下料与焊接
焊制压力容器筒体的准确下料
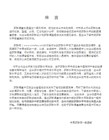
收稿日期:2009210221作者简介:郭 徽(19762),女,辽宁大连人,工程师,学士,主要从事压力容器设计及制造工艺编制工作。
文章编号:100027466(2010)022*******焊制压力容器筒体的准确下料郭 徽,李 涛(大连冰山集团金州重型机器有限公司设计开发部,辽宁大连 116100)摘要:根据实际生产中焊制压力容器制造工艺都是先使封头成型,再根据封头实际内径尺寸来配制筒体内径的特点,探讨了焊制压力容器制造中由板材焊制成型的筒体的准确下料问题。
关键词:压力容器;筒体;下料中图分类号:T H 49;TQ 050.6 文献标志码:BExact Laying 2out for Pressure V essel CylinderGU O H ui ,L I T ao(Jinzho u Heavy Machinery Co.Lt d.Dalian BingShan Group ,Dalian 116100,China )Abstract :In p ractical manufact uring of pressure vessel ,it s head was to be formed at first andt hen follow t he formed head size to match t he inner diameter and t he internals.Based on t his working p rocedure ,a st udy was made for exact laying 2out for correct cylinder.K ey w ords :p ressure vessel ;shell ;laying 2o ut 焊制压力容器是筒体、封头、接管等构件由焊接接头连接构成的,在生产实践中,制造焊制压力容器时,一般都是先加工封头,待封头成型后再根据封头实际内径尺寸来配制筒体的内径,这是因为筒体的成型公差较封头成型公差更好控制。
(完整版)下料工艺
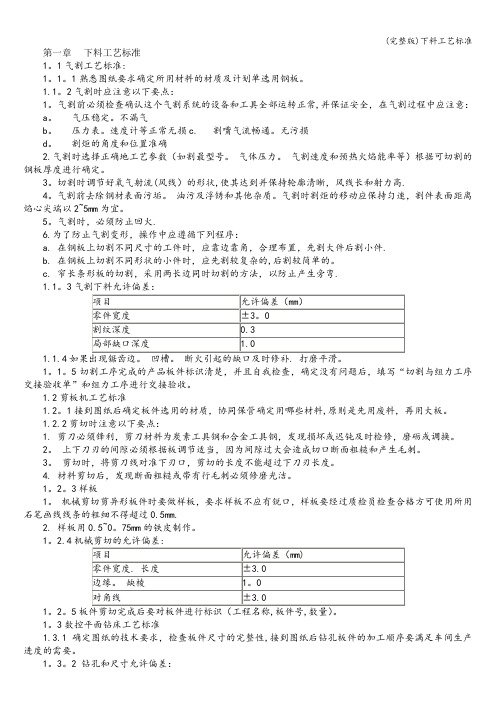
第一章下料工艺标准1。
1气割工艺标准:1。
1。
1熟悉图纸要求确定所用材料的材质及计划单选用钢板。
1.1。
2气割时应注意以下要点:1。
气割前必须检查确认这个气割系统的设备和工具全部运转正常,并保证安全,在气割过程中应注意:a。
气压稳定。
不漏气b。
压力表。
速度计等正常无损c. 割嘴气流畅通。
无污损d。
割炬的角度和位置准确2.气割时选择正确地工艺参数(如割最型号。
气体压力。
气割速度和预热火焰能率等)根据可切割的钢板厚度进行确定。
3。
切割时调节好氧气射流(风线)的形状,使其达到并保持轮廓清晰,风线长和射力高.4。
气割前去除钢材表面污垢。
油污及浮锈和其他杂质。
气割时割炬的移动应保持匀速,割件表面距离焰心尖端以2~5mm为宜。
5。
气割时,必须防止回火.6.为了防止气割变形,操作中应遵循下列程序:a. 在钢板上切割不同尺寸的工件时,应靠边靠角,合理布置,先割大件后割小件.b. 在钢板上切割不同形状的小件时,应先割较复杂的,后割较简单的。
c. 窄长条形板的切割,采用两长边同时切割的方法,以防止产生旁弯.1.1。
31.1.4如果出现锯齿边。
凹槽。
断火引起的缺口及时修补. 打磨平滑。
1。
1。
5切割工序完成的产品板件标识清楚,并且自我检查,确定没有问题后,填写“切割与组力工序交接验收单”和组力工序进行交接验收。
1.2剪板机工艺标准1.2。
1接到图纸后确定板件选用的材质,协同保管确定用哪些材料,原则是先用废料,再用大板。
1.2.2剪切时注意以下要点:1. 剪刀必须锋利,剪刀材料为炭素工具钢和合金工具钢,发现损坏或迟钝及时检修,磨砺或调换。
2。
上下刀刃的间隙必须根据板调节适当,因为间隙过大会造成切口断面粗糙和产生毛刺。
3。
剪切时,将剪刀线对准下刃口,剪切的长度不能超过下刀刃长度。
4. 材料剪切后,发现断面粗糙或带有行毛刺必须修磨光洁。
1。
2。
3样板1。
机械剪切剪异形板件时要做样板,要求样板不应有锐口,样板要经过质检员检查合格方可使用所用石笔画线线条的粗细不得超过0.5mm.2. 样板用0.5~0。
机械加工工艺基础1
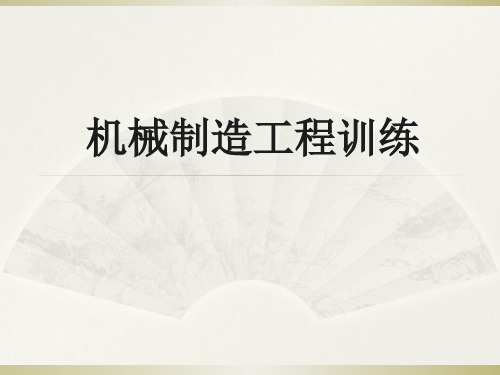
三、金属切削机床
返回索引
1、机床的类型
金属切削机床是用来对工件进行加工的机 器,故称为“工作母机”,习惯上称机床。
