车间现场改善与效率提升[优质PPT]
合集下载
最新现场改善与生产效率提升-PPT精选文档
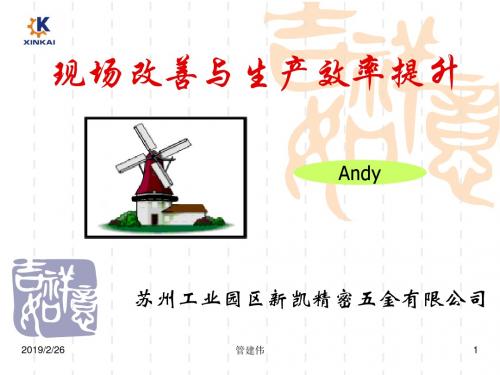
人员流动大
2019/2/26 管建伟
快交货
3
以最少的投入来获取最大的产出
最少资金 最少人力 最少设备 最少材料 最佳方法
5M
P Q C D S M
管建伟
最佳品种 最优质量 最低成本 准时交货 安全环保 良好情绪
4
2019/2/26
为什么要加强生产 现场管理?
2019/2/26
管建伟
5
80%的工作在现场 80%的人员在现场 80%的问题在现场
80%的事故在现场
2019/2/26
管建伟
6
现场 现场 改善 什么?
管理
什么?
2019/2/26
管建伟
7
四大目标 Q 质量 C 成本 D 交期 S 安全
现场管理要求
现场管理方法
一消:消除不增值活动 二化:标准化、可视化 三不:现场质量“三不” 三现:现场、现实、现物 四M:4M1E 五S:5S管理
环境
温度 湿度 灰尘 污染
2019/2/26
管建伟
14
现场管理的“单一最好”原则
一处保管 一日处理 一个资料夹 一小时会议 一张纸 一分钟电话 一件工具 一个单元 一个流 一天班长
2019/2/26
户口管理 今日事,今日毕 资料夹一册化 一事一议,半小时更好 报告、表格一张篇幅完全表达 长话短说,不拖泥带水 多样工具简化成一件 在一个小组或一组设备内完工 生产过程“一个流” 员工多能化培养
2019/2/26 管建伟 19
改善的十条基本原则
1、“存在的都是不合理的” 2、强调理由是不思进取的表现 3、立即改进,及时比正确更重要 4、反复追问为什么,总能找到问题根源 5、许多问题的解决,就在于否定不可能 6、更应该重视的是不花大钱的改善 7、不要追求完美,完美都是从不完美开始的 8、最清楚改善的是处于第一线的操作人员 9、只要是改善,最小的事也值得去做 10、改善永无止境,没有最好,只有更好
车间现场改善与效率提升ppt课件

2020/1/10
管建伟
11
现场管理的“五字检查”法
听 听设备运转过程中是否有异常声音
摸 有无异常的发热或抖动、振动等现象
查
监测,关键、特殊工序受控情况 油管阀门等有无跑、冒、滴、漏数据
看
有无松动、晃动、移动、错位、开裂、缺损现象 设备运行参数是否符合规定要求
闻
有无泄漏或其他引起的焦味、异常气味
2020/1/10
2020/1/10
管建伟
17
IE工业工程简介
工业工程(IE)是一门应用科学,它将传统的工程 技术融合于现代的科学管理技巧之中 ,弥补原有管理 及工程技术之脱节。IE是藉着设计、改善或设定人、料 机的工作系统,以求得到更高生产力的专门技术。IE要 求以工程技术为基础,配合科学管理的技巧来发现问题、 解决问题、预防问题。
作业现场由很多动作构成,我们所研究的现 场针对动作,而不是人,人的行动和举止都是 由身体各部分的动作组合而成。每个人都不一 样,我们不能要求所有人的高矮胖瘦、思想说 话都一致,但是我们可以要求所有人的动作标 准化,实现一致性。
2020/1/10
管建伟
24
作业标准化
所谓标准化就是明确的书面的工作方法 标准就是样板,是所有工作的依据 标准显示了迄今为止所能想到 最快、最好、最方便、最安全 的工作方法 可以避免不同人员因不同做法 而产生的不同结果
现场改善与生产效率提升
1
生产管理的铁三角
D
交
成
期 安全 本
Qபைடு நூலகம்
C
质量
用最低的成本 符合要求的质量 达成规定的交期
2020/1/10
管建伟
2
企业管理面临的共同难题
生产现场管理及效率提升 PPT

环境
温度 湿度 灰尘 污染
2020/9/2
14
现场管理的“单一最好”原则
2020/9/2
15
