增材制造术语
增材制造简介介绍

2000年代至今
03
增材制造技术得到了快速发展,被广泛应用于各个行
业和领域。
增材制造技术的重要性和优势
高度定制化
增材制造技术可以根据客户 需求进行定制化生产,满足
个性化的需求。
1
减少生产成本
增材制造技术可以减少材料 浪费和生产成本,提高生产
效率。
创新设计
增材制造技术可以应用于创 新设计,使产品更加独特和 新颖。
材料利用率高:能够减少材料浪费,降低成本。
特点 高效率:实现快速制造,节约生产时间。 高度定制化:能够根据客户需求进行定制化生产。
增材制造的技术类型
激光熔化技术(Laser Melting ):利用高能量激光束熔化金 属粉末,逐层堆积形成物体。
粉末烧结技术(Powder Sintering):利用激光或其他 能源将粉末颗粒烧结在一起,
环保可持续性
增材制造技术可以减少生产 过程中的废弃物和污染,更 加环保和可持续。
增材制造技术的挑战和限制
技术成熟度
增材制造技术的成熟度还需要进一步提高, 以满足更广泛的应用需求。
材料限制
增材制造技术的材料选择还需要进一步拓展 ,以满足不同领域的需求。
生产效率
增材制造技术的生产效率还需要提高,以满 足大规模生产的需求。
逐层堆积形成物体。
光固化技术( Photopolymerization):利 用光敏树脂作为材料,通过激 光束照射凝固,逐层堆积形成 物体。
熔融沉积技术(Fused Deposition Modeling):利 用热熔性材料作为材料,通过 喷嘴将材料逐层沉积形成物体 。
增材制造的应用领域
医疗
制造人体植入物、 医疗器械等。
增材制造技术
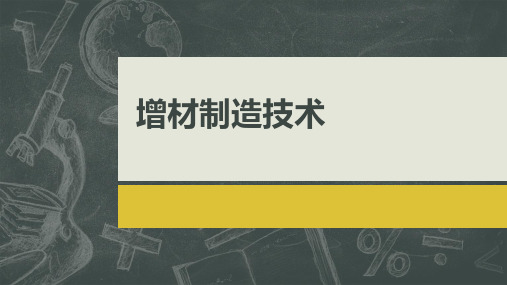
2.产品多样化不增加成本。(一台打印机,不需要改动模具) 3.生产周期短。(最大的优点) 4.零技能制造。(相对于传统制造所需要的操作技能很少) 5.不占空间,便携制造。(可应用于灾区,战场) 6.节省材料。(没有废料、回料等) 7.精确的实体复制。(3D照相馆) 缺点:1.材料限制:目前可用材料有限,无法支持各种各样的材料。 2.机器限制:对机器要求高,无法打印动态物体。 3.花费负担:成本昂贵,暂时难以进入大众家庭。
增材制造技术
主要内容
▪ 1.增材制造概述 ▪ 2.增材制造的原理与方法 ▪ 3.3D打印发展与现状
什么是增材制造技术?
▪ 增材制造技术是指基于离散-堆积原理,由零件三维数据驱动直 接制造零件的科学技术体系。基于不同的分类原则和理解方式,增材 制造技术还有快速原型、快速成形、快速制造、3D打印等多种称谓, 其内涵仍在不断深化,外延也不断扩展,这里所说的“增材制造”与 “快速成形”、“快速制造”意义相同。
常见的3D打印技术
2. SLA(光固化技术 ) :立体光固化成型 工艺(Stereolithography Apparatus, SLA),又称立体光刻成型。
原理:液槽中会先盛满液态的光敏树 脂,氦—镉激光器或氩离子激光器发射 出的紫外激光束在计算机的操纵下按工 件的分层截面数据在液态的光敏树脂表 面进行逐行逐点扫描,这使扫描区域的 树脂薄层产生聚合反应而固化从形成工 件的一个薄层。
增材制造的关键技术
一是材料单元的控制技术。 即如何控制材料单元在堆 积过程中的物理与化学变 化是一个难点,例如金属 直接成型中,激光熔化的 微小熔池的尺寸和外界气 氛控制直接影响制造精度
和制件性能。
二是设备的再涂层技 术。增材制造的自动化涂 层是材料累加的必要工序, 再涂层的工艺方法直接决 定了零件在累加方向的精 度和质量。分层厚度向 0.01mm发展,控制更小 的层厚及其稳定性是提高 制件精度和降低表面粗糙
增材制造在金属冶炼中的应用

加强基础研究
进一步深入研究增材制造技 术在金属冶炼中的应用原理 和工艺参数,提高技术的稳 定性和可靠性。
拓展应用领域
将增材制造技术应用于更多 种类的金属冶炼中,拓展其 应用领域,提高技术的应用 价值。
优化设备与材料
研发更加高效、智能的增材 制造设备,优化金属材料的 成分与组织结构,提高产品 的质量和性能。
加强跨领域合作
加强与材料科学、物理学、 化学等领域的合作,共同推 进增材制造技术在金属冶炼 中的应用和发展。
增材制造技术打破了传统加工方法的限制 ,为设计师提供了更大的创意空间,促进 了产品设计的创新。
增材制造在金属冶炼中的具体应用案例
钛合金零件的制造
利用增材制造技术,可以快速、精确地制造出钛合金零件,广泛 应用于航空航天、医疗等领域。
不锈钢零件的制造
增材制造技术能够生产出具有复杂内部结构的不锈钢零件,提高了 产品的性能和可靠性。
研究新型的熔化和凝固技术,优化相关工艺参数,提高制造效率,同时确保构件的冶金质 量和力学性能。
技术挑战的未来发展趋势和展望
跨学科合作推动技术创新
加强材料科学、机械工程、冶金学等领域的跨学科合作,共同推动增材制造在金属冶炼 中的技术创新和应用。
智能化和自动化制造
借助人工智能、机器学习等先进技术,实现增材制造过程的智能化和自动化,提高制造 精度和效率,进一步拓展增材制造在金属冶炼领域的应用。
拓展应用领域
增材制造技术在金属冶炼领域的应用将不仅局限于零件制造,还 将拓展到新材料研发、工艺优化等方面。
04
增材制造在金属冶炼中的技术 挑战和解决方案
增材制造在金属冶炼中的技术挑战
01
高温环境下材料的稳定性和可加工性