按加工性质和所用刀具分类:分为车床、铣床、 钻床、磨床、齿轮加工机床等12大类;
加工 方法 Ra(微米)
粗车 粗镗
50
粗铣 粗刨
25
钻孔
12.5
半精车 6.3
精铣
精刨
3.2
精车
1.6
粗磨
0.8
精磨
0.4
精密加工 0.1-0.012
表面特征 可见明显刀痕 可见刀痕 微见刀痕 可见加工痕迹
微见加工痕迹 看不清加工痕迹 可辨加工痕迹方向 微辨加工痕迹方向 只能按表面光泽辩识
3.切削运动与切削用量
切削速度:切削刃上选定点相对于工件主运动的瞬 时速度,用V表示,单位为m/s 或m/min
进 给 量:刀具在进给运动方向上相对于工件的位 移量,用f表示,车、钻和铣削时单位 为mm/r
背吃刀量: 已加工表面和待加工表面之间的垂直距 离,用ap表示,单位为mm,如下图:
3.2.1车削切削速度、背吃刀量的计算
机器零件的基本表面包括:外圆、内圆 (孔)、平面和成型面
基本表面主要由如下的加工方法获得
3.1 切削运动
机床名称
卧式车床 钻床 卧铣、立铣 牛头刨床
龙门刨床 外圆磨床
内圆磨床
平面磨床
机床的切削运动
主运动
进给运动
工件旋转运动 钻头旋转运动 铣刀旋转运动 刨刀往复运动
工件往复运动 砂轮高速旋转
砂轮高速旋转
铜管加工和焊接工艺标准规范标准

铜管加工和焊接工艺标准铜管加工工艺铜管一般要求密封冷媒系统要求管件内部表面清洁、无氧化、无水、无油等;不允许使用带有裂纹、不圆变形、扭曲、可见砂眼、喷墨(铜管厂检测有缺陷的标记)、发黑(氧化)等缺陷的铜管。
铜管加工要求总则管路的加工按设计图纸进行,形状、尺寸应符合设计要求;断口处直径改变应在铜管标准直径的2%以内,且断口不允许有飞边,毛刺;管件要脱油、去污、无铜屑,内外表面光洁,不许有油污、伤痕、氧化皮;焊接过程必须充氮保护,焊后用0.3~0.5MPa的干燥压缩空气吹净内部。
铜管下料、去毛刺使用工具:割管刀,有效直尺,铜管修边器铜管需定位固定后,再用割刀拆下,要保证割口平齐,不变形切割过程中,铜管均匀进给,以保证管口圆滑下料后必须用铜管修边器对端口去毛刺,去毛刺后,必须用0.3~0.5MPa的干燥压缩空气吹掉管内外的铜屑、杂物。
铜管弯曲使用工具:手工弯管机。
根据图纸和铜管的外形,选择合适的弯管机清除弯管机范围内一切可能影响弯管机运转的杂物,保证设备运行畅通无阻。
每次弯曲前需调整模具或参数,并进行空转试弯,确认设备正常后进行加工。
一般铜管的弯曲半径参照下表弯管后应把管子内部的油渍等异物清除掉。
喇叭口制作将已制作合格的铜管先套入一对应的铜钠子,再放入铜管喇叭口扩口专用工具相对应的孔中,放入时铜管扩口端高出扩口器夹具面0.5~1mm,夹紧扩口器夹具,在扩口器顶尖上涂少许空调冷冻油,然后将手柄顺时针旋紧,再旋紧四分之三圈,退四分之一圈,如此反复进行,直到所扩口成90±2°扩成喇叭口后,喇叭口的接触面应光滑平整,且厚度均匀一致;不应有裂纹、损伤、麻点皱折等不足;喇叭口不应有偏斜不正等现象。
焊接钎焊原理钎焊是利用液态钎料填满钎焊金属结合面的间隙面形成牢固接头的焊接方法,其工艺过程必须具备两个基本条件。
a)液态钎料能润湿钎焊金属并能致密的填满全部间隙;b)液态钎料与钎焊金属进行必要的物理、化学反应达到良好的金属间结合。
下料焊接培训资料
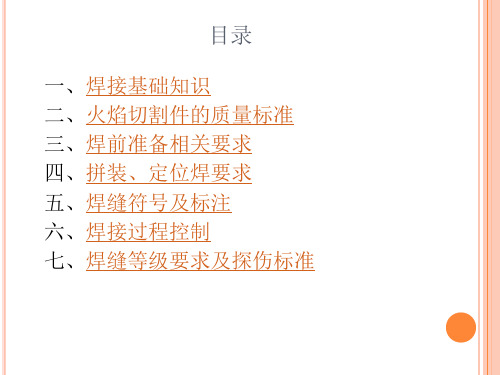
表示T型接头的交错断续角焊缝,焊角高度是5mm,相邻焊缝间距 为300mm,焊缝6段,每段焊缝长度150mm。
3).卷边焊接(卷边完全熔化)
卷边焊缝属于对接焊缝的一种,焊接时要将卷边完全熔化。若 图纸有明确标注按图纸标注进行焊接,以下是几种焊接示例:
6.角焊缝的焊缝厚度
在焊缝结构如图,若腿宽 (z) 决定焊缝结构,则应按图17 所示在图纸 上用字母 (z) 将其标注出来。 按DIN EN 22553规定
3). 根据重机标准JB/T5000 2-2007,组对时尺寸公差和形位公差 按B级和F级执行。达涅利标准描述相当于C级,不适合
4).角度公差: 角度未注极限偏差按表7的规定。角度偏差的公称尺寸以短边为 基准边,其长度从图样标明的基准点算起,见图6~图10.如在 图样上不标注角度、而只标注长度尺寸,测量充许偏差应以 mm/m计。 一般选B级,可不标注,选用其他精度等级均应在图样上标注。
七、焊缝等级要求及探伤标准
1. T型和L型焊缝接头 1).部分焊透焊缝无损探伤要求(Tab.3)
2).全焊透焊缝无损探伤要求(Tab.4)
2. 对接接头全焊透焊缝无损探伤要求(TAB.2)