现场管理的“三五”要求
操作“五按”: 按图纸、按标准、按程序、按时间、按操作指令
工作“五干”: 干什么、怎么干、什么时间干、按什么方法干、 干到什么程度
结果“五查”: 由谁来检查、什么时间检查、检查什么项目、检 查的标准是什么、检查的结果由谁来落实
可视化管理
员工提案
QC小组
2020/9/2
现场管理之屋
9
目前的现场
半成品堆积如山,生产线却停工待料 成品积压,客户却天天催货 放在旁边的是不需要做的,需要做的却不在旁边 一边交期紧急,一边返工返修不断 很容易买到的螺栓、螺母却保留一、二年的用量 整批产品常常因为一二个零件而搁浅耽误 有人没事做,有事没人做
2020/9/2
10
现场管理的五项要求
一、当问题发生时,要先去现场; 二、检查现物(有关的物品); 三、当场采取暂行处置措施; 四、发掘真正原因并将其排除; 五、标准化以防止再发生。
2020/9/2
11
案例分析
某班组自动车床经常发生故障,维修人员 只能通过维修和更换备件解决故障。目前该设 备故障平均约每半年发生一次,主要原因是主 轴轴承发生故障,一套轴承的备件价格为3000 元,每年更换备件费用达6000元。如何应用 “五问”活动对主轴轴承故障的原因进行分析。
工作规范:本岗位应遵守的制度、规定、要求和程序 设备操作维护:清楚设备的各项技术参数使用要求、维护保养、清
洁润滑、日常点检等要求 安全职责:清楚本岗位应遵循的安全操作事项和责任 危害辨识及应急预案:清楚该项工作的危害和怎样预防的措施要求
车间现场5S标准化管理企业工作效率与能力提升培训PPT模板课件
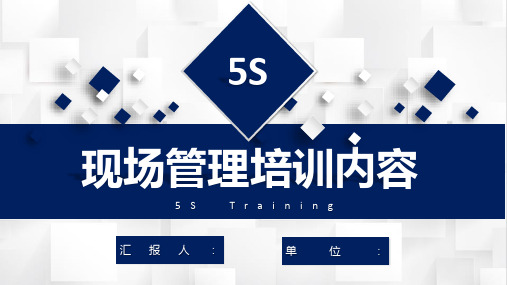
整顿
01
目的:不浪费时间寻找物品,提高工作效率和产品质量,保障
生产安全。
意义:把需要的人、事、物加以定量、定位。通过前一步整理
02
后,对生产现场需要留下的物品进行科学合理的布置和摆放,
以便用最快的速度取得所需之物,在最有效的规章、制度和最
简洁的流程下完成作业。
整顿
要点:① 物品摆放要有固定的地点和区域,以便于 寻找,消除因混放而造成的差错;② 物品摆放地点 要科学合理。例如,根据物品使用的频率,经常使 用的东西应放得近些(如放在作业区内),偶尔使 用或不常使用的东西则应放得远些(如集中放在车 间某处);③ 物品摆放目视化,使定量装载的物品 做到过目知数,摆放不同物品的区域采用不同的色 彩和标记加以区别。
五大原则
在采用看板作为管理工具时, 应遵循以下五个原则:
⑴后工序只有在必要的时候,才向 前工序领取必要数量的零部件:需 要彻底改变现有流程和方法。
⑵前工序应该只生产足够的数 量,以补充被后工序领取的零 件:在这两条原则下,生产系 统自然结合为输送带式系统, 生产时间达到平衡。
⑶不良品不送往后工序:后 工序没有库存,后工序一旦 发现次品必须停止生产,找 到次品送回前工序。
清洁
目的:认真维护并坚持整理、整顿、清扫的 效果,使其保持最佳状态。
意义:通过对整理、整顿、清扫活动的坚持 与深入,从而消除发生安全事故的根源。创 造一个良好的工作环境,使职工能愉快地工 作。
清洁
要点:① 车间环境不仅要整齐,而且要做到清洁卫生,保证工人身 体健康,提高工人劳动热情;② 不仅物品要清洁,而且工人本身也 要做到清洁,如工作服要清洁,仪表要整洁,及时理发、刮须、修 指甲、洗澡等;③ 工人不仅要做到形体上的清洁,而且要做到精神 上的“清洁”,待人要讲礼貌、要尊重别人;④ 要使环境不受污染, 进一步消除浑浊的空气、粉尘、噪音和污染源,消灭职业病。
《现场改善技巧》课件
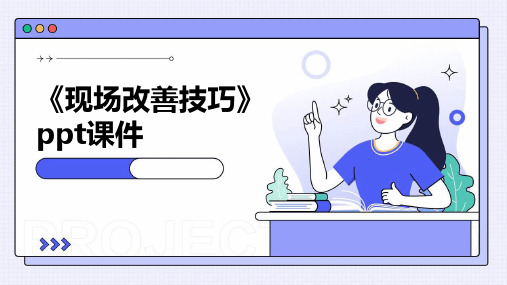
针对评估和审查中发现的问题,制定改进措施并组 织实施。
标准的更新与完善