【技术干货】一文详解复合材料领域的专业术语(中英对照版):上篇
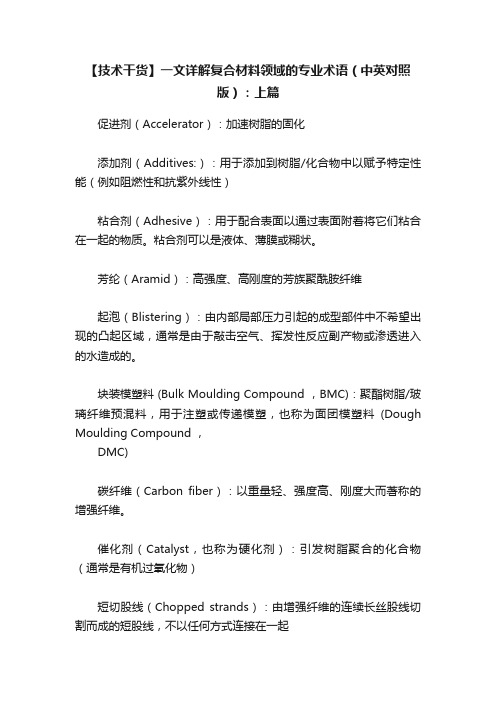
【技术干货】一文详解复合材料领域的专业术语(中英对照版):上篇促进剂(Accelerator):加速树脂的固化添加剂(Additives:):用于添加到树脂/化合物中以赋予特定性能(例如阻燃性和抗紫外线性)粘合剂(Adhesive):用于配合表面以通过表面附着将它们粘合在一起的物质。
粘合剂可以是液体、薄膜或糊状。
芳纶(Aramid):高强度、高刚度的芳族聚酰胺纤维起泡(Blistering):由内部局部压力引起的成型部件中不希望出现的凸起区域,通常是由于敲击空气、挥发性反应副产物或渗透进入的水造成的。
块装模塑料 (Bulk Moulding Compound ,BMC):聚酯树脂/玻璃纤维预混料,用于注塑或传递模塑,也称为面团模塑料(Dough Moulding Compound ,DMC)碳纤维(Carbon fiber):以重量轻、强度高、刚度大而著称的增强纤维。
催化剂(Catalyst,也称为硬化剂):引发树脂聚合的化合物(通常是有机过氧化物)短切股线(Chopped strands):由增强纤维的连续长丝股线切割而成的短股线,不以任何方式连接在一起无尘室(Cleanroom):无尘室是一个受控环境,它使用过滤去除空气中的污染物,创造一个一致且可重复的制造环境。
复合材料(Composite):由树脂和增强材料(通常是纤维)组成的材料抗压强度(Compression strength):材料破坏时的压碎载荷除以试样的横截面积芯(Core):在夹层结构中,连接内层和外层的中心组件。
泡沫、蜂窝和木材都是常用的芯材。
耐腐蚀性(Corrosion resistance):材料承受与周围自然因素接触而不降解或改变性能的能力。
对于复合材料,腐蚀会导致开裂。
偶联剂(Coupling agent):在树脂基体/增强材料界面促进或建立更牢固结合的化学物质开裂(Cracking):成型材料的分离,在零件的相对表面上可见并延伸到整个厚度(断裂)固化(Cure):热固性树脂在热作用下通过分子结构的交联硬化的过程固化剂(Curing agents):用于热固性树脂固化的化合物固化时间(Curing time):树脂完全固化所需的时间分层(Delamination):沿层压材料的层平面分裂、物理分离或失去粘合直接粗纱(Direct roving):通过直接从套管上缠绕一定数量的细丝制成的粗纱面团模塑料 (Dough moulding compound,DMC):聚酯/树脂纤维预混料,用于注塑或传递模塑,也称为块状模塑料(Bulk Moulding Compound,BMC)纤维(Fiber):一种长度连续的细丝状物质,其特点是长度与厚度或直径的比值很高长丝(Filament):连续的、细直径、长度很长的纤维填料(Filler):添加到树脂中以扩展树脂或赋予特殊性能的材料(通常成本较低)整理(Finishing):将偶联剂应用于纺织品增强材料以改善纤维/树脂的粘合弯曲强度(Flexural strength):材料弯曲时的强度,表示为弯曲试验样品在失效瞬间的应力。
增材制造术语

增材制造术语1. 增材制造(Additive Manufacturing):是一种通过逐层堆叠材料来制造三维实体产品的制造技术。
2. 三维打印(3D Printing):是增材制造的一种常见方法,利用计算机控制的逐层堆叠方式将材料逐渐构建成三维物体。
3. 材料堆积(Material Deposition):是增材制造过程中将材料层层堆积以构建产品的步骤。
4. 光固化(Photopolymerization):是一种增材制造技术,利用紫外线或其他光源对光敏材料进行硬化,将其逐层堆积以构建三维物体。
5. 粉末床融合(Powder Bed Fusion):是一种增材制造技术,通过将粉末材料逐层堆积并利用激光或电子束进行局部熔化,最终形成三维物体。
6. 可溶性支撑结构(Soluble Support Structures):是增材制造过程中使用的一种支撑结构,它可以在制造完成后通过特定的溶解剂溶解掉,以减少对产品表面的影响。
7. 层厚(Layer Thickness):是增材制造过程中每一层材料的厚度,决定了最终产品的精度和表面光滑度。
8. 制造方向(Build Orientation):是指在增材制造过程中,选择材料堆积的方向,以最大程度地减少支撑结构的使用和优化产品的物理性能。
9. 预处理(Preprocessing):是增材制造过程中的前期准备工作,包括模型切片、支撑结构的生成等。
10. 后处理(Postprocessing):是增材制造过程中的后期处理工作,包括去除支撑结构、表面光滑、热处理等。
11. 增材制造设备(Additive Manufacturing Equipment):是用于实施增材制造的设备,例如三维打印机、激光烧结机等。
12. 直接制造(Direct Manufacturing):是一种增材制造技术,可以直接从数字模型等电子数据中制造出产品,无需制造模具或工艺准备。
13. 拓扑优化(Topology Optimization):是一种设计方法,通过优化材料分布和结构形状,以最大程度地提高产品性能,同时减少材料使用。
“增才制造”:以增材原理推动个性化陶瓷材料“成型—成性一体化”设计
