复合材料泡沫夹层结构在汽车外饰中的应用和发展
玻璃钢复合材料船舶夹层结构中的泡沫芯材

结构泡沫芯材的历史回顾(复材在线原创文章)玻璃钢/复合材料(FRP/CM)中常用的泡沫芯材有聚氯乙烯(PVC)、聚苯乙烯(PS)、聚氨酯(PUR)、丙烯腈-苯乙烯(SAN)、聚醚酰亚胺(PEI)及聚甲基丙烯酰亚胺(PMI)等泡沫,其中PS和PUR泡沫通常仅作为浮力材料,而不是结构用途。
目前PVC 泡沫已几乎完全代替PUR泡沫而作为结构芯材,只是在一些现场发泡的结构中除外。
严格意义上讲,第一种用在承载构件夹层结构中的结构泡沫芯材是使用异氰酸酯改性的PVC泡沫,或称交联PVC。
第一个采用PVC泡沫夹芯的夹层结构是保温隔热车厢。
交联PVC的生产工艺是由德国人林德曼在上世纪30年代后期发明的。
二次大战以后法国将该工艺列入战争赔偿中,由克勒贝尔蕾洛雷特塑料公司(Kleber Renolit)开始生产Klegecell®交联PVC泡沫,主要是一些用在保温隔热车厢中的低密度产品。
上世纪50-60年代,克勒贝尔蕾洛雷特塑料公司给几家欧洲公司发放了PVC泡沫的生产许可证。
另外两家美国公司,B.F歌德雷奇(B.F Goodrich)和佳士迈威(Johns-Manville)也买到了许可证开始生产,但是几年以后就停产。
当所有的生产许可证都过期以后,交联PVC的生产工艺过程转为公开。
进入70年代以后,多数原来的欧洲许可生产厂家也已停产。
目前两个主要的生产厂家是戴博(Diab)公司的Divinycell®和Klegecell®系列PVC泡沫及爱瑞柯斯(Airex)公司的Herex®系列PVC泡沫。
20世纪40年代后期,林德曼使用高压气体作为发泡剂,制造出未经过改性的PVC泡沫,也叫线性PVC泡沫。
英国于1943年首先制成聚苯乙烯泡沫塑料,1944年美国道化学有限公司用挤出法大批量的生产聚苯乙烯泡沫塑料。
第二次世界大战期间,德国拜尔的试验人员对二异氰酸酯及羟基化合物的反应进行研究,制得了PUR硬质泡沫塑料、涂料和粘合剂。
夹层结构复合材料设计原理及其应用
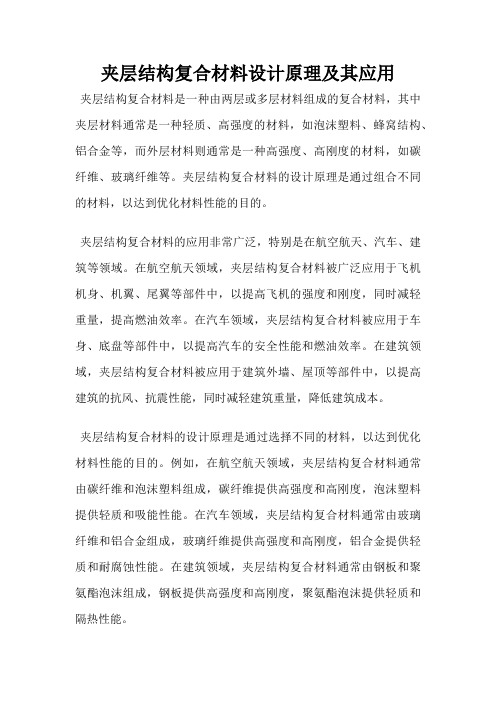
夹层结构复合材料设计原理及其应用
夹层结构复合材料是一种由两层或多层材料组成的复合材料,其中夹层材料通常是一种轻质、高强度的材料,如泡沫塑料、蜂窝结构、铝合金等,而外层材料则通常是一种高强度、高刚度的材料,如碳纤维、玻璃纤维等。
夹层结构复合材料的设计原理是通过组合不同的材料,以达到优化材料性能的目的。
夹层结构复合材料的应用非常广泛,特别是在航空航天、汽车、建筑等领域。
在航空航天领域,夹层结构复合材料被广泛应用于飞机机身、机翼、尾翼等部件中,以提高飞机的强度和刚度,同时减轻重量,提高燃油效率。
在汽车领域,夹层结构复合材料被应用于车身、底盘等部件中,以提高汽车的安全性能和燃油效率。
在建筑领域,夹层结构复合材料被应用于建筑外墙、屋顶等部件中,以提高建筑的抗风、抗震性能,同时减轻建筑重量,降低建筑成本。
夹层结构复合材料的设计原理是通过选择不同的材料,以达到优化材料性能的目的。
例如,在航空航天领域,夹层结构复合材料通常由碳纤维和泡沫塑料组成,碳纤维提供高强度和高刚度,泡沫塑料提供轻质和吸能性能。
在汽车领域,夹层结构复合材料通常由玻璃纤维和铝合金组成,玻璃纤维提供高强度和高刚度,铝合金提供轻质和耐腐蚀性能。
在建筑领域,夹层结构复合材料通常由钢板和聚氨酯泡沫组成,钢板提供高强度和高刚度,聚氨酯泡沫提供轻质和隔热性能。
夹层结构复合材料是一种非常重要的材料,它具有轻质、高强度、高刚度、吸能性能等优点,被广泛应用于航空航天、汽车、建筑等领域。
夹层结构复合材料的设计原理是通过选择不同的材料,以达到优化材料性能的目的。
未来,随着科技的不断发展,夹层结构复合材料将会得到更广泛的应用。
复合材料夹层结构

②叠合与压 制工序
在芳纶纸上涂印好规则均匀的胶条后,将连续的芳 纶纸裁切成一定长度,按一定规则进行叠合:即上一张 纸的胶条于下一张纸的胶条正中间。
叠合的定位方式可采取对胶条或打孔定位法。对胶 条法主要依靠操作人员的肉眼观察,主观性较大,容易 造成胶条偏斜。而打孔定位法采用机器打孔,消除了主 观误差,定位准确,因此在实际生产中打孔定位法被普 通采用。
具体工艺流程如下:
34
35
展开法制造蜂窝夹芯的工艺流程
玻璃布 胶液
涂胶条(印胶或漏胶)
叠合
压制固化
切割
拉伸
浸胶
Hale Waihona Puke 凉置固化成型 蜂窝夹芯36
① 涂胶与叠合
在玻璃布上涂胶条,常采用机械涂胶法即在涂 胶机上进行,也可用手工涂胶法涂胶。
37
手工涂胶法
a. 制作涂胶板。在塑料薄膜上,用刻纸刀刻出涂胶条。 胶条的宽度和间距根据蜂窝格子的边长确定,具体宽 度根据玻璃布的厚度、密度、粘接剂的粘度等具体条 件确定。
面-芯粘结不需要其它胶粘剂
主要几 何参数
Z-pin植入角度 植入密度
Z-pin细度
10
Z-pin夹层结构
植入工艺
Z-pin植 入工艺
缝 合 工 艺
11
Z-pin夹层结构
应用领域
12
Z-pin夹层结构
13
连体织物及复合材料
面层
纤维 芯柱
面层
三维间隔连体织物是一种层与 层之间由连续纤维芯柱相接而 成一体呈空芯结构的编织物
53
⑤蜂窝的拼接
制造大面积或异形制品时,蜂窝的尺寸往往不能满 足要求,因此需要拼接。拼接时取少量胶液,涂在拼接 处,搭接长度为六角形边长,用夹子固定,待固化后除 去夹子即可。也可通过填充泡沫胶的方式拼接。
复合夹层结构材料在厢式汽车上的应用

对 于 厢 式 汽车 厢 体 上 所 用 到 的 夹 层 结 构 来说 ,
动态疲 劳 强度 高 , 艺 性 能 好 并 具 有 良好 的 性 能 价 工
格 比是 其 基 本 要 求 。 复 合 夹 层 结 构 具 有 加 工 能 耗 低 、 质 高 强 、 计 自 由度 大 、 锈 蚀 、 型 工 艺 性 轻 设 不 成 好 、 用 寿命 长 等优 点 , 使 因此 是厢 式 汽 车厢 体 制造 以 塑代 钢 的理 想加 工材 料 。 3 1 泡 沫塑 料 夹层 结 构在 厢 式 汽车 厢 体 上 的应 用 . 为满 足 冷藏 保 温厢 式 车 隔 热 、 温 的 目的 , 种 保 这 厢 体 在制 造 中大 多 采用 泡 沫 塑料 夹 层 结构 。这种 结
隔音 、 微 波 、 透 防撞 、 防弹 等 多种 目的 。
3 夹 层 结构 在 厢 式汽 车厢 体 上 的应 用
夹 层结 构 一 般 是 由三 层 或三 层 以上 的材 料 或 结 构制 成 的 复合 结 构材 料 。夹 层复 合材 料 的上 下 面层 是高强 度 、 弹 性 模 量 的 薄 板 材 料 , 为 蒙 皮 或 面 高 称 板; 中间夹 着 一 层 较 厚 的轻 质 材 料 。复 合 夹 层 结 构 是 复合 材料 与 其 它 轻质 材 料 的再 复合 。蒙 皮 通 常 采 用 金属 ( 锈 钢 、 ) 、 R 不 铝 板 F P薄板 、 料 板 等 , 材 可 塑 芯
生产 中。 2 夹 层结 构 的设 计 原 理 2 1 夹 层 结构 的基本 概 念 .