根据改进效果和生产环境的变化,对作业标准进行 更新和完善,以保持标准的适用性和有效性。
05 目视化管理
目视化管理的定义和作用
01
目视化管理是一种利用视觉信息来管理和控制工作 场所的方法。
02
目视化管理能够提高工作效率,减少错误和浪费, 提升员工的安全意识。
认可和奖励
对积极参与改善活动的员工给予适当的认可和奖励,激发员工的积 极性。
团队合作与竞赛
组织跨部门的团队合作项目或竞赛,激发员工的团队合作精神和竞争 意识。
感谢您的观看
THANKS
作业标准的制定与实施
培训与教育
对员工进行作业标准的培训和教育,确保员工理解和 掌握标准。
监督与检查
建立监督检查机制,确保员工在实际工作中执行标准 。
反馈与改进
收集员工的反馈意见,对标准进行持续改进和优化。
作业标准的持续改进
定期评估与审查
定期对作业标准进行评估和审查,以发现存在的问 题和不足。
改进措施的实施
培养员工的问题意识
发现问题的能力
培养员工敏锐的观察力,能够及时发现现场存在的问题和改进空 间。
分析问题的能力
通过培训和引导,帮助员工学会分析问题产生的原因,并提出有 效的解决方案。
解决问题的能力
鼓励员工勇于承担责任,积极主动地解决问题,提高工作效率和 质量。
鼓励员工参与改善活动
提供培训和支持
为员工提供必要的培训和支持,使其具备参与改善活动的能力和信 心。
现场改善不仅关注单个环节的优化, 更强调整体流程的协同和整合。
现场改善的重要性
提高生产效率
标准的更新与完善
根据改进效果和生产环境的变化,对作业标准进行 更新和完善,以保持标准的适用性和有效性。
05 目视化管理
目视化管理的定义和作用
01
目视化管理是一种利用视觉信息来管理和控制工作 场所的方法。
02
目视化管理能够提高工作效率,减少错误和浪费, 提升员工的安全意识。
认可和奖励
对积极参与改善活动的员工给予适当的认可和奖励,激发员工的积 极性。
团队合作与竞赛
组织跨部门的团队合作项目或竞赛,激发员工的团队合作精神和竞争 意识。
感谢您的观看
THANKS
作业标准的制定与实施
培训与教育
对员工进行作业标准的培训和教育,确保员工理解和 掌握标准。
监督与检查
建立监督检查机制,确保员工在实际工作中执行标准 。
反馈与改进
收集员工的反馈意见,对标准进行持续改进和优化。
作业标准的持续改进
定期评估与审查
定期对作业标准进行评估和审查,以发现存在的问 题和不足。
改进措施的实施
培养员工的问题意识
发现问题的能力
培养员工敏锐的观察力,能够及时发现现场存在的问题和改进空 间。
分析问题的能力
通过培训和引导,帮助员工学会分析问题产生的原因,并提出有 效的解决方案。
解决问题的能力
鼓励员工勇于承担责任,积极主动地解决问题,提高工作效率和 质量。
鼓励员工参与改善活动
提供培训和支持
为员工提供必要的培训和支持,使其具备参与改善活动的能力和信 心。
现场改善不仅关注单个环节的优化, 更强调整体流程的协同和整合。
现场改善的重要性
提高生产效率
车间管理与现场改善方法PPT课件

③ 以现状为基础找出问题(发现浪费)
④ 问题对策与防止再发生
⑤制作新的标准作业表 ⑥ 按① 至⑤的步骤
无止境地反复很重要
作业的指导与训练
标准作业 标准作业的改善 把握问题(现状)
发现浪费
标准作业
改善
原因追究
13
如何进行现场改善
3-2 从作业改善到设备改善
① 作业改善 (A) 作业步骤、组合的改变 (B) 物品摆放, 作业工具及作业台摆放的改变 (C)简单的小工具, 滑道, 自动弹出, 吊具等的安装、改变等 (D) 改善现有设备
=面
(d) 公司的改善
= 立方体
27
如何进行现场改善
3 1
③ 总结
(a) 改善从观察现场开始
(b) 要热爱改善
(c) 事实胜于雄辩,实践是首要
改善是细而慢 不如粗而快! 不动则无成功!
