熔窑---熔窑1
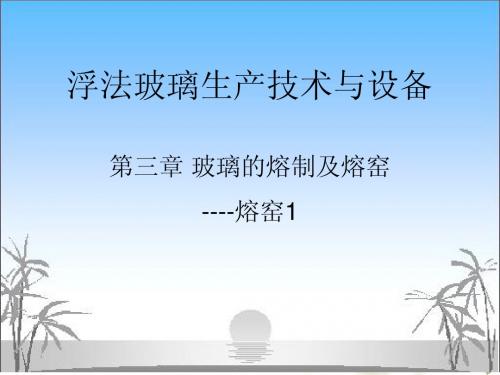
玻璃的池窑
(浮法玻璃熔窑各部分结构尺寸)
大碹:平碹:散热面积小。 拱碹:合适的股跨比,燃油的一般在1/7~1 /8。 股高越小,散热越小,但横推力越大。保证足够强度的前 提下适当减小股高。 材质:楔形的优质硅砖或电熔刚刚玉砖。砖长不得小于砖 厚的一半,砌筑时横向砖缝错开,纵横向砖缝不得大于 1mm,不得用黏土质泥浆砌筑。 厚度:以大碹跨度的1/20~1/25来考虑。 大碹的节数:一般分为3节,每节之间留80~100mm膨胀缝, 两端留要大于120mm的膨胀缝 。
玻璃的池窑
(浮法玻璃熔窑各部分结构尺寸)
投料易控,但易 飞料堵塞格子体。
振动式投料机
玻璃的池窑
(浮法玻璃熔窑各部分结构尺寸)
螺旋式投料机
玻璃的池窑
(浮法玻璃熔窑各部分结构尺寸)
a.投料机:
弧毯式投料机
螺旋式投料机
斜毯式投料机(后端漏料 )
玻璃的池窑
(浮法玻璃熔窑各部分结构尺寸)
弧毯式尺寸: 2.7/2.8/3.0/3.4/ 4.0/4.5/10.3米 斜毯式尺寸: 0.85/1米
弧毯式投料机
玻璃的池窑
(浮法玻璃熔窑各部分结构尺寸)
特点:投料池的宽度一般为熔化池宽度的80%以上。所玻璃 与配合料混合在一起加料,可以连续薄层加料,布料均匀, 覆盖面积大。 为目前使用最普遍的加料机。 b.投料口与投料池 投料口:由投料池与上部挡墙(前脸墙)组成 。 投料池:突出于窑池外面与池窑相通的矩形小池。 要求:配合料能按时按量加入,并且保持薄层和覆盖面尽可能 大,投料池内的玻璃液不冻结,窑内外没有飞料 。 投料口工作环境:温度高,散热慢,受到配合料的化学侵蚀与 机械磨损,尤其在拐角处更易损伤,所以经常选用优质耐火材 料电熔锆刚玉砖。。
玻璃熔制及熔窑---熔制的工艺制度解析
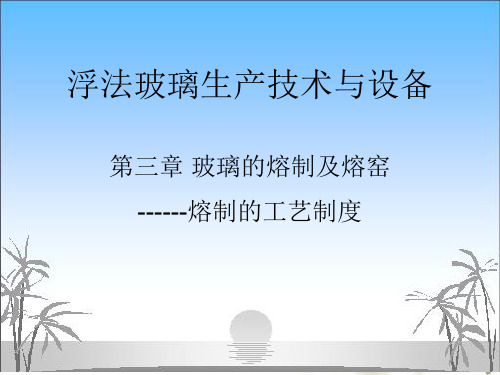
熔制的工艺制度
3.温度曲线 热点:不是一个点,而是玻璃液表面的最高温度带 (1)“山”型曲线
小炉序号 1 2 3 4 5 6
温度分布℃ 1430 1480 1530 1550 1520 1440
燃料分配% 16 18 20 21 16 8~9
特点:热点突出,热点与1#小炉及末对小炉间的温差大,玻璃 液对流剧烈,泡界线清晰稳定,容易达到稳定作业;配合料熔 化滞后,难以充分利用窑的潜力。
❖ d.温度 ❖ 当熔化部温度高时,玻璃液粘度减小,回流速度加快,
参与回流的玻璃液量增多,配合料迅速熔化,泡界线趋 近于投料口;
❖ 熔化部温度降低时,玻璃液粘度变大,回流慢,液量少, 未熔配合料增多,泡界线挪后变远;当窑内横向温差变 大时,横向液流明显加剧,泡界线紊乱、模糊,直至偏 斜,发生“跑料”现象。
熔制的工艺制度
窑内对火焰的要求 温度: 亮度:与火焰的碳黑量有关(燃料的性质、空气过剩系数) 长度:距离对面胸墙0.5m左右 宽度:覆盖面积 角度:平直稍向下斜 刚度:清亮有力,不分层,不发飘,与火焰喷出速度有关
玻璃池窑的工作原理
(玻璃液的流动和窑内应热交换)
玻璃液.增加了热量的损失; 4.加速了对窑体的侵蚀。 二、玻璃池窑内的热交换