起并 承 受剪 切 力 。在 夹 层 结 构 设 计 中 , 根 据 应 应 用要 求 , 虑夹 层结 构 的力 学 性 及功 能 性 , 考有 关 考 参 的复 合材 料 手册 , 择 不 同夹 芯 、 板 , 达 到保 温 、 选 面 能
复合材料在汽车行业的应用研究
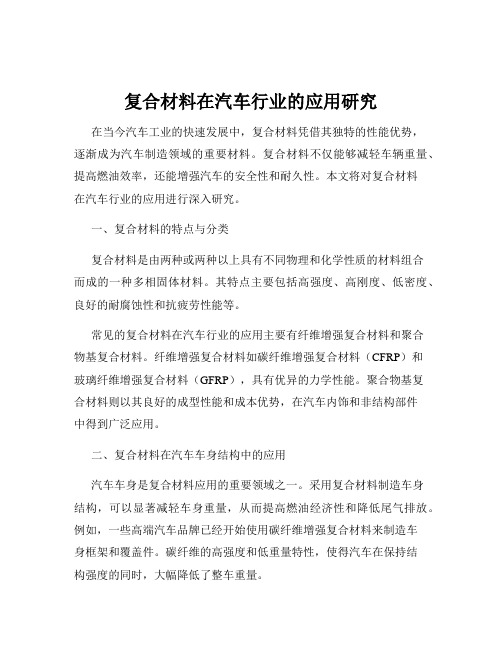
复合材料在汽车行业的应用研究在当今汽车工业的快速发展中,复合材料凭借其独特的性能优势,逐渐成为汽车制造领域的重要材料。
复合材料不仅能够减轻车辆重量、提高燃油效率,还能增强汽车的安全性和耐久性。
本文将对复合材料在汽车行业的应用进行深入研究。
一、复合材料的特点与分类复合材料是由两种或两种以上具有不同物理和化学性质的材料组合而成的一种多相固体材料。
其特点主要包括高强度、高刚度、低密度、良好的耐腐蚀性和抗疲劳性能等。
常见的复合材料在汽车行业的应用主要有纤维增强复合材料和聚合物基复合材料。
纤维增强复合材料如碳纤维增强复合材料(CFRP)和玻璃纤维增强复合材料(GFRP),具有优异的力学性能。
聚合物基复合材料则以其良好的成型性能和成本优势,在汽车内饰和非结构部件中得到广泛应用。
二、复合材料在汽车车身结构中的应用汽车车身是复合材料应用的重要领域之一。
采用复合材料制造车身结构,可以显著减轻车身重量,从而提高燃油经济性和降低尾气排放。
例如,一些高端汽车品牌已经开始使用碳纤维增强复合材料来制造车身框架和覆盖件。
碳纤维的高强度和低重量特性,使得汽车在保持结构强度的同时,大幅降低了整车重量。
此外,玻璃纤维增强复合材料也常用于车身部件的制造,如保险杠、车门和引擎盖等。
这些部件在碰撞时能够吸收能量,提高汽车的被动安全性。
三、复合材料在汽车动力系统中的应用在汽车动力系统中,复合材料也发挥着重要作用。
例如,复合材料可以用于制造发动机缸体、缸盖和曲轴等部件。
这些部件需要具备高强度、耐高温和良好的耐磨性,而复合材料的性能能够满足这些要求。
同时,复合材料还可以用于制造涡轮增压器叶片和排气管等部件。
由于其良好的耐热性和耐腐蚀性,能够延长部件的使用寿命,提高动力系统的可靠性。
四、复合材料在汽车内饰中的应用汽车内饰对于舒适性和美观性有着较高的要求,复合材料在这方面也有着出色的表现。
聚合物基复合材料可以制成各种形状和颜色的内饰部件,如仪表板、座椅靠背和中控台等。
夹层结构复合材料的应用
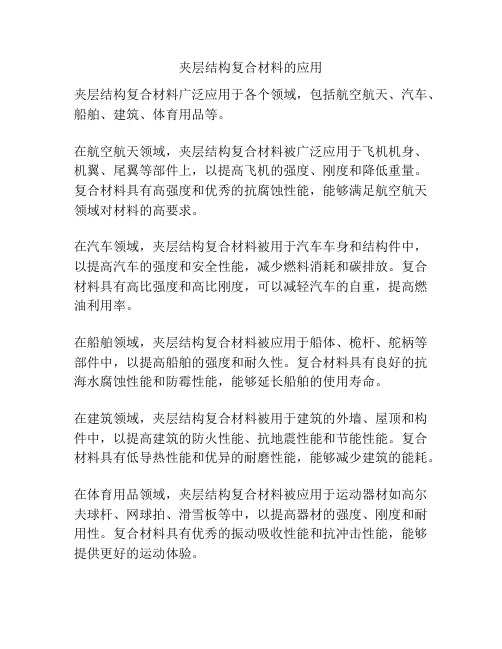
夹层结构复合材料的应用
夹层结构复合材料广泛应用于各个领域,包括航空航天、汽车、船舶、建筑、体育用品等。
在航空航天领域,夹层结构复合材料被广泛应用于飞机机身、机翼、尾翼等部件上,以提高飞机的强度、刚度和降低重量。
复合材料具有高强度和优秀的抗腐蚀性能,能够满足航空航天领域对材料的高要求。
在汽车领域,夹层结构复合材料被用于汽车车身和结构件中,以提高汽车的强度和安全性能,减少燃料消耗和碳排放。
复合材料具有高比强度和高比刚度,可以减轻汽车的自重,提高燃油利用率。
在船舶领域,夹层结构复合材料被应用于船体、桅杆、舵柄等部件中,以提高船舶的强度和耐久性。
复合材料具有良好的抗海水腐蚀性能和防霉性能,能够延长船舶的使用寿命。
在建筑领域,夹层结构复合材料被用于建筑的外墙、屋顶和构件中,以提高建筑的防火性能、抗地震性能和节能性能。
复合材料具有低导热性能和优异的耐磨性能,能够减少建筑的能耗。
在体育用品领域,夹层结构复合材料被应用于运动器材如高尔夫球杆、网球拍、滑雪板等中,以提高器材的强度、刚度和耐用性。
复合材料具有优秀的振动吸收性能和抗冲击性能,能够提供更好的运动体验。
总体而言,夹层结构复合材料在各个领域中都有广泛应用,通过其独特的性能和优势,为各行业带来了许多创新和发展机会。
复合材料夹层结构
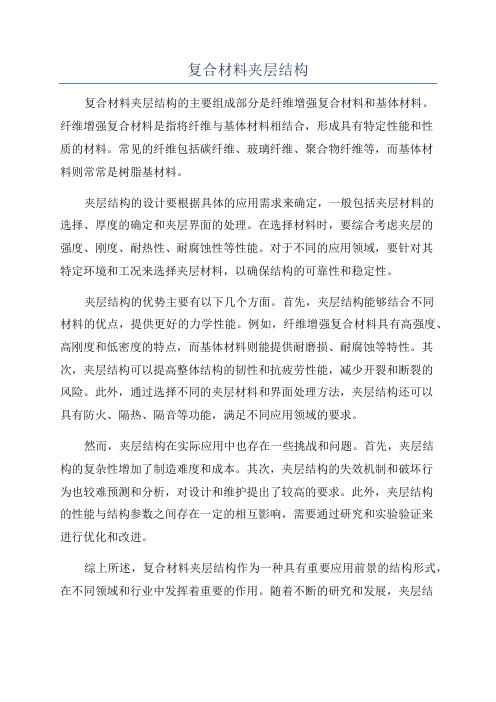
复合材料夹层结构复合材料夹层结构的主要组成部分是纤维增强复合材料和基体材料。