28
如何进行现场改善
3 2
Ⅳ. 标准作业的制作
1. 标准作业的再确认
1-1 标准作业是现场改善的原点, 不标准的地方不存在改善.
[2] 设备是瓶颈的时候
1. 不要让瓶颈工位闲下来 2. 将按启动钮的时间提前 3. 缩小送料行程(快送, 切削送料) 4. 使机器动作叠加起来,看 是否能缩短加工以外的时间 5. 加快快送, 快退的速度
2 5
22
如何进行现场改善
好的排位的思考方法
(A) 考虑了流线的排位 ― 有灵活性的排位 ― 可根据变化移动
生产过 剩的浪 费
加工的 浪费
4
如何进行现场改善 Ⅱ. 生产方法的两大支柱
1. Just-In-Time的生产
1-1 使工序流线化
S・P・S
新技术生产体系
④ 问题对策与防止再发生
⑤制作新的标准作业表 ⑥ 按① 至⑤的步骤
无止境地反复很重要
作业的指导与训练
标准作业 标准作业的改善 把握问题(现状)
发现浪费
标准作业
改善
原因追究
13
如何进行现场改善
3-2 从作业改善到设备改善
① 作业改善 (A) 作业步骤、组合的改变 (B) 物品摆放, 作业工具及作业台摆放的改变 (C)简单的小工具, 滑道, 自动弹出, 吊具等的安装、改变等 (D) 改善现有设备
=面
(d) 公司的改善
= 立方体
27
如何进行现场改善
3 1
③ 总结
(a) 改善从观察现场开始
(b) 要热爱改善
(c) 事实胜于雄辩,实践是首要
改善是细而慢 不如粗而快! 不动则无成功!
28
如何进行现场改善
3 2
Ⅳ. 标准作业的制作
1. 标准作业的再确认
1-1 标准作业是现场改善的原点, 不标准的地方不存在改善.
[2] 设备是瓶颈的时候
1. 不要让瓶颈工位闲下来 2. 将按启动钮的时间提前 3. 缩小送料行程(快送, 切削送料) 4. 使机器动作叠加起来,看 是否能缩短加工以外的时间 5. 加快快送, 快退的速度
2 5
22
如何进行现场改善
好的排位的思考方法
(A) 考虑了流线的排位 ― 有灵活性的排位 ― 可根据变化移动
生产过 剩的浪 费
加工的 浪费
4
如何进行现场改善 Ⅱ. 生产方法的两大支柱
1. Just-In-Time的生产
1-1 使工序流线化
S・P・S
新技术生产体系
现场改善与生产效率提升ppt

2020/5/7
16
现场管理的“五字检查”法
听 听设备运转过程中是否有异常声音
摸 有无异常的发热或抖动、振动等现象
查
监测,关键、特殊工序受控情况 油管阀门等有无跑、冒、滴、漏数据
看
有无松动、晃动、移动、错位、开裂、缺损现象 设备运行参数是否符合规定要求
闻
有无泄漏或其他引起的焦味、异常气味
2020/5/7
2020/5/7
19
改善的十条基本原则
1、“存在的都是不合理的” 2、强调理由是不思进取的表现 3、立即改进,及时比正确更重要 4、反复追问为什么,总能找到问题根源 5、许多问题的解决,就在于否定不可能 6、更应该重视的是不花大钱的改善 7、不要追求完美,完美都是从不完美开始的 8、最清楚改善的是处于第一线的操作人员 9、只要是改善,最小的事也值得去做 10、改善永无止境,没有最好,只有更好
7
四大目标 Q 质量 C 成本 D 交期 S 安全
现场管理要求
2020/5/7
现场管理方法
一消:消除不增值活动 二化:标准化、可视化 三不:现场质量“三不” 三现:现场、现实、现物
四M:4M1E
五S:5S管理
8
利润
Q
质 量
C
成 本
D
交 期
S
安 全
生产
设备
物料
人、机、料、法、环
作业标准化
现场5S 消除现场浪费
18
24
30
%
60 10
%
+50 10
%
50 10
20
35
50
60
20
30
40
50
20
30
生产现场改善ppt