玻璃池窑的工作原理
(玻璃液的流动和窑内应热交换)
A.火焰空间内的热交换(火焰、窑墙和碹顶、被加热的配合 料和玻璃液)
熔制的工艺制度
“桥形”曲线: 热点前后两对小炉的温度与最高温度相差不大,温度曲线似 拱桥形。 特点:熔化高温带较长,有利于配合料的熔化和玻璃液的澄 清。热点不明显,我浓度梯度小,向投料口的回流弱,易产 生“跑料”现象,但易于控制。
小炉序号
1
2
玻璃熔制过程的五个阶段
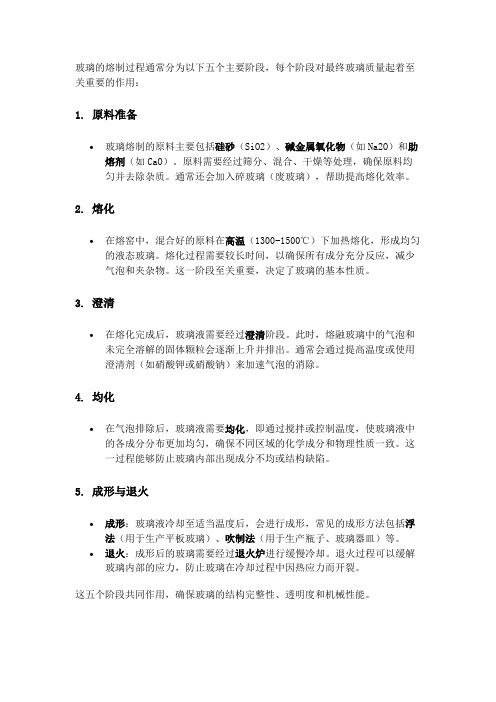
玻璃的熔制过程通常分为以下五个主要阶段,每个阶段对最终玻璃质量起着至关重要的作用:
1. 原料准备
•玻璃熔制的原料主要包括硅砂(SiO2)、碱金属氧化物(如Na2O)和助熔剂(如CaO)。
原料需要经过筛分、混合、干燥等处理,确保原料均
匀并去除杂质。
通常还会加入碎玻璃(废玻璃),帮助提高熔化效率。
2. 熔化
•在熔窑中,混合好的原料在高温(1300-1500℃)下加热熔化,形成均匀的液态玻璃。
熔化过程需要较长时间,以确保所有成分充分反应,减少
气泡和夹杂物。
这一阶段至关重要,决定了玻璃的基本性质。
3. 澄清
•在熔化完成后,玻璃液需要经过澄清阶段。
此时,熔融玻璃中的气泡和未完全溶解的固体颗粒会逐渐上升并排出。
通常会通过提高温度或使用
澄清剂(如硝酸钾或硝酸钠)来加速气泡的消除。
4. 均化
•在气泡排除后,玻璃液需要均化,即通过搅拌或控制温度,使玻璃液中的各成分分布更加均匀,确保不同区域的化学成分和物理性质一致。
这
一过程能够防止玻璃内部出现成分不均或结构缺陷。
5. 成形与退火
•成形:玻璃液冷却至适当温度后,会进行成形,常见的成形方法包括浮法(用于生产平板玻璃)、吹制法(用于生产瓶子、玻璃器皿)等。
•退火:成形后的玻璃需要经过退火炉进行缓慢冷却。
退火过程可以缓解玻璃内部的应力,防止玻璃在冷却过程中因热应力而开裂。
这五个阶段共同作用,确保玻璃的结构完整性、透明度和机械性能。
玻璃熔制及熔窑---熔制的工艺制度

(4)影响到玻璃的成型作业
熔制的工艺制度
3.温度曲线 热点:不是一个点,而是玻璃液表面的最高温度带 (1)“山”型曲线 小炉序号 1 2 3 4 5 6
温度分布℃ 1430 1480 1530 1550 1520 1440
燃料分配% 16 18 20 21 16 8~9
特点:热点突出,热点与1#小炉及末对小炉间的温差大,玻璃 液对流剧烈,泡界线清晰稳定,容易达到稳定作业;配合料熔 化滞后,难以充分利用窑的潜力。
熔制的工艺制度
“桥形”曲线: 热点前后两对小炉的温度与最高温度相差不大,温度曲线似 拱桥形。 特点:熔化高温带较长,有利于配合料的熔化和玻璃液的澄 清。热点不明显,我浓度梯度小,向投料口的回流弱,易产 生“跑料”现象,但易于控制。 小炉序号 温度分布℃ 燃料分配% 1 1490 15 2 1510 20.3 3 1540 20.7 4 5 6 1500 3.3
熔制的工艺制度
料层跑偏—因各加料机投料不一,致使沿窑宽的料层厚 度不均,数量上产生差异,料层集于一侧,极易导致泡 界线的偏斜。
d.温度