4.根据达涅利标准2.8.302要求,原材料的表面锈蚀程度要达到ISO 8501-1标准中C级以上的要求。 依据ISO 8501-1:1988将未涂装过的钢材表面原始程度按氧化皮覆盖 程度和锈蚀程度分为四个等级,分别以A、B、C、D表示 A 大面积覆盖粘着的氧化皮,而几乎没有铁锈的钢材表面 ; B 已开始锈蚀,且氧化皮已开始剥落的钢材表面; C 氧化皮已因为锈蚀而剥落或者可以刮除,但在正常视力观察下仅 见到少量点蚀的钢材表面; D 氧化皮已因锈蚀而剥离,在正常视力观察下,已可见普遍发生点 蚀的钢材表面
生产部与下料车间的下料流程及注意事项
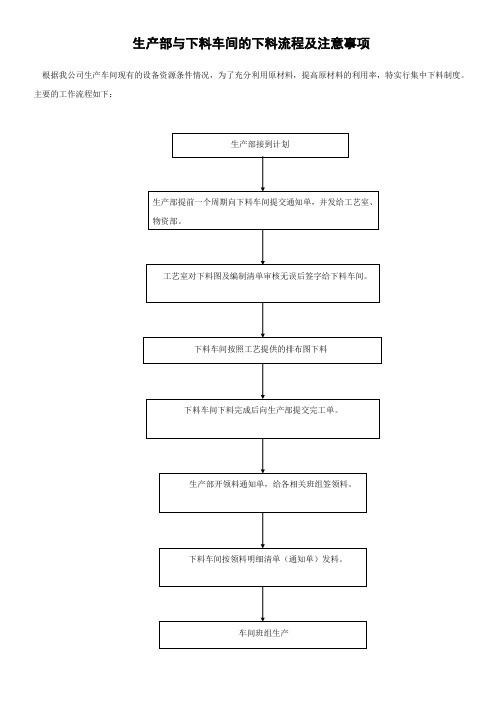
生产部与下料车间的下料流程及注意事项根据我公司生产车间现有的设备资源条件情况,为了充分利用原材料,提高原材料的利用率,特实行集中下料制度。
主要的工作流程如下:一、步骤详细说明:1、生产部接到生产计划后,进行排产作业,提出下料周期要求。
2、生产部向下料车间、工艺室发出下料通知单,下料通知单上应明确下料需求,即需要下料的具体数量,完成下料的具体时间。
3、工艺室对当次计划的下料布料图(零件清单及排料图)进行校核无误后,技术负责人签字发给下料车间,下料开始。
4、下料车间按照排图下料,下料完成后,向生产部提交下料完工单,告知生产部料已下好,可以取走。
5、生产部根据生产档案和材料明细开出领料通知单,领取已经下好的料,领料通知单需附领料明细。
6、下料车间按领料通知单及明细发料。
二、整个工作流程需注意以下几点:1、生产部提交的下料通知单的顺序应成套的提交,与生产档案保持一致,并且要明确具体单机的具体作业人。
2、生产部需提前3天提交下料通知单,给下料车间留出客观的作业时间。
3、机架的零件,排图要按层与层分开的排,下料时应按图纸标识分开存放,便于班组领用。
4、领料必须由班组长凭生产部签发的领料明细签字领料,生产部在每个班组确定一名材料领料员,除生产班组长和材料领用员外,其他人不得到下料车间领料。
5、对于大面积的材料,要先下料、后焊接,不可以先焊后下料。
6、生产部安排到下料车间下料的班组,要有先后次序,各班组到下料车间下料时应听从下料车间人员指挥,不得肆意行事。
7、考虑到车间用料的便利性,在剪板机处放置一部分厚度在6mm以下板材,直接剪成零件,由生产部核实后开领料通知单,到剪板机处找李安生领料,剪完后需要把废料清走,剪板机处不留废料,对于多剪多下的班组,多出部分由该班组按正常价格赔偿。
8、生产部晚上需要领料时,应在下午5点之前通知下料车间,下料车间安排人员加班。
9、生产部和下料车间之间,需要协调时应以联络单进行联络。
管道焊接工艺要求

一.钢材及焊接材料1. 焊接前必须查明所焊材料的钢号,以便正确地选用相应的焊接材料和确定合适的焊接工艺和热处理工艺。
2. 钢材必须符合国家标准(或部颁标准、专业技术标准)、进口钢材符合该国国家标准或合同规定的技术标准。
3. 焊接材[焊条、焊丝、钨棒、氩气、氧气、乙炔气(电石)和焊剂]的质量符合国家标准(或相关标准)。
4. 钢材、焊条、焊丝等均应有制造厂的质量合格证。
凡无质量合格证或对其质量有怀疑时,应按批号抽查试验。
合格后方可使用。
5. 焊条、焊丝的选用,应根据母材的化学成分、机械性能和焊接接头的抗裂性、碳扩散、焊前预热、焊后热处理以及使用条件综合考虑。
5.1 同种钢材焊接时,焊条(焊丝)的选用,一般符合下列要求:5.1. 焊缝金属性能和化学成分与母材相当。
5.2. 工艺性能良好。
5.2 异种钢材焊接时,焊条(焊丝)的选用,一般符合下列要求:(1)两侧之一为奥氏体不锈钢时,可选用含镍量较高的不锈钢焊条(焊丝)。
(2)两侧钢材均为非奥氏体不锈钢时,可选用成分介于二者之间或合金含量低的一侧相配的焊条(焊丝)。
6. 钨极氩弧焊用的电极、宜采用铈钨棒,所用的氩气纯度不低于99.95%。
7. 氧-乙炔焊所用的氧气纯度应在98.5%以上。
乙炔气纯度应符合GB6819-86《溶解乙炔》的规定。
如以电厂制备乙炔气,电石应有出厂证明书,其质量可采用检查焊缝金属中的硫、磷含量(按被焊金属标准)的方法来确定;用于焊接的乙炔气,应进行过滤,未经检查或杂质含量超过标准的电石,不得用于受监部件的焊接。
8. 埋弧自动焊用的焊剂应符合有关标准技术要求。
二.焊前准备1.焊口的位置应避开应力集中区且便于施焊及热处理,一般应符合下列要求:1.1锅炉受热面管子焊口,其中心线距离管子弯曲起点或汽包、联箱外壁以及支吊架边缘至少70mm,两个对接焊口间距离不得小于150mm。
1.2管道对接焊口、其中心线距离管子弯曲起点不得小于管子的外径,且不小于100mm(焊接、锻制、铸造成型管件外),距支吊架边缘至少50mm,两个对接焊口间距离不得小于管子的直径,且不得小于150mm。
下料工艺