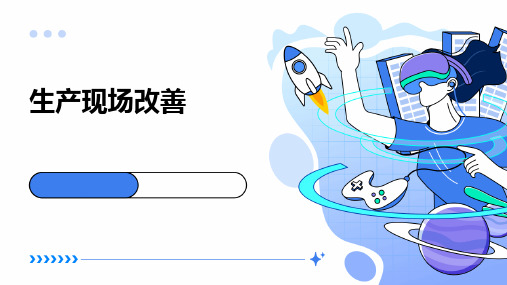
02
现场环境改善
清理整顿现场环境
清除垃圾和杂物
定期清理生产现场的垃圾、 废弃物和无用物品,保持 现场整洁。
整顿设备和工具
对生产设备和工具进行归 类、标识和定位,确保摆 放整齐、易于取用。
改善作业环境
优化生产布局,减少不必 要的搬运和等待,提高作 业效率。
标识标牌规范设置
设备标识
对生产设备进行标识,包括设备 名称、型号、状态等信息,方便
提高产品质量和客户满意度
建立完善的质量管理体系,明确质量标准和检验流程,确保产品质量符合客户要求。
加强员工培训和质量意识教育,提高员工技能和素质,减少人为因素对产品质量的 影响。
定期收集客户反馈和意见,及时响应并处理客户投诉和问题,不断改进产品和服务 质量。
05
员工培训与素质提
升
加强员工技能培训和教育
成果一
通过引入新的生产设备和工艺 ,提高了生产效率和产品质量
。
成果二
优化了生产流程,减少了浪费 和不必要的环节,降低了成本 。
经验教训一
在实施改善措施前,应充分调 研和评估,确保方案的科学性 和可行性。
经验教训二
在改善过程中,应注重团队协 作和沟通,确保各项工作的顺
利进行。
展望未来持续改善方向和目标
定期组织技能培训班
针对不同岗位和工种,定期开设技能培训班,提高员工的技能水 平和操作能力。
引入先进技术和设备培训
及时引入行业内的先进技术和设备,并对员工进行相应的操作和维 护培训。
鼓励员工自我学习
建立学习奖励机制,鼓励员工利用业余时间自我学习,提升个人技 能。
提高员工安全意识和操作规范
加强安全教育培训
方向一
- 1、下载文档前请自行甄别文档内容的完整性,平台不提供额外的编辑、内容补充、找答案等附加服务。
- 2、"仅部分预览"的文档,不可在线预览部分如存在完整性等问题,可反馈申请退款(可完整预览的文档不适用该条件!)。
- 3、如文档侵犯您的权益,请联系客服反馈,我们会尽快为您处理(人工客服工作时间:9:00-18:30)。
改善
维持 改善的能力 是评价管理者的重要基 准
2019/12/25
管建伟
14
改善的十条基本原则
1、“存在的都是不合理的” 2、强调理由是不思进取的表现 3、立即改进,及时比正确更重要 4、反复追问为什么,总能找到问题根源 5、许多问题的解决,就在于否定不可能 6、更应该重视的是不花大钱的改善 7、不要追求完美,完美都是从不完美开始的 8、最清楚改善的是处于第一线的操作人员 9、只要是改善,最小的事也值得去做 10、改善永无止境,没有最好,只有更好
2019/12/25
管建伟
6
案例分析
某班组自动车床经常发生故障,维修人员 只能通过维修和更换备件解决故障。目前该设 备故障平均约每半年发生一次,主要原因是主 轴轴承发生故障,一套轴承的备件价格为3000 元,每年更换备件费用达6000元。如何应用 “ 五问”活动对主轴轴承故障的原因进行分析。
2019/12/25
2019/12/25
管建伟
15
_____车间1-5月管理目标改善计划表
序
计划改善项目
1 交货期 2 生产周期 3 改机时间 4 停机时间 5 操作人员数 6 在制品数量 7 零部件(半成品)数量 8 库存品总额 9 搬运距离 10 不合格品发生率 11 一次交验合格率 12 返工返修品
1月
2月
3月
4
6
8
10
12
18
24
30
%
60 10
%
+50 10
%
50 10
20
35
50
60
20
30
40
50
20
30
40
50
2019/12/25
管建伟
16
在当今的工业时代,用“农业头脑”办事 肯定是不行的,但也不是一步跨越到“电子计 算机头脑”就行得通。在“农业头脑”和“电 子计算机头脑”之间应该还应该有一个“工业 头脑”的时代。