纤维增强复合材料是指将纤维与基体材料相结合,形成具有特定性能和性质的材料。
常见的纤维包括碳纤维、玻璃纤维、聚合物纤维等,而基体材料则常常是树脂基材料。
夹层结构的设计要根据具体的应用需求来确定,一般包括夹层材料的选择、厚度的确定和夹层界面的处理。
在选择材料时,要综合考虑夹层的强度、刚度、耐热性、耐腐蚀性等性能。
对于不同的应用领域,要针对其特定环境和工况来选择夹层材料,以确保结构的可靠性和稳定性。
夹层结构的优势主要有以下几个方面。
首先,夹层结构能够结合不同材料的优点,提供更好的力学性能。
例如,纤维增强复合材料具有高强度、高刚度和低密度的特点,而基体材料则能提供耐磨损、耐腐蚀等特性。
其次,夹层结构可以提高整体结构的韧性和抗疲劳性能,减少开裂和断裂的风险。
此外,通过选择不同的夹层材料和界面处理方法,夹层结构还可以具有防火、隔热、隔音等功能,满足不同应用领域的要求。
然而,夹层结构在实际应用中也存在一些挑战和问题。
首先,夹层结构的复杂性增加了制造难度和成本。
其次,夹层结构的失效机制和破坏行为也较难预测和分析,对设计和维护提出了较高的要求。
此外,夹层结构的性能与结构参数之间存在一定的相互影响,需要通过研究和实验验证来进行优化和改进。
综上所述,复合材料夹层结构作为一种具有重要应用前景的结构形式,在不同领域和行业中发挥着重要的作用。
随着不断的研究和发展,夹层结构的性能和可靠性将会得到进一步提升,为实现更高效、更可靠的结构设计和应用提供了新的可能性。
高分子复合材料的应用场景

高分子复合材料的应用场景随着科技的不断进步,高分子复合材料在各个领域得到了广泛的应用。
它具有轻质、高强度、耐腐蚀等优点,使得它成为了替代传统材料的理想选择。
下面将以人类的视角,介绍高分子复合材料在不同领域的应用场景。
1. 轻量化汽车制造高分子复合材料在汽车制造领域得到了广泛应用。
与传统金属材料相比,高分子复合材料具有更轻的重量和更高的强度,能够减轻汽车的整体重量。
这不仅能够提升汽车的燃油效率,减少尾气排放,还能提高汽车的安全性能。
高分子复合材料在汽车车身、车门、座椅等部件上的应用,使得汽车更加节能环保,同时保证了车辆的舒适性和安全性。
2. 航空航天领域航空航天领域对材料的要求非常高,高分子复合材料凭借其良好的物理性能和化学性能,在航空航天领域得到了广泛的应用。
例如,高分子复合材料可以用于制造飞机机身、翼面、螺旋桨等部件,能够大幅度减轻飞机的重量,提高燃油效率,同时还能提高飞机的强度和耐久性。
此外,高分子复合材料还可以用于制造航天器的外壳和热防护材料,能够承受极端的温度和压力,保护航天器的安全。
3. 建筑领域高分子复合材料在建筑领域的应用也越来越广泛。
在地震频发的地区,高分子复合材料可以用于制造抗震支撑结构,提高建筑物的抗震能力。
此外,高分子复合材料还可以用于制造外墙保温材料,能够有效隔热保温,提高建筑物的能源利用效率。
高分子复合材料还可以用于制造建筑物的屋顶、地板等部件,具有轻质、强度高的特点,提高了建筑物的整体质量。
4. 医疗器械领域高分子复合材料在医疗器械领域的应用也非常广泛。
例如,高分子复合材料可以用于制造人工关节、骨修复材料等,具有良好的生物相容性和机械性能,能够有效替代传统的金属材料。
高分子复合材料还可以用于制造医用导管、缝线等,具有良好的柔韧性和耐腐蚀性,能够提高手术的安全性和舒适性。
高分子复合材料在汽车制造、航空航天、建筑和医疗器械等领域都有广泛的应用。
它的轻质、高强度、耐腐蚀等优点使得它成为了替代传统材料的理想选择。
PMI高性能泡沫夹层材料的应用及国内研制现状

:
共聚反应技术
成核和发泡技术
泡沫组成和结构控制技术
PMI泡沫强度增强技术
PMI泡沫制备的关键设备
PMI泡沫关键工艺控制技术
PMI泡沫制备的基本配方如表
1所示。PMI泡沫制备的工艺流程如图
5所示。
和复合材料的最轻量化制备提供技术支持。
The
research
and
application
of
PMI
foam
in
china
Chen
Yimin1,He
Bin2
(
1.