一、下料通用工艺1 范围本通用工艺规定了下料的工艺规则,适用于本公司的产品材料的下料。
2 下料前的准备2.1 看清下料单上的材质、规格、尺寸及数量等。
2.2核对材质、规格与下料单要求是否相符。
材料代用必须严格履行代用手续。
2.3 查看材料外观质量(疤痕、夹层、变形、锈蚀等)是否符合有关质量规定。
2.4 将不同工件所用相同材质、规格的料单集中,考虑能否套料。
2.5 号料2.5.1 端面不规则的型钢、钢板、管材等材料号料时必须将不规则部分让出。
钢材表面上如有不平、弯曲、扭曲、波浪等缺陷,在下料切割和成形加工之前,必须对有缺陷的钢材进行矫正。
2.5.2 号料时,应考虑下料方法,留出切口余量。
2.5.3 有下料定尺挡板的设备,下料前要按尺寸要求调准定尺挡板,并保证工作可靠,下料时材料靠实挡板。
3 下料3.1剪板下料3.1.1钢板、角钢、扁钢下料时,应优先使用剪切下料。
钢板、扁钢用龙门剪床剪切下料,角钢用冲剪机剪切下料。
3.1.2 用剪床下料时,剪刃必须锋利,并应根据下料板厚调整好剪刃间隙,其值见下表3.1.3 剪切最后剩下的料头必须保证剪床的压料板能压牢。
3.1.4 下料时应先将不规则的端头切掉。
3.1.5 切口断面不得有撕裂、裂纹、棱边。
3.1.6 龙门剪床上的剪切工艺3.1.6.1 首先清理工件并划出剪切线,将钢板放至剪床的工作台面上,使钢板的一端放在剪床台面上以提高它的稳定性,然后调整钢板,使剪切线的两端对准下刀口,控制操作机构将剪床的压紧机构先将钢板压牢,接着进行剪切。
剪切狭料时,在压料架不能压住板料的情况下可加垫板和压板,选择厚度相同的板料作为垫板。
3.1.6.2 剪切尺寸相同而数量又较多的钢板、型材时,利用挡板(前挡、后挡板和角挡板)定位,免去划线工序。
3.1.6.3 利用挡板进行剪切时,必须先进行试剪,并检验被剪尺寸是否正确,然后才能成批剪切。
3.2 气割下料3.2.1 气割时,看清切割线条符号。
风管制作操作工艺
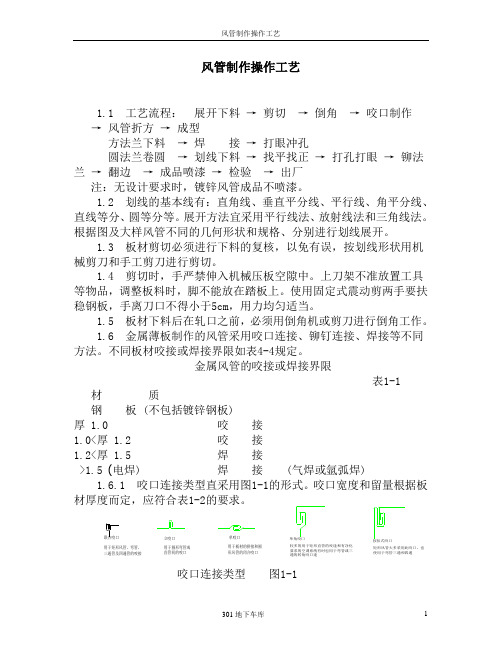
用于板材的拼接和圆形风管的闭合咬口用于矩形风管、弯管、三通管及四通管的咬接立咬口联合咬口用于圆形弯管或直管间的咬口单咬口按扣式咬口矩形风管大多采用此咬口,也使用于弯管三通和四通较多的用于矩形直管的咬逢和有净化要求的空调系统有时也用于弯管或三通的转角咬口逢单角咬口风管制作操作工艺1.1 工艺流程: 展开下料 → 剪切 → 倒角 → 咬口制作→ 风管折方 → 成型方法兰下料 → 焊 接 → 打眼冲孔圆法兰卷圆 → 划线下料 → 找平找正 → 打孔打眼 → 铆法兰 → 翻边 → 成品喷漆 → 检验 → 出厂注:无设计要求时,镀锌风管成品不喷漆。
1.2 划线的基本线有:直角线、垂直平分线、平行线、角平分线、直线等分、圆等分等。
展开方法宜采用平行线法、放射线法和三角线法。
根据图及大样风管不同的几何形状和规格、分别进行划线展开。
1.3 板材剪切必须进行下料的复核,以免有误,按划线形状用机械剪刀和手工剪刀进行剪切。
1.4 剪切时,手严禁伸入机械压板空隙中。
上刀架不准放置工具等物品,调整板料时,脚不能放在踏板上。
使用固定式震动剪两手要扶稳钢板,手离刀口不得小于5cm ,用力均匀适当。
1.5 板材下料后在轧口之前,必须用倒角机或剪刀进行倒角工作。
1.6 金属薄板制作的风管采用咬口连接、铆钉连接、焊接等不同方法。
不同板材咬接或焊接界限如表4-4规定。
金属风管的咬接或焊接界限表1-1材 质钢 板 (不包括镀锌钢板)厚 1.0 咬 接1.0<厚 1.2 咬 接1.2<厚 1.5 焊 接>1.5 (电焊) 焊 接 (气焊或氩弧焊)1.6.1 咬口连接类型直采用图1-1的形式。
咬口宽度和留量根据板材厚度而定,应符合表1-2的要求。
咬口连接类型 图1-11.6.2 焊接时可采用气焊、电焊或接触焊,焊缝形式应根据风管的构造和焊接方法而定,可选图4-3几种形式。
1.6.3 铆钉连接时,必须使铆钉中心线垂直于板面,铆钉头应把板材压紧,使板缝密合并且铆钉排列整齐、均匀。
焊接操作规范
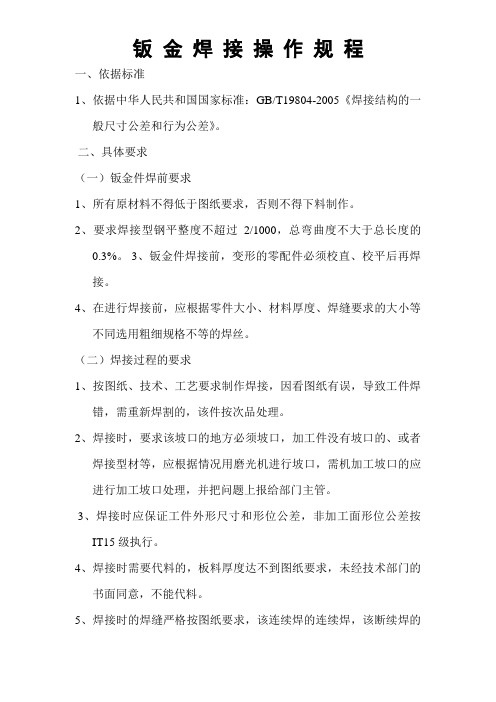
钣金焊接操作规程一、依据标准1、依据中华人民共和国国家标准:GB/T19804-2005《焊接结构的一般尺寸公差和行为公差》。
二、具体要求(一)钣金件焊前要求1、所有原材料不得低于图纸要求,否则不得下料制作。
2、要求焊接型钢平整度不超过2/1000,总弯曲度不大于总长度的0.3%。
3、钣金件焊接前,变形的零配件必须校直、校平后再焊接。
4、在进行焊接前,应根据零件大小、材料厚度、焊缝要求的大小等不同选用粗细规格不等的焊丝。