2019/12/25
管建伟
11
现场管理的“五字检查”法
或抖动、振动等现象
查
监测,关键、特殊工序受控情况 油管阀门等有无跑、冒、滴、漏数据
看
有无松动、晃动、移动、错位、开裂、缺损现象 设备运行参数是否符合规定要求
闻
有无泄漏或其他引起的焦味、异常气味
一个流
生产过程“一个流”
一天班长 员工多能化培养
2019/12/25
管建伟
10
现场管理的“三五”要求
操作“五按”: 按图纸、按标准、按程序、按时间、按操作指令
工作“五干”: 干什么、怎么干、什么时间干、按什么方法干、 干到什么程度
结果“五查”: 由谁来检查、什么时间检查、检查什么项目、检 查的标准是什么、检查的结果由谁来落实
现阶段的IE(工业工程)的主要工作范围大致是: 价值分析、动作分析、工程分析、时间分析、平面布 置、搬运设计、可视化管理、员工多能化、快速换模等
2019/12/25
管建伟
18
工业工程可以让生活与工作井然有序
北京市某机构的办事人潮不断,要办事有排不完的队;领表要排队 、申办要排队、照相要排队、缴费要排队、领证要排队。由于当时设计 并未考虑到现在的人潮,而现在的需求已经远超过几年前的情况,所以 排队的空间、设施以及规则都已经不适用。因此几乎每天都发生这样的 情况:让有礼貌的市民排得心烦意乱,让急着办事的市民直跺脚,让不 守规矩的人拼命钻空子;甚至因排队起的争吵与冲突此起彼落。
4月
5月
单 位
目标 计 -% 划
实计 绩划
实计 绩划
实计 绩划
实计 绩划
实 绩
加权 平均
天
50 10
天
30 6
小时 75 15
小时 50 10
个
5
千件 25 5
千件 20 4
万元 10 2
米/件 30 6
20
30
40
50
12
18
24
30
30
45
60
75
20
30
40
50
2
5
10
15
20
25
8
12
16
20
2019/12/25
管建伟
17
IE工业工程简介
工业工程(IE)是一门应用科学,它将传统的工程 技术融合于现代的科学管理技巧之中 ,弥补原有管理 及工程技术之脱节。IE是藉着设计、改善或设定人、料 机的工作系统,以求得到更高生产力的专门技术。IE要 求以工程技术为基础,配合科学管理的技巧来发现问题、 解决问题、预防问题。
管建伟
7
生产现场管理普遍存在问题
生产无计划 质量无标准 作业无方法 堆放无区域 物品无标识
消耗无定额 过程无记录
2019/12/25
管建伟
8
现场管理的五大要素(4M1E)
人
思想意识 配合度 能力 个体差异
设备
设备功能 精确度 设备能力 故障预警
材料
及时 适宜 合格
方法
方法合理 过程受控 标准化
环境
2019/12/25
管建伟
12
现场管理的 “A B C” 法
把现场所看到的东西或感想用笔记下来 把自己希望改进或与要求不符的部分分为 A B C 三级 A 是明天马上要改善的 B 是一周后需要改善的 C 是一个月后计划改善的 策划具体改善措施 检查改善情况并予以奖励
2019/12/25
管建伟
13
管理的根本 在于不断改善
现场改善与生产效率提升
生产管理的铁三角
D
交
成
期 安全 本
Q
C
质量
用最低的成本 符合要求的质量 达成规定的交期
2019/12/25
管建伟
2
企业管理面临的共同难题
内部 救火式生产 质量不稳定 浪费严重
人员流动大
2019/12/25
管建伟
外部 小批量 多品种
低价格
快交货
3
以最少的投入来获取最大的产出
最少资金 最少人力 5M 最少设备 最少材料 最佳方法
2019/12/25
管建伟
P 最佳品种 Q 最优质量 C 最低成本 D 准时交货 S 安全环保 M 良好情绪
4
为什么要加强生产 现场管理?