College
of
Aerospace
and
Material
省塑料研究所研制的性能达到了国外同类产品的水平,完全能满足航空航天等各领域应用的要求。
同时,可根据用户要求量身定制,在密度从
32~300
kg/m
3的范围内,制备各种密度
(如从国外买不
到的
90
kg/m3或
110~200kg/m
3
)的
PMI泡沫,为
PMI泡沫夹层结构复合材料结构和性能最优化设计
6研制的
PMI泡沫的光学照片
同时,采用在共聚过程中加入无机纳米增强技术来提高
PMI泡沫的性能,并取得了良好的提高
PMI
泡沫强度的效果。PMI泡沫力学性能测试结果表明,所研制的
PMI泡沫的性能指标与国外类似产品的
性能基本一致,表
2为研制的
PMI泡沫部分力学强度数据及与
复合材料在建筑结构中的应用分析
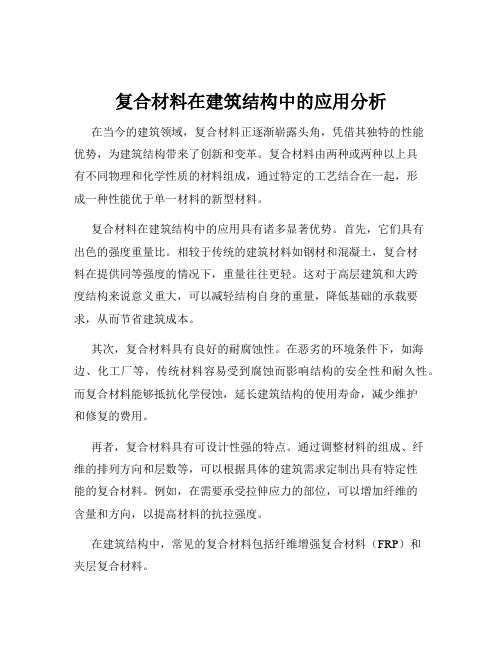
复合材料在建筑结构中的应用分析在当今的建筑领域,复合材料正逐渐崭露头角,凭借其独特的性能优势,为建筑结构带来了创新和变革。
复合材料由两种或两种以上具有不同物理和化学性质的材料组成,通过特定的工艺结合在一起,形成一种性能优于单一材料的新型材料。
复合材料在建筑结构中的应用具有诸多显著优势。
首先,它们具有出色的强度重量比。
相较于传统的建筑材料如钢材和混凝土,复合材料在提供同等强度的情况下,重量往往更轻。
这对于高层建筑和大跨度结构来说意义重大,可以减轻结构自身的重量,降低基础的承载要求,从而节省建筑成本。
其次,复合材料具有良好的耐腐蚀性。
在恶劣的环境条件下,如海边、化工厂等,传统材料容易受到腐蚀而影响结构的安全性和耐久性。
而复合材料能够抵抗化学侵蚀,延长建筑结构的使用寿命,减少维护和修复的费用。
再者,复合材料具有可设计性强的特点。
通过调整材料的组成、纤维的排列方向和层数等,可以根据具体的建筑需求定制出具有特定性能的复合材料。
例如,在需要承受拉伸应力的部位,可以增加纤维的含量和方向,以提高材料的抗拉强度。
在建筑结构中,常见的复合材料包括纤维增强复合材料(FRP)和夹层复合材料。
纤维增强复合材料(FRP)主要由纤维和树脂基体组成。
纤维通常采用玻璃纤维、碳纤维或芳纶纤维等,而树脂基体则有聚酯树脂、环氧树脂等。
FRP 具有高强度、高模量和轻质的特点,被广泛应用于建筑结构的加固和新建项目中。
在加固方面,FRP 可以用于加固混凝土柱、梁和板等构件。
通过在构件表面粘贴 FRP 片材或布材,可以显著提高构件的承载能力和抗震性能。
例如,对于受损的混凝土柱,可以在其四周包裹碳纤维布,增加柱的抗压能力和延性。
在新建项目中,FRP 也有出色的表现。
比如,FRP 筋可以替代传统的钢筋用于混凝土结构中。
FRP 筋具有非磁性、耐腐蚀性强等优点,适用于特殊环境下的建筑,如磁共振成像室、海洋平台等。
此外,FRP 还可以用于制造桥梁的箱梁、拉索等部件,提高桥梁的跨越能力和耐久性。
简析复合材料在汽车轻量化设计中的应用
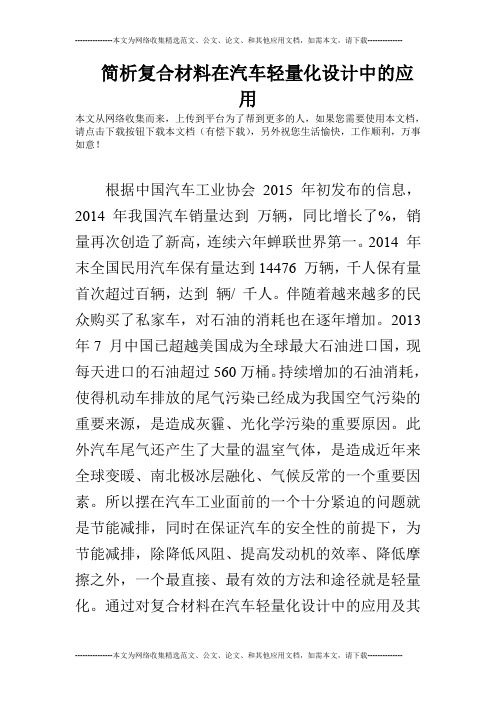
简析复合材料在汽车轻量化设计中的应用本文从网络收集而来,上传到平台为了帮到更多的人,如果您需要使用本文档,请点击下载按钮下载本文档(有偿下载),另外祝您生活愉快,工作顺利,万事如意!根据中国汽车工业协会2015 年初发布的信息,2014 年我国汽车销量达到万辆,同比增长了%,销量再次创造了新高,连续六年蝉联世界第一。
2014 年末全国民用汽车保有量达到14476 万辆,千人保有量首次超过百辆,达到辆/ 千人。
伴随着越来越多的民众购买了私家车,对石油的消耗也在逐年增加。
2013 年7 月中国已超越美国成为全球最大石油进口国,现每天进口的石油超过560万桶。
持续增加的石油消耗,使得机动车排放的尾气污染已经成为我国空气污染的重要来源,是造成灰霾、光化学污染的重要原因。
此外汽车尾气还产生了大量的温室气体,是造成近年来全球变暖、南北极冰层融化、气候反常的一个重要因素。
所以摆在汽车工业面前的一个十分紧迫的问题就是节能减排,同时在保证汽车的安全性的前提下,为节能减排,除降低风阻、提高发动机的效率、降低摩擦之外,一个最直接、最有效的方法和途径就是轻量化。
通过对复合材料在汽车轻量化设计中的应用及其成型工艺的介绍,更加清楚的了解到各成型工艺生产的复合材料所具有的性能及该生产方式的适用范围。
1 汽车轻量化的途径与意义一辆轿车每减重100kg,每百公里燃油消耗就平均减少,二氧化碳排放也随之减少12g/km。
如果采用新材料替代来做到这一点,相当于大约采用1kg的铝替代2kg 的钢,不过为了达到减重的目的须要进行结构的优化设计。
材料科学的进步推动了汽车轻量化技术的不断发展,并由此诞生了全新的汽车轻量化设计。
汽车轻量化的主要途径有:(1)汽车主流规格车型持续优化,规格主参数尺寸保留的前提下,提升整车结构强度、降低耗材用量;(2)采用轻质材料。
如铝、镁、陶瓷、玻璃纤维或碳纤维复合材料等;(3)采用计算机进行结构设计。
如采用有限元分析优化设计、局部加强设计等;(4)采用承载式车身,减薄车身板料厚度等。
聚氨酯发泡技术汽车应用发展趋势探讨

聚氨酯发泡技术汽车应用发展趋势探讨聚氨酯发泡技术是一种应用广泛的新型材料技术,它主要是利用多元醇和异氰酸酯等原料进行反应发泡而成,具有轻质、耐磨、绝缘、密封、吸音、防水、隔热等优良性能。
在汽车制造行业中,聚氨酯发泡技术得到了广泛的应用,并且在不断地发展和完善之中。
本文将就聚氨酯发泡技术在汽车应用中的发展趋势进行探讨。
一、聚氨酯发泡技术在汽车制造中的应用聚氨酯发泡技术在汽车制造中的应用非常广泛,主要包括以下几个方面:1.汽车座椅:聚氨酯发泡材料经过成型加工后,可以制成汽车座椅的坐垫和靠背,具有良好的弹性和舒适性。
2.内饰件:聚氨酯发泡材料还可以用于汽车的内饰件,如门板、仪表盘、中控台等,不仅外观美观,而且具有一定的吸音和隔热效果。
3.车身部件:聚氨酯发泡材料还可以用于汽车的车身部件,如保险杠、车门、尾翼等,具有良好的抗撞击性能和耐磨性。
4.隔音隔热材料:聚氨酯发泡材料还可以用于汽车的隔音隔热材料,如发动机舱隔音棉、隔热毡等,有效降低了车辆的噪音和振动。