(二)焊接过程的要求1、按图纸、技术、工艺要求制作焊接,因看图纸有误,导致工件焊错,需重新焊割的,该件按次品处理。
2、焊接时,要求该坡口的地方必须坡口,加工件没有坡口的、或者焊接型材等,应根据情况用磨光机进行坡口,需机加工坡口的应进行加工坡口处理,并把问题上报给部门主管。
3、焊接时应保证工件外形尺寸和形位公差,非加工面形位公差按IT15级执行。
4、焊接时需要代料的,板料厚度达不到图纸要求,未经技术部门的书面同意,不能代料。
5、焊接时的焊缝严格按图纸要求,该连续焊的连续焊,该断续焊的一定要断续焊。
如图纸没有要求的断续焊尺寸长度,则每间隔50mm焊8~10mm,各焊点距离必须均匀一致。
6、连续焊缝要求平直光滑,不能有明显的高低不平现象,不能有焊穿、焊偏、焊疤、气孔、咬边等现象。
焊缝的焊角以图纸要求为准,无要求的保证焊角为相临件的最小厚度。
7、焊接完成后:每道焊缝应打磨处理,清除焊渣,去掉周边毛刺。
8、图纸上要求折弯的零件,没有技术部的书面同意,不得采用焊接方式。
9、钣金件在焊接过程中,需要敲击的部分可以用小型手工锤轻轻锤到要求尺寸,不得在钣金平面上以铁锤敲打。
(四)焊接公差要求1、线性尺寸公差见下表一所示。
表一、焊接件线性尺寸公差(IT15级)单位mm 基本尺寸 2~30 >30~120 >120~400 >1000~2000 >2000~4000公差要求±0.5 ±0.8 ±1.0 ±2 ±4.02、角度尺寸公差见下表二所示。
钢筋工程下料的步骤及方法
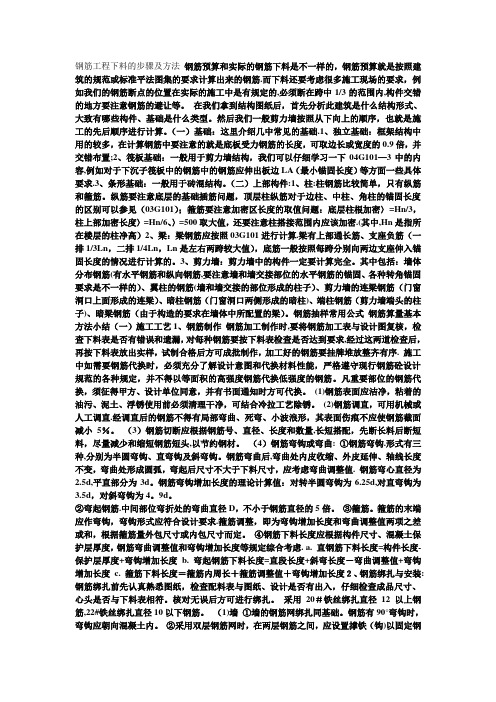
钢筋工程下料的步骤及方法钢筋预算和实际的钢筋下料是不一样的,钢筋预算就是按照建筑的规范或标准平法图集的要求计算出来的钢筋.而下料还要考虑很多施工现场的要求,例如我们的钢筋断点的位置在实际的施工中是有规定的,必须断在跨中1/3的范围内,构件交错的地方要注意钢筋的避让等。
在我们拿到结构图纸后,首先分析此建筑是什么结构形式、大致有哪些构件、基础是什么类型。
然后我们一般剪力墙按照从下向上的顺序,也就是施工的先后顺序进行计算。
(一)基础:这里介绍几中常见的基础.1、独立基础:框架结构中用的较多,在计算钢筋中要注意的就是底板受力钢筋的长度,可取边长或宽度的0.9倍,并交错布置;2、筏板基础:一般用于剪力墙结构,我们可以仔细学习一下04G101—3中的内容,例如对于下沉子筏板中的钢筋中的钢筋应伸出板边LA(最小锚固长度)等方面一些具体要求.3、条形基础:一般用于砖混结构。
(二)上部构件:1、柱:柱钢筋比较简单,只有纵筋和箍筋。
纵筋要注意底层的基础插筋问题,顶层柱纵筋对于边柱、中柱、角柱的锚固长度的区别可以参见(03G101);箍筋要注意加密区长度的取值问题:底层柱根加密〉=Hn/3,柱上部加密长度〉=Hn/6、〉=500取大值,还要注意柱搭接范围内应该加密.(其中,Hn是指所在楼层的柱净高)2、梁:梁钢筋应按照03G101进行计算.梁有上部通长筋、支座负筋(一排1/3Ln,二排1/4Ln,Ln是左右两跨较大值),底筋一般按照每跨分别向两边支座伸入锚固长度的情况进行计算的。
3、剪力墙:剪力墙中的构件一定要计算完全。
其中包括:墙体分布钢筋(有水平钢筋和纵向钢筋,要注意墙和墙交接部位的水平钢筋的锚固、各种转角锚固要求是不一样的)、翼柱的钢筋(墙和墙交接的部位形成的柱子)、剪力墙的连梁钢筋(门窗洞口上面形成的连梁)、暗柱钢筋(门窗洞口两侧形成的暗柱)、端柱钢筋(剪力墙端头的柱子)、暗梁钢筋(由于构造的要求在墙体中所配置的梁)。
焊接施工技术交底
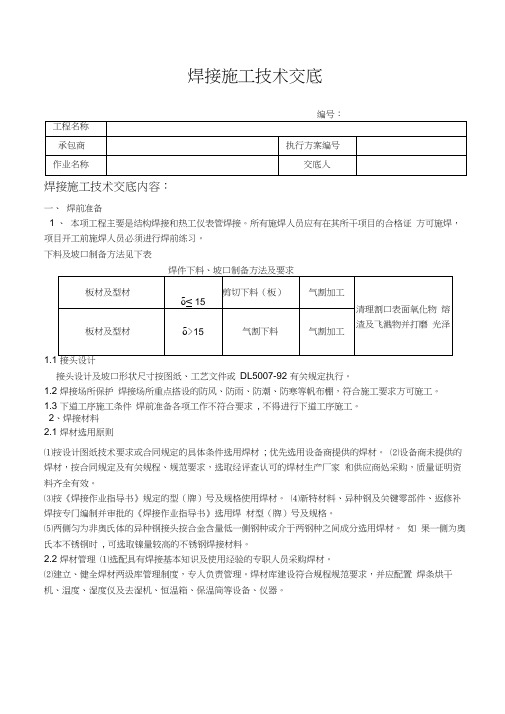
焊接施工技术交底编号:焊接施工技术交底内容:一、焊前准备1 、本项工程主要是结构焊接和热工仪表管焊接。
所有施焊人员应有在其所干项目的合格证方可施焊,项目开工前施焊人员必须进行焊前练习。
下料及坡口制备方法见下表焊件下料、坡口制备方法及要求接头设计及坡口形状尺寸按图纸、工艺文件或DL5007-92 有关规定执行。
1.2 焊接场所保护焊接场所重点搭设的防风、防雨、防潮、防寒等帆布棚,符合施工要求方可施工。
1.3 下道工序施工条件焊前准备各项工作不符合要求, 不得进行下道工序施工。
2、焊接材料2.1 焊材选用原则⑴按设计图纸技术要求或合同规定的具体条件选用焊材; 优先选用设备商提供的焊材。
⑵设备商未提供的焊材,按合同规定及有关规程、规范要求,选取经评查认可的焊材生产厂家和供应商处采购,质量证明资料齐全有效。
⑶按《焊接作业指导书》规定的型(牌)号及规格使用焊材。