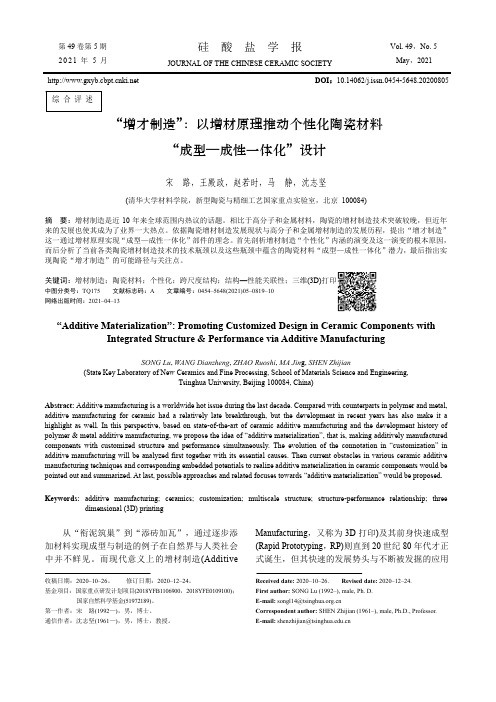
第49卷第5期2021年5月硅酸盐学报Vol. 49,No. 5May,2021 JOURNAL OF THE CHINESE CERAMIC SOCIETY DOI:10.14062/j.issn.0454-5648.20200805“增才制造”:以增材原理推动个性化陶瓷材料“成型—成性一体化”设计宋路,王殿政,赵若时,马静,沈志坚(清华大学材料学院,新型陶瓷与精细工艺国家重点实验室,北京 100084)摘要:增材制造是近10年来全球范围内热议的话题。
相比于高分子和金属材料,陶瓷的增材制造技术突破较晚,但近年来的发展也使其成为了业界一大热点。
依据陶瓷增材制造发展现状与高分子和金属增材制造的发展历程,提出“增才制造”这一通过增材原理实现“成型—成性一体化”部件的理念。
首先剖析增材制造“个性化”内涵的演变及这一演变的根本原因,而后分析了当前各类陶瓷增材制造技术的技术瓶颈以及这些瓶颈中蕴含的陶瓷材料“成型—成性一体化”潜力,最后指出实现陶瓷“增才制造”的可能路径与关注点。
关键词:增材制造;陶瓷材料;个性化;跨尺度结构;结构—性能关联性;三维(3D)打印中图分类号:TQ175 文献标志码:A 文章编号:0454–5648(2021)05–0819–10网络出版时间:2021–04–13“Additive Materialization”: Promoting Customized Design in Ceramic Components with Integrated Structure & Performance via Additive ManufacturingSONG Lu, WANG Dianzheng, ZHAO Ruoshi, MA Jin g, SHEN Zhijian(State Key Laboratory of New Ceramics and Fine Processing, School of Materials Science and Engineering,Tsinghua University, Beijing 100084, China)Abstract: Additive manufacturing is a worldwide hot issue during the last decade. Compared with counterparts in polymer and metal, additive manufacturing for ceramic had a relatively late breakthrough, but the development in recent years has also make it a highlight as well. In this perspective, based on state-of-the-art of ceramic additive manufacturing and the development history of polymer & metal additive manufacturing, we propose the idea of “additive materialization”, that is, making additively manufactured components with customized structure and performance simultaneously. The evolution of the connotation in “customization” in additive manufacturing will be analyzed first together with its essential causes. Then current obstacles in various ceramic additive manufacturing techniques and corresponding embedded potentials to realize additive materialization in ceramic components would be pointed out and summarized. At last, possible approaches and related focuses towards “additive materialization” would be proposed. Keywords: additive manufacturing; ceramics; customization; multiscale structure; structure-performance relationship; three dimensional (3D) printing从“衔泥筑巢”到“添砖加瓦”,通过逐步添加材料实现成型与制造的例子在自然界与人类社会中并不鲜见。
增材制造工艺

增材制造工艺
增材制造工艺是一种通过添加材料来建造三维物体的工艺。
增材制造可以分为多种类型,包括3D打印、激光烧结、电子束熔化、喷射沉积成型等。