二、聚氨酯发泡技术在汽车应用中的发展趋势1.环保性能的提升:随着人们对环境友好型汽车的需求日益增加,未来聚氨酯发泡技术在汽车制造中的应用将更加注重环保性能的提升,包括原材料的绿色化、生产工艺的减排等方面。
2.轻量化材料的需求:随着汽车制造业对车辆整体质量的要求越来越高,未来聚氨酯发泡技术将更加注重轻量化材料的研发和应用,以满足汽车制造业的需求。
3.智能化技术的融合:未来聚氨酯发泡技术在汽车应用中将更加注重智能化技术的融合,如智能汽车座椅、智能内饰件等,以提升汽车的舒适性和安全性。
4.功能性材料的发展:随着汽车功能的不断增多,未来聚氨酯发泡技术在汽车应用中将更加注重功能性材料的发展,如具有自愈合功能、具有智能感知功能等。
三、聚氨酯发泡技术在汽车应用中的挑战与机遇1.挑战:目前,聚氨酯发泡技术在汽车应用中仍面临一些挑战,如成本较高、技术壁垒较大等。
2.机遇:但是随着汽车行业的快速发展,聚氨酯发泡技术在汽车应用中也面临着巨大的发展机遇,如市场需求的不断增加、技术创新的不断推进等。
复合材料在汽车的应用
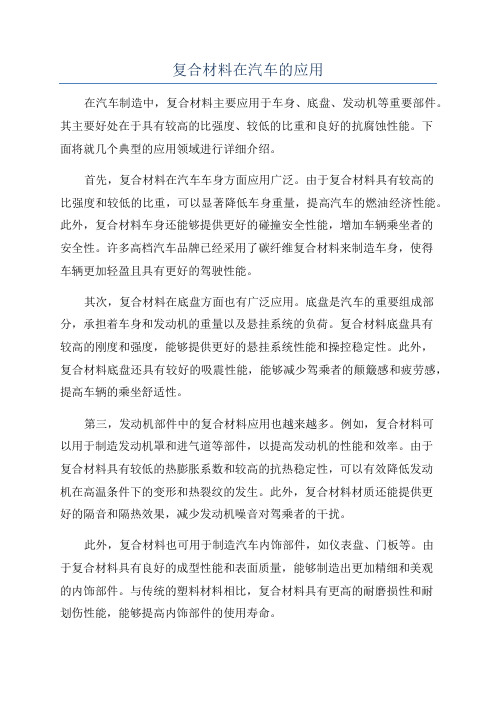
复合材料在汽车的应用在汽车制造中,复合材料主要应用于车身、底盘、发动机等重要部件。
其主要好处在于具有较高的比强度、较低的比重和良好的抗腐蚀性能。
下面将就几个典型的应用领域进行详细介绍。
首先,复合材料在汽车车身方面应用广泛。
由于复合材料具有较高的比强度和较低的比重,可以显著降低车身重量,提高汽车的燃油经济性能。
此外,复合材料车身还能够提供更好的碰撞安全性能,增加车辆乘坐者的安全性。
许多高档汽车品牌已经采用了碳纤维复合材料来制造车身,使得车辆更加轻盈且具有更好的驾驶性能。
其次,复合材料在底盘方面也有广泛应用。
底盘是汽车的重要组成部分,承担着车身和发动机的重量以及悬挂系统的负荷。
复合材料底盘具有较高的刚度和强度,能够提供更好的悬挂系统性能和操控稳定性。
此外,复合材料底盘还具有较好的吸震性能,能够减少驾乘者的颠簸感和疲劳感,提高车辆的乘坐舒适性。
第三,发动机部件中的复合材料应用也越来越多。
例如,复合材料可以用于制造发动机罩和进气道等部件,以提高发动机的性能和效率。
由于复合材料具有较低的热膨胀系数和较高的抗热稳定性,可以有效降低发动机在高温条件下的变形和热裂纹的发生。
此外,复合材料材质还能提供更好的隔音和隔热效果,减少发动机噪音对驾乘者的干扰。
此外,复合材料也可用于制造汽车内饰部件,如仪表盘、门板等。
由于复合材料具有良好的成型性能和表面质量,能够制造出更加精细和美观的内饰部件。
与传统的塑料材料相比,复合材料具有更高的耐磨损性和耐划伤性能,能够提高内饰部件的使用寿命。
综上所述,复合材料在汽车制造中有着广泛的应用,能够显著改善汽车的性能和重量。
随着技术的不断进步,相信复合材料在汽车制造中的应用将会更加广泛,为我们带来更安全、更环保和更高性能的汽车。
复合材料夹层结构分析
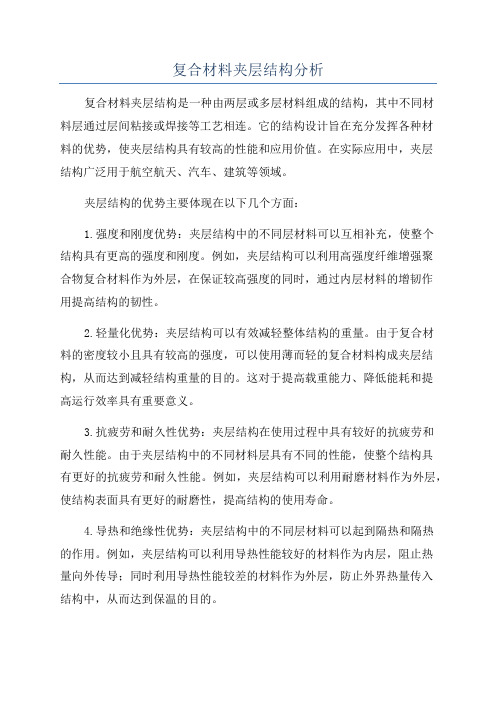
复合材料夹层结构分析复合材料夹层结构是一种由两层或多层材料组成的结构,其中不同材料层通过层间粘接或焊接等工艺相连。
它的结构设计旨在充分发挥各种材料的优势,使夹层结构具有较高的性能和应用价值。
在实际应用中,夹层结构广泛用于航空航天、汽车、建筑等领域。
夹层结构的优势主要体现在以下几个方面:1.强度和刚度优势:夹层结构中的不同层材料可以互相补充,使整个结构具有更高的强度和刚度。
例如,夹层结构可以利用高强度纤维增强聚合物复合材料作为外层,在保证较高强度的同时,通过内层材料的增韧作用提高结构的韧性。
2.轻量化优势:夹层结构可以有效减轻整体结构的重量。
由于复合材料的密度较小且具有较高的强度,可以使用薄而轻的复合材料构成夹层结构,从而达到减轻结构重量的目的。
这对于提高载重能力、降低能耗和提高运行效率具有重要意义。
3.抗疲劳和耐久性优势:夹层结构在使用过程中具有较好的抗疲劳和耐久性能。
由于夹层结构中的不同材料层具有不同的性能,使整个结构具有更好的抗疲劳和耐久性能。
例如,夹层结构可以利用耐磨材料作为外层,使结构表面具有更好的耐磨性,提高结构的使用寿命。
4.导热和绝缘性优势:夹层结构中的不同层材料可以起到隔热和隔热的作用。
例如,夹层结构可以利用导热性能较好的材料作为内层,阻止热量向外传导;同时利用导热性能较差的材料作为外层,防止外界热量传入结构中,从而达到保温的目的。
5.吸音和隔音优势:夹层结构中的不同层材料可以起到吸音和隔音的作用。
例如,在建筑领域中,夹层结构可以利用吸音性能较好的材料作为内层,增加结构对声音的吸收;同时利用密度较大的材料作为外层,阻止声音的传播,提高结构的隔音效果。
然而,夹层结构也存在一些挑战和问题。
首先,夹层结构的设计和制造要求较高,需要考虑不同材料层之间的界面粘接强度、尺寸匹配等问题;其次,夹层结构在使用过程中可能存在层间剥离、破裂等问题,需要进行结构损伤评估和修复;最后,夹层结构的成本较高,需要考虑材料选择、制造工艺等问题,以提高经济性。
HDPE泡沫复合材料在汽车上的应用
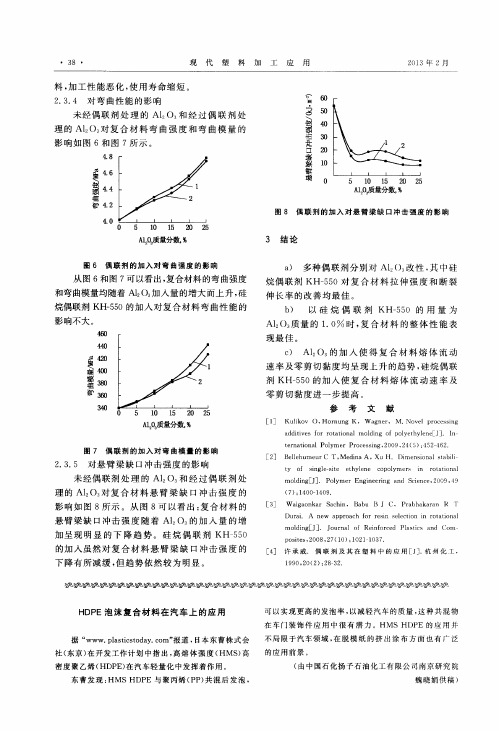
E 3 ] Wa i g a o n k a r S a c h i n ,B a b u B J C, P r a b h a k a r a n R I 、
t y o f s i n g l e — s i t e e t h y l e ne c op o l y me r s i n r o t a t i o n a l
2 . 3 . 5 对 悬臂 梁缺 口冲击 强度 的影 响 未经偶 联剂 处 理 的 A1 。 O。 和 经过 偶 联 剂 处
b ) 以 硅 烷 偶 联 剂 KH一 5 5 0 的 用 量 为
从图 6 和图 7 可 以看出 , 复合材料 的弯 曲强度 和弯曲模量均随着
一 . \
o 。 加入量 的增大而上升 , 硅
佰是 口塔 哟
烷偶联剂 KH - 5 5 0的加入对 复合 材料弯 曲性 能 的
影 响不大 。