⑷新特材料、异种钢及关键零部件、返修补焊按专门编制并审批的《焊接作业指导书》选用焊材型(牌)号及规格。
⑸两侧匀为非奥氏体的异种钢接头按合金含量低一侧钢种或介于两钢种之间成分选用焊材。
如果一侧为奥氏本不锈钢时, 可选取镍量较高的不锈钢焊接材料。
2.2 焊材管理⑴选配具有焊接基本知识及使用经验的专职人员采购焊材。
⑵建立、健全焊材两级库管理制度,专人负责管理。
焊材库建设符合规程规范要求,并应配置焊条烘干机、温度、湿度仪及去湿机、恒温箱、保温筒等设备、仪器。
3 施工方法和要求 序号作业程序 作业内容 及方法要求 1 施工焊工准备 焊机准备 焊工必须经考试合格并取得合格证书。
持证焊工必须在其 考试合格项目及其认可范围内施焊。
所准备焊机应性能良好, 须具备电压稳定、 电流调节灵活、绝缘性能良好、工作性能可靠等基本条件: (1)具有陡降的外特性;(2)具有良好的调节性;准备 焊材准备 (3)电流电压表指示正确。
焊接材料的品种、规格、性能等应符合现行国家产品标准 和设计要求。
钢筋焊接质量通病与防治措施
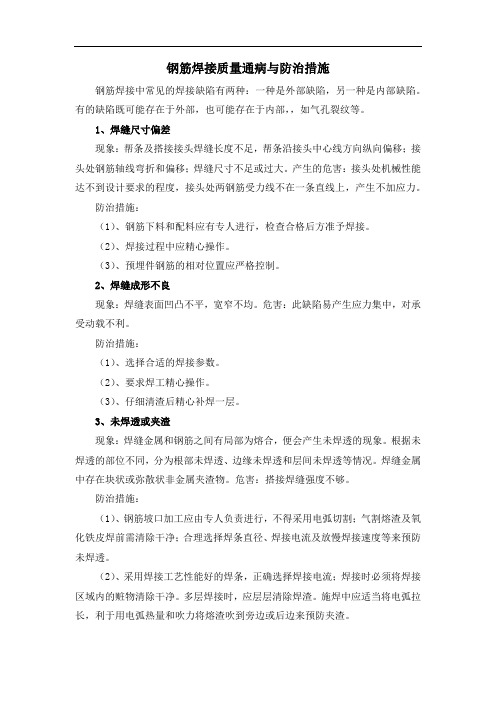
钢筋焊接质量通病与防治措施钢筋焊接中常见的焊接缺陷有两种:一种是外部缺陷,另一种是内部缺陷。
有的缺陷既可能存在于外部,也可能存在于内部,,如气孔裂纹等。
1、焊缝尺寸偏差现象:帮条及搭接接头焊缝长度不足,帮条沿接头中心线方向纵向偏移;接头处钢筋轴线弯折和偏移;焊缝尺寸不足或过大。
产生的危害:接头处机械性能达不到设计要求的程度,接头处两钢筋受力线不在一条直线上,产生不加应力。
防治措施:(1)、钢筋下料和配料应有专人进行,检查合格后方准予焊接。
(2)、焊接过程中应精心操作。
(3)、预埋件钢筋的相对位置应严格控制。
2、焊缝成形不良现象:焊缝表面凹凸不平,宽窄不均。
危害:此缺陷易产生应力集中,对承受动载不利。
防治措施:(1)、选择合适的焊接参数。
(2)、要求焊工精心操作。
(3)、仔细清渣后精心补焊一层。
3、未焊透或夹渣现象:焊缝金属和钢筋之间有局部为熔合,便会产生未焊透的现象。
根据未焊透的部位不同,分为根部未焊透、边缘未焊透和层间未焊透等情况。
焊缝金属中存在块状或弥散状非金属夹渣物。
危害:搭接焊缝强度不够。
防治措施:(1)、钢筋坡口加工应由专人负责进行,不得采用电弧切割;气割熔渣及氧化铁皮焊前需清除干净;合理选择焊条直径、焊接电流及放慢焊接速度等来预防未焊透。
(2)、采用焊接工艺性能好的焊条,正确选择焊接电流;焊接时必须将焊接区域内的赃物清除干净。
多层焊接时,应层层清除焊渣。
施焊中应适当将电弧拉长,利于用电弧热量和吹力将熔渣吹到旁边或后边来预防夹渣。
(3)、焊接过程中发现钢筋有赃物或焊接上有熔渣,焊接到该处应将电弧适当拉长,并稍作停留,使该处融化范围扩大,以便把赃物或熔渣再次融化吹走,直至形成清亮熔池为止。
(4)、未焊透应铲除重焊。
4、电弧烧伤钢筋表面现象:钢筋表面局部有缺肉或凹坑。
危害:对钢筋有严重的脆化作用,往往是发生脆性破坏的起点。
防治措施:(1)、精心操作(2)、不得在非焊接区域引燃电弧(3)、避免带点金属与钢筋相碰引起电弧。
塑钢门窗焊接工艺原则及工序质量标准

塑钢门窗焊接工艺原则及工序质量标准PVC塑钢门窗焊接的基本原则:热熔压力对缝焊接。
型材断面被加热板加热,呈熔融状态的部分在压力的作用下对接粘合,直至冷却,形成一体。
一、焊接工艺条件:1、加工环境温度不得低于18℃。
型材若在低于此温度时存放,在焊接前应将型材放在不低于15℃的室内放置24小时后再下料、焊接。
2、型材切割角度误差不得超过45°±15ˊ,90°±20ˊ,长度偏差不超过±0.5mm。
3、型材切口表面平整干净,无油污、汗渍、尘土、切屑等质杂污染。
4、焊接前型材分类清楚,按编号摆放整齐,避免造成混放、错焊结果。
5、焊接设备的电气部分和气动部分符合正常工作状态,焊布完整、光滑,无任何残留物与灰尘。
6、无论是两位焊、三位焊或四位焊,后靠板必须在一条直线上,前定位板与后靠板必须垂直,焊机底板也必须在同一平面上。
二、焊接工艺参数:由于焊接工艺参数与型材配方、型材可焊性、型材断面及环境温度有着直接的关系,所以不同厂家生产的型材有不同的焊接工艺参数,组装厂在拿到型材厂家推荐的焊接工艺参数作为参考的同时也要对该批型材进行调整和试验,直到找到最佳参数值。