这些技术都是通过分层制造的方法在建造物体的过程中添加材料,从而实现逐层堆积并形成所需形状。
与传统的制造方法相比,增材制造具有灵活性高、生产周期短、生产成本低等优点。
目前,增材制造技术已广泛应用于航空航天、医疗、汽车、船舶等领域,成为现代制造业重要的工艺手段之一。
增材制造简介
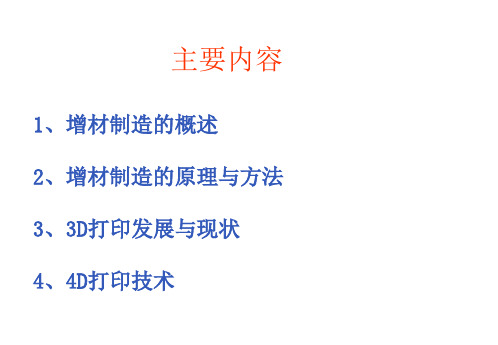
一是材料单元的控制技术。即如何控制材料单元在堆积过程中的物理与化学变化是一 个难点,例如金属直接成型中,激光熔化的微小熔池的尺寸和外界气氛控制直接影响制造 精度和制件性能。
二是设备的再涂层技术。增材制造的自动化涂层是材料累加的必要工序,再涂层的工 艺方法直接决定了零件在累加方向的精度和质量。分层厚度向0.01mm发展,控制更小的层 厚及其稳定性是提高制件精度和降低表面粗糙度的关键。
• 社会化制造 • 那么每个人都会成为一个工厂 • 它将改变制造商品的方式 • 并改变世界的经济格局 • 进而改变人类的生活方式
4D打印技术与3D打印技术从字面相比较,多了一个“D”,多出的这个“D”是指时间纬度, 准确地说是一种新型能够自动变形的材料,不需要借助于任何复杂的机电设备,就能够按 照事先所设计的产品自动折叠成相应的形状,并满足性能要求。4D打印的关键是记忆合金, 4D打印由MIT(MassachusettsInstituteofTechnology,麻省理工学院)与Stratasys(斯 特塔西有限公司)教育研发部门合作研发的一种能让材料快速成型的革命性新技术。
以制作结构比较复杂的模型 或零件。
缺点: 1.零件较易弯曲和变形,
需要支撑。 2.设备运转及维护成本
较高。 3.可使用需要避光保护。 5.液态树脂固化后的零
件较脆、易断裂。
2. SLS ( 粉末烧结技术 ):选择性激光烧结工艺(Selective Laser Sintering,SLS)。 原理:先采用压辊将一层粉末平铺到已成型工件的上表面,数控系统操控激光束按照该层截面轮 廓在粉层上进行扫描照射而使粉末的温度升至熔化点,从而进行烧结并于下面已成型的部分实现粘合。 当一层截面烧结完后工作台将下降一个层厚,这时压辊又会均匀地在上面铺上一层粉末并开始新一层 截面的烧结,如此反复操作直接工件完全成型。 优点:1.可直接制作金属制件(独有);2.材料选择广泛; 3.可制造复杂构件或模具;4.不需要增加基 座支撑;5.材料利用率高。 缺点:1.样件表面粗糙,呈现颗粒状; 2.加工过程会产生有害气体。
3D打印技术的起源与演变1

3D打印技术的起源与演变-13D打印技术是根据三维CAD模型或通过逆向工程重建的模型,采用离散材料(粉末、液体、片、丝、板、块等)逐层累加来制造实体零件的技术。
相对于传统机械加工去除材料的“减材”加工技术,锻/铸造和粉末冶金近似“等材”的制造技术,3D打印制造又被称为“增材制造”( Additive Manufacturing,AM)/(Additive Fabrication,AF)、自由成形制造(Freeform Fabrication,FF)或增层制造( Additive Layer Manufacture,ALM)。
3D打印的核心制造思想最早起源于美国。
1892年,J.E.Blanther在其美国专利中建议用分层构造法构建立体地形图,首创了叠层制造原理。
1902年Carlo Baese 的专利提出了用光敏聚合物制造塑料件的原理。
1904年Perera提出了将硬纸板切割轮廓线,再将这些纸板粘结成三维地形图的方法。
但学术和业界认为:现代意义上的3D打印技术出现在1980年代。
以1988(7)年美国3D System公司根据Hull的专利,采用“立体平版印刷快速原型”(又称为光敏液相固化法、光固化成形、立体光刻等)(Stereo Lithography,SL)/(Stereo Lithography Appearance,SLA)技术,通过紫外激光束在偏转镜作用下扫描照射树脂固化,逐层制造得到三维实体模型所推出的SLA-250型首台商用“液态光敏树脂选择性固化成形机”的诞生为标志,现代增材制造技术真正开始形成。
随后1992年(1993?),美国麻省理工学院(MIT)的Scans (Saches?)E. M.和 Cima M. J.等首先提出了3D打印技术的概念,并创建了三维打印企业Z Corp。
自此,3D打印概念和技术日益得到关注。
立体光刻诞生后的几年里,多种增材制造方法也迅速兴起,主要包括:1988年Feygin发明,Helisys公司的分层实体制造(Laminated Object Manufacturing,LOM);1989年Deckard发明,DTM公司的选区激光烧结(Selective Laser Sintering,SLS);1992年Crump/ Stratasys公司的熔融沉积造型(Fuesd Depostion Modeling,FDM);Cubital公司的Solid Ground Curing (SGC) ;以及原本狭义,今天却被媒体广义地用作增材制造代表性术语的“三维(3D)打印”(Three Dimension Printing,3DP)。
增材制造技术 课程知识点

增材制造技术课程知识点一、增材制造技术概述。
1. 定义。
- 增材制造(Additive Manufacturing,AM),俗称3D打印,是一种基于离散 - 堆积原理,由零件三维数据驱动直接制造零件的科学技术体系。