当熔化部温度高时,玻璃液粘度减小,回流速度加快, 参与回流的玻璃液量增多,配合料迅速熔化,泡界线趋 近于投料口; 熔化部温度降低时,玻璃液粘度变大,回流慢,液量少, 未熔配合料增多,泡界线挪后变远;当窑内横向温差变 大时,横向液流明显加剧,泡界线紊乱、模糊,直至偏 斜,发生“跑料”现象。
1570 1550 21.7 19
熔制的工艺制度
“双高”曲线:即“双高热负荷点”温度制度,核心是减少 处在泡沫稠密区的小炉燃料分配量,降低了此处的热负荷; 配合料入窑预助熔。 目前,国内浮法熔窑均采用此法。 小炉序号 1 2 3 4 5 6
玻璃熔制及熔窑---玻璃熔制过程

玻璃液的澄清
(4)几种气体在玻璃液中的性质
CO2:物理溶解度随着T升高,过饱和程度的增加而降低;玻璃液 的吸收能力随碱性氧化物浓度增加而增加。化学溶解为主 SO2:低于1200℃时玻璃液的吸收能力随着T升高而增大,超1200℃ 时,溶解量迅速减少。化学溶解为主 O2与N2:一般情况下以物理溶解为主,溶解度很小
硅酸盐的形成
影响配合料熔化的因素:
(1)熔制温度:温度越高,反应速度提高。温度每提高10 ℃, 反应速度约增加10%。 (2)原料的形式:复合原料可以降低熔制温度,同时有利于 玻璃液的澄清均化。
玻璃的形成
玻璃的形成过程:配合料中难熔的石英颗粒在各种硅酸盐 和液相的作用下,逐渐溶解、扩散而消失,形成透明的玻 璃液。约需要28~29min。 a. 石英颗粒固体表面的溶解:速度快 石英颗粒 的消失 b. 溶解后的SiO2自表面向熔体扩散:速度慢 玻璃的形成速度 主要取决于石英 颗粒的扩散速度
CO2 SO2
CO2 SO2
CO2 SO2
SO2 CO2 SO2 O2 澄清剂分 解的气体
PCO2熔体=PCO2气泡 PSO2熔体=PSO2气泡 P熔体=P气泡
平衡
玻璃液的澄清
气泡在玻璃液中上浮的过程: 气泡上浮的条件: 气泡在玻璃液中受到压力与浮力,只有气 泡的浮力大于压力时,气泡才能上浮排出。 气泡所受到的压力:窑气的压力(约0.1MPa); 气泡所受玻璃液的压力(池深1.5m计算,压力为0.0368MPa) 2σ/r(σ——表面张力, r——气泡的半径)
r=1mm时, 2σ/r =0.6kPa; r= 0.001mm时, 2σ/r= 0.6MPa。
结论:表面张力对大气泡的影响可以忽略,对小气泡的影响巨大
第八章玻璃的熔制与窑炉

11
铅硅酸盐玻璃
1 Na 2O K 2O PbO 8 其中:氧化物—各氧化物在玻璃中的重量百分数; —表示玻璃相对难熔的特征值; 与值相应的熔化温度
SiO 2Fra bibliotek值
6
1450~1460
5.5
1420
4.8
1380~1400
4.2
1320~1340
熔化温度℃
注意:常数是一经验值,确定熔制温度时,此常数不能认 为是唯一的决定因素,它未考虑如粒度、温度等因素。
玻璃工艺学 6
2.多组分反应:除了包括单组分和双组分的加热反应特点外, 还包括含自身反应特点,如复盐的反应;形成低共熔物,使得熔制 温度低,所以组成越多,熔制温度越低;硅酸盐的生成等。 如:生成CO2的来源有碳酸盐的单组分分解、碳酸盐生成硅酸 盐的反应、复盐的分解等。 因此配合料的加热反应基本上是单组分和多组分加热反应的综 合。