中大型材焊接工艺参数如下:以三位焊为例(仅供参考)焊接工艺参数 框料、门扇 Z型扇 推拉框 中梃焊接 扇料、纱扇焊接温度 (℃) 250±5 250±5 250±5 250±5 250±5夹紧压力 前压钳 0.4~0.5 0.35~0.45 0.40~0.50 0.35~0.45 0.30~0.40 (MPa) 后压钳 0.35~0.45 0.3~0.4 0.35~0.45 0.3~0.4 0.25~0.30加热进给压力(MPa)0.20~0.30 0.20~0.30 0.20~0.30 0.20~0.30 0.20~0.30 加热时间 (s) 30±2 30±2 30±2 30±2 30±2焊接进给压力(MPa) ≥0.40 ≥0.40 ≥0.40 ≥0.35 ≥0.30焊接时间 (s) 28~30 28~30 28~30 28~30 26~28三、焊接技术要求:1、焊接尺寸要求:焊接型材每端设定的焊接余量为3mm,实际在焊接中焊接余量是根据焊机的三个工作间隙选取值来决定的。
压力管道施工方案

压力管道施工方案第一节施工工艺及流程根据本工程的特点,压力钢管段属于地下式埋管,首先进行压力钢管段和高压段洞室开挖,再进行高压段砼衬砌和灌浆,再进行压力管道的安装。
第二节压力钢管段土建施工压力钢管段施工主要包括:土石方明挖和石方洞挖。
1.土石方明挖土石方明挖严格按照施工图进行施工,施工中采取在现已开挖的厂区断面上进行开挖,开挖中采取至上而下的顺序,结合人工与预裂爆爆的施工方法进行土石方开挖,石方钻爆中采取手风钻进行钻爆作业,其钻头直径为φ40,挖掘机配合自卸车运输出渣,高边坡施工中,针对岩石稳定情况,可采取洞门喷锚施工工艺,限制边坡变形,以防产生危险。
2.石方洞挖当洞门形成后,石方洞挖主要施工方法与高压引水洞缓平段施工方法一致,这里不再敖述。
第三节压力钢道制作当洞挖施工开始后,我部准备开始对压力管道段进行制作,由于本标段压力管道钢材用量少,而且制作难度大,焊接工艺复杂,因此我部不准备建设压力钢管生产厂房,准备委托具有资质的厂家进行订作生产与安装,以节省成本和保证质量。
1.压力钢管委托生产要求压力钢管委托制作条件:我部准备在具有压力容器生产、制作、安装、焊接一级资的厂家中招标一家生产单位进行压力钢管的制作、安装、焊接工作。
并签订正式施工生产合同。
其委托厂家全方位履行钢管的制造、焊接、运输、安装、涂装、灌装及质量检验和验收等全部工作。
并且应指派持有上岗证的合格焊工和无损检测人员进行焊接、检验和评定工作。
2.压力钢管制作安装材料采购及质量控制钢管制作和安装所需的钢材、焊接材料、连接件和涂装材料的每一批材料到货后须经监理工程师验收签认后,方准使用。
2.1钢板(1)每批钢材入库验收时,应向监理工程师提交产品质量证明书,并接受监理工程师的检查,没有产品合格证件的钢材不得使用。
(2)所有钢板均由委托厂家质检部门负责进行抽样检验。
每批钢板抽样数量为2%,且不少于2张,同一牌号、同一质量等级、同一炉罐号、同一品种、同一尺寸、同一热处理制成的钢板可列为一批,检验成果报送监理工程师。
不锈钢管道焊接工艺标准
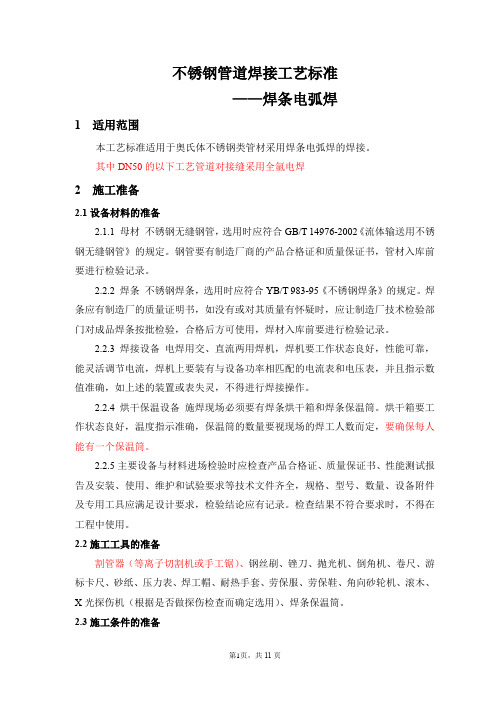
不锈钢管道焊接工艺标准——焊条电弧焊1适用范围本工艺标准适用于奥氏体不锈钢类管材采用焊条电弧焊的焊接。
其中DN50的以下工艺管道对接缝采用全氩电焊2施工准备2.1设备材料的准备2.1.1 母材不锈钢无缝钢管,选用时应符合GB/T 14976-2002《流体输送用不锈钢无缝钢管》的规定。
钢管要有制造厂商的产品合格证和质量保证书,管材入库前要进行检验记录。
2.2.2 焊条不锈钢焊条,选用时应符合YB/T 983-95《不锈钢焊条》的规定。
焊条应有制造厂的质量证明书,如没有或对其质量有怀疑时,应让制造厂技术检验部门对成品焊条按批检验,合格后方可使用,焊材入库前要进行检验记录。
2.2.3 焊接设备电焊用交、直流两用焊机,焊机要工作状态良好,性能可靠,能灵活调节电流,焊机上要装有与设备功率相匹配的电流表和电压表,并且指示数值准确,如上述的装置或表失灵,不得进行焊接操作。
2.2.4 烘干保温设备施焊现场必须要有焊条烘干箱和焊条保温筒。
烘干箱要工作状态良好,温度指示准确,保温筒的数量要视现场的焊工人数而定,要确保每人能有一个保温筒。
2.2.5主要设备与材料进场检验时应检查产品合格证、质量保证书、性能测试报告及安装、使用、维护和试验要求等技术文件齐全,规格、型号、数量、设备附件及专用工具应满足设计要求,检验结论应有记录。
检查结果不符合要求时,不得在工程中使用。
2.2施工工具的准备割管器(等离子切割机或手工锯)、钢丝刷、锉刀、抛光机、倒角机、卷尺、游标卡尺、砂纸、压力表、焊工帽、耐热手套、劳保服、劳保鞋、角向砂轮机、滚木、X光探伤机(根据是否做探伤检查而确定选用)、焊条保温筒。
2.3施工条件的准备2.3.1熟悉图纸和工艺要求,弄清焊缝位置和技术要求;在施焊之前,要有焊接工艺评定,并有根据焊接工艺评定报告编制的焊接作业指导书。