它与传统的减材制造(如切削加工)和等材制造(如铸造、锻造)方法不同,通过材料逐层累加的方式来构建三维实体。
2. 发展历程。
- 早期概念的起源可以追溯到20世纪80年代,美国的Charles Hull发明了立体光刻(Stereolithography,SLA)技术,这是最早的商业化增材制造技术。
- 随后,多种增材制造技术相继发展,如选择性激光烧结(Selective Laser Sintering,SLS)、熔融沉积建模(Fused Deposition Modeling,FDM)等,在不同的材料和应用领域不断拓展。
- 近年来,增材制造技术在航空航天、医疗、汽车等众多行业得到了广泛的应用,技术不断创新,朝着高精度、高性能、多材料复合等方向发展。
3. 增材制造技术的优势。
- 设计自由度高。
- 能够制造传统制造方法难以实现的复杂几何形状的零件。
例如,内部具有复杂流道结构的航空发动机零部件,通过增材制造可以一体成型,无需进行复杂的装配过程。
- 材料利用率高。
- 与传统切削加工相比,增材制造是逐层累加材料,减少了材料的浪费。
特别是对于一些昂贵的材料,如钛合金等,在航空航天领域可以大大降低成本。
- 快速原型制造。
- 可以快速将设计概念转化为实体模型,便于产品的设计验证、功能测试等。
在产品开发的早期阶段,能够快速迭代设计方案,缩短产品开发周期。
4. 增材制造技术的局限性。
- 制造精度相对较低。
- 虽然技术在不断进步,但与传统精密加工相比,目前部分增材制造技术的精度仍然有限。
例如,FDM技术在制造小型、精密零件时,可能会出现层间精度误差,需要进行后处理来提高精度。
- 生产效率较低。
- 对于大规模生产,增材制造的速度相对较慢。
增材制造--金属粉末再利用技术规范-最新国标

增材制造金属粉末再利用技术规范1 范围本文件规定了增材制造用金属粉末再利技术要求和质量保证规定。
本文件适用于单一材料粉末床熔融和定向能量沉积工艺金属粉末的再利用和质量控制,其他工艺的粉末再利用和质量控制可参考本文件执行。
2 规范性引用文件下列文件中的内容通过文中的规范性引用而构成本文件必不可少的条款。
其中,注日期的引用文件,仅该日期对应的版本适用于本文件;不注日期的引用文件,其最新版本(包括所有的修改单)适用于本文件。
GB/T 35351 增材制造术语GB/T 39251 增材制造金属粉末性能表征方法3 术语和定义GB/T 35351和GB/T 39251界定的以及下列术语和定义适用于本文件。
回收粉末 recovered powder从设备给料区、成形区、溢流区以及零件内部回收的可进行再利用的混合粉末。
注:若给料区回收的粉末作为原始粉末单独存放,则不视为回收粉末。
再利用粉末 reused powder回收后按规定对回收粉末进行筛分、干燥、混合等处理后获得的粉末。
粉末再处理 powder reconditioning对回收粉末进行的一系列处理,以调整粉末的颗粒形态、粒度分布、表面化学成分和残留水分等,使其满足适用的粉末规范。
粉末混合 powder blending将符合同一粉末规范的粉末混合在一起,使粉末特性始终保持一致的过程。
待混合的粉末可能来自一台或多台设备,来自同一个原材料批次并具有相似工艺历史的回收粉末,也可以是符合同一粉末规范的不同批次原材料进行混合。
粉末循环 powder recycling对回收粉末进行再处理(或筛分、干燥、混合等处理),并在使用期间进行检测等一系列活动。
粉末隔离 powder quarantine对回收后未进行再处理的粉末进行标识和隔离存储,以防止污染或混用。
循环次数 recycle time粉末进行再利用的次数,如经过一个成形周期的回收粉末,其循环次数为1次。
4 技术要求粉末再利用策略4.1.1 策略1:一次性使用粉末4.1.1.1 该增材制造过程不进行粉末的再利用。
增材制造技术的标准术语(f2792)

增材制造技术的标准术语(f2792)
增材制造技术是一种通过添加材料的方法来制造三维实物的先进制造技术。
它涵盖了多种不同的技术,如3D打印、激光烧结、电子束熔化等。
由于这些技术的快速发展和广泛应用,必须建立相关的标准术语来确保全球各地的制造商、研究机构和消费者之间的有效沟通。
以下是一些增材制造技术的标准术语:
1. 增材制造:一种制造方法,通过逐层堆积材料并逐步形成三维实物。
2. 3D打印:一种增材制造技术,通过将材料逐层堆积以形成三维实物。
3. 激光烧结:一种增材制造技术,通过激光束将粉末材料熔结在一起以形成三维实物。
4. 电子束熔化:一种增材制造技术,通过电子束将粉末材料熔化在一起以形成三维实物。
5. 材料:增材制造过程中使用的原材料,可以是金属、塑料、陶瓷等。
6. 层厚:堆积材料的每一层的厚度。
7. 光固化:一种增材制造技术,通过紫外线或可见光固化树脂来形成三维实物。
8. 粉末床:一种增材制造技术中的材料容器,通常是一个平坦的表面,用于放置粉末材料。
9. 构建平台:增材制造机器上用于构建三维实物的平台。
10. 支撑材料:一种特殊的材料,用于支撑堆积材料的三维结构。
在制造过程结束后,它们通常会被移除。
增材制造专业术语 中英对照
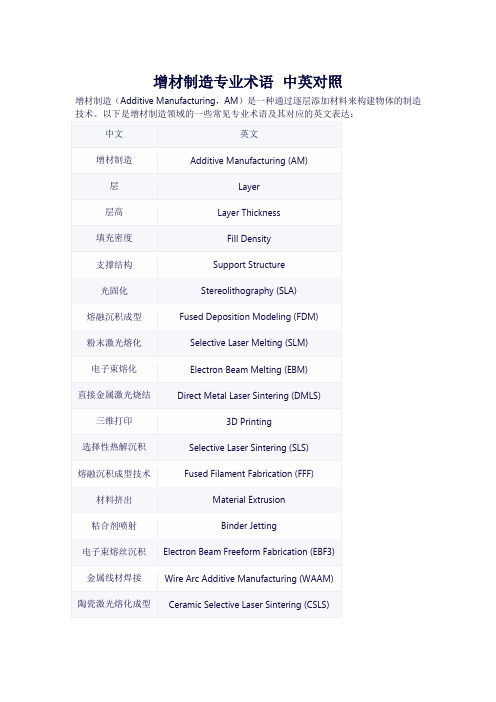
增材制造专业术语 中英对照