速率 及零 剪切黏 度均 呈现上 升 的趋 势 , 硅 烷偶 联 剂 KH一 5 5 0的加入 使 复 合 材料 熔 体 流 动 速 率 及 零剪 切黏度 进一 步提 高 。 参 考 文 献
[ 1 3 Ku l i k o v O, Ho r n u n g K, Wa g n e r ,M. No v e l p r o c e s s i n g a d d i t i v e s f o r r o t a t i o n a l mo l d i n g o f p 0 l y e t h y l e n e [ J ] . I n —
[ 4 1 许 承Байду номын сангаас. 偶 联剂 及 其 在 塑料 中 的应 用 [ J ] . 杭 州化 工,
复合材料在现代汽车工业中的应用与发展.pptx
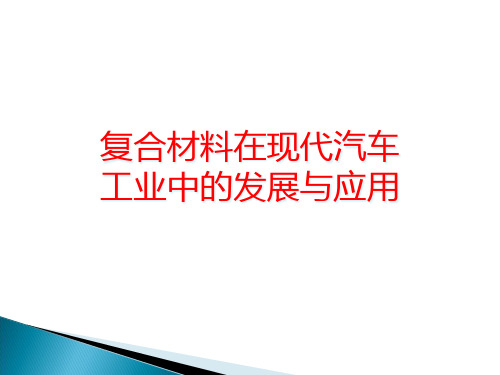
1.1 什么是复合材料?
再生树脂复合材料
第五代复合材料战机
复合材料电缆支架
verton复合材 料
pvd复合材料
印度复合材料 武装直升机
1.1 什么是复合材料?
复合材料的应用
①航空航天领域 可用于制造飞机机翼和前机身、卫星 天线及其支撑结构、太阳能电池翼和外壳、大型运载 火箭的 壳体、发动机壳体、航天飞机结构件等。 ②汽车工业 可用于制造汽车车身、受力构件、传动轴、 发动机架及其内部构件。 ③化工、纺织和机械制造领域 可用于制造化工设备、 纺织机、造纸机、复印机、高速机床、精密仪器等 ④医学领域 可用于制造医用X光机和矫形支架等。也 用作生物医学材料。此外,还用于制造体育运动器件 和用作建筑材料等。
不足之处:模具制造复杂,投 资较大。
1.3 复合材料著名生产企业
1麦格纳:加拿大汽车供应
商Magna公司与加拿大政府的 研发组织——国家研究委员会 (简称NRC)于2009年底结 成伙伴关系,旨在支持加拿大 汽车工业研发安全、经济、环 境友好和燃料效率高的“新一 代”车辆。双方将在加拿大安 大略省康科德创建一个 Magna-NRC复合材料优胜中 心,重点研发热塑性复合材料 汽车零部件。
图1 手糊成型工艺示意图
缺点:生产效率低,生产周期长,工作环境 差。生产的汽车零部件的质量往往不够稳定
图2 手糊成型工艺流 程
喷射成型
将混有引发剂和促进剂的两种聚酯分 别从喷枪两侧喷出,同时将切断的玻 纤由喷枪中心喷出,使其与树脂在空 间均匀混合后沉积到模具上。沉积到 一定厚度时,用压辊滚压使纤维浸透 树脂,排除气泡,经常温固化后成型 为汽车复合材料制品。也被称为“半 机械手糊成型工艺” 缺点:产品的均匀度取决于操作人员的 熟练程度;制品强度较低;阴模成型 比阳模成型难度大,小型制品比大型 制品生产难度大;生产现场工作环境 恶劣,环境污染程度一般均大于其他 的工艺方法。
汽车材料教学课件第四版第八章非金属材料及复合材料及其在汽车上的应用
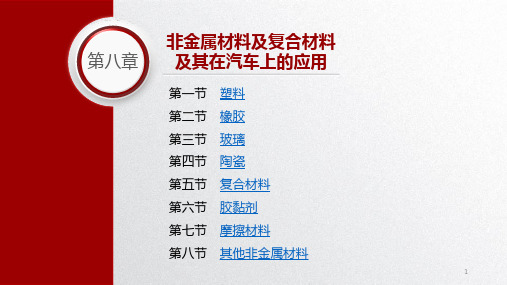
3. 增强材料 增强材料主要用来提高橡胶的力学性能,如强度、硬度、耐磨性和刚性等。
36
二、橡胶的分类
1. 按原料来源分类 橡胶的种类很多,按其原料来源不同,橡胶分为天然橡胶、合成橡胶和再生橡胶 三大类。 (1)天然橡胶天然橡胶是指以天然生胶制成的橡胶材料。天然橡胶是一种综合 性能优良的高弹性物质,大量用于制造各类轮胎以及各种胶带、胶管等橡胶制品。
5
6
一、汽车塑料件
汽车塑料零部件主要有三类:内饰件、外饰件和功能件。内饰件主要有仪表板、 车门内饰板、座椅、车厢内饰等。外饰件除要求具有内饰件的功能外,还要求强度 高、韧性好、耐环境条件及耐冲击性能好,主要有前后保险杠、挡泥板等。塑料材 料的前保险杠如下图所示,保险杠饰板和泡沫塑料碰撞吸能器可吸收车速低于 4 km/h时的轻微碰撞力,这些部件碰撞后会自动恢复原样。
37
(2)合成橡胶 合成橡胶是指以合成生胶制成的橡胶材料。合成橡胶品种繁多,通常分为通用合 成橡胶和特种合成橡胶。通用合成橡胶是汽车工业的重要材料,常用的有氯丁橡胶、 丁苯橡胶、顺丁橡胶等。
38
(3)再生橡胶 再生橡胶是利用废旧橡胶制品经再加工而成的橡胶材料。再生橡胶强度较低,但 有良好的耐老化性,且加工方便,价格低廉。汽车上常用于制造橡胶地毡、各种封 口胶条等。
39
2. 按性能和用途分类 橡胶按其性能和用途不同,分为通用橡胶和特种橡胶两大类。 (1)通用橡胶通用橡胶是指产量大、应用广,在使用上没有特殊性能要求的橡 胶,如天然橡胶、丁苯橡胶、顺丁橡胶、异戊橡胶等。汽车上使用的一般都是通用 橡胶。 (2)特种橡胶特种橡胶是指具有耐热、耐寒、耐油和耐化学腐蚀等特殊性能的 橡胶。主要用于在特殊环境下工作的零件,如硅橡胶、氟橡胶、聚氨酯橡胶等。
复合材料泡沫夹层结构力学性能与试验方法

FRP /C M 2005.N o .2收稿日期:2004 07 23作者简介:孙春方(1963 ),男,副研究员,博士研究生。
复合材料泡沫夹层结构力学性能与试验方法孙春方,薛元德,胡 培(同济大学航空航天与力学学院,上海200092)摘要:本文讨论纤维增强复合材料与聚合物泡沫组成的夹层结构的刚度、强度及弯曲性能试验方法;分析了复合材料面层的弹性常数、泡沫芯层的模量和夹层结构的刚度;阐述了夹层结构的应力分布和常见的5种破坏模式;对夹层结构的疲劳强度和冲击时的力学行为进行了探讨。
关键词:复合材料;泡沫;夹层结构;力学性能中图分类号:T B332 文献标识码:A 文章编号:1003-0999(2005)02-0003-041 引 言由轻质芯体与两层刚硬坚固的外壳制成的结构件称为夹层结构。
芯体对外壳的分隔增大了结构的惯性矩,而质量几乎没增加,得到一个抗弯曲和屈曲载荷的有效结构。
它常用于为减小重量的场合。
外壳或面材一般是金属(如铝)或纤维增强复合材料,芯体是蜂窝、聚合物泡沫、木材等。
本文讨论纤维增强复合材料与聚合物泡沫组成的夹层结构。
探讨轨道车辆用复合材料泡沫夹层结构中的一些力学性能及相应的试验方法。
复合材料是由两种或两种以上不同化学性质或物理性质的组分复合而成的材料。
复合材料具有质量轻、比强高,易于加工和改型、耐腐蚀、可设计性强等优点。
涉及到的材料包括碳纤维、玻璃纤维、环氧树脂和酚醛树脂等。