2019/12/25
管建伟
5
现场管理的五项要求
一、当问题发生时,要先去现场; 二、检查现物(有关的物品); 三、当场采取暂行处置措施; 四、发掘真正原因并将其排除; 五、标准化以防止再发生。
温度 湿度 灰尘 污染
2019/12/25
管建伟
9
现场管理的“单一最好”原则
一处保管 户口管理
一日处理 今日事,今日毕
一个资料夹 资料夹一册化
一小时会议 一事一议,半小时更好
一张纸
报告、表格一张篇幅完全表达
一分钟电话 长话短说,不拖泥带水
一件工具 多样工具简化成一件
一个单元 在一个小组或一组设备内完工
许振超的技术研究工作: 许振超和队员们在桥吊每个操作环节抠时间。桥吊启动时,说明书上写 着,达到最高时速需要5秒钟,许振超计算后提出,3.5秒钟就够用,一 些司机不以为然地提出,抠.1.5秒有什么用?许振超为大家算了一笔账 :“如果一船有1000个集装箱,就能节约25分钟出来”。
维持 改善的能力 是评价管理者的重要基 准
2019/12/25
管建伟
14
改善的十条基本原则
1、“存在的都是不合理的” 2、强调理由是不思进取的表现 3、立即改进,及时比正确更重要 4、反复追问为什么,总能找到问题根源 5、许多问题的解决,就在于否定不可能 6、更应该重视的是不花大钱的改善 7、不要追求完美,完美都是从不完美开始的 8、最清楚改善的是处于第一线的操作人员 9、只要是改善,最小的事也值得去做 10、改善永无止境,没有最好,只有更好
2019/12/25
管建伟
6
案例分析
某班组自动车床经常发生故障,维修人员 只能通过维修和更换备件解决故障。目前该设 备故障平均约每半年发生一次,主要原因是主 轴轴承发生故障,一套轴承的备件价格为3000 元,每年更换备件费用达6000元。如何应用 “ 五问”活动对主轴轴承故障的原因进行分析。
2019/12/25
2019/12/25
管建伟
15
_____车间1-5月管理目标改善计划表
序
计划改善项目
1 交货期 2 生产周期 3 改机时间 4 停机时间 5 操作人员数 6 在制品数量 7 零部件(半成品)数量 8 库存品总额 9 搬运距离 10 不合格品发生率 11 一次交验合格率 12 返工返修品
1月
2月
3月
4
6
8
10
12
18
24
30
%
60 10
%
+50 10
%
50 10
20
35
50
60
20
30
40
50
20
30
40
50
2019/12/25
管建伟
16
在当今的工业时代,用“农业头脑”办事 肯定是不行的,但也不是一步跨越到“电子计 算机头脑”就行得通。在“农业头脑”和“电 子计算机头脑”之间应该还应该有一个“工业 头脑”的时代。
2019/12/25
管建伟
11
现场管理的“五字检查”法
或抖动、振动等现象
查
监测,关键、特殊工序受控情况 油管阀门等有无跑、冒、滴、漏数据
看
有无松动、晃动、移动、错位、开裂、缺损现象 设备运行参数是否符合规定要求
闻
有无泄漏或其他引起的焦味、异常气味
一个流
生产过程“一个流”
一天班长 员工多能化培养
2019/12/25
管建伟
10
现场管理的“三五”要求
操作“五按”: 按图纸、按标准、按程序、按时间、按操作指令
工作“五干”: 干什么、怎么干、什么时间干、按什么方法干、 干到什么程度
结果“五查”: 由谁来检查、什么时间检查、检查什么项目、检 查的标准是什么、检查的结果由谁来落实
现阶段的IE(工业工程)的主要工作范围大致是: 价值分析、动作分析、工程分析、时间分析、平面布 置、搬运设计、可视化管理、员工多能化、快速换模等
2019/12/25
管建伟
18
工业工程可以让生活与工作井然有序