1000℃
900℃
SiO2+Na2O+CaO反应速度与温度
玻璃工艺学 8
分解% 100
75 50 25 0
4
3
2
1
10 20
30 40
50
60
70 80 分钟
CaCO3与SiO2在不同比例时的反应速度 1—CaCO3;2—CaCO3+SiO2;3—CaCO3+2SiO2; 4—CaCO3+3SiO2;
此外,还有部分气体吸附在玻璃表面上(量很少)。 玻璃的澄清过程一般是指排除可见气泡,完全排除包括化 学结合气体在内的玻璃中的气体(去气)只有采用特殊方法熔 制才可实现。 (三)气泡的生成和长大 气泡的形成即是玻璃中新相的形成,分两个阶段: 泡核的形成和气泡的长大 1.小于临界泡核的,不能长大,将溶解于玻璃内;大于临 界泡核的,长大。
玻 璃 的 熔 制 及 熔 窑培训课件2016.3

二、玻璃的熔制设备:
工业上用于玻璃熔制的设备有坩锅窑和池窑。前者产量 低、耗能 大,主要用于手工生产小批量的玻璃制品;后者用 于玻璃产品的
工业化大规模的连续生产。
池窑的分类 : 1. 按使用热源分: (1)火焰窑: 以燃料燃烧为热能来源。燃料可 以是煤气, 重油和水; (2)电热窑: 以电能作为热量来源; (3)火焰-电热窑: 以燃料为主要热源,电能 为辅助热源。
直接接触部位的部位。 AZS砖标号越高,ZrO2含量越高,
斜锆 石相越多,抗侵蚀性能越好。此外,AZS砖中玻璃 相受蚀后常 生成含ZrO2的高粘度长石质玻璃,这层高粘 度的玻璃液滞留在 砖表面,保护了砖体的进一步蚀变。
AZS砖的蚀变主要是:
玻璃相结合物被溶解;
刚玉与碱性氧化物发生变代反应,生成β-Al2O3和霞石。
(3)存在形式 :残留在玻璃液中的气体存在三种形式: 可见气泡 ; 物理溶解 ; 化学结合 。
其中可见气泡中的气体和以物理状态溶解的气体 与窑炉中 气体之间存在一定的平衡。
气体在熔窑中的平衡状态: 窑炉
②
⑤
①
③
气泡
玻璃液 ④
①②从过饱和的玻璃液中析出气体,进入气泡或炉气;
③④气泡中分离出来的气体,进入炉气 或溶解在玻璃中;
Hale Waihona Puke 玻璃熔窑主要部位所选用的耐火材料的确定表
使用部位 窑 拱(大碹) 拱脚砖 胸 墙 使用条件 高温碱蒸汽 粉料的飞散 和拱顶熔融后的流下 物 温度(℃) 1500~1600 1500~1600 1500~1600 1450~1600 1500~1600 1400~1600 1400~1600 选用的耐火材料 优 质 硅 砖BG96A 优质硅砖、低蠕变锆 英石砖 F-AZS、优质硅砖、低 蠕变锆英石砖、RA-H (流液洞砖) F-AZS、优 质 硅 砖 F-AZS F-AZS(QX和WS) F-AZS(WS、 ZrO2 41%级)、FAZSC F-AZS(WS、 ZrO2 41%级) F-AZS(WS、 ZrO2 41%级)、FAZSC F-AZS(WS) F-AZS(WS) 电熔铸AZS质捣打料+ 锆英石砖或B-AZS
- 1、下载文档前请自行甄别文档内容的完整性,平台不提供额外的编辑、内容补充、找答案等附加服务。