聚合物泡沫是一种最常见的芯材,主要有聚氯乙烯(PVC )、聚苯乙烯(PS)、聚氨酯(PU )、聚甲基丙烯酰亚胺(P M I)、聚醚酰亚胺(PE I)和丙烯腈 苯乙烯(SAN 或AS)。
密度从30kg /m 3到300kg /m 3不等。
通常在复合材料中使用的泡沫密度在40~200kg /m 3之间。
夹层结构的力学性能取决于表层和芯部材料的力学性能及几何尺寸。
主要涉及夹层结构的强度和刚度。
强度主要指复合材料的拉、压性能,泡沫的剪切强度,夹层结构的疲劳强度和冲击时的力学行为。
PMI泡沫塑料在国内外的研究与应用简介

聚甲基丙烯酰亚胺(PMI)泡沫塑料于1962由德国罗姆公司(德固赛的前身)开发出来,1971年代实现工业化,1972年开始应用于航空领域。
如今,PMI泡沫的应用领域已很广泛,近年来国内外的其他机构也开始了对该高性能泡沫的开发研究。
同密度的情况下,PMI泡沫具有比其他聚合物泡沫材料更高的抗压缩强度和刚度、更优异的耐高温和耐湿热性能、以及更好的抗高温蠕变性能和尺寸稳定性,其突出的耐热性能和高温下优异的抗蠕变性能使其能承受碳纤维/环氧、碳纤维/双马等树脂复合材料的高温固化工艺条件,可实现泡沫夹芯与预浸料的一次共固化,广泛应用于复合材料泡沫夹层结构件的制造。
此外,由于聚甲基丙烯酰亚胺泡沫采用固体发泡工艺制造,故泡沫材料的闭孔率高,孔径分布均匀,一致,吸湿率低。
上述性能特点使其在航天、航空、舰船、高速列车、风力发电等许多技术领域具有广泛的应用前景。
1 国外应用状况纵观国内外市场,目前德固赛的ROHACELL还处于垄断地位。
ROHACELL的型号及应用领域具体如下:ROHACELL 型号应用IG 主要用于运动器材,医疗床板,风机叶片和音响喇叭,是最常用的ROHACELL类型IG-F 力学性能基本和ROHACELLIG相同,孔隙更小。
A 用于航空航天领域,共固化工艺温度压力可达130C/0.35 Mpa,可以与中温固化环氧树脂预浸料共固化WF 用于航天航空领域,共固化工艺温度压力可达180C/0.7 MPa,可以与高温固化环氧树脂预浸料共固化XT 耐高温型产品,共固化工艺温度压力可达190C/0.7 MPa,可以与BMI树脂预浸料共固化RIST 适用于树脂注射工艺,作为结构材料RIMA 适用于树脂注射工艺,作为工艺辅助材料S 防火型,适用于铁路机车,船舶和小型飞机HF 主要用于天线,雷达罩,医疗EC 在制作共聚板的过程中因为加入了碳粉,所以制作出的泡沫能够吸收雷达波,适用于有隐身要求的夹层结构。
RHACELL应用举例:? PMI泡沫夹芯结构在A340和A380后压力框上取得应用。
- 1、下载文档前请自行甄别文档内容的完整性,平台不提供额外的编辑、内容补充、找答案等附加服务。
- 2、"仅部分预览"的文档,不可在线预览部分如存在完整性等问题,可反馈申请退款(可完整预览的文档不适用该条件!)。
- 3、如文档侵犯您的权益,请联系客服反馈,我们会尽快为您处理(人工客服工作时间:9:00-18:30)。
复合材料泡沫夹层结构在汽车外饰中的应用和发展作者:赢创德固赛范海涛汽车外饰目前的材料体系汽车外饰件,即汽车外部的功能性或装饰性部件,主要包括保险杠、翼子板、车身裙板、外侧围、进气道、车顶盖、车门、散热器格栅、发动机罩、扰流板、防擦条、后门拉手和脚踏板等。
由于其所处的位置(外部)和具有的功能(防撞等),这些部件所用材料要求具有较高的强度、韧性、耐环境条件的性能及抗冲击性能。
随着汽车工业和材料工业技术水平的不断提高,汽车外饰材料已逐渐走向多元化。
除了普通钢材以外,高强度钢、铝镁合金、工程塑料和各种复合材料也正得到越来越多的应用。
其中,复合材料以其质量轻、可设计性好和抗腐蚀等优点日益得到广泛应用。
图1 夹层结构的概念一般,选用汽车外饰材料的决定因素包括:材料成本、生产率、加工难度、设计方法的成熟性以及汽车重量等。
根据汽车类型的不同,所用复合材料种类也不尽相同。
对于普通轿车而言,成本和生产率是着重考虑的因素。
因此,除了金属材料外,目前此类汽车最常用的外饰材料是热塑性塑料(有时加入短玻璃纤维增强)。
这类材料可以通过注射模塑工艺实现量产,具有较高的生产率。
与热塑性塑料相比,热固性塑料的应用较少。
一般,只有两种工艺能够实现热固性复合材料的中高规模的量产:即片状模塑成型(SMC)和树脂转移模塑成型(RTM)。
图2 ROHACELL在雷诺第三代和第四代Espace汽车上的应用运动型和概念验证型轿车通常对低重量、高强度/刚度的要求较高,一般不需要实现大规模量产(即对生产率要求不高),其面向的市场可承受较高的成本,因此此类汽车的外饰广泛采用了纤维增强复合材料。
而承担运输任务的卡车和拖车,其车体重量对运输成本有较大的影响,因此此类汽车也有采用复合材料(纤维增强复合材料、夹层板等)的实例。
表中列出了复合材料在某些车型外饰上的应用。
其中SMC为片状模塑成型,RTM为树脂转移模塑成型,RIM为反应注射成型,VI为真空树脂注入成型。
可以看出,纤维增强复合材料等已随着技术的成熟而得到广泛应用,应用部件包括车门、发动机罩、前格栅、翼子板、保险扛骨架、门柱护板、通风百叶窗和导流罩等近20种外饰件。
多材料混合结构体系复合材料在汽车外饰上的应用动力来自于汽车的轻量化趋势。
图3 ROHACELL71 IG在奔驰McLaren SLR汽车上的应用汽车的轻量化包括材料的轻量化和结构的轻量化。
材料的轻量化一般通过采用轻量化的金属和非金属材料来实现,主要包括高强度钢、铝镁合金、工程塑料以及各种复合材料。
目前,尽管钢铁材料仍在汽车材料中占据主导地位,但其比例逐年下降,而铝合金、镁合金、工程塑料和复合材料等轻量化材料的应用比例则逐年上升。
材料轻量化,尤其是基于复合材料的材料轻量化,已成为世界汽车材料技术发展的主要方向之一。
自20世纪60年代复合材料被引入汽车制造业后,其在提高汽车性能及减轻重量方面的优点已得到证实。
复合材料具有比强度高、比刚度高、性能可设计和易于整体成形等许多优异特性,将其用于汽车结构上,可凭借比常规金属结构低的重量达到同等的性能,这是其他材料无法或难以实现的。
美国先进汽车技术能源事务部曾与美国汽车研究委员会联手,从事有关汽车结构的先进材料、加工方法和装配技术的开发项目,其重点之一就是汽车结构用复合材料的开发。