北京市某机构的办事人潮不断,要办事有排不完的队;领表要排队 、申办要排队、照相要排队、缴费要排队、领证要排队。由于当时设计 并未考虑到现在的人潮,而现在的需求已经远超过几年前的情况,所以 排队的空间、设施以及规则都已经不适用。因此几乎每天都发生这样的 情况:让有礼貌的市民排得心烦意乱,让急着办事的市民直跺脚,让不 守规矩的人拼命钻空子;甚至因排队起的争吵与冲突此起彼落。
4月
5月
单 位
目标 计 -% 划
实计 绩划
实计 绩划
实计 绩划
实计 绩划
实 绩
加权 平均
天
50 10
天
30 6
小时 75 15
小时 50 10
个
5
千件 25 5
千件 20 4
万元 10 2
米/件 30 6
20
30
40
50
12
18
24
30
30
45
60
75
20
30
40
50
2
5
10
15
20
25
8
12
16
20
2019/12/25
管建伟
17
IE工业工程简介
工业工程(IE)是一门应用科学,它将传统的工程 技术融合于现代的科学管理技巧之中 ,弥补原有管理 及工程技术之脱节。IE是藉着设计、改善或设定人、料 机的工作系统,以求得到更高生产力的专门技术。IE要 求以工程技术为基础,配合科学管理的技巧来发现问题、 解决问题、预防问题。
管建伟
7
生产现场管理普遍存在问题
生产无计划 质量无标准 作业无方法 堆放无区域 物品无标识
消耗无定额 过程无记录
2019/12/25
管建伟
8
现场管理的五大要素(4M1E)
人
思想意识 配合度 能力 个体差异
设备
设备功能 精确度 设备能力 故障预警
材料
及时 适宜 合格
方法
方法合理 过程受控 标准化
环境
2019/12/25
管建伟
12
现场管理的 “A B C” 法
把现场所看到的东西或感想用笔记下来 把自己希望改进或与要求不符的部分分为 A B C 三级 A 是明天马上要改善的 B 是一周后需要改善的 C 是一个月后计划改善的 策划具体改善措施 检查改善情况并予以奖励
2019/12/25
管建伟
13
管理的根本 在于不断改善
现场改善与生产效率提升
生产管理的铁三角
D
交
成
期 安全 本
Q
C
质量
用最低的成本 符合要求的质量 达成规定的交期
2019/12/25
管建伟
2
企业管理面临的共同难题
内部 救火式生产 质量不稳定 浪费严重
人员流动大
2019/12/25
管建伟
外部 小批量 多品种
低价格
快交货
3
以最少的投入来获取最大的产出
最少资金 最少人力 5M 最少设备 最少材料 最佳方法
2019/12/25
管建伟
P 最佳品种 Q 最优质量 C 最低成本 D 准时交货 S 安全环保 M 良好情绪
4
为什么要加强生产 现场管理?
2019/12/25
管建伟
5
现场管理的五项要求
一、当问题发生时,要先去现场; 二、检查现物(有关的物品); 三、当场采取暂行处置措施; 四、发掘真正原因并将其排除; 五、标准化以防止再发生。
温度 湿度 灰尘 污染
2019/12/25
管建伟
9
现场管理的“单一最好”原则
一处保管 户口管理
一日处理 今日事,今日毕
一个资料夹 资料夹一册化
一小时会议 一事一议,半小时更好
一张纸
报告、表格一张篇幅完全表达
一分钟电话 长话短说,不拖泥带水
一件工具 多样工具简化成一件
一个单元 在一个小组或一组设备内完工
许振超的技术研究工作: 许振超和队员们在桥吊每个操作环节抠时间。桥吊启动时,说明书上写 着,达到最高时速需要5秒钟,许振超计算后提出,3.5秒钟就够用,一 些司机不以为然地提出,抠.1.5秒有什么用?许振超为大家算了一笔账 :“如果一船有1000个集装箱,就能节约25分钟出来”。