- 2、"仅部分预览"的文档,不可在线预览部分如存在完整性等问题,可反馈申请退款(可完整预览的文档不适用该条件!)。
- 3、如文档侵犯您的权益,请联系客服反馈,我们会尽快为您处理(人工客服工作时间:9:00-18:30)。
玻璃的形成
2.石英颗粒的尺寸: τ---形成玻璃的时间
k1r03
石英颗粒越小,反应时间越短。注:过小,结团而成为大颗 粒,反而不宜熔化。 3.熔体温度: τ---形成玻璃的时间
aebt
b、t与玻璃成分、原料颗粒度等相关的常数
玻璃的形成
4.配合料及投料质量 a.原料的颗粒级配 难熔的小一些、易熔的大一些;密度小的 粗一些,密度大的细一些。 b.配合料质量 均匀性与水分含量 c.投料方式 薄层投料、均匀投料 d、碎玻璃
玻璃形成的动力学: 1.玻璃成分:τ---熔化速度常数,表示玻璃相对难熔的特征。
τ是一经验常数, 要综合各种因
一般工业玻璃:
SiO2
Al 2 O3
素后确定熔化 温度。
Na2O K 2O
硼酸盐玻璃:
SiO2 Al2O3
Na2O
K2O
1 2
B2O3
铅酸盐玻璃:
SiO2 Al2O3
Na2O K 2O 0.125 PbO
O2与N2:一般情况下以物理溶解为主,溶解度很小
玻璃液的澄清
(4)几种气体在玻璃液中的性质
CO2:物理溶解度随着T升高,过饱和程度的增加而降低;玻璃液 的吸收能力随碱性氧化物浓度增加而增加。化学溶解为主 SO2:低于1200℃时玻璃液的吸收能力随着T升高而增大,超1200℃ 时,溶解量迅速减少。化学溶解为主
500℃左右开始分解;白云石700 ℃左右MgCO3(先)分解 完全,CaCO3(后)分解很少;硝酸钠350 ℃左右开始分解。
c.脱水:结晶水、结构水、化学结合水
d.熔融:固态转变为液态
硅酸盐的形成阶段
3.各组分之间(多组分)的加热反应
a.固相反应:
注:多组分配合料中碳酸盐分解和
b. 形成复盐
硅酸盐形成开始的温度低,反应速
(2)原料的形式:复合原料可以降低熔制温度,同时有利于 玻璃液的澄清均化。
玻璃的形成
玻璃的形成过程:配合料中难熔的石英颗粒在各种硅酸盐 和液相的作用下,逐渐溶解、扩散而消失,形成透明的玻 璃液。约需要28~29min。
石英颗粒 的消失
a. 石英颗粒固体表面的溶解:速度快 b. 溶解后的SiO2自表面向熔体扩散:速度慢
50 90
注:SiO2和Al2O3的挥发率通常很小,但当配合料中含有氟化物时, 需要考虑SiO2的挥发量,一般每份CaF2,SiO2的挥发量为0.33份, 每份Na2SiF6, SiO2的挥发量为0.6或0.4份 。
硅酸盐的形成
影响原料挥发量的因素:
(1)熔制温度:温度越高,挥发量越大。熔制温度由1450℃变化
到1550℃,挥发率将增加一倍。
(2)同一种氧化物,原料不同,挥发量不同。无水硼砂比硼酸和
十水硼砂低。
(3)氧化物在原料中的含量越高,挥发量越高。
(4)配合料中的水分越高,Se的挥发率越高。 (5)同一种氧化物在不同的玻璃中挥发率不同。
硅酸盐的形成
影响配合料熔化的因素:
(1)熔制温度:温度越高,反应速度提高。温度每提高10 ℃, 反应速度约增加10%。
形成低共熔物
少量液相出现
硅酸盐的形成阶段
4.配合料组分在加热过程中的挥发损失