20世纪80年代末,USCAR下设的汽车复合材料委员会也开展了此方面的研究。
最近德国Paderborn大学的O.Hahn等人提出“多材料轻量化结构”及“合适材料用在合适的部位”两个概念,指出了车身材料的发展趋势,即通过对多材料复合体系进行结构优化,在改进汽车性能的同时,显著减轻车身重量。
当前,材料的组合以高强度钢、铝、镁和复合材料为主。
目前汽车中使用的复合材料形式主要有:金属基复合材料、纤维层压板、编织复合材料以及夹层板等。
图4 ROHACELL在Lancer Evolution 8上的应用基于复合材料的多材料轻量化应用的一个典型实例是道奇SRT-10。
该型轿车采用了多种复合材料及多种制造工艺。
其翼子板采用了玻璃纤维增强复合材料(反应注塑成型工艺),发动机盖采用了玻璃纤维增强复合材料(SMC工艺),翼子板支撑面、挡风玻璃窗框和门板采用了碳纤维增强复合材料(SMC工艺)。
但是,基于复合材料的多材料轻量化尚未在汽车领域得到广泛应用,主要原因是:复合材料的加工工艺大多不能适应高产量的生产需求,因此需要在工艺上进行改进,以缩短目前复合材料部件的生产时间;复合材料加工工艺的自动化水平有待提高(特别是增强材料铺放的自动化),以降低制造成本、缩短生产周期及实现质量控制的自动化;原材料价格较高,影响了复合材料的大量应用;目前能够满足新的报废汽车法规的复合材料及工艺十分有限;汽车用复合材料的检测方法还不够完善;需要开发专门的汽车合成材料的设计程序,尽管所有汽车制造厂都已开发了用于金属零件的设计程序,但该程序一般不能为复合材料所用;还需要开发新的复合材料数字模拟,并要求这些模拟在3个方面具有判定能力,即典型材料性能的可用性、材料模拟的精确性以及要求的计算结果。
基于多材料结构体系的轻量化过程的最终目的是:在基于多材料多结构体系基础上,实现模块化制造和装配,其中包括复合材料夹层结构。
图5 ROHACELL在宝马X5上的应用PMI泡沫夹层结构的特点夹层结构是一种多材料混合结构体系,通常由上下面板及中间的芯材组成,如图1所示。
芯材一般采用轻质材料(通常为蜂窝或者泡沫),它既可承受剪切载荷,也能起到减震和吸收噪音的作用。
面板一般采用强度和刚度均较高的复合材料,可以是层压板,也可以是缠绕或编织成型的复合材料板。
夹层结构传递载荷的方式类似于工字梁,上下面板提供面内的刚度和强度,承受由弯矩或面内拉压引起的面内拉压应力和面内剪应力,芯材提供面板法向方向的刚度和强度,承受压应力和横向力产生的剪应力,并支持面板,使其不失去稳定性,并可较大幅度地减轻构件的重量。
并且,由于芯材较轻,面板较强,从而能同时达到重量轻和性能好的要求。
复合材料夹层结构可以采用聚甲基丙稀酰亚胺(简称“PMI”)泡沫作为芯材。
PMI泡沫最早由德国罗姆公司于1972年开发研制出来,经过30多年的发展,目前已形成了一系列的产品。
现在市场上的PMI泡沫产品主要是德国赢创德固赛公司(前身为罗姆公司)生产的ROHACELL。
PMI泡沫是通过固体发泡工艺制作而成的,其孔隙基本一致,且为均匀的100%闭孔泡沫。
在相同密度条件下,PMI是已知泡沫材料中强度和刚度最高的泡沫材料之一。
PMI泡沫具有如下性能特点:不含氟里昂和卤素;易于机械加工,不需要特殊的机具;能够热成形,并保证100%闭孔泡沫,且具有各向同性;与各种树脂系统兼容(湿法和预浸料);具有较高的热变形温度、强度-重量比和耐疲劳性能;在加工过程中,具有很好的抗压缩蠕变性能,可以适用于包括中温环氧、高温环氧以及BMI树脂预浸料等的复合材料夹层结构共固化工艺。
该泡沫在高温下具有优异的耐蠕变性能,因而能够应用于需要高温固化的构件。
经适当的高温处理后,PMI泡沫能适应190℃的固化工艺并保持尺寸稳定性,适用于与环氧或BMI树脂共固化的夹层结构构件中。
PMI泡沫自身的优势结合复合材料层压板,就可以构成结构效率高、具有高比刚度和高比强度的复合材料夹层结构。
根据设计和工艺要求,通常可以采用的结构形式有PMI泡沫夹层结构板和PMI泡沫夹层结构加强筋。
应用实例近年来,ROHACELLPMI泡沫已在在汽车外饰件上得到了应用。
1999年至2001年,雷诺汽车公司采用RTM工艺,先后成功地在Espace第三代汽车的发动机罩和第四代汽车的车顶加强筋部位使用了ROHACELL 51 IG,并采用了玻璃纤维进行增强,如图2所示。
此外,奔驰McLaren SLR汽车的车门槛板和后保险杠底杆等部件则使用了ROHACELL 71 IG,如图3所示。
在Lancer Evolution 8中,ROHACELL 51 IG被用作扰流板的夹层结构芯材,它比原来的ABS部件减轻了2kg,如图4所示。
在宝马X5中,通过热压罐工艺固化成型的以ROHACELL 为芯材的夹层板发动机盖,其重量仅为金属制发动机盖的1/4左右,如图5所示。
2006年,赢创(中国)投资有限公司联合上海同济大学一起,就“采用复合材料设计和制造大型汽车覆盖件”进行了一系列的探索和研究。
其中,PMI泡沫夹心帽筋条结构的复合材料发动机盖和后背门部件已被安装在上海燃料电池汽车动力系统有限公司的新一代燃料电池汽车上。
与传统的金属结构部件相比,二者分别减重37.7%和34.6%。
在其开发过程中,通过采用最新的夹层结构帽筋条设计,以及树脂转移模塑工艺,实现了一步整体成型。
该项目的成功使得汽车复合材料的概念不再是单纯的短纤维增强复合材料(例如SMC、GMT),而是将纤维增强复合材料、设计与制造工艺相结合,并与其他材料相结合,实现了最终的多材料结构方案。
由上述实例可以看出,采用ROHACELL 泡沫芯材的夹层结构能大大减少汽车外饰件的重量。
总结将PMI泡沫与其他材料及加工工艺结合,有利于汽车的轻量化发展。
随着材料轻量化技术,包括设计、生产工艺、装配、连接及材料性能等的不断发展和成熟,未来基于复合材料的多材料轻量化结构是汽车轻量化及汽车外饰件材料的发展趋势。
通过不同材料、结构和制造工艺的相互结合和补充,可以简单方便地实现设计和制造的模块化,以使所用材料和零件的功能达到最佳的组合。
目前,汽车的轻量化技术还处于不成熟阶段,在未来将有很大的发展空间。