增材制造(Additive Manufacturing,AM)是一种通过逐层添加材料来构建物体的制造技术。以下是增材制造领域的一些常见专业术语及其对应的英文表达:
中文
英文
增材制造
Additive Manufacturing (AM)
层
Layer
层高
Layer Thickness
填充密度
Fill Density
支撑结构
Support Structure
光固化
Stereolithography (SLA)
熔融沉积成型
Fused Deposition Modeling (FDM)
粉末激光熔化
Selective Laser M源自lting (SLM)电子束熔化
Electron Beam Melting (EBM)
粘合剂喷射
Binder Jetting
电子束熔丝沉积
Electron Beam Freeform Fabrication (EBF3)
金属线材焊接
Wire Arc Additive Manufacturing (WAAM)
陶瓷激光熔化成型
Ceramic Selective Laser Sintering (CSLS)
直接金属激光烧结
Direct Metal Laser Sintering (DMLS)
三维打印
3D Printing
选择性热解沉积
Selective Laser Sintering (SLS)
31增材制造技术概述精
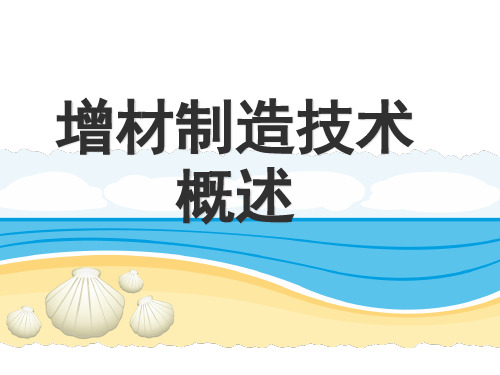
如:对于大尺寸金属零件,采用多激光束(4~6个激光源)同步加 工,提高制造效率,成形效率提高10倍。对于大尺寸零件,研究 增材制造与切削制造结合的复合关键技术,发挥各工艺方法的其 优势,提高制造效率。
3.高效制造技术
3.技术优势
1. AM技术不需要传统的刀具、夹具、模具及多道加工工序。 2. AM技术能够满足航空武器等装备研制的低成本、短周期需求。 3. AM技术有助于促进设计-生产过程从平面思维向立体思维的转变。 4. AM技术能够改造现有的技术形态,促进制造技术提升。 5. AM技术特别适合于传统方法无法加工的极端复杂几何结构。 6. AM技术非常适合于小批量复杂零件或个性化产品的快速制造。 7. AM技术特别适合各种设备备件的生产与制造。
其实质就是CAD软件驱动下的激光三维熔覆过程,其典型过程如图:
图 金属零件激光增材制造典型过程
电弧增材制造:
采用电弧送丝增材制造方法进行每层环形件焊接, 即送丝装置送焊丝,焊枪熔化焊丝进行焊接,由内 至外的环形焊道间依次搭接形成一层环形件;然后 焊枪提高一个层厚,重复上述焊接方式再形成另一 层环形件,如此往复,最终由若干层环形件叠加形 成钛合金结构件。
1. 增材制造的精度取决于材料增加的层厚和增材单元的尺寸和精 度控制。
未来将发展两个关键技术: 一是金属直接制造中控制激光光斑更细小,逐点扫描方式使增材 单元能达到微纳米级,提高制件精度; 二是光固化成形技术的平面投影技术,投影控制单元随着液晶技 术的发展,分辨率逐步提高,增材单元更小,可实现高精度和高 效率制造。
片状平面层。然后利用相关设备分别制造各薄 片层,与此同时将各薄片层逐层堆积,最终制 造出所需的三维零件,如图3-2所示。
增材制造的新名词及含义

增材制造的新名词及含义自从3D打印技术的发展,增材制造已成为制造业的一个热门话题。
以下是一些增材制造的新名词及其含义:1. 3D打印(3D Printing):一种将数字模型转化为实体物体的制造技术。
它通过不断堆叠材料来逐层构建物体。
2. 液体打印(Liquid Printing):一种使用液体型态材料的3D打印技术。
相比于传统的固体材料,液体型态材料具有更高的流动性和变形能力,能够打印出更复杂的结构。
3. 大型增材制造(Large-scale Additive Manufacturing):指可以制造比传统3D打印机更大尺寸的物体的增材制造技术。
这些大型打印机通常使用更多材料,并具备更高的打印速度,可以应用于建筑、汽车和航空等领域。
4. 金属3D打印(Metal 3D Printing):一种使用金属材料进行3D打印的增材制造技术。
与传统的塑料3D打印不同,金属3D打印需要使用激光熔化金属粉末或电子束熔化金属线来逐层打印金属物体。
5. 细胞打印(Bioprinting):一种使用活细胞、生物材料和生物相容性材料进行打印的3D打印技术。
细胞打印可用于生物组织工程、器官移植和药物开发等领域。
6. 纳米3D打印(Nanoprinting):一种使用纳米尺度材料进行3D打印的技术,用于制造微观和纳米级别的结构。
这种技术可以应用于纳米电子器件、纳米传感器和光子学器件等领域。
7. 混合材料打印(Multi-material Printing):一种在同一建筑过程中使用多种不同材料进行打印的技术。
这种技术可以在一个构件中使用不同材料的不同性能,提供更多的设计自由度和功能性。
8. 生物可降解打印(Biodegradable Printing):一种通过使用可降解材料进行3D打印,制造出可以分解为环境中无害物质的物体。
这种技术可以用于制造环境友好和可持续的产品。
9. 电子打印(Electronic Printing):一种利用印刷技术制造电子器件的增材制造技术。
每日科技名词生物增材制造技术