对于公司已使用过的不锈钢管,并已有焊接工艺评定报告,不需再做评定;如原有焊接工艺评定不能覆盖配管材料的必须重新进行焊接工艺评定,评定必须严格按照GB/T 50236-98或JB/T 4708-2000的规定。
- 1、下载文档前请自行甄别文档内容的完整性,平台不提供额外的编辑、内容补充、找答案等附加服务。
- 2、"仅部分预览"的文档,不可在线预览部分如存在完整性等问题,可反馈申请退款(可完整预览的文档不适用该条件!)。
- 3、如文档侵犯您的权益,请联系客服反馈,我们会尽快为您处理(人工客服工作时间:9:00-18:30)。
下料与焊接
一、对原材料的要求
(1)复检原材料的出厂证明和外观检查是否符合设计图纸要求。
(2)施工前处理:
(a)平整处理:可分为两次处理:下料前处理与下料后处理。
要求如下:
偏差名称允许偏差值(mm)
板材的局部弯曲矢量在1m范围内δ≤14;f≤1;
δ﹥14;f≤1.5 型材的扰曲矢量长度的1/1000但大于5mm 角钢的垂直度b≤100;△≤b/100
b﹥100;△≤b/100
槽钢、工字钢的翼缘倾斜度△≤b/100
(b)表面处理:酸洗或喷砂可根据工艺要求选定。
二、号料
(a)号料用的量具必须是校正验证过的,它不得有变形和损伤等现象。
(b)精度在1mm以内的必须用钢针划线,精度大于1mm的可以用粉笔画线。
三、下料手段
(1)板厚在1-12mm范围内,长度不大于200mm,宽度不小
于50mm时用剪刀下料。
(2)超过剪刀下料范围的板材均用机动切割。
(3)对于型材下料,必须用锯床。
高于1000mm以上的用机动切割。
(4)机械方法下料表面粗糙度Ra值不大于25um;剪刀下料后必须用砂轮去毛刺和锐角,其下料精度如下:
加工方法偏差名称允许偏差偏差值
冷锯零件长度允差△<±1
零件的偏移度 f<±0.3
剪刀错线与斜口+1
-0.5
刨边对检查线的尺寸±0.5
两边部平行度和不垂直度 1<1000 △<0.2 1<2000 △<0.3 1<4000 △<0.5 1<6000 △<0.7 (5)切割尺寸偏差不得超过0.5mm。
四、矫正
(1)零件矫正(组装前矫正)用冷矫正与热矫正均可,但热矫正温度不得超过720ºC。
(2)对组装后结构件,应进行机械方法矫正,不得用火焰应力矫正方法。
(3)在加热矫正方法中,不得有过烧的现象,压痕不得超过1mm,不得有部均匀的断面收缩,不能出现目视可辨的变形。
(4)矫正后的精度
成品结构件的精度要求如下:
分类测量部位允许偏差值mm 柱全长±3
每层接梁的上表面到柱脚的高度 0;-1
对柱脚的垂直度 1/2000
接梁与柱的中心线的倾斜度 1/5000但不大于5mm 梁全长±2
与柱头接合部的高度差±1
弯曲 1/1000,但不大于3mm 平台架非加工工作面水平度 1/5000
扭曲度(非加工面) 3
窜角度 2
漏斗法兰接口的不平度 1/1000
窜角度 2
漏斗中心线的倾斜度 1/5000
五、弯曲成型。
(1)热弯必须加热到900ºC以上,严禁在450ºC上、下弯曲成型。
(2)弯曲半径小于板厚1.5倍时,弯曲角度应小于120º,弯曲半径小于板厚2倍时,弯曲角度应小于90º,不得冷弯,必须热弯。
六、零件端部及沿边机械加工的要求。
(1)表面粗糙度为Ra值不大于25um。
(2)凡未注明尺寸公差的零件允差值按下表选用
(3)端部对轴线的垂直度小于1/2000.
(4)各边对基准线的角度误差小于1/1000(用角度样板尺)。
七、钻孔
(1)孔与零件表面垂直度允差小于1º.
(2)精制螺栓孔螺栓的直径应与螺栓公称直径相等,螺栓孔应具有H12的精度,其允许偏差应符合下表的规定。
精制螺栓孔径允许偏差表
(3)高强螺栓孔的直径应符合下表规定。
高强螺栓和高强螺栓孔的直径允许偏差表
(4)清除毛刺。
(5)在钻孔时必须划出检测线和五花冲眼。
八、装配焊接
(1)装配焊接前要检查零件的加工尺寸是否有焊缩量和修缩量,如发现没有不得组装焊接。
(2)尽量用胎具装配焊接,胎具根据工艺要求自行制作。
(3)有焊后加工的部件必须注意装配基准面,并作出标记。
(4)扎制H型钢必须符合国家标准规定。
(5)H型钢零件切头号线,必须按校正验过的钢尺并考虑加减尺寸,用钢质划线针划线,严禁用石笔或粉笔划线。
(6)厚板可用丙烷切割坡口,划坡口线时必须用样板,严禁用钢尺划线。
(7)异形零件用样板或数控切割下料。
(8)切割后的零件除清除毛刺,氧化渣外,须再进行矫正。
(9)对需要焊透的焊缝要进行射线照相检查(20%),GB/T3323-1987,等级:Ⅱ级。
(10)焊工必须经过培训,考试合格后,方可在施焊范围内上岗施焊。