意义:在配料设计过程充分考虑到挥发损失量,保证 配料计算的准确度。 玻璃中容易挥发的组分及挥发率:
组分
Na2O(纯 Na2O(芒 K2O ZnO PbO B2O3 F Se 碱引入) 硝引入)
挥发率 3.2 (%)
6.0
12 4.0 14 15
d.耐火材料气孔中气体的排出及被侵蚀过程释放的气体
e.燃料燃烧产物
玻璃液的澄清
(2)气体的存在形式 a. 可见气泡
物理溶解
b.溶解气体
化学溶解
(3)几种气体在玻璃液中的性质
CO2:物理溶解度随着T升高,过饱和程度的增加而降低;玻璃液 的吸收能力随碱性氧化物浓度增加而增加。化学溶解为主
SO2:低于1200℃时玻璃液的吸收能力随着T升高而增大,超1200℃ 时,溶解量迅速减少。化学溶解为主
玻璃的形成速度 主要取决于石英 颗粒的扩散速度
玻璃的形成
影响石英砂颗粒在熔体中溶解速度的主要因素: (1)溶解的SiO2从表向熔体的扩散系数; (2)砂粒表面的SiO2与熔体中SiO2的浓度梯度; (3)交界层的厚度; (4)接触面积。 而扩散系数与熔体的粘度有关,越大,扩散系数越小。
玻璃的形成
玻璃液澄清 阶段
干 净 的 玻 璃 液
适合成型的玻璃液
说明:五个阶段相互联系相互影响,并不是严格 按照顺序进行,常常是同时进行或交替进行。
硅酸盐的形成阶段
1.定义:
配合料在高温的作用下,各个组分本身、各个组分
之间经历一系列的物理反应、化学反应和物理化学反应,
最后变成硅酸盐和SiO2不透明烧结物的过程。约需 3~4min。
玻璃液的澄清
1.定义:玻璃液中可见的气体夹杂物消除的过程,称为玻璃液
的澄清过程。 澄清温度大概为1400℃~1500 ℃
2.玻璃液中气体
(1)来源与种类 a.配合料空隙中带入的空气 b.盐类分解放出的气体 c.易挥发物质挥发及水分蒸发和分解
种类:
O2、 N2、CO2、 SO2、 SO3、NO2、 NO、H2O、H2等
c.形成硅酸盐
度快。在实际生产中(投料口温度
d.生成低共熔物
达1300℃)各种反应同时进行。完 成时间极短(大概只有3~4min)。
固相之间的反应 (大量气体逸出,
其他组分与 SiO2作用
CaCO3与MgCO3的分解)
形成复盐
形成硅酸盐
固液之间的反应开始,
液相增加(由硅酸盐与游离
SiO2组成的不透明烧结物)
浮法玻璃生产技术与设备
第三章 玻璃的熔制及熔窑 ------熔制过程
玻璃的熔制过程
配合料的熔化阶段,约需32min
800℃~900 ℃
硅酸盐形成阶段
不透明 烧结物
1200 ℃完成
玻璃形成阶段
透明的 玻璃液
温度降低200~300 ℃
玻璃液冷却阶段
均匀的 玻璃液
1300~1400 ℃
玻璃液均化阶段
1400~1500 ℃
2.配合料中各单组分的加热变化
a.多晶转变:如SiO2 、芒硝等
β—石英→α石英 α石英→α鳞石英
575℃ 875℃
无水芒硝(斜方晶 系)→偏位芒硝 (单斜晶系)
α鳞石英→α方石英 1470℃
熔融
235℃左右 884℃
熔化
1710℃
分解
ቤተ መጻሕፍቲ ባይዱ
大于1200℃
硅酸盐的形成阶段
b.盐类分解:如碳酸盐、硫酸盐、硝酸盐 例如:纯碱—700℃左右开始分解放出CO2;石灰石