每日科技名词生物增材制造技术生物增材制造技术biological materials fabricated by 3D printing定义:将生物材料或生物单元(细胞或蛋白质等)按仿生形态学、生物体功能、细胞特定微环境等要求用增材制造的方法制造出具有复杂结构、功能和个性化的生物材料三维结构或体外三维生物功能体的制造方法。
学科:机械工程_机械制造工艺与设备_近净成形与快速制造相关词:增材制造数字化制造技术绿色制造技术【延伸阅读】组织、器官的损伤或功能衰竭是人类医学面临的一大难题。
“人造器官”一直以来是人类的梦想,生物增材制造技术便是实现这一梦想的有效途径。
从广义上讲,与生物医学领域相关的增材制造技术均可视为生物增材制造技术。
我国清华大学的一些学者根据原材料及打印成品的不同,将这一技术分成五个层次。
第一层次不涉及生物相容性,如打印精确的组织器官模型,以便于外科手术的路径规划;第二层次要求生物相容性但无需降解,如打印钛合金关节和硅胶假体;第三层次是制造具有生物相容性且可降解的产品,如打印骨支架和血管支架;第四层次是操纵活细胞直接构建生物组织或器官,如打印皮肤、血管,这也是狭义上对生物增材制造技术的定义;第五层次是以类器官(Organoid)或微器官为基本单元,制造复杂的生命系统。
生物增材制造技术的特点,在于其使用的是生物材料或生物单元(统称为生物墨水),技术原理和过程则与普通的增材制造技术大同小异,主要分为挤出型、液滴型和光固化三类。
挤出型增材制造最为常见,它采用压力驱动的方式挤出连续的细丝(其成分通常为细胞和水凝胶),可用于打印各种黏度的生物材料和不同浓度的细胞,得到的组织结构具有足够的机械性能。
液滴型增材制造以含有细胞的独立的液滴作为基本单元,其精度更高,能够打印高细胞密度的结构。
光固化增材制造利用的是光敏树脂的光聚合特性,相比于零维的液滴和一维的细丝,光固化方法打印的是二维的平面,因此具有更高的打印速度。
增材制造标准

增材制造标准引言:增材制造是一种新兴的制造技术,它通过逐层堆积材料来创建三维物体。
随着增材制造技术的快速发展和广泛应用,对其标准化的需求也日益增加。
本文将介绍增材制造标准的重要性以及目前已有的一些相关标准。
一、增材制造标准的重要性1. 保证产品质量:增材制造的产品广泛应用于航空航天、汽车、医疗等领域,对产品质量的要求非常高。
制定增材制造标准可以确保产品的性能、可靠性和一致性。
2. 促进技术发展:标准化可以促进技术的交流和合作,推动增材制造技术的进步和创新。
统一的标准可以让不同厂商、研究机构之间进行合作,加速技术的发展和应用。
3. 降低成本:通过制定标准,可以减少产品开发和制造过程中的重复工作,降低成本。
标准化还可以提高生产效率,减少废品率,降低生产成本。
二、增材制造标准的分类1. 材料标准:增材制造使用的材料种类繁多,需要制定相应的材料标准,包括材料的成分、力学性能、热学性能等要求。
2. 设备标准:增材制造设备种类众多,不同的设备具有不同的工艺和性能。
制定设备标准可以确保设备的质量和性能,提高设备的互换性和可靠性。
3. 工艺标准:增材制造涉及到许多不同的工艺,包括激光熔化、电子束熔化、粉末床熔化等。
制定工艺标准可以确保产品的质量和一致性,提高工艺的可控性和稳定性。
4. 检测标准:增材制造产品的质量检测非常重要,需要制定相应的检测标准,包括产品的尺寸精度、表面质量、材料性能等。
5. 设计标准:增材制造的设计方法和要求与传统制造有很大差异,需要制定相应的设计标准,包括设计规范、设计工具和方法等。
三、已有的增材制造标准1. ISO/ASTM 52900:这是国际标准化组织(ISO)和美国标准与测试协会(ASTM)联合制定的增材制造术语和定义标准。
该标准为增材制造领域的相关术语提供了统一的定义,有助于消除术语混淆和误解。
2. ISO/ASTM 52910:这是一项指南标准,旨在为增材制造过程中的材料选择和性能评估提供指导。
- 1、下载文档前请自行甄别文档内容的完整性,平台不提供额外的编辑、内容补充、找答案等附加服务。
- 2、"仅部分预览"的文档,不可在线预览部分如存在完整性等问题,可反馈申请退款(可完整预览的文档不适用该条件!)。
- 3、如文档侵犯您的权益,请联系客服反馈,我们会尽快为您处理(人工客服工作时间:9:00-18:30)。
49
Electrospun
电纺丝
50
Electrostaticjet
静电式喷射
51
Extruder
挤压器
52
Filament
丝材
53
Forced Forming
受迫成形
54
Free From Fabrication
FFF
自由成形制造
55
Freeform fabricationwithmicro-droplet Jetting
17
Computer-Aided Manufacturing
CAM
计算机辅助制造
18
Computer Numerical Control
CNC
计算机数字控制
19
Concept model / Conceptual model
概念模型
20
ContinuousPrinting/
Continuous InkJetting
LAMP
激光辅助制造
73
Laser cladding
激光熔覆
74
LaserCladdingRapidManufacturlng
LCRM
激光熔覆式快速制造
75
Laser EngineeredNet Shaping
(Laser Engineering Net Shaping)
微滴喷射自由成形
56
Freeform Manufacturing
FM
自由成形制造
57
Fused Deposition Modeling
FDM
熔融沉积成形
58
Green part
绿件,生坯件
59
Growing Forming
生长成形
60
Hard tooling
硬模
61
Hybrid rapid manufacturing of metallic objects
45
Ejection aperture/ Ejection orifice
喷孔
46ห้องสมุดไป่ตู้
Electron Beam Free Form Fabrication
EBF3
电子束自由形状制造
47
Electron Beam Melting
EBM
电子束熔化
48
Electrohydrodynamic jet
E-jet
64
Hybrid RM using powder-bed technology and CNC machining
SLM与CNC切削加工复合快速制造
65
Indirect fabricationprocesses
间接制造
66
Indirect Metal Forming
IMF
金属构件的间接成形
67
Ink
金属构件复合快速式制造
62
Hybrid RM using deposition technology and CNC machining
沉积技术与CNC切削加工复合快速制造
63
Hybrid RM using laminated manufacturing and CNC machining
LOM与CNC切削加工复合快速制造
AMT
先进制造技术
7
Ballistic Particle Manufacturing
BPM
弹道微粒制造
8
Bionical Forming
仿生制造
9
Bridge Tooling
过渡模,桥模
10
Brown part
褐色件,烧结后工件
11
Bubble jet
热泡式喷射
12
Build table
成形工作台
13
增材制造术语
1
英文全称
英文简称
中文
2
Absolute Accuracy
绝对精度
3
Accuracy
精度
4
Adaptive Slicing
自适应切片
5
AdditiveManufacturing
(Additive Fabrication)
AM
(AF)
增材制造
6
Advance Manufacturing Technology
墨水
68
Ink chamber
墨腔
69
Inkjet printer
喷墨打印机
70
Laminated Object Manufacturing
LOM
分层实体制造,叠层实体制造
71
Laser Additive Manufacturing
LAM
激光增材制造
72
Laser Aided Manufacturing Process
DOD
按需式
41
Droplet-based Metal Manufacturing
DMM
基于液滴的金属制造
42
Drop-On-Demand
DOD
按需式
43
Drop-on-Drop deposition
DoD
液滴沉积于液滴
44
Drop-on-Powder bed deposition
DoP
液滴沉积于粉床
Coaxialinside-beam powder feeding
同轴光内送粉
14
Coaxial powderfeeding laser cladding
同轴送粉激光熔覆
15
Computer-Aided Design
CAD
计算机辅助设计
16
Computer-Aided Engineering
CAE
计算机辅助工程
CP/CIJ
连续式打印
21
Coated paper
涂覆纸
22
Curable resin
光固化树脂
23
Deflection jet
电场偏转式喷射
24
Deposition ofMolten Metal Droplets
DMMD
熔化金属液滴沉积
25
Desk Top Manufacturing
DTM
桌面制造
DLF
直接激光制造
31
Direct Manufacturing
DM
直接制造
32
Direct Metal Deposition
DMD
直接金属沉积
33
Direct Metal Forming
DMF
直接金属成形
34
Direct Metal Laser Sintering
DMLS
直接金属激光烧结
35
DirectSelectiveLaserSintering
26
Digital Manufacturing
数字制造
27
Digital Materials
数码材料
28
Direct Ceramic Ink-Jet Printing
DCIJP
直接陶瓷喷墨打印
29
Direct Jetting deposition
直接喷射沉积
30
DirectLaser Fabrication
DSLS
直接选区激光烧结
36
Direct Shell Casting Process
DSCP
直接壳型铸造
37
Dispersed/Accumulated Forming
离散/堆积成形
38
dots per inch
dpi
每一英寸上能打印的墨点数
39
Drop generator
液滴发生器
40
Drop-On-Demand